Excellent products have detailed bills of materials (BoMs) that are documented and designed. The list of mechanical, software, firmware, and other components give the whole product design. The list of components is used to create the top-level assembly's finished product.
The parent-child relationships between each level of the assembly are included in a multi-level BoM, also known as an indented BoM. For each sub-assembly that makes up the ultimate product, it displays the hierarchical structure.
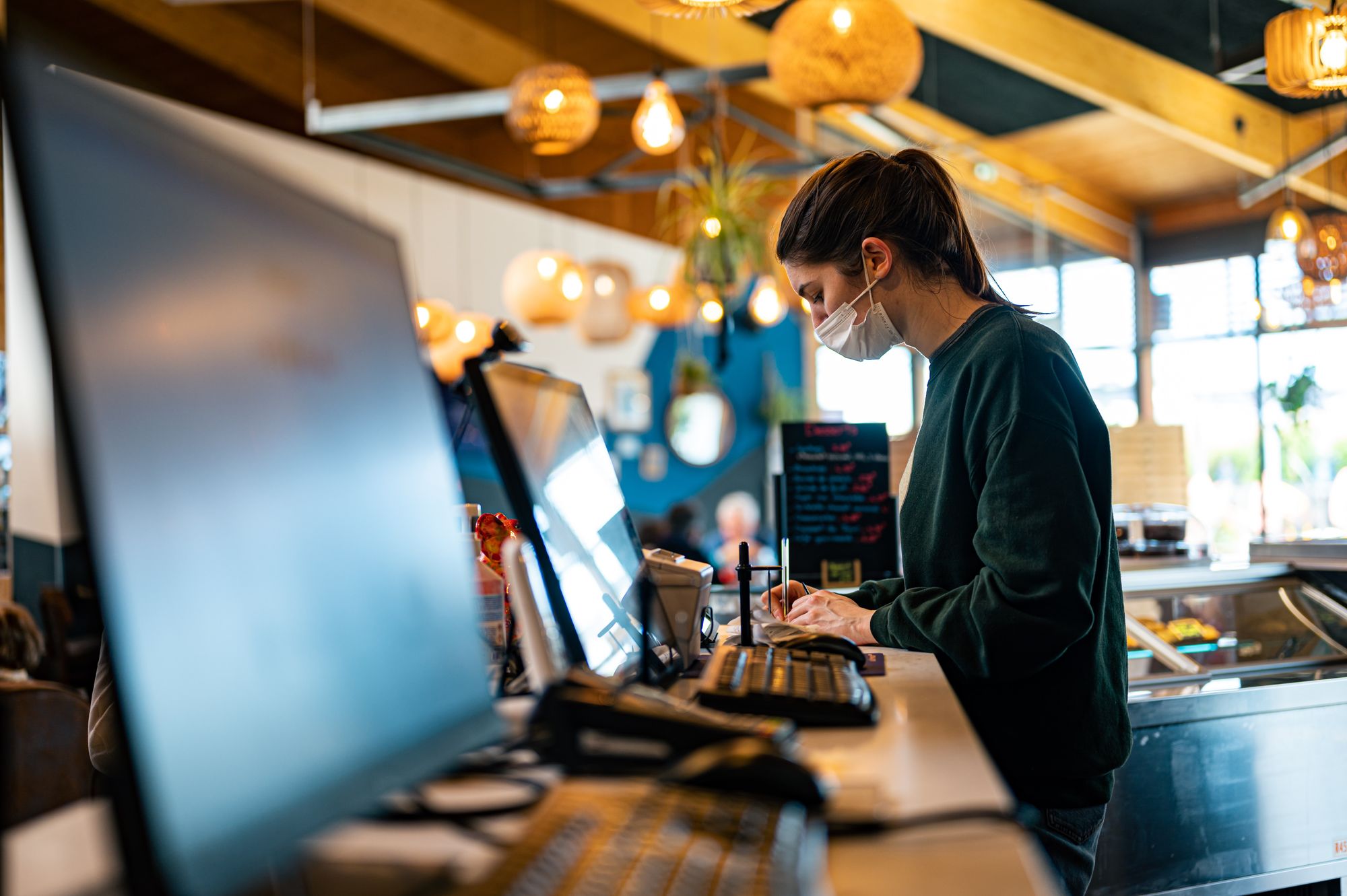
A multi-level BoM is a hierarchical list of parts and assemblies in two or more tiers assembly. For example, PCBAs, PC software, and hardware of the finished assembly. A single-level BoM, on the other hand, depicts an assembly at a lower level (e.g., PCBA).
In this article, we'll explore multi-level BoMs and all you should know to have more control over them. Following are the topics covered:
- What Is the Bill of Material?
- Multi-level Bill Of Materials
- What Is a Subassembly?
- Importance of Multi-Level Bill Of Materials
- 5 Benefits of Multi-level Bill of Materials
- Choosing Which Bill Of Materials Structure to Use
- Challenges With Creating Multi-Level Bill Of Materials
- Conclusion
- Key Takeaways
What Is the Bill of Material?
A product's structure is described in the bill of a material’s basic concept. A bill of materials or product structure is a list of the raw materials, sub-assemblies, intermediate assemblies, and sub-components.
It is a list of the quantities of each needed to make an end product. If we want to elaborate and gain a wider image, we can define it like in this wiki reference. "We can see that the BoM serves as a blueprint for any complex product."
- BoMs can be in the form of text files, spreadsheets, or databases and can be accessed by specialized software.
- BoMs are used in manufacturing, engineering, and design to help streamline the production process.
- They provide an at-a-glance view of the components and materials required for a specific product, allowing for quick and accurate ordering.
- BoMs provide a number of benefits, including improved accuracy and efficiency in the production process, improved inventory control, reduced costs, and better communication between teams. Additionally, they can help to reduce errors and simplify the tracking of changes and updates.
To ensure that BoMs are as effective as possible, it is important to keep them up to date and make sure that all relevant teams have access to the most current information. Additionally, keeping detailed records of changes and updates will help to ensure the accuracy of the information.
What Are the Different Types of BoMs?
There are two main types of BoMs, the Engineering BoM (EBoM) and the Manufacturing BoM (MBoM).
