In today’s fast-paced manufacturing landscape, efficiency isn’t just a goal—it’s a necessity. Companies that embrace lean manufacturing report an average waste reduction of 20-30%, showcasing its tangible impact on productivity and cost savings.
Lean manufacturing isn’t about cutting corners; it’s about being smart with time, materials, and energy. By streamlining processes, businesses can create high-quality products while keeping expenses in check, ensuring long-term profitability and sustainability.
At its core, lean manufacturing is a transformative approach that enables companies to do more with less, optimizing workflows for maximum efficiency. It’s no surprise that 89% of businesses implementing lean practices see an improvement in overall operational efficiency.
By systematically eliminating inefficiencies, manufacturers can enhance speed, reduce unnecessary costs, and boost customer satisfaction. Think of it as a business makeover—one that ensures smoother, smarter, and more agile operations.
The primary objective of lean manufacturing is straightforward: be exceptionally good at what you do. This means identifying and eliminating anything that wastes time, resources, or effort.
The approach focuses on speed, cost savings, and continuous improvement, much like a superhero training program for businesses. Moreover, lean principles drive substantial financial benefits, contributing to an average of 15% cost reduction across industries, making it a strategic advantage for modern manufacturers.
While lean manufacturing is undeniably a game-changer, even the best systems come with challenges. This blog will explore the benefits and hurdles of lean implementation, helping businesses navigate the complexities of this approach.
To support manufacturers in their lean journey, Deskera Manufacturing ERP offers real-time production planning, automated inventory management, and AI-powered insights, ensuring seamless operations and data-driven decision-making. With the right tools and strategies, manufacturers can fully harness the power of lean and drive sustainable growth.
What is Lean Manufacturing?
Lean manufacturing is a production approach focused on minimizing waste while maximizing efficiency and quality. It emphasizes delivering more value with fewer resources by eliminating inefficiencies in processes, reducing costs, and improving overall productivity. Originating from the Toyota Production System (TPS), lean manufacturing has become a widely adopted strategy across industries to streamline operations and enhance customer satisfaction.
By continuously refining workflows and cutting unnecessary steps, lean manufacturing enables businesses to produce high-quality products faster and at lower costs. This approach fosters a culture of continuous improvement, where every aspect of production is optimized for efficiency. Modern manufacturers often integrate automation, ERP systems, and data-driven decision-making to further enhance lean processes, ensuring long-term sustainability and competitiveness.
5 Principles of Lean Manufacturing
Lean manufacturing is guided by five core principles that help businesses eliminate waste, improve efficiency, and enhance product value. These principles serve as the foundation for implementing a lean approach in any organization.
Value
The first principle focuses on defining value from the customer’s perspective. While manufacturers create products, the real measure of value is how much customers are willing to pay. By understanding customer needs and expectations, companies can eliminate unnecessary costs and processes while maximizing both profitability and customer satisfaction.
Map the Value Stream
This step involves analyzing the entire production process—from raw materials to final product delivery—to identify areas of waste and inefficiencies. By mapping out the value stream, companies can pinpoint non-value-adding activities and work toward eliminating them, ensuring that every step in the process contributes to the final product’s value.
Create Flow
Flow ensures that production processes run smoothly and without delays. Bottlenecks, interruptions, or unnecessary steps in the workflow increase costs and lead times. Lean manufacturing emphasizes streamlining operations so that materials, information, and resources move seamlessly from one stage to another, minimizing downtime and improving productivity.
Establish a Pull System
A pull system means that production is driven by actual customer demand rather than forecasts. Unlike traditional push systems, which rely on estimated production needs, the pull system only produces goods when they are needed, reducing excess inventory, storage costs, and waste. This approach enhances flexibility and responsiveness to market demand.
Pursue Perfection (Continuous Improvement)
The final principle, often called Kaizen, is about ongoing improvement. Lean manufacturing is not a one-time initiative but a continuous process of refining operations, reducing waste, and optimizing efficiency. Businesses must regularly assess and improve their workflows to achieve higher quality, faster production, and cost savings over time.
By implementing these five principles, companies can enhance efficiency, reduce waste, and improve overall competitiveness, making lean manufacturing a crucial strategy for modern production.
8 Wastes of Lean Manufacturing
Lean manufacturing identifies eight types of waste (Muda) that reduce efficiency, increase costs, and slow down production. These wastes do not add value to the customer and should be minimized or eliminated.
Defects
Errors in production lead to rework, scrap, and wasted materials, increasing costs and slowing down operations. Defects often result from poor-quality control, lack of standardized processes, or human errors.
Overproduction
Producing more than what is needed leads to excess inventory, storage costs, and potential product obsolescence. Overproduction ties up resources and often results from inaccurate demand forecasting or inefficient scheduling.
Waiting
Time wasted due to delays between production steps, machine downtime, or slow decision-making leads to inefficiencies. This waste occurs when workers or equipment remain idle due to bottlenecks or supply chain disruptions.
Non-Utilized Talent
Underutilizing employee skills, creativity, or knowledge prevents organizations from maximizing productivity and innovation. Failing to engage employees in problem-solving or decision-making is a missed opportunity for continuous improvement.
Transportation
Unnecessary movement of materials or products between processes, warehouses, or facilities adds time and cost without increasing value. Poor factory layout, excessive handling, or inefficient supply chains contribute to this waste.
Inventory
Holding excessive raw materials, work-in-progress (WIP), or finished goods ties up capital and space. Large inventories can lead to obsolescence, damage, and higher storage costs, making the production system less responsive to customer demand.
Motion
Unnecessary movements of employees, such as reaching, bending, walking, or searching for tools, reduce efficiency. Poor workstation design and lack of organization contribute to excessive motion waste.
