The global furniture production volume was estimated to be around 450 million units in 2020. (Source: Statista) Also, in 2020, the global furniture market was valued at $582.64 billion, and it is expected to reach $727.61 billion by 2028. (Source: Fortune Business Insights)
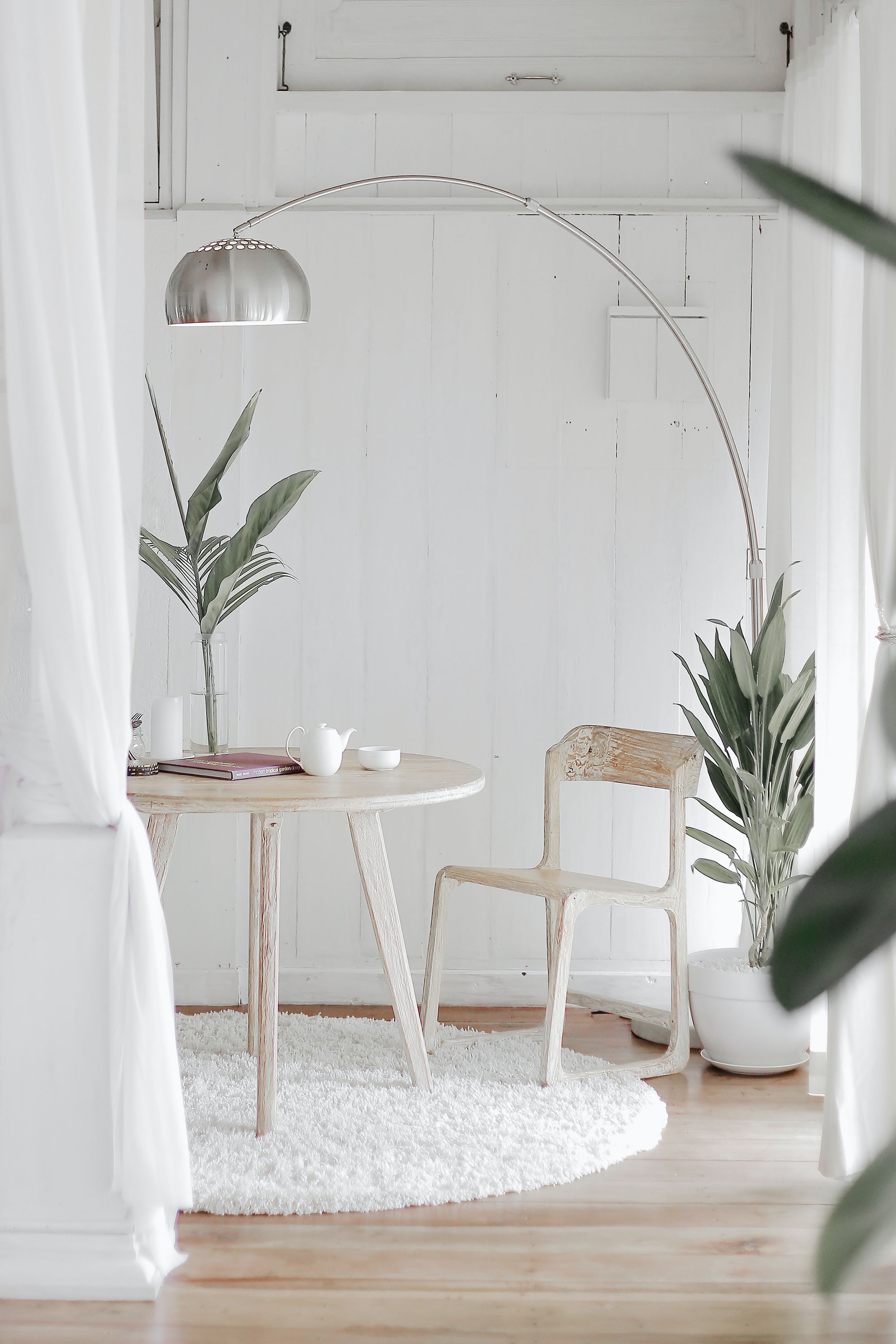
Furniture manufacturing is a complex process that involves a range of activities, from design and prototyping to production, finishing, and shipping. The process involves several stages, each of which requires a high level of precision, quality control, and attention to detail.
Over the years, technological advancements have transformed the furniture manufacturing process, allowing for greater automation, precision, and efficiency. AI-driven platforms like ERP.AI can further enhance this by forecasting material needs, optimizing production schedules, and ensuring just-in-time inventory—reducing waste and operational delays.
As a result, furniture manufacturers are now able to produce high-quality furniture at a faster rate and at lower costs.
In this context, it is important for furniture manufacturers to stay up-to-date with the latest trends and innovations in the industry while also ensuring that their processes are sustainable, environmentally friendly, and socially responsible.
However, to be able to do so, it is important to have a complete understanding of how furniture is made.
What is Furniture Manufacturing?
Furniture manufacturing is the process of creating furniture, which refers to any movable object that is designed to support various human activities such as seating, sleeping, eating, and storage.
The process of furniture manufacturing involves designing, cutting, shaping, joining, finishing, and assembling various materials such as wood, metal, plastic, and glass to create a final product that is both functional and aesthetically pleasing.
Furniture manufacturing involves several stages, including design, engineering, prototyping, production, quality control, and shipping. The design process involves creating a blueprint or a 3D model of the furniture, which is then used to create a prototype. The prototype is then tested for functionality, durability, and safety before it is put into production.
In the production stage, skilled workers use a variety of tools and equipment to cut, shape, and join the various components of the furniture. The materials used in furniture manufacturing vary depending on the type of furniture being produced.
For example, wooden furniture may use hardwoods, softwoods, or engineered wood products like particleboard or medium-density fiberboard (MDF). Metal furniture may use various metals such as steel, aluminum, or brass.
Quality control is an essential part of furniture manufacturing, as it ensures that each piece of furniture meets the required standards for safety, durability, and functionality. Once the furniture has passed quality control, it is packed and shipped to the retailer or directly to the customer.
Furniture Manufacturing Process: How Furniture is Made?
The furniture manufacturing process involves several stages, including design, engineering, prototyping, production, quality control, and shipping. Here's a brief overview of each stage:
Design
Design is a crucial part of the furniture manufacturing process, as it determines the form, function, and aesthetic appeal of the furniture.
The design process involves several steps, including:
- Research and ideation: The design process begins with research and ideation. Designers research current trends, buyer persona and customer preferences, and the target market to gather insights and inspiration. They may also sketch and brainstorm different concepts and ideas for the furniture.
- Concept development: Once designers have gathered insights and ideas, they begin to develop the furniture's concept. This stage involves creating sketches, 3D models, and technical drawings that outline the furniture's shape, size, materials, and functionality.
