In the world of manufacturing, projects lie at the heart of innovation, growth, and competitiveness. Whether it's the development of new products, the optimization of manufacturing processes, or the expansion of production facilities, these projects are pivotal in achieving organizational goals. However, managing the financial aspects of these projects can be a formidable challenge, requiring a specialized and meticulous approach.
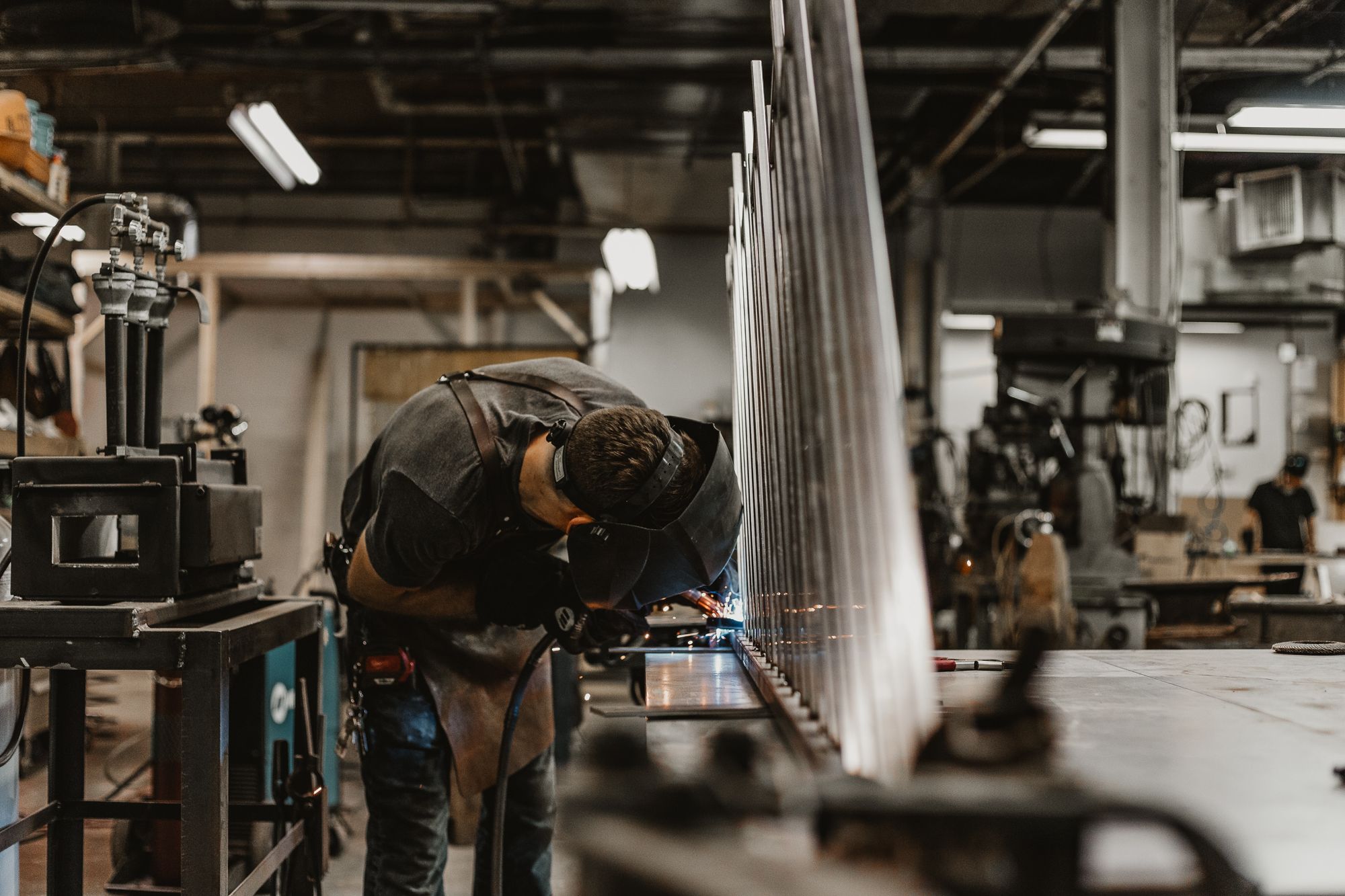
Manufacturing projects come in various forms, from research and development initiatives to process improvements and capital investments. Regardless of the project's nature, effective project accounting is the compass that guides decision-makers through the financial terrain. It ensures that resources are allocated efficiently, budgets are adhered to, compliance is maintained, and project outcomes are financially viable.
Whether you are a seasoned finance professional, a project manager, or an executive in a manufacturing organization, this guide aims to provide you with the knowledge and insights needed to excel in project accounting. It is a resource designed to empower you to make informed decisions, mitigate risks, enhance profitability, and drive the success of your manufacturing projects.
The topics covered in this article are:
- What is Project Accounting?
- All About Manufacturing Organizations
- How Does Project Accounting Differ from Regular Accounting in Manufacturing?
- Why is Project Accounting Important in Manufacturing?
- Types of Manufacturing Projects
- Who Needs Project Accounting?
- Core Project Accounting Processes
- Critical Phases of Manufacturing Project Accounting
- Best Practices of Manufacturing Project Accounting
- Forecasting in Manufacturing Project Accounting
- Integration in Manufacturing Project Accounting
- Benefits of Manufacturing Project Accounting
- Challenges Associated with Manufacturing Project Accounting
- Strategies to Overcome the Challenges Associated with Manufacturing Project Accounting
- Who is Responsible for Project Accounting in a Manufacturing Organization?
- How Can Project Accounting in Manufacturing Contribute to Sustainability Initiatives?
- How Can Project Accounting Help with Economic Uncertainty Management?
- What Role Does Cybersecurity Play in Manufacturing Project Accounting?
- How Can Manufacturing Organizations Adapt to Remote Work Collaboration in Project Accounting?
- Future Trends in Manufacturing Project Accounting
- How can Deskera Help You with Project Accounting?
- Key Takeaways
- Related Articles
What is Project Accounting?
Project accounting is a specialized branch of accounting that focuses on the financial management and reporting of individual projects or contracts within an organization. It involves tracking and analyzing all financial aspects associated with a specific project, from budgeting and cost tracking to revenue recognition and reporting.
Project accounting provides detailed insights into the financial performance of each project, helping businesses make informed decisions, manage resources effectively, and ensure the profitability of their projects.
This approach is particularly important for industries and businesses that undertake multiple projects with varying budgets and complexities, such as construction, consulting, research and development, and software development.
Key aspects of project accounting include:
- Cost Tracking: Project accountants monitor and record all costs associated with a project, including labor, materials, equipment, subcontractor expenses, and overhead. This helps in determining the total cost of the project.
- Revenue Recognition: Project accounting also involves recognizing revenue associated with a specific project. Revenue may be recognized as milestones are achieved, services are provided, or products are delivered, depending on the terms of the contract.
- Budget Management: Project accountants compare actual project costs and revenues against the budgeted amounts. This helps in identifying cost overruns, profitability, and the need for corrective actions.
- Resource Allocation: They allocate and manage resources such as labor and materials efficiently to ensure that projects stay on track and within budget.
- Compliance: Ensuring compliance with accounting standards, tax regulations, and contractual agreements is crucial in project accounting to avoid legal and financial risks.
- Reporting: Project accountants generate financial reports and financial statements specific to each project, providing stakeholders with detailed insights into the financial performance of individual projects.
- Forecasting: By analyzing historical data and project trends, project accountants can make informed forecasts about future projects, allowing organizations to plan and allocate resources effectively.
- Billing and Invoicing: In industries where projects are billed to clients or customers on a time and materials basis or based on project milestones, project accountants generate invoices and track payments.
- Profitability Analysis: Project accounting helps assess the profitability of each project, enabling organizations to make strategic decisions about which types of projects to pursue and which to avoid.
- Integration: Project accounting systems are often integrated with broader financial accounting systems to ensure consistency and accuracy in financial reporting across the organization.
Overall, project accounting provides businesses with a granular view of their project-related financial data, helping them make informed decisions, manage risks, and optimize resource allocation for better project outcomes. It is a valuable tool for organizations that rely on projects as a significant part of their business operations.
All About Manufacturing Organizations
Manufacturing organizations are enterprises that engage in the production of physical goods through various processes, including machining, assembly, chemical processing, and more.
These organizations play a pivotal role in the global economy, producing a wide range of products from automobiles and electronics to food and pharmaceuticals.
Here's an overview of key aspects of manufacturing organizations:
1.Types of Manufacturing:
- Discrete Manufacturing: This involves the production of distinct items, such as automobiles, electronics, and appliances, typically in small quantities or batches.
- Process Manufacturing: In process manufacturing, products are created through chemical or biological processes, often involving continuous production, such as in the pharmaceutical or food industries.
- Make-to-Stock (MTS) vs. Make-to-Order (MTO): Some manufacturing organizations produce goods to stock them on the market (MTS), while others only start production once they receive specific customer orders (MTO).
2.Production Processes:
- Assembly Line Production: A common method for mass production, where products move along a conveyor belt, with each station adding specific components or performing tasks.
- Lean Manufacturing: Emphasizes minimizing waste and improving efficiency by eliminating non-value-added activities.
- Just-In-Time (JIT) Manufacturing: A method to reduce inventory costs by producing items only as they are needed, reducing the need for stockpiling inventory.
- Custom Manufacturing: Some manufacturing organizations specialize in creating unique, custom-made products tailored to individual customer requirements.
3.Supply Chain Management: Manufacturing organizations rely on efficient supply chain management to procure raw materials, manage inventory, and distribute finished products to customers.
4.Quality Control: Ensuring product quality and consistency is paramount. Quality control processes, such as Six Sigma and Total Quality Management (TQM), help maintain high-quality standards.
5.Technology and Automation: Many manufacturing organizations employ advanced technologies, including robotics, computer-aided design (CAD), computer-aided manufacturing (CAM), and Internet of Things (IoT) devices, to improve production efficiency and product quality.
6.Safety and Compliance: Manufacturing organizations must adhere to safety regulations to protect workers and consumers. Compliance with environmental and industry-specific regulations is also critical.
7.Globalization: Manufacturing organizations often operate in a global marketplace, sourcing materials and selling products internationally, which brings both opportunities and challenges related to logistics, currency exchange, and international regulations.
8.Workforce: Manufacturing requires a diverse workforce, from machine operators and technicians to engineers and managers. Employee training and development are vital for maintaining and improving manufacturing processes.
9.Sustainability: Many manufacturing organizations are increasingly focused on sustainability, aiming to reduce their environmental impact through eco-friendly practices and resource conservation.
10.Cost Management: Managing production costs, including labor, materials, and energy, is crucial for competitiveness and profitability in the manufacturing sector.
11.Innovation: Continuous innovation is essential to stay competitive. Manufacturers invest in research and development to create new products, improve existing ones, and streamline production processes.
12.Market Trends: Manufacturers monitor market trends and consumer preferences to adjust their product offerings and production strategies accordingly.
13.Regulatory Compliance: Meeting regulatory standards and certifications is crucial for ensuring product safety, quality, and market access.
Manufacturing organizations vary widely in terms of size, industry, and specialization. Some may focus on high-volume production, while others emphasize customization and craftsmanship.
Regardless of their specific niche, manufacturing organizations play a central role in producing the goods that drive economies and improve quality of life.
How Does Project Accounting Differ from Regular Accounting in Manufacturing?
Project accounting and regular accounting in manufacturing are distinct accounting methodologies designed to address different aspects of financial management within a manufacturing organization.
Here's how they differ:
Project Accounting in Manufacturing:
- Focus on Individual Projects: Project accounting primarily focuses on tracking and managing the financial aspects of individual projects or contracts within a manufacturing organization. Each project is treated as a separate entity with its own financial records and reporting.
- Cost Allocation by Project: Project accounting allocates costs specifically to each project, enabling precise tracking of project-related expenses, labor, materials, and overhead costs. This allocation is crucial for determining the profitability of individual projects.
- Revenue Recognition Variability: Revenue recognition in project accounting is often based on project progress or contractual milestones. Projects may have different revenue recognition criteria, making them distinct from regular accounting, where revenue is typically recognized based on a standard time frame.
- Budgeting and Forecasting: Project accounting places a strong emphasis on project-specific budgeting and forecasting. It involves creating detailed project budgets, continuously tracking actual costs against the budget, and adjusting projections as needed to ensure project profitability.
- Resource Allocation: Resource allocation in project accounting is project-centric, ensuring that labor, materials, and equipment are allocated efficiently to meet the specific needs of each project. This differs from regular manufacturing accounting, where resource allocation may be more generalized.
- Risk Management: Project accounting involves assessing and mitigating financial risks associated with individual projects. It focuses on identifying potential risks that could impact a project's financial performance.
- Customer Billing: In project accounting, the billing process is tailored to each project's terms and milestones. Invoices are generated based on the progress of the project or the completion of specific deliverables.
Regular Accounting in Manufacturing:
- Company-Wide Perspective: Regular accounting in manufacturing takes a holistic view of the entire manufacturing organization. It looks at the financial health and performance of the organization as a whole, rather than focusing on individual projects.
- Cost Aggregation: In regular accounting, costs are aggregated across all manufacturing activities, encompassing all projects and operational activities. This approach provides a consolidated view of overall costs.
- Steady Revenue Recognition: Revenue recognition in regular accounting is typically based on standard accounting principles and timing, such as the sale of manufactured goods. It follows established revenue recognition rules.
- General Budgeting: Budgeting and forecasting in regular accounting pertain to the organization's overall financial plan. It may involve setting annual budgets and forecasts that encompass all manufacturing activities.
- Resource Allocation: Resource allocation in regular manufacturing accounting often follows broader resource allocation strategies for the organization, rather than being project-specific.
- Risk Management: Risk management in regular accounting addresses broader financial risks that affect the entire organization, such as market risks, economic fluctuations, and strategic risks.
- Financial Reporting: Financial reporting in regular accounting provides a consolidated view of the organization's financial performance, including income statements, balance sheets, and cash flow statements for the entire organization.
