Have you ever considered the vital part work orders play in facilitating effective manufacturing procedures? Work orders are most likely a crucial part of production planning and management if you operate in the manufacturing sector.
But what precisely are work orders, and how do they help to the smooth running of processes and the general success of industrial endeavors?
Work orders, in the context of manufacturing, are comprehensive and detailed instructions that guide production teams through the step-by-step execution of manufacturing tasks. They serve as formal authorization to begin production on a specific job, outlining all the necessary information to complete the task successfully.
Work orders contain critical details, such as the product specifications, quantities to be produced, the required raw materials, the sequence of operations, and the designated work centers.
They provide a roadmap for each stage of the production process, enabling efficient utilization of resources and ensuring that products are manufactured by quality standards and customer requirements.
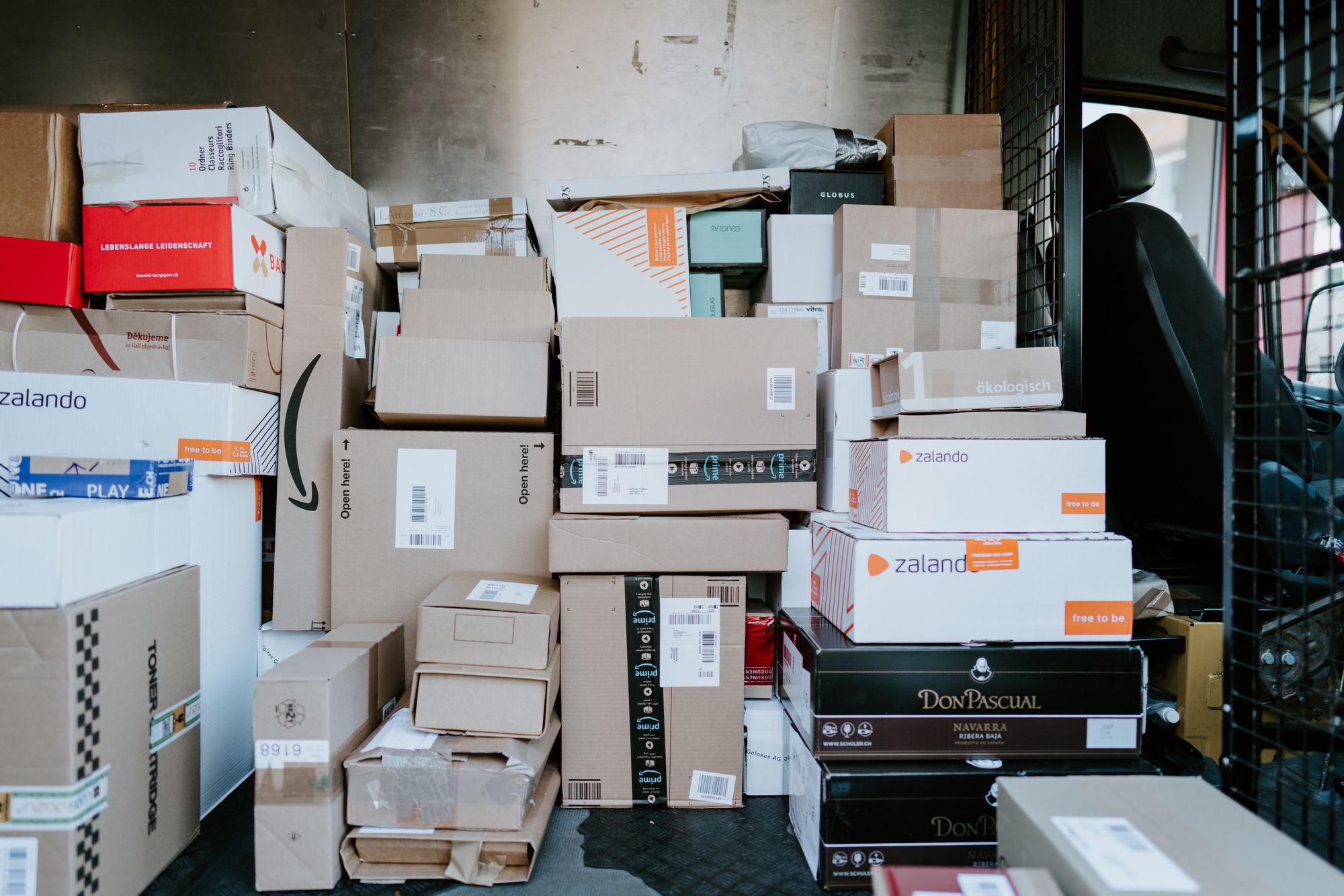
A Deloitte study found that businesses with effective work order administration may cut production lead times by up to 30%, increase worker productivity by 20%, and reduce material waste by 15%. These numbers demonstrate the considerable influence work orders have on production effectiveness and overall company performance.
Whether you are a production manager, a shop floor supervisor, or an aspiring manufacturing professional, this article will equip you with the knowledge and strategies needed to leverage work orders as a powerful tool for success in the dynamic and competitive manufacturing landscape.
So, let's unravel the significance of work orders in efficient manufacturing and unlock the potential of streamlined production processes and enhanced business outcomes.
Here's what we shall cover in this post:
- Introduction to Work Orders in Manufacturing
- Components of Work Orders
- Work Orders vs. Job Orders: Key Distinctions
- Importance of Work Orders in Production Planning
- Work Orders and Resource Allocation
- Work Orders and Cost Control in Production
- Future Trends in Work Order Management
- How Can Deskera Help You?
- Conclusion
- Key Takeaways
Introduction to Work Orders in Manufacturing
Work orders are a fundamental aspect of the manufacturing process, serving as essential documents that detail the necessary steps and instructions for the production of goods. They play a pivotal role in coordinating and guiding the entire manufacturing workflow, ensuring that tasks are executed efficiently and by established standards.
- A work order is a formal document that communicates instructions, specifications, and details to the production team regarding the manufacturing or assembly of a particular product.
- It serves as a crucial tool for managing and tracking the progress of work on the shop floor.
- Work orders encompass a range of information, such as the materials required, workstations involved, labor hours estimated, and any special instructions or quality standards that must be adhered to during the manufacturing process.
- Work orders may also include details about the production line or workstation where the item is to be manufactured, as well as any special tools or equipment needed for the process.
Types of Work Orders
Work orders are an essential part of the manufacturing process, providing detailed instructions and information for workers to execute production tasks effectively and efficiently. Different types of work orders are used in various manufacturing scenarios, each serving a specific purpose and function.
Here, we will explore the various types of work orders commonly used in manufacturing and their significance in streamlining production operations.
Standard Work Orders:
Standard work orders are the most common type used in manufacturing. They are employed for routine or repetitive production processes where the same product is manufactured regularly. Standard work orders provide a detailed step-by-step guide for workers to follow, ensuring consistency in the manufacturing process.
These work orders include information such as the product name or description, quantity to be produced, required materials, and the specific tasks and operations to be performed. Standard work orders are particularly valuable in industries with high-volume production, such as automotive manufacturing and electronics assembly.
Benefits of Standard Work Orders:
- Consistency: SWOs ensure that tasks are performed consistently and uniformly, reducing variations and errors.
- Quality: Clear instructions and quality standards help maintain product and process quality, reducing defects and rework.
- Efficiency: SWOs streamline operations by providing a standardized approach to tasks, which saves time and resources.
- Training: SWOs are valuable training tools for new employees, helping them learn tasks quickly and accurately.
Job Work Orders:
Job work orders are used for custom or one-off production jobs. Unlike standard work orders, job work orders are created for unique products tailored to a customer's specific requirements. Each job work order is customized based on the customer's order and may vary significantly from one job to another.
These work orders provide detailed instructions for producing the customized product, including any special design or specification changes. Job work orders are prevalent in industries like aerospace, shipbuilding, and custom-made machinery.
Benefits of Job Work Orders:
- Clarity: Job Work Orders provide a clear and detailed outline of the job's scope, requirements, and objectives, reducing ambiguity.
- Accountability: Assigning responsibilities and deadlines in the work order ensures that individuals or teams are accountable for completing their tasks.
- Resource Management: Job Work Orders help allocate resources efficiently, preventing overallocation or shortages.
- Communication: Work orders facilitate effective communication between stakeholders involved in the job, ensuring everyone is on the same page.
- Budget Control: Budget estimates in the work order help manage costs and prevent overspending.
Maintenance Work Orders:
Maintenance work orders are used to schedule and manage maintenance and repair tasks for machinery and equipment used in the production process. These work orders are essential to ensure that machines are kept in good working condition and to prevent costly breakdowns and production downtime.
Maintenance work orders include information such as the type of maintenance required, the specific equipment or machine involved, and any replacement parts or materials needed for the maintenance task. By following maintenance work orders, manufacturers can extend the lifespan of their equipment and reduce overall maintenance costs.
Benefits of Maintenance Work Orders:
- Organized Maintenance Management: Maintenance work orders provide a structured approach to managing maintenance tasks, ensuring that they are documented, tracked, and prioritized.
