In today's highly competitive business environment, efficiency is key. Did you know that implementing a Just-in-time (JIT) inventory system can reduce costs by up to 25%, according to a study by the International Federation of Accountants? This striking statistic highlights the significant impact JIT inventory can have on a company's bottom line.
Just-in-time (JIT) inventory is a management strategy that aligns raw-material orders from suppliers directly with production schedules. Developed and perfected by Toyota, this method aims to increase efficiency and decrease waste by receiving goods only as they are needed in the production process. This approach minimizes inventory costs and ensures a lean production cycle.
Understanding JIT is crucial for modern inventory management because it helps businesses operate more efficiently, reduce storage costs, and respond quickly to market demands. By implementing JIT, companies can avoid the pitfalls of overstocking and understocking, ensuring they meet customer needs without tying up capital in unnecessary inventory.
For businesses looking to integrate JIT principles seamlessly, Deskera ERP offers a robust solution. Deskera ERP supports JIT inventory management with features like real-time inventory tracking, demand forecasting, and automated reordering.
These capabilities help businesses maintain optimal inventory levels, reduce waste, and enhance overall operational efficiency. With Deskera ERP, companies can not only implement JIT effectively but also streamline their entire supply chain process, driving significant cost savings and operational improvements.
What is Just-in-time (JIT) Inventory?
Just-in-time (JIT) inventory is a highly efficient inventory management strategy that aims to streamline production processes and minimize waste by receiving goods only as they are needed in the production cycle. This method, first developed by Toyota, has become a cornerstone of modern manufacturing and inventory management.
JIT inventory management involves carefully planning and coordinating the arrival of raw materials and components to coincide perfectly with production schedules.
This eliminates the need for large stockpiles of inventory, reducing storage costs and the risk of obsolescence. By implementing JIT, businesses can optimize their inventory levels, ensuring they have just enough to meet current demand without overstocking.
Key Concepts and Principles
- Demand-Driven Supply Chain: JIT is inherently demand-driven, meaning production is based on actual customer orders rather than forecasts. This approach minimizes excess inventory and reduces the risk of unsold goods.
- Continuous Improvement: JIT emphasizes continuous improvement (kaizen) in all aspects of production and inventory management. This involves regularly reviewing and refining processes to enhance efficiency and reduce waste.
- Strong Supplier Relationships: Successful JIT implementation requires strong, reliable relationships with suppliers who can deliver materials quickly and consistently.
How Does Just-in-time (JIT) Inventory Work?
Just-in-time (JIT) inventory management is a strategy designed to increase efficiency and reduce waste by receiving goods only as they are needed in the production process. This method ensures that inventory levels are kept to a minimum, and production schedules are tightly aligned with demand.
Here's a closer look at how JIT inventory works:
Process Explanation
JIT inventory operates on the principle of synchronizing the arrival of raw materials and components with the production schedules.
Here’s a step-by-step breakdown of the JIT process:
1.Demand Signal: The process begins with a customer order or a demand signal. This signal triggers the production process, ensuring that production is directly aligned with actual customer demand.
2.Production Planning: Based on the demand signal, production planning is conducted. This involves determining the exact quantities of materials required for the production run. JIT inventory management ensures that only the necessary amount of materials is ordered, minimizing excess inventory.
3.Supplier Coordination: Strong coordination with suppliers is crucial. Orders for raw materials and components are placed with precise timing, so they arrive just as they are needed for production. This requires reliable suppliers who can deliver consistently and promptly.
4.Receiving and Inspection: Upon arrival, materials are immediately inspected and moved directly to the production line. This eliminates the need for large storage areas and reduces handling costs.
5.Production Execution: Production is carried out based on the received materials. The JIT system ensures that there is a continuous flow of production without delays caused by waiting for materials.
6.Quality Control and Continuous Improvement: Throughout the process, quality control measures are implemented to ensure that any defects are identified and addressed promptly. Continuous improvement (kaizen) is a core aspect of JIT, aiming to enhance processes and reduce waste continually.
Just-in-time Inventory Cycle
The JIT inventory cycle is a seamless loop where the receipt of materials, production, and delivery are closely integrated. Here’s how it flows:
- Order Placement: Materials are ordered based on precise production requirements.
- Just-in-time Delivery: Suppliers deliver materials just in time for production.
- Production: Goods are manufactured using the just-in-time materials.
- Product Delivery: Finished products are delivered to customers promptly, meeting their demands without delay.
Just-in-time Inventory Examples
Real-world examples of JIT inventory management include:
- Automotive Industry: Toyota, the pioneer of JIT, uses this strategy to keep inventory costs low and production efficiency high. Components arrive just as they are needed on the assembly line, reducing storage needs and costs.
- Retail Industry: Companies like Walmart use JIT principles to manage inventory levels in their stores. Products are restocked based on real-time sales data, ensuring shelves are filled with items that are in demand.
Advantages of Just-in-time (JIT) Inventory
Just-in-time (JIT) inventory management offers numerous benefits that can significantly enhance a company's efficiency and profitability. By adopting JIT principles, businesses can optimize their operations and maintain a competitive edge.
Here are some key advantages of JIT inventory:
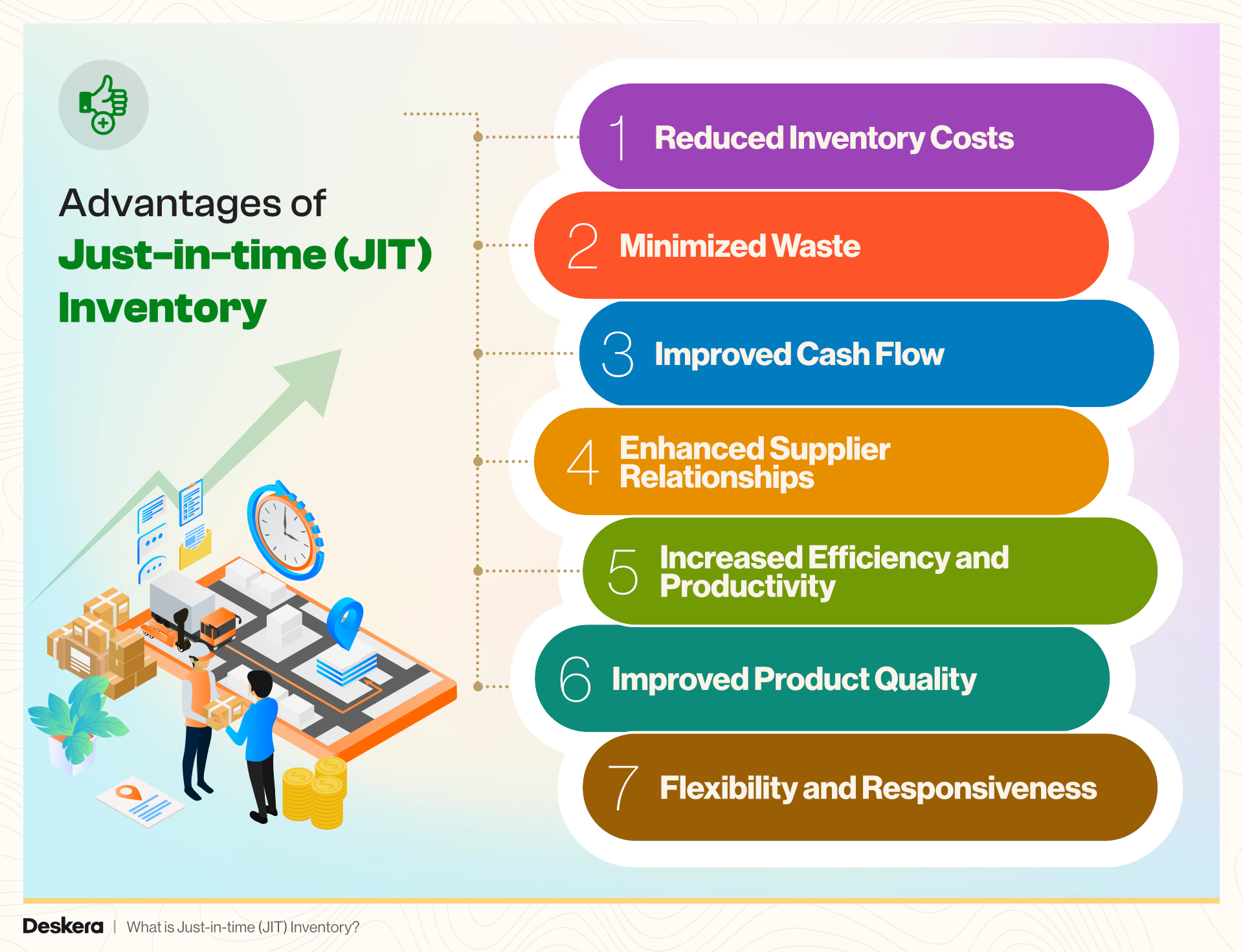
Reduced Inventory Costs
One of the most significant advantages of JIT inventory is the reduction in inventory costs. By receiving goods only as they are needed in the production process, businesses can minimize the amount of inventory they need to store.
