In the world of manufacturing, efficiency, waste reduction, and customer satisfaction are paramount. To achieve these goals, many organizations have turned to lean manufacturing principles, a methodology aimed at eliminating non-value-added activities and streamlining operations.
At the heart of this approach lies production planning, a critical process that plays a pivotal role in achieving lean manufacturing objectives.
Efficient production planning contributes to cost savings by minimizing waste and optimizing resource utilization. Research conducted by the National Institute of Standards and Technology (NIST) in the United States indicated that lean manufacturing implementation, including production planning, can lead to cost savings ranging from 20% to 30%.
Production planning can be defined as the strategic and tactical process of determining the most efficient way to produce goods while meeting customer demand. It encompasses various elements, including demand forecasting, capacity planning, production scheduling, inventory management, and quality control. These elements work in harmony to optimize resources, minimize waste, and ensure smooth operations.
One of the key objectives of production planning in lean manufacturing is to establish a synchronized flow of materials and information throughout the production process. By carefully analyzing customer requirements and forecasting demand, organizations can align their production activities to meet customer expectations efficiently. This proactive approach helps in avoiding overproduction, reducing excess inventory, and preventing delays or shortages.
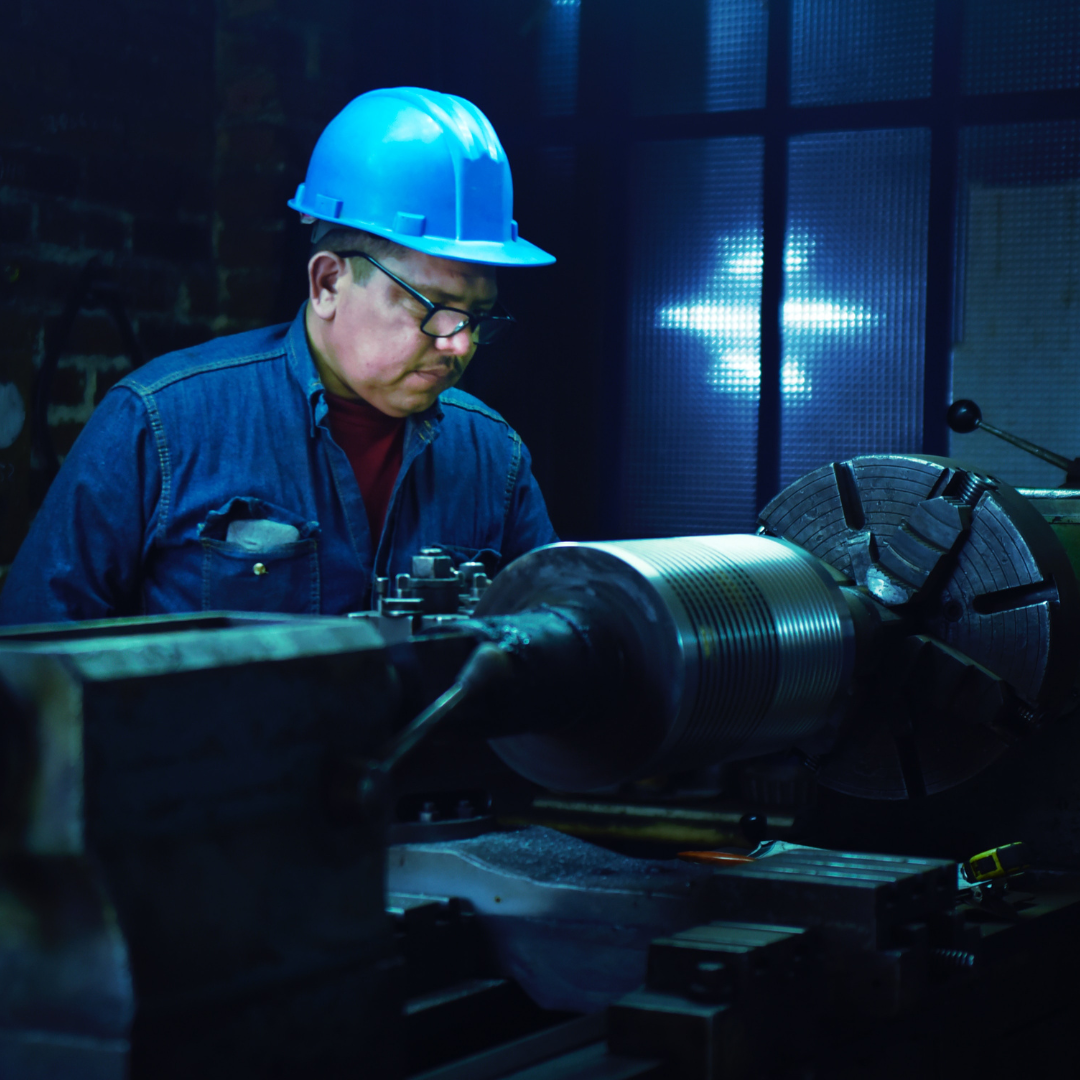
Effective production planning also enables organizations to implement just-in-time (JIT) principles, where materials and components are delivered to the production line exactly when they are needed. This approach minimizes inventory holding costs, reduces lead times, and enhances overall operational efficiency.
