Efficient inventory management is a critical aspect of business operations, enabling organizations to optimize their supply chain, reduce costs, and enhance customer satisfaction. For executives, understanding and implementing effective inventory management strategies can directly impact the bottom line and overall business success.
According to a survey conducted by Deloitte, 79% of companies with high-performing supply chains achieve above-average revenue growth within their industries. However, the same study found that only 8% of executives believe their organizations have effective inventory management practices in place.
These statistics highlight the urgent need for executives to gain a comprehensive understanding of inventory management and adopt efficient strategies. This executive guide aims to provide valuable insights into the world of inventory management, offering practical advice, best practices, and key performance indicators to monitor.
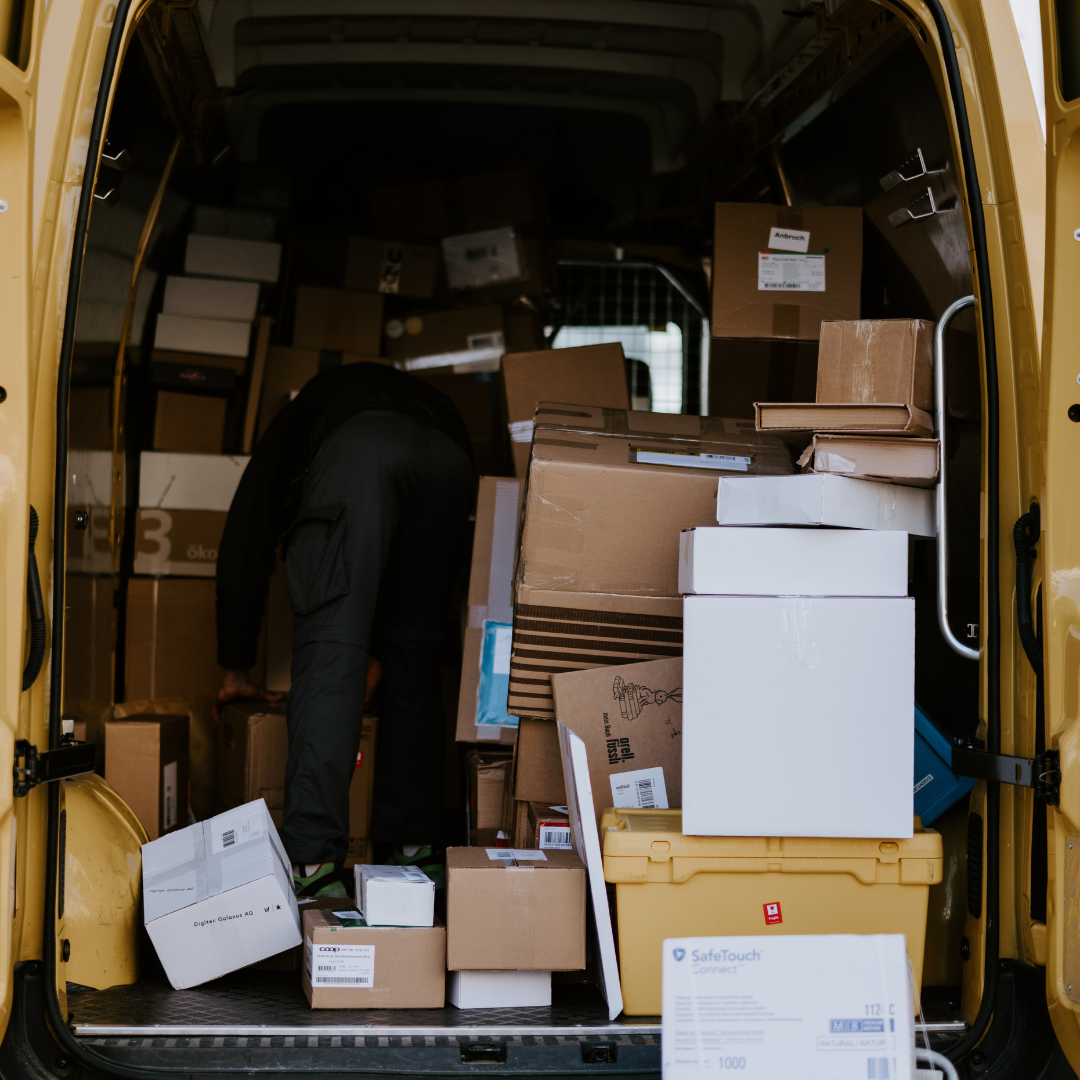
By implementing the principles outlined in this guide, executives can streamline their operations, reduce costs, and gain a competitive edge in today's dynamic business environment.
- Importance of Efficient Inventory Management for Executives
- Understanding Inventory Management
- Benefits of Efficient Inventory Management
- Strategies for Efficient Inventory Management
- Key Performance Indicators (KPIs) for Inventory Management
- Challenges and Solutions in Inventory Management
- Case Studies and Best Practices
- Future Trends and Advancements in Inventory Management
- Conclusion
- How can Deskera Help You?
- Key Takeaways
- Related Articles
Importance of Efficient Inventory Management for Executives
Efficient inventory management is of paramount importance for executives due to its direct impact on the overall financial health and success of the organization. Here are some key reasons why executives should prioritize and invest in efficient inventory management:
- Cost Savings: Effective inventory management helps minimize costs associated with excessive stock levels, storage, and obsolescence. By optimizing inventory levels and implementing lean practices, executives can reduce holding costs and improve overall profitability.
- Improved Customer Service: Maintaining optimal inventory levels ensures timely order fulfillment, reducing the risk of stockouts and backorders. This leads to enhanced customer satisfaction, loyalty, and ultimately, repeat business.
- Increased Productivity and Efficiency: Efficient inventory management streamlines workflows, enabling employees to spend less time on inventory-related tasks such as counting, tracking, and reconciling. This allows them to focus on more value-added activities, leading to increased productivity and operational efficiency.
- Better Cash Flow Management: By closely managing inventory levels and turnover, executives can free up working capital tied up in excess inventory. This enables better cash flow management, allowing organizations to allocate resources to other critical areas such as research and development or expansion.
- Competitive Advantage: Organizations with efficient inventory management gain a competitive edge by responding quickly to changing market demands. They can adapt to market trends, introduce new products faster, and minimize the risk of carrying outdated or obsolete inventory.
In summary, efficient inventory management empowers executives to make informed decisions, optimize resources, and drive overall business performance. By implementing effective inventory management strategies, executives can achieve cost savings, improve customer service, increase productivity, manage cash flow effectively, and gain a competitive advantage in the marketplace.
Understanding Inventory Management
Understanding inventory management is crucial for executives to effectively control and optimize the flow of goods within their organization. By grasping the key objectives, types of inventory, and associated costs, executives can make informed decisions to balance supply and demand, minimize stockouts, and maximize profitability.
A. Definition of inventory management
Inventory management refers to the systematic and strategic process of overseeing and controlling the procurement, storage, tracking, and utilization of goods within an organization. It involves managing the entire lifecycle of inventory, from the moment it enters the organization through its storage, distribution, and eventual consumption or sale.
The primary objective of inventory management is to ensure that the right quantity of goods is available at the right time, in the right place, and at the right cost. It encompasses activities such as demand forecasting, inventory classification, order placement, inventory tracking, and optimization of stock levels.
Effective inventory management enables organizations to meet customer demand, minimize holding costs, reduce stockouts, and maximize operational efficiency.
B. Key objectives of inventory management
The key objectives of inventory management can be summarized as follows:
- Meeting Customer Demand: One of the primary goals of inventory management is to ensure that the organization can meet customer demand effectively. By maintaining optimal inventory levels, organizations can fulfill orders promptly and prevent stockouts or backorders, leading to improved customer satisfaction.
- Minimizing Holding Costs: Inventory incurs costs such as storage, insurance, obsolescence, and depreciation. Efficient inventory management aims to minimize these holding costs by optimizing stock levels, implementing lean practices, and reducing excess or slow-moving inventory.
- Maximizing Operational Efficiency: Inventory management plays a crucial role in streamlining operations and maximizing efficiency. By having the right amount of inventory at the right time, organizations can minimize lead times, reduce production bottlenecks, and enhance overall operational productivity.
- Optimizing Working Capital: Inventory ties up a significant portion of a company's working capital. Effective inventory management seeks to strike a balance between maintaining adequate inventory levels and freeing up working capital for other essential business activities, such as investment, growth, or debt repayment.
- Managing Supply Chain Risks: Inventory management helps mitigate supply chain risks, such as disruptions in the availability of raw materials or components. By implementing effective inventory management strategies, organizations can ensure continuity of operations, minimize the impact of unforeseen events, and enhance supply chain resilience.
- Maximizing Profitability: Ultimately, the overarching objective of inventory management is to maximize profitability. By aligning inventory levels with demand, minimizing costs, and optimizing operational efficiency, organizations can achieve higher margins, reduce waste, and improve their bottom line.
These objectives collectively contribute to improving customer satisfaction, reducing costs, enhancing operational efficiency, and driving overall business success.
C. Types of inventory (raw materials, work-in-progress, finished goods)
Inventory can be categorized into three main types based on its stage in the production process:
- Raw Materials: Raw materials are the basic components or inputs used in the production process. These can include materials such as metals, fabrics, chemicals, or components that are directly used to create the final product. Raw material inventory ensures a smooth production flow and is typically held in anticipation of future production needs.
- Work-in-Progress (WIP): Work-in-progress inventory consists of partially completed goods that are in the process of being transformed into finished products. This inventory represents the value of materials, labor, and overhead costs that have been incurred in the production process but are not yet completed. WIP inventory is a crucial measure of production efficiency and is typically found in manufacturing or assembly operations.
