In today's fast-paced and complex business landscape, successful product development and manufacturing rely heavily on accurate and efficient information management.
One pivotal aspect of this process is the Multi-Level Bill of Materials (BOM) – a structured framework that lies at the heart of product design, production planning, procurement, and collaboration across departments.
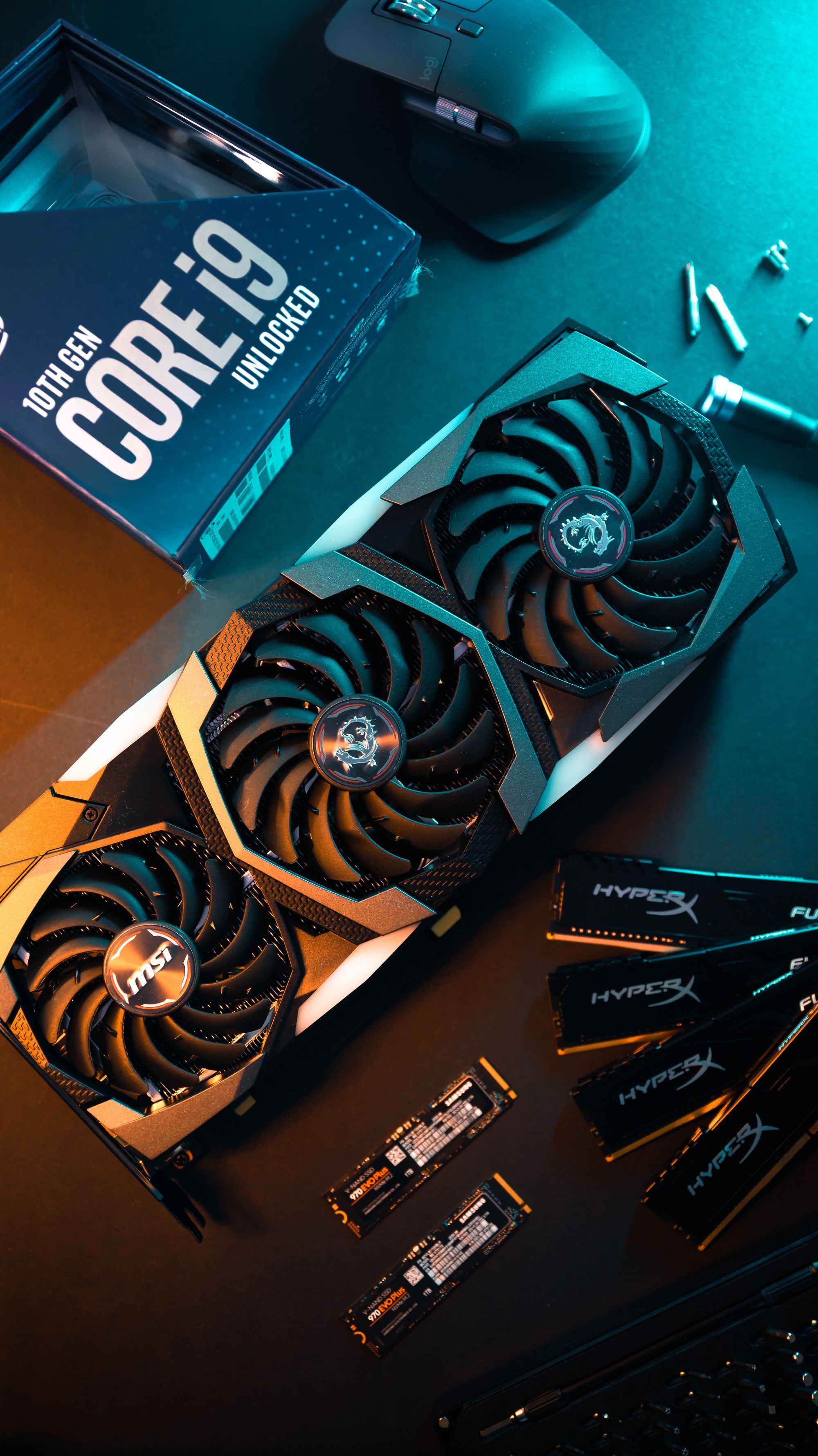
In this comprehensive guide, we will delve into the world of Multi-Level BOMs, exploring their significance, benefits, challenges, and strategies for effective implementation.
Whether you are a seasoned executive seeking to optimize your organization's operations or a decision-maker looking to enhance cross-functional collaboration, this guide will provide you with valuable insights to navigate the intricacies of Multi-Level BOMs and leverage them to drive success.
The topics covered in this article are:
- What are Bill of Materials?
- What is a Multi-Level Bill of Materials?
- Structure of Multi-Level Bill of Materials
- Types of Multi-Level Bill of Materials
- Uses of Multi-Level Bill of Materials
- Importance of Multi-Level Bill of Materials
- Key Benefits of Multi-Level Bill of Materials
- Challenges Associated with Multi-Level Bill of Materials
- Strategic Implications of Utilizing Multi-Level BOMs in Various Aspects of a Business
- Best Options to Manage Multi-Level Bill of Materials
- How Can Deskera Help You with a Multi-Level Bill of Materials?
- Key Takeaways
- Related Articles
What are Bill of Materials?
A Bill of Materials (BOM) is a comprehensive list of all the components, parts, raw materials, sub-assemblies, and other items required to manufacture or assemble a product. It is an essential document used in manufacturing, engineering, and project management to outline the structure and composition of a product.
BOMs are commonly used in various industries, including manufacturing, construction, electronics, automotive, aerospace, and more.
A typical BOM includes the following information:
- Part Number or Identifier: A unique code or label for each item in the BOM.
- Description: A brief description of the item, including its specifications and characteristics.
- Quantity: The quantity of each item required for the product's assembly or manufacturing.
- Unit of Measure: The unit in which the quantity is measured (e.g., pieces, kilograms, meters, etc.).
- Reference Designators: Identification of where each component is used within the product's assembly, often associated with specific locations on engineering drawings or diagrams.
- Manufacturer and Supplier Information: Details about the manufacturer or supplier of each component, including their part numbers and contact information.
- Material and Material Specifications: Information about the material composition and specifications for each component.
- Sub-Assemblies: If the product is composed of smaller sub-assemblies, the BOM may include these sub-assemblies and their respective components.
- Revision Control: Version or revision information to track changes and updates to the BOM.
BOMs play a critical role in ensuring accurate and efficient manufacturing processes, inventory management, cost estimation, and supply chain management. They help in maintaining consistency and transparency across different departments and stakeholders involved in the product life cycle.
What is a Multi-Level Bill of Materials?
A Multi-Level Bill of Materials (BOM) is an extension of the standard BOM concept that includes multiple levels of sub-assemblies and components, illustrating the hierarchical structure of a complex product. In other words, a multi-level BOM breaks down a product's assembly into various levels of components, sub-assemblies, and raw materials, showing how they are interconnected and assembled to create the final product.
Each level of the multi-level BOM represents a different level of detail, from the top-level assembly down to the smallest individual components. This hierarchical representation is useful for understanding the complete composition of a product and how its various parts come together.
It is commonly used in industries where products are made up of intricate assemblies and sub-assemblies, such as electronics, aerospace, automotive, and machinery manufacturing.
For example, consider the manufacturing of a computer:
Level 0: Computer System
- Level 1: Main Chassis
- Level 2: Motherboard
- Level 3: Central Processing Unit (CPU)
- Level 3: Memory Modules
- Level 3: Graphics Card
- Level 2: Power Supply Unit (PSU)
- Level 2: Hard Drive
- Level 1: Display Assembly
- Level 2: Screen
- Level 2: Frame
- Level 1: Keyboard and Mouse
- Level 2: Keyboard
- Level 2: Mouse
In this example, the "Computer System" is the top-level assembly, and each subsequent level breaks down the product into more detailed components and sub-assemblies. The multi-level BOM allows for better planning, procurement, production scheduling, and understanding of the product's structure.
The use of multi-level BOMs becomes particularly important when managing inventory, tracking costs, and ensuring efficient production processes. It helps manufacturers maintain a clear overview of all the components required at each level and enables them to manage the complexities of assembling and producing intricate products.
Structure of Multi-Level Bill of Materials
The structure of a Multi-Level Bill of Materials (BOM) is a hierarchical representation of the components and subcomponents required to manufacture or assemble a product. It provides a detailed breakdown of the materials, parts, and quantities needed at each level of the product's assembly.
The structure of a multi-level BOM typically consists of several levels, with each level representing a different level of assembly.
Here's a breakdown of the typical structure of a multi-level BOM:
1. Top-Level Assembly:
- At the highest level, you have the finished product or top-level assembly. This represents the end product that will be delivered to customers.
2. Subassemblies:
- Below the top-level assembly, you have subassemblies. These are intermediate assemblies that are made up of a group of components. Subassemblies can represent larger components or modules that are combined to create the final product.
3. Components and Parts:
- The next level includes individual components and parts that make up the subassemblies. These can be raw materials, purchased components, or internally manufactured parts.
4. Further Levels:
- The structure can continue to break down further into additional levels, representing increasingly detailed subcomponents and parts. This hierarchical structure can extend to several levels deep, depending on the complexity of the product.
Key Components of Each BOM Level:
- Part Number: A unique identifier for each component or part.
- Description: A brief description of the component or part.
- Quantity: The quantity of each component required for the assembly at that level.
- Unit of Measure: The unit in which the quantity is measured (e.g., each, kilogram, meters).
- Reference Designators: A label that identifies where each component is used in the assembly.
- Optional/Alternate Components: Different options or alternates for a particular component may be used based on availability or other factors.
- Notes: Additional information about the component, special instructions, or other relevant details.
- Routing Information: Information about the sequence of operations required to assemble the product, including work centers, tools, and processes.
The hierarchical structure of a multi-level BOM helps organizations manage the complexity of product design and assembly, plan production, estimate costs, manage inventory, and ensure accurate procurement of components. It forms the foundation for effective communication and collaboration across different departments involved in the product life cycle.
Types of Multi-Level Bill of Materials
Multi-level Bills of Materials (BOM) can be categorized into different types based on their specific use cases and the nature of the products they represent. Here are some common types of multi-level BOMs:
- Indented BOM: This is the most common type of multi-level BOM, where components and sub-assemblies are displayed in an indented format, showing the hierarchical relationship between levels. Each level is indented further to the right to visually represent the assembly structure.
- Single-Level BOM: A single-level BOM focuses on a specific assembly level and lists only the components and materials required for that level. It is useful for understanding the immediate components needed for a particular assembly.
- Phantom BOM: A phantom BOM includes sub-assemblies that are used for assembly purposes but are not part of the final product. Phantom BOMs help in managing complex assembly processes by simplifying the representation of the final product.
- Manufacturing BOM (MBOM): This type of BOM includes detailed information about manufacturing processes, work instructions, routing, and resources required for each assembly and sub-assembly. It's essential for production planning and execution.
- Engineering BOM (EBOM): An EBOM is used during the design and development phase, listing all components and sub-assemblies as they were initially designed. It serves as a basis for subsequent BOM types used in manufacturing and other processes.
- Service BOM (SBOM): SBOM focuses on the components and sub-assemblies required for servicing and maintaining products after they are sold. It helps technicians identify the right parts for repairs and replacements.
- Sales BOM (SBOM): A sales BOM is created for sales and marketing purposes, emphasizing the features and benefits of the final product rather than detailing its components. It is useful for communicating with customers and potential buyers.
- Configurable BOM: This type of BOM allows for variations and customization of the product. Different configurations are specified within the same BOM, making it useful for products with multiple options or variants.
- Planning BOM: A planning BOM is used for forecasting, capacity planning, and material requirements planning. It helps in estimating the quantities of components needed for a certain production volume.
- Costed BOM: A costed BOM includes the cost information associated with each component and sub-assembly. It is used for accurate cost estimation, pricing, and budgeting.
- Revised BOM: A revised BOM is created when changes are made to an existing BOM due to design modifications, updates, or improvements. It reflects the latest version of the product structure.
- Parent-Child BOM: This type of BOM explicitly shows the parent and child relationships between components and sub-assemblies. It's useful for understanding how different levels are interconnected.
These are just a few examples of the types of multi-level BOMs that exist. The choice of BOM type depends on the specific requirements of the industry, product, and business processes involved. In practice, a combination of these types might be used to effectively manage various aspects of product development, manufacturing, and other activities.
Uses of Multi-Level Bill of Materials
A Multi-Level Bill of Materials (BOM) serves a variety of important purposes across different stages of product development, manufacturing, and maintenance.
Here are some key uses of a multi-level BOM:
Product Design and Development:
- Structural Understanding: Engineers and designers use multi-level BOMs to visualize and understand how different components and sub-assemblies come together to form the final product.
- Design Iteration: BOMs help in evaluating design alternatives by analyzing the impact of different components and materials on the overall product structure and cost.
Manufacturing and Production:
- Production Planning: Manufacturers use BOMs to plan the sequence of assembly operations and ensure that all necessary components are available at the right time.
- Inventory Management: Multi-level BOMs assist in managing inventory levels by providing insights into which components need to be stocked and in what quantities.
- Work Orders and Routing: BOMs guide production workers through the assembly process by detailing the steps required to build each sub-assembly and the final product.
- Quality Control: BOMs help ensure that all required components are present and correctly assembled, contributing to product quality and consistency.
Cost Estimation and Pricing:
- Accurate Costing: Multi-level BOMs enable accurate cost estimation by accounting for the cost of each individual component, labor, and associated overhead.
- Pricing: Manufacturers can set competitive pricing for their products based on a thorough understanding of the costs involved in production.
Supply Chain Management:
- Supplier Collaboration: BOMs facilitate communication with suppliers, enabling them to understand the components needed and deliver them at the right time.
- Procurement: Multi-level BOMs guide the procurement process, ensuring that the correct components are sourced to meet production requirements.
Service and Maintenance:
- Repair and Replacement: Service technicians refer to multi-level BOMs to identify the specific components that need to be repaired or replaced when servicing products.
- Spare Parts Inventory: BOMs assist in maintaining an accurate inventory of spare parts needed for ongoing maintenance and repairs.
Documentation and Compliance:
- Regulatory Compliance: BOMs provide a comprehensive record of product components, aiding in compliance with regulatory standards and certifications.
- Auditing: BOMs serve as documentation for internal and external audits, ensuring transparency and traceability in the manufacturing process.
Collaboration and Communication:
- Cross-Departmental Communication: BOMs facilitate effective communication between engineering, manufacturing, procurement, and other departments involved in the product life cycle.
- Supplier Communication: BOMs help manufacturers communicate component specifications and requirements to suppliers accurately.
Version Control and Change Management:
- Design Changes: Multi-level BOMs assist in managing design changes by highlighting how modifications affect different levels of the product structure.
- Version Tracking: BOMs enable tracking of different product versions and revisions, ensuring that the correct components are used in each version.
Future Planning and Forecasting:
- Capacity Planning: BOMs aid in capacity planning by estimating the demand for different components and sub-assemblies based on production schedules.
