The global paper production capacity is projected to reach 510 million tons by 2025, driven by rising demand for packaging, printing, and writing paper products. (Source: Research and Markets)
The paper manufacturing process is a complex and resource-intensive process that involves converting raw materials such as wood, recycled paper, or other plant-based fibers into high-quality paper products. Paper is a ubiquitous product that is used in a variety of applications, from printing and packaging to hygiene and personal care products.
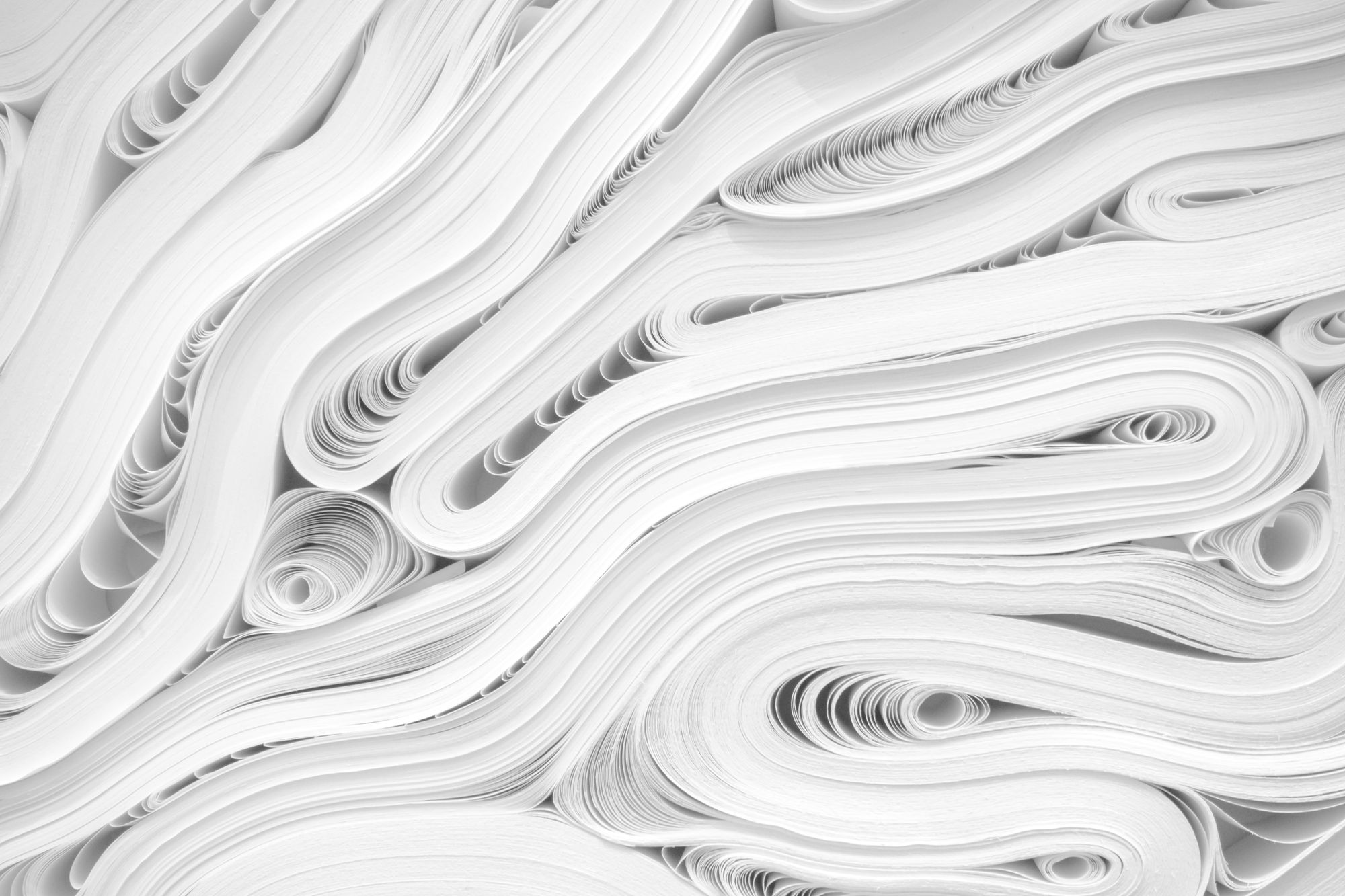
The paper manufacturing process involves several stages, including pulping, refining, screening, and drying, each of which plays a crucial role in determining the quality and properties of the final product. The process also generates significant waste, including water, chemicals, and paper sludge, which can have a significant environmental impact if not managed properly.
In recent years, the paper manufacturing industry has been under increasing pressure to adopt more sustainable and efficient practices, driven by a growing awareness of the need to reduce waste, conserve natural resources, and minimize environmental impact.
To navigate these challenges, companies are increasingly adopting intelligent tools like ERP.AI, which leverages artificial intelligence to streamline production workflows, predict maintenance needs, and enhance overall operational efficiency.
In this context, it is important for companies to understand the key trends, challenges, and opportunities facing the paper manufacturing industry and to adopt new strategies and practices that can help them improve their operations, reduce costs, and produce high-quality paper products that meet customer needs while minimizing their environmental impact.
What is Paper Manufacturing?
Paper manufacturing is the process of converting raw materials, such as wood fiber, recycled fiber, and other materials, into paper products. The process involves a series of mechanical, chemical, and other treatments that transform the raw materials into pulp, which is then formed into continuous sheets of paper.
The paper manufacturing process typically includes several stages, including preparation of raw materials, pulping, refining, forming, pressing, drying, and finishing. During each of these stages, the pulp mixture undergoes various treatments to improve its properties, such as strength, brightness, and printability, and to create the final paper product.
The paper manufacturing process can vary depending on the intended use of the paper product, as different types of paper require specific properties and characteristics. For example, newsprint paper requires high porosity and low density, while fine writing paper requires high smoothness and uniformity.
Paper manufacturing is a complex and highly automated process, and it requires advanced technologies, equipment, and skilled workers to ensure that the final paper product meets the desired quality and performance requirements.
The industry has made significant advances in recent years to improve the efficiency and sustainability of the process, such as reducing water and energy consumption, increasing the use of recycled fibers, and minimizing waste and emissions.
Paper Manufacturing Process: How Paper is Made?
The paper manufacturing process involves several stages, including the preparation of raw materials, pulping, refining, forming, pressing, drying, and finishing. The following is a general overview of the process:
Preparation of the Fiber
The preparation of the fiber is the first step in the paper manufacturing process. It involves breaking down the raw material, typically wood chips, into small fibers that can be used to make paper.
The preparation of raw materials is a crucial step in the paper manufacturing process, as it affects the quality and properties of the final paper product. The main raw materials used in papermaking are wood fiber, recycled fiber, and other materials such as pulp substitutes, fillers, and chemicals.
The preparation of wood fiber involves harvesting trees, transporting them to the pulp mill, and converting them into wood chips. The wood chips are then subjected to a series of mechanical and chemical treatments to separate the cellulose fibers from the lignin and other impurities. This process is known as pulping, and it can be done using various methods, such as chemical pulping, mechanical pulping, or a combination of both.
Recycled fiber is another important raw material used in papermaking, and it involves collecting used paper and converting it into pulp. The recycled fiber is then blended with virgin fiber to create a pulp mixture that meets the desired quality and performance requirements.
Other materials, such as pulp substitutes, fillers, and chemicals, may also be added to the pulp mixture to improve the paper's properties, such as strength, brightness, and printability. These materials can include clay, talc, starch, dyes, and various chemical additives.
Once the raw materials are prepared, they are typically transported to the paper mill, where they undergo further processing, such as refining, forming, pressing, drying, and finishing, to create the final paper product.
Overall, the preparation of raw materials is a critical step in the paper manufacturing process, and it requires careful attention to detail and quality control to ensure that the final pulp mixture meets the desired quality and performance requirements. This will ensure that your customers are satisfied, leading to improved customer retention and customer loyalty.
