In the dynamic landscape of the manufacturing industry, finding the right equilibrium between available resources and customer needs is crucial for success. In this article, we will explore valuable tips and strategies to help you master the art of manufacturing production scheduling and achieve optimal efficiency.
According to the latest statistics from the US Census Bureau, the manufacturing industry is a cornerstone of the US economy, contributing significantly to its growth and development.
With such substantial figures at stake, it becomes paramount for manufacturers to effectively manage their production schedules to meet customer demand while utilizing available resources efficiently.
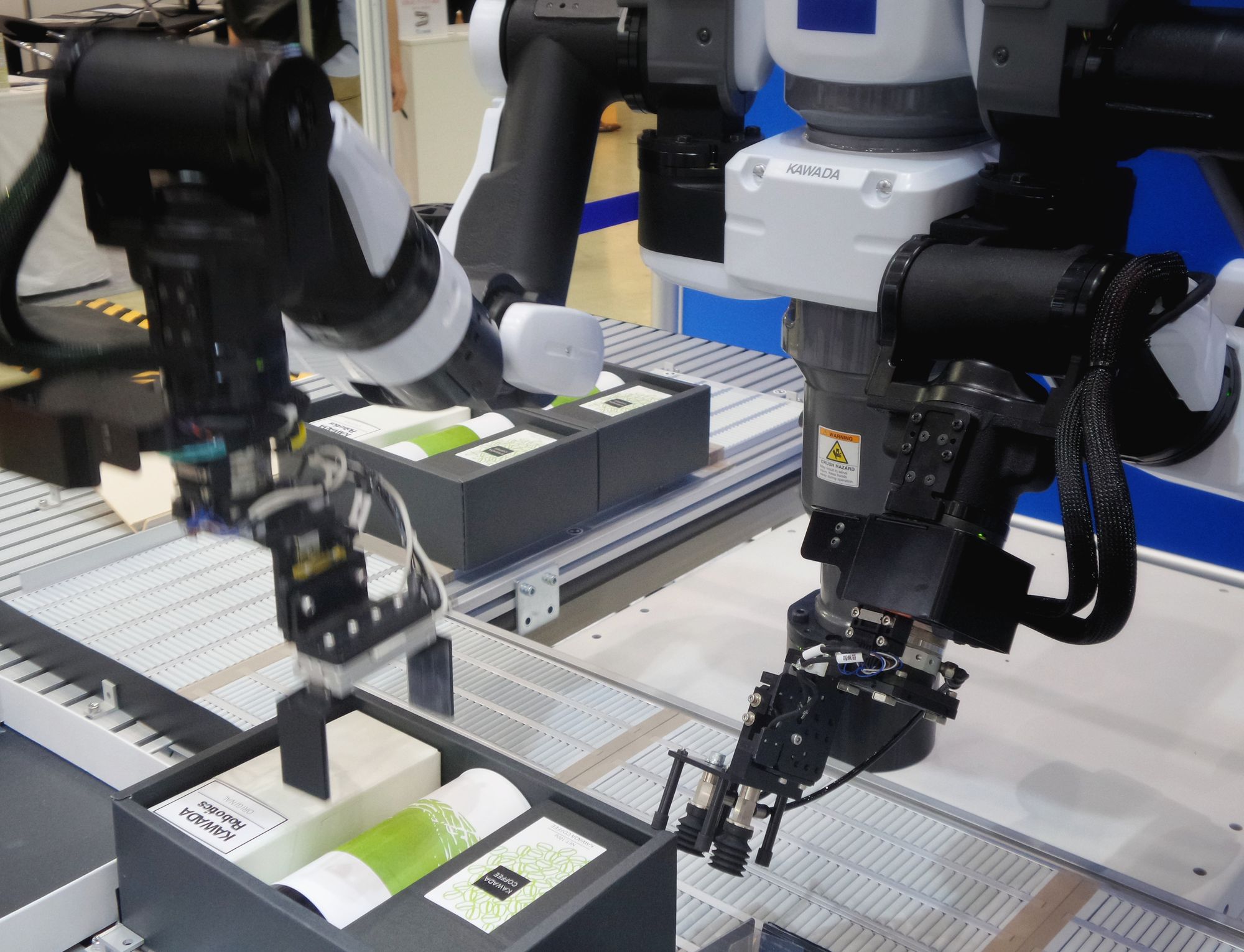
Balancing capacity and demand requires a deep understanding of market dynamics, customer preferences, and internal capabilities. It involves harmonizing the production capacity of your manufacturing facilities with the ever-changing demands of your customers. Striking the right balance empowers you to optimize your operations, reduce costs, and enhance customer satisfaction.
In this article, we will delve into the intricacies of manufacturing production scheduling and provide you with practical tips to help you navigate this challenging terrain. We will explore various capacity and demand management aspects, starting with demand forecasting.
As the manufacturing landscape continues to evolve, embracing digitalization and automation becomes increasingly important.
Let's dive into the world of capacity and demand management, uncover valuable tips and best practices, and empower you to streamline your production schedules for optimal efficiency and customer satisfaction.
Here's what we shall cover in this post:
- Understanding Capacity and Demand in Production Scheduling
- Assessing and Forecasting Demand Accurately
- Optimizing Resource Utilization for Capacity Balancing
- Strategies for Adjusting Production Capacity Based on Demand Fluctuations
- Leveraging Historical Data for Capacity Planning
- Managing Bottlenecks and Constraints in Capacity Planning
- Incorporating Lead Times in Capacity and Demand Balancing
- How Can Deskera Help You?
- Conclusion
- Key Takeaways
Understanding Capacity and Demand in Production Scheduling
Production scheduling plays a crucial role in ensuring efficient and effective operations in manufacturing environments. To optimize production schedules, it is essential to understand the concepts of capacity and demand.
What is Capacity?
- Capacity refers to the maximum amount of work that a manufacturing system or resource can handle within a given timeframe.
- It represents the production capability and resources available, such as machinery, labor, and facilities.