This leads to lower storage costs, reduced need for warehouse space, and decreased handling expenses. Companies can free up capital that would otherwise be tied up in excess inventory, improving overall cash flow.
Minimized Waste
JIT inventory management helps in minimizing waste across the production process. By aligning production schedules with actual demand, businesses can reduce the risk of overproduction and the accumulation of obsolete or unsold goods. This lean approach ensures that resources are used efficiently and sustainably, contributing to a more environmentally friendly operation.
Improved Cash Flow
With JIT inventory, businesses maintain lower inventory levels, which means less money is tied up in stock.
This improved cash flow can be redirected towards other critical areas of the business, such as research and development, marketing, or expanding operations.
By optimizing inventory levels, companies can operate more flexibly and respond quickly to market changes.
Enhanced Supplier Relationships
Implementing JIT inventory requires strong, reliable relationships with suppliers.
These partnerships are built on trust and consistent communication, ensuring that suppliers can meet the precise timing and quantity requirements of the business.
Strong supplier relationships lead to more reliable supply chains, better quality materials, and often more favorable terms.
Increased Efficiency and Productivity
JIT inventory management leads to more efficient production processes. By ensuring that materials arrive just in time for production, companies can streamline their operations and reduce downtime.
This results in higher productivity levels, as production lines are always supplied with the necessary materials. Employees can focus on value-added activities rather than managing and moving excess inventory.
Improved Product Quality
JIT systems emphasize continuous improvement (kaizen) and quality control throughout the production process.
By maintaining a close watch on the production line and implementing regular quality checks, businesses can quickly identify and address defects or issues.
This focus on quality leads to higher-quality products and increased customer satisfaction.
Flexibility and Responsiveness
JIT inventory management allows businesses to be more responsive to market demands and changes.
With lower inventory levels, companies can quickly adjust their production schedules to meet new orders or shifts in customer preferences.
This flexibility ensures that businesses can stay competitive in dynamic markets and better meet customer needs.
Disadvantages of Just-in-time (JIT) Inventory
While Just-in-time (JIT) inventory management offers many advantages, it also presents several challenges and potential disadvantages that businesses must consider.
Understanding these drawbacks is crucial for effectively implementing and managing JIT inventory systems.
Here are some key disadvantages of JIT inventory:
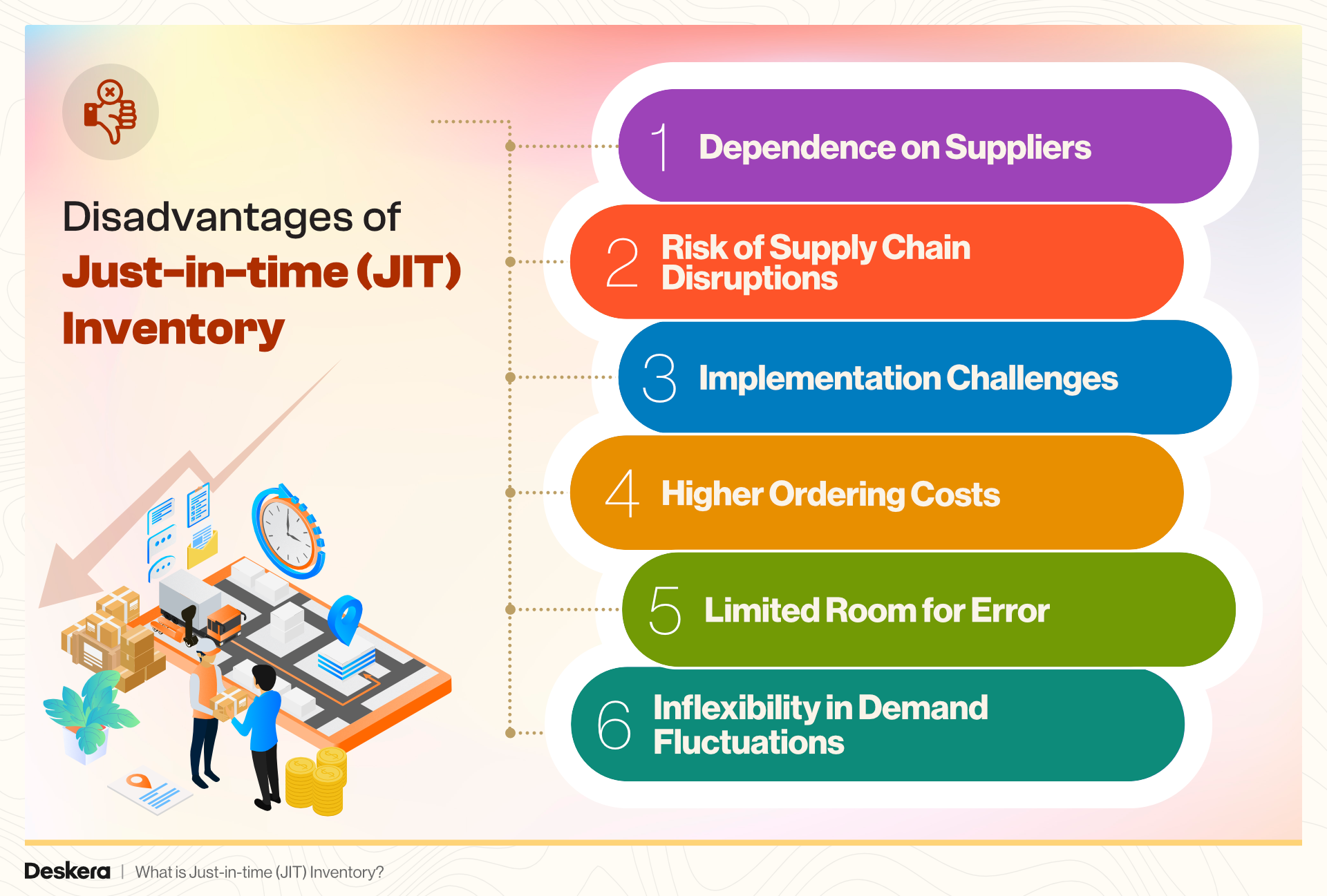
Dependence on Suppliers
One of the primary disadvantages of JIT inventory is the heavy reliance on suppliers. Since JIT requires materials to arrive precisely when needed, any delay or disruption in the supply chain can halt production.
This dependence makes businesses vulnerable to supplier issues, such as transportation delays, production problems, or quality issues. To mitigate this risk, companies need to establish strong, reliable relationships with their suppliers.
Risk of Supply Chain Disruptions
JIT inventory systems are highly susceptible to supply chain disruptions. Events such as natural disasters, political instability, or logistical challenges can severely impact the timely delivery of materials.
Without adequate buffer inventory, even minor disruptions can lead to significant production delays, affecting the company's ability to meet customer demands and potentially harming its reputation.
