Inventory management is a straightforward process for most businesses. It is the tracking of what comes in and what goes out. However, as countless inventory managers have discovered, effectively managing inventory is far more complex and critical to success than it first appears.
According to Gartner, 51% of businesses say they're inefficient in their inventory management. The reason might be one of the two things:
Either they are not using proper inventory management software like Deskera MRP, or they are using manual methods. And surprisingly, 41% of businesses still rely on spreadsheets and manual data entry.
Let’s take an example to understand the complexities involved in a poor inventory management environment.
Consider yourself an electronics manufacturer producing custom-made electronics for your clients. Your current system relies on manual data entry and spreadsheets to track inventory levels, leading to frequent errors and discrepancies.
As a result, your company often finds itself either overstocked on certain components, tying up valuable capital. Or understocked on others, causing production delays and missed deadlines. These inefficiencies have a ripple effect throughout the organization.
Sales representatives struggle to provide accurate lead times to customers. While production managers are forced to make last-minute adjustments to compensate for inventory shortages.
The purchasing department, in an effort to avoid stockouts, often over-orders materials, further compounding the problem of excess inventory.
None of this would occur if you have a
In this blog, you'll gain a complete understanding of inventory management, the complexities involved and how to optimize it for your business.
What is Inventory Management?
To understand inventory management, let's first define what inventory is.
Inventory refers to the raw materials, work-in-progress, and finished goods that a business holds for the purpose of production or sale.
In our electronics manufacturing example, inventory would include the electronic components.
These components will be PCBs, transmitters, and displays (raw materials). Then comes the partially assembled devices (work-in-progress). And finally the finished electronics, say headphones, ready for sale (finished goods).
Types of Inventory
Raw Materials
These are the components and materials used to create the final product. In our example, raw materials would include the various electronic components needed to assemble headphones.
Work-in-Progress (WIP)
This refers to the partially completed products that are still undergoing the manufacturing process. For our electronics company, WIP would be the devices that are currently being assembled on the production line.
Finished Goods
These are the completed products ready to be sold to customers. In our example, finished goods would be the fully assembled headphones that are packaged and ready for distribution.
Each type of inventory plays a significant role in a company's operations.
- Raw materials ensure that production can continue without interruption.
- WIP represents the value of partially completed work and helps track production progress.
- Finished goods are the lifeblood of a business, generating revenue when sold.
Now, what is inventory management?
In simple terms, the definition of inventory management is the process of overseeing and controlling a company's inventory. This includes ordering, storing, tracking, and using inventory in the most efficient and cost-effective way possible.
The main objectives of inventory management are to:
- Ensure the right amount of inventory is on hand to meet customer demand
- Minimize the cost of holding inventory
- Prevent stockouts (running out of inventory) and overstocking
- Maintain accurate inventory records
- Streamline inventory processes for maximum efficiency
Effective inventory management is crucial for businesses of all sizes and types. In the next section, we'll explore the key benefits of getting it right.
Benefits of Inventory Management
Proper inventory management offers a host of benefits for businesses. Some of the most significant advantages include:
Cost Savings
Effective inventory management ensures you won't waste money on items you don't need or that go bad before you can sell them. This means you'll have more cash available for other parts of your business.
Improved Cash Flow
Inventory management helps businesses avoid tying up too much cash in slow-moving or excess inventory. This frees up working capital that can be used to invest in growth or cover operating expenses.
Better Customer Service
The right products in stock ensure you can quickly fill customer orders and avoid disappointing them with out-of-stock items. This can lead to repeat business and good word-of-mouth.
Increased Efficiency
Streamlined inventory management processes reduce the time and effort required to manage inventory. This frees up employees to focus on other value-adding tasks.
Reduced Waste
Proper inventory management helps minimize waste from expired, damaged, or obsolete stock. This is particularly important for businesses dealing with perishable goods.
Better Decision Making
When you have accurate, up-to-date data about your inventory, you can make informed choices about what to order, when to order it, and how much to charge.
Improved Profitability
By saving money, improving efficiency, and keeping customers happy, effective inventory management can ultimately lead to higher profits for your business.
These benefits illustrate why inventory management is so crucial for businesses. In the following sections, we'll dive into how to actually do it.
Process of Inventory Management
The process of inventory management is a critical aspect of any business’s operations. It involves a series of interconnected steps that ensure we have the right components and finished products available when needed. Additionally, it minimizes the costs associated with holding inventory.
Let’s see how the process of inventory management would look like from our previously discussed example:
Inventory Planning
This involves forecasting customer demand, setting inventory levels, and determining inventory reorder points. For our electronics company, this would include analyzing sales data, market trends, and customer preferences to accurately predict demand for our headphones.