- Capacity is usually measured in units of time, such as hours, days, or weeks, and can vary based on the type of resource or process.
Types of Capacity
- Design Capacity: This is the maximum output a manufacturing system can achieve under ideal conditions and the perfect utilization of resources.
- Effective Capacity: It takes into account factors such as downtime, maintenance, and other disruptions that can impact the actual output of the system.
- Utilization: It represents the ratio of actual output to the maximum capacity, indicating how effectively the resources are utilized.
Importance of Capacity: Capacity is a critical factor in manufacturing as it directly impacts a company's ability to meet customer demand and achieve profitability. Insufficient capacity can lead to production bottlenecks, missed delivery deadlines, and dissatisfied customers.
On the other hand, excess capacity can result in underutilization of resources and increased costs. By effectively understanding and managing capacity, manufacturers can balance supply and demand, optimize resource utilization, and enhance overall operational performance.
Measuring Capacity: Capacity in manufacturing is typically measured using two approaches: theoretical capacity and effective capacity. Theoretical capacity represents the maximum output achievable under ideal conditions without any disruptions or downtime.
Effective capacity, on the other hand, takes into account factors such as planned downtime, scheduled maintenance, and efficiency losses due to factors like equipment breakdowns or changeovers. Effective capacity provides a more realistic measure of the actual output that can be achieved.
Factors Affecting Capacity: Several factors influence the capacity of a manufacturing system or process. These include the design and layout of the production facility, the capability and efficiency of equipment, the skills and productivity of the workforce, the availability and flow of raw materials, and the overall efficiency of the production process.
By identifying and understanding these factors, manufacturers can make informed decisions to optimize their capacity and address any constraints or limitations.
What is Demand?
- Demand refers to the quantity of products or services required by customers within a specific timeframe.
- It represents the market need or customer orders that drive production.
- Demand can vary based on factors such as market trends, customer preferences, and seasonal fluctuations.
Importance of Understanding Demand: Understanding demand is crucial for manufacturers as it influences production planning, inventory management, and revenue generation. Accurately assessing and forecasting demand helps manufacturers determine the appropriate level of production, optimize resource allocation, avoid excess inventory or stockouts, and meet customer requirements.
By aligning production with demand, manufacturers can enhance customer satisfaction, reduce costs, and improve overall business performance.
Analyzing Demand: Manufacturers employ various methods to analyze and assess demand patterns. These include market research, customer surveys, historical sales data, and statistical forecasting techniques. Market research provides insights into customer preferences, trends, and market dynamics.
Surveys help gather specific customer preferences and feedback. Historical sales data analysis allows manufacturers to identify demand patterns and seasonality. Statistical forecasting techniques, such as time series analysis and regression models, use historical data to project future demand.
Factors Affecting Demand: Several factors influence demand in the manufacturing industry. These include market trends, consumer behavior, changes in customer preferences, economic conditions, competition, marketing efforts, pricing strategies, and product quality.
Manufacturers need to consider these factors while analyzing and forecasting demand to make effective production and business decisions.
Managing Demand: Managing demand involves aligning production capabilities with customer requirements to ensure the timely availability of products.
Manufacturers employ various strategies to manage demand effectively, such as developing flexible production systems, implementing just-in-time (JIT) manufacturing, establishing strategic partnerships with suppliers, offering product customization options, and conducting regular market research to understand evolving customer needs.
Assessing and Forecasting Demand Accurately
Accurately assessing and forecasting demand is crucial to business planning and strategy. It allows companies to make informed production, inventory management, and resource allocation decisions.
Historical Data Analysis
- Analyzing historical sales data is essential for assessing demand accurately.
- Companies can identify demand patterns and make informed forecasts by examining past sales trends, seasonal patterns, and market fluctuations.
- Historical data analysis provides valuable insights into customer behavior, preferences, and buying patterns, helping companies accurately anticipate future demand.
- When analyzing historical data, it is important to consider factors such as sales volume, customer segments, geographical locations, and product categories.
Market Research
- Conducting market research allows companies to gather valuable data about their target market, customer preferences, and industry trends.
- Techniques such as surveys, focus groups, and interviews help gather insights into customer needs, purchasing habits, and potential demand drivers.
- Market research provides a deeper understanding of market dynamics, competitive landscape, and emerging trends, aiding in accurate demand assessment and forecasting.
- It is crucial to regularly update market research data to capture evolving customer preferences and changing market conditions.
Customer Feedback and Engagement
- Actively seeking and listening to customer feedback is key to accurately assessing demand.
- Engaging with customers through surveys, feedback forms, and social media channels helps gather insights into their preferences, expectations, and evolving needs.
- Incorporating customer feedback into demand forecasting processes ensures that forecasts align with actual customer demand, enhancing accuracy.
- Companies can establish feedback mechanisms such as customer satisfaction surveys, online reviews, or focus groups to consistently capture customer insights.
Collaboration with Supply Chain Partners
- Collaborating with supply chain partners, such as suppliers, distributors, and retailers, is crucial for accurate demand assessment and forecasting.
- Sharing data and insights with supply chain partners allows for a holistic view of the market and demand trends.
- Collaborative forecasting and demand planning processes help accurately align production capacities, inventory levels, and distribution strategies to meet anticipated demand.
- Regular communication and information sharing with supply chain partners help identify potential demand fluctuations and respond effectively.
Technology and Data Analytics
- Leveraging technology and data analytics tools can significantly enhance demand assessment and forecasting accuracy.
- Advanced analytics techniques, such as predictive modeling and machine learning algorithms, can analyze large datasets and identify demand patterns, leading to more precise forecasts.
- Demand forecasting software and customer relationship management systems streamline processes and automate data analysis, improving accuracy and efficiency.
- Companies should invest in technologies that capture and analyze real-time data from multiple sources to generate accurate demand forecasts.
External Factors and Market Intelligence
- Assessing and forecasting demand accurately requires considering external factors and market intelligence.
- Economic conditions, industry trends, regulatory changes, and geopolitical events can significantly impact customer demand.
