With a customer-centric business environment, achieving the delicate balance between safety stock and customer satisfaction has become a crucial aspect of effective inventory management. Maintaining adequate safety stock ensures uninterrupted supply and mitigates the risks of stockouts, while customer satisfaction plays a pivotal role in driving loyalty, repeat purchases, and positive brand reputation.
The emergence of Enterprise Resource Planning (ERP) systems has revolutionized inventory management, offering comprehensive solutions to optimize both safety stock levels and customer satisfaction simultaneously.
This article explores the significant role of ERP in achieving this delicate equilibrium. We will delve into the understanding of safety stock and its impact on customer satisfaction, examine the functionalities of ERP systems in inventory management, and present strategies and best practices for leveraging ERP to strike the right balance.
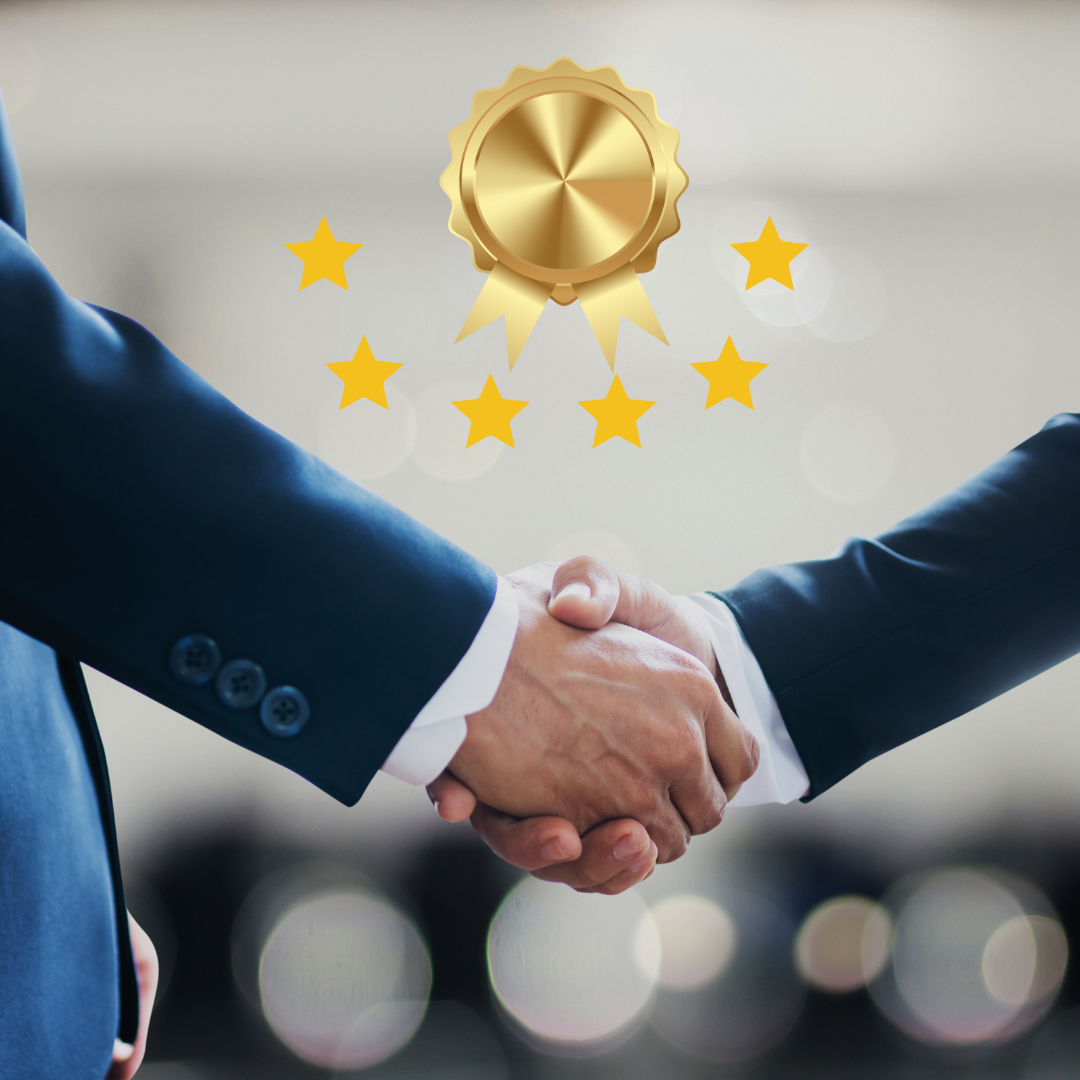
Furthermore, real-world case studies and insights into potential challenges and limitations will be discussed, providing a comprehensive perspective on how ERP can revolutionize inventory management for improved operational efficiency and customer-centric outcomes.
- ERP (Enterprise Resource Planning) in Inventory Management
- Importance of Balancing Safety Stock and Customer Satisfaction in Inventory Management
- Understanding Safety Stock
- Customer Satisfaction in Inventory Management
- Role of ERP in Balancing Safety Stock and Customer Satisfaction
- Strategies for Balancing Safety Stock and Customer Satisfaction with ERP
- Case Studies and Examples of Successful Implementation of ERP for Balancing Safety Stock and Customer Satisfaction
- Best Practices for Effective ERP Implementation
- Challenges and Limitations of ERP in Balancing Safety Stock and Customer Satisfaction
- Conclusion
- How can Deskera Help You?
- Key Takeaways
- Related Articles
ERP (Enterprise Resource Planning) in Inventory Management
Enterprise Resource Planning (ERP) systems have revolutionized various aspects of business operations, and inventory management is no exception. ERP in inventory management refers to the use of integrated software solutions that streamline and optimize the processes involved in managing and controlling inventory within an organization.
At its core, ERP serves as a centralized hub that consolidates data and provides real-time visibility into inventory levels, demand forecasting, order processing, and supply chain activities. It encompasses a range of functionalities, including inventory tracking, procurement management, warehouse management, and demand planning.
The benefits of implementing ERP in inventory management are numerous. Firstly, it enhances accuracy and efficiency by automating routine tasks, minimizing manual errors, and enabling real-time updates. This, in turn, leads to improved inventory control, reduced stockouts, and optimized stock replenishment.
Additionally, ERP systems provide valuable insights through data analytics and reporting, enabling businesses to make informed decisions regarding inventory optimization, demand forecasting, and supplier management. Moreover, ERP facilitates seamless collaboration and communication between different departments, suppliers, and customers, resulting in better coordination and customer service.
ERP in inventory management empowers businesses to achieve cost savings, operational excellence, and increased customer satisfaction by effectively managing their inventory levels, streamlining processes, and maintaining optimal stock levels to meet customer demand.
Importance of Balancing Safety Stock and Customer Satisfaction in Inventory Management
Balancing safety stock and customer satisfaction is of paramount importance in effective inventory management. Safety stock refers to the extra inventory maintained to mitigate the risks of stockouts caused by unexpected fluctuations in demand, supply chain disruptions, or lead time variability. On the other hand, customer satisfaction is a critical factor that directly impacts a company's reputation, customer loyalty, and profitability.
Maintaining an appropriate level of safety stock is crucial to ensure uninterrupted supply and meet customer demands promptly. Excessive safety stock ties up capital and storage space, resulting in increased holding costs. Conversely, insufficient safety stock can lead to frequent stockouts, dissatisfied customers, and potential revenue loss. Striking the right balance between safety stock and customer satisfaction helps companies optimize inventory levels, minimize costs, and maximize customer service levels.
Customer satisfaction plays a pivotal role in today's competitive market. Satisfied customers are more likely to make repeat purchases, provide positive referrals, and contribute to a company's long-term success. By managing inventory effectively, businesses can fulfill orders on time, reduce lead times, and enhance overall customer experience.
A well-balanced approach to inventory management ensures that customers receive their desired products promptly, resulting in increased customer satisfaction, loyalty, and a competitive edge in the market.
Ultimately, achieving the delicate equilibrium between safety stock and customer satisfaction not only optimizes inventory management but also drives business growth, profitability, and customer-centric outcomes. It is a strategic imperative for companies seeking to excel in today's dynamic and customer-focused business landscape.
