Are you looking to understand how you can improve your bottom line with a multi-level bill of materials? If your answer is yes, then you are on the right page.
A Multi-Level Bill of Materials (BOM) is a comprehensive and structured representation of a product's assembly, capturing the intricate relationships between its components and sub-components.
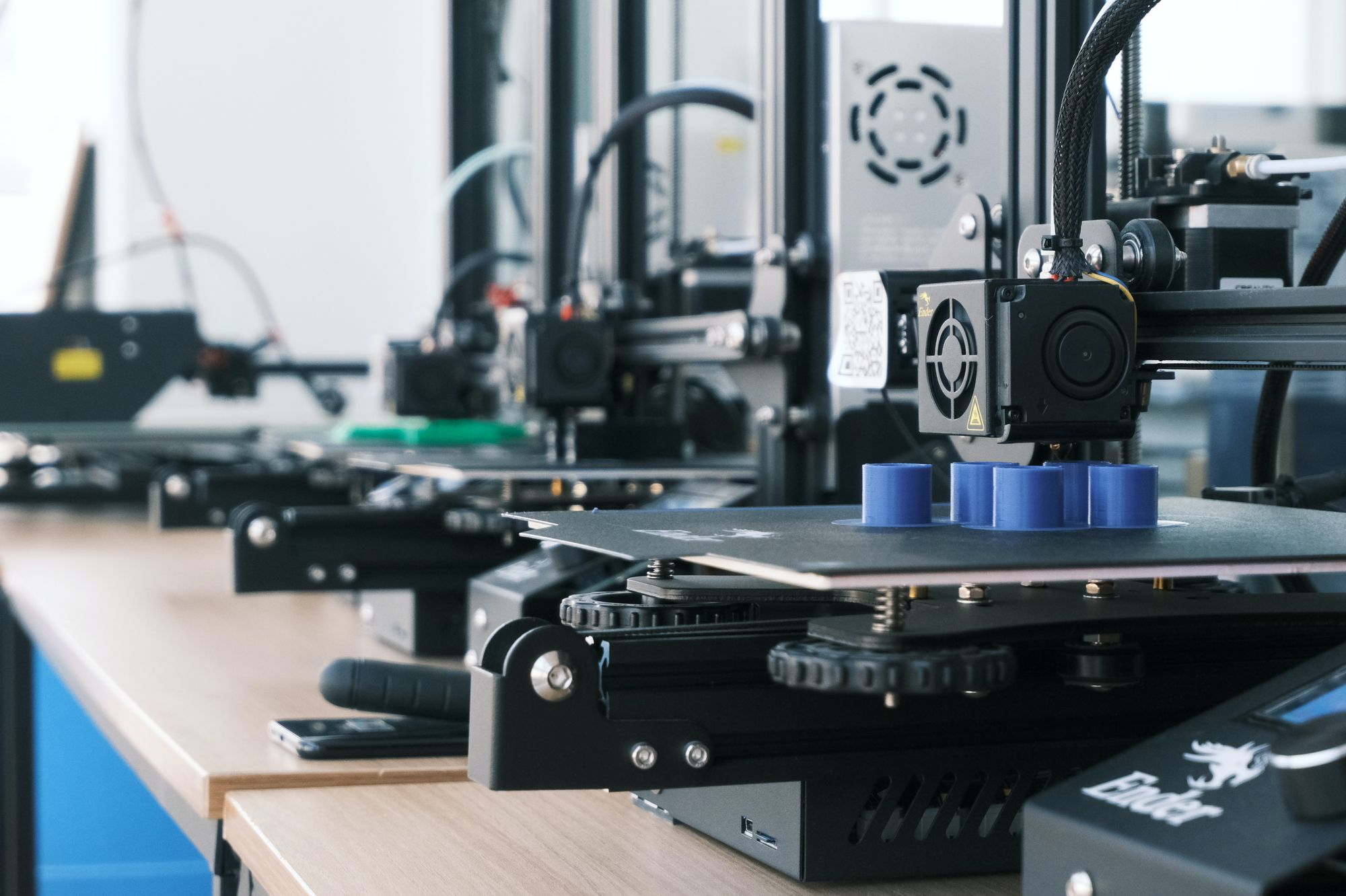
This dynamic tool goes beyond a mere list of parts; it provides a detailed roadmap of how these elements come together to create the final product. Leveraging a Multi-Level BOM can be a transformative strategy for businesses seeking to enhance their operational efficiency, optimize resource allocation, and ultimately boost their bottom line.
In this dynamic business landscape, where competitiveness and profitability are paramount, harnessing the power of a Multi-Level BOM offers a multifaceted approach to achieving these goals.
By delving into the intricate details of each component, assembly level, and associated costs, a Multi-Level BOM equips businesses with a wealth of insights that lay the groundwork for strategic decision-making.
In the following article, we will delve into ten compelling ways in which a Multi-Level BOM can significantly improve your bottom line. The topics covered in this article are:
- All About Multi-Level Bill of Materials
- What is Bottom Line?
- Significance of Bottom Line
- All About Improving Your Bottom Line
- Importance of Improving Bottom Line
- 10 Ways Multi-Level Bill of Materials Can Improve Your Bottom Line
- How Does a Multi-Level BOM Impact Quality Control?
- How Does a Multi-Level BOM Contribute to Data-Driven Decisions?
- How Can Businesses Adopt a Multi-Level BOM Effectively?
- How Can Deskera Help You with a Multi-Level Bill of Materials?
- Key Takeaways
- Related Articles
All About Multi-Level Bill of Materials
A Multi-Level Bill of Materials (BOM) is a hierarchical representation of a product's components and subcomponents, organized in multiple levels of detail. It is a crucial tool in manufacturing, engineering, and product management for planning, production, and tracking purposes. Multi-level BOMs provide a structured view of how products are assembled, showing the relationships between parent and child components.
Here's a comprehensive overview of the concept:
1. Hierarchy Levels: A multi-level BOM typically consists of several levels, each representing a different level of detail in the product's structure. The levels are organized in a parent-child relationship, where the highest level is the finished product (top-level assembly), and subsequent levels break down the product into its constituent parts and sub-assemblies.
2. Components and Subcomponents: Each level of the BOM contains a list of components required to build the parent assembly. These components can themselves be assemblies with their own BOMs, creating a nested structure. This hierarchy allows for a clear understanding of how a product is built from the ground up.
3. Part Numbers and Descriptions: Every component in the BOM is typically assigned a unique part number and description, which aids in identifying and locating the correct part during the manufacturing process. These details help prevent confusion and ensure accurate assembly.
4. Quantities: Quantities for each component are specified in the BOM, indicating how many of each part are required to build a single unit of the parent assembly. These quantities ensure that the correct amount of each part is ordered and used during production.
5. Indented BOM: An indented BOM is a visual representation of the multi-level structure, where each level is indented to show its relationship to higher and lower levels. This format makes it easier to understand the hierarchical arrangement of components.
6. Bill of Materials Explosion: BOM explosion refers to the process of breaking down a multi-level BOM into its individual components and subcomponents. This is essential for procurement, as it helps determine the quantities of each part required for a specific production run.
7. Bill of Materials Implosion: BOM implosion is the reverse process of explosion. It involves aggregating the requirements of multiple assemblies to calculate the total quantities of components needed for a certain number of finished products.
8. Engineering Change Management: Multi-level BOMs play a critical role in managing engineering changes. When modifications are made to a component or assembly, the BOM is updated to reflect these changes. This ensures that everyone involved in the manufacturing process is aware of and implements the necessary adjustments.
9. Manufacturing Planning and Costing: Multi-level BOMs are essential for production planning and cost estimation. They help determine the raw materials, labor, and resources needed for production, as well as the overall cost of manufacturing.
10. Software and Tools: There are various software applications and tools available to manage multi-level BOMs. These tools facilitate collaboration, version control, and real-time updates across different teams involved in product development and manufacturing processes.
In summary, a multi-level Bill of Materials is a structured representation of a product's components and subcomponents organized in a hierarchical manner. It is a crucial tool for managing product development, production, and cost estimation in various industries.
What is Bottom Line?
The term "bottom line" is commonly used in business and finance to refer to the final and most important result, figure, or conclusion of a situation or analysis. It is often used to summarize the overall financial performance or outcome of a business or an individual. The bottom line essentially represents the net profit or loss after all expenses, costs, and revenues have been accounted for.
In accounting and financial statements, the "bottom line" typically refers to the net income or net profit, which is calculated by subtracting all expenses (such as operating costs, taxes, interest, and depreciation) from the total revenue. The resulting figure represents the company's earnings, and it is an essential indicator of the financial health and profitability of the business.
In a broader context, the term "bottom line" is also used to convey the fundamental or most important point in a discussion, decision, or situation. It's often used idiomatically to emphasize the core outcome or takeaway. For example, if someone says, "The bottom line is that we need to increase our sales to remain competitive," they are emphasizing the essential conclusion or action point.
Overall, "bottom line" is a versatile term used in various contexts, primarily in business and finance, to highlight the ultimate result, financial performance, or core message.
Significance of Bottom Line
The significance of the "bottom line" lies in its central role as a key indicator of financial performance, profitability, and overall success in business and financial analysis.
Here are some of the key reasons why the bottom line is significant:
1. Financial Performance Evaluation: The bottom line, often represented as net income or net profit, provides a clear and concise summary of a company's financial performance over a specific period. It reflects the difference between total revenues and total expenses, offering insight into whether the company is making a profit or incurring a loss.
2. Business Sustainability: A positive bottom line is essential for a business's long-term sustainability and growth. It signifies that the company is generating enough revenue to cover its operating costs, debt obligations, and investments, and still has profits left over.