- Regular monitoring of market intelligence sources, industry reports, and economic indicators helps businesses stay informed and adjust demand forecasts accordingly.
- Companies should establish a system for tracking and analyzing external factors to ensure demand forecasts reflect market realities.
Sensitivity Analysis and Scenario Planning
- Conducting sensitivity analysis and scenario planning enables companies to assess the impact of various factors on demand forecasts.
- By simulating different scenarios, such as changes in pricing, competition, or market conditions, companies can evaluate the sensitivity of their demand forecasts and develop contingency plans.
- Sensitivity analysis helps identify potential risks and uncertainties in demand forecasts, allowing companies to make more informed decisions.
Optimizing Resource Utilization for Capacity Balancing
Efficient resource utilization is a critical aspect of capacity balancing in any organization. It involves aligning the available resources with the demand to ensure smooth operations, cost-effectiveness, and customer satisfaction.
Capacity Assessment and Planning: Assessing the capacity of resources, such as manpower, machinery, and facilities, is the first step in optimizing resource utilization. Understand each resource's capabilities, limitations, and constraints to make informed decisions.
Conduct regular capacity planning exercises to determine the optimal allocation of resources based on projected demand and future growth plans. Analyze historical data, market trends, and customer requirements to estimate resource requirements accurately.
Demand Forecasting: Accurate demand forecasting is crucial for optimizing resource utilization. Use historical data, market research, and predictive modeling techniques to forecast future demand.
Incorporate factors such as seasonality, market trends, and customer preferences in demand forecasts. By clearly understanding the anticipated demand, you can allocate resources efficiently to meet customer requirements.
Resource Allocation: Optimize resource allocation by matching the available resources with the demand. Analyze resource availability, capabilities, and costs to make informed decisions.
Consider factors such as skill sets, equipment capabilities, and availability when assigning resources to specific tasks or projects. Use resource allocation software or tools to streamline the process and ensure optimal utilization of resources.
Cross-Training and Skill Development: Cross-training employees and developing their skills can enhance resource utilization. Identify opportunities to upskill employees and provide them with training in multiple areas.
By having a versatile workforce, you can easily allocate resources based on demand fluctuations and skill requirements. Cross-training also improves employee engagement and job satisfaction and reduces dependency on specific individuals.
Real-Time Monitoring and Adjustments: Continuously monitor resource utilization in real-time to identify bottlenecks or underutilized resources. Data analytics and monitoring tools are used to track resource performance, productivity, and efficiency.
Make timely adjustments to resource allocation based on changing demand patterns or operational requirements. Regularly review resource utilization reports and identify areas for improvement.
Outsourcing and Collaboration: Consider outsourcing certain tasks or collaborating with external partners to optimize resource utilization. Identify non-core or specialized activities that external vendors can efficiently handle.
Collaborate with trusted partners to share resources or expertise, reducing the need for additional investments. Outsourcing or collaborating strategically can help balance capacity and optimize resource allocation.
Strategies for Adjusting Production Capacity Based on Demand Fluctuations
Scalable Production Infrastructure
- Invest in a production infrastructure that can scale up or down based on demand fluctuations.
- Modular and flexible manufacturing systems allow for easy reconfiguration of production lines.
- Leverage advanced technologies like robotics and automation to enhance production flexibility and responsiveness.
- Adopt cloud-based manufacturing solutions that enable rapid adjustments to production capacity.
Agile Workforce Management
- Maintain an agile workforce that can adapt to changing production requirements.
- Cross-train employees to have multi-functional skills and flexibility in their roles.
- Implement flexible work arrangements, such as part-time or contract workers, to handle demand spikes.
- Foster a culture of collaboration and continuous learning to empower employees to adapt quickly to changing production needs.
Strategic Partnerships and Outsourcing
- Collaborate with strategic partners or outsource certain production processes to adjust capacity effectively.
- Establish partnerships with contract manufacturers who can provide additional production capacity as needed.
- Outsource non-core activities to specialized service providers to free up internal resources for core operations.
- Maintain strong relationships with suppliers to ensure the timely availability of raw materials during capacity adjustments.
Just-in-Time (JIT) Inventory Management
- Implement JIT inventory management techniques to optimize production capacity.
- Maintain lean inventory levels by aligning procurement and production with actual demand.
- Continuously monitor inventory levels and adjust procurement schedules accordingly.
- Leverage technology solutions, such as inventory tracking systems and demand-driven replenishment, to support JIT practices.
Data-driven Decision Making
- Utilize data analytics and business intelligence tools to make informed decisions about adjusting production capacity.
- Analyze demand data, production metrics, and supply chain information to identify capacity gaps or surpluses.
- Leverage predictive modeling and scenario analysis to simulate different demand scenarios and optimize capacity adjustments.
- Monitor key performance indicators (KPIs) related to production efficiency and customer satisfaction to evaluate the impact of capacity adjustments.
Leveraging Historical Data for Capacity Planning
Identifying Capacity Constraints: Analyzing historical data allows organizations to identify capacity constraints and potential bottlenecks in their operations. By examining past periods of high demand or capacity shortages, businesses can pinpoint areas where additional resources or process improvements are needed.
This insight enables proactive capacity planning, ensuring that potential constraints are addressed before they impact operations.
Improving Production Efficiency: Historical data provides insights into production efficiency by analyzing past performance metrics. By examining factors such as production cycle times, machine utilization rates, and downtime incidents, businesses can identify areas for improvement and implement measures to enhance operational efficiency.
This information is invaluable for optimizing capacity planning and resource allocation.
Enhancing Financial Planning: Leveraging historical data for capacity planning also has financial implications. Organizations can make informed decisions regarding investment in additional capacity or outsourcing arrangements by analyzing past demand patterns and production costs.
This allows for more accurate financial planning and budgeting, ensuring that resources are allocated in a cost-effective manner.
Mitigating Risks: Historical data can help organizations identify and mitigate risks associated with capacity planning. By analyzing past periods of demand volatility or unexpected disruptions, businesses can develop contingency plans and build resilience into their capacity planning strategies.