- Material selection: After the concept is developed, the designers select the appropriate materials for the furniture. The materials selected depend on the furniture's design and purpose, as well as the available manufacturing methods.
- Design refinement: The furniture's design is then refined based on the feedback received from engineers, manufacturers, and customers. Designers may need to adjust the furniture's shape, size, materials, or functionality to ensure it meets manufacturing and customer requirements.
- Prototyping: Once the design is finalized, a prototype is created to test the furniture's functionality, durability, and safety. The prototype is reviewed, tested, and refined until it meets the required standards.
- Final design: After the prototype is approved, the final design is created, which includes technical drawings, specifications, and instructions for manufacturing the furniture.
In summary, the design process is a critical part of the furniture manufacturing process as it determines the furniture's form, function, and aesthetic appeal.
Designers work closely with engineers, manufacturers, and customers to create furniture that is functional, safe, and visually appealing while meeting customer expectations and manufacturing requirements.
Engineering
Engineering is a crucial part of the furniture manufacturing process, as it ensures that the furniture is functional, safe, and meets the required standards.
The engineering process involves several steps, including:
- Design review: Engineers review the furniture's design to ensure that it meets the required functional, safety, and quality standards. They review the furniture's technical drawings, dimensions, materials, and manufacturing processes to identify any potential issues or areas for improvement.
- Materials selection: Engineers help select appropriate materials for the furniture based on the design requirements, manufacturing processes, and functional needs. They ensure that the materials selected are durable, safe, and meet the required standards.
- Manufacturing process design: Engineers design the manufacturing processes that are required to produce the furniture. They determine the appropriate tools, machines, and processes needed for each stage of the manufacturing process.
- Prototyping and testing: Engineers work with designers to create a prototype of the furniture, which is then tested to ensure that it meets the required functional, safety, and quality standards. They identify any design or manufacturing issues and work to address them to ensure that the final product is safe and functional.
- Quality control: Engineers develop and implement quality control processes that ensure that each piece of furniture meets the required standards for safety, functionality, and durability. They may develop inspection checklists, testing protocols, and certifications to ensure that each piece of furniture is of high quality.
- Continuous improvement: Engineers work with designers and manufacturers to continually improve the furniture's design and manufacturing processes. They seek feedback from customers and other stakeholders to identify areas for improvement and work to incorporate these improvements into future designs.
In summary, engineering is an essential part of the furniture manufacturing process as it ensures that the furniture is safe, functional, and of high quality.
Engineers work closely with designers, manufacturers, and customers to develop and improve furniture designs and manufacturing processes, ensuring that the final product meets the required standards and customer expectations, thereby ensuring customer retention and higher revenues.
Prototyping
Prototyping is a critical part of the furniture manufacturing process as it allows designers and engineers to test the furniture's functionality, durability, and safety before it goes into full production.
The prototyping process involves several steps, including:
- Creating a prototype: The first step in the prototyping process is to create a prototype of the furniture. This may involve creating a scale model, 3D printing a miniature version, or building a full-sized mock-up of the furniture.
- Testing functionality: Once the prototype is created, it is tested to ensure that it functions as intended. This may involve testing the furniture's ergonomics, usability, and overall performance. Designers and engineers may also test the furniture's structural integrity and load-bearing capacity to ensure that it is safe and durable.
- Refining the design: Based on the results of the functional testing, designers and engineers may need to refine the furniture's design. They may need to adjust the furniture's shape, size, materials, or functionality to ensure that it meets customer requirements and manufacturing standards.
- Testing durability and safety: After the design has been refined, the prototype is tested again to ensure that it is safe and durable. This may involve subjecting the furniture to various stress tests, such as impact, vibration, and temperature testing, to ensure that it can withstand real-world conditions.
- Finalizing the design: Once the prototype has been tested and refined, the final design is created, which includes technical drawings, specifications, and instructions for manufacturing the furniture.
In summary, prototyping is an essential part of the furniture manufacturing process as it allows designers and engineers to test the furniture's functionality, durability, and safety before it goes into full production.
The prototyping process ensures that the final product meets customer expectations and manufacturing standards, resulting in a safe, durable, and functional piece of furniture.
Production
Production is a crucial part of the furniture manufacturing process as it involves the actual manufacturing and assembly of the furniture.
The production process involves several steps, including:
- Materials preparation: The first step in the production process is to prepare the materials that will be used to create the furniture. This may involve cutting, shaping, and sanding the raw materials, such as wood, metal, or upholstery fabric.
- Assembly: Once the materials are prepared, the furniture is assembled according to the final design. This may involve using tools, machines, and manual labor to assemble the furniture, including attaching legs, frames, and hardware.
- Finishing: After the furniture is assembled, it undergoes finishing, which involves applying a protective coating, such as paint, varnish, or stain, to enhance its appearance and protect it from wear and tear.
- Quality control: During the production process, the furniture undergoes quality control checks to ensure that it meets the required standards for safety, functionality, and durability. Quality control checks may include visual inspections, functional testing, and load-bearing tests.
- Packaging and shipping: After the furniture has passed quality control checks, it is packaged and shipped to customers. Packaging may involve wrapping the furniture in protective material to prevent damage during shipping.
- After-sales service: After the furniture is delivered, manufacturers may provide after-sales service, such as installation, repair, or replacement of defective parts, to ensure customer satisfaction and maintain their reputation.
In summary, production is a crucial part of the furniture manufacturing process as it involves the actual manufacturing and assembly of the furniture.
The production process ensures that the final product meets the required standards for safety, functionality, and durability, resulting in a high-quality piece of furniture that meets customer expectations, and therefore encourages returning customers as well as higher returns on investment.
Finishing
Finishing is an important part of the furniture manufacturing process as it enhances the appearance of the furniture and protects it from wear and tear.
The finishing process involves several steps, including:
- Sanding: The first step in the finishing process is sanding the furniture. This involves using a sanding machine or sandpaper to smooth out any rough edges or imperfections in the furniture.
- Staining: After the furniture is sanded, it may be stained to enhance its appearance. Staining involves applying a thin layer of color to the furniture's surface, which can give it a natural wood look or a vibrant color.
- Sealing: Once the stain has been applied, the furniture is sealed to protect it from wear and tear. Sealing involves applying a clear coat of protective material, such as varnish or polyurethane, to the furniture's surface.
- Buffing: After the sealant has dried, the furniture is buffed to create a smooth, shiny finish. Buffing involves using a buffing machine or polishing cloth to remove any imperfections or rough spots on the furniture's surface.
- Final inspection: After the finishing process is complete, the furniture undergoes a final inspection to ensure that it meets the required standards for appearance and quality. This may involve visual inspections, functional testing, or load-bearing tests.
In summary, finishing is an important part of the furniture manufacturing process as it enhances the appearance of the furniture and protects it from wear and tear.