Purchasing
Based on our inventory plan, we need to procure the necessary electronic components from our suppliers.
This involves identifying reliable suppliers who can provide high-quality components at competitive prices and negotiating favorable terms.
Then our purchasing team places purchase orders based on the required quantities and delivery schedules.
Receiving
When the electronic components arrive at our facility, our receiving team needs to verify the quantity and quality of the goods.
They check the shipment against the purchase order and inspect the components for any damage or defects.
Once verified, the inventory records are updated in our system, and the components are stored appropriately.
Storage
Our electronic components need to be stored in a manner that protects them from damage, such as electrostatic discharge (ESD) or moisture. We use ESD-safe storage racks and bins in our temperature-controlled warehouse.
The storage layout is designed to maximize space utilization and minimize handling costs. We also use an automated storage and retrieval system (AS/RS) for high-volume components to improve efficiency.
Tracking
Barcodes system in inventory softwares is an industry standard. We track our inventory using a combination of barcodes and RFID tags. Each component is assigned a unique identifier, which is scanned as it moves through our facility.
This allows us to know exactly what items are in stock, where they are located, and when they need to be replenished. Our inventory management software provides real-time visibility into our inventory levels and helps us make informed decisions.
Production and Assembly
As our production team assembles the headphones, they requisition the necessary components from the warehouse using their warehouse management system.
The inventory management system updates the stock levels in real-time as the components are consumed.
Finished products are then stored in a separate area of the warehouse, ready for shipping.
Picking, Packing, and Shipping
When we receive an order for our headphones, our picking team locates the appropriate items in the warehouse and brings them to the packing area.
The products are carefully packaged to prevent damage during shipping and labeled with the necessary information.
Our shipping team then arranges for the products to be delivered to the customer using our network of carriers.
Reporting and Analysis:
We regularly generate reports on our inventory levels, turnover rates, and carrying costs.
Our management team analyzes this data to identify trends, spot potential problems, and make continuous improvements to our inventory management processes.
We also monitor key metrics such as stock-out frequency and order fill rates to ensure we are meeting customer demands effectively.
This is how a typical process of inventory management looks like. By following these steps and continually refining their processes, businesses can effectively manage their inventory and reap the many benefits we discussed earlier.
Methods and Techniques in Inventory Management
We use various types of inventory management techniques and methods for effective control at managing our inventory. These strategies help us optimize stock levels, minimize costs, and improve overall efficiency.
Here are some of the methods we use in inventory management:
Economic Order Quantity (EOQ)
We use the EOQ model to determine the optimal order quantity for each component or material. This formula takes into account the cost of placing an order, the holding cost of inventory, and the demand rate.
By calculating the EOQ, we can minimize the total cost of ordering and holding inventory, while ensuring that we have sufficient stock to meet production needs. This helps us strike a balance between the risk of stockouts and the cost of carrying excess inventory.
ABC Analysis
We categorize our inventory items into three classes based on their value and importance. “Class A” items, such as high-value electronic components, are the most critical and require close monitoring and tight control.
“Class B” items are of moderate importance, while “Class C” items, such as common fasteners or packaging materials, are the least critical.
By prioritizing our inventory management efforts based on this classification, we can focus our resources on the items that have the greatest impact on our operations and bottom line.
Just-in-Time (JIT) Inventory
For electronics manufacturing , we can implement a just-in-time (JIT) inventory system for certain high-volume components. Under this approach, we receive components from our suppliers just as they are needed in the production process, rather than holding large quantities of stock.
This helps us reduce storage costs, minimize the risk of obsolescence, and improve cash flow. However, JIT requires close coordination with suppliers and reliable transportation to ensure that components arrive on time.
Safety Stock
We maintain a certain level of safety stock for critical components to buffer against unexpected demand spikes or supply chain disruptions. The amount of safety stock is determined based on factors such as lead time, demand variability, and service level targets.
By having a cushion of extra stock, we can reduce the risk of stockouts and minimize the impact of supply chain issues on our production schedule.
Cycle Counting
To maintain accurate inventory records, we perform regular cycle counts. This involves counting a subset of our inventory on a rotating basis, rather than conducting a full physical inventory.
By focusing on high-value or high-turnover items, we can quickly identify and correct any discrepancies between our records and actual stock levels. This helps us avoid stockouts or overstock situations and ensures that our inventory data remains reliable.
First-In, First-Out (FIFO)
We use the first-in, first-out or FIFO method for managing our inventory of electronic components and finished goods. Under this approach, the oldest items in stock are used or sold first, ensuring that we rotate our inventory and minimize the risk of obsolescence.