- Efficient Resource Allocation: Work orders help allocate the right personnel, tools, and materials to each maintenance task, optimizing resource utilization.
- Minimized Downtime: Timely maintenance through work orders reduces equipment downtime and prevents potential disruptions to operations.
- Preventive Maintenance: Work orders facilitate the scheduling and tracking of preventive maintenance activities, prolonging the lifespan of assets.
- Documentation and Compliance: Maintenance work orders serve as documentation of maintenance activities, which can be valuable for regulatory compliance and audits.
Rush Work Orders:
Rush work orders are issued when there is an urgent need to expedite production to meet tight deadlines or address unexpected demand spikes. These work orders prioritize certain tasks over others to ensure the timely delivery of products to customers.
Rush work orders may require additional resources or overtime work to meet the accelerated production schedule. They are commonly used in industries with time-sensitive products or those facing rapidly changing market demands, such as the fashion industry and seasonal products.
Key Characteristics of Rush Work Orders:
- Urgent Priority: Rush Work Orders are assigned the highest priority level to ensure immediate attention and quick resolution.
- Short Timeframe: RWOs typically have tight deadlines that require the task to be completed within a much shorter timeframe than regular work orders.
- Critical Situations: Rush Work Orders are used for critical situations, such as equipment breakdowns, safety hazards, customer emergencies, or unexpected disruptions.
- Approval Process: Due to their urgent nature, RWOs may involve a streamlined or expedited approval process to ensure rapid authorization for the work to proceed.
Benefits and Considerations of Rush Work Orders:
- Emergency Response: Rush Work Orders enable swift response to critical situations, minimizing downtime and mitigating potential risks.
- Customer Satisfaction: Rapid completion of urgent tasks contributes to enhanced customer satisfaction and trust.
- Priority Management: RWOs help teams manage and prioritize tasks during busy or crisis periods.
- Resource Allocation: Properly allocating resources ensures that urgent tasks are handled efficiently without causing bottlenecks in regular workflows.
- Efficiency vs. Quality: While speed is essential, maintaining quality workmanship remains a priority in rush situations.
Engineering Change Work Orders:
Engineering change work orders are used to implement design changes or improvements to existing products. When design modifications are required due to customer feedback, quality issues, or technological advancements, engineering change work orders are issued to update the manufacturing process.
These work orders detail the specific changes to be made, the reasons for the modifications, and the updated requirements for production. Engineering change work orders are crucial for ensuring that the latest design specifications are incorporated into the manufacturing process, leading to improved product quality and customer satisfaction.
Key Elements of an Engineering Change Work Order:
- Work Order Number: A unique identifier assigned to the engineering change work order for tracking and reference purposes.
- Change Description: A detailed description of the proposed change, including the reasons for the change, its scope, and the expected impact.
- Affected Components/Systems: Identification of the specific components, parts, systems, or processes that will be affected by the proposed change.
- Engineering Rationale: An explanation of the engineering rationale behind the change, including any calculations, analysis, or research conducted to support the decision.
- Design Documentation: Attachments or references to relevant design documents, drawings, specifications, and technical data that illustrate the proposed change.
- Change Approval: Details about the individuals or departments responsible for approving the change, along with any required signatures or authorization.
- Implementation Plan: A step-by-step plan outlining how the change will be implemented, including tasks, responsibilities, timelines, and milestones.
Benefits of Engineering Change Work Orders:
- Change Management: ECWOs provide a structured process for managing changes, ensuring that they are properly evaluated, documented, and executed.
- Quality Assurance: Proper testing and validation procedures ensure that changes do not compromise product quality, safety, or performance.
- Regulatory Compliance: ECWOs help ensure compliance with industry standards, regulations, and quality management systems.
- Traceability: Changes are traceable through documentation, making it possible to track the history of design modifications.
Service Work Orders:
Service work orders are used in industries where after-sales service and support are essential, such as equipment manufacturing or technology companies. These work orders are generated when customers require service or repairs for their purchased products.
Service work orders include information on the type of service required, the location of the product, and the specific parts or materials needed for the repair. They help ensure that customer service requests are handled efficiently and that the necessary resources are allocated for timely service delivery.
Benefits of Service Work Orders:
- Structured Process: SWOs provide a structured process for managing service tasks, ensuring that they are documented, prioritized, and completed efficiently.
- Customer Satisfaction: Delivering services based on well-defined work orders contributes to enhanced customer satisfaction and trust.
Batch Work Orders:
Batch work orders are used when producing multiple units of a product in a single production run. Instead of producing one unit at a time, batch work orders allow manufacturers to streamline production by manufacturing a set quantity of products together.
This approach can lead to improved efficiency and reduced setup time between each production run. Batch work orders typically include information about the batch size, production schedule, and any specific requirements for producing the batch.
Benefits of Batch Work Orders:
- Efficient Production: Batch Work Orders allow for the streamlined production of larger quantities of products with consistent quality.
- Quality Assurance: Detailed instructions and quality control procedures help ensure that each batch meets specified standards.
- Traceability: Batch work orders enable the tracking of production activities and materials used in each specific batch.
- Consistency: By following standardized procedures, batch work orders contribute to consistent product quality and specifications.
Subcontract Work Orders:
Subcontract work orders are used when certain tasks or components of the production process are outsourced to external suppliers or subcontractors. These work orders detail the specific tasks or components to be outsourced, the quantity required, and any quality standards or specifications to be met by the subcontractor.
Subcontract work orders help manufacturers manage their supply chain effectively and ensure that outsourced tasks are completed to the required standards and timeline.
Benefits of Subcontract Work Orders:
- Expertise Access: Subcontracting allows organizations to access specialized skills, expertise, and resources that they may not have in-house.
- Cost Efficiency: Subcontracting can be cost-effective, as organizations only pay for the specific services or tasks required.
- Risk Mitigation: Subcontractors may assume certain risks and responsibilities, reducing the potential impact on the contracting organization.
- Focus on Core Competencies: Subcontracting non-core tasks allows organizations to focus on their core competencies and strategic objectives.
- Global Reach: Subcontractors may provide access to a global network of suppliers, partners, or experts.
Components of Work Orders
Work orders are essential documents used in manufacturing to guide and manage production processes. They provide detailed instructions and information to workers, enabling them to carry out tasks efficiently and effectively.
Each work order is unique to the specific production job and contains various components that contribute to its effectiveness.
Work Order Number:
The work order number is a unique identifier assigned to each work order. It serves as a reference for tracking and managing the work order throughout its lifecycle.
The work order number is used to link the work order to other related documents, such as purchase orders, production schedules, and inventory records. Having a standardized numbering system for work orders helps maintain organization and facilitates easy retrieval of information when needed.
Key Points About Work Order Numbers:
- Uniqueness: Each work order is assigned a distinct work order number that is not duplicated within the organization's records or systems.
- Tracking: Work order numbers facilitate easy tracking and retrieval of specific work orders, allowing users to quickly locate relevant information.
- Reference: Work order numbers provide a convenient way to refer to a specific work order when communicating with team members, supervisors, or other stakeholders.
- Organization: Work order numbers contribute to the organization and categorization of work orders, making it easier to manage and prioritize tasks.
Product Information:
One of the primary components of a work order is the product information. This includes details about the product being manufactured, such as the product name, description, and specifications. It may also include information about the product's model number, version, or serial number, especially in industries where products have different variations or configurations.
Quantity:
The quantity component specifies the number of units of the product to be produced in the work order. It is essential to ensure that the correct quantity is produced to meet customer demands and maintain inventory levels.
The quantity component may also be used to determine the required amount of raw materials and components needed for production.
Bill of Materials (BOM):
The bill of materials is a critical component of a work order, especially for complex products with multiple components and sub-assemblies. The BOM provides a detailed list of all the materials, parts, and components required to assemble the final product.
It includes information such as part numbers, descriptions, quantities, and sometimes unit costs. Having an accurate BOM ensures that all the necessary materials are available and that the product is assembled correctly.
Routing Information:
Routing information outlines the sequence of steps and operations required to manufacture the product. It specifies the order in which tasks should be performed, the work centers or machines involved, and the estimated time for each operation. Routing information helps in optimizing production processes, reducing lead times, and improving overall efficiency.
Work Instructions:
Work instructions provide detailed step-by-step guidance on how to perform each task within the work order. These instructions may include specific techniques, measurements, or quality standards to ensure consistent and high-quality output. Work instructions are particularly important for complex products or processes that require precise execution.
Labor and Resource Allocation:
Work orders often include information about labor and resource allocation. This component specifies the number of workers required, the skill sets needed, and the amount of time allocated to each task. It may also include information about equipment or machinery required for specific operations.
Start and Due Dates:
The start and due dates indicate when the work order should begin and when it is expected to be completed. These dates are crucial for managing production schedules, coordinating resources, and meeting customer delivery deadlines. Manufacturers must ensure that work orders are scheduled and executed efficiently to avoid production delays.
