Plastic manufacturing is an essential part of the global economy. Every year, it continues to play an important role in developing new products, creating jobs, and mitigating waste.
The use of plastic has become ingrained in our everyday lives. From food packaging to medical devices, we rely on plastic to help us live a more sustainable lifestyle. However, like anything else, its use comes with consequences.
As we transition towards a more sustainable future, it is important to understand the key trends and innovations that will drive the growth of plastic manufacturing. In this article, we will take a look at some of the major developments that are currently taking place in the plastic industry. Let's take a look at the table of content below:
- Need of Innovation in Plastic Manufacturing
- Key Trends and Innovation in Plastic Manufacturing
- Wrapping Up
- How Deskera Can Assist You?
Let's begin!
Need of Innovation in Plastic Manufacturing
Plastic production has become an essential part of our daily lives because of its adaptability and affordability. The manufacture of plastic has had a significant negative impact on the environment, despite the fact that millions of tonnes of plastic waste end up in our oceans and landfills every year. The sector must embrace innovation if it is to create a more sustainable future for both the industry and the environment.
One of the key challenges in the manufacture of plastic is reducing the use of fossil fuels. By using sustainable practices including reducing energy use, utilizing renewable energy sources, and simplifying industrial processes, the industry can reduce its carbon footprint.
Using energy-efficient equipment and simplifying production processes, for example, can reduce energy consumption and greenhouse gas emissions.
Innovation can also help find alternatives to conventional plastic and help reduce reliance on fossil resources.
For instance, because they are made from renewable resources like corn flour or sugarcane and are biodegradable, bioplastics are a more sustainable alternative to traditional plastic. The creation of items on demand and cutting-edge developments like 3D printing, which enable more efficient manufacturing processes, can also help reduce waste.
Yet, the plastics industry faces a distinct set of challenges when it comes to innovation. For instance, efforts are ongoing to identify environmentally friendly alternatives to common plastic additives. Furthermore, because sustainable materials are expensive, some businesses can find it challenging to use them.
By supporting research and development, rewarding eco-friendly behaviour, and enacting regulations that favour eco-friendly manufacturing practices, governments may help address these concerns.
Key Trends and Innovation in Plastic Manufacturing
Plastics manufacturing is a significant industry, accounting for over $522 billion in global revenue in 2020, and is expected to continue to grow at a CAGR of 3.9% from 2021 to 2028. The industry is constantly evolving, with new trends and innovations emerging all the time.
Following, we've discussed some key trends and innovations currently shaping the plastic industry:
1. Interconnected Factories
According to a report by PwC, 91% of plastics manufacturers are investing in Industry 4.0 technologies, such as interconnected factories that use real-time data to optimize production processes. By 2025, the global market for Industry 4.0 technologies in plastics manufacturing is expected to reach $4.5 billion.
Interconnected factories, also known as smart factories, are a major trend in the manufacturing industry, including plastics manufacturing. Essentially, these are factories that are digitally integrated, with machines and systems that can communicate with each other in real-time, thanks to advancements on the Internet of Things (IoT) and other digital technologies.
There are several key benefits to interconnected factories in plastics manufacturing.
First, they allow for increased efficiency and productivity. Machines and systems can work together seamlessly, without human intervention, to optimize production and reduce downtime. For example, sensors can detect when a machine needs maintenance or repair and automatically schedule it, preventing costly downtime.
Second, interconnected factories enable better decision-making. Data collected from various machines and systems can be analyzed in real-time, allowing factory managers to identify issues, make adjustments, and optimize production in ways that would be difficult or impossible without such technology.
Third, interconnected factories can improve quality control. Sensors and other digital tools can detect defects or issues in real-time, enabling manufacturers to catch and correct problems before they become major issues. This can help reduce waste, improve product quality, and increase customer satisfaction.
Overall, interconnected factories are a major trend in plastics manufacturing, with many companies investing in digital technologies and other tools to improve their operations and stay competitive. While there are some challenges to implementing smart factory technology, such as the cost of investment and the need for specialized expertise, many companies see the benefits as outweighing the risks.
2. Paying Attention to the Environmental Impact
A survey by McKinsey found that 91% of plastics manufacturers are either already implementing or planning to implement sustainable practices in their operations. In 2020, the global market for recycled plastics was valued at $37.5 billion and is expected to grow at a CAGR of 6.8% from 2021 to 2028.