EBoM: Engineering BoM (EBoM) is a type of Bill of Materials (BoM) that provides a comprehensive representation of the product’s components, including their design parameters, materials, and other related information.
- An EBoM is the most detailed level of BoM which is maintained by designers and engineers, and it is the source of all other BoMs.
- EBoM is used to support the development, manufacturing and servicing of the product. It is also used to track and manage changes to the product’s design over time.
- EBoM is a hierarchical list of components and sub-components that make up a product. It includes information such as the name, part number, quantity, and unit price of each component.
- The EBoM is typically used in the engineering phase of a project. It is used to define the product’s design and ensure that the product meets all of its requirements.
- The EBoM is also used to generate the Manufacturing BoM (MBoM).
- EBoM is also used to support the service and maintenance of the product. It can be used to identify the parts that need to be replaced and the procedures that need to be followed.
MBoM: Manufacturing Bill of Materials (MBoM) is a document designed to provide a comprehensive listing of all the parts, subassemblies, components, and other materials required to build a product.
- It is an important tool in the manufacturing process, as it provides a comprehensive view of the parts needed, their quantities, and the order in which they should be used.
- MBoMs are used to improve communication between production and engineering departments and ensure accuracy in production.
- They can also be used to streamline production processes, reduce lead times, and increase quality.
- MBoMs can be used to reduce stock levels, improve inventory management, and provide data for vendor selection and management.
From very basic part lists to complex multi-disciplinary structures with a wide range of features at each level. One can design and manage all types of bills of materials. With regard to the definition of both simple part lists and complicated structures.
These BoM types provide you with complete flexibility. Three basic BoM types exist:
Single-level: Single-level BoMs (Bill of Materials) are used to represent the components of a product in a hierarchical structure. They are used to illustrate the relationships between each component and the overall product, and to provide a comprehensive overview of the product’s assembly.
- Single-level BoMs are the basic structure of most product documentation and are used in manufacturing, engineering, and purchasing processes.
- These line items are usually organized in the order of assembly, meaning that the first line item is the first component to be assembled.
- It's also easier to understand the bill of materials, since it's presented in a linear format.
- Single-level BoMs are ideal for small-scale production.
- They can become cluttered and difficult to manage if the product has many components.
Flattened (report): A flattened Bill of Materials (BoM) is a type of BoM structure which is simplified to a two-level structure and does not contain any of the complex subassemblies or components.
- It is typically used in manufacturing processes and product design, as it provides a streamlined and organized way to track and manage the parts of a product.
- In a flattened BoM, each component is listed separately and the quantity of each is listed in a single column.
- The structure of a flattened BoM is designed to reduce the complexity of a BoM, making it simpler for manufacturers to follow and easier for designers to create.
- Flattened BoMs are also beneficial for tracking inventory levels and ordering parts, as they make it easier to keep track of the parts needed for production.
Multi-level: Multi-level BoM (Bill of Materials) is a type of document used in manufacturing that outlines a product's components and sub-components.
- It is the hierarchical representation of individual parts and assemblies that make up a finished product. This makes it easier to manage inventory, as well as plan and organize production.
- It also helps to identify which parts are to be used in production and how they fit together.
- Multi-level BoMs typically have a hierarchical structure, with top-level components and sub-components listed in order of importance. This makes it easier to determine the assembly process and identify the necessary parts for each stage. We will discuss in-depth about Multi-level BoM further in the article.
Three different versions of the same product structure are represented by these B0M categories.
Fundamental Steps for Manufacturing Based on BoMs
Properly Managing the Bill of Materials (BoM): BoMs are a critical element in the manufacturing process and must be managed properly to ensure successful production.
BoMs are documents that list the parts, materials, and components that are needed to construct a product. They should be kept up-to-date and organized in an easily accessible format.
Establish a Production Schedule: Once the BoM is complete, the next step in manufacturing is to establish a production schedule.
This schedule should outline the steps necessary to produce the item, including the amount of time needed for each step. It should also provide an estimate of the total cost of the production process.
Obtain the Necessary Materials and Parts: Once the production schedule is in place, the next step is to obtain the necessary materials and parts.
This includes sourcing the components from suppliers, ordering the raw materials, arranging delivery, and ensuring that the components meet the specifications outlined in the BoM.
Assemble the Product: Once all of the materials and parts are secured, the next step in the manufacturing process is to assemble the product.
This step requires the use of specialized equipment to put the components together. It is important to ensure that the assembly is done correctly to avoid costly delays or mistakes.
Quality Assurance: Quality assurance is a critical step in the manufacturing process. This includes testing the product to ensure that it meets the necessary standards and specifications.
Quality assurance also includes inspecting the product for defects and ensuring that it meets the customer’s requirements.
Package and Ship the Product: The final step in the manufacturing process is to package and ship the product.
This involves preparing the product for shipping, labeling it correctly, and ensuring that it is delivered in a timely manner. Proper packaging and shipping are essential to ensure that the product arrives in optimal condition.
Perfect inventory is the basis for everything. If your organization lacks effective inventory control, you cannot even imagine implementing MRP. This implies that you have a method for:
- Opening new SKUs
- Tracking lot and serial numbers using barcodes or QR codes created by the system.
- You should also specify your warehouses (initial inventory, physical location, bins).
- To specify your vendors (lead time, purchase prices).
- To link your channels for sales (brick-and-mortar, eCommerce).
Multi-level Bill Of Materials
A multi-level BoM illustrates parent-child relationships and the hierarchical structure of product assemblies. It also illustrates the parts and components that go with them. A multi-level BoM's structure is like a family tree and lists all the parts and sub-assemblies for a product at two or more levels.
Every component that is directly or indirectly used in the manufacture of a parent item is listed at each BoM level.
Structure of a Multi-Level BoM
A multilevel BoM's structure, which depicts all the parts and sub-assemblies that go into making a product, is like a family tree.
- All the parts that are either directly or indirectly employed in the creation of a parent item are listed in detail at each BoM level.
- A BoM level, which will resemble a BoM tree, is where the acquired components and raw materials can also be discovered.
- Using SKUs to keep track of your inventory will make defining your multi-level BoMs much simpler.
- It can be challenging to come up with SKUs if you have a large number of inventory, though. Fortunately, you may go through this process with the use of SKU generators.