Extra Processing
Performing more work than required, such as over-polishing, excessive documentation, or redundant inspections, leads to wasted effort and increased costs. This waste often results from unclear customer requirements or inefficient process design.
By identifying and eliminating these eight wastes, lean manufacturing improves efficiency, reduces costs, and enhances overall productivity, making production systems more agile and responsive to customer needs.
Key Lean Manufacturing Techniques
Lean manufacturing focuses on eliminating waste while continuously improving processes. Below are key techniques used to achieve efficiency, quality, and cost reduction:
1. Just-in-Time (JIT) Manufacturing
JIT ensures that materials, components, and products are produced and delivered only as needed, reducing excess inventory and storage costs. It relies on demand-driven production and efficient supply chain coordination.
2. Continuous Improvement (Kaizen)
Kaizen promotes small, incremental changes in daily operations to enhance productivity and efficiency. It encourages employee involvement and fosters a culture of ongoing improvement.
3. Heijunka (Production Leveling)
This technique balances production schedules to reduce fluctuations and bottlenecks, ensuring a steady and predictable workflow.
4. 5S Workplace Organization
A method to organize and maintain an efficient workspace, 5S includes:
- Sort (Seiri): Remove unnecessary items
- Set in Order (Seiton): Arrange items for easy access
- Shine (Seiso): Keep the workplace clean
- Standardize (Seiketsu): Implement standardized work practices
- Sustain (Shitsuke): Continuously improve and maintain organization
5. Kanban (Visual Workflow Management)
A pull-based system using visual signals (e.g., boards, cards, or electronic alerts) to streamline workflows and control inventory, supporting JIT manufacturing.
6. Jidoka (Automation with a Human Touch)
Jidoka ensures that machines detect abnormalities and stop automatically to prevent defects. Workers analyze and resolve issues before restarting production, improving quality.
7. Andon (Visual Alert System)
Andon is a real-time visual signaling system (e.g., flashing lights or screens) that alerts teams about production problems, allowing for quick intervention and resolution.
8. Poka-Yoke (Error Proofing)
Poka-yoke is a technique to prevent errors before they occur, ensuring processes are designed to minimize human mistakes. Examples include:
- Sensors that detect missing components
- Color-coded parts to prevent misplacement
9. Gemba Walks
Gemba means "the actual place." Managers perform Gemba walks to observe processes firsthand, identify inefficiencies, and engage with employees to find improvement opportunities.
10. Hoshin Kanri (Strategic Planning)
A top-down planning approach that aligns long-term company goals with daily operations, ensuring all employees work toward a common vision through structured execution.
11. Total Productive Maintenance (TPM)
TPM focuses on proactive and preventive maintenance by involving operators in equipment upkeep, reducing breakdowns, and ensuring maximum machine efficiency.
12. 5 Whys (Root Cause Analysis)
A problem-solving method where teams ask "Why?" five times to identify the root cause of an issue and develop effective long-term solutions.
13. Single-Minute Exchange of Die (SMED)
SMED reduces machine setup and changeover times to under 10 minutes, allowing for quick production switching and improved flexibility.
By integrating these lean manufacturing techniques, businesses can reduce waste, improve efficiency, enhance quality, and increase profitability while meeting customer demands more effectively.
Lean vs. Six Sigma: Understanding the Key Differences
Lean and Six Sigma are both methodologies aimed at improving processes, reducing waste, and increasing efficiency. However, they have distinct focuses and approaches.
Lean Six Sigma: The Best of Both Worlds
Many organizations combine Lean and Six Sigma into Lean Six Sigma (LSS) to achieve both efficiency and quality in their operations. This hybrid approach focuses on eliminating waste while ensuring process accuracy through data-driven improvements.
Key Benefits of Lean Manufacturing
Lean manufacturing offers a wide range of advantages, from reducing waste to improving customer satisfaction. While some see it as a way to increase company profits, others focus on its role in enhancing efficiency and product quality.
Below are some of the most impactful benefits of adopting lean manufacturing principles.
1. Improved Product Quality
To stay competitive, businesses must continuously enhance product quality to meet evolving customer expectations. Lean manufacturing encourages total quality management (TQM) and continuous improvement (Kaizen), ensuring that production processes minimize defects and deliver superior products.
2. Optimized Inventory Management
Lean manufacturing relies on Just-In-Time (JIT) production, which ensures that materials and products arrive exactly when needed. This minimizes excess inventory, lowers storage costs, and prevents production delays caused by overstocking or shortages.
3. Waste Reduction
Eliminating waste is at the core of lean principles. By removing non-value-added activities such as overproduction, defects, unnecessary motion, and waiting time, companies can cut costs, streamline operations, and improve efficiency.
4. Increased Productivity and Efficiency
By streamlining workflows and eliminating bottlenecks, lean manufacturing allows employees to focus on value-adding tasks. This results in:
- Faster production cycles
- Reduced downtime
- Higher throughput without additional resource consumption
5. Cost Efficiency
Implementing lean principles leads to significant cost savings, including:
- Lower inventory costs due to reduced overproduction
- Reduced defect rates, minimizing rework and material waste
- Energy and material savings from eliminating unnecessary steps
- Better resource allocation, ensuring that labor and equipment are used efficiently
6. Reduced Lead Time
Time is a critical factor in manufacturing. Lean techniques improve project timelines by:
- Eliminating process delays
- Enhancing workflow automation
- Focusing on pull-based production to ensure timely manufacturing
7. Environmental Benefits
By cutting down on waste, lean manufacturing reduces the environmental footprint of production. This includes lower energy consumption, reduced material wastage, and optimized transportation, contributing to sustainable business practices.
