Bottlenecks can result in an average productivity loss of 20-30% in manufacturing operations. (Source: McKinsey & Company)
In the dynamic world of manufacturing and production, efficient scheduling is key to meeting customer demands, maximizing productivity, and staying competitive.
However, the complexity of production systems often gives rise to bottlenecks—constraints that limit the overall flow and efficiency of the process. These bottlenecks can hinder the smooth operation of the entire production system and lead to delays, increased costs, and missed opportunities.
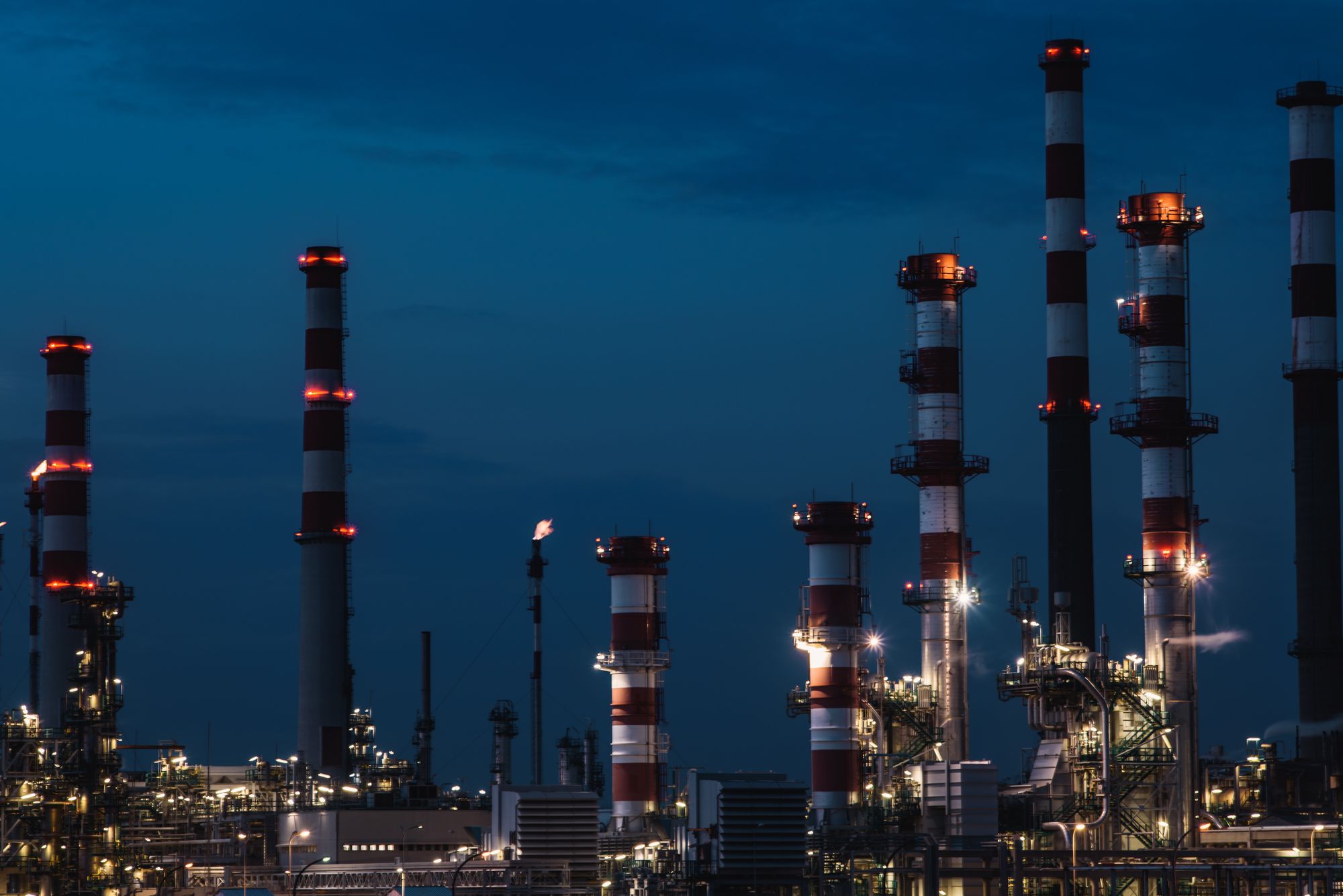
Bottleneck analysis is a critical tool in tackling these challenges. It involves systematically identifying, measuring, analyzing, and optimizing the bottlenecks within the production scheduling process.
By understanding and addressing these constraints, organizations can enhance their production efficiency, optimize resource allocation, reduce lead times, and improve customer satisfaction.
This crucial aspect of production scheduling requires a structured approach and careful analysis of various factors, such as process flow, resource utilization, capacity limitations, and dependencies.
Bottleneck analysis helps organizations gain valuable insights into areas where the production process is slowed down or resource constraints occur, allowing for targeted interventions and process improvements.
In this article, we will explore the importance of bottleneck analysis in effective production scheduling. The topics covered in this article are:
- What is Production Scheduling?
- What is a Bottleneck Analysis?
- Importance of Effective Production Scheduling
- Importance of Bottleneck Analysis
- Why is Bottleneck Analysis Important in Production Scheduling?
- Bottleneck Analysis: A Crucial Part of Effective Production Scheduling
- What are Some Common Causes of Bottlenecks in Production Scheduling?
- What Metrics are Used to Measure Bottlenecks in Production Scheduling?
- How can Bottlenecks be Addressed in Production Scheduling?
- How Often Should Bottleneck Analysis Be Performed in Production Scheduling?
- Can Bottleneck Analysis be Applied to Service-Based Industries?
- How can Bottleneck Analysis Help with Capacity Planning?
- What is the Relationship Between Bottlenecks and Lead Times in Production Scheduling?
- How Does Bottleneck Analysis Contribute to Lean Manufacturing Principles?
- Can Bottleneck Analysis be Applied to a Single Workstation or Process within a Production System?
- Is Bottleneck Analysis a One-Time Activity or an Ongoing Process?
- How Can Deskera Help You with Production Scheduling?
- Key Takeaways
- Related Articles
What is Production Scheduling?
Production scheduling is the process of planning and organizing production activities within a manufacturing or production facility. It involves determining the sequence, timing, and resources required to complete various tasks and activities involved in the production process.
The main objective of production scheduling is to optimize the utilization of resources, minimize costs, and meet customer demand within specified timeframes. It involves making decisions regarding which orders to prioritize, how to allocate resources such as labor, machines, and materials, and how to sequence the tasks and activities to ensure smooth and efficient production flow.
Production scheduling takes into account various factors such as available capacity, production rates, material availability, machine downtime, and order priorities. It considers the dependencies and constraints between different tasks and activities to create an achievable and realistic production plan.
By creating an effective production schedule, companies can improve efficiency, reduce lead times, minimize inventory levels, and enhance overall productivity. It helps in optimizing resource allocation, identifying potential bottlenecks, and ensuring timely delivery of products to customers.
Production scheduling can be done using various techniques and tools, ranging from manual methods like spreadsheets and whiteboards to advanced software systems that use algorithms and optimization techniques to create optimal schedules based on predefined criteria and objectives.
What is a Bottleneck Analysis?
Bottleneck analysis is a systematic process of identifying and analyzing the constraints or bottlenecks that limit the overall performance or throughput of a system, process, or operation. It involves identifying the specific resource, activity, or step that is causing a slowdown or hindrance to the smooth flow of work.
The purpose of bottleneck analysis is to understand and address the factors that impede efficiency, productivity, and overall system performance. By identifying and resolving bottlenecks, organizations can optimize their operations, improve throughput, reduce delays, and enhance overall effectiveness.
Here's an overview of the key aspects of bottleneck analysis:
- Identification: The first step in bottleneck analysis is identifying the bottleneck. This involves observing the flow of work, analyzing performance data, or conducting time studies to pinpoint the specific area or resource that is causing a constraint or slowdown.
- Measurement: Once the bottleneck is identified, measurement is done to understand its impact on the system. This includes gathering data on the capacity, cycle time, utilization, and efficiency of the bottlenecked resource or process.
- Analysis: Analyzing the bottleneck involves identifying root causes, examining process flow, evaluating constraints and dependencies, and considering the workload balance. This analysis provides insights into the factors contributing to the bottleneck and helps in formulating effective solutions.
- Solutions and Optimization: Based on the analysis, targeted interventions and optimization strategies are developed to alleviate the bottleneck. This may involve process redesign, resource reallocation, technology upgrades, or other approaches to increase capacity, improve efficiency, or streamline operations.
- Implementation and Monitoring: The solutions identified in step 4 are implemented, and their effectiveness is closely monitored. Ongoing monitoring, data collection, and feedback help assess the impact of the interventions and make necessary adjustments to ensure sustained improvements.
- Continuous Improvement: Bottleneck analysis is an iterative process, and continuous improvement is essential. Regular reviews, data analysis, and feedback from stakeholders help identify new bottlenecks, optimize processes, and drive ongoing enhancements.
Bottleneck analysis can be facilitated using various techniques and tools, ranging from manual methods like observation and data collection to advanced software systems that utilize algorithms and optimization techniques to support decision-making. The specific approach and tools used depend on the complexity and nature of the system being analyzed.
Bottleneck analysis is not a one-time event but rather an iterative process. As one bottleneck is resolved, new ones may arise due to changing circumstances or system dynamics. Therefore, continuous improvement efforts and regular bottleneck analysis are essential to maintain optimal performance.