3. Decision Making: The bottom line serves as a critical reference point for making strategic business decisions. Executives, investors, and stakeholders use the bottom line to assess the potential impact of various decisions on a company's financial health.
4. Performance Comparison: Comparing the bottom line across different time periods or with industry benchmarks allows businesses to track their progress and performance. It helps identify trends, opportunities for improvement, and areas where cost reductions or revenue enhancements may be needed.
5. Investment Decisions: Investors and financial analysts closely examine a company's bottom line when making investment decisions. A consistently healthy bottom line suggests a well-managed and financially stable company, which can attract potential investors.
6. Creditworthiness: Lenders and creditors assess a company's bottom line to determine its creditworthiness and ability to repay loans. A strong bottom line can lead to favorable borrowing terms and lower interest rates.
7. Valuation: The bottom line is a critical factor in determining the valuation of a company. When companies are valued for mergers, acquisitions, or potential sales, the bottom line plays a significant role in estimating the company's worth.
8. Employee Motivation and Incentives: A positive bottom line can lead to improved employee morale and job security. Companies with healthy profits are often better positioned to offer competitive compensation, benefits, and incentives to their employees.
9. Taxation: Tax authorities use the bottom line to assess a company's tax liability. The taxable income is derived from the net income after various deductions and allowances.
10. Accountability and Transparency: The bottom line is a clear and quantifiable measure that holds business leaders and management accountable for the financial performance of the company. It promotes transparency and facilitates effective communication with stakeholders.
In essence, the significance of the bottom line extends beyond mere financial figures; it serves as a critical metric for measuring a company's financial health, guiding decision-making, attracting investors, and ensuring the sustainability and growth of the business.
All About Improving Your Bottom Line
Improving the bottom line is a strategic objective for businesses seeking to enhance profitability and financial performance. Achieving this goal involves a combination of tactics and strategies aimed at increasing revenues, reducing costs, and optimizing operations.
Here's a comprehensive guide on how to improve your bottom line:
1. Revenue Growth: Increasing revenue is a primary driver of improving the bottom line. Consider these approaches:
- Market Expansion: Identify new markets or customer segments to target with your products or services.
- Product Innovation: Develop new offerings or enhance existing products to meet customer needs and preferences.
- Pricing Optimization: Review pricing strategies to ensure they reflect the value you provide and capture maximum customer willingness to pay.
- Upselling and Cross-Selling: Encourage customers to buy more by offering complementary products or higher-tier options.
2. Cost Management: Reducing costs is another effective way to improve profitability:
- Operational Efficiency: Streamline processes, eliminate waste, and improve productivity to reduce operational costs.
- Supply Chain Optimization: Negotiate favorable terms with suppliers, minimize inventory carrying costs, and improve logistics.
- Energy and Resource Efficiency: Implement eco-friendly practices to lower utility bills and environmental impact.
- Technology Adoption: Invest in automation, software, and systems that enhance efficiency and reduce manual labor.
3. Expense Reduction: Controlling expenses is crucial for a healthy bottom line:
- Overhead Costs: Identify areas where overhead costs can be reduced without compromising quality or customer satisfaction.
- Employee Costs: Evaluate staffing levels, optimize workforce scheduling, and implement cost-effective employee benefits.
- Outsourcing: Consider outsourcing non-core functions to specialized service providers to reduce fixed costs.
4. Strategic Investments: Certain investments can yield long-term benefits for your bottom line:
- Research and Development: Invest in innovation to create new products or improve existing ones, which can lead to increased market share and revenue.
- Marketing and Branding: Allocate resources to effective marketing campaigns that increase brand visibility and customer acquisition.
5. Customer Focus: Aim to enhance customer satisfaction and loyalty:
- Customer Service: Provide exceptional customer service to retain existing customers and attract new ones through positive word-of-mouth.
- Customer Feedback: Regularly gather feedback to improve products and services based on customer preferences.
6. Financial Management: Effective financial management is crucial for improving the bottom line:
- Cash Flow Management: Optimize cash flow to ensure sufficient liquidity for operations and growth initiatives.
- Debt Management: Refinance high-interest debts and negotiate favorable terms with lenders.
- Working Capital: Optimize inventory levels, accounts receivable, and accounts payable to maintain healthy working capital ratios.
7. Data-Driven Decision-Making: Use data and analytics to make informed decisions:
- Performance Metrics: Monitor key performance indicators (KPIs) to identify areas of improvement and measure progress.
- Market Trends: Analyze industry trends and customer behavior to identify growth opportunities.
8. Employee Engagement: Engaged and motivated employees contribute to improved performance:
- Training and Development: Invest in employee training and development to enhance skills and productivity.
- Recognition and Incentives: Reward employees for their contributions and provide incentives for achieving performance targets.
9. Continuous Improvement: Implement a culture of continuous improvement:
- Kaizen Philosophy: Encourage employees at all levels to identify and implement small improvements that add up over time.
- Lean Principles: Apply lean thinking to eliminate waste and streamline processes.
10. Adaptability and Innovation: Stay agile and open to change to remain competitive:
- Market Trends: Keep a close eye on market trends and consumer preferences to adapt your offerings accordingly.
- Disruption: Embrace digital transformation and disruptive technologies to stay ahead of competitors.
Remember that improving the bottom line is an ongoing effort that requires careful planning, execution, and adaptation. Each business is unique, so it's important to tailor these strategies to your specific industry, market conditions, and organizational strengths. Regularly assess your progress, measure results, and make adjustments as needed to achieve sustained improvement in your bottom line.
Importance of Improving Bottom Line
Improving the bottom line is a fundamental goal for businesses and organizations, as it directly impacts their financial health, growth potential, and overall success.
Here are several key reasons why improving the bottom line is important:
1. Financial Health and Sustainability: A strong bottom line reflects a healthy and sustainable financial position. By increasing net income and profitability, a business ensures that it can cover operating expenses, debt obligations, and investments, reducing the risk of financial instability or insolvency.
2. Business Growth and Investment: Higher profitability provides the necessary resources for a business to invest in growth opportunities. Whether it's expanding into new markets, launching new products, or acquiring other companies, a robust bottom line enables strategic investments that drive long-term success.
3. Competitive Advantage: Improving the bottom line can lead to cost efficiencies, allowing a company to offer competitive pricing while maintaining profitability. This can help the business gain an edge over competitors and attract more customers.
4. Innovation and R&D: Higher profits can be allocated to research and development (R&D), fostering innovation and the creation of new products or services. Innovation can lead to differentiation, increased market share, and enhanced customer satisfaction.
5. Attracting Investors and Capital: A strong bottom line is attractive to potential investors, lenders, and creditors. Businesses with a history of improving profitability are more likely to secure funding at favorable terms, providing capital for expansion and operational needs.
6. Employee Morale and Motivation: Improved profitability can lead to higher employee morale and motivation. When employees see that their efforts contribute to a successful bottom line, they are more likely to be engaged and committed to their work.
7. Compensation and Benefits: Higher profits may enable a company to provide better compensation packages, benefits, and incentives for employees. This can help attract and retain top talent, leading to a more skilled and dedicated workforce.
8. Risk Mitigation: A stronger bottom line provides a buffer against unexpected challenges or downturns in the market. Businesses with higher profits are better equipped to weather economic uncertainties and disruptions.
9. Shareholder Value: For publicly traded companies, a healthier bottom line can lead to increased shareholder value. Higher profits often translate to higher stock prices and dividends, rewarding shareholders for their investment.
10. Tax Efficiency: A well-managed bottom line can lead to better tax planning and optimization. By maximizing profits while managing expenses, a company can minimize its tax liability within legal and ethical boundaries.
11. Community and Social Impact: A profitable business is more likely to have the resources to contribute to social and community initiatives. This can enhance the company's reputation, strengthen relationships with stakeholders, and create positive social change.
In summary, improving the bottom line is essential for a business's financial strength, growth prospects, and overall success. It allows companies to invest in innovation, attract investment, retain talent, and better navigate challenges, ultimately contributing to long-term sustainability and positive impact.
10 Ways Multi-Level Bill of Materials Can Improve Your Bottom Line
A Multi-Level Bill of Materials (BOM) can play a significant role in improving your bottom line by enhancing efficiency, cost-effectiveness, and overall operational effectiveness. Here are 10 ways a Multi-Level BOM can contribute to your financial success:
Cost Transparency
Cost transparency refers to the clear and comprehensive visibility into the various costs associated with producing a product. In the context of a Multi-Level Bill of Materials (BOM), cost transparency involves understanding the costs of all the components and subcomponents required to assemble a finished product.
Here's a more detailed explanation of how cost transparency through a Multi-Level BOM can improve your bottom line:
1. Component-Level Cost Breakdown: A Multi-Level BOM breaks down the product's structure into its individual components and sub-components, each with its associated cost. This detailed breakdown allows you to see the cost contribution of each part to the overall product cost. As a result, you can identify which components have the highest cost impact and focus your cost-saving efforts accordingly.
2. Accurate Cost Estimation: With cost transparency provided by the Multi-Level BOM, you can accurately estimate the total cost of manufacturing a product. This accuracy is crucial for setting competitive prices that also ensure profitability. Overestimating costs might result in uncompetitive pricing while underestimating costs could lead to loss-making sales.
3. Cost Control and Reduction: By understanding the cost structure at a granular level, you can identify opportunities for cost reduction. You can analyze alternative suppliers, materials, or manufacturing methods for components with higher costs, thereby optimizing your sourcing decisions and reducing expenses.
4. Value Engineering: Cost transparency enables value engineering, where you assess whether specific components or features contribute enough value to justify their costs. You can explore ways to simplify designs without compromising quality, resulting in cost savings without sacrificing functionality.
5. Budgeting and Financial Planning: When you have a detailed breakdown of costs, you can create more accurate budgets and financial forecasts. This helps in managing cash flow, allocating resources efficiently, and planning for investments or expansion.
