Inventory, often seen as a mundane aspect of business, can make or break your company's success.
Consider a hypothetical scenario where a retail business loses an average of 3.5% of its revenue (the average US food retail industry loses about 2-3%, according to McKinsey) due to stockouts alone. That's a staggering $1.75 million for every $50 million in sales!
But it's not just about having enough stock. Excess inventory ties up capital and can lead to waste, especially in industries with perishable goods.
From just-in-time systems revolutionizing manufacturing to AI-powered demand forecasting in retail, inventory management is undergoing a radical transformation. In this blog, we'll explore different parts of inventory to help you make better decisions for your business. Let’s begin.
What is Inventory?
Inventory refers to the goods, materials, or products that a business has on hand. It's essentially a list or count of items that a company owns and intends to sell, use in production, or consume in its operations. This can include:
- Raw materials
- Work-in-progress items
- Finished goods ready for sale
- Merchandise in a retail store
Inventory is considered an asset on a company's balance sheet. It represents value that the business owns and can convert into cash through sales or use in operations.
Inventory is generally considered a tangible asset. However, it's worth noting that in some modern contexts, particularly with digital products or services, there can be forms of "inventory" that are less tangible.
For example, software licenses or digital content for sale could be considered a type of inventory, even though they don't have a physical form in the traditional sense.
Inventory Explained
Your inventory is more than just stock on shelves. It's a strategic asset that impacts your entire business operation. Inventory serves as a buffer against supply and demand fluctuations. It ensures you can meet customer needs while optimizing production processes. Your inventory levels directly impact cash flow, operational costs, and overall profitability.
Inventory valuation methods significantly impact your financial reporting and cost accounting. The three primary methods are
- First-In, First-Out
- Last-In, First-Out
- Weighted average
FIFO (First-In, First-Out) assumes the oldest inventory items are sold first. It often provides a more accurate reflection of current market values.
LIFO (Last-In, First-Out) assumes the newest inventory items are sold first. This can reduce taxable income in inflationary periods but may understate inventory value.
The weighted average method calculates the average cost of all inventory items. It provides a middle ground between FIFO and LIFO.
Your choice of valuation method can significantly impact reported profits and tax liabilities. It's a critical decision for your business's financial strategy.
Types of Inventory: Which Ones Apply to Your Business?
Your inventory types reflect your business model, market position, and operational efficiency. Understanding these types reveals opportunities for optimization and innovation in your supply chain. Primarily, there are 7 types of inventory:
Raw Materials
These are the essential components you use in your production processes. Efficient management of raw materials ensures smooth production flow and cost control.
Work-in-Progress (WIP)
This includes partially completed products at various stages of manufacture. Monitoring WIP helps identify bottlenecks and improve production efficiency.
Finished Goods
These are your completed products ready for sale. Balancing finished goods inventory is crucial for meeting customer demand without overstocking.
Maintenance, Repair, and Operating (MRO) Supplies
These items support your production and operations. Effective MRO management reduces downtime and operational disruptions.
Safety Stock
This extra inventory mitigates supply chain disruptions. Optimal safety stock levels protect against stockouts without excessive holding costs.
Cycle Inventory
This is your regular stock that fluctuates based on sales and replenishment cycles. Understanding your cycle inventory helps optimize order quantities and frequencies.
Anticipation Inventory
This additional stock is built up in anticipation of increased demand. It's crucial for seasonal businesses or when preparing for market changes.
Each type serves a specific purpose and carries unique management challenges. Identify which types apply to your business by considering your industry, production processes, customer demands, and supply chain structure. This understanding forms the foundation of your inventory strategy.
What Are the Ways to Effectively Control Your Inventory
Controlling your inventory is crucial for maintaining operational efficiency and financial health. Implement these strategies to optimize your inventory management:
Accurate Forecasting
Utilize historical data and market trends to predict demand. Employ advanced analytics to improve forecast accuracy. This reduces the risk of overstocking or stockouts.
Just-in-Time (JIT) Inventory
Minimize holding costs by receiving goods only as they're needed in production. JIT requires close coordination with suppliers and robust logistics. It significantly reduces warehousing costs and improves cash flow.
ABC Analysis
Categorize your inventory items based on their value and importance. Allocate resources and attention accordingly, focusing on high-value items. This method ensures you're not treating all inventory equally, allowing for more efficient management.
