A survey by Gartner found that implementing a culture of quality across the organization can lead to significant benefits for firms, including improved customer satisfaction, increased revenue, and reduced costs due to fewer errors and defects. (Source: Gartner, "Implement a Culture of Quality to Improve Business Performance," 2020)
In fact, according to a report by McKinsey & Company, firms that prioritize quality management are more likely to achieve long-term growth, with top-performing companies reporting a 26% higher return to shareholders than their peers. (Source: McKinsey & Company, "The case for quality: Quality matters more than ever in uncertain times," 2020)
A study by the National Institute of Standards and Technology (NIST) found that a lack of quality control processes can lead to significant costs for firms, with errors and defects costing U.S. manufacturers up to 4.5% of their total revenue. (Source: NIST, "The Cost of Poor Quality," 2021)
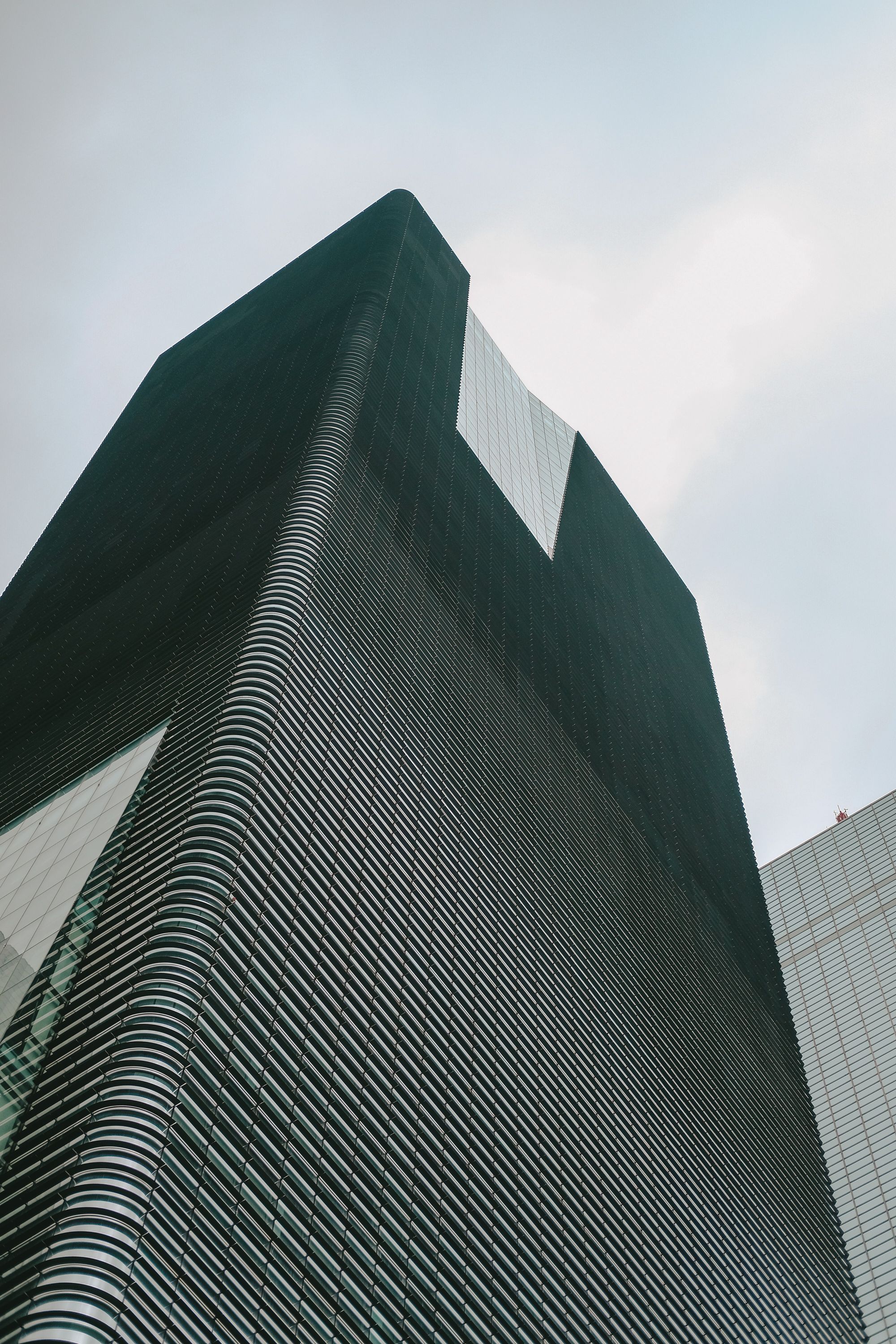
Lastly, a report by Deloitte found that implementing digital technologies, such as quality control software and automation tools, can help firms improve the speed and accuracy of their quality control processes, leading to increased efficiency and reduced costs. (Source: Deloitte, "2019 Quality Management Trends Report", 2019)
Managing quality control while scaling is a critical challenge that many firms face. As a firm grows, it becomes increasingly important to maintain consistent and high-quality standards across all aspects of the business.
Failure to do so can result in customer dissatisfaction, lost sales, and damage to the firm's reputation. To manage quality control while scaling, firms need to implement effective processes and systems that can help them maintain and improve quality control standards.
This article will be your complete guide to how firms can manage quality control while scaling by covering the following topics:
- What is Quality Control?
- Types of Quality Control
- Benefits of Quality Control
- Importance of Quality Control in Scaling Firms
- Challenges Faced in Quality Control by Scaling Firms
- How can Firms Manage Quality Control while Scaling?
- How can the Implementation of ERP and MRP Systems Help in Managing Quality Control in Scaling Firms?
- FAQs related to How can Firms Manage Quality Control while Scaling?
- How can Deskera Help You Manage Quality Control in Scaling Firms?
- Key Takeaways
- Related Articles
What is Quality Control?
Quality control is the process of ensuring that products or services meet a specific set of standards, specifications, and customer expectations. It involves monitoring and inspecting the production process to identify defects or flaws and taking corrective action to prevent or reduce their occurrence.
Quality control ensures that products or services are produced consistently to the required quality level and that they are free from defects that could affect their performance or safety.
Quality control can involve various activities such as testing, inspection, verification, validation, and certification, depending on the industry, product, or service. The goal of quality control is to ensure that the final product or service is of high quality, meets customer expectations, and is safe and reliable.
Types of Quality Control
There are several types of quality control, each with its own specific purpose and methods. Here are eleven types of quality control:
- Statistical Quality Control (SQC): SQC involves the use of statistical methods to monitor and control the quality of a product or service. This type of quality control uses tools such as control charts, histograms, and Pareto charts to identify and measure variation in the production process.
