The majority of businesses compete to find the cheapest raw materials and reduce operational expenses as much as they can. It is challenging since it calls for foresight into supply chain behavior. An inventory management operation cannot succeed without carefully acquiring and utilizing the raw materials.
Management of raw materials is where it all begins. Your raw materials inventory needs to be efficiently handled if you want to operate profitably. This is one criterion that enables you to assess the efficacy of your entire inventory management system.
Businesses understand that raw materials play a significant role in the general performance of their company. This is due to the fact that raw materials are listed on the balance sheet as a current asset. It significantly influences cash flow statements and financial results in the end.
This article has all that you need to know about maintaining your raw material inventory.
Here is all that follows:
- What is Raw Materials Inventory?
- How to Calculate Raw Materials Inventory Value?
- Tips to Manage Raw Materials Inventory
- What is Raw Material Inventory Turnover and How to Calculate it?
- Calculating the Raw Material Value with Weighted Average Costing?
- Example of Raw Material Inventory Turnover
- How Much Effort needs to go into Raw Materials Inventory Management?
- Overcoming Challenges with Raw Material Data Management
- Benefits of Raw Material Inventory Management Software Integrated with ERP
- Importance of Accurate Inventory Tracking of Raw Materials
- Raw Materials Inventory FAQs
- Conclusion
- How can Deskera Help You?
- Key Takeaways
- Related Articles
What is Raw Materials Inventory?
The total cost of goods in a company's inventory that has not been used for manufacturing or producing finished goods is known as raw materials inventory.
The goods which are now in stock and available for usage, are referred to as pre-production inventory. Due to their role in a manufacturer's overall product inventory, raw materials are frequently listed as a current asset in financial records (like a balance sheet) by businesses and organizations.
In addition to manufacturing duties, manufacturers have extensive responsibilities, which might leave them feeling overwhelmed. This holds true considering all the processes the products go through to reach completion. There are a number of operations to take care of from labor to supply chain to factory operations.
Business owners frequently buy their supplies through wholesale directories or internet markets. Ensure the companies you buy from have an active wholesale license to avoid being taken advantage of.
Therefore, it is vital to learn about the laws and regulations you must abide by to void any legal hassles at a later stage. This scenario requires you to carefully read the wholesale purchase agreement's contents to comprehend the laws and policies.
Types of Raw Material with Examples
You can categorize raw materials into two subcategories which are as follows:
Direct Raw Materials: The raw materials that are directly used up or are involved in the production process are called direct raw materials.
Direct raw materials, like wood for a chair, are substances that businesses employ directly in the production of completed goods. In order to provide more thorough expense reporting on the costs of goods supplied, manufacturing companies must also go above and beyond what non-manufacturing companies must do.
This category of raw materials is frequently seen as variable expenses because the quantity utilized depends on the output amounts.
Indirect Raw Materials: The raw materials that are not directly involved in the manufacturing of the final product but ultimately get used up in the process are terms of indirect raw materials.
Despite being heavily used during production, indirect raw materials are not found in the completed product. Indirect raw materials will be treated as long-term assets. Numerous categories, such as selling, general, and administrative also known as SG&A can be used to categorize them as long-term assets. The same goes for property, plant, and equipment or PP&E.
The depreciation schedule that long-term assets typically follow enables them to be expensed over time and matched with the revenue to which they contribute. The depreciation timeframe for indirect raw materials will normally be quicker than for other long-term assets like a structure, which are expensed over time.
Accounting of Raw Materials Inventory
In the initial recording of raw materials, a debit is made to the raw materials inventory account while credit is made to accounts payable. The accounting treatment of raw materials depends on whether they were consumed directly or indirectly.
- Direct materials: A debit should be applied to the work-in-process inventory account and credit should be applied to the raw materials inventory asset account. If the production process is short, you can debit finished goods inventory instead of work-in-process.
- Indirect materials: A debit is made to the factory overhead account and a credit is made to the raw materials inventory asset account. The ending balance in the overhead account is allocated to the cost of goods sold and ending inventory at the end of each month.
How To Calculate Raw Materials Inventory Value?
The calculation of raw materials varies depending on the material's kind and nature, such as direct and indirect materials. Typically, raw materials are recorded with a credit treatment in the liabilities account for the account payable and a debit treatment in the asset account for the inventory.
Direct materials are viewed as a credit to the asset account for raw materials and a debit in the work-in-progress inventory. The indirect materials are reported as a credit to the account for raw materials and as a debit to the factory overhead account.
Take the starting balance of the raw materials into account in order to calculate the end raw material balance. The raw materials used for either work-in-progress or finished goods inventory should then be subtracted. Add any raw material purchases made throughout the accounting period to reach the ending balance.
For calculating raw materials inventory, you will have to know the following elements as well:
- Beginning Raw Materials Inventory
- Raw Materials Purchased
- Cost of Goods Sold (COGS)
This is the same as calculating the value of finished goods inventory. Here, we must calculate the value of Beginning raw materials
Beginning Raw Materials Inventory Formula:
This will lead us to calculate the raw materials inventory. While finding the ending raw materials inventory is something that must be calculated, it is the beginning raw materials inventory for the new accounting cycle.
Tips to Manage Raw Materials Inventory
Your supply chain managers could face obstacles such as overstocking and underbuying without the right tools and inventory plans. Furthermore, this could result in excessive and unreasonable expenses. They can utilize some tips and tricks to avoid all this.
