Stocks, Inventory, Goods, Products, Items, Material, etc - these are the few names by which Inventory is commonly referred to by various businesses across the globe.
The nature of inventory items varies with each business segment. The business needs dictates how the stock is tracked, whether by batch, serial or SKUs.
The key aspect here is to understand how you want to utilize these stock items for each transaction.
Inventory is the materials, work-in-progress goods and final product that businesses sell in order to generate revenue. Without inventory going out, there is no money coming in.
Even more important than just having or not having inventory, is keeping track of inventory. That is the key to running an efficient and profitable business. Poor or bad inventory management is one of the top reasons why small businesses fail.
Inventory mismanagement is rampant across the industry despite operations managers, employees, and companies' best efforts. Mismanagement results in canceled orders due to inventory shortages, which in turn, lead to revenue losses.
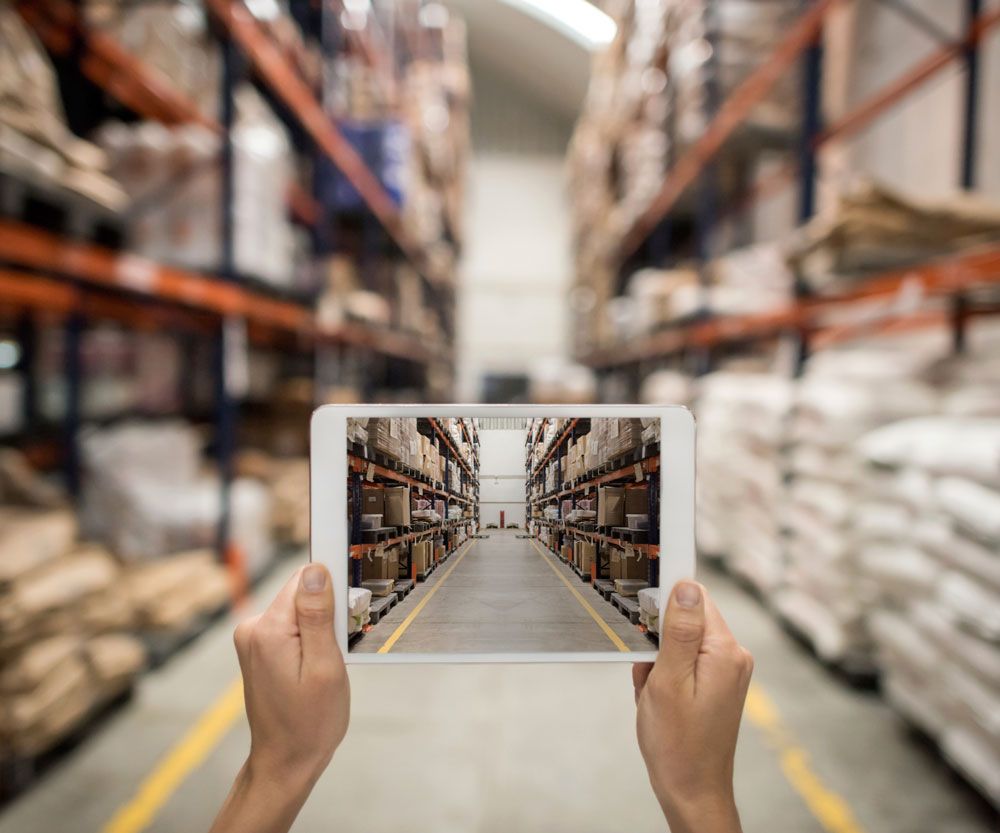
There are three ways of managing Inventory -
Batch Management
Serialized Inventory Management
SKU - Stock Keeping Unit
However, before we go into different inventory management methods, let us explore how businesses look at inventory and examples to different kinds of products.
Different Business Use Cases of Inventory
A business selling Pens needs to know the stock level of each brand and each type of Pen. For this business, what matters is which brand of pens sell the most. If any pen is damaged, they can simply return it to the parent company.
Consider another example of a business that sells Flour. This business cannot differentiate between 2 sacks of flour, if one of them turns out to be damaged, how do you identify its source? Both these sacks could have been produced in a different month or using a different type of Whole Wheat.
For such businesses, tracking is impossible unless they tag another detail with each sack of Flour. This detail is also known as “batch number” or “lot number”.
The batch number is a code that contains month, year and possibly the quality of wheat used. If we attach Batch number Jan20/Q1 to Sack 1 and Oct20/Q1 to both these sacks, we can understand the sack with an older batch date got damaged due to ageing.
Let’s look at a 3rd type of example.