- Finished Goods: Finished goods inventory includes the final, completed products that are ready for sale and delivery to customers. These are the end products of the manufacturing or production process. Finished goods inventory is held to meet customer demand and ensure timely order fulfillment. It represents the value of goods that are awaiting shipment or distribution to customers.
Each type of inventory serves a specific purpose in the production and supply chain. Effective management of raw materials, work-in-progress, and finished goods is essential to maintain a smooth production flow, meet customer demand, and optimize inventory levels throughout the organization.
D. Inventory costs and their impact on the business
Inventory costs can significantly impact a business's financial performance. Here are some key inventory costs and their impact on the organization:
- Holding (Carrying) Costs: Holding costs include expenses associated with storing and maintaining inventory, such as warehousing, insurance, security, obsolescence, and inventory management systems. Higher holding costs can erode profitability and tie up valuable working capital, limiting the organization's ability to invest in other areas of the business.
- Stockout Costs: Stockouts occur when inventory levels are insufficient to meet customer demand. Stockout costs can include lost sales, dissatisfied customers, damaged reputation, and potential long-term customer loss. These costs can significantly impact revenue and customer relationships.
- Ordering (Setup) Costs: Ordering costs encompass expenses associated with placing and processing orders, such as order processing, paperwork, communication, and supplier management. Higher ordering costs can reduce efficiency and profitability if not properly managed.
- Obsolescence Costs: Obsolescence costs arise from holding excess or outdated inventory that becomes obsolete or unusable. These costs can include markdowns, write-offs, and disposal expenses. In industries with rapidly changing technology or fashion trends, the risk of obsolescence is higher, and inefficient inventory management can lead to substantial losses.
- Transportation Costs: Transportation costs are incurred when moving inventory from suppliers to the organization and from the organization to customers. These costs can include freight charges, customs duties, fuel costs, and transportation logistics expenses. Inefficient transportation management can lead to higher costs and delays in delivering goods.
- Opportunity Costs: Opportunity costs represent the potential revenue or profit that could have been generated if the resources tied up in inventory were allocated elsewhere, such as investing in research and development or expanding the business. Inefficient inventory management may limit the organization's ability to seize new opportunities and maximize profitability.
It is crucial for businesses to carefully analyze and optimize these inventory costs to strike a balance between inventory levels, customer service, and overall financial performance. By implementing efficient inventory management practices, organizations can reduce costs, improve profitability, and enhance their competitive position in the market.
Benefits of Efficient Inventory Management
Efficient inventory management brings a multitude of benefits to organizations, empowering them to optimize their supply chain, reduce costs, enhance customer satisfaction, and gain a competitive advantage.
By adopting effective inventory management practices, businesses can achieve cost savings, improve operational efficiency, streamline workflows, and ensure the right products are available at the right time.
Furthermore, efficient inventory management enables organizations to better manage cash flow, mitigate supply chain risks, and stay ahead of market fluctuations.
In this section, we will explore the various benefits that executives can harness through efficient inventory management, demonstrating how it directly impacts the bottom line and contributes to overall business success.
A. Cost savings
Efficient inventory management directly translates into significant cost savings for organizations. Here are some key ways in which efficient inventory management leads to cost reductions:
- Holding Cost Reduction: By optimizing inventory levels, organizations can minimize holding costs associated with storage, insurance, obsolescence, and depreciation. Holding excessive inventory ties up working capital and incurs additional expenses, while maintaining insufficient inventory leads to stockouts and lost sales. Efficient inventory management ensures that inventory levels are balanced, reducing holding costs and improving overall profitability.
- Order and Transportation Cost Optimization: Efficient inventory management allows organizations to streamline their ordering processes. By consolidating orders, negotiating favorable terms with suppliers, and implementing efficient transportation logistics, businesses can reduce ordering and transportation costs. This optimization helps minimize administrative expenses, freight charges, and other costs associated with procurement and distribution.
- Obsolescence and Write-off Prevention: Inefficient inventory management increases the risk of holding obsolete or slow-moving inventory, resulting in write-offs and markdowns. By accurately forecasting demand, monitoring inventory levels, and implementing effective inventory control measures, organizations can minimize the likelihood of obsolescence and write-offs. This helps preserve revenue and reduces losses associated with disposing of or discounting obsolete inventory.
- Improved Production Efficiency: Effective inventory management ensures that the right materials and components are available when needed, reducing production delays and bottlenecks. By preventing shortages and ensuring a smooth production flow, organizations can enhance operational efficiency, minimize downtime, and reduce costs associated with idle labor and equipment.
- Better Cash Flow Management: Inefficient inventory management can tie up significant amounts of working capital in excess or slow-moving inventory. By adopting efficient inventory practices such as just-in-time (JIT) inventory management or lean principles, organizations can reduce their inventory carrying costs and improve cash flow. This enables better allocation of resources for growth, investment, or debt repayment.
By optimizing inventory levels, reducing holding costs, streamlining procurement and distribution processes, and preventing obsolescence, businesses can achieve substantial cost reductions and strengthen their competitive position in the market.
B. Improved customer service
Here are the key ways in which efficient inventory management directly contributes to improved customer service:
Timely Order Fulfillment: Efficient inventory management ensures that the right products are available when customers place orders. By accurately forecasting demand and maintaining optimal inventory levels, organizations can fulfill customer orders promptly, reducing lead times and improving order turnaround time.
This leads to enhanced customer satisfaction and builds a reputation for reliable and timely service.
Minimized Stockouts and Backorders: Inadequate inventory management often leads to stockouts, where products are unavailable when customers demand them. This can result in lost sales, dissatisfied customers, and damage to the organization's reputation.
Efficient inventory management helps minimize stockouts by ensuring sufficient inventory levels to meet customer demand. By having the right products in stock, organizations can avoid backorders and maintain a high level of customer satisfaction.
Accurate and Reliable Product Availability: Efficient inventory management enables organizations to have accurate visibility into their inventory levels. This visibility allows businesses to provide accurate information to customers regarding product availability, lead times, and delivery dates. Customers appreciate transparency and reliable information, which strengthens their trust in the organization and improves their overall experience.
Flexible Order Fulfillment Options: Efficient inventory management allows organizations to offer flexible order fulfillment options to customers. For example, by implementing drop-shipping or vendor-managed inventory (VMI) programs, organizations can expand their product offerings and provide customers with a wider range of choices.
This flexibility enhances customer satisfaction by meeting their specific needs and preferences.
Enhanced Product Quality and Freshness: Efficient inventory management ensures the rotation and timely utilization of inventory, reducing the risk of product spoilage or deterioration. This is particularly relevant for perishable goods or items with expiration dates.
By maintaining fresh and high-quality products in stock, organizations can deliver superior products to customers, leading to higher satisfaction and repeat purchases.
By prioritizing efficient inventory management, organizations can create a customer-centric approach that focuses on meeting customer demands promptly, minimizing stockouts, and providing accurate product availability information. Improved customer service enhances customer satisfaction, fosters loyalty, and establishes a competitive advantage in the marketplace.
C. Increased productivity and efficiency
Efficient inventory management directly contributes to increased productivity and operational efficiency within an organization. Here are the key ways in which efficient inventory management leads to improved productivity:
Streamlined Workflows: Efficient inventory management optimizes the flow of goods within the organization, reducing bottlenecks and delays. By having a clear understanding of inventory levels and demand patterns, organizations can streamline their production, procurement, and distribution processes. This leads to smoother workflows, minimized idle time, and increased overall productivity.
Reduced Time Spent on Inventory-related Tasks: Inefficient inventory management often results in excessive time spent on tasks such as manual tracking, counting, and reconciling inventory. By implementing automated inventory management systems and utilizing technology solutions like barcode scanning or RFID tagging, organizations can significantly reduce the time and effort required for inventory-related tasks. This allows employees to focus on more value-added activities, increasing their productivity.
Efficient Resource Allocation: Effective inventory management enables organizations to allocate resources more efficiently. By accurately forecasting demand and monitoring inventory levels, organizations can optimize their production and procurement schedules. This ensures that resources such as labor, equipment, and raw materials are allocated effectively, reducing wastage and improving overall productivity.
Minimized Stockouts and Production Delays: Efficient inventory management helps prevent stockouts and production delays by ensuring the availability of the right materials and components when needed.
This reduces the downtime caused by waiting for replenishments or alternative sourcing and allows for a consistent production flow. As a result, organizations can meet production targets, deliver orders on time, and increase overall operational efficiency.
Continuous Improvement and Lean Practices: Efficient inventory management often goes hand in hand with adopting lean principles and continuous improvement practices. By implementing techniques such as just-in-time (JIT) inventory management, Kanban systems, or value stream mapping, organizations can identify and eliminate waste, reduce lead times, and improve productivity throughout the supply chain.
Efficient inventory management streamlines processes, reduces idle time, and optimizes resource allocation, resulting in increased productivity and operational efficiency. By leveraging technology, automating tasks, and implementing lean practices, organizations can maximize their output, improve overall efficiency, and achieve higher levels of productivity.
D. Better cash flow management
Here are the key ways in which efficient inventory management improves cash flow:
Working Capital Optimization: Inventory ties up a significant portion of working capital. Inefficient inventory management can lead to excessive inventory levels, which immobilize cash and restrict its availability for other business needs. Efficient inventory management focuses on maintaining optimal inventory levels, minimizing excess stock, and aligning inventory with customer demand.