Understanding Safety Stock
In the realm of inventory management, understanding safety stock is crucial for maintaining a well-functioning supply chain.
Safety stock serves as a buffer, ensuring that businesses are prepared for unexpected demand fluctuations, supply chain disruptions, or other unforeseen events. It is the extra inventory held beyond what is required for regular demand, acting as a safety net against stockouts.
By delving into the concept of safety stock, its purpose, and the factors influencing its determination, businesses can optimize their inventory levels and minimize the risks associated with inadequate stock. In this section, we will explore the fundamental aspects of safety stock, its significance in mitigating supply chain risks, and the implications of having excessive or insufficient safety stock.
A. Definition of safety stock and its purpose
Safety stock, also known as buffer stock, is the additional inventory maintained by businesses beyond the regular stock required to meet customer demand. It acts as a cushion to protect against unexpected fluctuations in demand, supply disruptions, or lead time variability.
The purpose of safety stock is to ensure that businesses can fulfill customer orders even during unforeseen circumstances. It serves as a protective measure to mitigate the risks of stockouts, which can result in dissatisfied customers, lost sales, and damage to the company's reputation. By holding safety stock, businesses can maintain a certain level of flexibility and responsiveness to changes in demand or supply chain disruptions.
Safety stock is typically determined based on factors such as demand variability, supplier reliability, lead times, and desired service levels. It helps address uncertainties in the supply chain by providing a buffer of inventory that can be utilized during unexpected spikes in demand or delays in replenishment.
Overall, the purpose of safety stock is to strike a balance between inventory costs and customer service levels. It ensures that businesses have sufficient stock on hand to meet customer demand while minimizing the risks associated with stockouts, thereby contributing to improved customer satisfaction and maintaining a competitive edge in the market.
B. Factors influencing safety stock levels
Several factors influence the determination of safety stock levels in inventory management. These factors are essential for accurately calculating the optimal amount of buffer inventory required to maintain a balance between customer service levels and inventory costs.
The following are some key factors that influence safety stock levels:
Demand Variability: Fluctuations in customer demand play a significant role in determining safety stock levels. Higher demand variability necessitates larger safety stock quantities to accommodate unexpected spikes in demand and avoid stockouts.
Lead Time Variability: Variability in the time it takes to receive replenishment orders from suppliers can impact safety stock requirements. Longer lead times or increased lead time variability may require higher levels of safety stock to compensate for potential delays.
Supplier Reliability: The reliability and consistency of suppliers in delivering orders on time and in the expected quantity influence safety stock levels. Unreliable suppliers may necessitate higher safety stock to mitigate the risks of supply disruptions.
Service Level Objectives: The desired level of customer service also influences safety stock levels. Companies aiming for higher service levels, such as minimizing stockouts or providing quick order fulfillment, may need to maintain higher levels of safety stock.
Seasonality and Demand Patterns: Seasonal fluctuations and demand patterns impact safety stock requirements. Businesses experiencing predictable seasonal demand variations may adjust their safety stock levels accordingly to ensure sufficient inventory during peak periods.
Forecast Accuracy: The accuracy of demand forecasting plays a crucial role in determining safety stock levels. Poor forecasting accuracy can lead to inadequate safety stock and higher stockouts or excessive safety stock, resulting in increased holding costs.
Cost Considerations: Balancing safety stock levels with inventory costs is essential. Holding excessive safety stock can tie up working capital and increase storage costs, while holding insufficient safety stock can result in lost sales and dissatisfied customers.
By carefully considering these factors, businesses can accurately calculate and adjust their safety stock levels, striking an optimal balance between inventory costs and customer service levels. This enables them to effectively manage inventory and maintain a high level of customer satisfaction.
C. Implications of excessive or insufficient safety stock
Maintaining the right balance of safety stock is crucial in inventory management. Both excessive and insufficient levels of safety stock can have significant implications for businesses.
Let's explore the implications of each:
Excessive Safety Stock:
a. Increased Holding Costs: Holding excessive safety stock ties up working capital and occupies valuable storage space. This results in higher carrying costs, including storage fees, insurance, depreciation, and opportunity costs.
b. Obsolete Inventory: Excessive safety stock increases the risk of inventory becoming obsolete or outdated, especially for products with limited shelf life or frequent updates. This can lead to financial losses if the excess stock cannot be sold or repurposed.
c. Capital Constraints: When a substantial portion of capital is tied up in excessive safety stock, businesses may face limitations in investing in other growth opportunities, such as expanding product lines, improving infrastructure, or launching marketing campaigns.
d. Increased Waste: If excess inventory cannot be sold or utilized, it may eventually become waste, resulting in environmental concerns and potential disposal costs.
Insufficient Safety Stock:
a. Stockouts and Lost Sales: Insufficient safety stock increases the risk of stockouts, leading to unfulfilled customer orders and lost sales opportunities. This can damage customer satisfaction, erode brand reputation, and result in the loss of loyal customers.
b. Rush Orders and Expediting Costs: In the event of sudden demand spikes or supply disruptions, businesses with insufficient safety stock may need to expedite orders or source inventory at higher costs to meet customer demands promptly. This can increase procurement expenses and impact profit margins.
c. Reduced Customer Satisfaction: Inadequate safety stock levels can result in delayed order fulfillment, backorders, and dissatisfied customers. It can negatively impact customer loyalty, decrease repeat purchases, and harm long-term customer relationships.
d. Missed Growth Opportunities: Insufficient safety stock may limit the ability to take advantage of unexpected sales opportunities or new market demands. Businesses may miss out on potential revenue growth and market share expansion.
Finding the optimal balance of safety stock is crucial to minimize these implications. It requires a careful analysis of demand patterns, lead times, supplier reliability, and cost considerations. Striking the right balance ensures adequate customer service levels while minimizing holding costs and mitigating stockouts, contributing to improved customer satisfaction and overall business performance.
Customer Satisfaction in Inventory Management
Effective inventory management directly impacts customer satisfaction, as it ensures timely order fulfillment, product availability, and overall positive customer experiences. In this section, we will explore the significance of customer satisfaction in the context of inventory management and its impact on business success.
By understanding the relationship between inventory management practices and customer satisfaction, businesses can gain valuable insights into enhancing customer loyalty, driving repeat purchases, and fostering a positive brand image.
A. Importance of customer satisfaction in a competitive market
Customer satisfaction has emerged as a crucial differentiating factor for businesses. It goes beyond simply meeting customer needs; it encompasses creating exceptional experiences that foster loyalty, drive repeat purchases, and generate positive word-of-mouth referrals.
In this context, customer satisfaction holds significant importance in inventory management. Here's why:
Enhanced Customer Loyalty: Satisfied customers are more likely to remain loyal to a brand and continue purchasing its products or services. By consistently meeting or exceeding customer expectations, businesses can build trust and long-term relationships with their customers, reducing the likelihood of them switching to competitors.
Positive Brand Reputation: Customer satisfaction plays a pivotal role in shaping a company's brand reputation. When customers have positive experiences with a brand, they are more likely to share their satisfaction with others, both online and offline. This word-of-mouth marketing can significantly impact a company's image and attract new customers.
Competitive Advantage: In a crowded market, customer satisfaction can provide a competitive edge. Businesses that prioritize customer satisfaction differentiate themselves from competitors by offering superior products, services, and overall experiences. This can lead to higher customer retention rates and an increased market share.
Repeat Business and Revenue Growth: Satisfied customers tend to make repeat purchases, contributing to the company's revenue growth. They become loyal advocates who not only come back for more but also refer others to the brand, further expanding the customer base and driving additional sales.
Customer Lifetime Value: Customer satisfaction influences the lifetime value of a customer, which refers to the total revenue generated by a customer over their entire relationship with a company. Satisfied customers are more likely to make additional purchases, upsell opportunities, and become brand ambassadors, thereby increasing their lifetime value.
Customer Feedback and Improvement: Satisfied customers are more willing to provide feedback and suggestions for improvement. Their insights can be invaluable for enhancing products, services, and overall inventory management practices. Actively listening to customers and incorporating their feedback helps businesses stay competitive and adapt to changing market demands.