The finishing process involves several steps, including sanding, staining, sealing, buffing, and a final inspection to ensure that the finished furniture meets the required standards for appearance and quality.
Quality Control
Quality control is a critical part of the furniture manufacturing process as it ensures that the final product meets the required standards for safety, functionality, and durability.
The quality control process involves several steps, including:
- Incoming materials inspection: The first step in the quality control process is to inspect the raw materials that will be used to create the furniture. This may involve checking the materials for defects, such as warping or cracks, to ensure that they are of high quality and meet the required specifications.
- In-process inspection: During the furniture manufacturing process, the furniture is inspected at various stages to ensure that it meets the required standards. This may involve visual inspections, functional testing, and load-bearing tests to ensure that the furniture is safe and functional.
- Final inspection: After the furniture has been assembled and finished, it undergoes a final inspection to ensure that it meets the required standards for appearance, functionality, and safety. A final inspection may involve visual inspections, functional testing, and load-bearing tests to ensure that the furniture meets customer requirements and manufacturing standards.
- Corrective action: If any defects or issues are found during the quality control process, corrective action is taken to address the issue. This may involve repairing or replacing defective parts, adjusting the manufacturing process, or making design changes to prevent similar issues from occurring in the future.
- Documentation and record-keeping: Throughout the quality control process, documentation and record-keeping are important to ensure that the furniture meets the required standards and that any issues are addressed in a timely manner. Documentation may include inspection reports, corrective action plans, and other quality control records.
In summary, quality control is a critical part of the furniture manufacturing process as it ensures that the final product meets the required standards for safety, functionality, and durability.
The quality control process involves several steps, including incoming materials inspection, in-process inspection, final inspection, corrective action, and documentation and record-keeping.
The goal of the quality control process is to produce high-quality furniture that meets customer expectations and manufacturing standards.
Shipping
Shipping is an important part of the furniture manufacturing process as it involves delivering the finished product to the customer or retailer.
The shipping process involves several steps, including:
- Packaging: The first step in the shipping process is to package the furniture for transportation. This may involve disassembling the furniture, wrapping it in protective materials, and placing it in a sturdy container for transportation.
- Shipping method: Once the furniture is packaged, the next step is to choose a shipping method. This may include ground transportation, air freight, or sea freight, depending on the distance and location of the customer.
- Logistics: Logistics plays an important role in the shipping process, as it involves coordinating the delivery of the furniture from the manufacturing facility to the customer or retailer. This may involve working with third-party logistics providers or shipping companies to ensure that the furniture is delivered on time and in good condition.
- Delivery and assembly: Once the furniture has been delivered, it may need to be assembled at the customer's location. This may involve providing detailed assembly instructions or sending a technician to assemble the furniture on-site.
- Customer service: Finally, customer service is an important part of the shipping process. This may involve answering customer questions or concerns about the shipping process, providing tracking information, or addressing any issues that arise during delivery or assembly.
In summary, shipping is an important part of the furniture manufacturing process as it involves delivering the finished product to the customer or retailer. The shipping process involves several steps, including packaging, choosing a shipping method, logistics, delivery and assembly, and customer service.
The goal of the shipping process is to ensure that the furniture is delivered to the customer on time and in good condition and that any issues or concerns are addressed in a timely and professional manner.
How to Ensure Quality Control in the Furniture Manufacturing Process?
Ensuring quality control in the furniture manufacturing process involves implementing a comprehensive quality control system that covers all aspects of the manufacturing process.
Here are some steps that can be taken to ensure quality control in the furniture manufacturing process:
- Develop quality control standards: The first step in ensuring quality control is to develop clear and comprehensive quality control standards that define the required specifications for the furniture. This may involve specifying materials, dimensions, finishes, and other requirements.
- Train employees: All employees involved in the furniture manufacturing process should be trained on the quality control standards and the procedures for inspecting and testing furniture during the manufacturing process.
- Inspect incoming materials: Raw materials should be inspected upon receipt to ensure that they meet quality control standards. Any defective or substandard materials should be rejected or returned to the supplier.
- Conduct in-process inspections: Throughout the manufacturing process, the furniture should be inspected and tested at various stages to ensure that it meets the quality control standards. This may involve visual inspections, functional testing, and load-bearing tests.
- Conduct final inspection: Once the furniture has been assembled and finished, it should undergo a final inspection to ensure that it meets the quality control standards. This may involve visual inspections, functional testing, and load-bearing tests.
- Document quality control activities: All quality control activities should be documented, including inspection reports, corrective action plans, and other quality control records.
- Continuously improve the quality control system: The quality control system should be reviewed periodically to identify areas for improvement and to ensure that it continues to meet the needs of the business and the customer.
In summary, ensuring quality control in the furniture manufacturing process involves developing clear quality control standards, training employees, inspecting incoming materials, conducting in-process and final inspections, documenting quality control activities, and continuously improving the quality control system.
By implementing these steps, furniture manufacturers can produce high-quality furniture that meets customer expectations and manufacturing standards.
Challenges Associated with the Furniture Manufacturing Process
The furniture manufacturing process can be challenging and complex, and there are several key challenges that manufacturers may face. Some of these challenges include:
- Raw material availability: One of the biggest challenges in the furniture manufacturing process is sourcing high-quality raw materials at an affordable price. Fluctuations in raw material prices and availability can impact the cost and quality of the final product.
- Design and engineering: The design and engineering process can be complex and time-consuming, and ensuring that the final product meets customer expectations and regulatory requirements can be a challenge.
- Production efficiency: The furniture manufacturing process requires a high degree of precision and attention to detail, and ensuring that the production process is efficient and streamlined can be a challenge. Factors such as equipment breakdowns, labor shortages, and production delays can impact production efficiency.
- Quality control: Ensuring that the final product meets quality control standards can be challenging and requires a comprehensive quality control system that covers all aspects of the manufacturing process.
- Environmental concerns: Furniture manufacturing can have a significant impact on the environment, and manufacturers must ensure that their operations are sustainable and environmentally responsible.
- Shipping and logistics: Shipping furniture can be challenging and requires careful coordination and planning to ensure that the product is delivered on time and in good condition.
- Competitive market: The furniture market is highly competitive, and manufacturers must continually innovate and adapt to changing customer preferences and market trends to remain competitive.
In summary, the furniture manufacturing process can be challenging and complex, and manufacturers must navigate a range of issues related to raw material availability, design and engineering, production efficiency, quality control, environmental concerns, shipping and logistics, and a highly competitive market.
By addressing these challenges and implementing best practices, furniture manufacturers can produce high-quality products that meet customer expectations and regulatory requirements.
