In 2019, the unit labor cost in manufacturing rose 2.2%, the largest annual rise since 2012. Additionally, In the United States, the cost of manufacturing inputs increased by 4.3% in 2019, the largest annual increase since 2011, and the cost of manufacturing overhead increased by 3.7% in 2019.
Even more recently, according to the U.S. Bureau of Labor Statistics, the cost of manufacturing goods increased by 0.8% in February 2021. In fact, the cost of materials used in the manufacturing process increased by 2.1% in May 2021, whereas in the last six months, the manufacturing costs of consumer goods have risen by 0.7%.
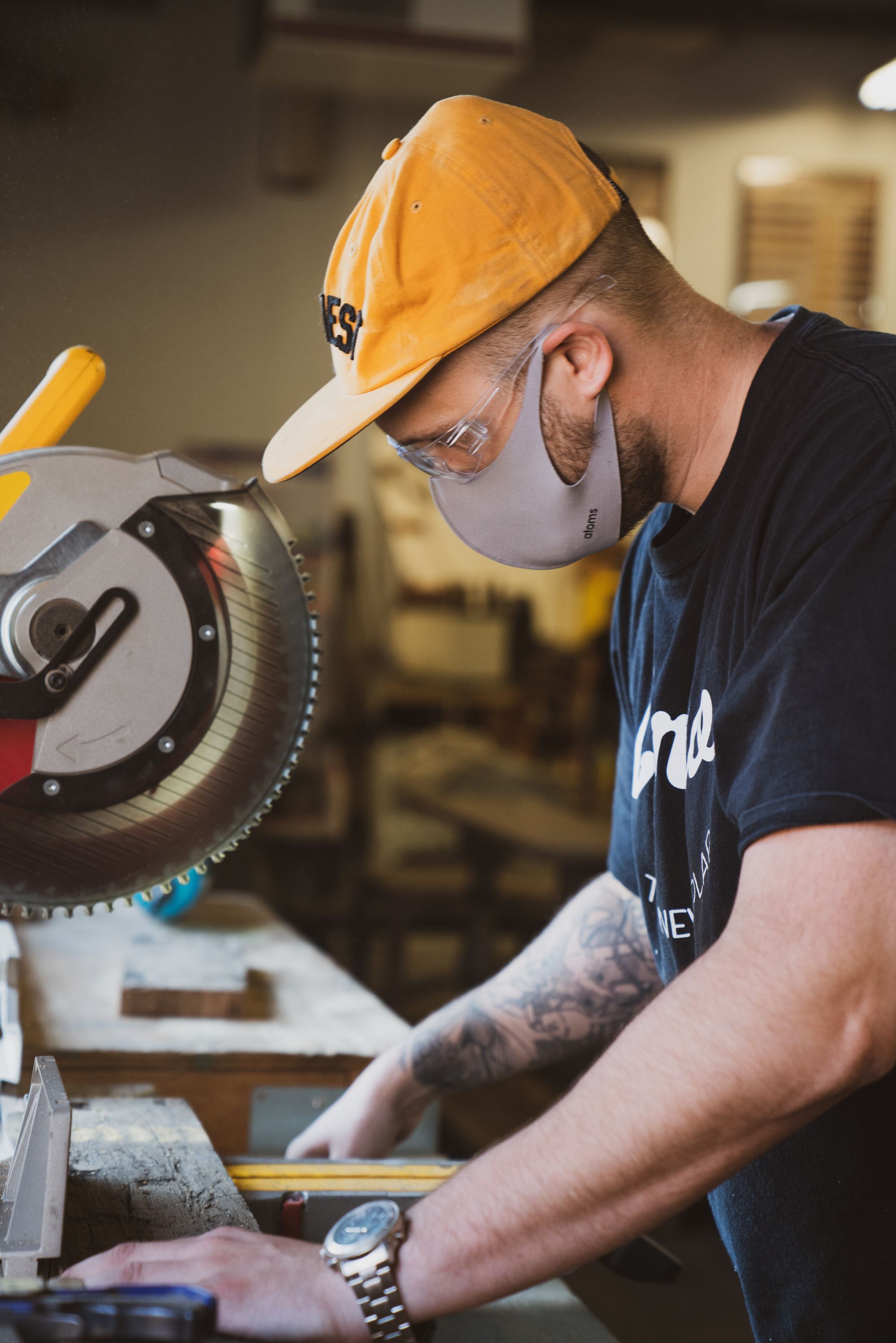
Thus, manufacturing costs are constantly under change, getting impacted by its various determining factors. But considering that the success of the business depends on its productivity as well as profitability, having an accurate prediction of its manufacturing costs will help it in reaching its targets.
Manufacturing cost is the sum of the costs of all resources consumed in the process of making a product. It is classified into three main categories: direct materials cost, direct labor cost, and manufacturing overhead.
Determining your manufacturing costs will help you correctly price your products and therefore ensure high net profits for your company.
In fact, by using the insights provided by the manufacturing costs, you will be able to find out whether you are meeting your goals and whether your production process is conducive to your desired level of productivity.
Maybe there is room to lean up your manufacturing by cutting down on hidden costs to your business. But how will you know where to start? What are manufacturing expenses beyond basic raw materials? What do you need to do to reduce these costs?