6. Cost Allocation in Pricing Strategies: Knowing the individual costs of components helps you decide how to allocate costs in your pricing strategies. You can set prices based on perceived value, competitive positioning, or cost-plus pricing models, all while ensuring a healthy profit margin.
7. Benchmarking and Supplier Negotiations: Cost transparency empowers you to benchmark component costs against industry standards and competitors. Additionally, during supplier negotiations, you can discuss pricing based on factual data, leading to better deals and potential cost savings.
8. Preventing Cost Overruns: A Multi-Level BOM helps prevent cost overruns by providing a clear overview of all anticipated costs. This ensures that there are no surprises during the manufacturing process, preventing unplanned expenses that could negatively impact profitability.
In essence, cost transparency through a Multi-Level BOM empowers you with accurate, detailed information about the cost structure of your products. This information allows for informed decision-making, better cost management, and strategic actions to improve your bottom line by maximizing profits and minimizing unnecessary expenditures.
Effective Resource Allocation
Effective resource allocation is a crucial aspect of optimizing your operations and improving your bottom line. In the context of a Multi-Level Bill of Materials (BOM), effective resource allocation refers to the strategic distribution of materials, labor, equipment, and other resources to different assembly levels and components within a product's structure.
Here's a more detailed explanation of how effective resource allocation through a Multi-Level BOM can contribute to your financial success:
1. Resource Optimization: With a Multi-Level BOM, you gain insights into the specific materials and quantities required for each component and sub-component. This information allows you to optimize your resource planning by ensuring that you procure and allocate the right amount of materials and resources to meet production demands, reducing waste and excess inventory.
2. Production Scheduling: Understanding the resource requirements at different assembly levels helps you create more accurate and efficient production schedules. You can allocate resources based on lead times, production capacities, and demand forecasts, minimizing production bottlenecks and delays.
3. Workforce Management: Effective resource allocation involves assigning the right people with the necessary skills to the appropriate tasks. With a Multi-Level BOM, you can match labor resources to specific assembly levels, ensuring that skilled workers are assigned where they are needed most.
4. Equipment Utilization: You can optimize the use of machinery and equipment by aligning them with the production needs of different components and subcomponents. This prevents underutilization or overutilization of equipment, leading to higher operational efficiency.
5. Cost Efficiency: Effective resource allocation helps control costs by preventing the overuse of resources, reducing excess inventory carrying costs, and minimizing overtime expenses due to poor scheduling. This cost control directly contributes to improving your bottom line.
6. Just-In-Time Production: Resource allocation guided by a Multi-Level BOM allows you to implement just-in-time (JIT) production practices. By allocating resources based on real-time demand, you can reduce the need for excess inventory, storage costs, and the risk of obsolescence.
7. Scalability and Growth: As your business grows, effective resource allocation becomes even more critical. A Multi-Level BOM enables you to scale your operations efficiently by ensuring that resources are allocated to meet increased production without causing inefficiencies or excessive costs.
8. Bottleneck Identification: Resource allocation based on the Multi-Level BOM can help identify potential bottlenecks in the production process. By analyzing resource availability and constraints at different assembly levels, you can proactively address production challenges and prevent disruptions.
9. Continuous Improvement: Resource allocation is an ongoing process that can benefit from continuous improvement efforts. Regularly analyzing resource utilization and making adjustments based on the Multi-Level BOM data allows you to refine your allocation strategies over time.
In summary, effective resource allocation through a Multi-Level BOM enables you to optimize the distribution of materials, labor, equipment, and other resources throughout your production process. This optimization leads to improved operational efficiency, reduced costs, and enhanced overall productivity, all of which contribute to a healthier bottom line.
Accurate Cost Estimation
Accurate cost estimation is a critical factor in effective financial planning, pricing, and overall profitability for businesses. In the context of a Multi-Level Bill of Materials (BOM), accurate cost estimation refers to the ability to precisely calculate the total cost of manufacturing a product by considering all the individual components, sub-components, labor, and other associated expenses.
Here's a more detailed explanation of how accurate cost estimation through a Multi-Level BOM can contribute to your financial success:
1. Comprehensive Cost Breakdown: A Multi-Level BOM provides a detailed breakdown of all components and sub-components required for a product. Each item is associated with its corresponding cost, allowing for a comprehensive view of the total cost structure.
2. Material Costs: Accurate cost estimation considers the costs of all materials needed for each component and sub-component. This includes raw materials, intermediate components, and any purchased parts.
3. Labor Costs: Labor costs associated with assembling, testing, and inspecting each component are factored into the cost estimation. The time and skill required for each assembly level contribute to the overall labor expenses.
4. Overhead Costs: Overhead costs, such as facility expenses, utilities, equipment depreciation, and administrative expenses, are accurately allocated to each component based on its share of the total production process.
5. Process Complexity: Different assembly levels may involve varying degrees of complexity, which affects costs. Accurate cost estimation reflects these complexities, helping you account for the resources and time required for each level.
6. Supplier Costs: Cost estimation considers the prices negotiated with suppliers for each component. This ensures that your cost calculations are aligned with your procurement agreements.
7. Currency Fluctuations and Inflation: Accurate cost estimation takes into account currency fluctuations and inflation that may affect the cost of materials and resources over time, allowing for more precise financial planning.
8. Pricing Strategies: By knowing the accurate cost of production, you can set pricing strategies that ensure profitability while remaining competitive in the market. This prevents underpricing that may erode margins or overpricing that may deter customers.
9. Profit Margin Calculation: Accurate cost estimation enables you to calculate profit margins with confidence. You can determine the appropriate margin that ensures both sustainability and a reasonable return on investment.
10. Cost Optimization: With accurate cost estimation, you can identify components or processes with high costs. This knowledge enables you to explore cost-saving alternatives, such as alternative suppliers, materials, or manufacturing methods.
11. Proposal and Bid Preparation: For projects involving bids or proposals, accurate cost estimation ensures that your offers are realistic and aligned with the actual costs of production. This increases your chances of winning contracts while maintaining profitability.
12. Financial Forecasting and Budgeting: Accurate cost estimation provides a solid foundation for financial forecasting and budgeting. It allows you to project costs accurately and plan for resource allocation in the short and long term.
In summary, accurate cost estimation through a Multi-Level BOM is essential for making informed business decisions, setting competitive prices, managing expenses, and ultimately improving your bottom line. It provides a precise view of the costs involved in manufacturing your products, enabling you to optimize your operations and maximize profitability.
Optimized Production Planning
Optimized production planning is a key aspect of efficient operations and improved profitability in manufacturing. In the context of a Multi-Level Bill of Materials (BOM), optimized production planning refers to the strategic scheduling, allocation of resources, and coordination of activities required to manufacture products while minimizing costs and maximizing output.
Here's a more detailed explanation of how optimized production planning through a Multi-Level BOM can contribute to your financial success:
1. Demand Forecasting: An optimized production plan starts with accurate demand forecasting. By analyzing historical data, market trends, and customer orders, you can predict future demand and adjust production levels accordingly.
2. Resource Allocation: Using the Multi-Level BOM, you can allocate resources such as materials, labor, and equipment based on the requirements of each assembly level. This prevents overallocation or under allocation of resources, leading to smoother operations.
3. Capacity Planning: Optimized production planning considers the capacities of various workstations, machines, and labor resources. By aligning production volumes with available capacities, you can prevent bottlenecks and ensure efficient utilization of resources.
4. Lead Time Management: Production planning involves managing lead times for the procurement of materials, production processes, and order fulfillment. A Multi-Level BOM helps you accurately estimate lead times at different assembly levels, enabling timely delivery to customers.
5. Minimized Changeovers: Efficient production planning minimizes changeover times between different product variants or assembly levels. By grouping similar production runs, you reduce downtime and setup costs associated with frequent changeovers.
6. Sequencing and Prioritization: Optimized production planning determines the sequence in which different components and sub-components are produced and assembled. Prioritization is based on factors such as customer orders, due dates, and resource availability.
7. Reduced Work-in-Progress (WIP): By synchronizing production with demand and minimizing excess inventory, optimized production planning reduces work-in-progress (WIP). This leads to better cash flow, less waste, and lower holding costs.
8. Just-in-Time (JIT) Implementation: Production planning based on the Multi-Level BOM supports JIT manufacturing, where materials are ordered and produced only as needed. JIT minimizes storage costs and reduces the risk of obsolete inventory.
9. Cost Reduction: Efficient production planning helps reduce production costs by eliminating inefficiencies, optimizing resource utilization, and preventing costly disruptions. This directly contributes to improved profitability.
10. On-Time Delivery: Optimized production planning enhances your ability to fulfill customer orders on time. Meeting delivery commitments boosts customer satisfaction, strengthens relationships, and encourages repeat business.
11. Continuous Improvement: Production planning is an iterative process that benefits from continuous improvement. By regularly analyzing production performance and adjusting plans based on Multi-Level BOM data, you can refine your planning strategies over time.
12. Scalability and Flexibility: An optimized production plan takes into account your business's growth trajectory and the ability to scale operations. It also provides the flexibility to adapt to changing market conditions and unexpected demand fluctuations.
In summary, optimized production planning through a Multi-Level BOM ensures that your manufacturing processes are aligned with demand, resources are efficiently allocated, and costs are minimized. This leads to smoother operations, reduced waste, enhanced customer satisfaction, and ultimately, improved bottom-line results.
Inventory Management
Inventory management is a critical aspect of efficient operations and cost control in manufacturing and distribution. In the context of a Multi-Level Bill of Materials (BOM), inventory management refers to the strategic planning, tracking, and optimization of inventory levels for the various components and sub-components required to produce finished products.
