Have you ever wondered how much it truly costs to keep your inventory in check? Understanding inventory costs is crucial for managing your business’s finances and optimizing your supply chain. Inventory costs encompass various expenses, from ordering and holding to managing stockouts and shrinkage.
By grasping these costs, businesses can make informed decisions that enhance profitability and operational efficiency. Moreover, accurate cost management helps in better financial planning and resource allocation, ultimately contributing to long-term business success.
To efficiently manage these costs, many businesses turn to advanced solutions like Deskera ERP. Deskera offers a comprehensive suite of tools that streamline inventory management, reduce costs, and enhance overall efficiency. With features like real-time tracking and automated processes, Deskera ERP helps businesses keep their inventory costs in check while focusing on growth and profitability.
With the integration of ERP.AI, businesses can further elevate inventory control through intelligent automation, demand forecasting, and real-time cost analysis—ensuring smarter decisions with minimal manual intervention.
In this blog, we’ll explore the different types of inventory costs and provide real-world examples to help you better grasp their impact on your business.
What Are Inventory Costs?
Inventory costs represent the total expenses associated with acquiring, storing, and managing inventory throughout its lifecycle. These costs are crucial for businesses to understand as they directly impact profitability and operational efficiency.
Inventory costs include all expenses incurred from the point of acquiring inventory to the point where it is sold or otherwise disposed of. This encompasses various financial outlays such as purchasing costs, storage fees, handling expenses, and potential losses due to obsolescence or shrinkage.
Managing inventory costs effectively involves more than just tracking expenditures. It requires a strategic approach to balancing inventory levels to ensure that capital is not unnecessarily tied up in excess stock while also avoiding stock outs that could lead to lost sales.
For instance, businesses must consider the cost of procuring inventory, which includes the price paid to suppliers and any associated shipping or handling fees.
Additionally, the costs of storing inventory, such as warehousing and insurance, contribute to the overall cost structure. Inventory costs also encompass the risk of having unsellable or outdated products, which can lead to additional expenses related to markdowns or disposal.
In essence, inventory costs are a critical component of a company's financial management. They impact key metrics like the Cost of Goods Sold (COGS), which affects gross profit margins, and can influence decisions related to pricing, purchasing, and inventory management strategies. By understanding and managing these costs, businesses can optimize their inventory practices, improve cash flow, and enhance overall profitability.
6 Types of Inventory Costs
The 6 main types of inventory costs are:
1. Ordering Costs
Definition: Expenses incurred each time an order is placed to replenish inventory.
Components:
- Purchase Orders: Costs associated with creating and processing orders.
- Shipping Fees: Costs for transportation of goods from suppliers to the warehouse.
- Handling Charges: Expenses for receiving and inspecting the inventory upon arrival.
- Order Processing Costs: Administrative costs related to order fulfillment, including labor and technology expenses.
Example: A company that frequently orders small quantities might face high ordering costs due to repeated administrative tasks and shipping expenses.
2. Holding Costs
Definition: Costs associated with storing and maintaining unsold inventory.
Components:
- Warehousing Fees: Costs for renting or operating storage facilities.
- Insurance: Expenses for insuring the inventory against risks such as damage or theft.
- Inventory Obsolescence: Costs related to products that become outdated or unsellable over time.
- Spoilage: Costs incurred when inventory, particularly perishable goods, deteriorates before sale.
Example: A company storing seasonal items may incur high holding costs due to the need for climate-controlled storage and the risk of obsolescence.
3. Stockout Costs
Definition: Costs that arise when inventory levels are insufficient to meet customer demand.
Components:
- Lost Sales: Revenue lost due to the inability to fulfill customer orders.
- Customer Dissatisfaction: Potential loss of customer goodwill and future sales.
- Production Delays: Additional costs incurred from halted production or expedited shipping to meet urgent demands.
Example: A toy manufacturer might face stockout costs if it runs out of popular toys during the holiday season, leading to missed sales and unhappy customers.
4. Shrinkage Costs
Definition: Losses due to theft, damage, or inaccuracies in inventory records.
Components:
- Theft: Losses resulting from stolen inventory.
- Damage: Costs related to inventory that is damaged during storage or handling.
- Errors in Records: Financial losses from discrepancies between physical inventory and recorded inventory levels.
Example: A retail store may experience shrinkage costs due to products being stolen by customers or damaged during handling.
5. Carrying Costs
Definition: A broader term that often encompasses both holding costs and costs associated with managing inventory.
Components:
- Storage Costs: General expenses for storing inventory.
- Capital Costs: Opportunity costs of tying up capital in inventory rather than investing elsewhere.
Example: A business might incur carrying costs from having large amounts of unsold inventory occupying valuable warehouse space and tying up financial resources.
6. Spoilage Costs
Definition: Costs associated with inventory that becomes unsellable due to deterioration or expiration.
Components:
- Product Loss: The value of inventory that has spoiled or expired and cannot be sold.
- Waste Management: Costs related to disposing of spoiled or expired goods.
- Replacement Costs: Expenses incurred to replace spoiled inventory, which can include purchasing new stock and any associated ordering or handling costs.
Example: A grocery store might incur spoilage costs for perishable items like fresh produce that go bad before they can be sold. This not only results in a loss of the product's value but may also involve additional costs for waste disposal and replacement inventory.
Examples of Inventory Costs in Practice
Understanding how different types of inventory costs impact various businesses can help in developing strategies to optimize inventory management.
1. Example: Clothing Retailer
Scenario: A clothing retailer frequently orders small quantities of seasonal items to keep up with changing fashion trends.
Types of Costs:
- Ordering Costs: The retailer incurs high ordering costs due to frequent purchase orders, shipping fees, and handling expenses.
- Holding Costs: Storage costs are minimized by keeping inventory levels low, but the retailer might still face moderate holding costs related to managing and organizing stock.
- Stockout Costs: Running out of popular items during peak shopping seasons can lead to lost sales and customer dissatisfaction.
- Spoilage Costs: Though less of a concern, there could be some costs related to unsold items that may need to be discounted or discarded.
2. Example: Electronics Warehouse
Scenario: An electronics warehouse stores high-value items that require specific climate control and security measures.
Types of Costs:
- Holding Costs: Significant holding costs arise from maintaining climate-controlled storage facilities and ensuring adequate security to prevent theft.
- Stockout Costs: Low risk of stockouts if managed well, but a sudden surge in demand for a particular electronic item could lead to missed sales.
- Ordering Costs: Generally lower as the warehouse may order in bulk to reduce the frequency of orders.
- Spoilage Costs: Minimal spoilage costs due to the non-perishable nature of electronics, though obsolescence costs can be a concern as technology evolves rapidly.
3. Example: Toy Manufacturer
Scenario: A toy manufacturer needs to manage inventory effectively during the holiday season to meet high consumer demand.
Types of Costs:
- Stockout Costs: High risk of stockouts if inventory levels are not accurately forecasted, leading to lost sales and potential long-term damage to customer relationships.
- Holding Costs: Increased holding costs due to storing large quantities of inventory to ensure availability during peak times.
- Ordering Costs: Costs related to frequent ordering and restocking to keep up with demand fluctuations.
- Spoilage Costs: Low spoilage costs for toys, but inventory obsolescence can be a concern if toys become outdated quickly.
4. Example: Grocery Store
Scenario: A grocery store manages a variety of perishable and non-perishable goods.
Types of Costs:
- Spoilage Costs: High spoilage costs due to the perishable nature of many items like fresh produce and dairy products that may go bad before being sold.
- Ordering Costs: Regular ordering and restocking to ensure a fresh supply of perishable goods, contributing to ordering costs.
- Holding Costs: Holding costs are influenced by the need for adequate refrigeration and storage facilities.
- Stockout Costs: Some stockout costs due to occasional shortages of popular items, which can affect customer satisfaction and sales.