Priority:
The priority component indicates the urgency or importance of the work order relative to other orders. It helps manufacturing managers and planners determine which work orders should be given priority in the production schedule. High-priority work orders may involve rush jobs or urgent customer demands.
Quality Control Requirements:
Quality control requirements outline the specific quality standards and checks that must be adhered to during production. This component ensures that products meet the required quality levels and that any defects or deviations are identified and addressed promptly.
Material Availability:
The material availability component specifies whether all the required materials and components are available for the work order. It helps prevent production delays and ensures that inventory levels are appropriately managed. If any materials are unavailable, the necessary steps can be taken to procure or reorder them.
Cost Estimation:
Work orders may also include a cost estimation component, which provides an estimate of the total production cost. This information helps in budgeting and cost control and allows manufacturers to assess the profitability of the production job.
Notes and Comments:
Notes and comments sections in work orders provide space for additional information, special instructions, or comments from production supervisors or workers. These notes can be used to communicate important details that may not fit into other components of the work order.
Work Order Management
Work order management is a critical aspect of manufacturing operations that involves the planning, scheduling, and execution of production tasks to ensure the efficient and timely completion of products. Work orders serve as essential documents that provide detailed instructions, specifications, and information to workers, enabling them to carry out their tasks effectively.
Proper work order management streamlines production processes, minimizes downtime, reduces lead times, and enhances overall productivity in the manufacturing facility.
Benefits of Work Order Management
Effective work order management brings numerous benefits to manufacturing operations:
- Improved Efficiency: Proper work order management streamlines production processes, reduces downtime, and eliminates inefficiencies, leading to improved overall efficiency in manufacturing.
- Reduced Lead Times: Efficient work order management helps in meeting production deadlines and reducing lead times, ensuring that products are delivered to customers on time.
- Enhanced Productivity: Work order management optimizes labor and resource allocation, leading to increased productivity and output in the manufacturing facility.
- Better Inventory Control: Work order management involves proper material management, which helps in maintaining optimal inventory levels and reducing the risk of stockouts or overstocking.
- Consistency and Quality: Work orders provide standardized instructions for production tasks, ensuring consistency in the quality of products.
- Real-time Monitoring: Work order management enables real-time monitoring of production progress, allowing managers to identify and address issues promptly.
- Cost Control: Efficient work order management helps in controlling production costs by optimizing resource utilization and minimizing wastage.
Strategies for Optimizing Work Order Management
To achieve optimal results in work order management, manufacturing facilities can implement the following strategies:
- Work Order Standardization: Standardizing work orders ensures consistency in instructions and helps in streamlining production processes.
- Automated Work Order Systems: Implementing automated work order systems eliminates manual paperwork, reduces errors, and enhances overall efficiency.
- Integration with ERP Systems: Integrating work order management with enterprise resource planning (ERP) systems allows for seamless data sharing and better visibility into production operations.
- Training and Skill Development: Providing training and skill development programs to production workers enhances their proficiency in following work order instructions and carrying out tasks.
- Continuous Improvement: Regularly reviewing and improving work order processes based on feedback and performance metrics helps in optimizing production efficiency.
Work Order Management Process
Work order management is a critical process in manufacturing and service industries that involves planning, scheduling, and executing production tasks or service jobs. It plays a crucial role in ensuring that products are manufactured efficiently, services are delivered on time, and customer expectations are met.
Work Order Creation
The first step in the work order management process is the creation of work orders. Work orders are documents that provide detailed instructions and information about the tasks or jobs to be performed. The work order creation process involves the following steps:
- Gathering Information: The process starts with gathering all the necessary information about the task or job. This includes product specifications, customer requirements, bill of materials (BOM), routing information, and any other relevant details.
- Defining Scope and Objectives: The scope and objectives of the work order are clearly defined to ensure that all stakeholders understand what needs to be accomplished.
- Identifying Resources: The resources required to complete the work order are identified, including labor, equipment, and materials.
- Assigning Priority: Work orders are often prioritized based on factors such as customer deadlines, production schedules, or service level agreements.
- Review and Approval: Once the work order is created, it is reviewed and approved by the appropriate personnel, such as production managers or service supervisors.
Scheduling and Planning
After work orders are created and approved, the next step is scheduling and planning. This involves determining the sequence of tasks, allocating resources, and setting timelines for completion. The scheduling and planning process includes the following:
- Sequencing Tasks: The tasks or jobs in the work order are sequenced in a logical order to ensure efficient flow and minimize downtime.
- Resource Allocation: The necessary resources, including manpower, equipment, and materials, are allocated to each task.
- Time Estimation: The time required to complete each task is estimated based on historical data, production rates, or service standards.
- Critical Path Analysis: For complex work orders with multiple tasks, a critical path analysis is performed to identify the longest sequence of tasks that must be completed on time to ensure timely project completion.
- Contingency Planning: Contingency plans are developed to address potential delays or disruptions that may arise during the execution of the work order.
Work Order Execution
Once the work orders are scheduled and planned, they are ready for execution. The work order execution process involves carrying out the tasks or jobs according to the instructions provided in the work order. The execution process includes the following:
- Work Assignment: Each task is assigned to the appropriate personnel or teams responsible for its completion.
- Progress Monitoring: The progress of each task is monitored regularly to ensure that it is on track and that any issues are addressed promptly.
- Quality Control: Quality control measures are implemented to ensure that each task is completed to the required standards.
- Record Keeping: Detailed records of work order execution are maintained for documentation and future reference.
Communication and Collaboration
Effective communication and collaboration are essential in work order management to ensure that all stakeholders are informed and involved throughout the process. This includes:
- Communication with Employees: Clear and timely communication with employees about their roles and responsibilities in executing the work order.
- Collaboration with Suppliers: Coordination with suppliers to ensure timely delivery of materials and resources required for the work order.
- Customer Communication: If the work order is related to a customer project, regular communication with the customer to provide updates on progress and address any concerns.
- Internal Collaboration: Collaboration between different departments or teams involved in the work order to ensure smooth coordination.
Work Order Completion and Review
Once all the tasks in the work order are completed, the work order is marked as finished, and the final deliverables are inspected for quality and compliance. After completion, a review of the work order process is conducted to identify any areas for improvement or lessons learned for future projects.
Work Order Documentation
Comprehensive documentation of the work order process is essential for future reference, audit purposes, and continuous improvement. Documentation includes:
- Work Order Records: Detailed records of each work order, including task descriptions, resource allocation, time taken, and any deviations from the plan.
- Quality Control Reports: Reports on quality control measures and any corrective actions taken during the execution of the work order.
- Cost Analysis: Analysis of the costs incurred in executing the work order, including labor, materials, and any additional expenses.
- Lessons Learned: A review of the work order process to identify successes and areas for improvement.
Work Orders vs. Job Orders: Key Distinctions
Work orders and job orders are both essential elements of the manufacturing and service industries, but they serve different purposes and have distinct characteristics.
Definition of Work Orders and Job Orders
Work Order: A work order is a document that provides detailed instructions and information about a specific task or job that needs to be completed. It includes the tasks to be performed, the resources required, the timeline for completion, and any other relevant details.
Work orders are used in various industries, including manufacturing, construction, maintenance, and service sectors, to ensure that tasks are carried out efficiently and effectively.
Job Order: A job order, on the other hand, is a document that represents a single project or job that a company undertakes for a customer. It includes all the tasks and activities involved in completing the project, the resources needed, the cost estimation, and the timeline for completion.
Job orders are commonly used in service industries, such as construction, repair, and professional services, where the work is customized to meet the specific needs of the customer.
Purpose and Use of Work Orders and Job Orders
Work Order: The primary purpose of a work order is to provide clear instructions to employees or workers about the tasks they need to perform and the resources they need to complete those tasks. Work orders are typically used for routine, repetitive tasks in manufacturing, maintenance, and other operational processes.
They help ensure consistency in the execution of tasks and contribute to process efficiency.
Job Order: Job orders, on the other hand, are used to manage complex, one-off projects that are unique to each customer. These projects may involve various tasks, materials, and timelines, and they require careful planning and coordination to meet the customer's specific requirements.
Job orders are commonly used in service industries, such as construction, where each project is customized to the customer's needs.
Flexibility and Customization
Work Order: Work orders are generally more standardized and less customizable than job orders. They are used for routine tasks that follow established procedures and may not require significant modifications for each occurrence. Work orders are often repetitive and can be quickly generated using templates or software systems.
Job Order: Job orders, on the other hand, are highly customizable and require careful planning and coordination for each project. Each job order is unique and tailored to the specific requirements of the customer.
Job orders may involve detailed specifications, custom materials, and specific timelines, making them more complex and time-consuming to create.
Cost Estimation and Billing
Work Order: Work orders are often used for internal purposes, such as managing production or maintenance tasks. They may not include detailed cost estimation, as the focus is on efficiency and resource allocation within the organization. Work orders are not typically used for billing customers.
Job Order: In contrast, job orders involve detailed cost estimation and billing. Since each job is unique and may require custom materials and resources, the cost estimation process is crucial to ensure accurate pricing and profitability.
