Have you ever wondered how some manufacturing companies are able to produce high-quality products while maintaining efficient production schedules? The key to their success lies in effective production scheduling techniques and tools.
In today's fast-paced manufacturing industry, streamlining your production schedule is essential for improving productivity, reducing lead times, and increasing profitability.
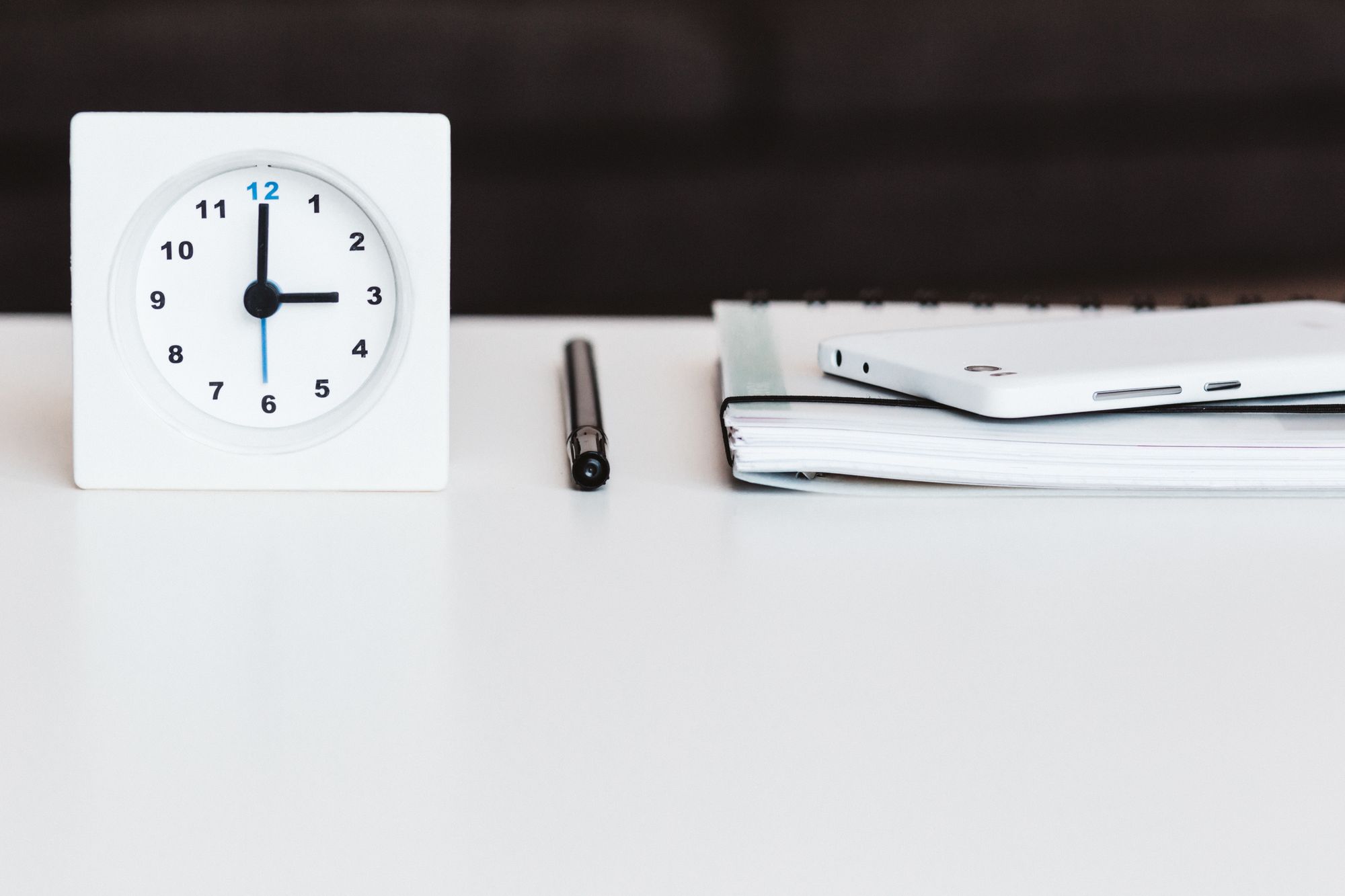
According to a recent report by Industry Week, over 65% of manufacturers cite "improving scheduling practices" as a top priority for improving their production processes. Additionally, a study by the National Institute of Standards and Technology (NIST) found that inefficient production scheduling is a major factor in decreasing manufacturing productivity, resulting in a 4% to 5% reduction in annual profits for some companies.
To avoid these losses and stay competitive, manufacturers need to implement best practices and tools for streamlining their production schedules. This article will explore some of the most effective techniques and tools for optimizing your manufacturing production schedule, along with real-world examples of companies that have successfully implemented them.
From leveraging advanced planning and scheduling (APS) software to implementing lean manufacturing principles, we'll cover everything you need to know.
Here's what we shall cover in this post:
- The Importance of Effective Manufacturing Production Scheduling
- Utilizing Lean Manufacturing Principles for Efficient Scheduling
- The Role of Data Analytics in Scheduling Optimization
- Choosing the Right Scheduling Software for Your Operations
- Minimizing the Impact of Unexpected Disruptions on Your Schedule
- Incorporating Machine Maintenance Into Your Production Schedule
- The Benefits of a Visual Scheduling System
- Continuous Improvement in Your Scheduling Process
- How can Deskera Help You?
- Conclusion
- Key Takeaways
The Importance of Effective Manufacturing Production Scheduling
Effective manufacturing production scheduling is crucial for any organization that wants to optimize its production process and increase efficiency. A well-designed production schedule ensures that resources are utilized effectively, resulting in lower production costs and higher profits.
- A well-planned production schedule ensures that customer demands are met promptly and efficiently. This is crucial for maintaining customer satisfaction and loyalty.
- Production scheduling ensures that resources such as labor, raw materials, and machinery are used efficiently, which results in lower production costs and higher profits.
- A good production schedule can help reduce lead times, which in turn leads to shorter delivery times and faster response to customer demands.
- Production scheduling can also help improve quality by identifying potential bottlenecks in the production process and addressing them before they become a problem.
- An effective production schedule allows for greater flexibility in responding to changes in customer demand or unexpected events such as equipment breakdowns.
- Organizations can reduce waste by optimizing production schedules and minimizing the environmental impact.
- An effective production schedule provides insight into production capacity, resource utilization, and overall efficiency. This information can be used to make informed decisions about future production planning and resource allocation.
Factors to Consider When Creating a Production Schedule
Creating an effective production schedule is crucial to ensure that manufacturing operations run smoothly and efficiently. It involves taking into account various factors to optimize production processes and meet demand while ensuring that resources are utilized efficiently.
Here are some factors to consider when creating a production schedule:
- Demand: Demand is the first factor to consider when creating a production schedule. Accurately forecasting demand is crucial to ensure that the production schedule is optimized to meet the demand without causing overproduction or stockouts. Factors that can influence demand include seasonality, customer preferences, and changes in market trends.
- Capacity: Capacity refers to the maximum amount of output that can be produced by a manufacturing facility in a given time period. It is essential to ensure that the production schedule takes into account the available capacity to avoid bottlenecks and ensure that resources are utilized efficiently.
- Lead time: Lead times refer to the time it takes to complete a production process, from the initial order to the final delivery. It is crucial to consider lead times when creating a production schedule to ensure that production processes are completed on time and that customer orders are fulfilled within the expected time frame.
- Raw materials: Raw materials are the basic materials that are used in the production process. It is vital to ensure that the production schedule takes into account the availability of raw materials, lead times for ordering them, and any potential supply chain disruptions that may impact the availability of raw materials.
- Workforce: The workforce is a crucial factor to consider when creating a production schedule. It is essential to ensure that the production schedule takes into account the availability of workers, their skills and experience, and any potential labor shortages that may impact production.
