In today's fast-paced manufacturing environment, efficient inventory management is crucial for maintaining a competitive edge. Vendor Managed Inventory (VMI) has emerged as a powerful strategy, offering manufacturers significant advantages.
For instance, VMI can reduce lead times by up to 40%, boost fulfillment accuracy by 25%, and increase repeat purchase rates by 20%. Additionally, VMI has been shown to increase sales by 15%, making it a compelling choice for businesses looking to streamline their operations and enhance customer satisfaction.
Beyond the immediate operational benefits, VMI plays a strategic role in strengthening partnerships between manufacturers and suppliers. By allowing suppliers to take responsibility for inventory management, manufacturers can focus on core activities such as production and innovation.
This collaboration fosters a deeper level of trust and communication, leading to more accurate demand forecasting and smoother supply chain operations. As manufacturing continues to evolve, integrating VMI with robust ERP systems like Deskera can be a game-changer, enabling companies to stay agile and responsive in an increasingly complex market.
To further optimize inventory management, manufacturers can leverage comprehensive ERP solutions like Deskera ERP. Deskera ERP provides real-time data visibility, advanced analytics, and seamless integration capabilities, empowering businesses to effectively manage inventory, improve production planning, and drive overall operational efficiency. With Deskera ERP, companies can fully realize the benefits of VMI while maintaining control over their entire supply chain.
What is Vendor Managed Inventory (VMI)?
Vendor Managed Inventory (VMI) is a supply chain management strategy where the supplier (vendor) takes on the responsibility of managing and replenishing the inventory for a customer, such as a retailer or manufacturer.
In this arrangement, the vendor monitors the customer’s inventory levels and makes decisions on when and how much inventory to ship, ensuring that the customer always has the right amount of stock on hand.
Key Features of VMI
- Inventory Responsibility: The vendor is accountable for maintaining adequate inventory levels at the customer’s location. This shifts the burden of inventory management from the customer to the vendor.
- Data Sharing: The customer provides the vendor with access to critical data, such as sales figures, inventory levels, and demand forecasts. This information allows the vendor to make informed decisions regarding inventory replenishment.
- Automatic Replenishment: Based on pre-agreed criteria, such as minimum stock levels, the vendor automatically restocks the inventory as needed, reducing the chances of stockouts or overstocking.
- Improved Efficiency: VMI helps streamline the supply chain by aligning inventory levels more closely with actual demand, reducing lead times, and optimizing the flow of goods.
VMI is designed to enhance supply chain efficiency by fostering closer collaboration between vendors and customers, ultimately leading to better inventory management and reduced operational costs.
Purpose of Vendor Managed Inventory (VMI)
The purpose of Vendor Managed Inventory (VMI) is to optimize inventory management and supply chain efficiency by shifting the responsibility of managing inventory levels from the customer to the supplier. This strategic approach helps streamline operations and improve collaboration between manufacturers and suppliers.
Key purposes of VMI include:
- Improved Inventory Control: VMI aims to maintain optimal inventory levels by allowing suppliers to monitor and manage stock based on real-time data and demand forecasts, reducing stockouts and overstock situations.
- Enhanced Supply Chain Efficiency: By delegating inventory management to the supplier, VMI improves the overall efficiency of the supply chain, leading to better alignment of inventory levels with actual demand and quicker response to changes.
- Cost Reduction: VMI helps reduce inventory holding costs and other related expenses by minimizing excess stock and optimizing inventory turnover.
- Strengthened Supplier Relationships: VMI fosters closer collaboration between suppliers and customers, improving communication and joint problem-solving, which can lead to more effective supply chain partnerships.
- Increased Fulfillment Accuracy: With the supplier managing inventory, there is often a reduction in order errors and improved accuracy in meeting customer demand.
What Does VMI Measure?
Vendor Managed Inventory (VMI) measures various aspects of inventory and supply chain performance to ensure effective management and optimal inventory levels. Key metrics and measurements in VMI include:
- Inventory Levels: Measures the quantity of stock on hand at any given time to ensure that inventory levels are aligned with demand and supply requirements.
- Stock Turnover Rate: Evaluates how frequently inventory is sold and replaced over a specific period, helping to assess inventory efficiency and demand forecasting accuracy.
- Order Accuracy: Tracks the accuracy of orders fulfilled by the supplier, including correct quantities and timely delivery, to ensure that inventory levels match customer needs.
- Lead Times: Measures the time taken from placing an order to receiving the goods, aiming to reduce lead times and improve overall supply chain responsiveness.
- Fulfillment Rates: Assesses the percentage of customer orders fulfilled without stockouts, reflecting the effectiveness of inventory management and replenishment processes.
- Demand Forecast Accuracy: Evaluates how accurately demand forecasts align with actual sales data, aiding in better inventory planning and stock management.
- Cost Savings: Measures reductions in inventory holding costs, stockouts, and other related expenses as a result of implementing VMI.
When Should VMI Be Used?
Vendor Managed Inventory (VMI) should be considered in scenarios where it can significantly enhance inventory management and supply chain efficiency. Ideal conditions for implementing VMI include:
- High Inventory Turnover: When products have a high turnover rate, VMI can help maintain optimal stock levels and reduce the risk of stockouts or excess inventory.
- Long Supply Chains: In complex supply chains with multiple stakeholders, VMI can improve coordination and visibility, leading to more efficient inventory management.
- Stable Demand Patterns: VMI is effective when demand patterns are relatively stable and predictable, allowing suppliers to accurately forecast and manage inventory levels.
- Strong Supplier Relationships: When there is a strong, reliable relationship with a supplier, VMI can be successfully implemented, leveraging the supplier's expertise and resources.
- High Stock Value: For products with high inventory carrying costs, VMI can help reduce these costs by optimizing inventory levels and reducing the need for safety stock.
- Complex Product Lines: When managing a wide range of products or SKUs, VMI can simplify inventory management by allowing suppliers to handle replenishment based on real-time data.
- Need for Reduced Lead Times: VMI is beneficial when reducing lead times is crucial for meeting customer demand and maintaining competitive advantage.
Examples of Vendor Managed Inventory (VMI)
Vendor Managed Inventory (VMI) is utilized across various industries to optimize inventory management and improve supply chain efficiency. Here are some notable examples of VMI in action:
Retail Sector
- Example: Large retailers like Walmart and Target often use VMI to manage inventory in their stores. Suppliers are responsible for monitoring stock levels and ensuring timely replenishment based on real-time sales data.
- Impact: This approach helps reduce stockouts, minimize excess inventory, and streamline the replenishment process.
Automotive Industry
- Example: Automotive manufacturers such as Toyota and Ford use VMI to manage parts and components. Suppliers track inventory levels at manufacturing facilities and adjust deliveries based on production needs.
- Impact: VMI improves production efficiency, reduces lead times, and helps maintain optimal inventory levels for critical components.
Consumer Goods
- Example: Companies like Procter & Gamble (P&G) implement VMI to manage products on retailer shelves. VMI allows P&G to monitor sales data and adjust inventory levels to ensure product availability.
- Impact: This leads to better stock management, increased product availability, and improved sales performance.
Pharmaceutical Industry
- Example: Pharmaceutical companies and distributors use VMI to manage inventory at hospitals and pharmacies. Suppliers monitor usage patterns and adjust inventory levels to ensure availability of essential medications.
- Impact: VMI helps maintain adequate stock levels, reduce the risk of stockouts, and improve healthcare service delivery.
Food and Beverage Industry
- Example: Beverage companies like Coca-Cola and Pepsi use VMI to manage inventory at distribution centers and retail locations. Suppliers oversee inventory levels and coordinate replenishment based on sales data.