Overall, bottleneck analysis enables organizations to identify the areas that hinder efficiency and productivity, make informed decisions for improvement, and optimize their operations for maximum output and performance.
Importance of Effective Production Scheduling
Effective production scheduling is of paramount importance for organizations across various industries. Here are some key reasons highlighting its significance:
- Optimal Resource Utilization: Production scheduling ensures that resources such as labor, machinery, materials, and time are utilized efficiently. By effectively allocating and coordinating resources, organizations can minimize idle time, reduce costs, and maximize productivity.
- Meeting Customer Demand: A well-executed production schedule enables organizations to meet customer demand effectively. By aligning production with customer orders, organizations can ensure timely delivery, improve customer satisfaction, and maintain strong relationships with customers.
- Reduced Lead Times: Efficient production scheduling helps in minimizing lead times, which is the time taken from receiving an order to delivering the finished product. Reduced lead times enable organizations to respond quickly to customer requirements, fulfill orders faster, and gain a competitive edge in the market.
- Effective Capacity Planning: Production scheduling involves careful capacity planning, ensuring that production resources are optimized to meet demand. By accurately estimating capacity requirements, organizations can avoid underutilization or overburdening of resources, leading to smoother operations and improved efficiency.
- Inventory Management: Effective production scheduling helps in managing inventory levels and optimizing inventory turnover. By synchronizing production with demand, organizations can avoid excessive inventory buildup or stockouts, minimize carrying costs, and maintain a lean and efficient supply chain.
- Cost Reduction: An optimized production schedule helps in reducing costs associated with overtime, setup times, inventory holding, and other inefficiencies. By streamlining production processes, eliminating bottlenecks, and improving resource utilization, organizations can achieve cost savings and enhance profitability.
- Enhanced Flexibility and Responsiveness: Effective production scheduling enables organizations to be more flexible and responsive to changes in customer demands, market conditions, or unforeseen events. It allows for efficient rescheduling, quick adjustments to production plans, and better adaptability to changing circumstances.
- Improved Production Planning: Production scheduling provides a structured approach to planning and sequencing production activities. It enables organizations to create realistic and achievable schedules, optimize production sequences, and ensure smooth workflow throughout the production process.
- Better Decision-Making: With accurate and up-to-date production scheduling information, organizations can make informed decisions regarding resource allocation, capacity expansion, order prioritization, and production sequencing. This leads to improved decision-making, optimized operations, and better overall business performance.
- Continuous Improvement: Effective production scheduling establishes a foundation for continuous improvement initiatives. By analyzing performance metrics, identifying bottlenecks, and implementing optimization strategies, organizations can drive ongoing process enhancements, increase efficiency, and maintain a competitive advantage.
In summary, effective production scheduling plays a crucial role in optimizing resources, meeting customer demand, reducing lead times, managing costs, enhancing flexibility, and driving continuous improvement. It enables organizations to streamline operations, improve productivity, and achieve operational excellence.
Importance of Bottleneck Analysis
Bottleneck analysis holds significant importance for organizations across various industries. Here are key reasons highlighting its significance:
- Efficiency and Throughput Improvement: Bottleneck analysis helps identify and address the constraints that limit the overall efficiency and throughput of a system or process. By focusing on the bottlenecks, organizations can optimize resource allocation, streamline operations, and enhance productivity.
- Resource Optimization: Bottleneck analysis enables organizations to identify underutilized resources and allocate them more effectively. By balancing workloads and addressing constraints, organizations can ensure that resources are utilized efficiently, reducing idle time and maximizing productivity.
- Timely Delivery and Customer Satisfaction: Bottlenecks can cause delays in production and impact delivery timelines. By analyzing and resolving bottlenecks, organizations can ensure the timely delivery of products or services, enhancing customer satisfaction and maintaining strong customer relationships.
- Cost Reduction: Bottlenecks often result in inefficiencies, such as increased inventory, overtime expenses, or missed opportunities for cost savings. By addressing bottlenecks, organizations can streamline processes, reduce wastage, minimize downtime, and optimize costs.
- Process Optimization: Bottleneck analysis provides insights into the overall flow of work and dependencies within a system. By identifying and addressing bottlenecks, organizations can optimize process flow, eliminate non-value-added activities, and improve overall process efficiency.
- Improved Decision-Making: Bottleneck analysis helps organizations make data-driven decisions by providing quantitative insights into the performance of critical resources or processes. This enables informed decision-making in areas such as capacity planning, resource allocation, and process improvement.
- Risk Management: Bottlenecks can create risks and vulnerabilities within a system. By proactively identifying and addressing bottlenecks, organizations can mitigate potential risks, prevent production delays, and enhance overall system reliability.
- Continuous Improvement: Bottleneck analysis fosters a culture of continuous improvement by systematically identifying and resolving constraints. It encourages organizations to regularly assess performance, collect data, and make ongoing improvements to enhance efficiency and productivity.
- Scalability and Growth: By addressing bottlenecks, organizations can enhance their ability to scale operations and accommodate increased demand. Optimizing processes and resources allows for smoother expansion, improved scalability, and better preparedness for future growth.
- Competitive Advantage: Effective bottleneck analysis provides organizations with a competitive edge. By continuously improving efficiency, reducing lead times, and enhancing productivity, organizations can deliver products or services faster and more effectively than their competitors.
In summary, bottleneck analysis plays a vital role in enhancing efficiency, optimizing resources, improving customer satisfaction, reducing costs, enabling process optimization, supporting decision-making, promoting continuous improvement, and providing a competitive advantage. It helps organizations unlock their full potential and achieve operational excellence in a dynamic business environment.
Why is Bottleneck Analysis Important in Production Scheduling?
Bottleneck analysis is important in production scheduling for several reasons:
- Efficiency Improvement: Bottleneck analysis helps identify constraints or bottlenecks within the production system that limit efficiency. By addressing these bottlenecks, organizations can optimize resource allocation, streamline processes, and improve overall productivity.
- Timely Delivery: Bottlenecks can cause delays in production, leading to late deliveries and customer dissatisfaction. By analyzing and resolving bottlenecks, organizations can ensure the timely delivery of products or services, enhancing customer satisfaction and maintaining strong customer relationships.
- Resource Utilization: Effective bottleneck analysis enables organizations to optimize the utilization of their resources, such as labor, machinery, and materials. By identifying and addressing bottlenecks, organizations can ensure that resources are allocated efficiently, minimizing idle time and maximizing productivity.
- Cost Reduction: Bottlenecks often lead to inefficiencies and additional costs. By addressing bottlenecks, organizations can streamline processes, reduce waste, minimize downtime, and optimize costs. This can result in significant cost savings and improved profitability.
- Process Optimization: Bottleneck analysis provides insights into the flow of work and dependencies within the production system. By identifying and addressing bottlenecks, organizations can optimize process flow, eliminate non-value-added activities, and improve overall process efficiency.
- Effective Decision-Making: Bottleneck analysis provides organizations with valuable data and insights to make informed decisions. It helps in resource allocation, capacity planning, order prioritization, and process improvement. Effective decision-making based on bottleneck analysis can lead to improved efficiency and better outcomes.
- Continuous Improvement: Bottleneck analysis fosters a culture of continuous improvement. By regularly evaluating and addressing bottlenecks, organizations can drive ongoing enhancements, optimize processes, and stay competitive in a dynamic business environment.
Overall, bottleneck analysis in production scheduling is important as it enables organizations to identify and resolve constraints, optimize resource allocation, streamline operations, reduce costs, improve customer satisfaction, and drive continuous improvement. It plays a crucial role in achieving operational excellence and maintaining a competitive edge in the market.
Bottleneck Analysis: A Crucial Part of Effective Production Scheduling
Bottleneck analysis in production scheduling is a systematic approach to identifying and addressing constraints or bottlenecks that limit the overall efficiency and throughput of a production system. It involves analyzing the flow of work, measuring performance metrics, and developing strategies to optimize resource allocation and process flow.
In production scheduling, a bottleneck refers to a resource, workstation, or process within the production system that has a lower capacity or slower performance compared to other areas. Bottlenecks restrict the overall output and efficiency of the system, causing delays and affecting the ability to meet customer demand.
Bottleneck analysis helps organizations identify these constraints and understand their impact on the production schedule. It involves identifying the bottleneck, measuring its performance, analyzing the root causes and dependencies, and developing targeted solutions to alleviate the bottleneck.
The goal of bottleneck analysis in production scheduling is to optimize the flow of work, balance workloads, maximize resource utilization, minimize delays, and improve overall productivity. By addressing bottlenecks, organizations can enhance the efficiency and effectiveness of their production scheduling process, leading to timely delivery, cost reduction, improved customer satisfaction, and better utilization of resources.
Here are a few key points about bottleneck analysis in production scheduling:
Identification
In the context of production scheduling, identification is a critical step in bottleneck analysis. It involves identifying the specific areas, resources, or processes that act as constraints and limit the overall production capacity or efficiency.
Here's a more detailed explanation of the identification phase in bottleneck analysis for production scheduling:
- Observing the Flow: Observing the flow of work within the production system is essential for identifying bottlenecks. This involves tracking the movement of materials, the sequence of tasks, and the interactions between different stages of the production process. By closely observing the flow, it becomes possible to identify areas where work is slowing down, queues are forming, or bottlenecks are becoming apparent.