- Equipment: Equipment is another crucial factor to consider when creating a production schedule. It is vital to ensure that the production schedule takes into account the availability of equipment, maintenance schedules, and any potential breakdowns that may impact production.
- Quality control: Quality control is crucial to ensure that products meet the required standards and specifications. Ensuring that the production schedule includes sufficient time for completion of quality control processes is important.
- Production costs: Production costs include all the costs associated with the production process, including labor costs, material costs, equipment costs, and overhead costs. It is crucial to ensure that the production schedule takes into account production costs to ensure that the manufacturing facility is operating efficiently and profitability.
- Flexibility: Flexibility is an essential factor to consider when creating a production schedule. It is crucial to have a production schedule that can be adjusted easily to accommodate changes in demand, supply chain disruptions, or any unexpected events that may impact production.
- Communication: Effective communication is crucial when creating a production schedule. It is essential to ensure that all stakeholders, including suppliers, production managers, and workers, are aware of the production schedule and understand their roles and responsibilities in the production process.
By considering these factors, manufacturing facilities can optimize their production processes and meet customer demand efficiently and effectively.
The Benefits of Automation in Scheduling
Here are some of the key benefits of automation in scheduling:
Increased Efficiency: Automated scheduling can reduce the time and effort required to create and update schedules. With automation, businesses can optimize their production schedules to minimize downtime and maximize throughput.
This can significantly improve productivity and efficiency, helping companies to meet their production goals more quickly and cost-effectively.
Improved Accuracy: Manual scheduling can be prone to errors, such as double bookings or missed tasks. Automated scheduling can eliminate these errors by providing real-time resource availability and capacity visibility.
With automated scheduling, businesses can avoid scheduling conflicts and ensure that all tasks are completed on time and to the required standard.
Better Planning and Coordination: Automated scheduling systems can help businesses plan and coordinate their production schedules more effectively. With real-time resource availability and capacity data, companies can make more informed scheduling and resource allocation decisions.
This can help them optimize their schedules to meet production goals while minimizing downtime and waste.
Enhanced Flexibility: Automated scheduling systems can be highly flexible, allowing businesses to adapt quickly to changing production requirements. By providing real-time visibility into resource availability and capacity, companies can adjust their schedules in response to unexpected events or changes in demand.
This can help them meet customer needs more effectively and remain agile in a rapidly changing market.
Improved Quality Control: Automated scheduling systems can help businesses maintain consistent quality control by ensuring that all tasks are completed on time and to the required standard.
Businesses can reduce the risk of quality issues by eliminating scheduling errors and minimizing downtime. This can help them build a strong reputation for quality and reliability, which is essential in today's competitive manufacturing industry.
Automated scheduling systems can help businesses optimize their production schedules and remain agile in a rapidly changing market by providing real-time visibility into resource availability and capacity.
Whether you are a small startup or a large-scale manufacturer, automation in scheduling can help you achieve your production goals and stay ahead of the competition.
Utilizing Lean Manufacturing Principles for Efficient Scheduling
Lean manufacturing is a production philosophy that focuses on maximizing efficiency and reducing waste. It is widely used in manufacturing industries to optimize production processes, increase productivity, and reduce costs. One of the key components of lean manufacturing is efficient scheduling.
Value Stream Mapping
Value stream mapping is a tool used in lean manufacturing to identify areas of waste in a production process. By mapping the value stream, manufacturers can identify steps in the process that do not add value and find ways to eliminate them. This approach can also be applied to scheduling, where manufacturers can map out the scheduling process to identify areas of inefficiency and waste.
Here are some points to consider when implementing VSM for efficient scheduling:
- Understand your current state: Before implementing VSM, it's essential to understand your current production process clearly. This involves analyzing the flow of materials, equipment, and information through the system and identifying any bottlenecks or areas of waste.
- Identify areas for improvement: Once you clearly understand the current state, it's essential to identify areas for improvement. This involves analyzing the data collected during the mapping process and identifying areas where waste can be eliminated, or processes can be streamlined.
- Develop a future state map: Based on the analysis of the current state and areas for improvement, it's essential to develop a future state map. This visual represents the ideal production process, which incorporates changes and improvements identified during the analysis process.
- Implement changes: Once the future state map has been developed, it's time to implement the changes necessary to achieve that ideal state. This may involve reorganizing the production process, implementing new tools or technologies, or changing how information is communicated.
- Monitor and adjust: Continuous improvement is key to efficient scheduling. It's essential to monitor the results of the changes made and make adjustments as needed to ensure the process remains efficient over time.
Implementing Value Stream Mapping for efficient scheduling can be a powerful tool for identifying and eliminating waste in your production process. Systematically analyzing and improving the flow of materials and information can reduce lead times, increase productivity, and improve customer satisfaction.
Just-in-Time (JIT) Production
Just-in-Time (JIT) is a production strategy used in lean manufacturing that aims to produce only what is needed when it is needed and in the right quantity. This approach reduces inventory costs and waste and improves efficiency by ensuring that production resources are used only when necessary.
By applying JIT principles to scheduling, manufacturers can avoid overproduction and reduce waiting times, leading to improved scheduling efficiency.
- Streamlining the supply chain: JIT production requires a streamlined supply chain that can quickly and efficiently deliver the necessary materials and components to the production line. This may involve working closely with suppliers to ensure timely delivery and implementing processes to reduce lead times.
- Minimizing inventory: One of the key principles of JIT production is minimizing inventory levels to reduce waste and improve efficiency. This involves producing only what is needed when it is needed and in the required quantity.
- Implementing a pull-based system: JIT production relies on a pull-based system, where production is triggered by actual customer demand. This ensures that products are produced only when they are needed, reducing the risk of overproduction and excess inventory.
- Improving quality control: JIT production requires high-quality control to ensure that products meet customer specifications and minimize the risk of defects or rework. This involves implementing robust quality control processes and continuously monitoring and improving them.
JIT production can be an effective strategy for achieving efficient scheduling in manufacturing operations.
By understanding customer demand, streamlining the supply chain, minimizing inventory, implementing a pull-based system, improving quality control, and adopting a continuous improvement mindset, manufacturers can achieve greater efficiency, reduce waste, and improve customer satisfaction.
Kanban Systems
Kanban systems are visual management tools used in lean manufacturing to track the production progress and inventory levels. By using a Kanban system, manufacturers can easily identify areas of excess inventory and adjust production schedules accordingly.
This approach can also be applied to scheduling, where Kanban systems can be used to track scheduling progress and identify areas of inefficiency or delay.
- Identifying the Bottlenecks: Kanban can help identify bottlenecks in the production process. Tracking the flow of materials and products through the system makes it easier to identify areas where work is piling up, or production is lagging. Once the bottlenecks are identified, it becomes easier to address them and make improvements.
- Setting Up Kanban Boards: Kanban boards are used to track the progress of work through the system. They are typically set up in a central location where all team members can see them. The boards are divided into columns representing different production process stages. Visual cues such as cards or colored sticky notes are used to represent the work that needs to be done.
- Determining Reorder Points: Reorder points are the levels at which materials or products need to be reordered. These levels are determined based on the production schedule and the rate at which materials or products are used. Setting up reorder points makes it easier to keep track of inventory levels and ensure that materials or products are always available when needed.
- Calculating Lead Times: Lead times are the time it takes to produce a product or deliver a material. Calculating lead times makes planning the production schedule easier and ensures that materials or products are delivered on time. Lead times can be calculated based on historical data or by tracking the time it takes to complete each stage of the production process.
Using visual cues to signal when work needs to be done makes it easier to maintain a consistent production flow and ensure that products are delivered on time. By continuously improving the system, achieving even greater efficiency and customer satisfaction is possible.
Total Productive Maintenance (TPM)
Total Productive Maintenance (TPM) is a lean manufacturing approach to equipment maintenance that aims to keep machines running at maximum efficiency.
By reducing downtime and increasing machine reliability, manufacturers can improve scheduling efficiency and reduce delays caused by machine breakdowns or maintenance.