- Impact: This ensures timely availability of products, reduces waste, and improves overall supply chain efficiency.
What Problems Does VMI Solve and What Value Does it Deliver?
Vendor Managed Inventory (VMI) addresses several common issues in inventory management and supply chain operations while delivering significant value. Here's how VMI solves problems and the value it provides:
Problems Solved by VMI
Stockouts and Overstocking:
- Problem: Frequent stockouts and overstocking can lead to lost sales, reduced customer satisfaction, and increased carrying costs.
- Solution: VMI helps maintain optimal inventory levels by allowing suppliers to monitor and manage stock based on real-time data, reducing the risk of stockouts and excess inventory.
Inefficient Replenishment Processes:
- Problem: Manual or infrequent replenishment can lead to inefficiencies and inaccuracies in inventory management.
- Solution: VMI automates the replenishment process, allowing suppliers to adjust inventory levels proactively based on sales trends and inventory data.
Poor Demand Forecasting:
- Problem: Inaccurate demand forecasts can result in mismatches between inventory levels and actual demand.
- Solution: VMI leverages real-time data to improve demand forecasting accuracy, leading to better alignment of inventory with actual sales patterns.
High Inventory Holding Costs:
- Problem: High levels of inventory lead to increased holding costs and tied-up capital.
- Solution: VMI optimizes inventory levels, reducing excess stock and associated holding costs, and freeing up capital for other business needs.
Supply Chain Inefficiencies:
- Problem: Lack of coordination between suppliers and customers can cause delays and inefficiencies in the supply chain.
- Solution: VMI improves supply chain coordination by enabling suppliers to manage inventory based on up-to-date information, streamlining the flow of goods.
Value Delivered by VMI
- Enhanced Inventory Efficiency: VMI ensures that inventory levels are closely aligned with demand, improving turnover rates and reducing carrying costs.
- Increased Fulfillment Accuracy: By managing inventory based on real-time data, VMI reduces order errors and improves the accuracy of product availability.
- Reduced Lead Times: VMI helps shorten lead times by allowing suppliers to anticipate and address inventory needs proactively, leading to faster replenishment and improved responsiveness.
- Cost Savings: VMI can lead to significant cost savings through reduced holding costs, fewer stockouts, and minimized waste, contributing to overall operational efficiency.
- Stronger Supplier Relationships: VMI fosters closer collaboration between suppliers and customers, improving communication and enhancing partnership quality.
- Improved Customer Satisfaction: With better inventory management and fewer stockouts, VMI helps ensure product availability, leading to higher customer satisfaction and customer loyalty.
Risks of Vendor Managed Inventory (VMI) and Mitigation Strategies
Vendor Managed Inventory (VMI) can offer significant benefits, but it also comes with potential risks that need careful management. Understanding these risks and implementing appropriate mitigation strategies is crucial for a successful VMI implementation.
Risks of VMI
Loss of Control Over Inventory:
- Risk: When vendors manage inventory, there can be a perceived or actual loss of control over stock levels and order accuracy.
- Mitigation: Establish clear communication channels and regular review processes to monitor inventory levels and ensure alignment with business needs.
Supplier Dependence:
- Risk: Increased reliance on suppliers for inventory management can lead to over-dependence, which may pose risks if the supplier faces disruptions or performance issues.
- Mitigation: Develop contingency plans and maintain a diversified supplier base to reduce risk and avoid dependency on a single supplier.
Data Security Concerns:
- Risk: Sharing inventory data with suppliers raises concerns about data security and confidentiality.
- Mitigation: Implement robust data security measures and agreements to protect sensitive information and ensure compliance with data protection regulations.
Misalignment of Goals:
- Risk: Differences in goals and priorities between the vendor and the buyer can lead to conflicts and inefficiencies in inventory management.
- Mitigation: Align objectives and expectations through regular meetings and collaborative planning to ensure both parties are working towards common goals.
Implementation Complexity:
- Risk: Implementing VMI can be complex, requiring changes to systems, processes, and relationships that may be challenging to manage.
- Mitigation: Plan and execute a phased implementation, provide adequate training, and involve key stakeholders to facilitate a smooth transition.
Inventory Cost Fluctuations:
- Risk: Fluctuations in inventory costs due to supplier pricing changes can impact overall cost management.
- Mitigation: Negotiate clear pricing agreements and review cost structures regularly to manage and stabilize inventory costs.
Supplier Performance Issues:
- Risk: Poor performance by suppliers in managing inventory can lead to stockouts, excess inventory, and operational disruptions.
- Mitigation: Monitor supplier performance closely, set performance metrics, and conduct regular reviews to ensure suppliers meet agreed-upon standards.
Is VMI Inventory Right for My Business?
Determining whether Vendor Managed Inventory (VMI) is suitable for your business involves evaluating specific factors and needs. Here’s how to assess if VMI aligns with your business requirements:
Evaluate Inventory Turnover
VMI is beneficial for businesses with high inventory turnover, as it helps manage stock levels more efficiently. Assess whether your business deals with products that have rapid turnover rates.
Analyze Supply Chain Complexity
If your supply chain is complex with multiple suppliers and distribution points, VMI can streamline processes and improve coordination. Consider the complexity of your supply chain when evaluating VMI.
Consider Demand Predictability
VMI is most effective when demand patterns are stable and predictable. Assess whether your business experiences consistent demand for its products or services.
Review Supplier Relationships
Strong, reliable relationships with suppliers are crucial for successful VMI implementation. Evaluate the quality and reliability of your supplier relationships.
Assess Inventory Costs
If your business faces high inventory holding costs, VMI can help optimize stock levels and reduce these costs. Review your current inventory costs and determine if VMI could offer financial benefits.
Examine Technological Readiness
Implementing VMI requires robust inventory management software and systems. Assess whether your business has the necessary technology or if upgrades are needed.
Determine Resource Availability
VMI requires dedicated resources for managing and monitoring inventory. Evaluate whether your business has the capacity to handle VMI or if additional resources are needed.
Evaluate Customer Service Impact
VMI can improve product availability and customer satisfaction. Consider whether enhancing these aspects aligns with your business goals.
Key Differences Between Vendor Managed Inventory (VMI) and Traditional Inventory Management
Vendor Managed Inventory (VMI) differs significantly from traditional inventory management approaches in several key ways:
1. Responsibility for Inventory Management
- VMI: The vendor takes on the responsibility for monitoring and replenishing inventory at the customer’s location. The vendor proactively manages stock levels based on real-time data, demand forecasts, and agreed-upon parameters.
- Traditional Inventory Management: The customer is responsible for managing their own inventory. They track stock levels, place orders with suppliers, and manage the replenishment process, often requiring significant internal resources and effort.
2. Data Sharing and Collaboration
- VMI: There is a high level of collaboration and data sharing between the customer and the vendor. The vendor is granted access to real-time sales data, inventory levels, and other relevant information, enabling them to make informed decisions about inventory replenishment.
- Traditional Inventory Management: Data sharing is typically minimal, with the customer placing orders based on their own internal analysis. The vendor is usually not involved in the day-to-day management of the customer’s inventory and relies on purchase orders from the customer to initiate replenishment.
3. Replenishment Process
- VMI: Replenishment is automated and managed by the vendor. Based on predefined triggers (such as minimum stock levels), the vendor automatically replenishes inventory without requiring the customer to place an order, ensuring a continuous supply of goods.
- Traditional Inventory Management: The customer is responsible for monitoring stock levels and placing orders when inventory runs low. This manual process can lead to delays, stockouts, or overstock situations if not managed effectively.
4. Supply Chain Efficiency
- VMI: VMI enhances supply chain efficiency by reducing lead times, minimizing stockouts, and optimizing inventory levels. It allows for better alignment between supply and demand, leading to cost savings and improved operational performance.