This proactive approach helps minimize the impact of unforeseen events and ensures continuity of operations.
Aligning Production Schedules With Customer Demand
In today's competitive business landscape, it is crucial for companies to align their production schedules with customer demand. By synchronizing production activities with customers' fluctuating needs and preferences, businesses can optimize operational efficiency, reduce costs, and enhance customer satisfaction.
Meeting Customer Expectations: Aligning production schedules with customer demand ensures that businesses can meet customer expectations effectively.
By understanding customer needs and preferences, organizations can adjust their production schedules to ensure the availability of products or services when and where customers need them. This proactive approach enhances customer satisfaction and builds long-term loyalty.
Minimizing Inventory Costs: When production schedules are aligned with customer demand, companies can minimize inventory costs. Businesses can avoid overstocking or stockouts by producing goods based on actual demand rather than speculative forecasts.
This reduces holding costs associated with excess inventory and eliminates potential revenue loss from missed sales opportunities.
Optimizing Resource Utilization: Aligning production schedules with customer demand allows businesses to optimize the utilization of their resources. Organizations can allocate their workforce, equipment, and raw materials efficiently by producing goods or delivering services based on customer orders. This leads to improved productivity, reduced idle time, and better cost management.
Enhancing Operational Efficiency: Operational efficiency improves when production schedules align with customer demand. Organizations can streamline workflows, minimize production bottlenecks, and reduce lead times by synchronizing production activities with customer orders.
This enables businesses to deliver products or services promptly, meeting customer expectations while maximizing operational efficiency.
Responding to Market Changes: Aligning production schedules with customer demand enables companies to respond quickly to market changes. Organizations can adjust their production schedules by monitoring customer preferences, market trends, and competitive dynamics.
This agility allows businesses to capitalize on emerging opportunities, adapt to shifting customer demands, and stay ahead of the competition.
Implementing Demand-Driven Planning: Demand-driven planning is a strategy that aligns production schedules with customer demand in real time. By leveraging demand sensing technologies, businesses can capture and analyze customer demand signals, such as point-of-sale data or online analytics, to drive production decisions.
This approach ensures that production schedules are continuously adjusted to match actual customer demand, improving responsiveness and reducing forecasting errors.
Managing Bottlenecks and Constraints in Capacity Planning
Capacity planning is critical to managing operations and ensuring that resources are allocated efficiently. However, bottlenecks and constraints can hinder the smooth flow of operations and impact productivity.
Understanding Bottlenecks and Constraints: Bottlenecks and constraints are points in the production process where the flow of work is limited or restricted, leading to reduced throughput and longer cycle times.
These bottlenecks can occur due to various factors, such as the limited capacity of a machine, labor shortages, or inefficient processes. Identifying and understanding these bottlenecks and constraints is the first step in managing them effectively.
Conducting Capacity Analysis: To manage bottlenecks and constraints, it is essential to conduct a thorough capacity analysis. This involves assessing the capacity of each resource, such as machines, equipment, and labor, and determining their maximum output.
By understanding the capacity limitations of each resource, businesses can identify potential bottlenecks and constraints and develop strategies to alleviate them.
Implementing Load Balancing: Load balancing is a strategy that involves redistributing workload across resources to optimize capacity utilization and alleviate bottlenecks.
By identifying bottlenecks and redistributing tasks or resources, businesses can ensure a more balanced workload across the production process. This can be achieved by adjusting schedules, reallocating resources, or implementing cross-training programs to enhance flexibility.
Investing in Technology and Automation: Technology and automation play a crucial role in managing bottlenecks and constraints. By implementing advanced technologies such as robotics, process automation, and predictive analytics, businesses can streamline operations, increase efficiency, and reduce the likelihood of bottlenecks.
Automation can help optimize resource utilization, minimize human errors, and improve overall productivity.
Process Improvement and Optimization: Process improvement is a continuous effort to identify and eliminate inefficiencies in the production process. By analyzing workflows, identifying non-value-added activities, and implementing lean principles, businesses can optimize processes and reduce bottlenecks.
This may involve reorganizing workstations, redesigning layouts, or implementing standardized work procedures to improve the flow of operations.
Capacity Expansion: In some cases, managing bottlenecks and constraints may require capacity expansion. This can involve investing in additional resources, such as machinery, equipment, or human capital, to increase overall capacity.
However, capacity expansion should be carefully evaluated to ensure it aligns with demand projections and provides a viable solution for long-term capacity needs.
Incorporating Lead Times in Capacity and Demand Balancing
When it comes to capacity and demand balancing in manufacturing, incorporating lead times is essential for ensuring efficient production planning and meeting customer expectations. Lead times represent the duration required to fulfill an order from the time it is placed until it is delivered.
By considering lead times, businesses can effectively align their capacity with demand and optimize their production processes.
Understanding Lead Times: Lead times are a critical component of the production process. They encompass the time required for various activities, such as order processing, raw material procurement, production, and shipping.
By understanding and tracking lead times, businesses can gain insights into the time it takes to fulfill customer orders and plan their production schedules accordingly.
Aligning Capacity with Lead Times: Incorporating lead times in capacity planning involves aligning the production capacity with the time required to fulfill orders.
By considering lead times, businesses can avoid overloading their resources or falling short of meeting customer demand. This alignment allows for a more realistic and efficient production schedule.
Factoring in Variability: Lead times can be subject to variability due to factors such as supplier delays, equipment breakdowns, or unforeseen circumstances. It is crucial to account for this variability when incorporating lead times in capacity and demand balancing. Businesses can establish buffer times or safety margins to accommodate unexpected delays and ensure that they can meet customer expectations.
Demand Forecasting with Lead Times: Incorporating lead times in demand forecasting helps businesses estimate the time required to fulfill future orders accurately. By considering lead times in demand forecasting models, businesses can project future demand more effectively and adjust their production capacity accordingly.
This integration enhances the accuracy of demand forecasts and supports better decision-making.