The plastics manufacturing industry has long been criticized for its negative impact on the environment. As a result, one major trend in the industry is a growing attention to environmental impact, with companies taking steps to reduce waste, emissions, and other negative effects.
Some of the ways in which plastics manufacturers are addressing environmental concerns include:
Using sustainable materials: Manufacturers are exploring alternative materials, such as bioplastics made from renewable resources, as well as recycled plastics, to reduce their reliance on non-renewable resources and reduce waste.
Implementing recycling programs: Many plastics manufacturers are implementing recycling programs for their own waste, as well as working to improve overall recycling rates for plastics. This can help reduce waste and emissions, as well as conserve resources.
Improving energy efficiency: By investing in energy-efficient technologies and processes, manufacturers can reduce their carbon footprint and save on energy costs.
Addressing supply chain concerns: Some companies are working to address environmental concerns in their supply chains, such as reducing the use of single-use plastics in packaging or sourcing materials from sustainable sources.
Engaging in advocacy and education: Many plastics manufacturers are engaging in advocacy efforts and public education campaigns to promote sustainable practices and raise awareness of environmental concerns.
Overall, there is a growing recognition in the plastics manufacturing industry that environmental sustainability is not only important for the planet, but also for long-term business success. As a result, more and more companies are taking steps to reduce their environmental impact and promote sustainable practices.
3. Light-Weighting Material Selection
According to a report by Grand View Research, the global market for lightweight materials in the automotive industry, a key market for plastics, was valued at $76.6 billion in 2020, and is expected to grow at a CAGR of 7.6% from 2021 to 2028.
Light weighting is a process in which manufacturers strive to reduce the weight of their plastic products without sacrificing performance or quality. This trend is driven by several factors, including the desire to reduce material usage, transportation costs, and environmental impact.
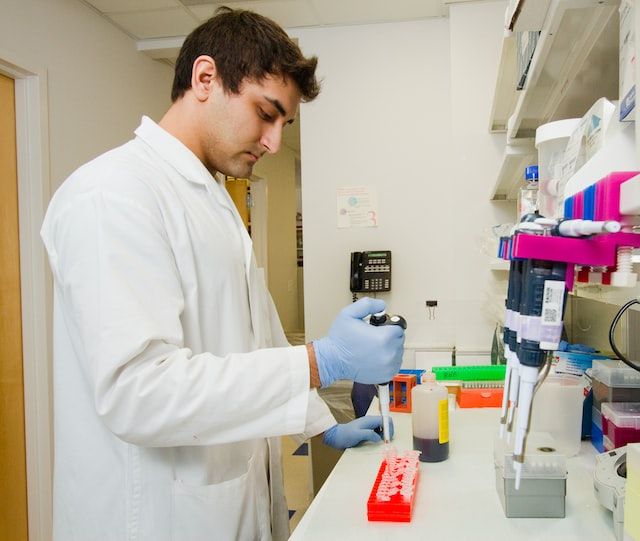
One-way manufacturers achieve light-weighting is through material selection. There are several types of plastic materials that can be used to make lighter-weight products, including:
Polypropylene (PP): PP is a lightweight, versatile material that is commonly used in packaging and consumer products. It is also known for its durability and resistance to moisture.
Polycarbonate (PC): PC is a lightweight, high-performance plastic that is often used in automotive and aerospace applications. It is known for its strength and toughness, making it ideal for products that need to withstand high stresses.
Polyethylene (PE): PE is a lightweight, low-density plastic that is commonly used in packaging and consumer products. It is also known for its flexibility and resistance to chemicals.
Acrylonitrile butadiene styrene (ABS): ABS is a lightweight, impact-resistant plastic that is often used in consumer products, such as toys and electronics. It is known for its strength and durability.
In addition to material selection, manufacturers may also use other techniques to achieve light-weighting, such as design optimization and using thinner walls. By reducing the weight of their products, manufacturers can not only reduce material usage and transportation costs, but also improve sustainability and reduce their environmental impact.
However, it's important to note that light-weighting must be done carefully, as reducing the weight of a product too much can result in decreased performance or durability. As a result, manufacturers must balance the desire for lighter-weight products with the need for quality and safety.
