What does the future hold for work orders in the ever-evolving landscape of manufacturing? As industries undergo rapid transformation driven by technological advancements and changing workforce dynamics, work orders, a fundamental element of production planning eand control, are also poised to evolve.
But what will the future of work orders in manufacturing look like, and how will it shape the way we approach production processes?
Work orders, in the context of manufacturing, have long been the backbone of production operations, providing detailed instructions and guidelines for manufacturing tasks.
However, with the advent of Industry 4.0 and the increasing integration of digital technologies, work orders are poised to transform, moving beyond traditional paper-based forms to embrace digitalization, automation, and real-time data-driven decision-making.
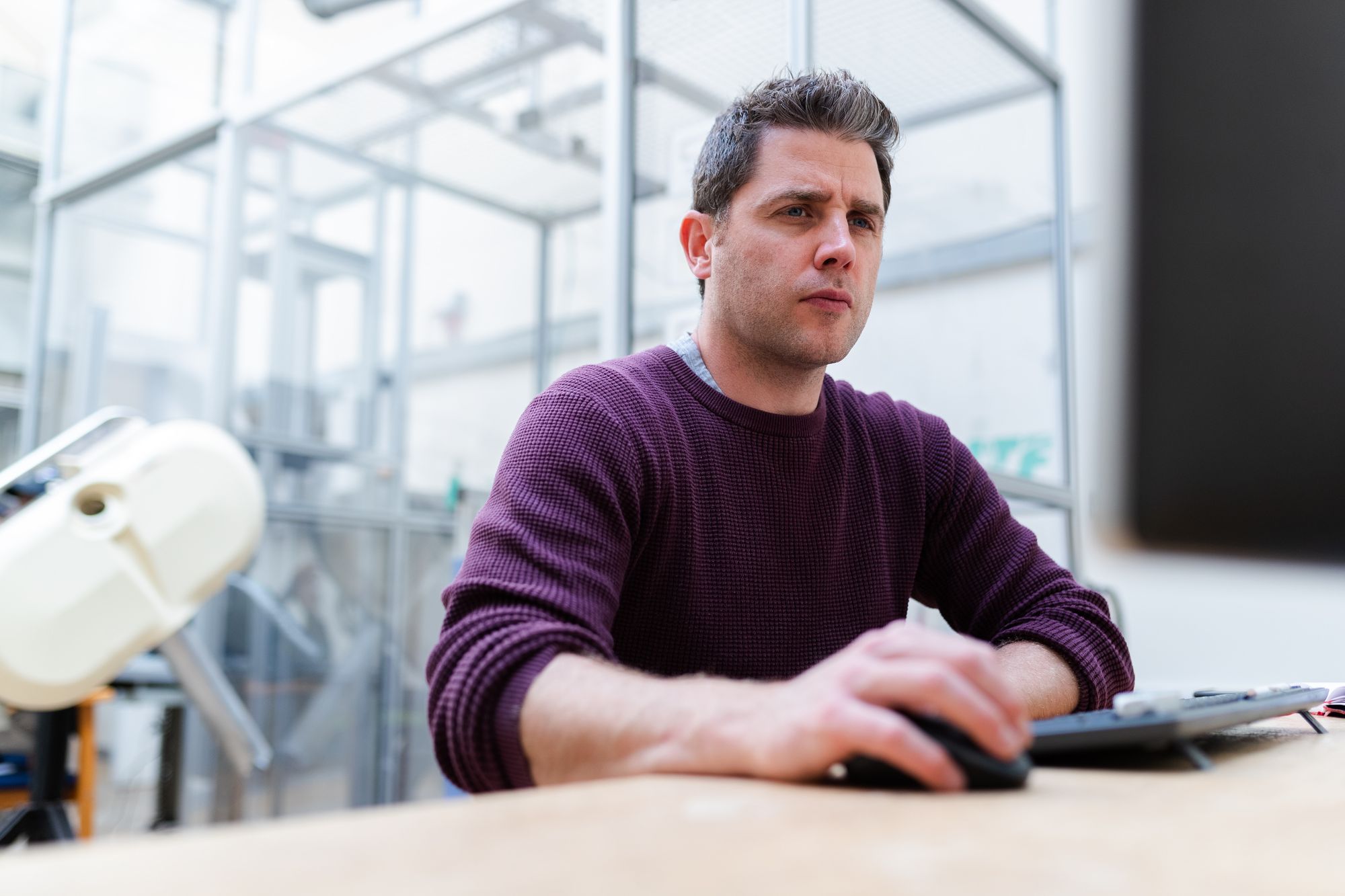
The future of work orders in manufacturing envisions a seamless and interconnected production environment, where communication between production managers, shop floor personnel, and automated systems is frictionless.
Digital work orders will play a pivotal role in orchestrating manufacturing activities, enhancing collaboration, and driving operational efficiency.
According to a report by MAPI Foundation, by 2025, manufacturers are projected to increase their investment in digital technologies for production scheduling and control by 46%. This statistic underscores the growing significance of digitalization in shaping the future of work orders and manufacturing operations as a whole.
As we embark on the journey to explore the future of work orders in manufacturing, we will uncover the untapped potential of digitalization, automation, and data-driven decision-making.
By embracing these transformative technologies, manufacturers can unlock new levels of efficiency, innovation, and competitiveness in an ever-evolving manufacturing landscape.
Here's what we shall cover in this post:
- Introduction to Work Orders in Manufacturing
- Work Orders in the Era of Industry 4.0
- Augmented Reality and Work Order Visualization
- AI-Driven Work Order Optimization
- Mobile Work Order Management for Flexibility
- Collaborative Work Orders in the Connected Factory
- 3D Printing and Customized Work Orders
- Remote Work Order Management in a Global Landscape
- Future Trends: Innovations Shaping the Future of Work Orders
- Conclusions
- Key Takeaways
Introduction to Work Orders in Manufacturing
Work orders play a vital role in the manufacturing industry, serving as a blueprint for various production processes. They provide clear instructions and details about what needs to be manufactured, how it should be done, and when it should be completed.
Work orders act as a roadmap, guiding workers through each step of the production process and ensuring that all tasks are executed efficiently and accurately.
Components of Work Orders
Work orders typically include the following key components:
a. Job Details: This section provides essential information about the work order, such as the job name, number, and description.
b. Materials and Components: Work orders list the materials, parts, and components needed for the job. This ensures that the correct items are available when the production process begins.
c. Work Instructions: This section outlines the step-by-step instructions for carrying out the manufacturing task. It includes details on how to set up equipment, perform the task, and conduct quality checks.
d. Labor Requirements: Work orders specify the number of workers and their skills required to complete the job.
e. Timeline: Work orders include a timeline or deadline for completing the task. This helps in planning and scheduling production activities.
Types of Work Orders
There are several types of work orders used in manufacturing, each serving a specific purpose:
a. Standard Work Orders: These are routine work orders used for repetitive tasks or standard products that follow a predetermined process.
b. Maintenance Work Orders: These work orders are issued for maintenance and repair tasks to ensure the smooth operation of equipment and machinery.
c. Project Work Orders: Project work orders are used for one-time or non-repetitive tasks, such as special orders or customized products.
d. Preventive Maintenance Work Orders: These work orders are scheduled to perform regular maintenance tasks to prevent equipment breakdowns and prolong their lifespan.
e. Emergency Work Orders: Emergency work orders are issued to address urgent issues or unexpected breakdowns that require immediate attention.
Work Orders in the Era of Industry 4.0
Work orders have been a staple in manufacturing for many years, providing a structured approach to managing production tasks and guiding workers through each step of the process.
With the advent of Industry 4.0, the digital transformation of manufacturing has revolutionized work order management, introducing new technologies and strategies that enhance efficiency, flexibility, and connectivity in the manufacturing ecosystem.
The Transformation of Work Order Management in Industry 4.0
Industry 4.0, also known as the Fourth Industrial Revolution, is characterized by the integration of digital technologies into manufacturing processes, resulting in the creation of "smart factories."
These smart factories leverage advanced technologies to connect machines, systems, and people in real-time, enabling data-driven decision-making and predictive capabilities.
In the era of Industry 4.0, work order management has undergone a significant transformation, with the following key aspects:
a. Connectivity: IoT devices and sensors have been integrated into manufacturing equipment and products, enabling real-time data collection and communication. This connectivity allows work orders to be updated automatically based on real-time conditions, leading to dynamic and agile manufacturing processes.
b. Data-driven Decision Making: Industry 4.0 facilitates the collection and analysis of vast amounts of data from various sources, including machines, production lines, and supply chains. This data-driven approach empowers manufacturers to make informed decisions, optimize work order scheduling, and improve overall efficiency.
c. Predictive Maintenance: By utilizing AI and machine learning algorithms, manufacturers can predict equipment failures and maintenance needs. Work orders can be automatically generated for preventive maintenance, reducing downtime and production disruptions.
d. Cloud-based Work Order Management: Cloud computing provides a centralized platform for managing work orders, making them accessible to relevant stakeholders across the manufacturing ecosystem. Cloud-based work order systems enable seamless collaboration, real-time updates, and secure data storage.