- Traditional Inventory Management: Efficiency in traditional inventory management depends heavily on the customer’s ability to forecast demand accurately and manage inventory levels effectively. Misalignment between supply and demand can result in higher carrying costs, stockouts, or excess inventory.
5. Inventory Control
- VMI: Inventory control is largely in the hands of the vendor, who is motivated to optimize inventory levels to reduce costs and ensure product availability.
- Traditional Inventory Management: The customer retains full control over inventory decisions, but this also means they bear the full responsibility for any inefficiencies or errors in inventory management.
In summary, VMI shifts the responsibility of inventory management from the customer to the vendor, fostering a more collaborative approach that leverages real-time data and automation to improve supply chain efficiency.
Traditional inventory management, on the other hand, relies on the customer to manage their inventory, often resulting in a more manual and less efficient process.
Key Components and Processes Involved in Vendor Managed Inventory (VMI)
- Data Sharing and Integration
- Real-Time Data Access: The customer provides the vendor with access to real-time data, including current inventory levels, sales data, and demand forecasts.
- System Integration: Integration between the customer’s inventory management system and the vendor’s system ensures seamless data exchange and accurate inventory tracking.
- Inventory Monitoring
- Continuous Tracking: The vendor monitors inventory levels at the customer’s location, using the provided data to assess stock status and demand trends.
- Alerts and Triggers: Automated systems generate alerts or triggers when inventory levels approach predefined thresholds, indicating the need for replenishment.
- Replenishment Planning
- Demand Forecasting: The vendor uses historical data, sales trends, and demand forecasts to determine the optimal replenishment schedule and quantities.
- Order Generation: Based on inventory levels and demand forecasts, the vendor generates and schedules replenishment orders to maintain optimal stock levels.
- Replenishment Execution
- Order Fulfillment: The vendor arranges for the delivery of inventory to the customer’s location according to the agreed-upon schedule and quantities.
- Delivery Management: Coordination of logistics and transportation to ensure timely and accurate delivery of inventory.
- Performance Monitoring and Reporting
- Key Performance Indicators (KPIs): The vendor and customer track KPIs such as inventory turnover rates, stockouts, and order accuracy to evaluate the effectiveness of the VMI arrangement.
- Regular Reviews: Periodic reviews and performance evaluations are conducted to address any issues, optimize processes, and make necessary adjustments.
- Collaborative Planning and Communication
- Joint Planning: The vendor and customer engage in collaborative planning sessions to align on inventory goals, demand forecasts, and supply chain strategies.
- Communication Channels: Effective communication channels are established to facilitate ongoing dialogue, resolve issues, and address changes in demand or supply conditions.
These components and processes ensure that VMI operates smoothly, enhancing inventory management efficiency and fostering a collaborative relationship between vendors and customers.
The Growing Importance of Vendor Managed Inventory (VMI) in Modern Manufacturing
As manufacturing evolves, Vendor Managed Inventory (VMI) is becoming increasingly significant. This strategy involves suppliers taking responsibility for managing and replenishing inventory at the customer’s location, leveraging real-time data to optimize stock levels.
Current trends in manufacturing are driving the adoption of VMI. With globalization and the complexity of modern supply chains, there is a growing need for real-time inventory management. VMI addresses this need by providing suppliers with direct access to inventory data, enabling them to predict demand accurately and reduce lead times.
In the global supply chain, real-time inventory management is crucial. It helps prevent stockouts and overstock situations, ensuring that manufacturers can respond swiftly to changes in demand.
VMI enhances this capability by automating inventory replenishment and improving accuracy, which is essential for maintaining smooth operations in a competitive market.
Several industries benefit significantly from VMI. For instance, in the retail sector, suppliers use VMI to manage inventory levels at retail locations, ensuring that products are consistently available while minimizing excess stock.
Similarly, in the manufacturing sector, VMI helps streamline the supply chain by managing components and raw materials efficiently, which is vital for production schedules and cost control.
In summary, VMI is increasingly important in modern manufacturing due to current trends emphasizing real-time inventory management and efficient supply chain operations.
By integrating VMI, industries can enhance their inventory management practices, optimize supply chain performance, and better meet market demands.
Vendor Managed Inventory's Role in Supply Chain Management
Vendor Managed Inventory (VMI) plays a crucial role in modern supply chain management by enhancing efficiency and responsiveness. In a VMI system, suppliers are entrusted with the responsibility of managing and replenishing inventory at the customer's location.
This approach helps address key challenges in supply chain management, such as reducing lead times, improving inventory turnover, and minimizing stockouts.
VMI integrates seamlessly with supply chain processes by providing suppliers with real-time access to inventory data, enabling them to make informed decisions about replenishment and demand forecasting.
This real-time visibility allows for more accurate inventory management, ensuring that stock levels align closely with actual demand and reducing the risk of excess inventory or shortages.
By shifting the responsibility for inventory management to the supplier, VMI fosters a collaborative approach to supply chain management. It enhances communication between manufacturers and suppliers, leading to more efficient operations and better alignment with market needs.
As a result, VMI not only improves inventory control but also strengthens overall supply chain performance, making it an essential component of modern supply chain strategies.
Vendor Managed Inventory: Advantages and Disadvantages
Vendor Managed Inventory (VMI) offers several benefits and drawbacks that can impact its effectiveness in different contexts. Understanding these advantages and disadvantages is crucial for determining whether VMI is the right approach for your supply chain management needs.
Advantages
- Improved Inventory Management: VMI helps reduce stockouts and overstock situations by allowing vendors to manage inventory levels based on real-time data and demand forecasts.
- Reduced Inventory Costs: By shifting inventory management responsibilities to the supplier, businesses can lower their carrying costs and reduce the need for safety stock.
- Enhanced Supplier Collaboration: VMI fosters closer collaboration between suppliers and customers, leading to better communication and more effective problem-solving.
- Streamlined Replenishment: Automated replenishment processes ensure timely restocking of inventory, improving overall supply chain efficiency.
- Increased Fulfillment Accuracy: With suppliers handling inventory management, there is often a reduction in order errors and increased accuracy in meeting customer demand.
- Better Demand Forecasting: Suppliers, having access to detailed sales and inventory data, can use advanced analytics to predict future demand more accurately, leading to more efficient inventory planning.
- Focus on Core Competencies: By outsourcing inventory management, companies can concentrate on their core business activities, such as production and product development.
Disadvantages
- Data Sharing Challenges: Effective VMI requires robust data sharing between the supplier and customer, which can be a challenge if systems are not well integrated or if there are concerns about data security.
- Dependency on Supplier: Relying on the supplier for inventory management can create dependency, which may be risky if the supplier faces disruptions or performance issues.
- Implementation Costs: Setting up a VMI system can involve significant initial costs, including investments in technology and changes to existing processes.
- Complexity in Coordination: Coordinating inventory levels and replenishment schedules with multiple suppliers can be complex and may require careful management to avoid errors.
- Loss of Control: Businesses may feel a loss of control over their inventory management processes, as the vendor takes over decision-making responsibilities.
- Potential for Supplier Bias: Suppliers might prioritize their own products or interests, potentially leading to biased inventory management that doesn’t fully align with the customer’s needs.
- Integration Issues: Integrating VMI with existing systems and processes can be challenging and may require significant adjustments to ensure smooth operation.
In summary, while VMI can provide significant benefits such as improved inventory management, reduced costs, and enhanced collaboration, it also presents challenges like data sharing issues, dependency on suppliers, and potential integration difficulties.
Balancing these advantages and disadvantages is key to successfully implementing VMI and achieving a more efficient and effective supply chain management strategy.
