In the highly competitive manufacturing industry, optimizing production efficiency and maximizing output is crucial for staying ahead in the market. One key aspect that directly impacts production success is effective work order handling. A work order is a critical document that outlines the necessary instructions, resources, and timelines for completing a specific task or project.
This article delves into the significance of effective work order handling and presents a structured approach to ensure seamless operations and enhanced manufacturing output.
Let’s take a look at the table of content:
- Definition of Work Order in Manufacturing
- Importance of Work Orders in the Manufacturing Process
- Common Types of Work Orders in Manufacturing
- Challenges in Work Order Handling
- The Impact of Effective Work Order Handling on Manufacturing Output
- Best Practices for Effective Work Order Handling
- Streamlining Work Order Execution
- Collaboration and Communication Across Departments
- Embracing Technology for Work Order Handling
- Work Order Performance Metrics and Evaluation
- Frequently Asked Questions (FAQs) Associated with Work Order Handling
- Wrapping Up
Definition of Work Order in Manufacturing
A work order in manufacturing is a detailed document or instruction that outlines a specific task, project, or job that needs to be completed within the production process. It serves as a comprehensive guide for workers, technicians, and supervisors, providing them with the necessary information to carry out the assigned tasks efficiently and effectively.
Work orders typically include essential details such as the scope of work, materials required, resources allocated, timelines, and any specific instructions or safety guidelines. These documents are essential for organizing and coordinating various activities, ensuring that production proceeds smoothly and meets quality standards.
Importance of Work Orders in the Manufacturing Process
Work orders play a crucial role in the manufacturing process for several reasons:
a. Clarity and Direction: Work orders provide clear and specific instructions to employees, minimizing confusion and potential errors. Workers can refer to the work order to understand what needs to be done, how it should be done, and the expected outcomes.
b. Resource Allocation: Work orders specify the resources required for each task, including raw materials, tools, equipment, and labor. Proper resource allocation helps prevent waste and ensures that all necessary elements are available at the right time, enhancing operational efficiency.
c. Time Management: Manufacturing processes often involve multiple tasks that need to be completed in a particular sequence. Work orders provide timelines and deadlines for each task, allowing supervisors to monitor progress and avoid delays.
d. Quality Control: Work orders may include quality control checkpoints and guidelines to maintain product quality throughout the production process. This helps in identifying defects or issues early on, reducing the likelihood of faulty products reaching the market.
e. Compliance and Safety: Work orders often incorporate safety instructions and compliance requirements, ensuring that workers follow industry regulations and best practices, minimizing workplace accidents and hazards.
f. Documentation and Traceability: Work orders serve as essential documentation, providing a record of completed tasks and activities. This documentation is valuable for audits, tracking performance, and identifying areas for improvement.
g. Streamlined Production Process: With work orders in place, the manufacturing process becomes more organized and systematic. Workers can easily refer to the work order to know what needs to be done next, reducing confusion and improving overall efficiency.
h. Improved Planning and Scheduling: Work orders help in better planning and scheduling of production activities. They allow managers to allocate resources and plan production sequences in advance, avoiding bottlenecks and ensuring a smooth flow of work.
i. Real-Time Tracking: Work orders provide a mechanism for real-time tracking of production progress. Managers can monitor the status of each work order, identify any delays or issues, and take corrective actions to keep production on track.
j. Regulatory Compliance: In industries with strict regulatory requirements, work orders are essential for ensuring compliance with safety, environmental, and other regulations.
k. Cost Control: By providing detailed information about the resources required, work orders help in better cost control. Manufacturers can accurately track the costs associated with each job, identify cost overruns, and implement cost-saving measures.
Common Types of Work Orders in Manufacturing
There are several types of work orders used in manufacturing, each serving a specific purpose:
a. Production Orders: This is the most fundamental type of work order in manufacturing. It is used to initiate and track the production of a specific quantity of a product. They detail the production of a specific quantity of a product, including the necessary raw materials, assembly steps, and production schedule.
b. Maintenance Orders: Maintenance work orders are used to schedule and track maintenance tasks for equipment, machinery, or facilities. They include details on the maintenance required, such as repairs, inspections, preventive maintenance, or upgrades. Maintenance work orders help ensure that machinery and equipment are well-maintained, reducing downtime and prolonging their lifespan.
c. Quality Control Orders: Quality control orders are utilized to inspect and verify the quality of products at various stages of production. These orders may include testing procedures, acceptance criteria, and documentation of test results.
d. Service Orders: Service work orders are used in manufacturing companies that offer after-sales service or repair services for their products. These work orders are issued when customers request service, and they include details about the customer, the product requiring service, the service required, and any associated costs.
e. Engineering Change Orders (ECOs): ECOs are used to implement design changes or improvements to products or processes. They communicate modifications to relevant teams and ensure the smooth integration of changes into the production process.
f. Repair Work Order: Repair work orders are similar to maintenance work orders but are specifically used for addressing equipment or product defects. When a defective product is identified, a repair work order is generated to outline the steps needed to rectify the issue and ensure the product meets quality standards.
g. Assembly Work Order: Assembly work orders are used in industries that produce complex products composed of multiple components or sub-assemblies. The work order specifies the assembly process and the components required for each step, guiding workers in the assembly process.
h. Material Requisition Work Order: Material requisition work orders are used to request the procurement of materials required for production. They specify the quantity and type of materials needed, helping procurement teams ensure that the necessary materials are available when needed.
i. Disassembly Work Order: Disassembly work orders are used when products need to be taken apart or dismantled. This can occur for repair, recycling, or refurbishment purposes. The work order specifies the steps to disassemble the product and may include instructions for the salvage or disposal of components.
j. Prototype Work Order: Prototype work orders are used when developing new products or processes. They guide the production of prototypes for testing and evaluation before full-scale production begins.
Each type of work order plays a crucial role in optimizing manufacturing operations, ensuring product quality, and meeting customer demand efficiently.
Challenges in Work Order Handling
Following, we’ve discussed challenges in work order handling. Let’s discuss:
1. Lack of Clarity and Specificity in Work Order Instructions:
One of the major challenges in work order handling is the lack of clarity and specificity in the instructions provided. When work orders are ambiguous or inadequately detailed, it leads to confusion among workers about the exact tasks they need to perform. This lack of clarity can result in errors, rework, and production delays.
To address this challenge, it is crucial to ensure that work orders are comprehensive and unambiguous. The following steps can help improve clarity in work order instructions:
a. Detailed Task Descriptions: Clearly outline the steps and procedures involved in each task, leaving no room for interpretation.
b. Specify Required Materials and Resources: Provide a list of necessary materials, tools, and equipment for each task to avoid delays caused by missing resources.
c. Set Quality Standards: Define the expected quality standards and acceptance criteria for the completed work to maintain consistency and uniformity in the final products.
d. Use Visual Aids: Incorporate diagrams, images, or videos to supplement textual instructions, making it easier for workers to understand complex processes.
e. Seek Feedback: Encourage feedback from workers who execute the tasks regularly. Their insights can help refine work order instructions for improved clarity.
2. Poor Communication Between Different Departments:
In a manufacturing environment, multiple departments need to collaborate seamlessly to execute work orders successfully. When communication channels are inadequate or fragmented, it can lead to miscommunication, delays, and inefficiencies.
To overcome this challenge, effective communication strategies must be implemented:
a. Cross-Functional Meetings: Regular meetings involving representatives from different departments can facilitate better understanding and coordination.
b. Digital Communication Tools: Utilize collaboration platforms, instant messaging, or project management software to foster real-time communication and information sharing.
c. Shared Documentation: Maintain a centralized database or system where all relevant work order information and updates can be accessed by authorized personnel from different departments.
d. Clear Points of Contact: Designate specific individuals as points of contact for each work order to ensure that information flows smoothly and responsibilities are clear.
3. Inefficient Scheduling and Resource Allocation:
Inefficient scheduling and resource allocation can lead to underutilization or overutilization of resources, resulting in production bottlenecks and increased costs.
To address this challenge and optimize scheduling and resource allocation:
a. Capacity Planning: Analyze production capacity and demand forecasts to allocate resources effectively and avoid overloading certain workstations.
b. Real-Time Monitoring: Implement systems to monitor resource usage and production progress in real-time, enabling quick adjustments to schedules and resources as needed.
c. Flexibility in Scheduling: Build in flexibility to adapt to unforeseen changes or urgent orders without disrupting the overall production schedule.
d. Consider Workforce Skills: Assign tasks to workers based on their skills and expertise to ensure efficient execution.
4. Delayed Work Order Processing and Execution:
Delays in work order processing and execution can have cascading effects on the entire production process, leading to missed deadlines and dissatisfied customers.
To minimize delays and streamline work order processing:
a. Prioritize Work Orders: Implement a clear prioritization system based on urgency, customer demands, and dependencies to focus on critical tasks first.
b. Workflow Automation: Utilize automation tools to streamline administrative tasks, reducing the time needed to initiate and process work orders.
c. Optimize Workflows: Continuously review and refine work processes to identify bottlenecks and optimize the flow of work orders through the system.
d. Monitor and Address Delays: Regularly track the progress of work orders and intervene promptly if delays are detected, identifying and addressing the root causes.
By addressing these challenges, manufacturers can significantly improve work order handling, enhance production efficiency, and meet customer demands more effectively.
