In 2021, US retailers faced $82 billion in lost sales due to empty shelves and out-of-stock items.
Are you struggling with efficient stock management? Do you want to be able to accurately calculate the level of stock you should have in your warehouse, and which would prevent stock-outs even in the face of new trends, fluctuating demands, delays in stock delivery, and other such variables?
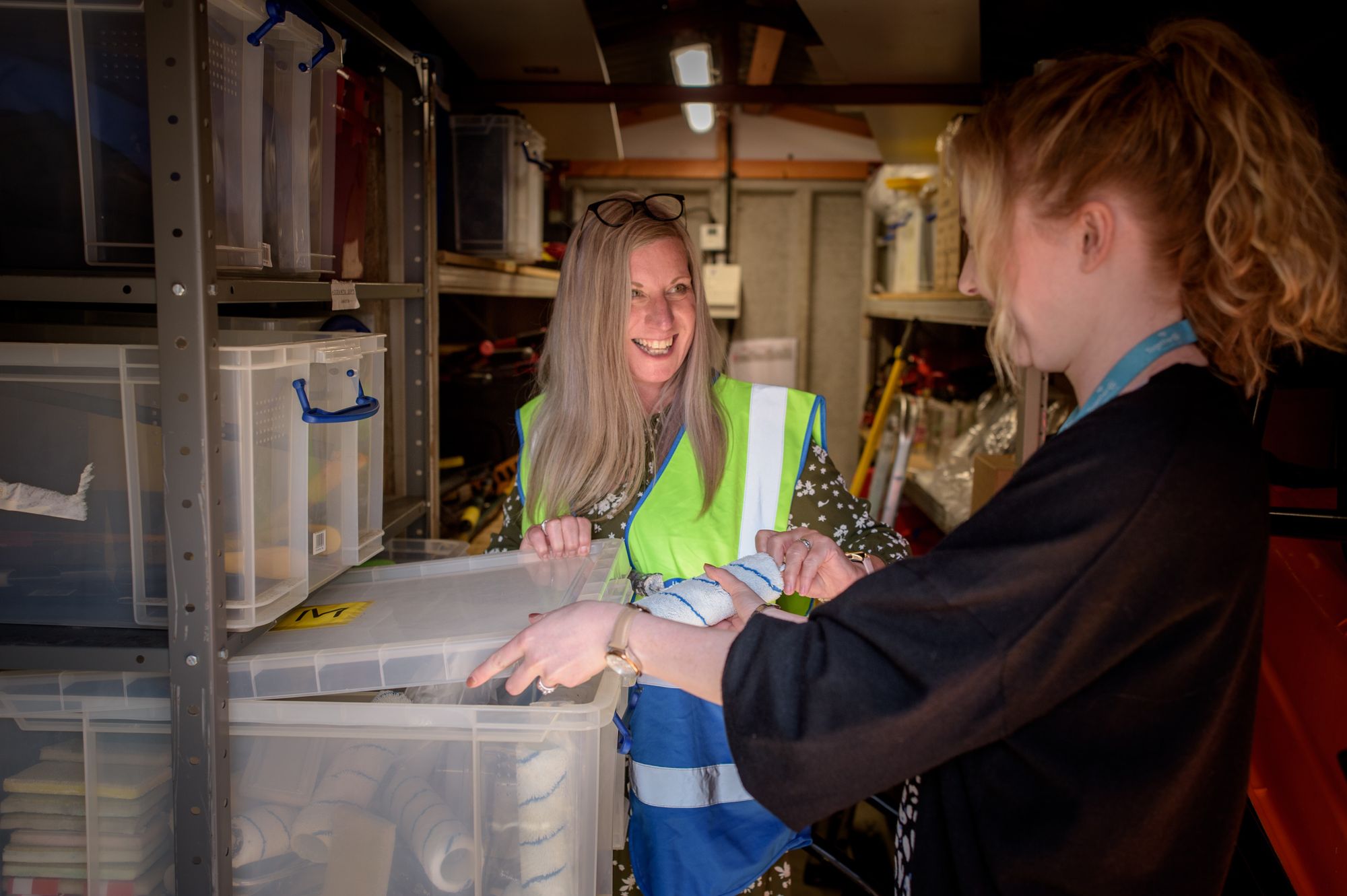
If you have answered yes to the above questions, then this article is the perfect guide for you. Your answer to these questions is safety stock, which is intended to work in conjunction with the reorder point formula.
Safety stock is an extra and additional quantity of a product that is stored in the warehouse to prevent an out-of-stock situation. It serves as insurance against fluctuations in demand, the constantly changing retail landscape, and other such variables which impact which products should be stocked and how many of each must be on the shelves and in the warehouse to maximize efficiency and reduce costs.
Additionally, it will also help in preventing loss of revenue as well as customers, who, in such situations, get their items from elsewhere and often never return to the business. In fact, stock-outs also reduce the overall efficiency of supply chains.
While running low on stock is an inevitability, it should not be able to disrupt your business. Learning how to calculate safety stock and keeping adequate amounts on hand will help ensure that the supply chain runs smoothly despite temporary outages and stocking delays. This will help you improve customer retention while ensuring your net revenue is not affected.
To be able to calculate safety stock using the safety stock formula, it is vital that you understand everything about it. To help you, the topics that are covered in this article are:
- What is Safety Stock?
- Safety Stock Examples
- How can Safety Stock Improve Inventory Management?
- Why Do Businesses Need Safety Stock?
- 6 Common Safety Stock Challenges and Risks
- How to Calculate Safety Stock and 8 Safety Stock Formulas
- Safety Stock with EOQ (Economic Order Quantity)
- Role of Safety Stock in Reorder Point Calculations
- 4 Limitations of the Safety Stock Formulas
- How to Choose the Right Formula for Your Safety Stock?
- Excel Calculator for Safety Stock
- Manage and Calculate Safety Stock with MRP System
- Safety Stock FAQs
- How can Deskera Help with Safety Stock Calculations?
- Key Takeaways
- Related Articles
What is Safety Stock?
Safety stock is simply extra inventory held by a manufacturer or a retailer in case demand increases unexpectedly. It is additional stock above the desired inventory level that you would usually hold for day-to-day operations. Safety stock is also known as “buffer stock” or “backup inventory.”
The prime reason why retailers or manufacturers implement a safety stock strategy is to prevent stock-outs. Usually, stock-outs are caused by the following:
- Changes in consumer demand
- Variability in lead times for raw materials and components
- Incorrect demand or stock forecasts
- Excess demand
- Failure to place timely reorders
- Supplier delays
- Financial constraints
And so on.
For such uncertainties and more, safety stock acts as a buffer amount that helps you mitigate the risks and consequences of stock-outs. It thus allows your supply chain to proceed as usual, even after cycle stock runs out.
