Effective inventory control lies at the heart of successful manufacturing operations. Yet, many companies struggle to strike the right balance between having enough inventory to meet demand and minimizing excess stock that ties up capital.
In fact, according to a recent survey by Deloitte, inefficient inventory management can result in an average of 25% higher inventory carrying costs for manufacturers. This statistic alone highlights the critical need for manufacturing executives to prioritize and optimize their inventory control strategies.
In this article, we will delve into the ABCs of inventory control, equipping manufacturing executives with essential strategies to enhance their operations. With a focus on minimizing costs, optimizing stock levels, and ensuring timely availability of materials, these strategies can pave the way for improved efficiency and profitability.
By leveraging advanced technologies, collaborative supply chain management, and continuous improvement practices, manufacturing executives can streamline their inventory control processes and unlock significant benefits.
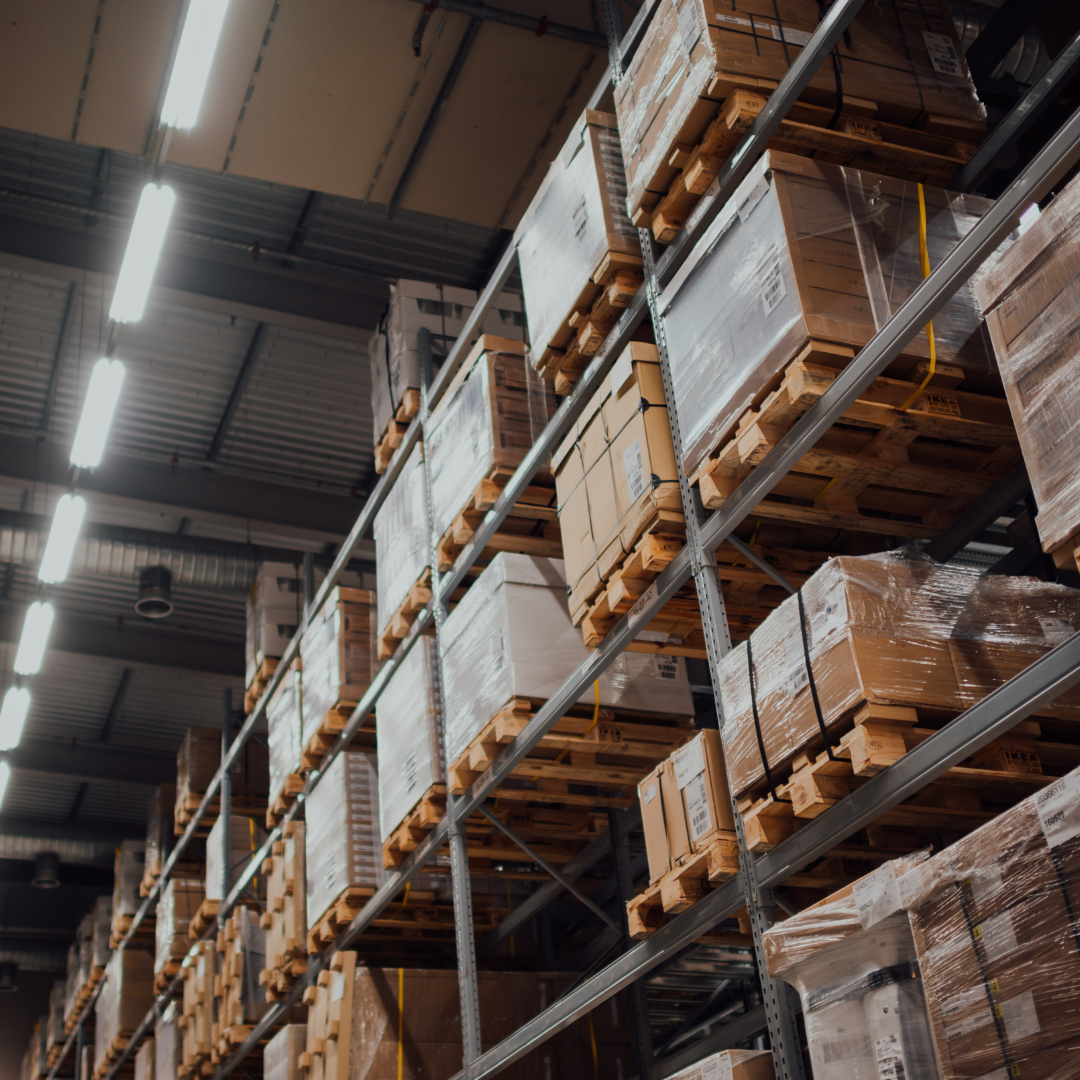
Join us as we explore the fundamental strategies that manufacturing executives need to know in order to take control of their inventory and drive success in today's competitive manufacturing landscape.
- Importance of Inventory Control in the Manufacturing Industry
- Impact of Ineffective Inventory Management on Costs and Operations
- Understanding Inventory Control
- ABC Analysis
- Managing A-Class Inventory
- Balancing B-Class Inventory
- Streamlining C-Class Inventory
- Technology Solutions for Inventory Control
- Collaborative Supply Chain Management
- Continuous Improvement and Evaluation
- Importance of Implementing these Strategies for Cost Reduction and Operational Efficiency
- Conclusion
- How can Deskera Help You?
- Key Takeaways
- Related Articles
Importance of Inventory Control in the Manufacturing Industry
Inventory control plays a crucial role in the manufacturing industry, and its importance cannot be overstated. It serves as the backbone of efficient operations, cost management, and customer loyalty and satisfaction.
Here are some key reasons why inventory control is essential in the manufacturing industry:
Cost Reduction: Effective inventory control helps manufacturers reduce costs by optimizing stock levels. Excessive inventory ties up capital and incurs carrying costs, including storage, insurance, and obsolescence.
On the other hand, insufficient inventory can lead to production disruptions and missed opportunities. By implementing proper inventory control strategies, manufacturers can strike the right balance, minimizing holding costs while ensuring uninterrupted production and timely order fulfillment.
Operational Efficiency: Efficient inventory control streamlines manufacturing operations. It enables better production planning and scheduling, as well as accurate demand forecasting. By maintaining optimal inventory levels, manufacturers can avoid bottlenecks, reduce lead times, and improve overall efficiency. This, in turn, leads to increased productivity, smoother workflows, and better utilization of resources.
Customer Satisfaction: Inventory control directly impacts customer satisfaction. By having the right products in stock and readily available, manufacturers can meet customer demands promptly. Timely order fulfillment enhances customer experience, builds trust, and fosters long-term relationships. Conversely, stockouts or delays in delivery can lead to dissatisfied customers, lost sales, and damage to the company's reputation.
Supply Chain Optimization: Inventory control is closely linked to supply chain management. By effectively managing inventory, manufacturers can collaborate with suppliers, align production with demand, and reduce lead times. This leads to improved supply chain visibility, enhanced coordination, and better responsiveness to market fluctuations. A well-optimized supply chain results in cost savings, reduced inventory holding, and increased agility.
Financial Management: Inventory represents a significant portion of a manufacturer's assets. Effective inventory control helps optimize working capital and cash flow. By minimizing excess inventory and accurately forecasting demand, manufacturers can free up capital for other business needs, invest in innovation, and reduce dependence on costly financing options.
Inventory control is a critical aspect of successful manufacturing operations. It enables cost reduction, operational efficiency, customer satisfaction, supply chain optimization, and better financial management. Manufacturers who prioritize and implement effective inventory control strategies gain a competitive edge, reduce costs, and improve overall business performance.
Impact of Ineffective Inventory Management on Costs and Operations
Ineffective inventory management can have significant negative impacts on costs and operations within the manufacturing industry.
Here are some key repercussions of poor inventory control:
- Increased Holding Costs: Excessive or obsolete inventory ties up capital and incurs holding costs. Warehousing, insurance, and maintenance expenses add up over time, reducing profitability. Inefficient inventory management leads to overstocking, resulting in higher carrying costs and reduced cash flow for the organization.
- Stockouts and Production Disruptions: Inadequate inventory levels can lead to stockouts, where products are not available to fulfill customer orders or support production needs. Stockouts not only result in dissatisfied customers but also disrupt manufacturing operations. Production delays, idle workforce, and missed sales opportunities can occur, leading to decreased revenue and decreased customer loyalty.
- Increased Order Lead Times: Poor inventory control can result in longer order lead times. This occurs when materials or components needed for production are not readily available, leading to delays in fulfilling customer orders. Longer lead times can result in customer dissatisfaction, lost sales, and damaged relationships with buyers.
- Inefficient Resource Utilization: Inaccurate demand forecasting and improper inventory management can lead to inefficient resource utilization. Manufacturers may either overutilize or underutilize resources, such as labor, equipment, and storage space. Overutilization strains resources, leading to higher costs and potential equipment breakdowns. Underutilization wastes resources and hampers overall productivity and efficiency.
- Obsolescence and Write-offs: Inadequate inventory control can result in obsolete or expired inventory. This occurs when products or materials become outdated or lose their value due to changing market trends or expiration dates. Obsolete inventory represents a loss in investment and may require write-offs, negatively impacting the company's financial statements.
- Inaccurate Financial Planning: Poor inventory management can lead to inaccurate financial planning and budgeting. When inventory levels are not properly tracked and managed, forecasting accuracy diminishes, making it difficult for manufacturing companies to plan their financial resources effectively. This can result in budget overruns, missed financial targets, and reduced profitability.
In summary, ineffective inventory management has significant consequences for costs and operations within the manufacturing industry. It leads to increased holding costs, stockouts, production disruptions, longer lead times, inefficient resource utilization, obsolescence, and inaccurate financial planning.
To mitigate these impacts, manufacturers must prioritize robust inventory control strategies to optimize stock levels, enhance operational efficiency, and ultimately improve their bottom line.
Understanding Inventory Control
In the dynamic landscape of manufacturing, having a solid grasp of inventory control is crucial for ensuring smooth operations, cost optimization, and customer satisfaction.
Effective inventory control involves the strategic management of stock levels, demand forecasting, and timely availability of materials. By mastering the principles and objectives of inventory control, manufacturing executives can navigate the complexities of supply and demand, minimize costs, and maintain a competitive edge.
In this section, we will delve into the fundamental concepts of inventory control, laying the groundwork for manufacturing executives to enhance their operations.
Inventory control and its role in manufacturing operations
Inventory control refers to the systematic management and oversight of inventory within a manufacturing operation. It involves the processes, strategies, and techniques used to track, monitor, and optimize the levels of raw materials, work-in-progress (WIP), and finished goods held by a company.
The primary objective of inventory control is to ensure that the right quantity of inventory is available at the right time, while minimizing costs and maintaining operational efficiency.
The role of inventory control in manufacturing operations is multifaceted and essential. Here are key aspects of its significance:
- Demand Fulfillment: Inventory control ensures that adequate stock is available to fulfill customer orders and meet production requirements. By accurately assessing demand and aligning inventory levels accordingly, manufacturing companies can avoid stockouts, minimize order lead times, and maintain high customer satisfaction.
- Cost Optimization: Efficient inventory control helps in minimizing inventory carrying costs. By closely monitoring stock levels, companies can avoid excess inventory that ties up capital and incurs expenses such as storage, insurance, and obsolescence costs. Additionally, optimized inventory levels prevent overproduction and reduce waste, leading to cost savings.
- Production Planning and Scheduling: Inventory control plays a crucial role in production planning and scheduling. By understanding inventory levels and demand patterns, manufacturers can optimize their production schedules, allocate resources effectively, and maintain a smooth workflow. This minimizes bottlenecks, optimizes resource utilization, and improves overall operational efficiency.
- Supply Chain Management: Inventory control is closely linked to effective supply chain management. By managing inventory levels in coordination with suppliers and distributors, manufacturers can achieve better supply chain visibility, reduce lead times, and enhance collaboration. This ensures a steady flow of materials and products, minimizing disruptions and optimizing the overall supply chain performance.