Here's a more detailed explanation of how effective inventory management through a Multi-Level BOM can contribute to your financial success:
1. Demand Forecasting: Inventory management starts with accurate demand forecasting. By analyzing historical data, market trends, and customer orders, you can predict future demand for each component and sub-component.
2. Reorder Points and Lead Times: Using the Multi-Level BOM, you can establish optimal reorder points and lead times for each inventory item. This ensures that you replenish stock at the right time to avoid stockouts while minimizing excess inventory.
3. Minimized Stockouts: Accurate inventory management based on the Multi-Level BOM helps prevent stockouts of critical components. By maintaining adequate stock levels, you ensure that production is not disrupted due to material shortages.
4. Reduced Excess Inventory: Optimized inventory management prevents overstocking by aligning inventory levels with actual production requirements. This reduces carrying costs, storage expenses, and the risk of inventory obsolescence.
5. Batch and Lot Control: For items subject to batch or lot control, the Multi-Level BOM helps you track the origin and history of each batch, ensuring compliance with quality standards and regulatory requirements.
6. FIFO/LIFO Management: Effective inventory management enables proper management of First-In-First-Out (FIFO) or Last-In-First-Out (LIFO) inventory methods, which can impact the cost of goods sold (COGS) calculations and tax implications.
7. Supplier Performance: By monitoring inventory levels and order frequencies for each supplier, you can assess their performance in terms of timely deliveries and order accuracy. This information informs supplier negotiations and decisions.
8. Lead Time Variability: The Multi-Level BOM allows you to consider lead time variability for different components and subcomponents. This is crucial for planning inventory levels to accommodate fluctuations in lead times.
9. Cost Efficiency: Accurate inventory management helps optimize working capital by minimizing tied-up funds in excess inventory. This can lead to improved cash flow and reduced borrowing costs.
10. JIT Implementation: Efficient inventory management supports Just-In-Time (JIT) production practices, where components are ordered and produced only as needed. JIT minimizes inventory holding costs and improves cash flow.
11. Seasonal and Cyclical Demand: For products with seasonal or cyclical demand patterns, optimized inventory management ensures that you have the right amount of inventory on hand to meet peak demand periods without overstocking during slower periods.
12. Inventory Turnover: Effective inventory management can lead to higher inventory turnover rates, indicating that you are efficiently utilizing inventory to generate sales. This is a key financial metric that impacts profitability.
13. Safety Stock Planning: Accurate inventory management helps in determining appropriate safety stock levels. Safety stock ensures that you can handle unexpected demand fluctuations without disruption.
In summary, effective inventory management through a Multi-Level BOM ensures that you have the right amount of inventory at the right time to support production and meet customer demand.
This reduces costs associated with carrying excess inventory, prevents stockouts, and enhances operational efficiency, ultimately contributing to improved financial performance and a healthier bottom line.
Supplier Negotiations
Supplier negotiations are a critical aspect of procurement and can significantly impact your operational costs and overall profitability. In the context of a Multi-Level Bill of Materials (BOM), supplier negotiations refer to the process of engaging with suppliers to secure favorable terms, pricing, and conditions for the components and materials required for your products.
Here's a more detailed explanation of how effective supplier negotiations through a Multi-Level BOM can contribute to your financial success:
1. Informed Decision Making: A Multi-Level BOM provides detailed insights into the components and sub-components required for your products. This information allows you to make informed decisions during supplier negotiations by clearly communicating your requirements and understanding the implications of different sourcing options.
2. Quantity Discounts: With accurate knowledge of the quantities needed for each component, you can leverage this information to negotiate volume-based discounts with suppliers. Bulk purchasing can lead to cost savings and improved profit margins.
3. Cost Breakdown: A Multi-Level BOM enables you to break down the costs associated with each component, including materials, labor, and overhead. This transparency can be shared with suppliers, promoting open discussions and potential cost-reduction opportunities.
4. Value Analysis: During negotiations, you can conduct value analysis discussions with suppliers. By examining the cost and performance of different materials or components, you can collaboratively explore options to optimize costs without compromising quality.
5. Long-Term Partnerships: Supplier negotiations based on the Multi-Level BOM foster collaborative relationships. Suppliers appreciate transparency and a clear understanding of your needs, which can lead to more favorable terms and support during supply chain disruptions.
6. Quality Standards: A Multi-Level BOM specifies the required quality standards for each component. During negotiations, you can emphasize the importance of meeting these standards and ensure that the agreed-upon quality is maintained.
7. Lead Time Agreements: By sharing lead time requirements from the Multi-Level BOM, you can negotiate lead time agreements that align with your production schedules. Timely deliveries help prevent production delays and associated costs.
8. Risk Mitigation: Supplier negotiations informed by the Multi-Level BOM allow you to discuss strategies for mitigating supply chain risks. This includes backup suppliers, safety stock agreements, and contingency plans.
9. Contractual Terms: Detailed information from the Multi-Level BOM enables you to negotiate contract terms that accurately reflect your product specifications, lead times, delivery schedules, and pricing.
10. Competitive Advantage: Effective supplier negotiations can lead to cost advantages that translate into competitive pricing for your end products. This can attract more customers and enhance your market position.
11. Continuous Improvement: Supplier negotiations are ongoing. Regularly sharing Multi-Level BOM data and engaging in discussions with suppliers can lead to continuous improvement initiatives that benefit both parties.
12. Total Cost Consideration: Supplier negotiations based on the Multi-Level BOM encourage a holistic approach to cost considerations. It helps you factor in not only the initial cost of components but also the long-term impact on production, quality, and overall profitability.
In summary, supplier negotiations informed by a Multi-Level BOM provide a solid foundation for constructive and effective discussions with suppliers. It ensures that you secure optimal terms, pricing, and conditions that contribute to cost savings, quality assurance, and improved profitability, ultimately enhancing your bottom line.
Root Cause Analysis
Root cause analysis is a systematic process used to identify the underlying causes of issues or problems within a business or operational context. In the context of a Multi-Level Bill of Materials (BOM), root cause analysis refers to the method of tracing defects, quality issues, or inefficiencies back to their origin within the product's structure and assembly process.
Here's a more detailed explanation of how root cause analysis through a Multi-Level BOM can contribute to your financial success:
1. Defect Identification: When defects or quality issues arise in a finished product, the Multi-Level BOM provides a roadmap to identify the specific components or sub-components that might be causing the problem.
2. Component Relationships: A Multi-Level BOM illustrates the interdependencies and relationships between different components and assembly levels. This helps in understanding how defects at one level might propagate to other levels.
3. Informed Decision Making: Root cause analysis using the Multi-Level BOM enables informed decision-making. You can accurately pinpoint which components or processes need improvement, guiding your corrective actions.
4. Process Optimization: Identifying root causes through the Multi-Level BOM allows you to optimize manufacturing processes. By addressing the specific components or assembly steps causing defects, you can enhance overall product quality and reduce waste.
5. Preventive Measures: Root cause analysis helps you implement preventive measures to avoid recurring defects. By identifying and addressing the root causes, you can reduce the likelihood of similar issues arising in the future.
6. Continuous Improvement: The insights gained from root cause analysis based on the Multi-Level BOM contribute to a culture of continuous improvement. You can use this knowledge to refine processes and prevent defects from occurring in subsequent production runs.
7. Quality Assurance: Accurate root cause analysis helps you maintain consistent product quality. By addressing root causes, you enhance the reliability and durability of your products, reducing the likelihood of costly recalls or customer dissatisfaction.
8. Cost Reduction: Addressing the root causes of defects leads to cost reduction. By minimizing rework, scrap, and production disruptions, you save on labor, materials, and operational expenses.
9. Supplier Collaboration: Root cause analysis using the Multi-Level BOM can involve collaboration with suppliers. Together, you can identify issues related to supplied components and work towards solutions that improve product quality and reliability.
10. Data-Driven Decisions: The Multi-Level BOM provides factual data for root cause analysis, facilitating data-driven decisions rather than relying on assumptions or guesswork.
11. Compliance and Regulatory Requirements: Addressing root causes can help ensure compliance with industry regulations and standards. It demonstrates a commitment to product quality and safety.
12. Problem Solving and Accountability: Root cause analysis promotes problem-solving and accountability within your organization. By identifying and addressing the root causes, you create a culture of responsibility and continuous improvement.
In summary, root cause analysis through a Multi-Level BOM is a powerful tool for identifying and addressing issues within your manufacturing processes. It helps you optimize operations, enhance product quality, reduce costs, and drive continuous improvement, all of which contribute to a stronger bottom line and improved financial performance.
Efficient Engineering Changes
Efficient engineering changes, often referred to as change management or engineering change orders (ECOs), involve making modifications to product designs, components, or processes in a streamlined and effective manner. In the context of a Multi-Level Bill of Materials (BOM), efficient engineering changes refer to the ability to implement design modifications or updates while minimizing disruptions, rework, and associated costs.
Here's a more detailed explanation of how efficient engineering changes through a Multi-Level BOM can contribute to your financial success:
1. Accurate Impact Assessment: A Multi-Level BOM provides a comprehensive view of a product's structure, detailing how components and subcomponents are interconnected. When engineering changes are proposed, this visibility allows for an accurate assessment of how the changes will impact various assembly levels and components.
2. Faster Decision-Making: With a Multi-Level BOM, you can quickly evaluate the implications of proposed engineering changes. This leads to faster decision-making as you can identify potential challenges, risks, and benefits before implementing the changes.
3. Minimized Rework and Scrap: Efficient engineering changes help prevent unnecessary rework or scrap. By accurately understanding the impact of changes, you can avoid situations where modifications lead to the need for extensive rework or disposal of materials.
4. Reduced Downtime: Accurate impact assessment through a Multi-Level BOM allows you to plan for the most efficient way to implement changes. This reduces downtime during the transition period, ensuring that production continues with minimal disruptions.