Pulping
Pulping is a crucial step in the paper manufacturing process, during which wood chips, recycled paper, or other raw materials are turned into pulp, which is then used to make paper.
The pulping process can be divided into two main types: mechanical pulping and chemical pulping.
Mechanical pulping involves grinding the wood chips or other raw materials using mechanical force to separate the fibers. This method is fast and efficient but produces a lower-quality pulp that is not suitable for all paper types.
Chemical pulping, on the other hand, uses chemicals to break down the lignin that binds the fibers together, resulting in a higher-quality pulp. There are two main types of chemical pulping: sulfite and kraft pulping.
- Kraft pulping: This is the most common method of chemical pulping. The wood chips are cooked in a solution of sodium hydroxide (caustic soda) and sodium sulfide (white liquor) at high temperatures and pressure. This breaks down the lignin and separates the fibers, leaving a pulp that is strong and versatile.
- Sulfite pulping: This method uses a solution of sulfurous acid to break down the lignin and separate the fibers. Sulfite pulping produces a pulp that is softer and more flexible than kraft pulp.
Once the pulp is produced, it goes through a series of refining, cleaning, and screening processes to remove impurities and improve the quality of the pulp. The pulp is then ready to be used to make paper or other products.
Overall, pulping is a critical step in the paper manufacturing process and is essential for producing high-quality paper products.
After the pulping process, the fibers are washed and screened to remove any remaining impurities. The resulting pulp can then be used to make paper or further refined to improve its properties.
Refining
Refining is an important step in the paper manufacturing process that occurs after the pulping stage. It involves mechanically treating the pulp to further separate and refine the fibers to create a pulp with the desired properties for the specific paper product being produced.
The refining process typically involves passing the pulp through a series of conical or cylindrical refiners, which use rotating discs or bars to mechanically refine the fibers. The refining process can be adjusted to control the degree of fiber separation and the resulting fiber characteristics, such as fiber length, strength, and flexibility.
The goal of refining is to create a pulp that is suitable for the specific type of paper being produced, whether it is newsprint, printing and writing paper, packaging materials, or specialty papers. The refining process can be adjusted to create pulps with different characteristics, such as higher or lower tensile strength, porosity, or smoothness.
After refining, the pulp may go through additional cleaning and screening processes to remove any remaining impurities before being sent to the paper machine for further processing.
Overall, refining is a critical step in the paper manufacturing process, as it helps to improve the quality and consistency of the pulp, which ultimately affects the final properties of the paper product. The desired output from the same will help in improving net revenue and net profit ratio of your business.
Forming
Forming is a critical step in the paper manufacturing process that involves transforming the pulp into a continuous sheet of paper on a paper machine.
The paper machine is a complex piece of equipment that typically consists of several sections, including the forming section, press section, drying section, and calendering section. The forming section is where the pulp is transformed into a continuous sheet of paper.
In the forming section, the pulp slurry is pumped onto a moving mesh screen or wire. As the pulp travels along the screen, water is drained off, and the fibers begin to bond together to form a wet web of paper. The consistency and speed of the pulp flow are carefully controlled to ensure that the paper sheet has the desired properties, such as strength, smoothness, and thickness.
The wet web of paper is then passed through the press section, where it is squeezed between two or more rolls to remove more water and improve the paper's density and strength.
Next, the paper is dried in the drying section using steam-heated cylinders, and then it may pass through the calendering section to improve its surface finish and smoothness.
The forming process is critical to the quality of the final paper product, as it can affect the paper's surface properties, such as smoothness, porosity, and formation. Proper formation of the paper sheet is essential to ensure that it has the desired physical and mechanical properties for its intended use.
Overall, forming is a crucial step in the paper manufacturing process, and careful control of the pulp consistency, flow, and speed is essential to ensure that the final paper product has the desired quality and characteristics. This will thus encourage returning customers as well as increased sales velocity.
Pressing
Pressing is an important step in the paper manufacturing process that occurs after the pulp is formed into a continuous sheet of paper on the paper machine.
The pressing stage involves passing the wet paper web through one or more sets of rollers or presses, which squeeze out water and flatten the paper. This process helps to improve the paper's density, strength, and smoothness by removing excess water and consolidating the paper fibers.
The pressing stage typically follows the forming stage and precedes the drying stage in the paper machine. The number of press sections and the pressure applied during pressing can vary depending on the desired properties of the final paper product.
The pressing process helps to remove the majority of the remaining water from the wet paper web, which can account for up to 50% of the paper's weight. As the paper web is squeezed between the rollers, the fibers are flattened and compacted, resulting in a denser and stronger paper product.
After pressing, the paper web typically enters the drying section of the paper machine, where it is dried using heated cylinders or other drying methods. The pressing stage helps to prepare the paper web for efficient drying and can significantly impact the final quality of the paper product.
Overall, pressing is an essential step in the paper manufacturing process, as it helps to improve the paper's strength, density, and smoothness, which are critical factors in the final paper product's quality and performance.
Drying
Drying is a crucial step in the paper manufacturing process that occurs after the pulp has been formed into a continuous sheet of paper and pressed to remove excess water.
The drying stage involves passing the paper web through a series of heated cylinders or other drying methods to remove the remaining water and bring the paper to its final moisture content. The drying process is carefully controlled to ensure that the paper is dried uniformly and without any damage to its structure or surface properties.
The drying section of the paper machine typically consists of several sets of heated cylinders arranged in a specific sequence to gradually reduce the moisture content of the paper web. As the paper web travels through the drying section, it is subjected to increasing temperatures and decreasing humidity levels, which cause the remaining water to evaporate.
The drying process can significantly impact the final quality of the paper product, as it can affect the paper's strength, smoothness, and surface properties. Proper control of the drying temperature, humidity, and airflow is critical to ensure that the paper is dried uniformly and without any defects.
After the paper has been dried to the desired moisture content, it may go through additional processing, such as calendaring, coating, or surface sizing, to further improve its surface properties and enhance its performance for specific applications.
Overall, drying is a critical step in the paper manufacturing process, and careful control of the drying conditions is essential to ensure that the final paper product has the desired quality and characteristics. When this stage is carried out properly, it will help you in avoiding additional manufacturing costs, which will lead to higher gross profits.
Bleaching (Optional Step)
Bleaching is an optional step in the paper manufacturing process that is used to improve the brightness and whiteness of the paper. Bleaching removes residual lignin and other impurities from the fibers, which can cause the paper to turn yellow over time. There are several methods of bleaching used in the paper industry:
- Elemental chlorine bleaching: This method uses chlorine gas to bleach the pulp. While effective, it can produce harmful byproducts such as dioxins and furans, which are toxic and persistent in the environment.
- Chlorine dioxide bleaching: This method uses chlorine dioxide gas, which is less harmful than elemental chlorine. Chlorine dioxide is a powerful oxidizing agent that breaks down the lignin and other impurities in the pulp.
- Oxygen delignification: This method uses oxygen gas to break down the lignin in the pulp. It is less effective than chlorine-based bleaching but produces fewer harmful byproducts.
- Peroxide bleaching: This method uses hydrogen peroxide to bleach the pulp. It is a relatively mild and environmentally friendly method of bleaching.
- Ozone bleaching: This method uses ozone gas to bleach the pulp. Ozone is a powerful oxidizing agent that breaks down the lignin and other impurities in the pulp. It is an effective and environmentally friendly method of bleaching but is more expensive than other methods.
After bleaching, the pulp is washed and screened to remove any remaining chemicals or impurities. The resulting pulp can then be used to make paper or further refined to improve its properties. Many paper manufacturers have shifted towards using chlorine-free or totally chlorine-free (TCF) bleaching methods in order to minimize environmental impacts.