B. Impact of inventory management on customer satisfaction
Inventory management directly impacts customer satisfaction in several ways. Here are some key impacts of effective inventory management on customer satisfaction:
Timely Order Fulfillment: Efficient inventory management ensures that products are available when customers place their orders. By maintaining optimal stock levels and accurately tracking inventory, businesses can fulfill customer orders promptly, reducing lead times and avoiding delays. Timely order fulfillment enhances customer satisfaction by meeting their expectations for quick and reliable service.
Minimized Stockouts: Stockouts, or situations where a desired product is not available, can be frustrating for customers and negatively impact their satisfaction. Effective inventory management helps minimize stockouts by accurately forecasting demand, setting appropriate safety stock levels, and implementing proactive replenishment strategies. Minimizing stockouts ensures that customers can reliably purchase the products they need, enhancing their satisfaction and loyalty.
Improved Product Availability: Having adequate inventory levels ensures a consistent supply of products, reducing the chances of customers encountering out-of-stock situations. Customers value having a wide selection of products available to choose from, and inventory management practices that prioritize product availability contribute to a positive customer experience and satisfaction.
Accurate Order Fulfillment: Inventory management systems enable businesses to maintain accurate and up-to-date information about product availability, sizes, variants, and other attributes. This accuracy helps prevent errors in order processing and fulfillment, ensuring that customers receive the correct products they ordered. Accurate order fulfillment improves customer satisfaction by eliminating frustrations associated with receiving incorrect or mismatched items.
Efficient Returns and Exchanges: Effective inventory management also encompasses managing returns and exchanges. When customers need to return or exchange a product, a well-organized inventory system can streamline the process, ensuring that the replacement or refund is handled smoothly. Efficient returns and exchanges contribute to customer satisfaction by demonstrating a commitment to excellent customer service and resolving issues promptly.
Flexibility and Responsiveness: Inventory management practices that promote flexibility and responsiveness to customer demands play a vital role in customer satisfaction. This includes the ability to quickly adjust inventory levels based on changing market trends, customer preferences, and seasonal demands. Being able to offer the right products at the right time enhances customer satisfaction and helps businesses stay competitive.
Role of ERP in Balancing Safety Stock and Customer Satisfaction
The role of Enterprise Resource Planning (ERP) systems in balancing safety stock and customer satisfaction is paramount. ERP systems provide a comprehensive framework that integrates various aspects of inventory management, including demand forecasting, supply chain visibility, order processing, and warehouse management.
By leveraging the capabilities of ERP systems, businesses can optimize their inventory practices to strike the right balance between safety stock levels and customer satisfaction. In this section, we will explore the crucial role of ERP in achieving this balance.
We will delve into the functionalities and benefits of ERP systems in managing safety stock, enhancing customer satisfaction, and driving operational efficiency.
A. Overview of ERP systems and their functionalities
Enterprise Resource Planning (ERP) systems are comprehensive software solutions that integrate various business processes and functions into a unified platform. They provide organizations with a centralized and real-time view of their operations, enabling efficient management of resources, data, and workflows.
In the context of inventory management, ERP systems offer a range of functionalities that contribute to effective inventory control and optimization. Here is an overview of some key functionalities provided by ERP systems:
Demand Forecasting: ERP systems facilitate accurate demand forecasting by analyzing historical data, market trends, and other relevant factors. This helps businesses anticipate customer demand and adjust inventory levels accordingly, ensuring sufficient stock to meet customer needs.
Inventory Tracking and Management: ERP systems enable real-time tracking and management of inventory across multiple locations or warehouses. They provide visibility into stock levels, stock movements, and item availability, allowing businesses to make informed decisions about inventory replenishment, stock transfers, and order fulfillment.
Order Processing and Fulfillment: ERP systems streamline the order processing and fulfillment cycle by automating tasks such as order entry, order confirmation, picking, packing, and shipping. This reduces manual errors, improves order accuracy, and accelerates order fulfillment, leading to faster delivery times and increased customer satisfaction.
Supplier Management: ERP systems facilitate supplier management by maintaining a database of suppliers, tracking supplier performance, and managing procurement processes. They streamline supplier communications, facilitate order placement, and help ensure reliable and timely supply of inventory, reducing the risk of stockouts and customer dissatisfaction.
Demand and Supply Planning: ERP systems support demand and supply planning activities by analyzing demand forecasts, inventory levels, and supply chain constraints. They assist in determining optimal safety stock levels, reorder points, and economic order quantities, aiding businesses in achieving the right balance between inventory availability and cost efficiency.
Reporting and Analytics: ERP systems provide robust reporting and analytics capabilities, allowing businesses to gain insights into inventory performance, stock turnover, demand patterns, and other key metrics. These insights help in identifying trends, making data-driven decisions, and continuously improving inventory management strategies.
Integration with Other Systems: ERP systems integrate with other business systems such as customer relationship management (CRM), financial management, and supply chain management. This integration enables seamless data flow and process synchronization across different functional areas, ensuring a holistic view of the business and facilitating effective inventory management.
B. ERP modules and features relevant to inventory management
ERP systems offer specific modules and features that are highly relevant to inventory management. These modules provide comprehensive tools and functionalities to optimize inventory control, streamline operations, and enhance customer satisfaction.
Here are some key ERP modules and features that are particularly relevant to inventory management:
Inventory Management Module: This module is specifically designed to handle inventory-related activities. It enables businesses to track and manage inventory levels, monitor stock movements, and optimize stock replenishment. It provides functionalities such as stock tracking, stock valuation, serial/lot number tracking, barcode scanning, and inventory categorization.
Demand Forecasting Module: This module aids in predicting customer demand accurately. It utilizes historical data, market trends, and statistical models to generate demand forecasts. By leveraging advanced forecasting algorithms, businesses can anticipate customer demand patterns and adjust inventory levels accordingly, minimizing stockouts and maximizing customer satisfaction.
Order Management Module: The order management module encompasses functionalities related to order processing, order tracking, and order fulfillment. It allows businesses to manage customer orders, handle order entry and confirmation, allocate inventory to orders, and track the status of orders in real-time. This module integrates with inventory management to ensure efficient order fulfillment and timely delivery.
Warehouse Management System (WMS) Module: The WMS module focuses on optimizing warehouse operations and inventory movement. It provides functionalities such as bin/location management, picking and packing optimization, inventory transfers, and warehouse task management. This module enables businesses to streamline warehouse processes, improve inventory accuracy, and enhance overall operational efficiency.
Supplier Management Module: This module is dedicated to managing relationships with suppliers and optimizing procurement processes. It enables businesses to maintain supplier databases, track supplier performance and compliance, manage purchase orders, and monitor supplier contracts and agreements. Effective supplier management ensures a reliable supply of inventory, minimizing the risk of stockouts and maintaining customer satisfaction.
Reporting and Analytics: ERP systems offer robust reporting and analytics capabilities that allow businesses to gain insights into inventory performance, demand trends, stock turnover, and other key metrics. Customizable dashboards, reports, and analytics tools enable data-driven decision-making, identification of inventory optimization opportunities, and continuous improvement of inventory management strategies.
Integration Capabilities: ERP systems provide integration capabilities with other business systems and applications such as CRM, e-commerce platforms, and financial management systems. Integration enables seamless data exchange and synchronization, facilitating a holistic view of inventory-related activities and supporting end-to-end inventory management processes.
C. How ERP systems help optimize safety stock levels
ERP systems play a crucial role in optimizing safety stock levels, ensuring that businesses strike the right balance between inventory availability and cost efficiency.
Here's how ERP systems help in optimizing safety stock levels:
Accurate Demand Forecasting: ERP systems incorporate demand forecasting modules that analyze historical data, market trends, and other relevant factors to generate accurate demand forecasts. By having a clear understanding of future demand, businesses can determine the appropriate safety stock levels needed to meet customer requirements and minimize stockouts.