The Impact of Effective Work Order Handling on Manufacturing Output
Following, we've discussed the impact of effective work order handling on manufacturing output. Let's learn:
Improved Production Planning and Coordination:
Effective work order handling contributes to improved production planning and coordination by providing clear instructions and timelines for each task. When work orders are well-defined and detailed, production managers can easily identify the sequence of operations, allocate resources efficiently, and schedule tasks appropriately. This leads to a more streamlined production process with reduced chances of bottlenecks and delays.
Key factors impacting production planning and coordination:
a. Sequencing Tasks: Work orders help establish the order in which tasks should be performed, ensuring a smooth flow of work and minimizing interruptions.
b. Resource Allocation: With clear instructions in work orders, managers can allocate resources (materials, equipment, and labor) based on the requirements of each task, optimizing their utilization.
c. Time Management: Work orders include timelines and deadlines for tasks, enabling production managers to schedule activities efficiently and meet delivery commitments.
d. Cross-Functional Coordination: Effective work orders encourage collaboration and communication among different departments involved in the production process, fostering a more cohesive and synchronized operation.
Enhanced Resource Utilization and Reduction in Wastage:
By providing detailed information about the required resources and quantities, work orders enable manufacturers to optimize resource utilization and minimize wastage. When workers have precise instructions, they can use materials efficiently and avoid unnecessary overconsumption or errors that result in scrap or rework.
Factors contributing to enhanced resource utilization and reduced wastage:
a. Material Optimization: Work orders specify the exact quantity and type of materials needed for each task, reducing excess inventory and material waste.
b. Equipment Efficiency: Clear instructions in work orders allow operators to use machinery more effectively, reducing downtime and improving overall equipment effectiveness (OEE).
c. Labor Efficiency: Workers can perform tasks more efficiently when they have detailed instructions, leading to reduced labor waste and higher productivity.
d. Waste Minimization: Work orders may include quality control measures that help identify defects early, minimizing the production of faulty products.
Minimized Downtime and Increased Equipment Availability:
Effective work order handling contributes to minimized downtime by ensuring that equipment is well-maintained, properly scheduled for servicing, and utilized optimally. When work orders include preventive maintenance schedules and equipment checklists, breakdowns and unexpected downtime can be minimized.
Factors influencing downtime reduction and equipment availability:
a. Preventive Maintenance: Work orders for regular maintenance and inspections help identify and address equipment issues before they lead to breakdowns.
b. Planned Equipment Servicing: By scheduling equipment servicing during non-production hours or planned downtime, overall equipment availability increases.
c. Quick Response to Issues: When work orders are processed promptly and executed efficiently, equipment breakdowns can be addressed swiftly, reducing downtime.
d. Data-Driven Maintenance: Work orders may incorporate data from predictive maintenance systems, enabling timely maintenance actions based on equipment performance data.
Optimized Labor Productivity and Reduced Lead Times:
Well-defined work orders enable workers to perform tasks with clarity and precision, leading to increased labor productivity. As workers understand their responsibilities and can work without ambiguity, the overall lead times for completing tasks and projects are reduced.
Factors influencing labor productivity and reduced lead times:
a. Clear Instructions: Work orders provide workers with detailed instructions, minimizing the time spent seeking clarification or correcting errors.
b. Task Prioritization: Effective work order handling ensures that tasks are prioritized appropriately, helping workers focus on critical activities first.
c. Continuous Improvement: By monitoring work order performance and identifying areas for improvement, manufacturers can optimize processes to reduce lead times.
d. Efficient Workflows: Streamlined work orders and processes reduce unnecessary delays, allowing workers to complete tasks more efficiently.
In conclusion, effective work order handling has a significant impact on manufacturing output. It leads to improved production planning, resource utilization, and coordination, resulting in minimized downtime, enhanced equipment availability, optimized labor productivity, and reduced lead times. Manufacturers who prioritize efficient work order handling can achieve higher levels of production efficiency, meet customer demands more effectively, and gain a competitive advantage in the market.
Work Order Scheduling and Resource Allocation
Work order scheduling and resource allocation are crucial components of efficient manufacturing operations. Proper scheduling ensures that work orders are executed in a timely manner, and resource allocation ensures that the necessary resources, such as labor, materials, and equipment, are available to complete the tasks.
Importance of Work Order Scheduling
Work order scheduling involves determining the start and end times for each task and establishing the sequence in which work orders will be executed. Proper scheduling is essential for several reasons:
a. Meeting Deadlines: Effective scheduling ensures that work orders are completed within the specified deadlines, preventing delays and customer dissatisfaction.
b. Minimizing Idle Time: By scheduling work orders in a logical sequence, manufacturers can reduce idle time between tasks, maximizing resource utilization.
c. Reducing Production Lead Times: Optimal scheduling helps reduce production lead times, allowing manufacturers to fulfill customer orders more quickly.
d. Improving Workflow: Proper scheduling creates a smooth workflow, minimizing bottlenecks and interruptions in production processes.
e. Enhancing Productivity: Well-planned scheduling improves overall productivity, as tasks are completed efficiently and on time.
Strategies for Work Order Scheduling
To optimize work order scheduling in manufacturing, manufacturers can implement the following strategies:
a. Sequencing by Priority: Prioritize work orders based on their urgency and deadlines. High-priority orders should be scheduled first to ensure they are completed on time.
b. Resource Availability: Consider the availability of resources, including labor, materials, and equipment, when scheduling work orders. Assign tasks to available resources to prevent delays.
c. Workstation Capacity: Take into account the capacity of workstations and equipment when scheduling tasks. Avoid overloading workstations to maintain smooth production flow.
d. Workflow Optimization: Arrange work orders in a sequence that minimizes movement between workstations and reduces material handling time.
e. Buffer Time: Allocate buffer time between work orders to account for unexpected delays or issues that may arise during production.
f. Real-Time Monitoring: Use real-time data monitoring and tracking to adjust scheduling as needed based on changing production conditions.
Importance of Resource Allocation
Resource allocation involves assigning the necessary resources to each work order to complete the tasks efficiently. Effective resource allocation is essential for the following reasons:
a. Maximizing Efficiency: Proper resource allocation ensures that the right resources are available at the right time, minimizing downtime and optimizing productivity.
b. Cost Control: Allocating resources efficiently helps control costs by avoiding unnecessary inventory holding or overstaffing.
c. Meeting Production Demands: Adequate resource allocation ensures that production demands are met, and work orders are completed on schedule.
d. Preventing Bottlenecks: Optimized resource allocation helps prevent bottlenecks and production delays by distributing resources evenly across work orders.
Strategies for Resource Allocation
To optimize resource allocation in manufacturing, manufacturers can adopt the following strategies:
a. Capacity Planning: Perform capacity planning to understand the available resources and their capabilities. Use this information to allocate resources effectively to different work orders.
b. Skill Matching: Assign skilled workers to tasks that require specific expertise to ensure efficient execution.
c. Material Availability: Ensure that the necessary materials are available and allocated to each work order to prevent delays.
d. Equipment Utilization: Schedule equipment usage efficiently to maximize its utilization and avoid conflicts in resource availability.
e. Real-Time Monitoring: Use real-time data to monitor resource utilization and make adjustments to allocation as needed.
Best Practices for Effective Work Order Handling
Following, we've discussed the best practices for effective work order handling. Let's learn:
1. Clear and Detailed Work Order Creation
Creating clear and detailed work orders is the foundation of effective work order handling. A well-crafted work order should leave no room for ambiguity and provide comprehensive instructions for the task at hand. Here are key elements to consider when creating work orders:
a. Task Description: Clearly describe the task or project that needs to be completed, including the specific steps and procedures involved.
b. Materials and Resources: List all the required materials, tools, equipment, and personnel needed for the task.
c. Timelines and Deadlines: Set realistic timelines and deadlines for completing the task, considering factors such as production schedules and customer demands.
d. Quality Standards: Define the expected quality standards and acceptance criteria for the completed work to maintain consistency and meet customer expectations.
e. Safety Guidelines: Incorporate safety instructions and precautions to ensure a safe working environment for employees.
f. Contact Information: Provide contact details for key personnel or supervisors in case of questions or emergencies.
2. Standardized Work Order Formats and Templates
Standardizing work order formats and templates streamlines the process of creating and processing work orders. When all work orders adhere to a consistent format, it becomes easier for employees to understand and execute them, reducing the chances of errors or confusion. Here are some benefits of standardized formats:
a. Consistency: Standardized formats ensure that all essential information is included in every work order, promoting uniformity and clarity.
b. Time Savings: Using pre-defined templates saves time, as managers and supervisors do not need to recreate work orders from scratch for each task.
c. Scalability: Standardized formats facilitate scaling up or down production, as the work order structure remains consistent regardless of the volume.
d. Ease of Analysis: Uniform data in standardized formats allows for easier data analysis and performance tracking across different work orders.
3. Real-time Updates and Communication
Real-time updates and communication are vital for efficient work order handling, especially in dynamic manufacturing environments. Timely information sharing ensures that all stakeholders stay informed about task progress, changes, and any potential issues. To achieve real-time updates and communication:
a. Digital Collaboration Tools: Utilize collaboration platforms, instant messaging, or team communication apps to facilitate quick and seamless information sharing.
b. Automated Notifications: Implement automated notifications for task assignments, completion, or any updates to keep all relevant parties informed.
c. Mobile Accessibility: Ensure that work order updates can be accessed via mobile devices, enabling workers to stay informed even on the shop floor.
d. Feedback Mechanisms: Encourage workers to provide feedback or updates on the status of tasks, enabling supervisors to make data-driven decisions.