This is particularly important in the electronics industry, where components can quickly become outdated due to rapid technological advancements. By using FIFO, we can ensure that our products always incorporate the latest and most up-to-date components.
Vendor-Managed Inventory (VMI)
For some critical components, we have established vendor-managed inventory or VMI agreements with our suppliers. Under this arrangement, the supplier is responsible for monitoring our inventory levels and replenishing stock as needed.
This helps us reduce the administrative burden of placing orders and managing inventory, while ensuring that we have a steady supply of components. VMI also allows our suppliers to better plan their production and optimize their own inventory levels.
Consignment Inventory
For certain specialized or high-value components, we have established consignment inventory agreements with our suppliers. Under this arrangement, the supplier owns the inventory until we use it in our production process.
We only pay for the components when we consume them, which helps us reduce our upfront inventory costs and improve cash flow.
Consignment inventory also allows us to hold a wider range of components without tying up our working capital, giving us greater flexibility to respond to changing customer requirements.
Six Sigma Inventory Management
Six Sigma is a data-driven approach that seeks to minimize defects and variability in business processes.
By applying Six Sigma tools, such as DMAIC (Define, Measure, Analyze, Improve, Control), we can systematically identify and eliminate sources of inventory-related inefficiencies, such as excess stock, slow-moving items, or inaccurate records.
This helps us optimize our inventory levels, improve inventory turns, and reduce carrying costs.
These were some of the most common inventory management methods used industry-wide. The right mix of these methods and techniques will depend on a business's specific products, supply chain, and operational needs.
Challenges in Inventory Management
While the benefits of effective inventory management are clear, it's not always easy to achieve. Businesses often face several challenges:
Demand Forecasting
Accurate demand forecasting can be difficult, especially in an industry like electronics industry where product life cycles are short, and consumer preferences can change rapidly.
Inaccurate demand forecasts can lead to either excess inventory or stockouts, both of which can be costly.
Supply Chain Disruptions
Unexpected events such as natural disasters, geopolitical issues, or supplier failures can disrupt the flow of raw materials and components, leading to production delays and inventory shortages.
Your electronics company must develop contingency plans and maintain adequate safety stock to mitigate the impact of supply chain disruptions.
Inventory Accuracy
Maintaining accurate inventory records can be challenging, especially in large, complex manufacturing operations.
Discrepancies between physical stock and recorded levels can lead to production inefficiencies, stockouts, and financial losses. Regular cycle counting and inventory audits are essential to ensure accuracy.
Inventory Costs
One of the key challenges in any business is the inventory costs. Holding excess inventory ties up working capital and incurs costs such as storage, insurance, and obsolescence. Balancing the need to meet customer demand with the financial impact of holding inventory is a constant challenge.
Perishability and Obsolescence
For businesses dealing with perishable or rapidly obsolescence goods (like food or technology), managing inventory is particularly tricky. Electronic components are subject to rapid obsolescence due to technological changes.
New product introductions and shifts in consumer preferences can quickly render existing components outdated. Managing this risk requires close collaboration with suppliers to stay informed about product lifecycles and being proactive in our inventory planning.
Inventory Visibility
With complex supply chains and multiple inventory locations, maintaining real-time visibility into stock levels can be challenging. Inaccurate or delayed inventory data can lead to poor decision-making and inefficiencies.
We need to invest in robust inventory tracking systems and ensure seamless integration between our various software platforms.
Change Management
Implementing new inventory management processes or technologies can be disruptive to an organization. Resistance to change, lack of training, or poorly executed rollouts can undermine the effectiveness of these initiatives.
Effective change management, including clear communication, employee training, and phased implementations, is essential for successfully adopting new inventory management practices.
Despite these challenges, businesses cannot afford to ignore inventory management. The key is to proactively identify and address these issues, leveraging best practices and technology solutions where appropriate.
Key Performance Indicators (KPIs) in Inventory Management
To effectively manage inventory, businesses need to track the right performance metrics. Some of the most important inventory management KPIs include:
Inventory Turnover Ratio
Inventory turnover ratio measures how quickly a company sells through its inventory. It's calculated by dividing the cost of goods sold by the average inventory value. A higher ratio generally indicates more efficient inventory management.
Days of Inventory on Hand (DOH)
This is the average number of days a company holds inventory before selling it. It's calculated by dividing the average inventory value by the cost of goods sold per day. A lower DOH is usually better.
Inventory Accuracy
This measures how closely the actual inventory on hand matches the inventory records. It's usually expressed as a percentage, with a goal of 100% accuracy.
Order Fill Rate
This is the percentage of customer orders that are filled on the first attempt, without backorders or lost sales. A higher fill rate indicates better inventory availability and customer service.