Benefits of Industry 4.0 for Work Order Management
The adoption of Industry 4.0 technologies in work order management offers numerous benefits, including:
a. Improved Efficiency: Real-time data and connectivity enable faster communication and decision-making, reducing production delays and optimizing work order execution.
b. Enhanced Visibility: IoT sensors and data analytics provide insights into the status of work orders, allowing manufacturers to monitor progress and identify potential bottlenecks.
c. Increased Flexibility: Industry 4.0 enables dynamic changes to work orders based on changing customer demands, market conditions, or unforeseen events.
d. Cost Savings: Predictive maintenance and data-driven decision-making can lead to reduced maintenance costs and optimized resource allocation.
e. Quality Control: Data analytics and AI can be used to identify patterns and trends related to product quality, allowing for early detection of defects and process improvements.
Challenges and Considerations in the Era of Industry 4.0
While Industry 4.0 offers promising advancements in work order management, manufacturers must also address several challenges and considerations, such as:
a. Data Security: With increased data connectivity, the risk of cyber threats and data breaches also rises. Manufacturers need to implement robust cybersecurity measures to protect sensitive information.
b. Skill Requirements: Implementing Industry 4.0 technologies requires a skilled workforce capable of leveraging digital tools effectively. Training and upskilling employees are essential for successful adoption.
c. Interoperability: Integrating various systems and technologies from different vendors can present challenges in achieving seamless data exchange and interoperability.
d. Initial Investment: Adopting Industry 4.0 technologies may require significant initial investment in infrastructure, equipment, and training.
Embracing Digitalization for Work Order Management
The integration of digital technologies, such as the Internet of Things (IoT), Artificial Intelligence (AI), cloud computing, and data analytics, has revolutionized work order management, offering manufacturers unprecedented capabilities to optimize their production processes and achieve new levels of productivity.
The Role of Digitalization in Work Order Management
Work order management is the backbone of manufacturing operations, guiding the execution of production tasks, resource allocation, and scheduling. Historically, work order management has been a manual and paper-based process, prone to errors, delays, and lack of real-time visibility.
However, with the rise of digitalization, manufacturers can now harness a myriad of technologies to streamline and optimize work order management:
a. Internet of Things (IoT): IoT devices and sensors are embedded in manufacturing equipment, allowing real-time data collection and communication. These connected devices provide valuable insights into equipment performance, allowing for predictive maintenance and optimized work order scheduling.
b. Artificial Intelligence (AI): AI-powered algorithms can analyze vast amounts of data to identify patterns, predict maintenance needs, and optimize work order execution. Machine learning capabilities enable continuous improvement and better decision-making.
c. Cloud Computing: Cloud-based work order management systems offer a centralized platform accessible from anywhere, enabling real-time collaboration among stakeholders, seamless updates, and secure data storage.
d. Data Analytics: Data analytics tools allow manufacturers to derive meaningful insights from production data, empowering them to identify bottlenecks, streamline processes, and optimize work order execution.
Implementing Digitalization Strategies for Work Order Management
To successfully implement digitalization in work order management, manufacturers should consider the following steps:
a. Assessing Current Processes: Conduct a thorough assessment of existing work order management processes to identify pain points and areas for improvement.
b. Identifying Relevant Technologies: Determine the digital technologies that align with your manufacturing objectives and can address the identified challenges.
c. Integrating Systems: Ensure seamless integration of digital systems with existing manufacturing processes and enterprise resource planning (ERP) systems.
d. Data Management: Develop a robust data management strategy to ensure the security, privacy, and integrity of collected data.
e. Employee Training: Provide comprehensive training and education to employees to ensure they can effectively utilize digital tools for work order management.
f. Pilot Projects: Consider piloting digitalization initiatives on a smaller scale to evaluate their effectiveness and make necessary adjustments before full-scale implementation.
Augmented Reality and Work Order Visualization
The manufacturing industry is continually evolving, driven by technological advancements that offer new possibilities to optimize processes and boost productivity. One such technology that has gained prominence in recent years is Augmented Reality (AR).
AR is a cutting-edge technology that superimposes digital information onto the physical world, enhancing real-time interactions and improving decision-making processes. When applied to work order visualization, AR offers manufacturers a powerful tool to streamline production, improve collaboration, and maximize efficiency.
Understanding Augmented Reality
Augmented Reality is a technology that integrates digital information, such as images, text, and 3D models, into the real-world environment, thereby augmenting the user's perception of reality. Unlike Virtual Reality (VR), which creates a completely immersive digital experience, AR enhances the physical environment by overlaying digital content onto real-world objects.
AR is typically accessed through devices like smartphones, tablets, or AR glasses, which act as a window to the augmented environment.
Key Features and Benefits of Augmented Reality
a. Real-Time Visualization: AR enables real-time visualization of digital content in the physical environment, allowing users to interact with digital elements while maintaining situational awareness.
b. Hands-Free Operation: AR glasses or headsets enable hands-free operation, freeing up users' hands to perform tasks without the need to look away from the work area.
c. Enhanced Collaboration: AR facilitates remote collaboration, as users can share their augmented view with colleagues, enabling real-time feedback and assistance.
d. On-The-Job Training: AR can be used for on-the-job training, providing step-by-step visual guidance and instructions to workers as they perform tasks.
e. Error Reduction: AR-guided work orders can reduce human errors by providing visual cues and prompts, leading to improved accuracy and quality.
f. Increased Efficiency: By overlaying digital instructions onto physical objects, AR streamlines work processes and reduces the time needed to complete tasks.
Applications of Augmented Reality in Work Order Visualization
a. Work Order Instructions: AR can superimpose digital work order instructions onto equipment or assembly lines, guiding workers through complex tasks in real-time.
b. Maintenance and Repairs: AR can assist maintenance technicians by providing visual guides for equipment inspections, repairs, and preventive maintenance.
c. Quality Control: AR can be used to visually highlight quality checkpoints and inspection criteria, ensuring that products meet specified standards.
d. Remote Assistance: AR enables remote experts to guide on-site workers through complex procedures, reducing the need for on-site visits and expediting problem-solving.
e. Inventory Management: AR can help workers locate and identify specific items in the warehouse, reducing search times and improving inventory accuracy.
Challenges and Considerations in Implementing Augmented Reality
a. Initial Investment: Implementing AR technology requires a significant upfront investment in hardware, software, and training.
b. Integration with Existing Systems: Integrating AR with existing manufacturing systems and work order management software may require customization and compatibility testing.
c. Workforce Training: Manufacturers must invest in comprehensive training programs to ensure that workers are proficient in using AR devices and applications.
d. Data Security: The use of AR involves handling sensitive data and intellectual property, requiring robust data security measures to prevent unauthorized access.
Real-World Use Cases of Augmented Reality in Manufacturing
a. Boeing: Boeing uses AR glasses to assist technicians in assembling complex aircraft components, reducing errors and speeding up production.
b. DHL: DHL employs AR to streamline warehouse operations, optimizing order picking processes and improving worker productivity.
c. Siemens: Siemens utilizes AR to provide remote maintenance and repair assistance to field technicians, minimizing downtime and travel costs.
Future Prospects of Augmented Reality in Manufacturing
As AR technology continues to evolve, its potential impact on manufacturing is vast. Future developments may include advancements in gesture-based interactions, wider adoption of AR glasses with improved field of view, and integration with AI for enhanced data analysis and decision support.
AR is also likely to play a significant role in the expansion of the Internet of Things (IoT), creating a more interconnected and intelligent manufacturing ecosystem.
IoT and Real-Time Data in Work Order Tracking
As Industry 4.0 continues to drive digital transformation, the Internet of Things (IoT) has emerged as a game-changing technology that enables real-time data collection and analysis.
By integrating IoT devices and sensors with work order tracking systems, manufacturers can gain unprecedented visibility into their production processes, leading to improved decision-making, enhanced efficiency, and reduced downtime.
The Role of IoT in Work Order Tracking
The Internet of Things refers to the network of interconnected devices and sensors that collect and exchange data over the Internet. In the context of manufacturing, IoT plays a crucial role in work order tracking by enabling the seamless flow of real-time data between equipment, systems, and personnel.
IoT devices can monitor various aspects of production processes, such as machine performance, environmental conditions, and product quality, providing valuable insights for work order management.
Benefits of IoT-Driven Work Order Tracking
a. Real-Time Visibility: IoT-enabled sensors continuously collect data, offering real-time visibility into equipment performance and production status.
b. Predictive Maintenance: IoT data analytics can predict potential equipment failures, enabling proactive maintenance to prevent costly downtime.
c. Improved Efficiency: With real-time data insights, manufacturers can identify bottlenecks and inefficiencies in production processes, leading to process optimization.
d. Enhanced Quality Control: IoT sensors can monitor product quality parameters, enabling manufacturers to identify defects and maintain consistent quality.
e. Reduced Downtime: Predictive maintenance and real-time alerts allow manufacturers to address issues before they escalate, minimizing unplanned downtime.
f. Streamlined Inventory Management: IoT-driven work order tracking ensures accurate inventory data, optimizing material and parts replenishment.