5. Resource Optimization: Efficient engineering changes help optimize the allocation of resources such as labor, equipment, and materials during the changeover process. This prevents overutilization of resources and minimizes associated costs.
6. Supplier Communication: When engineering changes involve modifications to components or materials, a Multi-Level BOM helps facilitate communication with suppliers. You can accurately convey the updated requirements, ensuring that the right components are sourced for the revised design.
7. Quality Control: Implementing engineering changes with a Multi-Level BOM ensures that quality control measures are effectively applied. You can verify that the revised components meet the required standards and specifications.
8. Faster Time to Market: Efficient engineering changes expedite the process of updating products to meet market demands or address issues. This results in a shorter time to market for new and improved products.
9. Regulatory Compliance: When engineering changes impact regulatory compliance, a Multi-Level BOM assists in ensuring that the modifications are properly documented and validated to meet industry standards.
10. Collaboration and Communication: A Multi-Level BOM enhances collaboration and communication among different departments involved in the change management process. It provides a clear reference point for cross-functional teams to work together seamlessly.
11. Version Control: Efficient engineering changes involve maintaining accurate version control of BOMs. This prevents confusion and ensures that the correct and latest version of the BOM is used for planning and production.
12. Cost Efficiency: By reducing rework, scrap, and downtime, efficient engineering changes contribute to cost savings. The streamlined process allows you to allocate resources more effectively, leading to improved operational efficiency.
In summary, efficient engineering changes through a Multi-Level BOM enable you to implement design modifications or updates with precision, minimizing disruptions, and optimizing resources. This leads to faster innovation, improved product quality, reduced costs, and enhanced overall profitability.
Product Lifecycle Management
Product Lifecycle Management (PLM) is a comprehensive approach to managing the entire lifecycle of a product, from its initial concept and design through manufacturing, distribution, use, and eventual retirement or disposal.
In the context of a Multi-Level Bill of Materials (BOM), PLM refers to the systematic management of product information and processes using the BOM as a central component.
Here's a more detailed explanation of how PLM through a Multi-Level BOM can contribute to your financial success:
1. Centralized Product Information: A Multi-Level BOM serves as a centralized repository of information about the product's structure, components, materials, and assembly processes. This information is crucial throughout the product's lifecycle for decision-making and coordination.
2. Design and Development: During the design and development phase, PLM based on the Multi-Level BOM ensures that all stakeholders have access to accurate and up-to-date information. This enables effective collaboration, reduces errors, and speeds up the design process.
3. Change Management: As products evolve and undergo modifications, a Multi-Level BOM within a PLM framework facilitates efficient change management. You can track and manage engineering changes, ensuring that updates are implemented seamlessly.
4. Version Control: PLM with a Multi-Level BOM enables version control, ensuring that the correct and current BOM version is used for production planning, manufacturing, and other activities. This prevents confusion and mistakes.
5. Regulatory Compliance: Throughout the product life cycle, compliance with industry regulations and standards is essential. A Multi-Level BOM within a PLM system helps manage compliance documentation and ensures that products adhere to applicable requirements.
6. Supplier Collaboration: PLM with a Multi-Level BOM fosters collaboration with suppliers. You can share accurate BOM information with suppliers, facilitating communication and ensuring that the right components are sourced.
7. Manufacturing and Production: During manufacturing, PLM ensures that the correct BOM is used for production planning, minimizing errors, rework, and disruptions. This leads to higher operational efficiency and reduced costs.
8. Quality Control and Testing: PLM helps manage quality control processes by providing detailed information about the product's structure and components. This facilitates testing, inspections, and quality assurance throughout the lifecycle.
9. Performance Tracking: PLM allows you to track the performance of products in the field. By monitoring data related to component failures, usage patterns, and maintenance, you can identify areas for improvement and design enhancements.
10. End-of-Life Management: As products reach the end of their lifecycle, PLM ensures proper documentation and coordination for retirement, disposal, or replacement. This helps manage costs associated with end-of-life processes.
11. Data-Driven Decisions: PLM with a Multi-Level BOM provides factual data and insights at every stage of the product life cycle. This supports data-driven decisions that lead to improved efficiency, quality, and profitability.
12. Continuous Improvement: PLM encourages a culture of continuous improvement. By analyzing data from different stages of the product life cycle, you can identify trends, patterns, and opportunities for enhancement.
In summary, Product Lifecycle Management through a Multi-Level BOM enhances the management of product information, processes, and collaboration across the entire lifecycle. It contributes to better decision-making, higher product quality, reduced costs, and improved financial performance.
Lean Manufacturing and Continuous Improvement
Lean manufacturing is a systematic approach to production that focuses on minimizing waste, optimizing efficiency, and continuously improving processes to enhance value for customers.
In the context of a Multi-Level Bill of Materials (BOM), lean manufacturing and continuous improvement refer to using the BOM as a tool to identify areas for process optimization, waste reduction, and ongoing enhancement.
Here's a more detailed explanation of how lean manufacturing and continuous improvement through a Multi-Level BOM can contribute to your financial success:
1. Waste Identification: A Multi-Level BOM provides a detailed breakdown of components and subcomponents, enabling you to identify waste in terms of excess inventory, overproduction, unnecessary transportation, and other inefficiencies.
2. Value Stream Mapping: By analyzing the flow of materials and information depicted in the Multi-Level BOM, you can create value stream maps that visualize the production process. This helps identify bottlenecks and areas for improvement.
3. Kaizen and Small Improvements: The Multi-Level BOM serves as a reference for incremental improvements. Kaizen principles can be applied to continuously make small, incremental changes to processes, resulting in cumulative improvements over time.
4. Standardized Work: Lean manufacturing emphasizes standardized work processes. The Multi-Level BOM provides a standardized reference for assembling products, ensuring consistency and reducing errors.
5. Pull-Based Production: Using the Multi-Level BOM, you can implement pull-based production systems, where materials and components are replenished only when needed. This reduces overproduction and excess inventory.
6. Visual Management: The Multi-Level BOM can be visualized in various formats, such as kanban boards or digital dashboards, to provide real-time insights into production status and identify areas for improvement.
7. Error Reduction: Detailed information in the Multi-Level BOM helps identify potential sources of errors. By addressing these issues, you can reduce defects, rework, and associated costs.
8. Cross-Functional Collaboration: Lean manufacturing encourages collaboration between different departments. The Multi-Level BOM serves as a common reference point that facilitates communication and alignment across functions.
9. Continuous Training: Lean manufacturing requires a culture of continuous learning. The Multi-Level BOM provides a visual tool for training employees on assembly processes and promoting consistent practices.
10. Waste Elimination: Through analysis of the Multi-Level BOM, you can systematically identify and eliminate different types of waste, including transportation, waiting, overprocessing, defects, and underutilized talent.
11. Resource Optimization: Lean principles aim to optimize the use of resources. By aligning resource allocation with the Multi-Level BOM, you can ensure that materials, labor, and equipment are used efficiently.
12. Cost Reduction: Lean manufacturing focuses on reducing costs by eliminating inefficiencies. The Multi-Level BOM helps identify cost-saving opportunities and supports evidence-based decision-making.
In summary, lean manufacturing and continuous improvement practices, supported by a Multi-Level BOM, promote waste reduction, process optimization, and a culture of ongoing enhancement.
By analyzing the BOM data, you can implement changes that lead to higher operational efficiency, improved product quality, reduced costs, and ultimately, enhanced financial performance.
How Does a Multi-Level BOM Impact Quality Control?
A Multi-Level Bill of Materials (BOM) plays a significant role in enhancing quality control throughout the product lifecycle which will in turn improve your bottom line.
Here's how a Multi-Level BOM impacts quality control:
1. Component Traceability: A Multi-Level BOM provides a detailed breakdown of components and their relationships within the product. This traceability allows for accurate tracking of the origin and history of each component, aiding in quality control audits and recalls.
2. Defect Identification: By mapping out the product's structure, a Multi-Level BOM helps in pinpointing the location of defects or quality issues. This allows for targeted inspections and corrective actions.
3. Root Cause Analysis: In the event of defects or quality deviations, a Multi-Level BOM assists in conducting root cause analysis. It helps identify which specific components or assembly steps might be contributing to the issue.
4. Consistency and Standardization: The Multi-Level BOM serves as a reference for standardized assembly processes. Consistency in assembly procedures leads to consistent product quality and reduces the likelihood of defects.
5. Testing and Inspection Planning: Quality control teams can refer to the Multi-Level BOM to plan testing and inspection procedures at different assembly levels. This ensures that critical components and sub-components are thoroughly examined.
6. Validation of Changes: When design changes or engineering updates are proposed, the Multi-Level BOM is used to validate the impact of these changes on product quality. This ensures that modifications do not compromise the product's integrity.
7. Supplier Quality Management: A Multi-Level BOM provides transparency into component specifications. This aids in evaluating supplier quality by comparing received components to the expected standards outlined in the BOM.
8. Documentation and Compliance: Detailed information in the Multi-Level BOM assists in maintaining compliance with industry regulations and quality standards. It ensures that product components meet the required specifications.
9. Error Prevention: Accurate BOM data helps prevent errors during assembly. Workers can cross-reference the BOM to ensure that correct components are used and assembly steps are followed accurately.
10. Continuous Improvement: Insights from the Multi-Level BOM can guide continuous improvement initiatives. By identifying areas prone to defects, quality control efforts can be focused on those specific components or processes.
In summary, a Multi-Level BOM contributes to quality control by providing visibility into the product's composition, facilitating defect identification, supporting root cause analysis, and ensuring consistency in assembly processes. This enhanced quality control directly translates to improved product quality, reduced defects, and greater customer satisfaction.
How Does a Multi-Level BOM Contribute to Data-Driven Decisions?