Job orders are used for customer billing, and the final invoice is based on the actual resources and materials used for the specific project.
Project Duration and Complexity
Work Order: Work orders are generally shorter in duration and involve routine tasks that are completed relatively quickly. They are used for daily or weekly tasks in manufacturing, maintenance, or service operations.
Job Order: Job orders are often longer in duration and involve more complex tasks and projects. They may take weeks, months, or even years to complete, depending on the scope and scale of the project. Job orders require careful planning and project management to ensure successful delivery.
Examples of Work Orders and Job Orders
Work Order: Examples of work orders include manufacturing work orders for production tasks, maintenance work orders for equipment repair, and service work orders for routine service tasks such as vehicle maintenance or HVAC repairs.
Job Order: Examples of job orders include construction projects for building houses or commercial buildings, repair projects for specific equipment or machinery, and professional services projects such as consulting engagements or software development projects.
Who Uses Work Orders?
Work orders are used by various stakeholders in different industries to facilitate and manage maintenance, service, and production tasks. They play a crucial role in ensuring that work is carried out efficiently, safely, and on time.
Maintenance Technicians and Service Teams
Maintenance technicians and service teams are the primary users of work orders. They are responsible for carrying out the tasks specified in the work orders, such as equipment repairs, preventive maintenance, installations, and inspections.
Work orders provide maintenance technicians with detailed instructions, including the scope of work, materials required, safety considerations, and any other relevant information.
Maintenance technicians rely on work orders to understand what needs to be done and how to do it properly. They follow the instructions in the work orders to ensure that maintenance tasks are completed accurately and efficiently, minimizing downtime and disruptions to operations.
Maintenance Managers and Supervisors
Maintenance managers and supervisors play a crucial role in the work order process. They are responsible for creating, assigning, and managing work orders. When maintenance needs are identified, maintenance managers or supervisors evaluate the urgency and priority of the tasks and determine the resources required.
They then create work orders, specify the details of the tasks, and assign them to the appropriate maintenance technicians or service teams. Maintenance managers and supervisors also monitor the progress of work orders, ensuring that tasks are completed on time and in compliance with safety and quality standards.
Production and Operations Managers
In manufacturing and production industries, work orders are used to plan and schedule production tasks. Production and operations managers use work orders to define the steps and processes required to produce goods. Work orders in production environments include details such as the number of products to be produced, the production schedule, and the materials needed.
Production and operations managers rely on work orders to optimize production workflows, minimize production lead times, and ensure that production targets are met. Work orders also help them track production progress and identify any bottlenecks or inefficiencies in the production process.
Facility Managers
Facility managers are responsible for the maintenance and management of physical assets and facilities, such as buildings, equipment, and infrastructure. They use work orders to coordinate and schedule maintenance and repair tasks for these assets.
Work orders help facility managers keep track of maintenance activities and ensure that assets are well-maintained and in good working condition. By using work orders, facility managers can effectively manage maintenance resources, plan preventive maintenance, and respond to maintenance needs promptly.
Project Managers
Project managers in construction and engineering industries use work orders to plan and execute specific project tasks. Work orders in construction projects may include details such as the scope of work, materials needed, labor requirements, and project schedules.
Project managers rely on work orders to track project progress, allocate resources efficiently, and ensure that project tasks are completed according to the project timeline and budget.
Service Providers and Contractors
In some cases, organizations may outsource maintenance or service tasks to external service providers or contractors. Work orders are used to communicate the specific requirements and scope of work to these service providers.
Service providers and contractors follow the instructions in the work orders to complete the assigned tasks and provide the necessary services. Work orders also serve as a basis for invoicing and payment, as they provide a detailed record of the services provided.
Procurement and Inventory Managers
Work orders often involve the use of materials and spare parts. Procurement and inventory managers use work orders to identify the materials and parts needed for maintenance and production tasks.
By referring to work orders, procurement, and inventory managers can ensure that the necessary materials are available when needed, reducing delays in task execution and minimizing inventory holding costs.
Importance of Work Orders in Production Planning
Work orders play a vital role in production planning as they serve as a blueprint for organizing, managing, and executing manufacturing processes. They provide detailed instructions and information that guide workers through each step of the production process, ensuring that tasks are carried out efficiently and accurately.
- Structured and Organized Workflow
Work orders provide a structured and organized workflow for production processes. They outline the sequence of tasks and operations required to manufacture a product, ensuring that each step is completed in the correct order. This organization helps in minimizing production delays and preventing errors that may arise from a disorganized workflow.
By following the instructions in the work orders, production teams can maintain consistency in their processes, resulting in a smoother and more efficient manufacturing operation.
- Resource Management
Work orders provide essential information about the resources needed for each production task, including materials, labor, and equipment. This information allows production planners to ensure that all necessary resources are available at the right time and in the right quantities.
Effective resource management based on work orders helps in preventing production bottlenecks and shortages, ensuring that production runs smoothly and on schedule.
- Standardization and Quality Control
Work orders specify the standards and quality requirements for each production task. By adhering to these standards, manufacturing teams can consistently produce high-quality products that meet customer expectations.
Work orders also include quality checkpoints and inspection steps to ensure that products meet quality standards before they are released to the next stage of production. This emphasis on quality control helps in reducing defects and rework, leading to cost savings and improved customer satisfaction.
- Time Management
Work orders contain detailed information about the time required to complete each production task. This information allows production planners to create realistic production schedules and allocate sufficient time for each operation.
By effectively managing time-based on work orders, production planners can avoid production delays, reduce lead times, and ensure that products are delivered to customers on time.
- Data Collection and Analysis
Work orders serve as a valuable source of data for performance analysis and process improvement. By tracking the time, resources, and costs associated with each production task, companies can identify areas for optimization and efficiency gains.
Analyzing data from work orders can help identify production bottlenecks, optimize resource allocation, and improve overall production efficiency.
- Compliance and Documentation
Work orders provide a documented record of production processes and compliance with industry regulations and standards. They are essential for ensuring that manufacturing operations meet legal and regulatory requirements.
Work orders also serve as an important reference for audits and quality certifications, demonstrating that production processes are carried out by established procedures and guidelines.
Creating and Managing Work Orders Effectively
Creating and managing work orders effectively is essential for optimizing production processes and ensuring smooth manufacturing operations.
- Defining Work Order Requirements
The first step in creating a work order is to clearly define the requirements for the production task. This includes specifying the product to be manufactured, the quantity to be produced, the materials and resources needed, and any special instructions or quality standards.
Effective communication between production planners, engineers, and other stakeholders is crucial to ensure that all requirements are accurately captured in the work order.
- Assigning Work Order Numbers and Identifiers
Each work order should be assigned a unique number or identifier to facilitate tracking and reference. This identifier can be used to link the work order to related documents, such as bills of materials (BOMs) and standard operating procedures (SOPs).
The work order number should be visible on the physical copy of the work order and entered into the manufacturing system for easy retrieval and management.
- Creating Detailed Work Instructions
Work orders should contain detailed instructions for each production task, including step-by-step procedures, safety guidelines, and quality control checkpoints. The instructions should be written in clear and concise language, ensuring that workers can easily understand and follow them.
Visual aids, such as diagrams and photographs, can also be included to further clarify the instructions and enhance comprehension.
- Incorporating Bill of Materials (BOMs) and Routings
A bill of materials (BOM) lists all the components and raw materials required to manufacture a product. It is a critical component of the work order as it ensures that the correct materials are available for production.
Routings, on the other hand, specify the sequence of operations required to complete the production task. They provide a roadmap for the manufacturing process, ensuring that tasks are carried out in the correct order.
Integrating BOMs and routings into the work order ensures that workers have access to all the necessary information to complete the production task efficiently.
- Setting Realistic Timeframes
Work orders should include realistic timeframes for each production task. This includes the estimated time required to complete each operation as well as the overall lead time for the entire production process.
Setting realistic timeframes helps in managing production schedules and ensures that customer orders are fulfilled on time.
- Assigning Resources and Personnel
Work orders should specify the resources and personnel assigned to each production task. This includes the equipment and machinery to be used, as well as the skilled workers or operators required.
By assigning resources and personnel in advance, production planners can optimize resource allocation and avoid conflicts or bottlenecks.
- Review and Approval
Before work orders are released to the production floor, they should undergo a thorough review and approval process. This includes checking for accuracy, completeness, and compliance with quality standards and safety guidelines.
Work orders should be reviewed by relevant stakeholders, including production managers, engineers, and quality control personnel, to ensure that all aspects of the production task have been considered.
- Communication and Training
Effective communication is crucial for successful work order management. Workers should be informed about the release of new work orders, and any changes or updates to existing work orders should be communicated promptly.
Training sessions can also be conducted to familiarize workers with the content of the work orders and to ensure that they understand the procedures and requirements.
- Tracking and Monitoring
Once work orders are in progress, it is important to track and monitor their status to ensure that tasks are completed on time and according to the specifications.
This can be achieved through a combination of manual tracking methods, such as production boards or spreadsheets, and digital tools, such as manufacturing execution systems (MES) or enterprise resource planning (ERP) software.