- Cash Flow Management: Proper inventory control contributes to efficient cash flow management. By avoiding excessive inventory, manufacturers can free up working capital for other business needs, such as research and development, marketing initiatives, and investments. This improves financial stability and flexibility within the organization.
In summary, inventory control plays a critical role in manufacturing operations. It enables companies to fulfill customer demands, optimize costs, streamline production processes, manage the supply chain effectively, and maintain healthy cash flow.
By implementing robust inventory control strategies, manufacturing companies can enhance their competitiveness, improve customer satisfaction, and drive overall business success.
Key objectives of inventory control: minimizing costs, optimizing stock levels, and ensuring timely availability of materials
The key objectives of inventory control in manufacturing revolve around minimizing costs, optimizing stock levels, and ensuring the timely availability of materials. These objectives play a crucial role in achieving operational efficiency and maximizing profitability.
Let's explore each objective in detail:
Minimizing Costs: One of the primary objectives of inventory control is to minimize costs associated with holding and managing inventory. Excessive inventory levels incur expenses such as storage costs, insurance, obsolescence, and financing charges. On the other hand, insufficient inventory levels can lead to production disruptions and missed sales opportunities.
By implementing effective inventory control strategies, manufacturing companies can strike a balance, avoiding excess inventory while ensuring enough stock to meet demand. This results in reduced holding costs, improved cash flow, and increased profitability.
Optimizing Stock Levels: Another objective of inventory control is to optimize stock levels. This involves finding the right balance between carrying enough inventory to meet demand and avoiding excessive stock that ties up capital. By conducting accurate demand forecasting and closely monitoring customer requirements, manufacturing companies can determine the optimal inventory levels for each product or material.
This optimization leads to improved production planning, reduced stockouts, minimized order lead times, and better resource allocation. Ultimately, optimizing stock levels improves operational efficiency, customer satisfaction, and cost-effectiveness.
Ensuring Timely Availability of Materials: Timely availability of materials is crucial for seamless manufacturing operations. Effective inventory control aims to ensure that the necessary materials and components are readily available when needed. By accurately forecasting demand and maintaining appropriate inventory levels, manufacturing companies can avoid production delays, minimize idle time, and enhance overall productivity.
Timely availability of materials also facilitates meeting customer orders promptly, resulting in higher customer satisfaction and increased sales.
These three objectives are interconnected and mutually reinforcing. Minimizing costs by optimizing stock levels reduces the financial burden on the company while ensuring that materials are available when required. Achieving these objectives requires a comprehensive understanding of demand patterns, efficient supply chain management, accurate inventory tracking, and the use of advanced technology and forecasting techniques.
By successfully meeting the key objectives of inventory control, manufacturing companies can enhance their operational efficiency, reduce costs, improve customer satisfaction, and gain a competitive edge in the market.
ABC Analysis
ABC analysis is a fundamental tool used in inventory control to categorize and prioritize inventory items based on their value and usage. It is named after the three categories it creates: A, B, and C. This analysis helps manufacturing executives gain insights into their inventory and make informed decisions about inventory management.
The concept behind ABC analysis is the Pareto principle, also known as the 80/20 rule, which states that a small percentage of items typically account for a large percentage of the value or usage.
By categorizing inventory items through ABC analysis, manufacturing executives can gain a clear understanding of the items that have the greatest impact on the business. This allows them to prioritize their efforts and allocate resources accordingly.
For example, Category A items may require more frequent monitoring, accurate demand forecasting, and closer relationships with suppliers to ensure availability. Category C items, on the other hand, may be managed with more standardized processes and automated replenishment systems.
Overall, ABC analysis serves as a valuable tool in inventory control, enabling manufacturing executives to focus their attention and resources on the items that have the greatest impact on value and usage. By effectively managing each category, companies can optimize inventory levels, reduce costs, and improve overall operational efficiency.
Explain how ABC analysis categorizes inventory items based on their value and usage
ABC analysis categorizes inventory items based on their value and usage by analyzing their contribution to the overall value and consumption within a company. The categorization is typically done using a combination of two factors: the item's monetary value (cost) and its usage or demand.
Here's how ABC analysis categorizes inventory items:
- Value Assessment: The first step is to determine the value of each inventory item. This is usually based on the cost of the item. Higher-cost items are considered more valuable than lower-cost items. The total cost of each item is calculated, taking into account the purchase price, production costs, and any associated expenses such as transportation or storage costs.
- Usage Assessment: The next step is to evaluate the usage or demand for each item. This can be measured in various ways, such as the number of units sold or consumed over a specific period. Items with higher usage or demand are considered more critical to the business.
- Categorization: Once the value and usage assessments are completed, the inventory items are categorized into three groups: A, B, and C.
Category A: Category A items are the highest-value and highest-usage items. They represent a relatively small percentage of the total inventory but have a significant impact on the company's revenue and operations. These items require close monitoring and careful management to ensure their availability and efficient utilization.
Category B: Category B items have moderate value and usage. They represent a larger portion of the inventory but are not as critical as Category A items. Proper management of Category B items is still important to maintain operational flow and customer satisfaction while avoiding excess holding costs.
Category C: Category C items are low-value and low-usage items. They make up the majority of the inventory but have a relatively low impact on value and consumption. These items typically require less attention and can be managed with more standardized processes and automated replenishment systems.
By categorizing inventory items based on their value and usage, ABC analysis provides a framework for prioritizing resources, attention, and decision-making in inventory control. It helps manufacturing executives focus on the items that have the greatest impact on the business and allocate resources effectively to optimize inventory levels, reduce costs, and improve overall operational efficiency.
Discuss the significance of categorizing items into A, B, and C groups
Categorizing inventory items into A, B, and C groups based on the ABC analysis holds significant significance for effective inventory control. Here are some key reasons why categorization is crucial:
Resource Allocation: Categorization allows for proper resource allocation. By identifying high-value and high-usage items (Category A), manufacturing executives can allocate more attention, resources, and strategic focus to ensure the availability and efficient management of these critical items. This ensures that the most valuable and impactful items receive the necessary resources to support production and meet customer demands.
Inventory Management Strategies: Each category requires different inventory management strategies. Category A items may require more frequent monitoring, accurate demand forecasting, and closer relationships with suppliers to ensure availability. Category B items, being moderately significant, may need periodic review and replenishment planning.
Category C items, with lower value and usage, can be managed with more standardized processes and automated replenishment systems. Categorization helps in tailoring the appropriate inventory management approach to each category, optimizing efficiency and cost-effectiveness.
Risk Mitigation: Categorization helps identify potential risks within the inventory. Category A items, due to their high value and usage, carry a higher risk if they are not properly managed or experience shortages. By focusing attention on these critical items, companies can mitigate risks associated with stockouts, production delays, or dissatisfied customers. Identifying and addressing potential risks proactively improves operational stability and customer satisfaction.
Cost Optimization: Categorization aids in cost optimization. Category A items often have higher holding costs due to their value, and effective management of these items can help minimize excess inventory and associated expenses. Category C items, with lower value and usage, can be managed with leaner inventory levels, reducing holding costs.
By assigning appropriate inventory control strategies to each category, companies can optimize costs by aligning resources with the value and usage of inventory items.
Strategic Decision-Making: Categorization provides valuable insights for strategic decision-making. By understanding the value and usage distribution across the inventory, manufacturing executives can make informed decisions about product pricing, supplier relationships, production planning, and investment in inventory. It allows them to prioritize their efforts and resources based on the items' impact on revenue, profitability, and customer satisfaction.
Overall, categorizing inventory items into A, B, and C groups provides a structured framework for effective inventory control. It helps in allocating resources efficiently, implementing tailored inventory management strategies, mitigating risks, optimizing costs, and making informed strategic decisions.
By focusing on the items that have the greatest impact, manufacturing companies can enhance operational efficiency, improve customer satisfaction, and drive overall business success.
Managing A-Class Inventory
Among the various categories of inventory, A-Class inventory holds paramount importance for manufacturing executives. Comprising high-value and high-usage items, this category plays a pivotal role in revenue generation, customer satisfaction, and overall operational efficiency. Managing A-Class inventory requires a focused and strategic approach that ensures the availability, proper utilization, and cost optimization of these critical items.
In this section, we delve into the intricacies of managing A-Class inventory, exploring the key challenges, best practices, and effective strategies employed by manufacturing executives. We will discuss the significance of accurate demand forecasting, establishing robust supplier relationships, implementing efficient inventory tracking systems, and employing advanced technologies to optimize inventory levels.
Strategies for managing A-class inventory items, which are high-value and high-usage
Strategies for managing A-class inventory items, which are high-value and high-usage, require careful attention and proactive measures to ensure their availability, proper utilization, and cost optimization.
Here are some effective strategies for managing A-class inventory:
Accurate Demand Forecasting: Accurate demand forecasting is crucial for managing A-class inventory. By analyzing historical data, market trends, and customer insights, manufacturing executives can anticipate demand patterns and plan inventory levels accordingly.
Implementing advanced forecasting techniques, such as statistical models or machine learning algorithms, can improve the accuracy of demand predictions and enable proactive inventory management.
Robust Supplier Relationships: Developing strong relationships with suppliers is essential for managing A-class inventory. Collaborating closely with trusted suppliers helps ensure a steady supply of high-quality materials, timely deliveries, and preferential treatment during high-demand periods.
Maintaining open communication, sharing demand forecasts, and negotiating favorable terms can lead to better supplier performance, reduced lead times, and increased reliability of A-class inventory supply.
Efficient Inventory Tracking Systems: Implementing efficient inventory tracking systems is vital for managing A-class inventory. Real-time visibility into inventory levels, stock movements, and usage patterns enables manufacturing executives to make informed decisions about replenishment, order scheduling, and resource allocation.
Utilizing inventory management software or enterprise resource planning (ERP) systems with robust tracking capabilities streamlines inventory control, minimizes stockouts, and improves overall inventory accuracy.
Just-in-Time (JIT) Inventory Management: Implementing Just-in-Time (JIT) inventory management principles can be beneficial for A-class items. JIT emphasizes receiving materials or producing goods just in time to meet customer demand, thereby reducing excess inventory and associated holding costs.
By closely coordinating production schedules, supply chain activities, and customer orders, manufacturing executives can minimize lead times, improve production efficiency, and optimize A-class inventory levels.
Strategic Safety Stock: While A-class items should be managed efficiently, it is also prudent to maintain strategic safety stock to mitigate unforeseen disruptions or variations in demand. Safety stock acts as a buffer to prevent stockouts and maintain continuity in production.
However, it is important to strike a balance to avoid excessive safety stock that ties up working capital. Analyzing historical demand variability and lead time fluctuations can help determine optimal safety stock levels for A-class items.
Continuous Process Improvement: Regularly reviewing and improving inventory management processes is crucial for managing A-class inventory effectively. Conducting periodic inventory audits, identifying process bottlenecks, and implementing lean principles can streamline operations and reduce waste.
Continuous improvement initiatives such as implementing automation, adopting barcode or RFID tracking systems, and optimizing order fulfillment processes can enhance efficiency and accuracy in managing A-class inventory.
By implementing these strategies, manufacturing executives can optimize the management of A-class inventory. This ensures the availability of high-value items to meet customer demands, minimizes holding costs, reduces stockouts, and enhances operational efficiency. Managing A-class inventory strategically contributes to overall business success, customer satisfaction, and profitability.
Importance of accurate demand forecasting and aligning production with demand
Accurate demand forecasting and aligning production with demand are of paramount importance in manufacturing operations. Here's why:
Customer Satisfaction: Accurate demand forecasting helps manufacturing companies meet customer expectations by ensuring that the right products are available at the right time. By understanding customer demand patterns, companies can anticipate fluctuations, plan production accordingly, and avoid stockouts or delays. This enhances customer satisfaction, builds trust, and fosters long-term relationships.
