The competitive manufacturing landscape today showcases that optimizing profitability has become a top priority for executives. One crucial aspect that directly impacts the bottom line is inventory management. The effective control and utilization of inventory can significantly enhance operational efficiency, customer satisfaction, and overall profitability.
This is where the power of inventory analytics comes into play. By harnessing the vast amount of data available in the manufacturing environment, executives can gain valuable insights into inventory levels, demand patterns, and supply chain dynamics.
According to recent studies, companies that adopt advanced inventory analytics techniques experience an average 15% reduction in carrying costs and a 25% decrease in stockouts. Moreover, a survey conducted among manufacturing executives revealed that 72% of respondents believed that inventory analytics had a significant positive impact on their company's profitability.
These statistics highlight the immense potential of inventory analytics as a strategic tool for executives seeking to maximize manufacturing profitability.
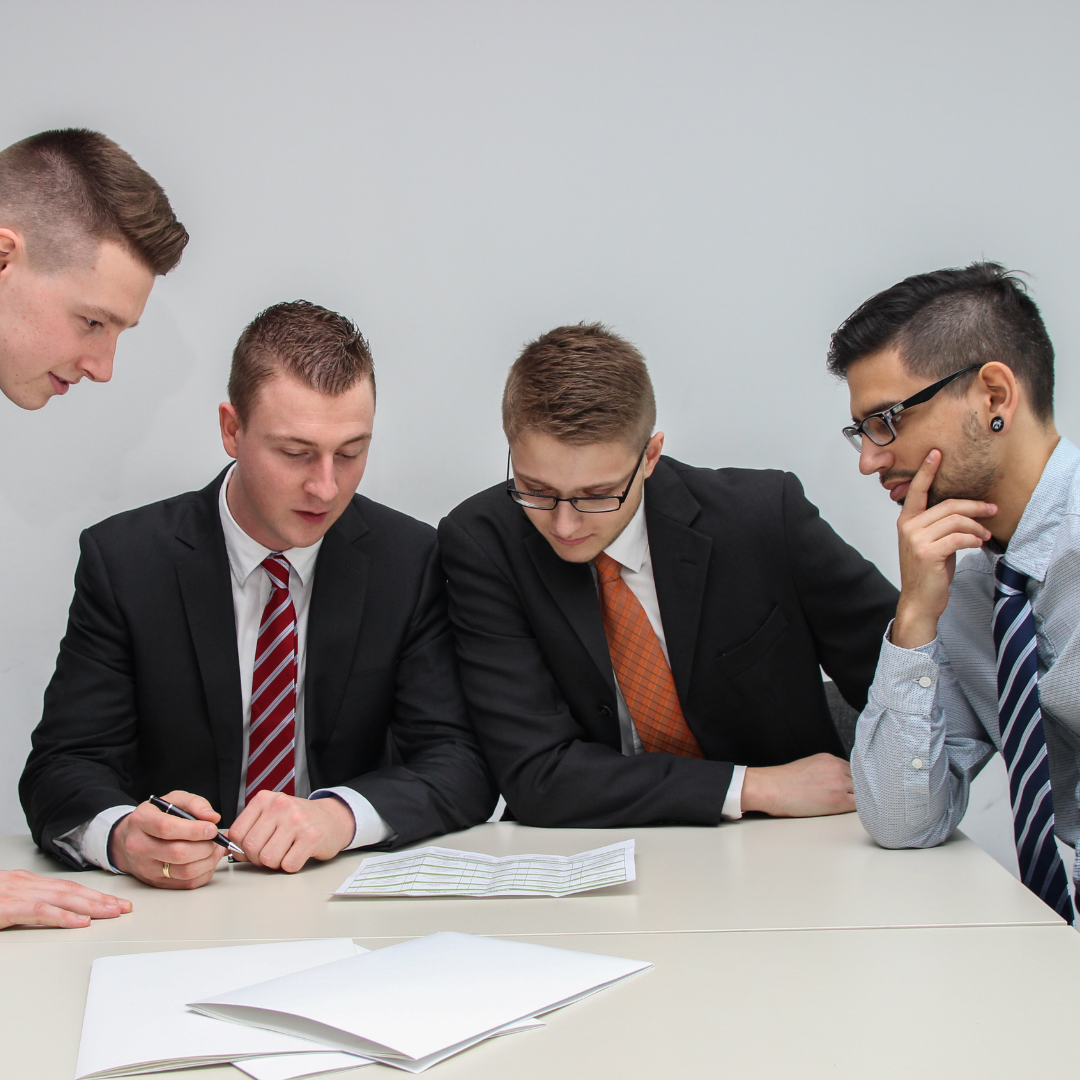
By leveraging inventory analytics, executives can make informed decisions regarding inventory levels, demand forecasting, and production planning, resulting in reduced costs, improved customer satisfaction, and increased revenue.
This article will delve into the power of inventory analytics for executives and provide insights on how to optimize manufacturing profitability through data-driven inventory management strategies.
Here is what we shall be learning in this post:
- Importance of Optimizing Manufacturing Profitability
- Role of Inventory Management in Driving Profitability
- Introduction to Inventory Analytics as a Powerful Tool for Executives
- The Role of Inventory Analytics in Manufacturing Profitability
- Understanding the Challenges in Inventory Management
- Leveraging Inventory Analytics for Profitability Optimization
- The Integration of Inventory Analytics with Supply Chain Management
- Overcoming Challenges in Implementing Inventory Analytics
- Best Practices and Recommendations for Executives
- Future Trends and Developments in Inventory Analytics for Manufacturing Companies
- Conclusion
- How can Deskera Help You?
- Key Takeaways
- Related Articles
Importance of Optimizing Manufacturing Profitability
Optimizing manufacturing profitability is of paramount importance in today's competitive business landscape. Manufacturers face numerous challenges, such as rising production costs, volatile market conditions, and increasing customer demands. By focusing on profitability, companies can achieve sustainable growth, enhance their market position, and ensure long-term success.
Here are some key reasons why optimizing manufacturing profitability is crucial:
- Cost Reduction: Maximizing profitability requires identifying and eliminating unnecessary costs throughout the manufacturing process. By streamlining operations, optimizing resource allocation, and minimizing waste, manufacturers can significantly reduce expenses and improve their profit margins.
- Competitive Advantage: In a global marketplace, businesses must stay ahead of their competitors. By optimizing profitability, manufacturers can invest in research and development, innovate their products, and enhance their competitive edge. This allows them to attract more customers, gain market share, and outperform rivals.
- Financial Stability: A profitable manufacturing operation ensures financial stability and resilience. It enables companies to weather economic downturns, invest in growth opportunities, and withstand unforeseen challenges. Strong profitability also strengthens their relationships with investors, lenders, and stakeholders.
- Customer Satisfaction: Profitability optimization directly impacts customer satisfaction and loyalty. By delivering high-quality products efficiently and at competitive prices, manufacturers can meet customer expectations, build loyalty, and cultivate long-term relationships. Satisfied customers contribute to repeat business, positive word-of-mouth, and increased market share.
- Strategic Decision Making: When profitability is optimized, executives have access to accurate financial data and insights. This empowers them to make informed decisions regarding pricing strategies, production volumes, inventory management, and investment priorities. Strategic decision-making based on profitability analysis drives sustainable growth and maximizes returns on investment.
- Employee Morale and Retention: A profitable manufacturing environment fosters employee satisfaction and job security. When employees see their company thriving, they feel motivated, engaged, and committed to their work. This leads to higher productivity, improved quality, and reduced turnover rates, ultimately benefiting profitability.
Optimizing manufacturing profitability is essential for companies to thrive in a competitive market. It enables cost reduction, enhances competitiveness, ensures financial stability, improves customer satisfaction, facilitates strategic decision-making, and boosts employee morale. By leveraging strategies and tools to maximize profitability, manufacturers can achieve sustainable growth and stay ahead in an ever-evolving industry.
Role of Inventory Management in Driving Profitability
Inventory management plays a pivotal role in driving profitability for manufacturing companies. Effectively managing inventory levels and processes can directly impact a company's financial performance and overall profitability.
Here are key ways in which inventory management contributes to driving profitability:
Cost Control: Efficient inventory management helps control costs associated with carrying inventory. By optimizing inventory levels, manufacturers can minimize holding costs, reduce storage expenses, and mitigate the risk of inventory obsolescence. This leads to improved cash flow and lower operational expenses, ultimately increasing profitability.
Customer Satisfaction: Inventory management ensures timely availability of products to meet customer demand. By maintaining optimal stock levels, companies can avoid stockouts and fulfill orders promptly, enhancing customer satisfaction. Satisfied customers are more likely to become repeat buyers, leading to increased sales, higher revenues, and improved profitability.
Demand Forecasting and Planning: Effective inventory management relies on accurate demand forecasting and planning. By leveraging historical data, market trends, and predictive analytics, manufacturers can anticipate customer demand patterns.
This enables them to align production schedules, optimize procurement, and prevent overstocking or understocking situations. Aligning supply with demand minimizes inventory holding costs and maximizes sales, positively impacting profitability.
Supply Chain Efficiency: Inventory management is closely tied to supply chain efficiency. By establishing strong relationships with suppliers, implementing just-in-time (JIT) inventory practices, and optimizing lead times, manufacturers can reduce the time and cost associated with inventory replenishment.
Streamlining the supply chain improves operational efficiency, reduces inventory holding costs, and increases profitability.
Risk Mitigation: Effective inventory management helps mitigate risks associated with inventory fluctuations. By closely monitoring inventory levels, manufacturers can identify slow-moving or obsolete items and take proactive measures to prevent losses. By minimizing inventory write-offs and avoiding excessive stock, companies can protect their financial health and profitability.
Cost of Capital Optimization: Inventory ties up a significant amount of capital for manufacturers. By adopting inventory management strategies such as lean manufacturing, just-in-time (JIT) practices, and vendor-managed inventory (VMI), companies can optimize their working capital. Reducing the amount of capital locked in inventory allows for greater financial flexibility, improved liquidity, and increased profitability.
In conclusion, effective inventory management directly contributes to driving profitability in manufacturing companies. By controlling costs, satisfying customer demand, optimizing supply chain efficiency, mitigating risks, and optimizing capital, companies can achieve higher profitability, gain a competitive edge, and ensure sustainable growth in the marketplace.
Introduction to Inventory Analytics as a Powerful Tool for Executives
Inventory analytics has emerged as a powerful tool for executives in the manufacturing industry, revolutionizing the way companies manage their inventory and driving profitability. As technology advances and data becomes more readily available, executives now have access to sophisticated analytical techniques that can unlock valuable insights and optimize their inventory management processes.