- New Product Development: Multi-level BOMs can serve as a foundation for developing new product variants or similar products with slight modifications.
In summary, a multi-level BOM is a versatile and crucial tool that supports various aspects of product development, manufacturing, quality control, and maintenance throughout the entire product lifecycle.
Importance of Multi-Level Bill of Materials
The Multi-Level Bill of Materials (BOM) holds significant importance across various stages of product development, manufacturing, and business operations. Its role extends to several key areas that contribute to overall operational efficiency, cost-effectiveness, and successful product outcomes.
Here's why the multi-level BOM is important:
- Clear Product Structure Understanding: Multi-level BOMs provide a visual representation of how components and sub-assemblies come together to form a product. This understanding is crucial for design, production planning, and effective communication among teams.
- Accurate Cost Estimation and Budgeting: Multi-level BOMs allow for precise cost estimation by accounting for all components, materials, labor, and associated expenses. This supports accurate budgeting and helps in setting competitive prices.
- Efficient Production Planning and Scheduling: By detailing the sequence of assembly operations, multi-level BOMs enable optimized production planning and scheduling. This minimizes production delays, reduces lead times, and enhances resource utilization.
- Inventory Management and Supply Chain Optimization: Multi-level BOMs aid in managing inventory levels, preventing shortages, and minimizing excess stock. They provide insights into component demand, supporting efficient supply chain operations.
- Quality Control and Product Consistency: Multi-level BOMs ensure that the correct components are used in the assembly, enhancing product quality and consistency. This reduces errors, rework, and potential defects.
- Effective Supplier Collaboration: Multi-level BOMs facilitate clear communication with suppliers by detailing component specifications and requirements. This enhances collaboration, minimizes misunderstandings, and promotes smoother procurement processes.
- Facilitation of New Product Development: Multi-level BOMs serve as a foundation for designing and developing new products or variants. They ensure that all necessary components are considered from the outset.
- Cross-Functional Collaboration: Multi-level BOMs encourage collaboration between different departments, such as design, engineering, manufacturing, procurement, and sales. This alignment leads to better decision-making and streamlined processes.
- Service and Maintenance Efficiency: For ongoing maintenance and repairs, multi-level BOMs help technicians identify and replace the correct components, minimizing downtime and improving customer satisfaction.
- Documentation and Regulatory Compliance: Multi-level BOMs serve as a comprehensive record of product composition, aiding in regulatory compliance, certifications, and audits.
- Change Management and Design Iteration: Multi-level BOMs support effective change management by highlighting how modifications impact different levels of assembly. They enable efficient design iterations and updates.
- Strategic Decision-Making: Executives can make well-informed strategic decisions based on insights derived from multi-level BOMs, contributing to optimized product designs, cost savings, and business growth.
In summary, the multi-level BOM is a critical tool that enhances operational efficiency, cost control, collaboration, and overall product quality. Its importance spans from design to manufacturing to service, ensuring that products are developed, produced, and maintained effectively in alignment with business goals and customer expectations.
Key Benefits of Multi-Level Bill of Materials
A Multi-Level Bill of Materials (BOM) offers several key benefits that contribute to efficient product development, manufacturing processes, and overall business success. Here are the key benefits:
Comprehensive Product Understanding
Comprehensive product understanding is a fundamental benefit derived from utilizing Multi-Level Bills of Materials (BOMs).
It involves gaining a clear, detailed, and visual insight into how a product is structured and assembled, from its highest-level assemblies down to individual components and raw materials.
This understanding is crucial for multiple aspects of product development, manufacturing, and business operations.
Let's delve deeper into this concept:
1. Visual Representation of Product Hierarchy:
- Multi-level BOMs provide a hierarchical representation of the product's structure, showing the relationships between different components and assemblies. This visual depiction enables stakeholders to grasp the complexity of the product and how its various parts interconnect.
2. Design and Engineering:
- Design Validation: Engineers and designers can assess how different components fit together and identify potential design clashes or interferences.
- Functionality Assessment: Understanding how components interact helps evaluate whether the product will function as intended.
3. Manufacturing and Production:
- Assembly Sequence: Manufacturers can visualize the order in which components are assembled, streamlining production planning and reducing errors.
- Resource Allocation: Clear understanding of the product structure helps allocate resources and equipment effectively.
4. Supply Chain Management:
- Sourcing Decisions: Procurement teams can make informed decisions about component sourcing based on their role within the product structure.
- Supplier Collaboration: Multi-level BOMs aid in communicating component specifications and requirements to suppliers.
5. Cost Estimation and Budgeting:
- Accurate Costing: Understanding the entire product structure enables accurate assessment of costs associated with each component and sub-assembly.
- Cost Reduction: Identifying costly components can lead to targeted cost-saving initiatives.
6. Quality Control and Compliance:
- Component Verification: QA teams can ensure that the correct components are used in assembly, enhancing product quality and reducing defects.
- Regulatory Compliance: Accurate documentation of components supports adherence to regulatory standards.
7. Sales and Marketing:
- Product Knowledge: Sales teams can communicate the product's features and benefits more effectively to potential customers.
- Customization: Understanding the product's structure helps offer tailored solutions to customers.
8. Service and Maintenance:
- Efficient Servicing: Technicians can quickly identify and replace the correct components during repairs or maintenance.
- Downtime Reduction: Comprehensive product understanding minimizes downtime and improves turnaround time for servicing.
9. Decision-Making:
- Strategic Decisions: Executives can make informed decisions about product development, pricing, and market positioning based on a deep understanding of the product's composition.
In essence, comprehensive product understanding through multi-level BOMs provides a holistic view that empowers various teams within an organization to work cohesively, make informed decisions, and ensure the successful development, manufacturing, and servicing of products.
It enables effective communication, reduces errors, and contributes to improved product quality and customer satisfaction.
Efficient Production Planning
Efficient production planning is a critical outcome of utilizing Multi-Level Bills of Materials (BOMs) and plays a pivotal role in optimizing manufacturing processes.
It involves using the detailed hierarchical structure provided by the multi-level BOM to strategically plan and manage various aspects of production.
Here's a more detailed elaboration on how multi-level BOMs contribute to efficient production planning:
1. Sequence of Assembly Operations: Multi-level BOMs outline the exact sequence in which components and sub-assemblies are assembled to create the final product. This sequence guides production teams in performing tasks in the correct order, minimizing backtracking, and reducing production bottlenecks.
2. Workforce and Resource Allocation: Multi-level BOMs provide insights into the labor and resources required at each assembly stage. This allows production managers to allocate human resources, machinery, tools, and equipment efficiently based on the production sequence.
3. Lead Time Calculation: By understanding the dependencies between components and sub-assemblies, production planners can calculate accurate lead times for each production stage. This helps set realistic expectations for delivery and ensures on-time production.
4. Material Planning and Procurement: Multi-level BOMs serve as a foundation for determining the quantity and timing of materials needed for production. This aids in effective procurement, preventing material shortages and overstocking.
5. Capacity Planning: Multi-level BOMs provide insights into the production workload at different stages. This information supports capacity planning, allowing manufacturers to adjust production schedules to meet demand while optimizing resource utilization.
6. Just-In-Time (JIT) Manufacturing: Multi-level BOMs enable JIT manufacturing principles by indicating precisely when each component is needed in the production process. This minimizes excess inventory, reduces carrying costs, and improves cash flow.
7. Subcontracting and Outsourcing: For complex products involving multiple suppliers or subcontractors, multi-level BOMs help coordinate the production process by specifying which components need to be manufactured in-house and which can be outsourced.
8. Production Scheduling: Multi-level BOMs contribute to accurate production scheduling by providing a clear roadmap for the timing of each assembly stage. This prevents production delays and helps in meeting delivery commitments.
9. Error Reduction and Quality Control: Efficient production planning using multi-level BOMs reduces the likelihood of errors, such as using incorrect components or assembling in the wrong order. This, in turn, enhances product quality and reduces rework.
10. Continuous Improvement Initiatives: Multi-level BOMs highlight areas for process optimization and continuous improvement by identifying production stages that can be streamlined, automated, or made more efficient.
11. Flexibility and Adaptability: In cases of unexpected changes, such as rush orders or design modifications, multi-level BOMs enable production planners to quickly assess the impact on the entire production process and make necessary adjustments.
By leveraging the insights provided by multi-level BOMs, manufacturers can create well-organized and optimized production plans that result in reduced lead times, improved resource utilization, minimized waste, and enhance overall operational efficiency.
Accurate Cost Estimation and Pricing
Accurate cost estimation and pricing are crucial aspects of business success, and Multi-Level Bills of Materials (BOMs) play a significant role in achieving these objectives.
BOMs provide a detailed breakdown of the components, sub-assemblies, labor, and other associated costs required to manufacture a product.
Here's a more detailed elaboration on how multi-level BOMs contribute to accurate cost estimation and pricing:
1. Component-Level Cost Calculation: Multi-level BOMs allow for the accurate calculation of costs associated with each individual component and sub-assembly. By attributing costs to specific parts, manufacturers can understand the cost distribution within the product.
2. Labor and Overhead Allocation: BOMs provide visibility into the labor hours required for assembling each component and sub-assembly. This information, combined with overhead costs, ensures that all expenses are accounted for in the cost estimation process.
3. Cost of Goods Sold (COGS) Calculation: Multi-level BOMs contribute to calculating the COGS by aggregating the costs of all components, labor, and overhead associated with producing the final product. This is essential for accurate financial reporting and profitability analysis.
4. Pricing Strategy Formulation: Armed with accurate cost data from the BOMs, businesses can develop pricing strategies that consider factors such as profit margin, market competition, and perceived value to customers.
5. Targeted Cost Reduction: Multi-level BOMs highlight expensive components or processes, allowing manufacturers to target cost reduction efforts where they will have the most significant impact on overall production costs.
6. Variants and Customization Pricing: For products with multiple variants or customization options, multi-level BOMs enable precise cost calculation for each configuration, aiding in setting differentiated prices.
7. Bid and Proposal Preparation: Multi-level BOMs support the preparation of accurate bids and proposals by providing a detailed breakdown of costs, which enhances transparency and builds trust with potential customers.
8. Cost Transparency and Negotiation: Multi-level BOMs enable businesses to provide customers with transparent breakdowns of costs, fostering open discussions during negotiations and building strong customer relationships.
9. Budgeting and Financial Planning: Accurate cost estimation derived from multi-level BOMs helps in formulating realistic budgets and financial forecasts, ensuring proper resource allocation and financial management.
10. Profit Margin Optimization: Multi-level BOMs assist in calculating profit margins for different product lines or variants, aiding in optimizing pricing strategies to achieve desired profit levels.
11. Continuous Improvement Initiatives: By analyzing cost data from multi-level BOMs, manufacturers can identify cost-saving opportunities, waste reduction measures, and process improvements to drive operational efficiency.
12. Competitive Advantage: Accurate cost estimation and pricing through multi-level BOMs allow businesses to offer competitive prices while maintaining profitability, positioning them favorably in the market.
In summary, multi-level BOMs provide the foundation for precise cost estimation and informed pricing decisions. They enable businesses to maintain profitability, make strategic pricing choices, and respond effectively to market dynamics, ultimately contributing to sustainable financial success.
Effective Inventory Management
Effective inventory management is a critical aspect of business operations, and Multi-Level Bills of Materials (BOMs) play a significant role in achieving optimal inventory levels.
BOMs provide a structured breakdown of the components and sub-assemblies required for product assembly, aiding in efficient inventory planning and control.
Here's a more detailed elaboration on how multi-level BOMs contribute to effective inventory management:
1. Demand Forecasting and Planning: Multi-level BOMs serve as a foundation for accurate demand forecasting by detailing the quantity and timing of components needed for production. This information supports procurement and production planning activities.
2. Material Requirement Planning (MRP): BOMs facilitate MRP by outlining the materials required at each assembly stage. This enables manufacturers to calculate precise material needs, reorder points, and safety stock levels.
3. Just-In-Time (JIT) Inventory: Multi-level BOMs support JIT inventory principles by providing insights into when specific components are needed in the production process. This minimizes excess inventory and carrying costs.
4. Preventing Stockouts and Shortages: Accurate multi-level BOMs help prevent stockouts by ensuring that the right quantity of components is available when needed, minimizing production disruptions.
5. Minimizing Excess Inventory: BOMs aid in avoiding overstocking of components and sub-assemblies by providing visibility into actual production requirements. This reduces carrying costs and ties up less working capital.
6. Efficient Procurement: Multi-level BOMs guide procurement teams in sourcing the correct quantities of components at the right time, preventing unnecessary purchases, and optimizing procurement processes.
7. Supplier Collaboration: Accurate BOMs support effective communication with suppliers by specifying component requirements, lead times, and delivery schedules. This enhances collaboration and reduces supply chain disruptions.
8. Inventory Turnover Optimization: Multi-level BOMs assist in optimizing inventory turnover ratios by ensuring that components are utilized efficiently in the production process, reducing the time products spend in inventory.
9. Product Variants and Customization: For products with multiple variants, multi-level BOMs aid in calculating the inventory requirements for each configuration, preventing overstocking of specific components.
10. Minimized Waste and Obsolescence: Accurate inventory planning based on multi-level BOMs helps minimize waste and the risk of component obsolescence, as only the necessary quantities are procured.
11. Consistency in Inventory Replenishment: Multi-level BOMs establish a consistent framework for determining when and how much to reorder, streamlining the inventory replenishment process.
12. Cash Flow Management: Effective inventory management through multi-level BOMs contributes to improved cash flow by reducing excess inventory holding costs and tying up less capital in inventory.
In summary, multi-level BOMs provide valuable insights that enable businesses to optimize inventory levels, prevent stockouts, reduce excess stock, enhance supplier collaboration, and streamline procurement processes.
By aligning inventory with actual production requirements, organizations can achieve cost savings, improve operational efficiency, and enhance overall supply chain performance.
Quality Control and Consistency
Quality control and consistency are crucial aspects of delivering products that meet customer expectations and adhere to industry standards. Multi-Level Bill of Materials (BOMs) play a significant role in ensuring product quality and maintaining consistency throughout the manufacturing process.
Here's a more detailed elaboration on how multi-level BOMs contribute to quality control and consistency:
1. Accurate Component Identification: Multi-level BOMs provide a clear list of components and sub-assemblies required for each product. This ensures that the correct parts are used during assembly, reducing the risk of using incorrect or incompatible components.
2. Component Traceability: BOMs enable effective traceability of components back to their sources. In the event of defects or quality issues, manufacturers can quickly identify the source of the problem and take corrective actions.
3. Assembly Sequence Verification: Multi-level BOMs define the sequence of assembly operations, ensuring that components are assembled in the correct order. This verification minimizes assembly errors and reduces the likelihood of rework.
4. Process Standardization: BOMs contribute to standardizing assembly processes by outlining the specific steps and components required. This consistency reduces variations in product quality caused by human error or process deviations.
5. Design Intent Preservation: Multi-level BOMs help maintain the integrity of the product's design intent. By ensuring that the correct components are used, the final product is more likely to perform as intended during design.