Applications of IoT in Work Order Tracking
a. Machine Health Monitoring: IoT sensors can monitor machine conditions, such as temperature, vibration, and operating parameters, to assess machine health.
b. Asset Tracking: IoT devices enable real-time tracking of assets and equipment, providing their location and usage status.
c. Environmental Monitoring: IoT sensors can monitor environmental conditions, such as temperature and humidity, to ensure optimal production conditions.
d. Predictive Maintenance: IoT data analytics can predict equipment failures based on usage patterns and trigger maintenance alerts.
e. Real-Time Production Data: IoT devices capture real-time production data, such as cycle times and production rates, for immediate analysis.
Real-World Use Cases of IoT in Work Order Tracking
a. General Electric: GE uses IoT sensors to monitor the performance of its industrial equipment, optimizing maintenance schedules and reducing downtime.
b. Bosch: Bosch leverages IoT-enabled asset tracking to manage its manufacturing assets efficiently and minimize asset loss.
c. Airbus: Airbus uses IoT for real-time monitoring of aircraft assembly processes, improving production quality and efficiency.
The Future of IoT-Driven Work Order Tracking
As IoT technology continues to evolve, work order tracking in manufacturing will become even more sophisticated. Predictive analytics will be further refined, allowing manufacturers to anticipate issues and make proactive decisions.
The integration of IoT with artificial intelligence and machine learning will enable more advanced data analysis and intelligent decision-making. Furthermore, the expansion of 5G networks will enhance connectivity and enable faster data transfer, enabling manufacturers to harness the full potential of IoT in work order tracking.
AI-Driven Work Order Optimization
Artificial Intelligence (AI) is revolutionizing various industries, and manufacturing is no exception. In recent years, AI has emerged as a powerful tool for optimizing work order management and improving overall operational efficiency in manufacturing facilities.
By harnessing AI algorithms, manufacturers can analyze vast amounts of data, make data-driven decisions, and automate repetitive tasks, leading to faster, more accurate, and cost-effective work order execution.
Benefits of AI-Driven Work Order Optimization
- AI algorithms can analyze historical work order data to identify patterns and optimize work order scheduling and execution for enhanced efficiency.
- AI can predict equipment failures and recommend proactive maintenance actions, reducing unplanned downtime and minimizing production interruptions.
- AI-driven optimization helps manufacturers streamline processes and resource allocation, leading to cost savings and improved resource utilization.
- AI-powered analytics provide real-time insights, enabling better decision-making for work order prioritization and resource allocation.
- By automating repetitive tasks, AI reduces the risk of human errors, leading to improved accuracy and consistency in work order execution.
Applications of AI in Work Order Optimization
a. Predictive Maintenance: AI analyzes equipment data to predict potential failures and triggers work orders for maintenance before issues escalate.
b. Work Order Scheduling: AI algorithms consider factors such as equipment availability, labor capacity, and production schedules to optimize work order sequencing.
c. Inventory Management: AI can analyze demand patterns and optimize inventory levels, ensuring the availability of necessary parts for work orders.
d. Resource Allocation: AI algorithms optimize the allocation of resources, such as labor, materials, and equipment, to meet work order requirements efficiently.
e. Quality Control: AI-driven quality control systems can identify defects and anomalies in production, triggering work orders for corrective actions.
Challenges in Implementing AI-Driven Work Order Optimization
a. Data Quality and Integration: AI requires high-quality data from various sources, and integrating data from disparate systems can be challenging.
b. Skill Gap: Implementing AI technologies may require specialized skills and expertise that may not be readily available within the organization.
c. Initial Investment: The adoption of AI technologies may involve significant initial investments in hardware, software, and training.
Real-World Use Cases of AI-Driven Work Order Optimization
a. Siemens: Siemens uses AI-powered predictive maintenance to optimize work order scheduling and reduce maintenance costs.
b. General Electric: GE employs AI-driven analytics to predict equipment failures, leading to proactive work order generation for maintenance.
c. Schneider Electric: Schneider Electric utilizes AI algorithms to optimize resource allocation and work order scheduling, improving production efficiency.
The Future of AI-Driven Work Order Optimization
As AI technology advances, work order optimization in manufacturing will become increasingly sophisticated. The integration of AI with other emerging technologies, such as the Internet of Things (IoT) and robotics, will enable manufacturers to create more agile, autonomous production systems. AI-driven predictive analytics will become even more accurate, facilitating faster decision-making and ensuring seamless work order execution.
Additionally, AI-driven work order management will become more accessible and affordable to smaller manufacturers, fostering widespread adoption across the industry.
Predictive Analytics for Proactive Work Orders
Reactive maintenance practices can be costly and inefficient, often resulting in prolonged downtime and increased repair expenses. However, with the advent of predictive analytics, manufacturers now have a powerful tool to transition from reactive to proactive maintenance.
Predictive analytics, fueled by artificial intelligence (AI) and machine learning (ML) algorithms, allows manufacturers to analyze historical data, monitor real-time information, and predict potential equipment failures.
By leveraging data insights, manufacturers can schedule proactive work orders for maintenance, repairs, and replacements before issues escalate, reducing unplanned downtime and optimizing overall operational efficiency.
The Need for Proactive Maintenance in Manufacturing
Manufacturers face constant pressure to maximize productivity, minimize downtime, and reduce operational costs. Unplanned equipment failures can disrupt production schedules, lead to increased repair expenses, and affect product quality and customer satisfaction.
Proactive maintenance is essential to ensure that equipment operates at its optimal performance level, preventing potential issues before they become critical problems.
Predictive analytics plays a vital role in enabling proactive maintenance by providing real-time insights into equipment health and identifying early warning signs of failures.
The Role of Predictive Analytics in Proactive Work Orders
Predictive analytics involves the use of historical data, statistical algorithms, and ML techniques to identify patterns and trends, enabling predictions about future events. In the context of manufacturing, predictive analytics focuses on equipment health monitoring and failure prediction.
By analyzing sensor data, machine parameters, and historical maintenance records, predictive analytics can identify anomalies and patterns that may indicate potential equipment failures.
Based on these insights, manufacturers can trigger proactive work orders for maintenance, replacements, or repairs, ensuring that critical equipment remains in optimal condition.
Benefits of Predictive Analytics for Proactive Work Orders
- Predictive analytics allows manufacturers to schedule maintenance during planned downtime, minimizing unplanned disruptions to production.
- Proactive maintenance ensures that equipment operates at peak performance levels, optimizing overall productivity.
- By predicting potential equipment failures, manufacturers can avoid costly breakdowns and minimize repair expenses.
- Predictive analytics helps identify safety hazards and potential risks, allowing manufacturers to address them before accidents occur.
- Predictive analytics provides real-time insights, enabling data-driven decision-making in work order prioritization and resource allocation.
Applications of Predictive Analytics in Proactive Work Orders
a. Equipment Health Monitoring: Predictive analytics continuously monitors equipment data and identifies anomalies that may indicate potential failures.
b. Condition-Based Maintenance: By analyzing equipment performance data, predictive analytics triggers work orders for maintenance based on the actual condition of the equipment.
c. Trend Analysis: Predictive analytics analyzes historical data to identify patterns and trends, enabling manufacturers to anticipate future maintenance needs.
d. Failure Prediction: AI algorithms predict potential equipment failures based on data patterns, triggering proactive work orders to prevent breakdowns.
The Future of Predictive Analytics for Proactive Work Orders
As predictive analytics technology continues to evolve, manufacturers will have access to even more advanced tools for proactive maintenance. The integration of predictive analytics with other emerging technologies, such as the Internet of Things (IoT) and augmented reality, will further enhance the capabilities of proactive work order management.
Additionally, predictive analytics will become more accessible and user-friendly, enabling smaller manufacturers to harness its power for proactive maintenance, fostering widespread adoption across the industry.
Mobile Work Order Management for Flexibility
Mobile Work Order Management (MWOM) has emerged as a game-changing technology, empowering manufacturing operations to be efficient, responsive, and adaptable on the go.
By providing real-time access to work orders, equipment data, and task assignments, MWOM enables workers to carry out their tasks with increased efficiency and accuracy.
Understanding Mobile Work Order Management
Mobile Work Order Management refers to the use of mobile devices, such as smartphones and tablets, to create, assign, update, and track work orders in real-time. MWOM applications are typically integrated with the organization's Enterprise Resource Planning (ERP) system, allowing seamless data synchronization and visibility across departments.
The use of MWOM enables workers to access and execute work orders remotely, eliminating the need for paper-based processes and increasing the overall efficiency of the manufacturing operation.
Benefits of Mobile Work Order Management
- MWOM provides real-time updates on work order statuses, enabling managers to monitor progress and make timely decisions.
- MWOM facilitates instant communication between workers, supervisors, and other stakeholders, reducing delays and misunderstandings.
- Mobile devices capture data directly at the point of work, reducing the likelihood of errors and improving data accuracy.
- With MWOM, workers can access work orders and instructions instantly, saving time on manual data entry and paperwork.
- MWOM allows workers to carry out tasks from any location, promoting flexibility in scheduling and resource allocation.