Challenges and Considerations in Implementing Vendor Managed Inventory (VMI)
Implementing Vendor Managed Inventory (VMI) can offer significant benefits, but it also presents several challenges and considerations that organizations need to address to ensure successful integration and operation.
Here are some key challenges and factors to consider:
1. Data Integration and Sharing
- Challenge: Effective VMI relies on seamless data integration between the supplier and customer. Incompatible systems or poor data quality can hinder real-time data sharing and accurate inventory management.
- Consideration: Invest in compatible inventory management software and ERP systems that facilitate efficient data exchange. Establish clear protocols for data sharing and ensure that both parties have access to accurate and timely information.
2. Supplier Dependency
- Challenge: Relying on a supplier for inventory management can create dependency, which may be risky if the supplier experiences disruptions or performance issues.
- Consideration: Evaluate the supplier’s reliability and capabilities before entering into a VMI agreement. Develop contingency plans to mitigate risks associated with supplier performance and ensure continuity in inventory management.
3. Implementation Costs
- Challenge: Setting up a VMI system involves initial costs, including investments in technology, process changes, and staff training.
- Consideration: Conduct a cost-benefit analysis to understand the potential return on investment. Budget for implementation costs and ensure that the benefits of VMI outweigh the initial expenditure.
4. Complexity in Coordination
- Challenge: Coordinating inventory levels and replenishment schedules with multiple suppliers can be complex and may lead to coordination issues.
- Consideration: Establish clear communication channels and coordination mechanisms. Use advanced VMI tools and software to streamline coordination and manage multiple supplier relationships effectively.
5. Loss of Control
- Challenge: Shifting inventory management responsibilities to the supplier may lead to a perceived loss of control over inventory levels and replenishment processes.
- Consideration: Maintain regular oversight and communication with the supplier to ensure that inventory management aligns with your business goals and requirements. Set clear performance metrics and review them periodically.
6. Supplier Bias
- Challenge: Suppliers might prioritize their own products or interests, potentially leading to biased inventory management that doesn’t fully meet the customer’s needs.
- Consideration: Establish clear agreements and guidelines regarding inventory management priorities. Ensure that the supplier’s incentives align with your business objectives and that inventory decisions are based on mutual benefits.
7. Integration with Existing Processes
- Challenge: Integrating VMI with existing inventory management processes and systems can be challenging and may require significant adjustments.
- Consideration: Plan for a phased implementation and involve key stakeholders in the transition process. Provide training and support to ensure a smooth integration of VMI into your current operations.
In summary, while VMI offers many advantages, successfully implementing it requires careful planning and management of challenges such as data integration, supplier dependency, and coordination complexity. By addressing these considerations, organizations can optimize their VMI strategy and enhance their overall supply chain efficiency.
Steps to Successfully Implement Vendor Managed Inventory (VMI) in Manufacturing
Implementing Vendor Managed Inventory (VMI) can significantly enhance inventory management and supply chain efficiency.
To ensure a successful VMI implementation in manufacturing, follow these key steps:
1. Assess Readiness and Define Objectives
- Evaluate Current Processes: Assess your current inventory management processes, systems, and capabilities. Identify areas where VMI can add value.
- Set Clear Objectives: Define specific goals for implementing VMI, such as reducing stockouts, improving inventory turnover, or enhancing supplier relationships.
2. Select the Right Supplier
- Evaluate Potential Suppliers: Choose suppliers who have a proven track record in managing inventory and can meet your specific requirements. Ensure they have the technological capability to integrate with your systems.
- Negotiate Terms: Establish clear agreements on inventory management responsibilities, performance metrics, and communication protocols.
3. Implement Technology Solutions
- Invest in VMI Software: Select and implement vendor managed inventory software that integrates with your existing ERP and inventory management software. Ensure the software supports real-time data sharing and analytics.
- Ensure System Compatibility: Verify that the VMI system is compatible with both your internal systems and those of your suppliers to facilitate smooth data exchange.
4. Establish Data Sharing Protocols
- Define Data Requirements: Agree on the types of data to be shared, such as inventory levels, sales forecasts, and order history.
- Set Up Data Integration: Implement systems and processes for seamless data integration between your organization and the supplier, ensuring data accuracy and timeliness.
5. Develop a Communication Plan
- Create Communication Channels: Establish clear communication channels for regular updates and issue resolution. Ensure both parties are aligned on expectations and processes.
- Schedule Regular Meetings: Conduct regular meetings with your supplier to review performance, address any issues, and adjust inventory strategies as needed.
6. Train and Onboard Teams
- Provide Training: Train your team and the supplier’s team on VMI processes, software usage, and communication protocols. Ensure everyone understands their roles and responsibilities.
- Onboard Stakeholders: Engage all relevant stakeholders in the onboarding process to ensure a smooth transition and buy-in from all parties involved.
7. Monitor and Evaluate Performance
- Track Key Metrics: Monitor performance metrics such as inventory levels, order accuracy, and fulfillment rates to evaluate the effectiveness of the VMI system.
- Review and Adjust: Regularly review performance data and make adjustments to the VMI processes or agreements as needed to optimize results.
8. Continuously Improve
- Solicit Feedback: Gather feedback from your team and the supplier to identify areas for improvement and address any challenges encountered during implementation.
- Optimize Processes: Continuously refine and enhance VMI processes based on performance data and feedback to ensure ongoing efficiency and effectiveness.
By following these steps, manufacturing organizations can successfully implement Vendor Managed Inventory (VMI) and leverage its benefits to enhance inventory management, reduce costs, and improve supply chain performance.
How Deskera ERP Can Help You with Vendor Managed Inventory (VMI)
Deskera ERP offers a range of features designed to support and optimize Vendor Managed Inventory (VMI) implementations. By leveraging Deskera ERP’s capabilities, businesses can effectively manage their VMI processes, improve inventory control, and enhance supply chain efficiency.