4. More Automation and Customization
The global market for plastics manufacturing automation is expected to grow at a CAGR of 6.7% from 2021 to 2028, according to a report by Grand View Research. Additionally, a survey by Deloitte found that 50% of plastics manufacturers are investing in customization technologies, such as 3D printing, to meet growing customer demands.
More automation and customization are two interrelated trends in the plastics manufacturing industry. Advances in digital technologies and automation have made it possible for manufacturers to produce more customized products at scale, while also reducing costs and improving efficiency.
Automation refers to the use of machines, robots, and other digital tools to perform tasks that were previously done by humans. In the plastics manufacturing industry, automation is increasingly being used for tasks such as injection molding, packaging, and quality control. Automation can help reduce costs by increasing efficiency and reducing the need for human labor, while also improving product quality and consistency.
Customization, on the other hand, refers to the ability to produce products that are tailored to specific customer needs or preferences. This can include customized colors, sizes, shapes, and other features. Advances in digital technologies have made it possible for manufacturers to offer more customized products without sacrificing efficiency or cost-effectiveness.
The intersection of these two trends means that manufacturers can now produce customized products at scale, thanks to the use of automation and other digital tools.
For example, a plastics manufacturer might use 3D printing technology to produce customized molds for injection molding, while also using robotics to automate the molding process. This can help reduce lead times and improve production efficiency, while also allowing for greater customization and flexibility.
Ultimately, the trend towards more automation and customization is driven by a desire to improve efficiency, reduce costs, and meet customer demands for more personalized products. As digital technologies continue to advance, we can expect to see even greater levels of automation and customization in the plastics manufacturing industry.
5. Near-Shoring
According to a report by Plastics Today, 38% of plastics manufacturers have already moved production facilities closer to end markets, and another 36% are planning to do so in the near future.
Near-shoring is a trend in the plastics manufacturing industry that involves relocating production facilities closer to the end markets they serve. This is in contrast to offshoring, which involves moving production to countries with lower labor costs and regulatory barriers.
The main drivers behind the trend towards near-shoring in the plastics manufacturing industry are:
Improved supply chain resilience: The COVID-19 pandemic highlighted the risks of relying on long, complex global supply chains. By moving production facilities closer to end markets, companies can reduce the risk of disruption caused by factors such as natural disasters, geopolitical tensions, or global pandemics.
Lower transportation costs: By reducing the distance between production facilities and end markets, companies can save on transportation costs, which can be a significant expense in the plastics manufacturing industry.
Faster lead times: Near-shoring can also help reduce lead times, which is especially important in industries where speed to market is critical. By producing products closer to end markets, companies can reduce the time it takes to get products to customers.
Improved quality control: Moving production closer to end markets can also improve quality control, as companies can more easily monitor production processes and ensure that products meet local quality standards.
Increased flexibility: Near-shoring can also provide companies with greater flexibility to respond to changes in customer demand or market conditions. By being closer to end markets, companies can more quickly adjust production volumes or product offerings to meet changing customer needs.
Eventually, the trend towards near-shoring in the plastics manufacturing industry is driven by a desire to improve supply chain resilience, reduce costs, and increase flexibility. While there may be some initial costs associated with relocating production facilities, many companies see near-shoring as a strategic investment in their long-term success.
Wrapping Up
In conclusion, the plastics manufacturing industry is a dynamic and constantly evolving industry, with new trends and innovations emerging all the time. The industry is driven by a variety of factors, including customer demand, technological advancements, environmental concerns, and regulatory requirements.
Key trends and innovations currently shaping the industry include the adoption of interconnected factories, a growing focus on reducing environmental impact, the use of lightweight materials, increased automation and customization, and the trend towards near-shoring.
While each of these trends and innovations is important in its own right, they are also interconnected and often reinforce each other.
For example, the adoption of Industry 4.0 technologies in interconnected factories can help improve efficiency and reduce waste, which in turn can help reduce the industry's environmental impact. Similarly, the use of lightweight materials can help reduce transportation costs, which can make near-shoring more attractive.
As the industry continues to evolve, it is likely that new trends and innovations will emerge, driven by changes in technology, customer demand, and global economic conditions.