6. Compliance with Specifications: BOMs include component specifications and requirements. This ensures that components meet the necessary standards and specifications, contributing to product compliance and safety.
7. Prevention of Counterfeit Components: Multi-level BOMs aid in preventing the use of counterfeit or unauthorized components by specifying approved sources and suppliers for each part.
8. Quality Audits and Inspections: Multi-level BOMs serve as a reference for quality audits and inspections. Inspectors can compare the actual product assembly against the BOM to verify compliance.
9. Continuous Improvement: By identifying components that are prone to defects or quality issues, multi-level BOMs enable targeted quality improvement initiatives to enhance product quality over time.
10. Rework Reduction: Accurate assembly guided by multi-level BOMs reduces the need for rework caused by incorrect component usage, ultimately saving time and resources.
11. Enhanced Customer Satisfaction: Ensuring product quality and consistency through multi-level BOMs results in higher customer satisfaction and confidence in the brand.
12. Regulatory Compliance: Multi-level BOMs provide documentation of compliant product assembly, which is crucial for meeting industry regulations and standards.
In summary, multi-level BOMs contribute to maintaining consistent product quality, reducing defects, improving process standardization, and ensuring compliance with industry regulations.
By guiding accurate assembly and preventing errors, multi-level BOMs play a pivotal role in delivering products that meet or exceed customer expectations and industry requirements.
Streamlined Supplier Collaboration
Streamlined supplier collaboration is essential for efficient procurement, on-time delivery, and successful product manufacturing. Multi-Level Bill of Materials (BOMs) play a crucial role in facilitating effective communication and collaboration between manufacturers and their suppliers.
Here's a more detailed elaboration on how multi-level BOMs contribute to streamlined supplier collaboration:
1. Clear Component Specifications: Multi-level BOMs provide detailed component specifications, enabling suppliers to understand the exact requirements for each part. This clarity reduces the risk of misunderstandings and ensures that suppliers deliver the right components.
2. Accurate Quantity Requirements: BOMs outline the quantity of each component needed for production. Suppliers can use this information to accurately plan their production and delivery schedules.
3. Lead Time Planning: Multi-level BOMs help suppliers understand when their components are needed in the production process. This allows suppliers to plan their production and delivery lead times accordingly.
4. Procurement Planning: Suppliers can use multi-level BOMs to align their procurement processes with manufacturers' production schedules, ensuring the timely availability of components.
5. Collaborative Sourcing: By sharing multi-level BOMs with suppliers, manufacturers and suppliers can collaborate on sourcing decisions, exploring options for cost savings, and identifying alternative suppliers.
6. Timely Issue Resolution: In the event of discrepancies or issues, multi-level BOMs serve as a reference for both parties to identify and resolve problems quickly, minimizing production disruptions.
7. Supplier Relationship Enhancement: Transparent communication through multi-level BOMs fosters stronger relationships between manufacturers and suppliers, based on mutual understanding and collaboration.
8. Customization and Variants: Suppliers can adapt their processes to accommodate product variants or customization requirements, as specified in the multi-level BOMs.
9. Demand Forecasting: Suppliers can use multi-level BOMs to forecast demand for their components and adjust their production accordingly, leading to optimized inventory levels and resource allocation.
10. Batch and Lot Tracking: Multi-level BOMs help suppliers track components and materials used in specific product batches or lots, enhancing traceability and quality control.
11. Cost Estimation and Negotiations: Multi-level BOMs provide suppliers with a detailed breakdown of component requirements, supporting accurate cost estimation and informed negotiations.
12. Agile Response to Changes: In case of design changes or modifications, suppliers can quickly assess the impact on their components and adapt their processes accordingly.
In summary, multi-level BOMs streamline supplier collaboration by providing a shared understanding of component requirements, production schedules, and customization needs.
This collaboration results in smoother procurement processes, on-time delivery of components, and improved overall supply chain performance.
Support for New Product Development
Support for new product development is a critical aspect of business growth and innovation. Multi-Level Bill of Materials (BOMs) play an essential role in providing a solid foundation for designing and introducing new products or variants.
Here's a more detailed elaboration on how multi-level BOMs contribute to supporting new product development:
1. Design and Engineering:
- Component Identification: Multi-level BOMs help designers identify the required components and their relationships early in the design phase, ensuring that all necessary parts are considered.
- Assembly Sequencing: BOMs guide engineers in determining the optimal sequence of assembly operations, minimizing complexity, and streamlining the manufacturing process.
- Design Iterations: Multi-level BOMs allow for rapid iteration and prototyping by providing a clear structure to build upon and modify as needed.
2. Component Sourcing and Procurement:
- Supplier Engagement: BOMs aid procurement teams in engaging with potential suppliers early in the development process to secure the required components for prototypes and initial production runs.
- Lead Time Considerations: Multi-level BOMs help evaluate lead times for critical components, allowing sufficient time for procurement and avoiding delays.
3. Production Planning and Scheduling:
- Resource Allocation: Multi-level BOMs assist production planners in allocating resources, labor, and equipment for the new product's manufacturing process.
- Production Sequence: BOMs guide the production team in determining the correct sequence of assembly operations, reducing errors, and minimizing downtime.
4. Cost Estimation and Budgeting:
- Accurate Costing: Multi-level BOMs enable precise cost estimation for the new product, helping in formulating accurate budgets and pricing strategies.
- Profitability Analysis: BOMs contribute to evaluating the potential profitability of the new product by accounting for all associated costs.
5. Supplier Collaboration:
- Component Specifications: Multi-level BOMs provide detailed specifications to suppliers, ensuring that they understand the requirements for the new product's components.
- Early Engagement: BOMs allow suppliers to get involved early in the development process, offering insights into component availability and potential challenges.
6. Regulatory Compliance and Certification:
- Documentation: Multi-level BOMs serve as a reference for regulatory compliance by documenting the components used and their adherence to industry standards.
- Certification Support: BOMs provide clarity on the components that need to meet specific certifications or standards, facilitating the certification process.
7. Collaboration Across Teams:
- Cross-Functional Alignment: Multi-level BOMs promote collaboration and alignment between design, engineering, manufacturing, procurement, and other departments involved in the new product's development.
8. Change Management and Iterations:
- Design Iterations: Multi-level BOMs allow for efficient design iterations, accommodating changes and improvements as the new product evolves.
- Change Impact Assessment: BOMs help assess the impact of design changes on the overall product structure and manufacturing process.
9. Customization and Variants: Multi-level BOMs enable the inclusion of different components or configurations for product variants, facilitating efficient customization.
10. Time-to-Market Reduction: Efficient new product development enabled by multi-level BOMs can help reduce time-to-market, allowing companies to seize opportunities and stay competitive.
In summary, multi-level BOMs provide a comprehensive framework for all stages of new product development, from design to production to compliance. They enable collaboration, accurate cost estimation, efficient planning, and effective communication across teams, leading to the successful introduction of innovative products to the market.
Enhanced Cross-Functional Collaboration
Enhanced cross-functional collaboration is a key benefit derived from Multi-Level Bills of Materials (BOMs) and plays a critical role in aligning various departments and teams within an organization. BOMs serve as a common reference point that facilitates communication, coordination, and information sharing across different functions.
Here's a more detailed elaboration on how multi-level BOMs contribute to enhanced cross-functional collaboration:
1. Common Information Platform: Multi-level BOMs provide a central repository of product information accessible to different departments. This shared platform ensures that everyone is working with the same accurate and up-to-date data.
2. Design and Engineering Collaboration:
- Design Reviews: Multi-level BOMs facilitate design reviews by allowing different teams to visualize the product structure and identify potential issues early in the process.
- Feedback Loop: Engineers and designers can collaborate on design improvements, modifications, and optimizations using the BOM as a reference point.
3. Manufacturing and Production Alignment:
- Production Planning: Multi-level BOMs enable production planners to align manufacturing processes with the product structure, optimizing assembly sequences and resource allocation.
- Real-Time Updates: Manufacturing teams can access the BOM to stay informed about any changes or updates to the product design.
4. Procurement and Supply Chain Coordination:
- Supplier Collaboration: Multi-level BOMs support collaboration with suppliers by sharing accurate component specifications, lead times, and sourcing requirements.
- Procurement Insights: Procurement teams can use the BOM to understand the impact of component availability on production schedules and make informed decisions.
5. Cost Estimation and Pricing Discussions:
- Financial Alignment: Multi-level BOMs provide the finance and pricing teams with the necessary information to accurately estimate costs and set appropriate pricing strategies.
- Profitability Analysis: Cross-functional collaboration ensures that the pricing strategy aligns with cost considerations while meeting revenue and profit targets.
6. Quality Control and Compliance:
- Quality Feedback Loop: Multi-level BOMs enable quality control teams to provide feedback on potential quality issues related to specific components or assemblies.
- Regulatory Compliance: Collaboration between quality control and design teams ensures that the product adheres to regulatory requirements.
7. Customization and Variants Management:
- Alignment on Variants: Cross-functional collaboration ensures that all departments understand and support the requirements for product customization or variants, from design to production.
8. Change Management and Iterations:
- Change Impact Assessment: Multi-level BOMs help different teams assess the impact of design changes on their respective functions, enabling coordinated change management.
9. Service and Maintenance Support: Multi-level BOMs provide service teams with insights into the product's structure, aiding in accurate diagnosis, maintenance, and replacement of components.
10. Decision-Making Support: Cross-functional collaboration through BOMs allows informed decision-making based on a comprehensive understanding of the product, its components, and its implications on different functions.
11. Knowledge Sharing and Training: Multi-level BOMs serve as a training resource, helping teams understand the product's structure and components, and fostering better collaboration and shared knowledge.
In summary, multi-level BOMs foster collaboration by providing a common language and reference point for various departments to work together effectively.
This collaboration leads to improved communication, faster decision-making, reduced errors, and better overall alignment, contributing to enhanced organizational efficiency and product success.
Efficient Service and Maintenance
Efficient service and maintenance are crucial for ensuring the longevity and reliability of products after they have been sold to customers. Multi-Level Bill of Materials (BOMs) play a significant role in supporting service and maintenance operations by providing a detailed roadmap of the product's structure and components.
Here's a more detailed elaboration on how multi-level BOMs contribute to efficient service and maintenance:
1. Component Identification: Multi-level BOMs provide a comprehensive list of components and sub-assemblies used in the product. This aids service technicians in accurately identifying and locating specific parts during repairs.
2. Accurate Diagnosis: Service teams can use multi-level BOMs to understand how components are interconnected and how they contribute to the product's functionality. This understanding helps in diagnosing issues and identifying the root cause of problems.
3. Efficient Parts Replacement: BOMs guide service technicians in the correct sequence of disassembly and reassembly, ensuring that components are replaced accurately and efficiently.
4. Maintenance Planning: Multi-level BOMs help service teams plan maintenance activities by outlining the components that require regular inspection, replacement, or servicing.
5. Spare Parts Management: BOMs aid in creating accurate spare parts lists and inventory management for service centers, ensuring that the right parts are available when needed.
6. Faster Turnaround Time: Multi-level BOMs streamline the service and maintenance process by providing step-by-step instructions, reducing the time required to diagnose and repair issues.
7. Compatibility and Interchangeability: BOMs indicate compatible and interchangeable components, allowing service technicians to make informed decisions when selecting replacement parts.
8. Technical Documentation: Multi-level BOMs serve as a valuable reference for creating technical manuals, repair guides, and documentation that assist service technicians in performing their tasks.
9. Training and Onboarding: BOMs provide a visual aid for training new service technicians, helping them understand the product's structure and components quickly.
10. Support for Remote Assistance: Multi-level BOMs can be used in remote assistance scenarios, where experts guide on-site technicians through complex repair procedures.
11. Recall and Warranty Management: In the case of recalls or warranty claims, multi-level BOMs help identify affected components and streamline the replacement process.
12. Historical Record Keeping: BOMs serve as a historical record of the product's assembly, facilitating tracking of past repairs, replacements, and maintenance activities.
In summary, multi-level BOMs contribute to efficient service and maintenance operations by providing service teams with accurate information about the product's structure, components, and assembly processes. This results in faster diagnosis, reduced downtime, improved repair accuracy, and enhanced customer satisfaction.
Regulatory Compliance and Documentation
Regulatory compliance and documentation are critical aspects of various industries, ensuring that products meet legal and safety standards. Multi-Level Bill of Materials (BOMs) play a significant role in supporting regulatory compliance efforts by providing a comprehensive record of a product's components, materials, and assembly processes.
Here's a more detailed elaboration on how multi-level BOMs contribute to regulatory compliance and documentation:
1. Component Traceability: Multi-level BOMs enable accurate tracing of components and materials used in the product, which is essential for demonstrating compliance with regulatory requirements.
2. Material Documentation: BOMs list the materials and substances used in the product, allowing manufacturers to provide Material Safety Data Sheets (MSDS) or other required documentation for hazardous materials.
3. Certification and Testing Data: BOMs can be linked to certification and testing data for components, demonstrating that the product adheres to specific industry standards and regulations.
4. Regulatory Reporting: Multi-level BOMs support the compilation of accurate data for regulatory reports, audits, and submissions required by regulatory agencies.
5. Product Labeling and Documentation: BOMs provide the necessary information for creating accurate product labels, user manuals, and documentation required for compliance with labeling and documentation regulations.
6. Supply Chain Transparency: BOMs enhance transparency by documenting the origin of components and the suppliers involved in the production process, which is often required for regulatory compliance.
7. Environmental Regulations: Multi-level BOMs assist in tracking materials subject to environmental regulations, such as RoHS (Restriction of Hazardous Substances) compliance.
8. Cross-Referencing Standards: BOMs can be cross-referenced with industry standards and regulations to ensure that each component meets the required specifications.
9. Change Control and Documentation: Multi-level BOMs help document changes made to product components, facilitating change control processes required for regulatory compliance.
10. Audit Trail Creation: BOMs contribute to establishing a clear audit trail of the product's assembly process, enabling regulators to verify compliance through documentation.
11. Batch and Lot Tracking: BOMs aid in tracking components used in specific product batches or lots, allowing for effective recalls and quality control in case of issues.
12. Verification and Validation: Multi-level BOMs assist in verifying and validating the product's compliance with specific regulations and industry standards through thorough documentation.
In summary, multi-level BOMs play a vital role in ensuring that products meet regulatory requirements and standards. By providing accurate and detailed documentation of components, materials, and assembly processes, multi-level BOMs contribute to successful regulatory compliance, audits, and reporting, while also facilitating transparency and traceability throughout the product lifecycle.
Improved Change Management
Improved change management is a significant benefit of using Multi-Level Bills of Materials (BOMs) within an organization.
BOMs provide a structured framework that supports effective change management processes, allowing businesses to manage modifications, updates, and revisions to products, components, and processes in a controlled and organized manner.
Here's a more detailed elaboration on how multi-level BOMs contribute to improved change management:
1. Change Request Documentation: Multi-level BOMs serve as a reference point for documenting change requests, capturing details about the proposed changes and their impact on the product.