In this article, we will delve into the fundamental aspects of production planning in the context of lean manufacturing. We will explore the key elements, benefits, challenges, and strategies associated with production planning.
Additionally, we will examine real-world examples and case studies that highlight successful implementation of production planning in achieving lean manufacturing excellence.
- Brief Overview of Lean Manufacturing Principles
- Importance of Production Planning in Lean Manufacturing
- Understanding Production Planning
- The Role of Production Planning in Lean Manufacturing
- A. Streamlining Workflow and Eliminating Waste
- B. Optimal Resource Utilization
- C. Meeting Customer Demand
- Benefits of Effective Production Planning in Lean Manufacturing
- Challenges and Strategies for Effective Production Planning in Lean Manufacturing
- Case Studies and Examples of Successful Production Planning in Lean Manufacturing
- Conclusion
- How can Deskera Help You?
- Key Takeaways
- Related Articles
Brief Overview of Lean Manufacturing Principles
Lean manufacturing is a systematic approach to production management that focuses on eliminating waste, optimizing processes, and maximizing value for the customer. It originated from the Toyota Production System (TPS) and has since been adopted by numerous industries worldwide. At its core, lean manufacturing aims to improve efficiency, quality, and overall productivity by minimizing non-value-added activities and streamlining operations.
The principles of lean manufacturing revolve around the concept of continuous improvement, also known as Kaizen. It involves engaging employees at all levels of the organization to identify and eliminate waste systematically. Waste, or "muda" in Japanese, refers to any activity that does not add value to the product or service. The main types of waste addressed in lean manufacturing are:
- Overproduction: Producing more than what is needed, leading to excess inventory and storage costs.
- Waiting: Delays between production steps or idle time for workers, which increases lead times and reduces efficiency.
- Transportation: Unnecessary movement of goods or materials, which adds no value and increases costs.
- Overprocessing: Performing more work than necessary or using more resources than required, leading to inefficiency.
- Excess Inventory: Having more inventory than necessary, tying up capital and increasing the risk of obsolescence.
- Defects: Quality issues that result in rework, scrap, or customer dissatisfaction.
- Underutilized Talent: Failing to tap into the full potential of employees and their ideas for improvement.
To address these wastes, lean manufacturing introduces various tools and techniques such as 5S (Sort, Set in Order, Shine, Standardize, Sustain), Kanban, Just-in-Time (JIT) production, value stream mapping, and continuous flow. These tools aim to create a visual, organized, and efficient work environment, reduce inventory levels, improve flow, and enhance quality.
Key principles of lean manufacturing include:
- Value: Identifying the specific value that customers are willing to pay for in a product or service.
- Value Stream: Mapping and analyzing the entire value stream to eliminate waste and create a smooth flow of value-adding activities.
- Flow: Ensuring a continuous and uninterrupted flow of work, materials, and information throughout the value stream.
- Pull: Establishing a pull-based system where production is triggered based on customer demand, reducing inventory and overproduction.
- Perfection: Pursuing a never-ending journey of continuous improvement to achieve perfection in all processes and activities.
By embracing lean manufacturing principles, organizations can achieve higher efficiency, reduced costs, improved quality, and increased customer satisfaction. It requires a cultural shift, where all employees are actively involved in identifying and solving problems, contributing to a more agile and responsive organization.
Importance of Production Planning in Lean Manufacturing
Production planning plays a crucial role in achieving lean manufacturing goals. Here are some key reasons why production planning is essential in the context of lean manufacturing:
Waste Reduction
Production planning helps identify and eliminate waste within the production process. By analyzing demand, capacity, and resource requirements, organizations can optimize production schedules, minimize overproduction, reduce excess inventory, and eliminate non-value-added activities. This waste reduction is fundamental to lean manufacturing principles and helps improve overall efficiency and productivity.