The Eight Pillars of TPM
TPM is built on eight pillars that are aimed at promoting equipment and process reliability. These pillars include:
- Focused improvement
- Autonomous maintenance
- Planned maintenance
- Quality maintenance
- Training and Education
- Early equipment management
- Office TPM
- Safety, health, and environment
Benefits of TPM for scheduling
TPM can help improve scheduling efficiency by reducing equipment downtime and increasing reliability. By promoting a culture of continuous improvement, TPM can also help identify and address process inefficiencies and bottlenecks, which can lead to improved scheduling accuracy.
Implementation of TPM for scheduling
To implement TPM for scheduling, it is crucial to develop a detailed plan that includes the following steps:
- Develop a TPM implementation team
- Define the scope of the TPM program
- Conduct a TPM baseline assessment
- Develop a TPM master plan
- Implement TPM strategies
- Monitor and evaluate the TPM program
Developing a detailed plan that includes training and education, standardization, data collection, and continuous improvement is essential to implement TPM effectively.
Continuous Improvement
Continuous improvement is a key principle of lean manufacturing that focuses on improving processes and reducing waste. By constantly analyzing and improving scheduling processes, manufacturers can identify areas of inefficiency and waste and find ways to eliminate them. This approach can lead to continuous improvements in scheduling efficiency over time.
Continuous improvement is a never-ending process that requires ongoing commitment and effort. It can help you achieve more efficient scheduling, reduce waste, and increase customer satisfaction, ultimately leading to improved profitability and business success.
Manufacturers can improve scheduling efficiency and stay competitive in a fast-paced manufacturing environment by using tools like value stream mapping, JIT production, Kanban systems, TPM, and continuous improvement.
The Role of Data Analytics in Scheduling Optimization
Real-Time Data Collection
Data analytics plays a crucial role in scheduling optimization by providing real-time data collection and analysis. This allows manufacturers to track production progress and identify issues that may be affecting the schedule.
By monitoring key performance indicators (KPIs), such as cycle time, downtime, and quality, manufacturers can quickly identify problems and take corrective action. Real-time data collection also enables manufacturers to make informed decisions about scheduling changes, such as resequencing or adjusting resource allocations.
Predictive Analytics
Predictive analytics is another essential tool in scheduling optimization. Manufacturers can predict future performance and anticipate potential bottlenecks by analyzing historical data and identifying patterns. This enables them to adjust schedules to avoid delays and minimize lead times proactively.
Predictive analytics can also be used to optimize inventory levels, ensuring that the right materials are available when needed.
Machine Learning
Machine learning is a subset of artificial intelligence (AI) that enables computers to learn from data and make predictions. In scheduling optimization, machine learning can be used to identify the optimal schedule based on a variety of factors, including production capacity, lead times, and resource availability.
By analyzing large amounts of data, machine learning algorithms can identify patterns and make predictions about future performance. This enables manufacturers to make informed decisions about scheduling changes, such as adjusting production rates or reallocating resources.
Optimization Algorithms
Optimization algorithms are another key component of scheduling optimization. These algorithms use mathematical models to identify the optimal sequence of activities and resources required to achieve production targets while minimizing lead times, costs, and waste.
Optimization algorithms can be used to solve complex scheduling problems, such as resource constraints and sequencing issues. Manufacturers can improve production efficiency and reduce costs by identifying the optimal schedule.
Types of Optimization Algorithms
There are several types of optimization algorithms used in scheduling, including:
Linear programming:
Linear programming algorithms use linear equations to create optimal solutions to scheduling problems. They are useful for problems with a large number of variables and constraints.
- The objective of linear programming is to maximize or minimize a linear objective function subject to linear constraints.
- Linear programming is useful for problems that involve allocating scarce resources, such as labor, materials, and machines, in an optimal way.
- LP is commonly used in production scheduling, transportation planning, and inventory management.
- The LP model can be formulated as a set of linear equations and inequalities and solved using specialized software called an LP solver.
- LP can handle both continuous and discrete decision variables, making it a versatile tool for optimization problems.
- LP is particularly useful when multiple objectives or constraints must be satisfied simultaneously.
- LP can be used to solve complex scheduling problems involving multiple resources, time constraints, and other constraints.
Genetic algorithms:
Genetic algorithms are inspired by natural selection and use a process of selection, mutation, and reproduction to find optimal solutions to problems.
Here are some key points to understand genetic algorithms as an optimization algorithm for efficient scheduling:
- Genetic algorithms are based on the principles of natural selection and genetics. They generate a population of potential solutions and then evolve them through successive generations to find the optimal solution.
- In the context of scheduling, genetic algorithms can be used to optimize resource allocation, minimize lead times, and reduce costs. They are particularly useful in situations where multiple variables need to be considered and optimized simultaneously.
- Genetic algorithms start with an initial population of potential solutions, which are then evaluated based on a fitness function that measures how well they meet the criteria for an optimal solution. The fittest solutions are then selected for reproduction, and their genetic material is combined to create new solutions.
- The process of genetic reproduction involves crossover and mutation, which allow for the creation of new solutions that may be better suited to the problem at hand. These new solutions are then evaluated again, and the selection, reproduction, and evaluation process continues until the optimal solution is found.
- Genetic algorithms can be used to optimize a wide range of scheduling problems, including production scheduling, workforce scheduling, and logistics scheduling. They are particularly useful in situations where there are complex interdependencies between variables that need to be considered.
- One of the key advantages of genetic algorithms is their ability to find solutions that are not immediately obvious or intuitive. By exploring a wide range of potential solutions, genetic algorithms can sometimes identify novel approaches that might not be considered through more traditional problem-solving techniques.
Simulated annealing:
Simulated annealing algorithms simulate the process of annealing in metallurgy, where a metal is heated and slowly cooled to create a more stable structure. The algorithm uses a similar process to find the most stable solution to a scheduling problem.
- Simulated annealing works by gradually decreasing the temperature of a system while searching for the best solution to a problem. The algorithm randomly searches for solutions and accepts some worse solutions as it searches for the optimal one.
- The algorithm can be applied to a variety of scheduling problems, including production scheduling, project scheduling, and workforce scheduling.
- One of the advantages of simulated annealing is that it is a flexible algorithm that can be tailored to specific scheduling problems. It can also handle complex scheduling constraints and variables.
- Another advantage is that simulated annealing can search for a globally optimal solution rather than getting stuck in local optima like some other optimization algorithms.
- Simulated annealing does have some drawbacks, such as requiring a lot of computational power and a large number of iterations to find the optimal solution. It can also be difficult to implement and may require some expertise in optimization algorithms.
Ant colony optimization:
Ant colony optimization algorithms are based on the behavior of ant colonies and use a process of pheromone trails and random exploration to find optimal solutions to problems.
Benefits of ACO for Scheduling
ACO has several benefits that make it useful for production scheduling. First, ACO is capable of handling complex scheduling problems that traditional optimization techniques cannot solve. This is because ACO uses a stochastic search process that is capable of exploring a large search space.
Second, ACO is capable of handling dynamic scheduling problems, where the production environment changes over time. This is because ACO is capable of adapting to changes in the problem space, allowing it to find a new solution quickly.
Finally, ACO is capable of finding near-optimal solutions in a relatively short amount of time. This is because ACO is a parallel algorithm, which means that it can explore multiple solutions at the same time, speeding up the search process.
Implementing ACO for Scheduling Implementing
ACO for scheduling involves several steps:
- The problem must be modeled as a graph, with the nodes representing the tasks and the edges representing the precedence relationships between the tasks.
- The parameters for the algorithm, such as the pheromone update rate and the number of ants, must be selected.
- The algorithm must be run, and the results must be analyzed to determine the optimal schedule.
Limitations of ACO for Scheduling
While ACO has several benefits, it also has some limitations that must be considered when using it for scheduling:
- ACO is a stochastic algorithm, which means that it may not always converge on the optimal solution.
- ACO is computationally intensive, which means that it may not be practical for large scheduling problems.