2. Impact Assessment: BOMs allow cross-functional teams to assess the impact of proposed changes on various aspects, such as design, manufacturing, cost, and supply chain.
3. Collaboration and Review: Multi-level BOMs facilitate collaboration among different departments involved in the change management process, enabling them to review and provide input on proposed changes.
4. Change Approval Workflow: BOMs support a structured workflow for change approval, ensuring that changes go through the appropriate review and approval stages before implementation.
5. Revision Control: BOMs provide a clear record of revisions, versions, and updates made to the product or its components, enhancing traceability and accountability.
6. Documentation of Rationale: Multi-level BOMs help document the rationale behind each change, providing a clear understanding of why a change was proposed and how it aligns with organizational goals.
7. Real-time Visibility: BOMs allow stakeholders to access up-to-date information about the product structure, making it easier to track ongoing changes and their status.
8. Supplier Communication: BOMs can be shared with suppliers to communicate approved changes, ensuring that they are aware of and aligned with modifications to components or materials.
9. Compliance Verification: BOMs support the verification of regulatory compliance for changes, ensuring that modifications do not adversely affect product safety or adherence to standards.
10. Risk Management: Multi-level BOMs aid in identifying potential risks associated with proposed changes, allowing teams to assess and mitigate risks before implementation.
11. Accelerated Decision-Making: BOMs streamline decision-making by providing a clear overview of proposed changes, their impact, and associated risks, facilitating informed decisions.
12. Configuration Management: BOMs contribute to effective configuration management by documenting and controlling changes to product configurations over time.
In summary, multi-level BOMs play a vital role in ensuring that changes are managed systematically, transparently, and efficiently across the organization.
By providing a structured framework for change management, BOMs help minimize risks, reduce errors, enhance communication, and promote collaboration among different teams, resulting in improved overall operational effectiveness and adaptability to evolving market demands.
Strategic Decision Making
Strategic decision-making is a crucial aspect of managing a business effectively, and Multi-Level Bills of Materials (BOMs) can provide valuable insights and support for making informed strategic decisions.
BOMs offer a comprehensive view of a product's structure, components, costs, and dependencies, which can influence various strategic choices and directions within an organization.
Here's a more detailed elaboration on how multi-level BOMs contribute to strategic decision-making:
1. Product Portfolio Management:
- Product Rationalization: BOMs help assess the complexity and cost structure of different products, aiding in decisions to optimize or streamline the product portfolio.
- New Product Introductions: BOMs provide insights into the feasibility and cost implications of introducing new products or variants.
2. Cost Management and Pricing Strategies:
- Profitability Analysis: Multi-level BOMs support analyzing the cost breakdown of products, and guiding decisions on pricing, discounts, and promotions.
- Cost Reduction Initiatives: BOMs help identify cost-intensive components or processes, enabling targeted efforts to reduce manufacturing costs.
3. Resource Allocation and Capacity Planning:
- Resource Optimization: BOMs aid in aligning resource allocation with the production requirements of different products, ensuring efficient resource utilization.
- Capacity Expansion: Strategic decisions to expand production capacity can be informed by analyzing the resource needs outlined in multi-level BOMs.
4. Outsourcing and Insourcing Strategies:
- Make vs. Buy Analysis: BOMs assist in evaluating whether to produce components in-house or outsource them based on cost, expertise, and other factors.
- Supplier Selection: BOMs support decisions about partnering with suppliers based on their ability to provide components at the required quality and cost.
5. Innovation and Research & Development:
- Technology Adoption: BOMs can influence decisions to adopt new technologies, materials, or components that align with product innovation strategies.
- Design Improvement: BOMs aid in identifying areas where design improvements can enhance product performance or reduce costs.
6. Market Segmentation and Targeting:
- Customization Strategies: BOMs help assess the feasibility and cost implications of offering product variants to target specific customer segments.
- Competitive Positioning: BOMs guide decisions on positioning products in the market based on features, quality, and pricing.
7. Regulatory Compliance and Sustainability:
- Environmental Considerations: BOMs support decisions related to sustainable materials, eco-friendly components, and compliance with environmental regulations.
8. Merger and Acquisition Strategies:
- Due Diligence: BOMs provide insights into the manufacturing and cost structure of target companies, aiding in due diligence during mergers and acquisitions.
9. Supply Chain Optimization:
- Supplier Collaboration: BOMs facilitate decisions to collaborate closely with suppliers for improved efficiency, quality, and supply chain resilience.
10. Risk Management and Contingency Planning: Multi-level BOMs contribute to identifying potential risks in the supply chain, production process, or component availability, enabling proactive risk management.
11. Investment Prioritization: BOMs help prioritize investments in equipment, technology, and processes based on their alignment with product requirements and strategic goals.
12. Competitive Differentiation: Strategic decisions based on BOM insights can lead to product differentiation through quality, cost-effectiveness, or innovative features.
In summary, multi-level BOMs provide a holistic view of a product's structure, costs, and dependencies, enabling organizations to make well-informed strategic decisions that align with their goals, resources, and market dynamics.
By leveraging BOM data, businesses can enhance their competitive positioning, operational efficiency, and overall success in the market.
Challenges Associated with Multi-Level Bill of Materials
While Multi-Level Bill of Materials (BOMs) offer numerous benefits, they also come with several challenges that organizations need to address for successful implementation and management.
Some of the challenges of multi-level BOMs include:
Data Accuracy and Maintenance
Data accuracy and maintenance are critical challenges that organizations often encounter when working with Multi-Level Bill of Materials (BOMs). BOMs serve as a foundation for various business functions, but ensuring that the data within the BOMs is accurate, up-to-date, and properly maintained can be a complex task.
Here's a more detailed elaboration on the challenge of data accuracy and maintenance and its impact on the use of multi-level BOMs:
1. Inaccurate Data: Inaccurate or incorrect information in the BOM can lead to errors in design, manufacturing, procurement, and other processes. Even small discrepancies can have significant repercussions.
2. Outdated Information: BOMs require constant updates to reflect changes in product design, components, suppliers, and other variables. Outdated BOM data can result in using incorrect parts or processes.
3. Lack of Standardization: Inconsistent naming conventions, units of measurement, and formatting can lead to confusion and misinterpretation of BOM data, affecting decision-making.
4. Duplication and Redundancy: Data duplication, such as having multiple BOM versions that are not synchronized, can lead to confusion, inefficiency, and increased risk of errors.
5. Change Management Challenges: Implementing changes to BOMs requires careful coordination and communication across different teams and departments, which can be difficult to manage.
6. Cross-Functional Collaboration: Maintaining accurate BOM data requires collaboration among different departments, and communication gaps or conflicting priorities can lead to data discrepancies.
7. Compliance and Regulatory Issues: Inaccurate or outdated BOM data can lead to non-compliance with industry regulations and standards, resulting in legal and financial consequences.
8. Supplier and Partner Collaboration: Inaccurate BOM data can lead to miscommunication with suppliers and partners, resulting in delays, quality issues, or incorrect component sourcing.
9. Manufacturing Errors: Errors in BOM data can lead to mistakes in assembly, quality control, and other manufacturing processes, affecting product quality and reliability.
10. Decision-Making Impact: Inaccurate BOM data can lead to incorrect cost estimations, pricing decisions, and strategic choices, impacting overall business performance.
11. Complexity Management: Managing accurate data in complex multi-level BOMs becomes more challenging as the number of components and dependencies increases.
12. Training and Onboarding: New employees and team members may struggle to understand and work with inaccurate or poorly maintained BOM data.
Mitigation Strategies:
- Data Governance: Implement clear data governance policies and procedures to ensure data accuracy, quality, and consistency.
- Regular Audits: Conduct routine audits of BOM data to identify and correct inaccuracies, outdated information, and inconsistencies.
- Version Control: Establish version control mechanisms to track changes and updates to BOMs, ensuring that accurate historical data is preserved.
- Cross-Functional Collaboration: Involve cross-functional teams in reviewing and updating BOM data to ensure comprehensive and accurate information.
- Automated Systems: Implement software tools and systems that automate data updates, changes, and notifications to minimize manual errors.
- Data Validation: Implement validation checks to ensure that BOM data is complete, accurate, and conforms to established standards.
In summary, data accuracy and maintenance are central challenges that organizations must address when working with multi-level BOMs.
By implementing robust data management practices and fostering a culture of accuracy and collaboration, businesses can overcome these challenges and leverage the full potential of multi-level BOMs for improved operational efficiency and decision-making.
Complexity Management
Complexity management is a significant challenge that organizations often face when using Multi-Level Bills of Materials (BOMs) in their operations. Multi-level BOMs provide detailed information about the structure and components of products, but as products become more complex, managing and navigating this information can become challenging.
Here's a more detailed elaboration on the challenge of complexity management and how it can impact the use of multi-level BOMs:
1. Information Overload: As products become more complex, the number of components, sub-assemblies, and dependencies in the BOM can increase significantly. This can lead to information overload, making it difficult to extract relevant insights from the BOM data.
2. Design Complexity: Complex products often have intricate designs with numerous interrelated parts. Managing and coordinating these components in the BOM can be challenging, leading to errors in design and assembly.
3. Change Management: Implementing changes in complex BOMs can be cumbersome. Changes may have cascading effects on various components and require extensive coordination across different teams and departments.
4. Communication Breakdown: Communicating complex BOM information across departments can be challenging. Miscommunication or misunderstanding of the BOM structure can lead to errors in manufacturing, procurement, and other processes.
5. Impact Analysis: Assessing the impact of changes or modifications to complex BOMs can be time-consuming and complex. It may involve cross-functional analysis to understand how changes affect different aspects of the product.
6. Version Control: Managing different versions of complex BOMs can be difficult, especially when multiple teams are involved in making modifications. Version control errors can lead to confusion and inconsistencies.
7. Training and Onboarding: Introducing new employees or team members to complex BOMs requires comprehensive training due to the intricate nature of the information.
8. Component Sourcing and Procurement: Complex BOMs can make component sourcing and procurement more challenging, as each component's specifications, suppliers, and lead times need to be carefully managed.
9. Manufacturing Efficiency: Complex BOMs can lead to inefficient manufacturing processes, as assembly sequences, work instructions, and quality control steps may become more complicated.
10. Integration with Systems: Integrating complex BOMs with other systems, such as Enterprise Resource Planning (ERP) or Product Lifecycle Management (PLM) systems, can be complex and require significant customization.
11. Customization and Variants: Managing customization and product variants within a complex BOM structure can lead to confusion and potential errors.
12. Supplier Collaboration: Complex BOMs may require close collaboration with suppliers to ensure accurate component specifications, which can be challenging to manage effectively.
Mitigation Strategies:
- Simplification: Simplify product designs and BOM structures when possible to reduce complexity.
- Modularization: Break down complex products into modular components, making it easier to manage and update BOMs.
- Standardization: Standardize components and sub-assemblies to reduce the number of unique parts in the BOM.
- Software Solutions: Use specialized software tools for BOM management that offer features for visualization, impact analysis, and change management.
- Cross-Functional Teams: Involve cross-functional teams in BOM design, management, and change processes to ensure comprehensive perspectives.
In summary, complexity management is a challenge that organizations must address when using multi-level BOMs. By implementing strategies to simplify, standardize, and effectively manage complex BOMs, businesses can overcome these challenges and leverage the benefits that multi-level BOMs offer for improved operational efficiency and decision-making.
Version Control and Change Management
Version control and change management are crucial challenges organizations often face when using Multi-Level Bill of Materials (BOMs) in their operations. BOMs are dynamic documents that evolve over time due to design changes, updates, and improvements. Properly managing these changes while maintaining accurate version control is essential to ensure the reliability and effectiveness of BOMs.
Here's a more detailed elaboration on the challenge of version control and change management and its impact on the use of multi-level BOMs:
1. Change Complexity: Changes to multi-level BOMs can be complex, especially in products with numerous components and dependencies. Managing and coordinating these changes across different levels of the BOM can be challenging.
2. Change Approval Workflow: Implementing a structured change approval process can be challenging, particularly when changes need to be reviewed and approved by multiple stakeholders from different departments.
3. Communication Breakdown: Ineffective communication regarding BOM changes can lead to misunderstandings, errors, and inconsistent implementations, impacting product quality and timelines.
4. Cross-Functional Coordination: Coordinating changes across various functions such as design, engineering, manufacturing, procurement, and quality control requires effective collaboration and communication.
5. Impact Analysis: Assessing the impact of proposed changes on the entire BOM structure, downstream processes, costs, and timelines can be time-consuming and complex.
6. Change Tracking: Properly tracking and documenting changes in multi-level BOMs is essential to maintain a clear history of modifications and understand the reasons behind each change.
7. Version Control Errors: Managing multiple versions of BOMs and ensuring that the correct version is used for different production runs can be challenging and prone to errors.
8. Compliance and Regulatory Considerations: Changes to BOMs must consider regulatory and compliance requirements, which can add complexity to the change management process.
9. Supplier and Partner Collaboration: Changes in BOMs need to be effectively communicated to suppliers and partners to ensure accurate component sourcing and production.
10. Change Documentation: Properly documenting the rationale, decisions, and approvals related to BOM changes is crucial for transparency and accountability.
11. Testing and Validation: Changes to BOMs may require additional testing and validation to ensure that the modified product still meets quality and performance standards.
12. Risk Assessment: Assessing the risks associated with proposed changes and implementing mitigations to prevent unintended consequences is essential.
Mitigation Strategies:
- Structured Change Management Process: Implement a well-defined and structured process for proposing, reviewing, approving, and implementing BOM changes.
- Change Control Boards: Establish cross-functional change control boards to review and approve BOM changes, ensuring that all relevant stakeholders are involved.
- Change Management Software: Utilize software tools designed for change management that offer version control, collaboration, and workflow capabilities.
- Impact Assessment Tools: Employ tools that help assess the impact of proposed changes on BOMs, processes, costs, and other relevant factors.
- Communication Protocols: Establish clear communication protocols to ensure that all stakeholders are informed of BOM changes and their implications.
- Training and Education: Provide training to employees involved in BOM changes to ensure they understand the process, requirements, and importance of accurate documentation.
- Documentation Standards: Define documentation standards for BOM changes, including change descriptions, rationales, approvals, and implementation details.
In summary, version control and change management are critical challenges that organizations must address to effectively use multi-level BOMs.
By implementing structured processes, utilizing specialized tools, fostering collaboration, and maintaining accurate documentation, businesses can navigate these challenges and ensure that BOM changes are managed in a controlled and efficient manner, leading to improved product quality and operational excellence.
Software Integration
Software integration is a significant challenge that organizations may encounter when using Multi-Level Bill of Materials (BOMs) as part of their operations. Integrating BOM data with other software systems and tools, such as Enterprise Resource Planning (ERP), Product Lifecycle Management (PLM), and Computer-Aided Design (CAD) software, can be complex and require careful planning and execution.
