Work orders are the backbone of any organization’s operational efficiency, directly influencing how resources, tasks, and maintenance are managed. Yet, many businesses struggle with inefficient work order systems that lead to delayed projects, increased costs, and wasted resources.
For executives, streamlining work orders is no longer just an option but a necessity to ensure smooth operations and remain competitive. In an increasingly fast-paced business environment, optimizing these processes can unlock significant value and drive higher productivity.
The global work order management market is projected to grow from USD 0.83 billion in 2024 to USD 1.22 billion by 2029, with a compound annual growth rate (CAGR) of 7.99% during the forecast period. This growth highlights the increasing demand for automated and efficient work order systems across industries.
As companies look for ways to reduce operational bottlenecks, the need for streamlined work order management is evident. Implementing the right tools and strategies can help businesses meet this demand while improving their bottom line.
For executives, it is crucial to understand that modern work order systems are more than just tools for task delegation—they are strategic assets that help optimize resources, improve accountability, and ensure timely project completion.
The shift towards cloud-based solutions, artificial intelligence (AI), and mobile access has revolutionized work order management, providing real-time updates and enhanced collaboration across departments. These advancements enable executives to track performance, make data-driven decisions, and reduce inefficiencies.
One such tool that stands out in this space is Deskera MRP. Known for its comprehensive material requirements planning (MRP) features, Deskera MRP offers powerful work order management capabilities that help businesses optimize production schedules, track task progress in real time, and ensure efficient resource allocation.
With built-in reporting and demand forecasting tools, Deskera MRP enables businesses to automate repetitive tasks and make informed decisions, ultimately improving operational efficiency.
What are Work Orders?
Work orders are formal documents or digital records that outline specific tasks, jobs, or maintenance activities to be completed within an organization. They serve as instructions that provide details such as the nature of the work, the person or team responsible, required resources, deadlines, and any other relevant information. Work orders are used across various industries, including manufacturing, facilities management, construction, and IT services, to ensure tasks are assigned and tracked efficiently.
Here are the key elements typically included in a work order:
- Task Description: A clear outline of what needs to be done.
- Assigned Personnel: The team or individual responsible for completing the task.
- Materials and Tools: Resources needed to complete the work.
- Deadlines: Start and end dates or times for the task.
- Status Updates: The current progress or completion status of the work.
- Approvals: Authorization by a manager or supervisor.
Work orders help streamline operations by providing clarity, improving accountability, and enabling tracking of tasks from creation to completion.
Why are Work Orders Essential for Business Operations?
Work orders are essential for business operations because they provide a structured way to manage tasks, streamline workflows, and ensure that resources are allocated effectively. They play a critical role in maintaining operational efficiency, reducing downtime, and enhancing overall productivity.
Here’s why work orders are vital:
1. Task Organization and Clarity
Work orders clearly define the tasks that need to be performed, outlining the necessary steps, responsibilities, and timelines. This clarity helps avoid misunderstandings and ensures that employees know exactly what is expected of them, reducing errors and increasing task completion efficiency.
2. Resource Management
Work orders help allocate resources such as materials, tools, and personnel efficiently. By outlining what is required for each task, they ensure that the right resources are available at the right time, preventing delays caused by shortages or over-allocation.
3. Improved Accountability
Assigning work orders to specific individuals or teams creates accountability. Workers are responsible for completing their assigned tasks, and managers can track progress through the work order system, ensuring that tasks are completed on time and according to plan.
4. Real-Time Tracking and Monitoring
Work orders enable real-time tracking of ongoing jobs, allowing managers to monitor the status of each task and make adjustments as necessary. This visibility helps identify potential bottlenecks early, allowing proactive problem-solving and ensuring projects stay on schedule.
5. Maintenance and Downtime Reduction
In industries like manufacturing or facilities management, work orders are crucial for scheduled maintenance tasks. By organizing preventive maintenance and repairs through work orders, businesses can reduce equipment downtime, increase asset longevity, and avoid costly breakdowns.
6. Data Collection and Reporting
Work orders capture valuable data on performance metrics, such as the time taken to complete tasks, labor costs, and resource usage. This data can be analyzed to identify inefficiencies, optimize workflows, and improve future business decisions.
Overall, work orders are critical for ensuring that tasks are completed in a systematic, efficient, and accountable manner, contributing to smoother operations and long-term business success.
Common Challenges Companies Face with Traditional Work Order Systems
Despite their importance, traditional work order systems often present several challenges that hinder operational efficiency and productivity. These challenges typically stem from manual processes, lack of integration, and limited visibility into work order progress.
Here are some of the most common issues:
Manual Tracking and Paper-Based Processes
Traditional work order systems often rely on manual entry or paper-based forms, which can lead to errors, lost paperwork, and delays. This outdated approach makes it difficult to track tasks in real time, resulting in inefficiencies and miscommunication between departments.
Lack of Real-Time Updates
Without digital or automated systems, work order status updates are often delayed, making it challenging for managers to monitor progress and make timely decisions. This lack of real-time visibility increases the risk of bottlenecks, missed deadlines, and poor resource allocation.
Communication Gaps Between Departments
Traditional work order systems often fail to provide a centralized platform for communication, leading to silos between departments. This can result in delayed approvals, incomplete task details, or confusion over responsibilities, all of which contribute to operational inefficiencies.
Difficulty in Prioritizing Tasks
In a manual system, prioritizing work orders based on urgency, resource availability, or other factors can be cumbersome. Without clear task prioritization, essential work may be delayed while less critical tasks are completed first, affecting the overall workflow.
Limited Reporting and Data Analytics
Traditional systems offer limited capabilities for generating detailed reports or analyzing performance data. Without data-driven insights, businesses struggle to assess their operational efficiency, identify areas for improvement, or optimize resource allocation.
Increased Labor Costs and Time Delays
Manual processes often require additional labor, leading to increased administrative overheads. Delays in processing, approving, and completing work orders can also result in downtime and higher costs, as companies may need to pay for overtime or outsource urgent tasks to third-party vendors.
By addressing these challenges, companies can move toward more efficient, automated work order systems that enhance productivity, improve communication, and reduce operational costs.
Key Benefits of Streamlined Work Order Processes
Streamlining work order processes can significantly improve business operations, driving efficiency and ensuring tasks are completed accurately and on time. By adopting automated and digital solutions, companies can eliminate the bottlenecks associated with traditional work order systems.
Here are the key benefits of optimizing work order management:
Increased Productivity and Efficiency
A streamlined work order process ensures that tasks are assigned, tracked, and completed with minimal delays. Automation reduces the time spent on manual tasks such as data entry and approval routing, allowing employees to focus on more critical responsibilities. This leads to faster completion of work orders and more efficient use of resources.
Improved Task Prioritization
With optimized work order systems, businesses can easily prioritize tasks based on urgency, resource availability, and project deadlines. This ensures that critical work is completed first, avoiding unnecessary delays and minimizing downtime for essential equipment or processes.