Inventory analytics leverages data-driven approaches to analyze and interpret vast amounts of information related to inventory levels, demand patterns, supplier performance, and production metrics. By applying statistical models, machine learning algorithms, and predictive analytics, executives can gain a deeper understanding of their inventory dynamics and make informed decisions to improve profitability.
The power of inventory analytics lies in its ability to provide executives with real-time visibility into inventory positions, demand forecasting accuracy, and supply chain performance. By identifying trends, patterns, and anomalies in the data, executives can proactively adjust production levels, optimize reorder points, and minimize stockouts or excess inventory. This not only improves operational efficiency but also enhances customer satisfaction by ensuring products are available when and where they are needed.
Furthermore, inventory analytics enables executives to identify and address inefficiencies and bottlenecks within the supply chain. By analyzing lead times, supplier performance, and transportation costs, executives can make strategic decisions to optimize sourcing, reduce costs, and improve overall supply chain effectiveness.
The implementation of inventory analytics also facilitates better collaboration and communication across departments. Executives can share insights and data-driven recommendations with procurement, production, and sales teams, fostering a more integrated and synchronized approach to inventory management.
Ultimately, inventory analytics empowers executives to make data-driven decisions, optimize profitability, and gain a competitive advantage in the market. By harnessing the power of analytics, executives can navigate the complexities of inventory management with greater precision and agility, resulting in improved financial performance and enhanced operational excellence.
The Role of Inventory Analytics in Manufacturing Profitability
In the quest to optimize manufacturing profitability, inventory analytics emerges as a critical tool for executives. With the advent of advanced technologies and the abundance of data, inventory analytics offers a transformative approach to inventory management.
From optimizing inventory levels to enhancing demand forecasting accuracy, inventory analytics empowers executives with real-time visibility and actionable insights. By leveraging advanced analytical techniques, executives can unlock the potential of their inventory data to drive efficiency, improve customer satisfaction, and ultimately boost the bottom line.
In this section, we explore the various ways in which inventory analytics serves as a strategic tool for executives in their quest for manufacturing profitability optimization.
Definition and scope of inventory analytics
Inventory analytics refers to the application of data analysis, statistical modeling, and advanced algorithms to extract meaningful insights and optimize inventory management processes. It involves collecting, processing, and analyzing large volumes of data related to inventory levels, demand patterns, sales trends, supplier performance, and other relevant metrics. The goal of inventory analytics is to enable executives to make informed decisions, improve operational efficiency, and maximize profitability.
The scope of inventory analytics encompasses a range of techniques and methodologies. These include:
- Demand Forecasting: Inventory analytics utilizes historical data and predictive models to forecast future demand accurately. By understanding demand patterns and fluctuations, executives can optimize inventory levels, reduce stockouts, and minimize excess inventory.
- Inventory Optimization: Through advanced algorithms and statistical techniques, inventory analytics helps determine optimal inventory levels, reorder points, and safety stock quantities. It enables executives to strike a balance between minimizing inventory carrying costs and avoiding stockouts.
- Supply Chain Visibility: Inventory analytics provides real-time visibility into the supply chain, allowing executives to monitor inventory movements, track lead times, and identify bottlenecks. This enhances supply chain transparency and enables proactive decision-making to improve efficiency.
- Performance Monitoring: By analyzing key performance indicators (KPIs) such as inventory turnover, fill rate, and order cycle time, inventory analytics helps executives monitor the performance of their inventory management strategies. It enables them to identify areas for improvement and make data-driven adjustments.
- Risk Management: Inventory analytics helps identify and mitigate risks associated with inventory, such as obsolescence, stockouts, or overstocking. By analyzing historical data and market trends, executives can proactively manage inventory risks and minimize financial losses.
- Supplier Management: Inventory analytics provides insights into supplier performance, including lead times, delivery reliability, and quality metrics. This enables executives to evaluate supplier relationships, optimize procurement processes, and enhance collaboration with suppliers.
In summary, inventory analytics encompasses a wide range of analytical techniques and methodologies that enable executives to gain actionable insights and optimize inventory management processes.
By leveraging data-driven approaches, executives can make informed decisions to improve demand forecasting, inventory optimization, supply chain visibility, performance monitoring, risk management, and supplier management, ultimately driving manufacturing profitability.
How inventory analytics can provide insights into inventory levels, demand forecasting, and lead times
Inventory analytics utilizes advanced data analysis techniques to provide valuable insights into various aspects of inventory management, including inventory levels, demand forecasting, and lead times. Here's how inventory analytics can contribute to each of these areas:
Inventory Levels
Inventory analytics helps determine optimal inventory levels by analyzing historical data, demand patterns, and other relevant factors. By assessing inventory turnover rates, carrying costs, and customer demand fluctuations, executives can identify the right balance between holding enough inventory to meet customer needs and minimizing excess stock. This ensures efficient use of resources, reduces carrying costs, and prevents stockouts or overstocking.
Demand Forecasting
Inventory analytics leverages historical sales data, market trends, and predictive modeling to improve demand forecasting accuracy. By analyzing patterns, seasonality, and external factors that impact demand, executives can make more accurate predictions.
This helps optimize inventory planning, align production schedules, and proactively manage supply chain activities to meet customer demand efficiently. Accurate demand forecasting minimizes inventory holding costs, reduces stockouts, and enhances customer satisfaction.
Lead Times
Inventory analytics enables executives to analyze and optimize lead times throughout the supply chain. By examining historical data and monitoring supplier performance, executives can identify areas of improvement, streamline processes, and reduce lead times.
Shorter lead times allow for faster replenishment of inventory, minimizing stockouts and improving responsiveness to customer demands. Analyzing lead times also helps identify potential bottlenecks and inefficiencies, leading to enhanced supply chain efficiency and reduced costs.
By harnessing the power of inventory analytics, executives gain deeper visibility into inventory levels, demand patterns, and lead times. These insights enable them to make data-driven decisions, optimize inventory management processes, and enhance operational efficiency. Ultimately, inventory analytics helps ensure the right inventory is available at the right time, reducing costs, improving customer satisfaction, and maximizing profitability.
Benefits of leveraging inventory analytics for executives in manufacturing companies
Leveraging inventory analytics offers numerous benefits for executives in manufacturing companies. Here are some key advantages of utilizing inventory analytics in the decision-making process:
- Improved Forecasting Accuracy: Inventory analytics leverages historical data, market trends, and advanced algorithms to enhance demand forecasting accuracy. By gaining insights into demand patterns, executives can make more informed decisions regarding inventory levels, production planning, and resource allocation. Accurate forecasting reduces stockouts, minimizes excess inventory, and optimizes customer satisfaction.
- Optimized Inventory Levels: Inventory analytics provides executives with real-time visibility into inventory levels, allowing for optimal inventory management. By analyzing inventory turnover rates, carrying costs, and customer demand fluctuations, executives can identify and maintain optimal stock levels. This reduces holding costs, improves cash flow, and avoids overstocking or understocking situations.
- Efficient Supply Chain Management: Leveraging inventory analytics enables executives to optimize supply chain processes. By analyzing lead times, supplier performance, and transportation costs, executives can identify areas for improvement and take proactive measures to streamline operations. This leads to improved supply chain efficiency, reduced costs, and enhanced responsiveness to customer demands.
- Cost Reduction: Inventory analytics helps identify cost-saving opportunities throughout the inventory management process. By optimizing inventory levels, reducing stockouts, and minimizing excess inventory, executives can reduce carrying costs, storage expenses, and the risk of inventory obsolescence. This results in improved financial performance and increased profitability.
- Enhanced Decision-Making: With inventory analytics, executives have access to actionable insights and data-driven recommendations. This enables them to make informed decisions regarding pricing strategies, production volumes, inventory replenishment, and supplier management. Data-driven decision-making reduces guesswork, minimizes risks, and increases the likelihood of successful outcomes.
- Increased Customer Satisfaction: Effective inventory management through analytics ensures products are available when and where customers need them. This leads to improved order fulfillment, reduced lead times, and enhanced customer satisfaction. Satisfied customers are more likely to become repeat buyers, contributing to increased sales and long-term profitability.
Understanding the Challenges in Inventory Management
Inventory management presents several challenges that manufacturing companies must navigate to ensure optimal efficiency and profitability. This section delves into the complexities and obstacles faced in inventory management, highlighting the importance of understanding and addressing these challenges. By recognizing the unique hurdles associated with inventory management, executives can develop effective strategies to overcome them and achieve improved operational performance.
From inventory inaccuracies and demand variability to supply chain disruptions and changing customer expectations, this section explores the multifaceted nature of the challenges in inventory management.
By gaining insights into these challenges, executives can proactively implement solutions, optimize inventory processes, and ultimately enhance profitability. In this section, we examine the key challenges in inventory management, their impact on manufacturing operations, and the strategies to mitigate them, ensuring smoother inventory management processes and improved financial outcomes.
Exploring common challenges in inventory management for manufacturing companies
Inventory management poses a range of challenges for manufacturing companies, requiring proactive strategies to ensure smooth operations and profitability. This section explores some of the common challenges faced in inventory management and highlights their impact on manufacturing processes. By understanding these challenges, executives can devise effective solutions to optimize inventory management. Here are some key challenges:
Inventory Inaccuracies: Maintaining accurate inventory records can be challenging, particularly as companies handle large volumes of diverse products. Inaccurate inventory data can lead to stockouts, overstocking, and difficulties in fulfilling customer orders. Executives must address this challenge by implementing robust inventory tracking systems and conducting regular audits.
Demand Variability: Fluctuating customer demand adds complexity to inventory management. Rapid shifts in market trends, seasonal variations, and unpredictable demand patterns make it challenging to forecast accurately. Executives need to employ demand forecasting techniques, leverage historical data, and adopt agile inventory replenishment strategies to mitigate the impact of demand variability.
Supply Chain Disruptions: Supply chain disruptions, such as delays in raw material delivery, production bottlenecks, or supplier issues, can disrupt inventory management processes. Executives must establish strong supplier relationships, diversify suppliers, and implement contingency plans to mitigate the risks associated with supply chain disruptions.
Changing Customer Expectations: Customer expectations continue to evolve, demanding shorter lead times, customized products, and faster order fulfillment. Meeting these expectations while efficiently managing inventory requires agility and flexibility in manufacturing processes. Executives should invest in technologies and processes that enable customization, shorten lead times, and enhance responsiveness to changing customer demands.
Cost Optimization: Balancing inventory carrying costs with the need to maintain sufficient stock levels is a constant challenge. Holding excessive inventory ties up capital, increases storage costs, and risks product obsolescence. On the other hand, inadequate inventory levels can lead to missed sales opportunities and dissatisfied customers. Executives must employ inventory optimization techniques, implement just-in-time (JIT) practices, and conduct cost-benefit analyses to strike the right balance.