- ACO requires a significant amount of domain expertise to implement effectively, which means that it may not be suitable for organizations that do not have the necessary expertise.
Optimization algorithms are a powerful tool for creating efficient schedules that can help organizations meet production demands, reduce costs, and minimize lead times. By selecting an appropriate algorithm and implementing it correctly, businesses can create schedules that are tailored to their specific requirements and constraints.
Visualization Tools
Visualization tools are an essential part of data analytics in scheduling optimization. These tools enable manufacturers to view data in a visual format, such as graphs or charts, making it easier to identify trends and patterns. Visualization tools can also identify improvement areas, such as bottlenecks or inefficiencies in the production process.
Visualization tools enable manufacturers to make informed decisions about scheduling changes by providing a clear picture of the production process. Here are some popular visualization tools for scheduling:
- Calendar Views: Calendar views are a simple yet effective visualization tool for scheduling. They visually represent tasks and events over time, allowing managers to see what's coming up, plan ahead, and avoid scheduling conflicts. Calendar views are particularly useful for managing recurring tasks or events.
- Heat Maps: Heat maps are a powerful visualization tool for identifying patterns and trends in data. They use color coding to highlight areas of high or low activity, making it easier to identify bottlenecks, inefficiencies, and areas for improvement. Heat maps are particularly useful for managing large datasets or tracking changes over time.
- Resource Allocation Graphs: Resource allocation graphs are a visualization tool for tracking resource utilization and availability. They visually represent how resources are being allocated and help managers identify areas where resources are being over or underutilized. Resource allocation graphs also help managers plan ahead and optimize resource allocation for maximum efficiency.
- Dashboards: Dashboards are a customizable visualization tool for scheduling that provide a single view of key metrics and KPIs. They allow managers to see how various aspects of the schedule are performing in real-time and make data-driven decisions to optimize scheduling for efficiency.
Data analytics plays a critical role in scheduling optimization by providing real-time data collection and analysis, predictive analytics, machine learning, optimization algorithms, and visualization tools, and enabling continuous improvement. Manufacturers can improve production efficiency, reduce costs, and stay competitive in a rapidly changing market by leveraging data analytics.
Choosing the Right Scheduling Software for Your Operations
Choosing the right scheduling software can be a daunting task, with numerous options available in the market. It is crucial to consider several factors when selecting the appropriate software for your organization.
Below are some factors to consider when choosing the right scheduling software for your operations:
- Features and Functionality: The scheduling software features and functionality should be tailored to your specific operational needs. Look for software that offers flexibility in scheduling, can handle complex scheduling scenarios, and has the ability to forecast future demand. Additionally, it should provide automated scheduling based on available resources, production capacity, and lead time.
- Ease of Use: The software should be user-friendly and intuitive. It should be easy to navigate and operate and should not require extensive training to get started. The user interface should be clean and organized, allowing easy customization of views and reports.
- Integration: The scheduling software should be able to integrate with your existing systems, such as ERP or MES, to avoid duplicating data entry and ensure data accuracy. The software should also be able to integrate with other systems such as barcoding, RFID, and machine data capture systems.
- Scalability: The software should be able to scale with your business needs. As your operations grow and change, the software should be able to accommodate these changes without requiring significant modifications or upgrades.
- Support and Maintenance: Consider the software vendor's level of support and maintenance. Make sure they offer technical support, training, and regular software updates to ensure the software remains up-to-date and continues to meet your operational needs.
- Cost: Cost is always a consideration when selecting software. Understanding the pricing structure and ensuring that the software provides a return on investment is essential. Look for software offering a range of pricing options, including flexible licensing models and a clear understanding of the costs associated with implementation and ongoing support.
- Security: The scheduling software should have robust security features to protect sensitive operational data. It should have access controls, data encryption, and regular security updates to protect data against unauthorized access.
- Pricing: Of course, pricing is always a factor when choosing any software. Look for software that fits your budget but provides the necessary features and functionality.
- Reviews and References: Finally, don't forget to read reviews and ask for references from other businesses that have used the software you're considering. This can help you better understand the software's strengths and weaknesses and how well it has worked for other businesses in your industry.
Consider factors such as scalability, integration, customization, user-friendliness, mobile access, analytics and reporting, customer support, security, pricing, and reviews and references when making your decision. With the right software in place, you can streamline your scheduling processes and take your business to the next level.
Techniques for Reducing Lead Times in Your Schedule
Lead time is the amount of time it takes to complete a process from start to finish, including any waiting time in between. Reducing lead times is vital for businesses to improve efficiency, productivity, and customer satisfaction.
- Lean Manufacturing: Lean manufacturing principles focus on eliminating waste and increasing efficiency in manufacturing processes. This can be achieved by identifying and eliminating non-value-added activities and processes, improving communication and collaboration, and implementing continuous improvement processes.
- Process Mapping: Process mapping involves visualizing the steps involved in a process and identifying areas for improvement. By mapping out the process, bottlenecks, and inefficiencies can be identified, and solutions can be implemented to reduce lead times.
- Capacity Planning: Capacity planning involves analyzing production capacity and adjusting production levels to meet demand. By planning production capacity in advance, businesses can ensure that they have the resources to meet demand, which can reduce lead times and improve customer satisfaction.
- Just-In-Time (JIT) Inventory: JIT inventory is a manufacturing strategy that involves producing products only when they are needed rather than producing large quantities in advance. By using JIT inventory, businesses can reduce inventory costs and improve efficiency, which can lead to shorter lead times.
- Quick Response Manufacturing (QRM): QRM is a manufacturing strategy that focuses on reducing lead times by increasing flexibility and responsiveness in the production process. This can be achieved by organizing production into small, cross-functional teams that can quickly respond to changes in demand.
- Kanban: Kanban is a visual scheduling system that can be used to manage production and reduce lead times. By using a Kanban system, businesses can monitor inventory levels and production status in real-time, which can help them make adjustments to production levels as needed.
- Electronic Data Interchange (EDI): EDI is a technology that enables businesses to exchange electronic documents with their suppliers and customers. By using EDI, companies can reduce lead times by automating the exchange of information, which can improve communication and reduce errors.
Reducing lead times is vital for businesses looking to improve efficiency and customer satisfaction. By implementing techniques such as lean manufacturing, process mapping, capacity planning, JIT inventory, QRM, Kanban, and EDI, businesses can reduce lead times and improve their competitiveness in the market.
It's essential to choose the best techniques for your specific business needs and goals and continuously monitor and evaluate your scheduling process to identify areas for improvement.
Minimizing the Impact of Unexpected Disruptions on Your Schedule
In the manufacturing industry, unexpected disruptions can cause significant delays and lost productivity. Such disruptions can occur due to various reasons, such as equipment breakdowns, supply chain interruptions, or unexpected changes in demand.
The key to minimizing the impact of such disruptions on your schedule is to have contingency plans in place and to be prepared to adjust your schedule quickly when needed.
Conduct a Risk Assessment
Before you can develop contingency plans to mitigate the impact of unexpected disruptions, you need to identify potential risks. Conduct a risk assessment to identify the most significant risks to your operations.
These risks can include equipment breakdowns, supply chain disruptions, labor shortages, and natural disasters. Once you have identified the most significant risks, you can develop contingency plans to address them.
Develop Contingency Plans
Contingency plans are essential for minimizing the impact of unexpected disruptions on your schedule. These plans should include steps to take in the event of a disruption, such as alternative sourcing strategies, backup equipment, and alternative production processes.
Developing contingency plans requires input from all stakeholders in your operations, including suppliers, employees, and customers.
Implement Real-Time Monitoring
Real-time monitoring of your operations can help you identify disruptions as soon as they occur. This allows you to take action quickly to mitigate their impact on your schedule.
Real-time monitoring can be done through sensors and other automated monitoring systems that track production processes and equipment performance. This data can be analyzed to identify potential issues before they cause significant disruptions.
Use Predictive Analytics
Predictive analytics can help you anticipate and mitigate the impact of unexpected disruptions on your schedule. These analytics use historical data and real-time monitoring data to identify patterns that can predict future disruptions.