Real-time Inventory Tracking: ERP systems provide real-time visibility into inventory levels and stock movements. With accurate and up-to-date information about inventory status, businesses can monitor stock levels against demand patterns, track inventory usage, and identify potential stockouts or overstock situations. This visibility allows for proactive decision-making in adjusting safety stock levels to meet changing demand dynamics.
Historical Data Analysis: ERP systems capture and store historical data related to inventory levels, demand patterns, and lead times. By analyzing this data, businesses can identify seasonality, trends, and demand fluctuations, enabling them to make informed decisions about safety stock levels. Historical data analysis helps identify patterns that influence safety stock requirements, ensuring that inventory is available when needed while minimizing excess inventory costs.
Reorder Point Optimization: ERP systems assist in optimizing the reorder point, which triggers the replenishment of inventory. By considering factors such as lead time, demand variability, and desired service levels, ERP systems calculate the ideal reorder point for each inventory item. This optimization helps ensure that safety stock is set at appropriate levels to account for variations in demand and lead time, reducing the risk of stockouts and customer dissatisfaction.
Demand Planning and Collaboration: ERP systems facilitate demand planning and collaboration across departments and with external stakeholders. By integrating sales forecasts, marketing plans, and customer insights, businesses can align inventory management strategies with expected demand. Collaboration within the ERP system allows for better coordination between sales, operations, and procurement teams, enabling more accurate safety stock calculations based on collective insights.
Analytics and Reporting: ERP systems provide robust analytics and reporting capabilities to analyze inventory performance, stockouts, and order fulfillment metrics. By monitoring key performance indicators (KPIs) such as fill rates, service levels, and stockout rates, businesses can assess the effectiveness of their safety stock levels. Actionable insights from these analytics enable continuous improvement and adjustment of safety stock levels to maintain customer satisfaction while optimizing inventory costs.
Integrated Supply Chain Management: ERP systems integrate various supply chain processes, including procurement, production, and distribution. This integration enables better coordination between suppliers, manufacturers, and distributors, resulting in improved visibility and efficiency throughout the supply chain. By having a holistic view of the supply chain, businesses can optimize safety stock levels based on reliable lead times, supplier performance, and production capacity.
D. Improving customer satisfaction through ERP-driven inventory management
Effective inventory management, driven by ERP systems, plays a significant role in improving customer satisfaction. Here are several ways in which ERP-driven inventory management contributes to enhancing customer satisfaction:
Accurate Order Fulfillment: ERP systems enable businesses to accurately track inventory levels and availability in real-time. This ensures that customer orders can be fulfilled promptly and accurately. By minimizing errors, delays, and stockouts, businesses can meet customer expectations for timely and reliable order fulfillment, resulting in higher customer satisfaction.
Enhanced Product Availability: ERP systems provide visibility into inventory levels across multiple locations or warehouses. This visibility helps businesses maintain optimal stock levels and avoid situations of stockouts or low availability. When customers can consistently find the products they desire, it improves their overall satisfaction and strengthens their trust in the business.
Faster Delivery Times: ERP systems streamline order processing and fulfillment processes. By automating tasks such as order entry, picking, packing, and shipping, businesses can expedite order processing and reduce lead times. Faster delivery times contribute to improved customer satisfaction as customers receive their orders quickly and efficiently.
Proactive Inventory Management: ERP systems facilitate proactive inventory management by using demand forecasting, historical data analysis, and real-time inventory tracking. With these tools, businesses can anticipate customer demand, identify trends, and adjust inventory levels accordingly. This proactive approach helps minimize stockouts and ensures that products are available when customers need them, leading to higher satisfaction.
Efficient Returns and Exchanges: ERP systems assist in managing returns and exchanges smoothly. With accurate inventory records and streamlined processes, businesses can efficiently handle returns or exchanges, providing a hassle-free experience for customers. Effective management of returns and exchanges demonstrates a commitment to customer service and contributes to overall customer satisfaction.
Personalized Customer Experiences: ERP systems integrate customer data and purchase history, allowing businesses to personalize the customer experience. By understanding customer preferences and purchase patterns, businesses can offer tailored product recommendations, promotions, and personalized services. This personalization enhances customer satisfaction by providing a unique and individualized shopping experience.
Improved Communication and Transparency: ERP systems facilitate effective communication and transparency across the supply chain. Businesses can share accurate and up-to-date information about product availability, order status, and delivery updates with customers. Clear and transparent communication enhances trust and customer satisfaction, as customers are informed and aware of the progress of their orders.
Continuous Improvement: ERP systems provide analytics and reporting capabilities that allow businesses to analyze inventory performance, customer feedback, and order metrics. By leveraging these insights, businesses can identify areas for improvement, optimize inventory management processes, and enhance the overall customer experience. Continuous improvement ensures that customer satisfaction remains a priority and evolves with changing market demands.
Strategies for Balancing Safety Stock and Customer Satisfaction with ERP
With the advent of Enterprise Resource Planning (ERP) systems, organizations have powerful tools at their disposal to navigate this delicate equilibrium. In this section, we will explore strategies for effectively balancing safety stock levels while ensuring customer satisfaction through the implementation and utilization of ERP systems.
By leveraging the functionalities and capabilities of ERP systems, businesses can optimize inventory control, demand forecasting, order processing, and supply chain visibility to enhance customer satisfaction while minimizing the risk of stockouts and excess inventory costs.
From demand-driven approaches to data-driven decision-making, we will delve into a range of strategies that empower businesses to achieve the delicate balance between safety stock and customer satisfaction.
A. Demand forecasting and accurate inventory planning
Demand forecasting and accurate inventory planning are key strategies for balancing safety stock levels and customer satisfaction with the help of ERP systems. Here's how these strategies contribute to achieving the desired balance:
Demand Forecasting: ERP systems provide sophisticated demand forecasting capabilities by analyzing historical data, market trends, and external factors. Accurate demand forecasting allows businesses to anticipate customer demand with greater precision, enabling them to optimize inventory levels accordingly. By understanding demand patterns and fluctuations, businesses can adjust safety stock levels to meet customer requirements while minimizing the risk of stockouts or excess inventory.
Real-time Inventory Visibility: ERP systems offer real-time inventory visibility across different locations and warehouses. This visibility allows businesses to track inventory levels, monitor stock movements, and identify potential gaps between demand and supply. By having a comprehensive view of inventory, businesses can make informed decisions regarding safety stock levels based on current demand, lead times, and inventory turnover rates.
Collaborative Planning: ERP systems facilitate collaboration between different departments and stakeholders involved in inventory management. By integrating sales, marketing, and supply chain functions within the ERP system, businesses can align demand forecasts with promotional activities, product launches, and other events that impact inventory requirements. Collaborative planning ensures that safety stock levels are determined collectively, taking into account inputs from various stakeholders and avoiding discrepancies between forecasts and actual demand.
Statistical Models and Algorithms: ERP systems employ advanced statistical models and algorithms to analyze demand patterns and forecast future requirements. These models take into account factors such as seasonality, historical sales data, market trends, and customer behavior. By leveraging these analytical capabilities, businesses can generate accurate demand forecasts and fine-tune safety stock levels to meet customer expectations while optimizing inventory carrying costs.
Inventory Optimization Tools: ERP systems often provide inventory optimization tools that help businesses determine the optimal levels of safety stock. These tools consider factors such as service level targets, demand variability, lead time variability, and cost constraints. By using these tools, businesses can calculate safety stock levels that strike a balance between meeting customer demand and minimizing excess inventory, resulting in improved customer satisfaction and cost efficiency.
Continuous Monitoring and Adjustments: ERP systems enable continuous monitoring of inventory performance and demand fluctuations. By regularly reviewing and analyzing inventory data, businesses can identify trends, address supply chain bottlenecks, and adjust safety stock levels accordingly. This ongoing monitoring and adjustment process ensures that safety stock remains aligned with changing customer demands, resulting in optimal inventory levels and improved customer satisfaction.