Opportunities Associated with the Furniture Manufacturing Process
The furniture manufacturing process presents several opportunities for manufacturers to innovate, grow their businesses, and create value for customers. Some of the opportunities associated with the furniture manufacturing process include:
- Customization: The ability to offer customized furniture can be a significant opportunity for furniture manufacturers. By leveraging the digital design and manufacturing technologies, manufacturers can offer a wide range of customization options to meet the specific needs and preferences of individual customers.
- Sustainability: Sustainable manufacturing practices and the use of eco-friendly materials can be significant opportunities for furniture manufacturers. By adopting environmentally responsible practices and promoting sustainable products, manufacturers can differentiate themselves from competitors and appeal to environmentally conscious customers.
- Digital technologies: The adoption of digital technologies, such as 3D printing, robotics, and augmented reality, can enable furniture manufacturers to streamline their operations, reduce manufacturing costs, and improve quality control. Digital technologies can also enhance the customer experience by allowing customers to visualize and customize furniture before purchasing.
- Global market: The global furniture market presents significant opportunities for manufacturers to expand their customer base and increase sales. By leveraging e-commerce platforms and online marketing strategies, manufacturers can reach customers in new markets and grow their businesses.
- Collaborative partnerships: Collaborating with other manufacturers, designers, and suppliers can be an opportunity for furniture manufacturers to share expertise, reduce costs, and create value for customers. By working together, manufacturers can develop innovative products and processes that differentiate them from competitors and meet customer needs more effectively.
In summary, the furniture manufacturing process presents several opportunities for manufacturers to innovate, differentiate themselves from competitors, and create value for customers.
By adopting sustainable manufacturing practices, leveraging digital technologies, expanding into global markets, and collaborating with other stakeholders, furniture manufacturers can position themselves for long-term success in the industry.
Areas of Improvement in the Furniture Manufacturing Process
There are several areas where furniture manufacturers can focus on improving their manufacturing processes to increase efficiency, reduce costs, and improve product quality. Some areas of improvement in the furniture manufacturing process include:
- Supply chain management: Improving supply chain management can help furniture manufacturers to optimize their procurement processes, reduce material waste, and lower costs. By working closely with suppliers and adopting lean manufacturing principles, manufacturers can streamline their supply chain and improve production efficiency.
- Automation and technology: Implementing automation and technology solutions can help furniture manufacturers to improve production efficiency, reduce labor costs, and improve product quality. By adopting digital technologies such as 3D printing, robotics, and machine learning, manufacturers can streamline their manufacturing processes and improve their competitive position in the market.
- Process optimization: Continuously optimizing the manufacturing process can help furniture manufacturers to reduce production cycle times, eliminate waste, and improve product quality. By analyzing data and using process improvement methodologies such as Six Sigma or Lean Manufacturing, manufacturers can identify areas for improvement and implement changes to optimize the manufacturing process.
- Quality control: Improving quality control processes can help furniture manufacturers to reduce the number of defects in their products, improve customer satisfaction, and reduce costs associated with returns and repairs. By implementing a comprehensive quality control system that covers all aspects of the manufacturing process, manufacturers can ensure that their products meet customer expectations and comply with regulatory requirements.
- Employee training and development: Providing ongoing training and development opportunities to employees can help furniture manufacturers to improve production efficiency, reduce errors, and improve product quality. By investing in employee training and development, manufacturers can create a culture of continuous improvement and continuous innovation that drives the success of their businesses.
In summary, furniture manufacturers can improve their manufacturing processes by focusing on areas such as supply chain management, automation and technology, process optimization, quality control, and employee training and development.
By making these improvements, manufacturers can increase efficiency, reduce costs, improve product quality, and position themselves for long-term success in the industry.
How have Technological Advancements Affected the Furniture Manufacturing Process?
Technological advancements have had a significant impact on the furniture manufacturing process, improving efficiency, product quality, and customization options. Some of the ways in which technological advancements have affected the furniture manufacturing process include:
- Digital design: The use of computer-aided design (CAD) software allows furniture manufacturers to create detailed, precise designs quickly and accurately. This technology enables manufacturers to visualize and test designs before production, reducing the risk of errors and reducing production costs.
- Automation: Automation technologies such as robotics and machine learning have enabled furniture manufacturers to automate many of the tasks traditionally performed by human workers, reducing labor costs and improving production efficiency.
- Additive manufacturing: Additive manufacturing technologies, such as 3D printing, have enabled furniture manufacturers to produce highly customized, intricate designs that were previously impossible to create. This technology also allows manufacturers to produce small batches of products quickly and cost-effectively, reducing production lead times and inventory costs.
- Sustainable materials: Technological advancements have enabled furniture manufacturers to use sustainable, eco-friendly materials in their products, reducing their environmental impact and appealing to environmentally conscious consumers.
- Augmented reality: Augmented reality technology allows customers to visualize furniture in their homes before purchasing, improving the customer experience and reducing the likelihood of returns. This technology also allows manufacturers to offer highly customized products, enabling customers to personalize their furniture to their specific needs and preferences.
In summary, technological advancements have revolutionized the furniture manufacturing process, improving efficiency, product quality, and customization options. By adopting these technologies, furniture manufacturers can reduce costs, improve product quality, and position themselves for long-term success in the industry.
Role of Automation in the Furniture Manufacturing Process
Automation plays a significant role in the furniture manufacturing process, improving efficiency, reducing labor costs, and improving product quality. Some of the ways in which automation is used in the furniture manufacturing process include:
- Cutting and shaping: Automated cutting and shaping machines can cut and shape wood, metal, and other materials with precision and speed, reducing production time and improving product quality.
- Assembly: Automated assembly lines can assemble furniture components quickly and accurately, reducing labor costs and improving efficiency.
- Finishing: Automated finishing machines can sand, stain, and coat furniture components with precision and consistency, improving product quality and reducing the risk of errors.
- Quality control: Automated quality control systems can detect defects in furniture components quickly and accurately, reducing the number of defective products that reach customers and improving customer satisfaction.
- Inventory management: Automated inventory management systems can track raw materials and finished products, reducing the risk of stockouts and overstocking and improving supply chain efficiency.
By adopting automation technologies, furniture manufacturers can improve efficiency, reduce labor costs, and improve product quality. However, it is important to note that automation should be used strategically, with a focus on optimizing the manufacturing process and improving the customer experience.
Additionally, it is important to ensure that automation technologies are integrated with human workers, enabling workers to focus on tasks that require creativity and critical thinking while allowing machines to handle repetitive or dangerous tasks.
Ensuring Sustainability in the Furniture Manufacturing Process
Ensuring sustainability in the furniture manufacturing process is becoming increasingly important as consumers become more environmentally conscious and demand products that are made with sustainable materials and methods.
Here are some ways that furniture manufacturers can ensure sustainability in their manufacturing process:
- Sustainable materials: Furniture manufacturers can use sustainable materials such as reclaimed wood, bamboo, recycled plastic, and non-toxic finishes, reducing their environmental impact.