Enhanced Communication and Collaboration
Streamlined work order systems promote better communication across departments by providing real-time updates and centralized platforms for sharing information. Teams can collaborate more effectively, reducing miscommunication, and ensuring that everyone has access to the same data, which improves task coordination.
Real-Time Tracking and Visibility
Modern work order systems offer real-time tracking of task progress, giving managers full visibility into what tasks are pending, in progress, or completed. This transparency allows for quicker decision-making, early detection of potential issues, and better control over project timelines.
Reduced Operational Costs
By automating routine tasks and eliminating manual processes, businesses can significantly reduce labor costs. Additionally, improved scheduling and task prioritization help avoid costly downtime, while efficient resource allocation reduces the likelihood of overstaffing or material waste.
Data-Driven Decision Making
Streamlined work order systems provide valuable insights into operational performance through detailed reporting and data analytics. By tracking key performance indicators (KPIs) such as task completion times, resource utilization, and maintenance costs, businesses can identify inefficiencies and continuously improve their processes.
Compliance and Accountability
A streamlined system ensures that all tasks are properly documented, and work orders are completed according to company policies and industry regulations. It also creates a clear audit trail, making it easier to review completed work orders and track accountability for each task.
By embracing a streamlined approach to work order management, companies can enhance overall efficiency, reduce costs, and improve task execution, leading to a more productive and agile organization.
How Technology Drives Efficiency in Work Order Management
The integration of technology into work order management has revolutionized how businesses handle tasks, projects, and maintenance operations. By automating and digitizing traditionally manual processes, companies can drastically improve the accuracy, speed, and transparency of their workflows.
Here's how technology is driving efficiency in work order management:
Automation of Routine Tasks
Technology automates repetitive tasks such as work order creation, assignment, and approval. This reduces the need for manual data entry and speeds up the entire process.
Automation tools can automatically generate work orders based on preset criteria, assign them to the right personnel, and send notifications, ensuring that no task is overlooked and that processes move forward seamlessly.
Real-Time Data and Updates
Digital work order systems provide real-time visibility into the status of tasks. With cloud-based platforms and mobile accessibility, employees can update work orders on the go, allowing managers and teams to see progress in real time.
This transparency reduces communication gaps and ensures that everyone is on the same page, improving coordination and minimizing delays.
Mobile Accessibility for On-the-Go Management
Mobile-enabled work order systems allow workers in the field to access, update, and close work orders from their smartphones or tablets.
This mobility enhances response times, improves accuracy in task reporting, and helps resolve issues faster. Managers can also monitor operations and make informed decisions from anywhere, increasing overall agility.
Integrated Systems and Centralized Data
Technological solutions integrate with other business systems, such as ERP (Enterprise Resource Planning), MRP (Material Requirements Planning), and asset management platforms.
This integration ensures that all relevant data is available in one place, from inventory levels to resource allocation. A centralized system eliminates data silos, reduces duplication of work, and enhances decision-making by providing a holistic view of operations.
Predictive Maintenance and Analytics
Advanced technologies like AI and IoT (Internet of Things) enable predictive maintenance, where systems can forecast potential equipment failures based on historical data and real-time monitoring.
By integrating these tools into work order management, businesses can schedule maintenance before issues arise, reducing downtime and avoiding costly repairs. Analytics tools also provide actionable insights, helping businesses identify inefficiencies and continuously optimize their processes.
Enhanced Reporting and Performance Monitoring
Technology simplifies data collection and reporting on key performance indicators (KPIs). Digital work order systems can track metrics like task completion time, labor hours, and cost efficiency, providing detailed reports that help managers assess performance.
This data-driven approach allows businesses to identify bottlenecks, monitor trends, and make improvements to ensure that work orders are completed faster and more efficiently.
Collaboration and Communication Tools
Cloud-based work order management platforms offer integrated communication tools, allowing teams to collaborate effectively, even across departments or locations. Team members can share updates, upload documents, and comment on work orders in real time, enhancing collaboration and ensuring smooth workflows.
By leveraging technology in work order management, businesses can achieve greater efficiency, improve productivity, and ensure that resources are used optimally. This not only enhances day-to-day operations but also positions companies for long-term growth and success.
Best Practices for Executives to Streamline Work Orders
To ensure efficient work order management, executives must adopt strategies that optimize workflows, improve communication, and maximize resource utilization. Implementing best practices not only reduces downtime but also drives productivity and operational success.
Here are key practices for executives to streamline work orders:
Automate Work Order Processes
One of the most effective ways to streamline work order management is by automating routine tasks. By adopting a digital work order system, businesses can automate task assignment, scheduling, and notifications.
This reduces the need for manual intervention, minimizes errors, and accelerates the process from order creation to completion. Automation also allows for consistent follow-ups and updates, ensuring that no work order is overlooked.
Prioritize and Categorize Work Orders
Executives should implement a system that prioritizes work orders based on urgency, impact, and resource availability.
Categorizing tasks by priority ensures that critical jobs are addressed first, reducing downtime and preventing disruptions in operations.
Additionally, creating categories for routine, preventive, and emergency work orders enables more structured and organized task management.
Enhance Communication Across Departments
Clear and open communication is key to efficient work order management. Implementing a centralized platform for work order tracking, where teams can collaborate in real-time, ensures that everyone is on the same page.
Executives should promote cross-department communication, especially between maintenance, operations, and management teams, to avoid misunderstandings and ensure tasks are completed seamlessly.
Use Data Analytics for Continuous Improvement
Data-driven decision-making is critical for optimizing work order efficiency. Executives should monitor key performance indicators (KPIs) such as completion times, cost per work order, and resource utilization to identify inefficiencies in their processes.
By analyzing this data, businesses can refine their workflows, make informed resource allocation decisions, and continuously improve performance.
Implement Mobile Solutions for Flexibility
Enabling mobile access to work order systems ensures that field workers and on-site teams can manage tasks from any location.
Mobile solutions improve response times, allow workers to update orders in real-time, and increase flexibility for managing operations.
For executives, this results in more efficient task management, faster resolution of issues, and improved overall productivity.
Standardize Work Order Procedures
To ensure consistency and reduce errors, businesses should standardize work order procedures. Creating clear guidelines and templates for different types of work orders (e.g., maintenance, repairs, installations) helps streamline the process.
Executives should ensure that these procedures are well-documented and accessible to all team members, reducing variations in how tasks are handled.
Focus on Preventive Maintenance
Preventive maintenance should be a priority for executives aiming to reduce unplanned downtime.
By proactively scheduling regular inspections and maintenance tasks through work orders, companies can prevent equipment failures and minimize disruptions to operations.
A well-organized preventive maintenance strategy keeps assets running smoothly and extends their lifespan.
Foster Accountability and Ownership
Assigning clear ownership for each work order improves accountability and ensures tasks are completed on time. Executives should encourage a culture where teams take responsibility for their assigned work, from start to finish.
By setting expectations and providing the necessary resources, employees are more likely to complete tasks efficiently and with higher accuracy.
Integrate Work Order Systems with Other Business Tools
To achieve full operational efficiency, work order systems should integrate seamlessly with other tools like ERP, MRP, and inventory management software.