This section focuses on the tips you can use for efficient raw material inventory management. Let’s check them here:
Utilize A Management System For Raw Material Inventories (MRP)
The science of figuring out the kinds and amounts of raw inventory required for production is known as material planning. Safety stock, buffer stock, and anticipation stock depots are required for both direct and indirect raw materials.
The software that helps you manage and monitor your business units can prove to be extremely useful. You can choose from a number of platforms based on your company’s requirements. While there may be a small difference in what each company offers, the unique advantages each of them provide help improve precision and regularity.
Also, you can achieve automation in most of your raw material inventory computations.
Platforms for material requirements planning or MRP help you assess supply chain complexity, lead times, modes of production, and historical consumption data. While an MRP is different from an ERP, the usefulness of both systems can not be undermined in any manner.
So, it is important that you understand the difference between the two and utilize them in the most profitable way. The following images shall give you a rough idea of the fundamental differences between them:
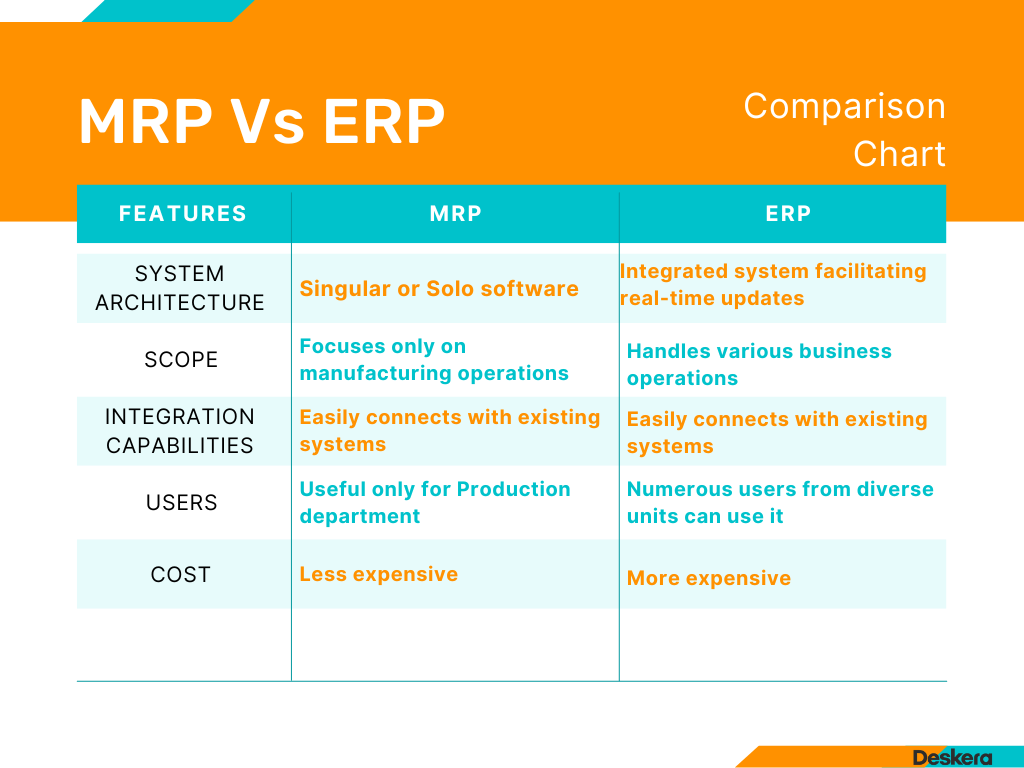
The systems can help compare future projections in order to recommend the ideal stock levels and buying cycles. With such platforms, you shall be able to establish adaptability and agility across various business processes, from manufacturing to supply chain.
Getting a software system is an excellent option for managing the inventory of raw materials and other industrial management requirements.
Use High-Quality Raw Materials
When companies and organizations attempt to employ lower-quality raw materials, they run the risk of encountering difficulties or problems that could slow down production, including inconsistent and defective finished goods. Although more expensive, higher-quality raw materials can help reduce other expenses over time and provide more goods that consumers will value.
Therefore, utilizing high-quality raw materials can help businesses cut costs and time to a great extent while potentially boosting customer engagement and satisfaction.
Beware of Understocking and Overstocking
As a business owner, you want to maintain a close eye on both overstock and understock. These problems will gradually fade away if your raw material inventory is properly managed.
A company may suffer from understock by experiencing lengthy delays. Understock can lead to serious time limitations across various transport points; whether they are between the manufacturer and the supplier of the raw materials, or between the factory and the store.
On the other hand, an increase in the overall carrying cost may result from an overstock. The costs associated with storing merchandise range widely. If your warehouse is overstocked, spoiling and expiration dates could lead to losses. Then again, some materials may necessitate electrical equipment, which will eventually raise overhead costs.
Transporting the supplies to another facility, moving goods for delivery pickups, and personnel time are additional frequent factors that might result in expenditures associated with overstock. Keep an eye on this metric because the expense of labor might consume a significant percentage of your budget. Before ordering a refill of raw materials, be careful to take into account all of these potential outcomes.
These costs frequently cause the profit margin to decline, which has an impact on both short-term and long-term business objectives. Supply chain and commercial processes, which demand consistent figures, can be guided by projection calculations. In order to forecast clearer projections, always store the appropriate amounts of goods.
Unsurprisingly, overstocking or understocking indicates poor raw material inventory management.