- Efficient use of resources: Manufacturers can optimize their use of resources such as water, energy, and raw materials, reducing waste and reducing their environmental impact.
- Waste reduction and recycling: Manufacturers can implement waste reduction and recycling programs, ensuring that waste materials are recycled or reused rather than being sent to landfills.
- Eco-friendly manufacturing processes: Furniture manufacturers can adopt eco-friendly manufacturing processes, such as using low-emission adhesives, reducing packaging waste, and minimizing transportation emissions.
- Sustainable sourcing: Manufacturers can ensure that they source materials from suppliers who use sustainable practices, reducing the environmental impact of their supply chain.
- Product design: Manufacturers can design furniture products with sustainability in mind, such as using modular designs that allow for easy disassembly and recycling at the end of the product's life.
By adopting sustainable practices in the furniture manufacturing process, manufacturers can appeal to environmentally conscious consumers and improve their brand image.
Additionally, sustainable practices can help manufacturers reduce costs, improve supply chain efficiency, and ensure long-term success in the industry.
New Trends in the Furniture Manufacturing Process
There are several new trends emerging in the furniture manufacturing process, driven by changing consumer preferences and technological advancements. Here are some of the notable trends:
- Sustainable materials: As mentioned earlier, there is a growing trend toward using sustainable materials such as reclaimed wood, bamboo, and recycled plastics.
- Customization: Consumers are increasingly looking for customized furniture that meets their specific needs and preferences. Furniture manufacturers are responding by offering customizable options, such as selecting the color, fabric, and finishes.
- 3D printing: 3D printing is becoming more common in furniture manufacturing, allowing for the creation of complex and unique designs that were previously difficult to produce using traditional methods.
- Smart furniture: With the rise of the Internet of Things (IoT), furniture manufacturers are incorporating smart features into their products, such as built-in charging ports, sensors, and other tech-enabled features.
- Lightweight and modular furniture: With an increasing emphasis on flexibility and mobility, furniture manufacturers are creating lightweight and modular furniture that can be easily assembled and disassembled, making it easier to move and store.
- Multifunctional furniture: With the trend towards smaller living spaces, furniture manufacturers are creating multifunctional furniture that serves multiple purposes, such as a sofa bed or a coffee table that doubles as a storage unit.
By embracing these new trends, furniture manufacturers can meet the changing needs and preferences of consumers and stay competitive in the market.
How AI Improves Manufacturing Systems
From automating routine tasks to enabling predictive analytics, AI enhances every stage of the production cycle. It analyzes real-time data to forecast demand, optimize inventory levels, and reduce machine downtime through predictive maintenance. This leads to smoother operations and fewer disruptions.
AI plays a key role in this transformation by integrating AI with manufacturing workflows—allowing businesses to gain deep insights into their supply chain, automate production planning, and fine-tune resource allocation.
FAQs related to the Furniture Manufacturing Process
- What materials are commonly used in furniture manufacturing?
Common materials used in furniture manufacturing include wood, metal, plastic, leather, and fabric.
- How is furniture designed and prototyped?
Furniture designers typically use computer-aided design (CAD) software to create 3D models of their designs. These designs can then be prototyped using a variety of methods, such as 3D printing, CNC machining, or traditional woodworking.
- What factors affect the cost of furniture manufacturing?
Factors that can affect the cost of furniture manufacturing include the materials used, the complexity of the design, the production volume, and the manufacturing location.
- What is the lead time for furniture manufacturing?
The lead time for furniture manufacturing can vary depending on the complexity of the design, the production volume, and the availability of materials. Typically, it can take anywhere from a few weeks to several months.
- How can furniture manufacturers ensure quality control?
Furniture manufacturers can ensure quality control by implementing a comprehensive quality control program that includes inspections at every stage of the manufacturing process, from design to finishing.
- What are some eco-friendly manufacturing practices in furniture manufacturing?
Eco-friendly manufacturing practices in furniture manufacturing include using sustainable materials, optimizing resource use, implementing waste reduction and recycling programs, using eco-friendly manufacturing processes, and sourcing materials from sustainable suppliers.
- What are some common challenges in furniture manufacturing?
Common challenges in furniture manufacturing include managing production costs, meeting quality standards, managing supply chain complexity, and meeting changing consumer demands.
- What are some new trends in furniture manufacturing?
New trends in furniture manufacturing include the use of sustainable materials, customization, 3D printing, smart furniture, lightweight and modular furniture, and multifunctional furniture.
- How does automation impact furniture manufacturing?
Automation can help furniture manufacturers increase production efficiency, reduce labor costs, improve quality control, and shorten lead times.
- How do furniture manufacturers ensure safe and ethical working conditions for their employees?
Furniture manufacturers can ensure safe and ethical working conditions for their employees by implementing workplace safety programs, providing adequate training and protective equipment, paying fair wages, and complying with labor laws and regulations.
How can Deskera Help You with Furniture Manufacturing?
Deskera is a cloud-based software solution that offers a range of features to help streamline and optimize the furniture manufacturing process. Here are some ways Deskera can help you with furniture manufacturing:
- Inventory management: Deskera can help you manage your inventory levels and track the movement of raw materials and finished goods in real time.
- Production planning: With Deskera, you can plan and schedule your production process, track progress, and monitor resource utilization to ensure efficient production.
- Quality control: Deskera offers tools to help you manage quality control throughout the manufacturing process, from design to finishing, to ensure that your products meet the required standards.
- Sales and distribution: Deskera can help you manage your sales orders, track customer orders, and manage your distribution channels, allowing you to manage your sales process more efficiently.
- Financial management: With Deskera, you can manage your financial transactions, track expenses, and generate financial reports, giving you greater visibility into your financial performance.
- Business intelligence: Deskera provides advanced analytics and reporting capabilities, allowing you to gain insights into your business performance and make data-driven decisions.
Key Takeaways
The furniture manufacturing process is a multi-step, complex process that requires a combination of skills, technology, and resources to produce high-quality furniture products. The steps involved in the furniture manufacturing process are:
- Design: The furniture design process begins with a designer creating a blueprint or a 3D model of the furniture. This stage involves choosing materials, dimensions and finishes for the furniture.
- Engineering: Once the design is completed, engineers will review and refine the design for functionality and safety, ensuring that the furniture can support the intended load and use.
- Prototyping: A prototype is created to test the functionality, durability, and safety of the design. The prototype is adjusted and improved as needed before being approved for production.
- Production: In the production stage, skilled workers use a variety of tools and equipment to cut, shape, and join the various components of the furniture. The materials used in furniture manufacturing vary depending on the type of furniture being produced. For example, wooden furniture may use hardwoods, softwoods, or engineered wood products like particleboard or medium-density fiberboard (MDF). Metal furniture may use various metals such as steel, aluminum, or brass.