5. Example: Pharmaceutical Distributor
Scenario: A pharmaceutical distributor manages a wide range of medications with varying shelf lives.
Types of Costs:
- Holding Costs: High holding costs due to the need for specialized storage conditions and inventory management systems to track expiration dates.
- Spoilage Costs: Significant spoilage costs for medications approaching their expiration dates, leading to waste and additional disposal expenses.
- Stockout Costs: High stockout costs due to the critical nature of pharmaceuticals, where shortages can have serious consequences.
- Ordering Costs: Regular ordering and procurement costs to ensure an adequate supply of essential medications.
These examples illustrate how different types of inventory costs can impact various businesses. Effective management of these costs involves balancing ordering frequency, holding levels, and ensuring timely turnover to optimize profitability and operational efficiency.
How to Calculate Inventory Costs?
Understanding how to calculate different types of inventory costs is essential for managing inventory effectively and optimizing profitability.
1. Ordering Costs
Ordering costs are the expenses associated with placing and receiving orders for inventory. These include administrative costs, transportation costs, and any other costs incurred during the order process.
Formula: Total Ordering Cost = Number of Orders per Period × Cost per Order
- Number of Orders per Period: Calculated by dividing total demand by order quantity.
- Cost per Order: Includes processing, shipping, and receiving costs.
Example:
If you place 10 orders per year, and each order costs $50:
Total Ordering Cost = 10 × 50 = $500
2. Holding Costs
Holding costs, also known as carrying costs, are the costs incurred for storing and maintaining inventory over a period. These costs include warehousing, insurance, depreciation, and opportunity costs.
Formula: Holding Cost = Average Inventory Level × Holding Cost per Unit
- Average Inventory Level: Typically calculated as (Beginning Inventory + Ending Inventory) / 2.
- Holding Cost per Unit: Includes storage, insurance, and other associated costs.
Example:
If the average inventory level is 1,000 units, and the holding cost per unit is $2:
Holding Cost = 1,000 × 2 = $2,000
3. Stockout Costs
Stockout costs occur when inventory levels are insufficient to meet demand, resulting in lost sales or delayed orders.
Formula: Stockout Cost = Number of Stockouts × Cost per Stockout
- Number of Stockouts: Frequency of stockouts during the period.
- Cost per Stockout: Includes lost sales, expedited shipping costs, etc.
Example:
If a company experiences 5 stock outs per year, and the cost per stockout is $300:
Stockout Cost = 5 × 300 = $1,500
4. Shrinkage Costs
Shrinkage costs refer to losses due to theft, damage, or administrative errors that reduce inventory levels.
Formula: Shrinkage Cost = (Recorded Inventory - Actual Inventory) × Cost per Unit
- Recorded Inventory: Amount recorded in the system.
- Actual Inventory: Actual count after auditing.
- Cost per Unit: Cost to produce or purchase each unit.
Example:
If recorded inventory is 1,000 units, actual inventory is 950 units, and cost per unit is $10:
Shrinkage Cost = (1,000 - 950) × 10 = $500
5. Carrying Costs
Carrying costs are the total of all expenses associated with holding inventory, including holding costs, shrinkage costs, and capital costs.
Formula: Carrying Cost = Holding Cost + Shrinkage Cost + Capital Cost
- Capital Cost: Opportunity cost of capital tied up in inventory.
Example:
If holding cost is $2,000, shrinkage cost is $500, and capital cost is $300:
Carrying Cost = 2,000 + 500 + 300 = $2,800
6. Spoilage Costs
Spoilage costs refer to the loss incurred when inventory becomes obsolete, expired, or otherwise unusable.
Formula: Spoilage Cost = Quantity of Spoiled Inventory × Cost per Unit
- Quantity of Spoiled Inventory: Amount of unusable inventory.
- Cost per Unit: Cost to produce or purchase each unit.
Example:
If 200 units spoil, and each unit costs $5:
Spoilage Cost = 200 × 5 = $1,000
Accurately calculating these inventory costs is vital for effective inventory management.
By understanding and controlling these costs, businesses can make more informed decisions, optimize inventory levels, and improve profitability.
Regularly reviewing these costs and their impact on your business will also help in identifying areas for cost reduction and efficiency improvement.
Key Factors Influencing Your Inventory Costs
Several factors influence the total cost of managing and maintaining inventory. Understanding these factors can help businesses optimize their inventory management processes and reduce unnecessary expenses.
Here are the key factors that affect your inventory costs:
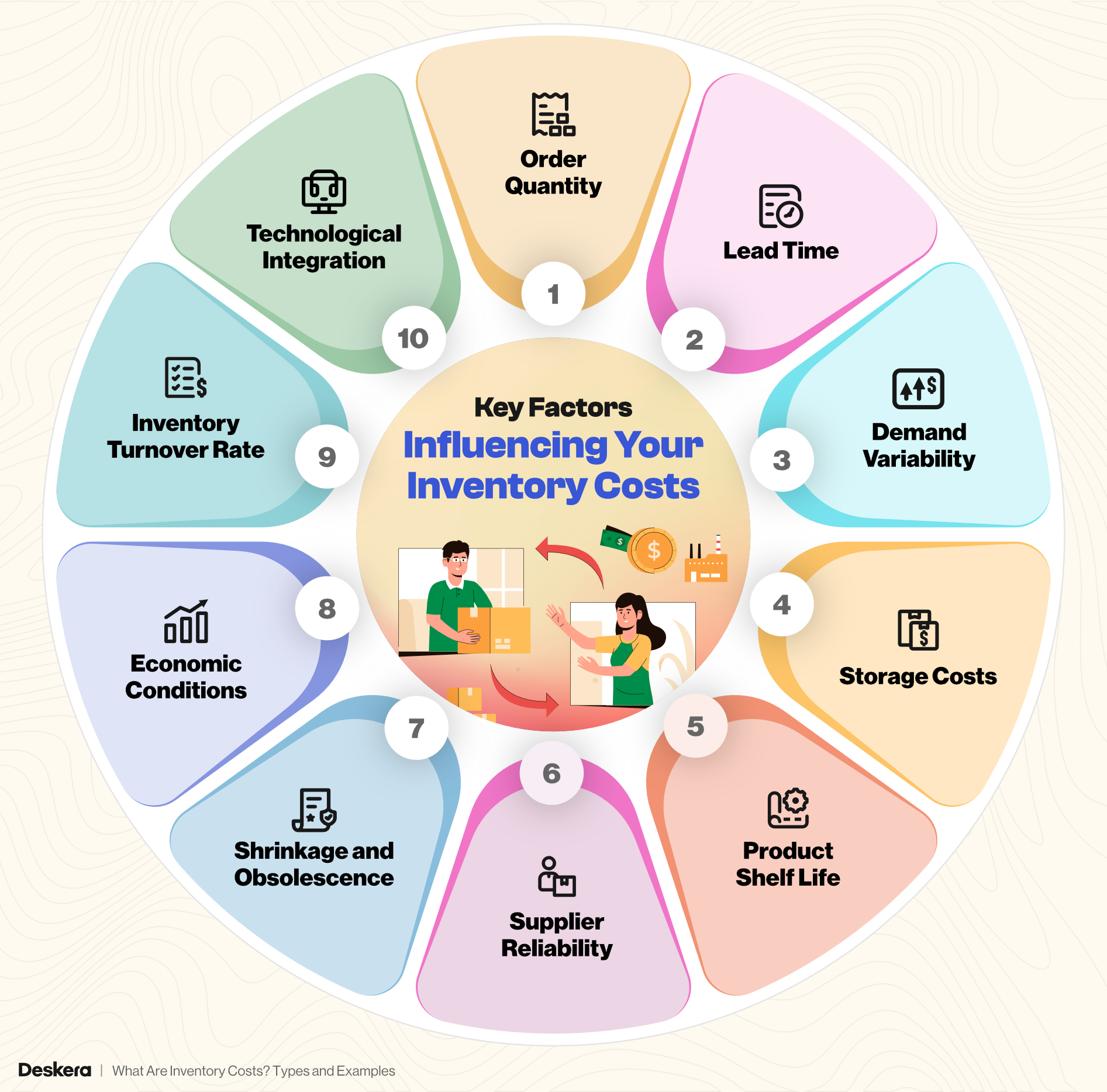
1. Order Quantity
The size of each order directly impacts inventory costs. Ordering in large quantities can reduce ordering costs due to economies of scale but may increase holding costs if excess inventory is stored. Conversely, smaller orders may reduce holding costs but increase ordering frequency and costs.