Ultimately, the ability of plastics manufacturers to stay ahead of these trends and innovate will be key to their long-term success in an increasingly competitive and rapidly changing industry.
How Deskera Can Assist You?
Deskera's integrated financial planning tools allow investors to better plan their investments and track their progress. It can help investors make decisions faster and more accurately.
Deskera Books enables you to manage your accounts and finances more effectively. Maintain sound accounting practices by automating accounting operations such as billing, invoicing, and payment processing.
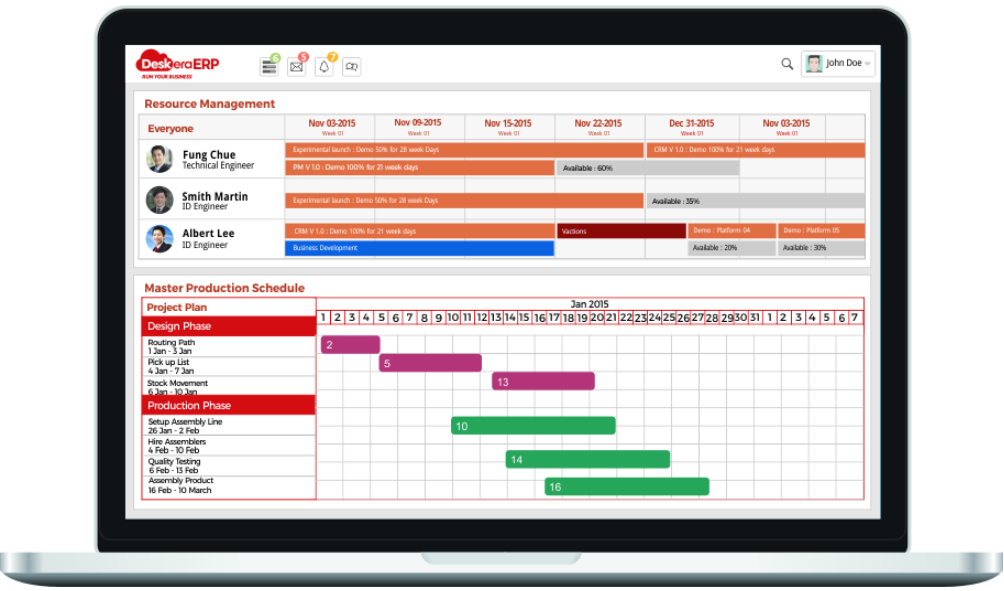
Deskera CRM is a strong solution that manages your sales and assists you in closing agreements quickly. It not only allows you to do critical duties such as lead generation via email, but it also provides you with a comprehensive view of your sales funnel.
Deskera People is a simple tool for taking control of your human resource management functions. The technology not only speeds up payroll processing but also allows you to manage all other activities such as overtime, benefits, bonuses, training programs, and much more. This is your chance to grow your business, increase earnings, and improve the efficiency of the entire production process.
Final Takeaways
We've arrived at the last section of this guide. Let's have a look at some of the most important points to remember:
- Interconnected factories, also known as smart factories, are a major trend in the manufacturing industry, including plastics manufacturing. Essentially, these are factories that are digitally integrated, with machines and systems that can communicate with each other in real-time, thanks to advancements in the Internet of Things (IoT) and other digital technologies.
- Using sustainable materials: Manufacturers are exploring alternative materials, such as bioplastics made from renewable resources, as well as recycled plastics, to reduce their reliance on non-renewable resources and reduce waste.
- Sensors and other digital tools can detect defects or issues in real-time, enabling manufacturers to catch and correct problems before they become major issues. This can help reduce waste, improve product quality, and increase customer satisfaction.
- Light-weighting is a process in which manufacturers strive to reduce the weight of their plastic products without sacrificing performance or quality. This trend is driven by several factors, including the desire to reduce material usage, transportation costs, and environmental impact.
- Addressing supply chain concerns: Some companies are working to address environmental concerns in their supply chains, such as reducing the use of single-use plastics in packaging or sourcing materials from sustainable sources.
- Automation refers to the use of machines, robots, and other digital tools to perform tasks that were previously done by humans. In the plastics manufacturing industry, automation is increasingly being used for tasks such as injection molding, packaging, and quality control. Automation can help reduce costs by increasing efficiency and reducing the need for human labor, while also improving product quality and consistency.