Technology Adoption and Integration: Implementing and integrating advanced inventory management technologies can be complex and time-consuming. Upgrading systems, training staff, and ensuring seamless integration with existing processes pose challenges. Executives must carefully plan and execute technology adoption strategies, considering scalability, compatibility, and employee training to optimize inventory management.
By addressing these challenges head-on, manufacturing executives can streamline inventory management processes, reduce costs, enhance customer satisfaction, and improve overall profitability.
Implementing effective strategies, leveraging technology, and embracing agile approaches empower executives to overcome these challenges and achieve operational excellence in inventory management.
Examples of issues related to overstocking, stockouts, and obsolete inventory
Issues related to overstocking, stockouts, and obsolete inventory can have significant implications for manufacturing companies. Here are some examples of each:
- Overstocking:
- Excessive carrying costs: Holding excess inventory ties up capital, increases storage costs, and requires additional resources for maintenance and handling.
- Risk of obsolescence: Overstocked items may become outdated or obsolete, resulting in financial losses if they cannot be sold or used.
- Reduced cash flow: Excessive inventory ties up working capital, limiting the company's ability to invest in other areas of the business or respond to market opportunities.
- Increased holding costs: Overstocking can lead to increased warehousing costs, including rent, utilities, and insurance expenses.
- Stockouts:
- Missed sales opportunities: Stockouts result in unfulfilled customer demand, leading to lost sales and potential damage to customer relationships.
- Reduced customer satisfaction: Customers expect products to be available when they need them. Stockouts can lead to dissatisfaction, lower customer loyalty, and negative word-of-mouth.
- Rush orders and expedited shipping: Stockouts may require expedited shipping or rush orders to meet customer demands, resulting in higher costs for the company.
- Impact on production planning: Stockouts can disrupt production schedules, causing delays and inefficiencies in the manufacturing process.
- Obsolete Inventory:
- Financial losses: Obsolete inventory becomes a financial burden as it cannot be sold or used, resulting in direct losses for the company.
- Holding costs: Keeping obsolete inventory incurs ongoing storage costs, further reducing profitability.
- Wasted resources: Obsolete inventory ties up valuable warehouse space and resources that could be utilized for more productive purposes.
- Inefficient use of capital: Capital tied up in obsolete inventory cannot be reinvested in more profitable areas of the business.
Addressing these issues requires effective inventory management strategies, such as implementing demand forecasting techniques, adopting just-in-time (JIT) inventory practices, improving supplier collaboration, and implementing efficient inventory monitoring systems.
By proactively managing inventory levels and optimizing inventory turnover, manufacturing companies can mitigate the risks associated with overstocking, stockouts, and obsolete inventory, improving financial performance and customer satisfaction.
Impact of poor inventory management on profitability and customer satisfaction
Poor inventory management can have a significant impact on both profitability and customer satisfaction for manufacturing companies. Here are some key ways in which inadequate inventory management practices can negatively affect these areas:
- Profitability:
- Increased carrying costs: Inefficient inventory management, such as overstocking or holding excess inventory, leads to higher carrying costs. This includes costs associated with storage, insurance, handling, and depreciation. These expenses eat into the company's profits.
- Obsolete inventory: Poor inventory management can result in the accumulation of obsolete or outdated inventory. This inventory becomes a financial burden as it cannot be sold or used, leading to direct financial losses for the company.
- Stockouts: Inadequate inventory management may result in stockouts, where products are not available when customers demand them. Stockouts lead to missed sales opportunities and potential revenue loss, impacting the company's bottom line.
- Inefficient resource allocation: Poor inventory management can lead to inefficient use of resources, including labor, warehouse space, and transportation. This inefficiency increases costs and reduces overall profitability.
- Customer Satisfaction:
- Stockouts: When customers are unable to find products they need due to stockouts, it leads to frustration and dissatisfaction. This can result in a loss of customer loyalty and negative word-of-mouth, impacting the company's reputation and future sales.
- Inconsistent order fulfillment: Poor inventory management can result in inconsistent order fulfillment. Customers expect timely and accurate delivery of their orders. Delays, incorrect shipments, or incomplete orders can lead to dissatisfaction and erode customer trust.
- Inaccurate demand forecasting: Inadequate inventory management may result in inaccurate demand forecasting. This can lead to understocking or overstocking, both of which negatively impact customer satisfaction. Understocking leads to unmet customer demand, while overstocking may result in delays or difficulties in fulfilling specific customer requirements.
- Poor product quality: Inefficient inventory management can increase the likelihood of product quality issues, such as holding inventory for too long, leading to expiration or deterioration. This can result in customer dissatisfaction and potential product returns.
Improving inventory management practices, such as implementing robust inventory tracking systems, optimizing inventory levels, and enhancing demand forecasting accuracy, is crucial for mitigating these negative impacts.
By aligning inventory levels with customer demand, ensuring product availability, and minimizing stockouts, manufacturing companies can enhance profitability and improve customer satisfaction, ultimately strengthening their competitive position in the market.
Leveraging Inventory Analytics for Profitability Optimization
In today's data-driven business landscape, manufacturing companies are increasingly turning to inventory analytics as a powerful tool for optimizing profitability. This section explores the significant role of inventory analytics in driving profitability optimization and how it enables executives to make informed decisions based on data-driven insights.
By harnessing the power of advanced analytical techniques and leveraging the abundance of inventory data, executives can unlock hidden opportunities, streamline operations, and maximize profitability. From optimizing inventory levels and improving demand forecasting accuracy to enhancing supply chain performance and reducing costs, inventory analytics empowers executives with real-time visibility and actionable insights.
This section delves into the various ways in which inventory analytics serves as a strategic asset, enabling executives to unlock the full potential of their inventory data and drive sustainable profitability in the competitive manufacturing landscape. By embracing inventory analytics, executives can gain a competitive edge, improve operational efficiency, and achieve their profitability goals.
Using data-driven demand forecasting to optimize inventory levels
Data-driven demand forecasting plays a vital role in optimizing inventory levels for manufacturing companies. By leveraging advanced analytical techniques and historical data, executives can make more accurate predictions about customer demand, allowing them to optimize their inventory levels.
This section explores how data-driven demand forecasting enables executives to achieve optimal inventory levels and maximize profitability.
Data-driven demand forecasting utilizes various data sources, including sales data, market trends, customer behavior, and external factors like promotions or seasonality. By analyzing this data, executives can identify demand patterns, trends, and seasonality, enabling them to make more accurate predictions about future demand.
Optimizing inventory levels involves finding the right balance between holding enough stock to meet customer demand and minimizing excess inventory. With data-driven demand forecasting, executives can forecast demand with greater accuracy, reducing the risk of stockouts or overstocking.
By accurately forecasting demand, executives can:
- Reduce stockouts: Data-driven demand forecasting helps executives understand customer demand patterns, allowing them to maintain adequate inventory levels to fulfill customer orders. By avoiding stockouts, companies can prevent lost sales, maintain customer satisfaction, and protect their reputation.
- Minimize excess inventory: Excess inventory ties up working capital and incurs additional costs such as storage, maintenance, and obsolescence. By accurately predicting demand, executives can avoid overstocking and reduce the carrying costs associated with excess inventory.
- Optimize production and procurement: Accurate demand forecasting enables executives to align production and procurement activities with anticipated demand. By understanding future demand trends, executives can adjust production schedules, optimize resource allocation, and streamline procurement processes. This minimizes wastage, improves production efficiency, and reduces inventory holding costs.
- Improve cash flow: Optimizing inventory levels through data-driven demand forecasting improves cash flow by reducing the amount of capital tied up in inventory. This provides companies with more financial flexibility to invest in other areas of the business or respond to market opportunities.
By leveraging data-driven demand forecasting, executives can make informed decisions about inventory management, reducing stockouts, minimizing excess inventory, and ultimately optimizing profitability. The ability to accurately predict and meet customer demand leads to improved customer satisfaction, increased sales, and enhanced overall financial performance.
Applying advanced analytics techniques to identify optimal reorder points and safety stock levels
Applying advanced analytics techniques to identify optimal reorder points and safety stock levels is a crucial aspect of inventory management for manufacturing companies. By leveraging these techniques, executives can make data-driven decisions to ensure the right balance between inventory availability and cost efficiency.
This section explores how advanced analytics enables executives to determine the optimal reorder points and safety stock levels for efficient inventory management.
- Reorder Points: The reorder point is the inventory level at which a new order should be placed to replenish stock. Advanced analytics techniques can help executives calculate the reorder point by considering factors such as lead time, demand variability, and desired service levels. By analyzing historical demand patterns and lead time variability, executives can determine the appropriate reorder point that minimizes the risk of stockouts while avoiding excessive inventory carrying costs.
- Safety Stock Levels: Safety stock acts as a buffer to protect against unexpected demand fluctuations or supply chain disruptions. Advanced analytics techniques can help executives determine the optimal safety stock levels by considering factors such as demand volatility, lead time variability, and desired service levels.
By analyzing historical demand data, seasonality, and supplier performance, executives can quantify the appropriate safety stock levels to ensure a high level of customer service while minimizing excess inventory.
Applying advanced analytics techniques to identify optimal reorder points and safety stock levels offers several benefits:
- Improved Customer Service: By maintaining optimal safety stock levels, manufacturing companies can ensure a higher level of product availability, reducing the risk of stockouts and enhancing customer satisfaction. Customers can rely on consistent product availability, leading to increased loyalty and positive brand perception.
- Cost Efficiency: Optimizing reorder points and safety stock levels through advanced analytics helps minimize excess inventory holding costs. By avoiding overstocking, companies can reduce warehousing expenses, inventory obsolescence risks, and associated carrying costs, contributing to improved cost efficiency and profitability.
- Supply Chain Resilience: Determining optimal reorder points and safety stock levels helps mitigate supply chain disruptions. By considering lead time variability and potential supplier issues in the analysis, executives can enhance supply chain resilience, ensuring continuity of operations and minimizing the impact of unforeseen disruptions.
- Data-Driven Decision-Making: Leveraging advanced analytics techniques enables executives to make informed, data-driven decisions. By analyzing historical data, demand patterns, and supply chain performance, executives can optimize inventory management strategies, reduce guesswork, and improve overall decision-making accuracy.