Cycle Counting
Regularly audit a subset of inventory instead of annual full counts. This improves accuracy, helps identify discrepancies early, and reduces disruption to daily operations.
Economic Order Quantity (EOQ)
Calculate the optimal order quantity that minimizes total inventory costs, including holding and ordering costs. This balances the cost of holding inventory against the cost of ordering too frequently.
Real-Time Tracking
Implement systems for real-time inventory visibility across all locations. This enables quick responses to changes in demand or supply, reducing the risk of stockouts or overstocking.
These methods are universally applicable and can be adapted to fit various business models and industries. Implementing a combination of these strategies will significantly improve the inventory control of your business.
Examples of Inventory
Different industries maintain various types of inventory to support their operations. Understanding these examples can help you identify parallels in your own business:
Manufacturing Inventory:
Automotive: Raw materials like steel and plastic, components such as engines and transmissions, and finished vehicles.
Electronics: Semiconductors, circuit boards, displays, and completed devices.
Retail Inventory:
Apparel: Clothing items, accessories, and seasonal collections.
Grocery: Perishables, dry goods, and household items.
Healthcare Inventory:
Hospitals: Medications, surgical supplies, and medical equipment.
Pharmacies: Prescription drugs, over-the-counter medications, and health products.
Food and Beverage Inventory:
Restaurants: Fresh ingredients, dry goods, and beverages.
Beverage Companies: Raw ingredients, packaging materials, and finished products.
Technology Inventory:
Software Companies: Licenses and cloud storage capacity.
Hardware Manufacturers: Components and finished devices.
Construction Inventory:
Building Materials: Lumber, steel, and concrete.
Tools and Equipment: Power tools and heavy machinery.
Energy Inventory:
Oil and Gas: Crude oil, refined products, and equipment parts.
Renewable Energy: Solar panels and wind turbine components.
Types of Inventory Management Systems
There are several types of inventory management systems. The most basic is the periodic inventory system. With this system, a physical count of inventory is done at regular intervals. This is usually at the end of an accounting period.
Perpetual inventory system continuously updates inventory records. This happens each time a product is received or sold.
ABC analysis divides inventory into three categories based on value. "A" items are high value and most important to track. "B" items are of moderate value. "C" items are lower value and focused on less.
Just-in-time (JIT) inventory systems aim to keep only the minimum stock needed. This reduces holding costs. But it requires precise forecasting and fast suppliers.
Enterprise resource planning (ERP) systems integrate inventory with other business processes. This includes inventory in accounting, sales and purchasing.
What is Inventory Turnover
Inventory turnover is a crucial metric measuring how efficiently you manage your inventory. It indicates the number of times your inventory is sold and replaced within a specific period, typically a year. Calculate your inventory turnover using this formula:
Inventory Turnover = Cost of Goods Sold / Average Inventory
A higher inventory turnover ratio generally indicates better inventory management. It suggests you're efficiently selling your stock without excess accumulation. However, the optimal turnover rate varies by industry and business model.
Retail and fast-moving consumer goods typically have higher turnover rates. Luxury goods or industrial equipment may have lower rates.
Impact of Inventory on Your Bottom Line
Your inventory management directly affects your financial performance and operational efficiency. Effective inventory control can significantly boost your profitability and competitive advantage.
Carrying Costs
Excess inventory ties up your working capital and incurs storage, insurance, and handling expenses. These costs can erode your profit margins if not managed properly. Optimizing inventory levels frees up capital for other investments or operational needs.
Stockout Costs
Insufficient inventory leads to lost sales, damaged customer relationships, and potential long-term revenue loss. Balance holding costs against stockout risks to maintain customer satisfaction and market share.
Cash Flow
Efficient inventory management improves your cash flow by reducing the cash conversion cycle. This enhanced liquidity can provide a competitive edge, especially during economic downturns or rapid growth phases.
Asset Utilization
Inventory is a significant asset on your balance sheet. Improving inventory turnover rates enhances overall asset utilization, potentially increasing return on assets (ROA) and attracting investors.
Supply Chain Efficiency
Streamlined inventory processes can lead to better supplier relationships, improved negotiation power, and reduced lead times. This efficiency can result in cost savings and improved responsiveness to market changes.
Product Quality
Proper inventory management ensures fresher products and reduces obsolescence risk. This can lead to higher customer satisfaction and fewer write-offs for outdated or damaged goods.