There are a number of approaches to discovering answers if a business encounters problems with inventory and stock management, including the following:
- Revising the sales projection
- Examining seasonal patterns
- Calculating the precise times to reorder safety stock
- Getting in touch with suppliers to check for delays
Here is a brief description of the problems of overstocking and understocking:
Despite being cautious and calculative, companies do face the overstocking issues. If your stocking problems persist even after calculating your raw material inventory, you may want to reevaluate your raw inventory management strategy. Again, using a software program can help you be more automatic and accurate, which will help you avoid these problems.
Avoid Supplier Issues
If and when you experience issues that are caused by delays on your supplier’s side, you may need to rethink your supplier relationship. Look to partner with a supplier that ensures a timely delivery so that all the inventory hassles are lowered and ultimately removed from the sales pipeline.
An enterprise resource system that lets you have complete knowledge about what is going on in your inventory can be helpful. For instance, Deskera’s inventory dashboard helps you monitor your products end-to-end, for successful inventory management. You can track everything in real time from warehousing to fulfilling orders and shipping.
Do not ignore Quality Control
Quality control lets you present just the right and the best products to your customers. Often, companies are of the thought that quality control is not a quantitative factor when it comes to raw materials. However, we must remember that the quality of the raw materials determines the quality of the end product.
Therefore, the quality of the raw material is crucial to the manufacturing and production process. We recommend that you do not ignore it while you are taking care of so many other vital aspects.
Automate Data Management
In the entire process, you can be sure of one thing and that is complications at each stage. There are so many tasks associated with inventory that you may think of automation as your best friend. Cut down your manual tasks and you shall be able to see the difference in the outcomes.
Here are some reasons you should be seeking automation.
Simple demand forecasting: Make estimates of client demand based on historical data using effective software. The software also helps with gauging the trends that you may expect in the coming times.
You will be better equipped to prioritize raw material orders if you include such projections in your inventory management approach. Additionally, effective decision-making procedures will aid organizations in producing more money while also making considerable savings.
Costing functions: The automation feature of software directs you to estimate the entire range of functions for an intelligent costing mechanism. Costing is the term the businesses must keep close track of. Therefore, carrying costs and manufacturing costs can be referred to as two of the most important costs to consider when placing raw material orders.
Costs associated with inventory storage can cause businesses to lose a significant amount of their overall income. The cost of warehousing might quickly rise if some products are not selling or are not being used in production.
Data Collection: Automation can be an impressive factor when it comes to extensive data gathering and analysis. Data collection includes information from every link in the supply chain. Numerous data points on inventory, demand and price projections are present in the supply chain.
These assessments can be streamlined with an automated data-mining tool, making it simpler to monitor different variables. In fact, automating the entire process could be very beneficial. It will help you to access many numbers for further assessment on a semi-regular basis.
Tracking product origin: In some circumstances, the information of the product’s origin and ingredients will be required to follow health and safety laws. Such details could be extra notes about different kinds of dietary restrictions or critical points labels for food allergies. The possibility of selling to a larger consumer base or niche market exists as a result of this.
Many sectors including the food and beverages sector may require an ERP with modules that support labeling. The labels denote the presence of accurate ingredients and the possible allergens the products may contain.
Thus, automation from these systems can eliminate manual label generation for such industries.
Automation for route optimization: The automation tools can work wonderfully well for industries that require them to monitor their routes. The software can assist in managing the timetable around fleet timelines, depending on a company's time constraints and sales objectives.
Route optimization software can be instrumental in cutting down on unnecessary travel time. It helps keep the warehouse staff in the loop about the information on delivery routes to preserve efficiency.
Special Tips for Small and Medium Businesses
It is often observed that SMBs rush to manage everything pertaining to their inventory management of raw materials. Taking too much on the plate can be mind-blogging and therefore, it is recommended that they concentrate on the raw and finished inventory before anything else.
It would rather be an easy job to calculate raw materials and finished goods, which would pave the way for an efficient production process. WIP inventory can wait at this stage.
Q: What is WIP (Work-in-Progress) Inventory?
A: These are the goods that are currently going through one or more stages of production. They cannot be sold because they are still in an incomplete stage. Basically, a work-in-process is a raw material that is handled by human labor.
Once you have understood and completed the pre-production and post-production inventory calculation, calculating WIP inventory will be straightforward.
What is Raw Material Inventory Turnover and How to Calculate it?
The rate at which raw inventory is used up and subsequently replenished is referred to as raw materials inventory turnover. It is a solid indicator of how precise a company's purchasing and inventory forecasting methods are.
For any specific time period, the formula for the raw materials inventory turnover ratio is:
Here, the average cost of raw materials inventory is given as follows:
Calculating the Raw Material Value with Weighted Average Costing
To understand how we may calculate the raw material value with this method, we must learn more about the Weighted Average Cost or WAC.
The COGS and inventory amounts are determined using a weighted average in the Weighted Average Cost (WAC) technique of inventory valuation in accounting. The carrying value of the items sold during a specific time period is the cost of goods sold or COGS.
One of the several formulas, such as specific identification, first-in-first-out, or average cost, is used to assign costs to specific commodities.
The weighted average cost method divides the goods for sale by the quantity or number of units available for sale.
The formula for the Weighted Average Cost method is given as follows:
Here,
Costs of goods available for sale = Beginning inventory value + Purchases
Units available for sale denotes the number of units a company can sell or the total number of units in inventory.
The WAC Method under Periodic and Perpetual Inventory Systems
Under a periodic and perpetual inventory system, the weighted average cost technique produces various allocations of inventory costs.