2. Lead Time
Lead time refers to the time it takes for an order to be fulfilled, from placing the order to receiving the inventory. Longer lead times often require businesses to hold more inventory as a buffer against stockouts, increasing holding costs. Shorter lead times can reduce the need for high safety stock levels, thus lowering inventory costs.
3. Demand Variability
Fluctuations in customer demand can significantly affect inventory costs. Unpredictable demand may lead to overstocking or stockouts, both of which are costly. Businesses with stable and predictable demand can manage inventory costs more effectively by aligning inventory levels closely with expected sales.
4. Storage Costs
The cost of storing inventory, including warehouse rent, utilities, and insurance, can substantially impact inventory costs. The more inventory a business holds, the higher the storage costs. Efficient use of storage space and optimization of inventory levels are crucial to managing these costs.
5. Product Shelf Life
Perishable or time-sensitive products add to inventory costs due to the need for special storage conditions and the risk of spoilage. Businesses dealing with such products must carefully manage inventory turnover to minimize losses and avoid excessive spoilage costs.
6. Supplier Reliability
The reliability of suppliers affects inventory costs. Inconsistent suppliers may force businesses to hold more safety stock to guard against delays, increasing holding costs. On the other hand, reliable suppliers can help reduce the need for high inventory levels, lowering overall costs.
7. Shrinkage and Obsolescence
Shrinkage due to theft, damage, or administrative errors, as well as obsolescence of products, contributes to inventory costs. Businesses must implement strong inventory controls and regularly review inventory to minimize these losses.
8. Economic Conditions
External economic factors, such as inflation, interest rates, and market demand, can influence inventory costs. For example, rising inflation can increase the cost of goods, which in turn raises the cost of holding and purchasing inventory.
9. Inventory Turnover Rate
The rate at which inventory is sold and replaced affects inventory costs. High turnover rates usually mean lower holding costs and fresher stock, while low turnover rates can lead to increased holding costs and higher risks of obsolescence and spoilage.
10. Technological Integration
The use of technology in inventory management, such as automated systems, barcoding, and real-time tracking, can reduce errors, improve efficiency, and lower inventory costs. Investing in advanced inventory management software can lead to long-term cost savings by optimizing inventory levels and reducing manual errors.
Understanding and managing these factors can help businesses effectively control inventory costs, leading to improved profitability and operational efficiency.
Why Are Inventory Costs Important?
Inventory costs are crucial for several reasons that directly impact the overall success and profitability of a business. Here’s why inventory costs are important:
1. Profitability
Inventory costs significantly affect a company’s profit margins. High inventory costs can eat into profits, while effectively managing these costs can improve the bottom line. Understanding and controlling inventory costs allows businesses to price their products more competitively while maintaining healthy profit margins.
2. Cash Flow Management
Effective inventory cost management ensures better cash flow. Inventory ties up capital, and high inventory costs can lead to cash flow problems. By optimizing inventory levels and reducing unnecessary costs, businesses can free up capital for other critical operations.
3. Pricing Strategy
Accurate knowledge of inventory costs is essential for setting the right pricing strategy. Businesses need to ensure that the prices of their products cover not only the cost of goods sold but also the associated inventory costs. This helps in maintaining competitiveness in the market while ensuring profitability.
4. Operational Efficiency
Understanding inventory costs is vital for operational efficiency. By tracking and analyzing these costs, businesses can identify inefficiencies in their supply chain, storage, and inventory management processes. This can lead to improved operational practices, reduced waste, and better resource allocation.
5. Risk Management
High inventory costs often indicate risks such as overstocking, obsolescence, or shrinkage. By monitoring and controlling these costs, businesses can mitigate risks associated with holding excessive or outdated inventory, leading to more agile and responsive operations.
6. Customer Satisfaction
Proper management of inventory costs ensures that businesses can meet customer demand without overstocking. This balance helps avoid stockouts and delays, which can lead to lost sales and dissatisfied customers. Efficient inventory cost management contributes to maintaining high levels of customer satisfaction.
7. Strategic Decision-Making
Inventory costs provide valuable insights for strategic decision-making. By understanding these costs, businesses can make informed decisions about product development, market expansion, and investment in new technologies or processes that can further optimize inventory management.
In summary, inventory costs are a key factor in determining a business's financial health, operational efficiency, and customer satisfaction. Managing these costs effectively is essential for maintaining competitiveness and ensuring long-term success.
How Inventory Costs Affect Your Business’s Bottom Line
Inventory costs play a crucial role in determining a company's financial health and operational efficiency. Understanding their impact helps businesses make strategic decisions to enhance profitability and performance.
Profit Margins
- Direct Influence: High inventory costs, including ordering, holding, and spoilage costs, directly reduce profit margins. Increased expenses lead to a higher Cost of Goods Sold (COGS), which can erode overall profitability.
- Example: If a company faces high holding costs due to excessive inventory, these costs eat into the profit margins of each sale, reducing the overall profit.
Cash Flow Management
- Capital Allocation: Excessive inventory ties up capital that could be used for other business needs. Managing inventory costs effectively ensures that capital is available for growth opportunities and operational needs.
- Example: A retailer with high holding costs might find its cash flow constrained, limiting its ability to invest in marketing or expansion.
Operational Efficiency
- Cost Optimization: Efficient management of inventory costs improves operational efficiency by minimizing waste, reducing unnecessary stock levels, and optimizing ordering processes. This leads to smoother operations and cost savings.
- Example: Implementing inventory management systems to reduce stockouts and excess inventory can streamline operations and lower operational costs.
Customer Satisfaction
- Service Levels: Effective inventory management helps maintain optimal stock levels, ensuring that customer demand is met promptly. Poor inventory control can lead to stockouts or excess inventory, affecting customer satisfaction and loyalty.
- Example: A business that consistently experiences stock outs may lose customers to competitors, impacting long-term revenue and customer loyalty.
Financial Reporting
- Impact on Statements: Inventory costs affect financial statements, including the income statement and balance sheet. Accurate inventory valuation ensures reliable financial reporting and aids in strategic financial planning.
- Example: High spoilage costs can impact the valuation of inventory on the balance sheet and affect the reported profit on the income statement.
Strategic Decision-Making
- Informed Choices: Understanding inventory costs enables better decision-making regarding pricing strategies, inventory policies, and supplier negotiations. This can lead to more effective and strategic business planning.
- Example: A company might negotiate better terms with suppliers or adjust pricing strategies based on an analysis of inventory costs to improve profitability.
Effectively managing inventory costs is essential for optimizing financial performance, ensuring efficient operations, and enhancing customer satisfaction. By addressing these costs, businesses can improve their bottom line and support long-term success.
10 Common Mistakes to Avoid When Managing Inventory Costs
Avoiding common pitfalls in inventory management can help businesses control costs, improve efficiency, and protect profit margins. Here are some critical mistakes to steer clear of:
1. Overestimating Demand
- Mistake: Ordering more inventory than needed due to inaccurate demand forecasting.
- Impact: Leads to excessive holding costs, increased risk of obsolescence, and potential spoilage, especially for perishable goods.