4. Integration of Digital Tools and Software for Work Order Management
Incorporating digital tools and software for work order management enhances efficiency and accuracy in handling work orders. Here are some key digital tools and software to consider:
a. Manufacturing Execution Systems (MES): MES software helps manage and track work orders, production schedules, and resources, providing real-time insights into manufacturing operations.
b. Internet of Things (IoT) Devices: IoT sensors on machinery and equipment can provide data on performance and health, enabling predictive maintenance and reducing unplanned downtime.
c. Enterprise Resource Planning (ERP) Software: ERP systems integrate various aspects of manufacturing, including work orders, inventory, and scheduling, ensuring seamless coordination between departments.
d. Artificial Intelligence (AI) for Predictive Analytics: AI-powered analytics can optimize work order scheduling, resource allocation, and maintenance planning based on historical data and patterns.
By implementing these best practices, manufacturers can significantly improve work order handling, streamline production processes, and ultimately enhance overall manufacturing efficiency and output.
Real-Time Tracking and Status Updates for Work Orders
Real-time tracking and status updates for work orders are essential components of modern manufacturing operations. With the advancement of technology and the implementation of digital solutions, manufacturers can now monitor work order progress in real-time, ensuring timely completion of tasks and efficient production processes.
Importance of Real-Time Tracking and Status Updates for Work Orders
Real-time tracking and status updates provide manufacturers with up-to-the-minute visibility into the progress of work orders throughout the production process. This level of transparency is crucial for several reasons:
a. Timely Decision-Making: Real-time data allows managers and supervisors to make informed decisions quickly, responding to production challenges and bottlenecks promptly.
b. Improved Communication: With real-time status updates, everyone involved in the production process can stay informed about the current status of work orders, fostering better communication and collaboration.
c. Proactive Issue Resolution: Real-time tracking helps identify potential issues or delays early on, allowing manufacturers to take proactive measures to resolve them before they escalate.
d. Resource Optimization: By monitoring work order status in real-time, manufacturers can allocate resources more efficiently, ensuring that tasks are completed on time and avoiding resource overloading.
e. Enhanced Customer Satisfaction: Real-time tracking enables manufacturers to provide accurate and timely updates to customers about their orders, leading to improved customer satisfaction.
f. Continuous Improvement: Access to real-time data allows manufacturers to identify patterns and trends, enabling continuous improvement in production processes and overall efficiency.
Real-Time Tracking Technologies
Various technologies facilitate real-time tracking and status updates for work orders. Some of the key technologies include:
a. Internet of Things (IoT): IoT devices equipped with sensors can collect data on equipment performance, material usage, and other production metrics in real time.
b. Radio Frequency Identification (RFID): RFID tags can be attached to products, materials, or equipment, enabling real-time tracking and identification throughout the manufacturing process.
c. Barcode Scanning: Barcode scanners can capture and update work order status as tasks are completed, providing real-time information to the central database.
d. Mobile Applications: Mobile apps allow workers to input data and update work order status directly from the production floor, eliminating the need for manual data entry.
e. Cloud-Based Systems: Cloud-based systems store and process data in real-time, enabling access from any location with an internet connection.
Benefits of Real-Time Tracking and Status Updates
The implementation of real-time tracking and status updates for work orders offers numerous benefits to manufacturers:
a. Improved Production Efficiency: Real-time data allows manufacturers to identify and address production bottlenecks promptly, leading to more efficient workflows and reduced lead times.
b. Enhanced Resource Utilization: Manufacturers can optimize resource allocation based on real-time information, ensuring that equipment and labor are utilized effectively.
c. Increased On-Time Delivery: Real-time tracking helps manufacturers closely monitor work order progress, reducing the likelihood of delays and ensuring on-time delivery to customers.
d. Better Quality Control: With real-time tracking, manufacturers can identify quality issues early on and take corrective actions to maintain high product quality.
e. Agility and Adaptability: Real-time data enables manufacturers to respond quickly to changes in customer demands, supply chain disruptions, or unexpected events.
f. Data-Driven Decision-Making: Real-time insights support data-driven decision-making, enabling manufacturers to make informed choices for process improvement.
Implementing Real-Time Tracking and Status Updates
To implement real-time tracking and status updates effectively, manufacturers can follow these steps:
a. Identify Key Metrics: Determine the critical performance indicators that need real-time monitoring and tracking, such as production cycle times, equipment uptime, or material usage.
b. Select Appropriate Technology: Choose the right combination of technologies, such as IoT sensors, RFID tags, or barcode scanning, based on the specific requirements of the manufacturing process.
c. Integrate with Existing Systems: Ensure that the real-time tracking system seamlessly integrates with existing manufacturing software and enterprise resource planning (ERP) systems.
d. Train Employees: Provide comprehensive training to employees on how to use real-time tracking tools and mobile applications for data input and status updates.
e. Monitor and Analyze Data: Continuously monitor and analyze real-time data to identify areas for improvement and optimize production processes.
Challenges and Solutions
Implementing real-time tracking and status updates may pose some challenges, such as:
a. Data Security: Ensure that the system has robust data security measures in place to protect sensitive production information.
b. Integration Complexity: Integrating real-time tracking technologies with existing systems can be complex; working with experienced IT professionals can streamline the process.
c. Cost Considerations: The initial investment in real-time tracking technology can be substantial, but the long-term benefits outweigh the costs.
d. Workforce Adoption: Encourage and support workforce adoption of the new technology through training and ongoing support.
Implementing Work Order Prioritization Strategies
Following, we've discussed the implementation of work order prioritization strategies. Let's learn:
1. Understanding Factors Affecting Work Order Priorities:
Work order prioritization involves determining the order in which tasks should be executed based on their relative importance and urgency. Several factors can influence work order priorities in a manufacturing environment:
a. Customer Demand: Customer orders with specific delivery dates or urgent requirements often take precedence to ensure customer satisfaction and on-time delivery.
b. Production Dependencies: Some tasks may be dependent on the completion of others, and prioritizing interdependent tasks ensures a smooth and efficient production flow.
c. Production Schedule: Aligning work orders with the overall production schedule helps optimize resource utilization and meet production targets.
d. Criticality of Tasks: Identifying high-priority tasks critical to the production process, product quality, or safety ensures they receive immediate attention.
e. Equipment Availability: Prioritizing work orders based on the availability of specialized equipment or machinery required for the tasks prevents unnecessary delays.
f. Inventory Levels: Work orders requiring specific raw materials with limited availability may need prioritization to ensure timely procurement.
g. Cost Considerations: Urgent or critical tasks that have the potential to impact costs significantly may be prioritized to mitigate financial risks.
2. Setting Criteria for Prioritization:
To establish a systematic approach for work order prioritization, manufacturers need to define clear criteria based on various factors. These criteria may vary depending on the specific needs and objectives of the manufacturing operation. Common criteria for prioritization include:
a. Customer Demand: Work orders with tight delivery deadlines or orders from key customers may be given higher priority.
b. Production Dependencies: Tasks that are prerequisites for subsequent tasks or that impact other production processes are prioritized to prevent bottlenecks.
c. Urgency: Tasks requiring immediate attention to prevent safety issues, equipment breakdowns, or production delays are given priority.
d. Resource Availability: Work orders that can be completed quickly based on resource availability may be prioritized to optimize utilization.
e. Complexity and Duration: Shorter and less complex tasks may be prioritized to increase overall task completion rate.
f. Impact on Production Schedule: Tasks that can significantly impact the production schedule or customer commitments are prioritized accordingly.
g. Cost-Effectiveness: Prioritizing work orders that offer cost-saving opportunities or enhance profitability can be beneficial.
It is essential to define and document these criteria clearly so that all stakeholders involved in work order handling understand the rationale behind prioritization decisions.
3. Role of Data Analytics in Determining Work Order Priorities
Data analytics plays a critical role in work order prioritization by providing valuable insights and supporting data-driven decisions. By analyzing historical data and real-time information, manufacturers can identify patterns, trends, and correlations that influence work order priorities. Data analytics enables the following:
a. Predictive Maintenance: Analytics can identify equipment health and predict potential breakdowns, allowing preventive maintenance to be prioritized to avoid unplanned downtime.
b. Demand Forecasting: Data analytics can help predict fluctuations in customer demand, enabling better resource allocation and work order prioritization.
c. Resource Utilization: Analyzing resource availability and performance data allows for optimized allocation and prioritization of tasks.
d. Cost Optimization: Data analytics can identify cost-saving opportunities and prioritize work orders that lead to better cost-effectiveness.
e. Production Efficiency: Analytics can identify process inefficiencies and prioritize work orders that contribute to improving overall production efficiency.
f. Real-time Monitoring: Data analytics facilitates real-time tracking of work order progress, enabling supervisors to adjust priorities as needed.
By leveraging data analytics, manufacturers can make informed decisions, improve work order handling efficiency, and enhance manufacturing output. It empowers businesses to proactively address challenges and capitalize on opportunities to optimize production processes and resource allocation.
Integrating Work Order Management With ERP Systems
Integrating work order management with Enterprise Resource Planning (ERP) systems is a critical step for manufacturers seeking to streamline their production processes and improve overall efficiency. ERP systems serve as central hubs for managing various business operations, including inventory, procurement, production planning, and financials.
By integrating work order management with ERP systems, manufacturers can achieve better coordination, real-time data access, and seamless communication across departments, leading to improved productivity and cost savings.