By optimizing working capital allocation, organizations can improve cash flow and have more resources available for investment, expansion, or debt repayment.
Reduced Holding Costs: Holding costs associated with inventory, such as storage, insurance, and obsolescence, directly impact cash flow. By managing inventory levels efficiently, organizations can reduce holding costs. Keeping inventory at optimal levels minimizes the need for additional storage space and lowers insurance premiums.
Additionally, efficient inventory management helps prevent obsolete or slow-moving inventory, reducing write-offs and preserving cash.
Improved Payment Terms with Suppliers: Efficient inventory management allows organizations to negotiate better payment terms with suppliers. By accurately forecasting demand, organizations can provide reliable volume estimates to suppliers and negotiate favorable terms, such as extended payment terms or discounts for early payment. These improved payment terms provide organizations with more flexibility and breathing room in managing their cash flow.
Minimized Stockouts and Lost Sales: Inefficient inventory management can lead to stockouts, which result in lost sales and missed revenue opportunities. By having the right amount of inventory to meet customer demand, organizations can prevent stockouts, fulfill orders promptly, and capture potential sales. This ensures a steady stream of revenue and positively impacts cash flow.
Accurate Cash Flow Projections: Efficient inventory management enables organizations to have a clear understanding of their inventory turnover rates and sales patterns. With accurate data on inventory levels, organizations can generate more precise cash flow projections. This allows for better financial planning, effective resource allocation, and improved cash flow management.
By optimizing inventory levels, reducing holding costs, negotiating favorable payment terms, and minimizing stockouts, efficient inventory management enhances cash flow management. This provides organizations with greater financial stability, flexibility, and the ability to allocate resources strategically for sustainable growth.
E. Competitive advantage
Here are the key ways in which efficient inventory management contributes to gaining a competitive edge:
Improved Customer Satisfaction: Efficient inventory management ensures that the right products are available when customers need them. This leads to faster order fulfillment, reduced stockouts, and improved customer satisfaction.
Satisfied customers are more likely to repeat purchases, provide positive reviews, and recommend the organization to others. This strengthens the organization's reputation, enhances customer loyalty, and provides a competitive edge over rivals.
Cost Leadership: Efficient inventory management helps organizations minimize holding costs, reduce stockouts, and optimize procurement and distribution processes. These cost savings can be passed on to customers through competitive pricing.
By offering competitive prices, organizations can attract price-conscious customers, gain market share, and outperform competitors who struggle with inefficient inventory management practices.
Enhanced Agility and Responsiveness: Efficient inventory management enables organizations to respond quickly to market demand fluctuations, changes in customer preferences, and industry trends. By having a clear view of inventory levels and utilizing agile supply chain practices, organizations can adjust their production, procurement, and distribution strategies swiftly.
This flexibility and responsiveness allow organizations to meet changing customer needs, capture new market opportunities, and stay ahead of competitors.
Supply Chain Resilience: Efficient inventory management mitigates supply chain risks and enhances resilience. By accurately forecasting demand, monitoring inventory levels, and optimizing supplier relationships, organizations can effectively manage disruptions such as supply shortages or production delays.
This resilience allows organizations to maintain a consistent supply of products, even during challenging times, and gain a competitive advantage over competitors who struggle with supply chain disruptions.
Innovation and New Product Introduction: Efficient inventory management frees up working capital and resources, allowing organizations to invest in research and development, innovation, and new product introduction.
By efficiently managing inventory and cash flow, organizations can allocate resources to drive product innovation, stay ahead of market trends, and introduce new products or services that differentiate them from competitors.
Operational Excellence: Efficient inventory management is a key component of overall operational excellence. By optimizing workflows, reducing waste, and improving productivity, organizations can achieve higher operational efficiency.
This translates into lower costs, faster lead times, improved quality, and better customer service. Organizations that excel in these areas gain a competitive advantage by delivering superior value to customers.
Strategies for Efficient Inventory Management
In order to achieve efficient inventory management, organizations need to adopt effective strategies that optimize inventory levels, streamline processes, and enhance overall operational performance.
This section will explore a range of proven strategies that executives can employ to ensure efficient inventory management within their organizations. By implementing these strategies, businesses can achieve cost savings, improve customer satisfaction, enhance productivity, and gain a competitive edge in the market.
From demand forecasting and inventory optimization to technology integration and collaboration with suppliers, this section will provide actionable insights and best practices to guide executives in their quest for efficient inventory management.
A. Demand forecasting and planning
Demand forecasting and planning is a critical strategy for efficient inventory management. It involves accurately predicting customer demand for products or services in the future. By analyzing historical sales data, market trends, customer behavior, and other relevant factors, organizations can forecast demand with greater accuracy.
This allows them to align their inventory levels and production schedules accordingly, avoiding excess inventory or stockouts. Demand forecasting and planning enable organizations to optimize inventory, reduce holding costs, improve customer satisfaction by ensuring product availability, and make informed business decisions.
Advanced forecasting techniques and technology solutions can further enhance the accuracy and effectiveness of demand forecasting and planning processes.
1. Importance of accurate demand forecasting
Accurate demand forecasting is of utmost importance for organizations for several key reasons:
Optimal Inventory Management: Accurate demand forecasting enables organizations to determine the right quantity of inventory to have on hand at any given time. By understanding customer demand patterns, organizations can avoid overstocking or understocking, leading to optimized inventory levels.
This helps in minimizing holding costs, reducing the risk of stockouts, and ensuring that the right products are available when customers need them.
Effective Production Planning: Accurate demand forecasting provides crucial insights into future customer demand, allowing organizations to plan their production activities effectively.
By aligning production schedules with expected demand, organizations can avoid unnecessary production surges or shortages. This leads to better resource utilization, streamlined workflows, and improved operational efficiency.
Efficient Supply Chain Management: Accurate demand forecasting helps organizations coordinate their supply chain activities more effectively. By sharing demand forecasts with suppliers, manufacturers, and logistics partners, organizations can collaborate on optimizing inventory levels, production schedules, and delivery timelines. This ensures smoother supply chain operations, reduces lead times, and enhances overall efficiency.
Cost Reduction: Accurate demand forecasting contributes to cost reduction across various aspects of the business. By avoiding excessive inventory levels, organizations can minimize holding costs such as storage, insurance, and obsolescence expenses. Furthermore, accurate forecasting helps organizations optimize procurement activities, negotiate better terms with suppliers, and minimize the costs associated with rush orders or emergency production.
Enhanced Customer Satisfaction: Accurate demand forecasting directly impacts customer satisfaction. By ensuring that the right products are available when customers want them, organizations can avoid stockouts and fulfill customer orders promptly. This leads to improved customer service, higher customer satisfaction levels, and increased customer loyalty.
Strategic Decision Making: Accurate demand forecasting provides organizations with valuable insights for strategic decision making. It helps in identifying market trends, understanding customer preferences, and anticipating changes in demand patterns. With this information, organizations can make informed decisions regarding product development, marketing strategies, capacity planning, and investment priorities.
In summary, accurate demand forecasting empowers organizations to align their operations with customer demand, minimize costs, enhance customer service, and maintain a competitive edge in the market.
2. Techniques and tools for demand forecasting
Demand forecasting relies on various techniques and tools to accurately predict future customer demand. Here are some commonly used techniques and tools for demand forecasting:
- Historical Data Analysis: This technique involves analyzing historical sales data to identify trends, patterns, and seasonality in customer demand. Organizations can use statistical methods such as moving averages, exponential smoothing, and regression analysis to forecast future demand based on historical patterns.
- Market Research and Surveys: Conducting market research and surveys allows organizations to gather insights directly from customers regarding their preferences, buying behavior, and anticipated demand. This qualitative data can be combined with quantitative analysis to create more accurate demand forecasts.
- Time-Series Analysis: Time-series analysis involves analyzing historical data to identify patterns and trends over time. It can include techniques such as trend analysis, seasonality analysis, and decomposition to understand and forecast demand fluctuations.
- Statistical Forecasting Models: Statistical forecasting models use mathematical algorithms and statistical techniques to predict future demand. Examples of such models include ARIMA (Autoregressive Integrated Moving Average), exponential smoothing, and Box-Jenkins models. These models consider factors such as historical sales data, seasonality, trend, and other variables to generate forecasts.
- Machine Learning and Artificial Intelligence (AI): Machine learning and AI algorithms are increasingly used in demand forecasting. These advanced techniques can analyze vast amounts of data, identify complex patterns, and adapt to changing demand dynamics. Machine learning algorithms can learn from historical data, incorporate external factors, and generate accurate demand forecasts.
- Collaborative Planning, Forecasting, and Replenishment (CPFR): CPFR involves collaborative efforts between suppliers, manufacturers, and retailers to jointly forecast demand. This approach combines input from multiple stakeholders, including sales data, market intelligence, and insights from each participant, to develop more accurate demand forecasts.
- Demand Planning Software: Demand planning software provides organizations with specialized tools and functionalities to streamline the demand forecasting process. These software solutions often incorporate statistical models, data analytics capabilities, and visualization tools to help organizations generate and manage demand forecasts more efficiently.
It's important to note that no single technique or tool is universally applicable, and organizations may employ a combination of these methods based on their industry, product characteristics, and available data. The choice of technique and tool depends on factors such as the level of accuracy required, the complexity of demand patterns, data availability, and the organization's specific needs and capabilities.
B. Inventory classification and prioritization
Inventory classification and prioritization play a crucial role in efficient inventory management. This section will delve into the importance of categorizing inventory based on its characteristics and value, as well as prioritizing inventory based on demand patterns and criticality.