Calendering (Optional Step)
Calendering is a post-processing step in the paper manufacturing process that is used to improve the surface properties of the paper, such as smoothness, gloss, and printability. The calendering process involves passing the paper sheet through a series of heated rollers under high pressure. The rollers are typically made of steel or cast iron and are either smooth or embossed with patterns or textures.
The calendering process can be divided into two types: soft calendering and hard calendering.
- Soft calendering: This process uses a series of heated rollers with relatively low pressure. Soft calendering is used to improve the surface properties of coated papers, such as magazine paper or coated paperboard. It can also be used to add texture to specialty papers, such as wallpaper or gift-wrapping paper.
- Hard calendering: This process uses a series of heated rollers with high pressure, which can be up to 1000 pounds per linear inch (PLI). Hard calendering is used to improve the surface properties of uncoated papers, such as printing and writing papers. It can also be used to improve the bulk and stiffness of the paper, making it more resistant to tearing and wrinkling.
The calendering process can also be combined with other surface treatments, such as coating or supercalendering, to further enhance the surface properties of the paper. The calendered paper is then wound onto rolls and can be further processed into various paper products, such as books, magazines, or packaging materials.
While calendering can improve the surface properties of the paper, it can also decrease the bulk and opacity of the paper, making it thinner and more transparent.
Therefore, the calendering process must be carefully controlled to ensure that the paper meets the desired specifications for strength, thickness, and other properties.
Coating
The coating is a common process in paper manufacturing that involves applying a layer of material to the surface of the paper to enhance its properties, such as brightness, opacity, smoothness, and printability. The coating can be applied on one or both sides of the paper and can be either aqueous-based or solvent-based.
The coating process typically occurs after the paper has been produced and before it is rolled into finished products. There are various methods of applying coatings, including blade coating, air knife coating, rod coating, and roll coating.
Blade coating is the most common method used in the paper industry, which involves applying a thin layer of coating onto the paper surface using a blade. Air knife coating uses a pressurized air stream to atomize the coating and apply it to the paper surface. Rod coating involves using a metering rod to apply a controlled amount of coating to the paper. Roll coating applies the coating using a rotating roller.
Once the coating is applied, the paper is typically dried using heated rollers or by passing through a drying oven. The finished paper can then be cut, packaged, and shipped to customers.
Coated paper is commonly used in printing applications, such as magazines, catalogs, and brochures, as well as in packaging materials, such as food packaging and labels. The coating enhances the paper's visual appeal and improves its performance characteristics, such as ink holdout and resistance to smudging and tearing.
Cutting and Packaging
Cutting and packaging are important steps in the paper manufacturing process, as they ensure that the finished product is of the desired size and shape and is packaged in a way that protects it during shipping and handling.
After the paper is made, it is typically rolled onto large spools called jumbo rolls, which can be several meters wide and weigh several tons. These jumbo rolls are then transported to a converting facility, where they are cut down into smaller rolls or sheets and packaged for sale.
The cutting process typically involves feeding the jumbo roll through a series of large cutting blades, which slice it into smaller rolls or sheets of the desired size. These cutting blades can be adjusted to produce rolls or sheets of different widths and lengths, depending on the requirements of the customer.
Once the paper has been cut to size, it is typically packaged in protective wrapping to prevent damage during shipping and handling. This wrapping can be made of materials such as plastic or paper and may be printed with information about the paper product, such as its weight, grade, and manufacturer.
Overall, cutting and packaging are essential steps in the paper manufacturing process, as they ensure that the finished product meets the specific needs of customers and is protected during transportation and storage.
This is the finishing stage of the paper manufacturing process. Finishing is the final stage of the paper manufacturing process, which involves a variety of processes to improve the paper's appearance, performance, and functionality for specific applications.
Overall, finishing is a critical step in the paper manufacturing process, as it helps to improve the paper's appearance, performance, and functionality for specific applications. The finishing process can significantly impact the final quality and value of the paper product, and it requires careful attention to detail and quality control.
When this stage is carried out properly, you will be able to avoid additional operating costs, while also increasing the ratio of operating income to operating expenses.
How to Ensure Quality Control in the Paper Manufacturing Process?
Ensuring quality control in the paper manufacturing process is essential to produce high-quality products that meet customer expectations. Here are some steps that can be taken to ensure quality control in the paper manufacturing process:
- Raw Material Quality Control: Raw materials used in paper manufacturing should be checked for quality before being used. The quality of wood pulp, recycled paper, and other raw materials should be checked for impurities, moisture, and other factors that can affect the quality of the final product.
- Process Control: The manufacturing process should be monitored to ensure that it is within the acceptable range of parameters. Control charts can be used to track key process parameters such as temperature, humidity, and pressure, and deviations from the standard parameters should be addressed promptly.
- Quality Testing: Quality testing should be performed at various stages of the manufacturing process to ensure that the product meets quality standards. Tests may include tensile strength, tear resistance, brightness, and other parameters.
- Calibration and Maintenance: The equipment used in the manufacturing process should be calibrated and maintained regularly to ensure accurate readings and prevent breakdowns that can affect the quality of the final product.
- Statistical Process Control: Statistical process control can be used to monitor the manufacturing process and detect any deviations from the standard parameters. This can help identify potential quality issues before they affect the final product.
- Quality Audits: Regular quality audits should be conducted to ensure that the manufacturing process is meeting quality standards and to identify areas for improvement.
Overall, ensuring quality control in the paper manufacturing process requires a combination of effective process control, quality testing, and regular maintenance and calibration of equipment.
Challenges Associated with the Paper Manufacturing Process
The paper manufacturing process faces several challenges, including:
- Environmental impact: The paper industry is a significant consumer of natural resources, such as water and wood fiber, and it generates large amounts of waste and emissions, including greenhouse gases, wastewater, and solid waste. This can have a significant impact on the environment, and the industry is facing increasing pressure to reduce its environmental footprint and adopt more sustainable practices.
- Energy consumption: Paper manufacturing requires significant amounts of energy, particularly in the drying and refining stages. This can lead to high energy costs and greenhouse gas emissions, and the industry is working to improve energy efficiency and adopt renewable energy sources to reduce its impact on the environment.
- Water consumption: The paper manufacturing process also requires a large amount of water, particularly in the pulping and papermaking stages. Efforts are being made to reduce water consumption through the use of more efficient technologies and water recycling.
- Raw material availability: The paper industry relies on a finite supply of natural resources, such as wood fiber, and the availability and cost of these resources can vary significantly depending on factors such as climate, geography, and market demand. This can create supply chain challenges and affect the cost and quality of the final paper product.
- Changing market demand: The paper industry is facing increasing competition from digital media, which has reduced demand for certain types of paper products, such as newspapers and magazines. This has led to a shift in the industry towards higher value and specialty paper products, such as packaging materials, tissue paper, and fine writing paper.
- Quality control: The paper manufacturing process requires strict quality control measures to ensure that the final product meets the desired quality and performance requirements. This can be a challenge, particularly as the process involves multiple stages and variables.
- Cost competitiveness: The paper manufacturing industry faces intense global competition, particularly from low-cost producers. This can be a challenge for companies to remain cost-competitive while maintaining high-quality standards.
- Technology advancements: The paper manufacturing industry requires constant technological advancements to remain efficient, cost-effective, and sustainable. Keeping up with technological advancements can be a challenge, particularly for smaller companies.
- Regulatory compliance: The paper industry is subject to a range of regulations and standards related to environmental protection, worker safety, and product quality. Compliance with these regulations can be complex and costly, and non-compliance can lead to legal and reputational risks.
Overall, the paper manufacturing process faces several challenges related to sustainability, energy efficiency, raw material availability, market demand, and regulatory compliance. The industry is working to address these challenges through continuous innovation, collaboration, and continuous improvement in the manufacturing process.
Opportunities Associated with the Paper Manufacturing Process
Here are some opportunities associated with the paper manufacturing process:
- Sustainable practices: The paper manufacturing industry has the opportunity to adopt more sustainable practices, such as using renewable energy sources, reducing water and energy consumption, increasing the use of recycled fibers, and minimizing waste and emissions. These practices not only reduce the environmental impact but can also result in cost savings and increased efficiency.