A business selling hard disks of Brand A finds out of 10 hard disks it has, one does not work. All 10 hard disks are of Brand A and 1 Tb capacity. How do we differentiate between these 10 hard disks? The answer is simple - Serial Number.
Tag a unique serial number to each of the hard disks and identify the source from where it was purchased. The supplier or the manufacturer will then use this Serial Number to find out about the damaged product.
Let’s look at the 4th type of example.
A business selling shirts of various brands, sizes and patterns. Let's consider a Brand A, Pattern B and Size 42. There are over 200 pieces of this available in stock. One of them is found to be damaged.
How do we find out the piece that got damaged was made from which batch of cotton?
Each of the 200 pieces of this shirt with the same pattern and sizes could have been manufactured at different times using different raw material quality. This raw material could have been further procured from different suppliers.
How do you isolate and identify the required back trail parameters?
To answer this question, we attach an SKU Code as well to each of the shirt pieces and Brand, Pattern, Size and Batch number.
Now let us look more into our different management methods using the business cases and examples provided above.
What is Batch Management?
We saw in our previous segment an example, a business segment where Batch management is required.
Batch Management is typically applicable for the FMCG industry, i.e. Fast Moving Consumer Goods. It is difficult to differentiate between 2 pieces of the same FMCG product, especially when you need to backtrack to find its source.
The finished good in this case cannot also be dismantled to get its raw materials for analysis. That is where batches come in.
By tagging a logical batch number to every product, the entire supply chain for the product can be tracked. Batches also help track the expiry dates of 2 pieces of the same product.
To understand this, consider 2 milk cartons in your refrigerator. If batch numbers were not known for them, how would the supplier tell which carton was made at what date. Thus the batch number with expiration date on each of the cartons helps you identify the expired product.
Whenever goods of the same type are needed to be distinguished from each other, and no other physical distinction is feasible, neither is it possible to separate out its constituent raw materials, batch numbers are utilized. Batch management is thus utilized for homogeneous products.
Some other business segments where Batch Management is used to track Inventory are as below
● Chemicals
● Pharmaceuticals
● Cosmetics
● Health Care
● Foodstuffs
● Retail
● Aerospace
● Mill Products
● Mining
What is Serialized Inventory Management?
In the business use case section of this article, the third example we examined pertained to serialized inventory management. This is typically used in electronic and electrical products.
The need arises when every single unit of a product produced needs to be uniquely identified, including its components.
Many accounting systems offer the facility to track Serial Numbers for inventory goods. These systems allow users to import the entire list of serial numbers for a particular stock item when moving them to the warehouse. At the same time, with every sales invoice and delivery order, the unique serial number of the product being sold is also mentioned.
Serialized inventory offers various advantages, due to which it is used in the respective industries. Let’s look at a few of these advantages
- Product Traceability - allows owners of the product to be able to track their products in case of repair, maintenance and even theft. Serial numbers are useful for the manufacturers to identify ownership and validity of support related details
- Warranty & Guarantee - warranties and guarantees are valid till a certain amount of time. Every serial number can be tagged with a warranty validity date to enable the manufacturer track its service costs
- Quality Control and Recalls - each serial number uniquely identifies the product. Hence the manufacturers can track quality defective products easily. In the automotive industry, every vehicle is given a unique vehicle registration number, which is the Serial number. They can track if some vehicles need to be recalled and the serial number helps them identify the car owners
Under serialized inventory management, accounting systems allow you to track each product's entire cycle from its purchase to its sales. The support team can also pull out records of a particular serial number and track its history. Such tracking enables them to find out past faults reported or warranty validity details.
What is SKU - Stock Keeping Unit?
Lastly we will discuss SKU based inventory management. As discussed in our 4th example, it is important for the garment industry to uniquely identify each individual garment. The garment, say a Shirt has various parameters like - brand, size, color, design, pattern etc. Each SKU code helps uniquely identify each garment or lifestyle product. For example if there’s a garments brand called Deskera, with Red color, Polo Neck Tshirt size 42, its SKU code can be something like - DSK-R-PN-42.
Such SKU codes help sellers and manufacturers identify the product being talked about clearly and are able to provide resolution quickly. Furthermore SKU codes are often mixed with Batches in order to track the date of manufacture, supplier code, raw material related information, country of origin etc. This further increases the precision with which any manufacturer is able to identify his product.
In order to maintain SKU wise stock, accounting systems today offer various advanced features at Product master level. These features allow you to define various SKU codes and track inventory based on each code.
There are various advantages of maintaining SKU wise inventory. Let’s discuss few of these examples
- Precision - SKU code gives precise information about product sales. The business owner can find out which of his stocks are selling more, while which ones are selling the least.