Predictive analytics can be used to identify potential equipment failures, supply chain disruptions, and labor shortages. This information can be used to develop contingency plans and proactively adjust your schedule.
Develop Strong Relationships with Suppliers
Strong relationships with your suppliers can help you mitigate the impact of unexpected disruptions on your schedule. You can quickly develop contingency plans to address supply chain disruptions by working closely with your suppliers. You can also work with your suppliers to identify potential risks and develop strategies to mitigate them.
Maintain a Flexible Schedule
Maintaining a flexible schedule is essential for minimizing the impact of unexpected disruptions on your operations. A flexible schedule allows you to adjust production processes quickly in response to disruptions.
This flexibility can be achieved by developing modular production processes that can be adjusted quickly, using multi-skilled employees who can work in different areas of your operations, and developing backup plans for equipment and production processes.
By implementing these techniques, you can reduce the risk of disruptions and ensure that your operations run smoothly, even in the face of unexpected challenges.
Incorporating Machine Maintenance Into Your Production Schedule
Here are some techniques to consider when incorporating machine maintenance into your production schedule:
Develop a preventative maintenance plan: Creating a preventative maintenance plan involves scheduling regular maintenance checks, inspections, and repairs based on the specific needs of your equipment. This plan should take into account the manufacturer's recommendations, operating conditions, and the age of the machine.
Prioritize maintenance tasks: Prioritizing maintenance tasks can help you determine which machines require immediate attention and which can be scheduled for maintenance at a later time. This approach can help prevent unexpected machine failure, reduce downtime, and optimize the use of maintenance resources.
Schedule maintenance during downtime: Scheduling maintenance during downtime, such as during off-hours or when production is low, can help minimize the impact on your production schedule. This approach can also allow for more thorough maintenance and repairs without disrupting regular operations.
Implement predictive maintenance: Predictive maintenance uses real-time data and analytics to monitor machine performance and identify potential problems before they occur. This approach can help you anticipate and address issues before they cause unplanned downtime or other disruptions to your production schedule.
Track maintenance history and performance: Keeping track of maintenance history and machine performance can help you identify patterns, identify potential areas for improvement, and develop more effective maintenance plans.
Train personnel on maintenance procedures: Properly trained personnel can perform routine maintenance tasks, identify potential issues, and provide valuable feedback on the performance of equipment. Investing in training programs can improve the effectiveness of your maintenance program and reduce downtime caused by human error.
Incorporating machine maintenance into your production schedule can be a challenging task, but with proper planning, prioritization, and execution, it can lead to significant improvements in equipment reliability, productivity, and cost savings.
Collaborating With Suppliers for Improved Scheduling Accuracy
Collaborating with suppliers is essential to ensuring that a company's production schedule runs smoothly. The accuracy of the schedule relies heavily on the timeliness and quality of the raw materials and other resources provided by suppliers. In order to optimize scheduling accuracy, it is essential to work closely with suppliers and build strong relationships.
Here are some techniques for collaborating with suppliers for improved scheduling accuracy:
Communicate regularly with suppliers: Maintaining open lines of communication with suppliers is crucial for scheduling accuracy. This means sharing production schedules, forecasted demands, and any changes in demand as soon as possible. In turn, suppliers should also provide updates on inventory levels, lead times, and other factors that may impact production schedules.
Establish clear performance metrics: Suppliers should be held to clear performance metrics to ensure accountability and transparency.
Key performance indicators such as on-time delivery rates, quality of materials, and lead times should be established and tracked regularly. This provides an objective measure of supplier performance and helps identify areas for improvement.
Build partnerships with key suppliers: Strategic partnerships with key suppliers can help reduce lead times and improve quality. This may involve sharing information on forecasts and schedules, collaborating on design and development, or even co-locating facilities to increase efficiency.
Utilize supplier-managed inventory: In some cases, suppliers can manage inventory levels, which can help reduce lead times and improve scheduling accuracy. This involves sharing real-time data on inventory levels and demand forecasts, allowing suppliers to adjust their production schedules accordingly.
Incorporate suppliers into scheduling software: Collaborating with suppliers is much easier when everyone is working from the same platform. By incorporating suppliers into scheduling software, companies can share real-time schedules and demand forecasts, reducing the risk of miscommunication and delays.
Provide incentives for performance: Incentivizing suppliers for high performance can help improve scheduling accuracy. This may involve bonuses for on-time delivery or long-term contracts for reliable suppliers. Suppliers are more likely to prioritize meeting production demands by aligning incentives with scheduling accuracy.
Building strong relationships with key suppliers, utilizing performance metrics, and incorporating suppliers into scheduling software are just a few of the techniques that can help optimize collaboration and improve scheduling accuracy.
Effective Communication Strategies for Production Scheduling
Define roles and responsibilities clearly: To ensure everyone is on the same page, clearly defining each team member's roles and responsibilities is essential. This includes specifying who is responsible for each task, who needs to be informed about each task's progress, and who needs to approve each task's completion.
Use a common language: To avoid confusion, it is essential to use a common language among all team members. Using technical terms, abbreviations, or jargon can lead to misunderstandings and mistakes. Using a common language will help ensure that everyone understands the tasks and requirements clearly.
Use visual aids: Visual aids like Gantt charts and flowcharts can help team members understand the schedule better. These tools can help identify critical path tasks, bottlenecks, and dependencies, making communicating scheduling changes and updates easier.
Provide regular updates: Providing regular updates to team members is crucial to keep everyone informed about schedule changes and progress. Regular updates help prevent misunderstandings, missed deadlines, and other issues that could affect production.
Use a centralized communication system: A centralized communication system is essential for effective communication between team members. A centralized system can ensure all team members receive the same information and help prevent missed messages or miscommunications.
Foster a culture of communication: Finally, fostering a culture of communication is essential for effective production scheduling. Encourage team members to ask questions, raise concerns, and provide feedback. This culture of communication can help prevent misunderstandings and ensure everyone is working towards the same goals.
The Benefits of a Visual Scheduling System
Scheduling is essential to any business, and keeping track of all the details can be challenging. A visual scheduling system is an effective way to help companies to streamline their scheduling process by presenting the schedule in a visual and intuitive format.
Improved Communication
A visual scheduling system provides a clear and concise way to communicate the schedule to all team members. By presenting the schedule in a visual format, it is easier to understand and follow. This ensures that everyone is on the same page and can work together to achieve the goals of the project.
Better Decision Making
A visual scheduling system allows you to quickly and easily see the status of all the tasks involved in the project. This information helps to make better decisions on allocating resources, adjusting the schedule, and identifying any potential roadblocks that may impact the timeline.
Increased Efficiency
A visual scheduling system provides a way to quickly identify potential bottlenecks or conflicts in the schedule. This allows you to make adjustments in real time and avoid delays in the production process. Streamlining the scheduling process can reduce the time and effort required to manage the schedule.
Enhanced Collaboration
A visual scheduling system encourages collaboration between team members by providing a centralized location to view the schedule. This helps to facilitate communication and coordination between team members, allowing for better decision-making and a more efficient workflow.
Improved Customer Satisfaction
Using a visual scheduling system can improve customer satisfaction by providing accurate delivery dates and reducing the risk of delays. By having a clear view of the schedule and being able to make adjustments in real time, businesses can better manage customer expectations and ensure that projects are completed on time.
Continuous Improvement in Your Scheduling Process
Regularly Review and Analyze Data
One of the most important things you can do to improve your scheduling process continuously is regularly reviewing and analyzing data. This includes data on cycle times, lead times, throughput, and other key performance indicators (KPIs). Reviewing this data regularly allows you to identify trends, bottlenecks, and areas where improvements can be made.
Identify and Eliminate Waste
Waste can take many forms in the scheduling process, including excessive waiting times, overproduction, unnecessary movement, and defects. Identifying and eliminating waste can streamline the scheduling process and improve efficiency.