A Multi-Level Bill of Materials (BOM) serves as a valuable source of data that enables data-driven decision-making across various aspects of product development, manufacturing, and operations.
Here's how a Multi-Level BOM contributes to data-driven decisions such that it also improves your bottom line:
1. Accurate and Comprehensive Information: A Multi-Level BOM provides a detailed breakdown of a product's components and their relationships. This accurate and comprehensive information forms the foundation for data-driven decisions.
2. Demand Forecasting: By analyzing historical data and trends within the Multi-Level BOM, businesses can make informed decisions about production levels, inventory management, and resource allocation based on projected demand.
3. Cost Estimation and Analysis: The Multi-Level BOM breaks down costs associated with materials, labor, and overhead. This enables businesses to perform cost analyses, assess profitability, and make pricing decisions based on accurate data.
4. Supplier Management: Data from the Multi-Level BOM supports data-driven supplier management decisions. This includes selecting suppliers, negotiating terms, and evaluating supplier performance based on component specifications and quality.
5. Production Planning and Scheduling: Data-driven decisions about production quantities, lead times, and scheduling are informed by the Multi-Level BOM. This ensures optimal resource allocation, reduced downtime, and efficient operations.
6. Inventory Management: Accurate demand forecasting based on the Multi-Level BOM helps optimize inventory levels, preventing excess stock and stockouts. Data-driven decisions about reorder points and safety stock are made using BOM data.
7. Lean Manufacturing Initiatives: The Multi-Level BOM identifies waste and inefficiencies within the production process. Data-driven decisions about implementing lean practices, such as reducing setup times or optimizing workflow, stem from insights provided by the BOM.
8. Engineering Changes and Modifications: When considering design modifications, the Multi-Level BOM provides data to assess the impact on production, costs, and quality. Data-driven decisions guide the implementation of engineering changes.
9. Quality Control and Defect Analysis: Data-driven quality control decisions are informed by the Multi-Level BOM, which helps identify areas prone to defects and guides testing and inspection procedures.
10. Continuous Improvement: The Multi-Level BOM provides a baseline for measuring performance and tracking improvements over time. Data-driven decisions about process enhancements and incremental changes are supported by BOM insights.
11. Compliance and Regulatory Requirements: Data-driven decisions about meeting regulatory standards are facilitated by the Multi-Level BOM, which ensures that products are designed, produced, and documented in accordance with regulations.
12. Resource Optimization: Data from the Multi-Level BOM aids in optimizing resource allocation, such as labor and equipment, based on actual production requirements and assembly processes.
In essence, a Multi-Level BOM transforms raw data into actionable insights, enabling businesses to make informed, strategic, and data-driven decisions across the entire product lifecycle. This approach enhances efficiency, reduces costs, improves product quality, and ultimately contributes to a healthier bottom line.
How Can Businesses Adopt a Multi-Level BOM Effectively?
Adopting a Multi-Level Bill of Materials (BOM) effectively involves a strategic approach that integrates the BOM into various aspects of product development, manufacturing, and operations.
Here's how businesses can successfully implement a Multi-Level BOM:
1. Select the Right Software or System: Choose a suitable software solution or enterprise resource planning (ERP) system that supports Multi-Level BOM functionality. Ensure that the chosen system aligns with your business needs and integrates well with existing processes.
2. Standardize BOM Structure: Establish a standardized format and structure for creating Multi-Level BOMs. Consistency in the way BOMs are structured ensures clear communication and easy interpretation across different departments.
3. Create Detailed BOMs: Develop comprehensive Multi-Level BOMs that provide detailed information about each component, including part numbers, descriptions, quantities, suppliers, and cost breakdowns.
4. Train Employees: Provide training to employees involved in creating, using, and interpreting Multi-Level BOMs. Ensure that teams understand the importance of accurate data entry and its impact on various operational processes.
5. Integrate BOM into Workflows: Integrate Multi-Level BOMs into various workflows, such as design, procurement, production planning, and quality control. Ensure that BOMs are consistently referenced and updated at each stage.
6. Collaborate Cross-Functionally: Encourage cross-functional collaboration between departments such as engineering, procurement, manufacturing, and quality control. Effective communication ensures that accurate BOM data is shared and utilized.
7. Implement Change Management: Establish a change management process for updating Multi-Level BOMs when design changes or modifications occur. Clearly define roles and responsibilities for approving and implementing changes.
8. Align with Lean Principles: Incorporate Multi-Level BOMs into lean manufacturing initiatives, using the data to identify waste, optimize processes, and support continuous improvement efforts.
9. Enable Real-Time Updates: Utilize technology to enable real-time updates to Multi-Level BOMs. Cloud-based solutions or ERP systems allow for seamless collaboration and immediate access to accurate BOM data.
10. Monitor and Audit BOM Data: Regularly monitor and audit Multi-Level BOM data to ensure accuracy and consistency. Conduct periodic reviews to identify and correct discrepancies or outdated information.
11. Ensure Data Security: Implement data security measures to protect sensitive BOM information from unauthorized access or tampering. Maintain data integrity and confidentiality.
12. Provide Documentation and Training Materials: Create user manuals, documentation, and training materials that outline the process of creating, maintaining, and utilizing Multi-Level BOMs. These resources help onboard new employees and reinforce best practices.
13. Continuous Improvement: Continuously evaluate the effectiveness of Multi-Level BOM adoption and seek opportunities for improvement. Gather feedback from teams to identify any challenges and implement refinements.
14. Vendor Support and Training: If utilizing specialized software, work closely with the vendor to receive training, support, and assistance in optimizing the use of Multi-Level BOM features.
15. Executive Sponsorship: Obtain executive sponsorship and support for Multi-Level BOM adoption. Clear leadership endorsement enhances the importance of accurate BOM management throughout the organization.
By implementing these strategies, businesses can effectively adopt a Multi-Level BOM, enhancing operational efficiency, and data-driven decision-making, and ultimately contributing to improved bottom-line performance.
How Can Deskera Help You with a Multi-Level Bill of Materials?
Deskera MRP is an integrated software solution designed to help businesses manage their manufacturing processes, including multi-level bills of materials.
Here’s how Deskera can assist you with the multi-level bill of materials:
- Multi-Level BOM Creation and Management: Manage product structures with ease using the multi-level bill of materials. Assign multiple components to a single product. Identify components and subcomponents of each product, and easily track their usage, movement, and costs.
- Improve Productivity: Deskera will help you improve productivity because it facilitates the automatic generation of bills of materials, thereby helping to reach your production goals faster. It also automates the process of managing and maintaining multi-level bills of materials.
- Enhances Collaboration: By increasing the visibility and communication between the departments of your company, Deskera will help improve collaboration between different teams. In fact, it also allows multiple users to access and edit the bill of materials. All of this will also facilitate faster and more informed decision-making.
- Improve Inventory Costs: With Deskera, you will be able to improve your inventory costs as the accuracy of data with a single source of truth for the entire bill of materials is ensured. Through Deskera, all the required documents can be automatically generated from this single source of information. Lastly, through the automatic generation of a bill of materials, manual errors will be reduced.
- Reduce Production Costs: By streamlining the process of the bill of materials through Deskera, operation costs will be reduced. In fact, the time and resources spent on managing and updating complex bills of materials will also be reduced.
Key Takeaways
A Multi-Level BOM is a detailed hierarchical representation of a product's components and sub-components, illustrating how they come together to create the final product.
The 10 ways in which a multi-level bill of materials can improve your bottom line are:
- Cost Transparency: A Multi-Level BOM provides detailed insights into the components and sub-components required to manufacture a product. This transparency helps identify cost drivers, allowing you to focus on cost-saving strategies and optimize your procurement processes.
- Effective Resource Allocation: By understanding the full scope of materials and resources needed at each assembly level, you can allocate resources more efficiently and minimize waste. This prevents over-purchasing or under-utilization of materials.
- Accurate Cost Estimation: With a Multi-Level BOM, you can accurately estimate the costs associated with producing each product variant or assembly configuration. This enables you to set competitive prices while maintaining profitability.
- Optimized Production Planning: Multi-Level BOMs facilitate better production scheduling and capacity planning. You can ensure that resources are allocated to meet demand and avoid bottlenecks, reducing production lead times and costs.
- Inventory Management: Improved visibility into component requirements allows for better inventory control. You can maintain optimal stock levels, reduce excess inventory, and avoid stockouts, all of which can positively impact costs.
- Supplier Negotiations: Armed with detailed BOMs, you can negotiate better terms with suppliers based on accurate demand forecasts. This may lead to volume discounts, better pricing, and more favorable supplier relationships.
- Root Cause Analysis: In the event of defects or quality issues, a Multi-Level BOM helps trace problems back to specific components or assembly levels. This enables you to quickly identify and address root causes, minimizing production delays and associated costs.
- Efficient Engineering Changes: Multi-Level BOMs streamline the process of implementing engineering changes. You can quickly assess the impact of design modifications on different assembly levels, reducing the risk of errors and costly rework.
- Product Lifecycle Management: By maintaining accurate and up-to-date BOMs throughout a product's lifecycle, you can extend product lifespans, introduce updates or enhancements, and make informed decisions about discontinuing or phasing out products.
- Lean Manufacturing and Continuous Improvement: Multi-Level BOMs support lean principles and continuous improvement initiatives. You can identify areas for process optimization, waste reduction, and value-added activities, leading to higher operational efficiency and lower costs.
Incorporating a Multi-Level BOM into your business processes can yield substantial benefits in terms of cost control, operational efficiency, and overall profitability. It provides a comprehensive view of your product's structure and enables you to make informed decisions that positively impact your bottom line.