Implementation Challenges
Implementing JIT inventory management can be complex and challenging. It often requires significant changes to existing processes and systems, including the adoption of new technologies and the retraining of staff.
The transition period can be disruptive and may involve a steep learning curve. Additionally, aligning production schedules and supplier deliveries with precise timing requires meticulous planning and coordination.
Higher Ordering Costs
Although JIT reduces inventory holding costs, it can lead to higher ordering costs. Since materials are ordered in smaller quantities and more frequently, the administrative and logistical costs associated with placing and receiving orders can increase. This can offset some of the savings achieved through reduced inventory levels.
Limited Room for Error
JIT inventory management leaves little room for error. Mistakes in demand forecasting, production planning, or supplier coordination can have immediate and significant impacts on the production process.
Companies must have robust systems in place to monitor and manage inventory levels accurately and respond quickly to any issues that arise.
Inflexibility in Demand Fluctuations
JIT systems can struggle to adapt to sudden changes in demand. Because inventory levels are kept to a minimum, unexpected spikes in customer demand can lead to stockouts and unfulfilled orders.
This inflexibility can result in lost sales and dissatisfied customers. Businesses need to balance the efficiency of JIT with the ability to respond to market fluctuations.
Which Methods Support Just-in-Time (JIT) Inventory Management?
Implementing Just-in-Time (JIT) inventory management effectively requires the integration of various methods and technologies that help streamline operations, reduce waste, and optimize inventory levels.
Here are some key methods that support JIT inventory management:
1. Vendor-Managed Inventory (VMI)
Definition: Vendor-Managed Inventory (VMI) is a system where suppliers are responsible for managing the inventory levels of their clients. Suppliers monitor inventory levels and provide goods as needed, based on pre-established agreements.
How it Supports JIT:
- Reduced Inventory Levels: Suppliers ensure that inventory levels are maintained just in time for production or sales, reducing the need for excess stock.
- Improved Supplier Relationships: VMI fosters closer collaboration between suppliers and businesses, leading to more reliable and timely deliveries.
2. Kanban System
Definition: The Kanban system uses visual signals, often in the form of cards or electronic notifications, to indicate when components or materials need to be replenished.
How it Supports JIT:
- Visual Management: Kanban provides a clear, visual method for managing inventory and production schedules, ensuring that materials are replenished precisely when needed.
- Flow Control: By signaling the need for more materials, Kanban helps maintain a continuous flow in production processes, aligning with JIT principles.
3. Point-of-Sale (POS) Tracking
Definition: Point-of-Sale (POS) tracking involves monitoring sales and inventory usage in real-time through POS systems. This data helps businesses identify which items need to be restocked promptly.
How it Supports JIT:
- Real-Time Data: POS tracking provides up-to-date information on inventory levels and sales, enabling businesses to make timely decisions about restocking.
- Demand Forecasting: By analyzing sales data, businesses can better forecast demand and adjust inventory levels accordingly, supporting JIT objectives.
4. Electronic Data Interchange (EDI)
Definition: Electronic Data Interchange (EDI) is a system that electronically shares inventory and order information between a supplier and a business.
How it Supports JIT:
- Efficient Communication: EDI streamlines communication between suppliers and businesses, reducing the time and errors associated with manual data entry.
- Timely Orders: Automated exchange of information helps ensure that orders are processed and fulfilled promptly, aligning with JIT inventory needs.
5. Automated Replenishment System (ARS)
Definition: Automated Replenishment Systems (ARS) monitor inventory levels and automatically place orders to replenish stock when levels fall below a predefined threshold.
How it Supports JIT:
- Inventory Control: ARS helps maintain optimal inventory levels by automatically triggering orders based on real-time data, minimizing the risk of stockouts.
- Operational Efficiency: By automating the replenishment process, ARS reduces the need for manual intervention, improving efficiency and responsiveness.
Just-in-Time (JIT) in Different Sectors
Just-in-Time (JIT) inventory management is a versatile approach that can be adapted to various industries to improve efficiency and reduce waste. Each sector applies JIT principles in unique ways to meet its specific needs and challenges.
Here’s how JIT is utilized across different sectors:
1. Automotive Industry
- Application: In the automotive sector, JIT is used to synchronize production with customer demand, minimizing inventory levels and streamlining the manufacturing process.
Key Practices:
- Kanban System: Visual signals are employed to manage inventory and production schedules.
- Supplier Coordination: Components are delivered precisely when needed for assembly, reducing storage requirements and costs.
- Continuous Improvement: Ongoing evaluation and enhancement of processes to eliminate waste.
Benefits:
- Reduced Inventory Costs: Lower storage and handling costs.
- Enhanced Production Efficiency: Streamlined processes and reduced lead times.
2. Retail Industry
- Application: Retailers use JIT principles to manage inventory across multiple locations, ensuring that products are restocked just in time to meet customer demand.
Key Practices:
- Real-Time Inventory Tracking: Advanced systems track inventory levels and sales in real time.
- Vendor Partnerships: Strong relationships with suppliers enable timely deliveries.
- Cross-Docking: Products are transferred directly from suppliers to stores, minimizing storage time.
Benefits:
- Optimized Stock Levels: Reduces excess inventory and associated costs.
- Improved Customer Satisfaction: Ensures that popular items are always available.
3. Technology Industry
- Application: The technology sector applies JIT to its supply chain and manufacturing processes, ensuring that components arrive just as they are needed for assembly.
Key Practices:
- Demand Forecasting: Accurate predictions of product demand drive production schedules.
- Lean Inventory: Minimal inventory levels are maintained to reduce costs and improve flexibility.
- Agile Manufacturing: Quick adjustments to production processes based on demand changes.
Benefits:
- Reduced Inventory Costs: Lower storage and handling costs.
- Flexibility: Ability to quickly adapt to changes in market demand.
4. Food and Beverage Industry
- Application: In the food and beverage sector, JIT ensures that food is prepared fresh and inventory levels are closely managed.
Key Practices:
- Made-to-Order: Food is prepared as orders are placed, minimizing waste and ensuring freshness.
- Inventory Control: Precise tracking of ingredients and supplies to match daily demand.
- Supplier Coordination: Timely delivery of ingredients to maintain quality.
Benefits:
- Reduced Waste: Freshly prepared food and minimal excess inventory.
- Consistent Quality: Ensures high standards in food preparation.
5. Healthcare Industry
- Application: In healthcare, JIT principles are used to manage medical supplies and equipment, ensuring that inventory levels are aligned with patient needs.
Key Practices:
- Just-in-Time Ordering: Supplies and equipment are ordered and delivered as needed to avoid stockouts.
- Inventory Management Systems: Advanced systems track usage and forecast demand.
- Supplier Relationships: Reliable suppliers ensure timely delivery of critical supplies.
Benefits:
- Improved Resource Utilization: Reduces waste and ensures timely availability of medical supplies.
- Cost Savings: Minimizes storage costs and avoids obsolescence.
What Are Some Examples of Just-In-Time (JIT) Inventory Processes?
Just-in-time (JIT) inventory processes have been successfully implemented across various industries to streamline operations, reduce waste, and enhance efficiency.
Here are some notable examples of JIT inventory processes, showcasing how different companies have adopted this strategy to improve their production and inventory management:
Automotive Industry: Toyota
Toyota Production System (TPS)
Toyota is the pioneer of the Just-in-time (JIT) inventory concept. The Toyota Production System (TPS) is a comprehensive approach that integrates JIT with other lean manufacturing principles to minimize waste and maximize efficiency. Here’s how it works:
- Demand-Driven Production: Toyota's production process is directly driven by customer orders. This means that cars are built based on actual demand rather than forecasts.
- Kanban System: Toyota uses a Kanban system, which employs visual signals to trigger the movement of materials within the production process. When a part is used, a Kanban card is sent to the supplier to request more, ensuring that inventory levels are kept minimal.
- Just-In-Time Delivery: Suppliers deliver components to Toyota's assembly line just as they are needed, reducing storage costs and ensuring a seamless flow of materials.