A multi-level bill of materials (BoM) is a hierarchical list of the components and materials that are used to assemble a product. It is a tool used to break down the required components and materials for a product into hierarchical levels.
- The first level of the BoM is the top level assembly, which is the complete product. Each component of the top level assembly is represented by a line item in the BoM. The line items in the BoM correspond to component assemblies, subassemblies and individual parts.
- The second level is the component assembly level. This is a list of the component assemblies and subassemblies that make up the top level assembly. The component assemblies may have additional components that make up the assembly.
- The third level of the BoM is the subassembly level. This is a list of the components that make up the component assembly. Each component is listed as a line item in the BoM with its own part number and description. This level of the BoM is used to identify each component that makes up the component assembly.
- The fourth level of the BoM is the individual part level. This is a list of the individual parts that make up the subassembly. This list includes all the individual components, such as screws, nuts, washers, etc. that make up the subassembly.
- The fifth and final level of the BoM is the raw material level. This is a list of the raw materials that are used to make the individual parts. This includes the materials such as aluminum, steel, plastic, etc. that are used to make the individual parts.
A multi-level BoM provides a detailed breakdown of the components and materials that are used to assemble a product. It is a tool that is used to organize the required components and materials into hierarchical levels. It is important to keep the BoM up to date in order to ensure that the product is assembled correctly.
Product Structure
- The easiest way to describe how components are broken down and how they relate to one another is through product structure.
- A collection of relationships between levels forms the basis of product structure. They are frequently referred to as "Parent-Child relationships".
- They serve to define the organization of assemblies, sub-assemblies, and components (parts).
Any sort of hierarchical structure is referred to as a DAG (direct acyclic graph – graph with no cyclic relationships ). Any type of hierarchical structure can use the abstraction level.
Indented BoM
An Indented BoM is a hierarchical representation of the components and parts that make up a product. It is used to provide an organized structure to the product’s assembly and is typically created in a spreadsheet or database.
The BoM typically starts with the top-level assembly and then “indents” each of the components and parts that make up the product. This makes it easy to quickly identify the parts and components of the product.
- Indented BoMs are typically used in the engineering process to document the assembly of a product or system.
- It creates a poor structure of levels because it follows the problematic Excel approach to handling structure. The problem is that it is a list of indented part numbers.
- It is generally used by engineers to describe how assemblies and components are put together.
- Indented BoMs provide a clear and organized structure for the product’s assembly, making it easier to quickly identify the components and parts of the product.
- The BoM is typically only displayed one level in many outdated systems, including MRPII.
The single-level BoM shows a component list for each assembly. You have the option to dig down, level by level, even though each item in the list may be a Part Number of another assembly. Thus, multi-level is the moniker that results from this process.
Parent-Child Relationships
Parent-Child Relationships in a Bill of Material (BoM) are used to define the relationship between a parent assembly and its components or sub-assemblies. It is used to define the hierarchical structure of a product and its sub-components.
- The parent-child relationship in BoMs provide a clear view of the product hierarchy, allowing for better management of the supply chain and overall product design.
- It also helps to keep track of the inventory of components, ensuring that the correct components are used in the correct assemblies.
- Parent-Child Relationships are used in a variety of industries, including automotive, electronics, aerospace, and medical device manufacturing.
- The relationships can be used to define the relationship between components, assemblies, and sub-assemblies, as well as the relationship between components and the finished product.
- Parent-Child Relationships in BoMs are important as they help to ensure that the correct components are used in the correct assemblies.
- This allows for a higher level of accuracy in the manufacturing process, as well as providing more efficient and cost-effective production.
An example of a parent-child relationship in a BoM would be a car. The parent assembly is the car itself, while the child assemblies would be the engine, wheels, and other components. The relationship between the car and the engine is defined by the BoM, as the car must contain the engine to be operational.
What Is a Subassembly?
This can be summed up by saying that many parts are combined to create a unit that can be employed as a part of a larger assembly or a final product. A sub-assembly can also serve as a finished good that is either used to complete the production of another good or sold separately to clients.
- Understanding sub-assemblies is crucial since they play a crucial role in creating your multi-level BoM.
- To create your indented bill of materials, you will need a thorough understanding of your materials and components. This includes your components and sub-assemblies.
- Consumer electronics include a wide range of products that use electronic sub-assemblies. Sub-assemblies are found in small home equipment like microwaves and portable media players.
- A microwave's real control panel, electrical plugs, and heating elements are all inside the appliance.
Smaller pieces or sub-assemblies may be found in any of these three sections. Here is a summary of the sub-assembly procedures.
- An assembler will locate the parts or components from the inventory and deliver them to the sub-assembly station. The assembler will then start the sub-assembly process.
- After the parts arrive at the sub-assembly station, they are linked and fastened to create the finished sub-assembly. Sub-assemblies that are complete are put onto carts or racks.
- Sub-assemblies that have been finished are subsequently supplied lineside. By delivering the appropriate parts to the appropriate location at the appropriate time.
- Lineside delivery aids in increasing production and efficiency. It is significant to remember that delivery frequently takes place within a single site. It can also happen between industrial plants.
- The finished sub-assemblies are then added to the finished item.
What Are Sub-Assembly Examples?
Sub-assembly examples will resemble a BoM tree made up of your raw materials, components, and sub-assemblies. This was discussed earlier in the article. Your finished product (or parent product/level 0) will be at the top of your tree.
All your sub-assemblies and their connections to the parent product branch off from there. Sub-assembly examples refer to components or parts of a larger assembly or system. Sub-assemblies are used to assemble larger systems, as they are typically easier to transport, handle, and store than the full assembly.
- Common examples of sub-assemblies include motors, pumps, valves, and other mechanical parts.
- Electrical sub-assemblies are also common, such as circuit boards and wiring harnesses.
- Sub-assemblies may also include peripheral components such as sensors, switches, and connectors.
- Sub-assemblies can be stand-alone components or they may be integrated into a larger system.
- A motor may be part of a larger pump assembly or it may be sold separately.
Examples of sub-assemblies for a bicycle will resemble these: As you can see, complex sub-assembly examples go into great detail to prove what specifically goes into the end product. They also show their inventory levels and the process that must be adhered to make that product.