- Solution: Utilize accurate forecasting tools and regularly review historical sales data to better predict demand.
2. Neglecting Inventory Turnover
- Mistake: Failing to monitor and maintain an optimal inventory turnover ratio.
- Impact: Low turnover can result in higher holding costs and increased risk of obsolescence, while high turnover might lead to stockouts and missed sales opportunities.
- Solution: Strive for a balanced turnover rate by regularly analyzing sales trends and adjusting inventory levels accordingly.
3. Ignoring the Cost of Stockouts
- Mistake: Underestimating the cost of running out of stock.
- Impact: Results in lost sales, damaged customer relationships, and potential long-term revenue loss.
- Solution: Implement safety stock strategies and monitor inventory levels to minimize the risk of stockouts.
4. Overlooking Spoilage Costs
- Mistake: Not accounting for the costs associated with inventory spoilage or obsolescence.
- Impact: Spoiled or outdated inventory leads to wasted resources and direct financial losses.
- Solution: Regularly rotate stock, implement first-in, first-out (FIFO) practices, and closely monitor the shelf life of perishable items.
5. Failing to Automate Inventory Management
- Mistake: Relying on manual processes for inventory management.
- Impact: Manual tracking is prone to errors, leading to inaccurate inventory records, mismanagement, and higher operational costs.
- Solution: Invest in inventory management software that automates tracking, forecasting, and ordering processes to improve accuracy and efficiency.
6. Inadequate Supplier Management
- Mistake: Not optimizing supplier relationships and contracts.
- Impact: Poor supplier performance can lead to delays, higher ordering costs, and inconsistent inventory levels.
- Solution: Regularly review and negotiate supplier contracts, and consider diversifying suppliers to mitigate risks.
7. Underestimating the Importance of Accurate Data
- Mistake: Failing to maintain accurate and up-to-date inventory data.
- Impact: Inaccurate data can lead to poor decision-making, including overstocking or understocking, which increases costs and reduces profitability.
- Solution: Implement robust data management practices and regularly audit inventory records to ensure accuracy.
8. Not Incorporating Inventory Costs into Pricing Strategies
- Mistake: Overlooking inventory costs when setting product prices.
- Impact: Failure to factor in inventory-related expenses can result in pricing that doesn't cover costs, thereby reducing profit margins.
- Solution: Integrate inventory costs into pricing strategies to ensure products are priced to reflect true costs and desired profit margins.
9. Ignoring the Impact of External Factors
- Mistake: Not considering external factors such as market trends, seasonality, or economic changes when managing inventory.
- Impact: Can lead to overstocking or stockouts, resulting in increased costs or lost sales.
- Solution: Stay informed about market conditions and adjust inventory strategies accordingly to mitigate risks and capitalize on opportunities.
10. Failing to Regularly Review and Adjust Inventory Policies
- Mistake: Sticking to outdated inventory policies without regular review.
- Impact: Outdated policies can lead to inefficiencies, increased costs, and reduced responsiveness to market changes.
- Solution: Regularly review and update inventory management policies to align with current business goals and market conditions.
Avoiding these common mistakes in managing inventory costs can help businesses maintain a healthy bottom line, ensure operational efficiency, and support long-term growth.
Effective Strategies to Reduce Inventory Costs
Managing inventory costs efficiently is essential for optimizing profitability and maintaining smooth operations. Here are key strategies to help reduce inventory costs:
1. Improve Demand Forecasting
- Strategy: Use advanced analytics and forecasting tools to predict demand accurately.
- Benefit: Reduces the risk of overstocking or understocking, leading to lower holding costs and minimized stockout risks.
- Implementation: Analyze historical sales data, market trends, and seasonality to refine forecasting accuracy.
2. Implement Just-in-Time (JIT) Inventory
- Strategy: Adopt a Just-in-Time inventory system to receive goods only when needed for production or sales.
- Benefit: Minimizes holding costs by reducing the amount of inventory stored on-site.
- Implementation: Work closely with suppliers to ensure timely deliveries and maintain tight control over production schedules.
3. Optimize Order Quantity with EOQ
- Strategy: Use the Economic Order Quantity (EOQ) model to determine the optimal order size that minimizes total inventory costs.
- Benefit: Balances ordering and holding costs, ensuring cost-effective inventory levels.
- Implementation: Calculate EOQ based on factors like demand rate, ordering cost, and holding cost, and adjust as needed.
4. Enhance Supplier Relationships
- Strategy: Build strong relationships with suppliers to negotiate better terms, such as bulk discounts or flexible delivery schedules.
- Benefit: Reduces ordering costs and ensures a reliable supply chain, which can lower overall inventory costs.
- Implementation: Regularly review supplier performance, negotiate contracts, and consider strategic partnerships for long-term benefits.
5. Implement ABC Analysis
- Strategy: Use ABC analysis to categorize inventory based on value and turnover rates.
- Benefit: Focuses attention on high-value items (A items) that require tighter control, while minimizing effort on lower-value items (C items).
- Implementation: Classify inventory into A, B, and C categories and apply differentiated management strategies for each group.
6. Reduce Lead Times
- Strategy: Work to shorten lead times by improving internal processes or collaborating with suppliers.
- Benefit: Shorter lead times reduce the need for large safety stock levels, thereby lowering holding costs.
- Implementation: Streamline procurement processes, automate order management, and maintain open communication with suppliers.
7. Utilize Technology and Automation
- Strategy: Implement inventory management software and automation tools to improve tracking, forecasting, and replenishment.
- Benefit: Enhances accuracy, reduces human error, and optimizes inventory levels, leading to lower costs.
- Implementation: Choose software that integrates with existing systems and provides real-time data on inventory levels, demand, and orders.
8. Adopt Lean Inventory Practices
- Strategy: Apply lean principles to inventory management, focusing on waste reduction and efficiency.
- Benefit: Minimizes excess inventory, reduces holding costs, and improves cash flow.
- Implementation: Identify and eliminate waste in inventory processes, such as overproduction or unnecessary storage, and continuously seek improvement.
9. Regularly Review and Adjust Safety Stock Levels
- Strategy: Periodically review safety stock levels to ensure they are aligned with current demand and supply variability.
- Benefit: Prevents overstocking and reduces holding costs without compromising service levels.
- Implementation: Use historical data and forecast accuracy to adjust safety stock levels, considering changes in demand patterns or lead times.
10. Implement Consignment Inventory
- Strategy: Negotiate consignment inventory agreements with suppliers, where inventory is owned by the supplier until sold.
- Benefit: Reduces holding costs and frees up working capital, as the business only pays for inventory once it is sold.
- Implementation: Work with key suppliers to set up consignment arrangements and define clear terms for inventory ownership and payment.
11. Conduct Regular Inventory Audits
- Strategy: Perform regular physical inventory audits to ensure accuracy in inventory records.
- Benefit: Helps identify discrepancies, prevent theft, and reduce costs associated with lost or misplaced inventory.
- Implementation: Schedule periodic audits, use cycle counting methods, and reconcile physical counts with inventory management system records.
12. Leverage Drop Shipping
- Strategy: Use drop shipping for certain products, where suppliers ship directly to customers without holding inventory.
- Benefit: Eliminates holding costs and reduces the need for warehousing, improving cash flow.
- Implementation: Partner with reliable drop shipping suppliers and integrate their systems with your sales platform for seamless order fulfillment.
By implementing these strategies, businesses can effectively reduce inventory costs, improve operational efficiency, and enhance their overall financial performance.
How AI Optimizes Cost Management
With real-time data analysis, AI enables companies to track, categorize, and forecast expenses more accurately than ever before. In the context of inventory, AI helps minimize holding, shortage, and carrying costs by optimizing stock levels and dynamically adjusting reorder points based on demand patterns.