In summary, project accounting in manufacturing focuses on managing the financial aspects of individual projects, tracking project-specific costs, and ensuring the profitability of each project.
Regular accounting in manufacturing, on the other hand, takes a broader perspective, consolidating financial data across the entire organization and providing a comprehensive view of its financial health.
Both approaches are essential for effective financial management within a manufacturing organization, as they serve different purposes and support different aspects of decision-making and reporting.
Why is Project Accounting Important in Manufacturing?
- Financial Control: Manufacturing projects can involve significant investments in terms of labor, materials, and equipment. Project accounting provides a structured way to monitor and control these expenses, helping organizations stay within budget and reduce the risk of cost overruns.
- Resource Optimization: Efficient allocation of resources is critical in manufacturing. Project accounting ensures that the right resources, including skilled labor and necessary materials, are allocated to each project, optimizing production efficiency.
- Profitability Assessment: Manufacturing organizations often engage in diverse projects, each with its own financial objectives. Project accounting allows for an accurate assessment of the profitability of each project, helping organizations make informed decisions about resource allocation and project prioritization.
- Resource Allocation and Management: Effective resource allocation and management are essential for meeting project timelines and quality standards. Project accounting assists in allocating resources based on project needs and tracking resource utilization.
- Billing and Invoicing: Manufacturing projects often require specific billing and invoicing practices. Project accounting helps in generating accurate invoices for customers, ensuring that billing aligns with project milestones and deliverables.
- Compliance and Reporting: Manufacturing organizations must comply with accounting standards, tax regulations, and industry-specific requirements. Project accounting facilitates compliance by providing a structured framework for accurate financial reporting.
- Risk Management: Manufacturing projects can be susceptible to various risks, such as supply chain disruptions or changes in project scope. Project accounting aids in identifying, managing, and mitigating these financial risks.
In the world of manufacturing, project accounting is a valuable tool that empowers organizations to maintain financial discipline, optimize resource allocation, assess project profitability, and ensure compliance.
By isolating and tracking the financial aspects of individual projects, manufacturing organizations can make informed decisions, control costs, and ultimately enhance their overall financial performance.
Types of Manufacturing Projects
Manufacturing organizations engage in various types of projects, each with its unique characteristics and objectives. These projects are integral to the manufacturing process and can impact a company's competitiveness and profitability.
Here are some common types of manufacturing projects:
New Product Development:
- Objective: Creating entirely new products or product variants to meet market demand or stay competitive.
- Example: Developing a new smartphone model with enhanced features.
Product Enhancement or Improvement:
- Objective: Enhancing existing products to improve quality, features, or cost-efficiency.
- Example: Updating a car model with better fuel efficiency and safety features.
Production Process Optimization:
- Objective: Streamlining and improving manufacturing processes to increase efficiency, reduce waste, and lower production costs.
- Example: Implementing lean manufacturing principles to reduce production cycle times.
Quality Improvement Initiatives:
- Objective: Enhancing product quality and consistency through quality control and process improvement.
- Example: Implementing Six Sigma principles to reduce defects in a manufacturing process.
Capacity Expansion:
- Objective: Increasing production capacity to meet growing demand or enter new markets.
- Example: Building a new factory or expanding an existing one to produce more units.
Cost Reduction Projects:
- Objective: Identifying and implementing cost-saving measures to reduce the overall cost of production.
- Example: Substituting expensive raw materials with more cost-effective alternatives.
Custom Manufacturing Projects:
- Objective: Producing unique, customized products tailored to specific customer requirements.
- Example: Manufacturing customized industrial machinery based on client specifications.
Supply Chain Optimization:
- Objective: Improving the efficiency of the supply chain by reducing lead times, optimizing inventory management, and enhancing supplier relationships.
- Example: Implementing just-in-time (JIT) inventory practices to minimize inventory holding costs.
Sustainability Initiatives:
- Objective: Implementing environmentally friendly practices and technologies to reduce the environmental impact of manufacturing operations.
- Example: Transitioning to renewable energy sources or recycling/reusing materials.
Facility Renovation or Modernization:
- Objective: Upgrading manufacturing facilities to improve safety, productivity, and compliance with regulatory standards.
- Example: Retrofitting a plant to meet modern safety and environmental regulations.
Compliance and Certification Projects:
- Objective: Ensuring compliance with industry-specific standards, certifications, and regulations.
- Example: Achieving ISO 9001 certification for quality management.
New Market Entry:
- Objective: Expanding into new geographic regions or markets, which may involve adapting products or production processes to meet local requirements.
- Example: Entering a foreign market with localized product versions.
Prototype Development:
- Objective: Creating prototypes of new products to test their functionality and feasibility before full-scale production.
- Example: Building a prototype of a new medical device for testing and validation.
Research and Development (R&D) Projects:
- Objective: Conducting research and development activities to innovate and create new technologies, materials, or products.
- Example: Researching advanced materials for use in aerospace components.
Efficiency and Automation Projects:
- Objective: Implementing automation and robotics to enhance production efficiency and reduce labor costs.
- Example: Integrating automated assembly lines for electronic devices.
These types of manufacturing projects can vary significantly in terms of scope, complexity, and duration. Manufacturing organizations often manage a combination of these projects to adapt to changing market dynamics, improve competitiveness, and drive innovation. Successful project management and project accounting are critical for achieving the desired outcomes in each of these project types.
Who Needs Project Accounting?
Project accounting is particularly valuable for organizations and industries where projects are a significant part of their business operations.
Here are some examples of who needs project accounting:
- Construction Companies: Construction firms often undertake multiple projects simultaneously, each with its own budget, timeline, and resource allocation. Project accounting helps them manage costs, track progress, and ensure profitability on each project.
- Consulting Firms: Consulting companies provide services to clients on a project basis. They need project accounting to accurately bill clients, manage project budgets, and assess the profitability of different consulting engagements.
- Engineering Firms: Engineering projects can be complex and involve substantial resources. Project accounting is crucial for tracking expenses, ensuring that projects stay within budget, and calculating revenues based on milestones or deliverables.
- Information Technology (IT) Services Providers: IT companies often work on software development projects, IT consulting, or system implementation. Project accounting helps them manage project finances, bill clients accurately, and assess project profitability.
- Research Organizations: Research institutions and organizations conducting research projects require project accounting to monitor and allocate funds, track expenses, and comply with grant and funding requirements.
- Manufacturing Companies: Manufacturing companies that engage in new product development or process improvement projects use project accounting to control costs, assess the return on investment, and manage project timelines.
- Advertising and Marketing Agencies: Advertising and marketing agencies often handle multiple client campaigns simultaneously. Project accounting helps them track costs, bill clients, and evaluate the effectiveness and profitability of each campaign.
- Event Management Companies: Event planners and organizers use project accounting to manage budgets, track expenses related to specific events, and ensure that events are financially viable.
- Nonprofit Organizations: Nonprofits engaged in various projects, such as community development or humanitarian aid, rely on project accounting to allocate funds, demonstrate financial accountability to donors, and ensure compliance with grant requirements.
- Government Agencies: Government agencies often undertake public infrastructure projects, and project accounting is essential to control costs, manage taxpayer funds, and ensure transparency in public spending.
- Architecture Firms: Architectural projects, including designing buildings and structures, involve project-specific budgets and resource allocation. Project accounting helps architects monitor costs and project profitability.
- Legal Firms: Some legal practices handle cases or projects that require specialized billing and financial tracking. Project accounting assists them in managing legal fees and expenses.
In summary, project accounting is relevant across various industries and organizations that manage multiple projects, contracts, or engagements. It helps ensure financial control, optimize resource allocation, maintain profitability, and meet regulatory and reporting requirements for each project.
Core Project Accounting Processes
Project accounting involves several key processes that enable organizations to effectively manage the financial aspects of individual projects within their operations. These processes help track project costs, revenues, and profitability, ensuring that projects stay within budget and meet their financial objectives.
Here are the core project accounting processes:
Budgeting and Cost Control
Budgeting and cost control are essential components of project accounting in manufacturing organizations. Effective budgeting helps organizations set financial expectations for a project, while cost control ensures that the project stays within budget.
Here's a closer look at budgeting and cost control in project accounting for manufacturing organizations:
Budgeting in Project Accounting:
- Project Scope Definition: Before budgeting, clearly define the project scope, objectives, and deliverables. Understanding the project's requirements is crucial for accurate budgeting.
- Detailed Cost Estimation: Create a comprehensive list of all anticipated costs related to the project. This should include direct costs (e.g., labor, materials, subcontractors) and indirect costs (e.g., overhead, utilities).
- Resource Allocation: Allocate resources based on the project's requirements. Consider the number of labor hours, materials, and equipment needed for each phase of the project.
- Contingency Planning: Include a contingency fund in the budget to account for unexpected costs or scope changes. Contingencies are essential to handle unforeseen challenges without disrupting the project's financial plan.
- Budget Approval: Once the budget is prepared, it should undergo approval from relevant stakeholders, including project managers and finance teams.
- Baseline Budget: The approved budget serves as the project's baseline budget. Any changes or variations from this baseline should be closely monitored and documented.
Cost Control in Project Accounting:
- Real-Time Cost Tracking: Continuously track and record project expenses as they occur. Use project management software or accounting systems to maintain real-time cost visibility.
- Expense Allocation: Ensure that all project-related costs are accurately allocated to the project. This includes labor costs, materials, subcontractor expenses, and any indirect costs associated with the project.
- Variance Analysis: Regularly compare actual project expenses against the budget. Identify any cost variances and investigate the causes. Common tools like variance reports can help in this analysis.
- Change Management: If there are changes in project scope or requirements, document them thoroughly. Assess the impact of changes on the project budget and obtain necessary approvals before proceeding.
- Cost Control Measures: Implement cost control measures, such as setting spending limits, monitoring resource utilization, and conducting regular financial reviews, to prevent budget overruns.
- Scope Management: Keep a close eye on project scope. Uncontrolled scope changes can lead to additional costs. Ensure that any changes are well-documented and approved.
- Resource Efficiency: Continuously monitor resource usage to identify areas where resources can be used more efficiently. This includes optimizing labor, materials, and equipment usage.
- Contingency Management: If contingency funds are used, monitor their utilization and ensure that they are only used for genuine unforeseen circumstances.
- Communication: Maintain open and transparent communication among project managers, finance teams, and stakeholders regarding cost performance. Ensure that everyone is aware of the project's financial status.
- Corrective Actions: If cost overruns are detected, take prompt corrective actions to bring the project back within budget. This may involve revising the project plan, reallocating resources, or implementing cost-saving measures.
- Regular Reporting: Generate and share regular cost reports with project stakeholders. These reports should highlight cost performance against the budget and any actions taken to control costs.
- Lessons Learned: At the end of the project, conduct a post-project review to identify lessons learned and opportunities for improving budgeting and cost control processes in future projects.
Effective budgeting and cost control are critical to ensuring the financial success of manufacturing projects. They help organizations manage project finances, minimize financial risks, and deliver projects within the defined budget constraints, ultimately contributing to improved profitability and customer satisfaction.
Resource Allocation and Management
Resource allocation and management are essential aspects of project accounting in manufacturing organizations. Efficiently allocating and managing resources, including personnel, materials, and equipment, is crucial to meet project objectives, control costs, and ensure successful project outcomes.
Here's a detailed look at resource allocation and management in project accounting for manufacturing organizations:
Resource Allocation:
- Resource Planning: Before a project begins, manufacturing organizations must identify the resources required to complete the project successfully. This includes labor, materials, equipment, and any other assets or facilities.
- Resource Estimation: Estimate the quantities and types of resources needed for each phase of the project. For example, calculate the number of labor hours, the quantity of materials, or the equipment specifications required.
- Resource Scheduling: Develop a resource schedule that outlines when and how resources will be allocated throughout the project. This schedule should align with project milestones and timelines.
- Resource Procurement: If necessary, initiate the procurement process to acquire the required resources. This may involve sourcing materials, hiring additional staff, or renting equipment.
- Resource Assignment: Assign specific resources to each project task or phase. Ensure that individuals or teams responsible for different aspects of the project have access to the necessary resources.
- Resource Constraints: Consider any resource limitations or constraints that may affect the project. For example, if a critical piece of equipment is in high demand, it may require careful scheduling and coordination.
Resource Management:
- Resource Tracking: Implement systems and processes for tracking resource usage in real time. This includes monitoring labor hours, material consumption, equipment utilization, and associated costs.
- Resource Optimization: Continuously assess resource utilization to identify opportunities for optimization. Look for ways to improve efficiency, reduce waste, and minimize resource idle time.
- Resource Allocation Adjustments: Be prepared to adjust resource allocations as needed throughout the project. If one aspect of the project requires more resources than initially planned, redistribute resources accordingly.
- Resource Availability: Keep a close eye on resource availability and potential bottlenecks. Ensure that resources are available when needed to avoid delays in project execution.
- Resource Balancing: Balance resource allocation across multiple projects if the organization is simultaneously managing multiple manufacturing projects. Avoid overloading certain projects with resources while neglecting others.
- Resource Maintenance: Regularly maintain and service equipment to prevent breakdowns and downtime. Proper maintenance can reduce unexpected project delays.
- Resource Communication: Maintain clear communication among project teams, resource managers, and project managers. Ensure that everyone is aware of resource allocation and availability.
- Resource Costs: Track resource costs accurately, including labor costs, material costs, and equipment maintenance expenses. This information is essential for project accounting and cost control.
- Resource Forecasting: Use historical resource data and project performance metrics to forecast future resource needs accurately. This helps in proactive resource planning for upcoming projects.
- Resource Documentation: Keep detailed records of resource allocation and usage. This documentation is valuable for project accounting, audits, and future resource planning.
Effective resource allocation and management enable manufacturing organizations to optimize project performance, control costs, and ensure that projects are completed on time and within budget.
By aligning resource allocation with project needs and continuously monitoring and adjusting resource utilization, organizations can enhance their competitiveness and profitability in the manufacturing sector.
Client and Stakeholder Communication
Effective client and stakeholder communication is critical in project accounting for manufacturing organizations. Clear and transparent communication helps build trust, ensures alignment with project goals, and allows stakeholders to make informed decisions.