8. Enhanced Customer Satisfaction
Delivering high-quality products on time at a lower cost improves customer experience. Satisfied customers are more likely to return, boosting brand loyalty and long-term profitability.
Lean manufacturing is a powerful approach that enhances efficiency, quality, and cost-effectiveness while driving customer satisfaction. Businesses that implement lean principles can stay competitive, reduce waste, and optimize their operations for long-term success.
Challenges in Implementing Lean Manufacturing
While lean manufacturing offers numerous benefits, its implementation is not without challenges. Companies must address several obstacles to ensure the successful adoption of lean principles.
1. Employee Resistance and Frustration
Employees accustomed to traditional processes may resist change due to fear of job loss, increased workload, or lack of understanding of lean principles. Without proper training and engagement, this resistance can hinder lean adoption.
2. Employee Safety and Well-being Concerns
The relentless focus on efficiency and waste reduction can sometimes overlook employee well-being. Workers may experience increased stress and burnout due to strict production schedules, limited margins for error, and high expectations for performance.
3. High Dependence on Supplier Reliability
Lean manufacturing relies heavily on Just-In-Time (JIT) inventory management, meaning raw materials must arrive exactly when needed. Any supplier delays or unexpected disruptions (e.g., transportation issues, raw material shortages) can cause production bottlenecks.
4. Equipment Reliability and Maintenance Risks
Lean manufacturing maximizes machine utilization, requiring equipment to function at optimal capacity. However, this increases the risk of machine failure, which can disrupt production and cause costly downtime. Regular preventive maintenance is essential but adds to operational costs.
5. Difficulty in Standardization
Unlike rigid manufacturing models, lean is a philosophy rather than a fixed framework. This lack of standardization can lead to inconsistent implementation across different departments or facilities, making it challenging to maintain uniform quality and efficiency.
6. Impact on Future Business Development
Lean’s focus on reducing waste may lead management to cut areas that are not immediately profitable but are critical for future innovation and expansion. This short-term focus can hinder long-term growth and business sustainability.
7. Risk of Delivery Inconsistencies
Since lean manufacturing operates with minimal inventory, any delays in production or supply chain disruptions can lead to inconsistent delivery times. This can be particularly problematic during seasonal demand spikes or unexpected market shifts.
Implementing lean manufacturing requires a strategic balance between efficiency and flexibility. Companies must proactively address employee concerns, invest in equipment maintenance, and establish strong supplier relationships to mitigate these challenges. While lean principles can drive efficiency and cost savings, their success depends on proper planning, training, and adaptability.
How to Successfully Implement Lean Manufacturing
Implementing lean manufacturing requires a structured, strategic, and people-centric approach to maximize efficiency while maintaining quality and sustainability. Here’s a step-by-step guide to effectively integrating lean principles into your manufacturing processes.
1. Define Your Purpose and Goals
Before implementing lean, you must identify your core objectives. Why does your organization need lean manufacturing? Is it to improve efficiency, reduce waste, enhance product quality, or lower operational costs? Defining a clear purpose ensures alignment across all levels of the organization.
- Set SMART goals (Specific, Measurable, Achievable, Relevant, and Time-bound) to track progress.
- Socialize your lean vision to gain company-wide support.
2. Design a Simple and Efficient Manufacturing System
Breaking down processes into simplified, manageable components makes it easier to identify inefficiencies and eliminate waste.
- Implement value stream mapping to analyze current workflows and pinpoint bottlenecks.
- Use Kanban boards to visualize tasks and streamline production.
- Standardize processes to reduce variability and ensure consistency.
3. Foster a Culture of Continuous Improvement
Lean manufacturing thrives on an ongoing cycle of refinement rather than one-time changes. Encourage all employees to actively look for improvement opportunities.
- Kaizen (Continuous Improvement): Regularly review and refine manufacturing processes.
- Encourage cross-functional collaboration to find innovative solutions.
- Use feedback loops to refine workflows based on real-time performance data.
4. Engage and Empower Employees
Employee resistance is one of the biggest obstacles to lean adoption. Ensuring staff buy-in is crucial for success.
- Provide training on lean principles so employees understand the benefits.
- Involve workers in decision-making and problem-solving initiatives.
- Implement a reward system to recognize employees who contribute to process improvements.
- Assign a Lean Champion—a leader who promotes lean methodologies across the organization.
5. Implement and Track Incremental Improvements
Instead of drastic changes, gradual, data-driven enhancements ensure long-term success.
- Start with small, measurable improvements before scaling up.
- Use key performance indicators (KPIs) to monitor progress, such as cycle time, defect rates, and inventory turnover.
- Audit supply chains to identify inefficiencies in sourcing, production, and delivery.
6. Prioritize Efficient Inventory Management
Managing inventory efficiently is central to lean manufacturing. Avoid overproduction and excess stock that ties up resources.
- Adopt Just-In-Time (JIT) inventory to minimize waste and reduce carrying costs.
- Leverage inventory control software for real-time tracking and optimization.
- Re-evaluate packaging and shipping processes to eliminate unnecessary handling and excess materials.
7. Establish a Preventive Maintenance Program
Lean manufacturing relies on equipment operating at peak efficiency. Downtime due to unexpected breakdowns can disrupt production.
- Create a preventive maintenance schedule to inspect, repair, and replace machinery proactively.
- Implement predictive maintenance technology to anticipate failures before they happen.
- Train operators in autonomous maintenance to enhance machine reliability.
8. Balance Agility with Organizational Needs
Companies often struggle to align lean with individual, departmental, and corporate objectives. Managing these competing needs effectively is key to success.
- Organize teams into cross-functional units to improve collaboration.
- Adopt lean portfolio management to balance cost control with agility.