Efficient Resource Allocation: Accurate demand forecasting enables efficient resource allocation. By aligning production with demand, companies can optimize the utilization of resources such as labor, raw materials, and production capacity. This minimizes waste, reduces costs, and improves overall operational efficiency. Effective resource allocation leads to streamlined production processes, shorter lead times, and improved profitability.
Inventory Optimization: Demand forecasting helps in optimizing inventory levels. By accurately predicting demand, manufacturing companies can maintain optimal stock levels, avoiding excess inventory or stockouts. Excessive inventory ties up working capital, incurs holding costs, and increases the risk of obsolescence.
On the other hand, stockouts result in missed sales opportunities and dissatisfied customers. Accurate demand forecasting ensures inventory is at the right level to meet customer needs while minimizing inventory carrying costs.
Production Planning and Efficiency: Aligning production with demand enables effective production planning. By synchronizing production schedules with forecasted demand, companies can optimize production workflows, minimize idle time, and reduce production lead times.
This results in efficient use of production resources, improved throughput, and increased overall productivity. Efficient production planning also allows for better coordination with suppliers, ensuring timely availability of raw materials and components.
Cost Reduction: Accurate demand forecasting and aligning production with demand contribute to cost reduction. By avoiding overproduction, companies can minimize costs associated with excess inventory, storage, and waste.
Additionally, by reducing stockouts and production disruptions, companies can avoid rush orders, expedited shipping costs, and potential penalties for missed delivery deadlines. Optimizing production based on accurate demand forecasts helps eliminate inefficiencies and drives cost savings throughout the supply chain.
Competitive Advantage: Accurate demand forecasting and aligning production with demand provide a competitive advantage. By consistently meeting customer demand, companies can differentiate themselves from competitors, establish a reputation for reliability, and gain customer loyalty.
Moreover, efficient production planning and optimized inventory management allow companies to respond quickly to market fluctuations and changing customer preferences, giving them a competitive edge in the industry.
By incorporating these practices, manufacturing companies can enhance their operational performance, improve profitability, and drive sustainable growth in the dynamic marketplace.
Understanding techniques such as just-in-time (JIT) and lean manufacturing for efficient management of A-class items
Just-in-Time (JIT) and lean manufacturing techniques are highly effective for the efficient management of A-class items, which are high-value and high-usage inventory items.
Here's how these techniques contribute to the efficient management of A-class items:
Just-in-Time (JIT) Inventory Management: JIT focuses on producing or receiving inventory items just in time to meet customer demand. It aims to minimize inventory levels, reduce waste, and optimize production processes. Applying JIT to A-class items offers several benefits:
- Reduced Inventory Holding Costs: JIT minimizes the need for excess inventory, resulting in reduced holding costs associated with A-class items. This frees up working capital that can be invested elsewhere.
- Improved Cash Flow: By synchronizing production and procurement with demand, JIT reduces tied-up capital, allowing for better cash flow management.
- Enhanced Flexibility and Responsiveness: JIT enables manufacturing companies to quickly respond to changes in demand, market trends, and customer preferences. This agility ensures that A-class items are produced or procured in alignment with actual demand, reducing the risk of excess inventory or stockouts.
Lean Manufacturing: Lean manufacturing is a systematic approach to eliminating waste and maximizing value in the production process. When applied to A-class items, lean principles can enhance efficiency and reduce costs:
- Value Stream Mapping: Value stream mapping identifies non-value-added activities in the production process. By streamlining workflows and eliminating unnecessary steps, companies can reduce lead times and optimize the production of A-class items.
- Continuous Improvement: Lean encourages a culture of continuous improvement, involving employees in identifying and implementing process enhancements. This can lead to greater efficiency and reduced waste in managing A-class inventory.
- Kanban Systems: Kanban systems, a key component of lean manufacturing, provide visual signals to control inventory levels and trigger production or replenishment. Implementing Kanban systems for A-class items ensures that production or procurement is initiated only when necessary, optimizing inventory levels and minimizing waste.
Combining JIT and lean manufacturing techniques for the management of A-class items can result in significant benefits, including improved inventory control, reduced waste, enhanced production efficiency, and optimized resource utilization.
These techniques enable manufacturing companies to respond swiftly to customer demand, minimize holding costs, and maintain a lean and efficient operation, ultimately enhancing the overall performance and competitiveness of the business.
Balancing B-Class Inventory
B-Class inventory, consisting of moderate-value and moderate-usage items, forms a substantial portion of a company's inventory. While not as critical as A-Class items, effectively managing B-Class inventory is essential for maintaining operational flow, minimizing costs, and meeting customer demands.
Striking the right balance between stock levels, replenishment strategies, and cost optimization is crucial in this category.
In this section, we explore the intricacies of balancing B-Class inventory, delving into key challenges, strategies, and best practices employed by manufacturing executives. We will discuss techniques for demand forecasting, implementing appropriate inventory control measures, optimizing reorder points, and leveraging technology to achieve optimal inventory levels and reduce carrying costs.
By mastering the art of balancing B-Class inventory, companies can enhance operational efficiency, maximize profitability, and deliver exceptional value to their customers.
Management of B-class inventory items, which are moderate in value and usage
Managing B-Class inventory items, which are moderate in value and usage, requires a strategic approach to strike a balance between maintaining adequate stock levels and optimizing cost-effectiveness.
Here are key considerations and best practices for managing B-Class inventory:
Demand Forecasting: Accurate demand forecasting plays a critical role in managing B-Class inventory. Analyzing historical data, market trends, and customer insights helps in understanding demand patterns and predicting future requirements. By forecasting demand for B-Class items, manufacturing executives can avoid overstocking or understocking, ensuring optimal inventory levels.
Reorder Point Optimization: Establishing an optimal reorder point is crucial for B-Class inventory management. The reorder point is the inventory level at which a replenishment order should be placed to avoid stockouts. It should consider factors such as lead time, demand variability, and desired service levels. By setting the reorder point appropriately, companies can maintain sufficient stock to meet customer needs while minimizing excess inventory and associated costs.
Supplier Collaboration: Building collaborative relationships with suppliers is essential for managing B-Class inventory effectively. By sharing demand forecasts, production plans, and inventory data with suppliers, manufacturing executives can align procurement and production schedules to ensure timely delivery of B-Class items. Collaborative supplier relationships can lead to improved reliability, better pricing agreements, and reduced lead times.
Inventory Segmentation: Segmenting B-Class inventory based on item characteristics, demand patterns, or seasonality can facilitate more targeted management. By categorizing B-Class items further, manufacturing executives can apply specific inventory control measures based on the unique requirements of each segment. This enables efficient allocation of resources, improved inventory tracking, and optimized replenishment strategies.
ABC Analysis Refinement: While ABC analysis primarily categorizes items based on their value, refining the categorization by incorporating usage or demand patterns can enhance B-Class inventory management. By considering both value and usage, manufacturing executives can prioritize B-Class items that have a higher impact on operations or customer satisfaction, and allocate resources accordingly.
Continuous Improvement and Process Efficiency: Regularly reviewing inventory management processes and implementing continuous improvement initiatives contribute to efficient B-Class inventory management. This involves eliminating waste, streamlining workflows, and optimizing inventory control procedures. By adopting lean manufacturing principles, companies can enhance process efficiency, reduce lead times, and minimize costs associated with B-Class inventory.
Technology Adoption: Leveraging technology solutions, such as inventory management software or enterprise resource planning (ERP) systems, can enhance B-Class inventory management. These tools provide real-time visibility into inventory levels, automate replenishment processes, and facilitate data-driven decision-making. Integration with suppliers' systems and implementing barcode or RFID tracking systems can improve accuracy, efficiency, and traceability of B-Class inventory.
By implementing these strategies, manufacturing executives can effectively manage B-Class inventory items. Maintaining optimal stock levels, aligning procurement and production schedules, optimizing costs, and enhancing process efficiency contribute to improved operational performance, customer satisfaction, and profitability.
Efficient management of B-Class inventory ensures that moderate-value items are available when needed, supporting smooth operations and maintaining a competitive edge in the market.
Explain the need for maintaining optimal stock levels without excessive holding costs
Maintaining optimal stock levels without excessive holding costs is crucial for efficient inventory management. Here's why it is necessary:
- Cost Optimization: Excessive stock levels result in higher holding costs. Holding costs include expenses such as storage space, insurance, handling, and obsolescence. By maintaining optimal stock levels, companies can minimize these costs and allocate their resources more efficiently. This leads to improved profitability and financial stability.
- Working Capital Management: Excess inventory ties up working capital that could be used for other critical business needs such as research and development, marketing, or expanding operations. By maintaining optimal stock levels, companies can free up working capital, allowing for investment in growth opportunities, debt reduction, or increased liquidity.
- Risk Mitigation: Excessive stock levels increase the risk of inventory obsolescence or deterioration. Products or materials that sit in inventory for extended periods may become outdated, damaged, or unsellable. By maintaining optimal stock levels, companies can reduce the risk of inventory obsolescence, minimize losses, and ensure the availability of fresh and up-to-date inventory.
- Efficient Space Utilization: Holding excessive inventory requires additional storage space. If warehouse space is limited or expensive, maintaining optimal stock levels becomes even more critical. By optimizing stock levels, companies can utilize their storage space efficiently, reducing the need for costly warehouse expansions or off-site storage.
- Agility and Responsiveness: Maintaining optimal stock levels enhances a company's ability to respond quickly to changes in customer demand, market conditions, or supply chain disruptions. Companies with excessive inventory may struggle to adapt to market fluctuations, leading to missed sales opportunities or excessive markdowns. By keeping stock levels in check, companies can be more agile, respond promptly to changes, and ensure that inventory aligns with actual demand.
- Customer Satisfaction: Optimal stock levels help meet customer demands effectively. Excess inventory can lead to delays in order fulfillment, while insufficient inventory may result in stockouts and dissatisfied customers. By maintaining the right balance, companies can consistently deliver products on time, improve customer satisfaction, and build strong relationships with their customers.
- Inventory Turnover: Maintaining optimal stock levels contributes to a healthy inventory turnover ratio. A higher inventory turnover indicates that inventory is efficiently utilized and replenished, reducing the risk of obsolete or slow-moving inventory. A balanced approach to stock levels promotes a faster inventory turnover, allowing companies to optimize cash flow and generate higher returns on their investments.
Maintaining optimal stock levels allows companies to optimize costs, free up working capital, mitigate risks, utilize storage space efficiently, be agile in responding to market changes, enhance customer satisfaction, and improve overall financial performance. Striking the right balance ensures that inventory remains a valuable asset rather than a burden on the business.
Discuss strategies like economic order quantity (EOQ) and safety stock to balance B-class inventory effectively
To balance B-Class inventory effectively, manufacturing executives can employ strategies such as Economic Order Quantity (EOQ) and safety stock. Let's explore these strategies in detail:
- Economic Order Quantity (EOQ): EOQ is a widely used inventory management technique that helps determine the optimal order quantity to minimize total inventory costs. The goal of EOQ is to find the balance between ordering costs and holding costs. Here's how it works:
- EOQ Calculation: EOQ is calculated using a formula that considers factors such as annual demand, ordering costs, and holding costs. The formula aims to find the order quantity that minimizes the total cost of inventory.
- Optimal Replenishment Frequency: By using EOQ, manufacturing executives can determine the most cost-effective replenishment frequency for B-Class items. This ensures that orders are placed neither too frequently (incurring high ordering costs) nor too infrequently (increasing holding costs).
- Safety Stock: Safety stock is an additional inventory buffer held to account for unexpected fluctuations in demand or supply chain disruptions. It acts as a cushion to mitigate the risk of stockouts. Implementing safety stock for B-Class items offers several benefits:
- Demand Variability: B-Class items may experience demand fluctuations due to factors like seasonality or market trends. Safety stock helps to absorb unexpected spikes in demand, ensuring product availability and customer satisfaction.