- Inspection: Inspection involves the physical examination of a product or service to detect defects or deviations from the required specifications. This type of quality control can be performed at different stages of the production process, including incoming materials, in-process manufacturing, and final product inspection.
- Testing: Testing involves subjecting a product or service to specific conditions or scenarios to determine its performance, durability, or reliability. This type of quality control is often used for products such as electronics, automotive parts, and medical devices.
- Quality Assurance (QA): QA is a proactive approach to quality control that involves the creation of policies and procedures to ensure that products or services consistently meet the required quality standards. This type of quality control focuses on preventing defects and improving processes rather than just detecting and correcting them.
- Six Sigma: Six Sigma is a data-driven quality control methodology that aims to reduce defects and improve processes. This method involves analyzing data to identify the root causes of defects and implementing solutions to eliminate them.
- Lean Manufacturing: Lean manufacturing is a method of quality control that focuses on reducing waste and improving efficiency. This method involves optimizing processes and eliminating any steps that do not add value.
- Total Quality Management (TQM): TQM is an approach to quality control that involves the entire organization in the effort to improve quality. This method involves a continuous improvement process that seeks to improve all aspects of the organization, from processes to employee training.
- Process Control: This type of quality control involves monitoring the production process to ensure that it meets the required quality standards. This can include controlling variables such as temperature, humidity, and pressure.
- Supplier Quality Control: Supplier quality control involves ensuring that the materials or components received from suppliers meet the required quality standards. This can involve performing inspections, audits, or testing on incoming materials.
- Continuous Improvement: Continuous improvement involves regularly reviewing and improving the production process to reduce defects and improve quality. This type of quality control involves identifying areas for improvement and implementing solutions to address them.
- Corrective and Preventive Action (CAPA): CAPA involves identifying the root cause of defects or quality issues and taking corrective action to prevent them from occurring again. This type of quality control focuses on preventing defects rather than just detecting and correcting them.
These are just a few examples of the types of quality control that are commonly used in various industries. The specific type of quality control used will depend on the product or service being produced, the industry, and the specific quality requirements.
Benefits of Quality Control
There are many benefits of quality control for businesses, some of which include:
- Improved product or service quality: Quality control ensures that products or services meet or exceed the required quality standards, leading to increased customer loyalty and satisfaction.
- Reduced costs: By identifying and correcting defects early in the production process, quality control can help to reduce the costs associated with rework, scrap, and warranty claims.
- Increased efficiency: Quality control can help to improve the efficiency of the production process by reducing downtime, improving workflow, and minimizing waste.
- Compliance with regulations: Quality control can help businesses to comply with regulations and standards, ensuring that their products or services meet legal and safety requirements.
- Improved reputation: Consistently delivering high-quality products or services can help to enhance a business's reputation and brand image, leading to increased customer retention.
- Increased employee satisfaction: Quality control can involve training employees and involving them in the quality improvement process, which can help to increase their satisfaction and engagement with their work.
- Better decision-making: Quality control provides businesses with data and insights that can be used to make better decisions about production, inventory, and other aspects of the business.
- Continuous improvement: Quality control involves a continuous cycle of monitoring, analyzing, and improving the production process, leading to ongoing improvements in quality, efficiency, and cost-effectiveness.
- Employee engagement: Quality control can involve training employees and involving them in the quality improvement process, which can help to increase their satisfaction and engagement with their work.
- Improved supply chain management: Quality control can help to improve supply chain management by identifying suppliers that consistently produce high-quality materials and components.
- Reduced risk: Quality control helps to reduce the risk of product recalls, liability claims, and other issues that can be costly and damaging to the business.
- Improved communication: Quality control promotes communication and collaboration among teams, which is essential for scaling firms that need to manage multiple teams and departments.
- Competitive advantage: By consistently delivering high-quality products or services, businesses can gain a competitive advantage over their competitors, attracting more customers and increasing market share.
Overall, quality control can help businesses to improve their bottom line by reducing costs, improving efficiency, and increasing customer satisfaction and loyalty.
Importance of Quality Control in Scaling Firms
Quality control is essential for scaling firms because it ensures that products or services maintain a consistent level of quality as the business grows. Here are some of the reasons why quality control is important for scaling firms:
- Maintaining customer satisfaction: As a business grows, it becomes more important to maintain high levels of customer satisfaction. Quality control ensures that products or services consistently meet or exceed customer expectations, leading to increased loyalty and returning customers.
- Building a strong reputation: Scaling firms need to build a strong reputation to attract new customers and investors. Quality control helps to establish the business as a reliable and trustworthy provider of high-quality products or services.
- Reducing costs: Scaling firms need to be cost-efficient to remain competitive. Quality control helps to reduce costs associated with rework, scrap, and warranty claims, improving the bottom line.
- Improving efficiency: Quality control can help to improve the efficiency of the production process, reducing downtime and waste and increasing productivity.
- Meeting regulatory requirements: As a business grows, it may be subject to more regulatory requirements. Quality control helps to ensure that products or services meet these requirements, reducing the risk of fines or legal action.
- Enabling continuous improvement: Quality control involves monitoring and analyzing data to identify areas for improvement. This allows scaling firms to continuously improve their processes and products, leading to ongoing growth and success.
Overall, quality control is critical for scaling firms because it helps to ensure that the business can maintain a consistent level of quality and efficiency as it grows.
By investing in quality control, scaling firms can build a strong reputation, reduce costs, improve efficiency, and meet regulatory requirements, leading to ongoing success and growth.
Challenges Faced in Quality Control by Scaling Firms
Scaling firms can face several challenges in maintaining quality control, including:
- Increased Complexity: As firms grow, their operations become more complex, and they may struggle to maintain the same level of quality control across all aspects of the business.
- Communication: Communication can become more challenging as firms scale, making it difficult to ensure that quality control standards are communicated effectively to all employees and stakeholders.
- Resource Constraints: Scaling firms may face resource constraints, including limited funding, staff, and technology, which can make it challenging to implement effective quality control processes.
- Supply Chain Management: As firms scale, their supply chains may become more complex, and they may struggle to monitor suppliers effectively and ensure that they meet the firm's quality standards.
- Cultural Resistance: Cultural resistance can be a significant challenge for scaling firms, as employees and stakeholders may be resistant to change and may not see quality control as a top priority.
- Lack of Standardization: As firms scale, they may struggle to standardize processes and procedures, making it challenging to maintain consistent quality control standards across different departments and teams.