- Analyzing Performance Data: Analyzing performance data provides insights into the performance of different resources, workstations, or processes within the production system. This includes metrics such as cycle times, throughput rates, work-in-progress inventory levels, and utilization rates. By comparing these metrics across different areas, it becomes possible to identify areas that are consistently underperforming or creating bottlenecks.
- Using Value Stream Mapping: Value stream mapping is a powerful tool for visualizing the entire production process from start to finish. It helps identify areas of waste, non-value-added activities, and bottlenecks. By creating a visual representation of the value stream, organizations can easily identify areas where work is piling up or where there are imbalances in the flow.
- Seeking Input from Employees: Gathering input from employees who are directly involved in the production process can provide valuable insights. They often have firsthand knowledge of areas where bottlenecks occur, inefficiencies exist, or resource constraints hinder production. Involving employees in the identification process can lead to more accurate and comprehensive bottleneck identification.
- Analyzing Historical Data: Historical production data, including records of past orders, lead times, and performance metrics, can be analyzed to identify recurring patterns and bottlenecks. This analysis helps identify specific areas or resources that consistently contribute to production delays or inefficiencies.
- Performance Variation Analysis: Analyze variations in performance metrics across different resources, workstations, or processes. Look for significant deviations or outliers that indicate areas of a potential bottleneck. These variations can point to specific resources or processes that consistently struggle to meet desired output levels.
- Considering Constraints and Dependencies: Bottlenecks can be influenced by constraints and dependencies within the production system. For example, the limited availability of raw materials, machine capacities, or specialized labor can create bottlenecks. Analyzing these constraints and dependencies helps identify areas where additional resources may be needed or where process redesign may be necessary to alleviate the bottlenecks.
By combining these methods and techniques, organizations can effectively identify the specific areas, resources, or processes that act as bottlenecks within their production scheduling. This identification lays the foundation for further analysis and optimization efforts to improve overall production efficiency and throughput.
Measurement
In production scheduling, the measurement phase of bottleneck analysis involves quantifying and collecting data related to the identified bottlenecks. This step aims to gather information about the capacity, cycle time, utilization, and efficiency of the bottlenecked resources or processes.
Here's a more detailed explanation of the measurement phase in bottleneck analysis for production scheduling:
- Capacity Measurement: Capacity measurement involves determining the maximum output or workload that the bottlenecked resource or process can handle within a given time frame. It provides a baseline for understanding the potential capacity of the bottleneck and its limitations. Capacity can be measured in units produced, tasks completed, or services delivered.
- Cycle Time Analysis: Cycle time analysis focuses on measuring the time it takes to complete one unit of work or to pass through the bottleneck. This metric helps in understanding the rate at which work can flow through the constrained area. Measuring cycle time provides insights into the speed and efficiency of the bottlenecked process.
- Utilization Assessment: Utilization assessment involves calculating the utilization rate of the bottlenecked resource or process. Utilization refers to the ratio of the actual time the resource is being used to the total available time. It indicates how intensively the bottlenecked resource or process is being utilized. High utilization may suggest that the resource is heavily loaded, potentially causing delays or congestion.
- Efficiency Evaluation: Efficiency evaluation focuses on assessing the efficiency of the bottlenecked resource or process. It involves comparing the actual output achieved by the bottleneck with the expected or optimal output. Efficiency measures how well the bottlenecked resource or process performs relative to its maximum potential. Low efficiency can indicate inefficiencies or performance gaps that need to be addressed.
- Quality Consideration: The measurement phase also includes evaluating the quality levels and defect rates associated with the bottlenecked resource or process. Poor quality can result in rework, scrap, or delays, further exacerbating the bottleneck. Assessing quality issues and defect rates helps identify opportunities for improvement and their impact on the overall performance of the bottleneck.
To perform these measurements effectively, organizations may need to collect data over a specific time period, track performance metrics in real time, or use appropriate tools and techniques. Regular monitoring and updating of these measurements are essential to track the performance of the bottleneck and assess the effectiveness of any implemented improvements.
The data collected during the measurement phase provides quantitative insights into the performance and capabilities of the bottlenecked resources or processes. These measurements serve as a basis for analysis and decision-making in subsequent steps of bottleneck analysis, enabling organizations to make informed choices to optimize their production scheduling.
Optimization
In production scheduling, the optimization phase of bottleneck analysis focuses on developing strategies and interventions to improve the performance and efficiency of the identified bottlenecks. This step aims to address the root causes, constraints, and dependencies that contribute to the bottlenecks, ultimately leading to a more optimized production scheduling process.
Here's a more detailed explanation of the optimization phase in bottleneck analysis for production scheduling:
- Process Redesign: Consider redesigning the production process to minimize or eliminate the bottlenecks. This may involve resequencing tasks, adjusting workstations, or reconfiguring the flow of materials to improve efficiency and reduce congestion. By optimizing the process design, it is possible to reduce the impact of the bottlenecks on the overall production schedule.
- Resource Reallocation: Evaluate the allocation of resources within the system to balance the workload and optimize performance. This can include redistributing tasks, cross-training employees to handle multiple roles, or adjusting shift schedules to maximize the utilization of resources. Proper resource allocation helps ensure that the bottlenecks are adequately supported and that there are no unnecessary idle times or overburdened resources.
- Technology Upgrades: Explore the adoption of advanced technologies or automation to improve the efficiency of the bottlenecked resources or processes. This may involve implementing new machinery, upgrading software systems, or leveraging data analytics to optimize scheduling and resource allocation. Technology upgrades can enhance productivity, reduce cycle times, and alleviate bottlenecks.
- Inventory Management: Optimize inventory management practices to reduce bottlenecks caused by material shortages or delays. This may include implementing just-in-time (JIT) inventory systems, establishing better communication channels with suppliers, or improving forecasting and demand planning to ensure the availability of materials when needed. Effective inventory management helps minimize disruptions and enhances the smooth flow of work.
- Constraint Mitigation: Develop strategies to manage and mitigate constraints that impact the bottlenecked resources or processes. This can involve implementing preventive maintenance programs, conducting capacity planning, or collaborating with suppliers to address constraints such as the limited availability of critical components or equipment. By proactively managing constraints, organizations can reduce the likelihood and impact of bottlenecks.
- Continuous Improvement: Foster a culture of continuous improvement to sustain optimization efforts and address emerging bottlenecks. Regularly review performance data, gather feedback from employees, and engage in ongoing process improvement initiatives. Continuous improvement helps identify new opportunities, optimize scheduling practices, and further enhance the production scheduling process.
Throughout the optimization phase, it is crucial to monitor the performance of the implemented interventions, collect relevant data, and evaluate their impact on the overall system performance. This allows organizations to make data-driven decisions, identify areas for further improvement, and ensure that the production scheduling process continues to be optimized over time.
By implementing optimization strategies tailored to the specific characteristics and constraints of the bottlenecks, organizations can enhance the efficiency, productivity, and overall performance of their production scheduling process.
Constraints and Dependencies
In production scheduling, understanding the constraints and dependencies associated with bottlenecks is crucial in bottleneck analysis. Constraints refer to any factors or limitations that hinder the smooth operation or optimization of the bottlenecked resources or processes.
Dependencies, on the other hand, are the relationships and interactions between different tasks, resources, or processes that influence the performance of the bottleneck.
Here's a more detailed explanation of constraints and dependencies in bottleneck analysis for production scheduling:
- Resource Constraints: Identify any constraints related to resources that affect the performance of the bottleneck. This may include limited availability of skilled labor, machinery, or equipment. Analyzing resource constraints helps determine if additional resources are required, whether it's through hiring, training, or investment in new equipment.
- Capacity Constraints: Assess any capacity constraints that limit the output or processing capability of the bottlenecked resources or processes. This can include limitations on the maximum number of units produced, tasks completed, or services delivered within a given timeframe. Identifying capacity constraints helps determine if additional resources, shifts, or process redesign is needed to increase the capacity.
- Material Constraints: Consider any constraints related to the availability or flow of materials required by the bottlenecked resources or processes. Material shortages or delays can significantly impact the performance of the bottleneck. Addressing material constraints involves effective inventory management, establishing better communication with suppliers, or exploring alternative sourcing options.
- Workload Dependencies: Analyze the dependencies and relationships between different tasks, resources, or processes that interact with the bottleneck. This includes understanding the sequence of operations, handoffs, and interdependencies within the production scheduling process. By identifying workload dependencies, organizations can ensure that the flow of work is properly coordinated to minimize disruptions and optimize the performance of the bottleneck.
- Lead Time Dependencies: Consider the dependencies on lead times, which are the time intervals required to complete specific activities or receive materials or information. Longer lead times can result in delays and impact the overall performance of the bottlenecked resources or processes. Analyzing lead time dependencies helps identify areas where lead times can be reduced, such as streamlining communication or implementing faster information exchange methods.
- External Dependencies: Assess any external dependencies that influence the performance of the bottlenecked resources or processes. This includes factors beyond the organization's control, such as regulatory requirements, customer demands, or supplier performance. Understanding these external dependencies helps organizations anticipate potential bottlenecks and proactively manage them.
By analyzing constraints and dependencies, organizations gain a comprehensive understanding of the factors that contribute to bottlenecks within their production scheduling process.
This understanding allows them to develop effective strategies for managing and mitigating these constraints, optimizing resource allocation, and coordinating tasks to ensure smooth and efficient operations.
It also helps in identifying opportunities for process improvements and making informed decisions to enhance the overall performance of the production scheduling process.