- Lead Time Variability: Unpredictable lead times from suppliers can impact inventory availability. Safety stock compensates for variations in lead time, reducing the risk of stockouts during extended lead times or supply disruptions.
- Risk Mitigation: Safety stock acts as a buffer against uncertainties in demand and supply. It helps companies manage unforeseen events such as production delays, quality issues, or transportation disruptions.
- Demand Planning and Collaboration: Accurate demand planning is essential for effective B-Class inventory management. By leveraging historical data, market trends, and customer insights, manufacturing executives can forecast demand more accurately. Collaborating with sales and marketing teams, as well as customers, can provide valuable input for demand planning, leading to better inventory decisions for B-Class items.
- Regular Inventory Analysis and Optimization: Ongoing analysis and optimization of B-Class inventory are critical for maintaining balance. Manufacturing executives should regularly review inventory levels, monitor demand patterns, and identify slow-moving or obsolete items. By optimizing stock levels and adjusting order quantities based on changing demand, companies can minimize excess inventory and associated holding costs.
- Technology and Automation: Leveraging technology solutions can enhance B-Class inventory management. Inventory management software, demand forecasting tools, and automated replenishment systems help streamline processes, improve accuracy, and optimize inventory levels. These technologies provide real-time visibility, enable data-driven decision-making, and facilitate effective inventory control for B-Class items.
By incorporating strategies like EOQ and safety stock, and utilizing effective demand planning, analysis, and technology, manufacturing executives can achieve a balanced approach to B-Class inventory management.
This ensures optimal stock levels, minimizes costs, reduces the risk of stockouts, and enables efficient utilization of resources. Ultimately, these strategies contribute to enhanced operational efficiency, improved customer satisfaction, and increased profitability.
Streamlining C-Class Inventory
C-Class inventory consists of low-value items that have relatively low usage. While they may individually contribute less to the overall inventory value, managing C-Class inventory effectively is still vital for operational efficiency and cost optimization. In this section, we delve into strategies and techniques employed by manufacturing executives to streamline C-Class inventory.
By implementing lean principles, optimizing procurement processes, leveraging technology, and adopting smart inventory management strategies, companies can achieve greater efficiency and cost savings in managing C-Class inventory. Join us as we explore the realm of streamlining C-Class inventory, uncovering practical insights and best practices that empower manufacturing executives to make informed decisions, improve processes, and optimize resource allocation for these items.
In this section, we shed light on the unique challenges associated with C-Class inventory, discuss the significance of effective management, and offer practical guidance on achieving streamlined operations. By streamlining C-Class inventory, companies can maximize efficiency, reduce costs, and unlock hidden value, ultimately strengthening their overall supply chain and organizational performance.
Focus on the management of C-class inventory items, which are low-value and low-usage
Managing C-Class inventory items, characterized by their low-value and low-usage, requires a systematic approach to ensure efficiency and cost-effectiveness.
Here are key considerations and strategies for effectively managing C-Class inventory:
- Categorization and Prioritization: While C-Class items may individually have lower value and usage, it is essential to categorize and prioritize them based on factors such as criticality, lead time, and supply chain dependencies. This helps in identifying items that require closer attention and those that can be managed more autonomously.
- Supplier Consolidation: Consolidating suppliers for C-Class items can streamline procurement processes and reduce administrative overhead. By working with fewer suppliers, companies can negotiate better pricing, simplify order management, and achieve economies of scale. Regular evaluation of supplier performance and fostering strong relationships can further enhance the efficiency of C-Class inventory management.
- Vendor-Managed Inventory (VMI): Implementing VMI can optimize C-Class inventory management. With VMI, suppliers are responsible for monitoring inventory levels and replenishing stock based on predetermined agreements. This reduces the administrative burden on the company and improves inventory visibility, ensuring that C-Class items are available when needed while minimizing excess stock.
- Demand Forecasting and Automation: Accurate demand forecasting is crucial even for C-Class items. Leveraging historical data, market trends, and demand patterns can help optimize stock levels and reduce the risk of stockouts or overstocking. Utilizing demand forecasting tools and automation can streamline the process, improve accuracy, and facilitate data-driven decision-making for C-Class inventory.
- Just-in-Time (JIT) Replenishment: JIT principles can be applied to C-Class inventory to minimize inventory holding costs and reduce waste. By synchronizing replenishment with actual demand, companies can avoid excessive inventory and improve cash flow. JIT practices such as Kanban systems, where inventory is replenished as it is consumed, can help maintain optimal stock levels for C-Class items.
- Technology Integration: Embracing technology solutions such as inventory management software, barcode scanning, and automated tracking systems can enhance the management of C-Class inventory. These tools provide real-time visibility, streamline data capture and analysis, facilitate accurate inventory counts, and improve overall efficiency in managing low-value and low-usage items.
- Continuous Improvement and Process Efficiency: Regularly reviewing and optimizing inventory management processes contribute to the streamlined management of C-Class inventory. Applying lean principles, eliminating waste, and continuously seeking process improvements enhance efficiency, reduce costs, and maximize the value derived from C-Class items.
Although they may individually have lower value and usage, collectively optimizing their management leads to improved operational efficiency, reduced costs, and better resource utilization. Efficient management of C-Class inventory ensures that even low-value items contribute to a streamlined and profitable supply chain, enhancing overall business performance.
Discuss strategies like vendor-managed inventory (VMI) and consignment inventory to streamline C-class items
Streamlining C-Class inventory items, characterized by their low-value and low-usage, can be achieved through strategies such as Vendor-Managed Inventory (VMI) and consignment inventory. These approaches optimize inventory management, reduce administrative burden, and enhance efficiency. Let's explore how these strategies can streamline C-Class items:
Vendor-Managed Inventory (VMI): VMI is a collaborative approach where the responsibility for managing inventory is shifted to the supplier. Here's how VMI can streamline C-Class inventory:
a. Inventory Monitoring: With VMI, the supplier monitors C-Class inventory levels on behalf of the company. They have access to real-time data and use it to determine when and how much inventory to replenish. This reduces the company's administrative workload and allows for timely restocking.
b. Reduced Stockouts and Overstocking: Suppliers using VMI systems have better visibility into inventory levels and demand patterns. They can proactively replenish stock, reducing the risk of stockouts. At the same time, they can avoid overstocking by adjusting deliveries based on actual usage.
c. Improved Collaboration and Communication: VMI fosters closer collaboration and communication between the company and its suppliers. Sharing inventory data, demand forecasts, and sales information allows for better coordination of supply and demand. This minimizes delays, improves response times, and enhances overall inventory management efficiency.
Consignment Inventory: Consignment inventory involves the supplier maintaining ownership of the inventory until it is consumed or sold by the company. Here's how consignment inventory can streamline C-Class items:
a. Reduced Upfront Costs: With consignment inventory, the company does not pay for the inventory until it is used or sold. This eliminates the need for upfront capital investment in C-Class items, reducing financial risk and improving cash flow.
b. Supplier Responsibility: The supplier retains ownership of the consignment inventory, making them accountable for its management. They ensure proper stock levels, monitor usage, and replenish as necessary. This frees up the company's resources and reduces the administrative burden associated with C-Class inventory management.
c. Inventory Flexibility: Consignment inventory allows companies to adjust inventory levels more easily based on demand fluctuations. As the supplier maintains ownership, the company can adjust inventory quantities without incurring additional costs. This flexibility supports lean inventory practices and helps avoid unnecessary stock holding.
d. Cost Control: Consignment inventory enables better cost control for C-Class items. Companies pay for the inventory only when it is consumed or sold, minimizing holding costs associated with low-value items. This cost-effective approach reduces inventory-related expenses and improves profitability.
It's important to note that both VMI and consignment inventory require strong collaboration and trust between the company and its suppliers. Clear agreements, accurate inventory tracking systems, and effective communication channels are vital for successful implementation.
By implementing VMI and consignment inventory strategies, manufacturing executives can streamline the management of C-Class inventory. These approaches enhance efficiency, reduce administrative burdens, optimize stock levels, and improve cost control. As a result, companies can focus their resources on higher-value activities, reduce inventory-related costs, and enhance overall operational performance.
Highlight the importance of monitoring and replenishing C-class items efficiently
Monitoring and replenishing C-Class items efficiently is crucial for several reasons:
- Cost Optimization: While C-Class items individually have low-value, their collective impact on inventory costs can be significant. Efficient monitoring and replenishment ensure that stock levels align with demand, avoiding unnecessary holding costs associated with excess inventory. By optimizing inventory levels, companies can allocate their resources more effectively and reduce financial strain.
- Avoiding Stockouts: C-Class items may have low usage, but their availability is still important for smooth operations. Stockouts can disrupt production schedules, delay order fulfillment, and result in dissatisfied customers. By monitoring inventory levels closely and replenishing in a timely manner, companies can minimize the risk of stockouts and ensure the availability of C-Class items when needed.
- Preventing Excess Inventory: Overstocking C-Class items ties up working capital and incurs additional holding costs. Excessive inventory can lead to obsolescence, increased warehousing needs, and higher risks of damage or spoilage. Efficient monitoring and replenishment help maintain optimal stock levels, reducing the likelihood of excess inventory and associated costs.
- Lean Inventory Management: Efficient management of C-Class items aligns with lean inventory principles, which aim to minimize waste and improve efficiency. By monitoring and replenishing only what is necessary, companies reduce inventory carrying costs, maximize space utilization, and streamline operations. This lean approach optimizes resource allocation and contributes to overall operational excellence.
- Streamlining Supply Chain Operations: C-Class items may have dependencies within the supply chain. Efficient monitoring and replenishment of these items ensure that downstream processes are not disrupted due to stockouts or delays. Maintaining a well-functioning supply chain relies on the smooth flow of all inventory items, including C-Class items.
- Demand Variability and Seasonality: Even though C-Class items have lower usage, they can still be subject to demand variability and seasonality. Efficient monitoring and replenishment allow companies to adjust stock levels based on changing demand patterns, ensuring that they are prepared for peak periods or unexpected fluctuations in demand.
- Risk Mitigation: Efficient monitoring and replenishment of C-Class items mitigate risks associated with supply chain disruptions or unforeseen events. By closely tracking inventory levels and promptly replenishing, companies can reduce the impact of disruptions, minimize production delays, and ensure continuity in operations.
By implementing effective inventory management practices for C-Class items, companies can achieve operational efficiency, improve customer satisfaction, and enhance their overall competitiveness.
Technology Solutions for Inventory Control
Harnessing the power of technology has become paramount in modern inventory control practices. In this section, we explore various technology solutions that empower manufacturing executives to optimize their inventory management processes.
From advanced software systems to automation tools and data analytics, technology offers unprecedented capabilities for real-time visibility, enhanced accuracy, and streamlined operations. Join us as we delve into the realm of technology solutions for inventory control, uncovering how they revolutionize inventory management, improve decision-making, and drive efficiency.
In this section, we examine cutting-edge technologies, their implementation challenges, and the benefits they bring to manufacturing executives in their quest for effective inventory control. By embracing technology solutions, companies can unlock new levels of operational excellence, gain a competitive edge, and navigate the complexities of inventory management with agility and precision.
Discuss the role of technology in enhancing inventory control processes
Technology plays a pivotal role in enhancing inventory control processes, revolutionizing how manufacturing executives manage and optimize their inventory. Here are key ways in which technology contributes to inventory control:
- Real-Time Visibility: Technology solutions provide real-time visibility into inventory levels, locations, and movements. With barcode scanning, RFID tagging, and advanced tracking systems, companies can accurately monitor stock in real-time. This visibility enables timely decision-making, reduces stockouts, minimizes excess inventory, and improves overall inventory accuracy.
- Automation and Efficiency: Technology automates manual inventory-related tasks, such as data entry, stock counting, and order processing. Automated systems not only eliminate human errors but also streamline processes, saving time and improving efficiency. Automated alerts and notifications can trigger reorder points, ensuring timely replenishment and optimizing stock levels.