To be able to answer these questions and take the necessary steps, you need to have a complete understanding of manufacturing costs.
This article will help you in that by covering the following topics:
- What are Manufacturing Costs?
- What is the Difference Between Direct and Indirect Manufacturing Costs?
- What is the Difference Between the Manufacturing Costs and Production Costs?
- What is the Difference Between the Total Cost of Manufacturing and the Cost of Goods Sold?
- What are the 5 Benefits of Using the Total Manufacturing Cost Formula?
- What Will You Need to Calculate your Total Manufacturing Cost as per the Formula?
- How to Find Total Manufacturing Costs?
- 5 Effective Ways to Reduce Manufacturing Costs
- How can an MRP System Help You Manage Your Total Manufacturing Costs?
- How can Deskera Help You Manage Your Manufacturing Costs?
- Key Takeaways
- Related Articles
What are Manufacturing Costs?
Manufacturing costs are the costs incurred during the production of a product. These costs include the costs of:
- Direct Material - This refers to the primary raw materials used in the construction of a final product.
- Direct Labor - It is that portion of the labor cost of the production process that is assigned to a unit of production. Thus, all the staff who have a hand in the refining, assembly, and manufacturing of your products are included here.
- Manufacturing Overheads - These are costs that are applied to units of production based on a variety of possible allocation systems, such as by direct labor hours or machine hours incurred. It includes all the indirect materials and labor costs that have a secondary or support role. Some examples of manufacturing overheads are-
- Salaries and wages for quality assurance, industrial engineering, factory management, materials handling, and equipment maintenance personnel.
- Equipment repair parts and supplies
- Factory utilities
- Depreciation on factory assets
- Factory-related insurance and property taxes
Typically, manufacturing costs are presented in the income statement as separate line items. In fact, when you are accounting for inventory, you must make sure to include all manufacturing costs in the costs of work-in-process inventory and finished goods inventory.
What is the Difference Between Direct and Indirect Manufacturing Costs?
To ensure that you do not make the mistake of counting your costs twice, it is important that you understand the two categories in which manufacturing costs fall:
Direct Costs
Direct costs refer to everything that is spent on the bulk of the manufacturing process. This could be material costs (for example, raw materials) and time costs (for example, staff wages). For any costs to be considered as direct costs, they must play a physical role in assembly or production.
Indirect Costs
Indirect costs in your manufacturing process do not come from raw materials or labor primarily used in manufacturing. Instead, these costs include:
- Maintenance costs
- Utility bills
- Salary of the non-manufacturing staff
- MRO inventory (i.e., maintenance, repair, and operations inventory)
Thus, for example, nails and glue holding a wooden cabinet together are indirect materials called consumables, and thus their cost will be added under indirect costs to your total manufacturing costs.
Also, one of the costs that you need to especially watch out for is the depreciation in the value of your raw materials. Additionally, if you produce comestibles (i.e., perishables), then your raw materials and finished products in waiting could spoil.
Knowing how much you can lose in such situations is crucial for keeping your business afloat. In fact, only if you know that there is probable wastage in your manufacturing process would you be able to do something about it.
What is the Difference Between the Manufacturing Costs and Production Costs?
While production costs reflect all of the expenses associated with a company conducting its business, manufacturing costs represent only the expenses necessary to make the product.
Thus, production costs include several of the fixed costs and variable costs of operating a business. Additionally, raw material and labor costs are also included in the production costs. In contrast, manufacturing costs fall into three broad categories - materials, labor, and overhead.
For example, in production costs, the salary of the company accountant or the accountant’s office supplies are included in addition to the salary and supplies of the foreman. In manufacturing costs, however, only the expense incurred for the salary and supplies of the foreman is included.
Production costs may increase or decrease as production volume changes. This is because while the fixed costs that are included in the production costs remain constant, variable costs do not.
Thus, with an increase in production, the per-unit production cost decreases, making your business more profitable. This motivates many businesses to continue expanding their production up to its total capacity, thereby maximizing their profits.
In contrast, manufacturing costs, for the most part, are sensitive to changes in production volume. In fact, total manufacturing costs tend to increase as production increases.
What is the Difference Between the Total Cost of Manufacturing and the Cost of Goods Sold?
The total cost of manufacturing refers to the cost incurred to produce a product, and it includes the cost of materials, labor, and overhead.
In contrast, the cost of goods sold (COGS) only includes the direct costs associated with producing a product, such as the cost of materials and labor.
However, because COGS excludes indirect costs, it is often used as a more accurate measure of profitability.
What are the Benefits of Using the Total Manufacturing Cost Formula?
You might be wondering whether calculating the total manufacturing cost is worth the hassle or not. However, some of the benefits that you will reap by calculating the manufacturing costs are:
Lower Costs
Once you know the total cost of manufacturing a product, you will be able to easily identify ways to reduce that cost. This can lead to lower prices for your consumers, thereby encouraging returning customers while also ensuring higher net revenues and profits for your business.
Additionally, lower costs will also help your company to expand its operations and hire more workers - thereby ensuring that all customer demands are met, which leads to higher customer loyalty. It also helps in boosting the economy by creating new jobs and consequently also increasing consumer spending.