Overall, Deskera MRP will serve as a comprehensive solution for managing multi-level bills of materials. It will help streamline your bill of materials, automate production processes, track production costs, monitor supplier performance, improve supply chain management, streamline production planning, reduce inventory errors, optimize production scheduling, track production costs, and help you maximize efficiency with the multi-level bill of materials.
Related Articles
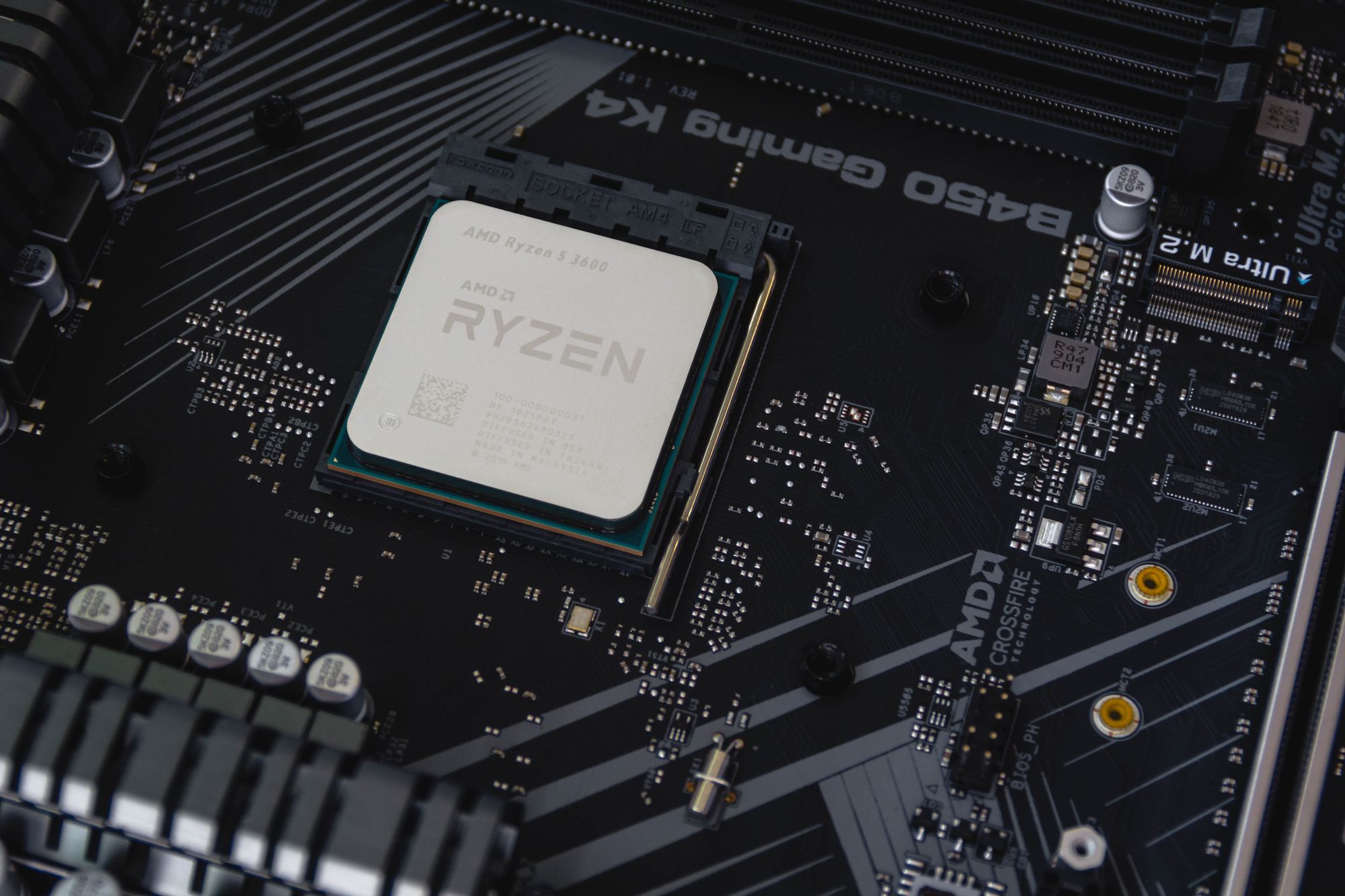
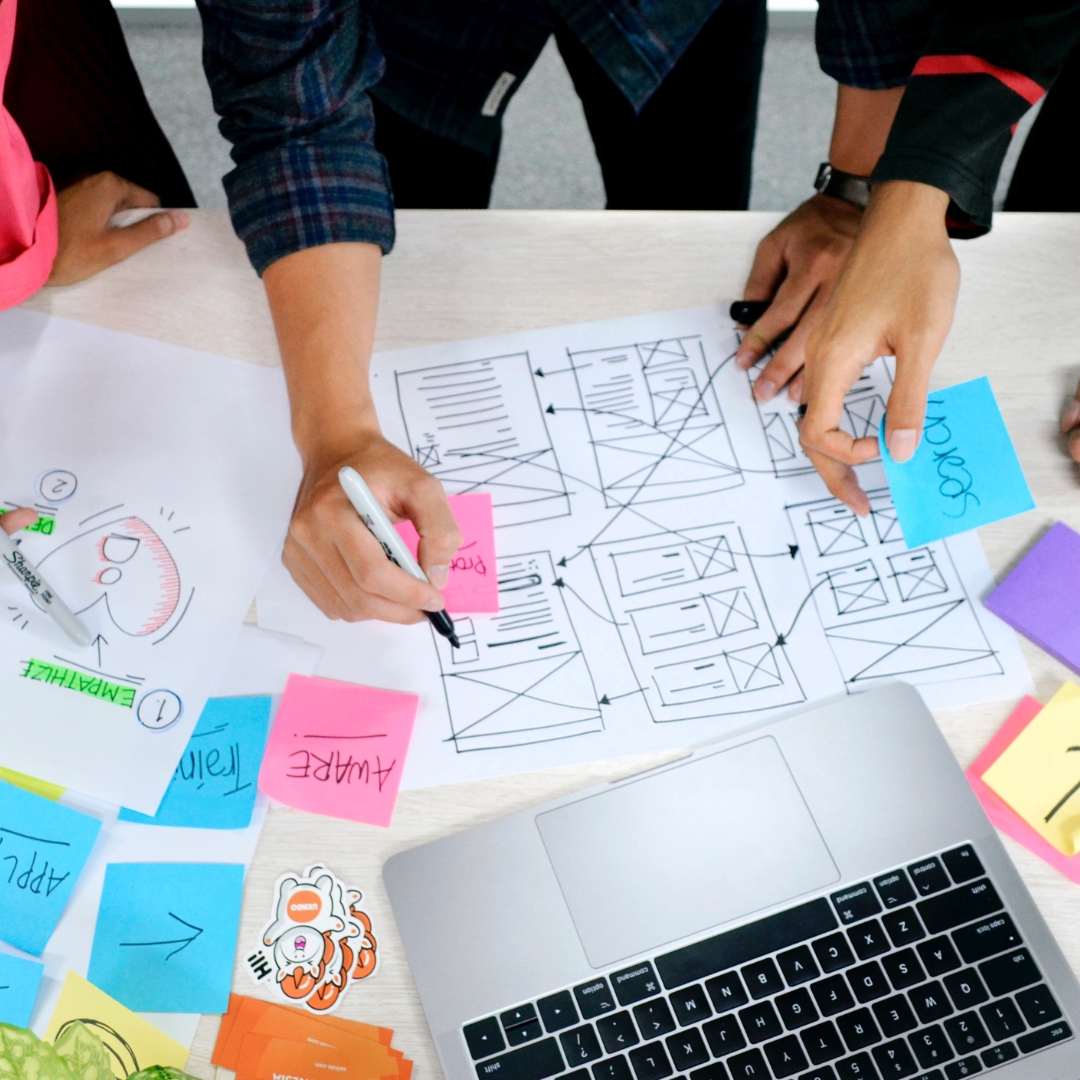
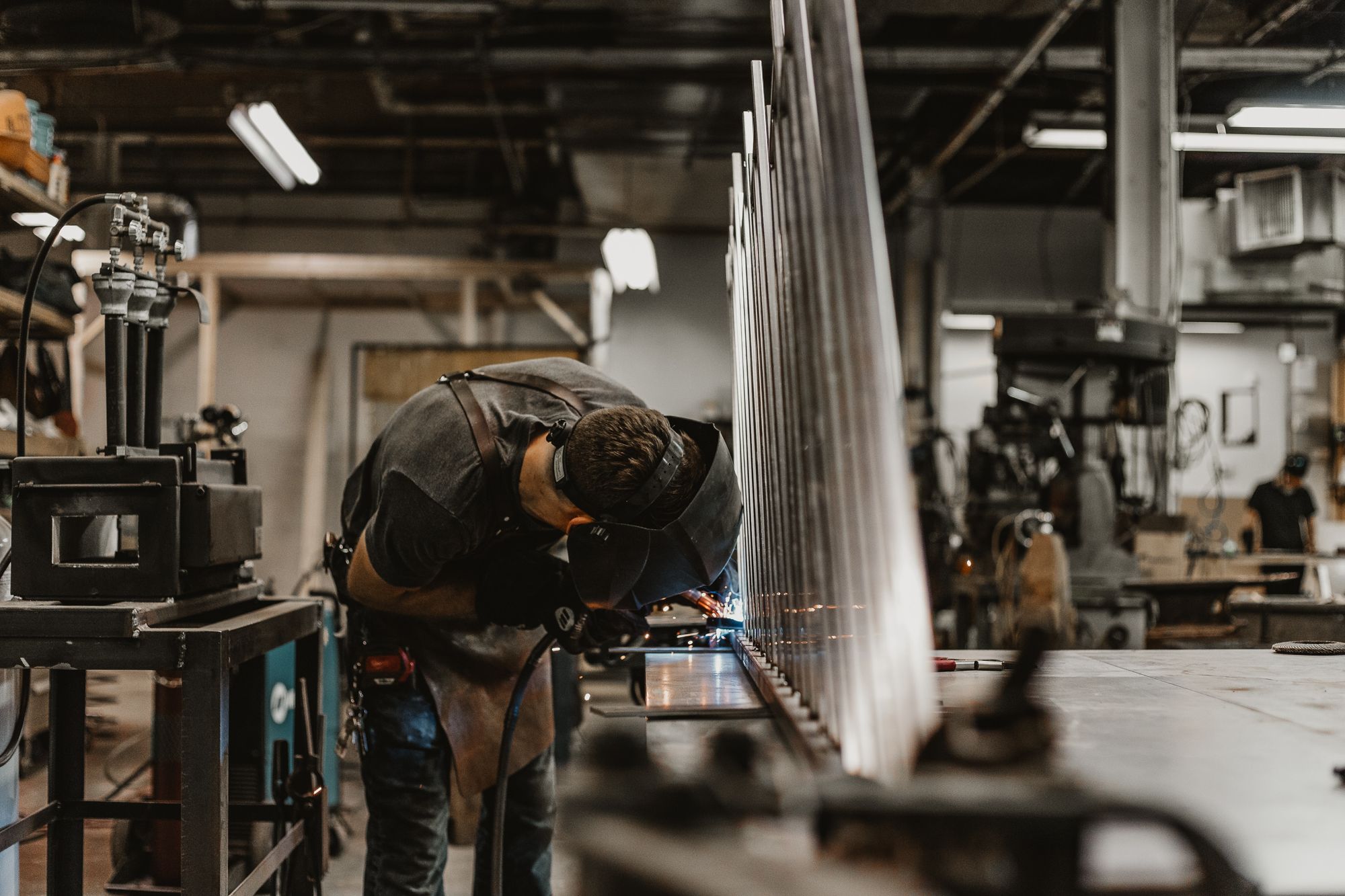
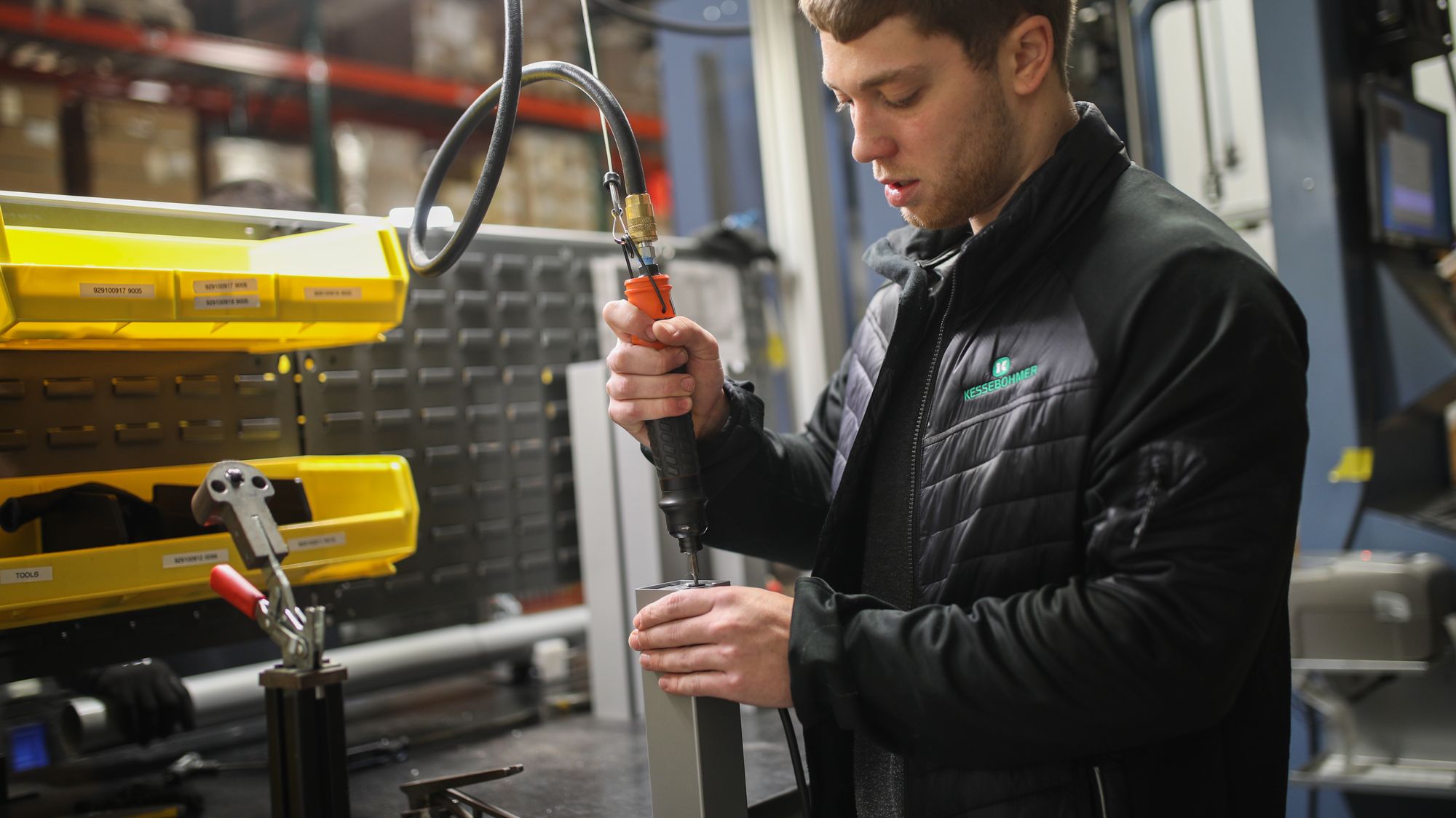
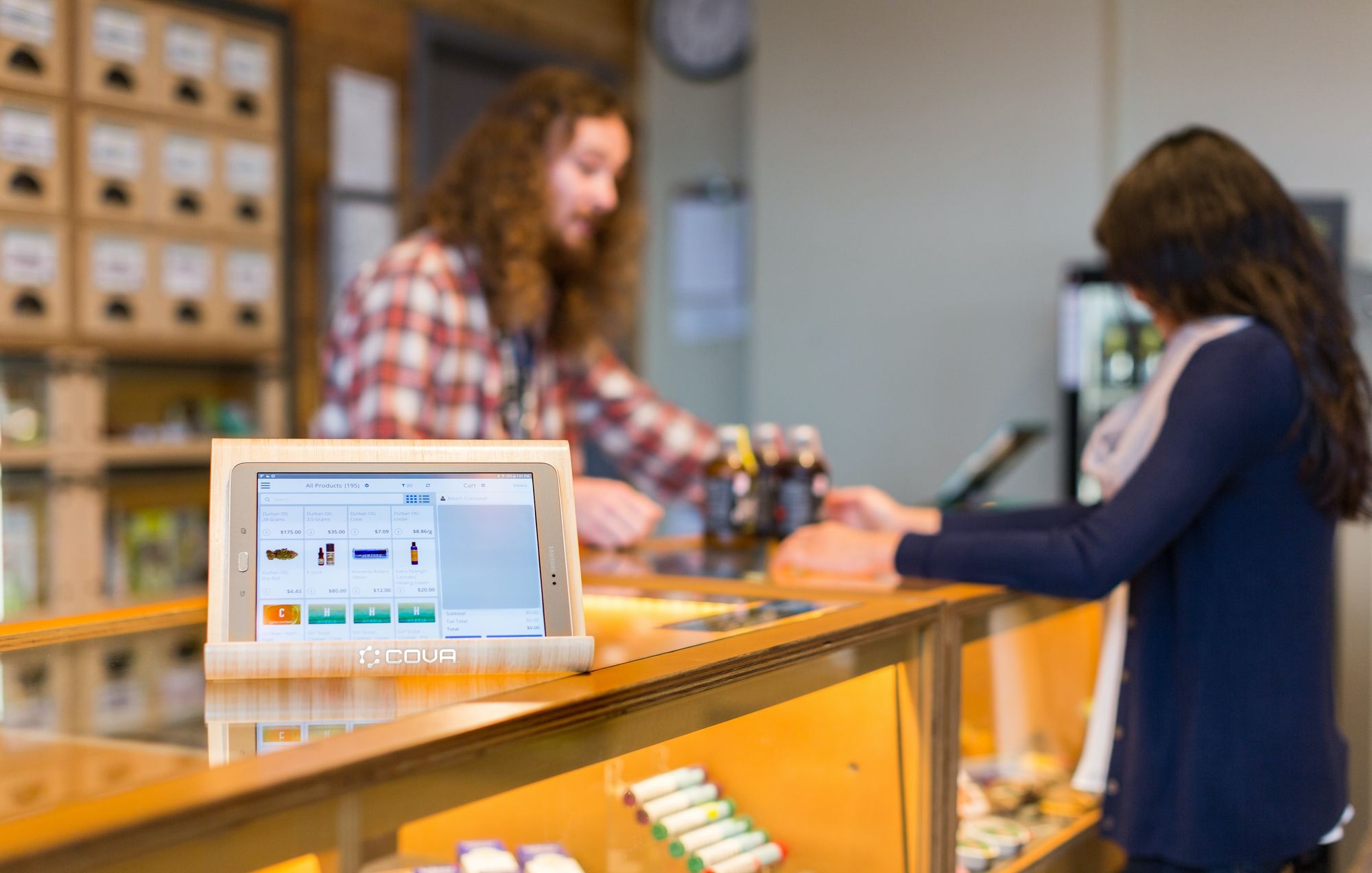