Stockout Frequency
This is the number of times a particular item is out of stock over a given period. A high stockout frequency suggests poor inventory planning and can lead to lost sales.
Inventory Carrying Cost
This is the total cost of holding inventory, including costs like storage, insurance, obsolescence, and capital costs. It's usually expressed as a percentage of the inventory value.
Inventory Shrinkage
Inventory shrinkage is the loss of inventory due to theft, damage, or administrative errors. It's usually calculated as a percentage of total inventory.
Backorder Rate
This is the percentage of orders that cannot be filled immediately due to out-of-stock items. A high backorder rate can indicate poor inventory planning and lead to customer dissatisfaction.
Inventory Visibility
While not a quantitative measure, the ability to see real-time inventory levels across the supply chain is a key indicator of inventory management effectiveness.
By regularly tracking and analyzing these KPIs, businesses can identify areas for improvement and make data-driven decisions about their inventory management strategies. The goal should be to continually improve these metrics over time, driving greater efficiency and profitability.
Inventory Management using Software
Given the speed and data demands of today’s businesses, manual inventory management isn’t feasible for most companies. This is why businesses now rely on warehouse and other inventory management softwares to streamline their operations and make informed decisions.
An inventory management software is a computer program that helps businesses track, manage, and organize their inventory. It automates many of the manual processes involved in inventory management, such as data entry, tracking, and reporting.
Some of the key features and benefits of inventory management software include:
Real-time Inventory Tracking
Software can provide real-time visibility into inventory levels, locations, and movements. This helps businesses avoid stockouts, overordering, and other costly mistakes.
Automated Ordering
Many software systems can automatically generate purchase orders when inventory levels fall below a predetermined threshold. This helps ensure that stock is replenished in a timely manner without constant manual monitoring.
Barcode and RFID Integration
Inventory management software can integrate with barcode scanners and RFID readers to enable faster, more accurate inventory tracking and counting.