Here are key considerations for client and stakeholder communication in project accounting:
- Project Kickoff Meeting: Begin the project with a kickoff meeting that includes clients, project managers, project accountants, and relevant stakeholders. Discuss project objectives, scope, timelines, budgets, and reporting expectations.
- Project Updates and Progress Reporting: Provide regular project updates and progress reports to clients and stakeholders. These reports should include financial performance data, such as budget vs. actuals, revenue recognition, and cost breakdowns.
- Financial Reporting: Share financial reports that detail project financials, including income statements, balance sheets, and cash flow statements. Ensure these reports are easily understandable by non-financial stakeholders.
- Budget Variance Analysis: Explain budget variances and the reasons behind them. When there are significant deviations from the budget, discuss potential impacts on the project and mitigation strategies.
- Scope Changes and Change Orders: Clearly communicate any changes in project scope and their financial implications. Discuss change orders with clients and stakeholders and obtain necessary approvals.
- Risk and Issue Reporting: Communicate identified risks and issues related to project finances promptly. Discuss risk mitigation plans and seek input from stakeholders on risk management strategies.
- Revenue Recognition: Explain the revenue recognition method used for the project and provide updates on recognized revenue based on project milestones or other criteria.
- Resource Allocation and Utilization: Share information on resource allocation, including labor, materials, and equipment. Discuss how resources are being utilized to achieve project objectives.
- Client Billing and Invoicing: Ensure that client billing and invoicing are transparent and align with project progress and milestones. Address any billing inquiries promptly and provide supporting documentation.
- Client Feedback and Input: Encourage clients and stakeholders to provide feedback and input regarding project financials and accounting practices. Their insights can help improve project accounting processes.
- Compliance and Regulatory Updates: Keep clients and stakeholders informed of any changes in accounting standards, regulations, or compliance requirements that may affect project accounting practices.
- Regular Meetings and Check-Ins: Schedule regular meetings or check-ins with clients and stakeholders to discuss project financials, address concerns, and provide updates on financial performance.
- Transparency in Reporting: Maintain transparency in financial reporting by clearly presenting financial data, assumptions, and methodologies used in calculations. Avoid jargon and use easily understandable language.
- Conflict Resolution: Be prepared to address conflicts or disagreements related to project accounting in a constructive and transparent manner. Seek resolutions that are fair and in the best interest of the project.
- Documentation and Record-Keeping: Maintain accurate records of all financial transactions, contracts, change orders, and project communications. Documentation helps in resolving disputes and ensuring accountability.
- Adherence to Agreements: Ensure that project accounting practices align with the terms and agreements outlined in contracts and project charters. Any deviations should be communicated and agreed upon.
- End-of-Project Review: Conduct a final project review with clients and stakeholders, discussing financial performance, lessons learned, and recommendations for future projects.
Effective client and stakeholder communication in project accounting is not only about sharing data but also about fostering collaboration and trust. Regular, transparent, and proactive communication helps manufacturing organizations build strong client relationships and ensures that project stakeholders are well-informed and engaged throughout the project lifecycle.
Billing and Invoicing
Billing and invoicing are critical components of project accounting in manufacturing organizations, especially when projects involve the delivery of products or services to customers.
Proper billing and invoicing practices ensure that organizations receive timely payments for their work, maintain healthy cash flow, and accurately account for project-related revenues.
Here's an overview of billing and invoicing in manufacturing project accounting:
Billing in Manufacturing Project Accounting:
- Billing Methods: Manufacturing organizations may use various billing methods based on project types, customer agreements, and industry norms. Common billing methods include:
- Milestone Billing: Invoices are generated at predefined project milestones, such as project initiation, completion of specific phases, or delivery of key deliverables.
- Time and Materials (T&M) Billing: Billing is based on the actual hours worked by labor and the materials used in the project. Hourly rates and material costs are typically specified in the contract.
- Fixed-Price Billing: Invoices are issued at a predetermined fixed price for the entire project. This method is often used for well-defined projects with clear scopes.
- Contractual Agreements: Ensure that billing practices align with contractual agreements and terms negotiated with the customer. Contracts should clearly define billing milestones, rates, and payment terms.
- Progress Tracking: Monitor project progress to determine when billing milestones or deliverables have been met. Accurate progress tracking is essential for generating invoices at the right time.
- Documentation: Maintain thorough documentation of project-related activities, including work performed, materials used, and milestones achieved. This documentation supports billing accuracy and can be useful in case of disputes.
- Approval Process: Establish an internal approval process for billing. Invoices should be reviewed and approved by project managers or designated personnel to ensure accuracy and compliance with contractual terms.
Invoicing in Manufacturing Project Accounting:
- Invoice Generation: Once billing milestones are reached or project phases are completed, generate invoices promptly. Invoices should contain all relevant details, such as customer information, project details, billing amounts, and payment instructions.
- Accuracy: Ensure that all billed amounts are accurate and reflect the work or products delivered. Errors in invoicing can lead to payment delays and customer dissatisfaction.
- Timeliness: Send invoices to customers promptly upon reaching billing milestones. Clear communication regarding payment due dates and methods is essential.
- Clarity and Transparency: Invoices should be clear and easy to understand. Include a breakdown of charges, itemized costs, and any additional details requested by the customer.
- Payment Terms: Clearly specify payment terms, such as payment due dates, accepted payment methods, and any late payment penalties or discounts for early payments.
- Electronic Invoicing: Consider electronic invoicing (e-invoicing) methods, which can expedite the invoicing process, reduce errors, and enhance document security.
- Invoice Tracking: Implement a system to track the status of invoices, including when they were sent, when they are due, and when payments are received. This helps manage cash flow and follow up on outstanding payments.
- Customer Communication: Maintain open communication with customers regarding invoicing and payment status. Address any inquiries or concerns promptly to build strong customer relationships.
- Payment Reconciliation: Reconcile payments received with invoiced amounts and project records. Ensure that payments match the agreed-upon terms and milestones.
- Credit Control: Monitor outstanding invoices and implement credit control measures for overdue payments. This may involve sending reminders, assessing late fees, or initiating collections procedures as necessary.
Effective billing and invoicing practices in manufacturing project accounting contribute to financial stability, customer satisfaction, and accurate financial reporting.
Timely and accurate invoicing helps manufacturing organizations maintain a positive cash flow, which is vital for sustaining ongoing operations and investing in future projects.
Profitability Analysis
Profitability analysis in project accounting for manufacturing organizations is crucial for evaluating the financial performance and success of individual projects. It involves assessing whether a project generates a profit and, if so, the extent of that profit.
Here are the key components and steps involved in profitability analysis in project accounting for manufacturing organizations:
- Cost Tracking: Accurately track all project-related costs, including labor, materials, equipment, overhead, subcontracting, and any other direct and indirect expenses. This data forms the foundation for profitability analysis.
- Revenue Recognition: Determine when and how revenue will be recognized for the project. In manufacturing, revenue recognition may be based on project milestones, the completion of specific tasks, or other criteria. Adhere to accounting standards such as ASC 606 or IFRS 15.
- Gross Profit Calculation: Calculate the gross profit for the project by subtracting the total project costs from the recognized revenue. Gross profit represents the project's profitability before considering indirect costs and overhead.
- Indirect Costs Allocation: Allocate indirect costs (also known as overhead costs) to the project. These costs may include facility costs, utilities, administrative expenses, and depreciation. Allocate them proportionally to projects based on relevant cost drivers.
- Net Profit Calculation: Calculate the net profit by subtracting both the gross profit and the allocated indirect costs from the recognized revenue. The net profit represents the project's profitability after accounting for all direct and indirect costs.
- Cost Control Analysis: Analyze cost control measures to identify areas where costs can be reduced or managed more efficiently. Regularly review cost variances and take corrective actions when necessary to improve profitability.
- Profit Margin Assessment: Calculate the profit margin as a percentage of the project's net profit compared to the total revenue. This metric helps assess the project's profitability in relation to its size.
- Return on Investment (ROI): Evaluate the ROI for the project by comparing the net profit to the total investment in the project, including initial capital expenditures. ROI provides insight into the project's financial success.
- Break-Even Analysis: Determine the break-even point for the project, which is the point at which total revenue equals total costs. Beyond this point, the project generates a profit; before it, the project operates at a loss.
- Sensitivity Analysis: Conduct sensitivity analysis to assess how changes in key variables, such as materials costs or project timelines, impact profitability. This helps in risk assessment and contingency planning.
- Benchmarking: Compare the profitability of the current project to historical projects or industry benchmarks. Benchmarking provides context for evaluating whether the project's profitability is in line with expectations.
- Project Closure Review: After project completion, conduct a comprehensive financial review to assess the actual profitability compared to the initial projections. Document lessons learned for future projects.
- Continuous Improvement: Use the insights gained from profitability analysis to continuously improve project management practices, cost control measures, and resource allocation strategies.
- Communication and Reporting: Share profitability analysis results and insights with project stakeholders, including management and finance teams, to ensure alignment and informed decision-making.
Profitability analysis in project accounting is essential for manufacturing organizations to assess the financial viability of their projects, make informed decisions, allocate resources effectively, and ultimately optimize profitability.
It helps organizations identify successful projects, prioritize resource allocation, and improve financial performance in a competitive manufacturing environment.
Compliance and Reporting
Compliance and reporting play a crucial role in manufacturing project accounting, ensuring that organizations adhere to financial regulations, industry standards, and contractual agreements while maintaining transparency and accountability.
Here's an overview of compliance and reporting in manufacturing project accounting:
Compliance in Manufacturing Project Accounting:
- Regulatory Compliance: Manufacturing organizations must adhere to financial regulations and accounting standards specific to their region or industry. Common regulatory frameworks include Generally Accepted Accounting Principles (GAAP) and International Financial Reporting Standards (IFRS).
- Tax Compliance: Ensure compliance with tax regulations at the local, state, national, and international levels. This includes handling sales tax, value-added tax (VAT), and income tax related to project revenues and expenses.
- Industry-Specific Standards: Manufacturing sectors often have industry-specific compliance requirements. For example, the automotive industry may have specific quality control standards, while pharmaceutical manufacturing must comply with strict regulatory requirements.
- Contractual Compliance: Review and adhere to contractual agreements with customers, suppliers, and subcontractors. Ensure that billing, invoicing, and reporting practices align with the terms negotiated in contracts.
- Audits and Documentation: Maintain detailed records and documentation related to project accounting, expenditures, revenues, and compliance efforts. These records are crucial for audits and regulatory reviews.
Reporting in Manufacturing Project Accounting:
- Financial Reports: Generate comprehensive financial reports specific to each project. These reports include income statements, balance sheets, and cash flow statements, allowing stakeholders to assess the financial health of individual projects.
- Project Status Reports: Provide regular project status reports to project stakeholders, including project managers, executives, and customers. These reports should include key financial metrics, project milestones, and progress updates.
- Variance Analysis: Prepare variance reports that compare actual project costs and revenues against budgeted amounts. Identify and explain variances to stakeholders, enabling informed decision-making.
- Compliance Reports: Develop compliance reports that detail adherence to financial regulations, industry standards, and contractual agreements. These reports demonstrate that the organization is meeting its compliance obligations.
- Tax Reports: Generate tax reports to ensure accurate and timely tax filings. These reports should provide a breakdown of project-related tax liabilities and payments.
- Resource Utilization Reports: Track resource utilization and efficiency to assess how resources are allocated and identify opportunities for optimization.
- Risk Assessment Reports: Evaluate financial risks associated with projects and create risk assessment reports. These reports help organizations identify and mitigate potential financial challenges.
- Forecasting and Planning Reports: Use historical project data to create forecasting reports, enabling organizations to make informed decisions about future projects, resource allocation, and financial planning.
- Customer Reports: Share project financial reports with customers or clients as stipulated in contractual agreements. Transparent reporting builds trust and transparency in customer relationships.
- Internal and External Audits: Prepare for internal and external audits by maintaining well-organized records and documentation. Compliance and reporting documentation should be readily accessible to auditors.
- Continuous Improvement Reports: Periodically assess project accounting processes and reporting practices to identify areas for improvement. Implement changes based on these assessments to enhance efficiency and accuracy.
Effective compliance and reporting in manufacturing project accounting ensure that organizations maintain financial integrity, transparency, and accountability.
By meeting regulatory requirements, adhering to industry standards, and providing accurate and timely reports to stakeholders, manufacturing organizations can demonstrate their commitment to responsible financial management and build trust with customers, investors, and regulatory authorities.
Risk Management
Risk management is a crucial aspect of project accounting in manufacturing organizations. Manufacturing projects often involve complex processes, resource allocation, and financial commitments, making them susceptible to various types of risks.
Effective risk management helps organizations identify, assess, mitigate, and monitor these risks to ensure that projects stay on track and achieve their financial objectives.
Here's an overview of risk management in project accounting for manufacturing projects:
1. Risk Identification:
- Scope Changes: Changes in project scope can lead to cost overruns, delays, and resource reallocation. Identify potential scope changes and their impact on project finances.
- Supply Chain Disruptions: Manufacturing projects often rely on a global supply chain. Identify risks related to supply chain disruptions, including shortages of materials, transportation issues, and geopolitical factors.
- Quality Control: Poor quality control can result in rework, product recalls, and reputation damage. Identify risks associated with quality control and ensure robust quality assurance processes.
- Cost Estimation Errors: Inaccurate cost estimates can lead to budget overruns. Identify risks related to cost estimation, including fluctuations in material prices, labor shortages, and unforeseen expenses.
- Resource Availability: Risks associated with resource availability, such as labor strikes or equipment breakdowns, can impact project timelines and costs.
- Regulatory and Compliance Changes: Changes in regulations or compliance requirements can affect project costs and timelines. Stay updated on relevant regulatory changes and their potential impact.
2. Risk Assessment:
- Probability and Impact Assessment: Evaluate the likelihood and potential impact of identified risks on project finances. Use risk matrices or scoring systems to prioritize risks.
- Qualitative and Quantitative Analysis: Perform both qualitative and quantitative risk analysis to assess the severity of risks. Quantify risks in monetary terms when possible to understand their financial implications.
3. Risk Mitigation:
- Risk Mitigation Strategies: Develop strategies to mitigate identified risks. These strategies may include contingency planning, risk insurance, dual sourcing of critical materials, and diversifying suppliers.