The business does an ending inventory count and applies product costs to determine the ending inventory cost in a periodic inventory system. The COGS can then be calculated by adding the initial and ending inventory costs, as well as the purchases made during the time.
Inventory levels and COGS are continuously tracked via a perpetual inventory system. The weighted average cost approach is also known as the moving average cost method in a perpetual inventory system.
While the perpetual inventory system offers more up-to-date information for controlling and managing inventory levels, it could be a little heavy on the pockets of a business.
Example of Raw Material Inventory Turnover
We shall take an example of a company that manufactures furniture. Such an organization that manufactures furniture would first calculate its average raw material inventory if it wanted to calculate its raw material turnover rate for the past fiscal year.
We take the following assumptions:
Starting inventory value = $50,000
Ending inventory value = $43,000
From its starting inventory value of $50,000 at the beginning of the year, it would add that to its ending inventory value of $43,000.
50,000 + 43,000 = 93,000
93,000/2 = $46,500
Taking that number and dividing it by two, you get $46,500. After taking the company's total annual cost of goods sold, which assumingly was $220,000, it would divide that number by the average raw material inventory of $46,500. The raw material inventory turnover of the company would be 4.73.
The company might want to explore inventory turnover further by dividing 365 days by 4.73. That would provide a more accurate estimate of how often it needs to replenish its inventory. By using the equation 365/4.73 for this particular example, 77.16 is what we get at the end.
In other words, the company replenishes its raw material inventory every 77 days on average.
How much effort needs to go into Raw Materials Inventory Management?
We have learned quite a lot about raw material inventory management till now. Yet, you may wonder, is it too much of an effort to track your raw materials inventory?
If yes, then how much is too much?
Well, taking care of your inventory can be a tedious task but you do not need to worry too much about it. This part of the article leads us to discuss some approaches that can be insightful.
According to the Pareto Principle or Pareto Analysis, only 20% of your input will result in 80% of your results. This indicates that even if you put in 100 hours a week of labor, only 20 hours might be useful and will account for most of your outcomes.
There are many examples where you shall spot and apply the Pareto Analysis. These include the following:
- 20% team members contributing to 80% profits or
- 20% defective machinery leading to 80% overall disruptions in business operations.
Besides these examples, the principle 80% of your operations employ only 20% of the knowledge you gain about managing your raw material inventories. The most crucial knowledge is this 20%, which is what you need to know if you want to manage your inventory effectively. The rest will come once you have this knowledge written down.
In the scenario that troubles you despite all the efforts, you can consider perpetual inventory workflow for creasing out the inventory management issues. By doing this, you shall be able to evaluate the monthly costs to reserve each square foot for the stock.
JIT or the just-in-time method is another principle of manufacturing that can help you out around this stage. Having learned about these mechanisms and methods, you may still want to examine the amount of raw material stock stored in your warehouses.
You must understand that there is no need to keep the raw materials that have not been put to use for the longest time; these could include the raw materials that may not be required even in near future.
Such inventory is only adding to your carrying costs apart from the other expenses for storing this inventory.
If you are facing such a scenario where you need to get a better and solid grip over your inventory, then the software is something you should consider. Such a system can indicate all the relevant parameters in real time, including inventory levels, efficient order fulfillment for cost reduction, timely backorder, and so on.
Such information can help you accomplish enhanced sales and better customer satisfaction and retention.
Overcoming Challenges with Raw Material Data Management
Just like any other field, there are multiple challenges when you set out to manage your inventory. However, with simple practices, you shall be able to overcome these challenges comfortably.
Let’s look at some of the steps you can take to achieve this:
Planning and Forecasting
Inventory forecasting, or demand planning, involves making predictions about needed inventory levels based on past data, trends, and events. Businesses should forecast accurately to ensure they have enough inventory to fulfill customer orders without tying up cash in inventory that is not needed.
The components required for accurate inventory forecasting include the following:
- present stock levels
- unfulfilled purchase orders
- historical patterns
- demand projections and seasonality
- maximum levels of stock
- sales velocities and trends
- customer reaction to particular products
Supply chains and consumer demands are constantly changing, which makes an accurate inventory forecast extremely valuable. Analyzing data, gaining experience in the industry, and analyzing the customer perspective are all needed to produce accurate forecasts.
Costing
Inventory costing or the cost of inventory include orders, storage, and paperwork associated with inventory. A company's management evaluates this cost when determining how much inventory to keep on hand.
There are five types of inventory costs, which are as follows:
Ordering costs: This includes payroll taxes, wages and employee benefits of the procurement unit, labor costs, and so on.
Carrying costs: This is the cost that refers to the money a business loses due to the unsold stock lying in the warehouse. Carrying costs include scrap costs, capital costs, inventory risk costs, maintenance costs, warehouse costs, and so on.
Inventory holding costs: Simply put, this is the amount of rent your company pays for an area to store the inventory. Basically, your warehouse describes the inventory holding cost.
Shortage costs: Also known as stock-out costs, these are the costs business experiences in times of shortage of stock for diverse reasons; which include emergency shipment costs, customer loyalty, and disrupted production costs, among others.
Spoilage costs: This cost is associated with the perishable items which are not sold in time. When companies have products that expire, they experience spoilage costs of inventory. This could apply to the food and beverages industry, cosmetics industry, and many other FMCG products.
These costs could impact the cash flow and hamper the profits of a business, and therefore are crucial to keeping in control.