Efficient Resource Allocation
Production planning enables organizations to allocate resources effectively based on demand forecasts and production requirements. By aligning capacity with customer demand, companies can avoid underutilization or overutilization of resources. This ensures a balanced and optimized production process, reduces bottlenecks, and improves resource utilization, contributing to cost savings and increased profitability.
Improved Customer Responsiveness
Lean manufacturing emphasizes meeting customer demand quickly and efficiently. Through production planning, organizations can align their production schedules with customer requirements, ensuring timely delivery of products. By having a clear understanding of demand patterns and capacity constraints, organizations can respond promptly to changes in customer demand, reducing lead times and enhancing overall customer satisfaction.
Enhanced Operational Efficiency
Effective production planning streamlines the flow of materials, information, and activities within the production process. By optimizing production sequences, minimizing setup times, and ensuring smooth material flow, organizations can achieve higher levels of operational efficiency. This leads to reduced cycle times, increased throughput, and improved overall productivity.
Facilitates Just-in-Time (JIT) Principles
Production planning is instrumental in implementing JIT principles, a key component of lean manufacturing. JIT aims to minimize inventory levels and associated costs by producing and delivering products just in time to meet customer demand. Production planning plays a critical role in coordinating material flow, synchronizing production activities, and maintaining appropriate inventory levels, enabling the successful implementation of JIT practices.
Continuous Improvement
Production planning provides a foundation for continuous improvement efforts within lean manufacturing. By monitoring production performance, analyzing data, and identifying areas for improvement, organizations can make data-driven decisions to enhance their production planning processes. This continuous improvement mindset helps organizations adapt to changing market conditions, optimize processes, and stay ahead of the competition.
In summary, production planning is integral to achieving lean manufacturing objectives. It enables waste reduction, efficient resource allocation, improved customer responsiveness, enhanced operational efficiency, facilitates JIT principles, and supports continuous improvement efforts.
By effectively planning and coordinating production activities, organizations can achieve higher levels of productivity, cost savings, and customer satisfaction, leading to a competitive advantage in the marketplace.
Understanding Production Planning
In the realm of manufacturing, achieving optimal efficiency and productivity requires careful orchestration of various processes and resources. At the heart of this coordination lies production planning, a vital component that serves as the backbone of efficient operations. Production planning involves a systematic approach to organizing, scheduling, and optimizing production activities to meet customer demand while minimizing costs and maximizing resource utilization.
In this section, we delve into the intricacies of production planning, exploring its key elements, objectives, and methodologies. By gaining a comprehensive understanding of production planning, businesses can unlock the potential for streamlined operations, improved productivity, and enhanced customer satisfaction.
Throughout this section, we will unravel the multifaceted nature of production planning, examining its role in driving lean manufacturing principles, addressing dynamic market demands, and enabling organizations to stay competitive in today's fast-paced business landscape. We will explore the core components of production planning, such as demand forecasting, capacity planning, scheduling, inventory management, and quality control.
A. Definition and Purpose of Production Planning
Production planning is a strategic and tactical process that forms the foundation of efficient manufacturing operations. It involves the systematic organization, coordination, and optimization of resources, activities, and schedules to ensure timely and cost-effective production while meeting customer demand.
At its core, production planning aims to strike a delicate balance between maximizing efficiency and minimizing costs. It encompasses various elements, including demand forecasting, capacity planning, production scheduling, and inventory management. By integrating these components, production planning seeks to align production capabilities with market requirements, enabling organizations to operate smoothly and meet customer needs in a timely manner.
The primary purpose of production planning is to establish a well-structured framework that optimizes resource allocation, reduces waste, and enhances overall operational efficiency. It provides a roadmap for decision-making, guiding organizations in making informed choices regarding production volumes, sequencing of operations, and resource utilization.
By effectively implementing production planning, organizations can achieve several key objectives. Firstly, it helps businesses meet customer demand promptly, ensuring products are available when and where they are needed. This responsiveness enhances customer satisfaction and loyalty.
Secondly, production planning facilitates efficient use of resources by minimizing idle time, reducing setup and changeover durations, and optimizing production sequences. This leads to improved productivity and cost savings.
Furthermore, production planning enables organizations to identify and address potential bottlenecks or constraints in the production process. By analyzing capacity requirements, organizations can make informed decisions regarding resource investments, workforce planning, and equipment utilization.