Applications of Mobile Work Order Management in Manufacturing
a. Work Order Creation and Assignment: Supervisors can create work orders and assign tasks to workers directly from their mobile devices.
b. Asset Management: MWOM allows technicians to access asset information, maintenance history, and equipment data on the go.
c. Inventory Management: Workers can update inventory levels and request replenishments in real-time using MWOM applications.
d. Quality Control: MWOM enables real-time inspection and quality control checks, ensuring product quality and compliance.
e. Workforce Tracking: Mobile devices can track workers' locations and work progress, improving workforce management.
Enhancing Flexibility with Mobile Work Order Management
a. Remote Accessibility: MWOM allows workers to access work orders and data from anywhere, promoting remote and flexible working arrangements.
b. Adaptable Scheduling: Mobile devices enable workers to adjust their schedules and prioritize urgent tasks on-the-fly.
c. Rapid Decision-Making: Real-time updates and data visibility through MWOM empower managers to make quick and informed decisions.
d. On-Demand Reporting: MWOM applications can generate instant reports and performance metrics, aiding in real-time analysis and decision-making.
e. Agility in Maintenance: Mobile access to asset data and maintenance histories allows technicians to respond quickly to equipment breakdowns and maintenance needs.
Blockchain and Secure Work Order Transactions
Blockchain technology has gained significant attention and popularity in recent years, primarily due to its association with cryptocurrencies like Bitcoin.
However, the potential applications of blockchain extend beyond digital currencies and into various industries, including manufacturing. Blockchain's decentralized and immutable nature makes it an ideal candidate for securing work order transactions in manufacturing operations.
Understanding Blockchain Technology
At its core, blockchain is a distributed and decentralized digital ledger that records transactions securely and transparently. It consists of a chain of blocks, with each block containing a list of transactions. Each block is linked to the previous block through cryptographic hashing, creating a chain of blocks.
Once a block is added to the chain, it becomes immutable, meaning that the data recorded in the block cannot be altered or deleted. This immutability and decentralized nature make blockchain highly secure and resistant to fraud and tampering.
The Role of Blockchain in Secure Work Order Transactions
In manufacturing, work order transactions involve various parties, such as suppliers, manufacturers, and distributors, who need to collaborate and exchange data securely. Blockchain can facilitate these transactions by providing a secure and transparent platform for recording and verifying work order details.
As each block in the chain contains a list of transactions, every step of the work order process is recorded in a tamper-proof and auditable manner. This ensures that all parties involved can trust the integrity of the data, leading to increased confidence in the work order process.
Advantages of Using Blockchain for Work Order Transactions
- Blockchain's cryptographic hashing and consensus mechanisms provide robust security against unauthorized access and tampering.
- All parties involved in the work order process can access and verify the data recorded on the blockchain, promoting transparency.
- By automating and streamlining work order transactions, blockchain reduces the need for intermediaries, leading to faster and more efficient processes.
- The elimination of intermediaries and the automation of processes can lead to cost savings in work order management.
- Blockchain's immutability ensures that all actions and data recorded in the work order process are transparent and accountable.
Applications of Blockchain in Work Order Transactions
a. Supply Chain Management: Blockchain can track and verify the movement of goods and materials across the supply chain, ensuring transparency and authenticity.
b. Smart Contracts: Blockchain can execute and enforce self-executing smart contracts, automating work order transactions based on predefined conditions.
c. Quality Control: Blockchain can record and verify quality control data, ensuring that products meet specified standards throughout the manufacturing process.
d. Maintenance and Repairs: Blockchain can record maintenance and repair data, providing an auditable trail of service history for equipment and assets.
Implementing Blockchain for Work Order Transactions
a. Selecting the Right Blockchain Platform: Manufacturers must choose a blockchain platform that aligns with their needs and requirements, such as public or private blockchains.
b. Integrating with Existing Systems: Integrating blockchain with existing ERP and other systems is crucial for seamless data synchronization.
c. Ensuring Data Privacy: Manufacturers must implement data privacy measures, as blockchain's transparent nature may reveal sensitive information.
d. Training and Adoption: Proper training and education are essential to ensure that all parties involved understand and adopt the blockchain-based work order process.
e. Regulatory Compliance: Manufacturers must ensure that the use of blockchain complies with relevant industry regulations and standards.
Challenges and Limitations of Blockchain in Work Order Transactions
a. Scalability: Blockchain's current scalability limitations may hinder its adoption for large-scale manufacturing operations.
b. Energy Consumption: Proof-of-Work blockchain consensus mechanisms can be energy-intensive, raising environmental concerns.
c. Interoperability: Integrating blockchain with existing systems and ensuring interoperability with other technologies can be complex.
d. Cost and Complexity: Implementing blockchain solutions may involve significant upfront costs and technical complexity.
Real-World Examples of Blockchain in Manufacturing
a. IBM and Maersk: IBM and Maersk have collaborated to create a blockchain-based platform for global trade, simplifying documentation and tracking cargo.
b. Bosch and IOTA: Bosch and IOTA are working on a blockchain-based data marketplace for the Internet of Things, facilitating secure data exchange.
c. Foxconn and Aergo: Foxconn and Aergo are exploring blockchain-based solutions for supply chain transparency and traceability.
The Future of Blockchain in Work Order Transactions
As blockchain technology continues to evolve, its potential impact on work order transactions in manufacturing will only grow stronger. Advancements in blockchain scalability, interoperability, and energy efficiency will enable broader adoption in the manufacturing sector.
Additionally, the integration of blockchain with other emerging technologies, such as IoT and AI, will further enhance its capabilities in securing work order transactions and optimizing manufacturing operations.
Collaborative Work Orders in the Connected Factory
The manufacturing landscape is undergoing a significant transformation with the rise of Industry 4.0 and the connected factory. In this digitally-driven era, manufacturers are leveraging advanced technologies to enhance operational efficiency, communication, and collaboration.
Collaborative Work Orders have emerged as a key component of the connected factory, enabling real-time communication and coordination among various stakeholders involved in the work order process.
Understanding Collaborative Work Orders
Collaborative Work Orders refer to a modern approach to work order management that emphasizes real-time collaboration, communication, and coordination among different teams and individuals involved in the work order process.
Traditional work order systems often relied on manual paperwork and disjointed communication channels, leading to delays, errors, and inefficiencies. In contrast, Collaborative Work Orders harness the power of digital technologies to streamline and automate the work order process, ensuring seamless collaboration and improved decision-making.
The Connected Factory and Collaborative Work Orders
The connected factory is a concept driven by Industry 4.0 principles, where manufacturing processes are interconnected, data-driven, and smart. Collaborative Work Orders are an essential part of the connected factory, as they enable real-time data exchange, communication, and collaboration between machines, workers, and systems.
By integrating Collaborative Work Orders with other technologies such as the Internet of Things (IoT), artificial intelligence (AI), and cloud computing, manufacturers can achieve a highly efficient and responsive production environment.
Technologies Enabling Collaborative Work Orders
a. Internet of Things (IoT): IoT devices, such as sensors and smart machines, gather real-time data from the factory floor, providing valuable insights into equipment performance and production status.
b. Cloud Computing: Cloud-based systems allow for seamless data storage, accessibility, and sharing, enabling real-time collaboration among geographically dispersed teams.
c. Mobile Devices: Mobile devices, such as smartphones and tablets, empower workers to access and update work order information on the go, increasing flexibility and responsiveness.
d. Artificial Intelligence (AI): AI-driven analytics can analyze vast amounts of data, providing actionable insights to optimize work order processes and resource allocation.
e. Augmented Reality (AR): AR technologies enable workers to receive visual instructions and data overlay in real-time, improving task accuracy and efficiency.
Benefits of Collaborative Work Orders in the Connected Factory
- Collaborative Work Orders facilitate instant communication and updates between workers, supervisors, and other stakeholders, reducing delays and misunderstandings.
- The seamless exchange of data and information enables effective collaboration among different teams, leading to improved decision-making.
- By enabling quick identification of issues and timely maintenance, Collaborative Work Orders minimize unplanned downtime and production disruptions.
- Real-time data and insights allow for better resource planning and allocation, optimizing workforce efficiency and material usage.
- Collaborative Work Orders provide actionable data and insights, supporting data-driven decision-making throughout the work order process.
Implementing Collaborative Work Orders in the Connected Factory
- Collaborative Work Orders require seamless integration with existing systems, such as ERP, MES, and CMMS, to ensure data synchronization and accuracy.
- Intuitive and user-friendly interfaces are essential to encourage adoption and ease the transition for workers and supervisors.
- As Collaborative Work Orders involve real-time data exchange, robust data security measures must be in place to protect sensitive information.
- Adequate training and education are crucial to ensure that all stakeholders understand and effectively use the Collaborative Work Order system.
- Regular performance monitoring and feedback gathering help identify areas for improvement and optimization.