Importance of Multi-Level Bill Of Materials
There are many things you must complete to set up your operation so that production runs as smoothly as possible. This will help you avoid slowing down production in the future. This entails selecting the most effective manufacturing routes. This will improve your manufacturing inventory control.
One document, yet, must be prepared well in advance of the start of production. The bill of materials (BoM), sometimes known as the product recipe, is the product's genetic code. The following are the goals of having a multi-level B0M:
- Overview of Assemblies: The goal is to have more specific information about the parent and child assemblies in the product. As well as the precise connections between the sub-assemblies and the end item.
- Avoid Mistakes When Working with Sub-Assemblies: As your manufacturing company grows, it may be required to divide your products into sub-assemblies. And those into smaller sub-assemblies and components, and so on. This will be crucial in avoiding mistakes and supporting precise part tracking.
- Improved Accuracy: The most important benefit of using an multi-level B0M is that it helps to ensure that all the parts needed for the production of a product are available and in the right quantities. This helps to ensure that the product is produced accurately and efficiently, reducing the potential for mistakes or delays.
- Increased Efficiency: By having a clear overview of all the components needed for a product, businesses can plan their production processes more efficiently. They can identify areas where resources may be wasted and where processes can be streamlined or improved. This helps to reduce costs and improve the overall efficiency of the production process.
- Increased Visibility: Using an multi-level B0M provides businesses with a comprehensive view of all the components needed for the production of a product. This helps them to identify any potential problems or delays in the supply chain. They can quickly identify where there may be a shortage of parts or materials and can take steps to address the issue.
- Improved Quality Control: By having a clear overview of all the components needed for a product, businesses can ensure that high-quality materials are used. They can also identify any potential problems with the quality of the components being used in the production process and take steps to rectify them. This helps to improve the overall quality of the product.
As you can see, to have better control over your multi-level BoMs, it is critical to understand what a sub-assembly is.
5 Benefits of Multi-level Bill of Materials
A multi-level bill's five benefits are:
- Enhanced Cost Control: A multi-level BoM helps to improve cost control by providing a clear view of how costs are assigned to each component of a product. This allows companies to accurately track costs and identify areas where cost savings can be made.
- Improved Quality: By providing a detailed view of a product’s components and materials, a multi-level BoM enables companies to monitor the quality of their products. This can help to ensure that products meet required standards and reduce the chances of customer dissatisfaction.
- Improved Traceability: A multi-level BoM can also improve traceability. This means that if a component fails, it can be easily identified and replaced. This can help to reduce downtime associated with product failures.
- Improved Collaboration: By providing a clear view of a product’s components and materials, a multi-level BoM can help to improve collaboration between departments. This can help to ensure that all components are sourced, assembled, and tracked efficiently.
- Improved Inventory Management: Multi-level BoM helps businesses to keep accurate records of their inventory. It enables them to track the components, parts, and assemblies that go into each product. This allows them to ensure that they have the right parts and materials in stock when needed.
To increase efficiency and close the gap between the shop floor and the top floor, more manufacturing organizations are taking efforts. They are shifting their inventory and manufacturing process management onto business software.
This is a major shift in the current digital era. The right software can assess the demands of businesses of all sizes and deliver a solution to meet those goals. If your company could gain from a solution to assist in managing your manufacturing operations. Whether it be anything from managing several levels of bills of material to many sites for inventory.
Choosing Which Bill Of Materials Structure to Use
It is crucial to take into account both the type of product you build using the B0M and who will be using it. This is done by defining the BoM structure that best meets your needs. Think about the following issues:
- Will engineering use of your BoM occur internally?
- Will a contract manufacturer, a business partner, or other team members have access to your BoM?
- What kind of products do you manufacture?
- What are your products' levels of complexity and customizability?
The structure of your bill of materials should take into account a number of essential elements, including these. Following, we go into greater depth on each of these.
Depending on the engineering field, the BoM structure for internal engineering use may change. A BoM with nested sub-assemblies is frequently preferred by designers and mechanical engineers.
The sub-assemblies can be used in a variety of product configurations. In these situations, the BoM frequently shows components that were specially created for the product. It also gives important details about its structure.
Electrical engineers favor un-nested BoMs. This is because they typically include commercially available components. The engineer in this case cares more about the schematic—the way the parts are connected—than the overall layout of the bill of materials.
- Utilizing a BoM with some structure might be beneficial. This is especially true when sharing BoMs with a contract manufacturer, partner, or collaborator.
- You can isolate particular subassemblies within your BoM by nesting and creating subassemblies. This allows you to share only the design data that your partner or CM needs to see.
- If your partner is assisting you with a design, you may decide to reveal only the portions of the subassembly that pertain to their contributions. This safeguards the intellectual property connected to the other facets of the product design.
- When you have complicated and highly configurable items, a layered BoM is also beneficial.
- If your BoM is organized with many indentation levels, updating a sub-assembly within a larger product assembly can be completed rapidly.
- An engineering change order (ECO) only needs to address a part of the product. The sub-assembly can be altered as needed and applied to various higher-level assemblies.
- The higher-level assemblies only need to be changed up the product structure tree to that point.
When your products need parts with extended lead times, large inventory costs, or single-source vendors. A tiered BoM can also lower risk.
A BoM with subassemblies gives your operations team more visibility. It gives more ideas for assemblies and subassemblies that might need extra work. It also enables them to identify potential alternatives to pricey items.
In the end, this structure might assist in addressing issues that might develop before to or during the production process. You may more accurately choose the BoM structure that is best for your firm by considering the stakeholders who use the BoM. You may also consider the kinds of products you manufacture.
Setting Up Critical Component Items from a Multi-Level BoMs
From a multi-level BoM, put up important component elements as follows:
Step 1- Open the Multi Level Critical Components Bill of Material Inquiry form.
Step 2- Fill in the appropriate values in these fields:
Number: Enter the number that the computer system gives an item. It can be formatted as a short, long, or third-item number. This field must be filled out.
Branch/Plant: If you want to track costs for a distinct entity within a business, enter an alphanumeric code that identifies it. A business unit could be a warehouse site, a task, a project, a work center, a branch, or a plant, for instance.
For responsibility reporting purposes, you can appoint a business unit to a piece of writing, an organization, or an individual. A different option is to include the branch/plant in an enhanced query. You might be unable to access information about business units over which you have no control due to business unit security. This field must necessarily be filled out.