By relying on these AI capabilities, companies gain actionable insights, streamline operations, and ensure smarter financial planning, ultimately leading to improved profitability and long-term cost efficiency.
How Deskera ERP Can Help You Optimize Inventory Costs
Deskera ERP offers a comprehensive suite of tools designed to help businesses manage and reduce their inventory costs effectively.
Here's how Deskera ERP can assist:
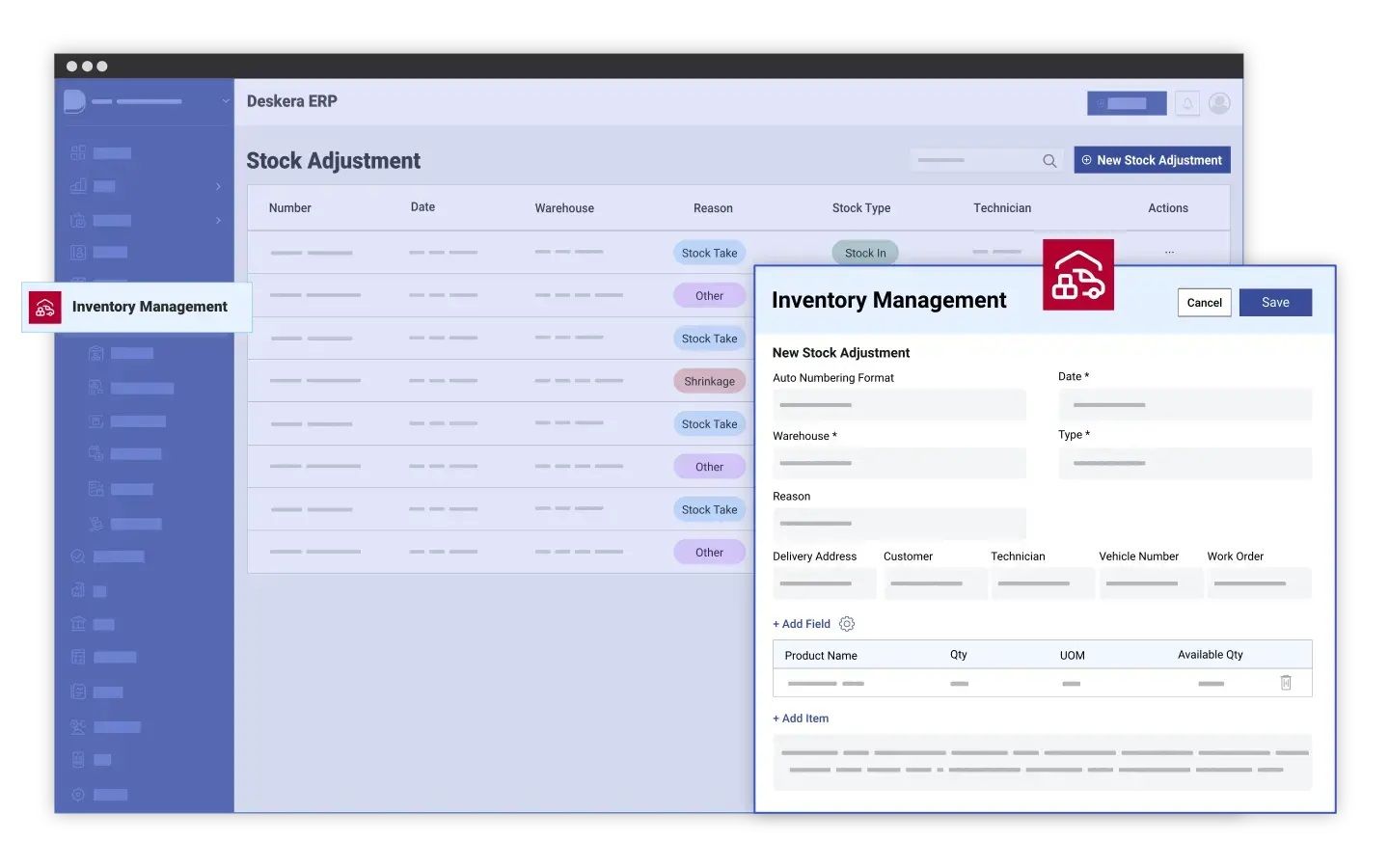
Automated Inventory Management
Deskera ERP automates key inventory processes, including tracking stock levels, reordering, and managing inventory across multiple locations. This automation reduces manual errors, prevents overstocking, and ensures optimal inventory levels, directly impacting inventory costs by minimizing excess stock and associated holding costs.
Real-Time Inventory Tracking
With real-time tracking, Deskera ERP provides up-to-date insights into your inventory status. This allows businesses to respond quickly to changes in demand, reducing the risk of stockouts or overstocking, both of which can significantly inflate inventory costs.
Demand Forecasting
Deskera ERP includes advanced demand forecasting tools that analyze historical sales data and market trends to predict future demand. Accurate forecasting helps businesses maintain the right inventory levels, reducing the need for excess safety stock and lowering holding costs.
Efficient Order Management
The platform’s order management features streamline the entire ordering process, from purchase order creation to supplier management. By optimizing order quantities and timing, Deskera ERP helps reduce ordering costs and avoid the high costs associated with rush orders or stockouts.
Inventory Valuation and Reporting
Deskera ERP provides detailed inventory valuation and reporting features, helping businesses accurately assess their inventory’s value over time. These insights are crucial for identifying slow-moving or obsolete stock, allowing businesses to take action to minimize carrying costs and reduce waste.
Integrated Accounting and Inventory
The integration of inventory management with accounting in Deskera ERP ensures that all inventory costs are accurately recorded and reflected in financial statements. This integration allows for better financial planning, cost analysis, and overall business transparency, enabling businesses to make informed decisions that can reduce inventory-related expenses.
Reduction of Shrinkage and Spoilage
Deskera ERP’s robust tracking and reporting capabilities help reduce shrinkage due to theft, damage, or errors, and manage spoilage more effectively. By providing clear visibility into inventory movements and expiration dates, the system helps businesses take timely actions to minimize these costs.
Mobile Accessibility
Deskera ERP’s mobile accessibility allows businesses to manage inventory on the go, ensuring that decision-makers have access to critical inventory data anytime, anywhere. This flexibility enhances the ability to respond quickly to inventory needs, further helping to control costs.
By leveraging Deskera ERP's features, businesses can optimize their inventory management processes, leading to significant reductions in inventory costs and overall improvement in operational efficiency.
Key Takeaways
Understanding Inventory Costs
Inventory costs encompass all expenses associated with storing, managing, and handling inventory. Key components include ordering costs, holding costs, stockout costs, shrinkage costs, carrying costs, and spoilage costs.
Types of Inventory Costs
- Ordering Costs: Expenses related to placing and receiving inventory orders.
- Holding Costs: Costs incurred from storing and maintaining inventory.
- Stockout Costs: Costs resulting from insufficient inventory to meet demand.
- Shrinkage Costs: Losses due to theft, damage, or errors.
- Carrying Costs: Total costs associated with holding inventory, including holding, shrinkage, and capital costs.
- Spoilage Costs: Costs related to inventory becoming obsolete or unusable.
Impact on Business
Inventory costs directly affect a business’s profitability, cash flow, pricing strategy, operational efficiency, and risk management. Proper management of these costs is essential for maintaining a healthy financial position and competitive edge.
Factors Influencing Inventory Costs
Factors such as order quantity, lead time, demand variability, storage costs, product shelf life, supplier reliability, shrinkage and obsolescence, economic conditions, inventory turnover rate, and technological integration all play a role in determining inventory costs.
Strategies for Reduction
Effective inventory cost management strategies include optimizing order quantities, improving demand forecasting, reducing holding and storage costs, minimizing shrinkage and spoilage, and leveraging technology for better inventory control.