All these costs must be tracked and controlled in time to avoid their impact on the PL statement.
Data-driven Management
Managing a business is synonymous with efficient data management. When we say data, we refer to the information that keeps pouring in from all sources and units in a company.
By gathering data from your sales, production lines, and anywhere else on your supply chain, you can ensure you always have the right amount of raw material on hand when you need it. Inefficient spreadsheets can be used to accomplish this. Making constant manual updates, however, can be challenging.
Companies must be prepared to face and overcome this challenge.
Benefits of Raw Materials Inventory Management Software Integrated with ERP
Technological advancements facilitate a world of fantastic tools and smart applications that can take care of your business information for you. Despite having the right set of talent pools and your own expertise to fall back on, your business may still struggle if you do not have the right tools by your side.
You certainly do not want to fall prey to ill-managed inventory owing to a lack of tools. This brings us to discuss the most important aspect of a game changer that can elevate the way things have been so far in the business.
Here are some reasons why you should consider inventory management software for your business:
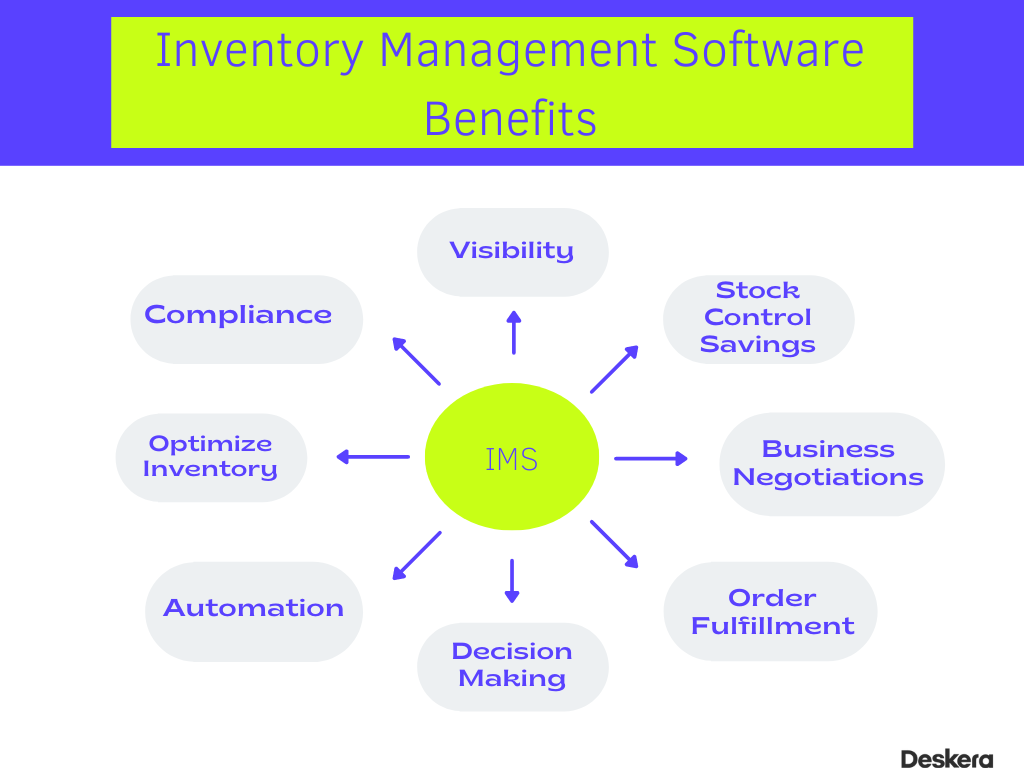
Improved Visibility
It is crucial to have clear visibility over your inventory for checks and tracking specific products or goods. Being able to locate a specific item quickly in the event that it needs to be recalled due to a defect is essential to ensuring that orders do not contain it. Your inventory management system guides you to discover any tampered or defective materials and has complete traceability for all of your products.
Attain savings from Stock Control
Lesser stock wastage annually can result in significant savings over time. Automated processing allows you to maintain optimal inventory levels at all times. You can reduce the amount of surplus and obsolete stock taking up valuable space and the associated costs by improving stock management.
Ordering smaller batches of your inventory or raw materials can be one of the ways to achieve lowered stock wastage.
Better Business Negotiations
Negotiations are integral to any business and are crucial to your business operations. However, an adept negotiation can take place only when you are armed with accurate and comprehensive information.
The system allows you to get access to relevant information across all units of your business, including inventory. This makes you better equipped for negotiation.
Ensuring Order Fulfillment
Timely order fulfillment is equivalent to greater customer satisfaction. This is possible only when you can meet your deadlines in time. However, it could be impossible to meet the deadlines if you face a stock crunch. A lack of essential raw materials can lead to disrupted order fulfillment and tarnish the business's reputation.
Inventory management software can sync your orders with the inventory, thereby, ensuring the completion of orders. It also offers automation of ordering and you can be sure of the availability of materials with long lead time.
Informed Decision-Making
Decisions are what drives a business. Right decisions can steer the business toward success and the wrong ones could be equally damaging. Inventory management software provides thorough data that enables you to make data-driven business decisions.
Effective planning and forecasting are made possible, and automatic reporting gives you the information you need to make strategic decisions.
Automate Manual Tasks
Automation is one of the key features of an inventory management system. Stocktakes, deliveries, and fulfillment can all be sped up using barcode and RFID scanning. Using software frees your staff from tedious chores and decreases errors caused owing to man-made entries.