Steps to Integrate Work Order Management With ERP Systems
a. Define Integration Objectives: Clearly define the objectives and goals of the integration process. Determine what data needs to be exchanged between the work order management system and the ERP system.
b. Choose Compatible Systems: Select work order management and ERP systems that are compatible and have well-documented integration capabilities.
c. Data Mapping: Determine how data will be mapped and transferred between the two systems. Define data fields and data formats to ensure seamless data exchange.
d. Develop Integration Strategy: Develop a comprehensive integration strategy, including timelines, resources, and key performance indicators to measure the success of the integration.
e. Test and Validate: Conduct thorough testing to ensure that data is accurately transferred between the work order management and ERP systems. Validate the integration by running test scenarios and resolving any issues that arise.
f. Train Employees: Provide training to employees on how to use the integrated system effectively and efficiently. This will ensure that the workforce is comfortable with the new processes and can take full advantage of the integrated features.
g. Monitor and Optimize: Continuously monitor the integration process and gather feedback from employees. Use this feedback to optimize the integration and make any necessary adjustments.
Challenges and Solutions
a. Data Compatibility: Work order management and ERP systems may have different data formats and structures. To address this challenge, use middleware or integration platforms that can handle data mapping and conversion.
b. Security and Privacy: Integrating two systems involves data sharing, which raises security and privacy concerns. Ensure that proper data encryption and access controls are in place to protect sensitive information.
c. Cost and Resources: Integration projects can be resource-intensive and costly. Conduct a thorough cost-benefit analysis to justify the investment and allocate the necessary resources.
d. Change Management: Implementing an integrated system may require changes to existing workflows and processes. Adopt a change management approach to ensure a smooth transition and employee buy-in.
Streamlining Work Order Execution
Following, we've discussed the streamlining of work order execution. Let's learn:
1. Delegating Responsibilities and Assigning Tasks:
Effective work order execution starts with a clear delegation of responsibilities and task assignments. This ensures that each team member knows their role and the tasks they need to complete. Here's how to streamline this process:
a. Role Clarification: Clearly define the roles and responsibilities of each team member involved in the work order execution process.
b. Task Allocation: Assign specific tasks to individuals based on their skills, expertise, and availability.
c. Communication: Communicate task assignments clearly, either through in-person meetings or via digital collaboration tools, to avoid misunderstandings.
d. Empowerment: Empower workers to make decisions within their assigned tasks, fostering a sense of ownership and accountability.
e. Cross-Training: Cross-train employees to handle multiple tasks, providing flexibility in task allocation and reducing dependencies on specific individuals.
2. Efficient Scheduling and Resource Allocation
Optimizing scheduling and resource allocation is essential for smooth work order execution. Efficiently managing resources ensures that tasks are completed on time and with minimal wastage. Consider the following steps:
a. Production Planning: Create a detailed production plan, incorporating work order timelines and dependencies, to ensure tasks are scheduled logically and efficiently.
b. Resource Availability: Check resource availability in advance to prevent delays and optimize resource utilization.
c. Real-time Updates: Use real-time data and communication tools to adjust schedules and resource allocations as needed based on changing circumstances.
d. Lean Manufacturing Principles: Apply lean manufacturing principles to reduce waste and enhance resource efficiency throughout the production process.
3. Tracking and Monitoring Work Order Progress
To ensure work orders stay on track and meet deadlines, tracking and monitoring progress is crucial. This involves monitoring tasks as they move through various stages of execution. Follow these steps:
a. Work Order Management System: Implement a work order management system or use digital tools to track work order progress and update status in real time.
b. Milestones and Checkpoints: Set milestones or checkpoints to monitor progress at specific stages, allowing for early identification of potential delays or issues.
c. Task Status Reports: Regularly generate and review task status reports to gauge progress and identify any deviations from the original plan.
d. Performance Metrics: Utilize key performance indicators (KPIs) related to work order execution to assess overall efficiency and identify areas for improvement.
4. Identifying and Addressing Bottlenecks in the Process
Bottlenecks can hinder work order execution and impact overall productivity. Identifying and resolving these bottlenecks is essential for streamlining the process. Follow these steps:
a. Process Mapping: Map out the entire work order execution process to identify potential bottlenecks and inefficiencies.
b. Root Cause Analysis: Perform root cause analysis to determine the underlying factors contributing to bottlenecks.
c. Process Improvement: Implement process improvement initiatives to remove or mitigate bottlenecks, enhancing overall workflow efficiency.
d. Continuous Improvement Culture: Foster a culture of continuous improvement, encouraging employees to identify and address bottlenecks proactively.
e. Collaboration and Communication: Facilitate open communication and collaboration between different departments to identify and resolve cross-functional bottlenecks.
By effectively delegating responsibilities, optimizing scheduling and resource allocation, tracking progress, and addressing bottlenecks, manufacturers can streamline work order execution, improve production efficiency, and maximize manufacturing output. A well-organized and efficient work order execution process leads to reduced lead times, enhanced customer satisfaction, and a more competitive manufacturing operation.
Work Order Management for Agile and Lean Manufacturing
Agile and Lean manufacturing methodologies have emerged as powerful strategies to drive efficiency, flexibility, and responsiveness in production processes. At the heart of these methodologies lies effective work order management, which plays a crucial role in orchestrating the entire production process.
The Significance of Work Order Management in Agile and Lean Manufacturing
Work order management is an essential aspect of Agile and Lean manufacturing as it serves as the central mechanism to plan, execute, and track production activities. By managing work orders effectively, manufacturers can achieve the following benefits:
a. Flexibility: Agile and Lean manufacturing emphasize the ability to respond quickly to changing customer demands and market trends. Work order management allows manufacturers to adjust production schedules, allocate resources, and adapt to changing priorities with ease.
b. Efficiency: Efficient work order management ensures that production processes are streamlined, reducing waste and improving overall productivity. This enables organizations to maximize the use of resources and minimize downtime.
c. Quality: Effective work order management ensures that production tasks are carried out with precision and adherence to quality standards, resulting in superior products and satisfied customers.
d. Cost-Effectiveness: Lean manufacturing principles aim to eliminate waste and unnecessary activities. By optimizing work orders, manufacturers can reduce unnecessary expenses and enhance cost-effectiveness.
e. Real-Time Visibility: Work order management provides real-time visibility into the status of production activities, allowing organizations to monitor progress, identify bottlenecks, and make informed decisions promptly.
Key Principles of Work Order Management in Agile and Lean Manufacturing
a. Demand-Driven: Work order management in Agile and Lean manufacturing is driven by actual customer demand rather than forecasts. It emphasizes producing only what is required when it is needed and in the right quantity.
b. Pull System: The work order management system operates on a pull-based approach, where production is initiated based on customer demand. This minimizes excess inventory and reduces the risk of overproduction.
c. Continuous Improvement: Agile and Lean manufacturing promote a culture of continuous improvement. Work order management is continually reviewed, refined, and optimized to eliminate inefficiencies and enhance performance.
d. Collaborative Approach: Work order management involves collaboration among various teams and departments. Cross-functional teams work together to align production with customer needs and market changes.
e. Visual Management: Visual cues and tools are used in work order management to provide real-time information, facilitate communication, and enable quick decision-making.
Implementing Effective Work Order Management in Agile and Lean Manufacturing
a. Demand Forecasting: Accurate demand forecasting is the foundation of effective work order management. Manufacturers need to use historical data, market trends, and customer feedback to predict future demand.
b. Just-In-Time (JIT) Production: JIT production aligns production schedules with actual demand, reducing the need for excessive inventory. Work orders are generated based on actual customer orders, ensuring efficient resource utilization.
c. Kanban Systems: Kanban is a visual tool used in work order management to manage inventory and production flow. It signals when production is required and ensures a smooth, continuous workflow.
d. Work Order Prioritization: Prioritize work orders based on customer deadlines, product complexity, and resource availability. This ensures that critical orders are given precedence and are completed on time.
e. Cross-Functional Collaboration: Work order management involves collaboration between production, procurement, and logistics teams. Regular meetings and communication channels are established to keep everyone aligned.
f. Standard Work Instructions: Provide clear and standardized work instructions for each work order to ensure consistency and minimize errors during production.
g. Continuous Monitoring and Improvement: Monitor work order execution and performance regularly. Analyze production data to identify areas for improvement and implement changes accordingly.
Overcoming Challenges in Work Order Management for Agile and Lean Manufacturing
a. Change Management: Implementing Agile and Lean manufacturing practices requires a significant cultural shift within the organization. Resistance to change may arise, and proper change management strategies should be employed to overcome it.
b. Data Accuracy: Work order management relies on accurate and up-to-date data. Organizations should invest in robust data collection and management systems to ensure data integrity.
c. Technology Integration: Adopting Agile and Lean manufacturing often involves using advanced technologies and software tools. Ensuring seamless integration between these systems and work order management is essential for success.
d. Resource Allocation: Efficient resource allocation is critical to meeting production demands. Balancing the allocation of resources to multiple work orders while minimizing bottlenecks can be challenging.
e. Adapting to Market Changes: Agile and Lean manufacturing require organizations to respond quickly to market changes. Work order management systems should be agile enough to accommodate sudden shifts in demand.
Collaboration and Communication Across Departments
Check the following sections where we've discussed collaboration and communication across the departments:
1. The Importance of Cross-Functional Collaboration:
Cross-functional collaboration is crucial in the manufacturing industry as it brings together teams from different departments to work towards common goals. Effective collaboration breaks down silos, fosters a shared understanding of objectives, and improves overall productivity and product quality. Here are the key benefits of cross-functional collaboration:
a. Comprehensive Perspective: Different departments bring diverse expertise, allowing for a comprehensive approach to problem-solving and decision-making.
b. Efficient Workflows: Collaborative efforts enable streamlined workflows and reduce the risk of miscommunication or duplicated efforts.
c. Faster Issue Resolution: Cross-functional teams can quickly address issues that may arise during work order execution, minimizing delays.
d. Innovation and Creativity: Collaboration encourages the exchange of ideas, leading to innovative solutions and process improvements.
e. Enhanced Decision-Making: With input from multiple perspectives, decisions can be more well-rounded and data-driven.