B. Real-time inventory visibility and data analytics
Real-time inventory visibility and data analytics are essential strategies for balancing safety stock levels and customer satisfaction through ERP systems. Here's how these strategies contribute to achieving the desired balance:
Real-time Inventory Visibility: ERP systems provide real-time visibility into inventory levels, locations, and stock movements. This visibility allows businesses to monitor inventory in real-time, enabling them to make informed decisions about safety stock levels. By having up-to-date information on inventory availability, businesses can respond promptly to changes in demand, avoid stockouts, and maintain optimal inventory levels to meet customer needs.
Inventory Tracking and Traceability: ERP systems enable businesses to track inventory from procurement to fulfillment. By capturing data on inbound and outbound inventory movements, businesses gain insights into inventory flow and can identify bottlenecks or delays in the supply chain. This information helps optimize safety stock levels by identifying areas where inventory may be tied up or where additional stock may be required to meet customer demand.
Data Analytics and Reporting: ERP systems offer robust data analytics and reporting capabilities that allow businesses to analyze inventory-related data. By leveraging data analytics, businesses can gain insights into demand patterns, sales trends, seasonality, and customer behavior. These insights help in making data-driven decisions about safety stock levels, optimizing inventory planning, and aligning inventory with customer demand.
Predictive Analytics: ERP systems equipped with predictive analytics capabilities can forecast future demand and provide insights into future inventory needs. By analyzing historical data, market trends, and external factors, predictive analytics algorithms generate forecasts that aid in determining the appropriate safety stock levels. This proactive approach enables businesses to anticipate customer demand and optimize inventory levels accordingly.
Supply Chain Analytics: ERP systems integrate supply chain data, enabling businesses to analyze supply chain performance and identify areas for improvement. Supply chain analytics can highlight inefficiencies, such as excessive lead times or supplier constraints, that may impact safety stock levels.
By addressing these issues, businesses can enhance supply chain efficiency, reduce the need for excessive safety stock, and improve customer satisfaction through timely and reliable product availability.
Exception Management: ERP systems equipped with exception management capabilities can flag anomalies or deviations in inventory levels, demand, or supplier performance. This allows businesses to address potential issues promptly and take corrective actions to minimize disruptions in supply and maintain optimal safety stock levels. By proactively managing exceptions, businesses can reduce the risk of stockouts and ensure consistent customer satisfaction.
Continuous Improvement: Real-time inventory visibility and data analytics enable businesses to continually assess and improve inventory management processes. By analyzing inventory performance metrics, identifying areas for optimization, and implementing data-driven improvements, businesses can refine safety stock levels to align with customer demand and enhance customer satisfaction over time.
C. Automated replenishment processes and order management
Automated replenishment processes and effective order management are vital strategies for balancing safety stock levels and customer satisfaction through ERP systems. Here's how these strategies contribute to achieving the desired balance:
Automated Replenishment: ERP systems streamline replenishment processes by automating inventory replenishment based on predefined rules and triggers. By setting up automated reorder points or minimum stock thresholds, businesses can ensure that inventory is replenished in a timely manner. This automation reduces the risk of stockouts and ensures that safety stock levels are maintained to meet customer demand consistently.
Demand-driven Ordering: ERP systems enable businesses to adopt a demand-driven approach to ordering. By integrating sales data, demand forecasts, and real-time inventory information, businesses can align ordering decisions with actual customer demand. This ensures that inventory is replenished based on customer requirements, reducing excess stock and improving customer satisfaction.
Order Tracking and Fulfillment: ERP systems provide order management functionality that facilitates efficient order processing and fulfillment. By automating order entry, tracking, and fulfillment processes, businesses can streamline operations, minimize errors, and ensure timely order delivery. Seamless order management enhances customer satisfaction by providing accurate and transparent information about order status and delivery times.
Inventory Allocation Optimization: ERP systems assist businesses in optimizing inventory allocation across different sales channels or locations. By considering factors such as demand patterns, geographical factors, and customer preferences, businesses can allocate inventory strategically to meet customer demand efficiently. This optimization ensures that safety stock is distributed effectively, reducing stockouts and maximizing customer satisfaction.
Integration with Suppliers: ERP systems facilitate seamless integration with suppliers and enable electronic data interchange (EDI) for automated order placement and fulfillment. This integration enhances communication and collaboration with suppliers, reducing lead times and ensuring a reliable supply of inventory. By improving supplier relationships and streamlining the procurement process, businesses can maintain optimal safety stock levels and meet customer demand effectively.
Order Prioritization and Customer Segmentation: ERP systems allow businesses to prioritize orders based on predefined criteria such as customer type, order value, or service level agreements. By segmenting customers and assigning different order fulfillment priorities, businesses can ensure that safety stock is allocated strategically to high-value or priority customers. This personalized approach enhances customer satisfaction and loyalty.
Order Analytics and Performance Tracking: ERP systems provide analytics and reporting capabilities to track order performance and identify areas for improvement. By analyzing order fulfillment metrics, businesses can identify bottlenecks, optimize order processing workflows, and improve order accuracy and timeliness. These improvements enhance customer satisfaction by ensuring smooth and efficient order management.
Customer Self-Service: ERP systems often include self-service portals or e-commerce platforms that allow customers to place orders, track shipments, and manage their accounts independently. By providing self-service options, businesses empower customers with convenience and control over their orders, enhancing the overall customer experience and satisfaction.
D. Collaborative supply chain management with ERP integration
Collaborative supply chain management with ERP integration is a crucial strategy for balancing safety stock levels and customer satisfaction. Here's how this strategy contributes to achieving the desired balance:
Integrated Supply Chain Visibility: ERP systems enable the integration of various stakeholders within the supply chain, including suppliers, manufacturers, distributors, and retailers. By sharing real-time data and information across the supply chain, businesses can gain a holistic view of inventory levels, demand patterns, and production capacities. This integrated visibility facilitates effective collaboration, allowing stakeholders to align their efforts and optimize safety stock levels to meet customer demand.
Demand Collaboration: ERP systems support demand collaboration by allowing businesses to share demand forecasts, sales data, and customer insights with their supply chain partners. This collaboration enables suppliers to align their production and delivery schedules with anticipated customer demand. By synchronizing supply with demand, businesses can ensure the availability of products, minimize stockouts, and enhance customer satisfaction.
Supplier Collaboration: ERP systems facilitate seamless communication and collaboration with suppliers through integrated platforms and electronic data interchange (EDI). By sharing inventory information, lead times, and production schedules, businesses can work closely with suppliers to optimize inventory levels and manage safety stock effectively. Supplier collaboration ensures that inventory replenishment is timely, reducing the risk of stockouts and enhancing customer satisfaction.
Just-in-Time (JIT) Inventory Management: ERP systems enable businesses to implement JIT inventory management practices by coordinating production schedules with customer demand. Through real-time data sharing, ERP systems help businesses align production and delivery schedules to minimize the need for excessive safety stock.
JIT inventory management reduces carrying costs, optimizes inventory levels, and ensures that customers receive products when they need them, leading to improved customer satisfaction.
Supply Chain Analytics: ERP systems offer advanced analytics capabilities that enable businesses to analyze supply chain performance and identify areas for improvement. By leveraging supply chain analytics, businesses can gain insights into lead times, supplier performance, production efficiency, and transportation logistics. This information helps optimize safety stock levels by addressing bottlenecks, reducing delays, and enhancing overall supply chain efficiency to meet customer expectations.
Collaborative Demand Planning: ERP systems support collaborative demand planning by integrating sales forecasts, market insights, and customer feedback. By involving sales teams, marketing departments, and other stakeholders in the demand planning process, businesses can incorporate diverse perspectives and align safety stock levels with anticipated customer demand. Collaborative demand planning minimizes the risk of overstocking or understocking, ensuring that customer needs are met efficiently.
Continuous Improvement: Collaborative supply chain management with ERP integration promotes a culture of continuous improvement. By collecting and analyzing data on inventory performance, supplier performance, and customer satisfaction, businesses can identify areas for optimization and implement data-driven improvements. Continuous improvement efforts lead to enhanced collaboration, optimized safety stock levels, and improved customer satisfaction over time.