Future Trends in Collaborative Work Orders and the Connected Factory
a. 5G Connectivity: The rollout of 5G technology will provide faster and more reliable connectivity, enabling real-time collaboration in the connected factory.
b. AI and Predictive Analytics: AI-driven predictive analytics will optimize Collaborative Work Orders by anticipating equipment failures and maintenance needs.
c. Edge Computing: Edge computing will enable real-time data processing and decision-making at the factory level, reducing latency and enhancing responsiveness.
d. Blockchain Integration: Blockchain technology can add an extra layer of security and transparency to Collaborative Work Orders, ensuring trust and data integrity.
e. Autonomous Systems: The integration of autonomous systems and robots will further optimize Collaborative Work Orders by automating repetitive tasks and workflows.
Work Orders and Sustainability in Manufacturing
As concerns about climate change, resource depletion, and environmental impact continue to rise, manufacturers are increasingly looking for ways to integrate sustainable practices into their operations.
Work orders play a vital role in manufacturing processes, and optimizing them for sustainability can lead to significant positive impacts on both the environment and the company's bottom line.
Resource Optimization and Waste Reduction
Work orders dictate the use of raw materials, components, and resources throughout the production process. By carefully planning and managing work orders, manufacturers can optimize resource utilization, minimize waste, and reduce material and product losses.
Implementing circular economy principles, such as recycling and reusing materials, can further enhance sustainability by closing the loop on resource consumption.
Lean Manufacturing and Green Work Orders
Lean manufacturing principles aim to eliminate waste and inefficiencies in production processes. When applied to work orders, lean practices can streamline operations, reduce unnecessary steps, and enhance productivity.
By aligning lean principles with eco-friendly practices, companies can develop "green" work orders that prioritize sustainability while maintaining high-quality production.
Sustainable Supplier Collaboration
Work orders often involve collaborations with suppliers and vendors. Companies can drive sustainability throughout their supply chain by selecting eco-friendly suppliers, using locally sourced materials, and evaluating the environmental impact of their partners.
By integrating sustainability requirements into work orders, manufacturers can ensure that all stakeholders are aligned with the company's green objectives.
Lifecycle Analysis for Product Design
Work orders are closely tied to product design and development. By conducting a life cycle analysis, manufacturers can assess the environmental impact of their products from raw material extraction to end-of-life disposal.
This analysis helps identify opportunities for reducing the product's carbon footprint and promoting sustainable design principles.
Renewable Energy Integration
Manufacturers can incorporate renewable energy sources, such as solar and wind power, into their work order execution. By scheduling energy-intensive processes during periods of high renewable energy availability, companies can reduce their reliance on fossil fuels and contribute to a cleaner energy grid.
Employee Engagement and Sustainability Training
Engaging employees in sustainability initiatives is essential for successful implementation. By promoting sustainability awareness, training employees on eco-friendly practices, and incentivizing green behavior, manufacturers can foster a culture of environmental responsibility and encourage employees to contribute to sustainable work order execution.
Sustainable Transportation and Logistics
Work orders often involve the transportation of raw materials, products, and components. Companies can implement sustainable transportation practices, such as using electric vehicles or optimizing delivery routes, to minimize emissions and reduce the environmental impact of logistics operations.
Environmental Metrics and Reporting
Monitoring and reporting on sustainability metrics related to work orders can help manufacturers track their progress and set targets for improvement. Key performance indicators (KPIs), such as energy consumption per unit produced, waste generation, and carbon emissions, can be incorporated into work order management systems for ongoing analysis and optimization.
3D Printing and Customized Work Orders
The advent of 3D printing technology has revolutionized the manufacturing industry, enabling the creation of complex and customized products with unprecedented speed and efficiency.
Coupled with customized work orders, 3D printing has the potential to transform traditional manufacturing processes, opening new possibilities for innovation, personalization, and sustainability.
Understanding 3D Printing in Manufacturing
3D printing, also known as additive manufacturing, is a process of creating three-dimensional objects by adding material layer by layer based on a digital model. It eliminates the need for traditional manufacturing techniques like machining, molding, and casting, allowing for greater design freedom and rapid prototyping.
Customized Work Orders: Tailoring Manufacturing Processes
Customized work orders involve tailoring manufacturing processes to meet specific customer demands and individual requirements. Instead of producing standardized products in bulk, customized work orders enable manufacturers to create unique and personalized items that align precisely with customer preferences.
The Synergy of 3D Printing and Customized Work Orders
a. Design Flexibility: 3D printing allows for intricate and complex designs that are difficult or impossible to achieve with traditional manufacturing methods. Customized work orders leverage this design flexibility to create one-of-a-kind products.
b. Rapid Prototyping: With 3D printing, manufacturers can quickly produce prototypes and iterations of products, facilitating the customization process in response to customer feedback.
c. Mass Customization: 3D printing enables cost-effective production of small batches of custom products, making mass customization a viable option for manufacturers.
d. Waste Reduction: 3D printing is an inherently sustainable process, as it only uses the exact amount of material needed to create a product, minimizing waste.
e. Local Manufacturing: Customized work orders paired with 3D printing allow for decentralized manufacturing, reducing shipping distances and lowering carbon emissions.
Benefits of 3D Printing and Customized Work Orders
a. Personalization: Customers can have products tailored to their preferences, leading to increased customer satisfaction and loyalty.
b. Reduced Inventory: Manufacturers can produce products on-demand, eliminating the need for large inventories and associated storage costs.
c. Improved Time-to-Market: Rapid prototyping and quicker production cycles result in faster time-to-market for new products.
d. Enhanced Innovation: The combination of 3D printing and customized work orders fosters a culture of innovation, encouraging experimentation and novel design ideas.
e. Sustainability: The waste reduction and localized manufacturing inherent in 3D printing contribute to more sustainable and environmentally friendly practices.
Challenges of Implementing 3D Printing and Customized Work Orders
- Initial investment in 3D printing equipment and materials can be substantial, especially for small and medium-sized manufacturers.
- 3D printing requires specialized knowledge and skills, necessitating training for employees to adapt to this technology.
- While 3D printing is suitable for customized production, it may face challenges in scaling up for high-volume manufacturing.
- Customized products may raise concerns about intellectual property rights and counterfeiting.
- The range of available materials for 3D printing may be more limited compared to traditional manufacturing methods.
Case Studies: Successful Implementation of 3D Printing and Customized Work Orders
a. Nike: Nike implemented 3D printing to create customized and personalized sports shoes, allowing customers to design their shoe patterns and colors.
b. General Electric: GE uses 3D printing to produce customized turbine components, improving product performance and reducing lead times.
c. Airbus: Airbus employs 3D printing to manufacture lightweight and complex aircraft parts, optimizing fuel efficiency and enhancing aircraft performance.
d. Shapeways: Shapeways is a 3D printing service that enables designers and customers to create and order customized products in a variety of materials.
Regulatory and Legal Considerations
a. Intellectual Property: Manufacturers must navigate intellectual property rights and ensure compliance with copyright and patent laws.
b. Quality Standards: Implementing 3D printing may require adherence to specific quality standards and certifications.
c. Liability: Manufacturers must address liability concerns, especially when producing customized products for critical applications.
d. Data Privacy: Personalized products involve the collection and use of customer data, necessitating robust data protection measures.
Future Implications of 3D Printing and Customized Work Orders
a. On-Demand Manufacturing: As 3D printing technology advances, on-demand manufacturing will become more accessible, transforming supply chains and distribution models.
b. Decentralized Production: 3D printing and customized work orders may lead to more localized production networks, reducing reliance on overseas manufacturing.
c. Co-Creation and Collaboration: Manufacturers and customers may increasingly collaborate in the design and production of personalized products.
d. Sustainability Innovations: 3D printing's inherent sustainability may drive manufacturers to explore more eco-friendly materials and production processes.
Autonomous Robots and Work Order Execution
The integration of autonomous robots in manufacturing has ushered in a new era of efficiency, precision, and productivity. These intelligent machines, equipped with advanced sensors and artificial intelligence, can execute work orders with minimal human intervention, revolutionizing manufacturing operations across industries.
Understanding Autonomous Robots in Manufacturing
Autonomous robots, also known as cobots or collaborative robots, are designed to work alongside humans, enhancing productivity and safety in manufacturing environments.
They can perform tasks autonomously, without direct human control, and are equipped with sophisticated sensors, cameras, and AI algorithms to perceive their surroundings and make real-time decisions.
The Role of Autonomous Robots in Work Order Execution
a. Task Automation: Autonomous robots can execute various tasks specified in work orders, such as assembly, welding, painting, and material handling, with high precision and repeatability.
b. Workforce Augmentation: Cobots complement human workers by taking over repetitive and physically demanding tasks, allowing employees to focus on more complex and value-added activities.
c. Continuous Operation: Unlike human workers, autonomous robots can operate 24/7, optimizing production schedules and reducing lead times.
d. Quality Control: Advanced vision systems on cobots can detect defects and inconsistencies during the manufacturing process, ensuring high-quality output.
e. Safety Enhancement: Cobots are designed with built-in safety features and collaborative capabilities to work safely alongside humans, minimizing workplace accidents.
Benefits of Autonomous Robots in Work Order Execution
- By automating routine tasks, cobots can significantly increase production output and overall productivity.
- Autonomous robots execute work orders with consistent precision, leading to higher product quality and reduced defects.