- Demand Forecasting and Analytics: Advanced technology solutions enable sophisticated demand forecasting and data analytics. By analyzing historical data, market trends, and customer behavior, companies can make more accurate demand projections. This helps in optimizing inventory levels, improving stock replenishment strategies, and aligning production with anticipated demand.
- Inventory Optimization: Technology offers powerful tools for inventory optimization. Software systems utilize algorithms and optimization models to calculate optimal reorder points, safety stock levels, and economic order quantities. These tools consider factors such as lead time, demand variability, and service level requirements to ensure that inventory levels are optimal and aligned with business objectives.
- Supply Chain Integration: Technology facilitates seamless integration and information sharing within the supply chain. Enterprise Resource Planning (ERP) systems, for example, enable end-to-end visibility and collaboration across various departments, suppliers, and customers. This integration enhances communication, streamlines processes, and facilitates effective inventory management across the entire supply chain network.
- Mobile and Cloud Solutions: Mobile applications and cloud-based platforms provide anytime, anywhere access to inventory information. Executives and inventory managers can monitor inventory, place orders, and track stock levels remotely. Cloud-based solutions also offer scalability, data security, and real-time updates, enabling agile and flexible inventory control.
- Predictive Analytics and AI: Advanced technologies like Artificial Intelligence (AI) and machine learning algorithms can analyze vast amounts of data to predict demand patterns, identify anomalies, and optimize inventory management. These predictive analytics capabilities help in proactive decision-making, reducing stockouts, and mitigating risks associated with inventory management.
By leveraging technology in inventory control processes, manufacturing executives can achieve greater accuracy, efficiency, and agility. The real-time visibility, automation, demand forecasting, inventory optimization, supply chain integration, mobile accessibility, and predictive analytics capabilities offered by technology solutions empower companies to make informed decisions, respond quickly to changing market demands, minimize costs, and achieve operational excellence.
Embracing technology in inventory control is no longer a luxury but a necessity in today's competitive landscape.
Explore inventory management software, barcode systems, and RFID technology
Inventory management software, barcode systems, and RFID (Radio Frequency Identification) technology are powerful tools that revolutionize inventory control processes. Let's explore each of these technologies:
Inventory Management Software: Inventory management software is a comprehensive solution that automates and streamlines inventory-related tasks. It offers a centralized platform to manage and track inventory, sales, orders, and suppliers. Key features and benefits include:
- Real-time Inventory Tracking: Inventory management software provides real-time visibility into stock levels, locations, and movements. It allows companies to accurately monitor inventory across multiple warehouses or locations, reducing stockouts and optimizing replenishment.
- Demand Forecasting and Analysis: Advanced software systems employ data analytics to forecast demand, analyze sales patterns, and identify trends. This helps in making informed decisions about inventory levels, production planning, and demand fulfillment.
- Order Management: Inventory software streamlines order processing, automates order fulfillment, and tracks order status. It enhances efficiency, reduces errors, and ensures timely delivery to customers.
- Supplier Management: The software facilitates supplier collaboration, automates purchase orders, and tracks supplier performance. It streamlines procurement processes, optimizes vendor relationships, and improves supply chain efficiency.
- Reporting and Analytics: Inventory management software generates comprehensive reports and analytics to monitor key performance indicators (KPIs), such as inventory turnover, stock accuracy, and fill rates. This data-driven approach enhances decision-making and enables continuous improvement.
Barcode Systems: Barcode systems are widely used for efficient and accurate inventory management. Barcodes consist of a series of parallel lines and numbers encoded with product information. Key benefits of barcode systems include:
- Efficient Data Entry: Barcodes eliminate manual data entry by scanning product information, reducing human errors and improving data accuracy.
- Inventory Tracking: Barcodes enable quick and accurate tracking of inventory movements, from receiving to storage, picking, and shipping. This enhances visibility, reduces errors, and improves overall inventory control.
- Stock Replenishment: Barcode systems streamline the replenishment process by scanning barcode labels on products or storage bins, triggering automatic reorder points, and optimizing stock levels.
- Warehouse Efficiency: Barcodes are used in conjunction with handheld scanners, enabling warehouse personnel to easily locate and pick items, reducing time and increasing efficiency.
RFID Technology: RFID technology uses radio waves to automatically identify and track objects. It offers several advantages over barcode systems:
- Increased Speed and Range: RFID tags can be read from a distance and do not require direct line-of-sight scanning. This enables faster and more convenient inventory tracking, especially in large warehouses or distribution centers.
- Batch Scanning: RFID technology allows multiple tags to be read simultaneously, speeding up inventory counts and reducing manual effort.
- Real-time Tracking: RFID tags can be continuously tracked, providing real-time visibility into inventory movements and reducing the chances of stockouts or misplaced items.
- Asset Security: RFID technology can be used for anti-theft measures by setting up RFID-based access control systems or triggering alerts when tagged items leave designated areas.
- Integration with Inventory Systems: RFID technology can seamlessly integrate with inventory management software, providing a holistic view of inventory and enabling automated data capture and analysis.
Implementing inventory management software, barcode systems, and RFID technology offers significant advantages in terms of efficiency, accuracy, and visibility in inventory control processes. These technologies empower manufacturing executives to make informed decisions, optimize stock levels, reduce costs, and enhance overall operational performance.
Highlight the benefits of real-time data, automation, and analytics in inventory control
Real-time data, automation, and analytics in inventory control bring numerous benefits to manufacturing executives. Let's explore the advantages of these key elements:
Real-Time Data
- Enhanced Visibility: Real-time data provides up-to-the-minute information on inventory levels, movements, and stock locations. It enables manufacturing executives to have a clear and accurate view of their inventory at any given time, facilitating better decision-making.
- Timely Decision-Making: Real-time data empowers executives to make quick and informed decisions based on the most recent information. It helps identify stock shortages, anticipate demand fluctuations, and respond promptly to changing market conditions.
- Improved Inventory Accuracy: Real-time data minimizes errors and discrepancies in inventory records. It enables instant updates when inventory is received, moved, or sold, reducing the risk of stockouts or overstocking due to outdated information.
- Efficient Replenishment: With real-time data, executives can set up automated triggers for reorder points and replenishment. This ensures timely restocking, avoids stockouts, and optimizes stock levels based on actual demand.
Automation
- Streamlined Processes: Automation reduces manual effort and streamlines inventory-related tasks such as data entry, order processing, and stock counting. It minimizes errors, improves efficiency, and frees up time for employees to focus on higher-value activities.
- Increased Accuracy: Automation reduces human errors associated with manual data entry or calculation. It eliminates the risk of transcription errors, miscounts, or misplaced decimal points, leading to more accurate inventory records and reducing costly mistakes.
- Time and Cost Savings: By automating repetitive tasks, manufacturing executives can significantly save time and reduce operational costs. Employees can be redeployed to more strategic roles, maximizing productivity and overall efficiency.
- Consistency and Standardization: Automation ensures consistency and standardization in inventory control processes. It enforces predefined rules and workflows, minimizing variations and maintaining data integrity across the organization.
Analytics
- Data-Driven Decision-Making: Analytics leverages historical and real-time data to provide actionable insights for inventory control. By analyzing trends, patterns, and correlations, executives can make data-driven decisions regarding stock levels, demand forecasting, and supply chain optimization.
- Improved Forecasting Accuracy: Analytics helps in demand forecasting by identifying seasonality, trends, and other demand patterns. It enables executives to make more accurate predictions, reducing the risk of stockouts or excessive inventory.
- Optimal Inventory Levels: Analytics enables executives to determine optimal inventory levels based on factors such as lead time, demand variability, and service level requirements. This helps balance inventory costs with customer satisfaction and ensures efficient stock management.
- Continuous Improvement: Analytics provides valuable performance metrics and KPIs for inventory control. It enables executives to monitor key indicators, identify areas for improvement, and track the impact of implemented strategies. This fosters a culture of continuous improvement in inventory management.
By harnessing real-time data, automation, and analytics, manufacturing executives can gain better control over their inventory, make informed decisions, improve efficiency, and optimize stock levels. These elements contribute to improved customer service, reduced costs, enhanced operational performance, and a competitive edge in the market.
Collaborative Supply Chain Management
In today's interconnected and globalized business landscape, collaborative supply chain management has emerged as a critical strategy for manufacturing executives. This section explores the power of collaboration within the supply chain and its profound impact on inventory control and overall operational success.
From supplier partnerships and information sharing to joint planning and synchronized production, collaborative supply chain management fosters a cohesive ecosystem where all stakeholders work together towards shared goals. Join us as we delve into the realm of collaborative supply chain management, uncovering the benefits, challenges, and best practices that empower manufacturing executives to optimize inventory control, enhance efficiency, and drive sustainable growth.
In this section, we explore the importance of collaboration, the technologies enabling seamless communication, and the strategies for building strong relationships across the supply chain.
Importance of collaboration with suppliers and partners for effective inventory control
Collaboration with suppliers and partners is paramount for effective inventory control in today's dynamic business environment. Here are key reasons why collaboration is crucial:
- Enhanced Supply Chain Visibility: Collaborative relationships with suppliers and partners provide increased visibility into the supply chain. Sharing real-time data, forecasts, and inventory information enables better demand planning, inventory optimization, and risk mitigation. It helps identify potential bottlenecks, anticipate disruptions, and make informed decisions to ensure timely availability of materials and products.
- Improved Demand Forecasting: Collaborating closely with suppliers and partners allows for a holistic understanding of market trends, customer preferences, and demand patterns. By sharing insights and aligning forecasts, manufacturing executives can improve the accuracy of demand forecasting. This leads to optimized inventory levels, reduced stockouts, and improved customer satisfaction.
- Streamlined Inventory Replenishment: Collaboration facilitates efficient inventory replenishment processes. By establishing effective communication channels and implementing collaborative planning systems, executives can automate and synchronize order placement, inventory replenishment, and production schedules. This minimizes lead times, reduces excess inventory, and ensures the right products are available at the right time.
- Risk Mitigation and Resilience: Collaborative relationships enable proactive risk management. By sharing information and working together, companies can collectively identify and address potential risks, such as supply chain disruptions, market fluctuations, or regulatory changes. Collaborative approaches like joint contingency planning and alternate sourcing strategies help build resilience and minimize the impact of unforeseen events on inventory control.
- Innovation and Continuous Improvement: Collaboration fosters innovation and continuous improvement in inventory control processes. By engaging with suppliers and partners, manufacturing executives can exchange ideas, share best practices, and explore new technologies or strategies. Collaborative initiatives such as joint product development or shared inventory optimization programs drive innovation, streamline processes, and deliver mutual benefits.
- Cost Reduction and Efficiency: Collaboration can result in cost reductions and improved efficiency throughout the supply chain. By working together to streamline processes, eliminate redundancies, and optimize logistics, companies can reduce lead times, inventory carrying costs, and overall operational expenses. Collaborative efforts also enable economies of scale, volume discounts, and shared resources, resulting in cost savings for all stakeholders.
- Customer Satisfaction: Effective inventory control is closely tied to meeting customer demands. Collaborating with suppliers and partners ensures timely availability of products, reduces lead times, and improves order fulfillment accuracy. This leads to increased customer satisfaction, loyalty, and repeat business.
Collaboration becomes a catalyst for optimizing inventory management processes and building a resilient supply chain that can adapt to ever-changing market dynamics.
Strategies such as vendor collaboration, supplier scorecards, and shared forecasts
To foster effective collaboration with suppliers and partners for inventory control, manufacturing executives can implement various strategies. Here are three key strategies:
Vendor Collaboration: Vendor collaboration involves establishing a close working relationship with suppliers to enhance inventory control. This includes sharing information, aligning goals, and jointly addressing challenges. Key aspects of vendor collaboration include:
- Open Communication: Regular and transparent communication channels enable the exchange of vital information such as inventory levels, demand forecasts, and production plans. This promotes better coordination, enables proactive decision-making, and minimizes inventory discrepancies.