Case Studies and Examples of Successful Implementation of ERP for Balancing Safety Stock and Customer Satisfaction
Here are some real-world case studies and examples of successful implementations of ERP for balancing safety stock and customer satisfaction:
Cisco Systems: Cisco, a global technology leader, implemented an ERP system to improve its inventory management and customer satisfaction. By integrating their ERP system with demand forecasting tools, they achieved accurate demand projections and optimized safety stock levels. This allowed them to maintain optimal inventory levels while meeting customer demands.
The ERP system also enabled real-time inventory visibility, enabling them to track stock levels across their global supply chain and promptly address any shortages or delays. As a result, Cisco experienced a significant reduction in stockouts, improved order fulfillment rates, and enhanced customer satisfaction.
Coca-Cola Bottling Company United: Coca-Cola Bottling Company United, one of the largest independent Coca-Cola bottlers, implemented an ERP system to optimize its inventory management and customer satisfaction. By integrating their ERP system with demand planning and inventory optimization modules, they improved their forecasting accuracy and achieved better visibility into demand patterns.
This allowed them to optimize safety stock levels and reduce excess inventory, ensuring product availability while minimizing carrying costs. As a result, they achieved improved customer satisfaction by consistently meeting demand and reducing stockouts.
L.L.Bean: L.L.Bean, a renowned outdoor retailer, implemented an ERP system to enhance its inventory management and customer satisfaction. By integrating their ERP system with advanced analytics capabilities, they gained insights into customer preferences, buying patterns, and seasonal trends.
This enabled them to accurately forecast demand and optimize safety stock levels based on customer needs. The ERP system also facilitated collaboration with suppliers, improving lead times and ensuring timely replenishment. As a result, L.L.Bean reduced stockouts, enhanced order fulfillment rates, and provided a better customer experience, leading to increased customer satisfaction and loyalty.
Johnson & Johnson: Johnson & Johnson, a global healthcare company, implemented an ERP system to improve its inventory management and customer satisfaction. By integrating their ERP system with real-time data analytics and supply chain visibility tools, they gained a comprehensive view of their inventory across multiple locations.
This enabled them to optimize safety stock levels, streamline order fulfillment processes, and minimize stockouts. The ERP system also facilitated better collaboration with distributors and retailers, ensuring timely product availability and improved customer satisfaction.
Best Practices for Effective ERP Implementation
Implementing an ERP system can be a complex and critical undertaking for any organization. To ensure a successful implementation, here are some best practices to follow:
- Define Clear Objectives: Clearly define your objectives and desired outcomes for implementing the ERP system. Identify the specific pain points and areas for improvement that the ERP system should address. This will guide the entire implementation process and help align stakeholders towards common goals.
- Conduct a Comprehensive Needs Assessment: Perform a thorough assessment of your organization's needs and requirements. This includes evaluating existing business processes, data structures, and IT infrastructure. Identify the gaps and areas that need improvement, and ensure that the selected ERP system aligns with your specific business needs.
- Establish a Dedicated Project Team: Form a dedicated project team consisting of key stakeholders, subject matter experts, and IT professionals. Assign clear roles and responsibilities to team members, and ensure that they have the necessary resources and support to carry out their tasks effectively. The project team should be actively involved in all stages of the implementation, from planning to post-implementation support.
- Plan and Prioritize Phases: Break down the implementation process into manageable phases or modules. Prioritize the implementation based on critical business functions or areas that need immediate attention. This phased approach allows for better control, testing, and risk management, ensuring smoother implementation and faster user adoption.
- Engage End Users: Involve end users early in the implementation process to gather their input and feedback. Conduct thorough training sessions and workshops to familiarize users with the new ERP system and its functionalities. User engagement and buy-in are crucial for successful adoption and utilization of the system.
- Data Migration and Cleansing: Develop a robust data migration strategy and ensure data integrity during the transition from legacy systems to the new ERP system. Cleanse and validate data before migrating it to the new system to avoid data inconsistencies or errors. Establish data governance processes to maintain data quality in the long term.
- Customize Wisely: While customization can address specific business requirements, it should be done judiciously. Excessive customization can complicate the implementation, increase costs, and impact system stability and future upgrades. Evaluate the need for customization carefully and consider industry best practices and standard processes before making customization decisions.
- Test Rigorously: Conduct thorough testing at each stage of the implementation to identify and resolve any issues or discrepancies. This includes unit testing, integration testing, user acceptance testing, and performance testing. Rigorous testing ensures that the system functions as intended, meets business requirements, and is stable before going live.
- Change Management and Training: Implementing an ERP system often involves significant changes in business processes and user workflows. Develop a comprehensive change management plan that includes communication, training, and support mechanisms to help users adapt to the new system. Provide ongoing training and support even after the initial implementation to address user concerns and ensure smooth operations.
- Continuous Evaluation and Improvement: Post-implementation, establish mechanisms to continuously evaluate and improve the ERP system's performance. Monitor key performance indicators, gather user feedback, and conduct regular system audits to identify areas for optimization and enhancement. Stay updated with vendor releases and updates to leverage new features and functionalities.
Challenges and Limitations of ERP in Balancing Safety Stock and Customer Satisfaction
While ERP systems offer numerous benefits in inventory management and customer satisfaction, they also present certain challenges and limitations that organizations need to be aware of.
Here are some common challenges associated with ERP in balancing safety stock and customer satisfaction:
Complex Implementation: Implementing an ERP system is a complex undertaking that requires significant time, resources, and expertise. The implementation process involves data migration, system configuration, and process reengineering. Organizations may face challenges in managing the complexities of implementation, which can lead to delays, cost overruns, and disruptions to regular business operations.
Change Management: ERP implementation often requires changes in business processes, roles, and responsibilities. Employees may resist these changes, leading to resistance and difficulty in adapting to the new system. Change management efforts, including communication, training, and ongoing support, are crucial to address these challenges and ensure successful user adoption.
Data Accuracy and Cleansing: ERP systems heavily rely on accurate and clean data for effective inventory management. However, organizations may struggle with data integrity issues, such as inconsistent or duplicate data. Data cleansing and validation processes are necessary to ensure accurate data migration and ongoing data quality, which is essential for maintaining safety stock levels and satisfying customer demands.
Customization Limitations: While customization of ERP systems can address specific business needs, it can also present limitations. Excessive customization can make the system complex, difficult to maintain, and costly. Organizations need to strike a balance between customization and leveraging the system's standard functionalities to avoid long-term limitations and challenges.
Integration with Legacy Systems: Many organizations have existing legacy systems that need to be integrated with the new ERP system. Integration challenges can arise due to differences in data formats, system architectures, and compatibility issues. Ensuring seamless integration between the ERP system and legacy systems is essential for accurate data exchange and real-time inventory visibility.
Scalability and Flexibility: As businesses grow and evolve, their inventory management needs may change. ERP systems should be able to accommodate scalability and flexibility requirements. Organizations may face challenges in aligning the ERP system with changing business processes, expanding product lines, and diverse customer demands. Flexibility in system configurations and scalability options is crucial to adapt to evolving business requirements.
Training and User Adoption: Effective training and user adoption are critical for maximizing the benefits of ERP systems. Employees need to be trained on the system's functionalities, processes, and workflows. However, training efforts can be challenging, especially in large organizations with diverse user groups. Inadequate training can result in underutilization of the system and hinder the ability to balance safety stock and meet customer satisfaction goals.
System Downtime and Technical Issues: ERP systems, like any other software, may experience downtime, technical issues, or system failures. These disruptions can impact inventory management and customer satisfaction. Organizations need to have appropriate backup and recovery mechanisms in place to minimize the impact of system downtime and ensure uninterrupted operations.
Despite these challenges and limitations, organizations can overcome them by proper planning, stakeholder engagement, change management, and ongoing system monitoring. It is important to address these challenges proactively to leverage the full potential of ERP systems in balancing safety stock levels and meeting customer satisfaction goals.
Conclusion
In conclusion, balancing safety stock and customer satisfaction is a critical aspect of inventory management, and ERP systems play a vital role in achieving this balance. While ERP systems offer numerous benefits in optimizing inventory levels and meeting customer demands, there are also challenges and limitations that organizations need to address.