- Reorder levels - with SKU code, the warehouse team is able to define reorder levels more accurately. In the absence of SKU code, they had to reorder all sizes, patterns, colors without any statistics. With SKU based inventory management systems, your stock levels can be maintained and reordered at the right level
- Fastens warehouse operations - with SKU barcodes available, the right set of products are picked, packed and shipped exactly as per customer order
- Better suited for multi channel sales - for businesses who want to sell on eCommerce platforms, SKUs are essential. They help their customers identify and buy the exact product they require in the color, brand and size of their choice
- Better customer service - especially for in store sales, if your customers are unable to locate a particular product in their size, a quick search using the SKU code can help you find all the information you need. Inform your customers about availability of their chosen product and if it can be sourced from another store.
Our Conclusion
We have gone through various methods in which Inventory or Stock can be maintained. This depends on the industry or business segment, as well as the nature of the goods.
The most important aspect is for a business to understand the stock reports and traceability they require for the products. This helps them understand which attributes of a product do they require, and if they need to be defined uniquely for each quantity purchased, or for each purchase instance.
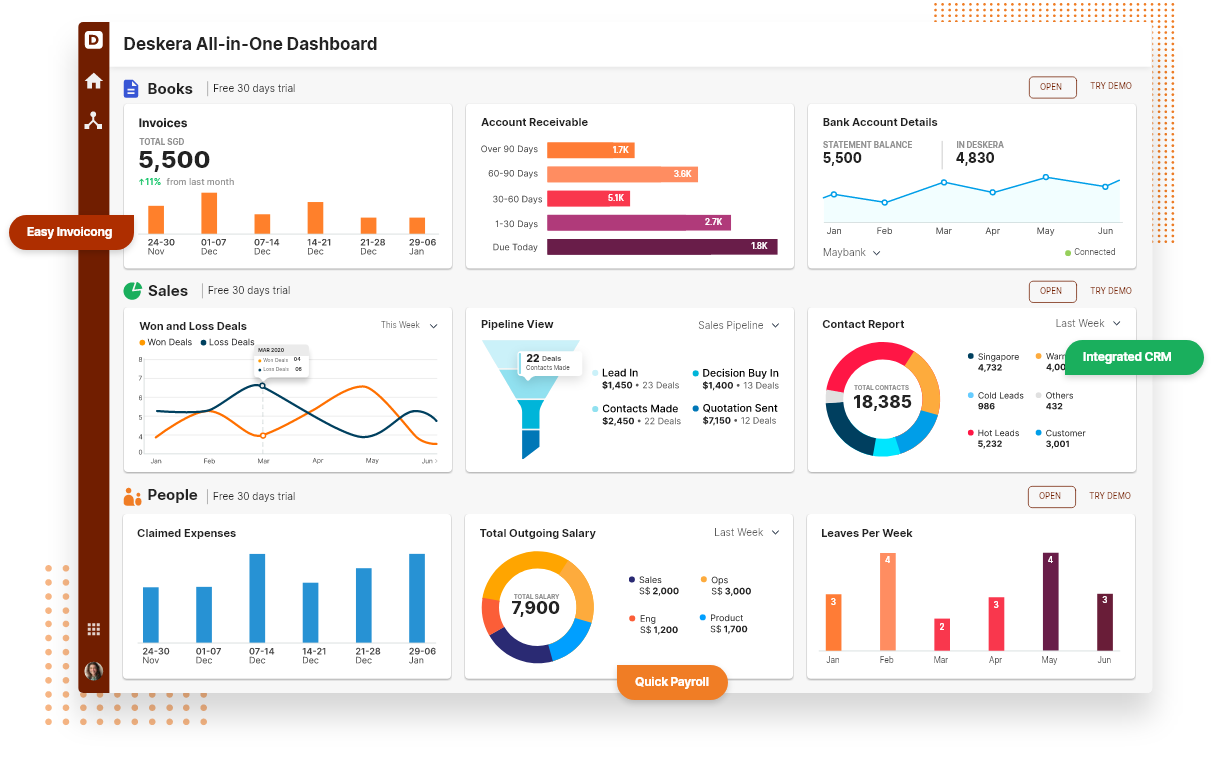
An inventory management system (or inventory system) is the process by which you track your goods throughout your entire supply chain, from purchasing to production to end sales.
It governs how you approach inventory management for your business. A lot of accounting systems help you maintain your Inventory in each of the above mentioned manners, helping you automate your inventory management process. It is highly recommended to use good inventory management software like Deskera can help with your business.