More Clarity Around Financial Health
Your company’s financial health depends on many factors, including your manufacturing costs. Thus, if you are able to understand your total manufacturing cost formula and then use it, then you will get a clearer picture of your overall financial situation.
This will help you in making better business decisions related to spending and investing. This will lead to increased returns on investment and assured growth of your business.
Informed Decisions Around Pricing
Knowing the total manufacturing costs of your product will help you in ensuring that you price your products appropriately, such that your business makes a profit. In fact, to do so, knowing the detailed product costing is crucial as this will ensure that you are making a well-informed decision.
Additionally, understanding your cost of products will help you and your managers in planning other strategic initiatives through which you can maximize your profitability.
If you do not understand your product cost clearly, then you will risk selling your product below its cost, resulting in a loss that will affect the health of your financial statements and financial KPIs.
On the other hand, if you price your products too high, then you might risk missing out on potential sales and market share. This will affect your revenue while risking the success of your company.
Thus, in either case, understanding your product costs is important for making informed pricing decisions.
In addition to profitability, your pricing decisions can also impact your other strategic objectives like market share and customer satisfaction.
For example, you may choose to price your products lower than your competitors to gain market share. Or, you may choose to price your higher to maximize your profits. Irrespective of whatever you decide your strategy to be, it should be based on a thorough understanding of product costs and other factors.
Less Waste
By understanding your total manufacturing costs, you will be able to identify ways to reduce your waste. This can lead to lower costs and a more efficient manufacturing process.
Having less waste is going to be very important to you because it will help you save costs, relieve undue pressure on your working capital, and improve your cash flow.
This is because when less material is wasted, there is less need to purchase new raw materials. Additionally, less waste will also lead to improved production efficiency and quality. One of the reasons behind this is that when there is less waste, there are fewer opportunities for defects to occur.
Due to this, products are more likely to be of higher quality overall. This will ensure that you meet your customer’s expectations, which in turn will maximize your profits.
Lastly, reducing waste will also promote green manufacturing and environmental sustainability, which, when carried out by you, will lead to positive brand awareness.
Insights that Drive Efficiency
Once you know your total manufacturing costs, you will be able to identify where inefficiencies exist. This will help you in making changes that lead to a more efficient manufacturing process and lower costs.
Thus, if you are looking to drive efficiency in your manufacturing process, then having insights imparted to you through manufacturing costs is one of the keys.
Based on these insights, you will be able to make changes that streamline your processes, identify and work on the areas that need improvement, identify and rectify the bottlenecks in your process, and thereby improve the overall efficiency of your manufacturing process.
These insights will thus help you in saving materials, labor, and other resources. In fact, sometimes, just by making a few small changes to your routing manufacturing, you will be able to have significant savings.
Lastly, improving the efficiency of your manufacturing process is important for ensuring that your products are of the highest quality and promptly meet your customers' demands. Thus, this will lead to an improvement in your operational metrics as well as business metrics.
What Will You Need to Calculate your Total Manufacturing Cost as per the Formula?
While the total manufacturing cost formula is a relatively easy calculation to make, it will require a lot of input from different areas of your business. However, let’s try to understand how the total manufacturing cost formula works through an example.
Imagine there is a skateboard manufacturer in the USA. Now let us consider what is likely to be consumed during its production. This will help us in identifying its different manufacturing costs.
- Direct material - The cost of plywood to make the board.
- Direct labor - The employees who will make and assemble the skateboard.
- Manufacturing overhead (Indirect labor) - For example, one of the manufacturing overheads might include the janitor in the workshop.
- Manufacturing overhead (indirect material) - For example, the masking tape for holding the board in place during its molding.
- Manufacturing overhead (Other) - This includes the costs of running machines like a belt sander or consuming spray paint canisters or the cost of its workshop’s rent and utilities.
Now that we have identified the areas of the business that have costs associated with it, we can move on to the formula and its application.
How to Find Total Manufacturing Costs?
The formula to find the total manufacturing costs is as follows:
Manufacturing Costs = Raw Materials + Direct Labor +Allocated Manufacturing Overhead
Now, to understand how you can apply your identified direct and indirect costs to the formula to find the total manufacturing cost, we will continue with the skateboard example discussed above.
Thus,
- The direct materials cost for one skateboard is the sum of the following:
- One deck ($20)
- Two metal trucks ($10)
- Four wheels ($16)
- Now, you could take the average of direct labor at $10 per unit as that company produces several skateboards per hour.
- The overhead costs can include the lubricant, bearing, staff, paint, and electricity at $10 per unit.
Therefore,
Total Manufacturing Costs = Raw Materials + Direct Labor +Allocated Manufacturing Overhead
56 = (20+10+16) + 10 + 10
Thus, your total manufacturing cost for one unit of the skateboard is $56. Once you know this total, you will be able to predict your total costs for a whole day, weeks, and even months of production.
However, you must remember to keep track of everything and run the actual total costs against the predicted costs. You should then assess if they are aligning at the end of the set time period or not and decide the necessary course of action to maintain or rectify the situation.
To be able to do this, though, it is important that you calculate the manufacturing costs with a production timeline in mind. This will make it easier and more manageable to pinpoint the number of funds that are being allocated to the manufacturing process in that time frame.