Effective implementation of ERP systems requires careful planning, stakeholder engagement, and change management to overcome challenges such as data accuracy, customization complexities, implementation cost and time, and user adoption. Additionally, organizations should consider scalability, flexibility, and ongoing technical support to ensure the ERP system can adapt to changing business needs.
Despite these challenges, successful implementation of ERP systems can lead to significant improvements in inventory management and customer satisfaction. Organizations can leverage functionalities such as demand forecasting, real-time inventory visibility, automated replenishment processes, and collaborative supply chain management to optimize safety stock levels and enhance customer experiences.
How can Deskera Help You?
Deskera ERP and MRP systems help you to keep your business units organized. The system's primary functions are as follows:
- Keep track of your raw materials and final items inventories
- Control production schedules and routings
- Keep a bill of materials
- Produce thorough reports
- Make your own dashboards
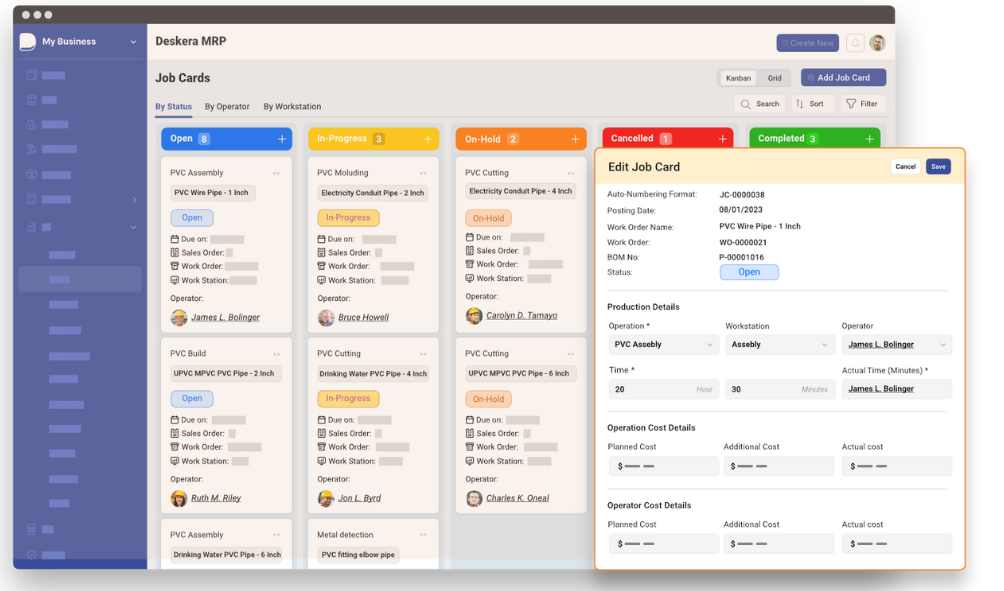
Deskera's integrated financial planning tools enable investors to better plan and track their investments. It can assist investors in making faster and more accurate decisions.
Deskera Books allows you to better manage your accounts and finances. Maintain good accounting practices by automating tasks like billing, invoicing, and payment processing.
Deskera CRM is a powerful solution that manages your sales and helps you close deals quickly. It not only enables you to perform critical tasks like lead generation via email, but it also gives you a comprehensive view of your sales funnel.