Retail Industry: Walmart
Efficient Inventory Management
Walmart has effectively implemented JIT principles to manage its vast inventory across numerous retail locations. The company’s approach includes:
- Real-Time Inventory Tracking: Walmart uses sophisticated inventory management software to monitor stock levels in real time. This allows the company to reorder products based on actual sales data, ensuring that inventory is replenished just in time to meet customer demand.
- Vendor Partnerships: Walmart maintains strong relationships with its suppliers, enabling efficient coordination and timely delivery of goods. This minimizes excess inventory and reduces storage costs.
- Cross-Docking: Products arriving at Walmart’s distribution centers are directly transferred to outbound trucks for delivery to stores, minimizing handling and storage time.
Technology Industry: Apple
Supply Chain Optimization
Apple utilizes JIT inventory processes to maintain efficiency and flexibility in its supply chain:
- Lean Inventory: Apple keeps inventory levels low by coordinating closely with its suppliers. Components are ordered in small quantities and delivered just in time for assembly.
- Demand Forecasting: Apple employs advanced demand forecasting techniques to anticipate customer orders and adjust production schedules accordingly. This helps reduce the risk of overproduction and excess inventory.
- Agile Manufacturing: Apple's manufacturing partners, such as Foxconn, use JIT principles to assemble products quickly and efficiently, allowing Apple to respond swiftly to changes in market demand.
Food and Beverage Industry: McDonald's
Just-In-Time Food Preparation
McDonald’s applies JIT principles to ensure fresh food and minimize waste:
- Made-to-Order: McDonald’s prepares food items only when they are ordered by customers, ensuring that meals are fresh and reducing the amount of pre-prepared food that might go to waste.
- Inventory Control: The company uses precise inventory management systems to keep track of ingredients, ensuring that supplies are ordered just in time to meet daily demand.
- Supplier Coordination: McDonald’s works closely with suppliers to ensure timely delivery of ingredients, maintaining the freshness and quality of its products.
Challenges and Solutions in JIT Inventory Management
Implementing Just-in-Time (JIT) inventory management can bring significant benefits, such as reduced costs and improved efficiency. However, it also comes with its own set of challenges.
Here are some common challenges associated with JIT inventory management and potential solutions to address them:
1. Supply Chain Disruptions
Challenge: JIT inventory relies heavily on timely deliveries. Any disruption in the supply chain, such as delays, natural disasters, or political instability, can lead to production halts and stockouts.
Solution:
- Supplier Diversification: Work with multiple suppliers to mitigate the risk of disruption from any single source.
- Robust Communication: Establish strong communication channels with suppliers to quickly identify and address potential issues.
- Buffer Inventory: Maintain a small buffer stock of critical components to cushion against unforeseen delays.
2. Demand Variability
Challenge: Fluctuations in customer demand can be difficult to predict, leading to either stock outs or overproduction.
Solution:
- Advanced Forecasting Techniques: Use data analytics and machine learning to improve demand forecasting accuracy.
- Flexible Production Systems: Implement flexible manufacturing processes that can quickly adjust to changes in demand.
- Real-Time Data Monitoring: Continuously monitor sales and inventory levels to respond promptly to demand shifts.
3. Supplier Reliability
Challenge: The success of JIT inventory depends on the reliability of suppliers. Any inconsistency in quality or delivery times can disrupt operations.
Solution:
- Supplier Assessment and Development: Regularly evaluate suppliers for reliability and performance, and work with them to improve their processes.
- Long-Term Contracts: Establish long-term agreements with reliable suppliers to ensure consistent quality and delivery.
- Performance Metrics: Implement key performance indicators (KPIs) to monitor supplier performance and address issues proactively.
4. Increased Transportation Costs
Challenge: Frequent small shipments required by JIT inventory can lead to higher transportation costs.
Solution:
- Consolidated Shipments: Coordinate with suppliers to consolidate shipments whenever possible to reduce transportation frequency and costs.
- Local Sourcing: Source materials and components from local suppliers to reduce transportation distance and costs.
- Efficient Routing: Use logistics software to optimize transportation routes and schedules for cost efficiency.
5. Quality Control Issues
Challenge: With minimal inventory on hand, any quality issues with incoming materials can have immediate and significant impacts on production.
Solution:
- Strict Quality Standards: Set high quality standards and conduct regular inspections of incoming materials.
- Supplier Audits: Perform regular audits of supplier facilities and processes to ensure they meet quality requirements.
- Quality Management Systems: Implement robust quality management systems (QMS) to identify and address quality issues quickly.
6. Technological Dependence
Challenge: JIT inventory management relies on sophisticated technology for real-time tracking, forecasting, and communication, which can be costly and complex to implement.
Solution:
- Invest in Technology: Allocate budget for reliable and scalable inventory management systems that support JIT principles.
- Training and Support: Provide adequate training for employees to effectively use inventory management technology.
- Deskera ERP: Utilize comprehensive ERP solutions like Deskera, which offer integrated features for real-time inventory tracking, demand forecasting, and automated reordering, making it easier to manage JIT inventory efficiently.
7. Employee Training and Engagement
Challenge: Implementing JIT requires a cultural shift and employee buy-in, which can be challenging to achieve.
Solution:
- Continuous Training: Offer ongoing training programs to ensure employees understand JIT principles and processes.
- Employee Involvement: Involve employees in the planning and implementation stages to gain their insights and foster a sense of ownership.
- Clear Communication: Maintain clear and open communication about the benefits and goals of JIT to keep employees motivated and engaged.
In conclusion, while Just-in-Time (JIT) inventory management presents several challenges, these can be effectively addressed through strategic planning, advanced technology, and strong supplier relationships.
By implementing the solutions outlined above, businesses can overcome obstacles and reap the benefits of JIT, such as reduced inventory costs, improved efficiency, and enhanced responsiveness to market demands.
7 Reasons for Manufacturers to Implement Just-in-Time (JIT) Inventory
Just-in-Time (JIT) inventory management is a powerful strategy that can significantly enhance the efficiency and competitiveness of manufacturing operations.
Here are seven compelling reasons why manufacturers should consider implementing JIT inventory:
1. Reduced Inventory Costs
Reason: JIT minimizes the amount of inventory that needs to be stored, which in turn reduces storage costs, handling costs, and the capital tied up in inventory.
Benefit: By ordering materials and components only as they are needed for production, manufacturers can significantly cut down on warehousing expenses and reduce the risk of inventory obsolescence.
2. Improved Cash Flow
Reason: With JIT, manufacturers maintain lower inventory levels, freeing up capital that can be used for other critical business activities.
Benefit: Better cash flow management allows manufacturers to invest in new technologies, expand operations, or improve product development efforts without being constrained by the costs of holding excess inventory.
3. Enhanced Production Efficiency
Reason: JIT promotes a streamlined production process where materials are available exactly when needed, reducing downtime and increasing operational efficiency.
Benefit: This leads to a more efficient production line, faster turnaround times, and the ability to meet customer demands more effectively. The reduction in lead times also allows manufacturers to respond quickly to market changes.
4. Higher Product Quality
Reason: With JIT, manufacturers can focus on quality control at every stage of production. Receiving smaller, more frequent deliveries of materials helps in identifying defects early and ensuring high-quality inputs.
Benefit: This results in higher-quality finished products, fewer returns, and greater customer satisfaction. Consistently high-quality products can also enhance the manufacturer’s reputation and competitive edge.
5. Better Supplier Relationships
Reason: JIT requires close collaboration with suppliers to ensure timely and accurate delivery of materials. This fosters stronger partnerships and more reliable supply chains.
Benefit: Strong supplier relationships can lead to better terms, more reliable deliveries, and increased flexibility. Suppliers may also provide value-added services such as inventory management and quality assurance.
6. Increased Flexibility and Responsiveness
Reason: JIT allows manufacturers to be more agile and responsive to changes in market demand and customer preferences. With lower inventory levels, manufacturers can quickly adjust production schedules and introduce new products.