Also, you must remember that as you scale up your manufacturing cost calculation, you will need to consider things that do not scale at the same rate. This could be:
- Cheaper wholesale prices, when ordered in bulk, will bring your costs down.
- Higher maintenance costs for machines will bring your costs up.
Anticipating all these changes will help you stay on top of everything. It will also give you all the necessary information and insights to reduce your costs and improve your profit margin.
5 Effective Ways to Reduce Manufacturing Costs
Reducing your manufacturing costs is crucial for increasing the profitability of your business. However, this is often associated with a decrease in product quality. But, this does not always hold true.
This is because there are several cost-cutting mechanisms that streamline the manufacturing process, thereby leading to higher-quality products and healthier books of accounts.
Thus, some of the few effective methods that you can resort to reduce manufacturing costs without hurting the process and the product are:
Cut Down on the Material Costs
One of the areas where businesses spend a significant amount of their money is on materials. Thus, to reduce the impact of these costs on your operation, you should look for less costly raw materials.
However, while you are looking for cheaper materials to help you drive down your costs, it is important that you ensure the quality and integrity of your products do not suffer because of it. This will ensure that you are increasing your profitability without losing your brand image and, consequently, customers.
In fact, by decreasing material costs, you might also be able to decrease the price of your products, thereby making them affordable to a wider group of your buyer personas.
Consider Changing Suppliers
If sourcing cheaper raw materials is ultimately impacting the quality of the products coming off the line, then you should consider looking for arrangements and deals with other suppliers.
In some instances, it can be possible for you to negotiate with the current supplier to cut back on their asking price. For example, the promise of you extending your contract with them might entice them into providing you with materials at a lesser cost. Oftentimes this tactic is used during outsourcing manufacturing.
Make Use of Waste and Leftover Material
One of the best ways to reduce your manufacturing costs is by not discarding your leftover material but rather feeding it back into the production line, thereby ensuring that you are drawing more value from it.
An alternative to this would be that you sell off the waste to other parties that have a use for it. This way, your business will be able to earn some money back, tipping the ratio of accounts receivable to accounts payable back in its favor.
Try the Automation Route
Labor costs are one of the highest contributors in significantly driving up your total manufacturing costs. Thus, it makes sense for your business to cut back on this area and thus make your manufacturing lean.
One of the ways of doing this is to tool your manufacturing plant with more automated machines. This investment will pay off in the long run. Additionally, automated machines tend to be more efficient than human inputs, which in turn, will make your process faster and more productive as well.
In fact, this will help you save on additional business expenses that you might have otherwise incurred, for example, storage costs for inventory, loss of perishable goods, and so on.
Save on Energy Consumption
One of the ways to reduce your manufacturing overhead and, therefore, your manufacturing costs is by cutting back on your energy consumption by going green.
According to Forbes, unsubsidized renewable energy is the cheapest source of energy for manufacturers. Thus, switching to this energy form will make your operation less costly.
Alternatively, you can choose to install edge devices that will manage your current machine setup. These devices will monitor the energy consumption on your factory floor, turn off machines that are not being used, and optimize supply to those that need it.
Your efficiency, productivity, as well as profitability will thus be maximized through this.
How can an MRP System Help You Manage Your Total Manufacturing Costs?
When you are running a complicated manufacturing operation with many moving parts, efficiency is the key. Thus, it is valuable to implement an MRP system that will be able to help you manage your total manufacturing costs.
An MRP system is software that will be able to help you manage all your core business processes like:
- Supply chain
- Manufacturing
- Services
- Financial
And other such processes that are related to your organization and its working.
MRP systems come equipped with features that will help you simplify, plan, budget, automate, and accurately report the operation of your organization.
These insights will help you with resource capacity planning, demand planning, and shop floor scheduling such that your use of unnecessary resources is reduced while maintaining the quality of your products.
Additionally, they also come with an alert feature that will notify you when you have reached the reorder point of your inventory. This will make sure that you do not lose out on any business due to a lack of inventory, nor do you incur additional expenses due to excess inventory.
In fact, this software will also help you determine the optimal level of safety stock for your business.
Modern MRP systems are designed in a manner that they flexibly support and integrate into any manufacturing business process, creating a complete business management platform for your company.
Some of the several benefits for manufacturing companies like yours to implement MRP systems are:
- Better supply chain management
- Better inventory management
- Better management of warehouse and transportation
- Improving communication between departments and comparing metrics across them
- Facilitating end-to-end visibility and traceability of business processes
- Capturing real-time reporting that you can quickly access
- Centralizing operational and financial information
- Optimizing operations for better productivity, efficiency, and proactive customer service
- Having the ability to adapt when faced with business changes or disruptions
Thus, MRP systems will provide you visibility and ease of execution, thereby helping you make more strategic business decisions, increasing the accuracy of business processes, and giving you the time to focus on core business processes.
How can Deskera Help You Manage Your Manufacturing Costs?
As a manufacturer or retailer, it is crucial that you stay on top of your manufacturing processes and resource management.
You must manage production cycles, resource allocations, safety stock, reorder points, and much more to achieve this.