- Limited Customer Feedback: Scaling firms may struggle to gather and analyze customer feedback effectively, which can make it challenging to identify quality issues and implement effective solutions.
To overcome these challenges, firms must implement effective quality control processes and continually monitor and improve them as they scale. This requires a commitment to quality from all employees and stakeholders and a willingness to invest in the resources and technology needed to maintain consistent quality control standards.
How can Firms Manage Quality Control while Scaling?
Managing quality control is essential for firms that are scaling, as it ensures that their products or services meet the required standards and specifications. Here are some ways firms can manage quality control while scaling:
Develop Quality Control Processes
Implementing effective quality control processes is critical for firms looking to manage quality while scaling. Here are some steps to develop quality control processes:
- Define Quality Standards: Clearly define quality standards for your product or service. This will help ensure that everyone in your organization understands what quality means and what they need to do to achieve it.
- Establish a Quality Control Team: Create a quality control team responsible for monitoring and managing quality control processes. This team should have members with expertise in quality control and be given the authority to make decisions that will impact the quality of the product or service.
- Develop a Quality Control Plan: Develop a quality control plan that outlines the processes and procedures that will be used to ensure that quality standards are met. This plan should include details such as inspection and testing procedures, as well as the frequency and methods of quality checks.
- Use Technology to Support Quality Control: Technology can help streamline quality control processes and make them more efficient. Consider using automated testing tools, software for tracking defects, and other tools that can help you quickly identify and address quality issues.
- Train Employees: Ensure that all employees are trained on quality control processes and understand their role in maintaining quality standards. Provide ongoing training and support to help employees improve their skills and stay up-to-date with changes in quality control processes.
- Monitor and Evaluate Quality Control Processes: Regularly monitor and evaluate your quality control processes to identify areas for improvement. Use metrics such as defect rates and customer feedback to assess the effectiveness of your quality control processes and make adjustments as needed.
By following these steps, firms can develop effective quality control processes that help them manage quality while scaling their operations.
Establish Quality Control Metrics
Establishing quality control metrics is essential for managing quality control while scaling. Here are some strategies for establishing quality control metrics:
- Define Quality Control Metrics: Define quality control metrics that align with overall business goals and objectives. These metrics might include defect rates, customer satisfaction ratings, delivery times, or other key performance indicators.
- Establish Benchmarks: Establish benchmarks for quality control metrics to provide a baseline for measuring progress and identifying areas for improvement. These benchmarks might be based on industry standards, customer expectations, or internal targets.
- Use Real-Time Data: Use real-time data to track quality control metrics and identify trends and patterns. This can help firms identify potential quality issues before they become major problems.
- Create Dashboards and Reports: Create dashboards and reports that provide visibility into quality control metrics and highlight areas for improvement. This can help teams stay focused on quality control and provide stakeholders with insights into performance.
- Conduct Regular Reviews: Conduct regular reviews of quality control metrics to evaluate performance and identify areas for improvement. These reviews might be conducted on a daily, weekly, or monthly basis, depending on the needs of the organization.
- Communicate Metrics to Stakeholders: Communicate quality control metrics to stakeholders, including employees, customers, and investors. This can help build trust and confidence in quality control processes and demonstrate a commitment to continuous improvement.
By establishing quality control metrics, firms can track performance, identify areas for improvement, and ensure that quality standards are maintained as they scale. This can help firms stay competitive and deliver high-quality products and services that meet customer expectations.
Foster a Culture of Quality
Fostering a culture of quality is essential for managing quality control while scaling. Here are some strategies for fostering a culture of quality:
- Communicate the Importance of Quality: Communicate the importance of quality to all employees and stakeholders, including how it impacts the customer experience and the success of the business.
- Lead by Example: Leaders should lead by example and demonstrate a commitment to quality by modeling best practices, providing resources and training, and making quality a priority.
- Empower Employees: Empower employees to take ownership of quality control processes by providing them with the tools and resources they need to identify and address quality issues.
- Recognize and Reward Quality: Recognize and reward employees who demonstrate a commitment to quality and excellence and celebrate successes and milestones.
- Foster Collaboration: Foster collaboration between teams and departments to ensure that quality control processes are integrated throughout the organization and that all stakeholders are working towards the same goals.
- Provide Ongoing Training: Provide ongoing training and development opportunities to ensure that employees have the skills and knowledge needed to maintain quality standards as the firm scales.
By fostering a culture of quality, firms can create a shared understanding of the importance of quality control and a commitment to delivering high-quality products and services.
This can help ensure that quality standards are maintained as the firm grows and scales, ultimately leading to higher levels of customer satisfaction and business success.
Conduct Quality Audits
Conducting quality audits is an effective way for firms to manage quality control while scaling. Here are some strategies for conducting quality audits:
- Define Audit Scope and Objectives: Define the scope and objectives of the audit, including the areas of the organization that will be audited, the audit criteria, and the expected outcomes.
- Identify Audit Team: Identify the audit team, which should consist of qualified and experienced auditors who are independent and objective.
- Develop an Audit Plan: Develop an audit plan that outlines the audit methodology, the audit schedule, and the resources required to conduct the audit.
- Conduct Audit: Conduct the audit, which may include document review, interviews, observation of processes, and testing of controls.
- Document Findings: Document the findings of the audit, including any non-conformances, opportunities for improvement, and best practices.
- Develop Corrective Action Plan: Develop a corrective action plan to address any non-conformances identified during the audit and implement the plan in a timely manner.
- Follow Up: Follow up on corrective actions to ensure they have been implemented effectively and that quality standards have been maintained.
By conducting quality audits, firms can identify areas for improvement in their quality control processes, ensure compliance with regulations and standards, and demonstrate a commitment to quality to customers and stakeholders.
Quality audits also provide valuable feedback to management on the effectiveness of quality control processes and help to identify opportunities for improvement. Conducting regular quality audits is essential for maintaining high-quality standards as the firm scales and grows.
Train Employees
Training employees is an essential step in helping firms manage quality control while scaling. Here are some strategies for training employees on quality control processes:
- Develop a Training Plan: Develop a training plan that outlines the skills and knowledge employees need to effectively implement quality control processes. This plan should include information on the specific quality control processes used by the firm, as well as the tools and techniques employees need to use to ensure quality standards are met.
- Use a Variety of Training Methods: Use a variety of training methods to help employees learn and retain information. This might include classroom training, online courses, job shadowing, and on-the-job training. Using a mix of training methods can help employees learn in ways that work best for them.
- Provide Hands-On Experience: Provide employees with hands-on experience using quality control tools and techniques. This might involve working on sample projects or participating in simulations that allow employees to practice using quality control processes in a safe and controlled environment.