Batch Quantity: The number you enter should be the approximate number of finished units that you expect this bill of materials or routing to produce. In accordance with the number of finished units that have been created. You might specify various component quantities.
Consider the scenario where 100 units of the finished product can be produced using a maximum of one ounce of solvent. You need two ounces of solvent for every unit of the finished product if 200 are made.
By indicating the proper quantity of solvent for each unit, you can configure batches for both 100 and 200 units of the end product. UOM (unit of measure) To express the quantity of an inventory item, enter a user-defined code (00/UM), such as CA (cases) or BX (box).
As of Date: Type the date that was used to check the effectiveness. If you provide a specific date, all papers that take effect on or after that date will be displayed. The papers include orders, bills of material, and routings, as appropriate. You can input any past or present date; the default is the current system date.
Step 4- Utilizing the QBE lines, add any additional requirements that apply.
Step 5- Select Find.
Step 6- Choose a valid batch quantity on the Bill of Material Selection form (optional).
Step 7- Decide which objects to include as important component elements.
Step 8- Select OK.
Best Strategy For Managing A Multi-Level BoMs
Any company that operates in the industrial sector needs to pay close attention to inventory management. That holds true for both. The number of finished goods in your stockroom and the raw materials in your warehouse are required to produce additional goods and restock your supply.
A multi-level bill of materials (BoM) provides an in-depth description of all the pieces that make up any product you sell.
It is necessary to make sure you have the necessary supplies on hand to fulfill forthcoming orders and keep your customers happy. Yet, how should they be handled in a busy company where there are many responsibilities to balance at once?
Get Rid of the Spreadsheets
This is the first step in organizing and streamlining your multi-level BoM management. It is to abandon outdated and ineffective procedures.
- Microsoft Excel might be useful while you're just starting out, but there are a variety of reasons why it isn't suitable for use in the long run. The complexity of multi-level BoMs makes them difficult to calculate accurately in a spreadsheet.
- There is a high potential for human mistakes. It is also difficult to add product variants.
- Spreadsheets aren't ideal for modern businesses for a variety of other reasons. But the ones mentioned above are particularly important when it comes to multi-level BoMs.
Use SKUs
Do you know what SKUs are? A stock-keeping unit, or SKU for short, is an alphanumeric designation that is allocated to each item in your inventory. This allows you to rapidly distinguish between them and identify them more effectively.
- SKUs can help you better comprehend and analyze the stock you have on hand while also putting things in a format that is easier for a computer to use.
- There are many advantages machine learning can offer your business. It makes sense to use SKUs to streamline your multi-level bill of materials as much as you can.
- This will not only help organize the information you have available. It can also speed up the processing of that information and raise the efficiency of your business as a whole. And you are aware of the adage "time is money" in business.
Select Software for Smart Manufacturing
Use multi-level bill of materials software that has been designed for the task. Rather than trying to fit round pegs into square holes with a spreadsheet.
Deskera foresees every difficulty you might run into while attempting to understand a complex BoM. It helpfully offers solutions to each one in convenient packaging.
- It has a user-friendly style and intuitive interface.
- The software enables you to quickly and easily generate a multi-level BoM.
Deskera is a one-stop shop for keeping track of all the comings and goings in a successful SME and optimizing your business for success. It is capable of integrating with other aspects of your operations, such as sales and accounts.
Challenges With Creating Multi-Level Bill Of Materials
Creating a multi-level bill of materials (BoM) is a complex task for any organization. A BoM is a comprehensive list of materials, components, and assemblies used in the production of a product. It is an important document for monitoring, tracking, and managing the manufacturing process. However, creating a multi-level BoM can be a challenge due to the following points:
- Lack of Visibility: A multi-level BoM requires all the components, parts and materials used in the production of a product to be visible. This can be difficult to achieve, especially if the organization has multiple suppliers and vendors. It is important to ensure that all the components, parts and materials are visible in the BoM in order to be able to accurately track the manufacturing process.
- Data Accuracy: Data accuracy is a key challenge when creating a multi-level BoM. The BoM must be kept up-to-date with accurate and up-to-date information about the components, parts and materials used in the production of the product. If the BoM contains inaccurate or outdated information, it can lead to costly errors and delays.
- Complexity: Creating a multi-level BoM can be a complex task due to the number of components, parts and materials used in the production of a product. Each component, part and material must be accurately tracked and monitored, which can be difficult to do manually.
- Cost: Creating a multi-level BoM can be a costly process as it requires a significant amount of time and resources. It can also be difficult to manage costs associated with the BoM if the organization does not have the right tools and resources.
Creating a multi-level BoM can be a complex and challenging task, but it is essential for the successful manufacturing of a product. It is important to ensure that the BoM is kept up-to-date with accurate and up-to-date information and that the organization has the right tools and resources to track and manage the manufacturing process.
Will all occurrences of a part in the BoM be updated, for instance, if the part number for a part for one product is updated? This can be at different BoM hierarchy levels.
Challenges in Spreadsheet for Managing Multilevel BoMs
Some producers who are just starting to manage product information frequently use spreadsheets. A multilevel BoM spreadsheet can be saved and kept. Although using a spreadsheet to manage your multi-level bill of materials can seem like the ideal option, is it really?
- Understanding the BoM Structure: One of the major challenges in spreadsheet for managing multilevel BoMs is understanding the BoM structure. It can be difficult to visualise how a BoM is laid out when it is represented as a spreadsheet. This can lead to mistakes being made when entering data into the spreadsheet, which can be costly and time consuming to rectify.
- Complex Calculations: Spreadsheets are often used to calculate the cost of a multilevel BoM, but this can be a difficult and labour-intensive process. Complex calculations such as quantity discounts, taxes, and currency conversions can be difficult to manage in a spreadsheet, and errors can easily occur.
- Manual Data Entry: Manual data entry can be a time consuming and tedious process, especially when dealing with multilevel BoMs. Data entry errors can easily be made, which can lead to costly mistakes.
- Version Control: Version control is a major challenge when using spreadsheets to manage multilevel BoMs. It can be difficult to keep track of the different versions of a spreadsheet, and this can lead to discrepancies between the different versions.