- Documenting Work Order Progress
Documenting the progress of work orders is essential for performance analysis and process improvement. This includes recording any deviations or issues encountered during production, as well as any corrective actions taken.
By documenting work order progress, manufacturing teams can identify areas for improvement and implement measures to enhance productivity and efficiency.
- Archiving and Retrieval
Work orders should be properly archived and stored for future reference. This includes maintaining a database or filing system where completed work orders can be easily retrieved for analysis or audits.
Archiving work orders also ensures that historical data is available for reference when planning future production tasks.
Work Orders and Resource Allocation
Work orders serve as a central point of reference for resource allocation. They provide all the necessary information for determining what resources are needed to complete a task and when they are required.
Without work orders, resource allocation would be much more challenging, as planners would need to rely on fragmented information from various sources to make decisions. Work orders consolidate all relevant information into a single document, streamlining the resource allocation process.
Optimizing Resource Allocation Through Work Orders
Effective work order management can lead to optimized resource allocation in several ways:
- Clear Task Requirements: Work orders clearly define the scope of each task and the resources required. This clarity helps planners allocate the right resources to each job, avoiding overallocation or under allocation of resources.
- Realistic Timeframes: Work orders include estimated completion times for each task. Planners can use this information to schedule resources efficiently and ensure that they are available when needed.
- Prioritization: Work orders often come with priority levels or due dates, indicating the importance of each task. This prioritization guides resource allocation decisions, ensuring that critical tasks receive the necessary resources.
- Resource Availability: Work orders can also indicate the availability of specific resources. Planners can use this information to avoid scheduling tasks that require the same limited resource simultaneously.
Challenges in Resource Allocation Through Work Orders
While work orders are a valuable tool for resource allocation, several challenges can affect their effectiveness:
- Incomplete or Inaccurate Information: Work orders must be accurate and comprehensive to support effective resource allocation. Incomplete or inaccurate information can lead to mistakes in resource planning.
- Changes and Updates: Work orders are not static documents. Changes may occur during a task, requiring adjustments in resource allocation. Keeping track of these changes and ensuring that resource plans are updated accordingly can be challenging.
- Competing Priorities: In situations where multiple tasks have high priority, planners must carefully weigh the importance of each task and allocate resources accordingly. Balancing competing priorities can be complex.
- Resource Constraints: In some cases, there may be limited availability of certain resources, such as skilled labor or specialized equipment. Planners must find creative solutions to optimize resource utilization despite these constraints.
Best Practices for Effective Resource Allocation Through Work Orders
To optimize resource allocation through work orders, organizations can adopt the following best practices:
- Standardize Work Order Format: Implementing a standardized work order format ensures consistency and clarity. Include all essential information, such as task description, materials, equipment, estimated time, and personnel.
- Regularly Review Work Orders: Review work orders regularly to identify potential issues or changes that may affect resource allocation. Keeping work orders up to date is essential for accurate resource planning.
- Use Resource Management Software: Resource management software can automate and streamline the resource allocation process. These tools provide real-time data on resource availability and utilization, making it easier to optimize allocation.
- Collaborate Across Departments: Collaboration between departments, such as production, maintenance, and procurement, is crucial for effective resource allocation. Share information and coordinate efforts to ensure the smooth flow of resources.
- Monitor Resource Utilization: Regularly monitor resource utilization and adjust allocations as needed. Identify trends or patterns in resource usage to identify opportunities for improvement.
Work Orders and Scheduling in Manufacturing
Work orders and scheduling are critical components of manufacturing operations. They work hand in hand to ensure the smooth and efficient execution of production tasks.
Scheduling involves the allocation of time and resources to specific tasks. It involves creating a timeline for production activities, coordinating the sequence of tasks, and managing resources to meet production deadlines.
The Role of Work Orders in Scheduling
Work orders play a crucial role in the scheduling process. They provide essential information that forms the basis for creating a production schedule:
- Task Details: Work orders contain detailed descriptions of each task, including its scope, objectives, and requirements. This information helps schedulers understand the nature of the tasks to be performed.
- Resource Requirements: Work orders specify the materials, equipment, and labor needed for each task. Schedulers use this information to allocate the necessary resources and ensure that they are available when needed.
- Estimated Time: Work orders often include estimated completion times for each task. Schedulers use these estimates to create a realistic production timeline and allocate sufficient time for each task.
- Dependencies: Work orders may also indicate task dependencies, showing which tasks must be completed before others can begin. This information is critical for sequencing tasks in the production schedule.
The Role of Scheduling in Work Orders
Scheduling complements work orders by providing a framework for their execution. It involves the following key aspects:
- Time Allocation: Scheduling involves allocating specific timeframes for each task to be completed. This ensures that production activities are carried out in an organized and timely manner.
- Sequence of Tasks: Schedulers arrange tasks in a logical order based on their dependencies and other considerations. This helps maintain a smooth flow of production and minimizes delays.
- Resource Management: Scheduling involves managing resources such as materials, equipment, and labor to ensure they are available when needed for each task.
- Production Deadlines: Schedulers set production deadlines based on factors like customer demand and inventory levels. They work to meet these deadlines while maintaining high-quality standards.
Challenges in Work Order Scheduling
Work order scheduling is not without its challenges. Some common issues that manufacturers may face include:
- Unexpected Changes: Changes in customer demand, material availability, or machine breakdowns can disrupt the production schedule. Manufacturers must be agile and adapt to such changes quickly.
- Task Dependencies: Work orders may have complex task dependencies, making it challenging to sequence tasks optimally. Schedulers must carefully analyze these dependencies to avoid bottlenecks.
- Resource Constraints: Limited availability of certain resources, such as skilled labor or specialized equipment, can impact the scheduling process. Schedulers must find ways to allocate resources efficiently despite these constraints.
- Meeting Production Deadlines: Striking a balance between meeting production deadlines and maintaining product quality can be challenging. Rushing production to meet deadlines may lead to errors and defects.
Best Practices for Effective Work Order Scheduling
To optimize work order scheduling, manufacturers can follow these best practices:
- Utilize Scheduling Software: Advanced scheduling software can automate and streamline the scheduling process. These tools consider various factors and help create efficient production schedules.
- Establish Buffer Times: Leave buffer times between tasks to account for unexpected delays or changes. This flexibility can help absorb disruptions without affecting the overall production timeline.
- Collaborate Across Departments: Effective communication and collaboration between production, procurement, and other departments are essential for accurate scheduling. Involve key stakeholders in the scheduling process to ensure alignment.
- Monitor and Adjust: Regularly monitor the progress of tasks and adjust the schedule as needed. Implement a feedback loop to capture lessons learned and continuously improve the scheduling process.
Work Orders and Cost Control in Production
Work orders play a crucial role in cost control in production processes. They serve as the foundation for planning, executing, and tracking production tasks, ensuring that resources are utilized efficiently and costs are managed effectively.
Work orders are detailed instructions that outline the tasks, materials, labor, and equipment required to complete a specific production job. They provide a clear roadmap for workers, guiding them through the production process to ensure that each task is carried out accurately and efficiently.
The Role of Work Orders in Cost Control
Work orders have a direct impact on cost control in production processes. Here's how they contribute to cost management:
- Resource Allocation: Work orders specify the resources needed for each task, including raw materials, equipment, and labor. By detailing the exact requirements, work orders help avoid overutilization of resources, preventing unnecessary costs.
- Cost Estimation: Work orders often include cost estimates for each task, considering factors such as material prices and labor rates. This allows production managers to plan and budget effectively, ensuring that production costs are within the allocated budget.
- Production Planning: Work orders help in creating an organized production plan, outlining the sequence of tasks and their timelines. Proper planning minimizes idle time and optimizes resource utilization, reducing production costs.
- Quality Control: Work orders specify quality standards and requirements for each task. Adhering to these standards helps reduce rework and waste, leading to cost savings in the long run.
Cost Factors in Work Orders
Several cost factors are considered in work orders to facilitate cost control:
- Material Costs: Work orders list the required materials for each task, along with their quantities and costs. Accurate material cost calculations enable better budgeting and cost management.
- Labor Costs: Work orders detail the labor hours and skill levels needed for each task. This information helps in calculating labor costs accurately.
- Overhead Costs: Overhead costs, such as utilities, maintenance, and administrative expenses, are also taken into account when creating work orders. Managing overhead costs contributes to overall cost control.
- Equipment Costs: Work orders may involve the use of specific equipment. Evaluating equipment costs ensures that their usage is efficient and cost-effective.
Using Work Orders for Cost Monitoring
Work orders are not only essential for cost planning but also for cost monitoring during the production process. By tracking the progress of each task, production managers can compare actual costs with estimated costs and identify any cost variances. Timely identification of cost overruns or savings allows for quick action and adjustments to keep production costs on track.
Streamlining Work Order Creation for Cost Efficiency
Efficient work order creation contributes to cost control. To streamline the process, manufacturers can consider the following:
- Standardization: Establishing standardized work order templates ensures consistency and reduces the time spent on creating individualized orders.