Deskera People is a straightforward tool for centralizing your human resource management functions.
Key Takeaways
- Safety stock is an essential component of inventory management, serving as a buffer to meet unexpected fluctuations in demand and ensure customer satisfaction.
- Factors influencing safety stock levels include demand variability, lead time variability, desired service levels, and supply chain uncertainties.
- Excessive safety stock ties up capital and storage space, while insufficient safety stock can lead to stockouts and dissatisfied customers.
- Customer satisfaction is vital in a competitive market, as it fosters loyalty, positive word-of-mouth, and repeat business.
- Inventory management directly impacts customer satisfaction by ensuring product availability, timely order fulfillment, and accurate delivery.
- Safety stock and customer satisfaction are interrelated, as maintaining appropriate safety stock levels directly influences the ability to meet customer demands.
- ERP systems provide comprehensive solutions for inventory management, integrating various modules and features to optimize safety stock and enhance customer satisfaction.
- ERP systems facilitate demand forecasting, accurate inventory planning, real-time visibility, data analytics, and automated replenishment processes to optimize safety stock levels.
- Effective implementation of ERP systems requires careful planning, stakeholder engagement, user training, and change management efforts.
- Continuous evaluation, improvement, and alignment with best practices are necessary to overcome challenges and fully leverage the potential of ERP systems in balancing safety stock and customer satisfaction.
Related Articles
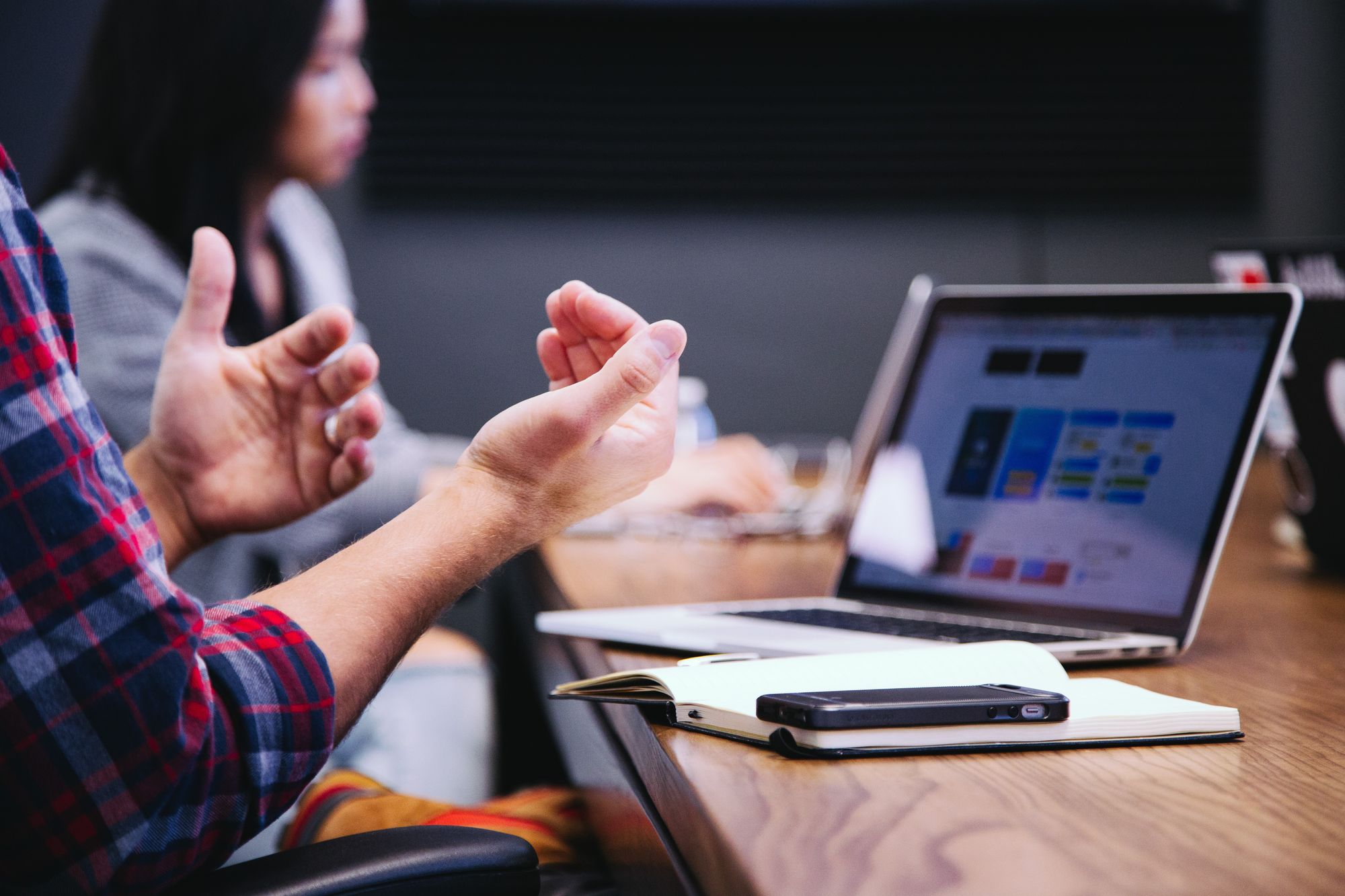

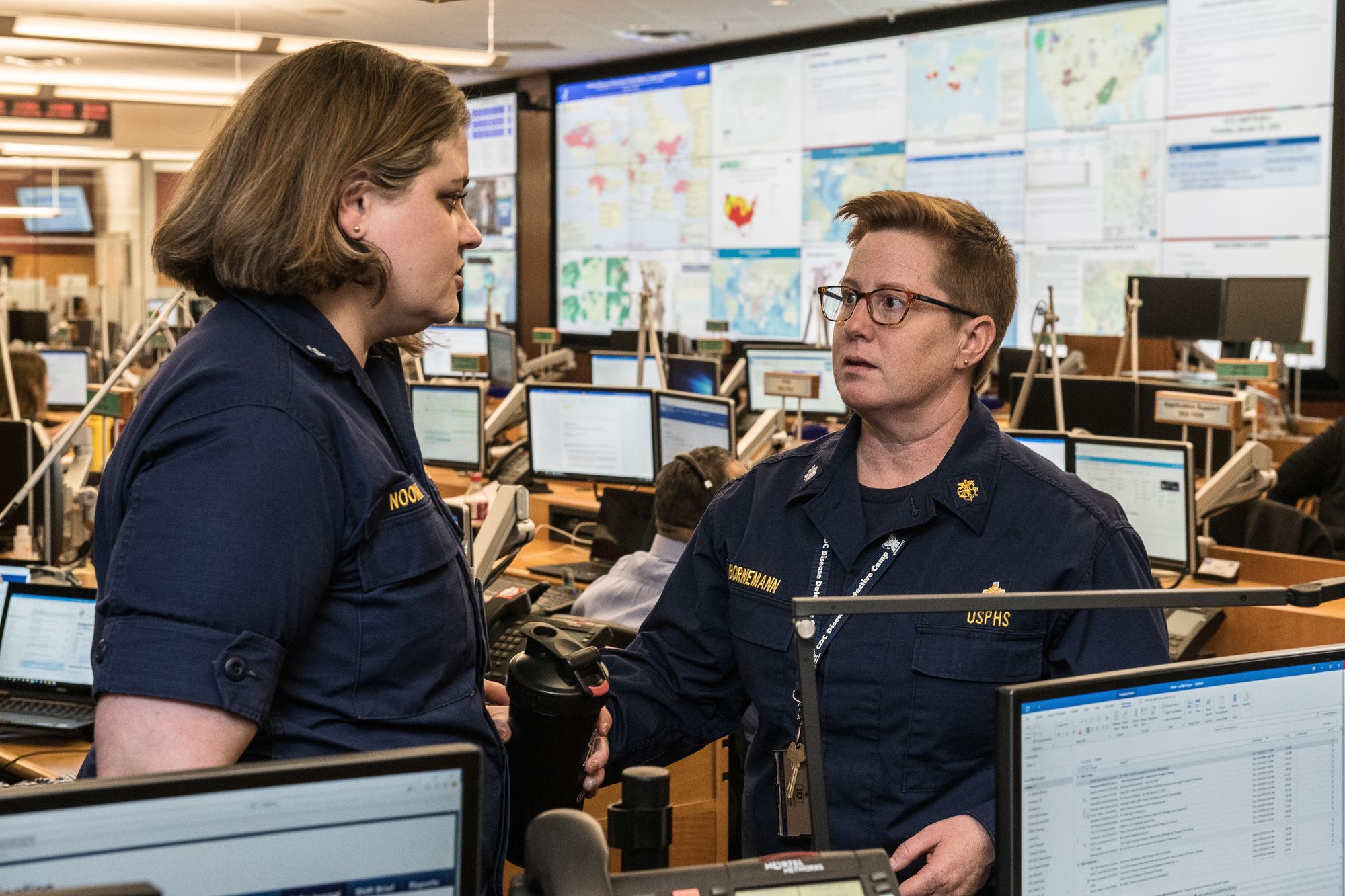
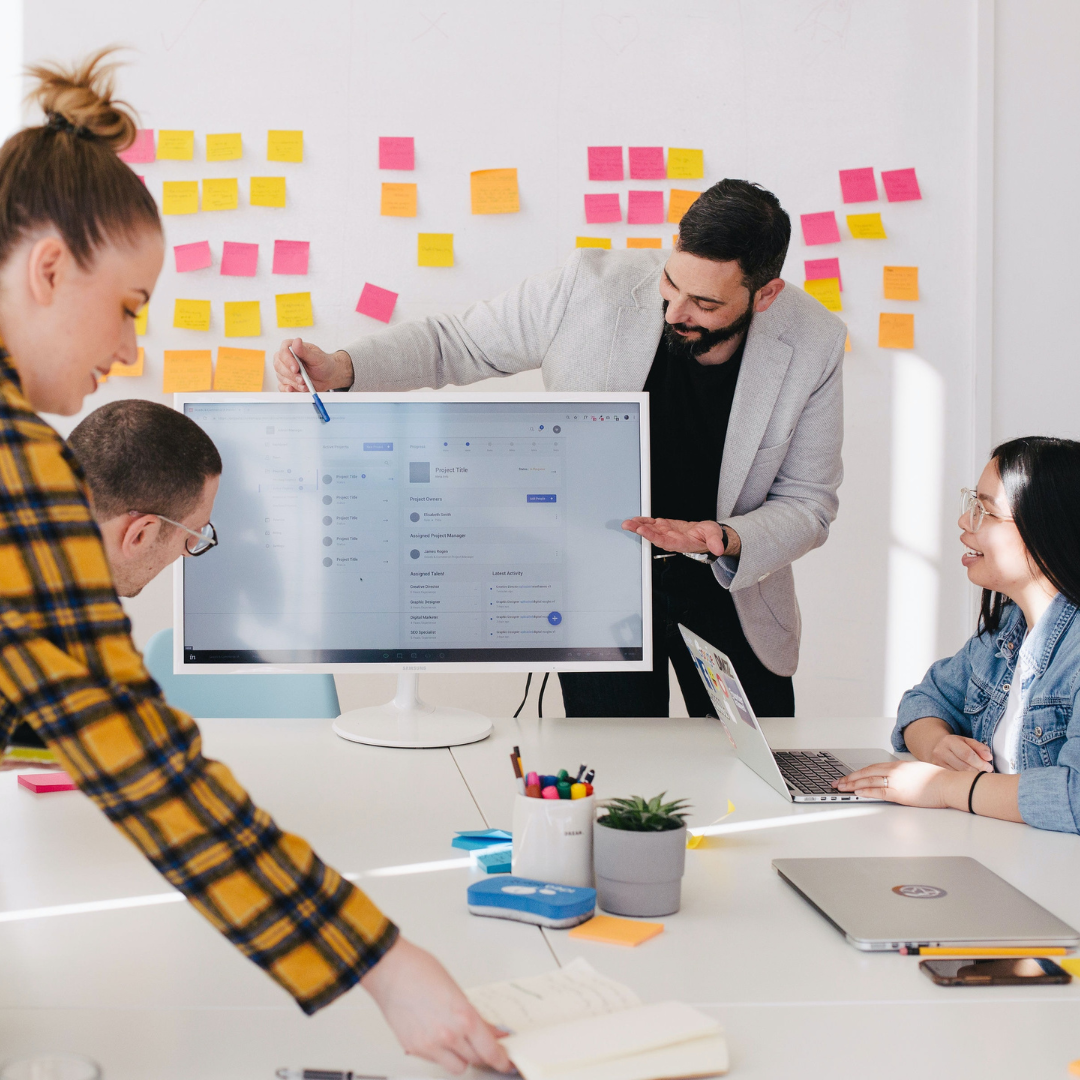