- Lack of Automation: Automation can save time and reduce errors when dealing with multilevel BoMs, but spreadsheets lack this capability. Automated processes such as data validation, data extraction, and data analysis can be difficult to achieve in a spreadsheet.
- Limited Security: Spreadsheets lack the security features that are often required when dealing with sensitive data. This can lead to data breaches, which can have serious consequences.
- Inadequate Reporting: Spreadsheets are not designed for reporting, and this makes it difficult to generate accurate reports from multilevel BoMs. Reports generated from spreadsheets can be difficult to read and interpret, and it can be difficult to identify trends or issues.
- Error-prone: BoMs stored in inefficient spreadsheets can be plagued with faults and will need to be regularly updated manually. This will consume a lot of your resources. These issues can range from copy/paste mistakes to more intricate macro and script issues.
- Tough to Add Variations: Adding your possible product versions is challenging. When a product has many variants, managing it in spreadsheet can be challenging. The number of resolved BoMs will increase with the number of variants, quickly becoming unmanageable.
- Determining Prices and Quantities: It may appear straightforward to calculate totals in spreadsheet, and for flat or single-level BoMs, it is. Yet, it becomes more challenging when working with multi-level BoMs. The following are just a few of the requirements needed to calculate costs and quantities for multi-level BoMs.
It includes many setup steps, complicated formulas, and VLOOKUPs. This consumes significant time that could be spent on other crucial duties, and as the complexity rises, it increases the risk of mistakes.
Spreadsheets are excellent tools for examining numerical data. Yet, combining BoM quantity and cost information in a spreadsheet can become difficult. This is especially true when parent-child connections are deeply nested.
You may want to start by providing answers to a few questions if you intend to use spreadsheets to manage multiple BoMs.
- Can the hazards associated with manual data entering be reduced?
- Will your organization have an issue if it can't swiftly acquire expense data?
How can Deskera Help You?
As a manufacturer, you must keep track of your inventory stock. The condition of your inventory has a direct impact on production planning, people and machinery use, and capacity utilization.
Deskera MRP is the one tool that lets you do all of the above. With Deskera, you can:
- Control production schedules
- Compile a Bill of Materials
- Produce thorough reports
- Make your own dashboard.
Deskera ERP is a complete solution that allows you to manage suppliers, track supply chain activity in real time, and streamline a range of other company functions.
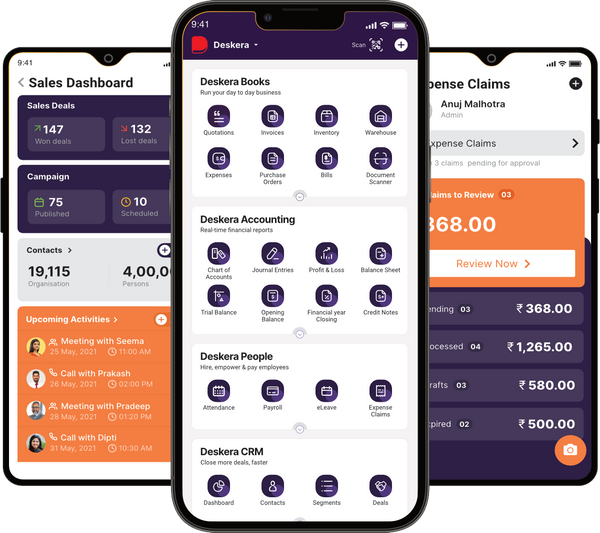
Deskera Books allows you to manage your accounts and finances better. It helps maintain good accounting standards by automating billing, invoicing, and payment processing tasks.
Deskera CRM is a powerful tool that organizes your sales and helps you close deals rapidly. It enables you to perform crucial tasks like lead generation via email and gives you a comprehensive view of your sales funnel.
Deskera People is a straightforward application for centralizing your human resource management activities. Not only does the technology expedite payroll processing, but it also helps you to handle all other operations such as overtime, benefits, bonuses, training programs, and much more.
ERP Manufacturing Software for Multi-Level Bill Of Materials Management
Your manufacturing company will have more control over your multi-level BoMs if you choose ERP manufacturing software. Such as the one provided by Deskera.
Deskera has a bill of materials program which centralizes your whole organization. From your sales channels to your production operations. All of this is done onto one, crazily simple-to-read, visual platform.
Deskera provides manufacturers with the tools they need to have better control over their multi-level BoMs. With accurate costings going different layers into the BoM level.
Conclusion
A multi-level bill of materials is a list of all the parts, materials, and sub-assemblies that go into the construction of a product. BoM is also known as an indented bill of materials.
The hierarchical BoM structures will display your finished product. It also includes your SKUs, part descriptions, quantities, costs, and any other specs. These are displayed at the top of your multi-level BoM.
Multilevel Bills of Materials (BoMs) are a crucial component of production. They are particularly important for companies that use many sub-assemblies to create their finished products.
Key Takeaways
- When we manufacture final goods, a mixture of semi-finished products, raw materials used at that stage, etc. may be employed. Thus, a multi-level bill of materials enables us to dissect the product structure down to a level.
- Finding material requirements planning software is the largest challenge faced by manufacturing companies. The software is used by both large and small manufacturing companies.
- It's crucial to research raw material inventory management to get better control over your inventory movements. This is particularly important for those who work with complex BoMs.
- To prevent your production floor from completely shutting down owing to being understocked or a bottleneck arising when building a sub-assembly, you'll need to maintain stock levels. You'll also need to design a smooth production flow for a multi-level BoM.
- A multi-level BoM is essentially a nested list of parts and assemblies in two or more levels of the finished assembly. For example, hardware, software, and PCBAs). A single-level BoM, on the other hand, depicts a lower-level assembly (e.g., PCBA).