By implementing effective inventory classification and prioritization strategies, organizations can optimize inventory levels, improve order fulfillment, reduce carrying costs, and enhance overall operational efficiency.
From ABC analysis and Pareto analysis to criticality assessment and safety stock calculation, this section will provide valuable insights and practical approaches for executives to effectively classify and prioritize their inventory for maximum efficiency and profitability.
1. ABC analysis
ABC analysis is a widely used inventory classification technique that categorizes items based on their relative importance and value. The technique derives its name from the three categories it creates: A, B, and C.
In ABC analysis, items are classified into categories based on their contribution to overall inventory value or sales revenue. The classification is typically determined by applying the Pareto principle, also known as the 80/20 rule, which suggests that a small number of items often account for a significant portion of the total value or revenue.
Here's how the ABC analysis categorizes inventory items:
- Category A: These items represent the highest-value or highest-revenue items in the inventory. They typically constitute a small percentage of the total number of items but contribute a significant portion of the overall value or revenue. These items require close monitoring, tighter inventory control, and frequent replenishment to ensure their availability.
- Category B: Items in this category have a moderate value or revenue contribution. They are more numerous than Category A items but still hold a considerable importance. Organizations need to maintain a balanced approach to managing Category B items, ensuring sufficient stock levels and timely replenishment.
- Category C: These items have the lowest value or revenue contribution but constitute the majority in terms of the total number of items in the inventory. Category C items are often low-value or low-demand items that require minimal attention and control. While they may not contribute significantly to the overall value or revenue, they still need to be managed efficiently to avoid stockouts or excess holding costs.
By classifying inventory items into these categories, organizations can prioritize their management efforts and allocate resources accordingly. This allows for a focused approach to inventory control, with more attention given to high-value items (Category A), followed by moderate attention to Category B items, and a more streamlined approach for Category C items.
ABC analysis helps organizations identify critical inventory items, reduce stockouts for high-value items, optimize replenishment strategies, and improve overall inventory management efficiency. It provides valuable insights for decision-making, such as identifying potential cost-saving opportunities and understanding which items require additional attention or investment.
2. Economic order quantity (EOQ) and reorder point
Economic Order Quantity (EOQ) and Reorder Point are two essential concepts in inventory management that help organizations optimize their ordering and inventory replenishment processes.
- Economic Order Quantity (EOQ): EOQ is a formula-based approach used to determine the optimal order quantity that minimizes the total cost of inventory management. It takes into account factors such as ordering costs (e.g., setup costs, administrative expenses) and carrying costs (e.g., holding costs, storage expenses). The goal of EOQ is to find the order quantity that minimizes the combined costs of ordering and holding inventory. By calculating the EOQ, organizations can strike a balance between minimizing ordering costs (by ordering in larger quantities) and minimizing carrying costs (by keeping inventory levels in check).
- Reorder Point: The reorder point is the inventory level at which a new order should be placed to replenish stock before it runs out. It is determined by considering factors such as lead time (the time it takes for a supplier to deliver the ordered items) and demand during the lead time. The reorder point helps organizations avoid stockouts by ensuring that there is sufficient inventory on hand to cover demand during the lead time. By setting the reorder point appropriately, organizations can strike a balance between preventing stockouts and avoiding excessive inventory.
Together, EOQ and reorder point help organizations optimize their inventory levels and ordering processes. By calculating the EOQ, organizations can determine the most cost-effective order quantity, reducing ordering costs and minimizing carrying costs.
The reorder point ensures that orders are placed in a timely manner to replenish inventory before it reaches a critical level. By setting the reorder point appropriately, organizations can maintain optimal inventory levels, avoid stockouts, and ensure smooth operations.
These concepts contribute to improved efficiency, cost savings, and enhanced customer satisfaction by striking the right balance between inventory investment and service levels.
4. Safety Stock Calculation
Safety stock calculation is a critical aspect of inventory management that helps organizations maintain buffer inventory to mitigate uncertainties and fluctuations in demand and supply. Safety stock acts as a cushion to ensure that the organization can meet unexpected increases in demand or disruptions in the supply chain. The calculation of safety stock involves several factors:
- Variability in Demand: The first step is to analyze historical demand data or forecasted demand to understand the variability or fluctuations in demand. Statistical techniques such as standard deviation or coefficient of variation can be used to quantify the demand variability.
- Lead Time Variability: Organizations need to assess the variability in lead time, which is the time taken from placing an order to receiving the inventory. Historical lead time data or supplier performance data can help determine lead time variability.
- Service Level: The desired service level is a key consideration in safety stock calculation. It represents the desired level of customer satisfaction or the probability of meeting customer demand. Commonly used service levels are expressed as percentages, such as 95%, 98%, or 99%. A higher service level implies a lower risk of stockouts but may require a higher safety stock.
- Reorder Point: The reorder point, as discussed earlier, indicates the inventory level at which a new order should be placed. The calculation of the reorder point should include the safety stock to account for demand and lead time variability.
- Safety Stock Formula: Once the above factors are determined, the safety stock can be calculated. Various methods and formulas can be used, such as the standard deviation method, the service level method, or probabilistic models like the normal distribution or Poisson distribution. These methods consider demand and lead time variability along with the desired service level to determine the appropriate level of safety stock.
By calculating the safety stock accurately, organizations can avoid stockouts, minimize the risk of disruptions, and ensure a higher level of customer service. It provides a buffer against uncertainties in demand and lead time, enabling organizations to meet customer needs even during unexpected situations.
Safety stock calculation is an essential aspect of inventory planning and ensures that organizations have the necessary inventory levels to maintain operational efficiency and customer satisfaction.
C. Just-in-Time (JIT) inventory management
Just-in-Time (JIT) inventory management is a lean approach to inventory control that aims to minimize inventory holding costs while ensuring the timely availability of materials and products. This section explores the principles and benefits of JIT inventory management, as well as the key strategies and considerations for implementing JIT practices.
1. Principles and advantages of JIT
Just-in-Time (JIT) inventory management operates on the principles of minimizing inventory, reducing waste, ensuring continuous flow, improving quality, and fostering strong supplier relationships. The advantages of JIT include reduced costs through lower inventory holding expenses, increased operational efficiency, improved product quality, enhanced flexibility to meet customer demands, and higher levels of customer satisfaction.
By adopting JIT practices, organizations can optimize their inventory management processes, streamline operations, reduce waste, and achieve a competitive advantage by delivering products efficiently, minimizing lead times, and responding quickly to changing market demands.
2. Implementing JIT in the supply chain
Implementing Just-in-Time (JIT) in the supply chain involves several key considerations.
- First, close collaboration and trust with suppliers are crucial to ensure the timely delivery of materials.
- Second, a strong focus on quality control and defect prevention is necessary to maintain product integrity.
- Third, a continuous flow of information and materials must be established, minimizing lead times and reducing waste.
- Fourth, production processes should be aligned with customer demand, avoiding overproduction.
- Finally, effective communication and coordination among all stakeholders in the supply chain are vital for successful JIT implementation.
By implementing JIT, organizations can achieve a leaner and more efficient supply chain, reducing inventory costs and enhancing overall responsiveness to customer needs.
D. Technology and automation
Technology and automation have revolutionized inventory management, enabling organizations to enhance efficiency, accuracy, and productivity in their operations. This section explores the role of technology and automation in inventory management and highlights the benefits and considerations associated with their implementation.
By leveraging these tools, organizations can streamline inventory processes, optimize stock levels, improve order accuracy, and reduce costs. This section delves into the various technologies and automation solutions available, providing insights for executives on harnessing technology's power to achieve efficient and effective inventory management.
1. Inventory management software and systems
Inventory management software and systems play a crucial role in modernizing and streamlining inventory management processes. These software solutions automate and centralize various aspects of inventory control, providing organizations with real-time visibility, accurate data, and efficient management capabilities. Here are the key features and benefits of inventory management software and systems:
- Real-time Inventory Tracking: Inventory management software enables real-time tracking of inventory levels, locations, and stock movements. This allows organizations to have accurate and up-to-date information on stock availability, facilitating better decision-making and reducing the risk of stockouts or overstocking.
- Demand Forecasting and Planning: Many inventory management systems incorporate demand forecasting and planning functionalities. By analyzing historical data, market trends, and customer demand patterns, these systems help organizations make more accurate predictions and optimize their inventory levels accordingly.
- Order Management: Inventory management software streamlines the order management process, from order placement to fulfillment. It automates order processing, tracks order status, and integrates with other systems like customer relationship management (CRM) and enterprise resource planning (ERP) to ensure efficient order fulfillment.
- Supplier and Vendor Management: These software solutions facilitate effective supplier and vendor management by providing tools for managing supplier information, monitoring delivery performance, and optimizing supplier relationships. This helps organizations maintain reliable and efficient supply chains.
- Reporting and Analytics: Inventory management software generates comprehensive reports and analytics, offering valuable insights into inventory performance, stock turnover, carrying costs, and more. These insights enable organizations to identify areas for improvement, optimize inventory strategies, and make data-driven decisions.
- Integration and Automation: Inventory management systems often integrate with other business systems, such as point-of-sale (POS) systems, accounting software, and warehouse management systems. This integration eliminates manual data entry, reduces errors, and streamlines information flow across different departments.
2. Barcode and RFID technologies
Barcode and Radio Frequency Identification (RFID) technologies have revolutionized inventory management by providing accurate and efficient tracking capabilities.
Barcodes are widely used in inventory management as they enable quick and error-free data capture. Each item is assigned a unique barcode that can be scanned using handheld barcode scanners or integrated into the organization's systems. Barcodes allow for easy identification, tracking, and retrieval of inventory data, enhancing inventory accuracy and reducing manual errors.