While planning for all the variables that can affect your stock management and target inventory level can be difficult, with a safety stock formula, it is made possible.
Once implemented, this strategy will encourage returning customers, improve customer loyalty, increase net profits, and improve business metrics and operational metrics.
Safety stock is thus an integral part of inventory management. In fact, safety stock levels can be incorporated into other inventory management tools, and formulas, such as the reorder point formula, to create a meaningful and effective inventory management system that will ensure success for your company.
Safety Stock Examples
For instance, a snow shovel manufacturer knows that demand for his products is low during the warmer months. He or she also knows that demand for his products will fluctuate significantly in the winter depending on several hard-to-predict aspects of the weather.
It is because of this reason that the inventory manager of this firm has decided to set aside a portion of each type of snow shovel that it sells (for, e.g., heavy duty for significant snow, metal shovels for ice, and more). The inventory manager does so to ensure that the company can meet demand across the board.
Another example, recently, a bicycle manufacturer was featured in a popular biking magazine and experienced a sharp increase in sales. As the manufacturer fulfills orders, inventory is exhausted faster than the average lead time, increasing the risk of a complete stock-out. Without safety stock, this company will be unable to fulfill orders once the regular inventory is gone, leading to lost sales.
How can Safety Stock Improve Inventory Management?
Safety stock provides the cushion that inventory management relies upon to be effective. In fact, accurately tracking current stock levels while considering the present and future market conditions and then accounting for supply lead times is just the starting point for ensuring effective inventory control.
To have an inventory management strategy that is profitable and productive in all situations, you would need to coordinate cycle stock and safety stock. This will ensure that the inventory levels stay in line with the demand and supply. This will make your inventory management more straightforward and consistent.
Why Do Businesses Need Safety Stock?
According to a study by IHL Group, stock-outs have resulted in $984 billion worth of lost sales worldwide. Thus, running out of stock is one of the most expensive issues for businesses across the globe.
While there are several reasons businesses should have safety stock on hand, here I will be discussing eleven of them:
Offset Demand Uncertainty
One of the primary reasons to maintain safety stock is fluctuations in demand. There are several factors that lead to spikes in demand. These are:
- Seasonal impacts
- Sudden shifts in buyer personas and customer trends
- Competitor’s departure
- Panic buying
And so on.
With safety stock, your company will get enough breathing room to replenish the stock while simultaneously also meeting this increased demand. This will help you in increasing the ratio of your operating income to operating expenses while keeping your customers satisfied.
Avoid Stockouts
One of the other benefits of resorting to keeping safety stock is that it will help your company in reducing the risk of completely running out of a certain product and prevent operations from coming to a halt while the business locates, purchases, and delivers this inventory.
Considering that this process can take days or weeks, safety stock is an invaluable bridge that will keep your business running while resolving the stock-out. This will help you keep a check on business expenses while also improving cash flow.
Minimize the Effects of Supply Disruptions
Your business is vulnerable to unexpected disruptions on the supplier side like:
- Raw material shortages
- Legislative or political measures
- Production issues
- Operational shutdowns
And so on.
These will end up having a major detrimental impact on your inventory levels. In fact, these interruptions will have far-reaching impacts on the rest of your supply chain, including:
- Delaying the completion of other product components
- Causing retail disruptions
- Derailing customer delivery schedules
With safety stock, you will be able to mitigate the impact of supplier interruptions and lead time uncertainty. Additionally, it will also help in keeping the supply chain moving until the disruption passes or the company has found a new supplier.
Reduce Administrative and Staff Hours
While safety stock will ensure that each step of your supply chain is running smoothly, it will also cut down on time spent on paperwork, communication, and warehouse duties. With safety stock, your supply chain managers will not have to frequently scramble about to find and reorder additional stock.
This will also save them from all the emails, calls, rush requests, and invoice processing that comes with it. Similarly, your warehouse staff will not have to deal unexpectedly with unloading trucks and restocking racks while their day-to-day warehouse activities get affected.
Compensate for Forecast Inaccuracies
Safety stock will help you maintain adequate inventory, which will ensure consistency, and allow you to develop more accurate forecasts across the organization. While demand forecasts are usually reliable, sudden changes can cause them to become inaccurate.
In those instances, the effects of stock disruptions compound in other forecasts, such as supply chain scheduling. When such stock disruptions cause a loss of revenue or customers as sales, these issues become especially troubling.
In fact, in these situations, even your financial forecast becomes invalid, and your financial statements and financial KPIs get affected negatively.
Limit Rushed Shipping
In situations of lack of inventory, there is not only a loss of revenue, but your business incurs other costs as well. When your business faces a lack of inventory, it is likely that it will also face increased administrative and warehouse payroll costs. Additionally, it is quite possible that your suppliers will charge you a premium for rushed delivery.
While these costs will not be a big problem if the stock-out is due to higher demand which is expected to continue, however, if you are facing a stock-out due to disruptions or other issues, then such costs incurred may not be recouped quickly, if at all.
This will lead to an increase in the cost of goods sold, with a decrease in returns on investments, a situation that can be prevented with safety stock.
Ensure Customer Satisfaction
One of the best ways of ensuring customer satisfaction and loyalty is through safety stock. This is because, with safety stock, your customers would also be able to rely on you to have what they need in stock.
This will not only make them repetitive customers but will also lead to valuable word-of-mouth advertising as well. This goodwill and positive brand image will pay off in a big way over the long term and will help your business grow.
Maintain Market Share
When you are unable to meet the demands of your customers, you might end up losing them, which will ultimately lead to you losing your market share. To prevent this from happening and mitigate the risk of stock-outs, resorting to safety stock is the best strategy.
This will play a major role in sustaining the satisfaction of your customers and reducing the risk of losing ground to competitors. This will also lead to an increase in gross profits.
Increase Efficiency
The advantage of safety stock is that it allows for more efficient operations even during supply disruptions. Due to safety stock, your:
- Suppliers aren’t rushed
- Warehouse staff isn’t overworked, and you do not have to pay overtime
- Delivery drivers stay on schedule
And you also have steady, trustworthy inventory numbers for reporting and forecasting purposes.
All of this will lead to improvement in your operational metrics and business metrics while cutting down on your operating costs. In fact, you would even be able to reduce the pressure on your working capital.
Improved Supplier and Retailer Relationships
With safety stock, you will have improved supplier and retailer relationships. This is because stock-out situations often result in urgent reorders, but most of the suppliers do not like to be rushed because it can disrupt their operations and customers. With safety stock, you would have a lesser need to put in rushed orders, and your suppliers will have a steady workload.
Similarly, if you are working with retailers, then you would be able to maintain good relationships with them as well, as you keep the items they sell in stock, irrespective of other uncertainties that could have disrupted your supply to them.