Here's a more detailed elaboration on the challenge of software integration and its impact on the use of multi-level BOMs:
1. Data Consistency and Synchronization: Integrating BOM data with other software systems requires ensuring data consistency and synchronization across different platforms. Inaccuracies or discrepancies in BOM data can lead to errors in downstream processes.
2. Technical Compatibility: Ensuring that BOM data can be effectively integrated with existing software systems may require addressing technical compatibility issues, data formats, and communication protocols.
3. Customization and Configuration: Software integration often involves customization and configuration to align with the specific needs and processes of the organization. This customization can be complex and time-consuming.
4. Data Mapping and Transformation: Converting BOM data from one system to another may require data mapping and transformation to ensure that the information is correctly interpreted and utilized by different software applications.
5. Workflow Alignment: Integrating BOM data with other systems requires aligning workflows and processes to ensure that data flows seamlessly between different tools without disrupting operations.
6. Change Management: Changes to BOM data may impact integrated software systems, necessitating careful change management to ensure that updates are implemented smoothly.
7. Vendor Collaboration: Collaborating with software vendors and third-party providers may be necessary to ensure effective integration and address any technical challenges that arise.
8. Data Security and Privacy: Integrating BOM data with external systems raises concerns about data security, access control, and compliance with privacy regulations.
9. Training and User Adoption: Integrating BOM data with new software systems requires training employees on how to use the integrated tools effectively.
10. Performance and Scalability: Ensuring that integrated systems can handle the volume of BOM data and user interactions without compromising performance is essential.
11. System Upgrades and Maintenance: Upgrading or maintaining integrated software systems may require adjustments to ensure continued compatibility and functionality with BOM data.
12. Return on Investment (ROI): The costs and efforts associated with software integration should be balanced with the potential benefits and improvements in operational efficiency.
Mitigation Strategies:
- Requirements Analysis: Clearly define integration requirements, objectives, and expected outcomes before embarking on integration projects.
- Vendor Evaluation: Select software vendors and solutions that offer strong integration capabilities and provide support for seamless data exchange.
- APIs and Integration Platforms: Utilize Application Programming Interfaces (APIs) and integration platforms to facilitate data exchange between different software systems.
- Data Standards: Establish data standards and formats that promote compatibility and consistency across integrated systems.
- Testing and Validation: Conduct thorough testing and validation of integrated systems to identify and address any issues or discrepancies.
- Change Management: Develop a change management plan to ensure smooth transitions and updates when making changes to integrated software systems.
- Security Measures: Implement robust data security measures and access controls to protect sensitive BOM data during integration.
In summary, software integration is a complex challenge that organizations must navigate when using multi-level BOMs.
By carefully planning, evaluating vendor solutions, addressing technical considerations, and ensuring effective change management, businesses can overcome these challenges and successfully integrate BOM data with other software systems to enhance operational efficiency and decision-making.
Cross-Departmental Communication
Cross-departmental communication is a significant challenge that organizations often face when utilizing Multi-Level Bills of Materials (BOMs) in their operations. BOMs contain critical information that impacts various functions within an organization, and ensuring effective communication and collaboration between different departments is essential for maximizing the benefits of multi-level BOMs.
Here's a more detailed elaboration on the challenge of cross-departmental communication and its impact on the use of multi-level BOMs:
1. Information Silos: Departments within an organization often work in silos, with limited communication and visibility into each other's activities. This can lead to isolated decision-making and missed opportunities for optimization.
2. Communication Barriers: Different departments may use specialized terminology and have distinct processes, making effective communication about BOM-related matters challenging.
3. Misalignment of Priorities: Departments may have different priorities and objectives, leading to conflicting perspectives on BOM data and its implications.
4. Lack of Visibility: Inadequate sharing of BOM data across departments can result in limited visibility into the entire product lifecycle, hindering the ability to make informed decisions.
5. Incomplete Information: Departments may possess only partial information about BOMs, leading to incomplete or inaccurate decision-making.
6. Slow Decision-Making: Delays in obtaining necessary information from other departments can slow down decision-making processes and hinder timely actions.
7. Resistance to Change: Departments may resist changes to established processes or BOM data, leading to friction and reluctance to adopt new practices.
8. Lack of Ownership: The absence of clear ownership or accountability for BOM-related data and decisions can lead to confusion and gaps in responsibility.
9. Coordination Challenges: Collaborating across departments to implement changes, updates, or improvements to BOMs can be challenging due to differing schedules and priorities.
10. Quality and Consistency: Lack of cross-departmental communication can result in inconsistencies, errors, and discrepancies in BOM data, affecting product quality and reliability.
11. Compliance and Regulations: Failure to communicate changes in BOM data to relevant departments can lead to non-compliance with industry regulations and standards.
12. Stakeholder Involvement: Engaging all relevant stakeholders in BOM-related discussions and decisions is crucial for ensuring that the full range of perspectives and expertise is considered.
Mitigation Strategies:
- Cross-Functional Teams: Form cross-functional teams that include representatives from different departments to facilitate collaboration and communication.
- Regular Meetings: Hold regular meetings or discussions to share BOM-related information, updates, and challenges among relevant departments.
- Centralized Information Repository: Establish a centralized platform where BOM data and related information can be accessed and shared by all relevant stakeholders.
- Communication Protocols: Define clear communication protocols, channels, and responsibilities for sharing BOM data and updates.
- Training and Education: Provide training to employees about the importance of cross-departmental communication and the impact of BOM data on various functions.
- Change Management: Implement change management strategies that involve and engage all relevant departments in BOM-related changes and updates.
- Leadership Support: Obtain support from organizational leaders to promote a culture of collaboration and communication across departments.
In summary, cross-departmental communication is a critical challenge that organizations must address to effectively use multi-level BOMs.
By fostering a culture of collaboration, implementing communication strategies, and involving all relevant stakeholders in BOM-related decisions, businesses can overcome these challenges and leverage the benefits of multi-level BOMs to enhance operational efficiency and achieve better outcomes.
Supplier Collaboration
Supplier collaboration is a significant challenge that organizations often encounter when utilizing Multi-Level Bill of Materials (BOMs) in their operations.
Collaborating effectively with suppliers is crucial to ensure the timely and accurate sourcing of components, materials, and parts required for product assembly.
Suppliers play a vital role in the overall supply chain, and challenges in supplier collaboration can impact production schedules, product quality, and cost management.
Here's a more detailed elaboration on the challenge of supplier collaboration and its impact on the use of multi-level BOMs:
1. Communication Complexity: Coordinating and communicating BOM changes, updates, and requirements with suppliers can be complex, especially when dealing with a diverse range of components and suppliers.
2. Supplier Variability: Different suppliers may provide variations of the same component, leading to challenges in maintaining consistency and compatibility within the BOM.
3. Component Specifications: Ensuring that suppliers adhere to the required specifications and quality standards for components listed in the BOM is essential for product performance and reliability.
4. Lead Times and Timely Delivery: Accurate BOM data is critical for suppliers to provide components within the specified lead times. Incorrect data can lead to production delays and disruptions.
5. Cost Estimation and Negotiation: Collaborating with suppliers on accurate cost estimates and negotiating prices based on BOM data is essential for effective cost management and profitability.
6. Component Sourcing: Inaccurate BOM data can result in incorrect component sourcing, leading to potential quality issues, compatibility problems, or production delays.
7. Supplier Capacity Planning: Suppliers rely on accurate BOM data to plan their own capacity and production schedules, which can be impacted by changes in BOMs.
8. Risk Management: Inadequate communication with suppliers regarding BOM changes can lead to supply chain disruptions, shortages, or quality issues.
9. Supplier Relationship Management: Maintaining strong relationships with suppliers requires effective communication and collaboration, which can be challenging when BOM data is not accurate or up-to-date.
10. New Product Introductions: Collaborating with suppliers during the introduction of new products or variants requires sharing accurate BOM data and coordinating production timelines.
11. Regulatory Compliance: Ensuring that suppliers are aware of and adhere to regulatory requirements related to BOM components is essential for compliance and risk mitigation.
12. Continuous Improvement: Suppliers play a role in product improvement and innovation, and effective collaboration is needed to leverage their expertise in enhancing product quality and performance.
Mitigation Strategies:
- Clear Communication Channels: Establish clear and efficient channels of communication with suppliers for sharing BOM data, updates, and requirements.
- Supplier Portals: Implement supplier portals or platforms where suppliers can access and download accurate BOM data, specifications, and changes.
- Data Validation: Ensure that BOM data provided to suppliers is validated and accurate before sharing, minimizing the risk of errors.
- Collaborative Tools: Utilize collaborative software tools that enable real-time communication, document sharing, and version control between organizations and suppliers.
- Supplier Training: Provide training to suppliers on how to interpret and utilize BOM data effectively.
- Regular Reviews: Conduct periodic reviews with suppliers to discuss BOM-related matters, changes, and improvement opportunities.
- Performance Metrics: Establish performance metrics and key performance indicators (KPIs) to measure and monitor supplier collaboration effectiveness.
- Supplier Involvement: Involve suppliers early in the design and development process to ensure their input is considered when creating or updating BOMs.
In summary, supplier collaboration is a critical aspect of using multi-level BOMs, and effective communication and coordination with suppliers are essential for smooth operations and supply chain management.
By implementing strategies that promote clear communication, accurate data sharing, and mutual understanding, organizations can overcome challenges in supplier collaboration and enhance their ability to leverage multi-level BOMs for improved operational efficiency and product quality.
Complex Procurement and Sourcing
Complex procurement and sourcing is a significant challenge that organizations often encounter when utilizing Multi-Level Bill of Materials (BOMs) in their operations.
BOMs provide detailed information about the components and parts required for product assembly, and effectively procuring and sourcing these components is crucial for efficient production and timely delivery.
Complex procurement and sourcing challenges can impact supply chain management, lead times, costs, and overall operational efficiency.
Here's a more detailed elaboration on the challenge of complex procurement and sourcing and its impact on the use of multi-level BOMs:
1. Diverse Component Requirements: Multi-level BOMs can encompass a wide range of components with varying specifications, suppliers, and lead times, making procurement and sourcing more complex.
2. Supplier Identification: Identifying suitable suppliers for each component listed in the BOM requires careful evaluation of capabilities, quality standards, and cost competitiveness.
3. Supplier Relationships: Building and maintaining strong relationships with a diverse set of suppliers for different components can be challenging and require ongoing communication and collaboration.
4. Lead Time Management: Procurement of components based on accurate BOM data is essential to ensure that components arrive in time for production, minimizing delays.
5. Component Compatibility: Ensuring that sourced components are compatible with other parts listed in the BOM is crucial to prevent assembly issues and ensure product quality.
6. Cost Management: Accurate BOM data is essential for negotiating costs with suppliers and effectively managing procurement expenses.
7. Supplier Performance: Monitoring and evaluating supplier performance for each component requires access to accurate BOM data to track quality, delivery times, and reliability.
8. Component Availability: Accurate BOM data is necessary to assess component availability and ensure that required parts are in stock or can be sourced within acceptable lead times.
9. Single Point of Contact: Dealing with multiple suppliers for different BOM components may require managing multiple points of contact, which can add complexity to procurement processes.
10. Regulatory Compliance: Ensuring that sourced components meet regulatory and quality standards is essential, and accurate BOM data helps verify compliance.
11. Forecasting and Planning: Complex procurement requires accurate forecasting and planning based on BOM data to ensure sufficient inventory levels and production capabilities.
12. Supply Chain Disruptions: Inaccurate BOM data can lead to supply chain disruptions if component availability, lead times, or other sourcing factors are not accurately represented.
Mitigation Strategies:
- Supplier Collaboration: Collaborate closely with suppliers to share accurate BOM data, component requirements, and production timelines.
- Supplier Performance Metrics: Establish performance metrics and KPIs to assess and monitor supplier performance for each BOM component.
- Supplier Diversity: Maintain a diverse supplier base to ensure flexibility and redundancy in sourcing options for BOM components.
- Digital Procurement Platforms: Utilize digital procurement platforms that facilitate accurate data sharing, supplier communication, and procurement processes.
- Procurement Automation: Implement automation tools for procurement processes, such as automated purchase order generation based on BOM data.
- Centralized Procurement: Establish a centralized procurement function to manage BOM components and streamline sourcing processes.
- Risk Management: Develop contingency plans and risk mitigation strategies to address potential supply chain disruptions caused by inaccurate BOM data.
In summary, complex procurement and sourcing challenges can have a significant impact on supply chain management and operational efficiency when using multi-level BOMs.
By implementing strategies that promote accurate BOM data sharing, effective supplier collaboration, and streamlined procurement processes, organizations can navigate these challenges and optimize their procurement and sourcing practices for improved production outcomes and supply chain resilience.
Training and Education
Training and education is a significant challenge that organizations often face when utilizing Multi-Level Bill of Materials (BOMs) in their operations.
BOMs contain intricate information about product structures, components, and processes, and ensuring that employees across different departments understand how to interpret and utilize BOM data is crucial for effective decision-making and operational efficiency.
Inadequate training and education can lead to misunderstandings, errors, and inefficiencies in various aspects of the organization.
Here's a more detailed elaboration on the challenge of training and education and its impact on the use of multi-level BOMs:
1. Interpretation Complexity: Multi-level BOMs can be complex to interpret, especially for employees who are not familiar with engineering or manufacturing terminology and concepts.
2. Departmental Differences: Different departments may require varying levels of BOM-related knowledge and skills based on their roles and responsibilities.
3. New Employee Onboarding: Training new employees on how to understand and work with BOM data effectively can be time-consuming, especially if the data is complex or not well-documented.
4. Change Management: Employees need to be educated on how to manage and implement changes to BOMs, especially when updates impact their roles or processes.
5. Process Integration: Ensuring that employees across departments understand how BOM data integrates with their respective processes is essential for seamless operations.
6. Data Integrity: Educating employees about the importance of data accuracy, maintenance, and documentation is critical to prevent errors in BOMs and downstream processes.
7. Cross-Functional Collaboration: Effective collaboration across departments requires employees to understand the roles and contributions of others in the context of BOM-related activities.
8. Supplier Interaction: Employees involved in supplier collaboration need training on how to effectively communicate BOM requirements and changes with external partners.
9. Regulatory Compliance: Educating employees about the regulatory and compliance implications of BOM data is essential to prevent legal issues and non-compliance.
10. Decision-Making Skills: Training employees to make informed decisions based on BOM data, such as cost estimation or sourcing decisions, requires understanding the broader context.
11. Continuous Improvement: Educating employees about the potential for using BOM data for continuous improvement initiatives can lead to enhanced product quality and operational efficiency.
12. Technological Proficiency: Ensuring that employees are proficient in using software tools and systems that manage BOM data is essential for accurate data entry and analysis.
Mitigation Strategies:
- Training Programs: Develop comprehensive training programs that cover BOM concepts, interpretation, and utilization for different employee roles.
- Role-Specific Training: Tailor training content to the specific needs of different departments and roles within the organization.
- Documentation and Resources: Provide clear and accessible documentation, guides, and resources for employees to refer to when working with BOM data.
- On-the-Job Training: Facilitate hands-on learning opportunities where employees can apply BOM-related concepts in real-world scenarios.