The most effective way to identify waste is to conduct a value stream mapping exercise, which involves mapping out the entire scheduling process and identifying areas where waste occurs.
Implement Standard Work Procedures
Standard work procedures are essential for ensuring consistency and reducing errors in the scheduling process. By implementing standard work procedures, you can improve quality and reduce the risk of errors or delays. These procedures should be well-documented and regularly reviewed to ensure they are up-to-date and effective.
Use Continuous Flow Scheduling
Continuous flow scheduling is a scheduling approach that prioritizes the smooth and continuous flow of work through the production process. This approach can reduce lead times, improve efficiency, and minimize the risk of delays or bottlenecks. Continuous flow scheduling is particularly effective for high-volume, low-variety production environments.
Invest in Automation and Technology
Investing in automation and technology can streamline the scheduling process and reduce the risk of errors or delays. Automation can be used to automate repetitive tasks, such as data entry or scheduling updates, freeing up staff time for more strategic tasks.
Technology can also be used to improve communication and collaboration between different parts of the organization, suppliers, and customers.
Engage Employees in Continuous Improvement
Finally, it's essential to engage employees in the continuous improvement process. Employees are often the best source of ideas for improving the scheduling process, as they are the ones who are most familiar with the day-to-day operations.
By encouraging employee involvement and providing training and support, you can create a culture of continuous improvement and drive positive change in the scheduling process.
How can Deskera Help You?
Deskera MRP allows you to closely monitor the manufacturing process. From the bill of materials to the production planning features, the solution helps you stay on top of your game and keep your company's competitive edge.
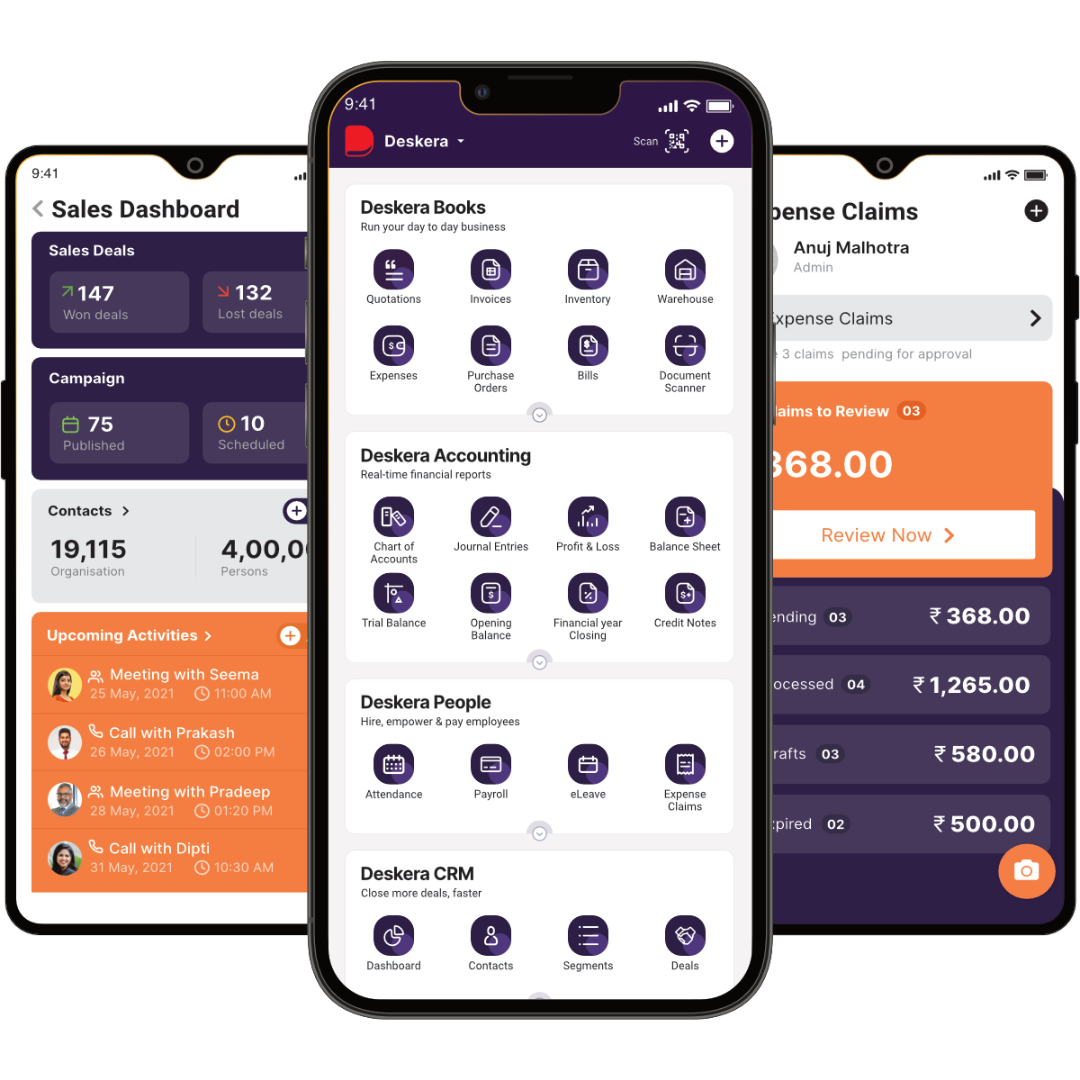
Deskera ERP and MRP system can help you:
- Manage production plans
- Maintain Bill of Materials
- Generate detailed reports
- Create a custom dashboard
Deskera ERP is a comprehensive system that allows you to maintain inventory, manage suppliers, and track supply chain activity in real-time, as well as streamline a variety of other corporate operations.
Deskera Books enables you to manage your accounts and finances more effectively. Maintain sound accounting practices by automating accounting operations such as billing, invoicing, and payment processing.
Deskera CRM is a strong solution that manages your sales and assists you in closing agreements quickly. It not only allows you to do critical duties such as lead generation via email, but it also provides you with a comprehensive view of your sales funnel.
Deskera People is a simple tool for taking control of your human resource management functions. The technology not only speeds up payroll processing but also allows you to manage all other activities such as overtime, benefits, bonuses, training programs, and much more. This is your chance to grow your business, increase earnings, and improve the efficiency of the entire production process.
Conclusion
Streamlining your manufacturing production schedule is crucial for maximizing efficiency, reducing costs, and meeting customer demands. Effective production scheduling requires careful planning, monitoring, and adjustment.
By implementing best practices and utilizing advanced scheduling tools, manufacturers can create a flexible and dynamic production schedule that can adapt to changes in demand, capacity, and resource availability. This allows them to minimize lead times, optimize resource utilization, and improve overall production performance.
Some of the best practices for effective production scheduling include analyzing historical data, identifying bottlenecks, prioritizing critical tasks, setting realistic deadlines, involving stakeholders, and continuously monitoring and adjusting the schedule.
Additionally, advanced scheduling tools like APS systems, MES software, and IoT sensors can provide real-time visibility into production processes, facilitate communication and collaboration, and automate many scheduling tasks. However, manufacturers should carefully evaluate their specific needs and requirements before selecting a scheduling tool, as not all tools are suitable for all operations.
Overall, by leveraging effective scheduling techniques and tools, manufacturers can gain a competitive advantage and achieve sustainable growth in the dynamic manufacturing industry.
Key Takeaways
- A streamlined production schedule is critical for maximizing manufacturing efficiency and profitability.
- Automation tools can be used to simplify the scheduling process and optimize production runs.
- Accurate data collection is essential for creating a realistic production schedule and identifying bottlenecks and inefficiencies.
- Flexibility is key to creating an effective production schedule that can adapt to changing demand, equipment availability, and production needs.
- Creating a standardized scheduling process can ensure consistency and accuracy across multiple production lines and facilities.
- Regular monitoring and analysis of production data can help identify opportunities for optimization and continuous improvement.
- Implementing a lean manufacturing approach can help eliminate waste and improve the efficiency of the production process.