In summary, applying advanced analytics techniques to identify optimal reorder points and safety stock levels empowers executives to strike the right balance between inventory availability and cost efficiency. By leveraging data-driven insights, manufacturing companies can enhance customer service, improve supply chain resilience, and optimize profitability through efficient inventory management practices
Utilizing predictive analytics to anticipate demand fluctuations and adjust production accordingly
Utilizing predictive analytics to anticipate demand fluctuations and adjust production accordingly is a strategic approach that empowers manufacturing companies to optimize their operations and meet customer demands efficiently. This section explores how predictive analytics enables executives to forecast demand, identify patterns, and make informed decisions to adjust production proactively.
Predictive analytics leverages historical data, market trends, customer behavior, and other relevant variables to forecast future demand accurately. By applying advanced statistical models and machine learning algorithms, executives can uncover patterns, seasonality, and trends that help anticipate demand fluctuations.
Here's how predictive analytics supports production adjustment based on demand anticipation:
- Accurate Demand Forecasting: Predictive analytics enables executives to generate accurate demand forecasts by analyzing historical data and identifying patterns and trends. By understanding the drivers of demand, such as seasonal variations or promotional events, executives can anticipate demand fluctuations and adjust production plans accordingly.
- Real-Time Visibility: Predictive analytics provides real-time visibility into demand patterns, allowing executives to detect shifts in customer behavior, market trends, or external factors that influence demand.
- Optimal Production Planning: By using predictive analytics, executives can optimize production planning based on forecasted demand. They can adjust production schedules, allocate resources, and coordinate with suppliers to ensure timely delivery of materials.
- Supply Chain Optimization: Predictive analytics enables executives to optimize their supply chain by anticipating demand fluctuations and adjusting procurement, logistics, and distribution processes accordingly.
- Cost Efficiency: Anticipating demand fluctuations through predictive analytics helps companies optimize their production processes and inventory levels. By aligning production with anticipated demand, manufacturing companies can reduce wastage, lower inventory carrying costs, and minimize the need for expedited or rush orders.
- Enhanced Customer Satisfaction: By adjusting production based on anticipated demand, manufacturing companies can improve customer satisfaction by ensuring timely delivery of products.
This data-driven approach empowers executives to make proactive decisions that align with anticipated market demands and gain a competitive advantage in the industry.
The Integration of Inventory Analytics with Supply Chain Management
The integration of inventory analytics with supply chain management is a strategic approach that enables manufacturing companies to enhance operational efficiency, reduce costs, and improve overall supply chain performance. This section explores how the integration of inventory analytics with supply chain management can drive significant benefits and create a competitive advantage for businesses.
By aligning inventory analytics with supply chain management strategies, manufacturing companies can achieve greater visibility, agility, and resilience, ultimately maximizing profitability and delivering value to customers.
Exploring the connection between inventory analytics and supply chain optimization
Inventory analytics and supply chain optimization are closely interconnected, working in tandem to improve operational efficiency and drive profitability for manufacturing companies.
This section explores the connection between inventory analytics and supply chain optimization, highlighting how leveraging inventory analytics can enhance supply chain performance.
- Demand Forecasting: Inventory analytics provides valuable insights into demand patterns, customer behavior, and market trends. Accurate demand forecasting enables executives to align their supply chain activities with anticipated demand, minimizing stockouts, reducing excess inventory, and optimizing production and procurement processes.
- Inventory Optimization: Inventory analytics plays a crucial role in optimizing inventory levels throughout the supply chain. By analyzing historical data, demand variability, lead times, and other relevant factors, executives can determine the appropriate reorder points, safety stock levels, and replenishment strategies. This ensures that inventory is efficiently managed, minimizing carrying costs while maintaining desired service levels.
- Supplier Collaboration: Inventory analytics facilitates better collaboration with suppliers. By sharing demand forecasts and inventory data with suppliers, companies can improve communication, align production and delivery schedules, and optimize the overall supply chain flow. This collaboration helps minimize lead times, reduce supply chain disruptions, and enhance responsiveness to customer demands.
- Supply Chain Visibility: Leveraging inventory analytics provides real-time visibility into inventory levels, demand trends, and supply chain performance. This visibility enables executives to proactively identify bottlenecks, optimize logistics and transportation, and enhance overall supply chain efficiency. With improved visibility, companies can make timely decisions, respond to changing market dynamics, and minimize costly inefficiencies.
- Cost Reduction: Inventory analytics integrated with supply chain optimization helps identify cost-saving opportunities. By optimizing inventory levels, reducing stockouts, and minimizing excess inventory, companies can reduce carrying costs, storage expenses, and waste. Furthermore, improved supply chain efficiency leads to lower transportation costs, reduced lead times, and improved resource allocation, contributing to overall cost reduction.
- Continuous Improvement: The integration of inventory analytics with supply chain optimization fosters a culture of continuous improvement. By leveraging data-driven insights, companies can analyze performance metrics, identify areas for improvement, and implement corrective measures. This iterative approach helps drive supply chain optimization initiatives and enhances overall operational effectiveness.
The connection between inventory analytics and supply chain optimization is symbiotic. Inventory analytics provides the necessary insights and data-driven decision-making capabilities to optimize inventory levels, improve demand forecasting, and enhance supplier collaboration. These improvements, in turn, contribute to supply chain optimization by reducing costs, improving efficiency, and increasing responsiveness.
The role of real-time data in improving supply chain visibility and responsiveness
Real-time data plays a pivotal role in improving supply chain visibility and responsiveness for manufacturing companies. By providing up-to-date and accurate information, real-time data enables executives to make informed decisions, proactively identify issues, and respond swiftly to dynamic market demands.
This section explores the role of real-time data in enhancing supply chain visibility and responsiveness.
Enhanced Visibility: Real-time data provides executives with a comprehensive and current view of their supply chain. By integrating data from various sources such as sales transactions, inventory levels, production schedules, and logistics, executives gain real-time visibility into every stage of the supply chain. This visibility allows them to track inventory, monitor order status, identify potential bottlenecks, and assess overall supply chain performance.
Demand and Supply Alignment: Real-time data enables executives to align demand and supply effectively. By continuously monitoring customer demand, inventory levels, and production capacity, executives can identify demand fluctuations, anticipate potential supply shortages, and adjust production and procurement activities accordingly. This agility in decision-making ensures that customer demands are met while minimizing stockouts and excess inventory.
Proactive Issue Identification: Real-time data allows for the early identification of issues within the supply chain. By monitoring key performance indicators (KPIs) and analyzing real-time data, executives can quickly detect deviations from expected performance levels. This proactive approach enables them to identify potential bottlenecks, address supply chain disruptions, and mitigate risks before they escalate, thereby minimizing the impact on customer service and overall operations.
Rapid Decision-Making: With access to real-time data, executives can make rapid and informed decisions. Real-time data analytics tools and dashboards provide actionable insights, enabling executives to analyze trends, assess performance, and identify improvement opportunities. This enables them to make timely decisions on inventory replenishment, production adjustments, and supply chain optimization, ensuring efficient operations and meeting customer expectations.
Collaboration and Communication: Real-time data facilitates effective collaboration and communication within the supply chain. By sharing real-time data with suppliers, logistics partners, and other stakeholders, executives can enhance coordination, improve visibility across the supply chain network, and foster collaboration in addressing supply chain challenges. Real-time data enables stakeholders to have a shared understanding of the current situation, enabling quicker responses and more efficient decision-making.
Continuous Improvement: Real-time data supports a culture of continuous improvement within the supply chain. By analyzing real-time data, executives can identify areas for optimization, measure performance against predefined KPIs, and implement process improvements. This iterative approach drives continuous improvement initiatives, enhances supply chain responsiveness, and ensures ongoing efficiency gains.
In summary, real-time data plays a vital role in improving supply chain visibility and responsiveness for manufacturing companies. By providing up-to-date insights, executives can align demand and supply, proactively address issues, make informed decisions, foster collaboration, and drive continuous improvement. Leveraging the power of real-time data empowers manufacturing companies to optimize their supply chain operations, enhance customer satisfaction, and gain a competitive advantage in the market.
Collaborative planning and forecasting using inventory analytics to enhance supplier relationships
Collaborative planning and forecasting using inventory analytics can significantly enhance supplier relationships for manufacturing companies. This approach promotes open communication, data sharing, and joint decision-making between companies and their suppliers.
By leveraging inventory analytics in the collaborative planning and forecasting process, executives can foster stronger partnerships and achieve mutual benefits. This section explores how collaborative planning and forecasting using inventory analytics can enhance supplier relationships.
Data Sharing and Transparency
Collaborative planning and forecasting involve sharing relevant data and insights with suppliers. By utilizing inventory analytics, companies can provide suppliers with real-time visibility into demand patterns, inventory levels, and production plans.
This transparency allows suppliers to align their operations, adjust their manufacturing schedules, and optimize their own inventory levels accordingly. The shared data fosters trust, facilitates more accurate forecasting, and enables both parties to make informed decisions based on a comprehensive view of the supply chain.
Improved Forecast Accuracy: Inventory analytics helps enhance the accuracy of demand forecasting by considering various factors such as historical sales data, market trends, and customer behavior. Collaborating with suppliers and involving them in the forecasting process allows for their input, experience, and knowledge of the market.
By combining their insights with inventory analytics, more accurate and reliable demand forecasts can be achieved. This leads to better planning, reduced lead times, minimized stockouts, and improved overall supply chain performance.
Demand-Supply Balancing: Collaborative planning and forecasting using inventory analytics enables companies and suppliers to proactively balance demand and supply. By jointly analyzing demand trends, seasonality, and market dynamics, both parties can adjust their production schedules, raw material procurement, and inventory replenishment plans accordingly.
This collaboration helps to optimize the entire supply chain, improve responsiveness, and reduce the risk of excess inventory or stockouts.
Risk Mitigation: By collaborating with suppliers and leveraging inventory analytics, companies can mitigate supply chain risks. Through data-driven insights, executives can identify potential risks such as supply disruptions, changes in customer preferences, or market fluctuations.
Collaborative planning and forecasting allow for proactive risk management, ensuring that suppliers are aware of potential challenges and can work together with companies to develop contingency plans, alternative sourcing strategies, or production adjustments.
Efficient Resource Allocation: Collaborative planning and forecasting using inventory analytics enable better resource allocation across the supply chain. By sharing demand forecasts and inventory data with suppliers, companies and suppliers can coordinate their production and procurement activities more efficiently.
This results in optimized resource allocation, reduced lead times, improved on-time delivery, and cost savings throughout the supply chain.
Continuous Improvement and Innovation: Collaborative planning and forecasting foster a culture of continuous improvement and innovation. By involving suppliers in the decision-making process and sharing insights from inventory analytics, companies and suppliers can collectively identify areas for improvement, develop innovative solutions, and implement best practices.
This collaborative approach drives supply chain innovation, strengthens relationships, and enhances the overall competitiveness of both parties.