RFID technology takes inventory tracking to a new level by using radio frequency signals to identify and track items. RFID tags are attached to individual items or pallets, and RFID readers capture the data wirelessly. This enables real-time and automated tracking of inventory throughout the supply chain. RFID provides advantages such as faster and more accurate inventory counting, improved visibility, and reduced labor costs.
Both barcode and RFID technologies facilitate faster inventory audits, streamlined order fulfillment, and improved inventory accuracy. They enable organizations to track inventory in real-time, reduce stockouts and overstocking, enhance supply chain visibility, and improve operational efficiency. By leveraging these technologies, organizations can optimize inventory management, reduce costs, and enhance overall productivity.
E. Supplier collaboration and relationship management
Supplier collaboration and relationship management are critical aspects of efficient inventory management. This section explores the importance of fostering strong partnerships with suppliers and implementing effective collaboration strategies. By establishing close relationships, organizations can enhance supply chain visibility, improve communication, and achieve mutual benefits.
From supplier selection and performance evaluation to joint forecasting and shared data exchange, this section delves into the key principles and practices of supplier collaboration.
It highlights the advantages of collaborative supplier relationships, such as reduced lead times, improved product quality, lower costs, and enhanced responsiveness to market changes.
1. Vendor-managed inventory (VMI)
Vendor-managed inventory (VMI) is a collaborative inventory management approach in which the supplier takes responsibility for managing and replenishing the inventory at the customer's location. In VMI, the supplier has real-time visibility into the customer's inventory levels and is authorized to make inventory decisions, such as replenishment orders and stock adjustments, based on agreed-upon parameters.
The key features and benefits of Vendor-managed inventory (VMI) include:
- Reduced Inventory Holding Costs: VMI eliminates the need for the customer to carry excess inventory by allowing the supplier to monitor and control inventory levels. This leads to reduced holding costs, including storage, obsolescence, and carrying costs.
- Enhanced Supply Chain Visibility: VMI enables real-time visibility into inventory levels, sales data, and consumption patterns. Both the supplier and customer have access to accurate and up-to-date information, facilitating better demand forecasting, production planning, and order fulfillment.
- Improved Efficiency and Order Fulfillment: With VMI, the supplier proactively manages inventory levels, ensuring that the right products are available at the right time. This minimizes stockouts and reduces lead times, resulting in improved order fulfillment and customer satisfaction.
- Collaborative Planning and Forecasting: VMI promotes collaboration between the supplier and customer in terms of demand planning and forecasting. By sharing data and insights, both parties can align their production, inventory, and sales strategies, leading to better inventory accuracy and more effective supply chain management.
- Stronger Supplier-Customer Relationships: VMI fosters closer relationships and trust between suppliers and customers. The collaborative nature of VMI encourages open communication, joint problem-solving, and shared goals, leading to long-term partnerships and improved overall business performance.
2. Collaborative planning, forecasting, and replenishment (CPFR)
Collaborative Planning, Forecasting, and Replenishment (CPFR) is a collaborative approach to inventory management that involves joint planning and decision-making between trading partners, typically suppliers and retailers. CPFR aims to synchronize supply and demand by sharing information, aligning forecasts, and coordinating replenishment activities.
The key features and benefits of Collaborative Planning, Forecasting, and Replenishment (CPFR) include:
- Information Sharing: CPFR emphasizes the exchange of accurate and timely information between trading partners. This includes sales data, demand forecasts, inventory levels, and promotional plans. By sharing information, organizations can gain better visibility into demand patterns and make informed inventory decisions.
- Demand Collaboration: CPFR facilitates joint planning and forecasting activities. Trading partners collaborate to develop a unified demand forecast, considering factors such as historical sales data, market trends, and promotional events. This collaborative approach leads to more accurate demand forecasts, reducing stockouts and excess inventory.
- Replenishment Coordination: CPFR enables trading partners to synchronize their replenishment activities based on the shared demand forecast. This ensures that inventory is replenished in a timely manner, avoiding stockouts while minimizing inventory holding costs.
- Reduced Bullwhip Effect: By aligning forecasts and sharing information, CPFR helps mitigate the bullwhip effect, which is the amplification of demand fluctuations as they move up the supply chain. With reduced variability in demand, organizations can optimize their inventory levels, reduce costs, and improve overall supply chain efficiency.
- Enhanced Supply Chain Efficiency: CPFR fosters closer collaboration and communication between trading partners. This leads to better coordination of activities, improved inventory visibility, and increased responsiveness to changes in demand or market conditions. Ultimately, CPFR helps organizations achieve a more efficient and resilient supply chain.
Key Performance Indicators (KPIs) for Inventory Management
Key Performance Indicators (KPIs) are essential metrics used to assess the performance and effectiveness of inventory management practices. This section explores the significance of KPIs and their role in evaluating and improving inventory management processes.
By measuring and analyzing specific KPIs, organizations can gain valuable insights into inventory performance, identify areas for improvement, and make data-driven decisions.
From inventory turnover and carrying costs to fill rate and order accuracy, this section delves into the key KPIs that executives should monitor to optimize inventory management.
A. Inventory turnover ratio
The inventory turnover ratio is a critical Key Performance Indicator (KPI) that measures the efficiency of inventory management by assessing how quickly inventory is sold and replaced within a specific period. It is calculated by dividing the cost of goods sold (COGS) by the average inventory value during the same period.
A high inventory turnover ratio indicates that inventory is being effectively managed and quickly converted into sales, minimizing holding costs and reducing the risk of obsolete or expired stock. On the other hand, a low inventory turnover ratio suggests potential issues such as overstocking, slow-moving items, or poor sales performance.
By monitoring the inventory turnover ratio, executives can gain insights into inventory efficiency, optimize inventory levels, and make informed decisions regarding purchasing, production, and sales strategies. It helps organizations to strike a balance between maintaining sufficient inventory to meet customer demand and minimizing the associated costs, ultimately enhancing profitability and operational performance.
B. Stock-out rate
The stock-out rate is a crucial Key Performance Indicator (KPI) that measures the frequency and impact of stockouts, which occur when inventory is depleted and unavailable to fulfill customer orders or meet internal demand. The stock-out rate is calculated by dividing the number of stockouts by the total number of opportunities for a stockout within a given period.
A high stock-out rate indicates poor inventory management and can have negative consequences such as dissatisfied customers, lost sales, and damage to the organization's reputation. On the other hand, a low stock-out rate signifies effective inventory planning, replenishment, and fulfillment processes, ensuring product availability and customer satisfaction.
By monitoring the stock-out rate, executives can identify trends, pinpoint areas for improvement, and take proactive measures to minimize stockouts. This may involve optimizing inventory levels, implementing robust demand forecasting systems, improving supplier relationships, or enhancing order fulfillment processes. A lower stock-out rate enables organizations to meet customer expectations, drive sales, and maintain a competitive edge in the market.
C. Order cycle time
Order cycle time is a significant Key Performance Indicator (KPI) that measures the time it takes to fulfill a customer order from the moment it is placed until the order is delivered. It encompasses various stages, including order processing, picking and packing, transportation, and final delivery to the customer.
A shorter order cycle time is desirable as it indicates efficient and prompt order fulfillment, leading to increased customer satisfaction and loyalty. It also allows organizations to respond quickly to market demands and changes.
By monitoring the order cycle time, executives can identify bottlenecks and inefficiencies in the order fulfillment process. This KPI helps them identify areas for improvement, optimize workflow, and streamline operations to reduce cycle times. This may involve implementing automation, improving coordination between departments, enhancing communication with suppliers and logistics partners, and investing in technology solutions that expedite the order fulfillment process.
Ultimately, a reduced order cycle time enables organizations to improve customer service, increase operational efficiency, and gain a competitive advantage in the marketplace.
D. Fill rate
Fill rate is a significant Key Performance Indicator (KPI) that measures the percentage of customer orders fulfilled in their entirety without any backorders or stockouts. It reflects the organization's ability to meet customer demand and deliver products as promised.
A high fill rate indicates effective inventory management and order fulfillment processes, ensuring that customers receive their complete orders on time. It signifies that the organization has sufficient stock levels, accurate demand forecasting, and efficient replenishment systems in place.
On the other hand, a low fill rate suggests potential issues such as inventory shortages, poor demand planning, or order fulfillment inefficiencies. This can lead to dissatisfied customers, lost sales opportunities, and damage to the organization's reputation.
Monitoring the fill rate enables executives to identify gaps in inventory management and fulfillment processes, enabling them to take corrective actions. This may involve optimizing inventory levels, improving demand forecasting accuracy, enhancing supplier relationships, or streamlining order fulfillment operations.
By maintaining a high fill rate, organizations can enhance customer satisfaction, drive repeat business, and establish a reputation for reliable and responsive order fulfillment.
E. Carrying cost of inventory
The carrying cost of inventory is a critical Key Performance Indicator (KPI) that measures the expenses associated with holding and storing inventory over a specific period. It encompasses various costs, including warehousing, insurance, depreciation, obsolescence, taxes, and opportunity costs.
A high carrying cost of inventory indicates inefficiencies in inventory management, such as excessive stock levels or slow inventory turnover. It signifies that a significant portion of the organization's financial resources is tied up in inventory, leading to increased holding costs and reduced profitability.
By monitoring the carrying cost of inventory, executives can identify opportunities to optimize inventory levels and reduce holding costs. This may involve implementing strategies such as just-in-time (JIT) inventory management, demand forecasting, and supply chain optimization to reduce inventory carrying requirements.