- The use of advanced analytics and machine learning algorithms can help predict demand, optimize inventory levels, and improve scheduling accuracy.
- Collaboration and communication between production managers, planners, and operators are critical for ensuring the success of the scheduling process.
- The use of real-time monitoring and feedback systems can help identify and address production issues as they arise, improving efficiency and reducing downtime.
Related Articles
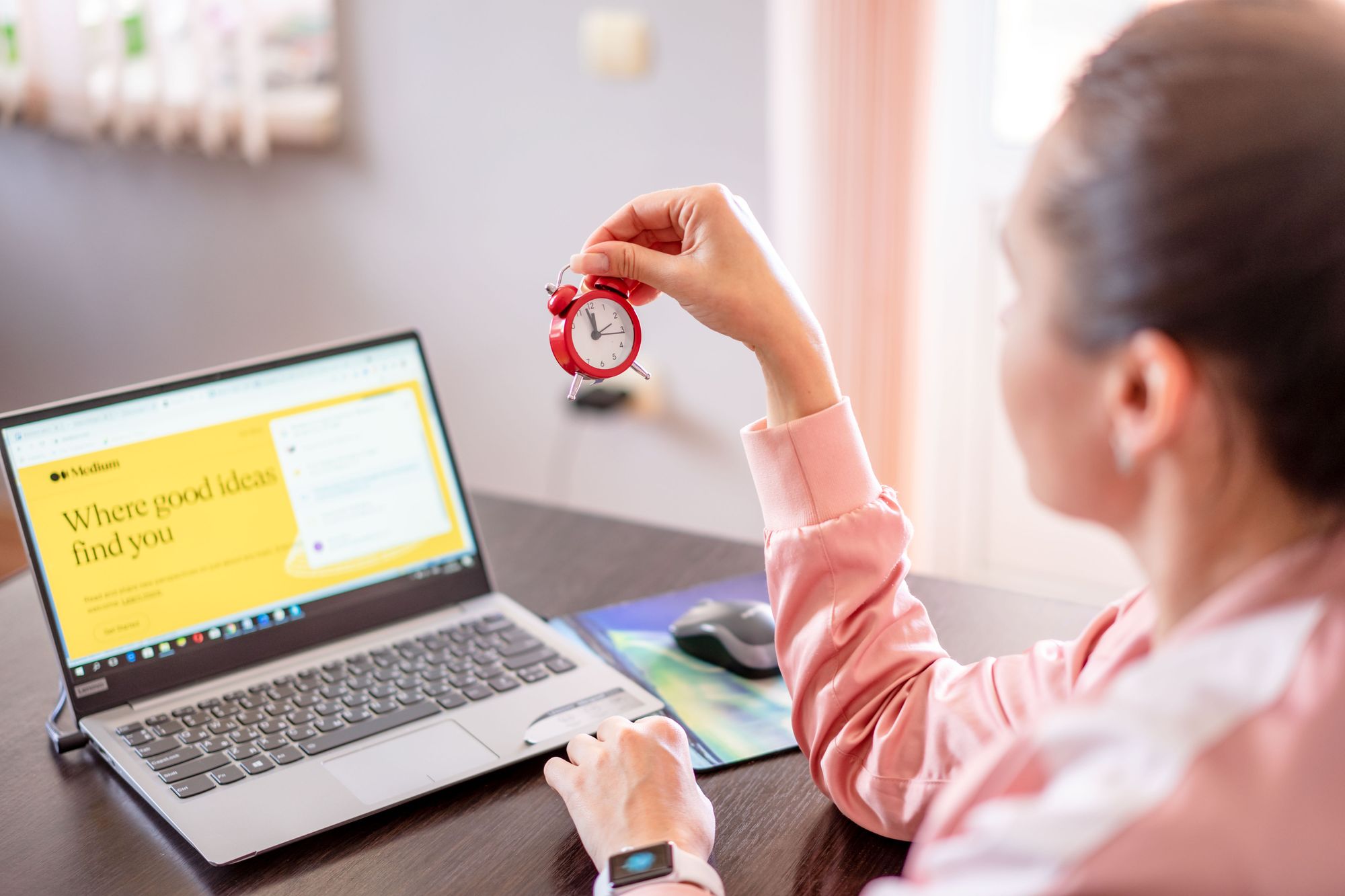
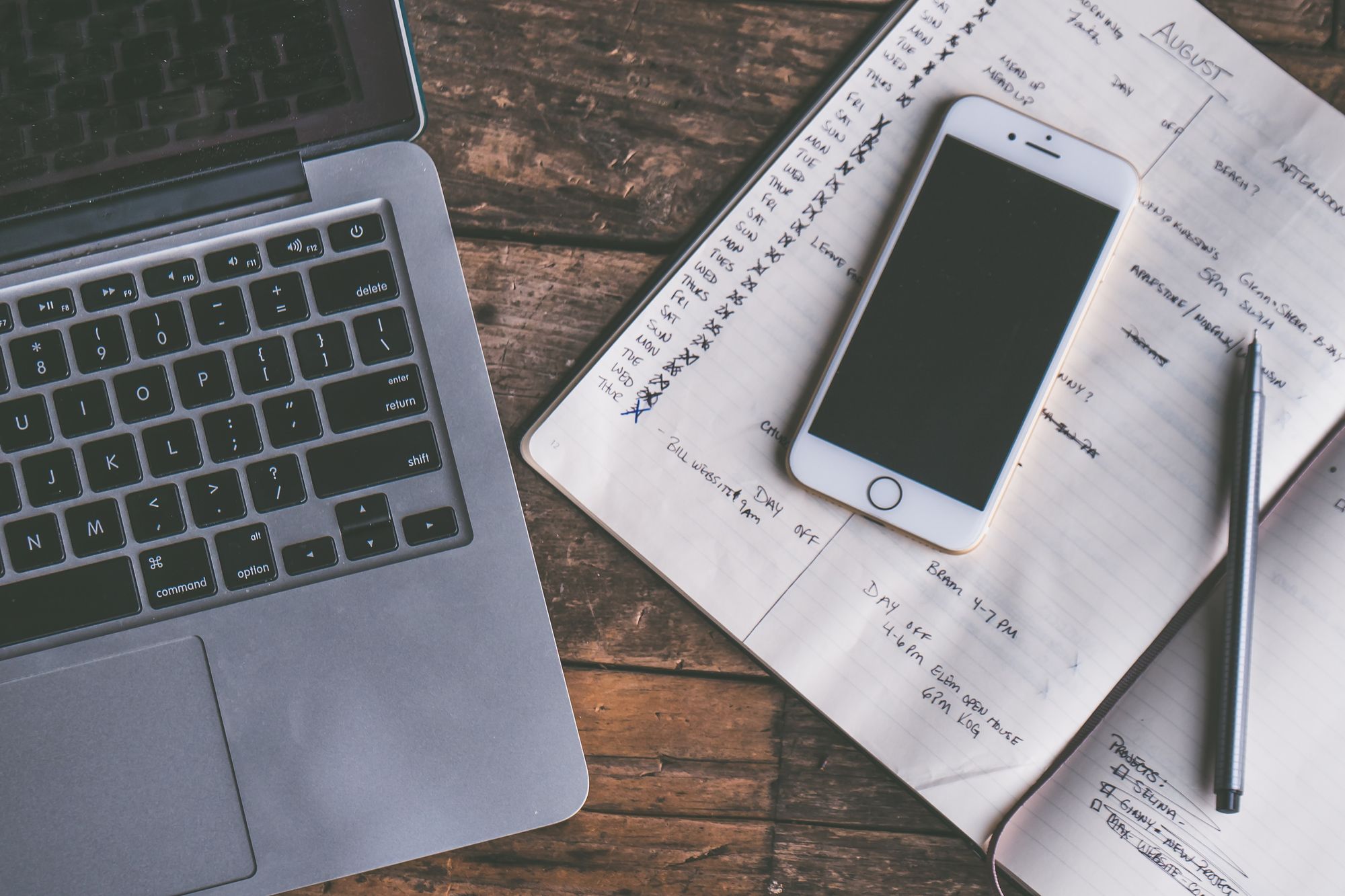
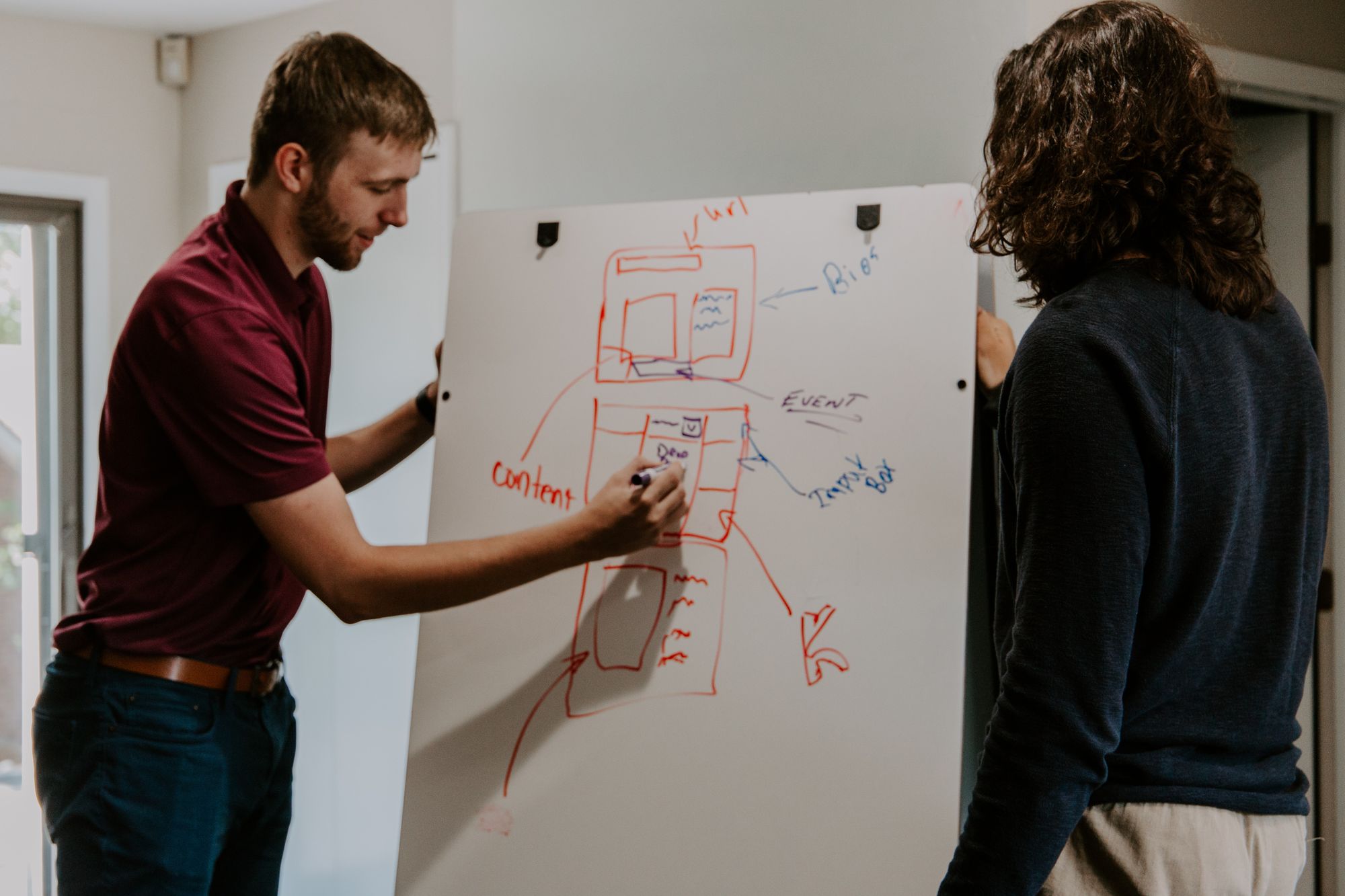
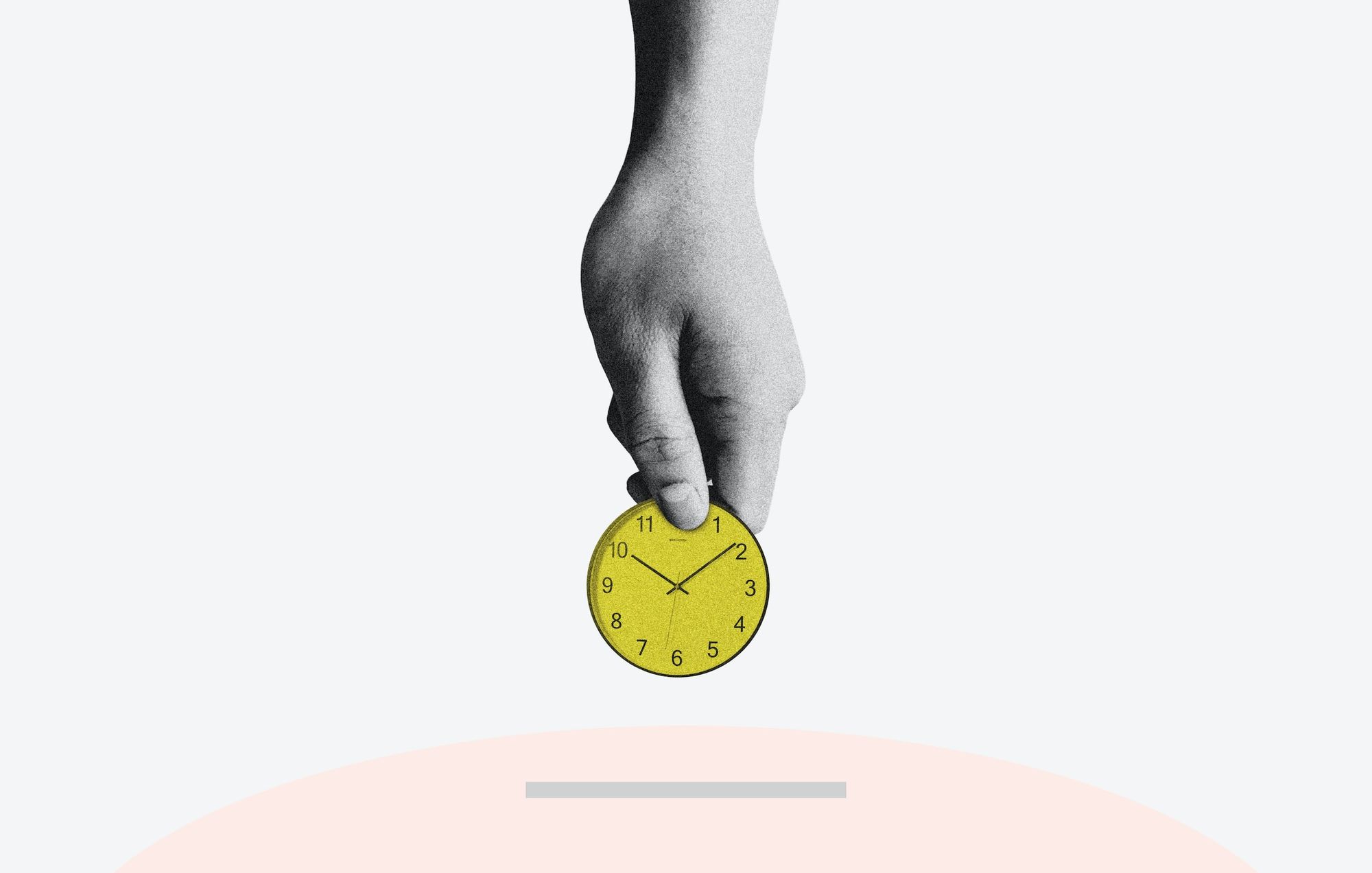