Deskera for Simplifying Your Inventory
Simplifying your inventory gives you more control over other important parts of your business, like customer satisfaction and product development. To achieve that control, you need robust inventory management software that handles everything effortlessly.
Deskera ERP does exactly that. With integrated inventory management software, Deskera ERP not only gives you control over your inventory but also gives you full control over customer satisfaction.
With Deskera ERP, you get:
- Automated Reordering
- Multi-Warehouse Management
- Barcode Scanning
- Demand Forecasting
- Lot Tracking
- Integration Capabilities
- Mobile Access
- Customizable Reporting
- Vendor Management
Still thinking?
Schedule a call with our experts today and discover all you can achieve with us. Your first month is on us!
Key Takeaways
To summarize, here are the key takeaways from our blog on inventory:
- Effective inventory management is crucial for your financial health and operational efficiency.
- Understand and implement the right mix of inventory types for your business to optimize your supply chain.
- Utilize data-driven control methods like ABC analysis, cycle counting, and accurate forecasting to enhance inventory management.
- Monitor and improve your inventory turnover ratio to boost operational efficiency and profitability.
- Balance holding costs against stockout risks to maintain optimal inventory levels and customer satisfaction.
- Regularly review and adapt your inventory strategies to align with changing market conditions and business growth.
Related Articles
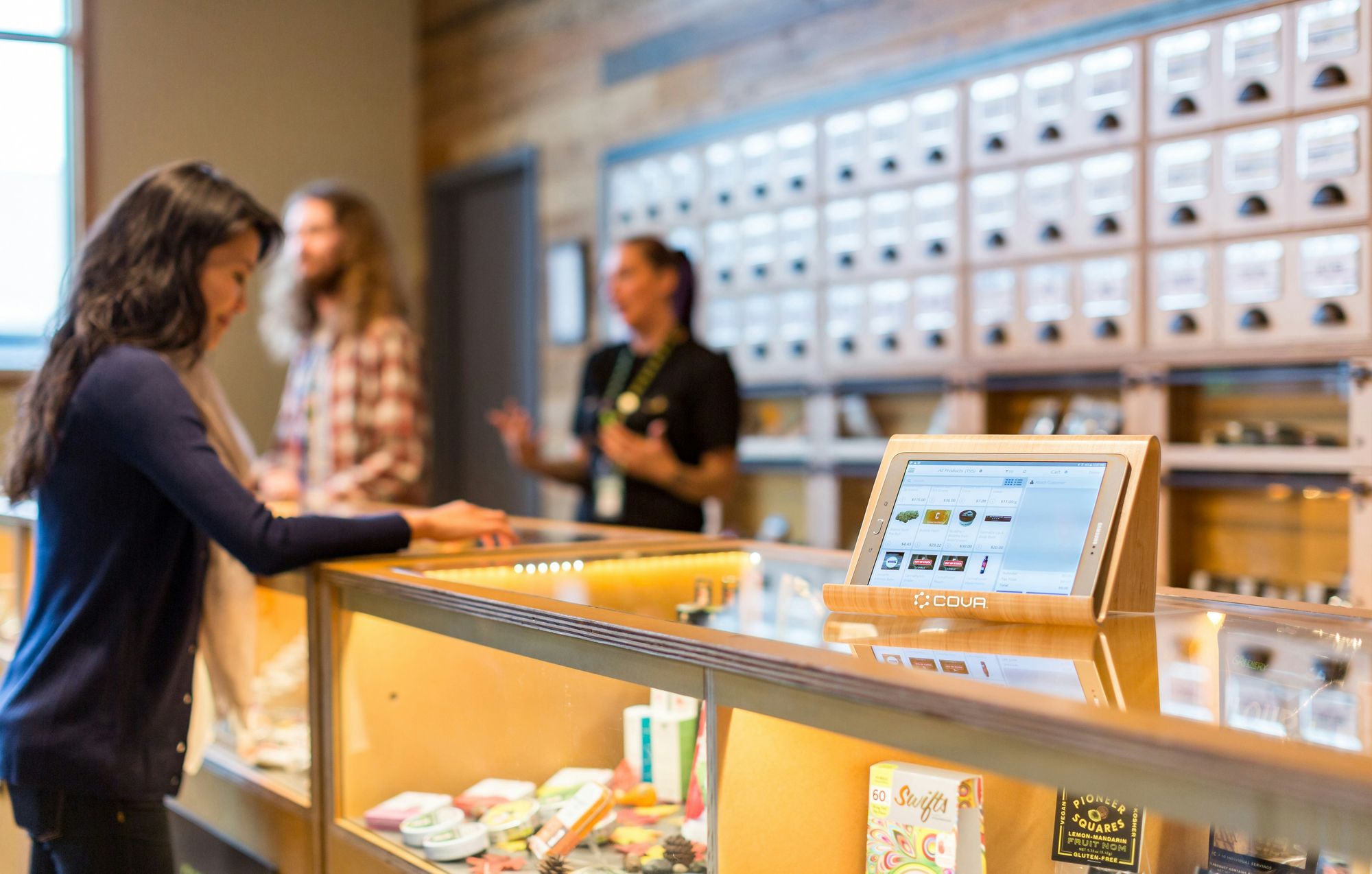
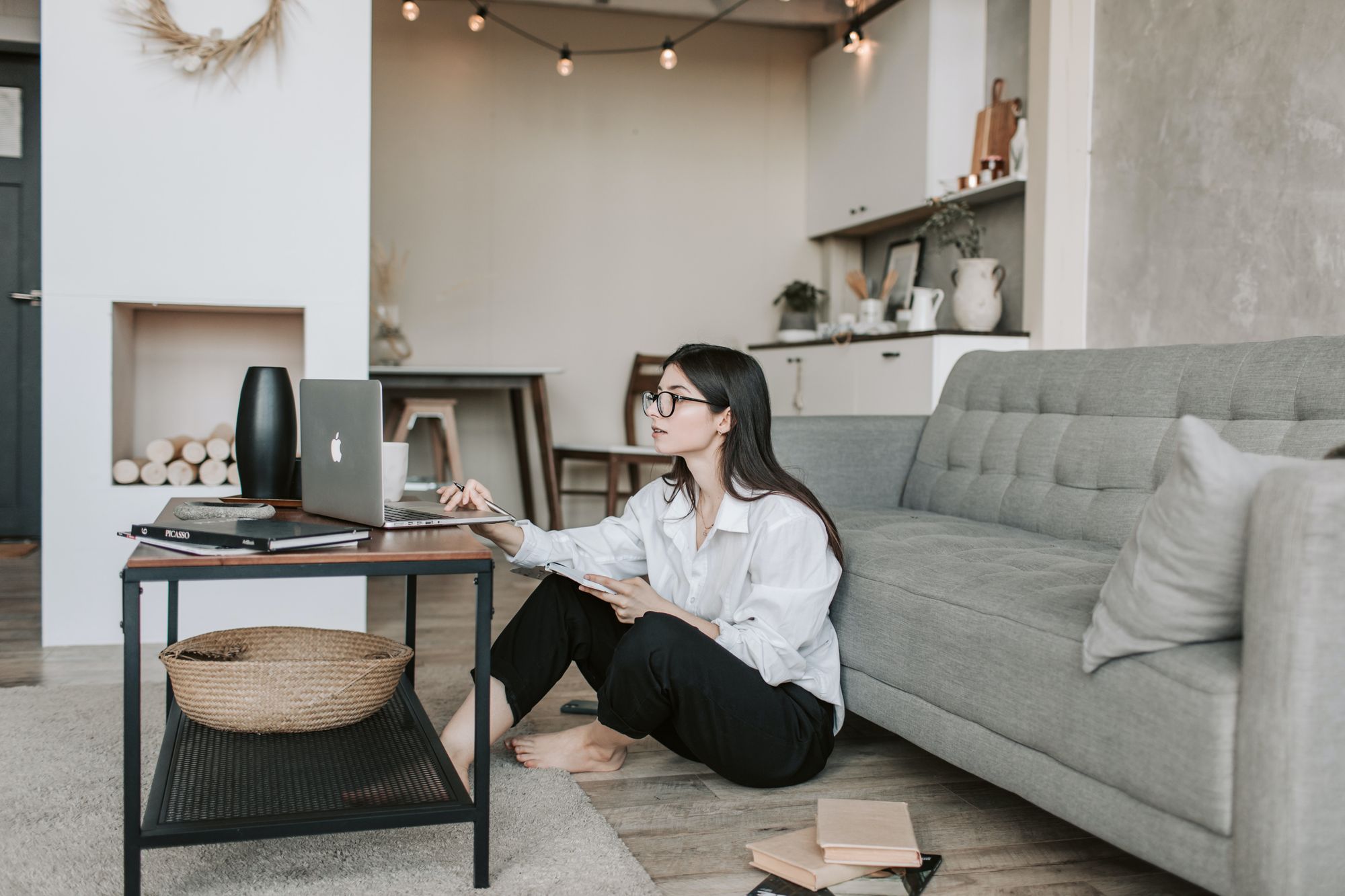
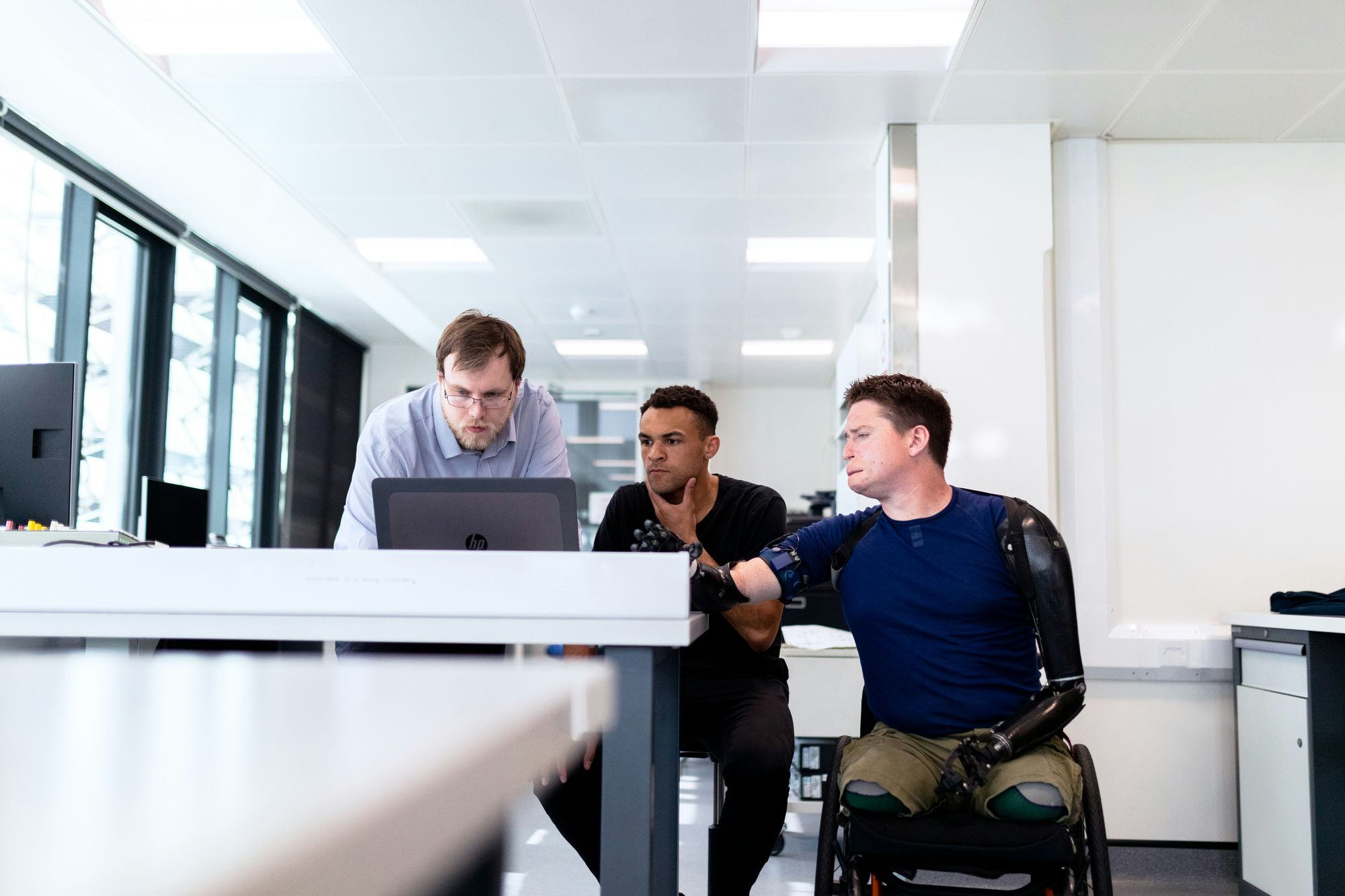