The integration of inventory analytics in collaborative planning and forecasting strengthens supplier relationships, fosters collaboration, and ultimately leads to a more responsive and efficient supply chain.
Overcoming Challenges in Implementing Inventory Analytics
While the benefits of inventory analytics are significant, the successful implementation requires careful planning, technological infrastructure, and organizational alignment. From data quality and integration issues to resistance to change and resource constraints, manufacturing companies must address these challenges to unlock the full potential of inventory analytics.
By understanding the obstacles that may arise, executives can develop effective strategies and solutions to overcome them, ensuring a smooth and successful implementation process.
This section explores the key challenges faced in implementing inventory analytics and offers practical guidance on how to navigate these hurdles to maximize the value of data-driven inventory management.
Identifying potential obstacles and resistance to adopting inventory analytics
Implementing inventory analytics in manufacturing companies may encounter various obstacles and resistance from different stakeholders. This section highlights some potential obstacles and resistance that organizations may face when adopting inventory analytics:
Data Quality and Integration: One of the significant challenges is ensuring data quality and integrating data from various sources. Inaccurate or incomplete data can undermine the effectiveness of inventory analytics. It requires organizations to establish data governance practices, invest in data cleansing and validation, and integrate data from disparate systems to create a comprehensive and reliable data foundation.
Technology Infrastructure: Implementing inventory analytics often necessitates robust technological infrastructure and advanced analytics capabilities. Organizations may encounter challenges related to the availability of suitable tools, data storage capacity, and computational resources. Upgrading or investing in new technologies may be required to support the analytics requirements, which can pose financial and technical challenges.
Organizational Culture and Change Management: Resistance to change is a common hurdle when introducing inventory analytics. Employees may be accustomed to traditional inventory management practices and may be hesitant to adopt new analytical approaches. Overcoming resistance requires effective change management strategies, clear communication of benefits, and training programs to help employees embrace and utilize inventory analytics.
Skill Set and Talent Gap: Leveraging inventory analytics requires skilled professionals who possess expertise in data analytics, statistics, and inventory management. Organizations may face challenges in recruiting or upskilling employees to develop the necessary analytical capabilities.
Bridging the talent gap often involves training programs, hiring specialized personnel, or partnering with external experts to support the implementation and utilization of inventory analytics.
Resource Constraints: Implementing inventory analytics can require significant investments in technology, personnel, and infrastructure. Organizations with limited resources may face challenges in allocating sufficient budgets and resources for implementation. It is crucial to conduct a cost-benefit analysis, prioritize investments, and seek potential cost-saving opportunities to optimize resource allocation.
Resistance from Stakeholders: Resistance to change can also stem from stakeholders, including executives, managers, and even suppliers. Some may question the value and benefits of inventory analytics or feel threatened by potential changes to existing processes.
Engaging stakeholders early on, providing clear explanations of the advantages, and involving them in the decision-making process can help alleviate resistance and gain their support.
Integration with Existing Systems: Integrating inventory analytics with existing systems, such as enterprise resource planning (ERP) software or supply chain management platforms, can be challenging. Ensuring seamless integration and data flow between different systems requires careful planning, coordination with IT teams, and possibly customization or integration efforts.
By proactively identifying these potential obstacles and addressing them through proper planning, communication, and resource allocation, organizations can overcome resistance and ensure a successful implementation of inventory analytics.
This enables them to harness the power of data-driven insights to optimize inventory management, drive profitability, and gain a competitive advantage in the manufacturing industry.
Strategies for addressing data quality, technology integration, and organizational change management
Addressing data quality, technology integration, and organizational change management are crucial for the successful implementation of inventory analytics. Here are some strategies for overcoming these challenges:
1. Data Quality
- Establish Data Governance: Implement robust data governance practices to ensure data accuracy, consistency, and completeness. Define data ownership, data quality standards, and data validation processes.
- Data Cleansing and Validation: Invest in data cleansing tools and techniques to identify and rectify errors, duplicates, and inconsistencies in the data. Regularly validate data quality to maintain accuracy and reliability.
- Standardize Data Definitions: Define clear and consistent data definitions across the organization to ensure uniformity and avoid ambiguity in data interpretation.
2. Technology Integration
- Assess Existing Infrastructure: Conduct a thorough assessment of the existing technology infrastructure to identify gaps and requirements for integrating inventory analytics. Determine if any upgrades or new systems are needed.
- Scalable and Flexible Solutions: Select inventory analytics tools and technologies that are scalable and can integrate seamlessly with existing systems, such as ERP or supply chain management platforms. Ensure compatibility and ease of data exchange.
- Collaboration with IT Teams: Work closely with the IT department to ensure smooth integration of inventory analytics solutions with existing systems. Involve IT teams in the planning and implementation process to address technical challenges effectively.
3. Organizational Change Management
- Executive Support and Sponsorship: Secure executive support and sponsorship for the implementation of inventory analytics. Leaders should communicate the strategic importance and benefits of inventory analytics to gain buy-in from employees at all levels.
- Training and Skill Development: Provide training programs and resources to equip employees with the necessary skills to effectively use inventory analytics tools. This helps in overcoming resistance and building a data-driven culture within the organization.
- Change Communication: Develop a clear and compelling communication plan to inform employees about the objectives, benefits, and progress of the inventory analytics initiative. Address concerns, provide regular updates, and emphasize the positive impact on their work and the organization.
- Pilot Projects and Quick Wins: Start with pilot projects to demonstrate the value of inventory analytics in specific areas. Identify quick wins that showcase tangible benefits, which can help build confidence and enthusiasm among employees.
By implementing these strategies, organizations can address data quality issues, integrate technology effectively, and manage organizational change during the implementation of inventory analytics.
These efforts contribute to the successful adoption of inventory analytics, enabling organizations to make data-driven decisions, optimize inventory management, and drive profitability.
Building a data-driven culture to support the effective use of inventory analytics
Building a data-driven culture is essential to support the effective use of inventory analytics in manufacturing companies. It involves fostering a mindset and practices that prioritize data-driven decision-making, encourage data literacy, and promote the use of analytics throughout the organization. Here are key strategies to build a data-driven culture:
- Leadership Commitment: Leadership plays a crucial role in setting the tone and demonstrating the importance of data-driven decision-making. Executives should actively promote and champion the use of inventory analytics, emphasizing its value in driving profitability and operational efficiency.
- Clear Communication: Clearly communicate the benefits of data-driven decision-making to employees at all levels of the organization. Explain how inventory analytics can help optimize inventory levels, enhance customer satisfaction, and improve overall business performance. Regularly share success stories and case studies to illustrate the positive impact of data-driven practices.
- Data Literacy Training: Invest in data literacy training programs to enhance employees' understanding and proficiency in working with data. Offer training on basic statistical concepts, data visualization, and data analysis techniques. This empowers employees to interpret and analyze inventory analytics insights effectively.
- Accessible Data and Tools: Provide employees with easy access to relevant data and user-friendly analytics tools. Implement self-service analytics platforms or dashboards that enable employees to explore data and generate insights independently. Ensure that the data is accurate, up-to-date, and available in a format that is easily understandable and actionable.
- Cross-Functional Collaboration: Encourage collaboration and knowledge sharing across different departments and functions. Create forums or communities of practice where employees can exchange ideas, share best practices, and collaborate on data-driven initiatives. Foster a culture of openness and collaboration, breaking down silos and encouraging cross-functional data analysis.
- Celebrate Data-Driven Successes: Recognize and celebrate instances where data-driven decision-making has led to positive outcomes. Acknowledge individuals or teams who have successfully utilized inventory analytics to improve processes, reduce costs, or enhance customer satisfaction. This helps reinforce the value of data-driven practices and encourages others to adopt similar approaches.
- Continuous Learning and Improvement: Encourage a mindset of continuous learning and improvement when it comes to data-driven practices. Encourage employees to seek feedback, learn from failures, and iterate on their analytical approaches. Foster a culture of curiosity, experimentation, and innovation in leveraging inventory analytics.
By implementing these strategies, manufacturing companies can cultivate a data-driven culture that supports the effective use of inventory analytics. This culture empowers employees to make informed decisions, drives continuous improvement, and ultimately enhances the organization's ability to optimize inventory management and drive profitability.
Best Practices and Recommendations for Executives
In the ever-evolving landscape of manufacturing, executives are constantly seeking ways to optimize profitability and stay ahead of the competition. This section provides a comprehensive overview of best practices and recommendations for executives to leverage the power of inventory analytics effectively. From understanding the challenges in inventory management to implementing data-driven strategies, these recommendations equip executives with actionable insights to drive profitability, streamline operations, and enhance customer satisfaction.
This section serves as a guide, offering practical recommendations and proven strategies to help executives navigate the complexities of implementing and utilizing inventory analytics successfully.
Key considerations for selecting inventory analytics solutions
Selecting the right inventory analytics solution is crucial for manufacturing companies aiming to optimize profitability. Here are key considerations to keep in mind when evaluating and choosing inventory analytics solutions:
- Functionality and Features: Assess the functionality and features of the inventory analytics solution. Look for features such as demand forecasting, inventory optimization, lead time analysis, and supplier performance tracking. Ensure that the solution aligns with your specific business needs and provides the necessary tools to address your inventory management challenges.
- Scalability and Flexibility: Consider the scalability and flexibility of the inventory analytics solution. Determine whether it can accommodate the growth of your business and handle increasing data volumes. Additionally, evaluate its ability to integrate with existing systems and data sources, such as ERP or supply chain management platforms.
- Data Integration and Compatibility: Ensure that the inventory analytics solution can seamlessly integrate with your data sources, including inventory data, sales data, and supply chain data. Verify if the solution supports various data formats and has the capability to integrate data from multiple sources to provide a comprehensive view of your inventory operations.
- Ease of Use and User Interface: Evaluate the user-friendliness and intuitiveness of the inventory analytics solution. A user-friendly interface and intuitive navigation can enhance user adoption and enable employees at various levels to effectively utilize the solution. Look for solutions that offer interactive dashboards, customizable reports, and easy-to-understand visualizations.
- Analytics Capabilities: Assess the analytical capabilities of the solution, such as statistical modeling, predictive analytics, and optimization algorithms. The solution should have the ability to generate accurate demand forecasts, optimize inventory levels, and provide actionable insights to support decision-making. Additionally, consider whether the solution offers real-time analytics and alerts to respond promptly to inventory-related issues.
- Vendor Reputation and Support: Research the reputation and track record of the vendor providing the inventory analytics solution. Consider factors such as customer reviews, case studies, and industry recognition. Additionally, evaluate the level of customer support and availability of training resources provided by the vendor to ensure ongoing assistance and guidance.