Additionally, improving inventory turnover through effective sales and operations planning (S&OP) and supply chain coordination can also help minimize carrying costs.
Reducing the carrying cost of inventory allows organizations to free up capital, improve cash flow, and allocate resources more efficiently. It also minimizes the risk of inventory obsolescence and improves overall financial performance.
Challenges and Solutions in Inventory Management
The effective management of inventory comes with its own set of challenges, and organizations must be prepared to tackle them head-on. This section explores the common challenges faced in inventory management and provides insights into potential solutions.
From maintaining optimal inventory levels and mitigating supply chain disruptions to addressing demand variability and optimizing inventory accuracy, executives will gain a comprehensive understanding of the hurdles that can hinder efficient inventory management.
A. Inventory inaccuracies and shrinkage
Inventory inaccuracies and shrinkage pose significant challenges to efficient inventory management. Inaccurate inventory records, discrepancies between physical and recorded stock, and theft contribute to inventory shrinkage. These challenges result in stockouts, excess inventory, and financial losses.
This section delves into the causes of inventory inaccuracies and shrinkage, such as poor tracking systems and inadequate security measures. It also provides solutions, including implementing robust inventory control procedures, utilizing technology for real-time tracking, conducting regular audits, and enhancing security measures to mitigate these challenges and improve overall inventory accuracy.
1. Root causes and impact on the business
Root causes of inventory inaccuracies and shrinkage can vary, but some common factors include:
- Poor Inventory Tracking: Inadequate inventory management systems or manual tracking processes can lead to errors in recording and monitoring inventory levels, resulting in inaccuracies.
- Lack of Training and Accountability: Insufficient training of employees responsible for inventory management can contribute to errors and discrepancies. Additionally, a lack of accountability and adherence to inventory control procedures can lead to shrinkage.
- Internal Theft: Employee theft or unauthorized use of inventory can significantly impact inventory accuracy and contribute to shrinkage. This can occur through various means, such as theft of physical inventory or manipulation of inventory records.
- External Theft: External theft, including shoplifting, break-ins, or theft during transportation, can also contribute to inventory shrinkage.
The impact of inventory inaccuracies and shrinkage on a business can be substantial. It leads to several negative consequences, including:
- Stockouts and Lost Sales: Inaccurate inventory records can result in stockouts, causing delays in order fulfillment and lost sales opportunities.
- Excess Inventory and Holding Costs: Inaccurate tracking and control of inventory can lead to overstocking, tying up capital and increasing holding costs, such as storage, insurance, and depreciation.
- Reduced Profitability: Shrinkage directly impacts a company's profitability, as lost inventory represents a financial loss that cannot be recovered.
- Damaged Reputation: Inaccurate inventory records and stockouts can harm a company's reputation, leading to customer dissatisfaction and potential loss of business.
2. Inventory control measures and cycle counting
Inventory control measures and cycle counting are essential components of effective inventory management. Inventory control measures refer to the strategies and practices implemented to maintain accurate inventory records, prevent stockouts and overstocking, minimize discrepancies, and optimize inventory levels.
These measures typically involve establishing policies, procedures, and systems to track and manage inventory throughout its lifecycle.
Cycle counting, on the other hand, is a method of regularly auditing and verifying the accuracy of inventory records by counting a subset of inventory items on a scheduled basis. It involves counting a specific group of items within a predetermined time frame, often using a systematic approach that ensures all items are counted over a defined period.
The goal of cycle counting is to identify and correct any discrepancies between the recorded inventory and the actual physical count, enabling proactive measures to address inaccuracies and improve inventory accuracy.
Implementing inventory control measures and cycle counting offers several benefits:
- Improved Inventory Accuracy: By regularly monitoring and verifying inventory levels through cycle counting, organizations can identify and rectify discrepancies, leading to more accurate inventory records.
- Timely Identification of Issues: Cycle counting allows for the early detection of issues such as shrinkage, data entry errors, or process inefficiencies, enabling prompt corrective actions.
- Minimized Stockouts and Overstocking: Accurate inventory records and proactive monitoring help prevent stockouts by ensuring that sufficient stock is available to meet customer demand. It also reduces overstocking, which ties up capital and increases holding costs.
- Enhanced Operational Efficiency: Effective inventory control measures and cycle counting streamline inventory management processes, reduce manual errors, and optimize inventory levels, leading to improved operational efficiency and productivity.
- Improved Customer Satisfaction: Accurate inventory records and timely order fulfillment resulting from effective inventory management positively impact customer satisfaction by minimizing stockouts and ensuring on-time delivery.
To implement inventory control measures and cycle counting effectively, organizations should establish clear inventory management policies and procedures. They must invest in appropriate inventory management systems and technologies, train staff on accurate record-keeping and cycle counting practices.
B. Supply chain disruptions and risk management
Supply chain disruptions and risk management are crucial aspects of ensuring a smooth and uninterrupted flow of goods and services throughout the supply chain. Here's an explanation of strategies for mitigating supply chain risks and the importance of alternative sourcing and contingency planning:
- Strategies for Mitigating Supply Chain Risks:
To mitigate supply chain risks, organizations can implement the following strategies:
a) Diversification of Suppliers: Relying on a single supplier can create vulnerability. Diversifying the supplier base helps reduce dependence on a single source and minimizes the impact of supplier-specific disruptions.
b) Supplier Relationship Management: Building strong relationships with suppliers can foster collaboration, communication, and mutual trust. This allows for better risk identification and mitigation strategies.
c) Supply Chain Visibility: Enhancing visibility across the supply chain enables organizations to identify potential risks and proactively address them. Real-time data sharing and analytics can provide insights into demand fluctuations, inventory levels, and potential disruptions.
d) Risk Assessment and Contingency Planning: Conducting thorough risk assessments to identify potential risks and their potential impact is crucial. Organizations can then develop contingency plans, such as alternative sourcing options, safety stock provisions, and backup logistics arrangements.
e) Collaborative Planning: Collaborating with key stakeholders in the supply chain, including suppliers, distributors, and logistics partners, helps in aligning strategies, sharing information, and collectively managing risks.
- Alternative Sourcing and Contingency Planning:
Alternative sourcing and contingency planning play a vital role in mitigating supply chain disruptions:
a) Alternative Sourcing: Identifying and establishing relationships with secondary or backup suppliers can help mitigate risks associated with primary supplier disruptions. This ensures a fallback option for critical components or materials during unforeseen circumstances.
b) Dual Sourcing: Implementing dual sourcing strategies involves working with multiple suppliers for the same product or component. This approach provides flexibility and reduces the risk of supply chain disruptions if one supplier faces challenges.
c) Safety Stock and Buffer Inventory: Maintaining safety stock or buffer inventory can help mitigate disruptions by ensuring an adequate supply of critical items during unforeseen events. This additional inventory acts as a cushion against supply disruptions or delays.
d) Scenario Planning: Conducting scenario planning exercises allows organizations to evaluate potential disruptions, simulate their impacts, and develop proactive strategies to address them. This helps in identifying vulnerabilities and crafting contingency plans accordingly.
e) Business Continuity Planning: Developing comprehensive business continuity plans ensures that organizations have a roadmap to follow during disruptions. This includes establishing communication protocols, backup systems, and coordination mechanisms to minimize downtime and resume operations swiftly.
By adopting these strategies and investing in robust risk management practices, organizations can enhance their resilience to supply chain disruptions, minimize potential disruptions' impacts, and maintain a stable and efficient supply chain.
C. Seasonality and demand variability
Supply chain disruptions and risk management are crucial aspects of ensuring a smooth and uninterrupted flow of goods and services throughout the supply chain. Here's an explanation of strategies for mitigating supply chain risks and the importance of alternative sourcing and contingency planning:
- Strategies for Mitigating Supply Chain Risks:
To mitigate supply chain risks, organizations can implement the following strategies:
a) Diversification of Suppliers: Relying on a single supplier can create vulnerability. Diversifying the supplier base helps reduce dependence on a single source and minimizes the impact of supplier-specific disruptions.
b) Supplier Relationship Management: Building strong relationships with suppliers can foster collaboration, communication, and mutual trust. This allows for better risk identification and mitigation strategies.
c) Supply Chain Visibility: Enhancing visibility across the supply chain enables organizations to identify potential risks and proactively address them. Real-time data sharing and analytics can provide insights into demand fluctuations, inventory levels, and potential disruptions.
d) Risk Assessment and Contingency Planning: Conducting thorough risk assessments to identify potential risks and their potential impact is crucial. Organizations can then develop contingency plans, such as alternative sourcing options, safety stock provisions, and backup logistics arrangements.
e) Collaborative Planning: Collaborating with key stakeholders in the supply chain, including suppliers, distributors, and logistics partners, helps in aligning strategies, sharing information, and collectively managing risks.
- Alternative Sourcing and Contingency Planning:
Alternative sourcing and contingency planning play a vital role in mitigating supply chain disruptions:
a) Alternative Sourcing: Identifying and establishing relationships with secondary or backup suppliers can help mitigate risks associated with primary supplier disruptions. This ensures a fallback option for critical components or materials during unforeseen circumstances.
b) Dual Sourcing: Implementing dual sourcing strategies involves working with multiple suppliers for the same product or component. This approach provides flexibility and reduces the risk of supply chain disruptions if one supplier faces challenges.
c) Safety Stock and Buffer Inventory: Maintaining safety stock or buffer inventory can help mitigate disruptions by ensuring an adequate supply of critical items during unforeseen events. This additional inventory acts as a cushion against supply disruptions or delays.
d) Scenario Planning: Conducting scenario planning exercises allows organizations to evaluate potential disruptions, simulate their impacts, and develop proactive strategies to address them. This helps in identifying vulnerabilities and crafting contingency plans accordingly.
e) Business Continuity Planning: Developing comprehensive business continuity plans ensures that organizations have a roadmap to follow during disruptions. This includes establishing communication protocols, backup systems, and coordination mechanisms to minimize downtime and resume operations swiftly.