Continuous Improvement
Continuous improvement is a crucial aspect of bottleneck analysis in production scheduling. It involves an ongoing effort to identify, address, and optimize bottlenecks in order to improve the overall performance and efficiency of the production scheduling process.
Here's a more detailed explanation of continuous improvement in bottleneck analysis for production scheduling:
- Performance Monitoring: Continuously monitor the performance of the production scheduling process, including the identified bottlenecks. Regularly collect relevant data and track key performance indicators (KPIs) such as cycle time, throughput, resource utilization, and customer satisfaction. This monitoring provides insights into the effectiveness of implemented solutions and helps identify areas for further improvement.
- Data Analysis: Analyze the data collected during performance monitoring to identify patterns, trends, and potential root causes of bottlenecks. Utilize statistical analysis, process mapping, or data visualization techniques to gain insights into the underlying factors impacting the bottlenecks. This analysis helps in identifying areas where further optimization is needed.
- Feedback and Input: Seek feedback and input from employees, supervisors, and other stakeholders involved in the production scheduling process. They often have valuable insights based on their day-to-day experiences and can provide suggestions for process improvements. Encourage an open feedback culture and consider incorporating their suggestions into the continuous improvement efforts.
- Root Cause Analysis: Conduct root cause analysis to identify the underlying causes of bottlenecks. This involves investigating the factors contributing to the bottlenecks, understanding the dependencies and interactions within the system, and assessing any process inefficiencies or constraints. By addressing the root causes, organizations can implement more effective solutions and prevent bottlenecks from recurring.
- Lean and Six Sigma Techniques: Utilize Lean and Six Sigma methodologies to drive continuous improvement. Lean principles focus on eliminating waste, optimizing flow, and improving process efficiency. Six Sigma techniques aim to reduce process variations and defects. These methodologies provide structured frameworks and tools to systematically identify and address bottlenecks, leading to sustained process improvement.
- Kaizen Events: Conduct Kaizen events or improvement workshops focused on bottleneck analysis and process optimization. These events bring together cross-functional teams to identify and implement improvements. By fostering collaboration, brainstorming, and problem-solving, Kaizen events enable rapid and targeted improvements in the production scheduling process.
- Regular Reviews and Adjustments: Schedule regular reviews and evaluations of the production scheduling process to assess the effectiveness of implemented improvements and identify new bottlenecks. Continuously adjust and refine the solutions and optimization strategies based on feedback, performance data, and changing business needs. This ensures that the continuous improvement efforts remain aligned with organizational goals and evolving requirements.
By embracing continuous improvement, organizations can create a culture of ongoing learning, innovation, and optimization. This iterative process allows for the identification and resolution of bottlenecks, leading to improved efficiency, increased productivity, and better overall performance in production scheduling.
What are Some Common Causes of Bottlenecks in Production Scheduling?
Bottlenecks in production scheduling can be caused by various factors. Here are some common causes of bottlenecks:
- Limited Resource Capacity: Insufficient capacity or availability of key resources such as labor, machinery, or equipment can create bottlenecks. If the demand exceeds the capacity of a particular resource, it can slow down the entire production process.
- Imbalanced Workloads: Unequal distribution of workloads among resources or workstations can lead to bottlenecks. If certain resources are overloaded while others are underutilized, it can create imbalances that hinder the flow of work and cause delays.
- Material Shortages: Delays or shortages in the availability of raw materials or components can create bottlenecks. When production relies on timely material deliveries, any disruptions in the supply chain can lead to production delays and bottlenecks.
- Equipment Breakdowns: Unexpected breakdowns or maintenance requirements of critical equipment can cause bottlenecks. If a key piece of equipment fails or requires repair, it can halt the production process and impact the overall efficiency.
- Inefficient Processes: Inefficient or poorly designed processes can result in bottlenecks. This can include redundant or unnecessary steps, excessive waiting times, or complex workflows that slow down the production schedule.
- Dependencies on Slow Suppliers: If the production process relies on external suppliers who consistently deliver materials or components late, it can create bottlenecks. Dependence on slow or unreliable suppliers can disrupt the flow of work and lead to production delays.
- Lack of Visibility and Coordination: Insufficient visibility and coordination between different stages of the production process can cause bottlenecks. Lack of real-time information sharing, poor communication, or inadequate coordination among teams can lead to inefficiencies and delays.
- Inaccurate Planning and Scheduling: Inaccurate planning or scheduling of production activities can contribute to bottlenecks. If production orders are not properly sequenced, resources may be underutilized or overwhelmed, resulting in bottlenecks.
- Lack of Cross-Training: If employees are not adequately cross-trained or there is a heavy reliance on specific skilled individuals, it can create bottlenecks. Absences or limitations of those skilled individuals can disrupt the production schedule and lead to inefficiencies.
- Quality Issues: Quality issues that require rework or repairs can cause bottlenecks. If a high number of defective products is detected, it can slow down the production process and impact the overall flow of work.
Identifying the specific causes of bottlenecks in production scheduling is essential to develop effective strategies for alleviating them. Organizations should conduct thorough analyses to understand the root causes and implement targeted solutions to optimize the production process.
What Metrics are Used to Measure Bottlenecks in Production Scheduling?
Several metrics can be used to measure bottlenecks in production scheduling. These metrics provide insights into the performance and impact of bottlenecks on the production process.
Here are some commonly used metrics:
- Cycle Time: Cycle time refers to the time taken to complete one unit of work or to pass through a particular stage of the production process. It measures the speed at which work flows through the system and can indicate bottlenecks if there are significant variations in cycle times across different stages or resources.
- Throughput: Throughput represents the total number of units or tasks completed within a given time period. It measures the overall capacity and productivity of the production system. Lower throughput in specific areas or resources compared to others can indicate potential bottlenecks.
- Utilization Rate: Utilization rate measures the extent to which a resource or workstation is being used relative to its available capacity. Low utilization rates in certain resources or workstations suggest underutilization and can be indicative of bottlenecks in other areas where demand exceeds their capacity.
- Efficiency: Efficiency measures the actual output achieved compared to the expected or ideal output. It provides insights into the effectiveness of resources or processes in converting inputs into outputs. Lower efficiency in specific areas or processes can indicate bottlenecks or inefficiencies.
- Work-in-Progress (WIP) Inventory: WIP inventory refers to the amount of unfinished work or inventory in various stages of the production process. High levels of WIP inventory at specific stages can indicate bottlenecks or imbalances in the flow of work.
- Lead Time: Lead time measures the time taken from order placement to order fulfillment or product delivery. Longer lead times can be indicative of bottlenecks that delay the overall production schedule.
- Queue Length: Queue length refers to the number of units or tasks waiting in a queue or backlog. High queue lengths at specific stages or resources can indicate bottlenecks and potential delays in the production process.
- Resource Capacity: Assessing the capacity of resources or workstations is important in identifying bottlenecks. If certain resources consistently operate near or at full capacity while others have significant idle time, it may indicate bottlenecks in resource allocation.
These metrics should be tracked and analyzed to identify patterns, variations, and potential bottlenecks within the production scheduling process. Combining these metrics with other contextual information and observations provides a comprehensive view of the bottlenecks and helps in developing targeted strategies for improvement.
How can Bottlenecks be Addressed in Production Scheduling?
Bottlenecks in production scheduling can be addressed through various strategies and interventions. The specific approach depends on the root causes and constraints associated with the bottlenecks.
Here are some common ways to address bottlenecks:
- Process Redesign: Consider redesigning the production process to minimize or eliminate the bottlenecks. This may involve resequencing tasks, adjusting workstations, or reconfiguring the flow of materials to improve efficiency and reduce congestion.
- Resource Reallocation: Evaluate the allocation of resources within the system to balance the workload and optimize performance. This can include redistributing tasks, cross-training employees to handle multiple roles, or adjusting shift schedules to maximize the utilization of resources.
- Technology Upgrades: Explore the adoption of advanced technologies or automation to improve the efficiency of the bottlenecked resources or processes. This may involve implementing new machinery, upgrading software systems, or leveraging data analytics to optimize scheduling and resource allocation.
- Inventory Management: Optimize inventory management practices to reduce bottlenecks caused by material shortages or delays. This may include implementing just-in-time (JIT) inventory systems, establishing better communication channels with suppliers, or improving forecasting and demand planning to ensure the availability of materials when needed.
- Constraint Mitigation: Develop strategies to manage and mitigate constraints that impact the bottlenecked resources or processes. This can involve implementing preventive maintenance programs, conducting capacity planning, or collaborating with suppliers to address constraints such as the limited availability of critical components or equipment.
- Continuous Improvement: Implement a culture of continuous improvement to sustain optimization efforts and address emerging bottlenecks. Regularly review performance data, gather feedback from employees, and engage in ongoing process improvement initiatives. Continuous improvement helps identify new opportunities, optimize scheduling practices, and further enhance the production scheduling process.
It is important to note that addressing bottlenecks may require a combination of these strategies and a tailored approach based on the specific circumstances. Regular monitoring, evaluation, and adjustment of the implemented solutions are essential to ensure their effectiveness and to continuously optimize the production scheduling process.
How Often Should Bottleneck Analysis Be Performed in Production Scheduling?
The frequency of bottleneck analysis in production scheduling can vary depending on factors such as the complexity of the production system, the nature of the industry, and the dynamics of the business environment.
However, it is generally recommended to perform bottleneck analysis on a regular basis to ensure optimal performance and responsiveness to changes.
Here are some considerations:
- Regular Reviews: Conduct regular reviews of the production scheduling process to assess its performance, identify bottlenecks, and make necessary adjustments. The frequency of these reviews can vary based on the organization's needs and resources but could range from monthly to quarterly.