- Regular Updates: Offer regular training updates to keep employees informed about changes in BOM processes, software tools, and best practices.
- Cross-Functional Workshops: Organize workshops or sessions that promote cross-departmental collaboration and understanding of BOM-related activities.
- Mentoring and Coaching: Pair experienced employees with newcomers to provide guidance and mentorship in working with BOM data.
- Software Training: Provide specialized training for software tools used for BOM management and analysis.
- Feedback Mechanisms: Create channels for employees to provide feedback on training programs and suggest areas for improvement.
In summary, training, and education are essential for overcoming the challenge of effectively utilizing multi-level BOMs. By investing in comprehensive training programs, providing resources, and fostering a culture of continuous learning, organizations can equip their employees with the skills and knowledge needed to leverage BOM data for improved operational efficiency, decision-making, and collaboration across departments.
Maintenance and Updates
Maintenance and updates are crucial challenges that organizations often face when utilizing Multi-Level Bill of Materials (BOMs) in their operations.
BOMs are dynamic documents that require continuous maintenance and updates to reflect changes in product design, components, suppliers, and other variables.
Properly managing these updates is essential to ensure the accuracy, reliability, and effectiveness of BOMs throughout the product life cycle.
Here's a more detailed elaboration on the challenge of maintenance and updates and their impact on the use of multi-level BOMs:
1. Change Complexity: BOMs can undergo frequent and complex changes due to design revisions, component substitutions, engineering changes, and other factors. Managing these changes can be challenging.
2. Data Accuracy: Updates to BOMs must be accurate to avoid errors in downstream processes such as procurement, manufacturing, and quality control.
3. Version Control: Managing different versions of BOMs, especially when multiple teams are making modifications simultaneously, can lead to confusion and discrepancies.
4. Timely Updates: Delays in updating BOMs with new information can lead to misinformed decisions, production delays, and increased costs.
5. Communication Breakdown: Inadequate communication about BOM updates among relevant departments can lead to misunderstandings and incorrect implementations.
6. Cross-Functional Coordination: Coordinating updates across various departments, such as design, engineering, procurement, and manufacturing, requires effective collaboration and communication.
7. Impact Analysis: Assessing the impact of proposed updates on the entire BOM structure, downstream processes, costs, and timelines can be time-consuming and complex.
8. Supplier Collaboration: Accurate and timely communication of BOM updates to suppliers is critical to ensure that components are sourced correctly.
9. Regulatory Compliance: Updates to BOMs must consider regulatory requirements and compliance, which can add complexity to the update process.
10. Training and Education: Employees need to be trained on how to interpret and work with updated BOM data to avoid errors and misunderstandings.
11. Documentation and Traceability: Properly documenting and tracking BOM updates is essential for maintaining a clear history of changes and the reasons behind each update.
12. Risk Management: Implementing updates without thorough analysis or consideration of potential risks can lead to unintended consequences and disruptions.
Mitigation Strategies:
- Change Management Process: Implement a structured change management process that includes clear procedures, roles, and responsibilities for updating BOMs.
- Cross-Functional Teams: Establish cross-functional teams to review and approve BOM updates, ensuring that all relevant stakeholders are involved.
- Version Control Tools: Use version control tools and software to track changes and updates to BOMs and ensure accurate historical data.
- Communication Protocols: Define clear communication protocols for sharing BOM updates and changes among relevant departments.
- Automated Notifications: Implement automated notifications and alerts to inform relevant parties of BOM updates in real-time.
- Supplier Collaboration Platforms: Utilize digital platforms to facilitate communication and collaboration with suppliers for sharing updated BOM information.
- Training and Education: Provide ongoing training to employees on how to interpret and implement BOM updates effectively.
- Documentation Standards: Establish documentation standards for BOM updates, including change descriptions, rationales, approvals, and implementation details.
- Impact Assessment Tools: Use software tools that assist in assessing the impact of proposed updates on BOMs, processes, and costs.
In summary, maintenance and updates are essential aspects of effectively using multi-level BOMs. By implementing robust change management processes, fostering collaboration, and leveraging technology tools, organizations can navigate the challenges of maintaining and updating BOMs to ensure accurate, reliable, and up-to-date information for improved operational efficiency and decision-making.
Customization and Variability
Customization and variability are significant challenges that organizations often face when utilizing Multi-Level Bills of Materials (BOMs) in their operations.
BOMs need to accommodate a wide range of product variations, configurations, and customizations to meet diverse customer needs and market demands. Balancing the need for flexibility and customization with the complexity of managing these variations can be a challenging task.
Here's a more detailed elaboration on the challenge of customization and variability and its impact on the use of multi-level BOMs:
1. Diverse Product Configurations: Organizations often offer products with various configurations, features, and options, leading to a higher number of BOM variations to manage.
2. Complex Data Structures: Accommodating multiple configurations within a single BOM can result in complex data structures that are challenging to manage and interpret.
3. Customization Requests: Customization requests from customers may lead to changes in BOMs, requiring effective management of unique product specifications.
4. Compatibility Challenges: Ensuring that customizations and variations are compatible with other components and systems listed in the BOM can be intricate.
5. Change Management Complexity: Managing changes and updates across multiple BOM variations requires careful coordination and communication across different departments.
6. Procurement and Sourcing: Customized or variable BOMs may involve unique components or suppliers, leading to complexities in procurement and sourcing.
7. Inventory Management: Managing inventory for various BOM configurations can lead to challenges in stock levels, storage, and cost control.
8. Production Planning: Production planning for custom or variable products requires accurate BOM data and clear communication across production teams.
9. Documentation and Traceability: Documenting and tracing changes in customized or variable BOMs is essential for maintaining accurate records and accountability.
10. Cost Estimation and Pricing: Calculating costs and pricing for customized products based on variable BOMs can be complex and may require accurate data.
11. Training and Onboarding: Educating employees about the different BOM configurations and variations is essential for accurate interpretation and implementation.
12. Data Integrity: Ensuring data integrity and accuracy across multiple BOM variations is critical to prevent errors and inconsistencies.
Mitigation Strategies:
- Modular BOM Structures: Create modular BOM structures that allow for easy customization and variation while maintaining consistency.
- Configuration Management Tools: Utilize configuration management tools or software to manage and track different BOM variations.
- Documentation Standards: Establish clear documentation standards for customizations and variations, including change history and reasons.
- Collaboration and Communication: Foster collaboration and communication among departments involved in managing customizations and variations.
- Cross-Functional Reviews: Implement cross-functional reviews for changes to customized or variable BOMs to ensure accuracy and compatibility.
- Automation and Integration: Leverage automation and integration between BOM management systems and other software tools to streamline processes.
- Supplier Collaboration: Involve suppliers in discussions about customizations and variations to ensure accurate sourcing and component availability.
- Data Validation: Implement data validation checks to ensure that customized BOMs adhere to compatibility and design standards.
- Regular Audits: Conduct regular audits and reviews of customized BOMs to identify and address discrepancies or inconsistencies.
In summary, managing customization and variability within multi-level BOMs is a complex challenge that requires careful planning, effective communication, and streamlined processes.
By adopting appropriate tools, standards, and collaborative practices, organizations can navigate these challenges and leverage the benefits of customizability while maintaining accurate and efficient BOM management.
Regulatory Compliance
Regulatory compliance is a significant challenge that organizations often encounter when utilizing Multi-Level Bill of Materials (BOMs) in their operations.
BOMs contain crucial information about the components and materials used in products, and ensuring that these components meet regulatory requirements and standards is essential to avoid legal and compliance issues.
Regulatory compliance challenges can impact product quality, safety, and market access.
Here's a more detailed elaboration on the challenge of regulatory compliance and its impact on the use of multi-level BOMs:
1. Evolving Regulations: Regulatory standards and requirements can change over time, necessitating continuous updates and adjustments to BOMs to ensure ongoing compliance.
2. Industry-Specific Regulations: Different industries and markets may have unique regulatory requirements that need to be incorporated into BOMs for accurate compliance.
3. Component Certification: Ensuring that components listed in the BOM have the necessary certifications, such as safety, environmental, or quality certifications, is critical for compliance.
4. Traceability and Documentation: Regulatory compliance often requires detailed documentation and traceability of components throughout the supply chain, which can be complex to manage.
5. International Compliance: Organizations operating in multiple regions or countries must navigate varying regulatory frameworks and standards, adding complexity to BOM management.
6. Impact on Design and Manufacturing: Changes to BOMs due to regulatory compliance can impact product design, manufacturing processes, and lead times.
7. Product Labeling and Documentation: Accurate BOM data is essential for creating accurate product labels, documentation, and information required by regulatory authorities.
8. Audits and Inspections: BOM data may be subject to audits and inspections by regulatory agencies to ensure compliance with applicable standards.
9. Risk Assessment and Mitigation: BOM data plays a role in assessing and mitigating risks related to compliance violations, product recalls, and legal liabilities.
10. Supplier Compliance: Collaborating with suppliers to ensure that the components they provide meet regulatory requirements is crucial for compliance.
11. Data Accuracy: Inaccuracies in BOM data can lead to non-compliance, which can result in legal penalties, product recalls, and damage to the organization's reputation.
12. Change Management: Regulatory updates or changes may require corresponding updates to BOMs, necessitating effective change management processes.
Mitigation Strategies:
- Regulatory Expertise: Employ regulatory experts or consultants to ensure that BOMs accurately reflect the latest regulatory requirements.
- Regulatory Software Tools: Utilize software tools that track and incorporate regulatory standards and requirements into BOMs.
- Supplier Collaboration: Collaborate closely with suppliers to verify the compliance of components and materials used in products.
- Documentation Management: Establish standardized documentation processes to ensure accurate records of component certifications and compliance.
- Automated Alerts: Implement automated alerts and notifications for regulatory updates that may impact BOMs.
- Regular Audits: Conduct regular audits of BOMs to ensure compliance with changing regulatory standards.
- Training and Education: Provide training to employees on the importance of regulatory compliance and how it relates to BOM data.
- Cross-Functional Reviews: Involve cross-functional teams in reviewing BOMs for compliance to ensure accurate interpretation and implementation.
In summary, regulatory compliance is a critical consideration when using multi-level BOMs, especially in regulated industries.
By implementing strategies that incorporate regulatory expertise, effective documentation practices, and collaboration with suppliers, organizations can navigate the challenges of regulatory compliance and ensure that BOMs accurately reflect the necessary standards and requirements.
Cultural and Organizational Challenges
Cultural and organizational challenges are important considerations that organizations often encounter when utilizing Multi-Level Bills of Materials (BOMs) in their operations.
These challenges relate to the organizational culture, structure, and processes that influence how BOM data is managed, communicated, and utilized within the company. Overcoming cultural and organizational challenges is crucial to ensure effective BOM management and maximize the benefits of using multi-level BOMs.
Here's a more detailed elaboration on the challenge of cultural and organizational challenges and their impact on the use of multi-level BOMs:
1. Siloed Departments: Organizational silos, where departments work independently with limited collaboration, can hinder the accurate sharing and utilization of BOM data across functions.
2. Communication Barriers: Poor communication between departments can lead to misunderstandings, data discrepancies, and inefficiencies in BOM-related processes.
3. Resistance to Change: Employees may resist changes in BOM-related processes or systems, especially if they are accustomed to existing practices.
4. Lack of Data Ownership: Unclear ownership and accountability for BOM data can lead to inconsistencies, errors, and delays in updates.
5. Cultural Differences: Multinational organizations may face challenges in standardizing BOM practices and terminology across different cultural contexts.
6. Inconsistent Processes: Different departments may have varied processes for creating, updating, and managing BOMs, leading to inconsistencies and errors.
7. Lack of Awareness: Some employees may not fully understand the importance of accurate BOM data or how it impacts various aspects of the organization.
8. Limited Training and Education: Inadequate training and education about BOM data and its significance can lead to misinterpretation and underutilization.
9. Lack of Collaboration: Insufficient collaboration between departments can hinder the identification and resolution of BOM-related issues.
10. Change Resistance: Employees may resist changes to BOM-related processes or systems, even if they are designed to improve efficiency.
11. Hierarchical Structures: Hierarchical organizational structures can impede cross-functional collaboration and hinder effective BOM management.
12. Data Culture: The overall organizational culture regarding data accuracy, sharing, and accountability can impact how BOM data is managed and utilized.
Mitigation Strategies:
- Cross-Functional Teams: Establish cross-functional teams to promote collaboration and communication between departments involved in BOM-related activities.
- Leadership Support: Obtain support from organizational leaders to promote a culture of collaboration, data accuracy, and change readiness.
- Clear Communication: Implement clear communication channels and protocols for sharing BOM data, updates, and changes.
- Change Management: Develop change management strategies that involve employees in the process of implementing new BOM-related practices.
- Training and Education: Provide comprehensive training and education to employees at all levels about the importance of BOM data and its impact.
- Standardized Processes: Implement standardized processes for creating, updating, and managing BOMs to ensure consistency and accuracy.
- Performance Metrics: Establish performance metrics and KPIs related to BOM accuracy, updates, and collaboration to drive accountability.
- Incentives: Introduce incentives or recognition programs to encourage collaboration, accurate data entry, and effective BOM management.
- Cross-Departmental Workshops: Organize workshops or training sessions that bring together employees from different departments to enhance mutual understanding and collaboration.
- Technology Adoption: Implement technology tools that facilitate cross-functional communication and collaboration, such as digital BOM management platforms.
In summary, addressing cultural and organizational challenges is essential for effectively utilizing multi-level BOMs.
By fostering a culture of collaboration, promoting clear communication, providing training, and aligning processes, organizations can overcome these challenges and create an environment where BOM data is accurately managed and leveraged for improved operational efficiency and decision-making.
Strategic Implications of Utilizing Multi-Level BOMs in Various Aspects of a Business
Utilizing Multi-Level Bills of Materials (BOMs) can have significant strategic implications across various aspects of a business. The effective implementation of multi-level BOMs can lead to improved operational efficiency, cost management, customer satisfaction, and overall competitiveness.
Here are the strategic implications of using multi-level BOMs in different areas of a business:
Product Development and Innovation
- Streamlined Design Processes: Multi-level BOMs provide a clear visualization of product structures, aiding in efficient design and reducing design iteration time.
- Rapid Prototyping: With accurate BOMs, prototypes can be developed more precisely, allowing for quicker testing and validation of new product concepts.
- Effective Collaboration: Multi-level BOMs facilitate cross-functional collaboration between design, engineering, and manufacturing teams, ensuring that innovative ideas translate into feasible and manufacturable products.
Manufacturing and Operations
- Optimized Production Planning: Multi-level BOMs guide production processes, reducing lead times, minimizing bottlenecks, and enhancing overall manufacturing efficiency.
- Lean Manufacturing: BOMs help identify opportunities for reducing waste, streamlining processes, and improving resource utilization, aligning with lean principles.
- Quality Control: Accurate BOMs ensure that the correct components are used, leading to improved product quality and reduced defects.