2. Effective Communication Tools and Strategies
To facilitate seamless communication between departments, utilizing appropriate tools and strategies is essential. Here are some effective communication tools and strategies:
a. Digital Collaboration Platforms: Implementing collaborative software like Microsoft Teams or Slack allows for real-time messaging, file sharing, and project updates.
b. Project Management Software: Use project management tools such as Asana or Trello to track work order progress, assign tasks, and manage deadlines.
c. Email Updates: Regular email updates and notifications can help disseminate information efficiently to relevant stakeholders.
d. Visual Communication Aids: Use charts, graphs, and visual representations of data to enhance clarity and understanding in communication.
e. Centralized Communication Channels: Establish a centralized communication hub, like an intranet or shared document repository, for easy access to information by all team members.
f. Open-Door Policy: Encourage an open-door policy where team members feel comfortable seeking clarification or offering suggestions.
g. Feedback Mechanisms: Create avenues for feedback and suggestions from employees across departments to continuously improve collaboration and communication.
3. Holding Regular Meetings and Reviews to Discuss Work Order Status
Regular meetings and reviews are essential to keep all relevant stakeholders updated on work order progress and to address any challenges that may arise. Here's how to conduct effective meetings and reviews:
a. Daily Huddles: Hold short daily huddles or stand-up meetings to discuss work order status, roadblocks, and priorities for the day.
b. Weekly Progress Meetings: Conduct weekly meetings to review overall progress, address bottlenecks, and align priorities for the upcoming week.
c. Monthly Performance Reviews: Conduct monthly performance reviews to assess overall work order handling efficiency and identify areas for improvement.
d. Cross-Functional Review Meetings: Hold cross-functional review meetings to discuss work orders that involve multiple departments, ensuring coordination and collaboration.
e. Actionable Outcomes: Ensure that meetings result in actionable outcomes and clear responsibilities for addressing any issues or improvement opportunities.
f. Performance Metrics: Use data from meetings and reviews to track key performance metrics and identify trends or patterns in work order handling.
By prioritizing cross-functional collaboration, implementing effective communication tools and strategies, and holding regular meetings and reviews, manufacturers can enhance work order execution, improve overall productivity, and create a more harmonious and efficient production environment. Collaborative efforts and open communication foster a culture of teamwork, leading to better decision-making and a positive impact on the entire manufacturing process.
Embracing Technology for Work Order Handling
Check the following sections where we've discussed embracing technology for work order handling:
1. Utilizing Manufacturing Execution Systems (MES)
Manufacturing Execution Systems (MES) are software solutions that play a critical role in work order handling and overall production management. MES systems bridge the gap between the enterprise resource planning (ERP) system and the shop floor, providing real-time visibility and control over manufacturing processes. Here's how MES benefits work order handling:
a. Work Order Management: MES allows seamless creation, tracking, and management of work orders, ensuring that tasks are executed in a systematic and organized manner.
b. Real-time Data Capture: MES systems capture data from various stages of production, enabling real-time monitoring of work order progress and immediate action in case of deviations.
c. Resource Allocation: MES optimizes resource allocation by matching work orders with available resources, ensuring efficient production scheduling.
d. Quality Control: MES integrates quality control processes, ensuring adherence to work order specifications and identifying deviations promptly.
e. Traceability and Compliance: MES systems provide complete traceability of work order execution, ensuring compliance with industry standards and regulations.
2. Implementation of Internet of Things (IoT) Devices for Real-time Data Collection
The Internet of Things (IoT) involves the integration of smart devices, sensors, and actuators with network connectivity to collect and exchange data. IoT devices can significantly enhance work order handling through real-time data collection and process automation:
a. Asset Tracking: IoT-enabled devices can track the location and status of equipment and tools, helping optimize their utilization and reducing the risk of losses.
b. Condition Monitoring: IoT sensors can monitor the health and performance of machinery, providing data for predictive maintenance and minimizing unplanned downtime.
c. Inventory Management: IoT devices can track inventory levels, alerting teams when materials or parts need replenishment, ensuring seamless work order execution.
d. Work Order Status Updates: IoT devices can provide real-time updates on work order progress, helping supervisors monitor tasks remotely and take prompt actions when needed.
e. Process Automation: IoT devices can automate certain tasks, such as material handling or assembly, increasing efficiency and reducing manual errors.
3. Leveraging Artificial Intelligence (AI) for Predictive Maintenance and Demand Forecasting
Artificial Intelligence (AI) technologies, including machine learning algorithms, can analyze vast amounts of data and provide valuable insights. Leveraging AI can significantly enhance work order handling:
a. Predictive Maintenance: AI algorithms can analyze equipment data from IoT sensors to predict equipment failures or maintenance needs before they occur. This proactive approach minimizes equipment downtime and reduces maintenance costs.
b. Demand Forecasting: AI can analyze historical sales data, market trends, and external factors to generate accurate demand forecasts. This ensures that production schedules align with customer demands and reduces the risk of overproduction or stockouts.
c. Task Prioritization: AI can assist in prioritizing work orders based on various factors, such as production dependencies, resource availability, and customer requirements, ensuring optimal task sequencing and efficient resource utilization.
d. Process Optimization: AI can identify process inefficiencies in work order handling, offering recommendations for streamlining workflows and improving overall efficiency.
e. Resource Management: AI-powered analytics can assist in allocating resources effectively, considering factors like worker skills, equipment capabilities, and production constraints.
By embracing technology such as MES, IoT devices, and AI, manufacturers can revolutionize work order handling. These technologies facilitate data-driven decision-making, real-time monitoring, and process optimization, leading to enhanced production efficiency, reduced downtime, and improved overall manufacturing performance.
Work Order Performance Metrics and Evaluation
Check the following sections where we've discussed work order performance metrics and evaluation:
1. Key Performance Indicators (KPIs) for Work Order Handling
Key performance indicators (KPIs) are essential metrics used to evaluate the efficiency and effectiveness of work order handling processes. These KPIs help manufacturers track progress, identify areas for improvement, and ensure work orders are executed successfully. Here are some crucial KPIs for work order handling:
a. Work Order Completion Time: Measures the time taken to complete work orders from initiation to closure. It indicates how efficiently tasks are executed.
b. Work Order Backlog: This represents the number of pending work orders at any given time, providing insights into the workload and resource capacity.
c. On-Time Completion: Measures the percentage of work orders completed within their scheduled timelines. High on-time completion rates signify effective planning and execution.
d. Work Order Accuracy: Tracks the number of work orders with errors, rework, or deviations from specifications. A lower accuracy rate indicates the need for improved clarity in work order instructions.
e. Work Order Response Time: Measures the time taken to acknowledge and start work on a newly assigned work order, indicating responsiveness and agility.
f. Work Order Cost: Calculates the total cost associated with executing work orders, including labor, materials, and equipment costs. This KPI helps monitor cost efficiency.
g. First-Time Fix Rate: Evaluates the percentage of work orders completed successfully without requiring additional work or rework. A higher first-time fix rate signifies better efficiency and quality.
2. Monitoring and Analyzing Work Order Data
Monitoring and analyzing work order data is crucial to gaining insights into process performance and identifying opportunities for improvement. Here's how to effectively monitor and analyze work order data:
a. Data Collection: Collect and centralize data from various stages of work order execution, including initiation, progress tracking, completion, and feedback.
b. Data Visualization: Use charts, graphs, and dashboards to visualize work order data, making trends and patterns easier to identify.
c. Performance Trend Analysis: Analyze historical data to identify trends in work order handling performance, allowing for better forecasting and decision-making.
d. Deviation Detection: Monitor work order performance against predefined KPI targets to identify deviations and take corrective actions promptly.
e. Root Cause Analysis: Conduct root cause analysis for any recurring issues or bottlenecks to understand the underlying factors affecting work order handling.
f. Cross-Functional Analysis: Analyze data across departments and teams to identify areas where cross-functional collaboration can be improved.
3. Continuous Improvement Strategies Based on Performance Metrics
Continuous improvement is a fundamental aspect of work order handling. Based on performance metrics, manufacturers can implement strategies to enhance efficiency and effectiveness. Here are some continuous improvement strategies:
a. Process Standardization: Standardize work order handling processes to ensure consistency and clarity in task execution.
b. Employee Training and Development: Invest in employee training to enhance skills and expertise, promoting better work order handling.
c. Implementing Best Practices: Incorporate best practices from successful work order executions to improve overall performance.
d. Cross-Functional Collaboration: Foster a culture of collaboration and teamwork across departments to optimize work order execution.
e. Technology Adoption: Embrace advanced technologies like automation, IoT, and AI to streamline work order handling and reduce manual errors.
f. Regular Reviews: Conduct regular reviews and meetings to discuss performance metrics and identify improvement opportunities.
g. Feedback and Employee Engagement: Encourage feedback from employees involved in work order handling and engage them in continuous improvement initiatives.
h. Benchmarking: Compare work order handling performance with industry benchmarks and best-in-class organizations to identify areas for improvement.