- Change Management: Implement robust change management processes to control scope changes and ensure that any changes are properly assessed and approved.
- Quality Assurance: Enhance quality control measures to reduce the likelihood of defects or quality-related issues.
- Resource Contingency: Maintain contingency plans for resource availability, such as backup labor sources or alternative equipment suppliers.
- Contractual Protections: Include risk-mitigating clauses in project contracts, such as penalty clauses for delays or cost overruns caused by external factors.
4. Risk Monitoring and Control:
- Regular Monitoring: Continuously monitor project risks throughout the project lifecycle. Update risk assessments and evaluate the effectiveness of mitigation strategies.
- Contingency Activation: Activate contingency plans when risks materialize, and monitor the impact on project finances closely.
- Communication: Maintain transparent communication with project stakeholders, including project managers, executives, and customers, regarding risk status and mitigation efforts.
- Lessons Learned: Conduct post-project reviews to identify lessons learned and improve risk management practices for future projects.
- Documentation: Maintain detailed documentation of risk assessments, mitigation plans, and risk-related decisions.
Effective risk management in manufacturing project accounting ensures that projects remain financially viable, adhere to budgets, and meet customer expectations.
It also minimizes the likelihood of costly disruptions and enhances overall project success.
By proactively identifying and addressing risks, manufacturing organizations can mitigate financial uncertainties and deliver projects on time and within budget.
Project Closure and Evaluation
Project closure and evaluation are essential phases in project accounting for manufacturing organizations. These activities mark the end of a project and involve a thorough assessment of its financial performance, adherence to budgets, and achievement of objectives.
Here's a detailed overview of project closure and evaluation in manufacturing project accounting:
Project Closure:
- Completion of Deliverables: Ensure that all project deliverables, whether physical products, process improvements, or milestones, have been successfully completed and meet the project's defined scope and quality standards.
- Financial Reconciliation: Conduct a final financial reconciliation to compare actual project expenses and revenues against the budget. Identify any variances and investigate the causes.
- Documentation Review: Review project documentation, including financial records, invoices, contracts, change orders, and resource allocation logs. Ensure that all project-related documents are accurate, complete, and well-organized.
- Resource Release: Release project resources, including personnel, materials, and equipment, as they are no longer needed for the project. Ensure that resources are reallocated efficiently to other projects or organizational activities.
- Outstanding Payments: Verify that all outstanding payments from customers have been received, and invoices have been settled. Address any outstanding billing or invoicing issues promptly.
- Contractual Closure: Ensure that all contractual obligations have been met, including scope, quality, timelines, and any specific contractual terms related to billing, invoicing, or warranties.
- Customer Acceptance: Obtain formal acceptance of the project's deliverables from the customer or client, confirming that they are satisfied with the results.
- Lessons Learned: Conduct a lessons-learned session with project stakeholders to identify successes, challenges, and areas for improvement. Document these lessons for future reference.
- Project Closure Report: Prepare a project closure report that summarizes the project's financial performance, scope completion, and any issues or challenges encountered. Include recommendations for improvement based on lessons learned.
Project Evaluation:
- Financial Performance Evaluation: Assess the project's financial performance, including whether it was completed within the allocated budget and whether it achieved its revenue and profitability targets. Analyze any cost overruns or cost savings.
- Scope and Quality Evaluation: Evaluate whether the project delivered the expected scope and quality. Assess whether there were any scope changes or deviations from the original project plan and their impact on costs.
- Timeline Evaluation: Analyze whether the project was completed within the planned timeline. Identify any delays and their causes, as well as any schedule adjustments made during the project.
- Resource Utilization: Review how resources, such as labor, materials, and equipment, were allocated and utilized. Assess whether resource allocation was efficient and cost-effective.
- Risk Assessment: Evaluate how well risk management strategies were implemented and whether any unforeseen risks had a significant impact on project finances.
- Stakeholder Satisfaction: Gather feedback from project stakeholders, including customers, project teams, and management, to assess their satisfaction with the project's financial performance and outcomes.
- Lessons Learned: Summarize the lessons learned during the project, both positive and negative, and outline recommendations for improving project accounting practices in the future.
- Final Reporting: Generate a comprehensive project evaluation report that provides a holistic view of the project's financial performance, compliance with project accounting standards, and overall success. Share this report with relevant stakeholders.
Project closure and evaluation in manufacturing project accounting serve as a critical steps for continuous improvement. By analyzing project performance, identifying areas for enhancement, and documenting lessons learned, manufacturing organizations can refine their project accounting practices and optimize financial outcomes in future projects.
Critical Phases of Manufacturing Project Accounting
Manufacturing project accounting involves several critical phases that span the entire lifecycle of a manufacturing project. Each phase has its own set of activities and financial considerations.
Here are the critical phases of manufacturing project accounting:
1. Project Initiation:
- Scope Definition: Clearly define the project's objectives, deliverables, and scope. Ensure that financial objectives align with project goals.
- Budgeting: Develop an initial project budget based on cost estimates and revenue projections. Obtain approval for the budget from stakeholders.
- Contract Negotiation: If applicable, negotiate contracts with customers or clients, including pricing, terms, and revenue recognition methods.
- Risk Assessment: Identify potential financial risks and uncertainties associated with the project. Create a risk management plan.
2. Project Planning:
- Detailed Budget: Refine the project budget with more detailed cost estimates, taking into account labor, materials, equipment, and overhead costs.
- Resource Allocation: Allocate resources, such as labor and materials, based on the project schedule and budget.
- Procurement Planning: Develop a procurement plan for sourcing materials and services, including supplier selection and cost considerations.
3. Project Execution:
- Cost Tracking: Continuously track project costs, including labor, materials, and other expenses, against the budget. Monitor cost variances.
- Revenue Recognition: Recognize revenue as the project progresses, following appropriate accounting standards (e.g., percentage of completion method).
- Change Management: Manage scope changes, change orders, and variations from the original project plan. Update budgets and financial projections accordingly.
- Resource Management: Monitor resource allocation and utilization to ensure efficiency and cost control.
4. Project Monitoring and Control:
- Regular Reporting: Provide regular financial reports and updates to project stakeholders, management, and finance teams.
- Variance Analysis: Conduct variance analysis to compare actual costs and revenues against the budget. Identify and address any discrepancies.
- Risk Management: Continuously monitor and manage identified financial risks. Adjust risk mitigation strategies as needed.
5. Project Closure:
- Financial Reconciliation: Perform financial reconciliation to ensure that all project costs and revenues are accounted for accurately.
- Customer Acceptance: Obtain formal acceptance of project deliverables from the customer or client.
- Document Review: Review and archive all project-related financial documents, including invoices, contracts, and change orders.
- Final Reporting: Prepare final financial reports summarizing the project's financial performance, including profit and loss statements.
6. Project Evaluation:
- Lessons Learned: Conduct a thorough evaluation of the project's financial performance, including a review of lessons learned and areas for improvement.
- Financial Auditing: If necessary, undergo financial auditing to ensure compliance with accounting standards and regulatory requirements.
- Performance Metrics: Analyze financial performance metrics, such as profitability, return on investment, and cost performance indices.
Each of these phases is critical to effective manufacturing project accounting, and they must be executed diligently to ensure financial control, compliance, and successful project outcomes.
By following these phases and best practices within each, manufacturing organizations can optimize their project accounting processes and achieve their financial objectives.
Best Practices of Manufacturing Project Accounting
Best practices in manufacturing project accounting are essential for efficiently managing the financial aspects of manufacturing projects while ensuring compliance with industry regulations and achieving project objectives.
Here are key best practices in manufacturing project accounting:
1. Accurate Cost Estimation:
- Begin with precise cost estimation for each project. Take into account labor, materials, equipment, overhead, and any other relevant costs. Regularly review and update cost estimates as the project progresses.
2. Real-Time Cost Tracking:
- Implement systems and processes for real-time cost tracking. Monitor project expenses continuously and compare them against the budget. This enables timely identification of cost overruns and corrective action.
3. Detailed Budgeting:
- Develop comprehensive project budgets that outline expected costs and revenues. Include contingencies for unexpected expenses, scope changes, and risks. Ensure that budgets are approved and communicated to all stakeholders.
4. Transparent Reporting:
- Provide clear and transparent financial reporting throughout the project's lifecycle. Share financial updates and performance metrics with project managers, executives, and relevant teams regularly.
5. Revenue Recognition Compliance:
- Ensure adherence to revenue recognition standards (e.g., ASC 606 or IFRS 15) and recognize revenue accurately based on project progress or contractual milestones. Consider the percentage of completion methods for long-term projects.
6. Cost Control Measures:
- Implement cost control measures and procedures to monitor and manage project expenses effectively. Conduct regular reviews to identify cost-saving opportunities and reduce wastage.
7. Resource Allocation Optimization:
- Optimize resource allocation by matching labor, materials, and equipment to project needs. Avoid overallocation or underutilization of resources, which can impact project profitability.
8. Compliance with Regulatory Requirements:
- Stay informed about industry-specific regulations and ensure project accounting practices comply with relevant standards. This includes environmental, safety, and quality standards.
9. Risk Management:
- Develop a robust risk management strategy that includes risk identification, assessment, mitigation, and monitoring. Consider the financial impact of identified risks on the project.
10. Change Order Management:
- Establish a systematic process for managing change orders and scope changes. Document and communicate changes to the project team, customers, and stakeholders, and adjust project budgets accordingly.
11. Vendor and Supplier Management:
- Maintain strong relationships with vendors and suppliers. Negotiate favorable terms, track procurement costs, and ensure timely payment processing.
12. Project Closure and Evaluation:
- Conduct thorough project closure activities, including financial reconciliation, document review, and customer acceptance. Evaluate project performance against the initial budget and objectives.
13. Technology Utilization:
- Leverage project accounting software and technology tools for streamlined financial management, reporting, and data analysis. Ensure data accuracy and security.
14. Continuous Improvement:
- Promote a culture of continuous improvement by reviewing lessons learned from previous projects. Apply insights to enhance future project accounting practices.
15. Team Training and Development:
- Invest in the training and development of project accountants and financial staff to ensure they are well-versed in project accounting principles, regulations, and technology.
16. Data Security and Compliance:
- Implement robust data security measures to protect sensitive financial information. Ensure compliance with data privacy regulations, such as GDPR or HIPAA, if applicable.
17. Communication and Collaboration:
- Foster effective communication and collaboration between project managers, finance teams, procurement, and other relevant departments to ensure alignment and coordination.
Adhering to these best practices in manufacturing project accounting can lead to improved financial control, accurate project cost management, better decision-making, and successful project outcomes.
It also helps organizations maintain compliance, reduce financial risks, and optimize profitability in the highly competitive manufacturing sector.
Forecasting in Manufacturing Project Accounting
Forecasting in manufacturing project accounting involves predicting future financial outcomes and performance metrics for ongoing or upcoming manufacturing projects. Accurate forecasting is crucial for effective financial planning, resource allocation, and risk management.
Here are the key aspects and steps involved in forecasting within manufacturing project accounting:
1. Project Scope and Objectives:
- Begin by understanding the project's scope, objectives, and deliverables. A clear understanding of what the project aims to achieve is essential for accurate forecasting.
2. Historical Data Analysis:
- Review historical project data, if available, to identify trends, patterns, and cost drivers. Past project performance can provide valuable insights for forecasting.
3. Cost Estimation:
- Estimate project costs based on the project's scope, resource requirements, and known cost factors. Break down costs into direct, indirect, and allocated categories.
4. Revenue Projections:
- Forecast project revenue based on contract terms, milestones, or other revenue recognition criteria. Consider variable considerations, change orders, and potential adjustments.
5. Timeline and Milestones:
- Develop a project timeline with key milestones and delivery dates. The project schedule is essential for resource allocation and cost forecasting.
6. Risk Assessment:
- Identify potential risks and uncertainties that could impact project costs and revenue. Assess the probability and potential impact of each risk.
7. Scenario Analysis:
- Consider different scenarios and their potential financial implications. Create best-case, worst-case, and most likely scenarios to evaluate the range of possible outcomes.
8. Budget Preparation:
- Create a detailed project budget that includes estimated costs, revenues, and profit margins. The budget serves as the baseline for financial forecasting.
9. Cash Flow Forecasting:
- Develop a cash flow forecast that outlines when cash inflows and outflows are expected during the project's lifecycle. This helps ensure adequate liquidity.
10. Resource Allocation:
- Allocate resources, including labor, materials, and equipment, based on the project schedule and cost estimates. Ensure that resource allocation aligns with project needs.
11. Monitoring and Control:
- Continuously monitor project performance against the forecasted data. Compare actual results to the forecasts and identify any variances.
12. Adjustments and Re-Forecasting:
- If significant discrepancies between forecasts and actual performance are identified, make necessary adjustments to the forecasts. Re-forecast periodically to account for changes in project conditions.
13. Risk Mitigation Strategies:
- Implement risk mitigation strategies based on the identified risks and their potential impact on project costs and revenue.
14. Communication:
- Share the forecasts and updates with relevant stakeholders, including project managers, finance teams, and senior management. Effective communication is essential for informed decision-making.
15. Reporting:
- Prepare regular financial reports and dashboards that highlight forecasted vs. actual performance. Include explanations for any variances and actions taken.
16. Documentation:
- Maintain detailed records of forecasts, assumptions, and changes made during the forecasting process. This documentation is valuable for audits and project evaluations.
17. Continuous Improvement:
- Use insights gained from forecasting to improve future project estimates, resource allocation strategies, and risk management practices.
Forecasting in manufacturing project accounting is an iterative process that requires ongoing analysis and adjustment as the project progresses.
Accurate forecasting helps manufacturing organizations make informed decisions, allocate resources effectively, and proactively address potential challenges, ultimately contributing to successful project outcomes.
Integration in Manufacturing Project Accounting
Integration in manufacturing project accounting involves the seamless connection and sharing of data, processes, and information between different systems and departments within an organization.
The goal is to streamline operations, enhance efficiency, and provide real-time visibility into project financials.
Integration plays a crucial role in manufacturing project accounting, as it enables various components of the project accounting process to work together effectively.