Effective Communication and Coordination to Balance Capacity and Demand
Achieving a balance between production capacity and customer demand is essential for the success of any business. To accomplish this delicate balance, effective communication, and coordination play a vital role.
By establishing clear lines of communication and fostering collaboration among different teams and stakeholders, businesses can optimize their capacity utilization while meeting customer demand efficiently.
Establishing Open Communication Channels: Open communication channels are the foundation for effective capacity and demand balancing. By fostering an environment where all teams and stakeholders can freely share information, businesses can gain valuable insights into customer demand, production capacity, and any challenges or constraints.
This open communication allows for a holistic understanding of the overall picture and promotes informed decision-making.
Sharing Demand Forecasts: Sharing demand forecasts across departments is crucial for aligning capacity with expected customer demand. By providing accurate and up-to-date demand forecasts, sales and marketing teams can help production teams plan their capacity requirements.
This collaboration ensures that the production capacity is optimally allocated to meet anticipated customer needs.
Implementing Cross-Functional Teams: Cross-functional teams bring together individuals from different departments or functions to work on specific projects or initiatives.
By forming cross-functional teams focused on capacity and demand balancing, businesses can break down silos and foster collaboration. These teams can collectively analyze data, share insights, and develop strategies to optimize capacity utilization while meeting customer demand.
Regular Meetings and Reviews: Regular meetings and reviews provide a platform for teams to discuss capacity and demand balancing, share progress updates, and address any challenges or bottlenecks.
By scheduling periodic meetings, businesses can ensure that all stakeholders are aligned and informed about the current status and future plans. These meetings facilitate proactive decision-making and timely adjustments to optimize capacity and meet demand effectively.
Implementing a Centralized Planning System: A centralized planning system serves as a hub for capacity and demand information. By implementing a robust planning system, businesses can consolidate data from various sources, analyze capacity constraints, and make informed decisions.
This centralized approach ensures that all teams have access to real-time data, facilitating effective communication and coordination.
How Can Deskera Help You?
Deskera MRP allows you to closely monitor the manufacturing process. From the bill of materials to the production planning features, the solution helps you stay on top of your game and keep your company's competitive edge.
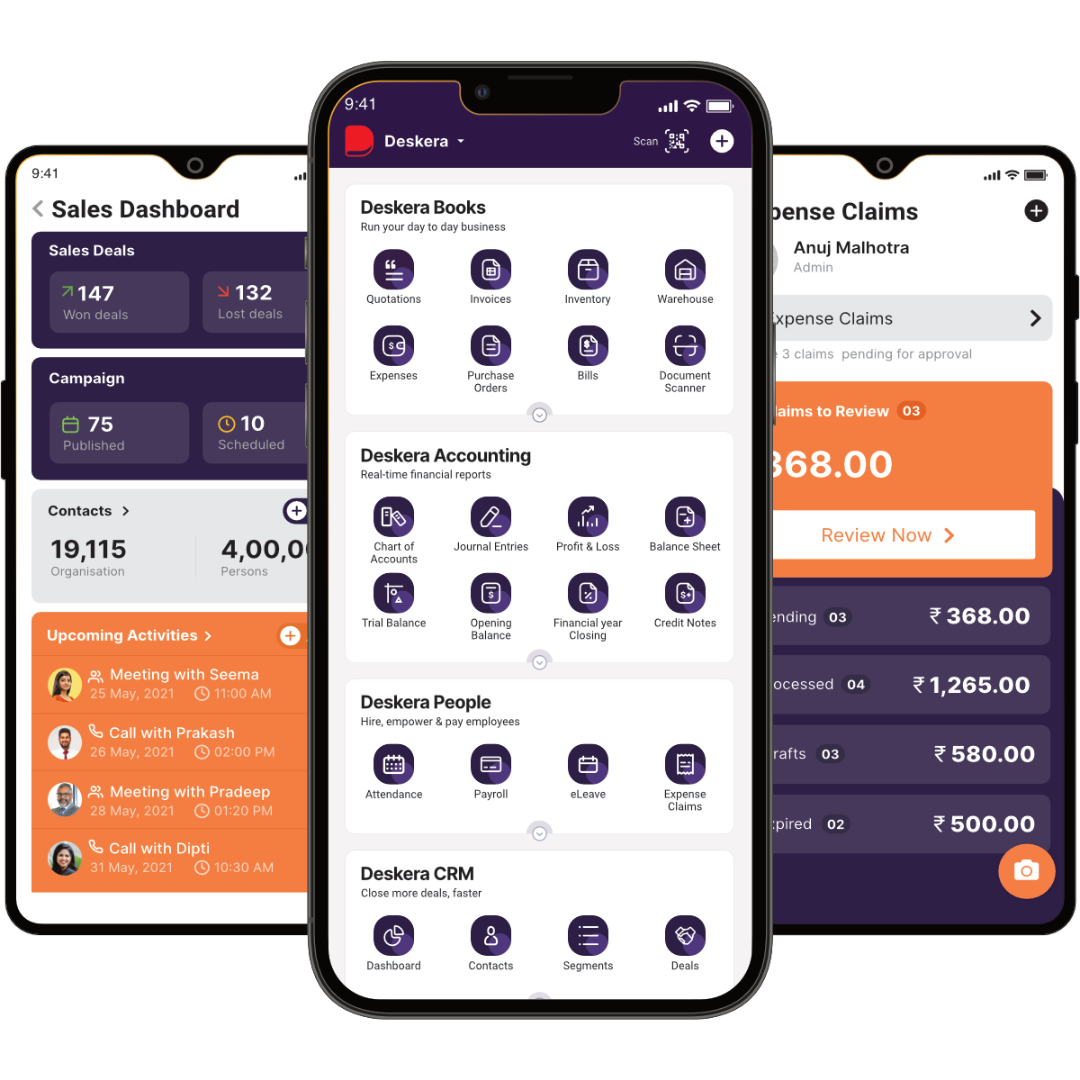
Deskera ERP and MRP system can help you:
- Manage production plans
- Maintain Bill of Materials
- Generate detailed reports
- Create a custom dashboard
Deskera ERP is a comprehensive system that allows you to maintain inventory, manage suppliers, and track supply chain activity in real-time, as well as streamline a variety of other corporate operations.