By continuously monitoring performance metrics and implementing improvement strategies, manufacturers can optimize work order handling processes, reduce lead times, improve resource utilization, and enhance overall manufacturing output. Continuous improvement efforts ensure that work order handling remains adaptive and responsive to changing business needs and customer demands.
Future Trends in Work Order Management and Manufacturing Optimization
Work order management is continuously evolving to meet the demands of modern manufacturing environments. As technology and industry practices advance, several future trends are expected to shape work order management and manufacturing optimization:
Industry 4.0 Integration
Industry 4.0, also known as the Fourth Industrial Revolution, is a driving force behind the future of work order management and manufacturing optimization. It emphasizes the integration of digital technologies, such as the Internet of Things (IoT), artificial intelligence (AI), cloud computing, and big data analytics, into manufacturing processes.
Manufacturers will increasingly adopt smart factories, where production systems are interconnected, and data is collected and analyzed in real time. This integration will enable more agile and responsive work order management, as real-time data will facilitate predictive maintenance, demand forecasting, and optimized production scheduling.
Internet of Things (IoT) for Predictive Maintenance
The IoT will revolutionize work order management through predictive maintenance. IoT-enabled sensors embedded in machines and equipment will collect real-time data on performance, temperature, and wear. This data will be used to predict potential failures and schedule preventive maintenance before breakdowns occur.
Manufacturers can proactively address equipment issues, reducing downtime, and minimizing repair costs. With predictive maintenance, work orders will be generated automatically based on equipment conditions, streamlining maintenance processes and ensuring optimal machine availability.
Artificial Intelligence (AI) for Automated Workflows
AI-powered work order management systems will transform how manufacturers create, manage, and execute work orders. AI algorithms will analyze historical data, identify patterns, and optimize production workflows. Automated work order assignment, scheduling, and resource allocation will improve overall efficiency and resource utilization.
AI will also facilitate predictive analysis, enabling manufacturers to foresee potential bottlenecks and adjust production plans accordingly. As AI evolves, it will increasingly handle routine tasks, freeing up human operators to focus on higher-value activities.
Augmented Reality (AR) for Enhanced Work Instructions
Augmented Reality (AR) will play a pivotal role in work order management by providing interactive and immersive work instructions to operators. AR-enabled smart glasses or mobile devices will overlay digital information onto the physical environment, guiding workers through complex assembly tasks.
This technology will reduce errors, increase productivity, and enhance the accuracy of work orders. AR will also facilitate remote assistance, allowing experts to guide technicians from different locations, resulting in faster problem-solving and reduced downtime.
Cloud-Based Work Order Management Systems
Cloud computing will continue to shape the future of work order management, offering scalability, flexibility, and accessibility. Cloud-based work order management systems will centralize data and facilitate real-time collaboration between different stakeholders, including engineers, operators, and managers.
Manufacturers can access work orders from anywhere, on any device, streamlining communication and decision-making processes. Moreover, cloud-based solutions offer automatic backups and enhanced security, ensuring data integrity and protection against potential system failures.
Mobile Work Order Management
The increasing use of mobile devices in manufacturing will drive the adoption of mobile work order management solutions. With Bring Your Own Device (BYOD) policies becoming prevalent, workers will use smartphones and tablets to access and update work orders on the factory floor.
Mobile applications will enable real-time communication, empowering workers to stay connected and updated on work order statuses. The mobility of work order management will enhance communication and responsiveness, leading to faster and more accurate task execution.
Work Order Optimization through Advanced Analytics
Data analytics will be a key enabler of work order optimization in manufacturing. Advanced analytics tools will process vast amounts of data collected from production processes and supply chain operations.
Manufacturers can use this data to identify inefficiencies, uncover patterns, and make informed decisions for continuous process improvement. With data-driven insights, work orders can be optimized to reduce lead times, minimize material waste, and enhance overall productivity.
Work Order Management in Global Supply Chains
The globalization of manufacturing will necessitate efficient work order management across multiple locations and supply chain partners. Manufacturers will utilize digital platforms and communication tools to coordinate work orders with suppliers, contract manufacturers, and distribution centers across different countries and time zones.
Real-time visibility into work order statuses will improve coordination, reduce delays, and enhance supply chain efficiency.
Work Order Customization and Personalization
As customer demands for personalized products increase, work order management will evolve to accommodate customization requirements. Manufacturers will implement flexible work order management systems capable of handling unique specifications and configurations for each order.
Customized work orders will drive increased customer satisfaction, reduced lead times, and improved competitiveness in the market.
Blockchain for Secure and Transparent Work Order Transactions
Blockchain technology will find applications in work order management, ensuring secure and transparent transactions throughout the manufacturing process. Work orders recorded on a blockchain will be tamper-proof, providing a reliable and auditable record of every transaction, from order creation to final delivery.
This technology will instill trust among all stakeholders, streamline payment processes, and reduce the risk of fraud.
Frequently Asked Questions (FAQs) Associated with Work Order Handling
Here are some frequently asked questions (FAQs) about work order handling with detailed answers:
FAQ 1: What is a work order, and why is it important in manufacturing?
Answer: A work order is a document that specifies tasks, instructions, and resources required to complete a specific job or project in manufacturing. It acts as a roadmap for workers and supervisors, ensuring tasks are executed efficiently and in a coordinated manner. Work orders are essential in manufacturing as they provide clarity, improve productivity, and help maintain consistency in the production process.
FAQ 2: How do you prioritize work orders in manufacturing?
Answer: Prioritizing work orders in manufacturing involves considering factors such as customer demand, production dependencies, urgency, resource availability, and impact on production schedules. Establishing clear criteria and key performance indicators (KPIs) helps prioritize tasks based on their importance and impact on overall production efficiency.
FAQ 3: What are some common challenges in work order handling?
Answer: Common challenges in work order handling include lack of clarity in instructions, poor communication between departments, inefficient scheduling, and delayed processing and execution. Addressing these challenges requires clear communication, standardized processes, and the implementation of digital tools to streamline work order management.
FAQ 4: How can technology improve work order handling in manufacturing?
Answer: Technology can significantly improve work order handling by enabling real-time data collection, streamlining communication, optimizing resource allocation, and supporting predictive maintenance. Manufacturing Execution Systems (MES), Internet of Things (IoT) devices, and Artificial Intelligence (AI) are some technologies that manufacturers can leverage for enhanced work order execution.
FAQ 5: What are some key performance indicators (KPIs) used to evaluate work order handling efficiency?
Answer: Key performance indicators (KPIs) for work order handling include work order completion time, on-time completion rate, work order accuracy, work order backlog, work order cost, first-time fix rate, and work order response time. These KPIs provide insights into process efficiency, resource utilization, and overall production performance.
FAQ 6: How can manufacturers continuously improve work order handling?
Answer: Manufacturers can continuously improve work order handling by standardizing processes, providing regular training and employee development, implementing best practices, fostering cross-functional collaboration, adopting advanced technologies, conducting regular reviews, and encouraging feedback and employee engagement. Continuous improvement efforts lead to enhanced productivity and overall manufacturing effectiveness.
FAQ 7: How do data analytics and predictive maintenance impact work order handling?
Answer: Data analytics and predictive maintenance play a significant role in work order handling by providing real-time insights, identifying potential equipment failures before they occur, and optimizing maintenance schedules. By analyzing historical data and predicting maintenance needs, manufacturers can reduce downtime, increase equipment availability, and improve work order execution efficiency.
FAQ 8: Why is cross-functional collaboration crucial in work order handling?
Answer: Cross-functional collaboration is vital in work order handling as it brings together teams from different departments to work towards common goals. Collaboration fosters a comprehensive perspective, efficient workflows, faster issue resolution, innovation, and enhanced decision-making. Effective communication and coordination across departments lead to seamless work order execution and improved overall production performance.
Wrapping Up
Effective work order handling is a cornerstone of successful manufacturing operations, directly impacting production efficiency, resource utilization, and overall output. By embracing best practices, leveraging technology, and fostering cross-functional collaboration, manufacturers can optimize work order execution and achieve higher levels of productivity and customer satisfaction.
Clear and detailed work order creation, along with standardized formats and templates, ensures that tasks are well-defined, minimizing errors and confusion. Real-time updates and communication tools facilitate seamless information sharing and enable quick responses to changes or challenges in the production process.
Manufacturing Execution Systems (MES), Internet of Things (IoT) devices, and Artificial Intelligence (AI) are valuable technological assets that streamline work order handling. MES provides real-time visibility and control, while IoT devices offer data collection and process automation capabilities. AI enhances predictive maintenance and demand forecasting, enabling proactive decision-making and resource optimization.
Monitoring and analyzing key performance indicators (KPIs) are essential for continuous improvement. Regular reviews and data-driven decision-making help identify areas for enhancement, enabling manufacturers to implement strategies to optimize processes and increase overall efficiency.
In conclusion, embracing efficient work order handling practices and harnessing the power of technology and collaboration empower manufacturers to meet customer demands, reduce lead times, and gain a competitive advantage in the dynamic manufacturing landscape. By continuously striving for excellence, manufacturers can unlock their full potential and achieve a seamless, agile, and highly productive manufacturing environment.
How Deskera Can Assist You?
Deskera ERP and MRP systems help you to keep your business units organized. The system's key features of demand forecasting with Deskera include as follows:
- Establish Demand Forecasting Process
- Automate Data Collection
- Monitor Market Trends
- Analyze Historical Data
- Estimate Future Demand
- Adjust Production Levels
- Manage Supply Chain...and much more!