Benefit: Increased flexibility helps manufacturers stay competitive by adapting to market trends and customer needs more rapidly. It also reduces the risk of overproduction and excess inventory.
7. Sustainability and Waste Reduction
Reason: JIT encourages the efficient use of resources and minimizes waste by producing only what is needed, when it is needed.
Benefit: This sustainable approach not only reduces material waste but also decreases energy consumption and environmental impact. Manufacturers can achieve cost savings while contributing to corporate social responsibility goals.
How Deskera ERP Can Help You with Just-in-Time (JIT) Inventory Management
Deskera ERP is a comprehensive solution designed to streamline various business processes, including inventory management.
Implementing Just-in-Time (JIT) inventory management can be challenging, but Deskera ERP offers robust features that can facilitate this process.
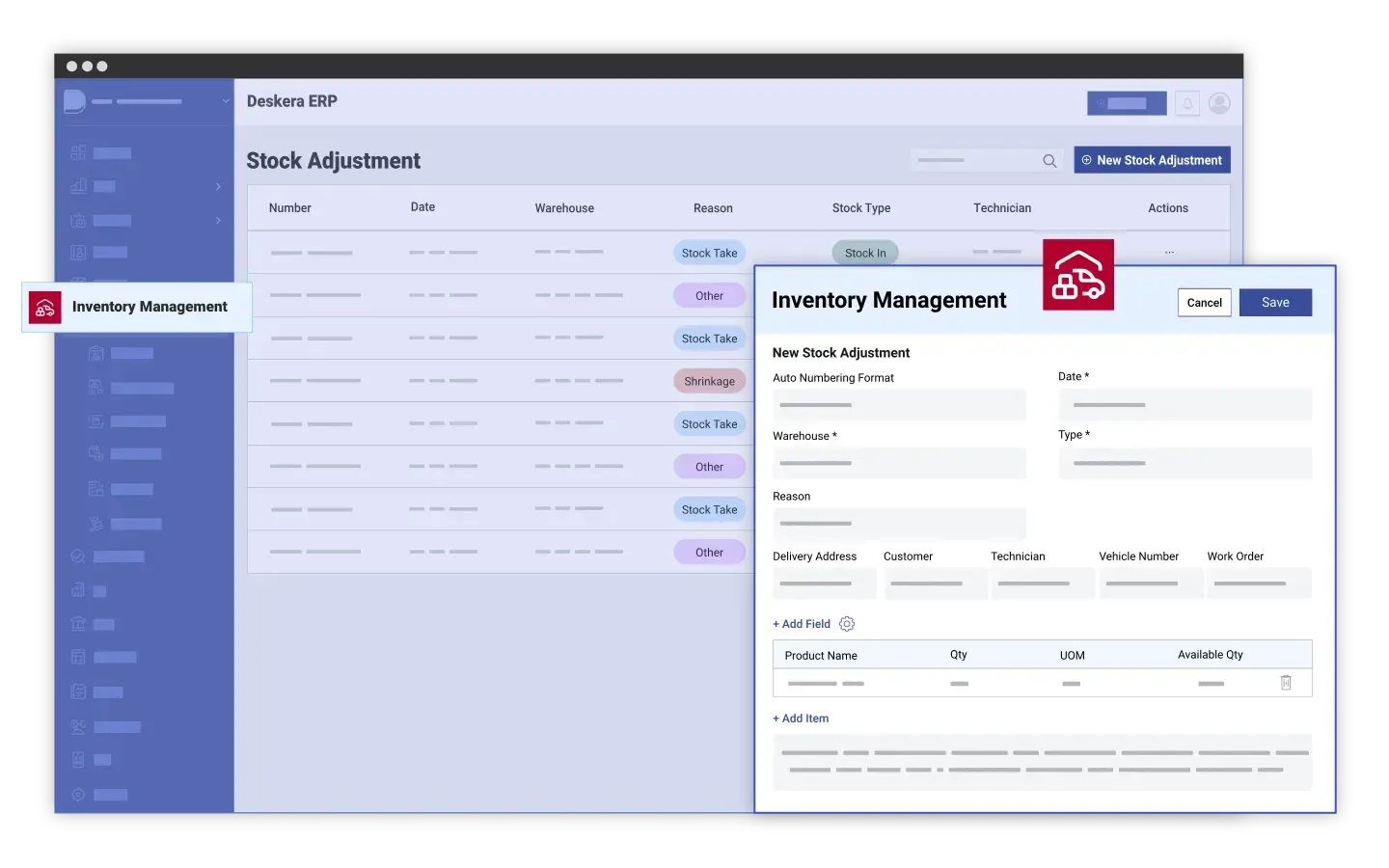
Here’s how Deskera ERP can help you effectively manage JIT inventory:
1. Real-Time Inventory Tracking
Feature: Deskera ERP provides real-time visibility into inventory levels across multiple locations.
Benefit: With real-time tracking, you can monitor stock levels and movement accurately. This ensures that you always know what inventory is available, what needs to be ordered, and when it should arrive, which is crucial for JIT inventory management.
2. Advanced Demand Forecasting
Feature: The system leverages advanced algorithms and data analytics to forecast demand accurately.
Benefit: Accurate demand forecasting helps in planning inventory needs precisely, reducing the risk of overstocking or stockouts. Deskera ERP’s forecasting tools enable you to align inventory orders closely with actual demand, a key principle of JIT.
3. Automated Reordering
Feature: Deskera ERP supports automated reordering based on predefined inventory thresholds.
Benefit: Automated reordering ensures that materials and products are ordered just in time to meet production needs. This reduces manual intervention and minimizes the chances of errors, ensuring a smooth JIT process.
4. Supplier Management
Feature: The ERP system includes robust supplier management tools that facilitate communication and coordination with suppliers.
Benefit: Strong supplier relationships are essential for JIT. Deskera ERP enables better collaboration with suppliers, ensuring timely deliveries and adherence to quality standards. The system can also manage supplier performance and streamline the procurement process.
5. Integration with Production Planning
Feature: Deskera ERP integrates inventory management with production planning and scheduling.
Benefit: This integration ensures that inventory levels are aligned with production schedules. By synchronizing inventory orders with production requirements, manufacturers can avoid delays and ensure a seamless flow of materials through the production line.
6. Real-Time Analytics and Reporting
Feature: The system provides real-time analytics and customizable reporting features.
Benefit: Real-time data and insights allow you to make informed decisions quickly. You can track key performance indicators (KPIs), monitor inventory turnover rates, and identify trends that impact inventory levels. This information is vital for maintaining optimal inventory levels in a JIT environment.
7. Inventory Optimization
Feature: Deskera ERP includes tools for inventory optimization that help reduce excess stock and minimize waste.
Benefit: By optimizing inventory levels, Deskera ERP helps you maintain lean inventory practices, reducing costs associated with excess stock and storage. This is a core aspect of JIT, which aims to keep inventory levels as low as possible without affecting production.
8. Scalability and Flexibility
Feature: Deskera ERP is scalable and can be customized to meet the unique needs of different businesses.
Benefit: Whether you are a small business or a large enterprise, Deskera ERP can be tailored to support your specific JIT requirements. Its flexibility allows you to adjust processes and workflows as your business grows and evolves.
9. Mobile Accessibility
Feature: Deskera ERP offers mobile accessibility, allowing you to manage inventory and operations on the go.
Benefit: Mobile access ensures that you can monitor and manage inventory from anywhere, providing greater flexibility and responsiveness. This is particularly useful for managers and employees who need to make quick decisions while away from their desks.
Thus, Deskera ERP helps ensure that your inventory management processes are efficient, accurate, and aligned with JIT principles. By leveraging Deskera ERP, businesses can achieve significant improvements in operational efficiency, cost savings, and overall productivity.
Key Takeaways
Just-in-Time (JIT) inventory management is a powerful strategy that can transform manufacturing operations by reducing costs, improving efficiency, and enhancing product quality.