- Automation: Utilizing digital systems or software to create and manage work orders can save time and reduce manual errors.
- Integration: Integrating work order systems with other production and inventory management systems provides real-time data and enhances cost visibility.
- Training: Providing training to production teams on work order management ensures that the process is executed accurately and efficiently.
Integrating Work Orders With Manufacturing Software
Work orders are critical documents in manufacturing that provide detailed instructions for production processes. Integrating work orders with manufacturing software is a strategic approach that streamlines operations, enhances efficiency, and improves overall productivity.
Manufacturing Software Solutions for Work Order Integration
Various manufacturing software solutions can be integrated with work orders:
- Enterprise Resource Planning (ERP) Software: ERP systems integrate various aspects of manufacturing operations, including work order management, inventory control, accounting, and human resources.
- Manufacturing Execution Systems (MES): MES systems focus on managing production processes in real-time, enabling better tracking and control of work orders on the shop floor.
- Manufacturing Resource Planning (MRP) Software: MRP systems focus on materials planning and scheduling, ensuring that work orders are fulfilled with the right resources.
- Customer Relationship Management (CRM) Software: CRM software helps in managing customer orders and aligning them with work orders for seamless production execution.
- Production Scheduling Software: Production scheduling software optimizes the allocation of resources and schedules work orders based on available capacity and demand.
Steps to Implement Work Order Integration
To successfully implement work order integration with manufacturing software, manufacturers should follow these steps:
- Identify Requirements: Understand the specific needs and objectives of the organization, and assess the software solutions available to find the best fit.
- Choose the Right Software: Select a software solution that aligns with the manufacturing processes and integrates smoothly with existing systems.
- Data Migration: Ensure a smooth transfer of data from the existing work order management system to the new software.
- Employee Training: Provide comprehensive training to employees on how to use the new integrated software effectively.
- Test and Monitor: Conduct thorough testing to ensure that the integration works as expected and continue monitoring the system for any potential issues.
- Address Challenges: Be prepared to address any challenges or issues that may arise during the implementation process.
Common Challenges and Solutions in Work Order Integration
Integrating work orders with manufacturing software may encounter some challenges, including:
- Data Inconsistency: Ensure that data is consistent and accurate across all integrated systems by implementing data validation and synchronization measures.
- Software Compatibility: Select software that is compatible with existing systems and can seamlessly exchange data.
- Resistance to Change: Address resistance to change through effective communication, training, and highlighting the benefits of the integrated system.
- Security Concerns: Implement robust security measures to protect sensitive data and ensure data privacy and compliance.
- Software Customization: Customization may be required to tailor the software to specific manufacturing processes and requirements.
Key Performance Indicators (KPIs) for Work Order Integration
To measure the success of work order integration, manufacturers can monitor the following KPIs:
- Work Order Completion Time: Measure the time taken to complete work orders, ensuring that they are fulfilled within the scheduled timeframe.
- Production Efficiency: Assess production efficiency metrics such as Overall Equipment Efficiency (OEE) to gauge how well work orders are executed.
- Inventory Turnover: Evaluate inventory turnover to ensure that work orders align with inventory levels, avoiding excess stock or shortages.
- Customer Satisfaction: Monitor customer feedback and satisfaction levels to ensure that work orders meet customer requirements.
- Resource Utilization: Measure resource utilization to optimize the allocation of labor and materials based on work order demand.
Future Trends in Work Order Management
As technology continues to advance, the future of work order management promises significant innovations that will transform manufacturing efficiency and productivity.
Automation and Artificial Intelligence
Automation and artificial intelligence (AI) are revolutionizing various industries, and manufacturing is no exception. In the future, AI-powered work order management systems will automate tasks, optimize production schedules, and predict maintenance needs.
AI algorithms can analyze historical data to improve production planning, identify patterns, and make data-driven decisions. By automating routine tasks, manufacturing companies can save time, reduce errors, and increase overall efficiency.
Predictive Maintenance
Predictive maintenance is a game-changer for manufacturing industries, allowing them to move from reactive to proactive maintenance approaches. In the future, work order management systems will leverage data from sensors and IoT devices to predict equipment failures and maintenance needs.
By addressing issues before they escalate, manufacturers can prevent downtime, reduce maintenance costs, and optimize equipment performance.
Augmented Reality (AR) and Virtual Reality (VR)
AR and VR technologies are transforming the way work orders are executed in manufacturing. In the future, technicians can use AR glasses to access work instructions, diagrams, and real-time data, superimposed on physical equipment.
VR simulations can also be used for training purposes, enabling employees to practice complex tasks in a virtual environment before executing them in the real world. These technologies enhance the accuracy and speed of work order execution, reducing human errors and increasing productivity.
Mobile Work Order Management
Mobile devices have already become essential tools in manufacturing operations, and their role will only grow in the future. Mobile work order management applications will allow technicians to access work orders, update statuses, and receive notifications on their smartphones and tablets.
This real-time connectivity enables better communication, faster response times, and seamless collaboration between teams.
Cloud-Based Work Order Management Systems
Cloud-based work order management systems will become the norm in the future, providing manufacturers with the flexibility and scalability they need. Cloud solutions offer real-time updates, easy data access, and automatic backups, eliminating the need for manual data entry and paper-based work orders.
With cloud-based systems, work orders can be accessed from anywhere, ensuring that all stakeholders have the most up-to-date information.
Blockchain for Enhanced Transparency
Blockchain technology is gaining traction in various industries, and its application in work order management holds immense potential. Blockchain can enhance transparency and security by providing an immutable and decentralized ledger of all work order-related transactions.
This technology can improve traceability, prevent unauthorized modifications, and build trust among stakeholders.
Internet of Things (IoT) Integration
IoT integration will play a crucial role in the future of work order management. IoT devices can continuously monitor equipment performance, collect data on machine health, and communicate maintenance requirements to the work order management system.
By enabling real-time data analysis and predictive maintenance, IoT integration optimizes work order execution and minimizes downtime.
3D Printing and Additive Manufacturing
As 3D printing and additive manufacturing continue to evolve, they will impact work order management in several ways.
Work orders for custom parts and prototypes can be executed more efficiently using 3D printing technologies. Moreover, the ability to create spare parts on demand can reduce lead times and inventory costs.
Data Analytics and Business Intelligence
In the future, work order management systems will rely heavily on data analytics and business intelligence tools to make informed decisions. Advanced analytics can optimize production schedules, identify bottlenecks, and uncover opportunities for process improvement.
Business intelligence dashboards will offer real-time insights into work order status, production KPIs, and resource allocation.
Integration with Supply Chain and ERP Systems
To achieve seamless coordination and data flow, work order management systems will be integrated with supply chain and enterprise resource planning (ERP) systems.
This integration ensures that work orders align with inventory levels, customer demands, and overall production planning, optimizing resource utilization and reducing lead times.
Environmental Sustainability and Green Work Orders
Sustainable practices will become a top priority for manufacturers in the future. Green work orders will focus on minimizing waste, reducing energy consumption, and adopting eco-friendly materials.
Work order management systems will track and report on environmental impact, enabling companies to make sustainability-driven decisions.
Digital Twins for Work Order Simulations
Digital twins are virtual replicas of physical assets, and they will be increasingly used to simulate work orders and production processes. Manufacturers can test different scenarios, identify potential issues, and optimize production sequences before implementing changes in the real world.
How Can Deskera Help You?
Deskera MRP allows you to closely monitor the manufacturing process. From the bill of materials to the production planning features, the solution helps you stay on top of your game and keep your company's competitive edge.