- Provide Ongoing Support: Provide ongoing support to employees as they learn and implement quality control processes. This might involve coaching, mentoring, or providing access to resources such as training materials and job aids.
- Incorporate Quality Control into Performance Evaluations: Incorporate quality control into employee performance evaluations to reinforce the importance of quality control and ensure that employees are held accountable for their role in maintaining quality standards.
- Celebrate Success: Celebrate successes along the way to help motivate employees and reinforce the importance of quality control. This might involve recognizing employees who have implemented quality control processes effectively or celebrating when the firm achieves quality goals.
By following these strategies, firms can help employees develop the skills and knowledge they need to effectively implement quality control processes while scaling their operations.
Use Technology
Technology can be a powerful tool for firms looking to manage quality control while scaling. Here are some ways that technology can be used to help firms manage quality control:
- Automated Testing Tools: Automated testing tools can help firms quickly and efficiently test products and services to ensure they meet quality standards. These tools can automate the testing process, saving time and reducing the risk of human error.
- Quality Management Software: Quality management software can help firms manage quality control processes, track defects, and monitor performance. This software can provide real-time data on quality control processes, making it easier to identify areas for improvement and make data-driven decisions.
- Internet of Things (IoT) Devices: IoT devices can be used to monitor products and services in real-time, providing valuable data on performance and quality. This data can be used to identify potential quality issues and make adjustments to improve quality control processes.
- Machine Learning and Artificial Intelligence: Machine learning and artificial intelligence can be used to analyze data and identify patterns that can help firms improve quality control processes. These technologies can help firms identify potential quality issues and make proactive adjustments to prevent defects and improve overall quality.
- Customer Relationship Management (CRM) Systems: CRM systems can help firms collect and analyze customer feedback, providing valuable insights into customer satisfaction and areas for improvement. This data can be used to make data-driven decisions and improve quality control processes.
By leveraging technology, firms can improve the efficiency and effectiveness of their quality control processes, allowing them to scale their operations without sacrificing quality.
However, it is important to ensure that technology is used in conjunction with effective processes and well-trained employees to ensure that quality standards are met.
Leverage Data Analytics
Leveraging data analytics is a powerful strategy for managing quality control while scaling. Here are some ways to leverage data analytics to manage quality control:
- Collect and Analyze Data: Collect and analyze data from various sources, such as customer feedback, operational metrics, and production data, to identify trends and patterns in quality control processes.
- Use Predictive Analytics: Use predictive analytics to identify potential quality issues before they occur, allowing firms to take proactive measures to prevent problems and improve quality control.
- Utilize Machine Learning: Utilize machine learning algorithms to identify patterns and anomalies in data, which can help identify potential quality issues and improve quality control processes.
- Visualize Data: Use data visualization tools to create charts and graphs that help stakeholders understand and interpret data, which can help inform decisions and identify opportunities for improvement.
- Monitor Key Metrics: Continuously monitor key metrics, such as defect rates, customer satisfaction, and delivery times, to ensure that quality standards are maintained and identify areas for improvement.
- Integrate Data into Quality Control Processes: Integrate data analytics into quality control processes, such as using real-time data to monitor production lines or using predictive analytics to identify potential quality issues.
By leveraging data analytics, firms can gain valuable insights into quality control processes, which can help them identify potential issues, improve processes, and maintain high-quality standards as they scale.
Data analytics also helps organizations to stay agile and adaptable to changing market conditions, allowing them to adjust their quality control processes as necessary to stay competitive.
Monitor Suppliers
Monitoring suppliers is an essential aspect of managing quality control while scaling. Here are some strategies for monitoring suppliers to ensure that they meet quality standards:
- Develop a Supplier Quality Management Program: Develop a supplier quality management program that outlines the standards and expectations for suppliers. This program should include criteria for selecting suppliers, as well as procedures for monitoring supplier performance and ensuring that they meet quality standards.
- Conduct Supplier Audits: Conduct regular supplier audits to evaluate their performance and identify any potential quality issues. These audits can include on-site inspections, document reviews, and performance evaluations.
- Establish Performance Metrics: Establish performance metrics to evaluate supplier performance and track progress over time. These metrics might include defect rates, delivery times, and customer satisfaction ratings.
- Use Data Analytics: Use data analytics to analyze supplier performance data and identify trends and patterns that can help improve supplier performance. This might include using tools such as machine learning and artificial intelligence to identify potential quality issues.
- Establish Communication Channels: Establish clear communication channels with suppliers to ensure that they are aware of quality expectations and any potential quality issues. These channels might include regular meetings, performance reviews, and feedback mechanisms.
- Provide Training and Support: Provide training and support to suppliers to help them improve their quality control processes. This might include providing access to training materials, sharing best practices, and offering coaching and mentoring.
By monitoring suppliers, firms can ensure that they meet quality standards and maintain quality control while scaling their operations.
By working closely with suppliers and providing support and feedback, firms can improve supplier performance and strengthen their supply chain, ultimately leading to better quality products and services for customers.
Gather Customer Feedback
Gathering customer feedback is a critical component of managing quality control while scaling. Here are some strategies for gathering customer feedback:
- Implement a Customer Feedback Program: Implement a customer feedback program that provides a structured process for collecting and analyzing customer feedback. This program should include a mechanism for customers to provide feedback, as well as a process for analyzing and acting on that feedback.
- Use Surveys and Questionnaires: Use surveys and questionnaires to collect feedback from customers. These tools can help gather quantitative data on customer satisfaction, as well as qualitative data on specific issues or areas for improvement.
- Monitor Social Media and Review Sites: Monitor social media and review sites to gather feedback on products and services. This can help firms identify potential quality issues and make adjustments to improve quality control processes.
- Provide Easy-to-Use Feedback Mechanisms: Provide customers with easy-to-use feedback mechanisms, such as online forms, email addresses, or dedicated feedback hotlines. This can encourage customers to provide feedback and make it easier for them to do so.
- Act on Customer Feedback: Act on customer feedback by making adjustments to quality control processes or addressing specific customer concerns. This can help improve customer satisfaction and build trust and loyalty.
- Engage with Customers: Engage with customers to understand their needs and expectations. This might include hosting focus groups, conducting interviews, or attending industry events to connect with customers.
By gathering customer feedback, firms can identify potential quality issues and make adjustments to improve quality control processes. This can help ensure that quality standards are maintained as the firm scales, ultimately leading to better products and services and higher levels of customer satisfaction.