Here are key areas where integration is essential:
1. Financial Systems Integration:
- ERP (Enterprise Resource Planning) Systems: Integrate project accounting modules within the organization's ERP system. This allows for the automatic transfer of financial data, such as project costs and revenues, between project accounting and the broader financial system.
- Accounts Payable and Receivable: Seamlessly connect project-related accounts payable and accounts receivable processes to ensure accurate billing, invoicing, and payment tracking. Integration ensures that project costs and revenue recognition align with financial data.
2. Project Management Software Integration:
- Project Planning and Scheduling: Integrate project management software with project accounting to align project timelines, milestones, and resource allocation with financial data. This facilitates real-time monitoring of project progress and costs.
- Task and Time Tracking: Enable integration with time tracking tools to capture labor hours and resource usage directly within project accounting systems. This data feeds into cost calculations and payroll processing.
3. Procurement and Supply Chain Integration:
- Inventory and Materials Management: Connect inventory and materials management systems with project accounting to track the consumption of materials and their associated costs in real-time.
- Supplier and Vendor Management: Integrate supplier and vendor information, purchase orders, and invoices into project accounting to streamline procurement processes and track costs accurately.
4. Human Resources Integration:
- Payroll Systems: Integrate payroll systems with project accounting to ensure accurate labor cost allocation. This integration automates the calculation of wages and benefits associated with project labor.
- Resource Allocation: Align resource allocation processes with project accounting to optimize workforce utilization and ensure that labor costs align with project budgets.
5. Reporting and Analytics Integration:
- Business Intelligence Tools: Connect business intelligence and reporting tools to project accounting systems to generate real-time financial reports and dashboards. This allows stakeholders to make data-driven decisions.
6. Customer Relationship Management (CRM) Integration:
- Sales and Customer Data: Integrate CRM systems with project accounting to link customer data with project contracts, billing, and revenue recognition. This ensures accurate invoicing and contract compliance.
7. Compliance and Regulatory Integration:
- Tax and Regulatory Compliance: Integrate tax and compliance systems to ensure that project accounting practices align with changing tax laws and industry-specific regulations.
8. Cloud-Based Solutions:
- Consider using cloud-based project accounting software that offers integration capabilities with various other software applications. Cloud solutions often provide APIs (Application Programming Interfaces) and connectors for seamless data exchange.
9. Mobile Integration:
- Enable mobile access to project accounting data through integration with mobile apps. This allows project managers and team members to access real-time financial information on the go.
Effective integration in manufacturing project accounting streamlines processes reduces manual data entry, minimizes errors, and enhances data accuracy.
It also provides stakeholders with the visibility and insights needed to make informed decisions, control project costs, and optimize project outcomes.
However, successful integration requires careful planning, IT expertise, and ongoing monitoring to ensure that systems work harmoniously to support project accounting objectives.
Benefits of Manufacturing Project Accounting
Manufacturing project accounting offers numerous benefits to organizations involved in manufacturing projects. These benefits contribute to improved financial control, better decision-making, and enhanced project outcomes.
Here are some of the key advantages:
- Cost Control: Manufacturing project accounting enables organizations to track project costs meticulously. This allows for better cost control and helps prevent budget overruns by identifying and addressing cost variances promptly.
- Accurate Budgeting: Project accounting facilitates the creation of detailed project budgets. Accurate budgeting helps organizations allocate resources efficiently and ensures that projects remain financially viable.
- Resource Optimization: By monitoring resource allocation and utilization, manufacturing project accounting helps organizations make informed decisions about labor, materials, and equipment, optimizing resource allocation and reducing waste.
- Financial Transparency: Project accounting provides real-time visibility into project financials. This transparency allows project managers and executives to monitor progress, assess financial health, and take corrective actions when necessary.
- Compliance: Manufacturing projects often involve complex regulatory and industry-specific requirements. Project accounting helps organizations ensure compliance with financial regulations, quality standards, and contractual obligations.
- Risk Management: Effective risk management is crucial in manufacturing projects. Project accounting allows organizations to identify, assess, and mitigate risks by providing the financial data needed for informed risk-related decisions.
- Billing and Invoicing Efficiency: Manufacturing project accounting streamlines the billing and invoicing process. This ensures that invoices are accurate, delivered promptly, and align with project milestones or contractual terms.
- Profitability Analysis: Project accounting enables organizations to assess the profitability of individual projects. This analysis helps identify profitable projects and those that may require adjustments or additional resources.
- Real-time Reporting: With real-time financial reporting, manufacturing organizations can make timely decisions based on up-to-date project data. This agility is essential for adapting to changing project circumstances.
- Resource Allocation Alignment: Organizations can align resource allocation with project priorities by using project accounting data to determine which projects require additional resources or adjustments in resource allocation.
- Customer Satisfaction: Accurate project accounting can lead to improved customer satisfaction by ensuring that projects are delivered on time and within budget. Satisfied customers are more likely to engage in repeat business and referrals.
- Improved Decision-making: Access to comprehensive financial data helps project managers and executives make informed decisions throughout the project lifecycle. This includes decisions related to scope changes, resource adjustments, and risk mitigation.
- Continuous Improvement: Project accounting encourages organizations to review and analyze project outcomes and lessons learned. This process supports continuous improvement in project management practices.
- Transparency in Project Evaluation: Manufacturing project accounting makes it easier to evaluate project success based on financial performance, adherence to timelines, resource utilization, and stakeholder satisfaction.
- Resource Planning: The data generated by project accounting aids in long-term resource planning and investment decisions, allowing organizations to allocate resources strategically and prioritize projects accordingly.
- Audit Trails: Manufacturing project accounting provides comprehensive audit trails, making it easier to trace financial transactions and demonstrate compliance with regulations and industry standards during audits.
In summary, manufacturing project accounting offers a wide range of benefits, including cost control, resource optimization, financial transparency, and compliance, all of which contribute to improved project outcomes, profitability, and organizational efficiency in the manufacturing sector.
Challenges Associated with Manufacturing Project Accounting
Manufacturing project accounting involves unique challenges due to the complex nature of manufacturing projects, resource allocation, and financial management.
Here are some of the key challenges associated with manufacturing project accounting:
- Accurate Cost Estimation: Estimating project costs accurately can be challenging, especially for large and complex manufacturing projects. Errors in cost estimation can lead to budget overruns.
- Scope Changes: Manufacturing projects often experience scope changes due to evolving requirements, design modifications, or customer requests. Managing these changes while controlling costs is a significant challenge.
- Resource Allocation: Efficiently allocating and managing resources, including labor, materials, and equipment, can be complex. Overallocation or underutilization of resources can impact project profitability.
- Complex Billing and Invoicing: Manufacturing projects may involve various billing methods, such as milestone billing or time and materials billing. Managing billing intricacies and ensuring accurate invoicing can be challenging.
- Regulatory Compliance: Manufacturing organizations often need to comply with industry-specific regulations, which can complicate project accounting. Ensuring that project accounting practices align with these regulations is crucial.
- Risk Management: Manufacturing projects are exposed to various risks, including supply chain disruptions, quality control issues, and market volatility. Effectively identifying, assessing, and mitigating these risks is a constant challenge.
- Real-time Financial Visibility: Maintaining real-time visibility into project financials is essential for proactive decision-making. Ensuring that project managers have access to up-to-date financial data can be challenging without the right systems in place.
- Resource Constraints: Resource constraints, such as labor shortages or equipment breakdowns, can disrupt project timelines and increase costs. Managing and mitigating these constraints is essential.
- Change Management: Implementing changes to project scope, schedule, or resource allocation requires effective change management practices to prevent cost overruns and delays.
- Cost Tracking: Continuously tracking project costs and ensuring that they align with the budget can be cumbersome, especially when projects involve numerous cost components and revisions.
- Interdepartmental Coordination: Collaboration between different departments, such as finance, project management, and procurement, is crucial for successful project accounting. Ensuring effective communication and coordination can be challenging.
- Quality Control: Maintaining strict quality control standards throughout the manufacturing process is essential. Deviations from quality standards can result in rework and additional costs.
- Multi-project Management: Manufacturing organizations often handle multiple projects simultaneously. Balancing resource allocation and managing priorities across various projects can be complex.
- Vendor and Supplier Management: Managing relationships with vendors and suppliers, including negotiating contracts and tracking costs, is critical for cost control and resource management.
- Currency and Exchange Rate Fluctuations: Manufacturing organizations operating globally may face challenges related to currency exchange rate fluctuations, which can impact project costs and revenues.
- Data Accuracy: Ensuring the accuracy of project accounting data, especially in large-scale projects with numerous transactions, requires robust data management and validation processes.
- Legacy Systems: Some manufacturing organizations may still rely on legacy systems or manual processes for project accounting, which can hinder efficiency and accuracy.
Addressing these challenges requires a combination of effective project management practices, technology adoption, risk management strategies, and a deep understanding of the manufacturing industry's unique dynamics.
Proactive planning and continuous improvement efforts are key to overcoming these challenges and achieving successful project outcomes in manufacturing organizations.
Strategies to Overcome the Challenges Associated with Manufacturing Project Accounting
Overcoming the challenges of manufacturing project accounting requires a combination of strategies that address specific issues and improve overall project accounting practices. Here are strategies to tackle the challenges mentioned earlier:
1. Integration of Systems and Data:
- Strategy: Implement integrated project accounting software that seamlessly connects with other systems, such as ERP (Enterprise Resource Planning) and project management tools.
- Benefits: This integration streamlines data flow, reduces manual data entry, minimizes errors, and ensures consistency across systems.
2. Complex Cost Allocation:
- Strategy: Develop a well-defined cost allocation methodology that clearly assigns costs to specific projects based on predetermined criteria.
- Benefits: A clear allocation methodology eliminates ambiguity, simplifies cost tracking, and ensures accurate project cost accounting.
3. Accurate Revenue Recognition:
- Strategy: Establish clear revenue recognition policies aligned with accounting standards (e.g., ASC 606 or IFRS 15) and automate revenue recognition processes.
- Benefits: Accurate revenue recognition ensures compliance, reduces revenue leakage, and provides a clear picture of project profitability.
4. Resource Allocation and Management:
- Strategy: Implement resource management tools and processes that allow for efficient allocation and utilization of labor, materials, and equipment.
- Benefits: Optimizing resource allocation minimizes wastage, improves project efficiency, and enhances cost control.
5. Billing and Invoicing Efficiency:
- Strategy: Automate billing and invoicing processes to ensure they align with project milestones and client agreements. Use software that generates invoices accurately and promptly.
- Benefits: Automation reduces billing errors, speeds up the invoicing cycle, and enhances cash flow management.
6. Compliance and Reporting:
- Strategy: Invest in compliance management software and develop standardized reporting templates to ensure timely and accurate reporting.
- Benefits: Streamlined compliance and reporting processes reduce the risk of errors, non-compliance, and costly penalties.
7. Risk Management:
- Strategy: Implement risk management frameworks that identify, assess, and mitigate financial risks associated with manufacturing projects.
- Benefits: Proactive risk management minimizes unexpected financial setbacks and ensures project financial stability.
8. Project Closure and Evaluation:
- Strategy: Conduct thorough project closure reviews that include financial performance analysis, lessons learned, and recommendations for future projects.
- Benefits: Continuous improvement based on project evaluations leads to more effective project accounting practices.
9. Training and Skill Development:
- Strategy: Provide training and development opportunities for project accountants to ensure they have the necessary skills and knowledge to handle complex accounting tasks.
- Benefits: Skilled project accountants are better equipped to address challenges and improve project accounting practices.
10. Technology Adoption and Upgrades:
- Strategy: Stay up-to-date with technology trends and invest in modern project accounting software that offers automation, real-time reporting, and analytics capabilities.
- Benefits: Up-to-date technology improves efficiency, accuracy, and the ability to adapt to evolving accounting requirements.
11. Change Management:
- Strategy: Implement change management practices to ensure smooth transitions when adopting new technologies or processes. Communicate changes effectively to all stakeholders.
- Benefits: Effective change management minimizes resistance, accelerates adoption, and ensures that changes align with organizational goals.
12. Collaboration and Cross-Functional Teams:
- Strategy: Promote collaboration between project accountants, project managers, finance teams, and other relevant departments to address challenges collectively.
- Benefits: Cross-functional teams bring diverse perspectives and expertise, leading to more effective solutions.
13. Data Analytics and Predictive Analysis:
- Strategy: Leverage data analytics and predictive analysis tools to identify trends, forecast financial outcomes, and proactively address potential challenges.
- Benefits: Data-driven insights help organizations make informed decisions and anticipate issues before they become major challenges.
By implementing these strategies, manufacturing organizations can enhance their project accounting practices, overcome challenges, and ensure more efficient and effective financial management for their projects.
Who is Responsible for Project Accounting in a Manufacturing Organization?
In a manufacturing organization, the responsibility for project accounting typically falls on several key roles and departments, working collaboratively to ensure effective financial management of manufacturing projects.
These roles include:
- Project Accountants: Project accountants are responsible for the day-to-day financial management of individual projects. Their tasks may include budgeting, cost tracking, revenue recognition, financial reporting, and ensuring compliance with accounting standards for each project. They work closely with project managers to monitor project finances.
- Project Managers: Project managers play a critical role in project accounting. They are responsible for project planning, execution, and delivery. They work closely with project accountants to provide updates on project progress, scope changes, and milestones, which impact project financials.
- Finance Department: The finance department, led by the Chief Financial Officer (CFO) or finance manager, oversees the overall financial management of the organization, including project accounting. They ensure that project accounting aligns with the organization's financial strategy, budget, and financial reporting requirements.
- Controller or Finance Manager: The controller or finance manager is often responsible for the financial controls and accounting processes within the organization. They oversee the project accounting function, ensuring compliance with accounting standards and internal controls.
- Cost Analysts: Cost analysts play a role in project accounting by analyzing project costs, conducting cost variance analysis, and providing insights to project accountants and project managers. They help identify cost-saving opportunities and improve cost efficiency.
- IT Department: The IT department plays a crucial role in supporting project accounting by maintaining and configuring accounting software, integrating financial systems, ensuring data security, and providing technical support to users.