- Cost and Return on Investment (ROI): Evaluate the cost of implementing and maintaining the inventory analytics solution. Consider both the upfront investment and the ongoing costs, such as licensing fees and support charges. Compare the potential benefits and ROI of the solution with the associated costs to make an informed decision.
- Security and Data Privacy: Ensure that the inventory analytics solution adheres to industry-standard security protocols to protect sensitive data. Evaluate the vendor's data privacy policies, data encryption practices, and compliance with relevant regulations, such as GDPR or CCPA.
By carefully considering these key factors, manufacturing companies can select an inventory analytics solution that aligns with their specific requirements, supports their business goals, and empowers them to optimize profitability through data-driven inventory management.
Building a cross-functional team to implement and manage inventory analytics initiatives
Building a cross-functional team is essential for the successful implementation and management of inventory analytics initiatives in manufacturing companies. Here are key considerations for creating a cross-functional team:
- Define Roles and Responsibilities: Clearly define the roles and responsibilities of team members based on their expertise and areas of knowledge. Include representatives from departments such as inventory management, data analytics, IT, operations, and finance. Assign a project manager to oversee the implementation and coordination of inventory analytics initiatives.
- Diverse Skill Sets: Ensure that the cross-functional team consists of individuals with diverse skill sets and expertise. This includes data analysts, inventory experts, statisticians, IT professionals, and subject matter experts from relevant departments. Each member brings a unique perspective and contributes to different aspects of the inventory analytics project.
- Collaborative Communication: Foster a collaborative communication environment within the cross-functional team. Encourage open dialogue, active participation, and knowledge sharing among team members. Establish regular meetings, workshops, and brainstorming sessions to facilitate collaboration and alignment.
- Executive Sponsorship: Secure executive sponsorship for the cross-functional team. Executive support provides the necessary resources, authority, and visibility for the team's initiatives. Executives can also help remove any organizational barriers and ensure the team's recommendations are implemented effectively.
- Data Governance and Management: Include team members who specialize in data governance and management. They can ensure data integrity, quality, and security throughout the inventory analytics process. Establish data governance practices, including data standards, data cleansing procedures, and data validation protocols.
- Change Management Expertise: Incorporate change management experts who can address the organizational and cultural aspects of implementing inventory analytics. They can help manage resistance to change, facilitate training programs, and ensure that employees understand the benefits of data-driven inventory management.
- Continuous Learning and Improvement: Encourage a culture of continuous learning and improvement within the cross-functional team. Stay updated on industry trends, new analytics techniques, and technological advancements related to inventory analytics. Provide opportunities for team members to enhance their skills through training, workshops, and certifications.
- Stakeholder Engagement: Engage key stakeholders from various departments throughout the implementation process. Involve them in decision-making, seek their input, and address their concerns. Collaborating with stakeholders helps ensure that the inventory analytics initiatives align with the broader organizational goals and objectives.
By assembling a cross-functional team with diverse expertise and a collaborative mindset, manufacturing companies can effectively implement and manage inventory analytics initiatives. This approach promotes a holistic understanding of inventory dynamics, enhances data-driven decision-making, and maximizes the benefits of inventory analytics for the organization's profitability optimization efforts.
Continuous improvement and monitoring of inventory analytics performance
Continuous improvement and monitoring of inventory analytics performance are critical for manufacturing companies to ensure the ongoing effectiveness and relevance of their inventory analytics initiatives.
Here are key considerations for continuous improvement and monitoring:
- Establish Performance Metrics: Define relevant performance metrics that align with the goals of your inventory analytics initiatives. These metrics can include inventory turnover, stockout rates, forecast accuracy, lead time reduction, and cost savings. Clear performance metrics provide a baseline for measuring the success and impact of your inventory analytics efforts.
- Regular Performance Reviews: Conduct regular reviews of inventory analytics performance to assess the accuracy and reliability of the insights generated. Compare the actual outcomes with the predicted outcomes to identify any discrepancies and areas for improvement. Analyze performance metrics to understand trends, patterns, and potential issues that require attention.
- Root Cause Analysis: When discrepancies or issues arise, perform root cause analysis to identify the underlying factors contributing to the problem. Evaluate whether the issue stems from data quality, modeling techniques, algorithm selection, or process execution. This analysis helps pinpoint areas for improvement and guides corrective actions.
- Collaboration and Feedback: Foster a culture of collaboration and feedback within the team responsible for managing inventory analytics. Encourage team members to share insights, lessons learned, and improvement suggestions. Collaborate with stakeholders from relevant departments to gather feedback on the performance and usability of the inventory analytics initiatives.
- Continuous Training and Skill Development: Invest in ongoing training and skill development for the team members involved in inventory analytics. Stay abreast of industry best practices, new techniques, and emerging technologies related to inventory analytics. Provide opportunities for team members to enhance their knowledge and skills through workshops, conferences, and online courses.
- Technology Evaluation and Upgrades: Regularly assess the technology infrastructure supporting your inventory analytics initiatives. Stay updated on advancements in inventory analytics tools and technologies. Evaluate whether your current solutions align with your evolving needs and consider upgrading or adopting new technologies if necessary.
- Feedback from End Users: Seek feedback from end users who interact with the inventory analytics insights on a regular basis. Understand their experience, challenges, and suggestions for improvement. Incorporate user feedback to enhance the usability and effectiveness of the inventory analytics tools and outputs.
- Continuous Innovation: Encourage a culture of continuous innovation in inventory analytics. Explore new techniques, methodologies, and data sources to improve the accuracy and scope of inventory analytics. Foster a mindset of experimentation and learn from both successes and failures to drive continuous improvement.
This iterative approach ensures that the insights generated remain accurate, relevant, and valuable for optimizing inventory management, driving profitability, and enhancing operational efficiency.
Emphasizing the importance of executive leadership and support for successful implementation
Executive leadership and support play a crucial role in the successful implementation of inventory analytics initiatives in manufacturing companies. Here are the key reasons why executive leadership and support are essential:
Setting the Strategic Direction: Executives provide the vision and strategic direction for the organization. They define the goals, objectives, and priorities that guide the implementation of inventory analytics initiatives. Their leadership ensures that inventory analytics aligns with the overall business strategy and contributes to the company's profitability optimization efforts.
Allocating Resources: Executives have the authority to allocate resources, including budget, personnel, and technology, to support the implementation of inventory analytics. Their support ensures that the necessary resources are available for data acquisition, analytics tools, infrastructure, and talent. Adequate resource allocation is critical for the success and scalability of inventory analytics initiatives.
Overcoming Organizational Barriers: Implementing inventory analytics often involves overcoming organizational barriers, such as resistance to change, data silos, and departmental conflicts. Executive leadership can help break down these barriers by actively supporting and promoting the use of inventory analytics. They can address resistance, encourage collaboration, and foster a culture of data-driven decision-making.
Championing Data-Driven Decision-Making: Executives set the tone for data-driven decision-making within the organization. By emphasizing the importance of using data and analytics for inventory management, they encourage employees at all levels to adopt data-driven practices. Executives themselves can lead by example, making data-driven decisions and showcasing the positive outcomes achieved through inventory analytics.
Providing Guidance and Direction: Executives provide guidance and direction to the cross-functional team responsible for implementing and managing inventory analytics initiatives. They clarify expectations, provide strategic guidance, and ensure that the team's efforts align with the broader organizational goals. Executive involvement demonstrates the significance of inventory analytics and keeps the initiatives on track.
Influencing Organizational Culture: Executives have the power to shape the organizational culture to support the effective use of inventory analytics. By prioritizing data-driven decision-making, promoting collaboration, and recognizing the value of analytics, they can foster a culture that embraces inventory analytics as a strategic tool for profitability optimization. This cultural shift enhances the adoption and acceptance of inventory analytics across the organization.
Monitoring Performance and Results: Executives are responsible for monitoring the performance and results of inventory analytics initiatives. They review key performance metrics, assess the impact on profitability, and track the progress towards achieving the desired outcomes. Their oversight ensures that the initiatives stay aligned with business objectives and yield tangible results.
By emphasizing the importance of executive leadership and support, manufacturing companies can create an environment conducive to successful implementation of inventory analytics initiatives. Executive buy-in, support, and involvement set the foundation for a data-driven culture, resource allocation, and organizational alignment, ultimately driving the successful adoption and utilization of inventory analytics for profitability optimization.
Future trends and developments in inventory analytics for manufacturing companies
Inventory analytics is an evolving field, and several future trends and developments are expected to shape its application in manufacturing companies. Here are some key trends to watch for:
- Artificial Intelligence and Machine Learning: The integration of artificial intelligence (AI) and machine learning (ML) techniques will continue to advance inventory analytics capabilities. AI-powered algorithms can analyze vast amounts of data, identify patterns, and generate accurate demand forecasts and optimal inventory levels. ML models can learn from historical data to improve forecast accuracy and optimize inventory management decisions.
- Internet of Things (IoT) Integration: The proliferation of IoT devices will enable real-time tracking and monitoring of inventory. By integrating IoT data with inventory analytics systems, manufacturers can gain valuable insights into inventory levels, location, condition, and movement. This enhanced visibility enables proactive inventory management, reduces stockouts, and streamlines supply chain operations.
- Predictive Analytics for Supply Chain Risk Management: Predictive analytics will play a crucial role in mitigating supply chain risks. By leveraging historical data, external data sources, and machine learning algorithms, manufacturers can anticipate and proactively address potential disruptions, such as supplier delays, demand fluctuations, and natural disasters. This helps optimize inventory levels, improve customer service, and minimize supply chain disruptions.
- Prescriptive Analytics for Decision Optimization: Prescriptive analytics goes beyond descriptive and predictive analytics by recommending optimal courses of action. By utilizing advanced optimization algorithms, manufacturers can optimize inventory allocation, production planning, and order fulfillment. Prescriptive analytics considers multiple variables, constraints, and business objectives to generate actionable recommendations that maximize profitability.
- Integration of Big Data and Cloud Computing: The integration of big data and cloud computing technologies will enable manufacturers to process and analyze large volumes of data efficiently. Cloud-based inventory analytics solutions offer scalability, flexibility, and real-time access to data. Manufacturers can leverage big data analytics techniques to uncover hidden insights, identify trends, and make informed decisions to optimize inventory management.
- Enhanced Visualization and Reporting: User-friendly dashboards, interactive visualizations, and intuitive reporting capabilities will become more prevalent in inventory analytics solutions. These features enable executives and stakeholders to easily interpret and communicate complex inventory data, key performance indicators, and actionable insights. Advanced visualization tools facilitate data-driven decision-making and promote cross-functional collaboration.