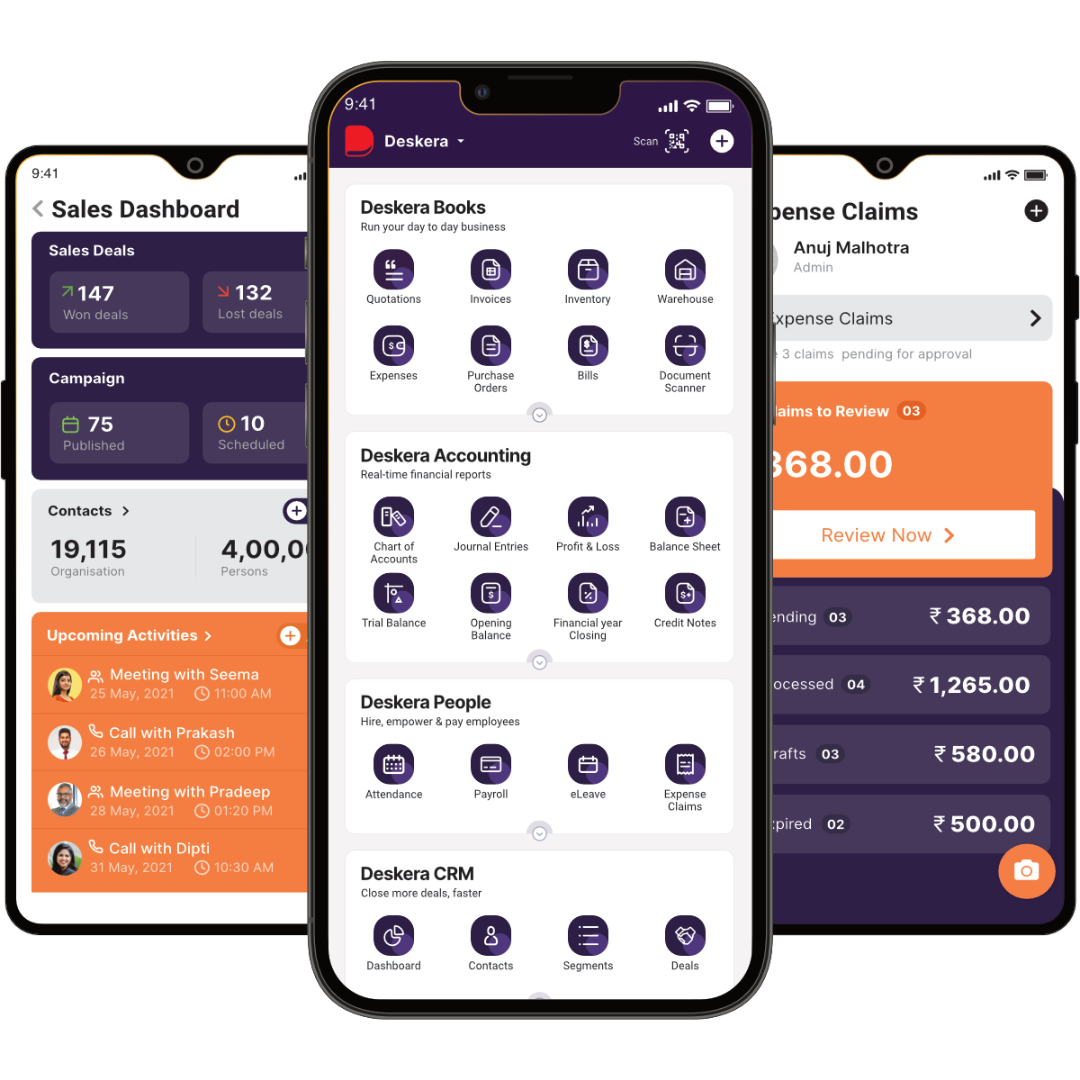
Deskera ERP and MRP system can help you:
- Manage production plans
- Maintain Bill of Materials
- Generate detailed reports
- Create a custom dashboard
Deskera ERP offers comprehensive features for work order management, empowering businesses to efficiently plan, execute, and track work orders across various departments and functions. Whether in manufacturing, maintenance, or service industries, Deskera ERP's work order management capabilities streamline operations, improve productivity, and enhance collaboration. Here's how Deskera ERP can help in work order management:
- Work Order Creation: Deskera ERP enables businesses to create work orders for various tasks, projects, maintenance activities, or service requests. Work orders can be initiated based on customer requests, preventive maintenance schedules, or production requirements.
- Priority Assignment: Work orders can be categorized and assigned priority levels based on factors such as urgency, criticality, and customer agreements.
- Resource Allocation: Deskera ERP helps allocate the necessary resources, such as manpower, equipment, materials, and tools, to each work order. This ensures efficient utilization of resources.
- Scheduling and Planning: The system supports scheduling work orders based on available resources, skill sets, and timelines. It helps prevent conflicts and optimize work order execution.
- Real-Time Status Tracking: Deskera ERP provides real-time visibility into the status of work orders, allowing stakeholders to monitor progress, track completion, and address any delays promptly.
Deskera Books enables you to manage your accounts and finances more effectively. Maintain sound accounting practices by automating accounting operations such as billing, invoicing, and payment processing.
Deskera CRM is a strong solution that manages your sales and assists you in closing agreements quickly. It not only allows you to do critical duties such as lead generation via email, but it also provides you with a comprehensive view of your sales funnel.
Deskera People is a simple tool for taking control of your human resource management functions. The technology not only speeds up payroll processing but also allows you to manage all other activities such as overtime, benefits, bonuses, training programs, and much more. This is your chance to grow your business, increase earnings, and improve the efficiency of the entire production process.
Conclusion
Work orders play an integral role in efficient manufacturing processes, providing the necessary structure, documentation, and guidance to ensure smooth and organized operations. This article has explored the definition of work orders, their significance in manufacturing, and the key elements involved in creating and managing them effectively.
Work orders act as a vital bridge between planning and execution, enabling seamless coordination and communication throughout the manufacturing workflow. By providing clear instructions and guidelines, work orders minimize ambiguity, reduce errors, and facilitate proper resource allocation, ultimately enhancing overall productivity and reducing operational costs.
Moreover, we highlighted the key components of a work order, such as work descriptions, task details, bill of materials (BOM), and standard operating procedures (SOPs). These components provide comprehensive instructions and specifications to guide workers and ensure consistent quality across production.
Advanced Manufacturing Execution Systems (MES) and Enterprise Resource Planning (ERP) software have revolutionized work order processes, enabling real-time tracking, automation, and data-driven decision-making. Clear and detailed instructions foster effective teamwork and enable smooth workflow coordination.
Key Takeaways
- Work orders are detailed instructions that play a vital role in efficient manufacturing, providing a clear roadmap for production tasks.
- They bridge the gap between planning and execution, ensuring seamless coordination and communication throughout the manufacturing workflow.
- Work orders minimize ambiguity, reduce errors, and optimize resource allocation, ultimately enhancing overall productivity and reducing operational costs.
- Different types of work orders, such as production, maintenance, and repair work orders, cater to specific needs within a manufacturing facility.
- Key components of a work order include work descriptions, task details, bill of materials (BOM), and standard operating procedures (SOPs).
- Technology, such as Manufacturing Execution Systems (MES) and Enterprise Resource Planning (ERP) software, has transformed work order management, enabling real-time tracking and automation.
- Digital work orders offer improved accuracy, accessibility, and data integration, streamlining operations and reducing paperwork.
- Work orders play a significant role in resource planning and management, facilitating the effective allocation of labor, equipment, and materials.
- They are essential in maintenance and repair operations, scheduling preventive tasks, and detailing necessary actions to minimize downtime.
- Work orders contribute to inventory control by specifying required materials and quantities, helping maintain appropriate inventory levels.