Prevention Against Price Fluctuations
Unpredicted market fluctuations can cause the cost of your goods to increase suddenly. This can be due to the following:
- The sudden scarcity of raw materials
- Increase in price of raw materials
- Unexpected demand surges in the market
- New competitors
- New government regulations and policies
And other such reasons.
Having enough safety stock during these unpredictable times and situations will help you avoid the costs of buying the stock at higher prices without sacrificing sales. This will help in maximizing your net profit ratio.
6 Common Safety Stock Challenges and Risks
While safety stock is a valuable tool to combat stock-outs, it has its own set of disadvantages and risks as well. For example, it is possible to over-optimize stock levels, which is not always the best approach.
Thus, a few factors that you and your inventory managers need to consider when developing safety stock strategies are:
Setting Safety Stock to Zero
It is a common tendency of supply chain managers to attempt to combat the costs of having too much stock on hand by setting the safety stock to zero. This practice is especially common when an unexpected spike in demand has subsided or when the demand has returned to normal levels.
While this approach does solve the issue of having too much inventory, it reignites the risk of not having a buffer to handle any future fluctuations in demand or supplier delays. These situations can prove to be more expensive than handling extra stock.
Safety Stock is Static
What needs to be kept in mind is that safety stock does not grow with your business. This means that the number of units that you have earmarked currently as safety stock may not be enough as your business expands.
Thus, to mitigate this risk, it is important that you and your inventory managers review the bottlenecks and safety stock numbers regularly and, based on the new updates, adjust the safety stock unit number accordingly.
Too Much Safety Stock
In order to avoid losing sales to stock-outs, it is necessary to carry safety stock, it also leads to a reduction in your company’s available cash. This thus means that having an excess of safety stock will lead to less room for new products or current cycle stock.
Additionally, it also leads to an increase in your business expense, as often, holding costs represent 20% or more of the inventory’s total cost. This expense is due to the additional amounts that had to be purchased and increased storage costs and staff hours.
This is detrimental to the growth and profitability of your business as it is just additional expenses without any returns.
Standard Safety Stock Formulas
Another challenge of safety stock is that the standard safety stock formulas may not work for all industries or operational strategies. This is especially true when there are numerous unknown variables.
In order to mitigate this challenge, it is important to tweak these formulas to fit your business and individual situations, so that you get reliable calculations and you are able to avail all of its benefits.
Letting Safety Stock Decline
As the average lead times go down, supply chain managers tend to be tempted to decrease the amount of safety stock. However, considering that there are several other factors that can cause inventory issues, keeping adequate safety stock should be a priority of all.
Overuse of Safety Stock
While safety stock is a good shield against stock-outs, it is not a cure for all inventory issues. This is why it is vital that your supply chain managers determine the optimal amount of safety stock for each item and find a careful balance between the risks and costs of stock-outs compared to the risks and costs of having too much stock on hand.
How to Calculate Safety Stock and 8 Safety Stock Formulas
In order to get the benefits of keeping safety stock, you will first need to know how much safety stock to keep. This is crucial because too much safety stock can lead to higher holding costs, and too little safety stock results in a loss of sales.
Thus, using a formula will help you calculate the optimal amount of safety stock for your business. There are several methods of calculating safety stock, with each method using slightly different details from the other.
However, they all require you to know your lead time - which is the time between the initiation of an order and the completion of the delivery process.
The eight safety stock formulas and methods are:
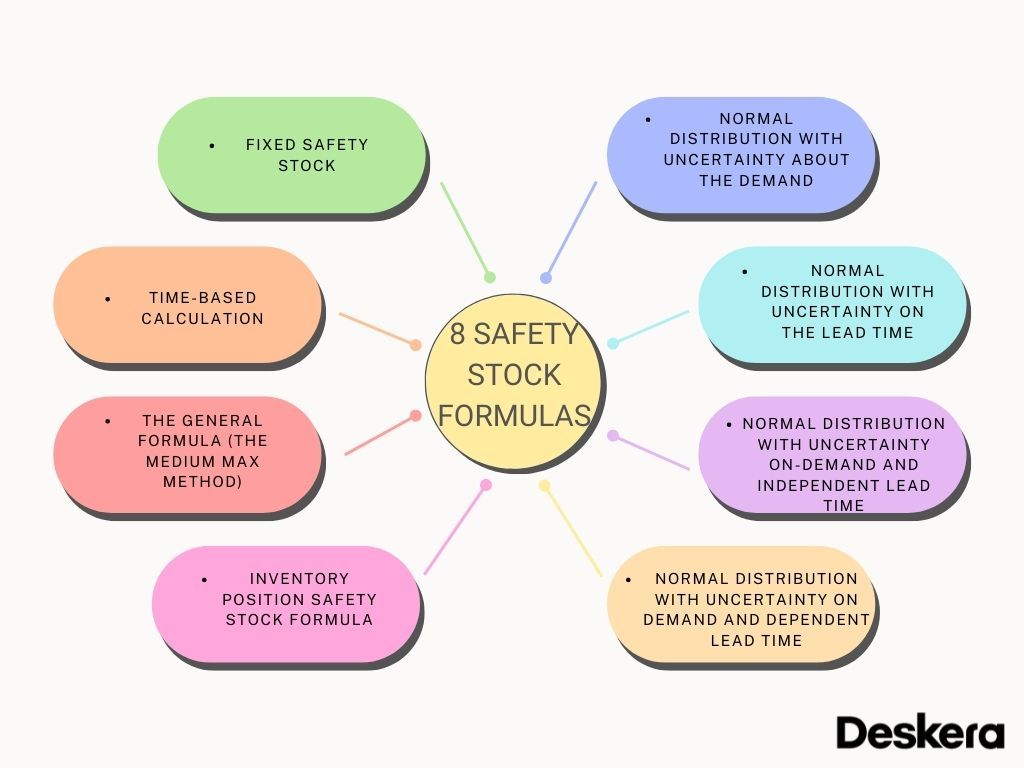
Fixed Safety Stock
This method is used by production planners. In this method, the production planners determine the amount of safety stock to keep based on the maximum daily usage for over a period of time. However, they do so without using a particular formula.
Generally, the value for fixed safety stock remains unchanged unless the production planner decides to change it. In fact, fixed safety stock levels can even be set to zero for items that you want to phase out.
However, if you are following this method, and there is a sudden increase in demand for an item with very little safety stock, then you might not be able to fulfill the orders.
Time-Based Calculation
In this method, you will calculate the safety stock levels over a particular time period based on the future forecast for the product. This method includes a combination of actual demand from sales orders and forecasted demand based on statistical methods.
However, considering that in this method, you will not be able to predict business uncertainties, using it involves a risk that you might end up carrying too much-unwanted stock if your products are moving slower than forecast or too less stock if your products are moving faster than forecasted.