Automation also keeps the hassles of repeated and redundant tasks at bay.
Optimize Inventory
It is a technique for reconciling financial restrictions with corporate goals and fulfillment standards over a wide range of inventory stock-keeping units. This is an essential component of inventory management that considers the erratic nature of supply and demand.
Inventory optimization is a collection of best practices for businesses looking to conserve cash while keeping their inventory available for purchase.
Ensure Compliance with GAAP
Compliance with GAAP – Generally Accepted Accounting Principles – depends heavily on effective inventory management. It can prevent inventory values, which are recorded as the market value, from being overstated in terms of profits and/or worth.
For financial transparency, stock prices must be calculated correctly. Your inventory management system offers the accuracy needed by GAAP.
Importance of Accurate Inventory Tracking of Raw Materials
Inventory is an asset that companies must always keep monitoring. The tendencies of your business are analyzed and predicted by accurate raw material inventory management. Buying merchandise in amounts you know you will use is always helpful. Also, it also enables you to plan if you are expecting busy times.
Here are the top elements that describe the importance of accurate inventory tracking of raw materials:
Maintaining Stock Levels
Additionally, knowing this avoids buying too much or too little. This is to say that you are spared the problems of overstocking or missing orders due to a lack of inventory. Overstocking yourself with stuff can be expensive and wasteful.
A business owner may not use all of the materials they acquire if they overbuy. Depending on the kind of materials, the quality may deteriorate before they are even used, causing the materials to be thrown away.
Another issue is buying too little. You will eventually run out of the supplies you need to create your products if you consistently underbuy them. This can lead to delays or order cancellations. Moreover, you will frequently encounter dissatisfied customers and lose out on loyal customers.
To summarize, we can say that inventory mismanagement can be troublesome for you and your customers.
Fewer Missed Sales
Missed sales are a result of mismanaged inventory when you do not know the exact inventory levels. Your business can suffer huge losses if there are frequently missed orders. Not only does it reflect badly on the reputation, but also repels your existing loyal customer base.
Accuracy in inventory management can provide important insights that can help you avoid such issues. Insights include quickly viewing the products that are low in stock or gauging the success of the products that are selling well.
Accurate inventory management also lets you place reorders before the products run out of stock.
More Accurate Reports
Accurate stock cost values are generated by accurate stock reports. If you employ cost-of-sale accounting, they are crucial to the accuracy of various financial reports. With this approach, each sale is associated with a cost that is derived directly from the asset value of the goods. Correct cost values are therefore crucial to your balance sheet, cost of sales, and profit and loss reporting.
In other words, accurate reports lead you to get a clearer picture of your financial well-being.
Better-invested Capital
You must invest your money appropriately by purchasing the proper quantity of each product. This is essential if you want to succeed in the retail industry. It helps to maintain accurate inventory reports.
Slow-moving products become easily identifiable, allowing you to price them down and get them away from your inventory. This further frees up funds for marketing, new raw materials, and other investments.
Early detection of any upcoming Disruption
Problem detection before it actually occurs is significant for any business. A close watch on your inventory levels can help you foresee or detect the issues that may crop up later.
By regularly comparing sales and purchases using well-maintained inventory software, you shall be able to overcome this issue easily.
Satisfied and Happy Customers
Exact inventory reports also enable you to deliver superior client support. You must be able to examine your report and verify that you have one excess product in the warehouse when clients complain that they have not received one of the items they requested.
Additionally, you will be able to sell customers the products they desire if your stock system is up to date with purchase orders. This is because you know that there are more products on their way.
In a similar vein, if you constantly monitor inventory levels, you can spot faulty shipments earlier. All these components lead to fostering better trust among your customer base.
Well-organized Reordering
If you wish to maintain control over reordering, you must keep all the information pertaining to it handy. When your reports let you know accurately what is in stock, reordering will be quick and simple.
This way, you can avoid personally visiting your warehouse shelves to submit a purchase order. Instead, you can proceed gradually through your product range and make good purchasing decisions.
Furthermore, you can determine if you currently have products on order with a supplier or if your supplier has long wait times. Additionally, you can gain insights into the efficiency of your supplier’s deliveries from these reports.
Reduced Warehouse Costs
The pick-pack-ship procedure functions more effectively when your inventory report shows you what you have in stock. This gives you the option to balance your resources differently or handle more orders in the same period of time with the same workforce.
Also, your warehouse staff can heave a sigh of relief; they will not have to waste time searching for the most recent item because they will be aware of its specific sale and shipping dates.
Stock take and Year-end Efficiency
Periodic stock takes are quicker and more effective if all of your inventory levels are accurate at all times. Instead of performing numerous time-consuming data entry tasks, you are simply verifying information that is already in your system.
Raw Materials Inventory FAQs
Let's run through some frequently asked questions about raw materials inventory here:
Q: Does Inventory Include Raw Materials?
A: Inventory includes unfinished goods, raw materials, and other tangible goods that are used to create finished goods. Therefore, raw materials do count as a type of inventory.
Despite all the expertise, you may still require an inventory management system. It helps prevent improper categorization of your raw materials. Your warehouse personnel can be aware of the exact location and quantity of each type of item.
Q: How Can I find an Inventory of Raw Materials?
A: Finding raw materials inventory involves looking into potential suppliers and selecting one that is a suitable fit for your company. You can spot this information in a wholesale directory of suppliers that can provide you with the raw materials you are looking for. Alternatively, you can visit the numerous websites that include these wholesale suppliers' contact information and the products they provide.