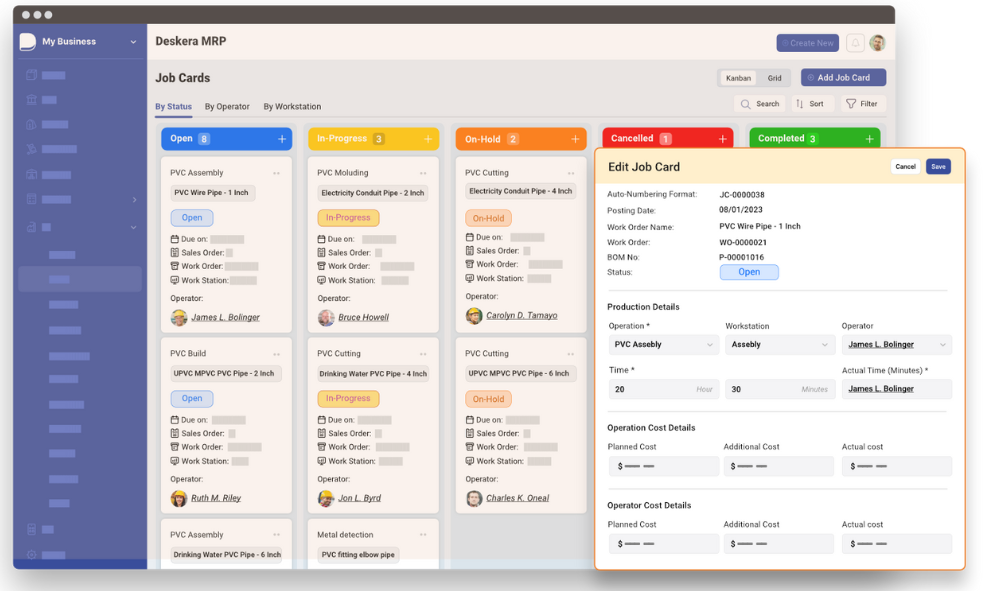
- Deskera's integrated financial planning tools enable investors to better plan and track their investments. It can assist investors in making faster and more accurate decisions.
- Deskera CRM is a powerful solution that manages your sales and helps you close deals quickly. It not only enables you to perform critical tasks like lead generation via email, but it also gives you a comprehensive view of your sales funnel.
- Deskera Books allows you to better manage your accounts and finances. Maintain good accounting practices by automating tasks like billing, invoicing, and payment processing.
- Deskera People is a straightforward tool for centralizing your human resource management functions.
Final Takeaways
We've arrived at the last section of this guide. Let's have a look at some of the most important points to remember:
- A work order in manufacturing is a detailed document or instruction that outlines a specific task, project, or job that needs to be completed within the production process. It serves as a comprehensive guide for workers, technicians, and supervisors, providing them with the necessary information to carry out the assigned tasks efficiently and effectively.