This integration allows executives to have a comprehensive view of operations, ensuring that all relevant data is aligned and accessible, from resource availability to production schedules.
By following these best practices, executives can streamline their work order processes, leading to improved operational efficiency, reduced downtime, and enhanced productivity across the organization.
Leveraging Data Analytics to Improve Work Order Processes
Data analytics has become a powerful tool for organizations seeking to enhance their work order processes. By harnessing the vast amounts of data generated during work order management, businesses can gain valuable insights that drive efficiency, improve decision-making, and optimize resource allocation.
Here’s how leveraging data analytics can transform work order processes:
Identifying Trends and Patterns
Data analytics allows organizations to analyze historical work order data, revealing trends and patterns in task completion, resource utilization, and downtime.
By understanding these patterns, companies can identify recurring issues and root causes of delays, enabling them to implement targeted improvements.
For instance, if analytics reveal that specific equipment frequently requires repairs, proactive maintenance schedules can be established to minimize unplanned downtime.
Optimizing Resource Allocation
By analyzing data related to resource availability and usage, businesses can optimize how they allocate personnel, equipment, and materials to various work orders.
Data analytics helps executives understand which resources are overused or underutilized, allowing for more efficient scheduling and improved productivity.
This optimization ensures that the right resources are available for critical tasks, reducing delays and enhancing overall workflow.
Enhancing Predictive Maintenance
Data analytics can be instrumental in implementing predictive maintenance strategies. By analyzing equipment performance data, businesses can predict when machinery is likely to fail or require maintenance.
This proactive approach minimizes unexpected breakdowns and reduces the frequency of emergency work orders, allowing organizations to schedule maintenance at convenient times and extend the lifespan of their assets.
Improving Work Order Prioritization
With insights gained from data analytics, organizations can enhance their work order prioritization processes.
By assessing the impact of different tasks on overall operations, companies can prioritize work orders based on factors such as urgency, potential impact on productivity, and resource availability.
This ensures that critical tasks are addressed promptly, leading to smoother operations and reduced downtime.
Streamlining Workflow Processes
Data analytics provides insights into workflow efficiencies and bottlenecks in the work order process. By mapping out the entire work order lifecycle and analyzing where delays occur, organizations can streamline processes and eliminate inefficiencies.
For example, if data shows that approvals take too long, businesses can automate the approval process or establish clearer guidelines to speed up decision-making.
Enhancing Reporting and Performance Metrics
With data analytics, organizations can create detailed reports and dashboards that visualize key performance indicators (KPIs) related to work orders.
These analytics enable executives to monitor task completion times, labor costs, and resource utilization in real-time.
By continuously tracking performance metrics, businesses can make informed decisions and adapt their strategies to enhance operational efficiency.
Facilitating Continuous Improvement
The insights gained from data analytics empower organizations to adopt a culture of continuous improvement. By regularly reviewing performance data, businesses can identify areas for enhancement and implement changes to their work order processes. This iterative approach fosters a proactive mindset among employees, encouraging them to seek innovative solutions and efficiencies.
Enhancing Customer Satisfaction
Efficient work order management directly impacts customer satisfaction. By leveraging data analytics to improve response times and the quality of service delivery, organizations can enhance the overall customer experience.
Customers benefit from timely and accurate service, which can lead to increased customer loyalty and repeat business.
Benchmarking Against Industry Standards
Data analytics allows organizations to benchmark their work order processes against industry standards and competitors. By understanding where they stand in relation to peers, businesses can identify areas for improvement and adopt best practices from leading organizations. This benchmarking process supports strategic decision-making and helps organizations stay competitive in the marketplace.
In conclusion, leveraging data analytics in work order management not only drives efficiency but also enhances decision-making and overall business performance. By harnessing data insights, organizations can optimize their workflows, reduce costs, and ultimately improve service delivery, positioning themselves for long-term success.
The Role of AI and Automation in Modern Work Order Systems
In today’s fast-paced business environment, the integration of Artificial Intelligence (AI) and automation into work order systems has become essential for enhancing efficiency and streamlining operations.
These advanced technologies offer significant advantages, transforming how organizations manage tasks, allocate resources, and ensure operational excellence.
Here’s a closer look at the critical role AI and automation play in modern work order systems:
Automating Routine Tasks
AI and automation significantly reduce the burden of repetitive and mundane tasks associated with work order management. By automating processes such as order creation, assignment, and notifications, organizations can minimize human error and speed up workflow.
This automation ensures that work orders are generated promptly and assigned to the right personnel without manual intervention, freeing employees to focus on higher-value tasks.
Intelligent Work Order Routing
AI-powered systems can analyze various factors—such as employee skill sets, workload, and equipment availability—to intelligently route work orders to the most suitable team members.
This capability ensures that tasks are assigned to personnel best equipped to handle them, optimizing efficiency and improving the likelihood of timely completion. Additionally, this intelligent routing reduces the risk of overburdening certain team members while underutilizing others.
Predictive Analytics for Maintenance and Operations
AI enhances work order systems through predictive analytics, which helps organizations anticipate equipment failures and maintenance needs.
By analyzing historical data and identifying patterns, AI can forecast when machines are likely to require maintenance or are at risk of failure.
This proactive approach enables businesses to schedule preventive maintenance and reduces unplanned downtime, ultimately improving operational efficiency.
Enhanced Data Insights and Reporting
AI can process vast amounts of data quickly and accurately, offering organizations valuable insights into their work order processes. By leveraging machine learning algorithms, businesses can analyze work order completion times, resource utilization, and cost data to identify trends and areas for improvement.
These insights enable managers to make informed decisions based on real-time data rather than relying on guesswork or outdated information.
Natural Language Processing (NLP) for Communication
Natural Language Processing (NLP), a branch of AI, enhances communication within work order systems. Employees can interact with the system using natural language, whether through voice commands or text.
This capability allows for quick updates, inquiries, and feedback regarding work orders, making it easier for team members to engage with the system and access the information they need.
This improves overall workflow and reduces the time spent on administrative tasks.
Real-Time Monitoring and Alerts
AI and automation provide real-time monitoring capabilities for work order systems, enabling organizations to track progress and performance continuously.
Automated alerts can notify managers and team members about important milestones, delays, or issues that require immediate attention.
This real-time visibility fosters accountability and ensures that work orders are completed on time, contributing to overall operational efficiency.
Integration with IoT Devices
The integration of AI and automation with Internet of Things (IoT) devices enhances work order management by providing real-time data from connected equipment.
For instance, sensors can monitor machine performance and send alerts when maintenance is needed, automatically generating work orders based on predefined thresholds. This seamless integration allows for more effective resource allocation and minimizes downtime.
Improving Customer Experience
AI-driven work order systems can also enhance customer satisfaction. By automating the work order process and providing real-time updates, customers can receive timely information about their service requests.
This transparency fosters trust and builds stronger relationships with clients, as they can track the progress of their requests and expect timely resolutions.