- Procurement and Supply Chain Teams: These teams are responsible for sourcing materials and services for manufacturing projects. Their decisions and negotiations impact project costs, and they work closely with project accountants to track procurement expenses.
- Compliance and Legal Teams: Compliance and legal professionals ensure that project accounting practices adhere to relevant regulatory requirements and industry standards. They may provide guidance on contract terms, revenue recognition, and compliance issues.
- Audit and Internal Control Teams: Audit teams, whether internal or external, review project accounting processes and financial statements to ensure accuracy, transparency, and compliance. They may conduct audits of project financials periodically.
- Human Resources: The HR department supports project accounting by managing labor-related matters, including payroll, benefits, and workforce allocation. They ensure that labor costs are accurately recorded and allocated to projects.
- Senior Management: Senior executives, including the CEO and COO, oversee the organization's overall financial performance, including project profitability. They rely on project accounting data to make strategic decisions and allocate resources effectively.
In summary, project accounting in a manufacturing organization involves collaboration among various departments and roles, including project accountants, project managers, finance professionals, cost analysts, IT experts, procurement teams, compliance and legal experts, audit teams, HR professionals, and senior management. Effective coordination among these stakeholders is essential for successful project accounting and financial management within the organization.
How Can Project Accounting in Manufacturing Contribute to Sustainability Initiatives?
Project accounting in manufacturing can play a significant role in supporting sustainability initiatives by helping organizations track, analyze, and optimize the environmental and financial impacts of their projects.
Here's how project accounting can contribute to sustainability efforts in manufacturing:
- Cost Allocation for Sustainability Investments: Project accounting can allocate costs specifically to sustainability initiatives within manufacturing projects. This includes investments in energy-efficient equipment, renewable energy sources, waste reduction, and environmentally friendly materials. Tracking these costs separately allows organizations to assess the financial impact of sustainability measures.
- Resource Efficiency Monitoring: Through project accounting, organizations can monitor the consumption of resources such as energy, water, and raw materials in manufacturing projects. By analyzing resource usage data, they can identify opportunities to reduce consumption and minimize environmental impact.
- Life Cycle Cost Analysis: Project accounting can incorporate life cycle cost analysis, which considers the total cost of ownership over the life of an asset or project. This approach allows organizations to assess the long-term financial and environmental impacts of their investments, helping them make sustainable choices.
- Carbon and Emissions Tracking: Project accounting can include the tracking of carbon emissions and other greenhouse gasses associated with manufacturing projects. This data is essential for understanding the environmental footprint of projects and identifying opportunities for emission reduction.
- Green Procurement and Supplier Evaluation: Organizations can use project accounting to track and evaluate procurement decisions related to sustainability. This includes sourcing materials and components from environmentally responsible suppliers and assessing the financial and environmental impacts of these choices.
- Sustainable Design and Engineering: Project accounting can support sustainable design and engineering practices by allocating costs to eco-friendly design features and innovations. This encourages the integration of sustainability principles into project planning and execution.
- Incentive and Rebate Tracking: Many governments and utilities offer incentives and rebates for sustainability initiatives, such as energy efficiency upgrades or renewable energy installations. Project accounting can help organizations track these incentives and factor them into project financials.
- Environmental Reporting and Disclosure: Project accounting can facilitate the reporting of environmental performance metrics, which is increasingly important for regulatory compliance and stakeholder transparency. This includes reporting on waste reduction, emissions reduction, and resource conservation.
- Cost-Benefit Analysis for Sustainability Projects: Project accounting allows organizations to conduct cost-benefit analyses specifically for sustainability-focused projects. It helps assess the financial feasibility and environmental impact of initiatives, ensuring that they align with sustainability goals.
- Integrated Sustainability Reporting: Project accounting can be integrated with sustainability reporting systems to provide a comprehensive view of both financial and non-financial performance metrics. This supports organizations in presenting a balanced picture of their sustainability efforts to stakeholders.
- Continuous Improvement: By analyzing project accounting data, organizations can identify areas where sustainability initiatives have been successful and where improvements are needed. This continuous improvement process helps refine sustainability strategies over time.
In conclusion, project accounting in manufacturing can serve as a valuable tool for organizations striving to meet sustainability objectives. By integrating environmental and financial data, organizations can make informed decisions, optimize resource use, reduce environmental impacts, and enhance the financial performance of sustainability initiatives within their manufacturing projects.
How Can Project Accounting Help with Economic Uncertainty Management?
Project accounting can be a valuable tool for managing economic uncertainty in manufacturing organizations. Economic uncertainty often arises from factors such as market volatility, changing customer demand, supply chain disruptions, and unforeseen events (e.g., economic downturns or global crises).
Here's how project accounting can help with economic uncertainty management:
- Scenario Analysis and Sensitivity Modeling: Project accounting allows organizations to create multiple financial scenarios based on different economic conditions. By modeling the potential impact of various scenarios, organizations can make informed decisions and prepare contingency plans to address economic uncertainty effectively.
- Risk Assessment and Mitigation: Project accounting facilitates the identification and assessment of financial risks associated with individual projects. By quantifying these risks and their potential impact on project budgets, organizations can implement risk mitigation strategies to reduce exposure to economic uncertainties.
- Resource Allocation Flexibility: Project accounting enables organizations to adjust resource allocation based on changing economic conditions. This flexibility allows organizations to allocate resources where they are needed most, optimizing cost management during uncertain times.
- Cost Control and Variance Analysis: Organizations can use project accounting to closely monitor project costs and conduct variance analysis. This helps identify cost overruns and inefficiencies promptly, allowing for corrective action to be taken to control expenses in response to economic uncertainty.
- Cash Flow Forecasting: Project accounting includes cash flow forecasting capabilities, enabling organizations to project cash inflows and outflows accurately. This helps maintain adequate liquidity to weather economic uncertainties and financial challenges.
- Contract Renegotiation and Change Orders: In uncertain economic environments, organizations may need to renegotiate contracts or address scope changes. Project accounting can track changes to project terms and assess their financial impact, helping organizations make informed decisions during negotiations.
- Revenue Recognition Adaptation: Economic uncertainties can affect the timing and amount of revenue recognition. Project accounting allows organizations to adjust revenue recognition methods based on changing circumstances, ensuring compliance with accounting standards.
- Cost-Benefit Analysis for New Projects: Before initiating new projects, organizations can use project accounting to conduct thorough cost-benefit analyses. This helps assess whether investing in new projects aligns with the organization's financial goals during uncertain economic periods.
- Resource Reallocation and Project Prioritization: Project accounting data can inform resource reallocation decisions. Organizations can prioritize projects that are more likely to yield positive financial outcomes during economic uncertainty and temporarily defer or scale back projects that are higher risk.
- Comprehensive Reporting and Dashboards: Project accounting provides real-time access to financial data and performance metrics through reporting and dashboards. This visibility enables organizations to monitor project health, identify trends, and make informed decisions in response to economic changes.
- Integration with Economic Data Sources: Project accounting systems can be integrated with external economic data sources, such as market indices and economic indicators. This integration allows organizations to incorporate external economic data into their financial models and forecasts.
- Audit and Compliance Support: Project accounting helps ensure that financial data and project-related activities are compliant with accounting standards and regulatory requirements, reducing the risk of financial penalties during economic uncertainty.
In summary, project accounting provides manufacturing organizations with the tools and insights needed to adapt to economic uncertainty effectively. By enabling scenario analysis, risk mitigation, flexible resource allocation, and real-time financial monitoring, project accounting empowers organizations to navigate economic challenges, make data-driven decisions, and enhance financial resilience.
What Role Does Cybersecurity Play in Manufacturing Project Accounting?
Cybersecurity plays a critical role in manufacturing project accounting, ensuring the confidentiality, integrity, and availability of financial data and sensitive information.
Here's how cybersecurity is essential in this context:
- Protecting Financial Data: Manufacturing project accounting involves the handling of financial data, including budgets, cost estimates, revenue projections, and payment information. Cybersecurity measures are necessary to safeguard this sensitive financial information from unauthorized access, data breaches, or theft.
- Data Privacy Compliance: Regulations such as GDPR (General Data Protection Regulation) and industry-specific standards require the protection of personal and financial data. Cybersecurity measures help manufacturing organizations maintain compliance with these regulations by safeguarding financial data from data breaches and privacy violations.
- Preventing Unauthorized Access: Access to project accounting systems and financial data should be restricted to authorized personnel only. Strong access controls, including user authentication and authorization mechanisms, are critical in preventing unauthorized access.
- Data Encryption: Cybersecurity practices include encrypting financial data both in transit and at rest. Encryption ensures that even if data is intercepted or stolen, it remains unreadable without the appropriate decryption keys.
- Secure Communication: Secure communication protocols, such as HTTPS for web-based project accounting systems, protect data as it is transmitted between users and servers. This is especially important when accessing financial information remotely.
- Vulnerability Management: Regular vulnerability assessments and security audits help identify and address potential weaknesses in project accounting systems and associated software. Timely patching and updates mitigate security risks.
- Phishing and Social Engineering Protection: Manufacturing organizations must educate their employees about phishing attacks and social engineering attempts, which could compromise login credentials and financial data. Cybersecurity awareness training is essential.
- Monitoring and Intrusion Detection: Implementing intrusion detection systems and security monitoring tools allows organizations to detect and respond to suspicious activities and potential security breaches in real time.
- Incident Response Plan: Manufacturing organizations should have a well-defined incident response plan in place for handling security incidents related to project accounting. This plan outlines the steps to take in the event of a security breach or data compromise.
- User Training and Awareness: Training employees to recognize and report security threats and incidents is crucial. Employees should be aware of cybersecurity best practices and be vigilant in protecting financial data.
- Backup and Recovery: Regularly backing up financial data ensures that it can be restored in case of data loss due to cybersecurity incidents or other unforeseen events.
- Secure Vendor Relationships: If third-party project accounting software or services are used, organizations should assess the cybersecurity practices of vendors and ensure that they meet the necessary security standards.
- Access Logs and Auditing: Maintaining access logs and conducting regular audits of financial data access helps organizations track who has accessed the data and detect any unusual or unauthorized activity.
- Data Segmentation: Segregating financial data from other operational data can help contain and limit the impact of a cybersecurity breach. Access controls should be applied to restrict access to financial databases.
- Physical Security: Physical security measures, such as secure data centers and access controls to server rooms, are essential to protect the infrastructure that hosts financial data.
In summary, cybersecurity is an integral part of manufacturing project accounting, as it safeguards sensitive financial data, ensures compliance with regulations, and protects against potential security threats and breaches.
Implementing robust cybersecurity practices helps maintain the integrity and confidentiality of financial information, ultimately contributing to the success and trustworthiness of project accounting systems in manufacturing organizations.
How Can Manufacturing Organizations Adapt to Remote Work Collaboration in Project Accounting?
Manufacturing organizations can adapt to remote work collaboration in project accounting by implementing a combination of technology, processes, and cultural changes.
Here are several strategies to facilitate remote collaboration in project accounting:
- Cloud-Based Project Accounting Software: Transition to cloud-based project accounting software that allows remote access from anywhere with an internet connection. Cloud solutions enable real-time collaboration and data sharing among project accountants, managers, and stakeholders.
- Secure Remote Access: Implement robust security measures to ensure secure remote access to project accounting systems. Use virtual private networks (VPNs), multi-factor authentication (MFA), and encryption to protect sensitive financial data.
- Collaboration Tools: Utilize collaboration tools and software, such as video conferencing, chat, and project management platforms, to facilitate communication and collaboration among remote team members. These tools help bridge the gap between geographically dispersed teams.
- Document Management Systems: Implement document management systems that allow for centralized storage, sharing, and version control of project-related documents, contracts, invoices, and financial reports. Ensure that remote team members can access and collaborate on these documents securely.
- Digital Workflow Automation: Automate project accounting workflows to reduce manual processes and paperwork. Workflow automation tools streamline approvals, invoicing, expense tracking, and other financial tasks, making them accessible from remote locations.
- Data Security and Compliance: Maintain stringent data security and compliance practices, especially when working with financial data remotely. Ensure that remote work setups comply with data privacy regulations (e.g., GDPR or HIPAA) and industry-specific standards.
- Remote Training and Onboarding: Provide remote training and onboarding sessions for project accountants and team members to ensure they are proficient in using remote collaboration tools and following security protocols.
- Regular Check-Ins: Schedule regular virtual meetings and check-ins to maintain team cohesion and communication. These meetings can include project status updates, financial reviews, and collaborative discussions.
- Project Management Software Integration: Integrate project accounting software with project management tools. This integration ensures that project managers and accountants have real-time visibility into project progress, resource allocation, and financial data.
- Performance Metrics and KPIs: Establish performance metrics and key performance indicators (KPIs) to monitor the effectiveness of remote project accounting collaboration. Regularly review these metrics to identify areas for improvement.
- Flexibility and Work-Life Balance: Encourage a culture of flexibility and work-life balance for remote team members. Promote trust and accountability, allowing employees to manage their work hours effectively.
- Remote Expense Management: Enable remote expense tracking and management. Employees should be able to submit expenses and receipts electronically, with approvals and reimbursement processes in place.
- Cybersecurity Training: Conduct cybersecurity training for remote employees to educate them on best practices for protecting financial data and recognizing potential security threats or phishing attempts.
- Disaster Recovery and Business Continuity Plans: Develop and test disaster recovery and business continuity plans to ensure that remote work operations can continue smoothly in the event of unexpected disruptions, such as natural disasters or cyberattacks.
- Feedback and Continuous Improvement: Solicit feedback from remote team members to identify challenges and opportunities for improvement in remote collaboration. Make adjustments to processes and tools based on this feedback.
By implementing these strategies, manufacturing organizations can successfully adapt to remote work collaboration in project accounting while maintaining data security, compliance, and effective financial management.
This adaptability not only supports remote work arrangements during periods of necessity (e.g., pandemics) but also offers long-term benefits in terms of flexibility and efficiency.
Future Trends in Manufacturing Project Accounting
As manufacturing organizations continue to evolve and adapt to changing market dynamics and technological advancements, several future trends are expected to impact the field of manufacturing project accounting.