- Integration with Supply Chain Collaboration Platforms: Integration between inventory analytics systems and supply chain collaboration platforms will enhance visibility and collaboration across the supply chain. Real-time data sharing, collaborative planning, and synchronized demand forecasting enable manufacturers and their partners to optimize inventory levels, improve lead times, and enhance overall supply chain performance.
- Ethical and Responsible Inventory Analytics: With increased focus on sustainability and ethical business practices, manufacturers will incorporate ethical considerations into inventory analytics. This includes optimizing inventory to minimize waste, reducing environmental impact, and ensuring ethical sourcing practices. Responsible inventory analytics aims to balance profitability with social and environmental responsibility.
As technology advances and businesses embrace the power of data-driven decision-making, these future trends in inventory analytics will shape the way manufacturing companies optimize inventory management, drive profitability, and achieve competitive advantage in the evolving landscape of the industry.
Conclusion
In conclusion, inventory analytics has emerged as a powerful tool for executives in manufacturing companies seeking to optimize profitability. By harnessing the power of data-driven insights, executives can gain a deeper understanding of inventory dynamics, demand patterns, and supply chain performance. This understanding enables informed decision-making, streamlined operations, and maximized profitability.
Throughout this article, we explored the pivotal role of inventory analytics in driving manufacturing profitability. We discussed how inventory analytics provides insights into inventory levels, demand forecasting, and lead times, allowing executives to make data-driven decisions and optimize their inventory management practices. We also highlighted the benefits of leveraging inventory analytics, including improved operational efficiency, reduced costs, enhanced customer satisfaction, and increased revenue.
Furthermore, we delved into the challenges faced in inventory management, such as overstocking, stockouts, and obsolete inventory, and the detrimental impact these challenges can have on profitability and customer satisfaction. However, with the application of inventory analytics, executives can mitigate these challenges and optimize their inventory performance.
We also explored the integration of inventory analytics with supply chain management, emphasizing the role of real-time data, collaborative planning, and forecasting in enhancing supply chain visibility and responsiveness. Additionally, we discussed strategies for overcoming obstacles in implementing inventory analytics, such as data quality, technology integration, and organizational change management, emphasizing the importance of building a data-driven culture.