- Joint Planning: Collaborative planning involves working together with suppliers to align production schedules, lead times, and order quantities. By synchronizing activities, executives can optimize inventory levels, reduce stockouts, and improve overall supply chain efficiency.
- Supplier Performance Evaluation: Evaluating supplier performance based on metrics like on-time delivery, product quality, and responsiveness helps identify areas for improvement. Collaborative discussions and feedback sessions enable both parties to enhance performance and address any issues promptly.
Supplier Scorecards: Supplier scorecards provide a structured approach to assess and monitor supplier performance. By measuring key performance indicators (KPIs) and setting performance targets, executives can ensure accountability and drive continuous improvement. Key elements of supplier scorecards include:
- Performance Metrics: Identify relevant KPIs such as delivery reliability, lead time compliance, product quality, and responsiveness. These metrics provide a quantitative basis for evaluating supplier performance.
- Regular Monitoring: Establish a regular review process to track supplier performance against defined metrics. This enables proactive identification of any deviations and facilitates timely corrective actions.
- Feedback and Collaboration: Supplier scorecards should not be one-sided evaluations. They should serve as a basis for constructive feedback and collaboration. Engage in discussions with suppliers to jointly identify improvement opportunities and implement corrective actions.
Shared Forecasts: Shared forecasts involve collaborative demand planning and forecasting between manufacturers and suppliers. By sharing insights and data, both parties can align their production and inventory plans. Key elements of shared forecasts include:
- Data Sharing: Exchange historical sales data, market trends, and customer insights with suppliers. This shared information helps suppliers understand demand patterns and adjust their production accordingly.
- Collaborative Forecasting: Collaboratively develop demand forecasts based on shared insights and data. Involve suppliers in the forecasting process to obtain their input and expertise, ensuring more accurate predictions.
- Demand Variability Considerations: Collaborative forecasting helps manage demand variability by jointly identifying and addressing factors that may impact demand, such as seasonality, promotions, or new product launches.
Implementing these strategies fosters closer collaboration with suppliers and partners, leading to improved inventory control. By working together through vendor collaboration, implementing supplier scorecards, and embracing shared forecasts, manufacturing executives can optimize inventory levels, reduce lead times, enhance supply chain efficiency, and ultimately deliver superior customer satisfaction.
Benefits of collaborative supply chain management, including reduced lead times and improved inventory accuracy
Collaborative supply chain management offers several benefits that positively impact inventory control. Here are two key advantages:
Reduced Lead Times: Collaboration within the supply chain enables the reduction of lead times, which refers to the time taken from placing an order to receiving the goods. By working closely with suppliers and partners, manufacturing executives can streamline processes, improve communication, and eliminate bottlenecks. This leads to:
- Faster Response to Market Demands: Collaborative supply chain management allows for real-time information sharing and demand visibility. It enables executives to respond swiftly to changes in customer demand, market trends, or unforeseen events. By aligning production schedules, coordinating inventory replenishment, and optimizing logistics, lead times can be significantly reduced.
- Improved Speed to Market: Effective collaboration with suppliers and partners facilitates efficient product development cycles. By involving suppliers early in the design and planning stages, manufacturers can leverage their expertise and reduce time-consuming iterations. This accelerates the time to market, ensuring products reach customers faster.
- Agile and Responsive Operations: Collaborative supply chain management supports agile practices, enabling rapid adjustments to production and inventory plans. By sharing forecasts, demand insights, and production capabilities, executives can make informed decisions to meet fluctuating market demands, reducing lead times and maintaining competitiveness.
Improved Inventory Accuracy: Collaboration enhances inventory accuracy, ensuring that the right inventory is available at the right time. Key benefits include:
- Enhanced Demand Forecasting: By collaborating closely with suppliers and partners, manufacturers gain access to valuable insights and data. This enables more accurate demand forecasting by considering market trends, customer preferences, and supply chain dynamics. Improved forecasting accuracy leads to optimized inventory levels, reducing the risk of stockouts or excessive inventory.
- Reduced Inventory Carrying Costs: Collaborative supply chain management helps align production schedules and inventory levels with actual demand. By avoiding overstocking and eliminating excessive safety stock, manufacturers can significantly reduce inventory carrying costs. This frees up working capital and improves overall financial performance.
- Efficient Order Fulfillment: Collaboration enables real-time visibility into inventory levels, both within the organization and across the supply chain. This visibility facilitates effective order management, allowing for quicker order processing, accurate order promising, and on-time deliveries. As a result, customer satisfaction improves while minimizing inventory write-offs or obsolescence.
- Inventory Optimization: Collaborative supply chain management supports the optimization of inventory levels throughout the supply chain. By aligning production plans, sharing demand forecasts, and coordinating inventory replenishment, excess inventory is minimized while maintaining adequate stock levels. This leads to improved inventory accuracy and avoids the costs associated with stockouts or excess holding.
By embracing collaborative supply chain management, manufacturing executives can realize reduced lead times, which enable faster response to market demands and improved speed to market.
Additionally, improved inventory accuracy allows for better demand forecasting, reduced inventory carrying costs, efficient order fulfillment, and optimized inventory levels. These benefits contribute to enhanced customer satisfaction, increased operational efficiency, and a competitive advantage in the market.
Continuous Improvement and Evaluation
Continuous Improvement and evaluation play a vital role in the realm of inventory control for manufacturing executives. This section focuses on the importance of ongoing improvement initiatives and the evaluation of inventory control strategies.
From performance measurement and data analysis to process refinement and employee involvement, continuous improvement and evaluation ensure that inventory control remains effective, efficient, and aligned with organizational goals.
In this section, we delve into need and importance to foster a culture of continuous improvement. Thus, empowering manufacturing executives to stay ahead of the competition and continuously enhance their inventory control practices.
The need for continuous improvement in inventory control processes
Continuous improvement in inventory control processes is not just desirable but essential for the success of manufacturing operations. Here are key reasons why continuous improvement is crucial:
Efficiency and Productivity: Continuous improvement allows organizations to streamline their inventory control processes, eliminating waste and inefficiencies. By regularly evaluating and refining procedures, executives can identify areas for improvement and implement changes that enhance efficiency and productivity. This leads to optimized resource utilization, reduced lead times, and increased throughput.
Cost Optimization: Effective inventory control directly impacts the bottom line. Continuous improvement helps identify cost-saving opportunities, such as reducing holding costs, minimizing excess inventory, and improving supply chain efficiency. By continuously evaluating processes and implementing improvements, manufacturing executives can achieve cost optimization and maximize profitability.
Customer Satisfaction: Inventory control directly affects customer satisfaction. Continuous improvement ensures that the right products are available at the right time, reducing stockouts and enhancing order fulfillment. By consistently meeting customer demands and expectations, organizations can build strong relationships, improve customer loyalty, and gain a competitive edge in the market.
Adaptability to Changing Market Conditions: Market dynamics are constantly evolving, and inventory control processes must adapt accordingly. Continuous improvement enables organizations to stay agile and responsive to changing customer demands, market trends, and industry disruptions. By regularly evaluating and adjusting inventory control strategies, executives can effectively navigate uncertainties and maintain a competitive advantage.
Quality Assurance: Continuous improvement promotes quality assurance in inventory control. By implementing robust quality control measures, conducting regular audits, and addressing root causes of errors or defects, organizations can ensure accurate inventory records and deliver high-quality products to customers. This focus on quality enhances customer satisfaction and strengthens the brand reputation.
Innovation and Growth: Continuous improvement fosters a culture of innovation and growth within an organization. By encouraging employees to contribute ideas and suggestions for process improvement, executives can tap into their expertise and harness their creativity. This leads to the development of innovative inventory control practices, adoption of new technologies, and identification of strategic growth opportunities.
Risk Management: Continuous improvement plays a crucial role in risk management. By regularly evaluating and addressing potential risks and vulnerabilities in inventory control processes, organizations can mitigate the impact of disruptions, minimize supply chain risks, and ensure business continuity. Proactive risk management reduces the likelihood of costly disruptions and enhances organizational resilience.
Importance of regular evaluation, data analysis, and performance metrics
Regular evaluation, data analysis, and performance metrics play a vital role in the success of inventory control processes. Here's why they are important:
Performance Measurement: Regular evaluation allows organizations to measure the performance of their inventory control processes. By establishing key performance indicators (KPIs) and metrics, manufacturing executives can assess the effectiveness and efficiency of their operations. Performance measurement provides insights into areas of improvement, identifies bottlenecks, and highlights strengths and weaknesses in inventory control.
Data-Driven Decision Making: Data analysis is essential for informed decision making in inventory control. By collecting and analyzing relevant data, executives can gain valuable insights into inventory levels, demand patterns, supplier performance, and other critical factors. Data-driven decision making ensures that inventory control strategies are based on accurate and up-to-date information, leading to more effective and efficient operations.
Continuous Improvement: Regular evaluation and data analysis facilitate continuous improvement in inventory control processes. By reviewing performance metrics and analyzing data, organizations can identify areas for enhancement and implement changes to optimize processes. This iterative approach allows for ongoing refinement and ensures that inventory control practices remain aligned with organizational goals and industry best practices.
Identifying Efficiency Gaps: Evaluation and data analysis help identify gaps in efficiency within inventory control processes. By examining the flow of materials, information, and resources, organizations can pinpoint areas of inefficiency or waste. This enables executives to implement targeted improvements, streamline workflows, and eliminate unnecessary steps, resulting in improved operational efficiency and cost savings.
Benchmarking and Best Practices: Evaluation and data analysis allow organizations to benchmark their inventory control processes against industry best practices and standards. By comparing performance metrics with industry benchmarks, executives can identify areas where they excel or lag behind. This insight enables the adoption of proven strategies and best practices, leading to improved inventory control performance and a competitive edge.
Proactive Problem Identification: Regular evaluation and data analysis help in identifying potential problems or risks in inventory control processes before they escalate. By monitoring performance metrics and analyzing trends, executives can detect deviations or anomalies that may indicate issues such as inventory inaccuracies, supplier delays, or demand fluctuations. Proactive problem identification allows for timely interventions and mitigates the risk of disruptions.
Continuous Adaptation to Changing Conditions: Evaluation and data analysis enable organizations to adapt to changing market conditions and customer demands. By monitoring performance metrics and analyzing data, executives can identify shifts in market trends or customer preferences. This information helps in adjusting inventory control strategies, optimizing stock levels, and aligning operations with evolving market dynamics.
Role of feedback loops and Kaizen principles in driving ongoing improvements
Feedback loops and Kaizen principles play a crucial role in driving ongoing improvements in inventory control processes. Here's how they contribute to continuous enhancement:
Feedback Loops
Feedback loops are mechanisms that capture and incorporate feedback from various stakeholders in the inventory control process. This includes feedback from customers, suppliers, employees, and other relevant parties.
Feedback loops allow organizations to gather valuable insights, identify areas for improvement, and address issues in a timely manner. By actively seeking and integrating feedback, executives can make informed decisions and drive continuous improvement in inventory control.
Continuous Learning
Kaizen, a Japanese term meaning "continuous improvement," is a principle that encourages a culture of ongoing learning and innovation. It emphasizes the idea that small, incremental changes made consistently over time can result in significant improvements.
Kaizen principles promote the involvement of employees at all levels of the organization in identifying opportunities for improvement and implementing changes. By embracing Kaizen, manufacturing executives foster a culture of continuous learning, encourage employee engagement, and empower individuals to contribute to the ongoing improvement of inventory control processes.
Problem-Solving Approach
Feedback loops and Kaizen principles promote a problem-solving approach to inventory control. They encourage organizations to identify root causes of issues, rather than just addressing symptoms.
By using techniques such as root cause analysis, process mapping, and brainstorming, executives can systematically analyze problems and implement sustainable solutions. This approach ensures that improvements are targeted, effective, and address underlying issues, leading to long-term success in inventory control.