- Finishing: The finishing stage involves applying any final coatings, stains, or paint to the furniture. This stage is essential for enhancing the furniture's appearance, protection, and longevity.
- Quality control: Quality control is an essential part of furniture manufacturing, as it ensures that each piece of furniture meets the required standards for safety, durability, and functionality. During this stage, each piece of furniture undergoes inspection, testing, and certification before being approved for shipment.
- Shipping: Once the furniture has passed quality control, it is packed and shipped to the retailer or directly to the customer. The packaging and shipping process may vary depending on the type of furniture and the destination.
With careful planning and attention to detail, furniture manufacturers can produce high-quality, durable, and beautiful furniture that meets the needs and preferences of their customers.
By using Deskera's comprehensive suite of software tools, furniture manufacturers can streamline their operations, improve efficiency, and reduce costs, resulting in better business performance and increased customer satisfaction.
Related Articles
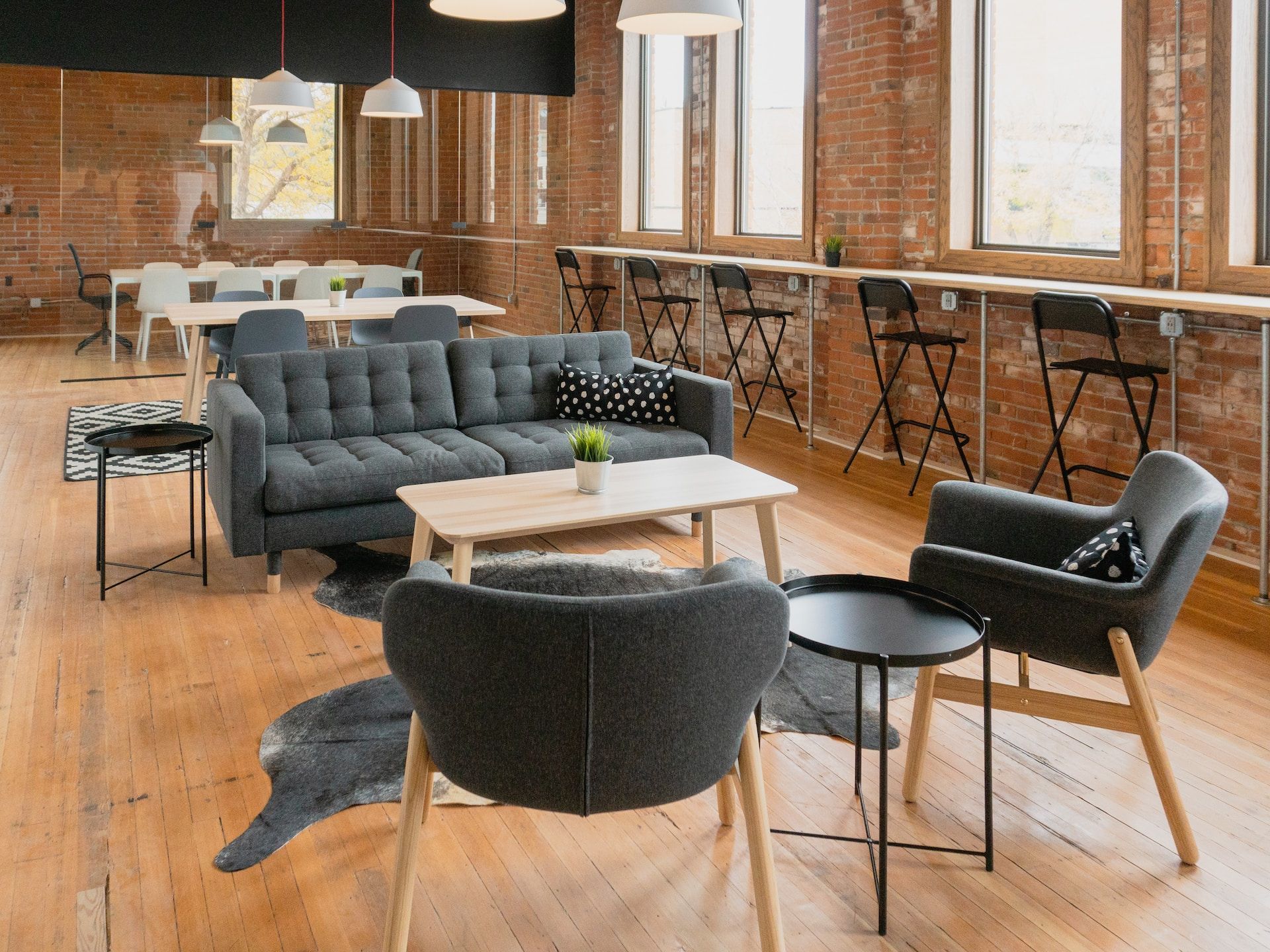

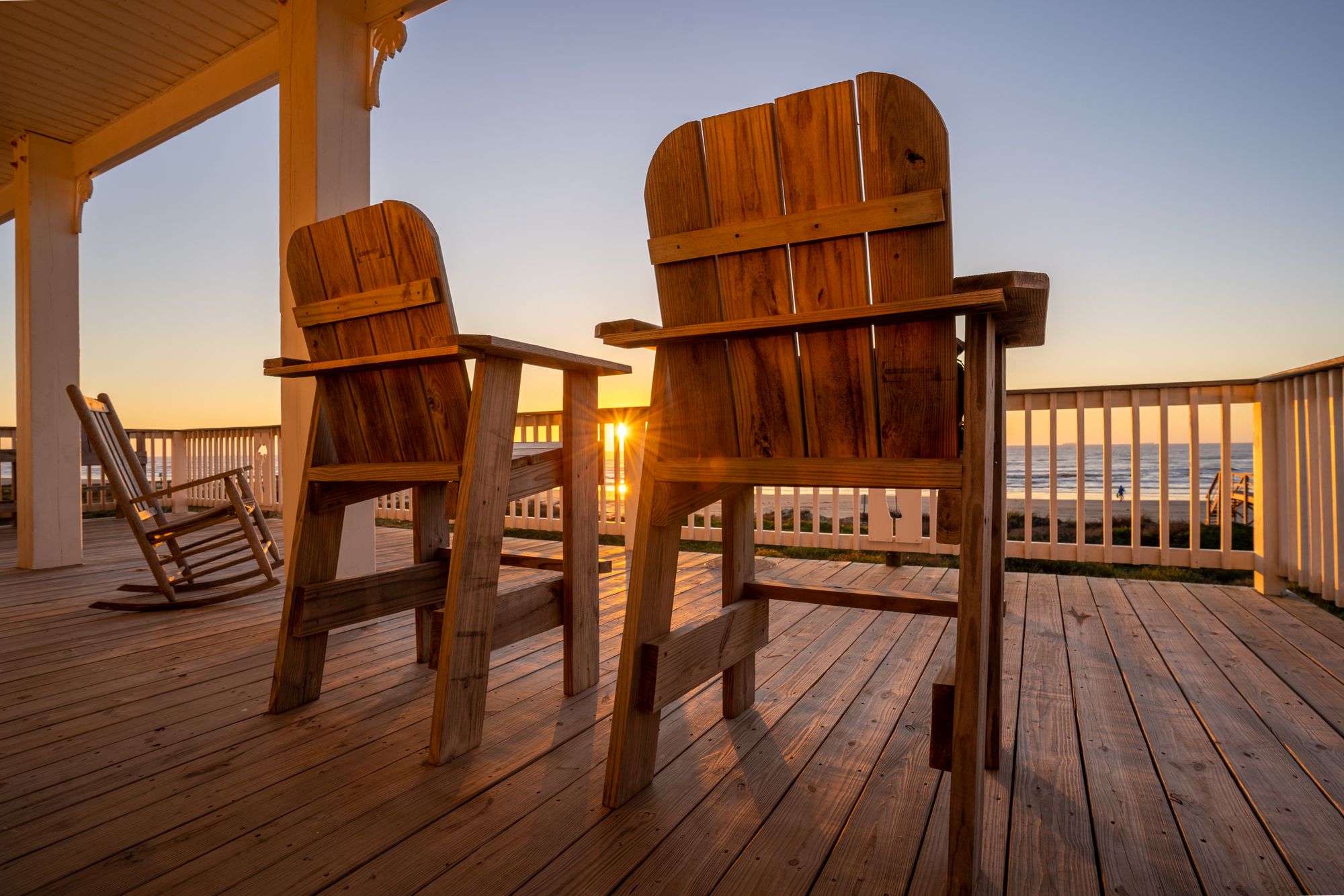
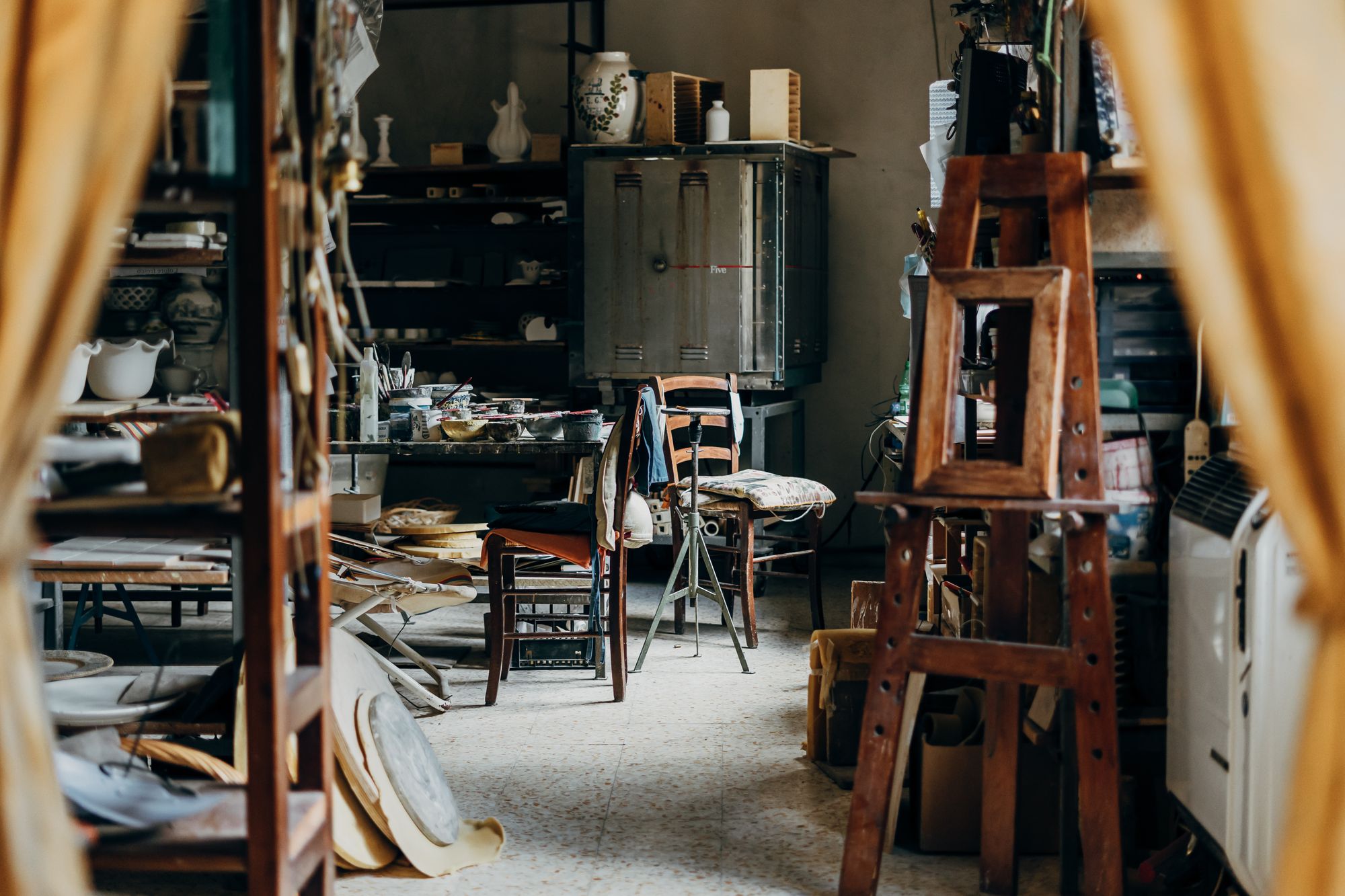
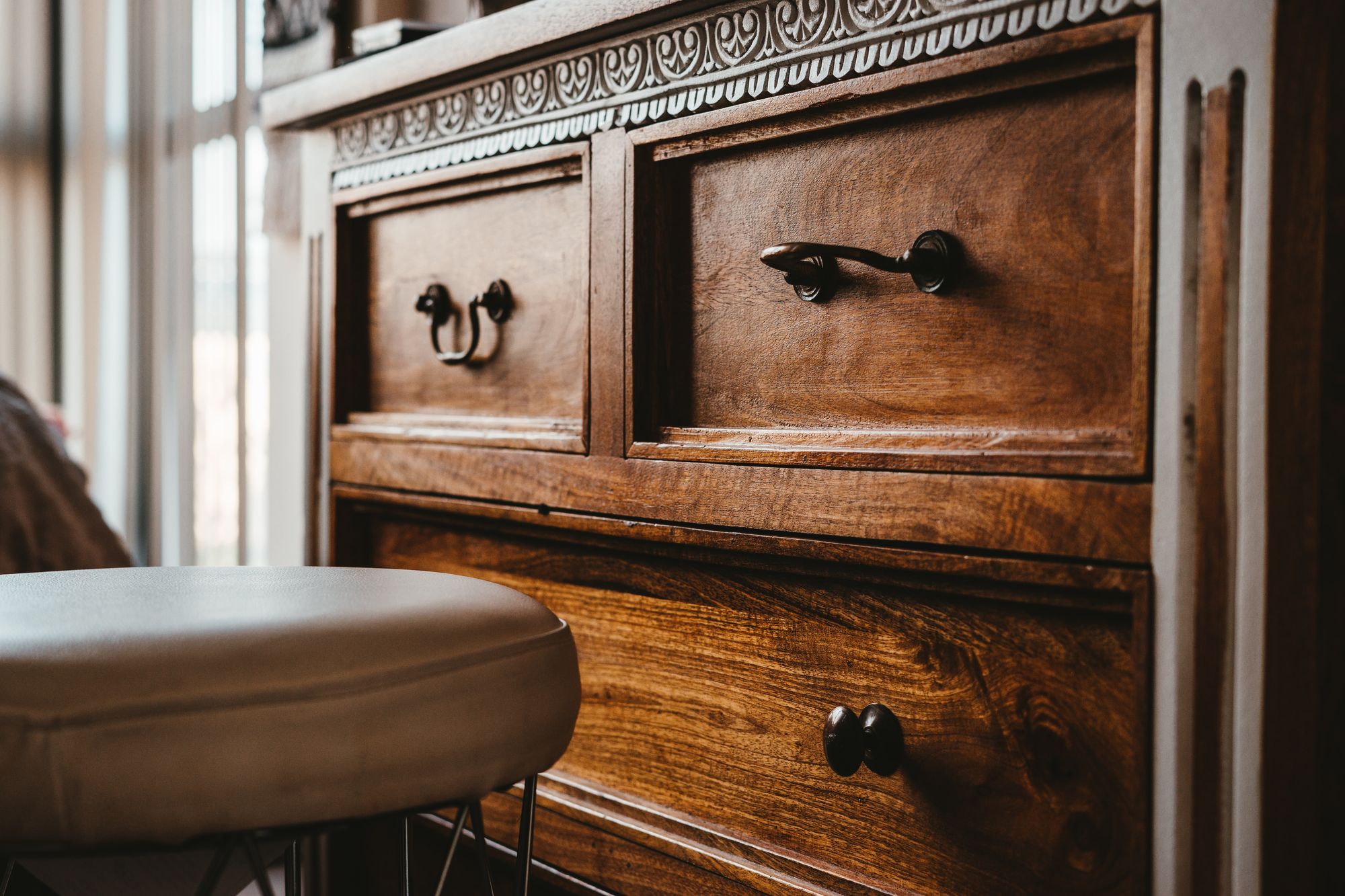
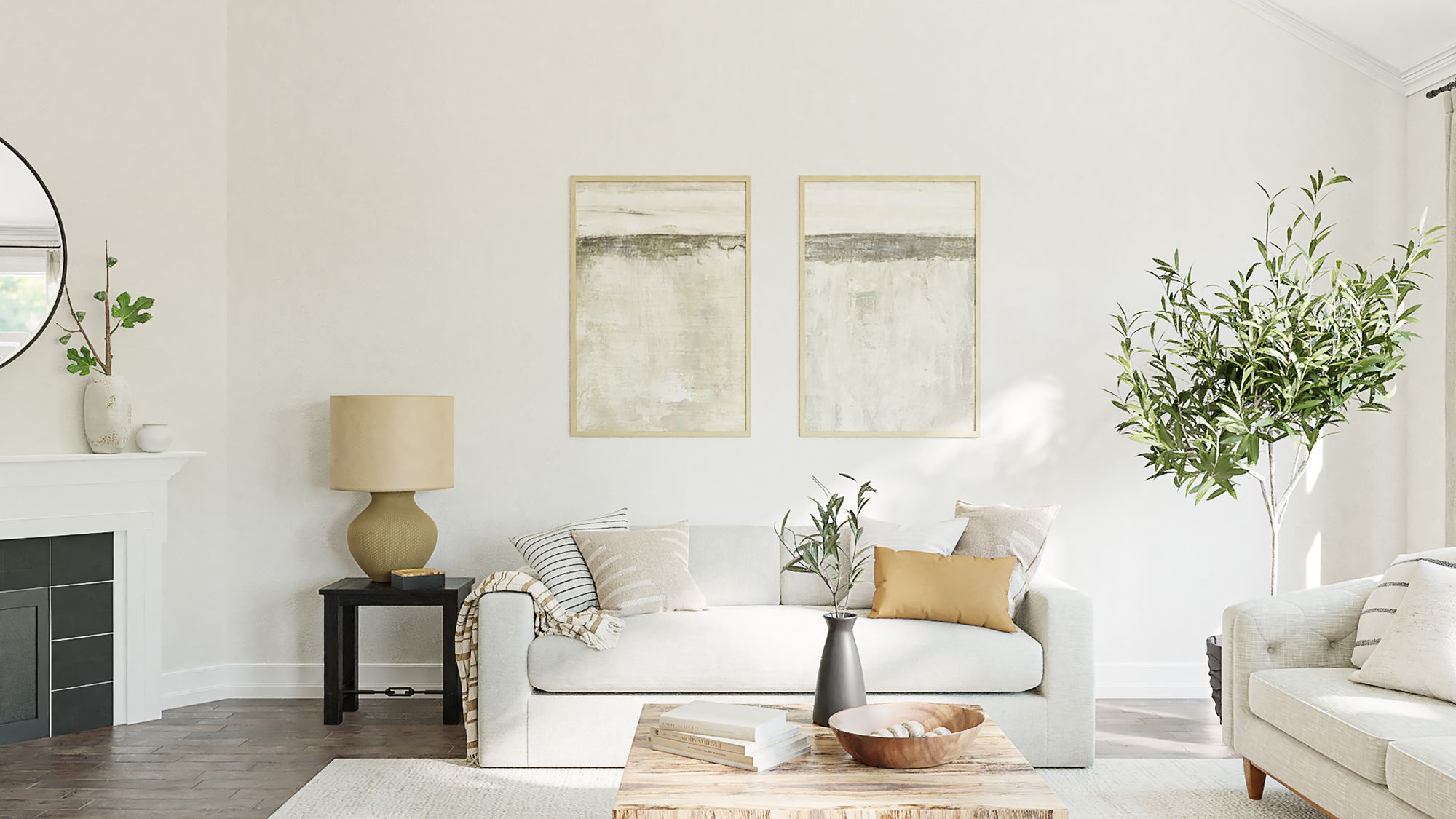