Multi-location Management
For businesses with multiple warehouses or stores, software systems like warehouse inventory management can provide a centralized view of inventory across all locations. This enables more efficient transfer and allocation of stock.
Reporting and Analytics
Inventory management software can generate a variety of reports and analytics, providing insights into key performance metrics, trends, and problem areas.
Integration with Other Systems
Many inventory management systems can integrate with other business software, such as accounting, order management, and shipping systems. This enables seamless data flow and reduces manual data entry.
Cloud-based Accessibility
Many modern inventory management systems are cloud-based. This means they can be accessed from anywhere with an internet connection. This is particularly useful for businesses with multiple locations or remote employees.
When selecting an inventory management system, businesses should consider factors like scalability, ease of use, integration capabilities, and cost. The right system will depend on the size, scale and unique needs of a business.
Use Deskera for Your Inventory Management Needs
If inventory plays a critical role in your business, it is essential to choose a reliable inventory management solution that seamlessly integrates with a ledger system.
Deskera ERP offers complete inventory management capabilities that empower businesses to efficiently control, track, and optimize their inventory operations.
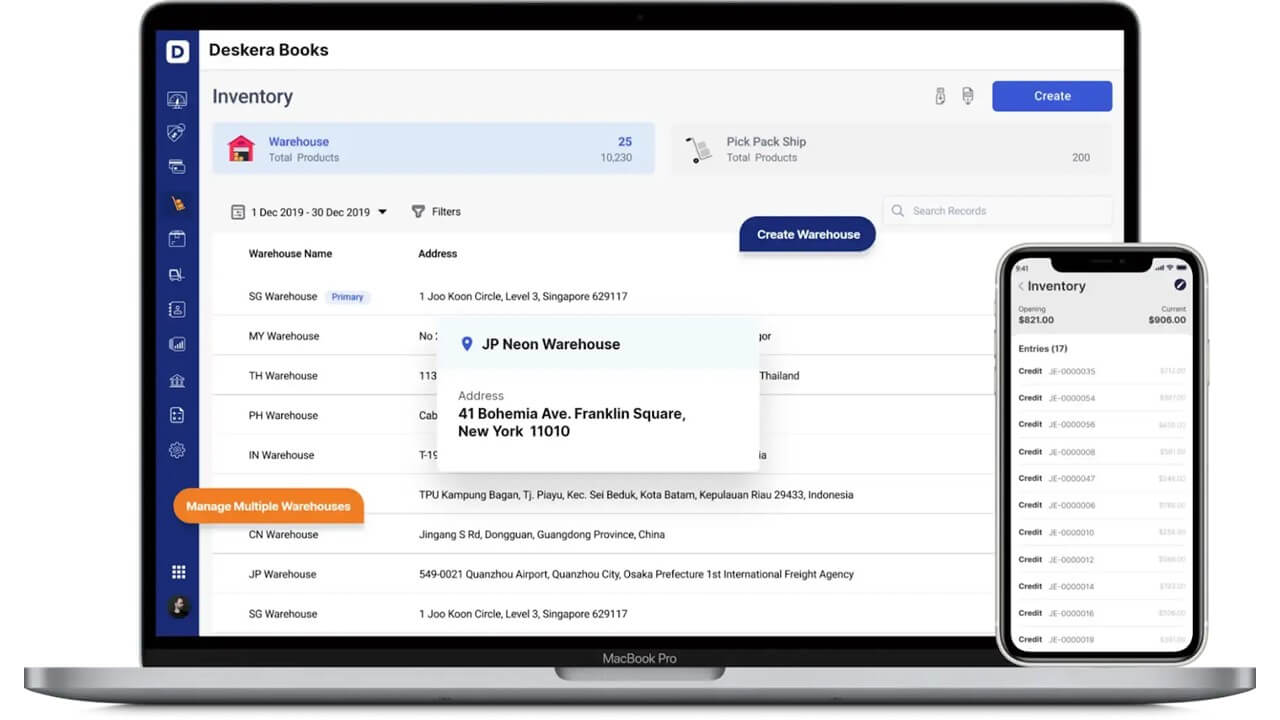
Whether you are in manufacturing, distribution, retail, or any other industry, Deskera ERP's inventory management features help your business achieve accurate inventory levels, reduce carrying costs, and enhance supply chain efficiency.
Here's how Deskera ERP can help you in inventory management:
- Real time inventory tracking across multiple locations, warehouses and sales channels that allows you to track inventory movements, transfers, and stock levels at each location.
- Automated stock reordering based on predefined reorder points or minimum stock levels.
- Purchase order management to streamline purchase order creation, approval, and tracking.
- Sales order integration allows businesses to allocate inventory based on customer orders and prioritize fulfillment based on demand.
Schedule a call with us today!
Key Takeaways