Related Articles
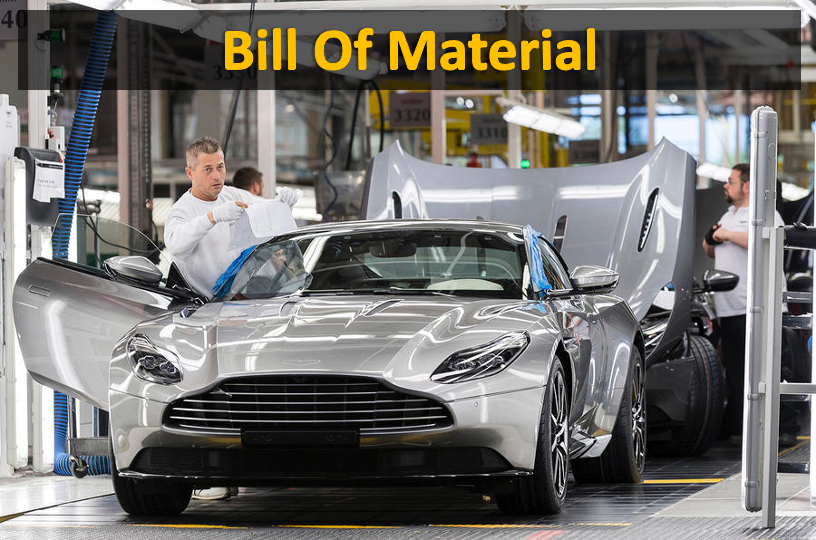
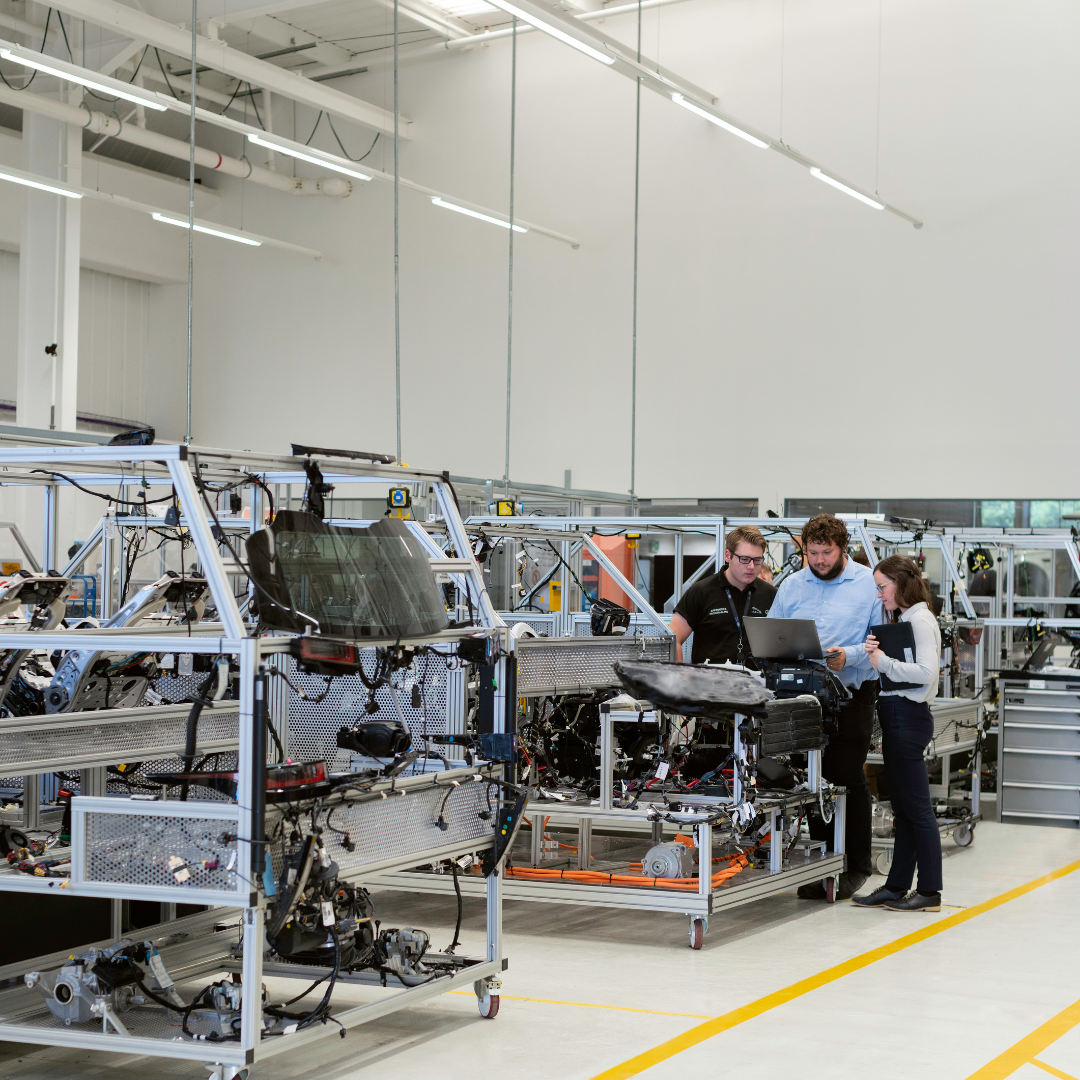