By adopting these strategies and investing in robust risk management practices, organizations can enhance their resilience to supply chain disruptions, minimize potential disruptions' impacts, and maintain a stable and efficient supply chain.
Case Studies and Best Practices
This section takes us through case studies and some of the best practices in the process of an efficient inventory management. Let’s take a look:
A. Success stories of companies with efficient inventory management
There are several success stories of companies that have implemented efficient inventory management practices and achieved notable results. Here are a few examples:
Walmart: Walmart is renowned for its efficient inventory management practices. The company implemented a sophisticated inventory tracking system that uses real-time data to manage inventory levels and minimize stockouts. By leveraging technology and data analytics, Walmart reduced inventory holding costs, improved product availability, and enhanced customer satisfaction.
Amazon: Amazon revolutionized the e-commerce industry with its highly efficient inventory management practices. The company employs advanced algorithms and predictive analytics to forecast demand accurately, optimize inventory levels, and streamline order fulfillment. Amazon's focus on inventory turnover, fast shipping, and accurate demand forecasting has contributed to its rapid growth and customer-centric reputation.
Zara: Zara, a leading fast-fashion retailer, is known for its agile inventory management approach. The company employs a "fast fashion" model that enables it to quickly respond to changing market trends and customer preferences. Zara's vertically integrated supply chain and efficient logistics operations allow for shorter lead times, reduced inventory levels, and faster product replenishment.
Procter & Gamble (P&G): P&G, a consumer goods company, implemented a collaborative inventory management system called Vendor Managed Inventory (VMI). Through VMI, P&G collaborates closely with its retail partners to monitor inventory levels and replenish stock automatically based on demand data. This partnership-based approach has resulted in improved inventory accuracy, reduced stockouts, and enhanced supply chain efficiency.
Toyota: Toyota is renowned for its adoption of lean manufacturing principles, including efficient inventory management practices. The company implements the just-in-time (JIT) approach, which aims to minimize inventory holding costs while ensuring the availability of materials and components when needed. Toyota's focus on reducing waste, optimizing production flow, and maintaining low inventory levels has resulted in improved operational efficiency and cost savings.
B. Lessons learned and key takeaways
Here are some lessons learned from these case studies:
Embrace technology and data analytics: Companies that have achieved efficient inventory management leverage technology and data analytics to gather real-time data, forecast demand accurately, and make informed inventory decisions.
Implementing inventory management software, utilizing predictive analytics, and adopting automation can significantly enhance inventory control and visibility.
Collaborate with partners: Successful companies recognize the importance of collaboration with suppliers, distributors, and retail partners. Sharing information, aligning goals, and jointly planning inventory management activities can lead to improved supply chain coordination, reduced stockouts, and enhanced customer service.
Focus on demand forecasting and agility: Accurate demand forecasting is a critical component of efficient inventory management. Companies that excel in this area invest in demand forecasting techniques, closely monitor market trends, and adjust production and procurement accordingly. Additionally, they emphasize agility and responsiveness to rapidly changing customer demands and market conditions.
Optimize inventory turnover: Efficient inventory management involves optimizing inventory turnover to minimize carrying costs and maximize working capital. Companies can achieve this by implementing strategies such as just-in-time (JIT) principles, reducing lead times, implementing effective order fulfillment processes, and closely monitoring inventory levels.
Continuous improvement and process optimization: Successful companies prioritize continuous improvement and process optimization in their inventory management practices. They regularly evaluate performance metrics, analyze bottlenecks, and seek opportunities for streamlining processes, reducing waste, and enhancing overall supply chain efficiency.
Customer-centric approach: Companies with efficient inventory management prioritize meeting customer demand and enhancing customer satisfaction. They align their inventory levels with customer expectations, implement strategies to minimize stockouts, and ensure timely delivery. Understanding customer preferences, analyzing buying patterns, and adapting inventory strategies accordingly contribute to their success.
Future Trends and Advancements in Inventory Management
Inventory management is a dynamic field that continues to evolve with advancements in technology and changing business landscapes. Here are some future trends and advancements that are likely to shape the future of inventory management:
- Advanced Analytics and Artificial Intelligence (AI): The integration of advanced analytics and AI technologies will enable more accurate demand forecasting, optimized inventory levels, and proactive decision-making. AI-powered algorithms will analyze large volumes of data to identify patterns, predict demand fluctuations, and optimize replenishment strategies.
- Internet of Things (IoT) and RFID: The widespread adoption of IoT devices and RFID technology will provide real-time visibility into inventory levels, location tracking, and condition monitoring. This will enable businesses to have a holistic view of their inventory across the supply chain and facilitate seamless inventory management, reducing stockouts and enhancing supply chain efficiency.
- Blockchain Technology: Blockchain has the potential to revolutionize inventory management by providing a decentralized and secure platform for tracking and tracing inventory movements. It can enhance transparency, accuracy, and trust among supply chain partners, reducing the risk of counterfeit products and enabling efficient inventory management.
- Robotics and Automation: Robotics and automation will play a significant role in inventory management, especially in warehouse operations. Autonomous robots and automated systems will streamline order picking, packing, and inventory replenishment processes, reducing manual errors and increasing efficiency.
- Mobile and Cloud Solutions: Mobile applications and cloud-based inventory management systems will enable real-time access to inventory data, anytime and anywhere. This will empower businesses to make informed decisions on-the-go, collaborate with partners, and manage inventory efficiently, even across multiple locations.
- Sustainable Inventory Practices: With the growing focus on sustainability, businesses will increasingly adopt environmentally friendly inventory management practices. This includes optimizing packaging materials, implementing reverse logistics for product returns, and reducing waste in the supply chain.
- Collaboration and Visibility: Enhanced collaboration and visibility across supply chain partners will be key to efficient inventory management. Real-time sharing of data, forecasts, and inventory information will enable partners to make informed decisions, reduce lead times, and improve overall supply chain performance.
Conclusion
Efficient inventory management is a critical aspect of running a successful business. This executive guide has provided valuable insights into the key components, strategies, and benefits of effective inventory management. By understanding the definition of inventory management and its objectives, executives can establish a solid foundation for optimizing their inventory practices.
They have also gained knowledge about the various types of inventory and the costs associated with them, enabling them to make informed decisions that impact the bottom line.
Moreover, this guide has highlighted the numerous benefits of efficient inventory management, including cost savings, improved customer service, increased productivity, better cash flow management, and a competitive advantage in the market.
Executives now understand the importance of leveraging strategies such as demand forecasting and planning, inventory classification and prioritization, just-in-time (JIT) management, and the use of technology and automation to enhance their inventory operations.
Furthermore, this guide has shed light on the significance of supplier collaboration, the measurement of key performance indicators (KPIs), and the challenges faced in inventory management. By recognizing these challenges and implementing appropriate solutions, executives can mitigate risks and drive continuous improvement in their inventory management processes.
In conclusion, efficient inventory management is crucial for achieving operational excellence, customer satisfaction, and financial success.
How can Deskera Help You?
Deskera ERP and MRP systems help you to keep your business units organized. The system's primary functions are as follows:
- Keep track of your raw materials and final items inventories
- Control production schedules and routings
- Keep a bill of materials
- Produce thorough reports
- Make your own dashboards
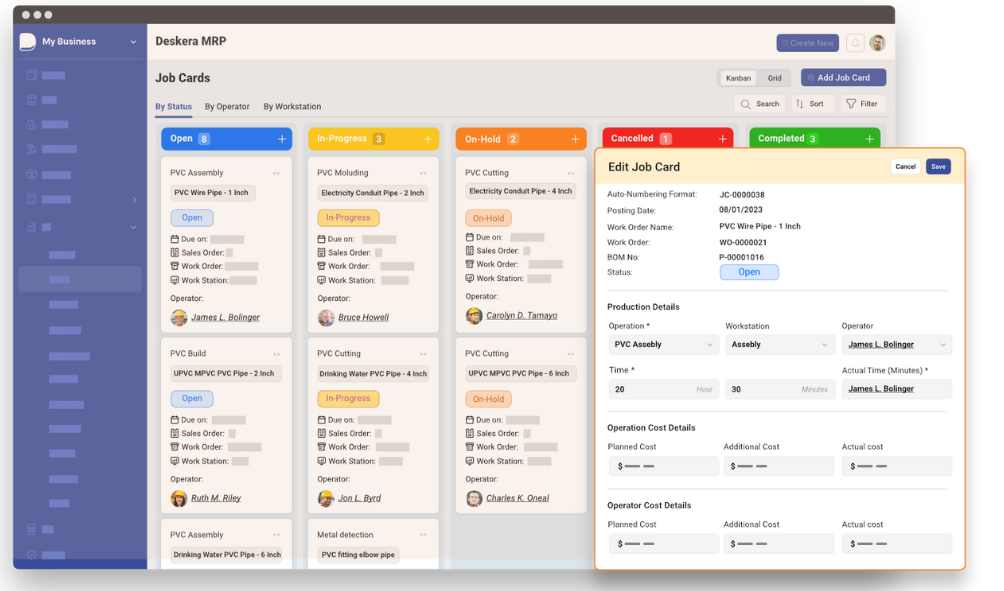
Deskera's integrated financial planning tools enable investors to better plan and track their investments. It can assist investors in making faster and more accurate decisions.