Here’s how Deskera ERP can help with VMI:
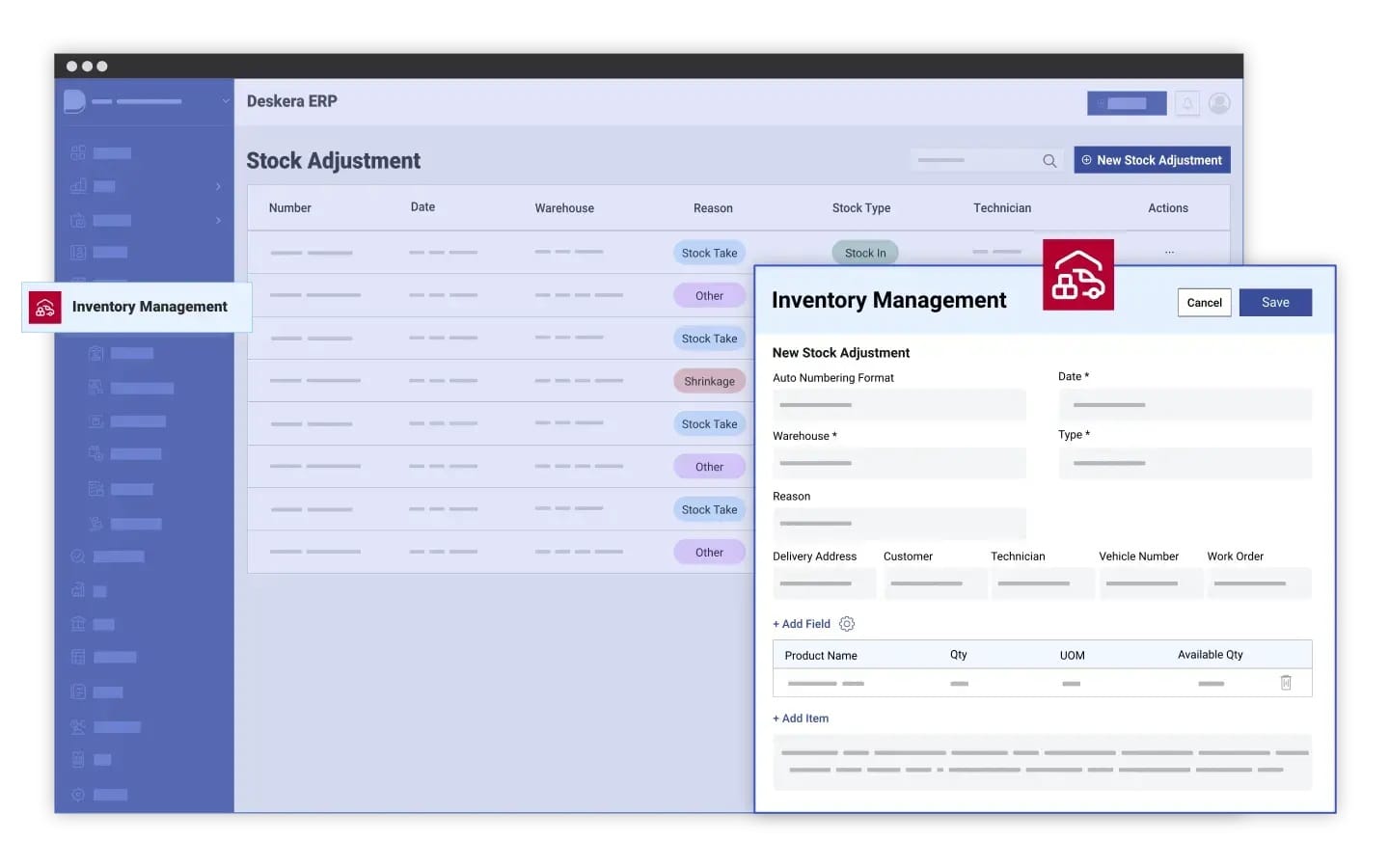
- Real-Time Inventory Visibility:
- Feature: Deskera ERP provides real-time inventory tracking and visibility.
- Benefit: Vendors can access up-to-date inventory levels, sales data, and stock movements, allowing for timely and accurate inventory management.
- Automated Replenishment:
- Feature: Deskera ERP includes automated replenishment capabilities.
- Benefit: This feature helps ensure that inventory levels are maintained based on predefined thresholds and demand patterns, reducing the risk of stockouts and overstocking.
- Advanced Reporting and Analytics:
- Feature: Deskera ERP offers advanced reporting and analytics tools.
- Benefit: Vendors and businesses can generate detailed reports and analyze inventory performance, helping to optimize stock levels and improve forecasting accuracy.
- Integrated Supply Chain Management:
- Feature: Deskera ERP integrates various supply chain management functions.
- Benefit: This integration ensures seamless communication and coordination between vendors and businesses, improving overall supply chain efficiency and reducing lead times.
- Demand Forecasting:
- Feature: Deskera ERP includes demand forecasting tools.
- Benefit: Accurate demand forecasting helps vendors and businesses predict future inventory needs, allowing for better planning and inventory management.
- Supplier Collaboration:
- Feature: Deskera ERP facilitates collaboration with suppliers.
- Benefit: Improved communication and data sharing between businesses and vendors help streamline inventory management processes and enhance the effectiveness of VMI.
- Inventory Control and Optimization:
- Feature: Deskera ERP provides tools for inventory control and optimization.
- Benefit: These tools help maintain optimal inventory levels, manage stock turnover, and reduce carrying costs, supporting the goals of VMI.
- Customizable Dashboards:
- Feature: Deskera ERP offers customizable dashboards.
- Benefit: Users can tailor dashboards to display key VMI metrics and performance indicators, providing quick access to critical information and insights.
- Seamless Integration with Existing Systems:
- Feature: Deskera ERP integrates with other business systems.
- Benefit: This seamless integration ensures that VMI processes are well-coordinated with other aspects of inventory and supply chain management.
By utilizing Deskera ERP’s features, businesses can effectively implement and manage VMI, leading to improved inventory control, enhanced supplier relationships, and greater overall efficiency in their supply chain operations.
Key Takeaways
- VMI can significantly enhance manufacturing operations by reducing lead times by 40%, increasing fulfillment accuracy by 25%, boosting repeat purchase rates by 20%, and improving sales by 15%. Deskera ERP supports VMI with features such as real-time inventory visibility, automated replenishment, and advanced analytics.
- VMI is a supply chain strategy where suppliers manage and replenish inventory levels at the customer's location. Key features include real-time inventory management, automated replenishment, and improved coordination between suppliers and customers.
- The primary aim of VMI is to optimize inventory levels, reduce stockouts and overstocking, and enhance order fulfillment. It focuses on improving supply chain efficiency through better coordination and communication.
- VMI provides real-time data access for accurate inventory management, includes automated replenishment systems to maintain optimal inventory levels, and enhances coordination between suppliers and customers for better inventory planning.
- VMI measures inventory levels, order fulfillment accuracy, lead times, and stock turnover rates. It tracks key performance indicators such as inventory turnover ratio, order cycle time, and demand forecast accuracy.
- VMI is best used when inventory turnover is high, demand patterns are predictable, and strong supplier relationships exist. It is particularly effective in complex supply chains needing improved inventory efficiency.
- VMI is utilized in industries such as retail, automotive, and consumer goods for efficient stock replenishment. Examples include major retailers and automotive manufacturers managing inventory through VMI.
- VMI solves issues such as stockouts, overstocking, inefficient replenishment, and poor demand forecasting. It delivers benefits such as enhanced inventory efficiency, cost savings, and improved customer satisfaction.
- Risks associated with VMI include loss of control over inventory, supplier dependence, data security concerns, and implementation complexity. Mitigation strategies involve clear communication, supplier diversification, robust data security, and phased implementation.
- To determine if VMI is right for your business, evaluate factors such as inventory turnover, supply chain complexity, demand predictability, and supplier relationships. Consider technological readiness and resource availability for supporting VMI.
- VMI differs from traditional inventory management approaches by shifting inventory management responsibilities to suppliers, using real-time data, and automating replenishment. It offers improved coordination and inventory optimization compared to traditional methods.
- VMI plays a critical role in enhancing supply chain efficiency, collaboration between suppliers and customers, and inventory management. It contributes to better supply chain visibility, reduced lead times, and improved overall performance.
- Key components of VMI include real-time data sharing, automated inventory management, and collaborative planning. Important processes involve inventory monitoring, replenishment planning, and performance measurement.
- Implementing VMI presents challenges such as system integration, data accuracy, supplier training, and change management. Considerations include selecting the right technology, establishing clear communication channels, and setting realistic implementation goals.
- Successfully implementing VMI involves assessing readiness, selecting technology, establishing supplier agreements, and monitoring performance. Best practices include involving key stakeholders, setting clear objectives, and conducting regular reviews.
- The growing importance of VMI in modern manufacturing reflects trends like increased complexity, demand for real-time data, and the need for efficient inventory management. VMI is becoming increasingly vital for enhancing supply chain efficiency and adapting to market demands.
- VMI offers significant benefits, including improved inventory management, cost savings, and enhanced supply chain efficiency. Deskera ERP provides valuable support for VMI with its robust features and tools, helping businesses optimize their operations and gain a competitive edge.