Facilitating Continuous Improvement
AI systems can identify inefficiencies and suggest process improvements based on data analysis. By continuously learning from past performance and outcomes, AI can recommend adjustments to workflows, resource allocation, and scheduling. This iterative improvement process helps organizations adapt to changing needs and ensures they remain competitive in the market.
In conclusion, the role of AI and automation in modern work order systems cannot be overstated. These technologies enhance efficiency, improve decision-making, and foster a culture of continuous improvement.
By leveraging AI and automation, organizations can streamline their operations, optimize resource utilization, and ultimately drive better business outcomes. Embracing these advancements positions companies for success in an increasingly competitive landscape.
Executive Strategies for Long-Term Work Order Optimization
Optimizing work order processes is not just a one-time initiative; it requires ongoing strategies that align with an organization’s long-term goals. Executives play a critical role in driving these strategies to enhance efficiency, reduce costs, and improve service delivery.
Here are some key strategies that executives can implement to ensure sustained work order optimization:
Foster a Culture of Continuous Improvement
Creating an organizational culture that prioritizes continuous improvement is essential for long-term success in work order optimization. Executives should encourage teams to regularly assess their processes, identify inefficiencies, and suggest improvements.
This proactive mindset empowers employees at all levels to take ownership of their work, leading to innovative solutions and sustained performance enhancements.
Invest in Training and Development
To optimize work order processes effectively, organizations must equip their employees with the necessary skills and knowledge.
Executives should prioritize training and development programs that focus on best practices in work order management, as well as the use of new technologies.
Well-trained employees are more likely to perform efficiently, reduce errors, and contribute to overall process improvement.
Leverage Technology and Automation
Investing in advanced technologies, such as AI and automation, is crucial for optimizing work order processes over the long term.
Executives should assess their current systems and identify opportunities to integrate automation tools that streamline tasks, enhance communication, and provide real-time data analytics.
Embracing technology not only improves efficiency but also positions organizations to adapt to future changes in the industry.
Implement Data-Driven Decision Making
Data analytics should be at the core of work order optimization strategies. Executives must ensure that data collection and analysis are integrated into work order processes.
By leveraging key performance indicators (KPIs) and historical data, organizations can make informed decisions regarding resource allocation, task prioritization, and process improvements. This data-driven approach enhances transparency and accountability across the organization.
Establish Clear Communication Channels
Effective communication is vital for optimizing work order management. Executives should implement clear communication channels that facilitate information sharing among team members, departments, and stakeholders.
This includes providing access to real-time updates on work order status, progress, and challenges. Open lines of communication help teams collaborate more effectively and ensure that tasks are completed on time.
Regularly Review and Adjust Workflows
Long-term work order optimization requires regular reviews of workflows to identify inefficiencies and bottlenecks.
Executives should establish a systematic approach to evaluate work order processes periodically, ensuring that they remain aligned with organizational goals.
This includes soliciting feedback from employees who interact with the systems daily and making necessary adjustments based on their insights.
Emphasize Preventive Maintenance
Preventive maintenance strategies play a critical role in optimizing work order processes. Executives should prioritize scheduling regular maintenance tasks to reduce unexpected equipment failures and minimize emergency work orders.
By investing in preventive measures, organizations can extend the lifespan of assets, improve operational efficiency, and lower overall maintenance costs.
Encourage Cross-Department Collaboration
Work order optimization often requires input and collaboration from multiple departments. Executives should encourage cross-departmental collaboration to ensure that all stakeholders contribute to the optimization process.
This collaboration allows for a comprehensive understanding of how different functions impact work orders and enables organizations to identify opportunities for improvement.
Benchmark Against Industry Standards
Regularly benchmarking work order processes against industry standards helps organizations identify areas for improvement and adopt best practices.
Executives should stay informed about emerging trends and innovations in work order management, ensuring their organizations remain competitive.
This benchmarking process provides valuable insights into areas where adjustments can lead to enhanced efficiency.
Set Long-Term Goals and Metrics
Establishing clear long-term goals and associated metrics for work order optimization is essential for measuring progress and success.
Executives should define specific objectives, such as reducing lead times, minimizing costs, or improving customer satisfaction, and regularly track performance against these goals.
This structured approach enables organizations to stay focused on their optimization efforts and make data-driven adjustments as needed.
By implementing these executive strategies, organizations can achieve long-term work order optimization, leading to improved operational efficiency, reduced costs, and enhanced customer satisfaction.
Embracing a culture of continuous improvement and leveraging technology will position businesses for success in an increasingly competitive landscape.
Key Performance Indicators (KPIs) for Measuring Work Order Efficiency
Measuring the efficiency of work orders is essential for organizations aiming to optimize their operations and improve overall productivity. Key Performance Indicators (KPIs) provide valuable insights into how well work order processes are functioning and highlight areas for improvement.
Here are some critical KPIs that executives and managers can use to evaluate work order efficiency:
Work Order Cycle Time
This KPI measures the total time taken from the creation of a work order to its completion. A shorter cycle time indicates higher efficiency, while longer cycle times may signal bottlenecks in the process. Tracking cycle time helps organizations identify delays and optimize workflows to enhance overall performance.
First-Time Fix Rate (FTFR)
The First-Time Fix Rate measures the percentage of work orders completed successfully on the first attempt without the need for rework or follow-up visits. A high FTFR indicates effective troubleshooting and resource allocation, while a low FTFR may suggest issues with training, communication, or resource management.
Work Order Backlog
This KPI tracks the number of work orders that remain pending or unresolved over a specific period. A growing backlog can indicate resource constraints or inefficiencies in the work order process. Monitoring the backlog helps organizations prioritize tasks and allocate resources effectively to reduce delays.
Resource Utilization Rate
The Resource Utilization Rate measures how efficiently personnel and equipment are being utilized to complete work orders. By comparing the actual hours worked against available hours, organizations can identify underutilized resources and make necessary adjustments to improve efficiency.
Work Order Completion Rate
This KPI calculates the percentage of work orders completed within a given time frame compared to the total number of work orders created. A high completion rate indicates that the organization is effectively managing its workload and meeting operational goals.
Cost per Work Order
Measuring the total cost associated with completing a work order, including labor, materials, and overhead, provides insights into the financial efficiency of the work order process. Organizations can use this KPI to identify areas where costs can be reduced, ultimately improving profitability.
Repeat Work Orders
This KPI tracks the percentage of work orders that are reopened or created again within a specific time frame due to unresolved issues. A high percentage of repeat work orders suggests underlying problems that need to be addressed, such as insufficient training or inadequate resources.
Customer Satisfaction Score
Measuring customer satisfaction related to the completion of work orders provides valuable insights into the effectiveness of the process. Gathering feedback from customers can help organizations identify strengths and weaknesses in their service delivery and make necessary improvements to enhance satisfaction.
Mean Time to Repair (MTTR)
MTTR measures the average time taken to repair equipment or complete a work order after a failure occurs. This KPI is critical for assessing responsiveness and effectiveness in addressing maintenance issues. A lower MTTR indicates a more efficient work order process and better resource management.