Deskera MRP is the one tool that lets you do all of the above. With Deskera, you can:
- Track raw materials and finished goods inventory
- Manage production plans and routings
- Maintain bill of materials
- Optimize resource allocations
- Generate detailed reports
- Create custom dashboards
And a lot more.
It is also possible to export information and data on Deskera MRP from other systems. Additionally, Deskera MRP will give you analytics and insights to help you make decisions.
So go ahead and book a demo for Deskera MRP today!
Key Takeaways
Manufacturing cost is the sum of the costs of all resources consumed in the process of making a product. It is classified into three main categories: direct materials cost, direct labor cost, and manufacturing overhead.
Thus, essentially, your total manufacturing costs are an expense analysis that calculates how each of your company’s departments has contributed to producing a finalized product. This looks at all stages of your manufacturing process, from raw materials to work in progress to the final result.
Manufacturing cost thus showcases how much your company has spent to produce its inventory in a given period of time. Therefore, some of the benefits that you will be able to reap by calculating your manufacturing costs are:
- Lower costs
- More clarity around financial health
- Informed decisions around pricing
- Less waste
- Insights that drive efficiency
The five effective ways to reduce your manufacturing costs are:
- Cut down on the material costs
- Consider changing suppliers
- Make use of waste and leftover material
- Try the automation route