- Near-shoring is a trend in the plastics manufacturing industry that involves relocating production facilities closer to the end markets they serve. This is in contrast to offshoring, which involves moving production to countries with lower labor costs and regulatory barriers.
Related Articles
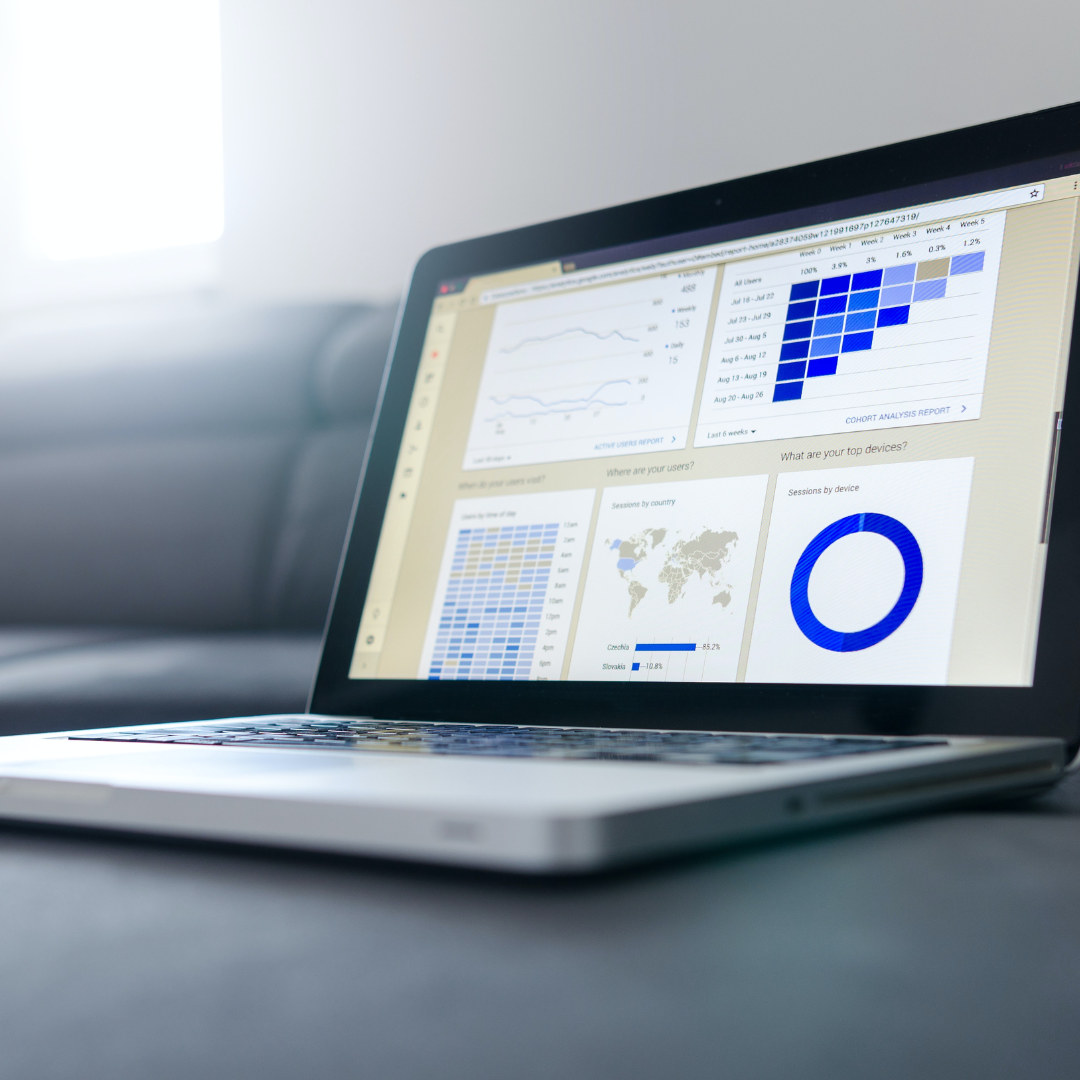
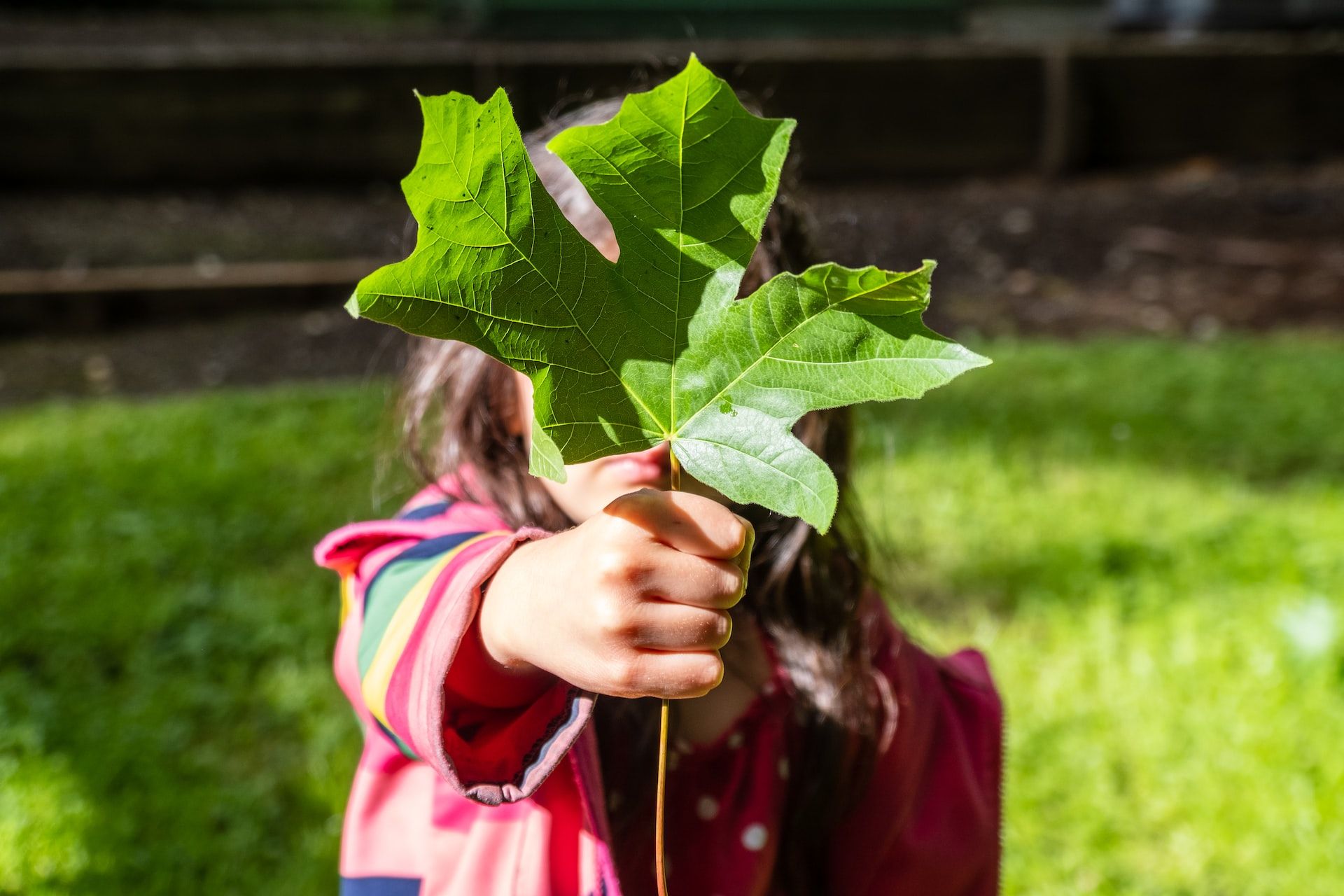