Ensure Leadership Support
Leadership support is critical to ensuring that firms can effectively manage quality control while scaling. Here are some steps that firms can take to ensure leadership support:
- Communicate the Importance of Quality Control: Communicate the importance of quality control to leadership and ensure that they understand how it affects the firm's reputation, customer satisfaction, and bottom line.
- Assign Responsibility: Assign responsibility for quality control to a specific individual or team, and ensure that they have the resources and support they need to implement effective quality control processes.
- Establish Quality Objectives: Establish quality objectives that align with the firm's overall business objectives, and ensure that leadership supports these objectives and promotes a culture of quality throughout the organization.
- Allocate Resources: Allocate the necessary resources, including funding, staff, and technology, to support quality control initiatives and ensure that leadership is aware of the importance of investing in quality control.
- Monitor Progress: Monitor progress towards quality objectives, and provide regular updates to leadership on quality control initiatives, including successes, challenges, and areas for improvement.
- Reward Quality Control Success: Reward employees and teams that successfully implement quality control processes, achieve quality objectives, and contribute to a culture of quality throughout the organization.
- Lead by Example: Ensure that leadership leads by example and promotes a culture of quality throughout the organization, including demonstrating a commitment to quality control processes and encouraging employees to prioritize quality in their work.
By following these steps, firms can ensure that leadership supports quality control initiatives and promotes a culture of quality throughout the organization. This can help the firm maintain high-quality standards, improve customer satisfaction, and gain a competitive advantage in the marketplace.
Implement Continuous Improvement
Implementing continuous improvement is critical for managing quality control while scaling. Here are some strategies for implementing continuous improvement:
- Establish a Continuous Improvement Framework: Establish a framework for continuous improvement that defines goals, processes, and metrics for evaluating progress and identifying areas for improvement.
- Encourage Employee Feedback: Encourage employees to provide feedback on quality control processes and identify areas for improvement. This can help identify potential quality issues and ensure that all stakeholders are working towards the same goals.
- Analyze Data and Metrics: Analyze data and metrics on quality control processes to identify trends and patterns and gain insights into potential areas for improvement.
- Conduct Root Cause Analysis: Conduct root cause analysis to identify the underlying causes of quality issues and address them at the source.
- Implement Best Practices: Implement best practices for quality control and leverage industry standards and frameworks, such as ISO 9001, to guide quality control processes.
- Use Technology: Use technology to automate and optimize quality control processes, such as using machine learning algorithms to identify patterns in data or using automated testing tools to streamline testing processes.
- Monitor Performance: Continuously monitor performance metrics to track progress and identify areas for improvement.
By implementing continuous improvement processes, firms can maintain quality standards and optimize operations as they scale. This can help ensure that products and services meet customer expectations, which is critical to maintaining a competitive edge in today's marketplace.
Continuous improvement also helps organizations to stay agile and adaptable to changing market conditions, allowing them to adjust their quality control processes as necessary to stay competitive.
How can the Implementation of ERP and MRP Systems Help in Managing Quality Control in Scaling Firms?
The implementation of Enterprise Resource Planning (ERP) and Material Requirements Planning (MRP) systems can help in managing quality control in scaling firms in several ways:
- Streamlining Operations: ERP and MRP systems can streamline operations by integrating all aspects of the business, including production, inventory management, and quality control.
- Improved Data Management: ERP and MRP systems can improve data management by providing real-time access to data, making it easier to monitor and manage quality control processes.
- Automating Quality Control Processes: ERP and MRP systems can automate quality control processes, such as inspection and testing, making it easier to monitor and maintain quality control standards.
- Supply Chain Management: ERP and MRP systems can help firms manage their supply chain more effectively, ensuring that suppliers meet quality control standards.
- Analytics and Reporting: ERP and MRP systems can provide advanced analytics and reporting capabilities, allowing firms to track quality control metrics and identify areas for improvement.
- Real-Time Monitoring: ERP and MRP systems can provide real-time monitoring of quality control processes, enabling firms to respond quickly to quality control issues and take corrective action.
Overall, the implementation of ERP and MRP systems can help scaling firms improve their quality control processes by providing a unified view of all aspects of the business, streamlining operations, and automating quality control processes.
By using these systems, firms can also gain valuable insights into their quality control performance and identify areas for improvement, leading to improved quality control standards and ultimately contributing to the success and growth of the firm.
FAQs related to How can Firms Manage Quality Control while Scaling?
- How can firms manage quality control across multiple locations?
Firms can manage quality control across multiple locations by establishing standard operating procedures, using technology to share data and insights across locations, and training employees on quality standards.
- How can firms ensure compliance with regulatory requirements while scaling?
Firms can ensure compliance with regulatory requirements while scaling by implementing quality control processes that address regulatory requirements, monitoring compliance regularly, and seeking expert advice if necessary.
- How can firms balance quality control with production efficiency while scaling?
Firms can balance quality control with production efficiency while scaling by investing in automation and process improvement initiatives that reduce waste and inefficiencies while maintaining consistent quality.
- How can firms ensure that suppliers and vendors meet quality standards?
Firms can ensure that suppliers and vendors meet quality standards by setting clear quality expectations, establishing quality control processes for suppliers and vendors, and monitoring their performance regularly.
- How can firms incorporate customer feedback into their quality control processes?
Firms can incorporate customer feedback into their quality control processes by soliciting feedback from customers, analyzing feedback data, and using the insights to improve products and services.
- How can firms measure the effectiveness of their quality control processes?
Firms can measure the effectiveness of their quality control processes by establishing quality metrics and goals, monitoring performance regularly, and using data and feedback to make improvements.
- How can firms train employees on quality control standards and processes?
Firms can train employees on quality control standards and processes by providing clear guidelines and expectations, offering training programs and workshops, and incentivizing employees to meet quality goals.
- How can firms use technology to improve quality control?
Firms can use technology to improve quality control by implementing automated quality control processes, using data analytics to identify areas for improvement, and using software tools to monitor quality metrics and performance.
- How can firms identify and address quality control issues quickly?
Firms can identify and address quality control issues quickly by monitoring quality metrics in real time, establishing clear protocols for addressing issues, and incentivizing employees to report issues promptly.
- How can firms ensure that quality control remains a priority as the business scales?
Firms can ensure that quality control remains a priority as the business scales by establishing a culture of quality, setting clear quality goals and metrics, and regularly communicating the importance of quality control to employees.
- How can firms balance the cost of quality control with the need to maximize profits?
Firms can balance the cost of quality control with the need to maximize profits by investing in quality control processes that provide the most value, using data to identify areas for cost savings, and incentivizing employees to meet quality goals.
How can Deskera Help You Manage Quality Control in Scaling Firms?