- Use data-driven decision-making to assess and adjust lean strategies.
9. Embrace Experimentation and Innovation
Lean manufacturing encourages a culture of learning from failures to drive continuous innovation.
- Test new processes on a small scale before full implementation.
- Seek customer feedback to refine product designs and production methods.
- Reduce the impact of failure by failing fast, testing often, and iterating quickly.
Successfully implementing lean manufacturing is a continuous journey, not a one-time initiative. By defining clear goals, engaging employees, simplifying workflows, and leveraging technology, organizations can maximize efficiency, reduce waste, and enhance overall productivity. The key lies in commitment, collaboration, and a willingness to evolve.
Future Trends in Lean Manufacturing
As manufacturing continues to evolve, lean principles are adapting to new technologies, sustainability goals, and workforce transformations.
Here are the key future trends shaping the next phase of lean manufacturing:
1. Integration of Industry 4.0 and Smart Manufacturing
- Advanced automation, IoT, and AI-driven analytics are enhancing lean efficiency.
- Real-time data collection and predictive maintenance reduce downtime and waste.
- Digital twins allow manufacturers to simulate and optimize production before implementation.
2. AI-Driven Process Optimization
- Machine learning algorithms analyze historical data to predict inefficiencies.
- AI-powered demand forecasting minimizes overproduction and stockouts.
- Intelligent automation streamlines workflows while maintaining lean principles.
3. Sustainable and Green Lean Manufacturing
- Energy-efficient production processes align with lean’s waste-reduction philosophy.
- Circular economy models promote recycling, reuse, and minimal environmental impact.
- Carbon footprint tracking helps companies meet sustainability compliance standards.
4. Agile and Resilient Supply Chains
- Lean principles are merging with supply chain agility to manage global disruptions.
- Vendor Managed Inventory (VMI) and Just-In-Time (JIT) models are adapting to dynamic demand.
- Digital supply chain twins enhance visibility and proactive decision-making.
5. Employee-Centric Lean Approaches
- Workforce upskilling programs integrate lean methodologies with digital literacy.
- Collaborative robotics (cobots) support human workers while reducing repetitive tasks.
- Lean culture now focuses more on employee well-being and engagement.
6. Hyper-Personalization in Manufacturing
- Lean processes are being adapted for mass customization and small-batch production.
- AI-driven production planning enables faster shifts between product variations.
- Smart factories leverage real-time customization while maintaining lean efficiency.
How Deskera Manufacturing ERP Supports Lean Manufacturing
Lean manufacturing focuses on eliminating waste, optimizing processes, and improving efficiency. Deskera Manufacturing ERP helps businesses achieve these lean principles through automation, real-time insights, and streamlined operations. Here’s how:
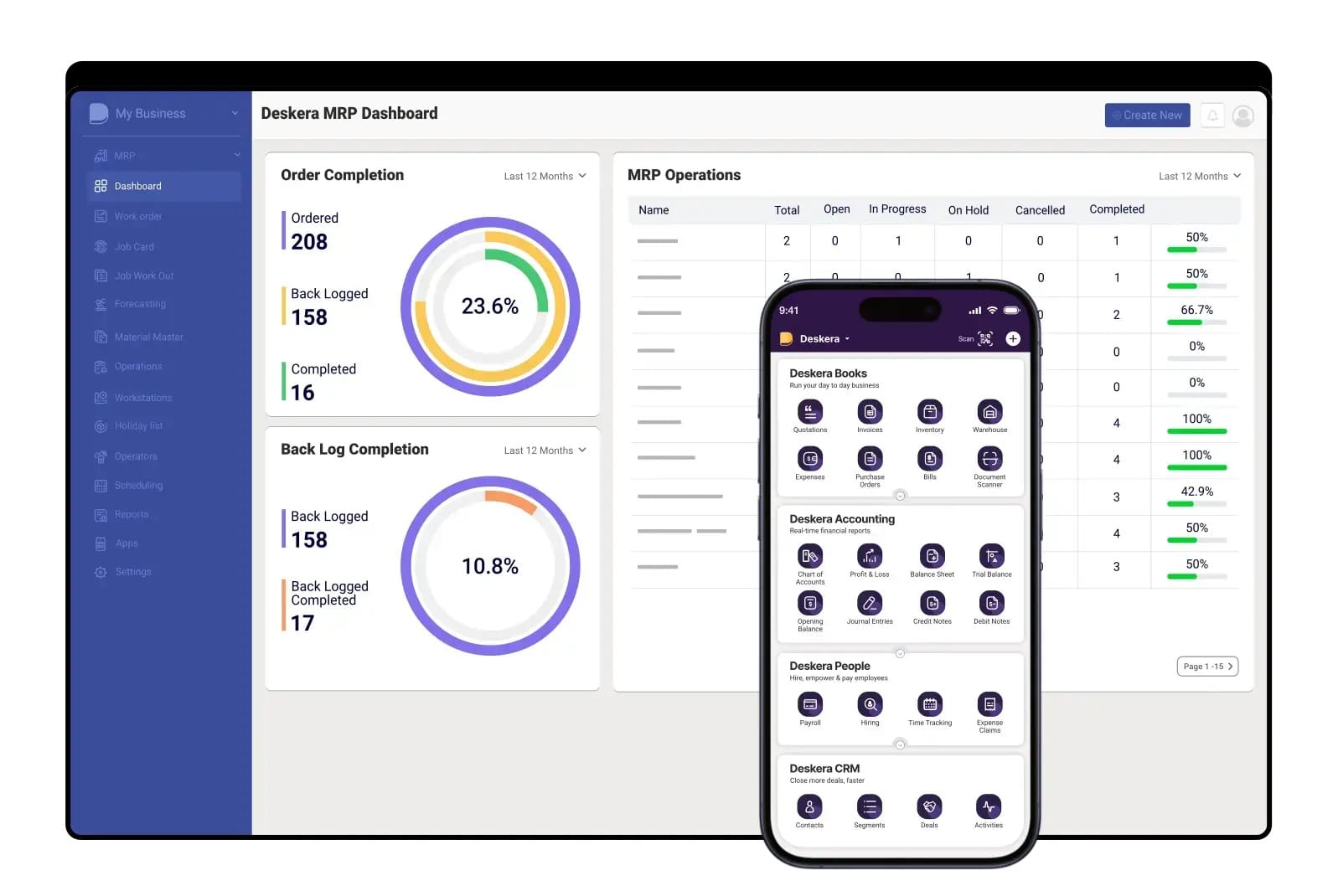
1. Real-Time Production Monitoring
- Track production progress, machine efficiency, and resource utilization in real time.