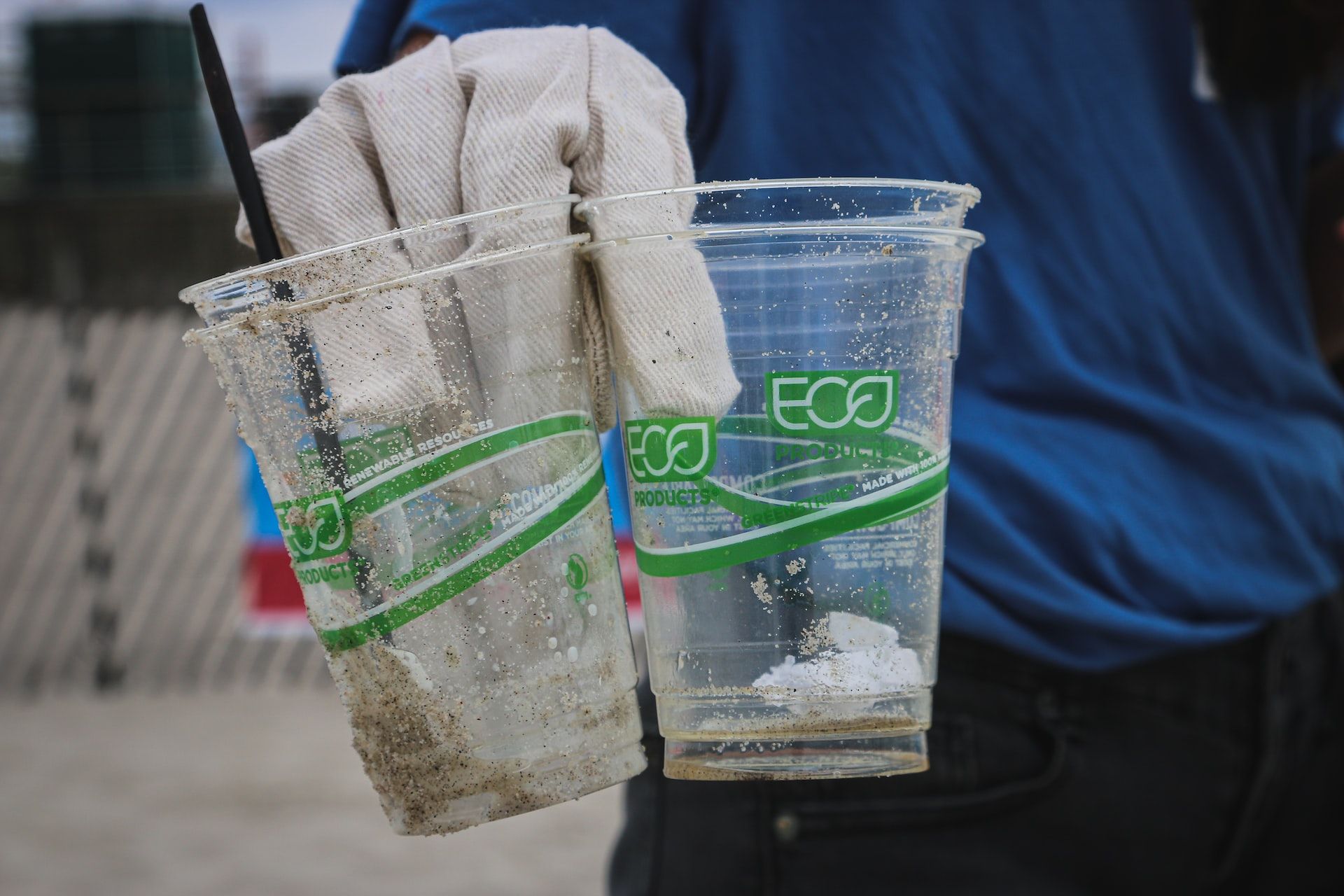
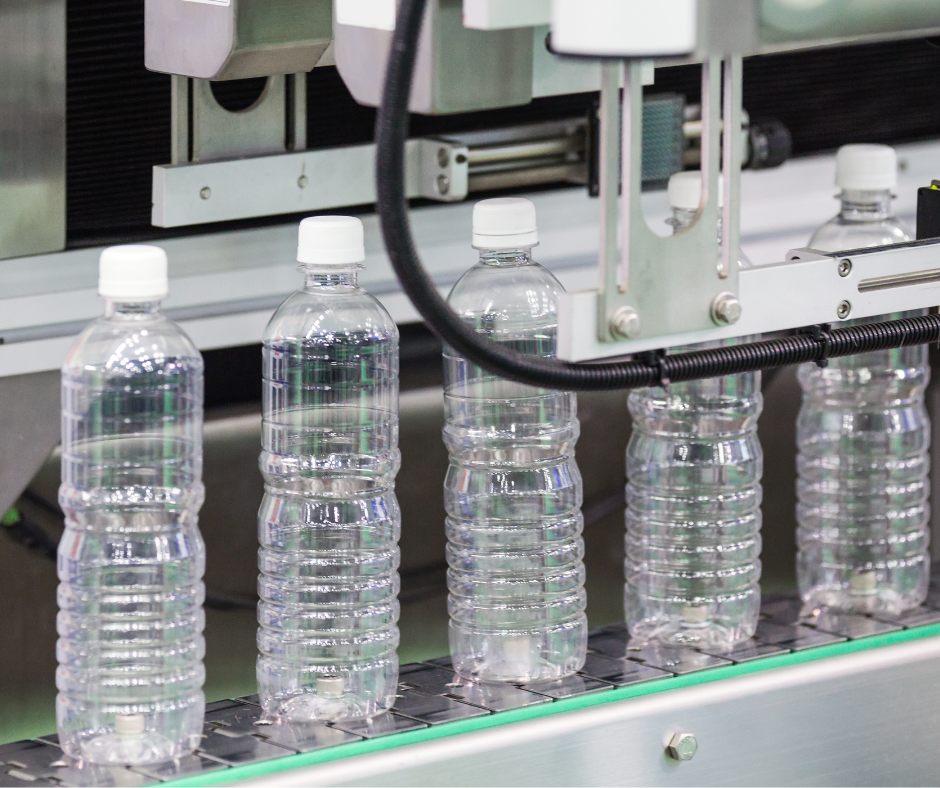
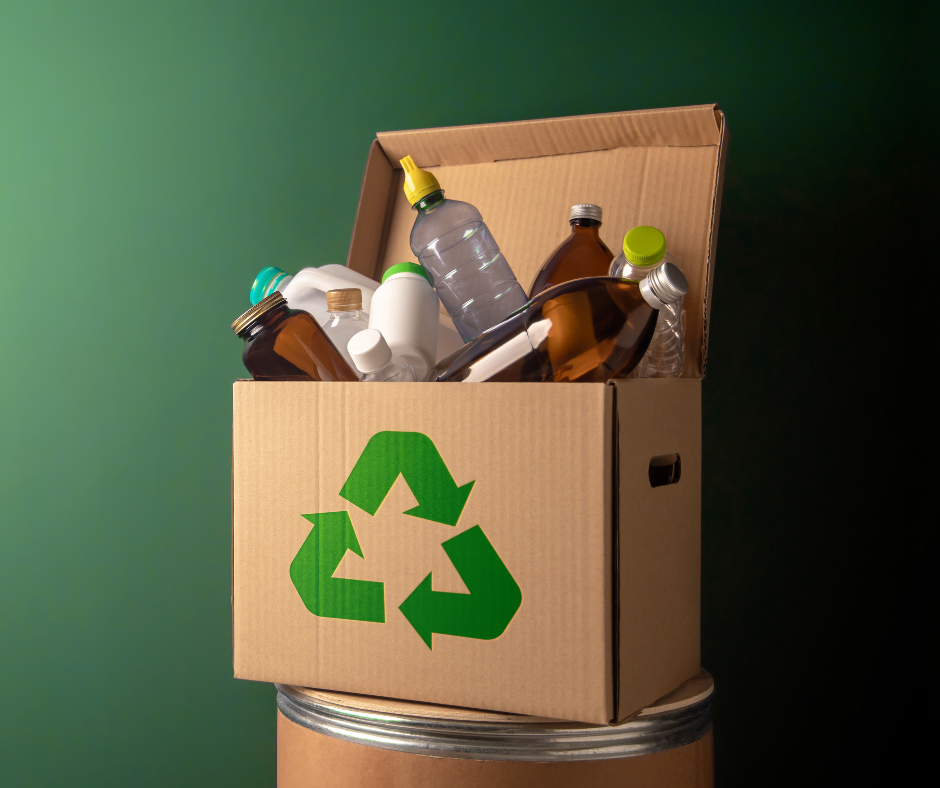