- Cobots can work around the clock, accelerating production timelines and improving order fulfillment.
- By offloading repetitive tasks to robots, manufacturers can optimize their human workforce for higher-skilled and strategic roles.
- Collaborative robots are designed to work safely with humans, minimizing the risk of workplace accidents.
Applications of Autonomous Robots in Work Order Execution
a. Assembly: Cobots excel at assembling products, ensuring precise alignment and fitting of components.
b. Welding: Autonomous robots can perform welding tasks with exceptional accuracy, even in complex shapes and materials.
c. Material Handling: Cobots can efficiently transport materials and components between workstations, reducing manual labor and streamlining production flows.
d. Inspection and Quality Control: Autonomous robots equipped with advanced vision systems can inspect products for defects and deviations from specifications.
e. Packaging and Palletizing: Cobots are proficient in packaging products and palletizing them for shipment, improving logistics efficiency.
Challenges in Implementing Autonomous Robots for Work Order Execution
a. Cost: The initial investment in cobots and associated infrastructure can be significant for some manufacturers.
b. Integration with Existing Systems: Integrating cobots into existing manufacturing processes and work order systems may require specialized expertise.
c. Skills Gap: Implementing cobots necessitates skilled technicians who can program, maintain, and troubleshoot these advanced machines.
d. Safety Compliance: Ensuring safety compliance when cobots work alongside humans requires careful risk assessment and mitigation measures.
e. Scalability: Some manufacturing processes may be difficult to scale with cobots, leading to challenges in accommodating fluctuating demand.
Successful Case Studies of Autonomous Robots in Work Order Execution
a. BMW: BMW uses cobots in its automotive assembly lines to enhance production speed and accuracy, resulting in improved quality and reduced cycle times.
b. Amazon: Amazon employs cobots in its fulfillment centers to pick and pack items, streamlining order fulfillment and increasing operational efficiency.
c. Siemens: Siemens integrates cobots into its manufacturing processes to improve product quality and optimize workforce allocation.
d. ABB: ABB utilizes cobots in its welding applications, resulting in faster and more precise welding processes.
e. Foxconn: Foxconn deploys cobots in its electronics manufacturing, increasing production capacity and reducing human-intensive tasks.
Future Implications of Autonomous Robots in Work Order Execution
a. Increased Adoption: As cobot technology matures and costs decrease, more manufacturers will adopt autonomous robots for work order execution.
b. Cross-Industry Integration: Cobots will find applications in diverse industries, expanding their role beyond traditional manufacturing sectors.
c. Customization and Flexibility: Future cobots may become more adaptable, allowing for easy reprogramming and customization to suit specific tasks.
d. AI Advancements: Autonomous robots will benefit from AI advancements, becoming more intuitive and capable of handling complex tasks.
e. Human-Robot Collaboration: As cobots become more sophisticated, they will collaborate seamlessly with human workers, maximizing workforce efficiency.
Remote Work Order Management in a Global Landscape
Remote work order management involves overseeing and coordinating work orders from diverse locations, with teams collaborating virtually through digital tools and platforms. It allows organizations to efficiently manage work orders, allocate resources, and monitor progress without the need for physical presence at the worksite.
Benefits of Remote Work Order Management
a. Global Collaboration: Remote work order management enables teams from different parts of the world to collaborate seamlessly, fostering diverse perspectives and efficient problem-solving.
b. Real-Time Updates: Digital platforms facilitate real-time updates on work orders, ensuring that teams stay informed about progress, changes, and potential delays.
c. Cost Savings: Remote work order management reduces travel costs and expenses associated with physical meetings and on-site visits.
d. Flexibility: Remote work allows for flexible work arrangements, accommodating the needs of a diverse and global workforce.
e. Enhanced Productivity: Remote work order management eliminates time-consuming commutes and allows employees to focus on tasks without disruptions.
Challenges in Remote Work Order Management
a. Communication: Maintaining effective communication across different time zones and cultures can be challenging.
b. Technology Infrastructure: Access to stable and reliable internet connections and appropriate digital tools is crucial for successful remote work order management.
c. Security Concerns: Protecting sensitive data and ensuring secure communication channels is essential in a global environment.
d. Cultural Differences: Working with teams from diverse cultural backgrounds may require sensitivity and adaptation to ensure effective collaboration.
e. Team Cohesion: Remote work may pose challenges in building team cohesion and a sense of belonging among global team members.
Best Practices for Remote Work Order Management
a. Technology Integration: Utilize robust project management and communication tools to ensure seamless coordination and real-time updates.
b. Clear Communication Protocols: Establish clear communication protocols, including scheduled virtual meetings, to keep teams aligned.
c. Goal Setting: Set clear goals and objectives for each work order, ensuring that all team members understand their roles and responsibilities.
d. Regular Performance Review: Conduct regular performance reviews to monitor progress, identify challenges, and implement necessary improvements.
e. Cultural Awareness: Promote cultural awareness and sensitivity among team members to foster a positive and inclusive work environment.
Implementing Remote Work Order Management in a Global Landscape
a. Infrastructure Assessment: Evaluate the technology infrastructure and capabilities of each location to ensure smooth communication and collaboration.
b. Training and Development: Provide training and development opportunities to equip employees with the necessary skills for remote work order management.
c. Data Security: Implement robust data security measures to safeguard sensitive information and comply with relevant data protection regulations.
d. Performance Metrics: Establish key performance indicators (KPIs) to measure the success of remote work order management and make data-driven improvements.
e. Feedback Mechanism: Create a feedback mechanism to gather insights from global teams and continuously enhance the remote work process.
Future Trends: Innovations Shaping the Future of Work Orders
The future of work orders is being reshaped by rapid advancements in technology, changing work dynamics, and evolving business needs. As organizations strive for greater efficiency, agility, and collaboration, innovations are emerging to transform the way work orders are managed and executed.
Artificial Intelligence (AI) and Automation
AI and automation are revolutionizing work order management by streamlining processes, enhancing decision-making, and reducing manual intervention. AI-powered algorithms can analyze historical data to predict potential issues and optimize work order schedules, leading to improved productivity and reduced downtime.
Automation can automatically trigger work orders based on predefined conditions or sensor data, ensuring proactive maintenance and prompt responses to equipment failures.
Internet of Things (IoT) Integration
The integration of IoT devices with work order management systems allows for real-time monitoring of equipment and assets. IoT sensors can detect anomalies, trigger work orders, and collect data for predictive maintenance.
This enables organizations to move from reactive to proactive maintenance strategies, increasing operational efficiency and reducing costly downtime.
Augmented Reality (AR) for Remote Assistance
AR technology is transforming work order execution by enabling remote assistance and guidance. Field technicians can wear AR glasses or use mobile devices to receive step-by-step instructions, view equipment schematics, and access real-time data while on-site.
This immersive experience enhances troubleshooting capabilities, reduces human errors, and accelerates work order completion.
Blockchain for Enhanced Transparency
Blockchain technology is revolutionizing work order management by providing a decentralized and transparent record of all work order transactions. This ensures data integrity, minimizes disputes, and facilitates secure collaboration among different stakeholders.
Blockchain-based smart contracts can automate payment processing and trigger work orders based on predefined conditions, improving efficiency and trust in the supply chain.
Predictive Analytics for Resource Allocation
Predictive analytics leverages historical data and AI algorithms to forecast resource requirements for upcoming work orders.
By analyzing past performance and project demands, organizations can optimize resource allocation, ensuring the right skill sets and equipment are available at the right time and place. This results in cost savings and improved project timelines.
Cloud-Based Collaboration
Cloud-based work order management platforms enable seamless collaboration among global teams, contractors, and suppliers. Real-time access to work order data, progress updates, and communication tools foster enhanced teamwork and decision-making.
Cloud solutions also eliminate the need for manual data entry and facilitate instant updates across the organization.
Mobile Work Order Apps
Mobile work order apps empower technicians to access, update, and complete work orders directly from their mobile devices. This eliminates the need for paper-based processes and allows for immediate data entry and synchronization.
Mobile apps also support offline capabilities, ensuring work orders can be executed even in areas with limited connectivity.
Integration with Enterprise Resource Planning (ERP) Systems
Seamless integration between work order management systems and ERP platforms enables real-time data exchange and a holistic view of operations. Integration streamlines workflows enhances data accuracy, and improves financial visibility.
This enables organizations to make data-driven decisions and optimize their entire supply chain.
Remote Work Order Execution
Remote work orders are becoming more prevalent as the world embraces flexible work arrangements. With the right technology and collaboration tools, teams can efficiently execute work orders from anywhere, enabling organizations to tap into a global talent pool and foster a more diverse and agile workforce.
How Can Deskera Help You?
Deskera MRP allows you to closely monitor the manufacturing process. From the bill of materials to the production planning features, the solution helps you stay on top of your game and keep your company's competitive edge.