- Identify bottlenecks and eliminate inefficiencies before they impact output.
2. Just-In-Time (JIT) Inventory Management
- Automate procurement and ensure materials arrive only when needed.
- Reduce excess inventory, lower carrying costs, and minimize waste.
3. Demand Forecasting and Production Planning
- AI-powered demand forecasting prevents overproduction and stock shortages.
- Advanced planning tools align production schedules with actual demand.
4. Digital Work Order Management
- Automate and optimize work orders to reduce delays and manual errors.
- Improve coordination between departments for seamless operations.
5. Waste Reduction and Cost Optimization
- Identify and eliminate non-value-adding activities through data-driven insights.
- Automate reporting to track key performance indicators (KPIs) and cost-saving opportunities.
6. Quality Control and Compliance
- Maintain high-quality standards with automated inspections and compliance tracking.
- Reduce defects and rework, ensuring a lean and efficient production process.
Deskera Manufacturing ERP empowers businesses with real-time monitoring, automated workflows, and data-driven decision-making, making it an ideal solution for achieving lean manufacturing efficiency, cost reduction, and process optimization.
Key Takeaways
- Definition of Lean Manufacturing – Lean manufacturing is a production methodology focused on minimizing waste while maximizing value for the customer.
- The Five Principles of Lean Manufacturing – The core principles include identifying value, mapping the value stream, creating a smooth workflow, establishing a pull system, and striving for continuous improvement.
- Types of Waste in Lean Manufacturing – Lean manufacturing aims to eliminate common types of waste, including overproduction, waiting time, excess inventory, motion inefficiencies, defects, transportation, and underutilized talent.
- Benefits of Lean Manufacturing – Key advantages include cost savings, improved productivity, enhanced product quality, faster delivery times, and increased customer satisfaction.
- Lean Manufacturing Tools and Techniques – Popular lean tools such as Kaizen, 5S, Kanban, Value Stream Mapping, and Just-In-Time (JIT) help businesses streamline operations and eliminate inefficiencies.