Role of Deskera ERP
Deskera ERP provides a robust solution for managing and optimizing inventory costs through its comprehensive suite of tools. By automating inventory processes, offering real-time tracking, and delivering advanced demand forecasting, Deskera ERP helps businesses maintain optimal inventory levels and reduce unnecessary expenses.
Related Articles
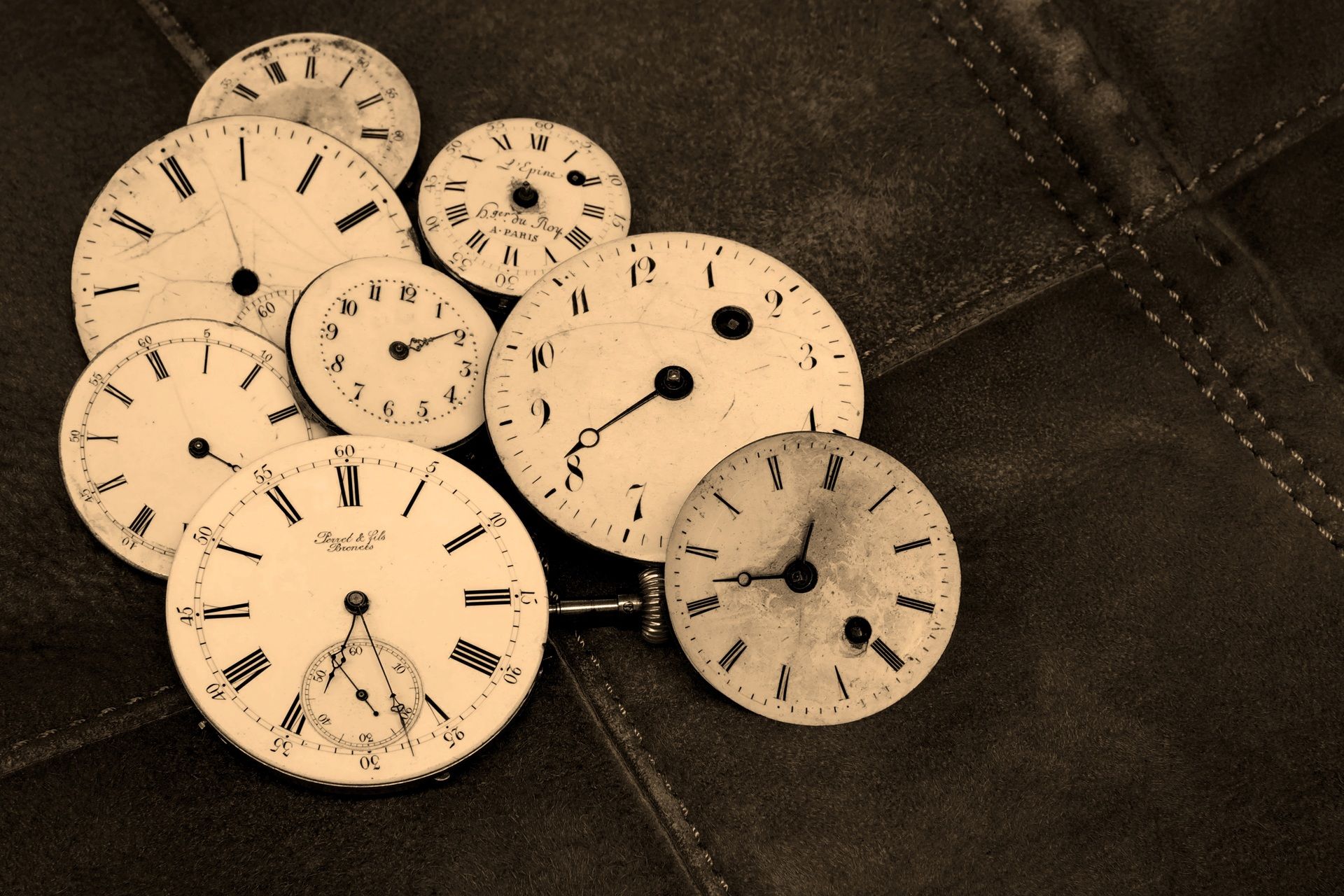