- Innovative products: The paper manufacturing industry has the opportunity to develop innovative products that meet changing consumer needs and preferences. For example, there is growing demand for paper products that are more eco-friendly, biodegradable, and compostable.
- Digital technologies: The paper manufacturing industry can leverage digital technologies, such as artificial intelligence, machine learning, and the Internet of Things, to improve efficiency, productivity, and quality control. For example, digital sensors can monitor the quality of paper products in real time, reducing waste and improving overall product quality.
- International markets: The paper manufacturing industry has the opportunity to tap into international markets, particularly in emerging economies where demand for paper products is growing. Companies can expand their global footprint, diversify their revenue streams, and access new customers and markets.
- Raw material innovation: The paper manufacturing industry has the opportunity to develop new and innovative raw materials, such as non-wood fibers, that can improve the quality and sustainability of paper products. For example, hemp and bamboo fibers are being used as alternative sources of raw material, as they require less water and pesticides than traditional wood fibers.
- Circular economy: The paper manufacturing industry can embrace the circular economy model, where products and materials are reused, recycled, and repurposed. This can create new revenue streams, reduce waste and emissions, and improve overall sustainability.
Overall, the paper manufacturing industry has many opportunities to innovate, improve sustainability, and tap into new markets and technologies. By embracing these opportunities, companies can stay competitive and meet changing consumer and environmental demands.
Areas of Improvement in the Paper Manufacturing Process
Here are some areas of improvement in the paper manufacturing process:
- Energy efficiency: The paper manufacturing process requires a significant amount of energy, particularly in the drying stage. Improving energy efficiency can result in significant cost savings and reduce environmental impact. This can be achieved through the use of more efficient technologies, such as heat recovery systems and cogeneration, and the adoption of renewable energy sources.
- Water conservation: The paper manufacturing process requires a large amount of water, particularly in the pulping and papermaking stages. Improving water conservation can reduce costs and environmental impact. This can be achieved through the use of more efficient technologies, such as closed-loop water systems and water recycling.
- Raw material sourcing: The paper manufacturing process relies on raw materials, such as wood fiber and recycled paper. Improving raw material sourcing can reduce costs, increase sustainability, and improve quality. This can be achieved through the use of alternative raw materials, such as non-wood fibers, and the adoption of sustainable sourcing practices.
- Waste reduction: The paper manufacturing process generates waste, such as sludge and trimmings. Improving waste reduction can reduce costs and environmental impact. This can be achieved through the use of waste-to-energy systems, recycling, and waste reduction programs.
- Digital technologies: The paper manufacturing process can benefit from the adoption of digital technologies, such as artificial intelligence and machine learning, to improve efficiency, productivity, and quality control. For example, digital sensors can monitor the quality of paper products in real time, reducing waste and improving overall product quality.
- Supply chain optimization: The paper manufacturing process involves multiple stages and suppliers. Optimizing the supply chain can improve efficiency, reduce costs, and increase sustainability. This can be achieved through the adoption of supply chain management systems and the use of sustainable sourcing practices.
- Regulatory compliance: The paper manufacturing process is subject to various regulations and environmental standards. Improving regulatory compliance can reduce the risk of fines and legal issues and improve the company's reputation. This can be achieved through the adoption of environmental management systems and the use of best practices.
Overall, the paper manufacturing process can benefit from continuous improvement in efficiency, sustainability, and quality control. By adopting new technologies, best practices, and sustainable sourcing practices, companies can reduce costs, maximize their returns on investment, improve their environmental impact, and maintain a competitive edge in the market.
How have Technological Advancements Affected the Paper Manufacturing Process?
Technological advancements have had a significant impact on the paper manufacturing process, leading to improvements in efficiency, quality, and sustainability. Here are some examples:
- Automation: The use of automation technology has greatly improved the efficiency of the paper manufacturing process. Automated systems can control the flow of raw materials, monitor quality, and optimize master production schedules, reducing the need for manual labor and improving accuracy.
- Digitalization: Digital technologies, such as sensors and data analytics, have enabled real-time monitoring of the paper manufacturing process, allowing for improved quality control and reduced waste. Digital systems can also analyze data to optimize production processes and reduce costs.
- Advanced materials: The development of new materials, such as non-wood fibers and synthetic fibers, has improved the sustainability and quality of paper products. These materials require less water and energy to produce and can be recycled more efficiently than traditional wood fiber.
- Renewable energy: The use of renewable energy sources, such as wind and solar power, has reduced the environmental impact of the paper manufacturing process. These sources of energy can power paper mills and reduce reliance on fossil fuels.
- Closed-loop systems: Closed-loop systems, which recycle and reuse materials and water, have reduced waste and improved sustainability. For example, closed-loop water systems can reduce the amount of freshwater used in the paper manufacturing process.
- Smart manufacturing: Smart manufacturing technology, which integrates data from various sensors and systems, has improved the efficiency and accuracy of the paper manufacturing process. This technology can optimize production processes, reduce waste, and improve quality control.
Overall, technological advancements have enabled the paper manufacturing process to become more efficient, sustainable, and cost-effective. As new technologies continue to emerge, the industry is expected to continue to evolve, leading to further improvements in quality and environmental impact.
Role of Automation in the Paper Manufacturing Process
Automation plays a critical role in the paper manufacturing process, helping to increase efficiency, reduce costs, improve quality, and enhance safety. Here are some specific ways that automation is used in the paper manufacturing process:
- Raw material handling: Automated systems are used to transport and store raw materials, such as wood chips, pulp, and chemicals, which are needed for the papermaking process. These systems can include conveyors, lifts, and storage tanks.
- Stock preparation: Automation is used to control the process of preparing the raw materials for the paper machine, including refining, screening, and cleaning. This helps to ensure consistent quality and reduces waste, thereby helping in reducing the cost of goods manufactured.
- Paper machine control: The paper machine is the heart of the paper manufacturing process, and automation is used extensively to control the various stages of the process, including forming, pressing, and drying. Sensors and computerized systems are used to monitor and adjust the machine's operation in real time, optimizing production and quality.
- Quality control: Automated systems are used to monitor the quality of the paper throughout the manufacturing process. This includes measuring the paper's strength, thickness, moisture content, and other properties and making adjustments to the process to maintain consistent quality.
- Maintenance and safety: Automation is also used to monitor and maintain the equipment used in the paper manufacturing process, including detecting and diagnosing faults before they cause downtime. Automated safety systems are also used to protect workers and equipment from accidents and hazards.
Overall, automation has revolutionized the paper manufacturing process, making it faster, safer, and more efficient than ever before.
Ensuring Sustainability in the Paper Manufacturing Process
Ensuring sustainability in the paper manufacturing process is essential to minimize the impact of the industry on the environment and to meet the increasing demand for environmentally responsible products. Here are some ways that the paper manufacturing process can be made more sustainable:
- Use sustainable raw materials: The use of sustainable raw materials, such as FSC (Forest Stewardship Council) certified wood or recycled paper, can help to reduce the environmental impact of paper manufacturing.
- Reduce waste: The paper manufacturing process can generate significant amounts of waste, including pulp and paper sludge. By implementing recycling and waste reduction programs, this waste can be reused or disposed of responsibly.
- Improve energy efficiency: The paper manufacturing process is energy-intensive, and improving energy efficiency can reduce greenhouse gas emissions and save costs. Energy-efficient technologies, such as heat recovery systems and energy-efficient lighting, can be used to reduce energy consumption.
- Use renewable energy: Renewable energy sources, such as wind and solar power, can be used to power the paper manufacturing process, reducing reliance on non-renewable sources of energy.
- Reduce water usage: The paper manufacturing process requires a significant amount of water, and reducing water usage can help to conserve this valuable resource. Water conservation strategies, such as the use of closed-loop systems and water reuse, can be implemented to reduce water usage.