Related Articles
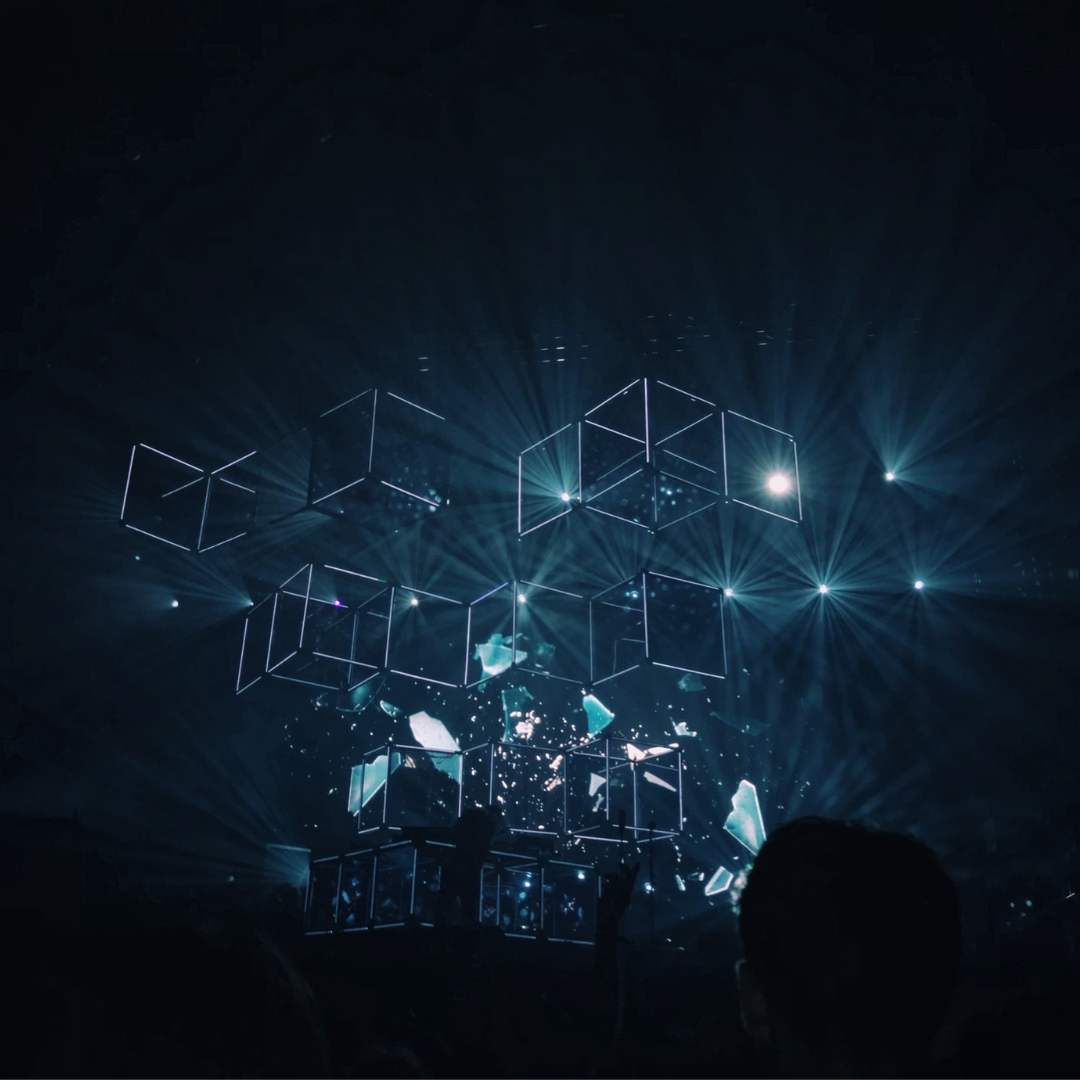
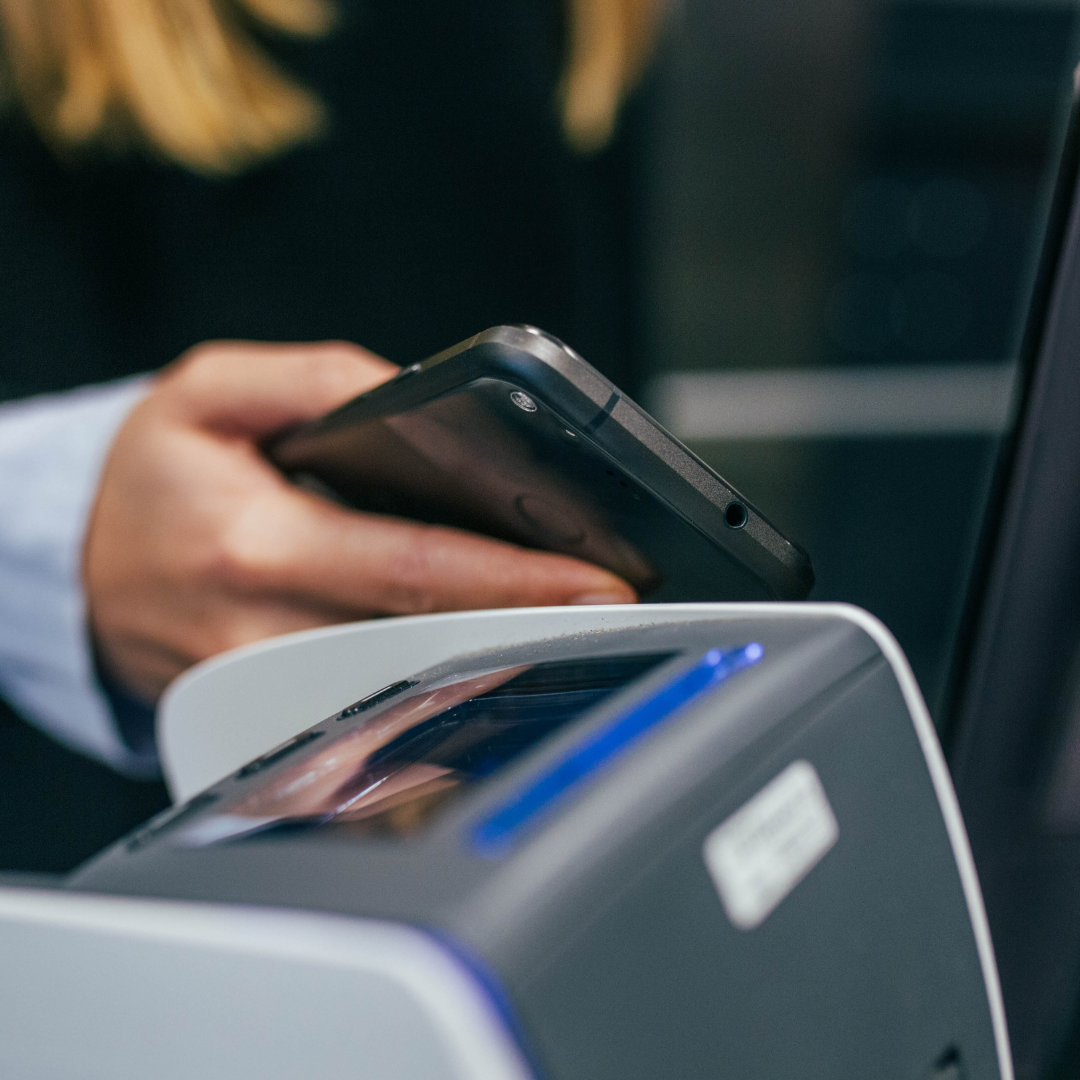