Compliance Rate
This KPI tracks the percentage of work orders that are completed in compliance with regulatory standards, safety protocols, and company policies. A high compliance rate indicates that the organization is effectively managing risks and adhering to required practices, which is essential for maintaining operational integrity.
By closely monitoring these KPIs, organizations can gain valuable insights into their work order processes, identify areas for improvement, and implement strategies to enhance efficiency.
Regularly evaluating performance against these indicators ensures that organizations remain agile and responsive to evolving operational demands.
How Deskera MRP Can Help You Streamline Work Orders
Deskera MRP (Material Requirements Planning) is an essential tool for organizations looking to streamline their work order processes. By integrating various functions within the manufacturing and inventory management landscape, Deskera MRP enhances efficiency, reduces errors, and improves overall productivity.
Here’s how Deskera MRP can help you streamline work orders:
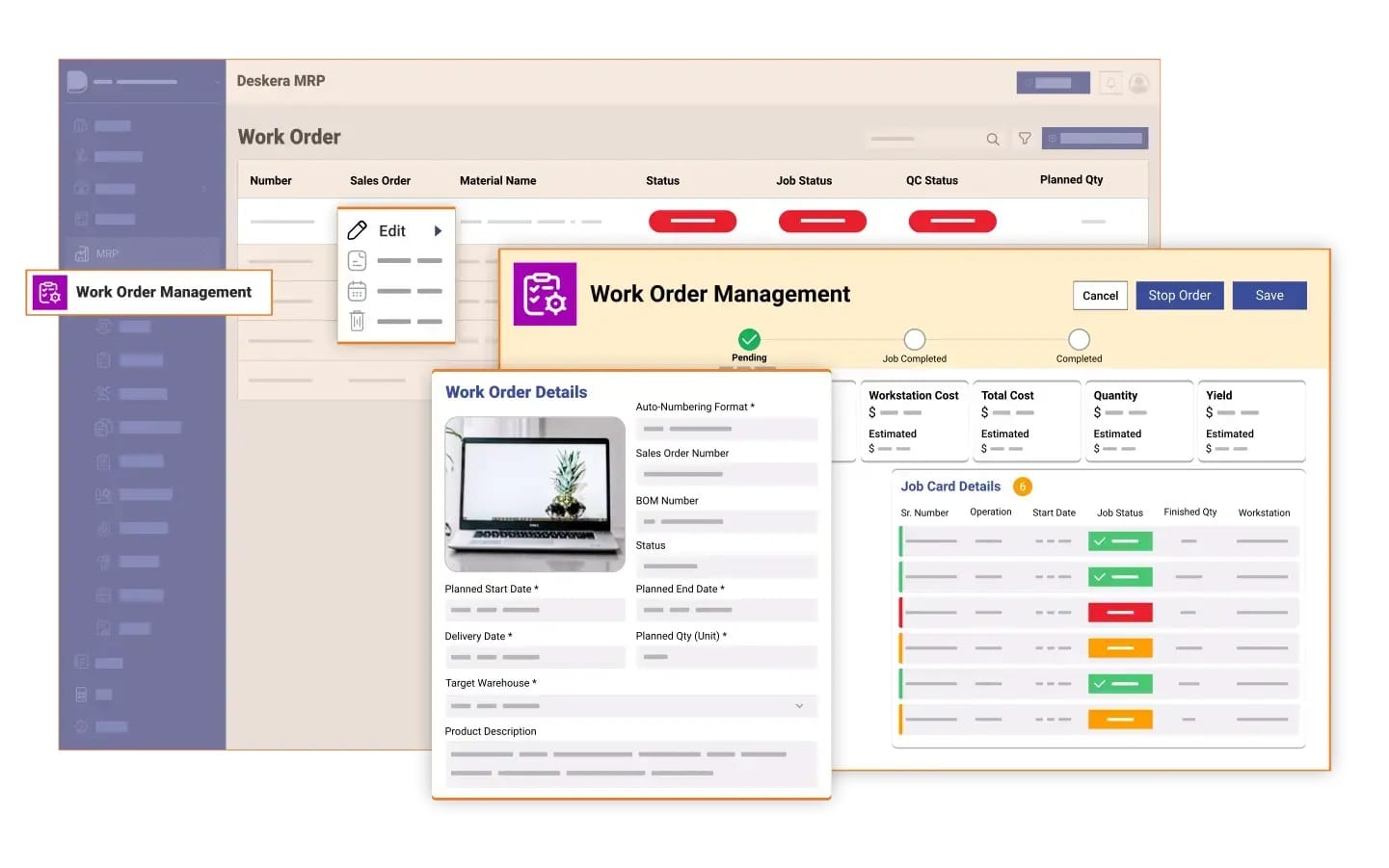
Automated Work Order Creation
Deskera MRP automates the work order creation process based on demand forecasts, inventory levels, and production schedules. This automation reduces the time and effort spent on manual entries, minimizes errors, and ensures that work orders are generated promptly, keeping production on track.
Real-Time Inventory Tracking
With real-time inventory visibility, Deskera MRP allows you to monitor stock levels and availability as work orders are processed. This capability helps in accurately determining whether you have the necessary materials on hand, reducing delays and ensuring that production can proceed smoothly without interruptions.
Streamlined Production Scheduling
Deskera MRP provides tools for effective production scheduling by aligning work orders with resource availability and production capacity. By optimizing schedules, organizations can minimize downtime, reduce lead times, and enhance overall workflow efficiency.
Enhanced Communication and Collaboration
The platform promotes better communication between teams by providing a centralized system for work order information. All stakeholders, from production teams to inventory managers, can access the same data, ensuring that everyone is on the same page regarding work order status, priorities, and requirements.
Prioritization of Work Orders
Deskera MRP enables users to prioritize work orders based on various factors such as customer demand, production capacity, and deadlines. This prioritization helps ensure that critical tasks are completed first, improving service levels and customer satisfaction.
Integrated Workflow Management
Deskera MRP integrates workflow management tools that allow organizations to define and track the steps involved in completing each work order. This visibility helps identify bottlenecks or inefficiencies in the workflow, enabling teams to make necessary adjustments and improve overall productivity.
Real-Time Reporting and Analytics
The platform offers robust reporting capabilities that provide insights into work order performance metrics, such as cycle times, completion rates, and resource utilization. By analyzing this data, organizations can identify trends, spot inefficiencies, and make informed decisions to optimize their work order processes.
Preventive Maintenance Scheduling
Deskera MRP facilitates the scheduling of preventive maintenance activities to reduce unexpected equipment failures that can disrupt work orders. By proactively managing maintenance schedules, organizations can ensure that machinery and equipment are in optimal condition, minimizing downtime.
Scalability and Adaptability
As businesses grow, their work order needs may change. Deskera MRP is designed to scale with your organization, allowing for the addition of new users, features, and functionalities as needed. This adaptability ensures that the system continues to meet your evolving operational requirements.
User-Friendly Interface
Deskera MRP features an intuitive user interface that simplifies navigation and enhances user experience. This ease of use promotes quicker onboarding and adoption, allowing teams to focus on streamlining work orders rather than navigating complex software.