Here are some key trends to watch for:
- Advanced Data Analytics and AI: Manufacturing project accounting will increasingly leverage advanced data analytics and artificial intelligence (AI) to gain deeper insights into project financials. AI-powered algorithms can analyze large datasets, identify patterns, and make predictive forecasts, aiding in cost estimation, risk management, and resource allocation.
- Blockchain for Transparency: Blockchain technology is expected to play a role in enhancing transparency and traceability in manufacturing project accounting. It can provide immutable records of financial transactions, making audits and compliance checks more efficient and reliable.
- Real-time Reporting: Real-time financial reporting will become the norm, allowing project managers and executives to access up-to-the-minute data on project costs, revenues, and profitability. This real-time visibility enables more agile decision-making.
- Cloud-Based Solutions: The adoption of cloud-based project accounting software will continue to rise. Cloud solutions offer scalability, accessibility, and cost-effectiveness, making them attractive to manufacturing organizations of all sizes.
- Integration of IoT Data: The Internet of Things (IoT) will enable the integration of data from connected devices and machinery into project accounting systems. This data can be used for real-time monitoring of equipment performance, maintenance costs, and resource utilization.
- Evolving Regulatory Compliance: As regulatory requirements evolve, manufacturing organizations will need to keep pace with changing compliance standards. Project accounting systems will be adapted to ensure seamless compliance with tax, accounting, and industry-specific regulations.
- Sustainability Accounting: Manufacturers will increasingly incorporate sustainability metrics into project accounting. Tracking environmental impacts, such as carbon emissions, waste reduction, and energy efficiency, will become integral to project reporting.
- Remote Work Collaboration: The trend toward remote work will require project accounting systems to support collaboration among dispersed teams. Cloud-based solutions with collaborative features will facilitate remote financial management.
- Mobile Apps: Mobile apps for project accounting will become more sophisticated, allowing project managers and team members to track expenses, log hours, and access financial data on smartphones and tablets.
- Supplier and Vendor Integration: Enhanced integration with suppliers and vendors will enable smoother procurement processes, cost tracking, and payment management, reducing manual data entry and errors.
- Predictive Financial Modeling: Advanced financial modeling tools will incorporate predictive analytics to simulate various scenarios, helping organizations assess the financial impact of different project decisions and external factors.
- Economic Uncertainty Management: Given the increasing economic uncertainties, manufacturing project accounting will focus on robust risk management strategies, scenario planning, and contingency fund allocation to mitigate financial risks.
- Cybersecurity Focus: With the growing reliance on digital tools, cybersecurity will be a top priority to protect financial data from cyber threats and breaches.
- Industry-Specific Solutions: Manufacturers in specialized industries, such as aerospace, pharmaceuticals, and automotive, will seek industry-specific project accounting solutions tailored to their unique needs and regulatory requirements.
Staying current with these trends and adopting relevant technologies and practices will be essential for manufacturing organizations to maintain financial competitiveness, optimize project outcomes, and adapt to evolving market dynamics in the years ahead.
How can Deskera Help You with Project Accounting?
Deskera ERP offers a comprehensive suite of cloud-based business software solutions that can assist organizations with various aspects of project accounting.
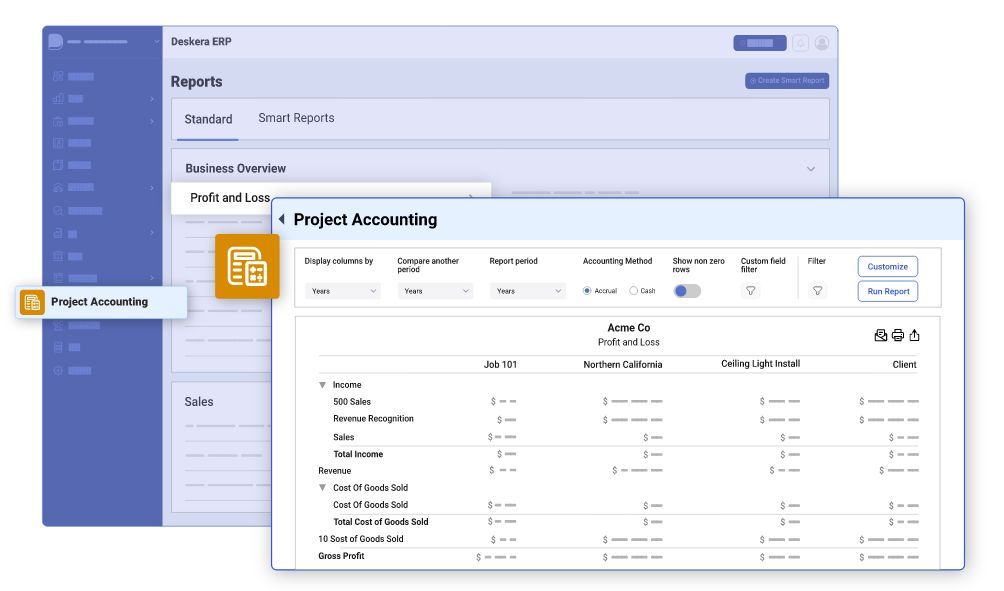
Here's how Deskera can help you with project accounting:
- Bill of Quantities: This will help you accurately track project costs and revenue. This is because Deskera automatically calculates prices, discounts, taxes, and other factors for each item, while also ensuring real-time updates of a project’s bill of quantities.
- Project Time Tracking: Through Deskera, you would be able to monitor your project progress because it automatically logs time spent on tasks and projects. It also ensures accurate billing based on actual project time. Deskera ERP also enables efficient project tracking and management.
- Payment Milestones: With Deskera, you will be able to create payment milestones to streamline accounts payable, set custom payments with specific dates and amounts, and ensure timely payments by setting reminders and notifications.