- Save on energy consumption
To be able to accurately calculate your manufacturing costs in real-time and make better decisions based on it, you should implement Deskera MRP, which comes equipped with all the features that will automate several of your business processes while helping in setting the path for its success.
Related Articles
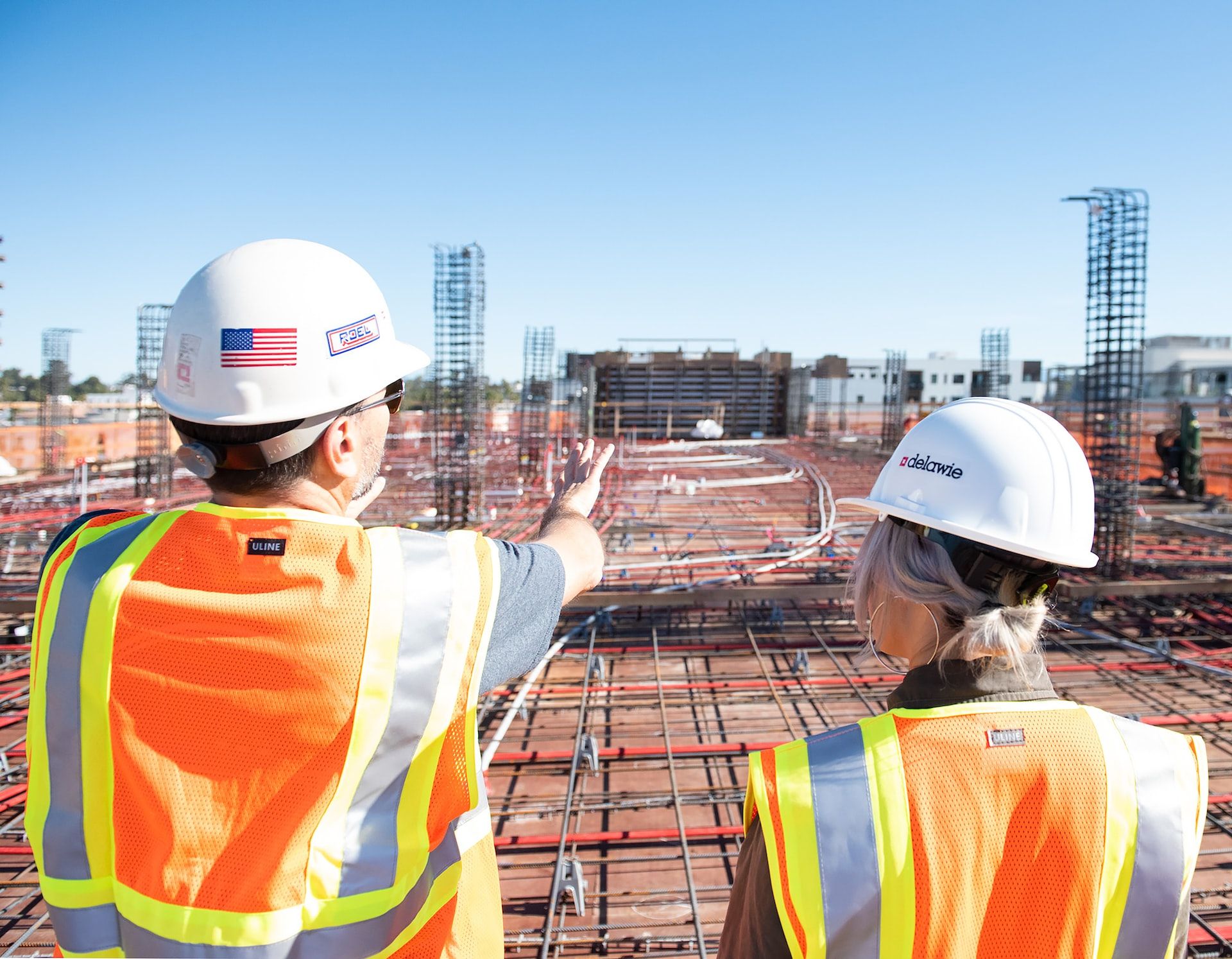
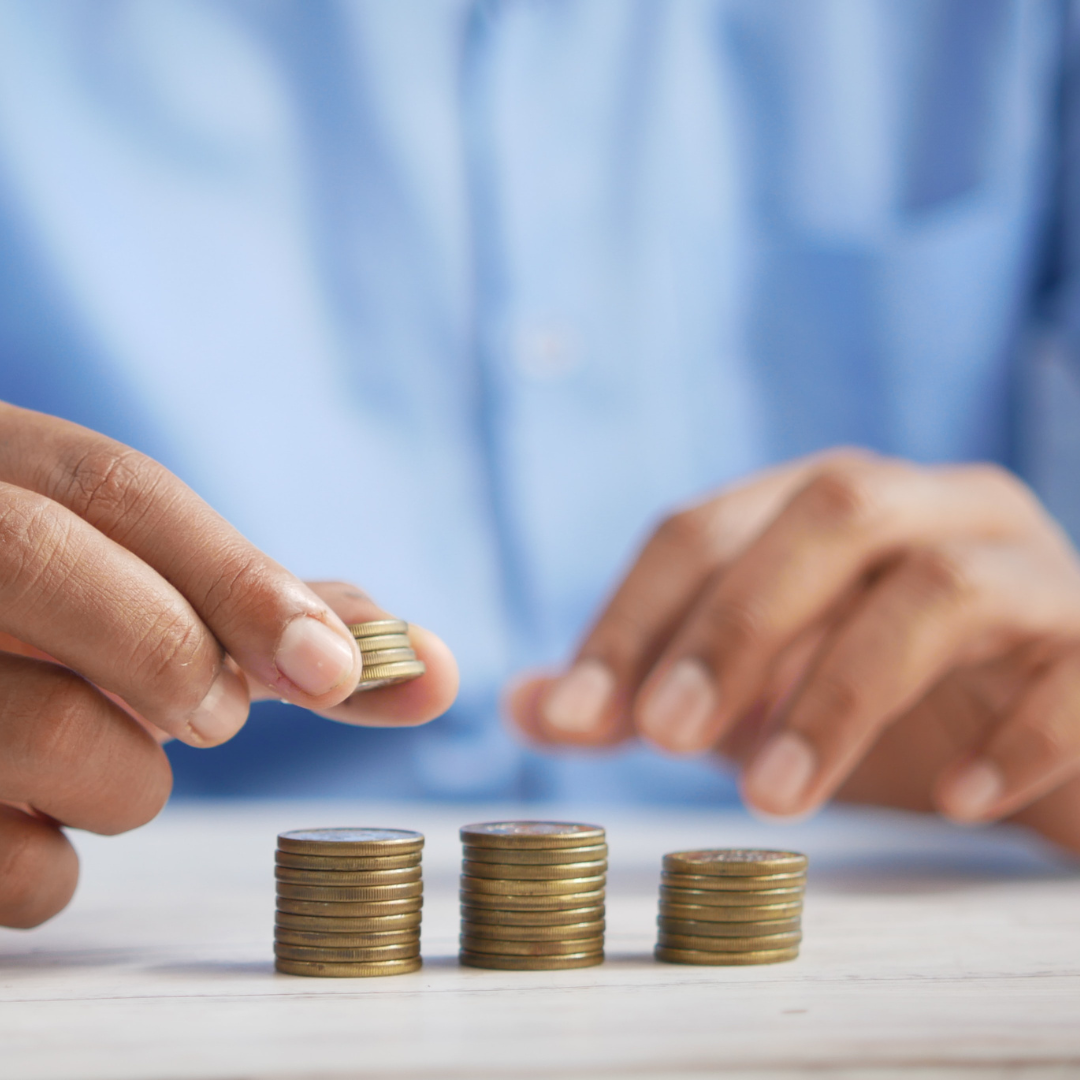
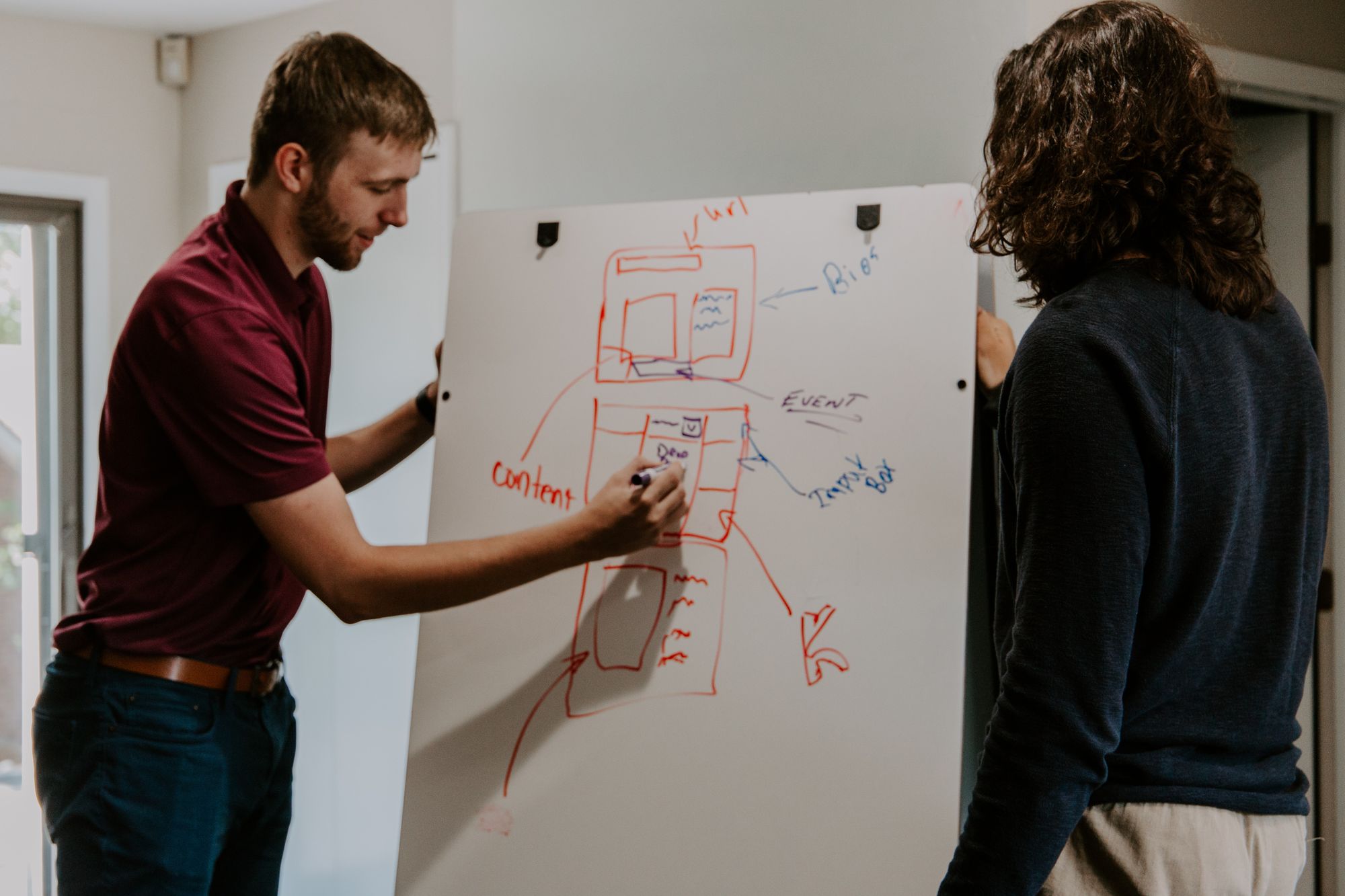
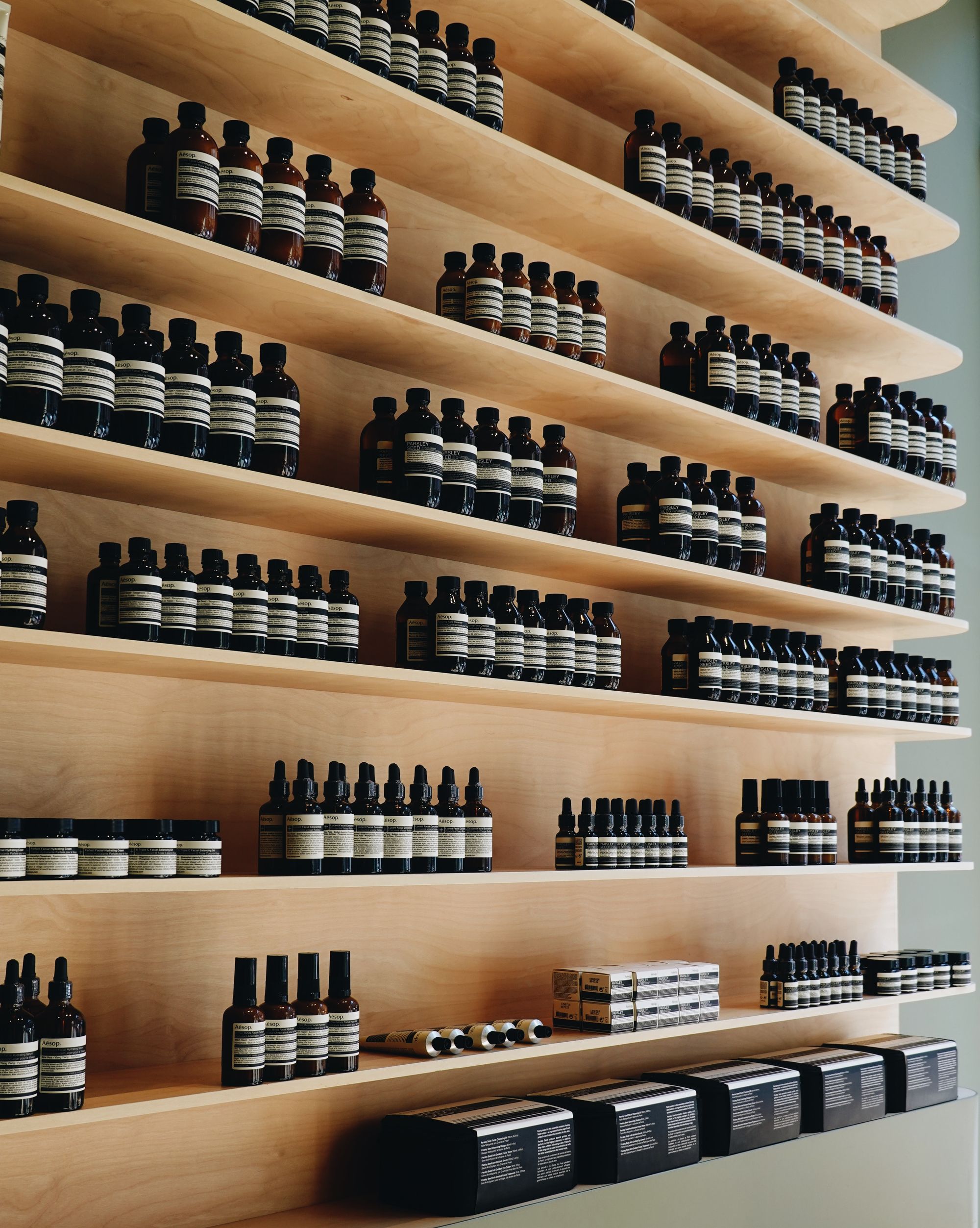
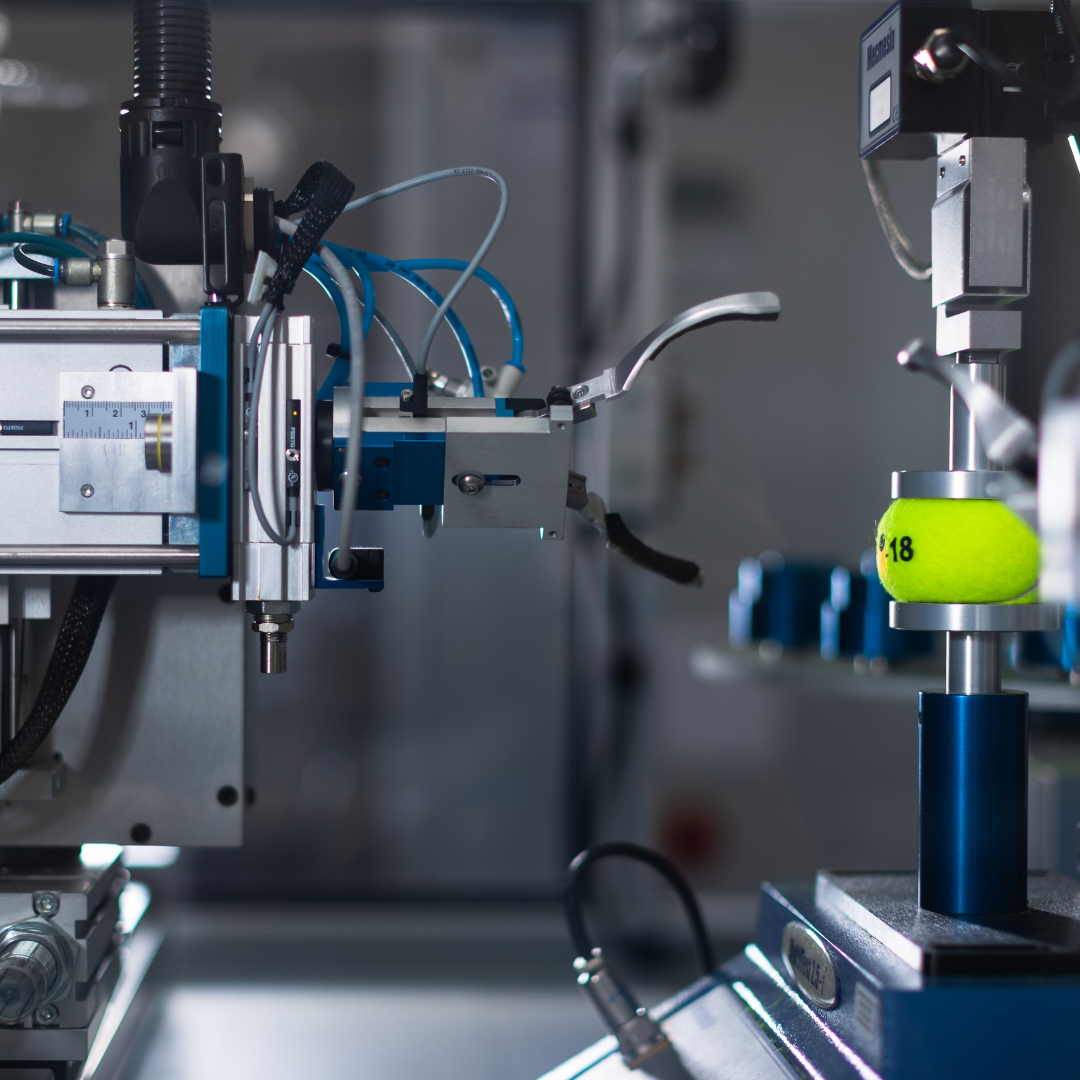