Key Takeaways
- Work orders are essential documents that facilitate the planning, execution, and tracking of tasks within an organization. A clear understanding of their purpose and function is crucial for optimizing business operations.
- Work orders play a vital role in enhancing operational efficiency, improving communication, and ensuring accountability, ultimately contributing to better resource allocation and customer satisfaction.
- Organizations often face challenges such as inefficiencies, lack of real-time visibility, and communication gaps with traditional work order systems. Addressing these challenges is key to achieving streamlined processes.
- Streamlining work order processes leads to reduced lead times, improved resource utilization, and enhanced productivity, allowing organizations to respond more effectively to customer demands and operational changes.
- Leveraging technology, such as cloud-based software and automated systems, can significantly enhance work order management by providing real-time data, improving communication, and facilitating better decision-making.
- Executives should implement best practices such as establishing clear processes, prioritizing communication, and fostering a culture of continuous improvement to effectively streamline work order management.
- Utilizing data analytics enables organizations to gain insights into work order performance, identify trends, and make informed decisions that drive process optimization and operational efficiency.
- AI and automation can enhance work order processes by reducing manual tasks, minimizing errors, and providing predictive insights, leading to more efficient and agile operations.
- Developing long-term strategies that focus on continuous assessment, employee training, and process improvement can help executives ensure sustainable work order optimization and operational excellence.
- Establishing relevant KPIs allows organizations to measure work order efficiency, identify bottlenecks, and implement targeted improvements that enhance productivity and performance.
- By utilizing Deskera MRP, organizations can significantly enhance their work order processes, leading to improved operational efficiency, reduced lead times, and higher customer satisfaction. The comprehensive features offered by Deskera MRP empower businesses to adapt to changing demands and stay competitive in today’s dynamic market environment.
Related Articles
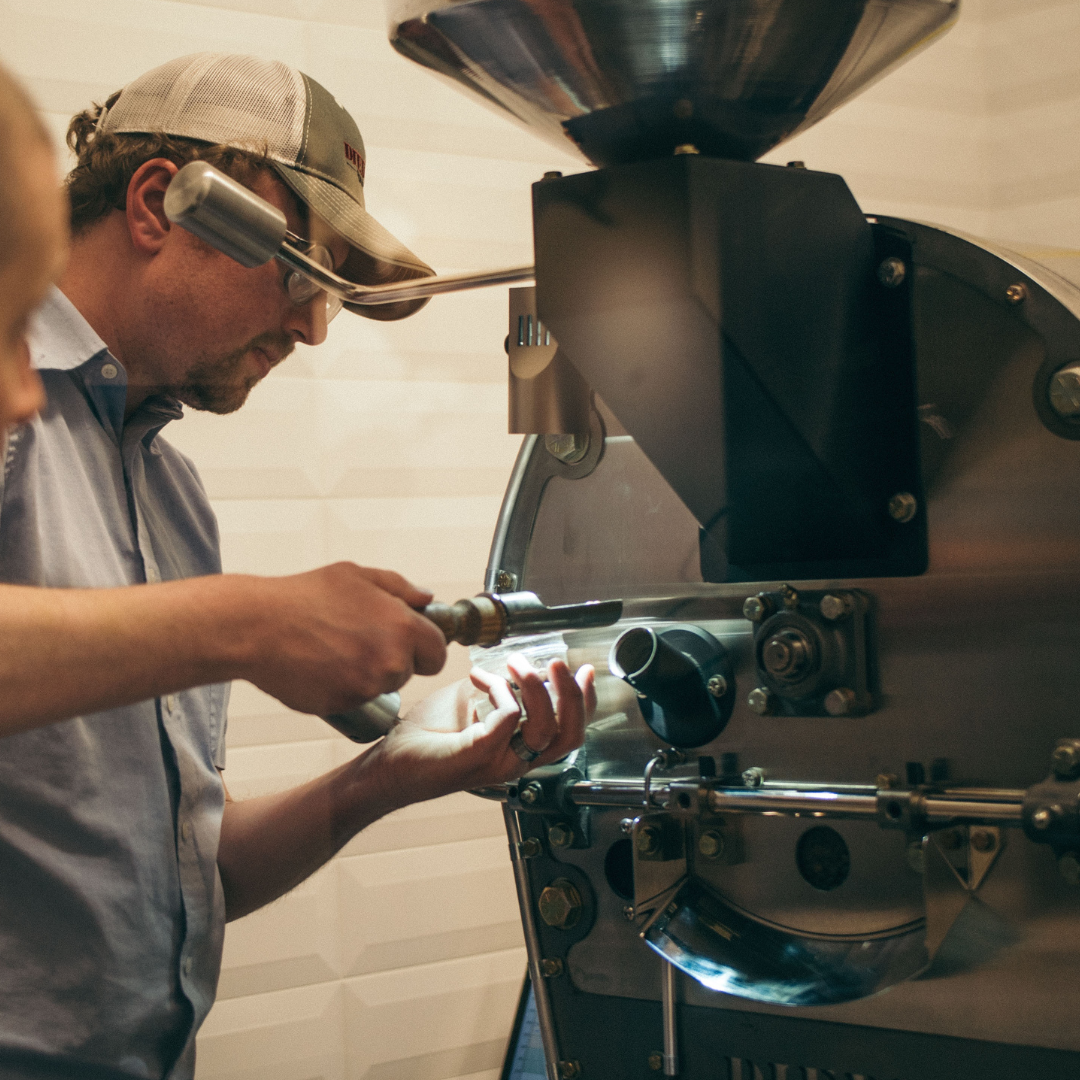
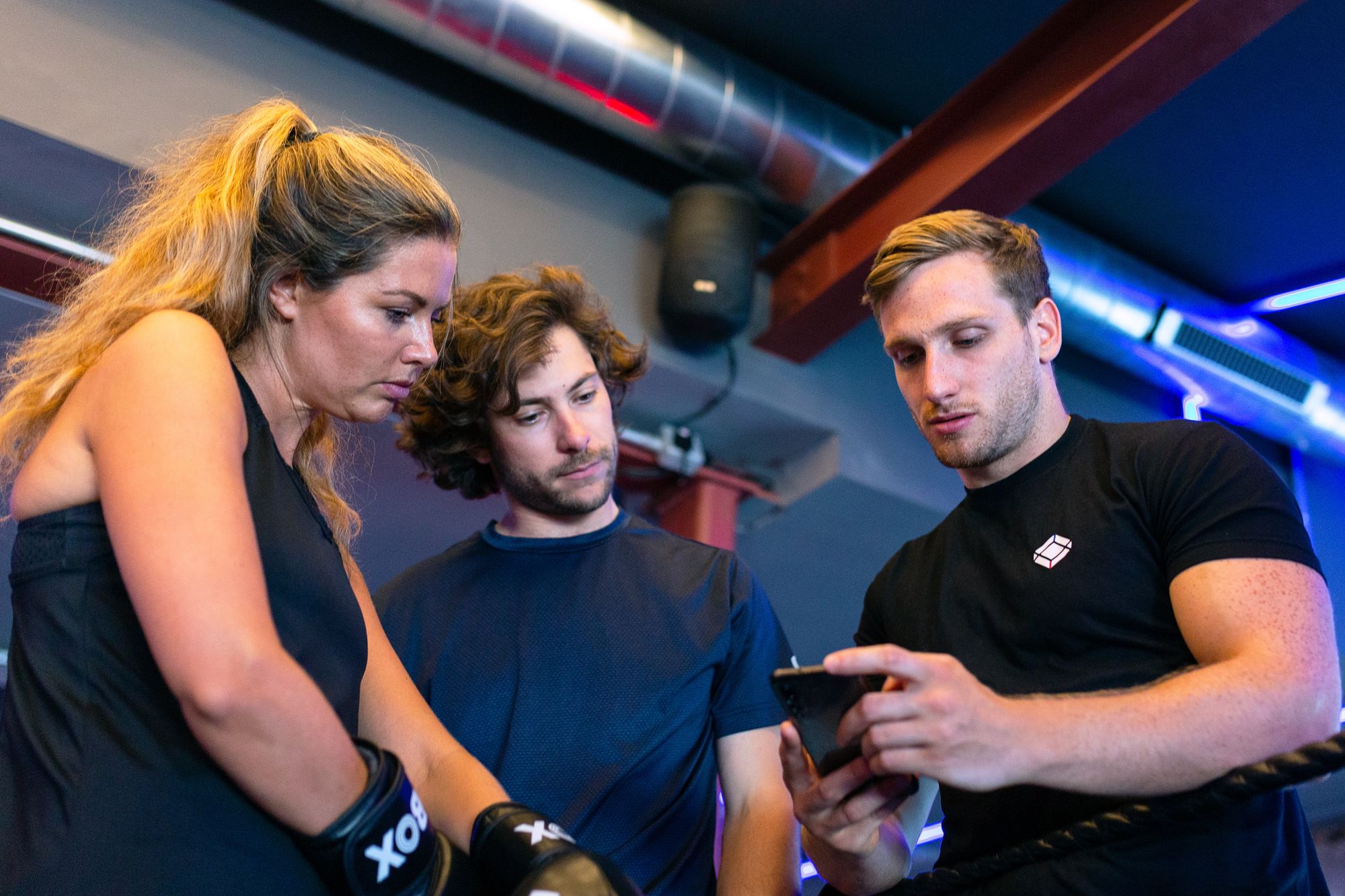
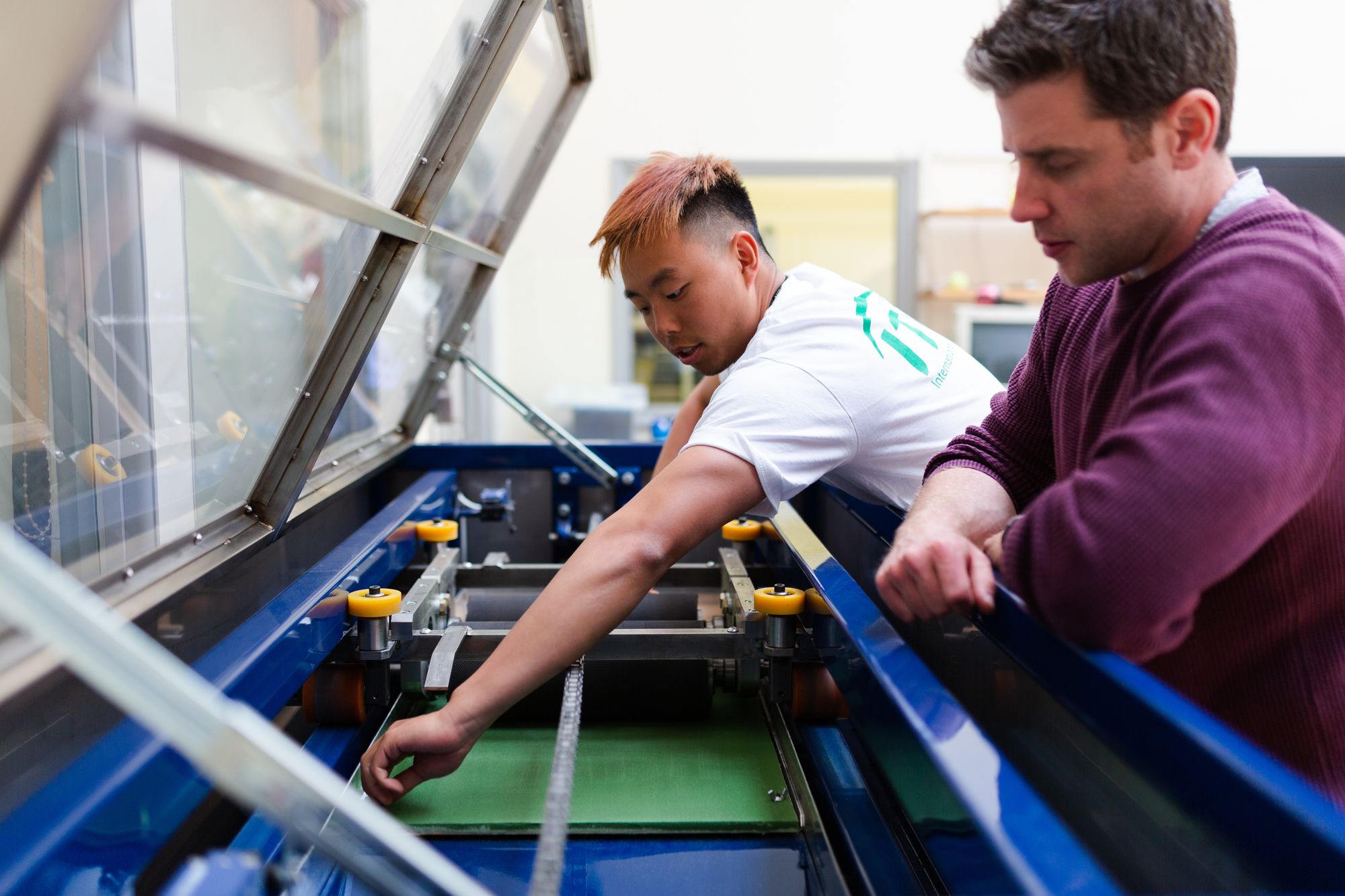

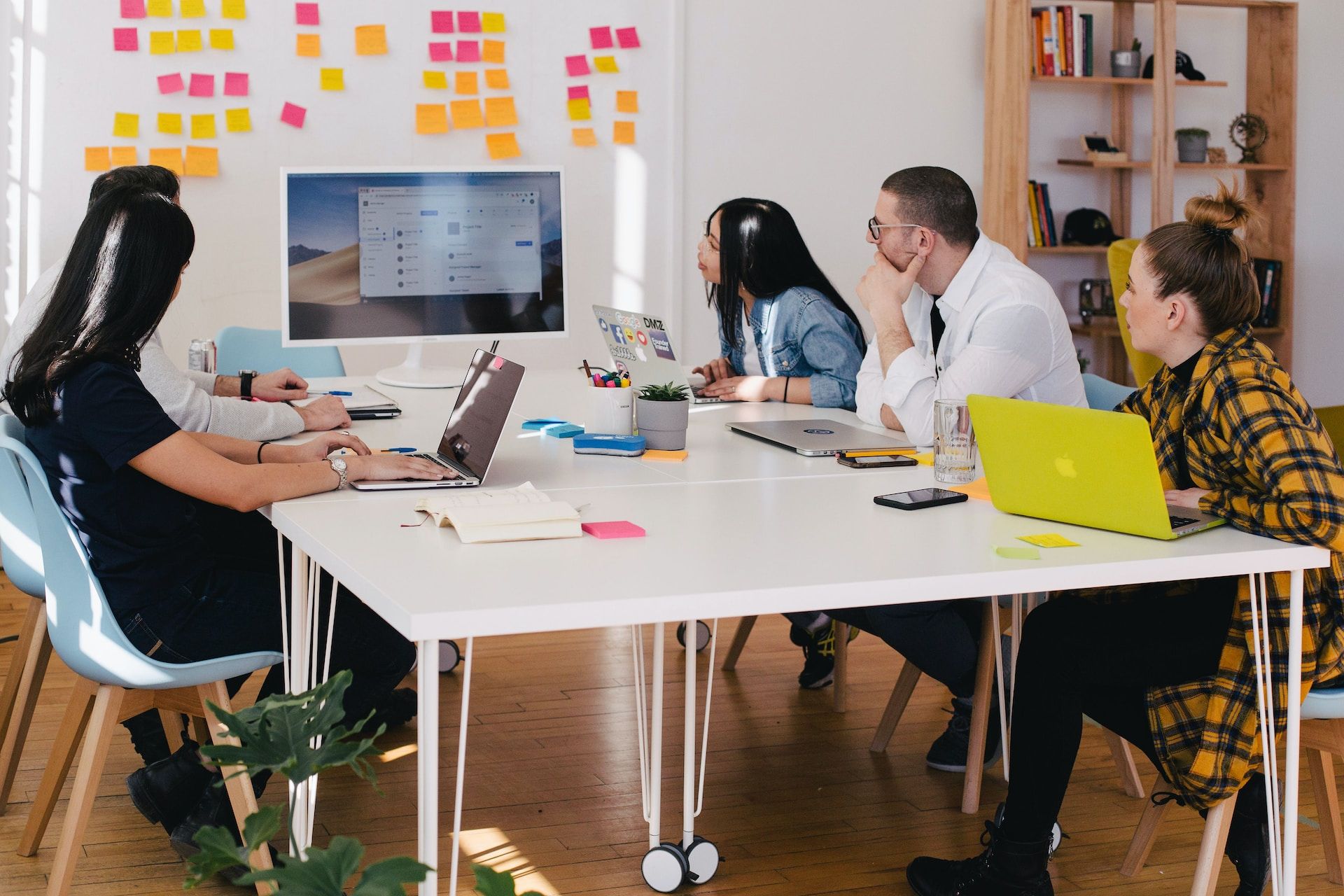
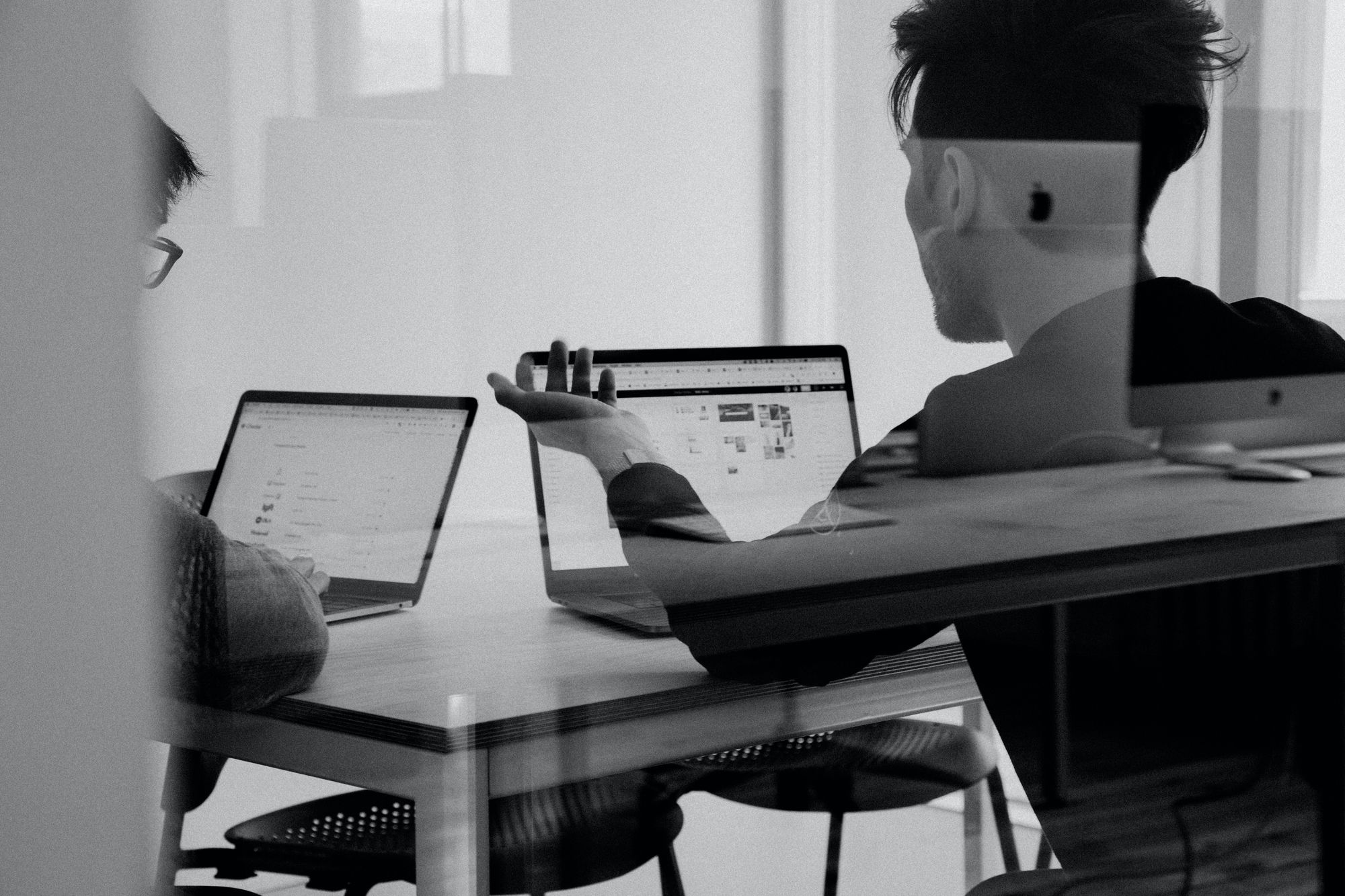