- Trigger Events: Perform bottleneck analysis when specific trigger events occur. These events may include changes in demand patterns, the introduction of new products or processes, changes in resource availability, or significant disruptions in the supply chain. Trigger events may warrant more immediate bottleneck analysis to ensure timely adjustments.
- Continuous Improvement: Integrate bottleneck analysis into a culture of continuous improvement. This means conducting ongoing monitoring and analysis of key performance metrics and utilizing the insights to drive improvements. Continuous improvement initiatives often involve frequent bottleneck analysis to address emerging constraints and optimize production scheduling.
- Business Reviews: Align bottleneck analysis with regular business reviews or strategic planning cycles. These reviews provide opportunities to assess the effectiveness of the production scheduling process, identify areas for improvement, and set goals for optimizing performance. By incorporating bottleneck analysis into these strategic discussions, organizations can ensure that it receives regular attention.
- External Factors: Consider external factors that may influence the need for bottleneck analysis. Changes in market conditions, customer preferences, or regulatory requirements can impact production scheduling. Monitoring these external factors can help determine the frequency of bottleneck analysis required to stay responsive and competitive.
Ultimately, the goal is to strike a balance between regular monitoring and analysis without causing excessive disruptions to ongoing operations. By establishing a routine for bottleneck analysis, organizations can proactively identify and address constraints, optimize resource allocation, and continuously improve their production scheduling process.
Can Bottleneck Analysis be Applied to Service-Based Industries?
Yes, bottleneck analysis can be applied to service-based industries as well. While the concept of bottlenecks originated in manufacturing and production contexts, it can be extended to service environments where there is a flow of tasks, processes, and resources.
In service-based industries, bottlenecks can manifest in various ways, such as delays in service delivery, congestion at certain service points, or limitations in the capacity of service resources. By applying bottleneck analysis, organizations can identify and address these constraints, improving the efficiency and effectiveness of service operations.
For example, in a call center, bottlenecks may occur if there are limited customer service representatives available to handle incoming calls during peak periods. By analyzing call volume patterns, resource utilization, and response times, organizations can identify bottlenecks and implement strategies such as cross-training agents, adjusting staffing levels, or implementing call routing systems to optimize the flow of calls.
Similarly, in healthcare, bottlenecks may occur in areas such as patient admissions, diagnostic tests, or treatment processes. By analyzing patient flow, resource availability, and waiting times, healthcare organizations can identify bottlenecks and implement measures to improve patient throughput, reduce waiting times, and enhance overall service delivery.
The key is to identify the flow of work, dependencies, and resource utilization within the service environment, and then apply bottleneck analysis techniques to identify and address constraints that limit efficiency and productivity.
Applying bottleneck analysis in service-based industries can help organizations improve customer service, reduce delays, optimize resource utilization, and enhance overall service delivery. It enables organizations to identify areas of improvement, make data-driven decisions, and continuously optimize their service processes.
How can Bottleneck Analysis Help with Capacity Planning?
Bottleneck analysis plays a crucial role in capacity planning by providing insights into the constraints and limitations of resources within a production system. Here's how bottleneck analysis can help with capacity planning:
- Identify Resource Constraints: Bottleneck analysis helps identify the specific resources or workstations that act as constraints within the production system. These bottlenecks can include machines, equipment, labor, or other critical resources that limit the overall capacity. By pinpointing these constraints, organizations can assess their impact on capacity planning.
- Optimize Resource Utilization: Bottleneck analysis allows organizations to optimize the utilization of resources. By identifying bottlenecks and addressing them, capacity planning can be done more effectively. For example, if a particular machine is a bottleneck, efforts can be made to optimize its usage, reduce downtime, and increase its capacity to align with the overall production requirements.
- Adjust Workloads and Shift Schedules: Bottleneck analysis provides insights into imbalances in workloads and resource allocation. It helps identify areas where workloads are unevenly distributed, leading to bottlenecks and inefficient capacity utilization. By adjusting workloads, cross-training employees, or modifying shift schedules, organizations can balance the utilization of resources and maximize capacity.
- Determine Resource Requirements: Understanding bottlenecks and their impact on production capacity allows organizations to assess resource requirements more accurately. Capacity planning can be based on the specific needs of the bottlenecked resources. This helps in allocating resources effectively, ensuring that the right resources are available to meet demand and avoid overburdening critical constraints.
- Forecasting and Demand Management: Bottleneck analysis provides insights into the capacity limitations of the production system. This information is valuable for forecasting and demand management. By considering bottlenecks, organizations can align production capacity with expected demand, avoiding overcommitment or underutilization of resources.
- Investment Planning: Bottleneck analysis helps organizations identify areas where investments in additional resources or process improvements may be required to alleviate capacity constraints. It provides valuable data for decision-making regarding capital investments, technology upgrades, or expansion plans to increase overall production capacity.
By incorporating bottleneck analysis into capacity planning, organizations can optimize resource utilization, balance workloads, ensure efficient production, and make informed decisions to meet demand.
It helps organizations identify areas of constraint and take proactive measures to align capacity with production requirements, leading to improved efficiency, reduced bottlenecks, and enhanced operational performance.
What is the Relationship Between Bottlenecks and Lead Times in Production Scheduling?
Bottlenecks and lead times in production scheduling are closely related. The presence of bottlenecks within a production system directly impacts lead times, which is the time taken from order placement to order fulfillment or product delivery.
Here's how the relationship between bottlenecks and lead times works:
- Impact of Bottlenecks on Lead Times: Bottlenecks represent constraints or limitations within the production system that restrict the overall flow of work. When a bottleneck occurs at a particular resource, workstation, or process, it slows down the production process, causing delays. These delays directly affect lead times, as orders take longer to be processed and fulfilled due to the bottlenecked area.
- Amplification Effect: Bottlenecks tend to amplify lead times throughout the production process. Even if other areas of the production system are operating efficiently, the presence of a bottleneck can create a ripple effect, causing delays that propagate through subsequent stages. This amplification effect leads to longer lead times overall.
- Bottleneck Management and Lead Time Reduction: Effective management and mitigation of bottlenecks can result in reduced lead times. By identifying and addressing bottlenecks, organizations can streamline processes, optimize resource utilization, and improve the flow of work. This leads to faster throughput, shorter cycle times, and ultimately, reduced lead times.
- Balancing Capacity and Demand: Managing bottlenecks involves aligning production capacity with demand. By addressing bottlenecks, organizations can ensure that the production system can handle the required volume of orders within a reasonable time frame. This balanced capacity and demand relationship contribute to shorter lead times.
- Process Optimization and Lead Time Improvement: Bottleneck analysis helps identify areas where process optimization can be applied to reduce lead times. By streamlining processes, eliminating non-value-added activities, and improving the efficiency of bottlenecked areas, organizations can achieve significant improvements in lead times.
- Continuous Improvement and Lead Time Reduction: Continuous improvement initiatives driven by bottleneck analysis can result in ongoing reductions in lead times. By regularly monitoring performance, identifying emerging bottlenecks, and implementing targeted improvements, organizations can achieve continuous lead time reduction and enhance customer satisfaction.
In summary, bottlenecks directly impact lead times in production scheduling. By effectively managing bottlenecks, organizations can reduce delays, streamline operations, and optimize resource utilization, leading to shorter lead times and improved overall efficiency.
How Does Bottleneck Analysis Contribute to Lean Manufacturing Principles?
Bottleneck analysis and lean manufacturing principles are closely aligned, with bottleneck analysis playing a significant role in achieving the goals of lean manufacturing.
Here's how bottleneck analysis contributes to lean manufacturing principles:
- Identify Waste: One of the core principles of lean manufacturing is the identification and elimination of waste. Bottleneck analysis helps identify areas of inefficiency and waste within the production system. Bottlenecks often indicate areas where work is piling up, waiting times are excessive, or resources are underutilized, all of which are forms of waste. By addressing bottlenecks, organizations can reduce waste and improve overall efficiency.
- Flow Optimization: Lean manufacturing emphasizes the smooth and continuous flow of work. Bottleneck analysis provides insights into the flow of work within the production system. By identifying and addressing bottlenecks, organizations can optimize the flow of work, eliminate interruptions, and reduce cycle times. This leads to improved flow and better synchronization of production activities.
- Pull System Implementation: Lean manufacturing promotes the use of pull systems, where work is pulled based on customer demand rather than pushed through the system. Bottleneck analysis helps identify areas where the push system prevails due to bottlenecks or imbalances. By addressing bottlenecks, organizations can move towards implementing pull systems, enabling a more efficient and demand-driven production process.
- Continuous Improvement: Bottleneck analysis is an integral part of the continuous improvement philosophy of lean manufacturing. It encourages organizations to regularly assess the performance of the production system, identify bottlenecks, and implement targeted improvements. By continuously analyzing and addressing bottlenecks, organizations can drive ongoing optimization, enhance efficiency, and achieve sustained improvement.
- Respect for People: Lean manufacturing emphasizes the importance of engaging and empowering employees. Bottleneck analysis provides an opportunity to involve employees in the identification and resolution of bottlenecks. By seeking input from employees who work directly with the bottlenecks, organizations can tap into their knowledge and expertise, fostering a culture of collaboration and respect for people.