Lastly, we provided recommendations and best practices for executives, including key considerations for selecting inventory analytics solutions, building a cross-functional team, and continuous improvement and monitoring of inventory analytics performance. We also highlighted future trends and developments in inventory analytics, such as AI and machine learning, IoT integration, and predictive and prescriptive analytics.
How can Deskera Help You?
Deskera ERP and MRP systems help you to keep your business units organized. The system's primary functions are as follows:
- Keep track of your raw materials and final items inventories
- Control production schedules and routings
- Keep a bill of materials
- Produce thorough reports
- Make your own dashboards
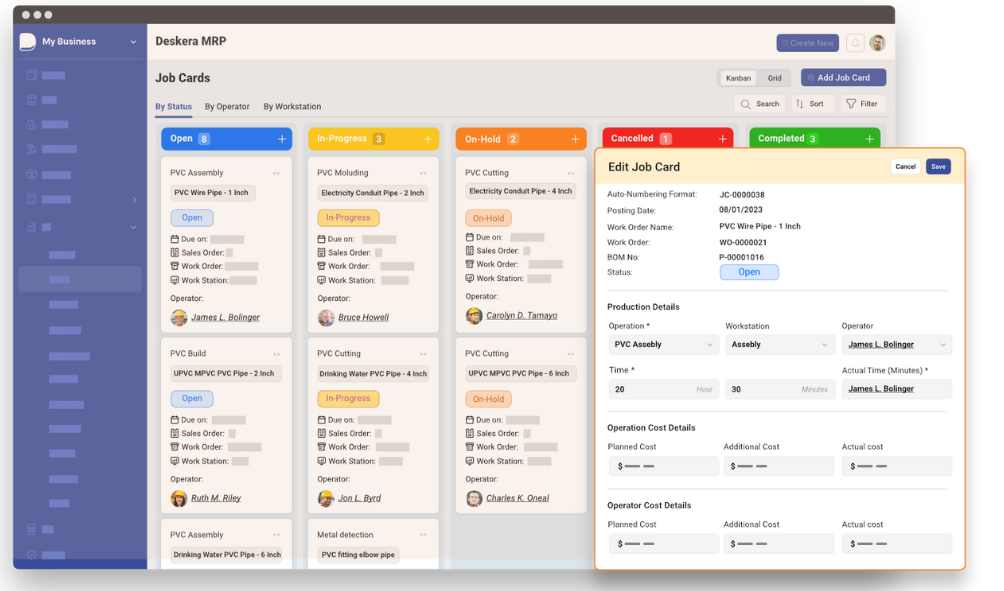
Deskera's integrated financial planning tools enable investors to better plan and track their investments. It can assist investors in making faster and more accurate decisions.
Deskera Books allows you to better manage your accounts and finances. Maintain good accounting practices by automating tasks like billing, invoicing, and payment processing.
Deskera CRM is a powerful solution that manages your sales and helps you close deals quickly. It not only enables you to perform critical tasks like lead generation via email, but it also gives you a comprehensive view of your sales funnel.
Deskera People is a straightforward tool for centralizing your human resource management functions.
Key Takeaways
- Inventory analytics is a critical tool for executives in manufacturing companies seeking to optimize profitability.
- Advanced technologies and abundant data have transformed inventory management, making inventory analytics a transformative approach.
- Inventory analytics provides insights into inventory levels, demand forecasting, and lead times, enabling informed decision-making.
- By leveraging inventory analytics, executives can streamline operations, make data-driven decisions, and maximize profitability.
- Overstocking, stockouts, and obsolete inventory pose challenges in inventory management that can negatively impact profitability and customer satisfaction.
- Implementing inventory analytics helps mitigate these challenges by optimizing inventory levels, reducing costs, and improving customer satisfaction.
- Real-time data plays a crucial role in enhancing supply chain visibility and responsiveness, enabling proactive decision-making.
- Collaborative planning and forecasting using inventory analytics strengthens supplier relationships and improves supply chain coordination.
- Addressing potential obstacles in implementing inventory analytics requires strategies for data quality, technology integration, and organizational change management.
- Building a data-driven culture and continuous improvement are key to the effective use of inventory analytics for profitability optimization.
Related Articles
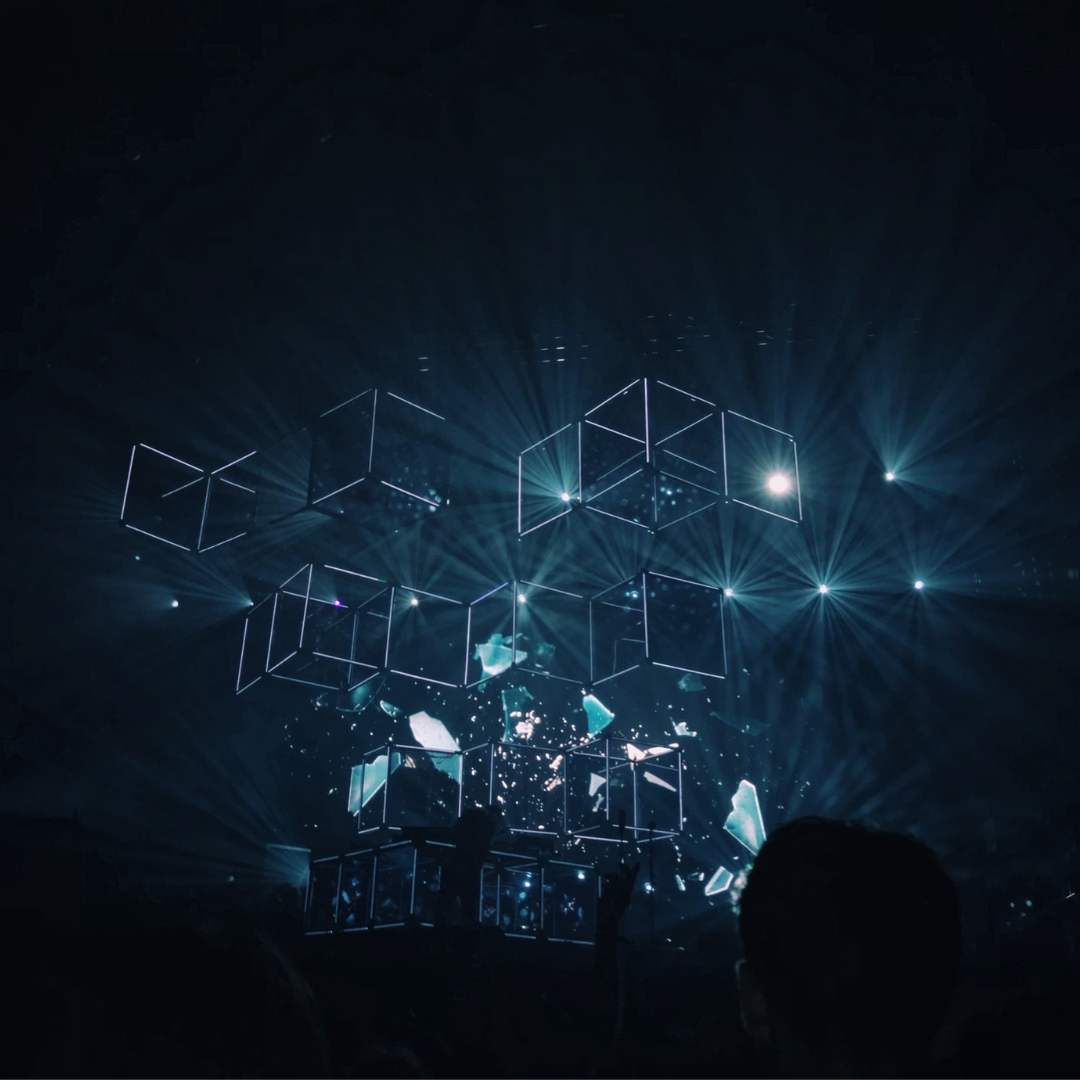
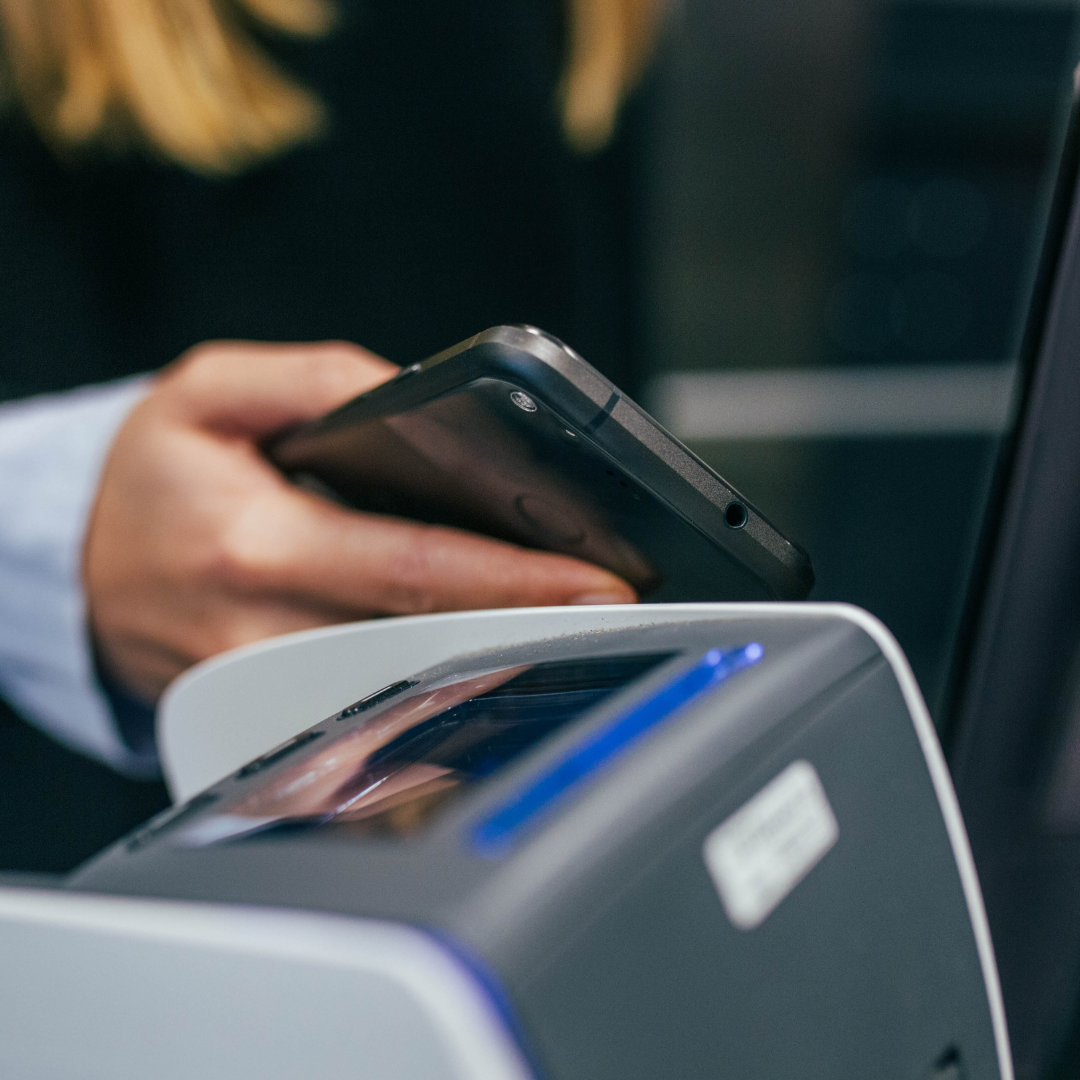
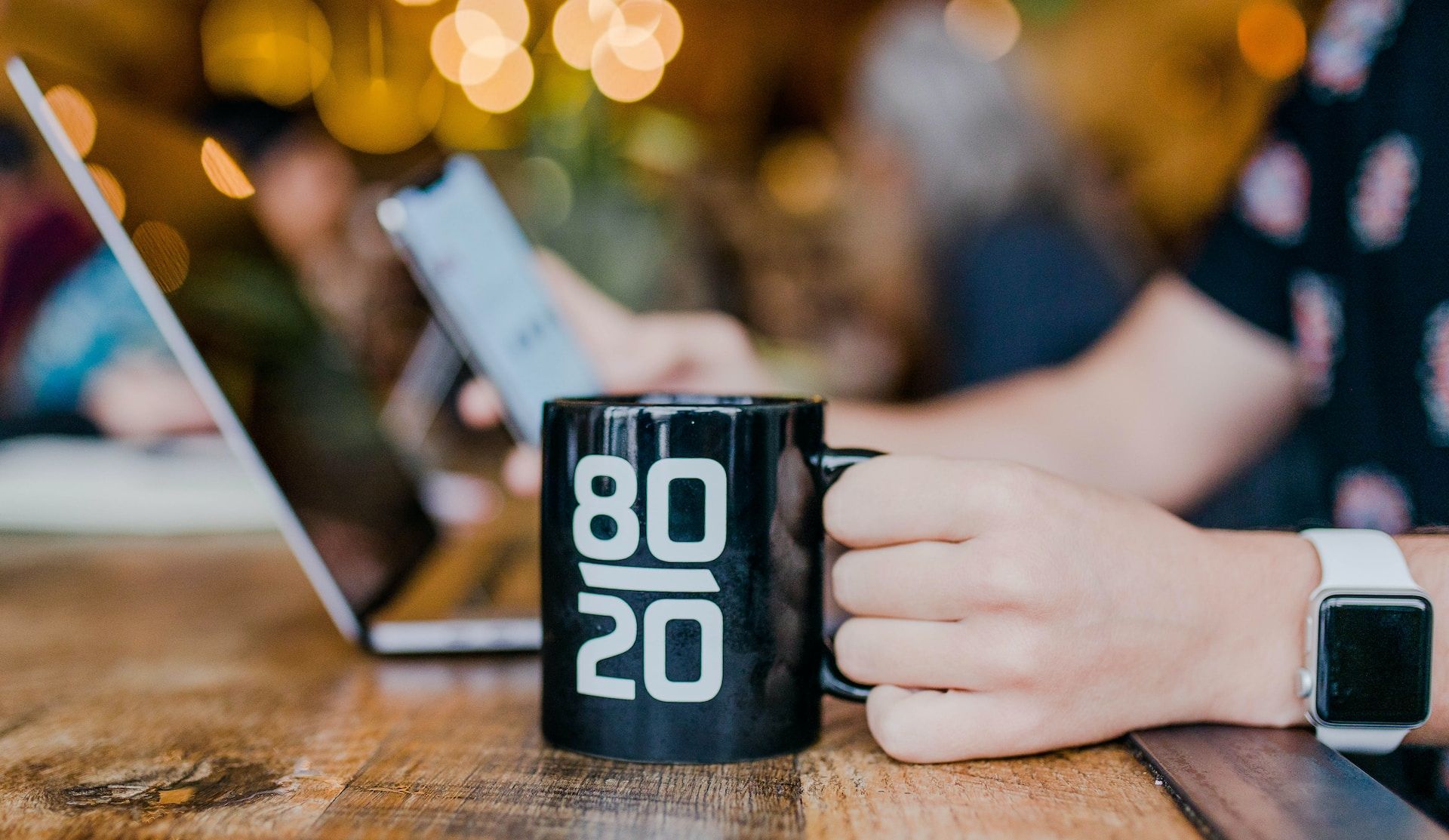
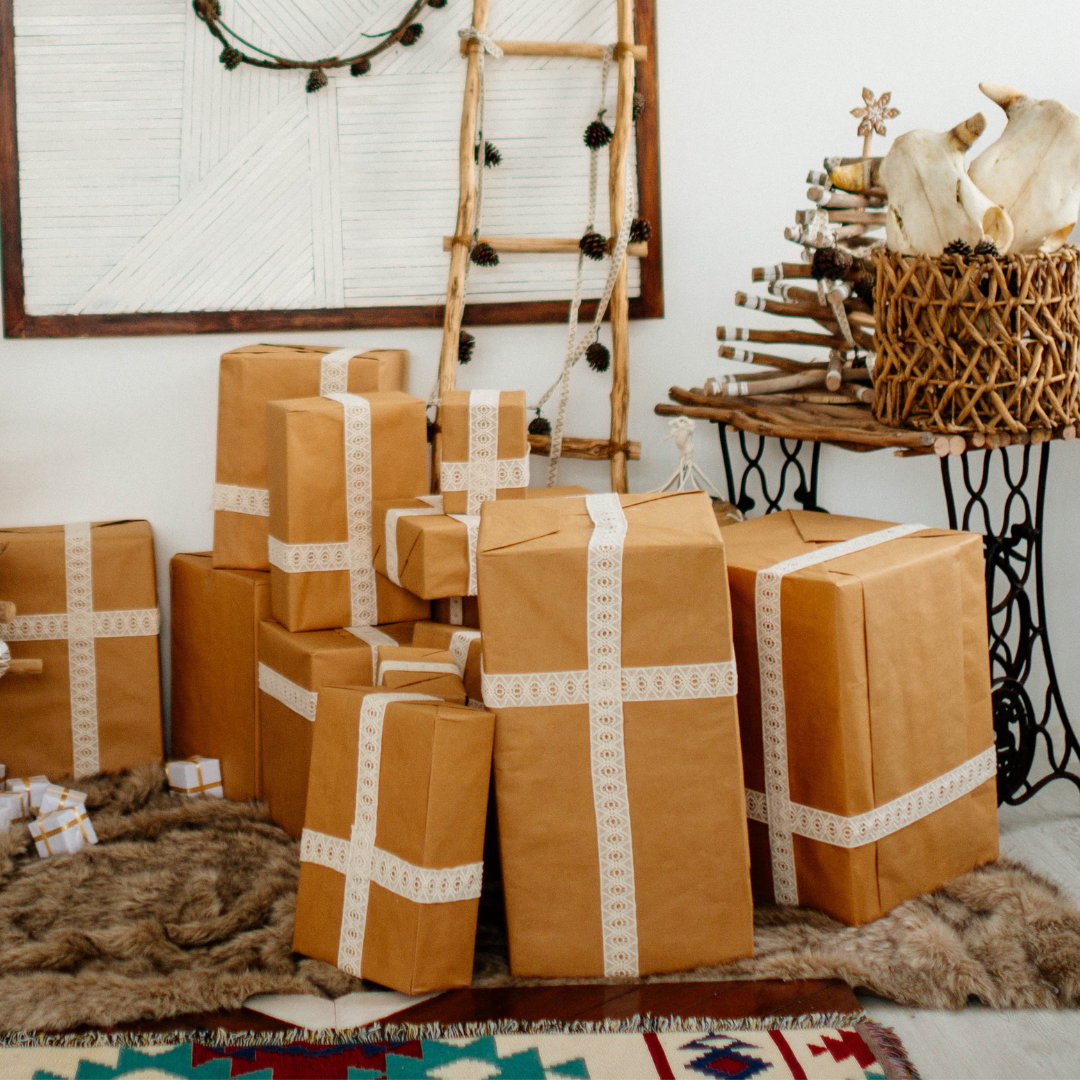