Deskera Books allows you to better manage your accounts and finances. Maintain good accounting practices by automating tasks like billing, invoicing, and payment processing.
Deskera CRM is a powerful solution that manages your sales and helps you close deals quickly. It not only enables you to perform critical tasks like lead generation via email, but it also gives you a comprehensive view of your sales funnel.
Deskera People is a straightforward tool for centralizing your human resource management functions.
Key Takeaways
- Efficient inventory management is crucial for optimizing operational efficiency, reducing costs, and enhancing customer satisfaction.
- Accurate demand forecasting is essential for maintaining optimal inventory levels and avoiding stockouts or excess inventory.
- Different types of inventory, such as raw materials, work-in-progress, and finished goods, require specific management strategies.
- Inventory costs, including carrying costs, holding costs, and ordering costs, directly impact the profitability of a business.
- Efficient inventory management brings several benefits, including cost savings, improved customer service, increased productivity, better cash flow management, and a competitive advantage.
- Strategies such as just-in-time (JIT) management, ABC analysis, economic order quantity (EOQ), and safety stock calculation are effective in optimizing inventory levels and minimizing costs.
- Technology and automation, such as inventory management software, barcode and RFID technologies, play a significant role in streamlining inventory processes and improving accuracy.
- Collaborating with suppliers and partners, implementing vendor-managed inventory (VMI), and utilizing collaborative planning, forecasting, and replenishment (CPFR) can enhance supply chain efficiency.
- Key performance indicators (KPIs) like inventory turnover ratio, stock-out rate, order cycle time, fill rate, and carrying cost help measure and monitor the effectiveness of inventory management.
- Challenges in inventory management, such as inaccuracies, shrinkage, supply chain disruptions, and seasonality, can be mitigated through effective control measures, cycle counting, risk management strategies, and collaboration with stakeholders.
Related Articles
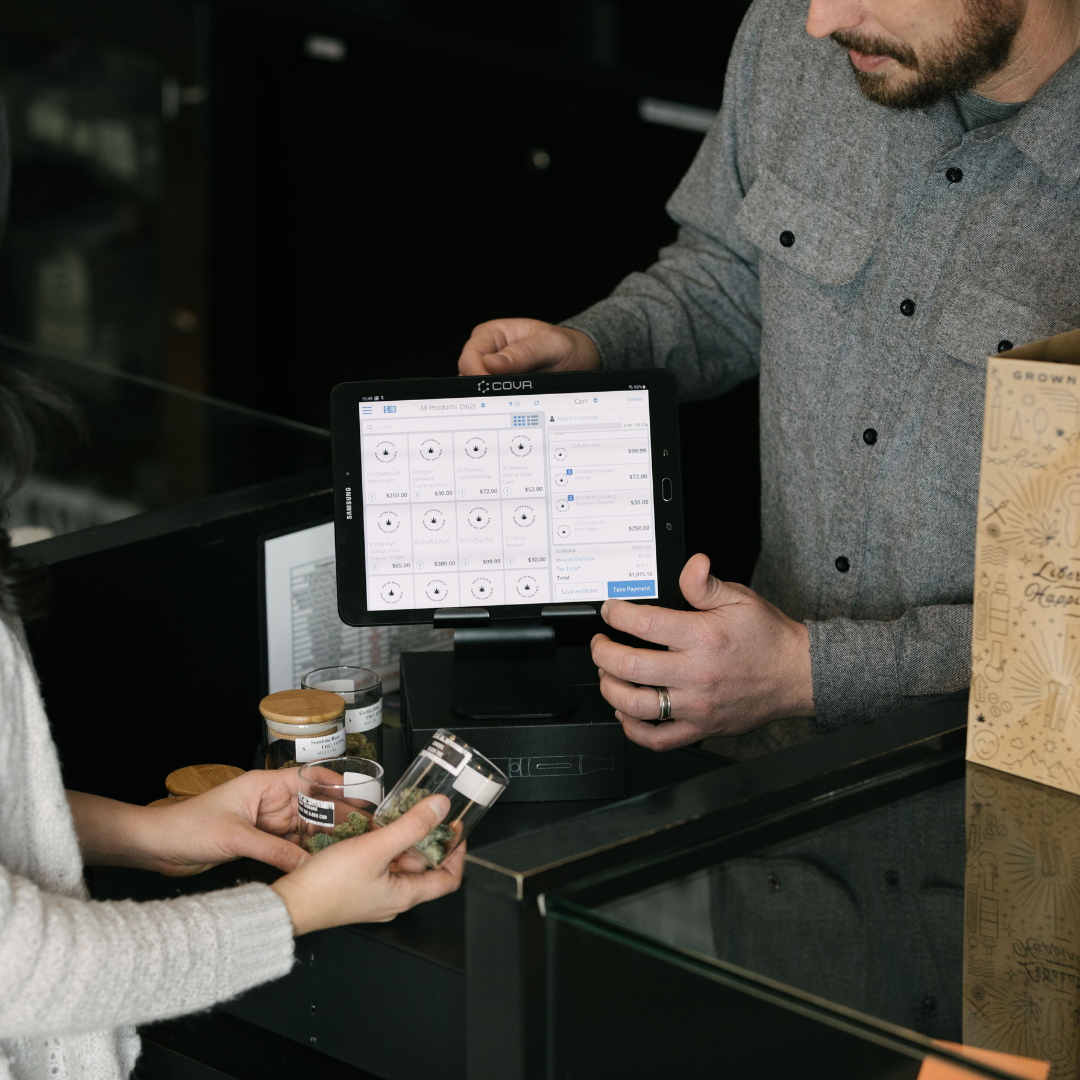
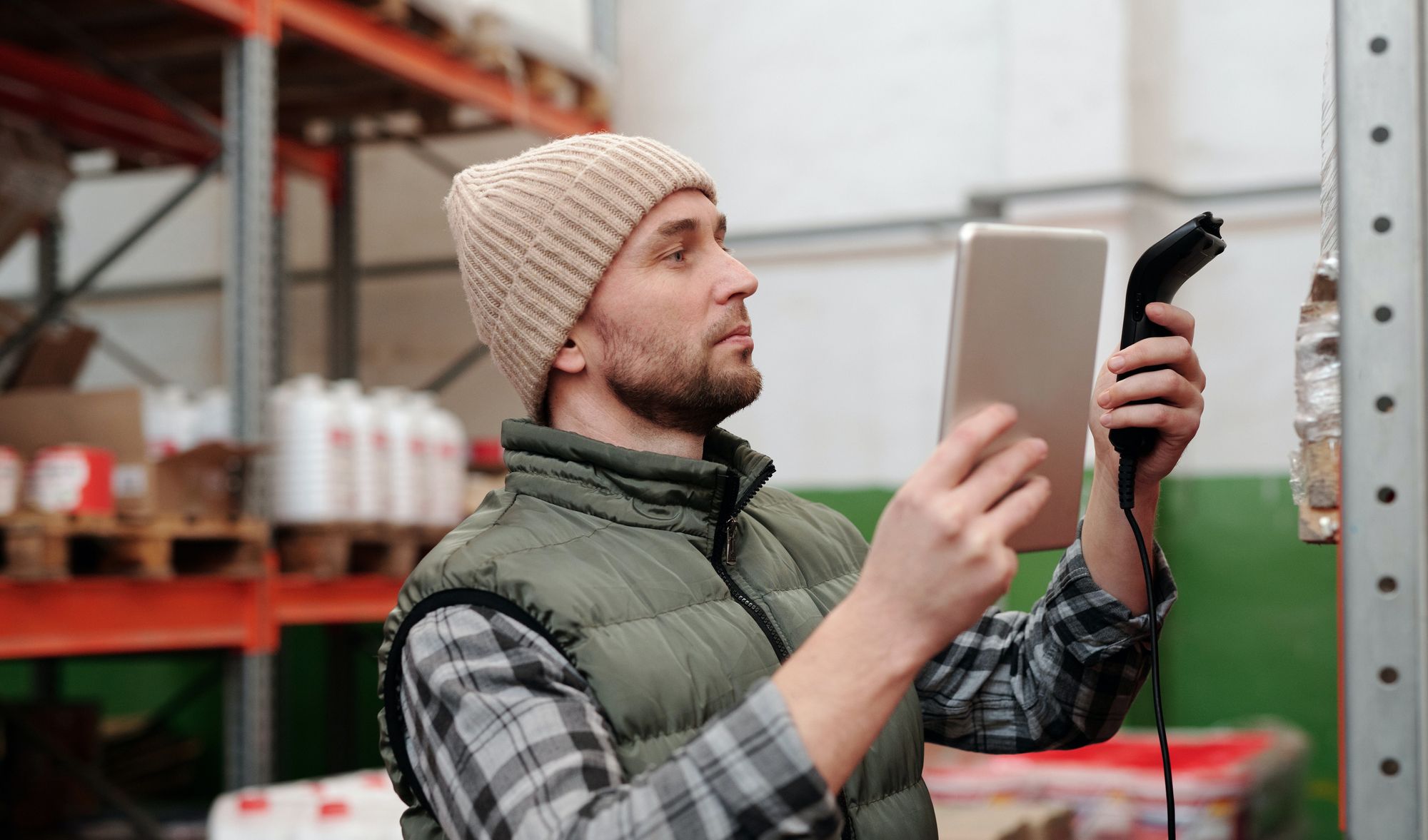