Deskera Books enables you to manage your accounts and finances more effectively. Maintain sound accounting practices by automating accounting operations such as billing, invoicing, and payment processing.
Deskera CRM is a strong solution that manages your sales and assists you in closing agreements quickly. It not only allows you to do critical duties such as lead generation via email, but it also provides you with a comprehensive view of your sales funnel.
Deskera People is a simple tool for taking control of your human resource management functions. The technology not only speeds up payroll processing but also allows you to manage all other activities such as overtime, benefits, bonuses, training programs, and much more. This is your chance to grow your business, increase earnings, and improve the efficiency of the entire production process.
Conclusion
Balancing capacity and demand is a critical aspect of manufacturing production scheduling, and implementing effective strategies can greatly enhance operational efficiency and customer satisfaction.
The key to achieving this balance lies in adopting a proactive approach, leveraging technology, and optimizing various factors that influence production scheduling.
Effective communication and collaboration across different departments are vital for successful production scheduling. By fostering strong interdepartmental communication, manufacturers can align their production plans with sales, marketing, and procurement functions.
Regular performance monitoring and analysis are essential for continuous improvement in production scheduling. Key performance indicators (KPIs) such as on-time delivery, production cycle time, and resource utilization should be tracked and analyzed regularly.
Finally, it is crucial to involve employees in the production scheduling process. Operators and supervisors who are closest to the production floor often have valuable insights and suggestions for improving scheduling efficiency. By fostering a culture of employee involvement and empowerment, manufacturers can tap into the collective knowledge of their workforce and drive innovation in production scheduling.