- Minimize emissions: The paper manufacturing process can generate emissions, including air and water pollution. To minimize these emissions, technologies such as air pollution control devices and wastewater treatment systems can be implemented.
- Support sustainable forestry practices: Supporting sustainable forestry practices, such as reforestation and conservation, can help to ensure the long-term availability of raw materials for paper manufacturing.
Overall, by implementing sustainable practices, the paper manufacturing process can be made more environmentally responsible and economically viable in the long term.
New Trends in the Paper Manufacturing Process
The paper manufacturing industry is continually evolving, and new trends are emerging that are transforming the way paper is produced. Here are some of the latest trends in the paper manufacturing process:
- Digitalization: Digitalization is rapidly transforming the paper manufacturing process, with new technologies such as the Internet of Things (IoT) and Artificial Intelligence (AI) being used to optimize production, quality, and efficiency.
- Circular Economy: The concept of the circular economy is gaining traction in the paper manufacturing industry, with companies seeking to minimize waste and maximize resource efficiency by reusing and recycling materials.
- Bio-based materials: Bio-based materials, such as cellulose nanofibers and lignin, are being explored as potential alternatives to traditional materials, such as petroleum-based plastics.
- Energy Efficiency: The focus on energy efficiency continues to be a key trend in the paper manufacturing process, with companies investing in new technologies to reduce energy consumption and greenhouse gas emissions.
- Smart packaging: Smart packaging, which incorporates sensors and other technologies to provide information about the contents of the package, is becoming increasingly popular in the paper manufacturing industry, as it enhances product safety and traceability.
- Sustainable Forestry: Sustainable forestry practices, such as reforestation and conservation, are becoming increasingly important in the paper manufacturing process as companies seek to ensure a reliable supply of raw materials and minimize the environmental impact of their operations.
- Digital Printing: Digital printing is becoming more prevalent in the paper manufacturing industry, as it enables faster turnaround times, reduced waste, and greater flexibility in product design.
Overall, these trends are transforming the paper manufacturing process, making it more efficient, sustainable, and innovative.
How AI Enhances Manufacturing Processes
AI is revolutionizing manufacturing by making operations smarter, faster, and more efficient. It enables real-time monitoring of equipment and production lines, allowing manufacturers to detect issues early and prevent costly breakdowns through predictive maintenance.
AI also helps optimize workflows by analyzing production data to identify bottlenecks and recommend process improvements. When integrated into ERP platforms, AI brings together all operational data in one place, enabling informed decision-making, improved productivity, and streamlined communication across departments—driving continuous growth.
FAQs related to the Paper Manufacturing Process
- What is the paper manufacturing process?
The paper manufacturing process involves several steps, including preparing the raw materials, pulping the wood or recycled paper, refining the pulp, and forming the paper sheets.
- What types of raw materials are used in the paper manufacturing process?
The raw materials used in the paper manufacturing process can include wood pulp, recycled paper, and agricultural residues, among others.
- What is pulping, and why is it necessary?
Pulping is the process of breaking down wood fibers or recycled paper into pulp. It is necessary to make the fibers suitable for papermaking.
- How is the pulp refined?
The pulp is refined using mechanical or chemical methods, which break down the fibers further, making them more suitable for papermaking.
- How are the paper sheets formed?
The paper sheets are formed by pressing the pulp onto a wire mesh, where the water drains away, leaving behind the paper fibers.
- What is the purpose of drying the paper sheets?
Drying the paper sheets removes the remaining water and creates a stronger, more durable paper product.
- How is the paper product finished?
The paper product may be finished by coating, calendaring, or embossing, depending on the desired properties.
- What is the environmental impact of the paper manufacturing process?
The paper manufacturing process can have a significant environmental impact, including deforestation, greenhouse gas emissions, and water pollution. However, sustainable practices can help to mitigate these impacts.
- How can paper manufacturers reduce their environmental impact?
Paper manufacturers can reduce their environmental impact by using sustainable raw materials, minimizing waste and emissions, and improving energy efficiency.
- What is FSC certification, and why is it important?
FSC certification is a certification system for sustainable forestry practices. It is important because it ensures that the wood used in paper manufacturing comes from responsibly managed forests.
- What is the role of automation in the paper manufacturing process?
Automation plays a critical role in the paper manufacturing process, helping to increase efficiency, reduce costs, improve quality, and enhance safety.
- How has digitalization affected the paper manufacturing process?
Digitalization has transformed the paper manufacturing process, with new technologies such as the Internet of Things (IoT) and Artificial Intelligence (AI) being used to optimize production, quality, and efficiency.
- What is the circular economy, and how does it relate to the paper manufacturing process?
The circular economy is a concept that emphasizes the reuse and recycling of materials. It is relevant to the paper manufacturing process because it encourages companies to minimize waste and maximize resource efficiency.
- What is smart packaging, and why is it becoming popular in the paper manufacturing industry?
Smart packaging incorporates sensors and other technologies to provide information about the contents of the package. It is becoming popular in the paper manufacturing industry because it enhances product safety and traceability.
How can Deskera Help You with the Paper Manufacturing Process?
Deskera is a material requirements planning (MRP) software that can help with the paper manufacturing process by streamlining and automating various aspects of the production process, including inventory management, production planning, scheduling, and order management. Here are some specific ways Deskera can help:
- Material Management: Deskera can help manage raw material inventory levels and ensure the timely procurement of required materials.
- Production Planning: Deskera can help with production planning by creating production schedules, managing production workflows, and ensuring efficient production processes.
- Quality Control: Deskera can assist with quality control by enabling real-time monitoring of production processes and quality parameters.
- Maintenance Management: Deskera can help manage maintenance schedules, equipment downtime, and work orders, ensuring minimal disruption to the production process.
- Cost Management: Deskera can help with cost management by tracking production costs, comparing actual costs against budgets, and identifying areas of cost-saving.
- Sales Management: Deskera can help with sales management by tracking sales orders, invoicing, and delivery schedules and ensuring efficient order fulfillment.
- Financial Management: Deskera can help with financial management by tracking expenses, revenue, and profitability, providing insights into financial performance, and facilitating timely decision-making.
Key Takeaways
The paper manufacturing process involves several stages, including the preparation of raw materials, pulping, refining, forming, pressing, drying, and finishing. The following is a general overview of the process:
- Preparation of raw materials: Wood chips, recycled paper, or other raw materials are collected, sorted, and processed to remove any impurities, such as metals or plastics. The raw materials are then washed and debarked.
- Pulping: The raw materials are chopped into small pieces and mixed with water and chemicals to form a pulp. The pulp is then heated and stirred to break down the fibers and remove any remaining impurities.
- Refining: The pulp is further refined to improve the quality of the fibers and make them more suitable for papermaking. Refining involves passing the pulp through a series of screens and filters.
- Forming: The pulp is poured onto a wire mesh screen, and water is drained away. The remaining fibers form a wet mat, which is then pressed to remove more water.
- Pressing: The wet mat is pressed between rollers to remove even more water and compact the fibers.
- Drying: The paper is dried by passing it through a series of heated rollers or by hanging it on a drying rack.
- Finishing: The paper is cut into the desired size and shape and may be coated or treated with chemicals to improve its properties, such as brightness, smoothness, or resistance to water.
Overall, the paper manufacturing process is complex and requires careful attention to detail at each stage to produce high-quality paper products.
To ensure sustainability and efficiency in the paper manufacturing process, companies need to adopt new technologies and best practices, such as automation, digitalization, circular economy, bio-based materials, energy efficiency, smart packaging, sustainable forestry, and digital printing. These trends are transforming the paper manufacturing process, making it more efficient, sustainable, and innovative.
To ensure quality control in the paper manufacturing process, companies need to monitor the manufacturing process, perform quality testing, calibrate and maintain equipment, and conduct regular quality audits. By implementing these measures, companies can produce high-quality paper products that meet customer expectations and minimize their environmental impact.