- Maintenance orders are issued to address equipment breakdowns, perform preventive maintenance, or conduct repairs. They outline the maintenance tasks required, spare parts needed, and the schedule for maintenance activities.
- Effective work order handling contributes to improved production planning and coordination by providing clear instructions and timelines for each task. When work orders are well-defined and detailed, production managers can easily identify the sequence of operations, allocate resources efficiently, and schedule tasks appropriately.
- Cross-functional collaboration is crucial in the manufacturing industry as it brings together teams from different departments to work towards common goals. Effective collaboration breaks down silos, fosters a shared understanding of objectives, and improves overall productivity and product quality.
- Manufacturing Execution Systems (MES) are software solutions that play a critical role in work order handling and overall production management. MES systems bridge the gap between the enterprise resource planning (ERP) system and the shop floor, providing real-time visibility and control over manufacturing processes.
Related Articles
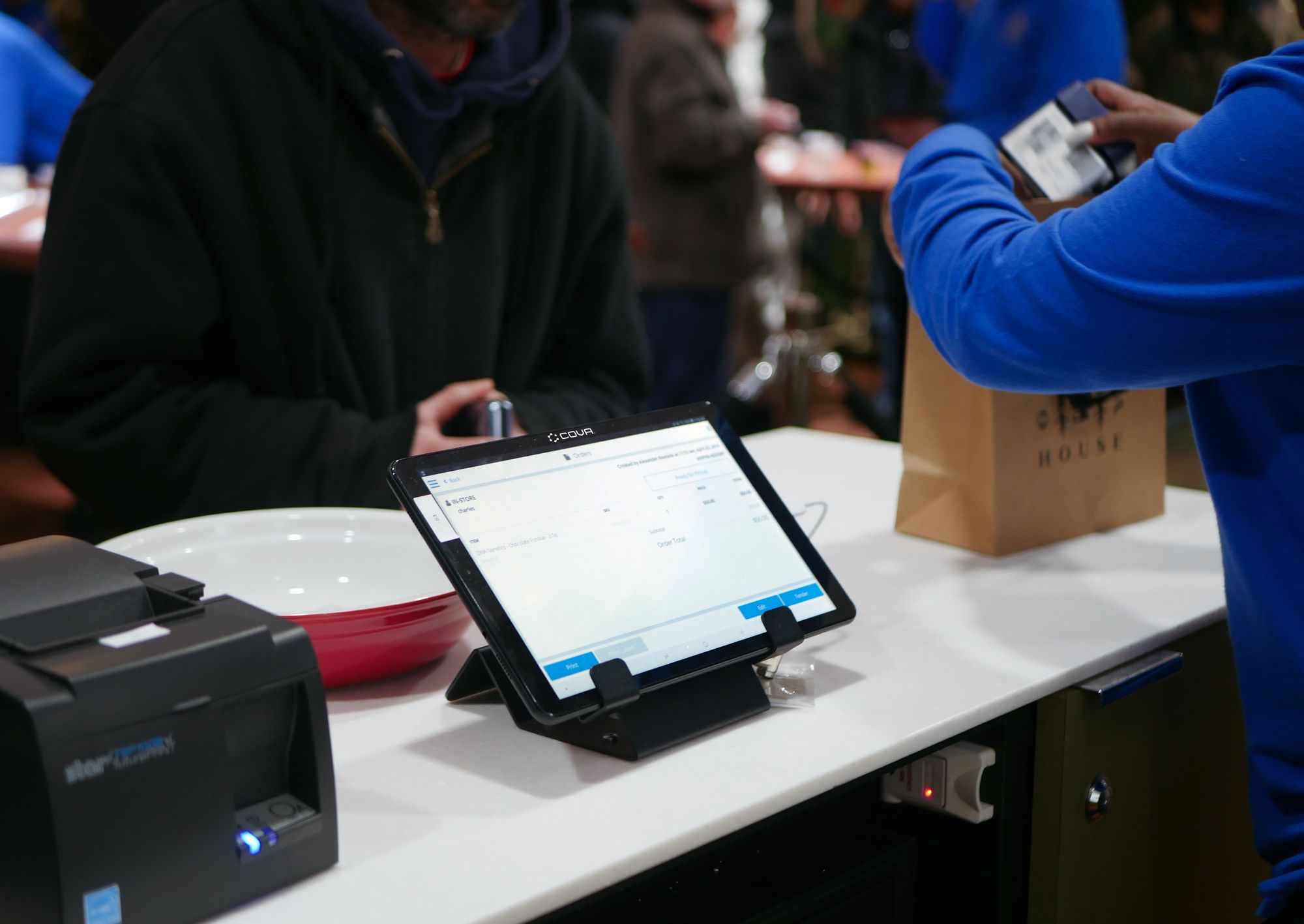
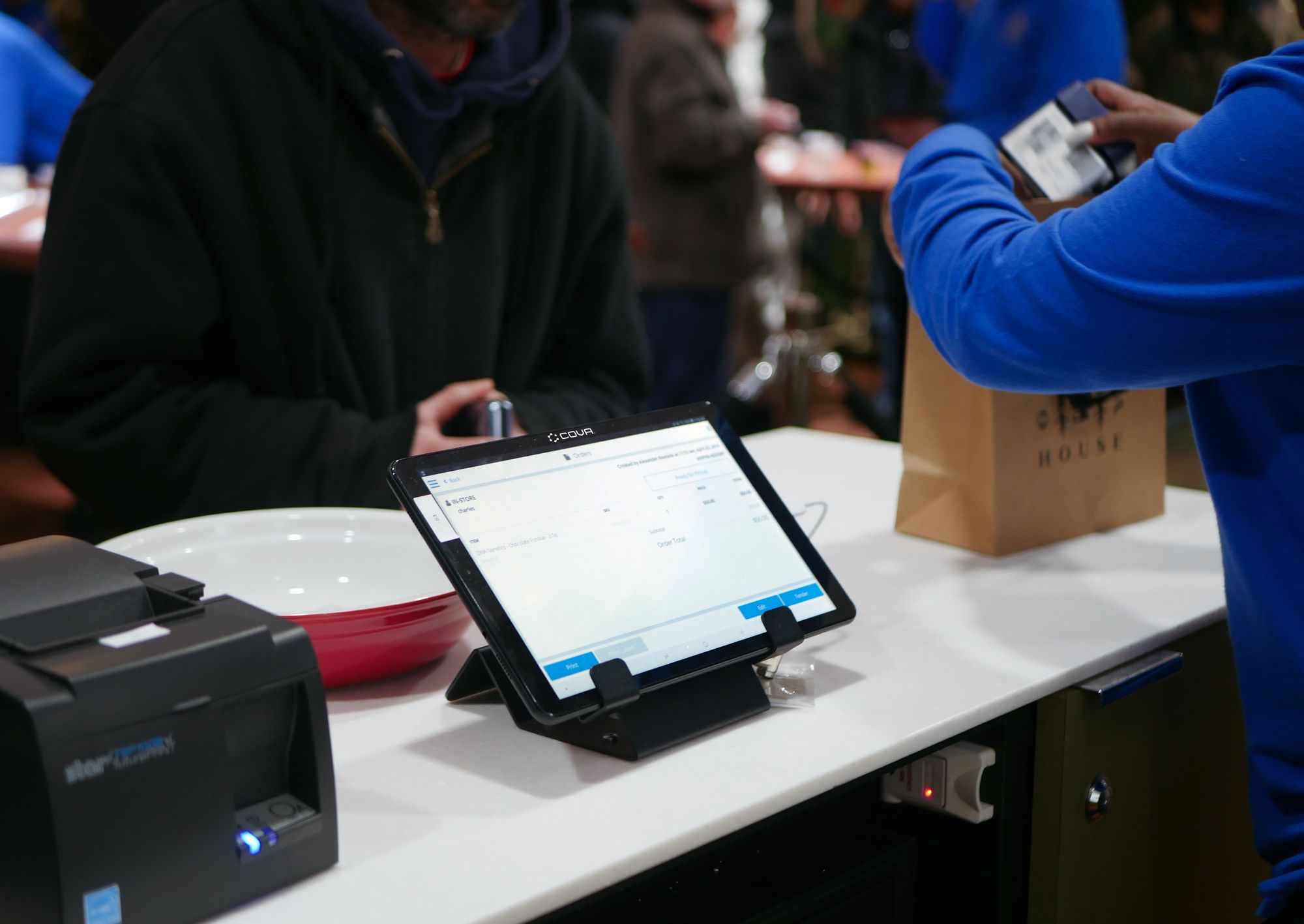
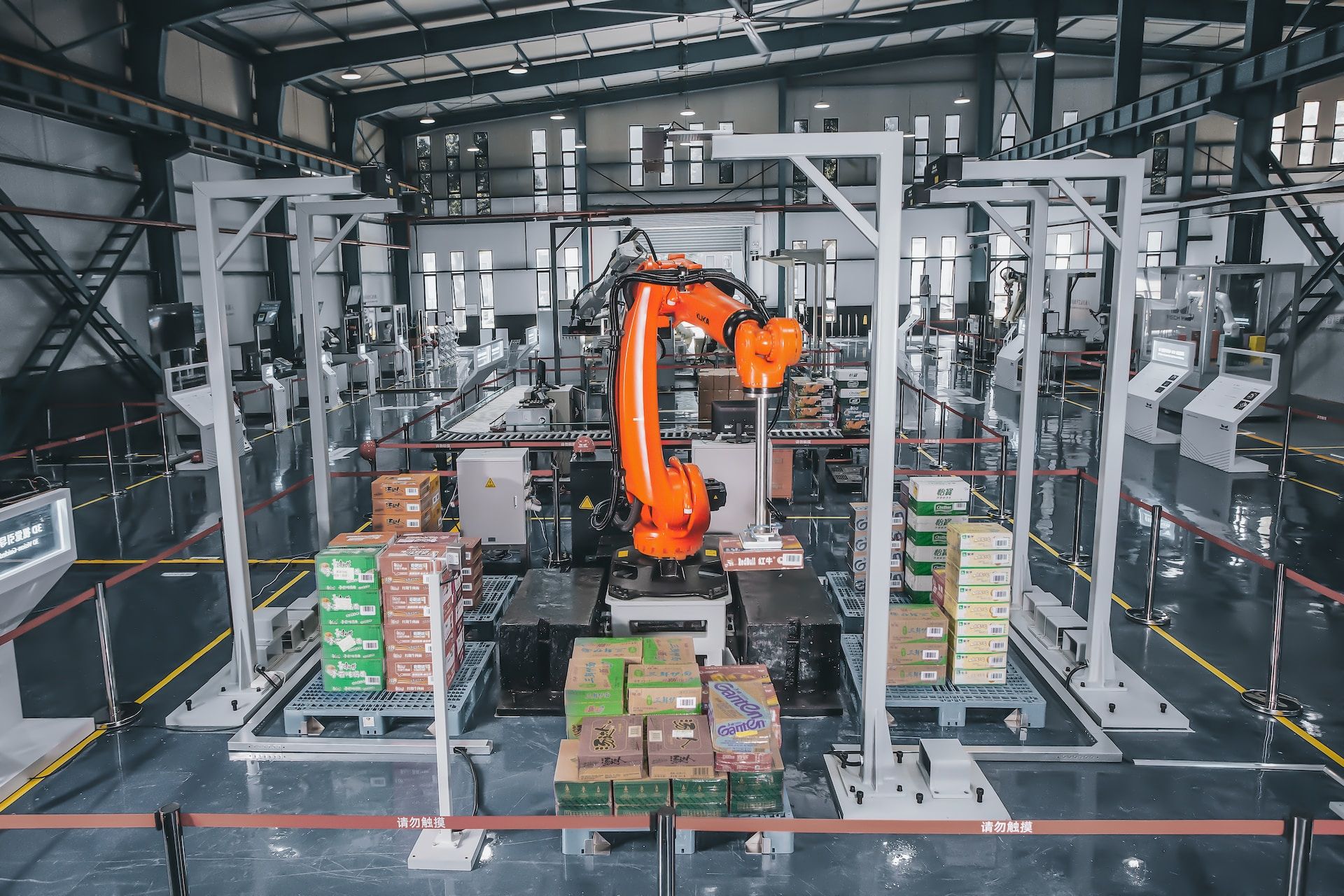
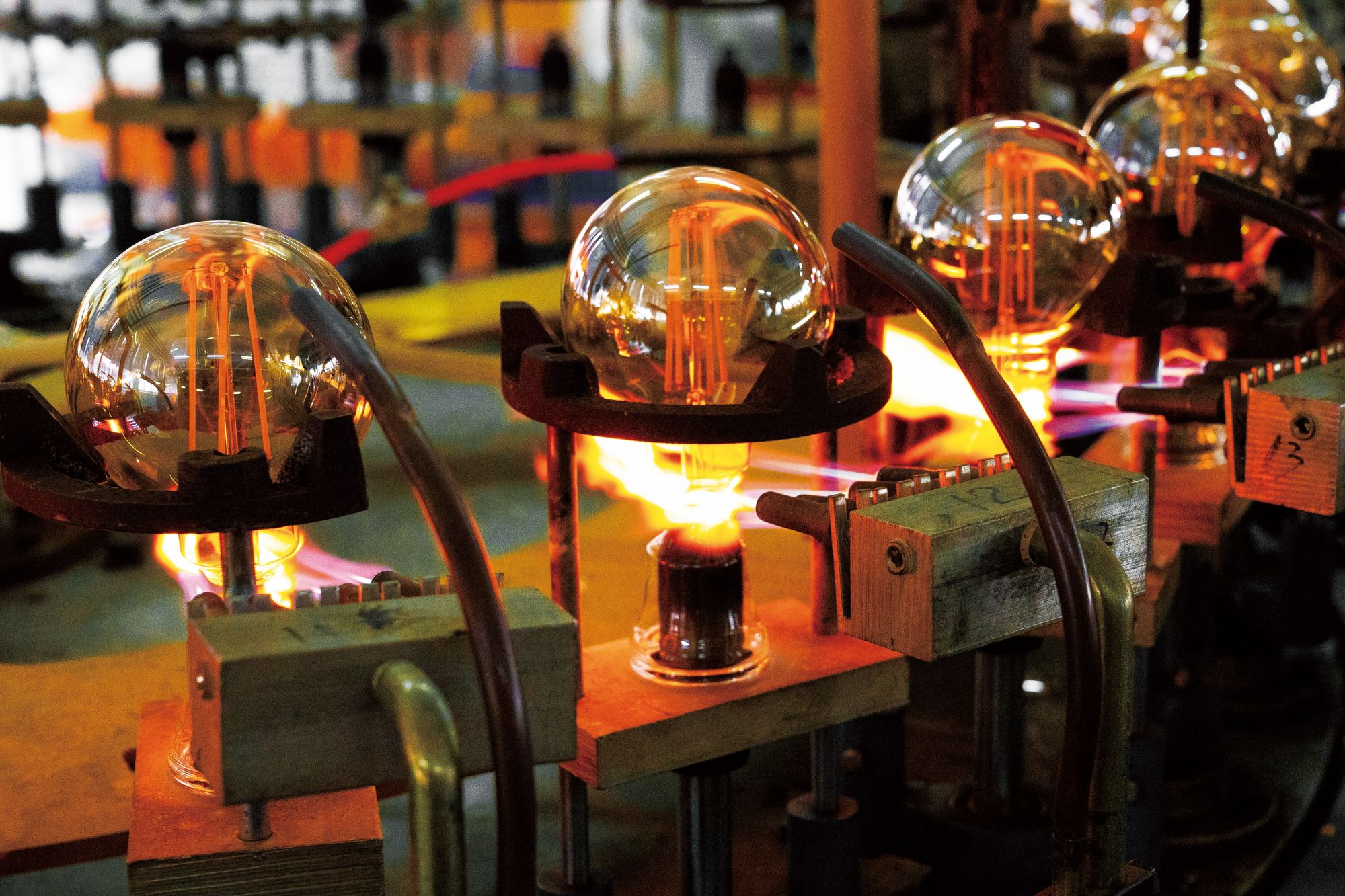