The General Formula (The Medium Max Method)
This is the most simple and commonly used method to calculate the safety stock. Here, you will have to calculate the average safety stock the company needs to hold during a stock-out scenario. However, it does not consider the seasonal fluctuations of demand.
As per this method, safety stock is calculated by multiplying the maximum daily usage (which is the maximum number of units sold in a single day) with the maximum lead time (which is the longest time it has taken the vendor to deliver the stock), then subtracting the product of average daily usage (which is the average number of units sold in a day) and average lead time (which is the average taken by the vendor to deliver the stock).
Safety Stock = (Max. daily usage x Max. lead time in days) - (avg. daily usage x avg. lead time in days)
Remember, this is a useful formula for balancing out sales and lead times that are not uniform. However, it is important to remember some key principles when handling your data. One instance of the same is that you should remove ‘anomalous’ results when looking to find your average.
For example, if you were selling 100 units of Product X every day throughout 2022 except one day when you sold 12,000 units, then it would be reasonable to remove that particular day from your calculation of the daily average sales. This will help you prevent a one-off occurrence from skewing your data.
Inventory Position Safety Stock Formula
Safety stock = Inventory on hand - Backorders + Inventory currently on order
This formula will help you monitor your net inventory. The resulting figure should be higher than the reorder point to avoid running out of stock.
Normal Distribution with Uncertainty About the Demand
This method is most useful when there are fluctuations in demand while the lead times are relatively stable.
The formula is:
Safety Stock = Standard deviation of the demand x The root of the average delay
Now, to calculate the standard deviation in demand, you will first need to calculate the average demand (i.e., total monthly demand/number of months). Next, you will need to calculate the variability in demand by taking the square of each month’s difference, then the average of those squares together. The square root of the deviation is the standard deviation which represents the sales variability.
Remember, to determine the lead time variability, you should always use the same unit of measure as demand variability. This could be months, weeks, or days. To find lead time variability, you need to calculate your average lead time, then find the square root of the average squared differences.
Finally, you will use both of these figures to calculate your safety stock.
Normal Distribution with Uncertainty on the Lead Time
This method and formula should be used when only your lead time is variable.
Safety Stock = Z x Average sales x The lead time deviation
Z is the desired service level. The service level factor means deciding on the correct service level for a certain product by balancing inventory costs vs. the cost of stock out. The higher the desired service level, the more safety stock is required.
In order to calculate the desired service level into a value that you can use in the safety stock calculation, you will need to use a normal distribution chart. This will help you determine your service factor based on the service level you want to reach.
For example, if you are trying to maintain a service level of 90%, then your service factor will be 01.28. This number will serve as your service factor, or Z, in the equation.
How to calculate the lead time deviation has been discussed in the preceding method of calculating the safety stock.
Remember, if your lead time variation is small, you will tend to have a much lower safety stock. This is because you are assured that your supply will be fairly consistent. On the other hand, if your supply fluctuates dramatically, then you will require more safety stock to cover these longer lead time periods.
Normal Distribution with Uncertainty On-Demand and Independent Lead Time
For all the situations where there is a high degree of uncertainty about both demand and lead time, this method is the most effective. Lead time and demand both work independently of each other.
Considering them working independently and that there are many variations, the formula is more complex than the others being discussed here.
Safety Stock = Z x sqrt (( Average LT x (Demand standard deviation) squared + (Average Sales x Lead Time Standard Deviation) Squared)
Thus, this formula is incredibly useful when there is a great deal of uncertainty as it factors in both lead time uncertainty and sales uncertainty. If your business is operating with these unstable factors, then safety stock is especially important for you.
Note: sqrt is an abbreviation for square root
Normal Distribution with Uncertainty on Demand and Dependent Lead Time
If you are in a situation where demand and lead time are linked, this is the formula that you should consider using. In such situations, it could be that demand is having an impact on lead times or lead time is causing uncertainty on demand.
The formula for the same is,
Safety Stock = Z x Demand Standard Deviation x sqrt (Average LT) + Z x Average sales x Lead time standard deviation
Typically, for such unpredictable variations, more safety stock will be required.
Note: sqrt is an abbreviation for square root
Safety Stock with EOQ (Economic Order Quantity)
In this method, where safety stock is used in conjunction with economic order quantity, it is usually used by companies making purchasing decisions rather than production decisions.
Economic order quantity (EOQ) which is also known as the Wilson formula, is a calculation used to determine the least costly number of units to order. Here, the aim is to minimize the cost of ordering and holding stock while still meeting demand and service level requirements.
The cost of ordering products is made up of the cost of placing your order, delivery and transportation costs, and the cost of receiving the order. Holding costs, however, consist of the financial costs of paying for stock in advance, warehousing and storage costs, and depreciation costs.
EOQ = Economic order quantity in units
Q = Estimated annual quantity used in units (can be found in the annual purchases budget)
O = Estimated cost of placing one order
C = Estimated cost to carry one unit in stock for one year
Considering that the ultimate aim of EOQ is to have as little stock as possible while still being able to fulfill the level of demand and service requirements. Achieving this fine balance is made possible by clearly knowing your safety stock requirements.
Role of Safety Stock in Reorder Point Calculations
Reorder point is the level of inventory when a new order is positioned with suppliers to procure added inventory, equaling the economic order amount. Thus, the reorder point is a signal that will notify you when your business needs to place an order.
However, to calculate the reorder point, you will need knowledge of the lead time between receipt and ordering of merchandise. This process may be influenced by the monthly supply or total dollar (or other currency) ceilings of the held or ordered inventory.
Reorder point is, therefore a metric that will tell your organization the following essential things:
- The right time to order more materials from your supplier(s)
- The right time to produce more products by creating a manufacturing order
Thus, as is evident, the final element to consider before you calculate safety stock using the safety stock formula is the reorder point calculation.
For example, you have a 15-day lead time, and you know that you will need to place your order 15 days in advance of your current stock running out. While in the ideal situation, this would mean that you would never have to use safety stock, this is quite unlikely because of the multiple variables involved.
It is during these times of variability in demand and lead time that safety stock will cover for you, ensuring that it stops issues with your lead time and limits the impact of your service rate.
Thus, the reorder point calculation will be done as follows:
Reorder Point = Safety Stock + Average Sales x Lead Time
4 Limitations of the Safety Stock Formulas
Four limitations of the safety stock formulas are:
- In reality, it is difficult to predict buying behavior. This is why sales trends and buying habits may not sit perfectly within the mathematical bounds of these formulas. This means that while the safety stock (as calculated through these formulas) will help you in preventing stock-outs, they will still occur.
- The formulas that we discussed do not take seasonal variations into account. Thus, if you are a retailer or a manufacturer who is impacted by seasonal buying trends, you will find it more difficult to calculate your safety stock levels.