The paper manufacturing process is evolving rapidly, driven by new technologies and a growing awareness of the need for sustainability and efficiency. Companies that adopt these new trends and best practices can improve productivity, reduce costs, and ensure efficient and sustainable operations while producing high-quality paper products that meet customer needs.
Overall, Deskera can help paper manufacturers improve productivity, reduce costs, and ensure efficient operations by providing a unified view of the entire production process.
Related Articles
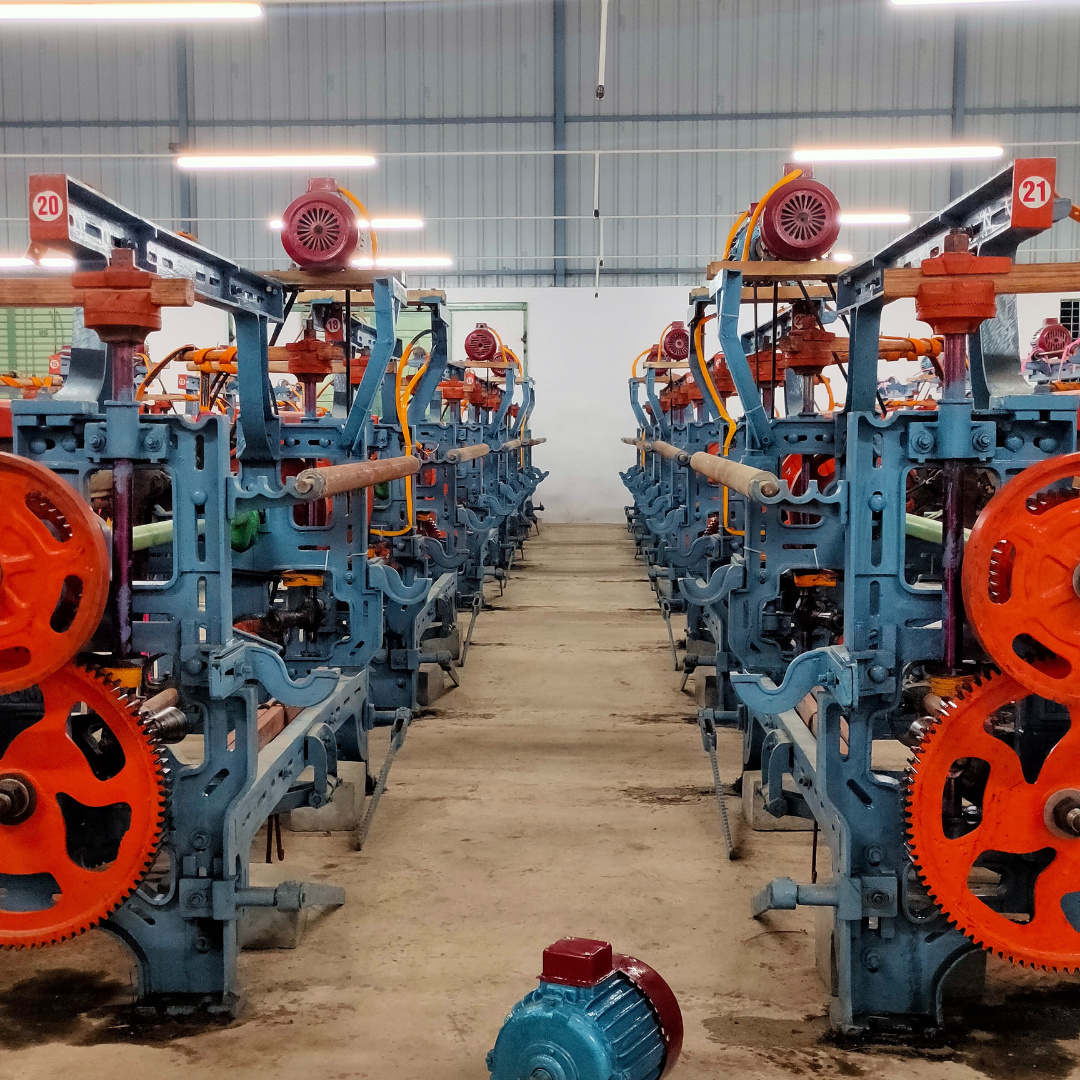
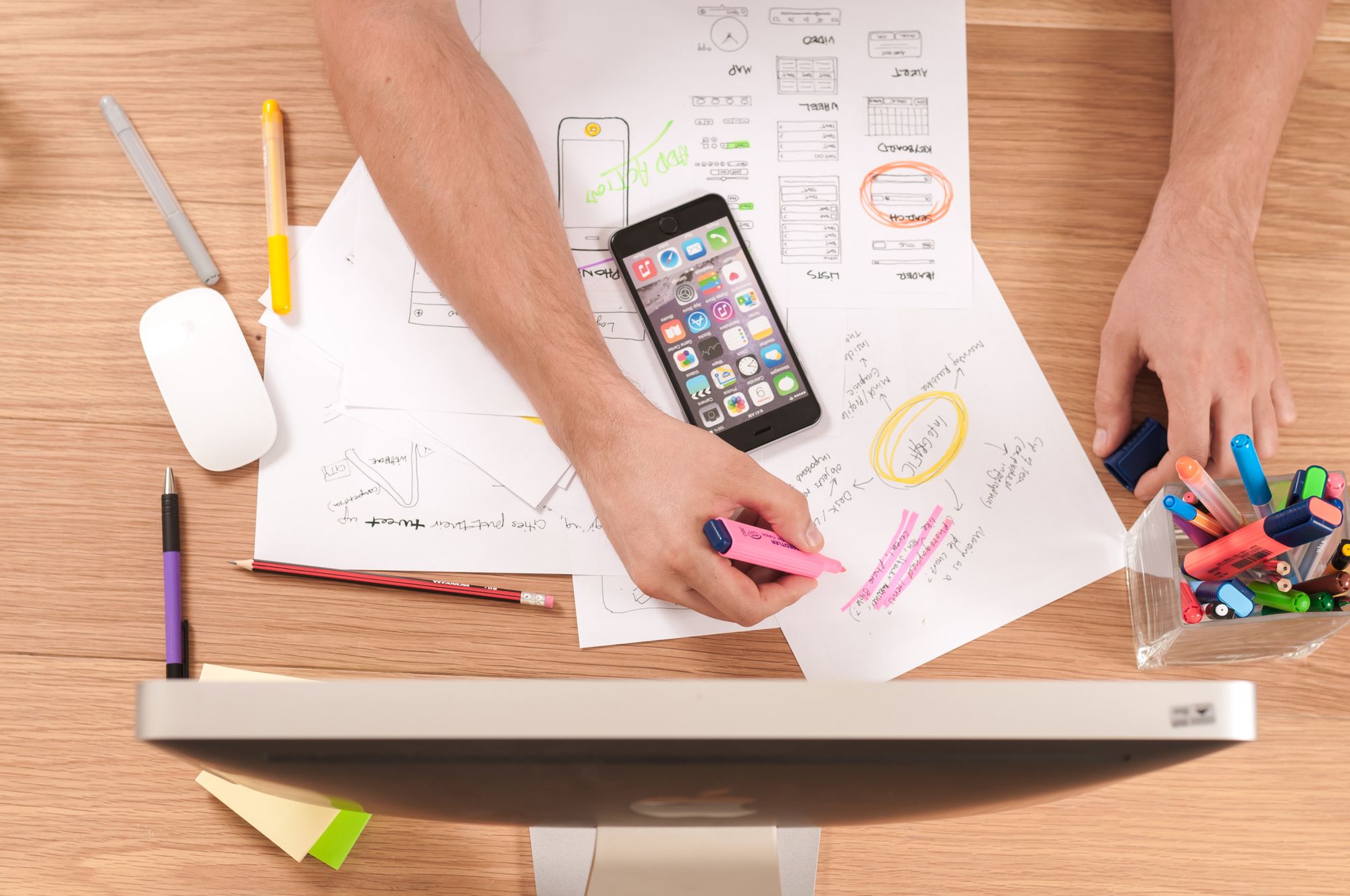
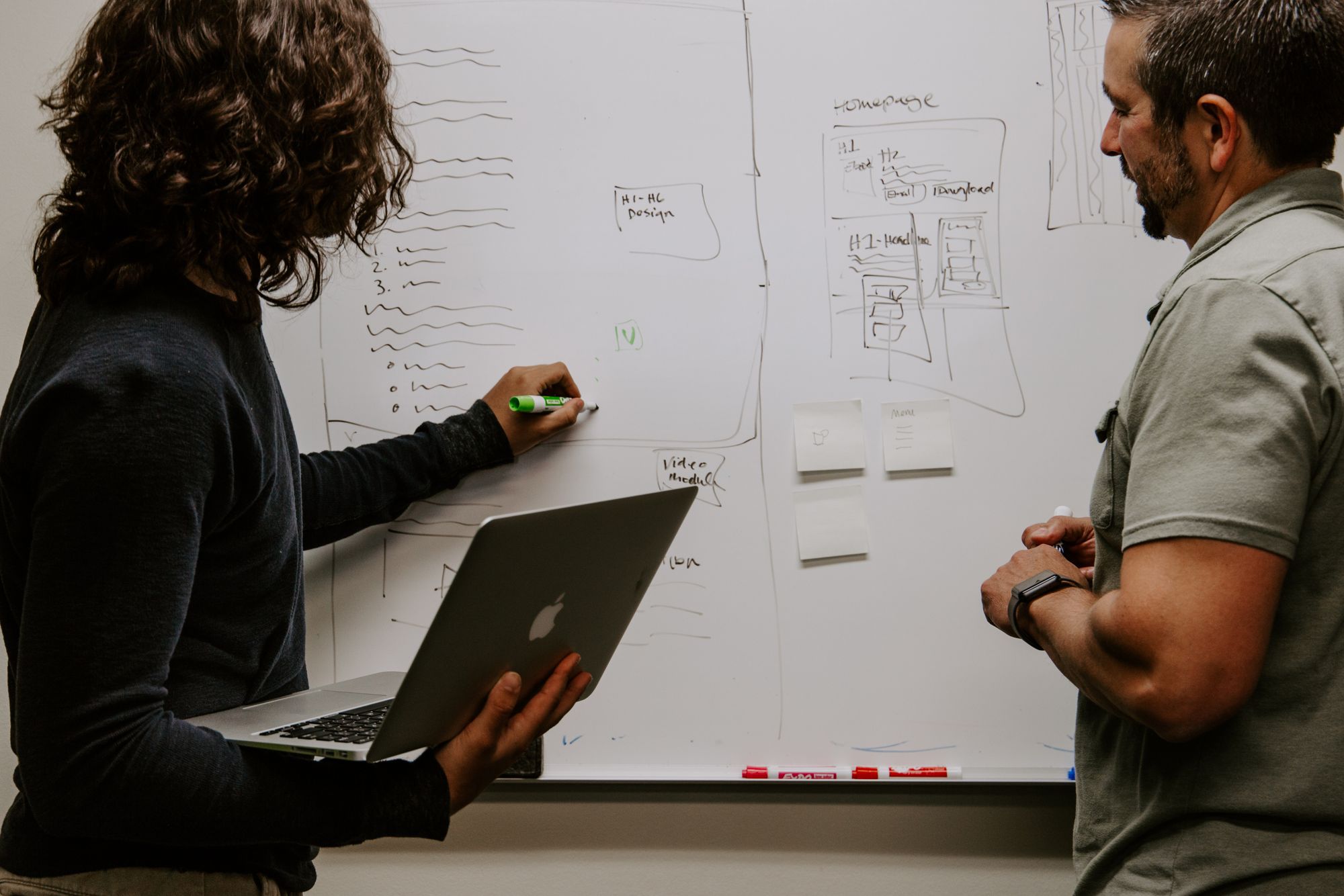
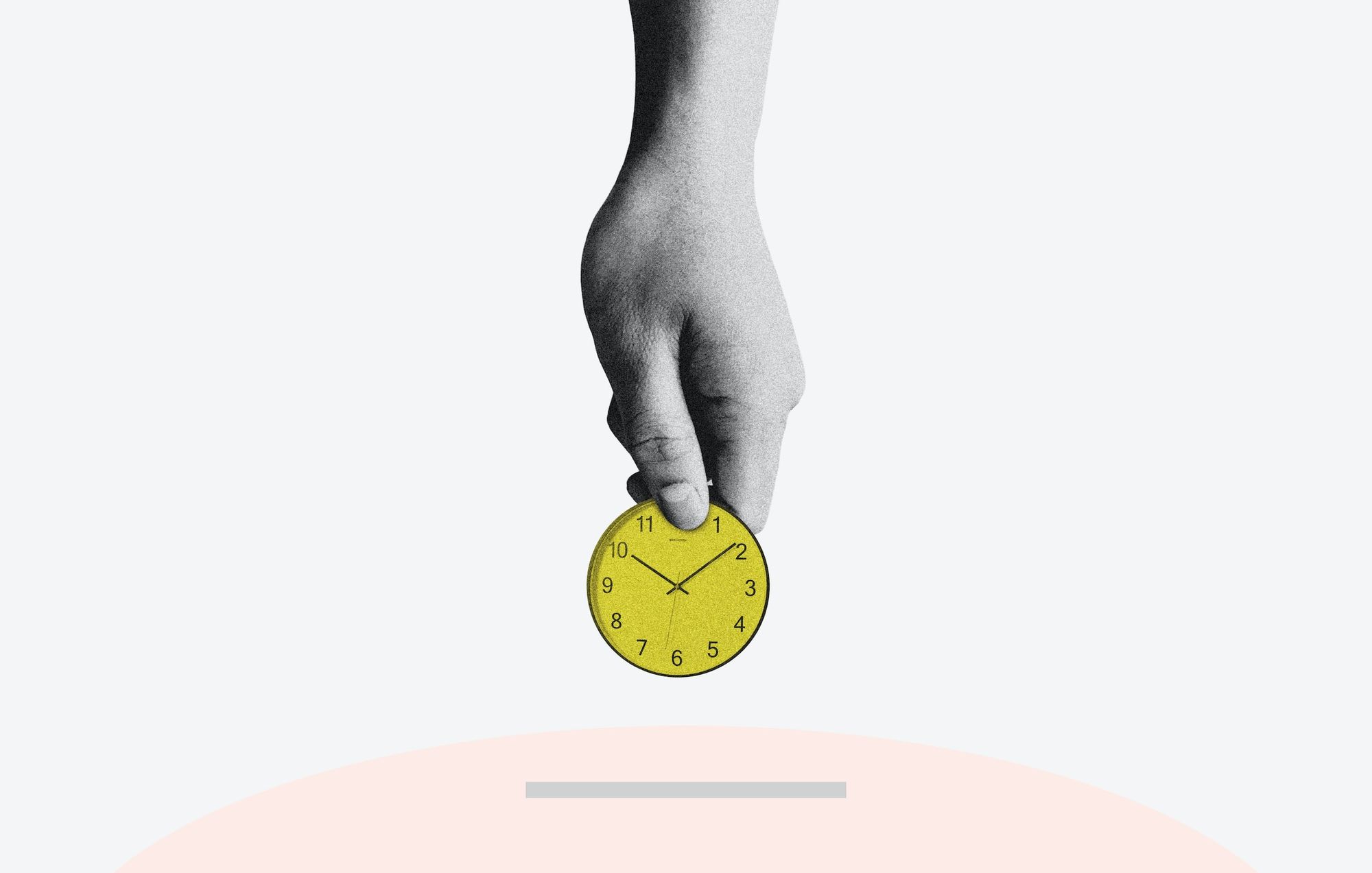
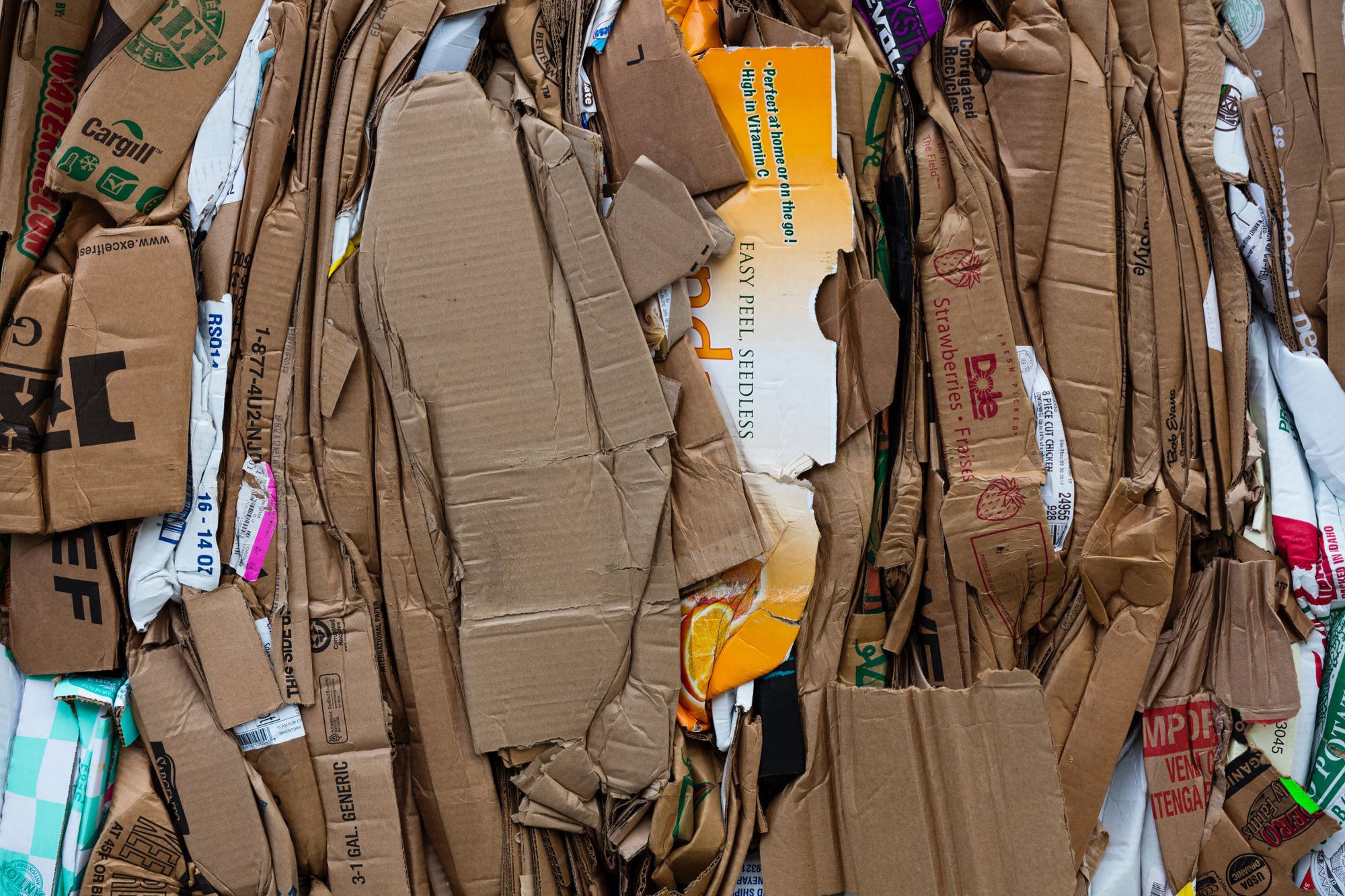
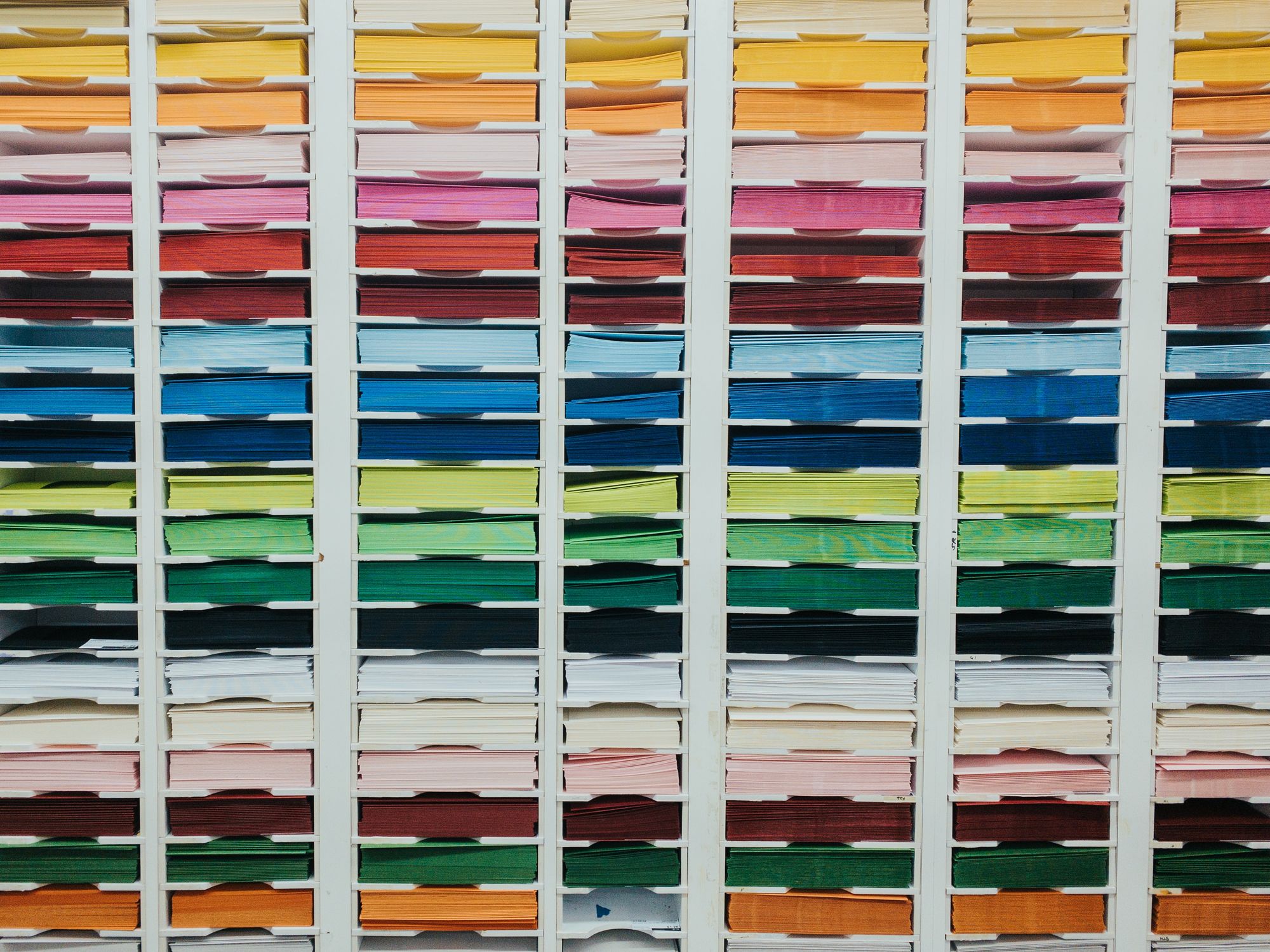