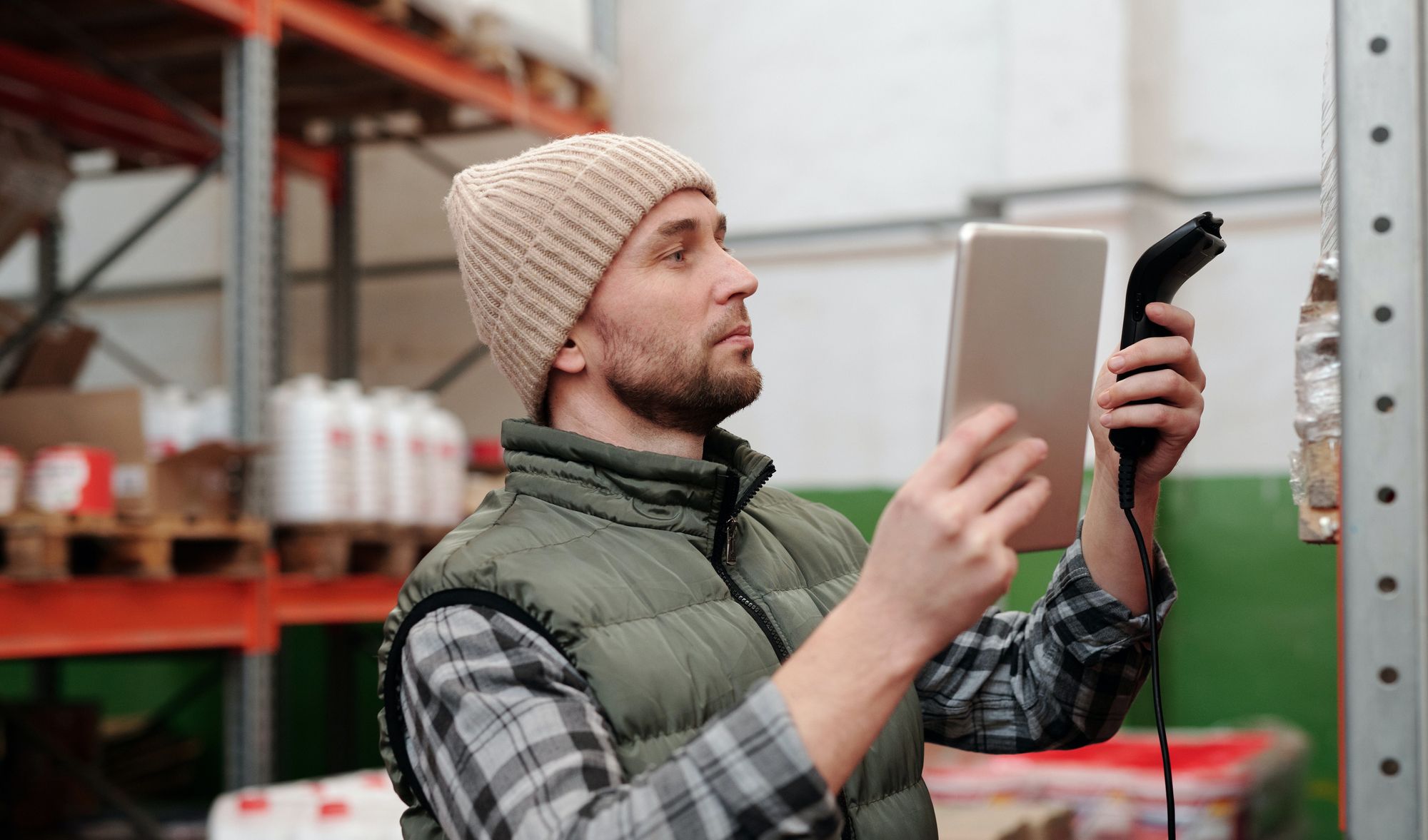
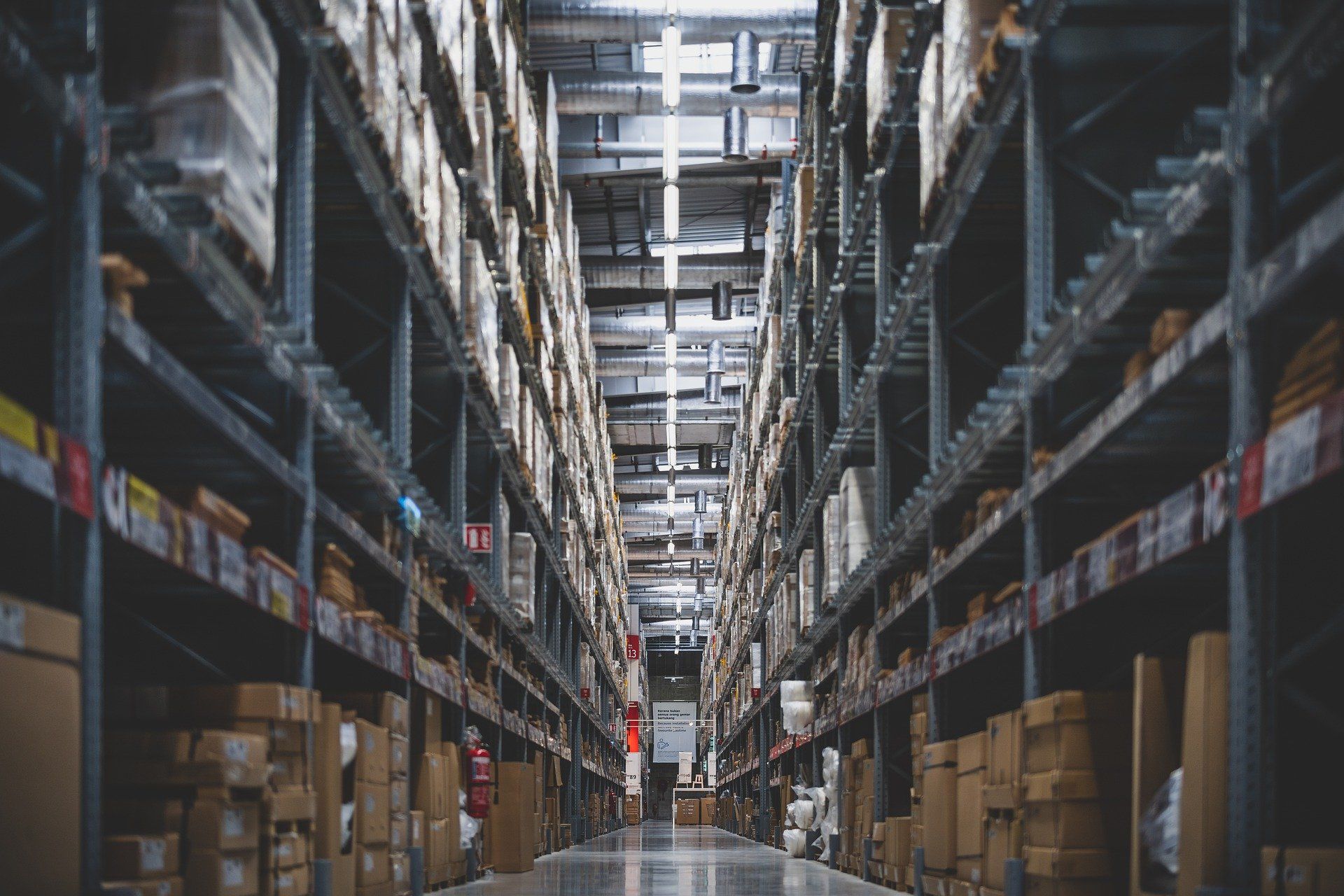
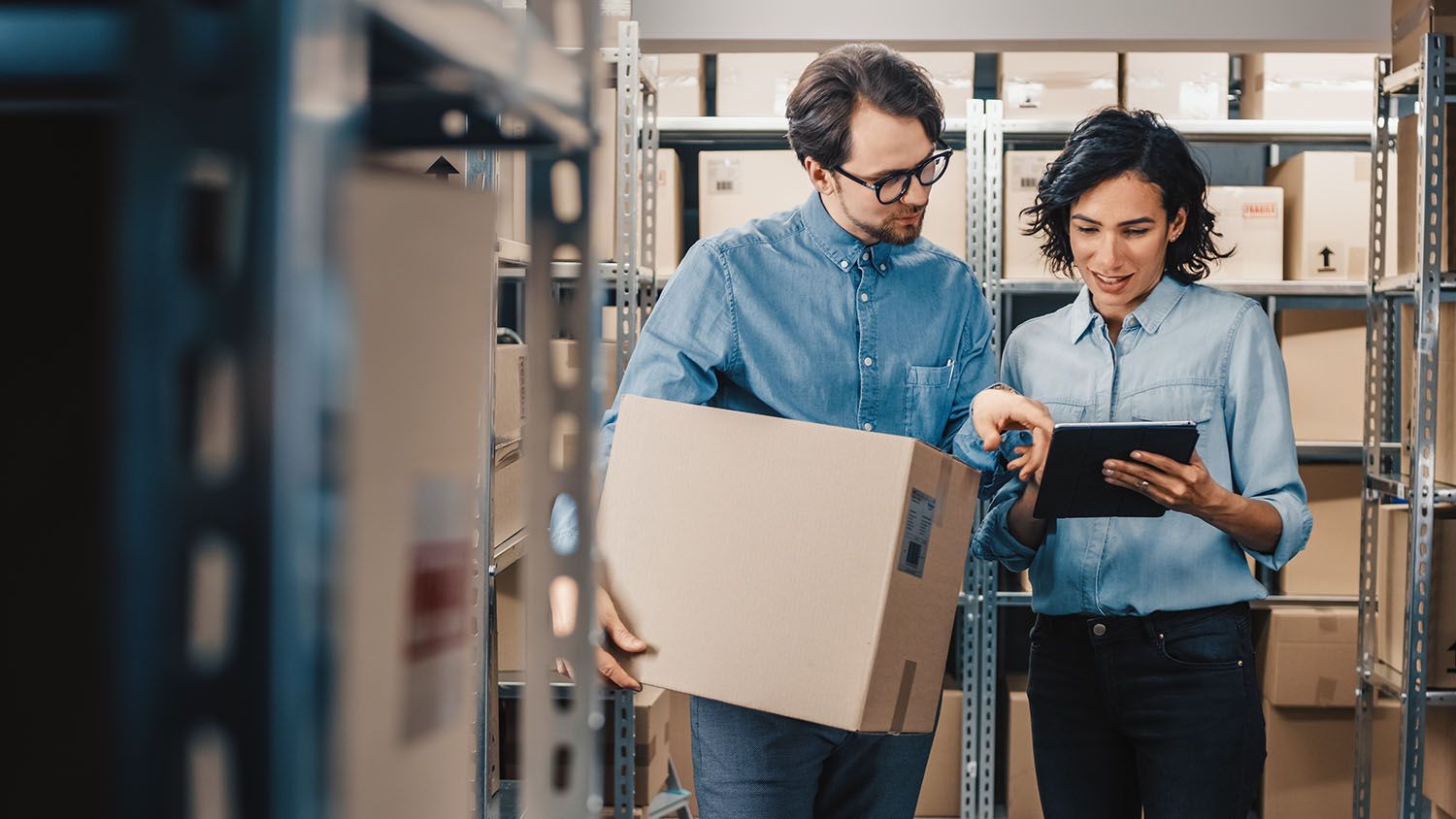
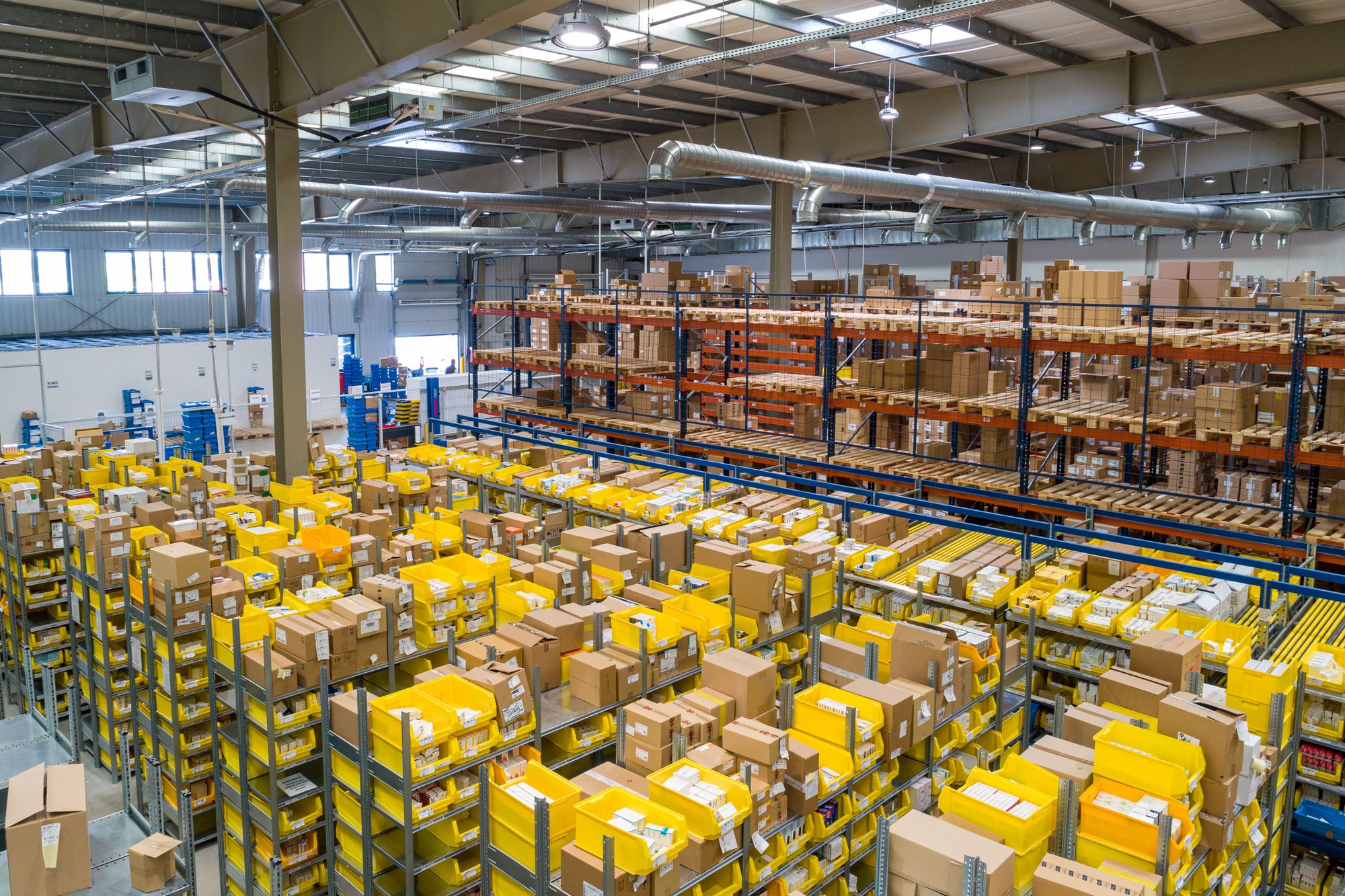
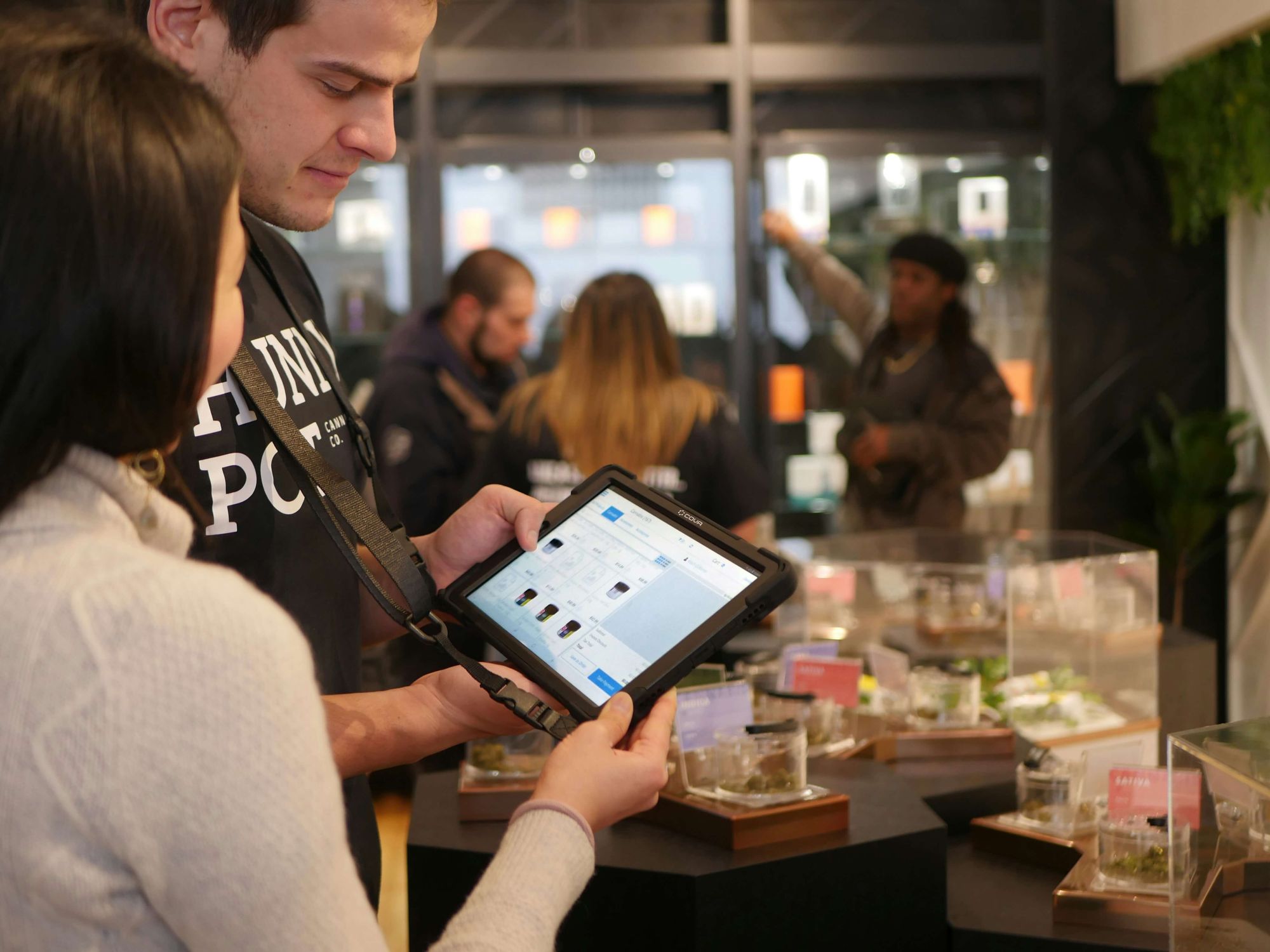