By focusing on delivering materials and products only as they are needed, JIT minimizes waste and maximizes resource utilization. However, successful implementation requires overcoming challenges such as supply chain disruptions, demand variability, and supplier reliability.
Technological solutions like Deskera ERP play a crucial role in enabling JIT by providing real-time inventory tracking, advanced forecasting, and automated reordering. These features help businesses maintain lean inventory levels, improve supplier coordination, and respond swiftly to market demands.
Incorporating JIT inventory management can lead to significant operational benefits, making it an essential strategy for modern manufacturers looking to enhance their competitiveness and sustainability. By leveraging tools like Deskera ERP, businesses can effectively implement JIT and achieve greater efficiency, cost savings, and customer satisfaction.
Related Articles
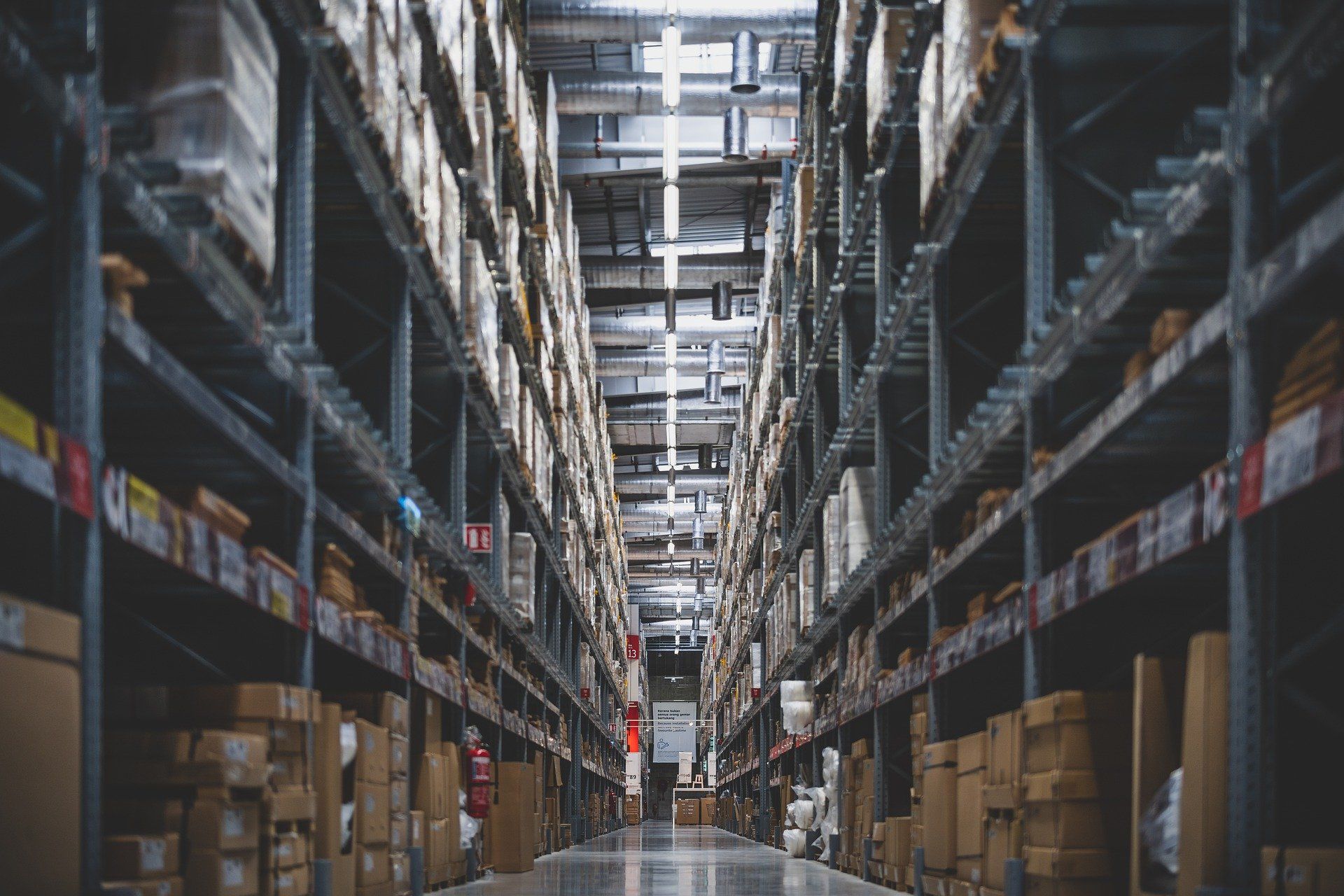
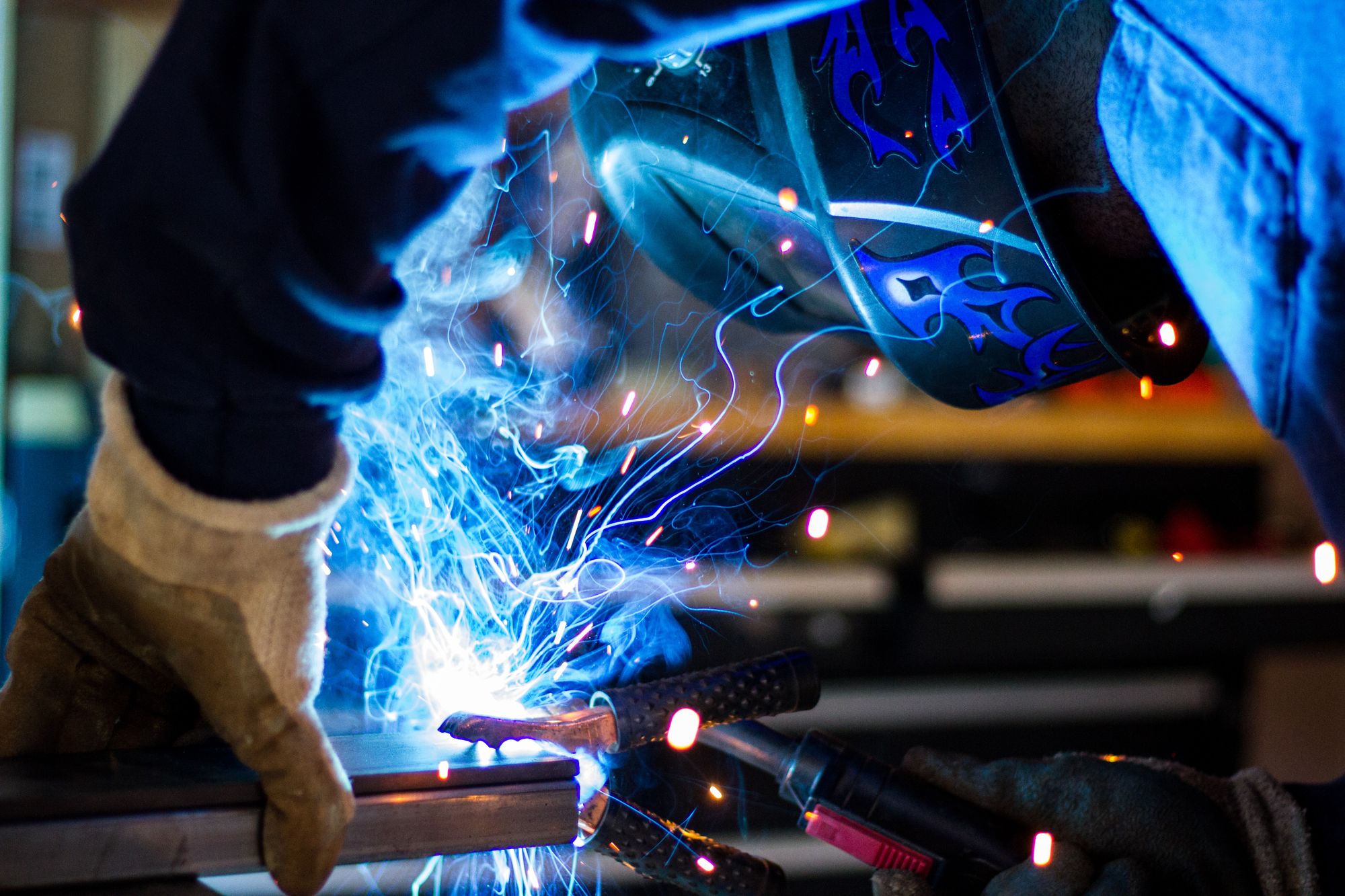
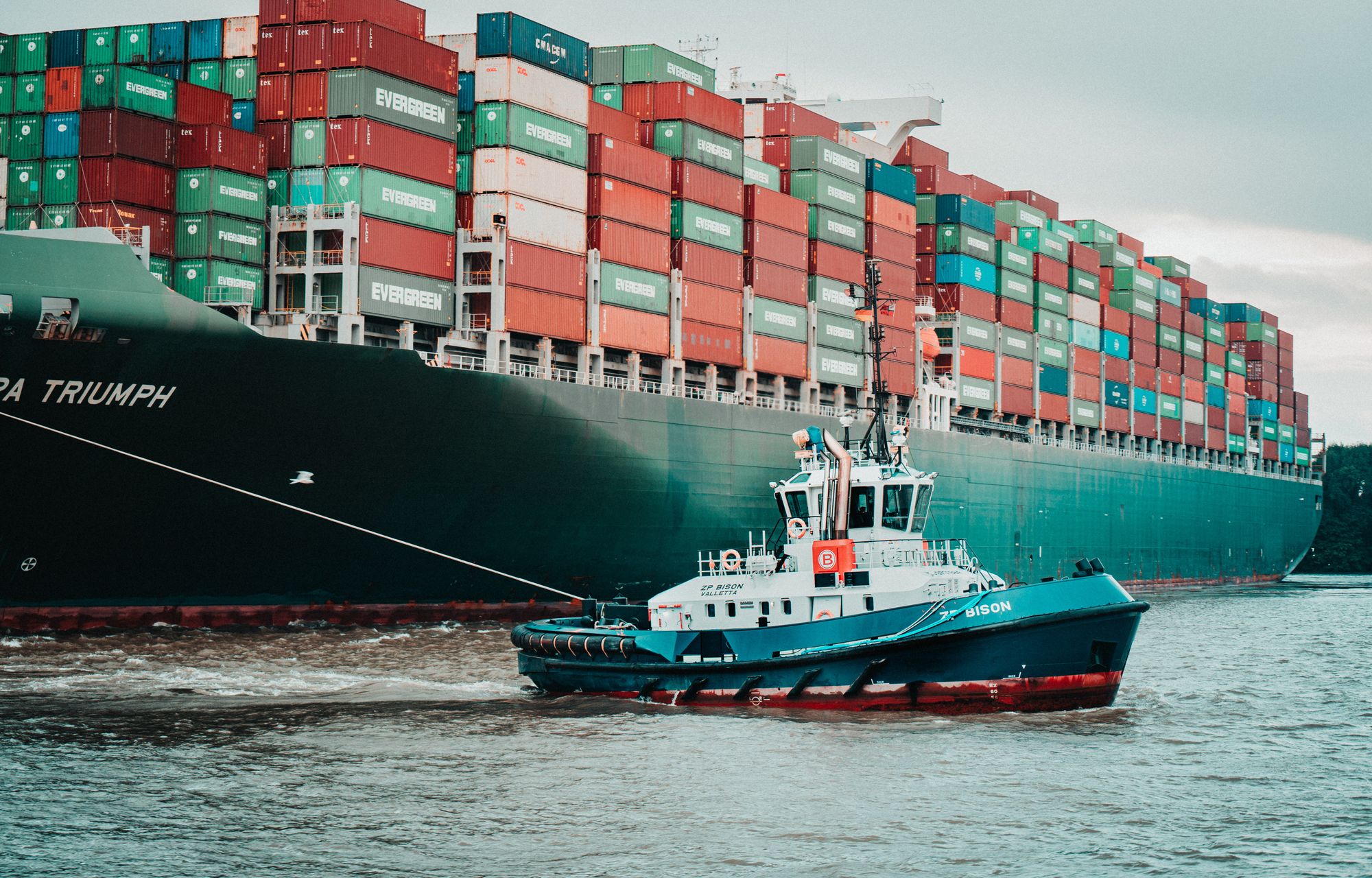
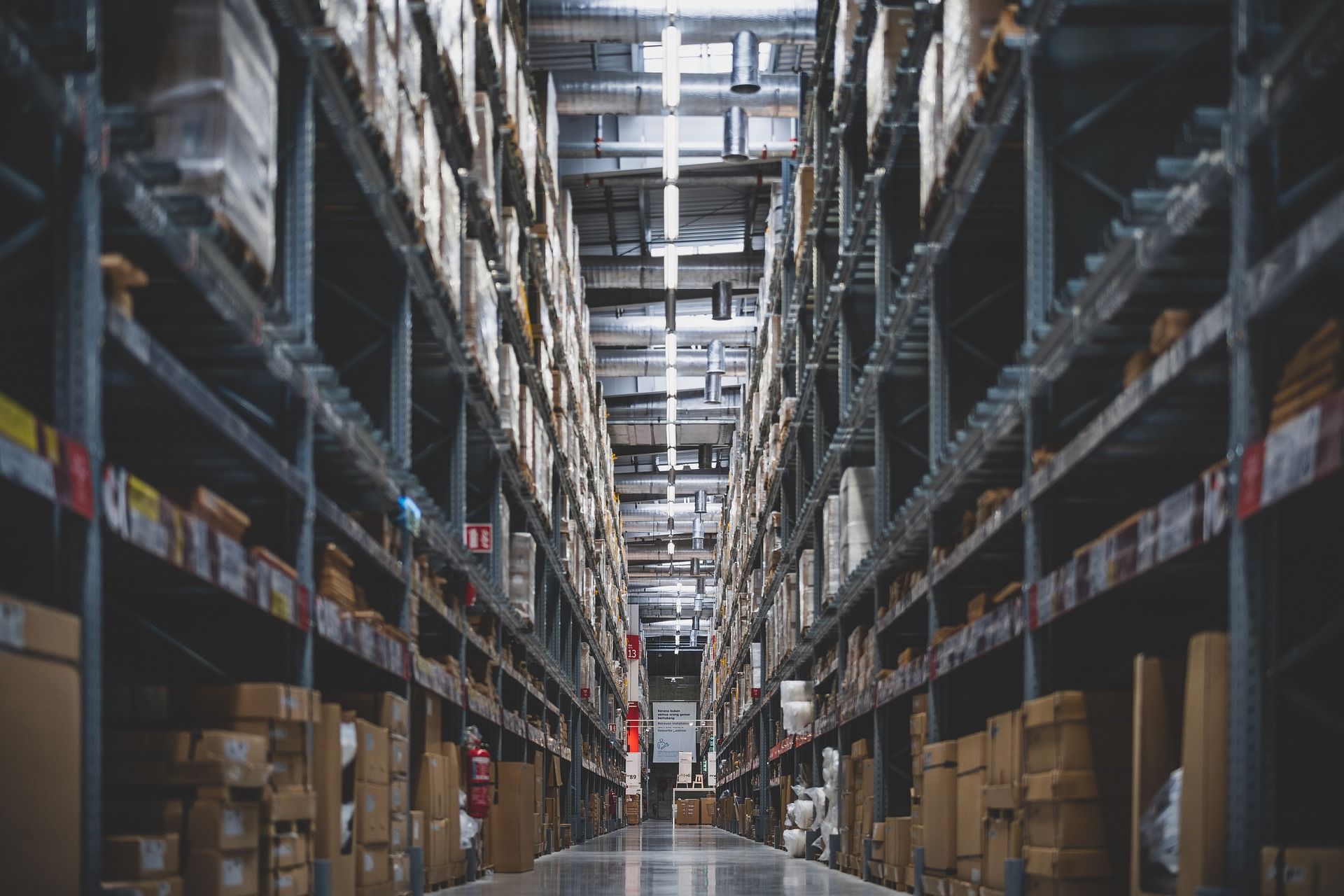
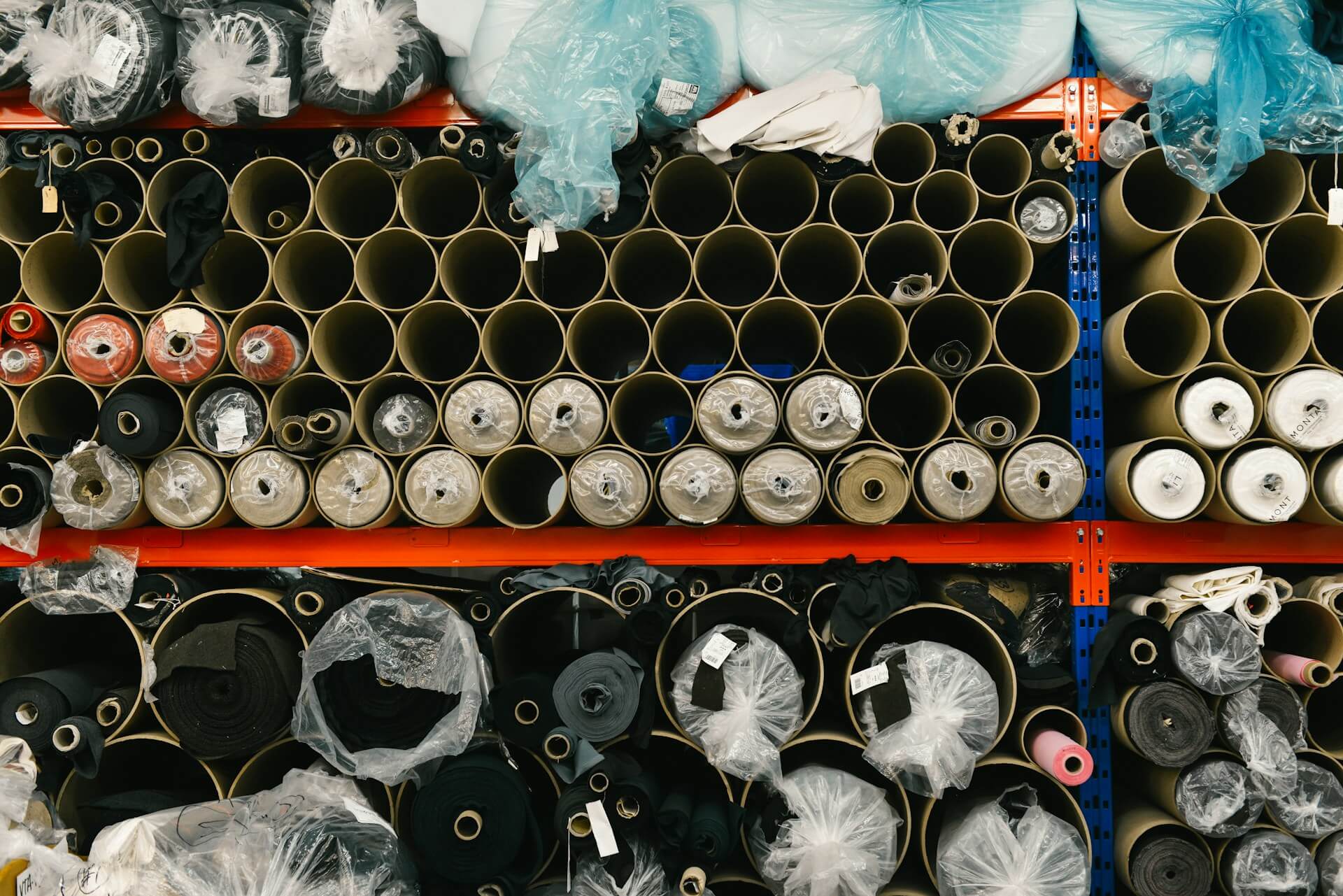
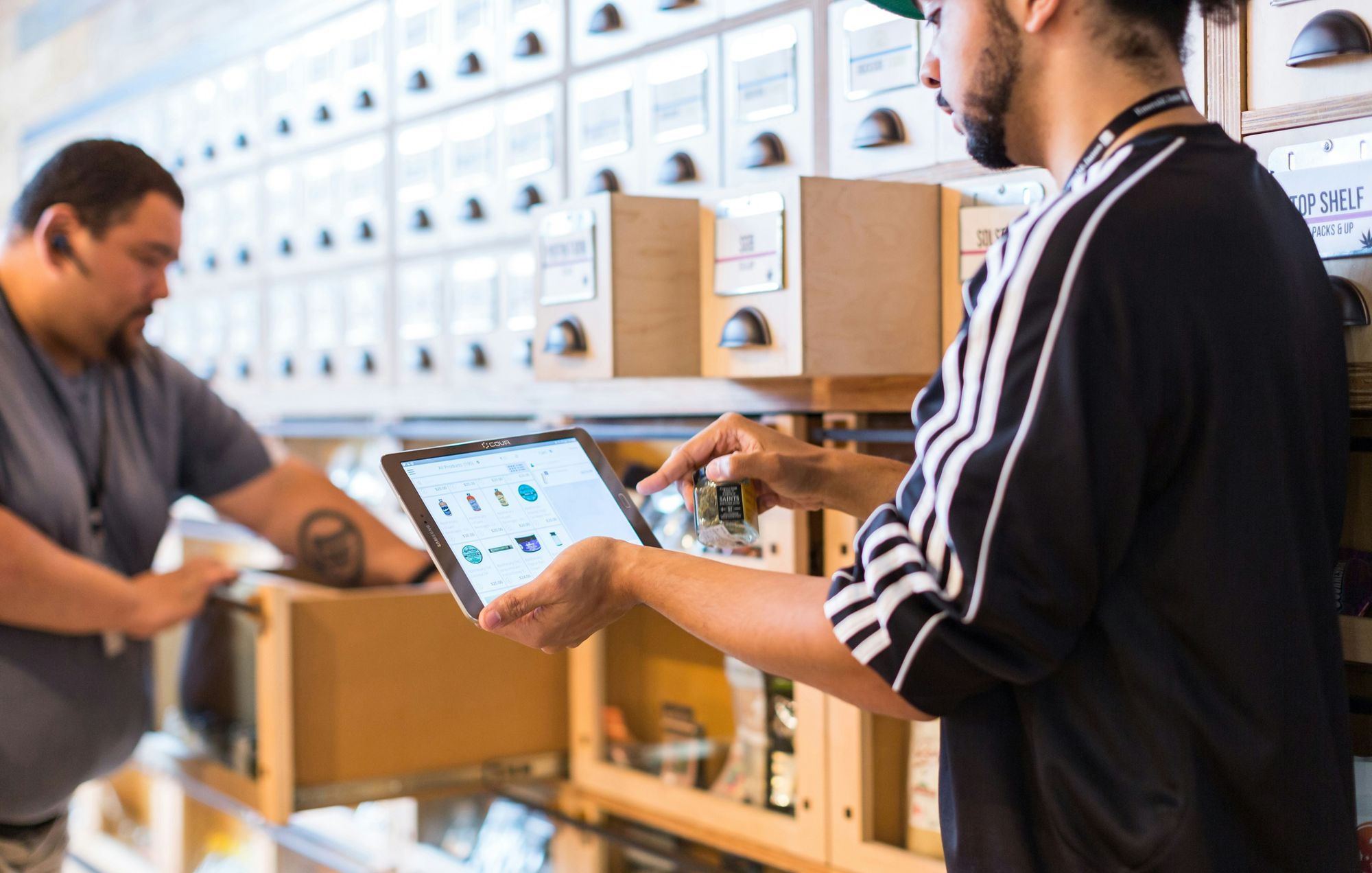