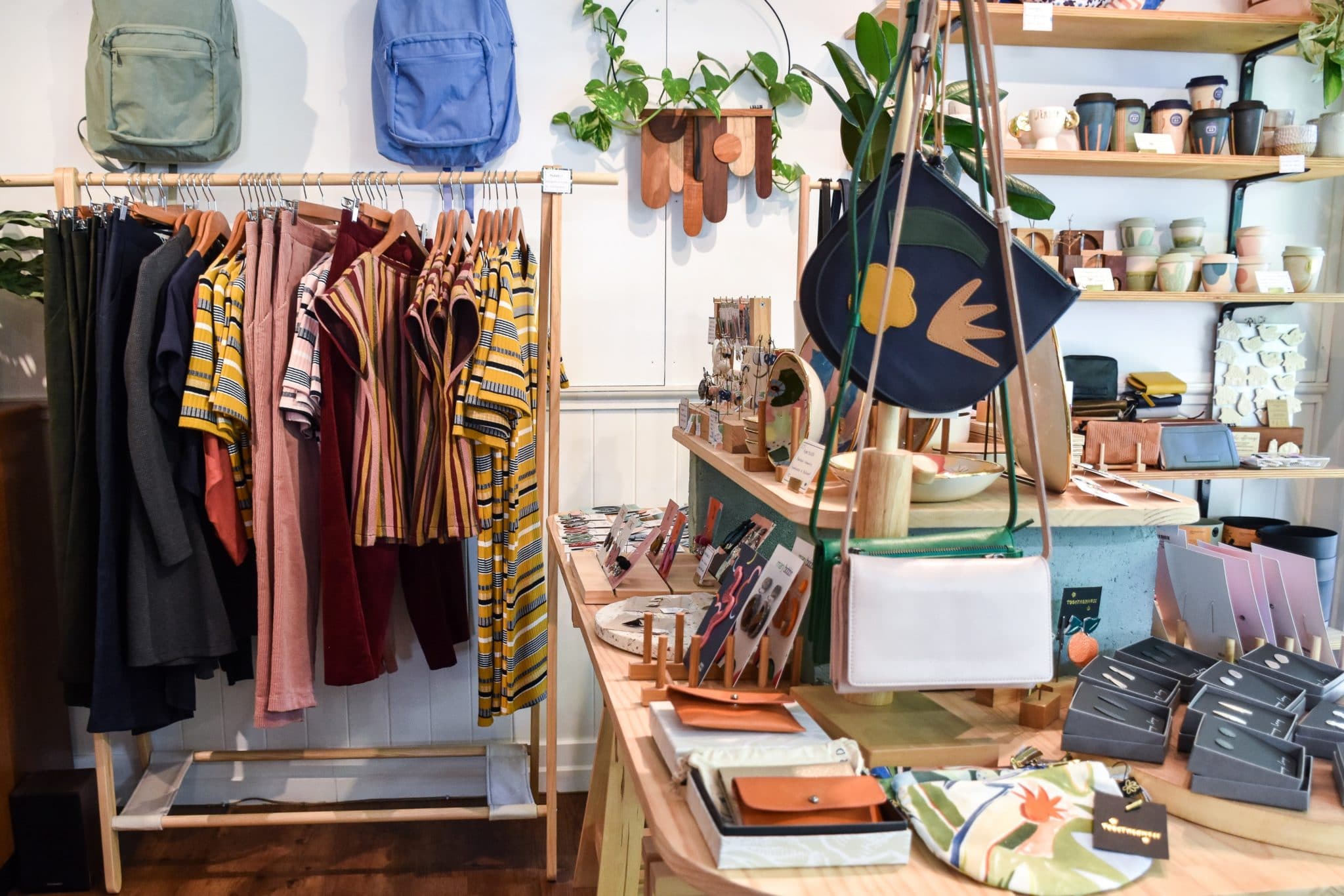
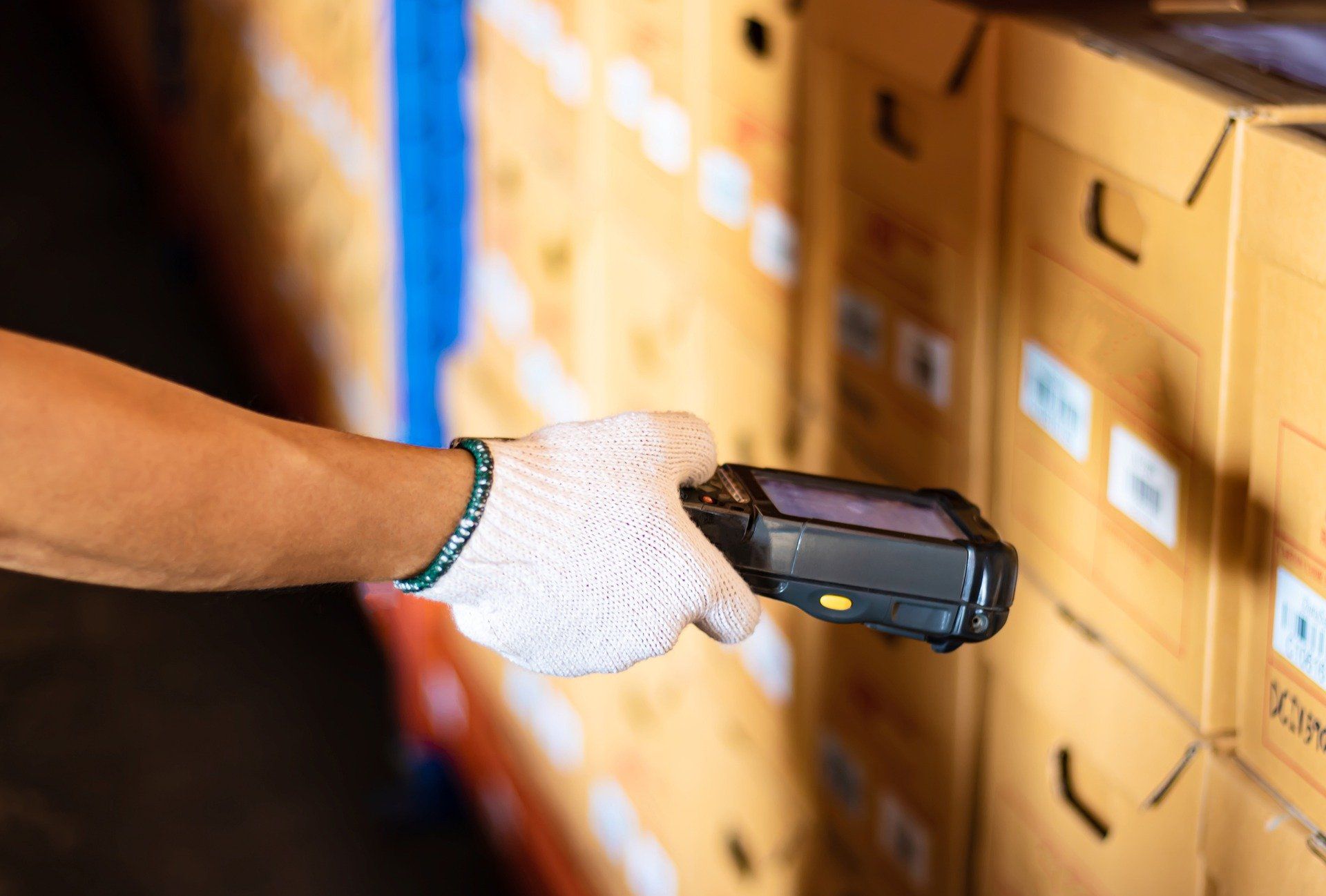