- Value Stream Mapping: Value stream mapping, a key tool in lean manufacturing, helps visualize the entire production process, including bottlenecks. By creating value stream maps, organizations can identify waste, optimize process flow, and prioritize improvement efforts. Bottleneck analysis plays a vital role in identifying bottlenecks within the value stream, guiding the development of future state maps, and driving lean initiatives.
By applying bottleneck analysis, organizations can address inefficiencies, reduce waste, optimize process flow, and continuously improve the production system in alignment with lean manufacturing principles. It provides a structured approach to identify and eliminate bottlenecks, ultimately leading to enhanced efficiency, reduced costs, and improved customer satisfaction.
Can Bottleneck Analysis be Applied to a Single Workstation or Process within a Production System?
Yes, bottleneck analysis can certainly be applied to a single workstation or process within a production system. While bottleneck analysis is often used to assess the overall flow and performance of a production system, it can also be valuable for identifying constraints and optimizing the performance of specific areas or processes.
By focusing on a single workstation or process, organizations can gain insights into its capacity, efficiency, and impact on the overall production flow. Here's how bottleneck analysis can be applied at the workstation or process level:
- Identify the Critical Workstation/Process: Determine the specific workstation or process that is causing delays or limiting the overall production capacity. This can be identified based on factors such as long cycle times, high work-in-progress inventory, or frequent disruptions.
- Measure Performance Metrics: Analyze performance metrics related to the identified workstation or process. This can include cycle time, throughput, utilization rate, efficiency, or any other relevant metrics that help assess the performance and identify potential bottlenecks.
- Assess Resource Utilization: Evaluate the utilization of resources at the workstation or process level. Consider factors such as available capacity, labor requirements, equipment availability, and any dependencies on other resources.
- Identify Constraints: Identify any constraints or limitations that impact the performance of the workstation or process. This can include factors such as equipment breakdowns, material shortages, or labor constraints.
- Optimize Workflow: Based on the analysis, develop strategies to optimize the workflow at the workstation or process level. This can involve process redesign, resource reallocation, cross-training of employees, or implementing technology improvements to enhance efficiency.
- Monitor and Improve: Continuously monitor the performance of the identified workstation or process and implement improvement initiatives as needed. Regularly review performance metrics, gather feedback from employees, and make adjustments to further optimize the workflow and eliminate bottlenecks.
By applying bottleneck analysis to a single workstation or process, organizations can enhance the efficiency and productivity of that specific area, leading to improved overall performance of the production system. It allows for targeted optimization efforts and ensures that constraints at a micro-level are addressed to achieve maximum efficiency and throughput.
Is Bottleneck Analysis a One-Time Activity or an Ongoing Process?
Bottleneck analysis is not a one-time activity but an ongoing process that should be conducted regularly.
While an initial bottleneck analysis can provide valuable insights and help identify constraints within the production system, it is important to recognize that production environments are dynamic and subject to changes over time.
Therefore, ongoing bottleneck analysis is necessary to adapt to evolving circumstances and maintain optimal efficiency.
Here are some reasons why bottleneck analysis is an ongoing process:
- Changing Production Conditions: Production systems are influenced by various internal and external factors such as market demand, technology advancements, resource availability, and operational changes. These factors can introduce new bottlenecks or modify existing ones. Regular bottleneck analysis helps identify emerging constraints and ensures that the production scheduling process remains optimized.
- Continuous Improvement: Bottleneck analysis is closely tied to the principle of continuous improvement. By conducting ongoing analyses, organizations can identify areas for improvement, implement changes, and monitor the effectiveness of the implemented solutions. Regular bottleneck analysis allows for the evaluation of the impact of improvement efforts and the identification of new opportunities for optimization.
- Proactive Risk Management: Ongoing bottleneck analysis helps organizations proactively manage risks associated with potential bottlenecks. By monitoring performance metrics and conducting regular assessments, organizations can identify and address potential bottlenecks before they escalate and impact production schedules or customer satisfaction. This proactive approach helps minimize disruptions and maintain a smooth flow of work.
- Changing Business Environment: Business environments are subject to fluctuations and uncertainties. Changes in market conditions, customer requirements, or supply chain dynamics can impact production scheduling. Regular bottleneck analysis allows organizations to adapt to these changes, identify new bottlenecks that may arise, and optimize the production process accordingly.
- Resource Optimization: Ongoing bottleneck analysis helps organizations optimize the utilization of resources. As production demands and resource availability fluctuate, conducting regular analyses ensures that resources are allocated efficiently, workloads are balanced, and potential bottlenecks are addressed. This supports effective capacity planning and resource management.
- Performance Monitoring: Regular bottleneck analysis allows for continuous monitoring of key performance metrics. By tracking these metrics over time, organizations can identify trends, patterns, or deviations that may indicate the presence of bottlenecks. This information can be used to implement timely corrective actions and drive ongoing performance improvement.
In summary, bottleneck analysis is an ongoing process that should be integrated into the production scheduling routine. By conducting regular analyses, organizations can stay proactive, adapt to changing conditions, drive continuous improvement, and optimize their production systems for optimal efficiency and customer satisfaction.
How Can Deskera Help You with Production Scheduling?
Deskera MRP is an integrated software solution designed to help businesses manage their manufacturing processes, including production scheduling.
Here's how Deskera MRP can assist you with production scheduling:
- Resource Planning: Deskera MRP enables you to efficiently plan and allocate resources for your production schedule. You can define the availability and capacity of your resources, such as labor, machinery, and equipment, and schedule tasks accordingly. This helps in optimizing resource utilization and balancing workloads.
- Production Order Management: With Deskera MRP, you can easily create and manage production orders. You can define the bill of materials (BOM) and set up routing for each order, specifying the sequence of operations and dependencies. This allows you to schedule and track the progress of production orders, ensuring timely execution.
- Real-Time Visibility: Deskera MRP provides real-time visibility into your production schedule. You can monitor the status of production orders, track work in progress (WIP), and identify bottlenecks or potential delays. This visibility enables you to make informed decisions and take proactive actions to optimize your production scheduling.
- Capacity Planning: Deskera MRP helps you plan and manage production capacity effectively. You can evaluate resource availability, track utilization rates, and forecast capacity requirements based on production demand. This enables you to align your capacity with the production schedule and avoid overloading resources or creating bottlenecks.
- Demand Planning and Forecasting: Deskera MRP incorporates demand planning and forecasting capabilities. By analyzing historical data and market trends, you can accurately forecast future demand. This information can be used to adjust production schedules, allocate resources, and ensure that you meet customer requirements on time.
- Collaboration and Communication: Deskera MRP facilitates collaboration and communication among stakeholders involved in production scheduling. You can share real-time updates, task assignments, and production-related information with your team members, suppliers, and other relevant parties. This streamlines communication reduces errors, and enhances coordination.
- Reporting and Analytics: Deskera MRP provides robust reporting and analytics features. You can generate various reports related to production scheduling, such as resource utilization, lead times, production efficiency, and capacity analysis. These insights help in monitoring performance, identifying areas for improvement, and making data-driven decisions.
Key Takeaways
Bottleneck analysis in production scheduling is the process of identifying and addressing constraints or bottlenecks that limit the overall efficiency and throughput of a production system. It involves analyzing the flow of work, measuring performance metrics, and developing strategies to optimize resource allocation and process flow.
The key points about bottleneck analysis in production scheduling are:
- Identification: The first step in bottleneck analysis is to identify the specific resource or process that is causing the bottleneck. This can be done by monitoring and analyzing the flow of work, observing production data, or conducting time studies.
- Measurement: Once the bottleneck is identified, it is important to measure its impact on the overall production system. This involves gathering data on the capacity, cycle time, and efficiency of the bottleneck resource or process.
- Optimization: After understanding the nature and impact of the bottleneck, efforts can be focused on optimizing it. This can include measures such as increasing the capacity of the bottleneck resource, improving the efficiency of the process, implementing better scheduling strategies, or reallocating resources to alleviate the bottleneck.
- Constraints and Dependencies: Bottlenecks are often influenced by constraints and dependencies within the production system. For example, the availability of raw materials or the synchronization between different processes can affect the performance of a bottleneck. Considering these factors is essential when analyzing and addressing bottlenecks.
- Continuous Improvement: Bottleneck analysis should be an ongoing process, as the dynamics of the production system can change over time. Regular monitoring, data analysis, and optimization efforts are necessary to ensure that bottlenecks are effectively managed and minimized.
It is important for organizations to continuously monitor and improve their production systems, as bottlenecks may change over time due to evolving demands, resource availability, or market conditions.
By embracing a culture of continuous improvement and proactively addressing bottlenecks, organizations can achieve enhanced efficiency, better customer satisfaction, and a competitive advantage in the ever-changing manufacturing landscape.
By conducting bottleneck analysis as part of production scheduling, companies can make informed decisions, allocate resources effectively, and optimize production processes to maximize productivity, minimize lead times, and meet customer demands more efficiently.
Overall, Deskera MRP serves as a comprehensive solution for managing production scheduling. It helps streamline your manufacturing processes, optimize resource utilization, improve visibility, and enhance overall efficiency. By leveraging its features, you can effectively plan and execute your production schedule while minimizing bottlenecks and ensuring timely order fulfillment.