- Also, a safety stock formula cannot account for extreme fluctuations in demand or lead time. Thus, if your lead times suddenly increases by nine months, it will not show within the normal distribution figure. This is because that figure is a mean calculation and not an average.
- If there are extreme cases that have an impact on stock and sales, then there is a risk that you may not be able to trust the safety stock formulas at all and strive for high service levels. As we have seen, a service level of 100% would mean having infinite stock, which, however, is not a financially viable or safe option.
How to Choose the Right Formula for Your Safety Stock?
The step that precedes the one where you choose the safety stock formula that suits you the best involves considering the quality and quantity of your data. This is because data is a critical element in all these calculations. Thus, having solid and reliable data is a must to ensure that your calculations are accurate and you are able to solve issues.
If your business has low sales volumes of 100 or less, then you should prefer using the general formula (i.e., the medium max method). This is because, essentially, you will want to calculate the average maximum units you will need at any one time.
However, if your business experiences sales of 100-300 units per product per month, then you should use the formula - normal distribution with uncertainty about the demand. This is a useful method when there are fluctuations in demand, but your lead time is relatively stable.
However, if yours is a business that experiences a great deal of uncertainty, then you should use the formula - normal distribution with uncertainty on-demand and independent lead time. This would be the aptest formula for you because it factors in both lead time uncertainty and sales uncertainty.
Now, whether you choose to use the same formula across all stock items or pick and choose formulae across the range is a crucial question.
While more complicated formulas will require more complex calculations and data collection, using standard calculations across all stock items can be automated.
This is made possible if you have data sets that are strong and uniform across all stock items. This will negate any complicated division of stock into different groups based on their characteristics.
Thus, the key to a successful inventory management system is to put in place a system that works according to the data available and as per the needs of your business.
Conditions Under Which Using Safety Stock Formula will not be Ideal
The conditions under which using the safety stock formula might not be ideal are:
- If yours is a brand-new startup that does not have enough historical data on demand, supply, average sales, and lead time.
- If money is tight for your business, then buying a safety stock will not be the best investment for you. However, if stock-outs are a significant factor in your cash flow problems, then you should resort to safety stock.
- If you are involved in the manufacturing and selling of perishable goods, then you should be extra cautious with safety stock as the risk of spoilage is much higher.
Best Practices for Using Safety Stock Formula
No inventory analysis is perfect because of the dynamics and complexities involved. However, incorporating a safety stock formula will definitely give you an edge against your competition when demand spikes by providing a much-needed insurance policy against stock-outs.
Thus, the best practices that you can incorporate while using safety stock formulas are:
- Make sure that you start small. This means that if your surplus level is zero currently, then you do not need to order 1,000 extra units. Instead, you should rather resort to making gradual adjustments as you gather more data.
- If your operations are running smoothly, then you should not buy or increase your safety stock levels. This is because you should purchase safety stock only if you start to notice potential issues with stock-outs. This will ensure that you do not add undue pressure on the working capital.
- You should establish a system that will closely and regularly monitor your data. Not only should this system automate your calculations, but should ensure that your formula is up to date. This will ensure that your safety stock calculations are accurate.
Excel Calculator for Safety Stock
To get an excel calculator for safety stock, which will largely automate your calculations and ensure their accuracy, click on the link below.
Manage and Calculate Safety Stock with MRP System
An MRP system like Deskera MRP comes with built-in demand planning and forecasting tools. This will help you to calculate your optimal safety stock levels while reducing the chances of having too much or not enough buffer inventory.
Through an MRP system, you will be able to centralize supply chain functions which will facilitate better planning and collaboration between operational units. This will also allow integration and streamlining of data across all departments and locations of your business.
A leading MRP system like that of Deskera will also offer advanced analytics capabilities. This will help in accounting for demand and supply fluctuations while improving the forecasting of the same. These insights will reduce the chances of holding excess safety stock.
Additionally, it will also reduce the need for safety stock by optimizing management across your entire company. Such software will thus be able to perform every task required to calculate and manage safety stock accurately, thereby improving overall operational efficiencies.
Lastly, this software will take the manual processes out of the equation and help your company maximize sales, minimize disruptions, optimize safety stock, and drive profits. It will make this possible through the quality and quantity of data that it will collect on one platform. In fact, such software also facilitates exporting of data from different platforms.
Safety Stock FAQs
- Should you calculate safety stock for every SKU?
Not every product of your business will require a buffer of safety stock. In fact, if you end up keeping safety stock even when you do not need it will harm your business in more than one way ranging from storage costs, loss of quality, and change in demand. Hence, you should set a safety stock level for any product or component that you cannot afford to run out of rather than for every SKU.
- What is a good safety stock level?
The optimal level of safety stock depends on several factors like:
- Inventory velocity
- Current and future demand
- Sales volume
- Supplier lead times
Based on your business needs, you will then need to choose a safety stock formula, which will then give you the optimal level of safety stock.
- What is the difference between safety stock and buffer stock?
While generally, both of these terms are used interchangeably, in some industries, safety stock refers to excess inventory held for supplier delays or other internal variations, whereas buffer stock refers to excess inventory covering variations in demand.
- What is the importance of safety stock?
Safety stock is one of the easiest ways to avoid running out of stock and not fulfilling orders. Without it, your business is most likely to lose sales and, ultimately, customers as well as customer loyalty.
How can Deskera Help with Safety Stock Calculations?
As a manufacturer or retailer, it is crucial that you stay on top of your manufacturing processes and resource management.
You must manage production cycles, resource allocations, safety stock, reorder points, and much more to achieve this.
Deskera MRP is the one tool that lets you do all of the above. With Deskera, you can:
- Track raw materials and finished goods inventory
- Manage production plans and routings
- Maintain bill of materials
- Optimize resource allocations
- Generate detailed reports
- Create custom dashboards
And a lot more.
It is also possible to export information and data on Deskera MRP from other systems. Additionally, Deskera MRP will give you analytics and insights to help you make decisions.
So go ahead and book a demo for Deskera MRP today!
Key Takeaways
Safety stock is an extra quantity of a product that is stored in the warehouse to prevent an out-of-stock situation. Safety stock is very important as it acts as a defense against unexpected circumstances.
To avoid losing sales due to stock-outs or supply chain interruptions, it is crucial that you calculate safety stock. Additionally, safety stock also helps to avoid production inefficiencies, unhappy customers, lost sales, and reduced profits.