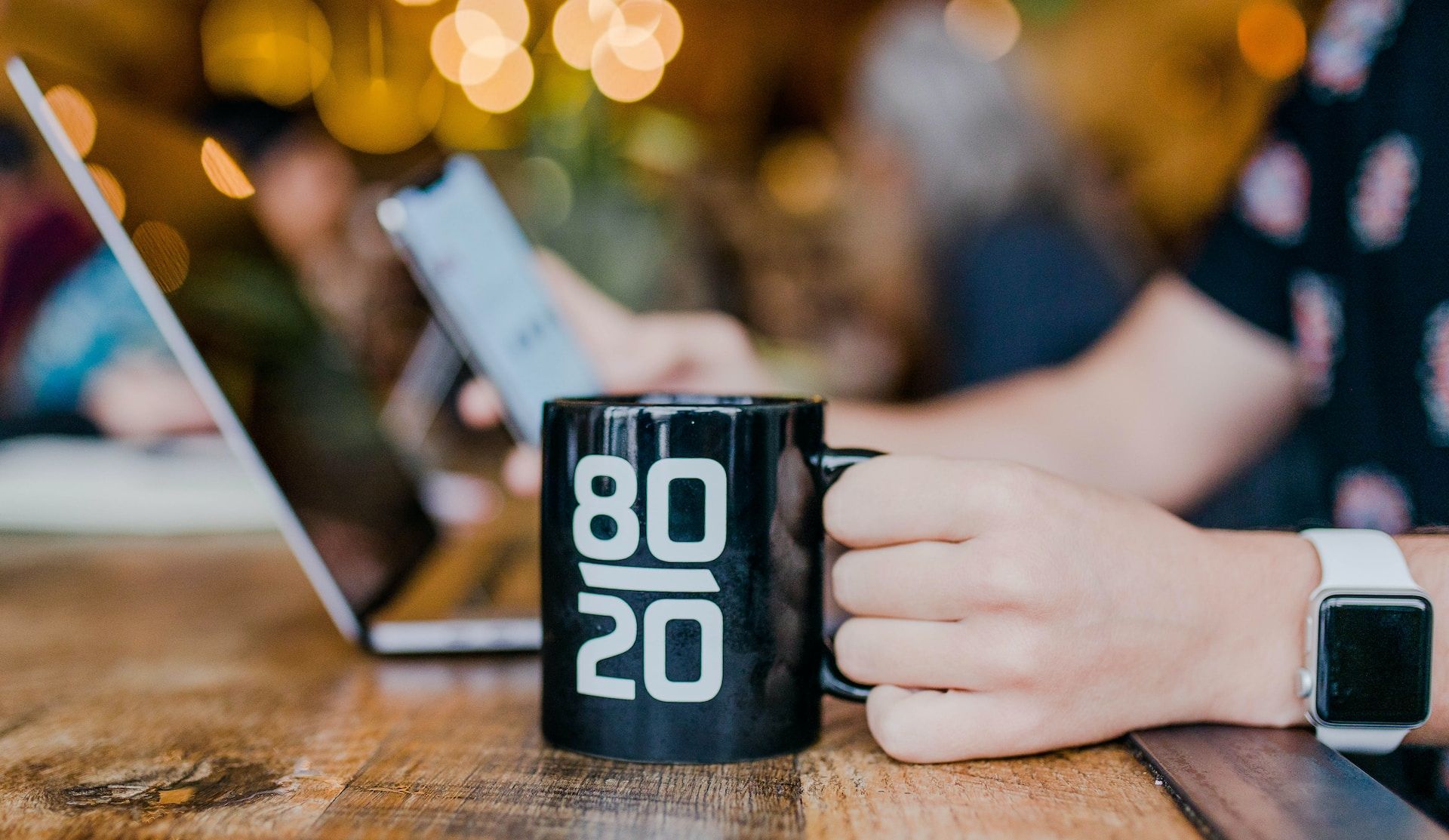
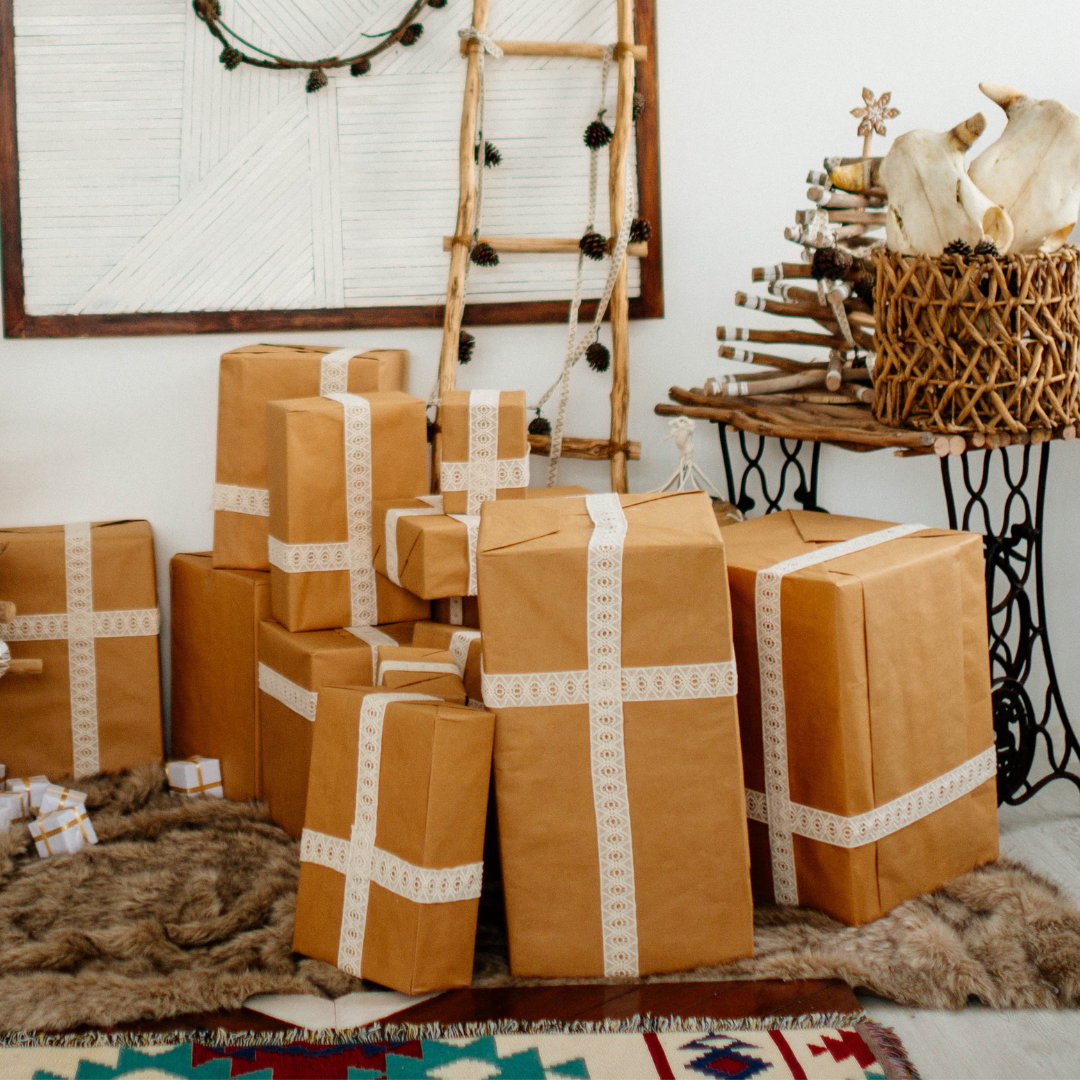