Related Articles

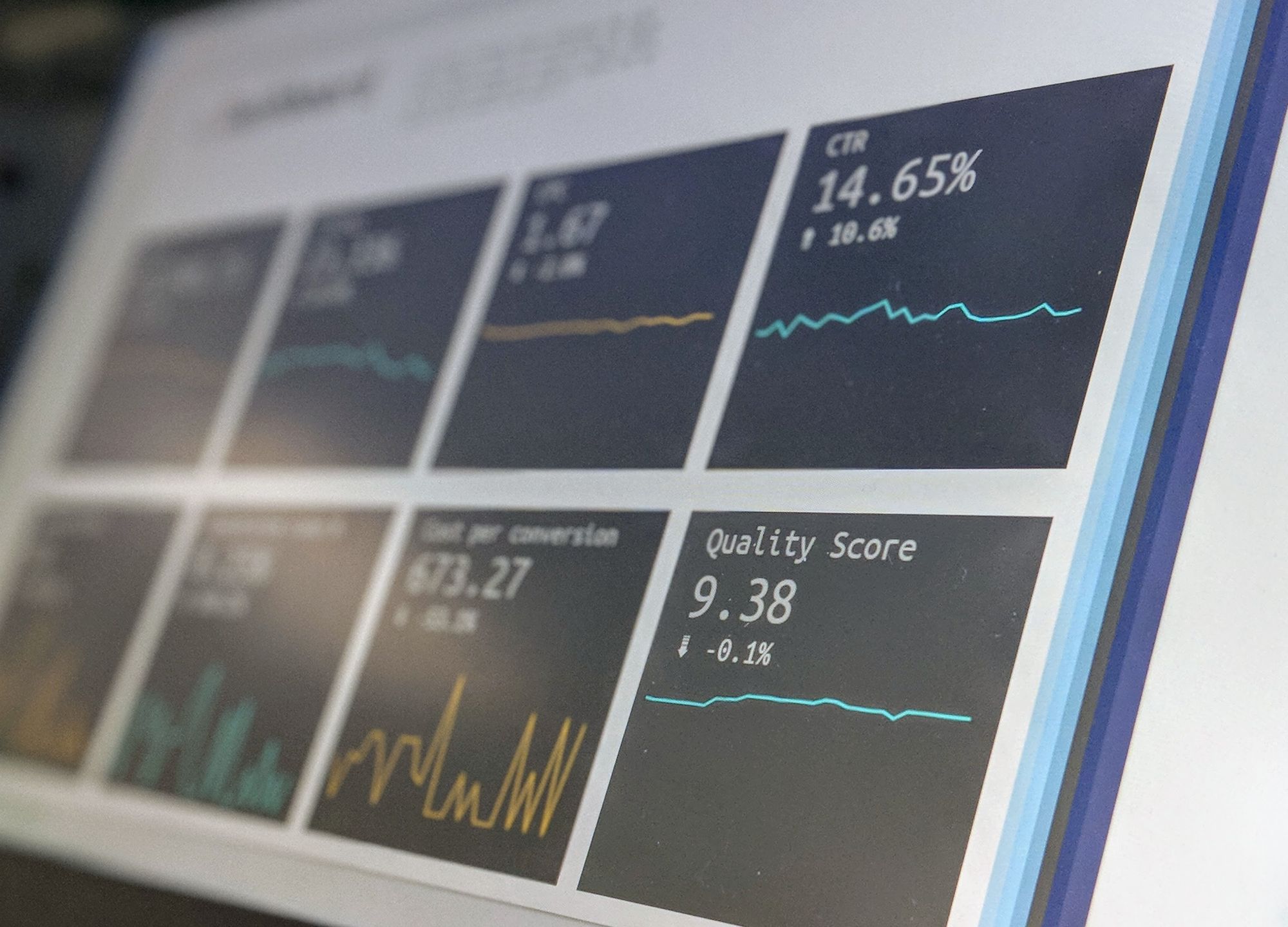
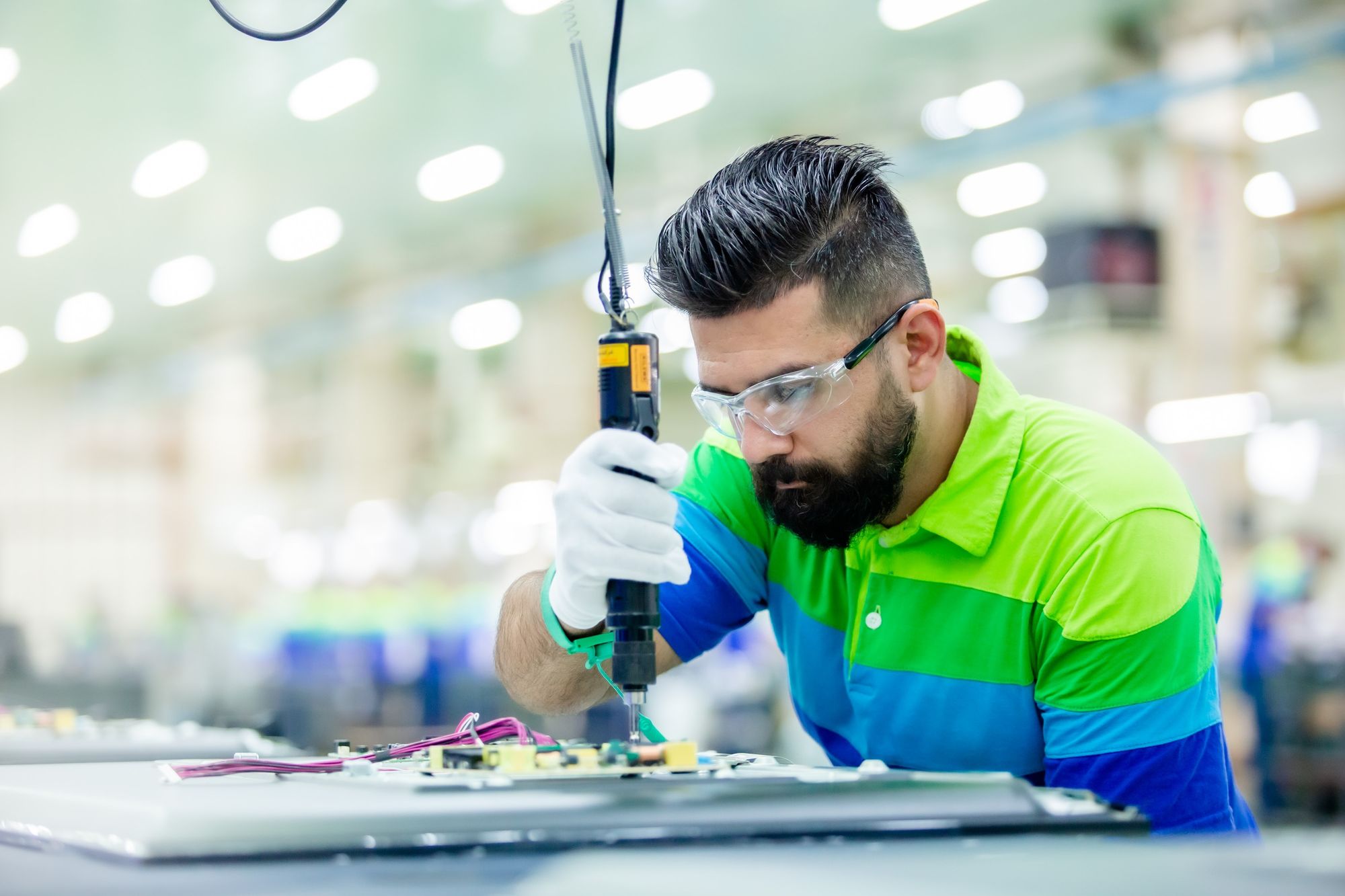
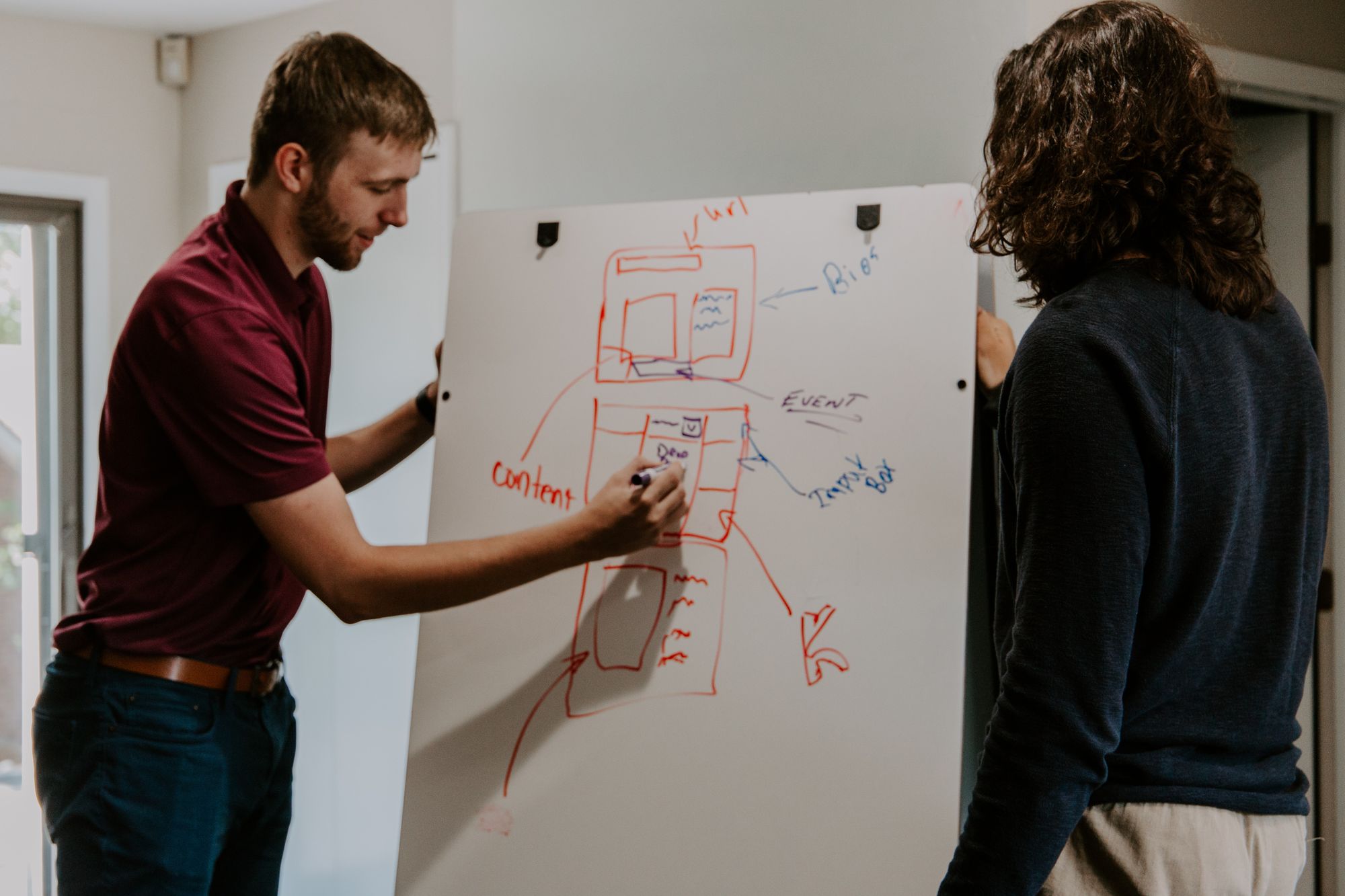