The benefits of keeping safety stock in your business are:
- Offset demand uncertainty
- Avoid stock-outs
- Minimize the effects of supply disruptions
- Reduce administrative and staff hours
- Compensate for forecast inaccuracies
- Limit rushed shipping
- Ensure customer satisfaction
- Maintain market share
- Increase efficiency
- Improve supplier and retailer relationships
- Prevention against price fluctuations
However, there are risks associated with the use of safety stock. These are:
- Setting safety stock to zero
- Safety stock is static
- Too much safety stock
- Standard safety stock formulas
- Letting safety stock decline
- Overuse of safety stock
There are several formulas and approaches for calculating your safety stock. Similar to many other kinds of business decisions, there is no one-size-fits-all formula that will work for all businesses. You will thus have to choose the method that works best for your business. Some of these formulas and methods are:
- Fixed Safety Stock
- Time-Based Calculation
- The General Formula (The Medium Max Method)
- Inventory Position Safety Stock Formula
- Normal Distribution with Uncertainty About the Demand
- Normal Distribution with Uncertainty on the Lead Time
- Normal Distribution with Uncertainty On-Demand and Independent Lead Time
- Normal Distribution with Uncertainty on Demand and Dependent Lead Time
The best way to keep safety stock is with the help of MRP systems like Deskera, which will facilitate the centralization of supply chain functions. This will ensure better planning and collaboration between operational units.
Related Articles
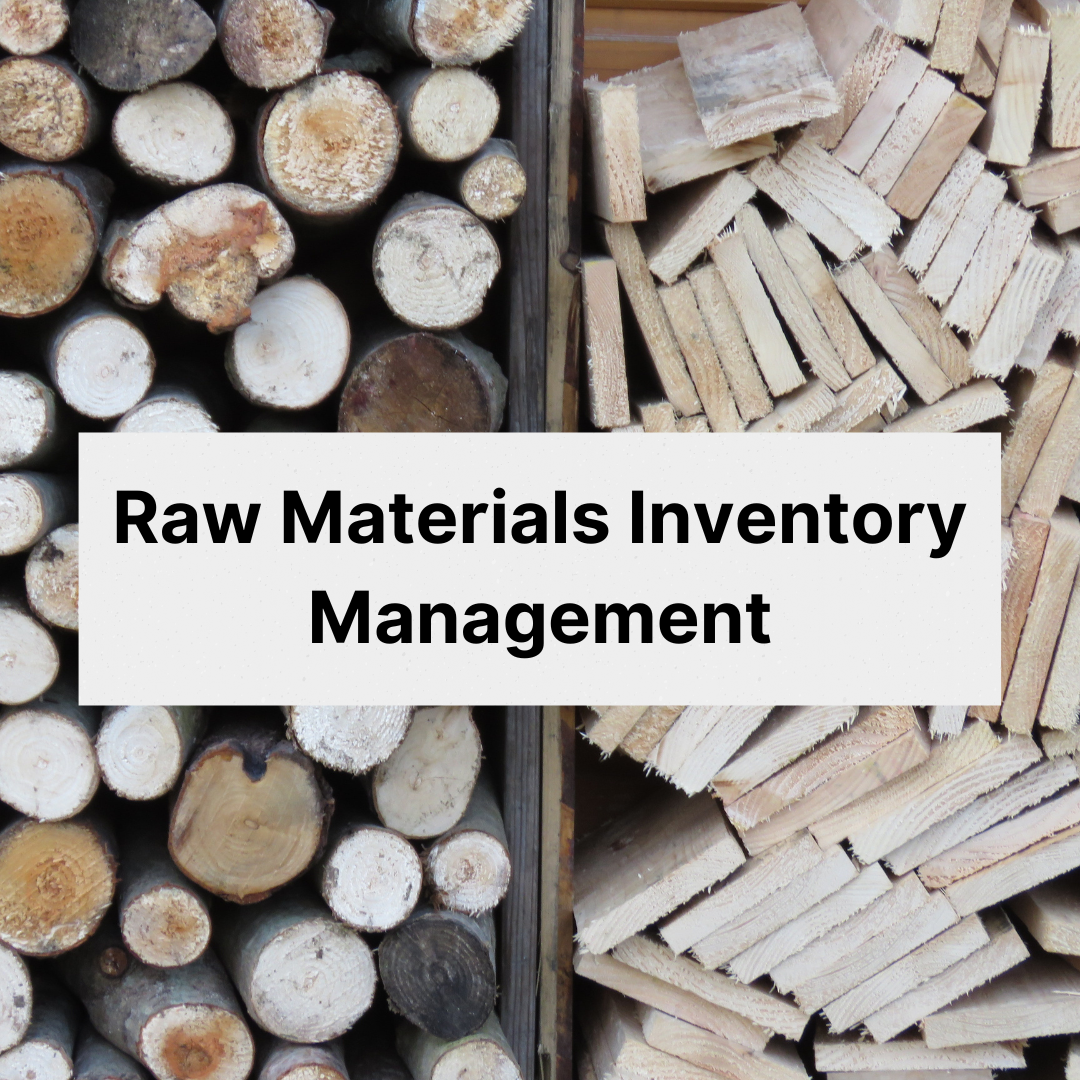
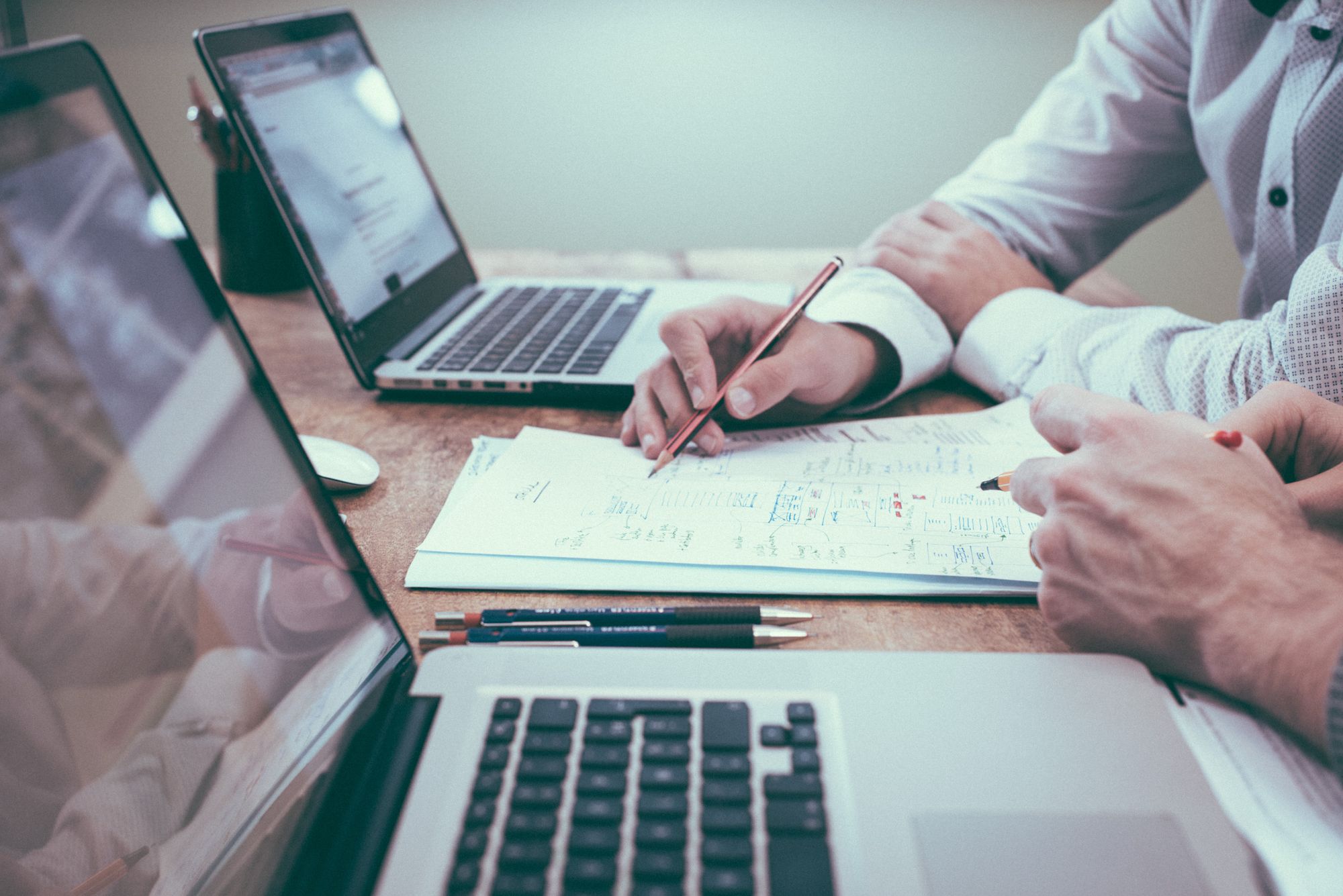
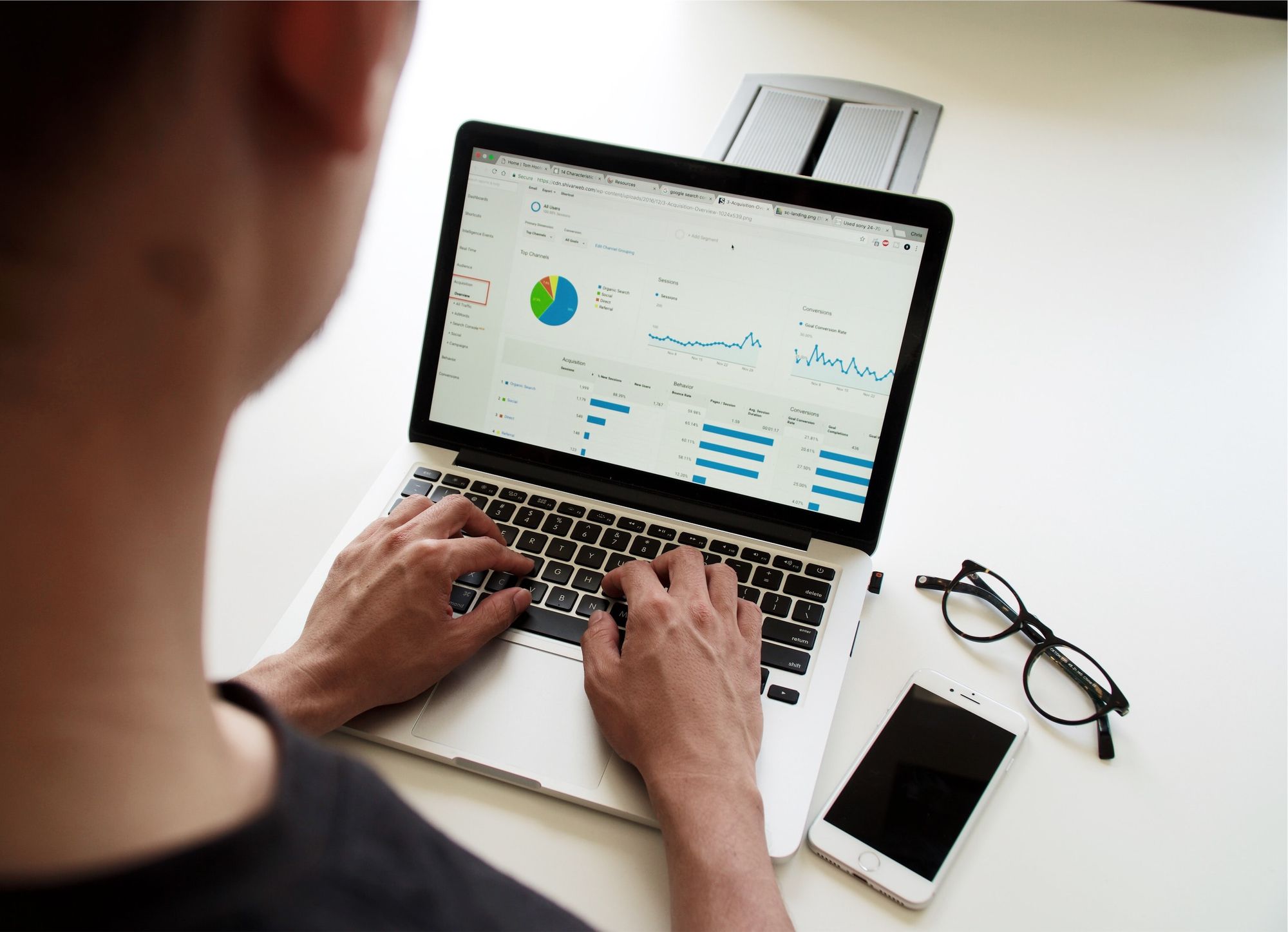
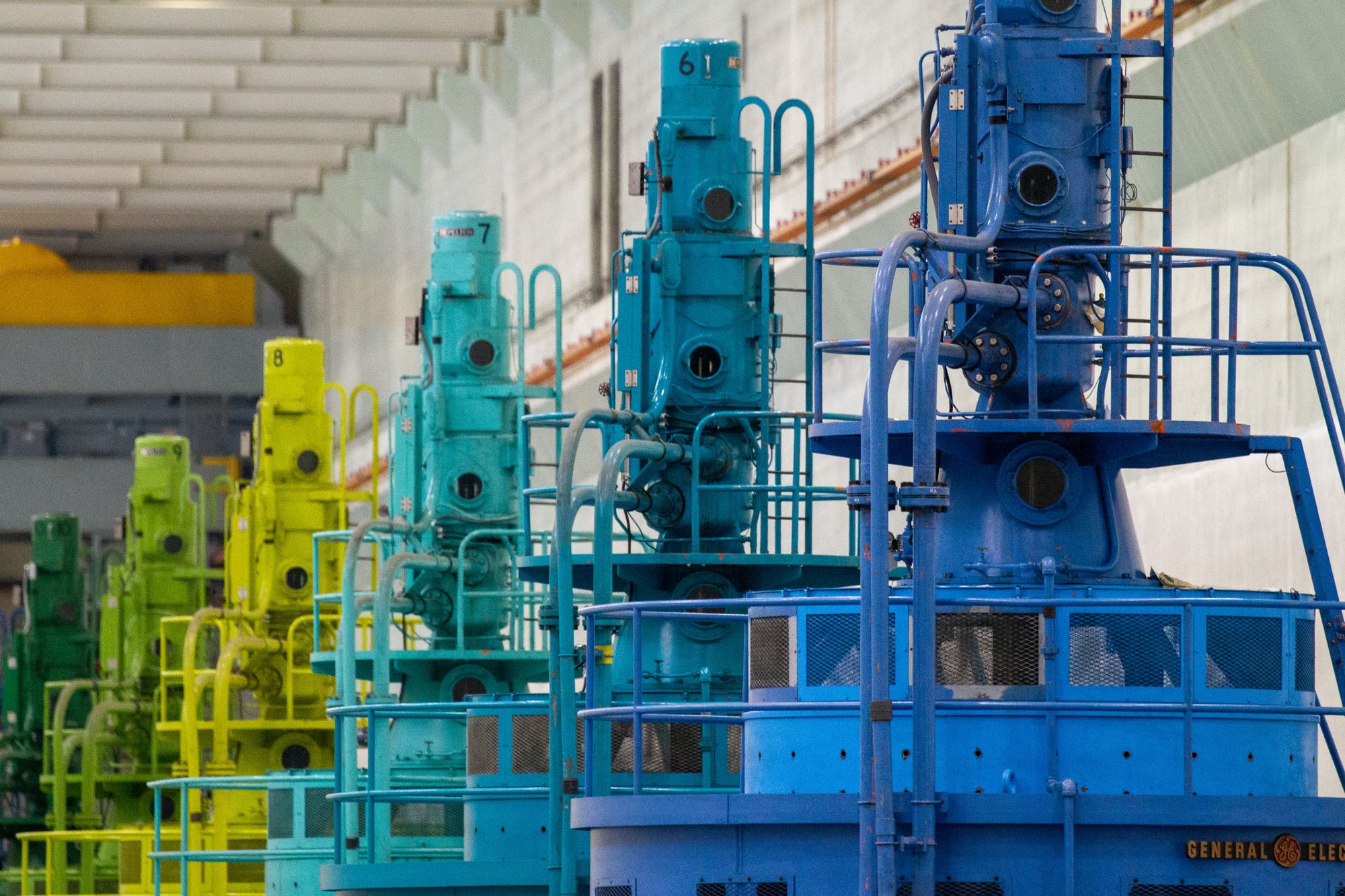
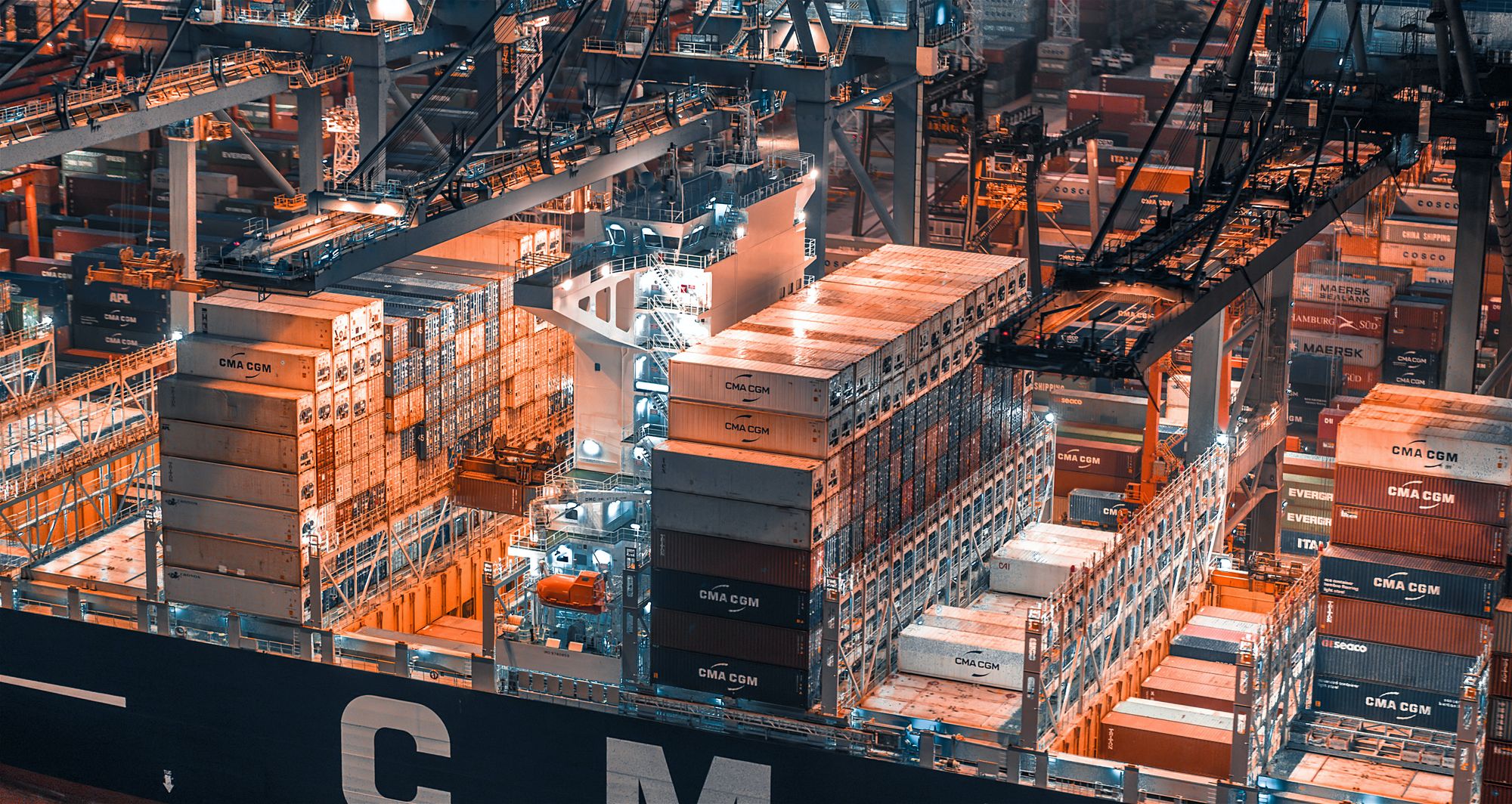