Related Articles

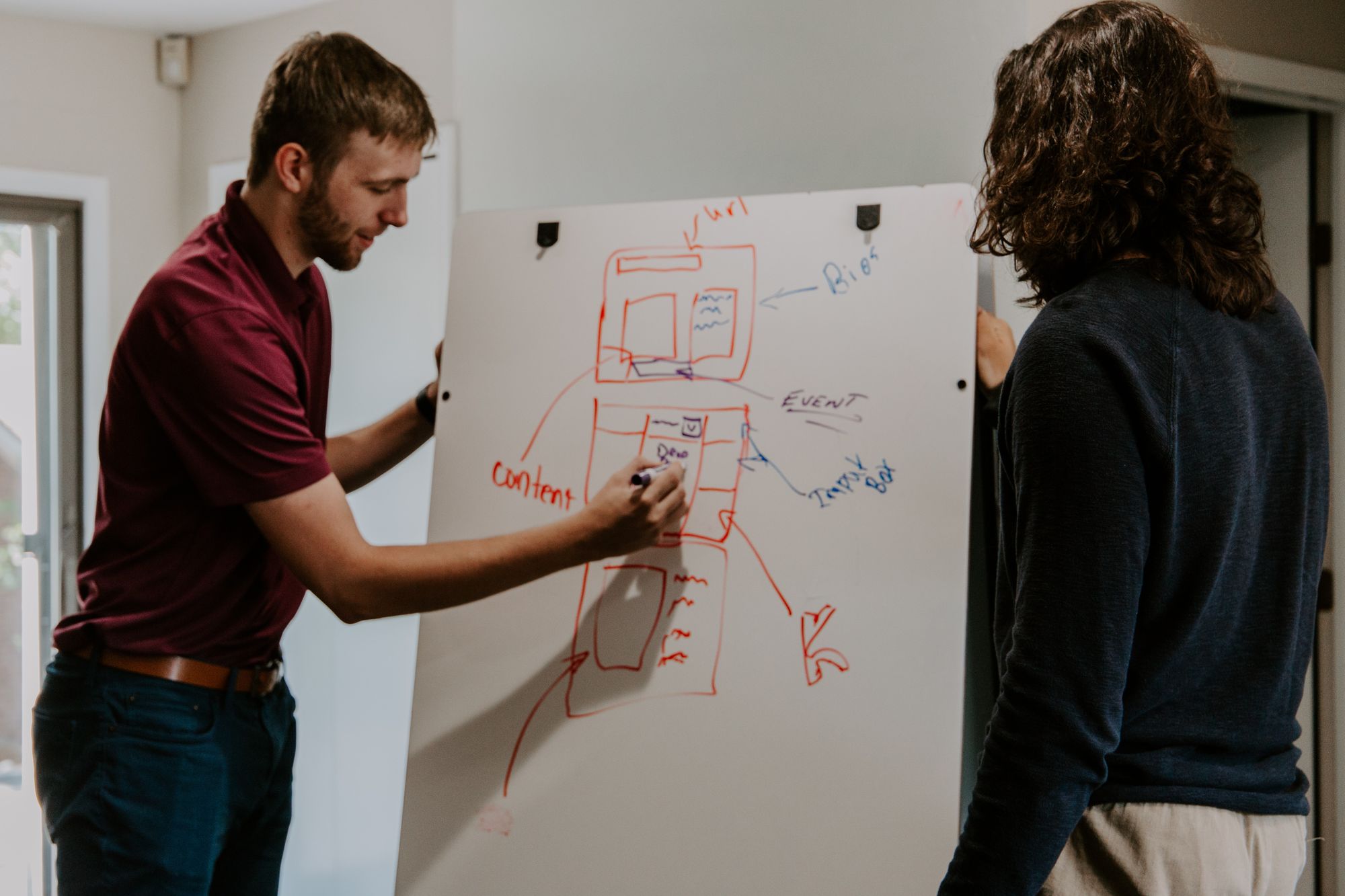
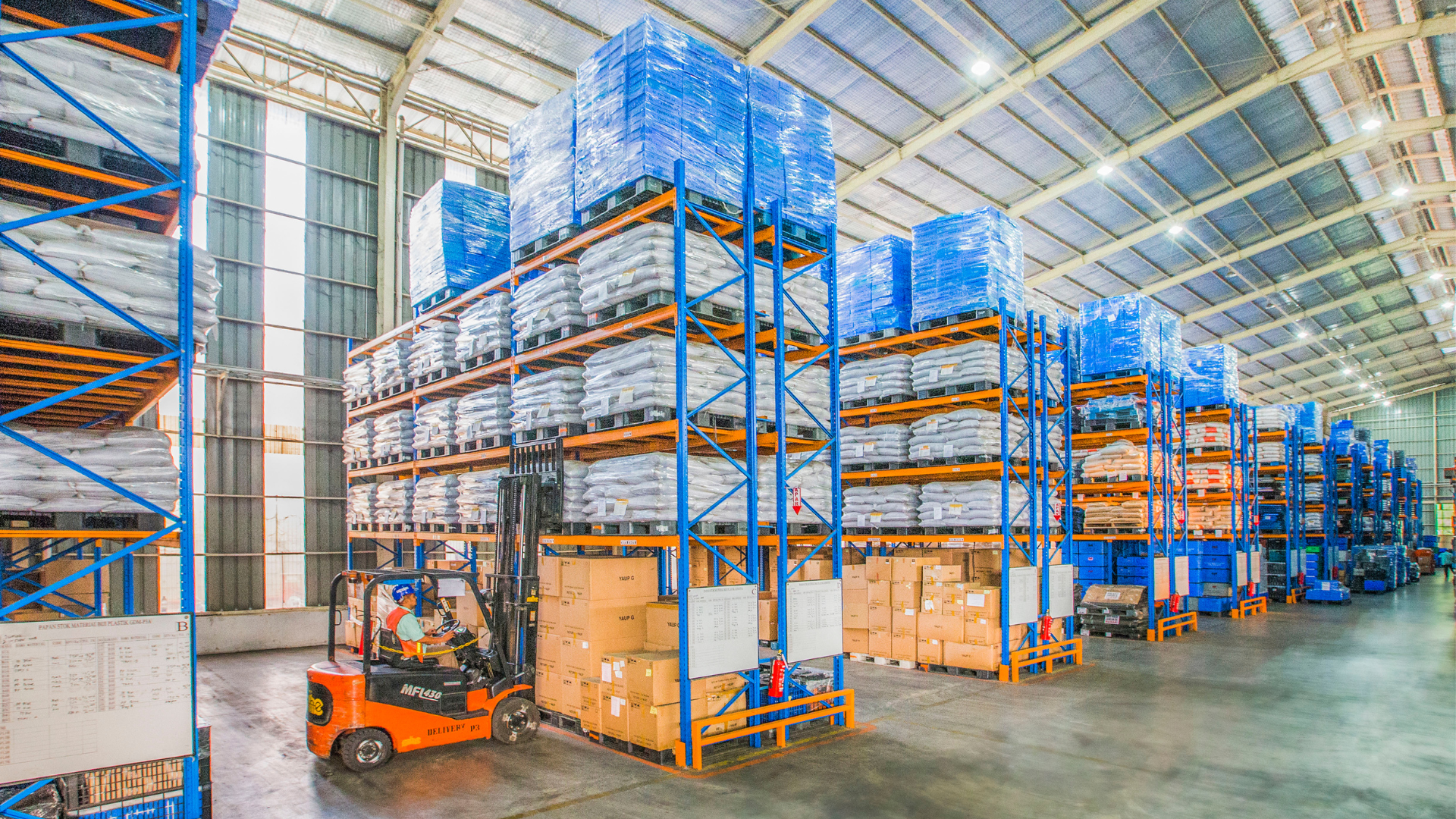