- Challenges in Implementing Lean Manufacturing – Organizations may face resistance to change, implementation costs, cultural shifts, and the need for continuous employee training when adopting lean practices.
- Future Trends in Lean Manufacturing – The integration of Industry 4.0 technologies, automation, AI-driven analytics, and IoT is shaping the future of lean manufacturing, making processes even more efficient and data-driven.
Related Articles
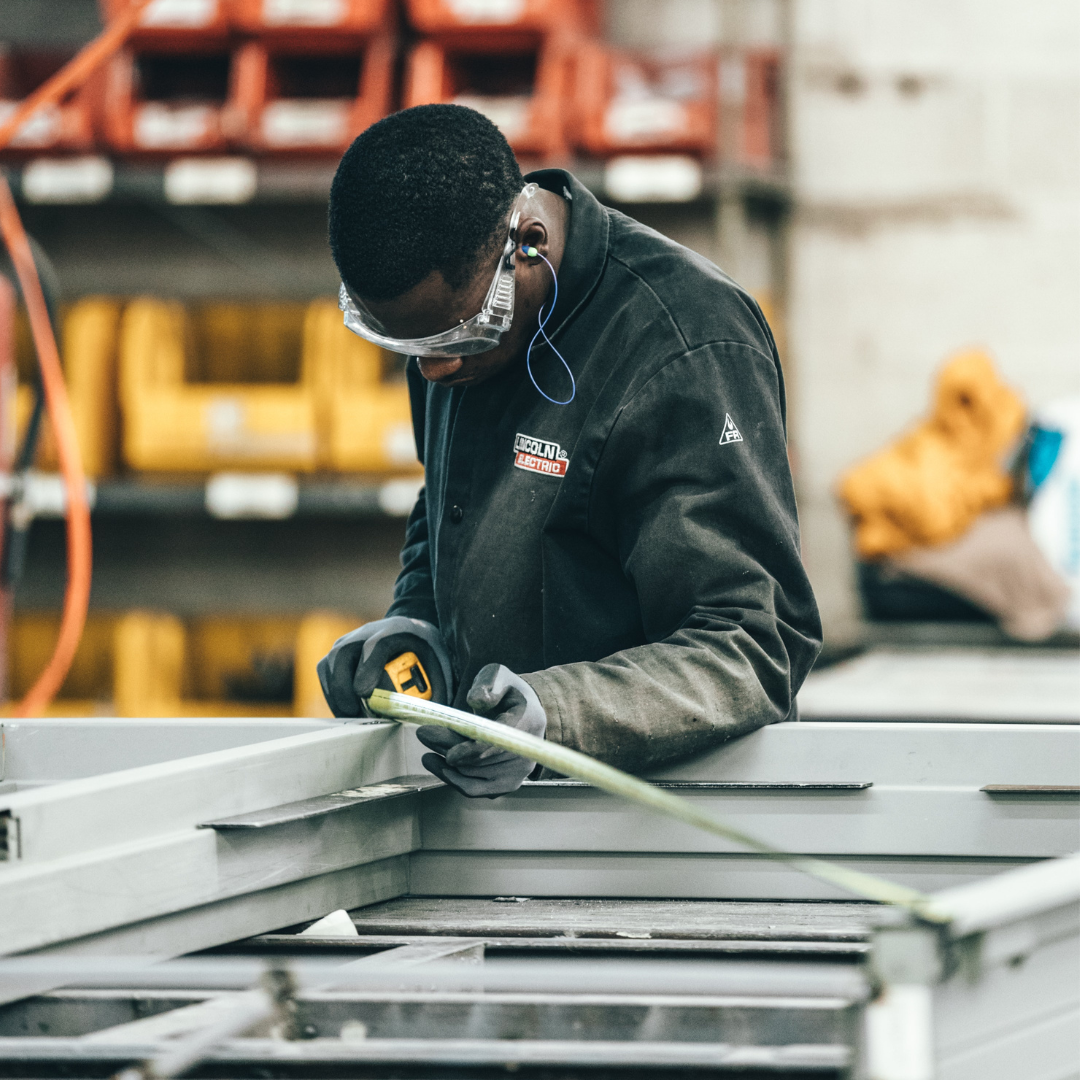
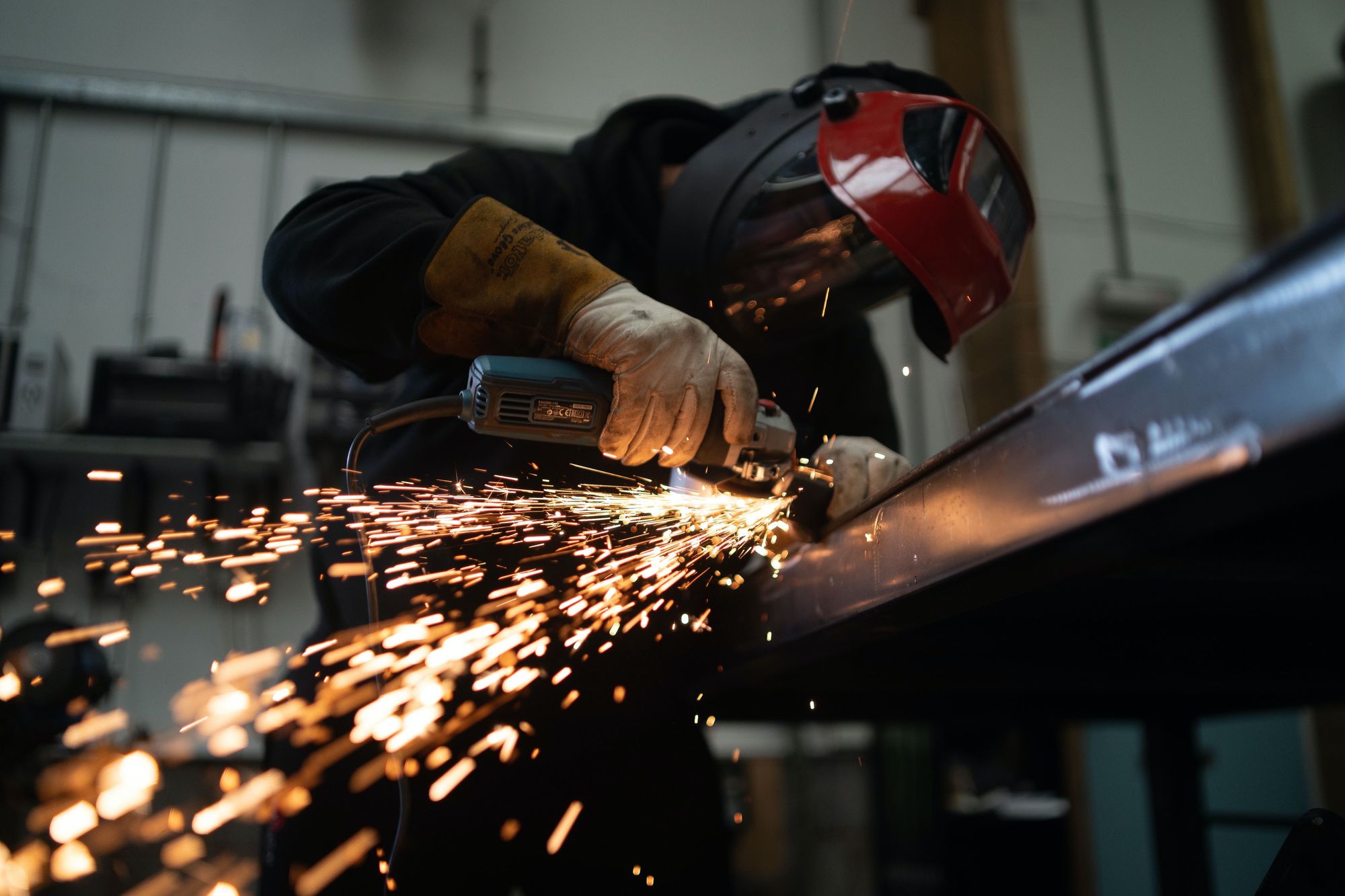
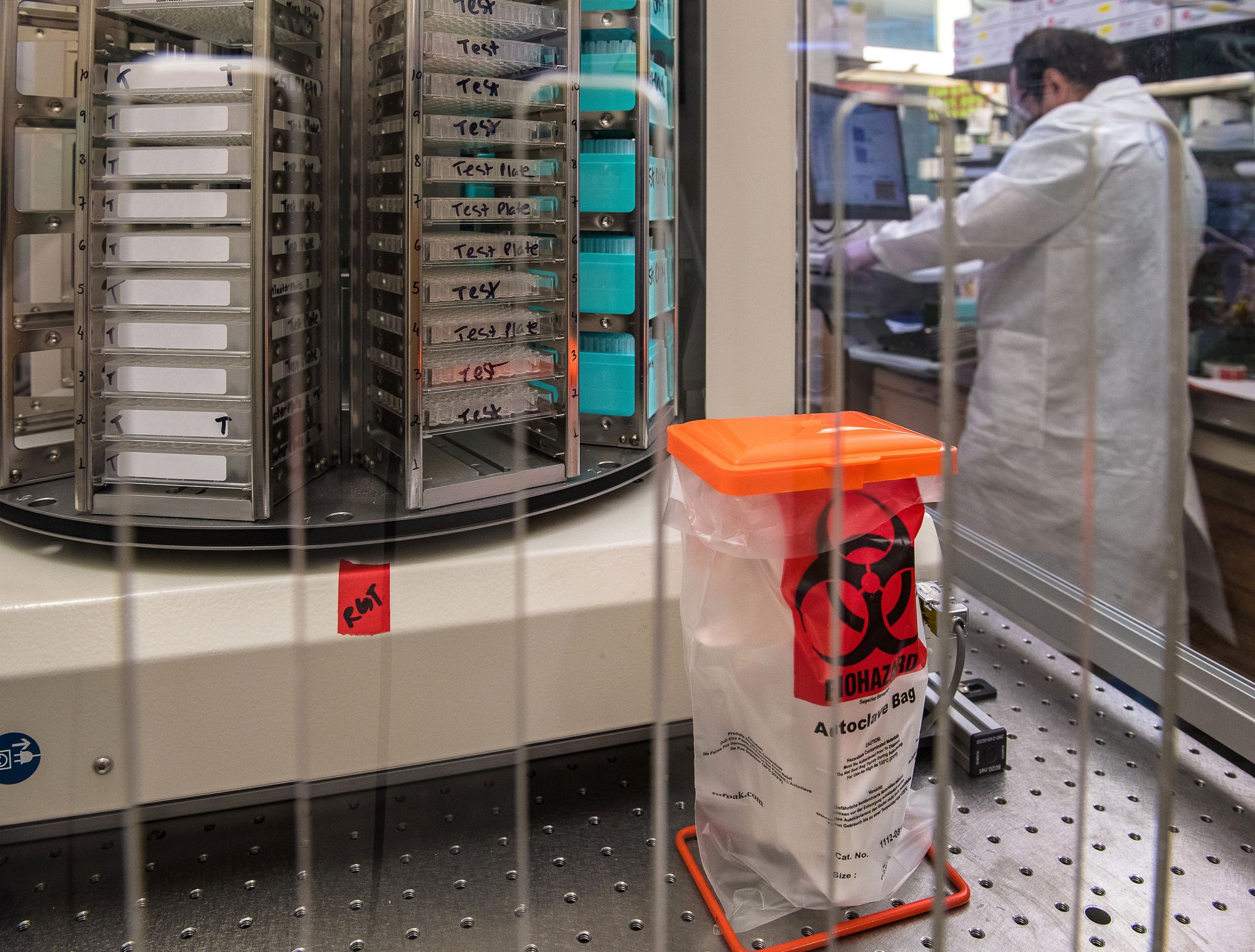
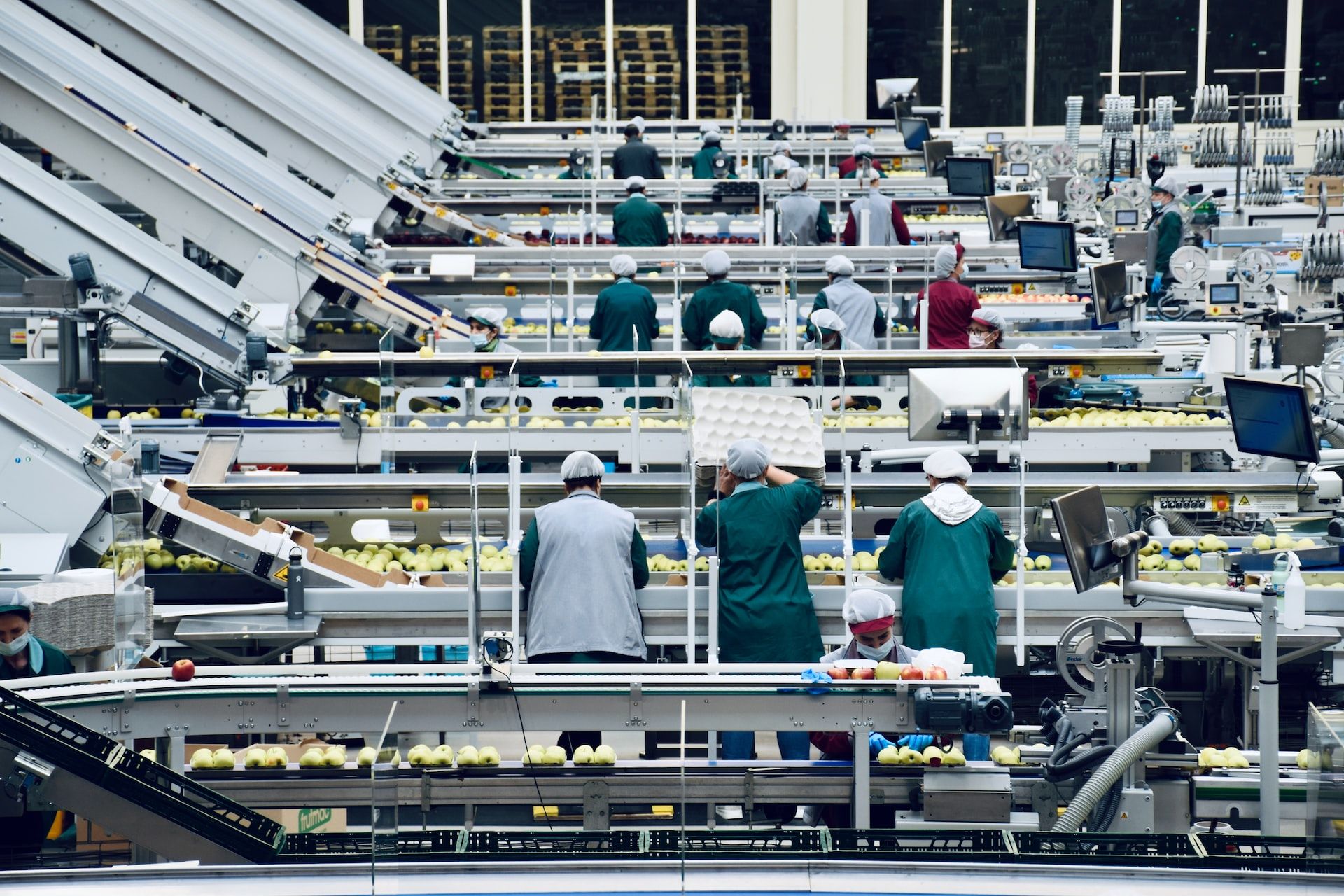

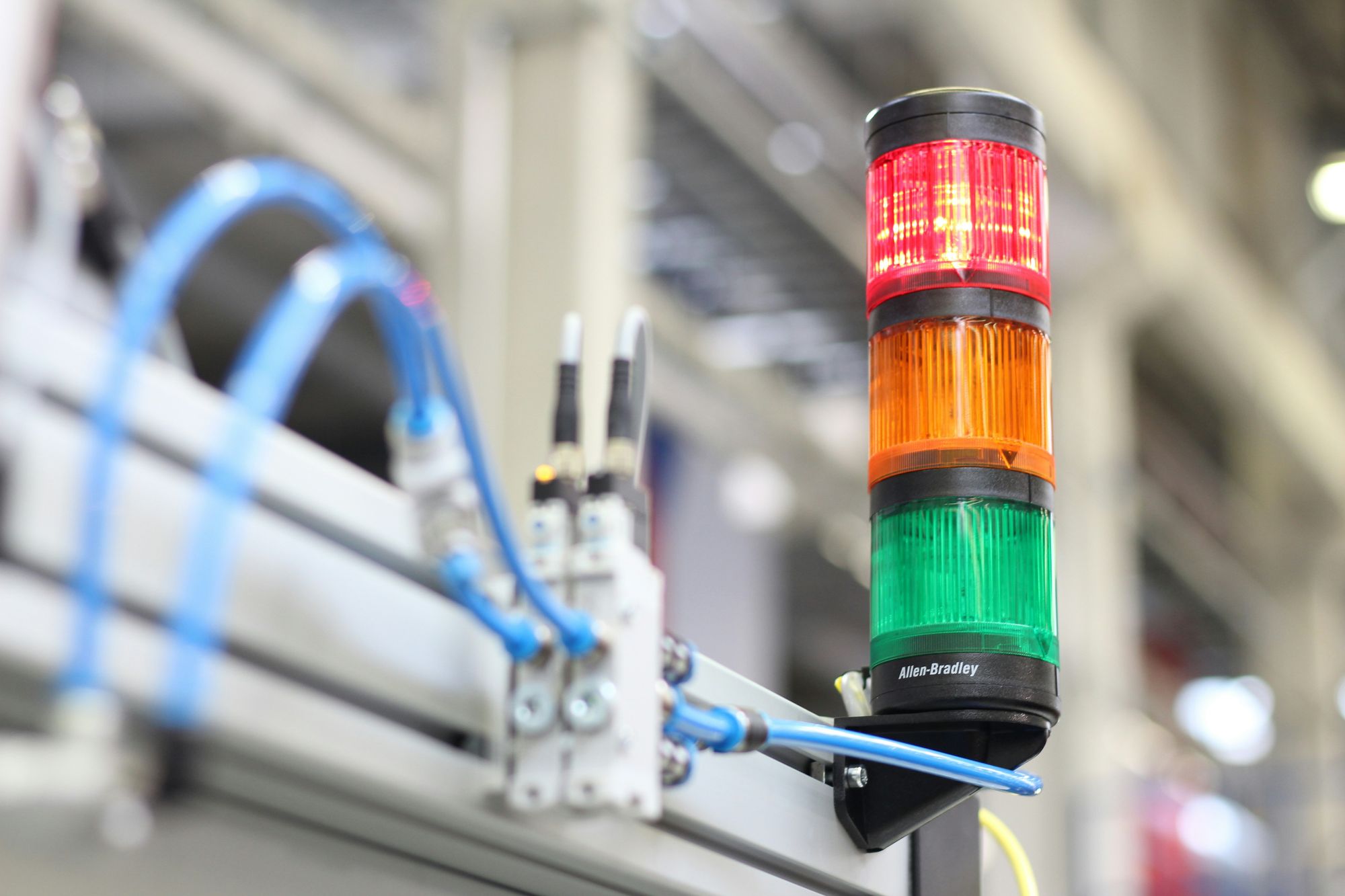