- Revenue Recognition: With Deskera you will be able to ensure timely invoicing because it enables upfront recognition of revenue. It also allows cost-based accounting for revenue recognition. Lastly, Deskera ERP ensures accurate reporting of revenue.
- Project Costing and P&L: Deskera will assist you in tracking financial health by monitoring, managing, and tracking project costs. It will also help in identifying and analyzing cost overruns, as well as monitoring and reviewing budget performance. Deskera ERP will also generate real-time Profit and Loss reports, and analyze cost and benefit performance, while also giving you financial visibility.
Moreover, you can use these features to create detailed reports and dashboards that provide you with an in-depth understanding of your project finances. With Deskera ERP, you can easily keep track of your project's financials and make better decisions that lead to increased profitability.
Key Takeaways
Manufacturing organizations need project accounting to manage costs, optimize resource allocation, ensure compliance, and maximize profitability for individual projects. It provides financial control and transparency.
The difference between project accounting and regular accounting in manufacturing is that while project accounting focuses on managing the financial aspects of individual projects, tracking project-specific costs, and ensuring the profitability of each project; Regular accounting takes a broader perspective, consolidating financial data across the entire organization and providing a comprehensive view of its financial health.
The core project accounting processes are as follows:
- Budgeting and cost control
- Resource allocation and management
- Client and stakeholder communication
- Billing and invoicing
- Profitability analysis
- Compliance and reporting
- Risk management
- Project closure and evaluation
The best practices of manufacturing project accounting are:
- Accurate cost estimation
- Real-time cost tracking
- Detailed budgeting
- Transparent reporting
- Revenue recognition compliance
- Cost control measures
- Resource allocation optimization
- Compliance with regulatory requirements
- Risk management
- Change order management
- Vendor and supplier management
- Project closure and evaluation
- Technology utilization
- Continuous improvement
- Team training and development
- Data security and compliance
- Communication and collaboration
The benefits of manufacturing project accounting are:
- Cost control
- Accurate budgeting
- Resource optimization
- Financial transparency
- Compliance
- Risk management
- Billing and invoicing efficiency
- Profitability analysis
- Real-time reporting
- Resource allocation alignment
- Customer satisfaction
- Improved decision making
- Continuous improvement
- Transparency in project evaluation
- Resource planning
- Audit trails
The challenges associated with manufacturing project accounting are:
- Accurate cost estimation
- Scope changes
- Resource allocation
- Complex billing and invoicing
- Regulatory compliance
- Risk management
- Real-time financial visibility
- Resource constraints
- Change management
- Cost tracking
- Interdepartmental coordination
- Quality control
- Multi-project management
- Vendor and supplier management
- Currency and exchange rate fluctuations
- Data accuracy
- Legacy systems
Also, remote work collaboration and cybersecurity measures play pivotal roles in modern project accounting, ensuring data security and business continuity. Additionally, project accounting supports sustainability initiatives and helps organizations manage economic uncertainty through data-driven insights and compliance.
Thus, in a rapidly changing business landscape, embracing project accounting as a fundamental financial tool empowers manufacturing organizations to make informed decisions, optimize resource allocation, and ensure the financial health of their projects.
Project accounting is not only a necessity but also a strategic advantage for manufacturing organizations seeking growth, profitability, and sustainability in an evolving market.
Deskera ERP will help you with project accounting by tracking, monitoring, and analyzing project revenue, expenses, and billable hours. It will help you leverage real-time visibility into project finances and performance to ensure cost control and profitability. It will also help you in entering timesheets, monitoring profit and loss, and managing bills of quantities.
Related Articles
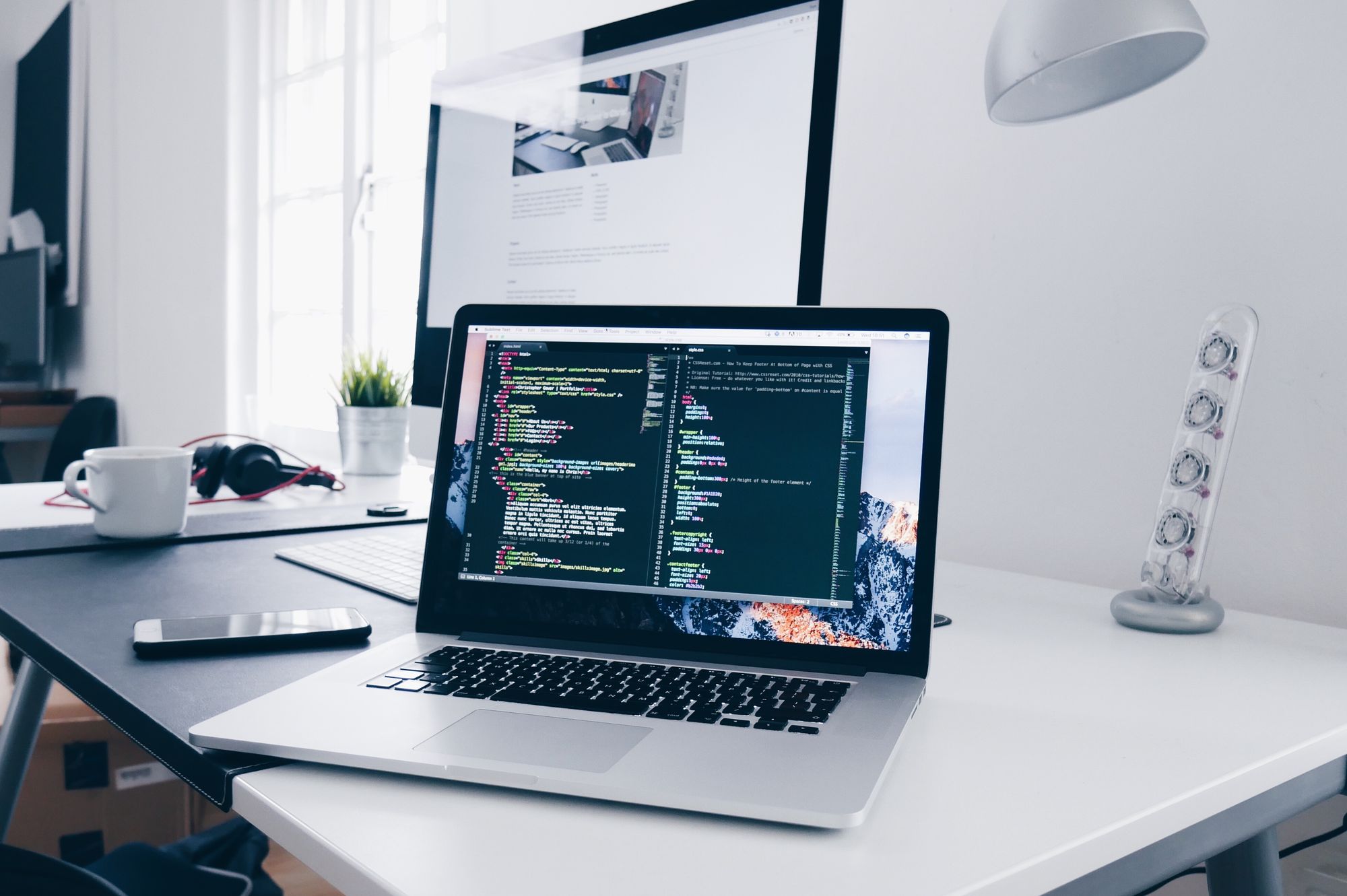
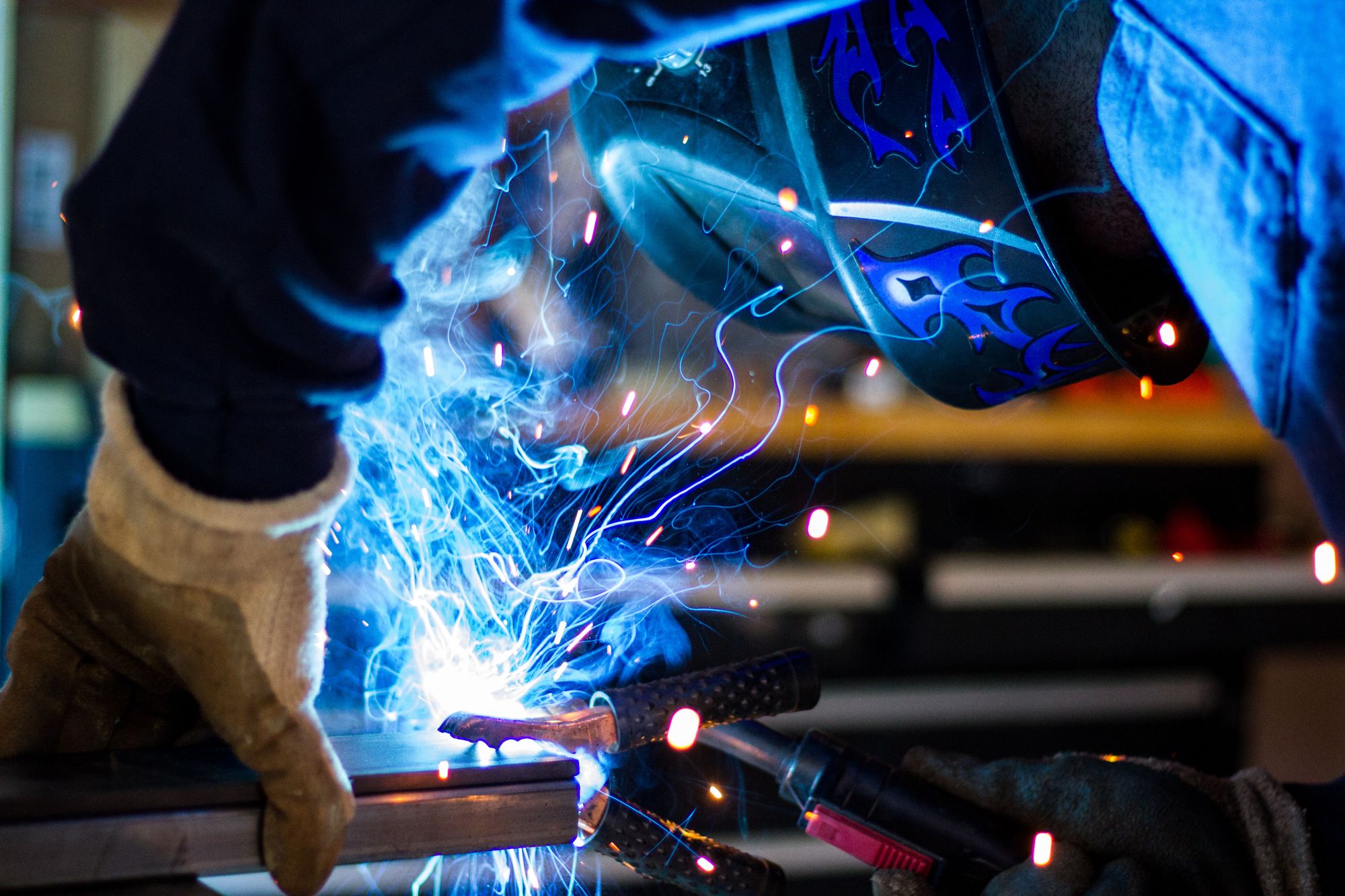
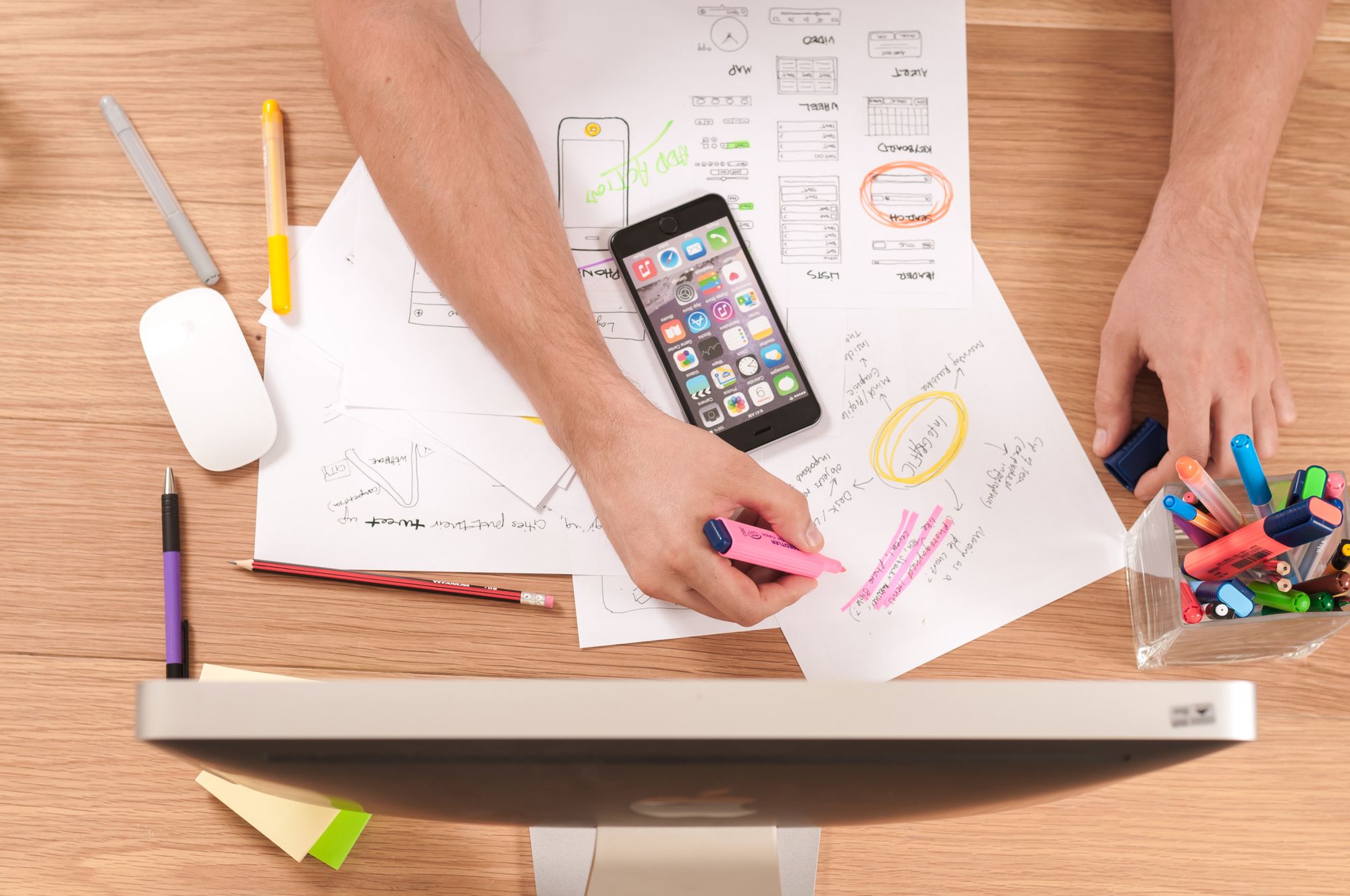
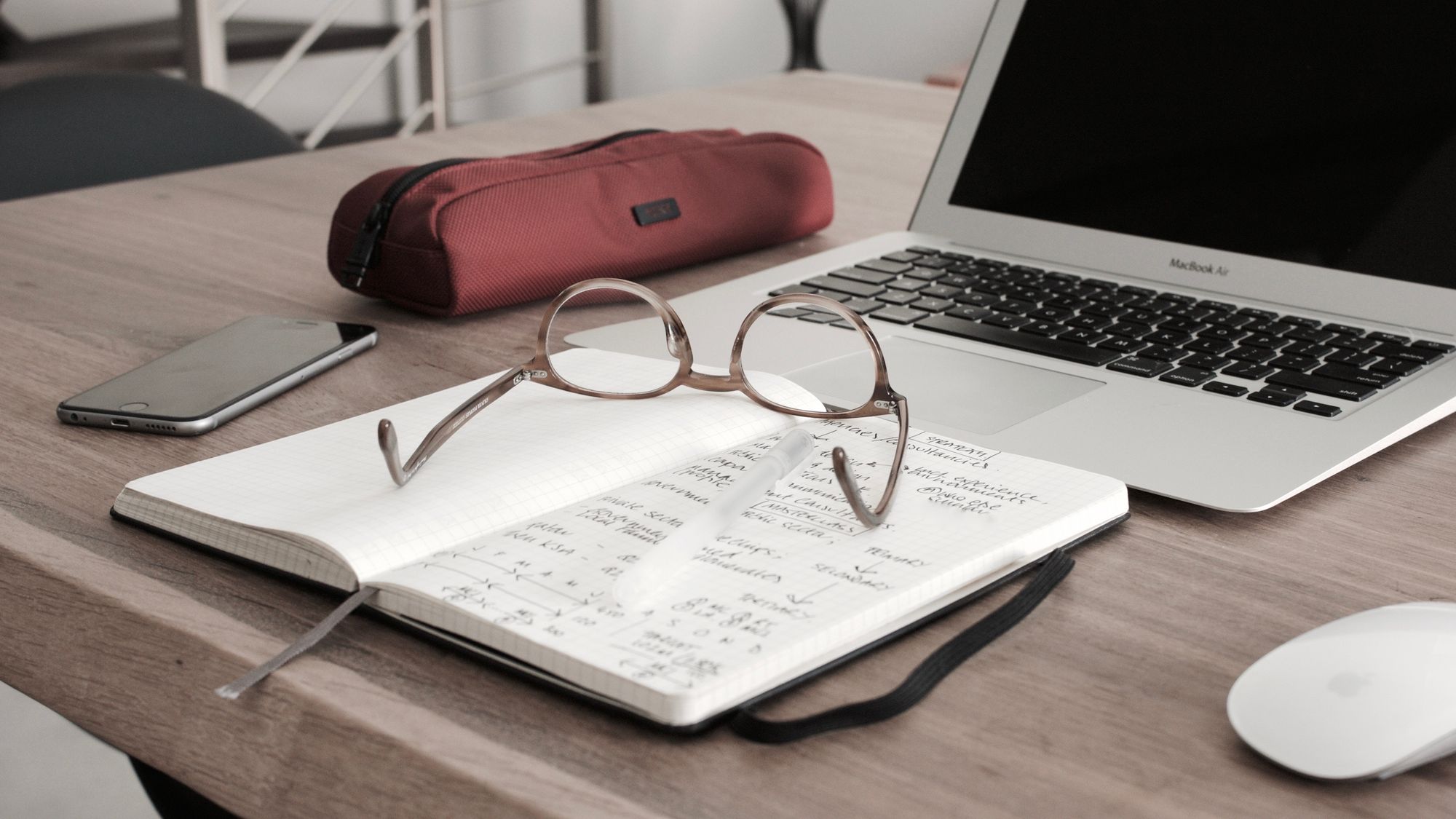
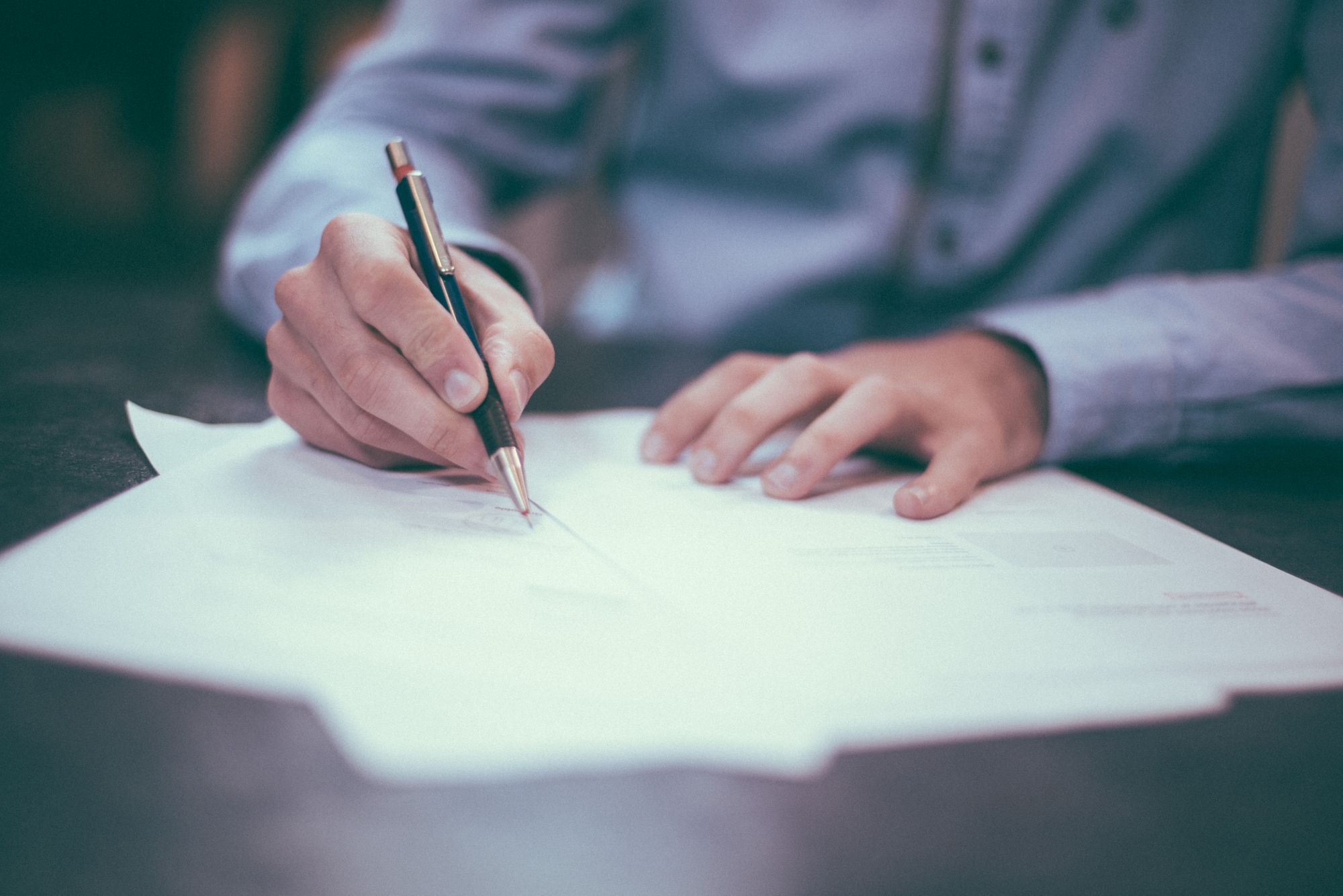