- Inventory Management: Multi-level BOMs support efficient inventory management, reducing excess stock, preventing shortages, and optimizing working capital.
Supply Chain Management
- Enhanced Supplier Collaboration: Multi-level BOMs facilitate effective communication with suppliers, improving procurement processes, lead times, and supply chain visibility.
- Demand Forecasting: BOMs provide insights into component demand, enabling more accurate demand forecasting and supply planning.
- Vendor Relationship Management: Multi-level BOMs contribute to stronger vendor relationships by ensuring clear expectations and specifications.
- Cost Management and Pricing:
- Accurate Cost Estimation: Multi-level BOMs enable precise cost estimation, allowing for better pricing strategies and cost control.
- Profit Margin Improvement: Accurate costing based on multi-level BOMs helps optimize profit margins by identifying cost-saving opportunities and avoiding underpricing.
Customer Satisfaction
- Product Customization: Multi-level BOMs support customization by ensuring that variants and options are properly integrated into the overall product structure.
- Service and Maintenance: Accurate multi-level BOMs aid in quick and accurate product servicing, minimizing downtime, and improving customer satisfaction.
Change Management and Continuous Improvement
- Efficient Design Changes: Multi-level BOMs streamline change management processes by illustrating how modifications impact different levels of assembly.
- Continuous Process Improvement: BOMs provide insights into production processes, allowing for continuous improvement initiatives to be targeted effectively.
Strategic Decision-Making
- Informed Business Strategies: Executives can make strategic decisions based on insights derived from multi-level BOMs, such as optimizing product designs, identifying new market opportunities, and evaluating cost structures.
Regulatory Compliance and Risk Mitigation
- Mitigation of Regulatory Risks: Multi-level BOMs ensure compliance with industry regulations and standards by providing accurate documentation of product components and materials.
In summary, the strategic implications of utilizing multi-level BOMs span across product development, manufacturing, supply chain management, cost control, customer satisfaction, and decision-making. Effective utilization of multi-level BOMs can drive operational excellence and contribute to the overall success and competitiveness of a business.
Best Options to Manage Multi-Level Bill of Materials
Managing Multi-Level Bills of Materials (BOMs) effectively requires the use of specialized tools and approaches to ensure accuracy, collaboration, and efficiency. Here are some of the best options for managing multi-level BOMs:
- Product Lifecycle Management (PLM) Software: PLM software provides end-to-end management of product data, including BOMs, design documentation, change management, and collaboration. It offers robust capabilities for managing complex BOMs throughout the product life cycle.
- Enterprise Resource Planning (ERP) Software: ERP systems integrate various business functions, including BOM management, procurement, inventory, manufacturing, and financials. They offer a holistic view of BOM-related activities and support efficient operations.
- Computer-Aided Design (CAD) Software: CAD tools are essential for creating and visualizing product designs, which can be linked to BOM data. Some advanced CAD systems offer integrated BOM management features.
- BOM Management Software: Specialized BOM management software focuses specifically on creating, editing, and collaborating on BOMs. These tools often integrate with other systems like PLM, ERP, and CAD.
- Cloud-Based Collaboration Platforms: Cloud platforms allow teams to collaborate on BOMs in real time, enabling cross-functional teams to work together, make updates, and track changes seamlessly.
- Spreadsheet Software: While less specialized, spreadsheet software like Microsoft Excel can be used for simpler BOM management. However, it may lack the advanced features and collaboration capabilities of dedicated tools.
- Integration with Supplier Portals: Integrating BOM data with supplier portals allows for seamless communication and collaboration on component sourcing, pricing, and availability.
- Version Control Systems: Implementing version control tools helps manage different versions of BOMs, especially when multiple teams are making changes simultaneously.
- Master Data Management (MDM) Systems: MDM systems ensure consistent and accurate BOM data across the organization by providing a single source of truth for data governance.
- Integrated Software Suites: Some software suites combine elements of PLM, ERP, and BOM management to provide comprehensive solutions for product and BOM lifecycle management.
When selecting the best option for managing multi-level BOMs, consider factors such as the complexity of your products, the size of your organization, collaboration needs, integration with existing systems, regulatory requirements, and budget constraints.
The chosen solution should align with your organization's goals and provide the necessary tools to streamline BOM management, improve data accuracy, enhance collaboration, and support informed decision-making across departments.
How Can Deskera Help You with a Multi-Level Bill of Materials?
Deskera MRP is an integrated software solution designed to help businesses manage their manufacturing processes, including multi-level bills of materials.
Here’s how Deskera can assist you with the multi-level bill of materials:
- Multi-Level BOM Creation and Management: Manage product structures with ease using the multi-level bill of materials. Assign multiple components to a single product. Identify components and subcomponents of each product, and easily track their usage, movement, and costs.
- Improve Productivity: Deskera will help you improve productivity because it facilitates the automatic generation of bills of materials, thereby helping to reach your production goals faster. It also automates the process of managing and maintaining multi-level bills of materials.
- Enhances Collaboration: By increasing the visibility and communication between the departments of your company, Deskera will help improve collaboration between different teams. In fact, it also allows multiple users to access and edit the bill of materials. All of this will also facilitate faster and more informed decision-making.
- Improve Inventory Costs: With Deskera, you will be able to improve your inventory costs as the accuracy of data with a single source of truth for the entire bill of materials is ensured. Through Deskera, all the required documents can be automatically generated from this single source of information. Lastly, through the automatic generation of a bill of materials, manual errors will be reduced.
- Reduce Production Costs: By streamlining the process of the bill of materials through Deskera, operation costs will be reduced. In fact, the time and resources spent on managing and updating complex bills of materials will also be reduced.
Key Takeaways
In the dynamic world of modern business, a thorough understanding of the Multi-Level Bill of Materials is a cornerstone of success. A Multi-Level BOM is a hierarchical representation of a product's components and subassemblies, showing how they are structured and assembled.
The key benefits of multi-level BOMs include:
- Comprehensive Product Understanding: Multi-level BOMs provide a detailed and hierarchical view of a product's components and sub-assemblies. This helps teams understand how each part contributes to the final product's structure and functionality.
- Efficient Production Planning: Multi-level BOMs guide the sequence of assembly operations, ensuring that components are available when needed. This streamlines production processes reduces downtime, and enhances overall manufacturing efficiency.
- Accurate Cost Estimation and Pricing: By accounting for all components and their associated costs, multi-level BOMs enable accurate cost estimation. This, in turn, supports informed pricing decisions and better profitability management.
- Effective Inventory Management: Multi-level BOMs assist in managing inventory levels by providing insights into the quantity and timing of component requirements. This prevents shortages, reduces excess stock, and minimizes holding costs.
- Quality Control and Consistency: Multi-level BOMs help maintain product quality by ensuring that the correct components and sub-assemblies are used in assembly. This reduces errors, and rework, and ensures consistency in the final product.
- Streamlined Supplier Collaboration: Multi-level BOMs facilitate effective communication with suppliers, enabling them to understand component requirements, specifications, and delivery schedules. This fosters better collaboration and reduces supply chain disruptions.
- Support for New Product Development: When introducing new products or variants, multi-level BOMs serve as a foundation for design, production planning, and sourcing, ensuring that all necessary components are accounted for.
- Enhanced Cross-Functional Collaboration: Multi-level BOMs promote better communication and collaboration between different departments, such as engineering, manufacturing, procurement, and sales. This alignment leads to smoother workflows and improved decision-making.
- Efficient Service and Maintenance: For products requiring maintenance or repairs, multi-level BOMs help technicians identify and replace the correct components, reducing downtime and improving customer satisfaction.
- Regulatory Compliance and Documentation: Multi-level BOMs serve as documentation for regulatory compliance, certifications, and audits. They provide a clear record of product components and their specifications.
- Improved Change Management: When design changes are necessary, multi-level BOMs help manage the impact of modifications across different levels of assembly, ensuring that the entire product structure is updated correctly.
- Strategic Decision-Making: Executives can make informed strategic decisions based on insights derived from multi-level BOMs, such as optimizing product designs, identifying cost-saving opportunities, and aligning production with business goals.
In summary, multi-level BOMs offer a holistic perspective on product composition, support efficient operations, enable accurate cost management, and enhance collaboration across departments. These benefits collectively contribute to improved product quality, reduced costs, and increased competitiveness in the marketplace.
Some of the challenges of multi-level BOMs include:
- Data Accuracy and Maintenance: Keeping the BOM data accurate and up-to-date can be challenging, especially in environments where frequent design changes, part substitutions, or updates occur. Inaccurate or outdated BOMs can lead to production errors and quality issues.
- Complexity Management: Multi-level BOMs can become incredibly complex, especially for products with numerous components, sub-assemblies, and variants. Managing and visualizing the intricate relationships between levels can be daunting.
- Version Control and Change Management: Ensuring that the correct version of the BOM is being used across departments and throughout the product lifecycle is essential. Design changes and updates must be carefully managed to avoid confusion and errors.
- Software Integration: Implementing and integrating specialized software for managing multi-level BOMs may require significant effort and resources. Ensuring seamless integration with other enterprise systems, such as ERP and PLM systems, can be challenging.
- Cross-Departmental Communication: Effective collaboration between different departments, such as design, engineering, manufacturing, and procurement, is crucial. Miscommunication or lack of alignment can result in incorrect BOMs being used in different processes.
- Supplier Collaboration: Coordinating with suppliers to ensure accurate and timely delivery of components can be challenging. Miscommunication or delays in the supply chain can disrupt production schedules.
- Complex Procurement and Sourcing: Multi-level BOMs can involve components from various suppliers. Managing procurement and sourcing for these components, while ensuring quality and timely delivery, can be complex.
- Training and Education: Ensuring that employees across different departments understand how to create, interpret, and utilize multi-level BOMs effectively requires proper training and education.
- Maintenance and Updates: As products evolve and undergo changes, updating the multi-level BOMs accordingly can be time-consuming and error-prone. Failure to update BOMs can lead to discrepancies and inefficiencies.
- Customization and Variability: Products with numerous options, variants, or configurations can complicate the creation and management of multi-level BOMs, as different combinations must be accurately represented.
- Regulatory Compliance: Ensuring that multi-level BOMs comply with industry regulations, certifications, and standards requires attention to detail and thorough documentation.
- Cultural and Organizational Challenges: Cultural resistance to change, lack of buy-in from stakeholders, and resistance to new processes can hinder the successful implementation and adoption of multi-level BOMs.
Despite these challenges, organizations can mitigate them through proper planning, process improvements, dedicated resources, training, and the use of specialized software tools designed to manage multi-level BOMs. Overcoming these challenges can lead to improved operational efficiency, better collaboration, and enhanced decision-making throughout the product lifecycle.
Overall, Deskera MRP will serve as a comprehensive solution for managing multi-level bills of materials. It will help streamline your bill of materials, automate production processes, track production costs, monitor supplier performance, improve supply chain management, streamline production planning, reduce inventory errors, optimize production scheduling, track production costs, and help you maximize efficiency with the multi-level bill of materials.