To sum up, here are the key takeaways that we can conclude from this inventory management guide:
- Inventory management is crucial for manufacturing companies to optimize stock levels, reduce costs, and improve customer satisfaction.
- The three main types of inventory are raw materials, work-in-progress, and finished goods, each requiring different management strategies.
- Effective inventory management involves planning, control, replenishment, storage, and distribution processes.
- Methods such as ABC analysis, EOQ, JIT, and cycle counting can help optimize inventory management.
- Challenges in inventory management include demand forecasting, supply chain disruptions, inventory accuracy, and holding costs.
- Key performance indicators such as inventory turnover ratio, days of inventory on hand, order fill rate, and inventory accuracy help monitor the effectiveness of inventory management.
- Inventory management software, such as ERP and WMS systems, along with barcode and RFID technology, can greatly improve inventory visibility, accuracy, and efficiency.
Related Articles
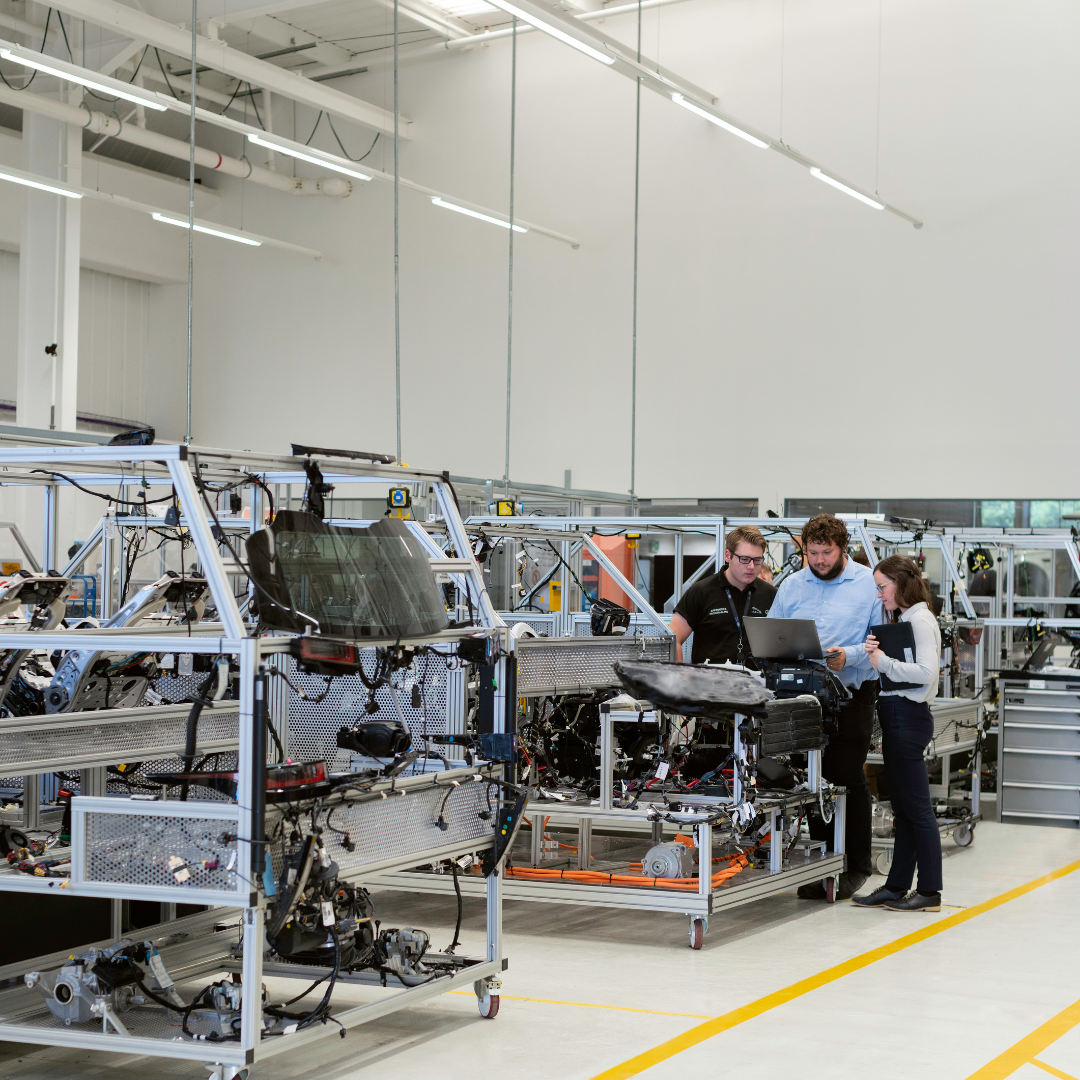
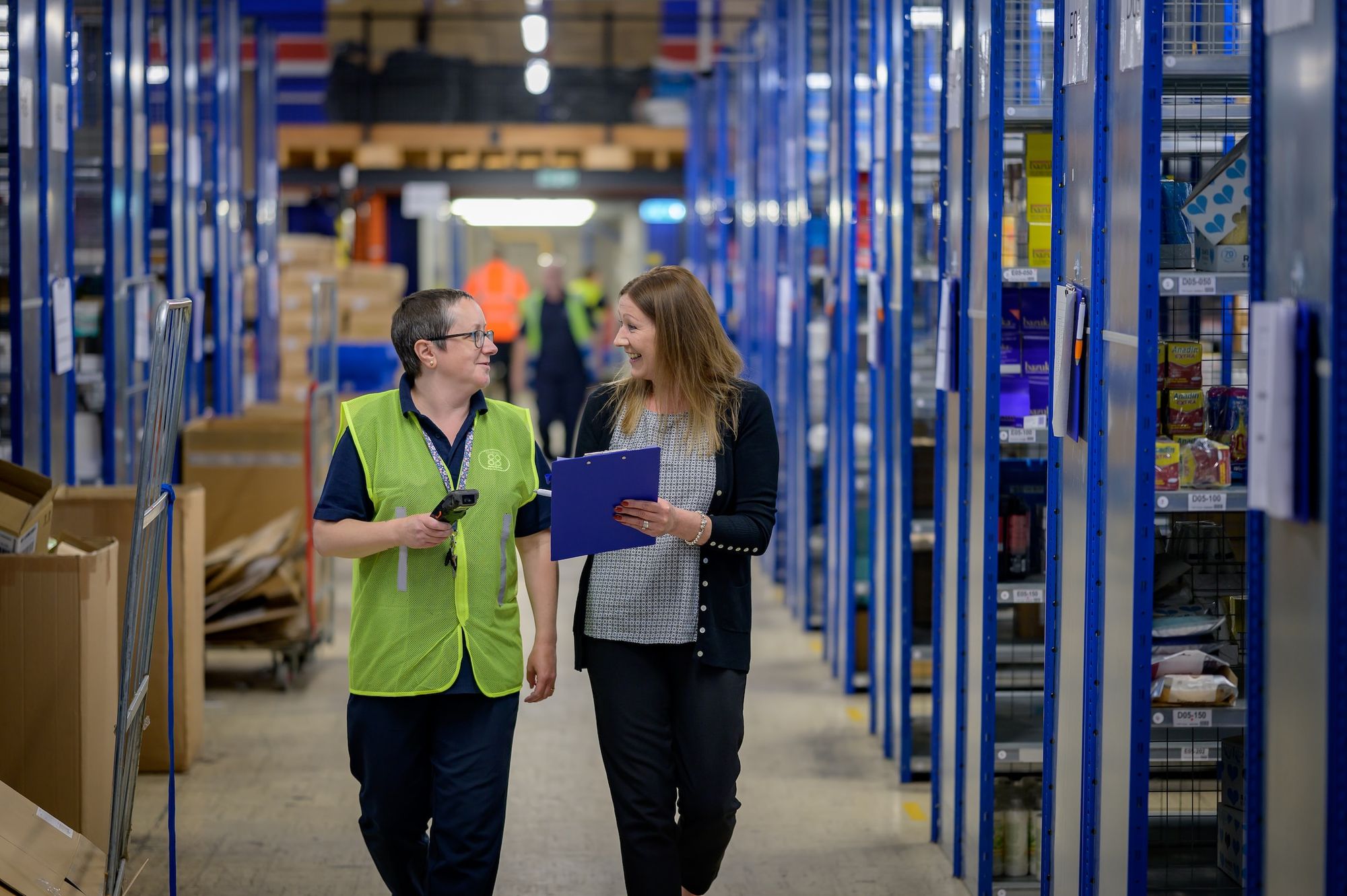
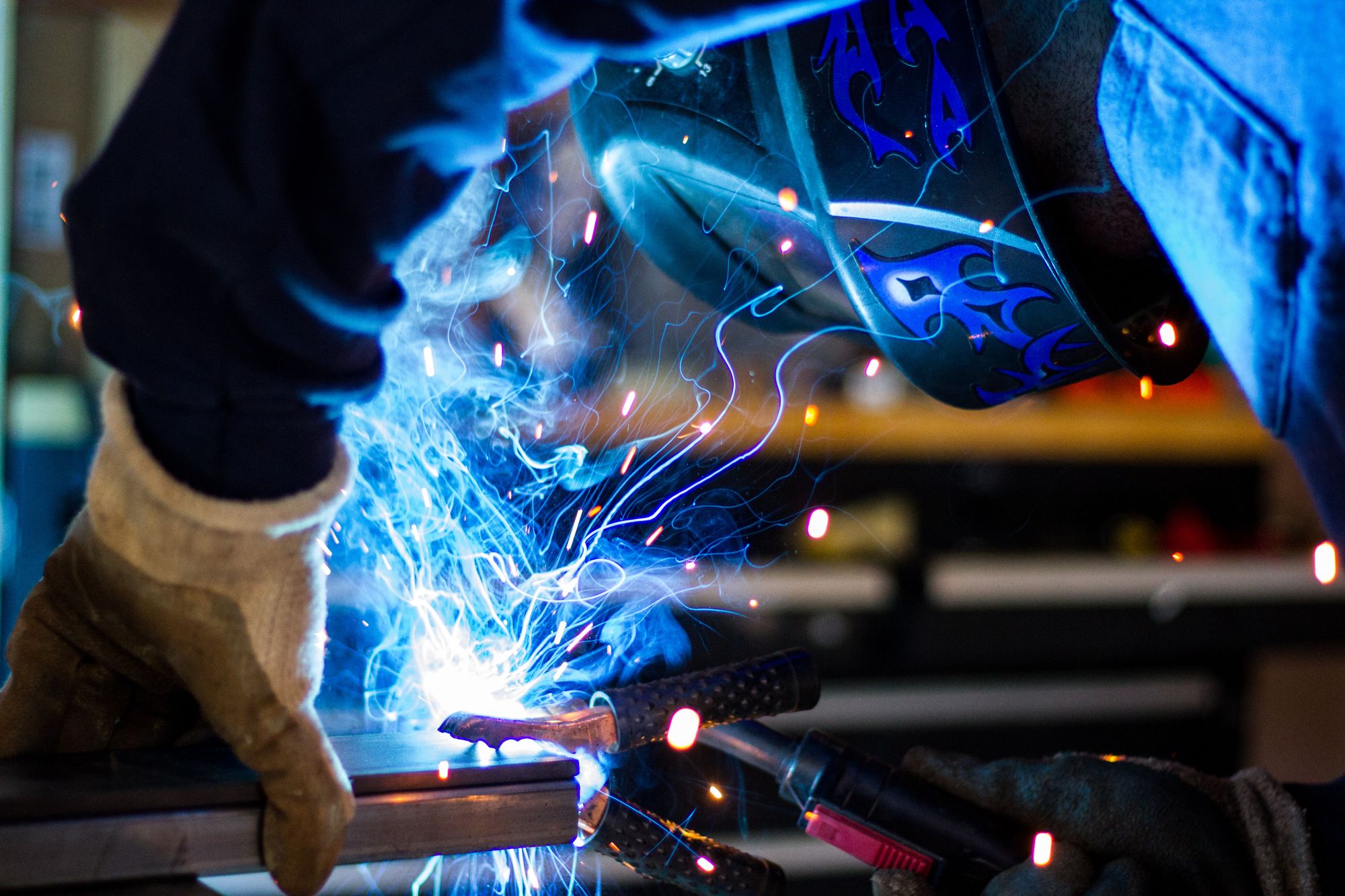
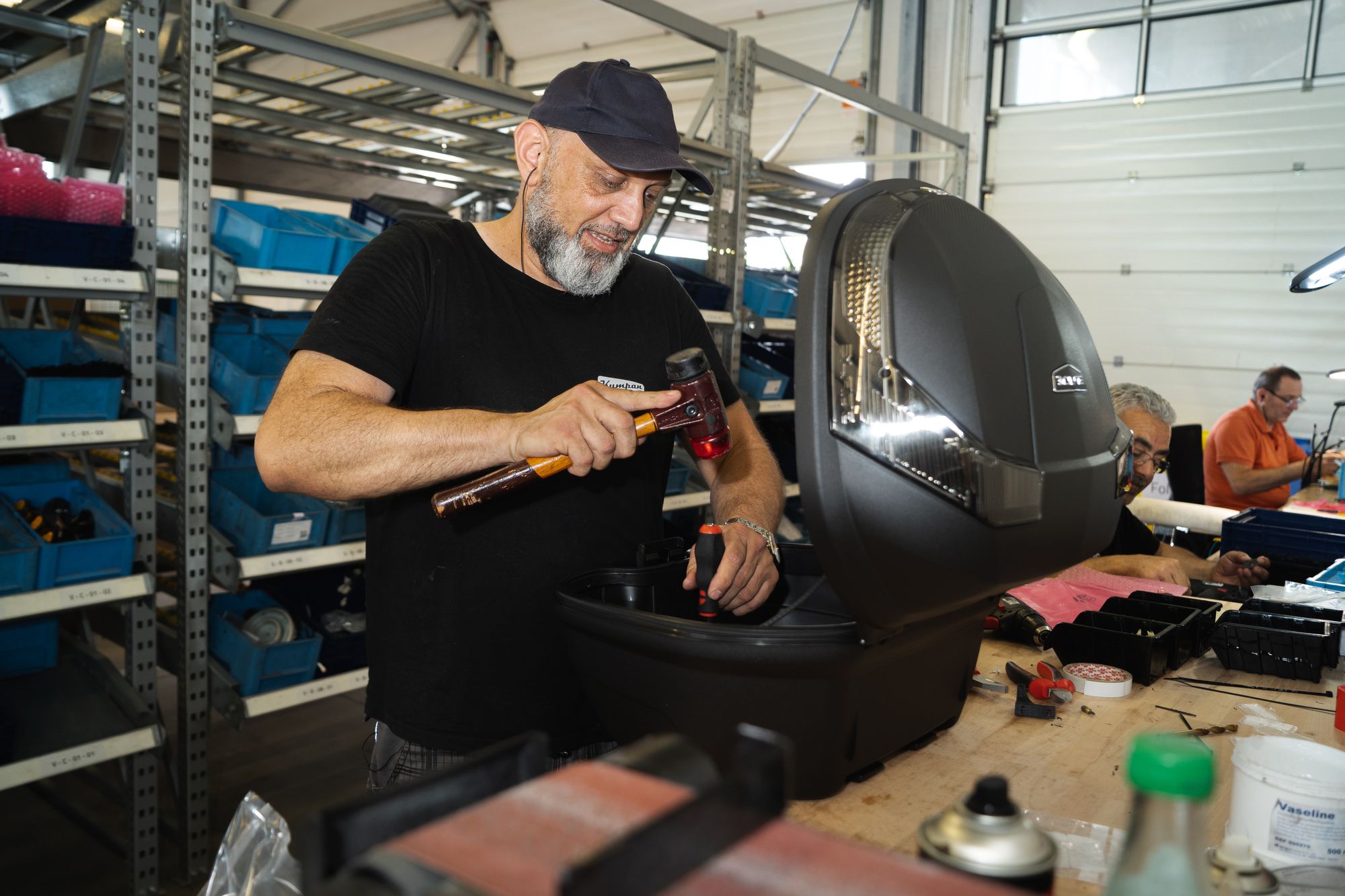