Ultimately, production planning plays a vital role in achieving operational excellence. It enables organizations to streamline operations, eliminate inefficiencies, and respond quickly to changing market dynamics. By effectively aligning resources with demand, businesses can drive productivity, reduce manufacturing costs, and maintain a competitive edge in the marketplace.
In the upcoming sections, we will explore the key components and strategies involved in production planning, providing insights into how organizations can leverage this essential process to optimize their manufacturing operations and achieve sustainable success.
B. Key Objectives of Production Planning
Production planning serves several key objectives that are essential for the success of manufacturing operations. By strategically coordinating various aspects of production, organizations can achieve optimal efficiency, minimize waste, and enhance customer satisfaction. Let's explore the key objectives of production planning:
Meeting Customer Demand
One of the primary objectives of production planning is to meet customer demand effectively. By analyzing historical data, market trends, and customer forecasts, organizations can align their production schedules to match customer requirements. This ensures that the right products are available in the right quantities and at the right time, leading to improved customer satisfaction and retention.
Optimal Resource Utilization
Production planning aims to optimize the use of resources such as labor, materials, and equipment. By carefully scheduling production activities and coordinating workflows, organizations can minimize idle time, reduce setup and changeover durations, and maximize the utilization of available resources. This objective helps to drive efficiency, reduce costs, and enhance overall productivity.
Minimizing Inventory Levels
Another crucial objective of production planning is to maintain optimal inventory levels. By analyzing demand patterns, organizations can determine the appropriate stock levels needed to support production and customer demand. Effective production planning ensures that inventory is neither excessive, leading to unnecessary carrying costs, nor inadequate, causing stockouts and customer dissatisfaction.
Efficient Production Scheduling
Production planning involves creating a well-structured production schedule that optimizes the sequencing of operations. By considering factors such as equipment availability, skill requirements, and dependencies between tasks, organizations can streamline production processes and minimize idle time. This objective helps to minimize bottlenecks, reduce lead times, and improve overall operational efficiency.
Quality Control and Assurance
Production planning includes considerations for quality control and assurance throughout the production process. By integrating quality checks and inspections at various stages, organizations can identify and rectify potential defects early on, ensuring that only products of high quality reach the customers. This objective helps to enhance product reliability, brand reputation, and customer satisfaction.
Flexibility and Adaptability
Production planning should also address the need for flexibility and adaptability in response to changing market conditions or unexpected disruptions. By building in contingency plans, alternative production scenarios, and efficient change management processes, organizations can quickly adjust their production plans to accommodate unforeseen circumstances. This objective helps to maintain continuity of operations, mitigate risks, and preserve customer relationships.
By focusing on these key objectives, production planning enables organizations to optimize their manufacturing processes, reduce waste, and deliver products that meet customer expectations. It empowers businesses to achieve operational excellence, enhance competitiveness, and drive long-term success in the dynamic and ever-evolving manufacturing landscape.
C. Key Components of Production Planning in Lean Manufacturing
In the context of lean manufacturing, production planning plays a vital role in achieving efficient and streamlined operations. It encompasses several key components that work together to optimize resource utilization, reduce waste, and drive continuous improvement. Let's explore the key components of production planning in lean manufacturing:
- Demand Forecasting: Accurate demand forecasting is the foundation of effective production planning. By analyzing historical data, market trends, and customer insights, organizations can forecast future demand for their products. This information serves as a basis for determining production volumes, scheduling, and inventory management.
- Capacity Planning: Capacity planning involves evaluating the organization's production capabilities and aligning them with forecasted demand. It includes assessing the availability of resources such as labor, machinery, and production facilities. By understanding the capacity constraints, organizations can make informed decisions regarding resource allocation, workforce planning, and production scheduling.
- Production Scheduling: Production scheduling focuses on determining the optimal sequence and timing of production activities. It involves assigning tasks, setting priorities, and coordinating workflows to minimize idle time, reduce changeover durations, and improve overall efficiency. Scheduling should consider factors such as machine availability, skill requirements, and dependencies between tasks.
- Inventory Management: Lean manufacturing emphasizes the concept of just-in-time (JIT) production, where inventory levels are minimized to reduce waste and costs. Effective inventory management ensures that materials and components are available when needed, without excess stock. It involves monitoring inventory levels, implementing kanban systems, and establishing robust supplier relationships to maintain a lean and responsive supply chain.
- Standardized Work: Standardized work refers to the establishment of consistent and standardized processes for each task within the production system. It includes defining the best practices, documenting work instructions, and providing clear guidelines for workers to follow. Standardized work enables consistency, reduces variability, and enhances quality and productivity.