Employee Empowerment: Feedback loops and Kaizen principles empower employees to actively participate in the improvement process. By involving employees in problem-solving activities, organizations tap into their expertise, creativity, and firsthand knowledge of day-to-day operations.
This involvement fosters a sense of ownership, accountability, and commitment to continuously improving inventory control processes. Empowered employees become active contributors to the ongoing enhancement of processes and are more likely to embrace change and drive innovation.
Iterative Improvement: Feedback loops and Kaizen principles promote an iterative approach to improvement. Rather than seeking a one-time fix, organizations continuously evaluate, refine, and optimize inventory control processes.
This iterative improvement cycle allows for gradual enhancements based on real-time data, feedback, and changing business conditions. It ensures that inventory control processes remain adaptable, responsive, and aligned with organizational goals.
Culture of Continuous Improvement: Feedback loops and Kaizen principles help foster a culture of continuous improvement within an organization. By consistently seeking feedback, encouraging open communication, and recognizing and rewarding innovative ideas, executives create an environment where continuous improvement becomes ingrained in the organizational DNA.
This cultural shift promotes a proactive mindset, encourages collaboration, and fuels the drive for ongoing enhancements in inventory control processes.
By embracing these principles, manufacturing executives can leverage the collective intelligence and creativity of their workforce, respond to changing market dynamics, and continuously enhance inventory control practices to achieve operational excellence and competitive advantage.
Importance of Implementing these Strategies for Cost Reduction and Operational Efficiency
Implementing strategies such as feedback loops, Kaizen principles, and continuous improvement in inventory control processes is of utmost importance for achieving cost reduction and operational efficiency in manufacturing organizations. These strategies directly contribute to the bottom line by optimizing inventory management practices and streamlining operations.
By continuously evaluating and refining processes, organizations can identify and eliminate inefficiencies, reduce waste, and optimize resource utilization. This leads to significant cost savings in terms of reduced holding costs, lower inventory carrying costs, and minimized stockouts or overstocking.
Furthermore, these strategies enhance operational efficiency by promoting a culture of ongoing learning, problem-solving, and employee empowerment. The implementation of feedback loops allows organizations to capture valuable insights from various stakeholders, enabling them to identify areas for improvement and address issues promptly.
The involvement of employees at all levels fosters a sense of ownership, accountability, and commitment to continuous improvement. This results in enhanced collaboration, increased employee engagement, and the generation of innovative ideas that drive operational efficiency.
Moreover, the Kaizen principles of continuous improvement encourage organizations to adopt a proactive mindset and seek incremental changes that collectively lead to significant improvements over time. By consistently evaluating performance metrics, analyzing data, and benchmarking against industry best practices, organizations can identify opportunities for optimization and make data-driven decisions.
This enables them to respond to changing market dynamics, customer demands, and technological advancements, staying agile and competitive.
Implementing these strategies also helps in reducing lead times, improving order fulfillment, and enhancing customer satisfaction. By aligning production with accurate demand forecasting and adopting lean manufacturing principles, organizations can ensure timely availability of materials, reduce cycle times, and minimize stockouts. This results in improved customer service levels, increased customer loyalty, and a positive brand image.
Overall, the implementation of feedback loops, Kaizen principles, and continuous improvement in inventory control processes is essential for achieving cost reduction and operational efficiency. These strategies not only drive tangible cost savings but also foster a culture of continuous learning, employee engagement, and innovation. Why Should Manufacturing executives prioritize inventory control and adapt their processes for optimal outcomes?
Conclusion
In conclusion, effective inventory control is a critical component of successful manufacturing operations, and implementing the ABC strategies discussed in this article is essential for manufacturing executives. By categorizing inventory items into A, B, and C groups based on their value and usage, executives can prioritize their focus and allocate resources accordingly.
Managing A-class inventory items, which are high-value and high-usage, requires accurate demand forecasting, alignment of production with demand, and the implementation of techniques like just-in-time (JIT) and lean manufacturing.
Balancing B-class inventory, which is moderate in value and usage, involves maintaining optimal stock levels without excessive holding costs. Strategies like economic order quantity (EOQ) and safety stock play a crucial role in achieving this balance. Streamlining C-class inventory, which consists of low-value and low-usage items, involves efficient management and strategies like vendor-managed inventory (VMI) and consignment inventory.
Leveraging technology solutions such as inventory management software, barcode systems, and RFID technology enhances inventory control processes by providing real-time data, automation, and analytics. Collaborative supply chain management, including vendor collaboration, supplier scorecards, and shared forecasts, strengthens relationships and improves inventory accuracy.
Continuous improvement and evaluation, driven by feedback loops, Kaizen principles, and data analysis, ensure ongoing enhancements in cost reduction, operational efficiency, and customer satisfaction.
Embracing the ABCs of inventory control empowers executives to make informed decisions, adapt to market changes, and drive sustainable growth for their organizations.
How can Deskera Help You?
Deskera ERP and MRP systems help you to keep your business units organized. The system's primary functions are as follows:
- Keep track of your raw materials and final items inventories
- Control production schedules and routings
- Keep a bill of materials
- Produce thorough reports
- Make your own dashboards
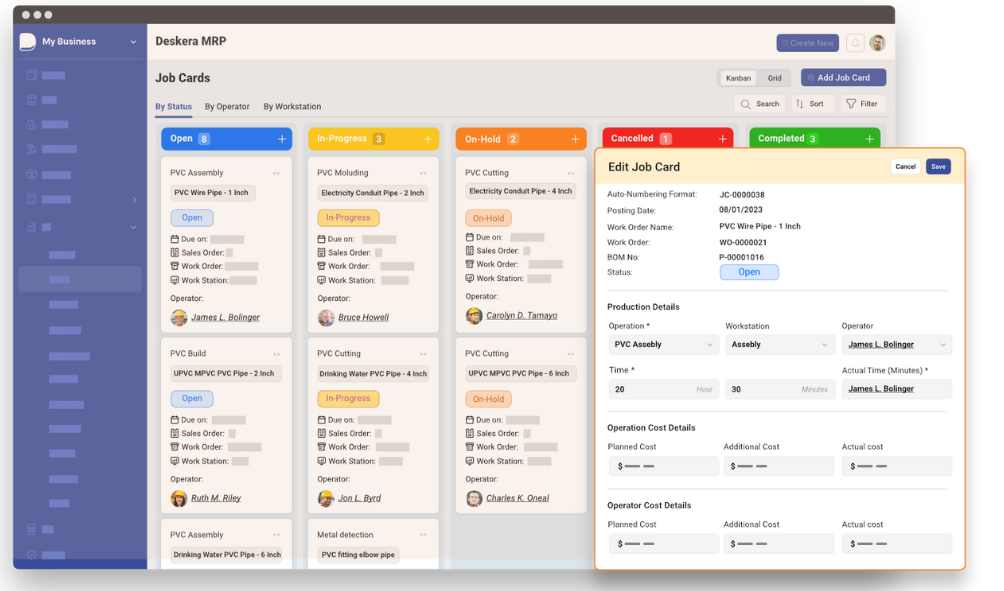
Deskera's integrated financial planning tools enable investors to better plan and track their investments. It can assist investors in making faster and more accurate decisions.
Deskera Books allows you to better manage your accounts and finances. Maintain good accounting practices by automating tasks like billing, invoicing, and payment processing.
Deskera CRM is a powerful solution that manages your sales and helps you close deals quickly. It not only enables you to perform critical tasks like lead generation via email, but it also gives you a comprehensive view of your sales funnel.
Deskera People is a straightforward tool for centralizing your human resource management functions.
Key Takeaways
- Inventory control is crucial for manufacturing executives to optimize operations, reduce costs, and improve efficiency.
- Categorizing inventory items into A, B, and C groups based on their value and usage helps prioritize resources and focus efforts.
- Managing A-class inventory items requires accurate demand forecasting, production alignment, and techniques like JIT and lean manufacturing.
- Balancing B-class inventory involves maintaining optimal stock levels without excessive holding costs, utilizing strategies like EOQ and safety stock.
- Streamlining C-class inventory, consisting of low-value and low-usage items, requires efficient management and strategies like VMI and consignment inventory.
- Technology solutions such as inventory management software, barcode systems, and RFID technology enhance inventory control by providing real-time data, automation, and analytics.
- Collaborative supply chain management, including vendor collaboration, supplier scorecards, and shared forecasts, improves inventory accuracy and reduces lead times.
- Continuous improvement and evaluation through feedback loops, Kaizen principles, and data analysis drive ongoing enhancements in cost reduction, operational efficiency, and customer satisfaction.
- Regular evaluation, data-driven decision making, and benchmarking against industry best practices are essential for successful inventory control.
- The implementation of these strategies empowers manufacturing executives to optimize inventory control, adapt to market changes, and drive sustainable growth in the manufacturing industry.