Key Takeaways
- Streamlining processes and eliminating bottlenecks improves efficiency.
- Communication and collaboration among departments ensure alignment with market demand.
- Technology solutions like MES and ERP provide real-time visibility into production.
- Flexibility is crucial to accommodate changes in demand or unforeseen events.
- Regular performance monitoring helps identify areas for improvement.
- Effective inventory management prevents stockouts or excess inventory.
- Prioritizing high-demand products helps optimize production schedules.
- Aligning production schedules with supplier capabilities ensures smooth operations.
- Continuous improvement through data analysis and optimization enhance efficiency.
- Balancing capacity and demand minimizes costs associated with idle resources.
Related Articles
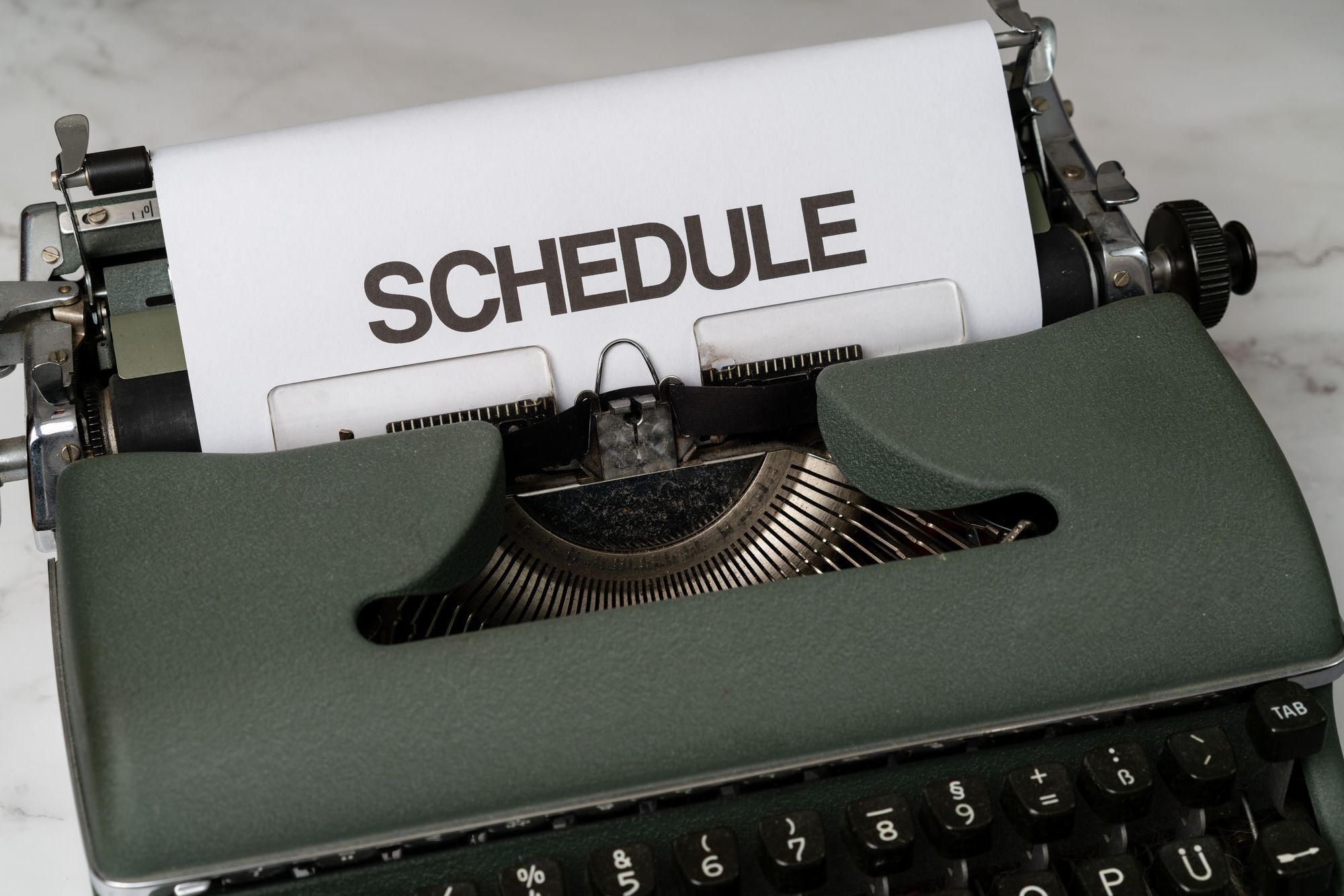
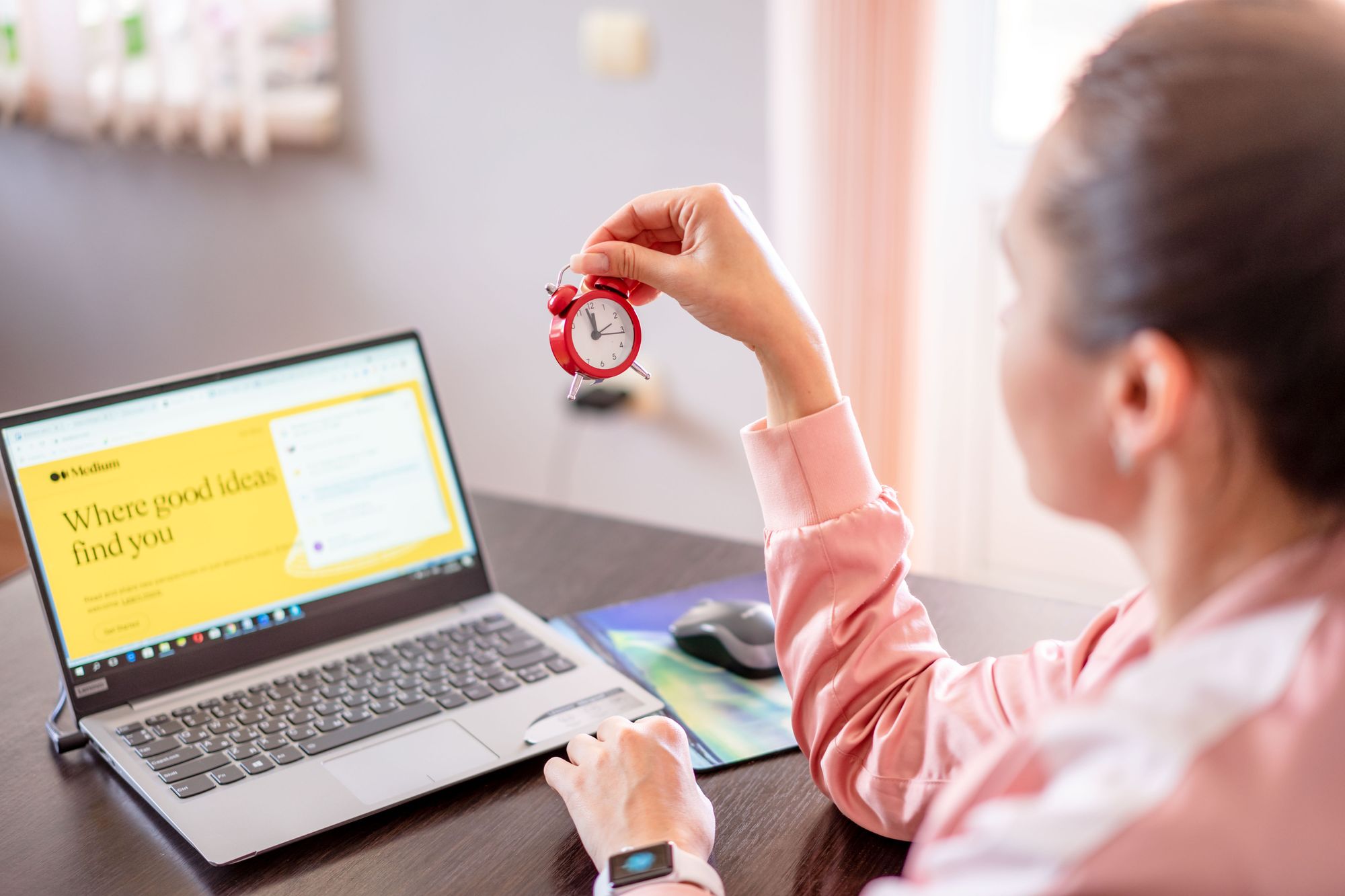
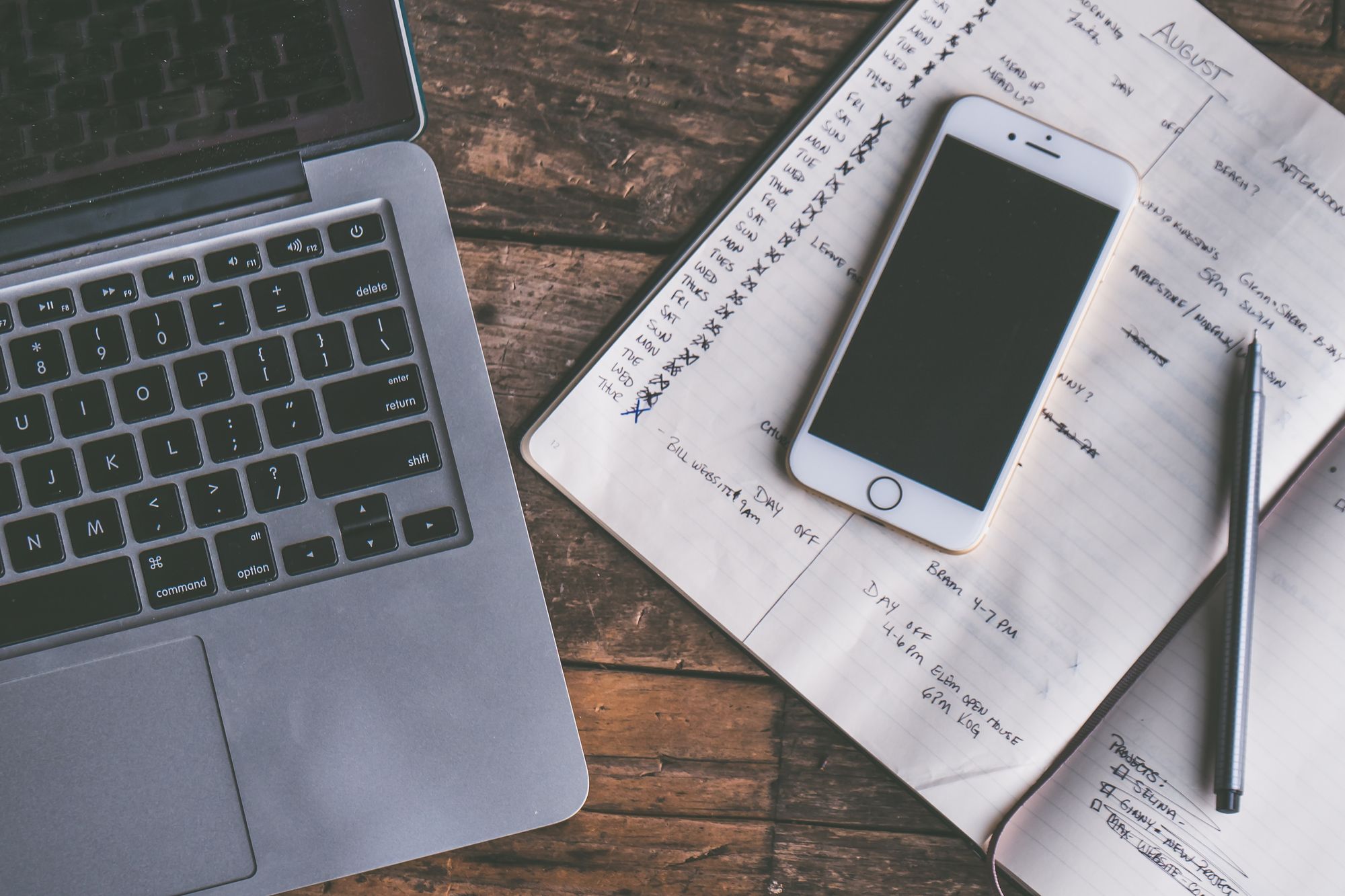
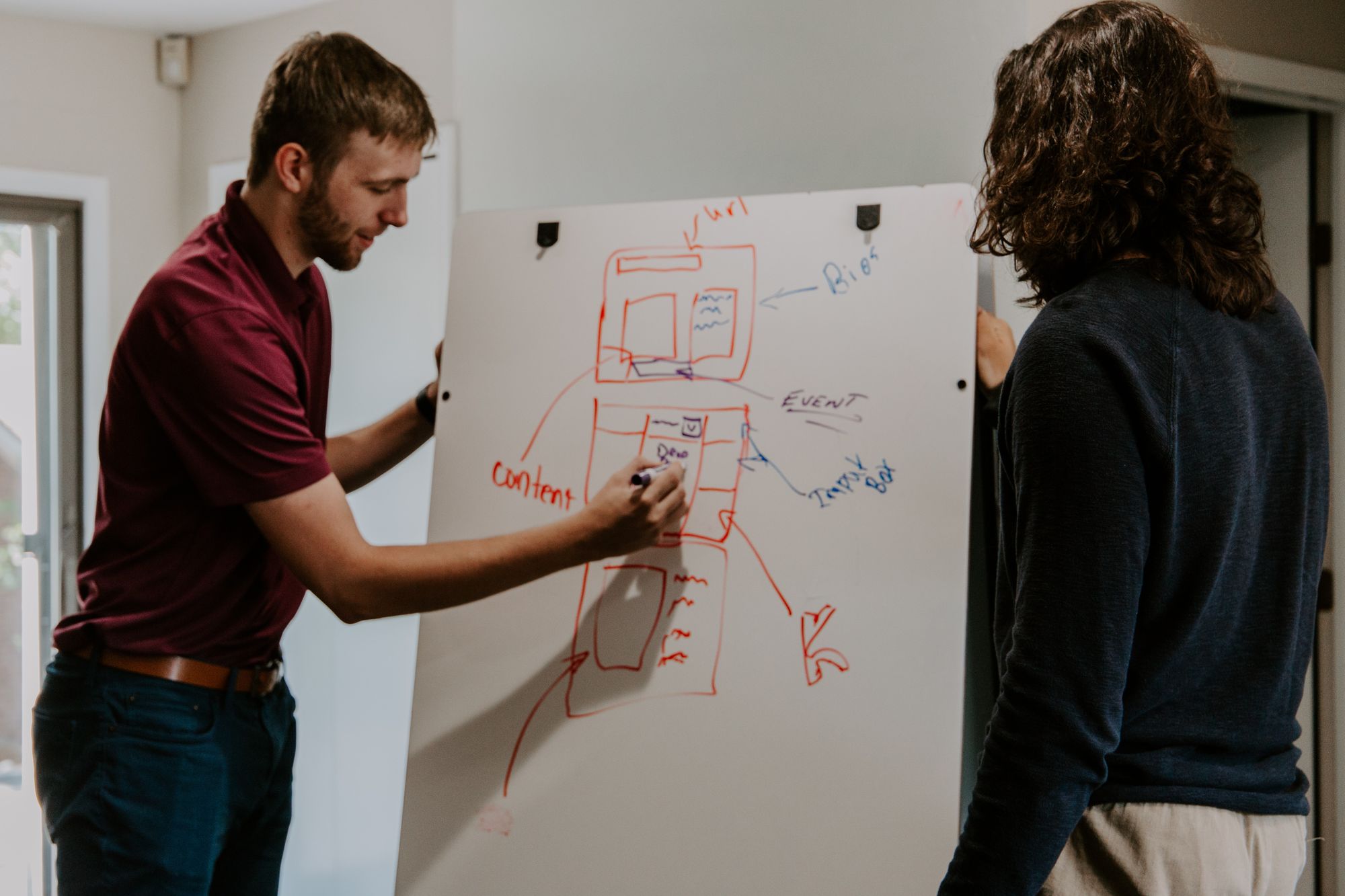