Additionally, you may enquire within your corporate network for the same. Asking other business owners where they obtain their supplies is another technique to locate raw material inventory. Your friends in the industry will be more than happy to offer you essential personal advice to get connected with the right suppliers for your business.
Q: What is the ideal value of the raw materials inventory ratio?
A: An ideal balance between sales and replenishment is thought to be between a ratio of 4 and 6. A company's raw materials are utilized and replaced frequently if its raw materials inventory turnover rate is higher than that.
On the other hand, a lower rate of materials inventory turnover indicates improper coordination between purchase planning and demand forecasts.
Conclusion
The article leads us to understand how raw material inventory is integral to the productivity of a business. It also enables us to grasp why the raw materials inventory management can be proportional to your business profitability.
The creation of finished goods begins with raw materials. However, some raw materials may degrade over production or storage; as a result, they are added to the company's cost of goods sold. Consequently, the company would like to maintain an inventory of all such materials utilized in the production of items.
How can Deskera Help You?
Raw material inventory management has never been easier before. With Deskera’s ERP system, take care of your accounting, get better visibility in all business operations, and establish excellent supply chain and inventory mechanisms.
In a nutshell, Deskera’s inventory management software offers you everything you need to streamline your processes and achieve heightened inventory control. Following are some of the areas where the software can work wonders:
- Track stock-keeping units (SKUs) easily with customer fields
- Reduce human errors with dropship automation
- Efficient assembling of products with Bill of Materials
- Transfer stocks in seconds from anywhere anytime
- Track shipments in real-time with USPS and FedEx
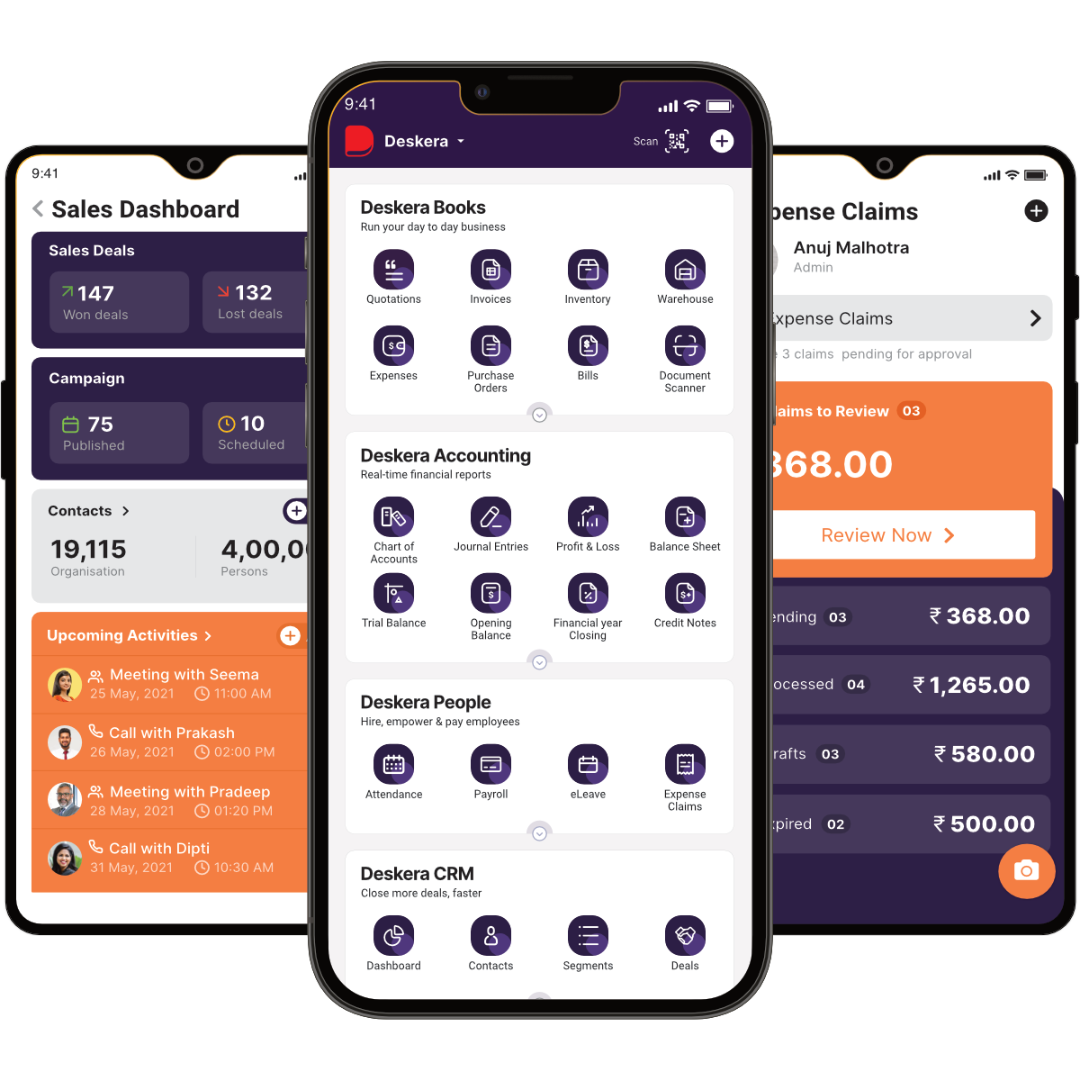
Deskera Books is the tool that lets you keep healthy accounting practices. The impeccable accounting software automates your accounting tasks including billing, invoicing, expenses, payments, and so on.