Related Articles
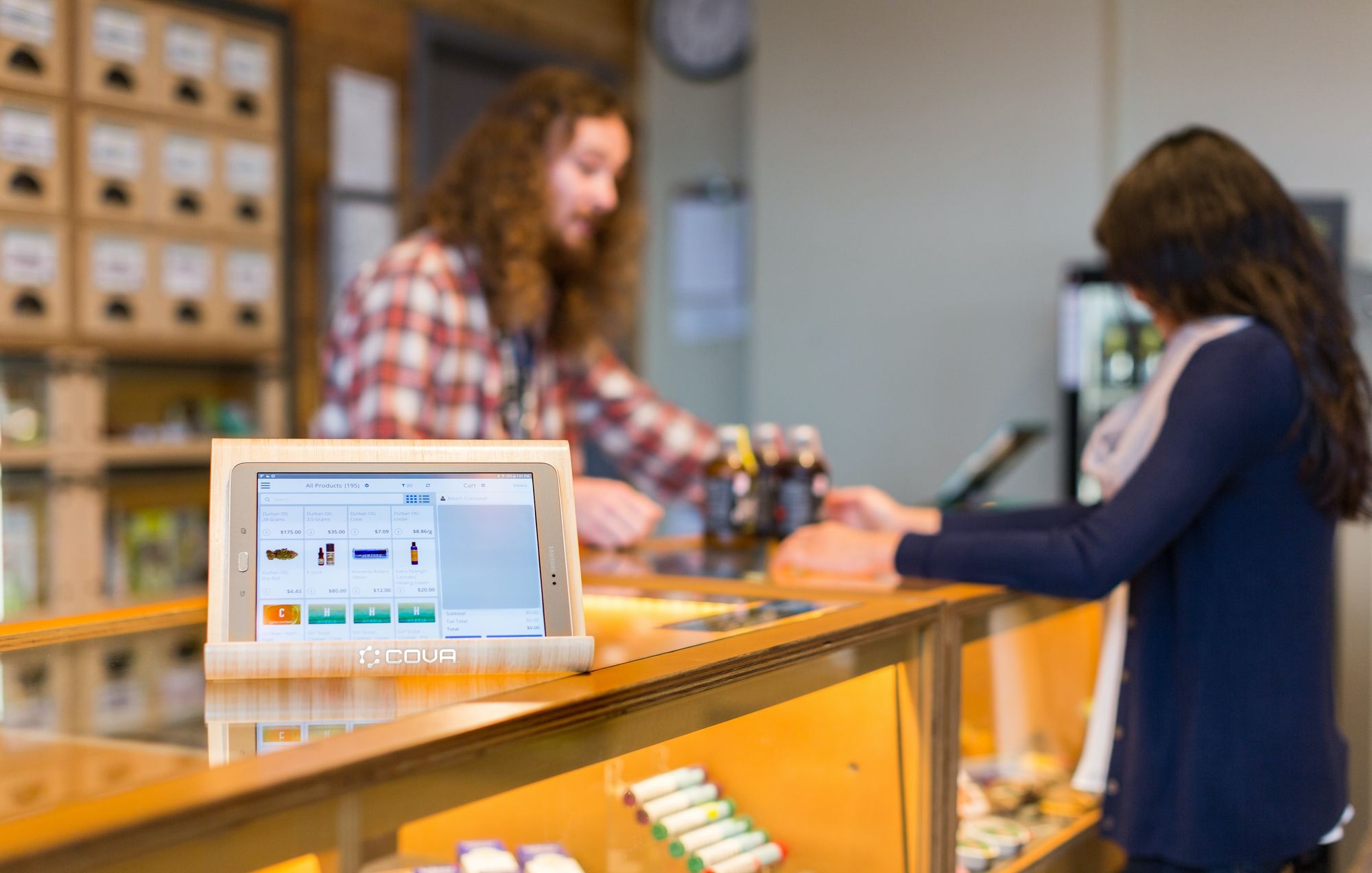
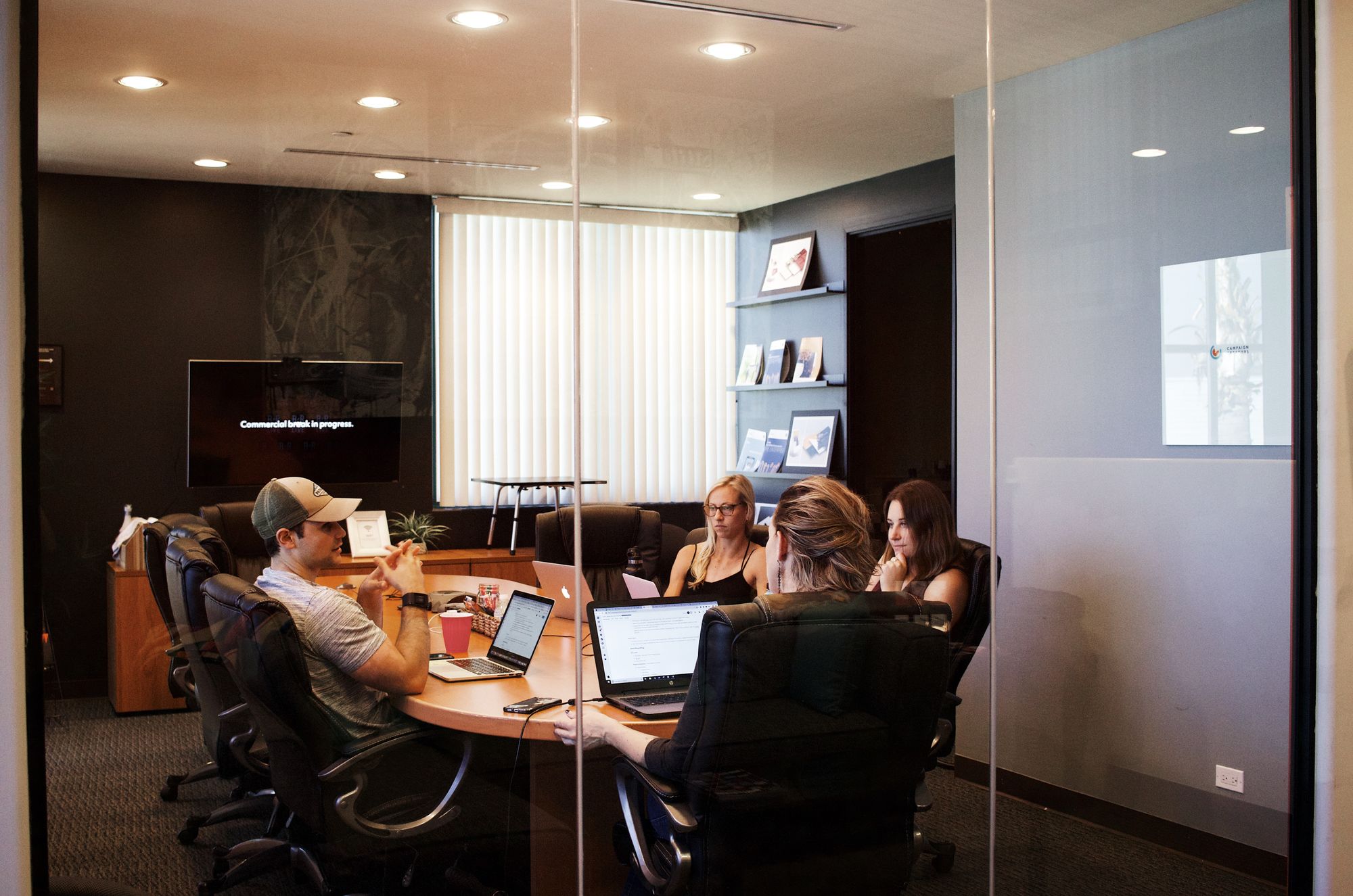
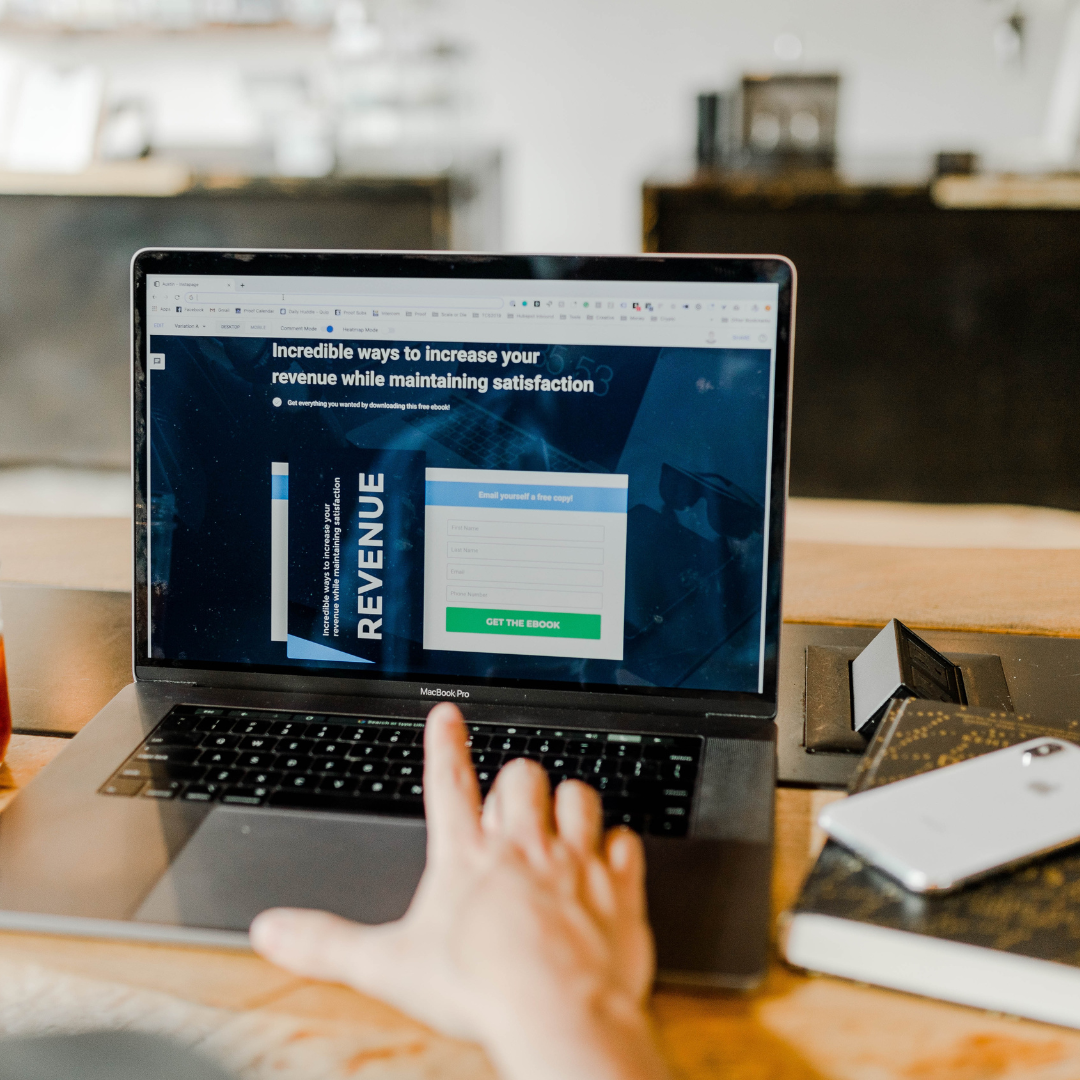
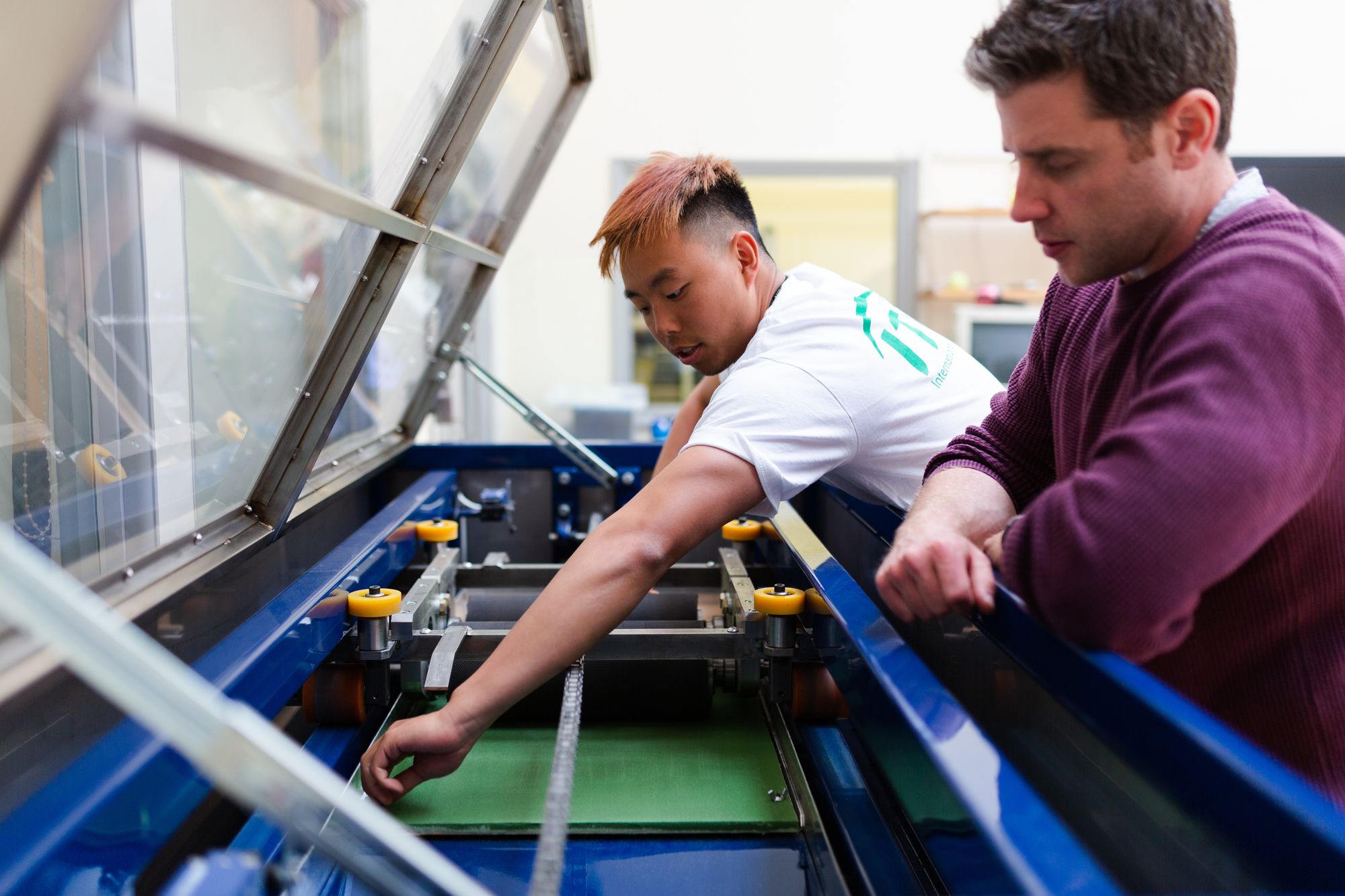
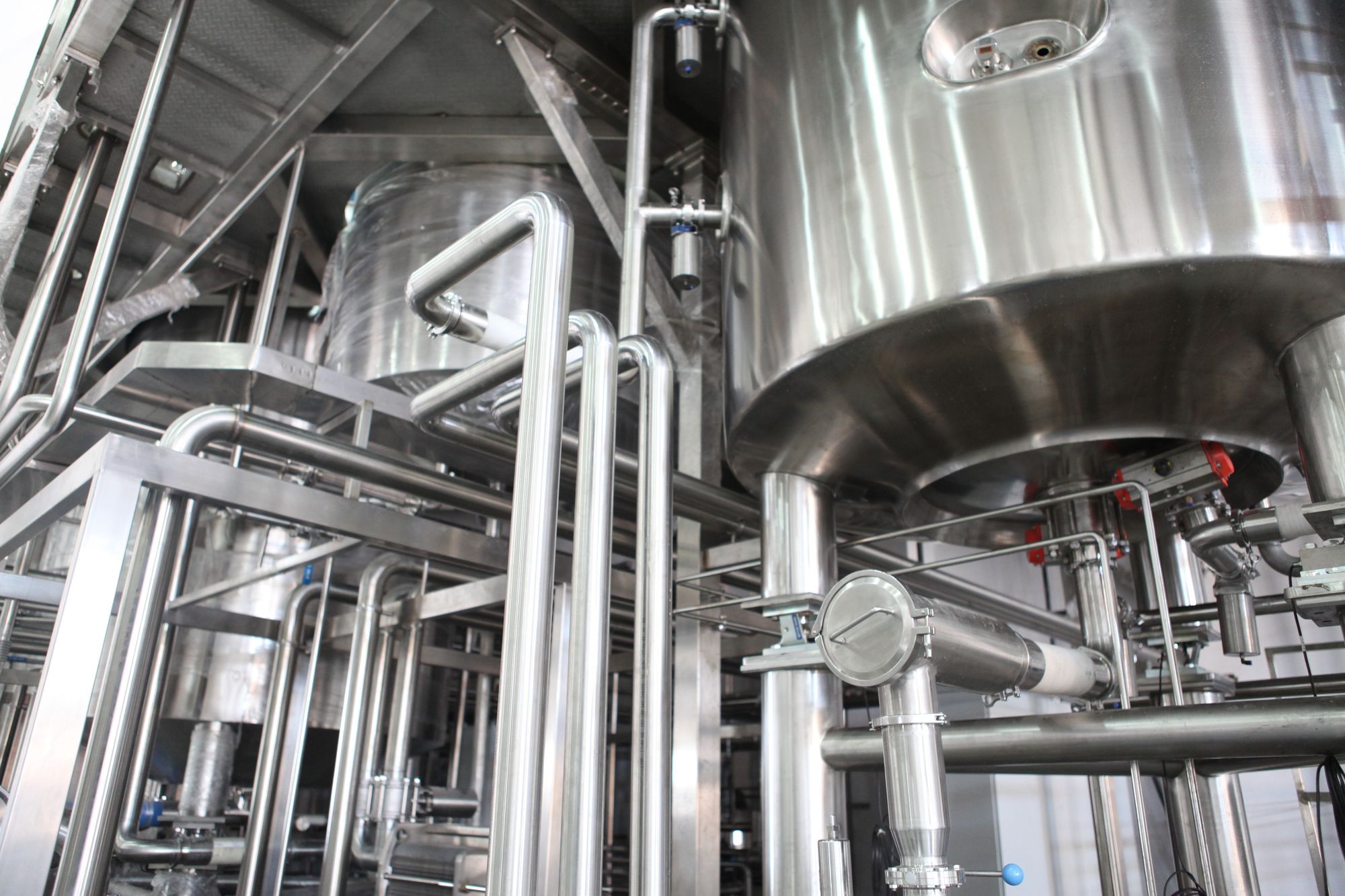