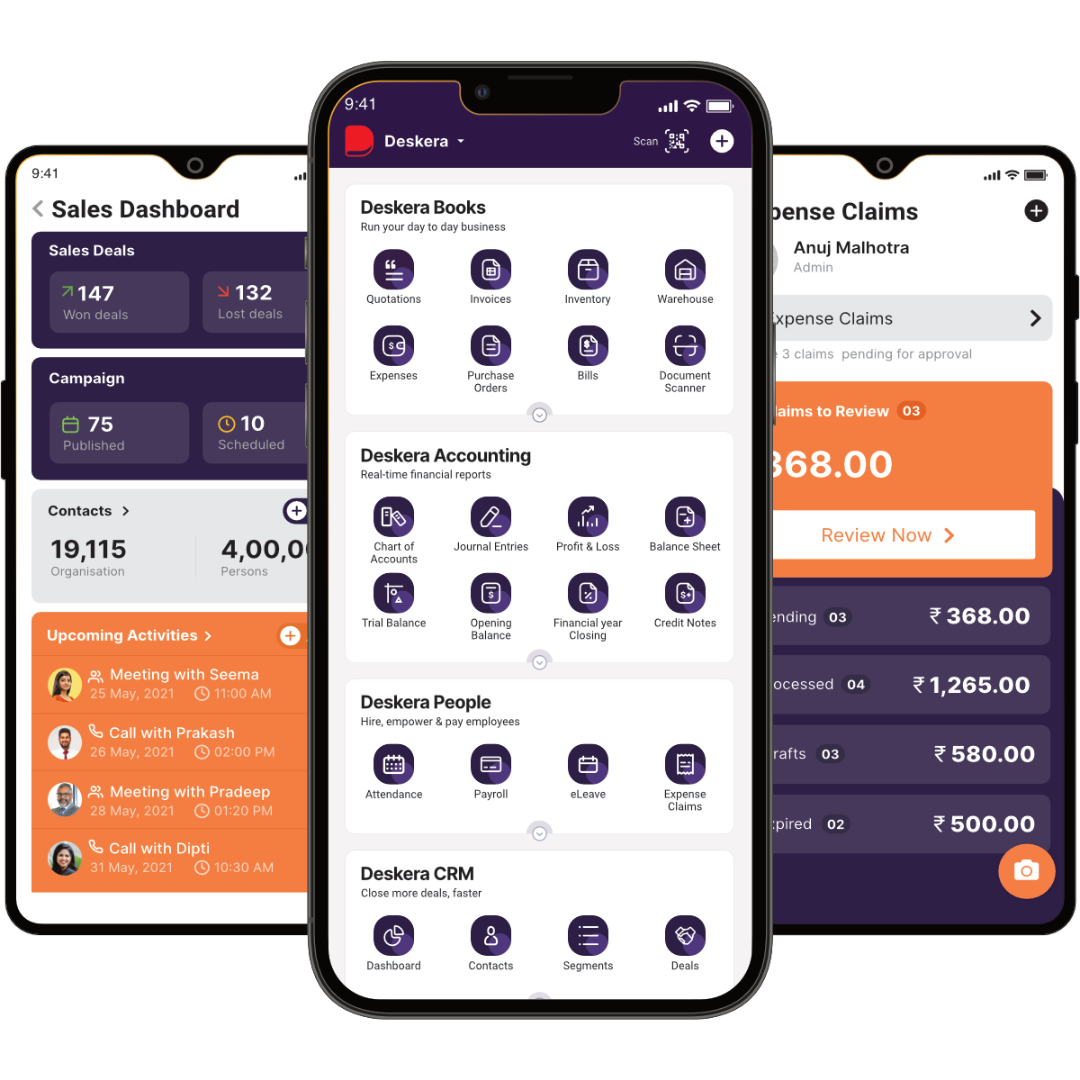
Deskera ERP and MRP system can help you:
- Manage production plans
- Maintain Bill of Materials
- Generate detailed reports
- Create a custom dashboard
Deskera ERP is a comprehensive system that allows you to maintain inventory, manage suppliers, and track supply chain activity in real time, as well as streamline a variety of other corporate operations.
Deskera Books enables you to manage your accounts and finances more effectively. Maintain sound accounting practices by automating accounting operations such as billing, invoicing, and payment processing.
Deskera CRM is a strong solution that manages your sales and assists you in closing agreements quickly. It not only allows you to do critical duties such as lead generation via email, but it also provides you with a comprehensive view of your sales funnel.
Deskera People is a simple tool for taking control of your human resource management functions. The technology not only speeds up payroll processing but also allows you to manage all other activities such as overtime, benefits, bonuses, training programs, and much more. This is your chance to grow your business, increase earnings, and improve the efficiency of the entire production process.
Conclusions
The future of work orders in manufacturing holds great promise as technology continues to advance, and industries embrace digital transformation. This article has explored the evolving landscape of work orders, their significance inefficient manufacturing, and the potential transformative impact of emerging technologies.
Work orders serve as crucial communication tools, providing detailed instructions to workers and enabling efficient resource allocation, ultimately enhancing overall productivity and reducing operational costs.
Digitalization and automation are reshaping work order management, offering opportunities for real-time tracking, predictive analytics, and seamless integration with other manufacturing systems.
Digital work orders offer improved accuracy, accessibility, and data integration, streamlining operations, reducing paperwork, and enabling faster decision-making. Internet of Things (IoT) devices, Artificial Intelligence (AI), and Augmented Reality (AR) are revolutionizing work order execution, enabling predictive maintenance, remote assistance, and data-driven insights.
By embracing these advancements and leveraging data analytics, manufacturers can continuously improve work processes and achieve operational excellence. As the manufacturing landscape evolves, work orders remain a cornerstone in guiding and optimizing manufacturing operations, ushering in a future of innovation, efficiency, and competitiveness.
Key Takeaways
- Work orders play a vital role in guiding and streamlining manufacturing processes, ensuring clear communication and efficient resource allocation.
- The future of work orders in manufacturing is digital, as industries embrace technological advancements and digital transformation.
- Digital work orders offer improved accuracy, accessibility, and data integration, streamlining operations and reducing paperwork.
- Emerging technologies, such as IoT, AI, AR, and blockchain, are transforming work order management, enabling real-time tracking, predictive analytics, and enhanced collaboration.
- Predictive maintenance powered by AI algorithms anticipates maintenance needs, minimizing downtime and optimizing asset performance.
- Augmented Reality (AR) provides hands-free work instructions and remote assistance, reducing errors and speeding up tasks.
- Digital twin technology allows manufacturers to simulate and optimize work order processes, identifying the most efficient workflows.
- Blockchain's decentralized nature ensures transparency and trust in work order execution across the supply chain.
- Collaborative platforms and cloud-based systems facilitate real-time data sharing and communication among team members.
- The ultra-fast and low-latency capabilities of 5G networks support real-time data exchange and seamless integration of IoT devices and AR applications.