Deskera CRM is a platform that empowers you to drive better sales and close deals at lightning speed. It facilitates critical functions such as generating leads with emails, lead-generation landing pages, and amazing customer support.
Deskera People is a user-friendly tool that automates your payroll. From the hiring, onboarding, and managing employee benefits and bonuses, to leave and attendance management, the tool processes payroll faster.
So why wait, grab your free trial now!
Key Takeaways
- The stock or input materials a business needs to manufacture its final products are known as raw materials.
- A few examples of raw materials are steel, natural gas, coal, oil, gasoline, lumber, forestry resources, corn, grain, plastic, and minerals.
- Direct raw materials are those that are used right away in the production process, like wood for a chair.
- Despite being heavily used during production, indirect raw materials are not found in the completed product.
- The direct raw material inventory cost is displayed as a current asset on the balance sheet.
- Raw materials may occasionally be separated into Direct and Indirect categories.
- The placement of raw material on the balance sheet and how it is expensed on the income statement will depend on whether it is direct or indirect.
- The total cost of goods in a company's inventory that has not been used for manufacturing or producing finished goods is known as raw materials inventory.
- For managing raw materials inventory, you can utilize a Material Requirements Planning system. The other methods include avoiding supplier issues, quality control, using good quality raw materials, automation, and avoiding understocking and overstocking.
- The rate at which raw inventory is used up and subsequently replenished is referred to as raw materials inventory turnover. It is a solid indicator of how precise a company's purchasing and inventory forecasting methods are.
- Costing, planning, forecasting, and having data-driven management are some of the top challenges while managing the raw materials inventory.
- An inventory management system can offer better visibility, better order fulfillment, inventory optimization, automation, and informed decision-making and helps attain savings from stock control.
- Accurate inventory tracking is significant due to many factors. These include maintaining stock levels, fewer missed sales, accurate reports, early detection of problems, and reduced warehouse cost among others.
Related Articles
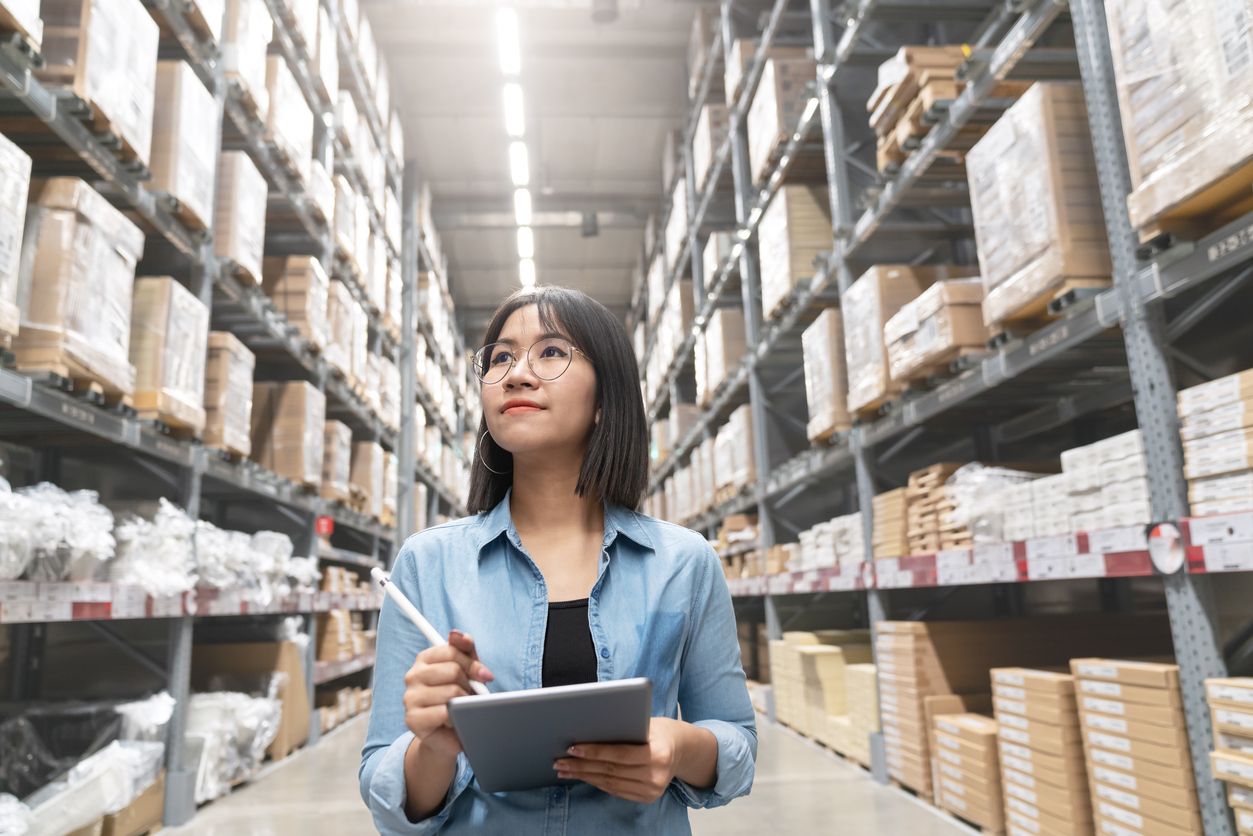