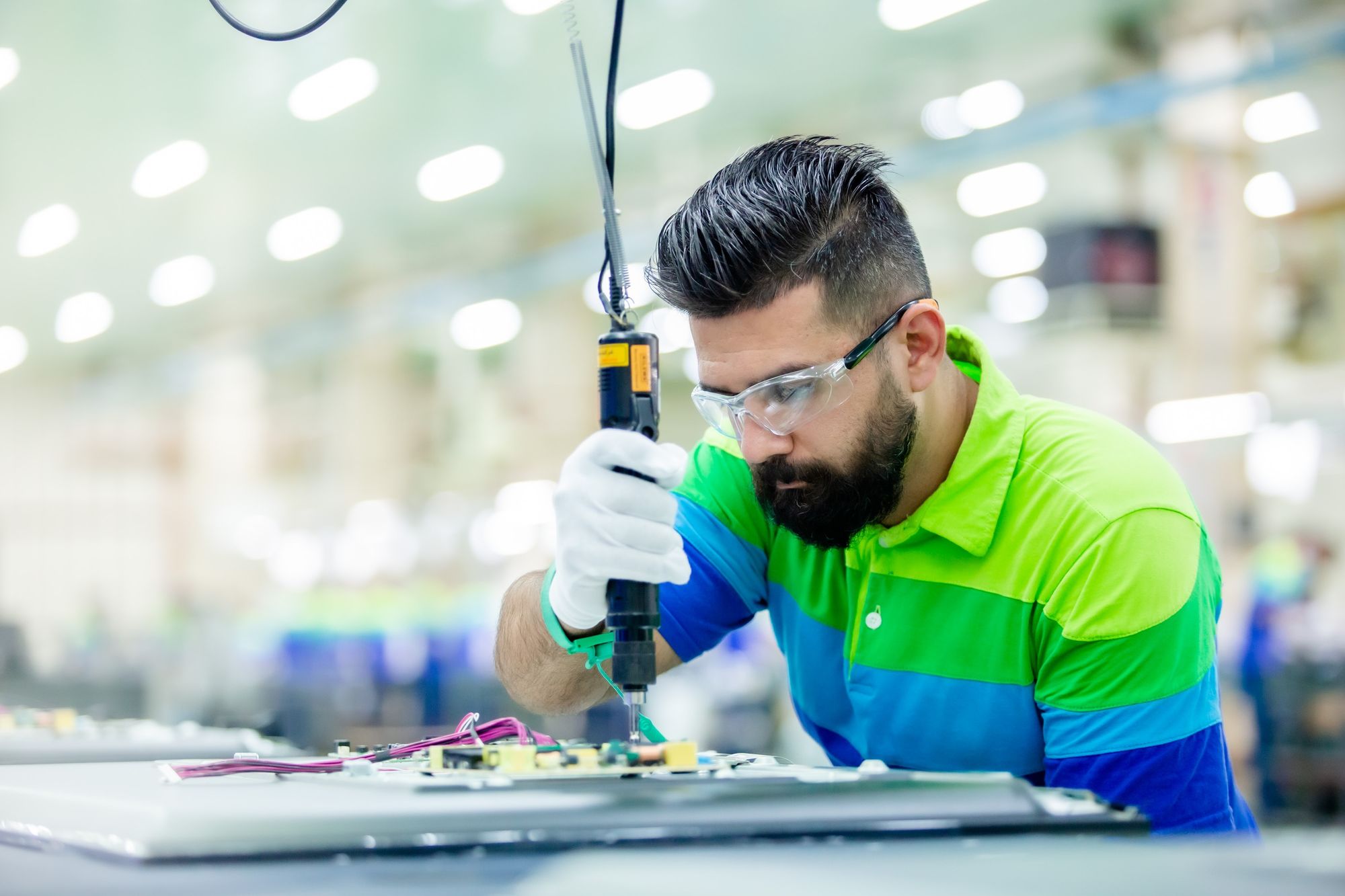
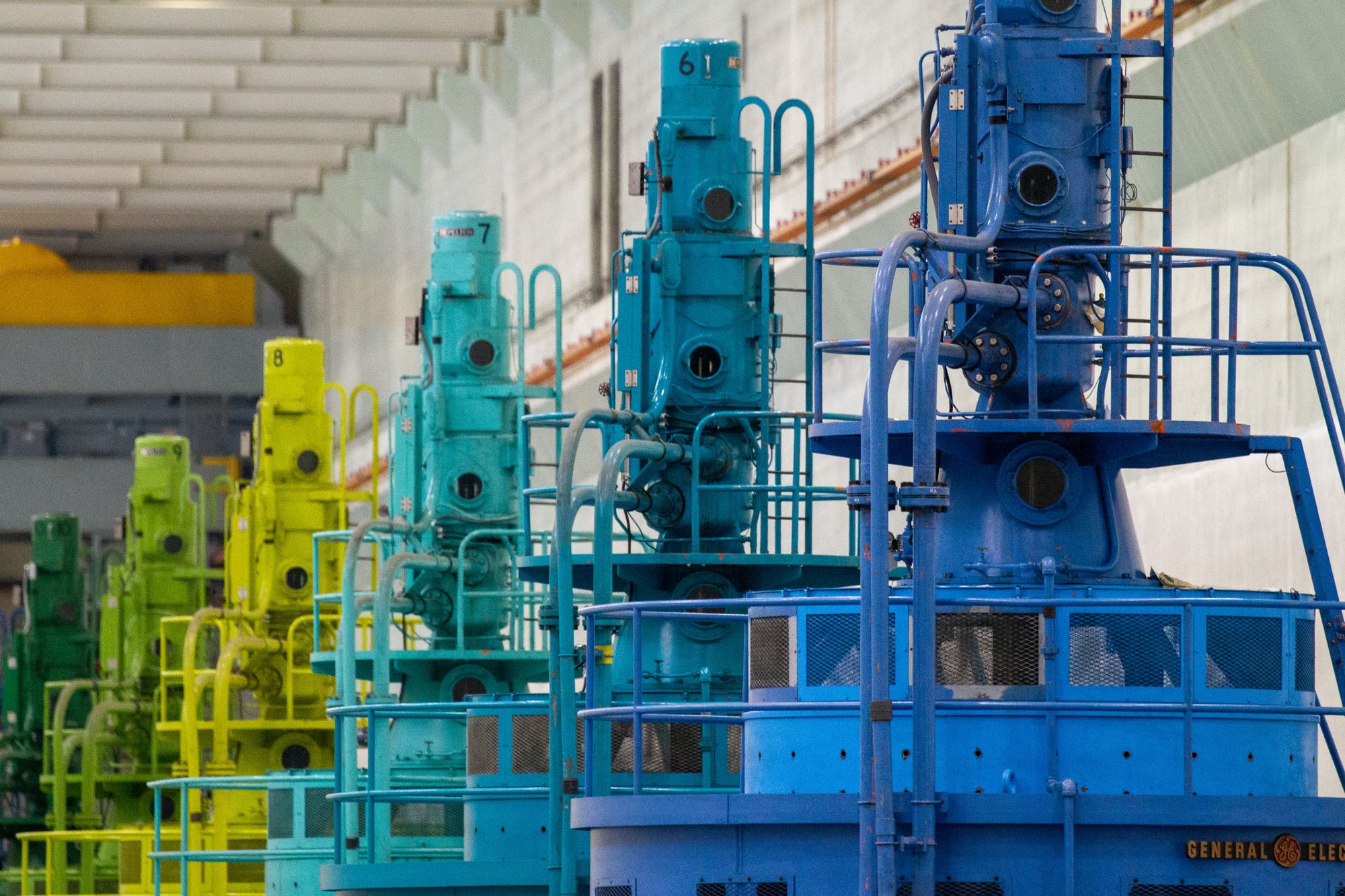
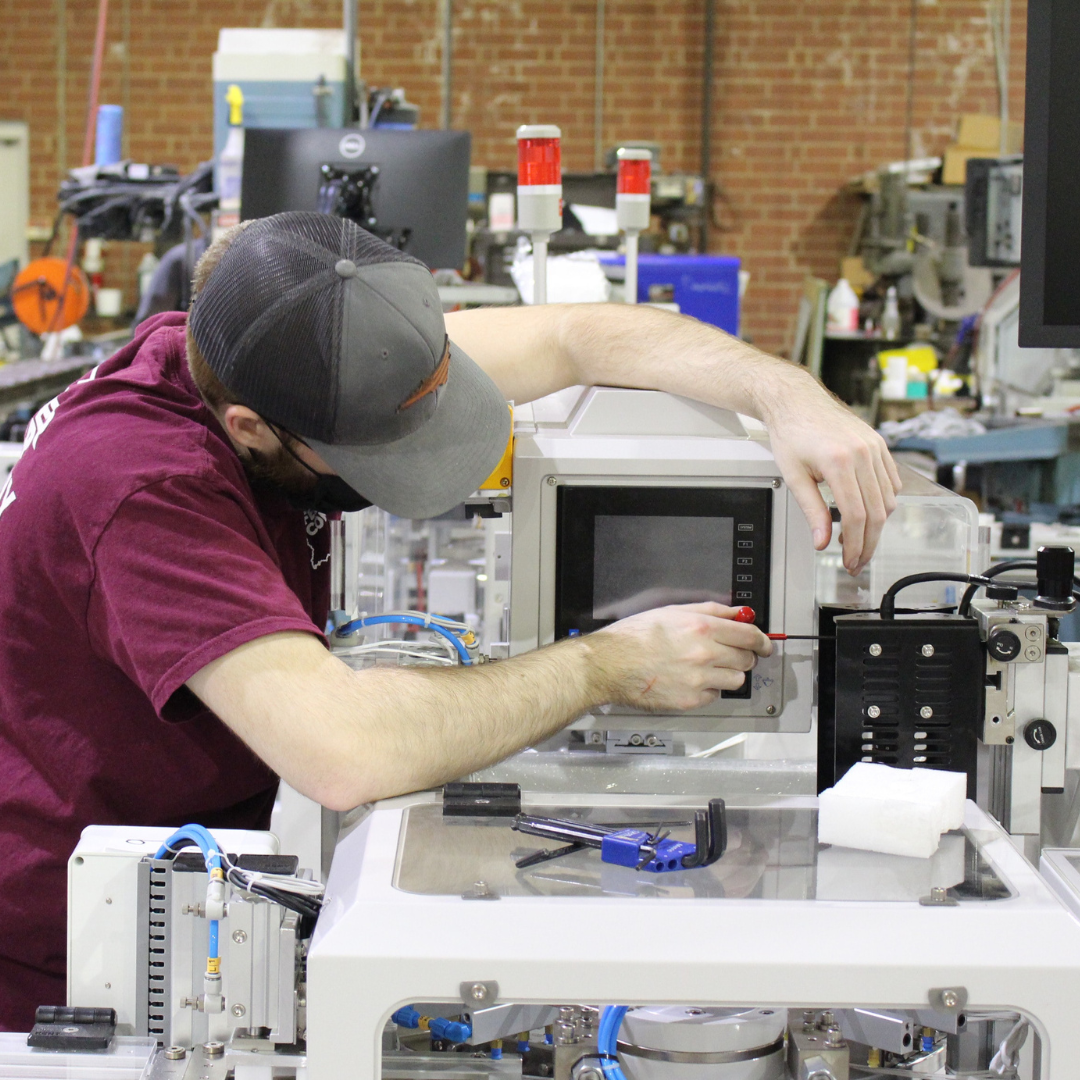