Related Articles

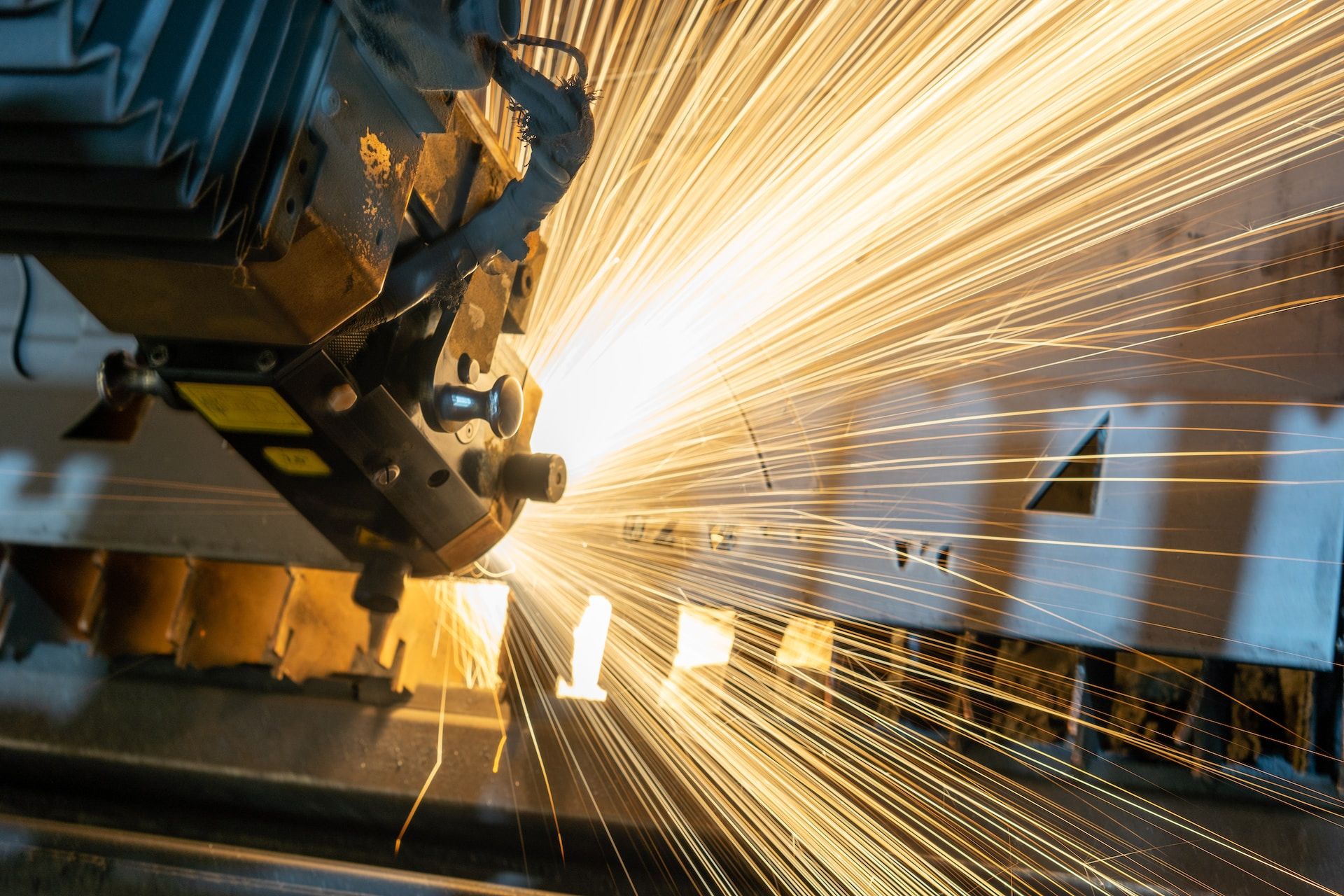
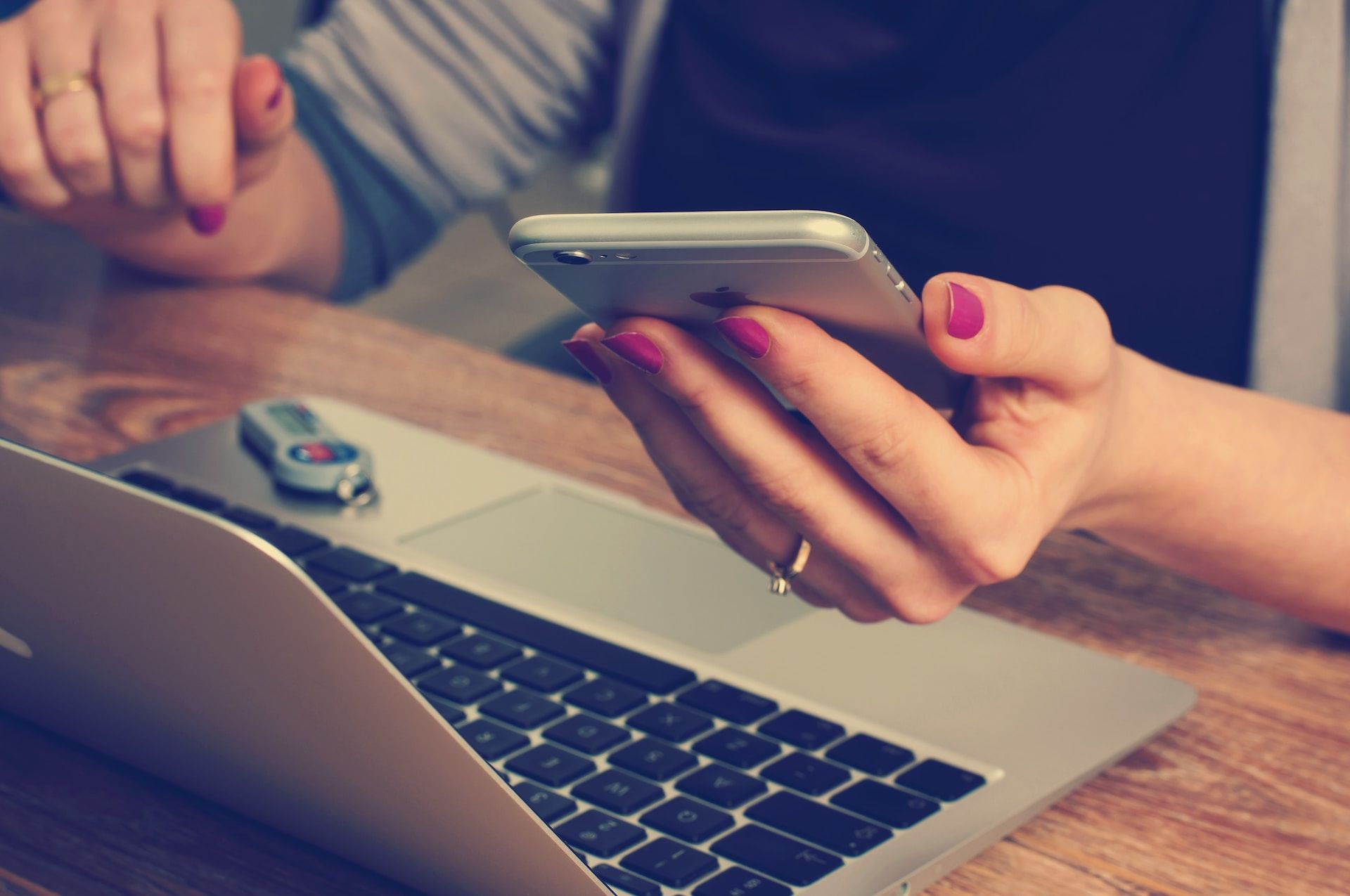
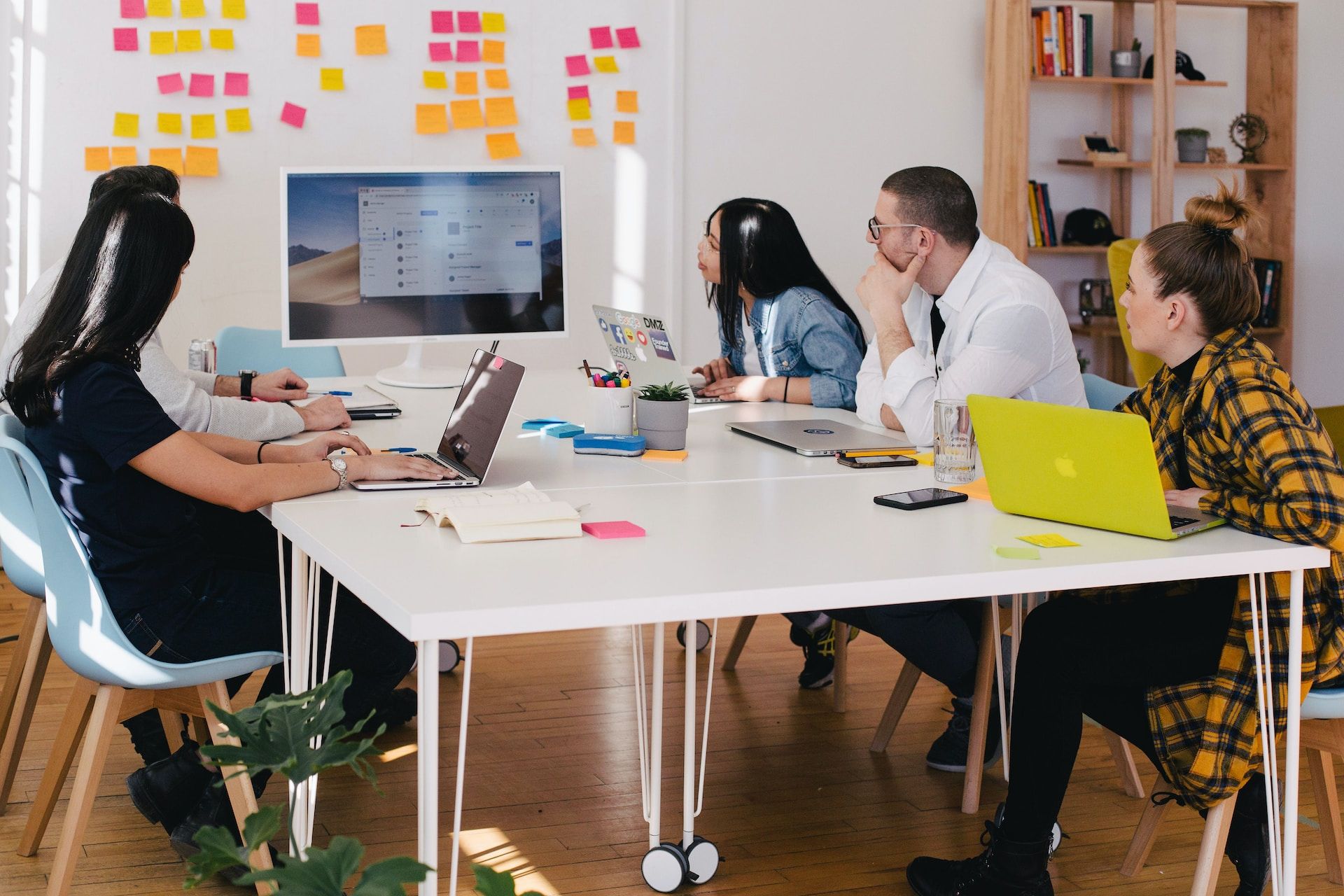