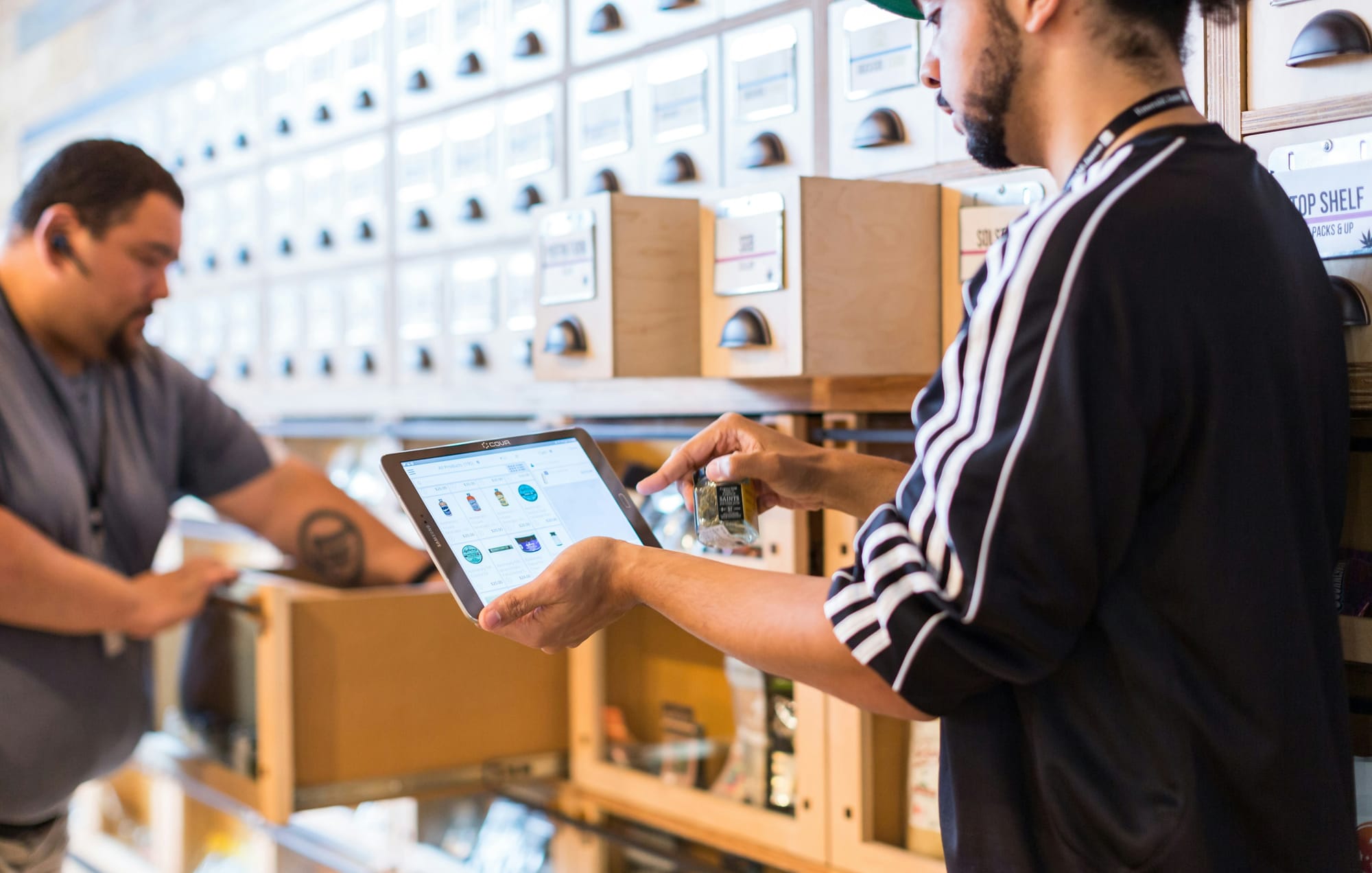
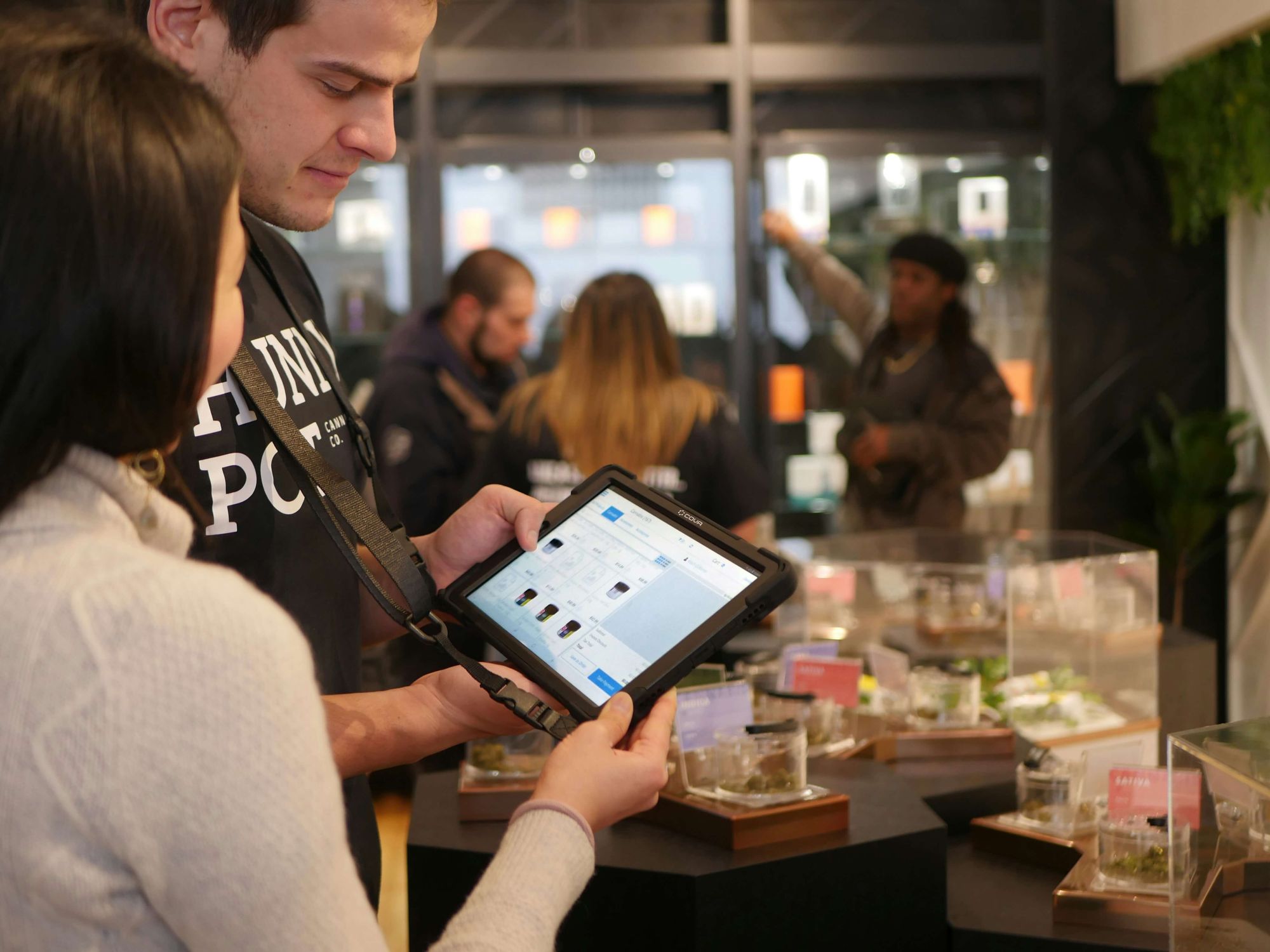