Related Articles
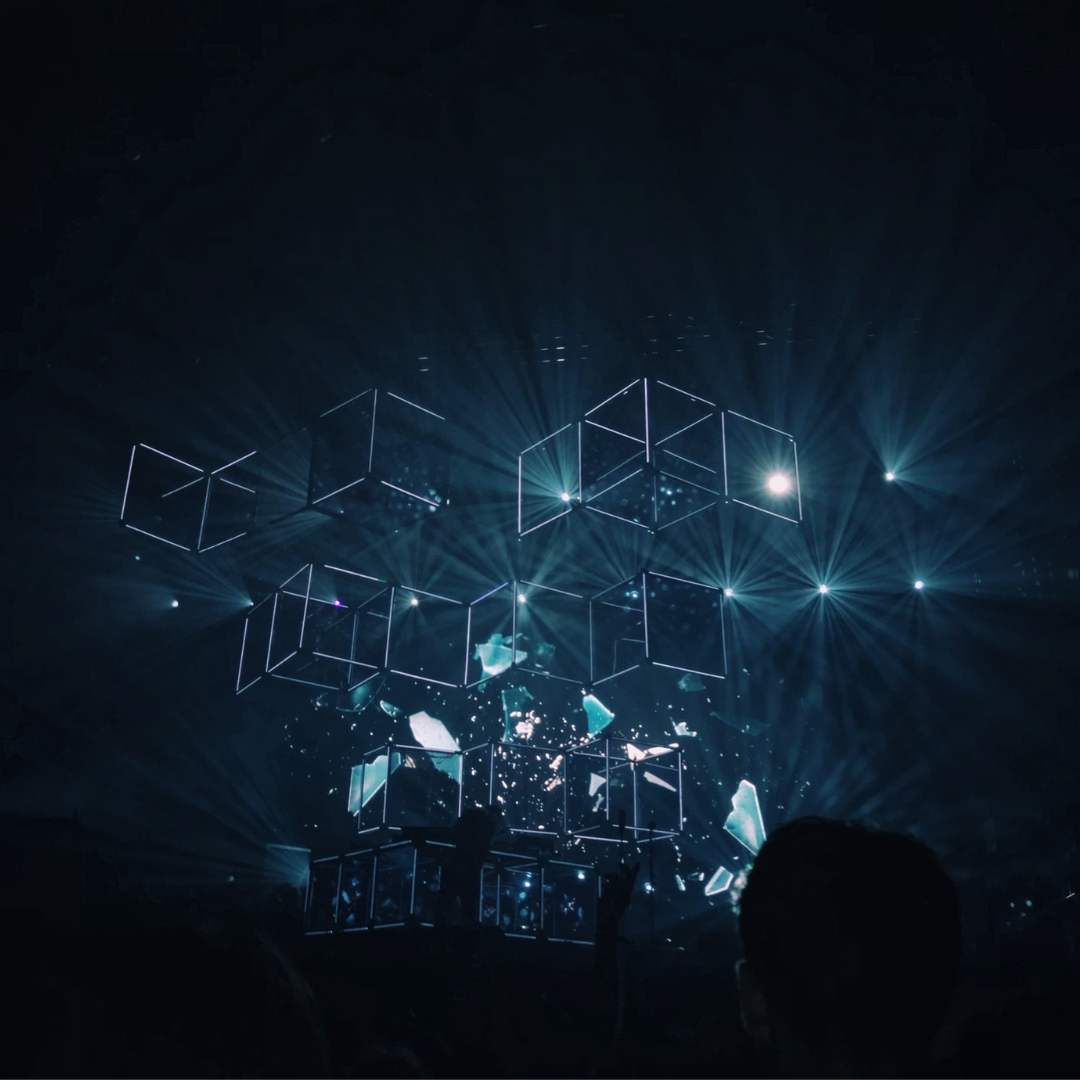
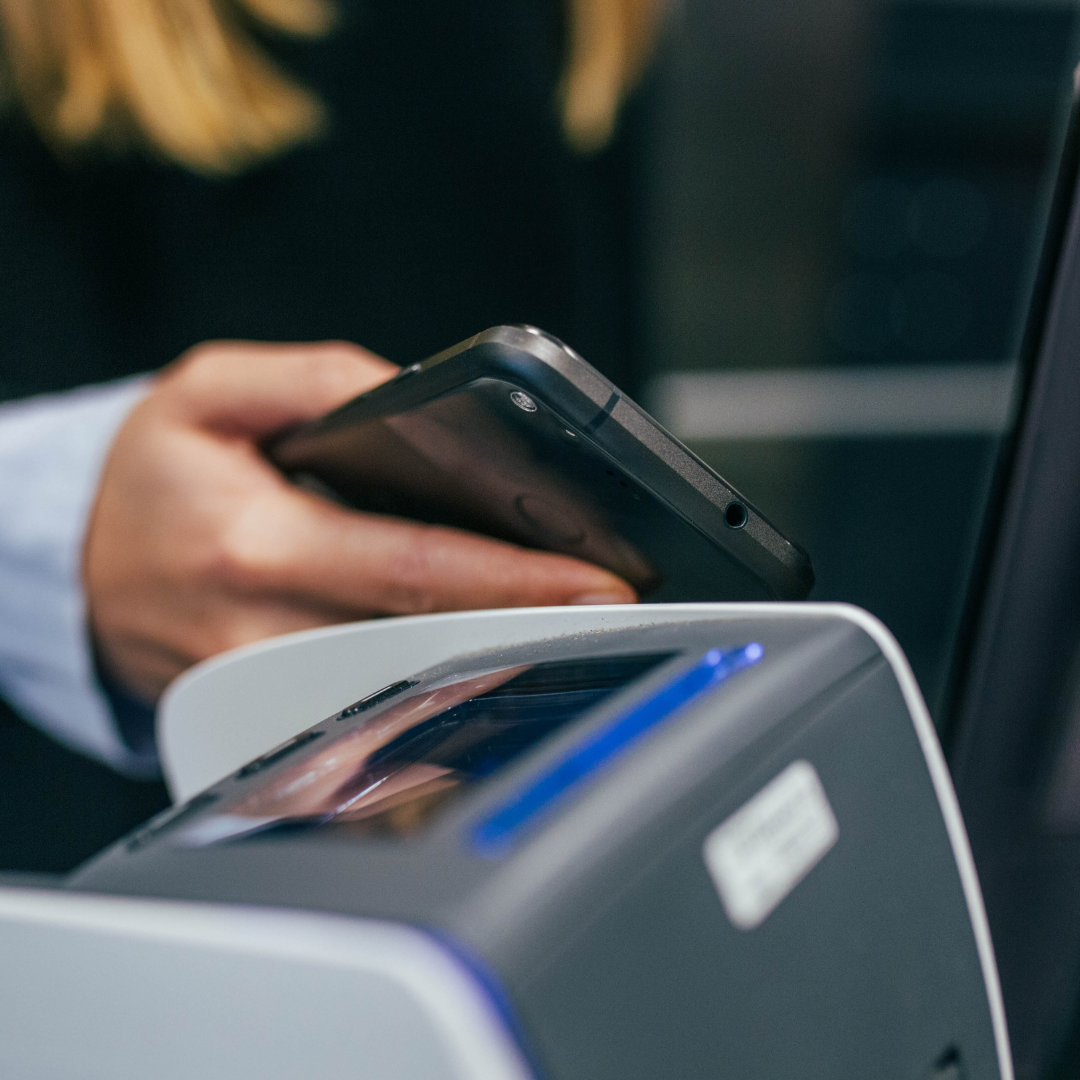
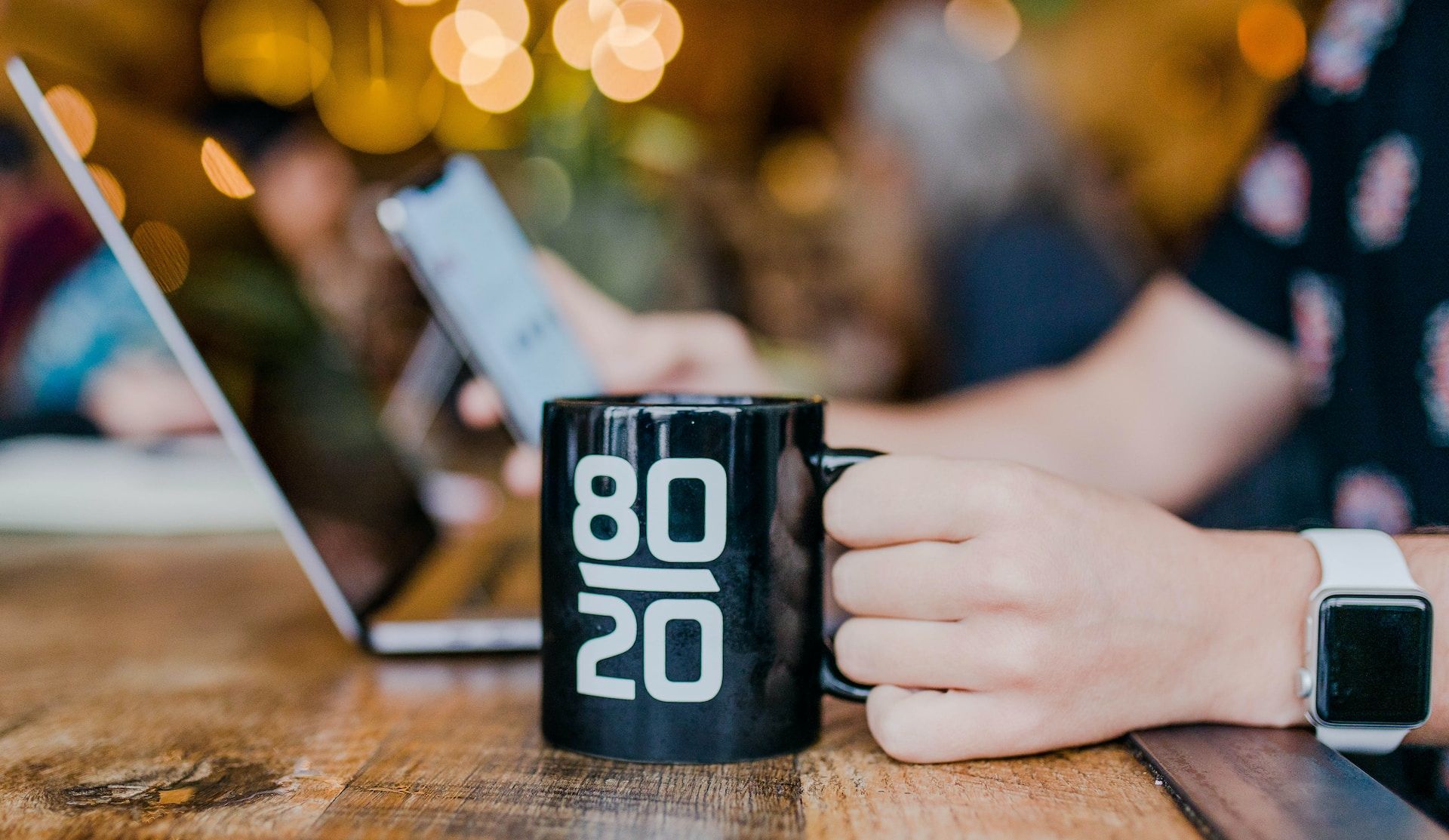
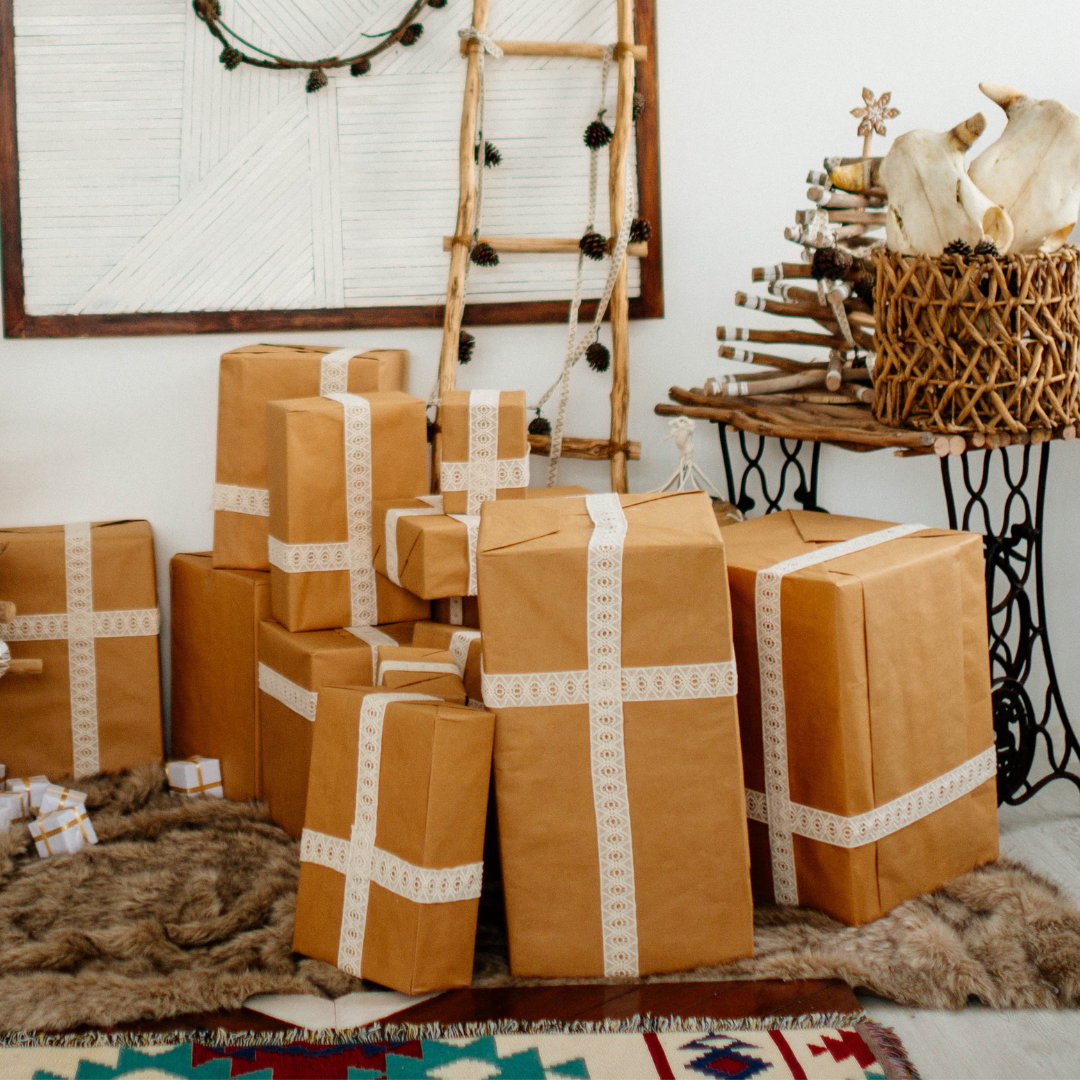