Deskera is an all-in-one cloud-based business management software that can help manage quality control in scaling firms. Here are some ways in which Deskera can help:
- Quality Control Management: Deskera provides a complete quality control management module that can help you create and manage quality control plans, track quality control metrics, and manage quality control processes from end to end.
- ERP and MRP System: Deskera provides a comprehensive ERP and MRP system that can help streamline operations and automate quality control processes.
- Supplier Management: Deskera's supplier management module allows you to manage suppliers and monitor their quality control standards, ensuring that they meet your firm's quality control requirements.
- Customer Feedback Management: Deskera's customer feedback management module enables you to gather and analyze customer feedback, identifying areas where quality control needs improvement.
- Analytics and Reporting: Deskera provides advanced analytics and reporting capabilities, allowing you to track quality control metrics and identify areas for improvement.
- Compliance Management: Deskera helps you ensure that your quality control processes meet regulatory requirements.
- Collaboration and Communication: Deskera's collaboration and communication tools enable you to collaborate with team members and communicate with suppliers and customers, improving the efficiency and effectiveness of quality control processes.
Key Takeaways
Quality control is the process of ensuring that products and services meet or exceed customer expectations. It is important for scaling firms because it helps them to maintain consistent quality, reduce costs, comply with regulations, and increase customer satisfaction and loyalty.
Some of the ways in which firms can manage quality control while scaling are:
- Develop quality control processes
- Establish quality control metrics
- Foster a culture of quality
- Conduct quality audits
- Train employees
- Use technology
- Leverage data analytics
- Monitor suppliers
- Gather customer feedback
- Ensure leadership support
- Implement continuous improvement
Overall, Deskera can help you manage quality control in scaling firms by providing a comprehensive set of tools and features to automate and streamline quality control processes, track quality control metrics, and identify areas for improvement.
Deskera's cloud-based platform is also highly scalable, making it suitable for firms of all sizes, from small startups to large enterprises.
Related Articles
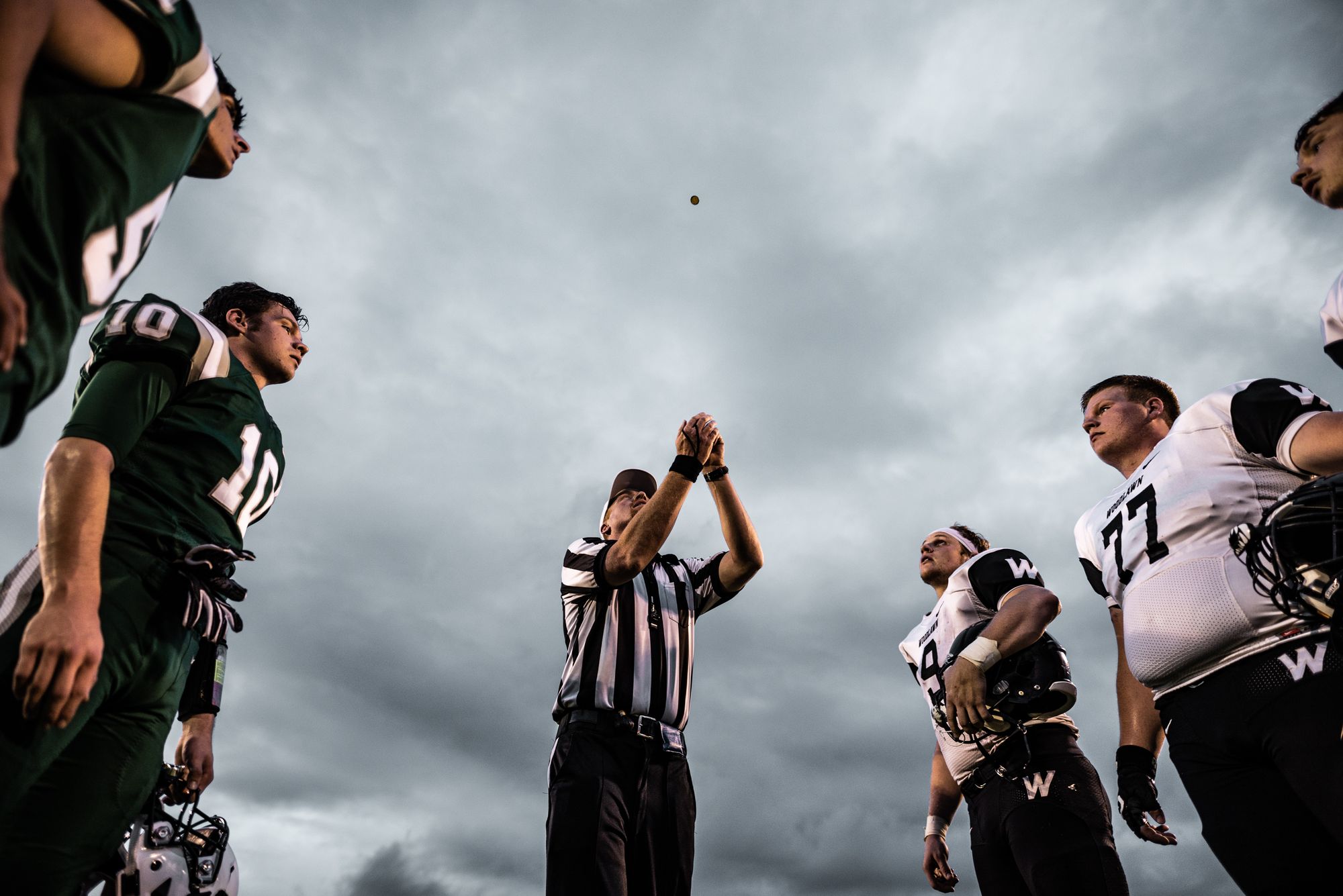
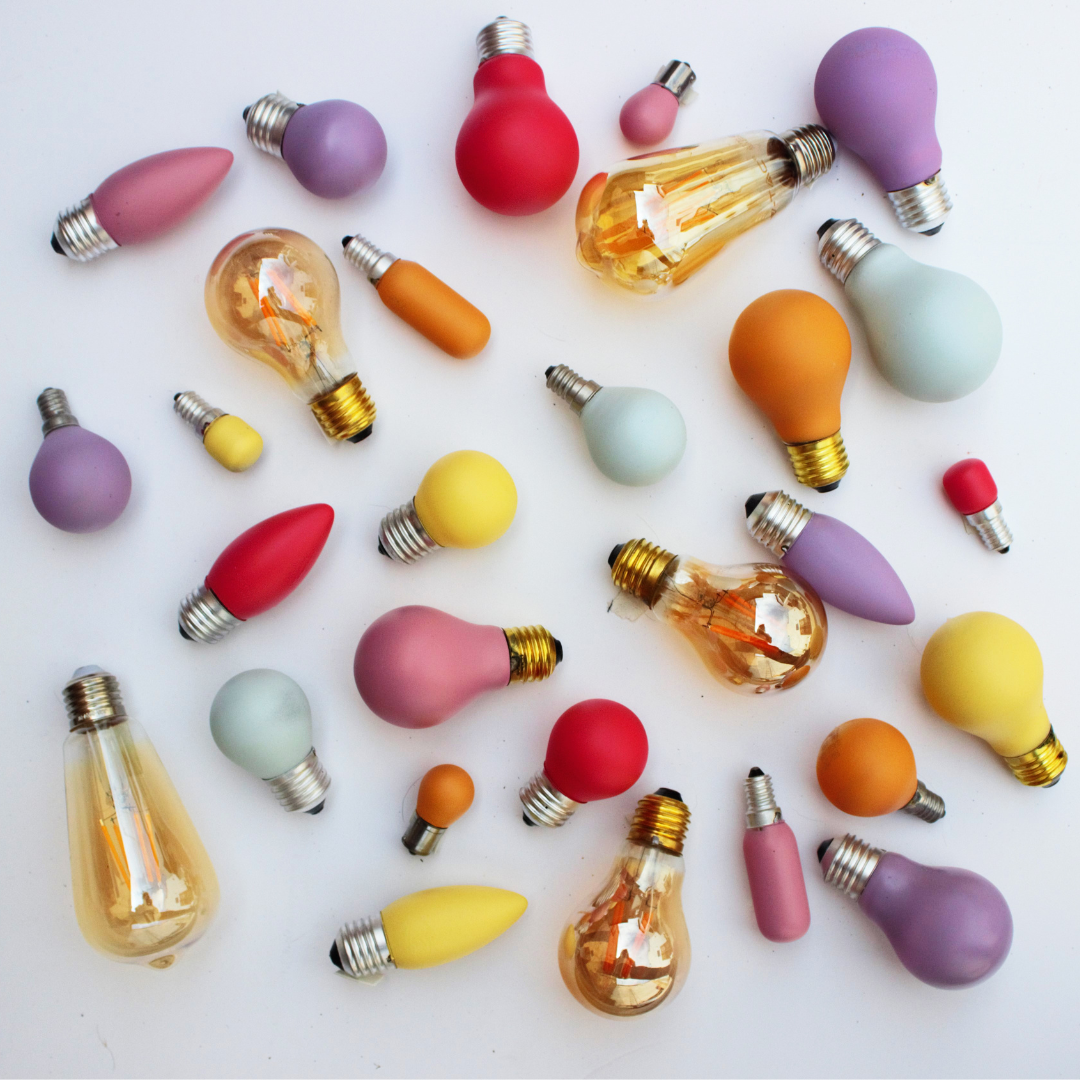
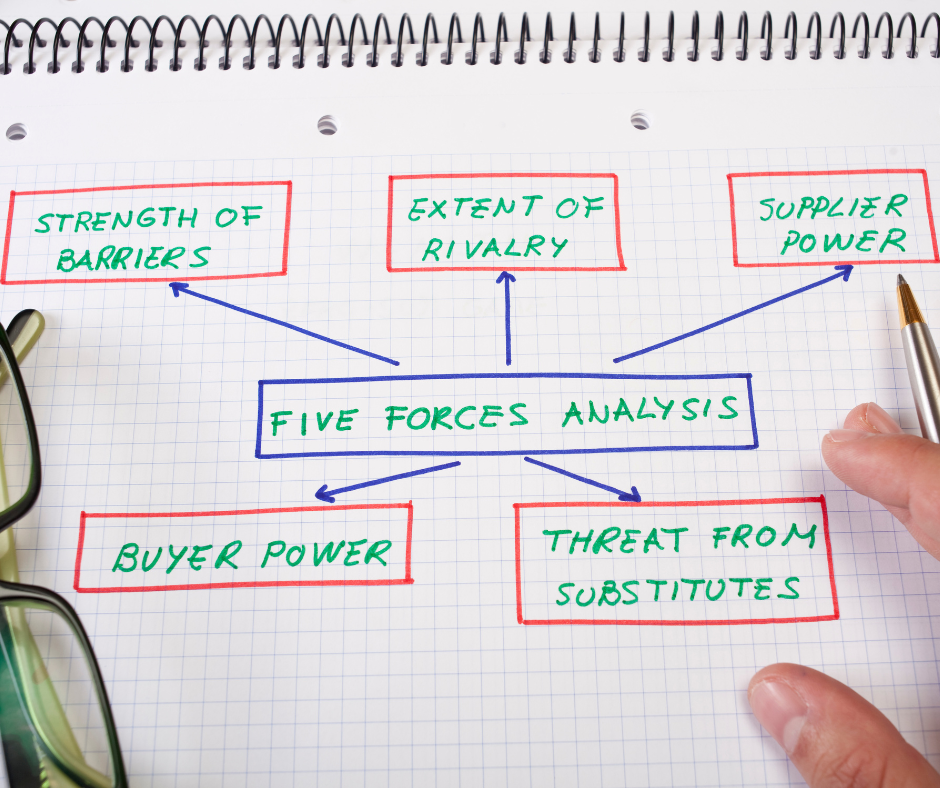
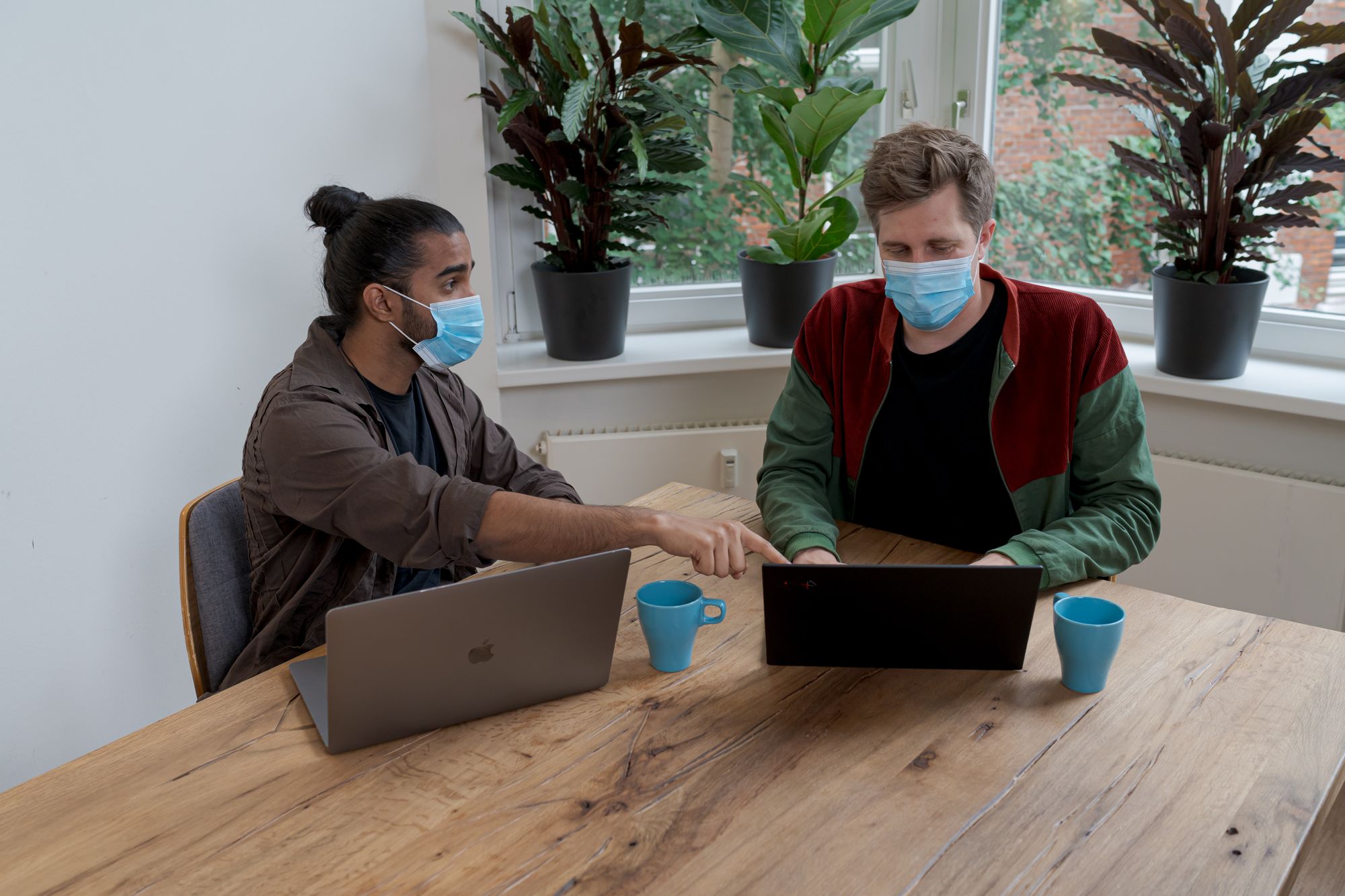
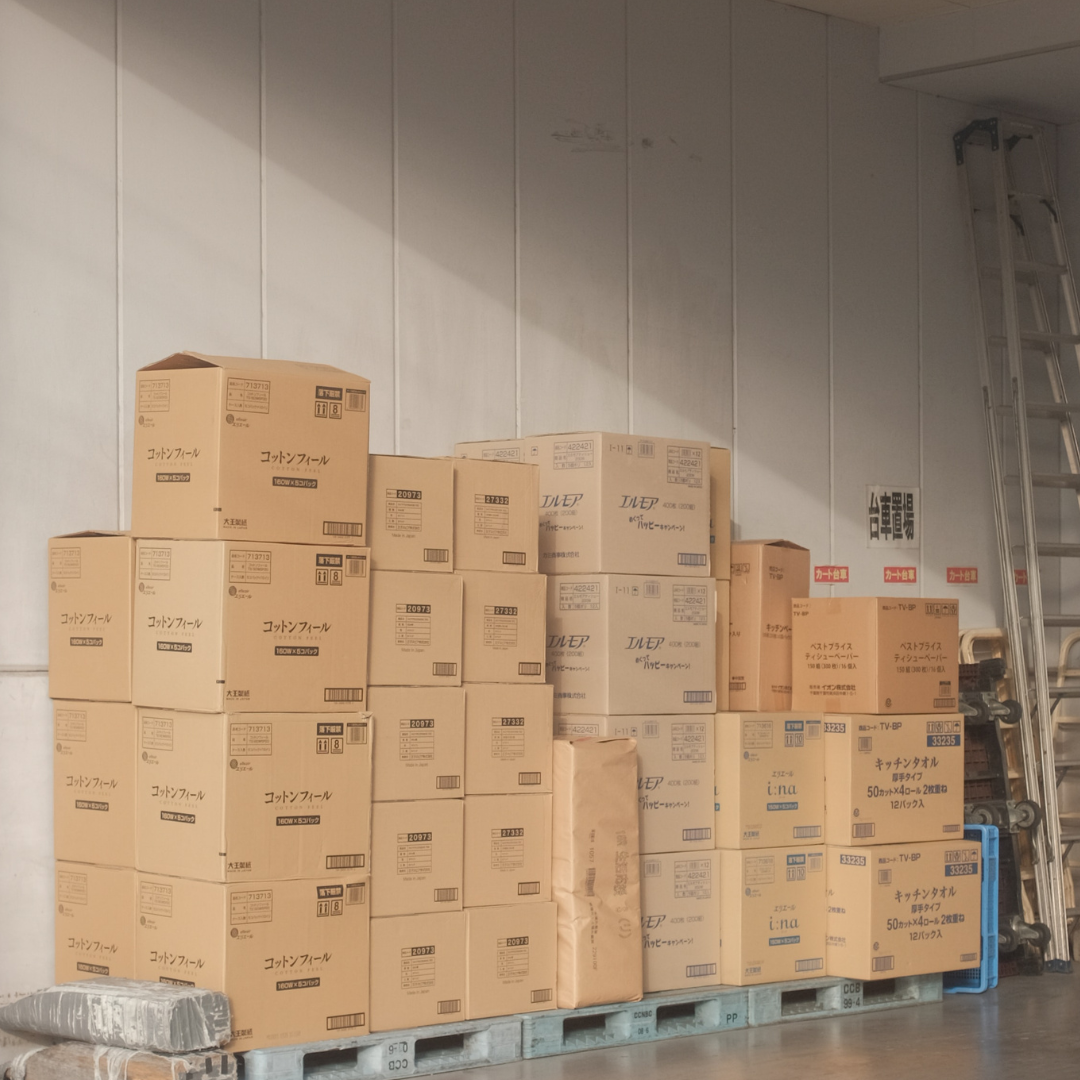