- Continuous Improvement: Continuous improvement, or Kaizen, is a core principle of lean manufacturing. Production planning provides a platform for identifying areas of improvement, analyzing performance data, and implementing changes to enhance efficiency and eliminate waste. It involves engaging employees at all levels to contribute their ideas, participate in problem-solving, and drive a culture of continuous learning and improvement.
These key components of production planning work in synergy to create an efficient and responsive production system. By integrating demand forecasting, capacity planning, production scheduling, inventory management, standardized work, and continuous improvement, organizations can achieve a smooth flow of materials, minimize waste, reduce lead times, and meet customer demands effectively.
The Role of Production Planning in Lean Manufacturing
In the realm of lean manufacturing, where efficiency, waste reduction, and continuous improvement reign supreme, production planning takes center stage. As a crucial element of the lean philosophy, production planning plays a vital role in orchestrating operations, optimizing resources, and ensuring the smooth flow of materials and information throughout the production process.
In this section, we delve into the intricacies of production planning and its pivotal role in lean manufacturing.
A. Streamlining Workflow and Eliminating Waste
In the pursuit of lean manufacturing excellence, organizations strive to optimize their workflows, eliminate waste, and drive efficiency throughout their operations. This section delves into the critical role of streamlining workflow and eliminating waste in achieving lean manufacturing goals.
By implementing lean principles such as value stream mapping, 5S methodology, and Kaizen, organizations can identify and eliminate non-value-added activities, reduce lead times, and enhance overall operational efficiency. Through a systematic approach to process improvement, organizations can unlock new levels of productivity, minimize waste, and deliver greater value to customers.
1. Just-in-Time (JIT) Production
Just-in-Time (JIT) production is a cornerstone of lean manufacturing, emphasizing the delivery of materials, components, and products precisely when they are needed, in the quantities required, and in the desired quality. This section explores the principles and benefits of JIT production in achieving operational excellence.
By adopting JIT production, organizations can minimize inventory levels, reduce carrying costs, and eliminate the need for excessive storage space. The JIT approach focuses on creating a smooth flow of materials through the production process, avoiding stockpiling and reducing the risk of obsolete inventory.
JIT production relies on a close collaboration between suppliers and manufacturers, with a strong emphasis on efficient communication, reliable delivery schedules, and high-quality inputs. This ensures that raw materials and components arrive just in time for production, minimizing waste and enabling greater flexibility to meet changing customer demands.
The benefits of JIT production are multifaceted. It leads to reduced lead times, allowing organizations to respond quickly to customer orders and market changes. With a lean and agile production system, organizations can minimize the risk of overproduction, defects, and excess inventory, resulting in cost savings and increased profitability.
Moreover, JIT production promotes a culture of continuous improvement, as it requires a relentless focus on identifying and eliminating bottlenecks, process inefficiencies, and sources of waste. By embracing JIT principles, organizations can foster a culture of lean thinking, empowering employees to contribute to problem-solving, quality improvement, and waste reduction.
Join us as we delve deeper into the world of JIT production, exploring its principles, strategies, and implementation techniques. By embracing JIT, organizations can streamline their production processes, reduce waste, and achieve higher levels of efficiency and customer satisfaction.
2. Kanban System
The Kanban system is a visual management tool that plays a vital role in lean manufacturing by optimizing workflow, reducing inventory levels, and improving overall efficiency. This section explores the principles and benefits of the Kanban system in achieving operational excellence.
Originating from the Toyota Production System, the Kanban system provides a visual representation of the production process, enabling teams to track and manage work in progress effectively. It employs a card-based or digital system to signal the need for materials, parts, or tasks, ensuring a smooth flow of work throughout the production system.
The Kanban system operates on the "pull" principle, where items are replenished based on actual demand rather than anticipated demand. This approach minimizes overproduction, reduces excess inventory, and allows organizations to respond quickly to changes in customer requirements.
By using Kanban cards or visual signals, teams can easily identify the status of each task or component, enabling them to prioritize work, manage bottlenecks, and prevent overburdening of resources. This visual representation fosters transparency, collaboration, and continuous improvement within the organization.
Implementing the Kanban system brings several benefits. It helps organizations achieve just-in-time (JIT) production by aligning the replenishment of materials with actual consumption. This leads to reduced lead times, lower inventory holding costs, and increased production flexibility.
Additionally, the Kanban system improves communication and coordination among different teams, ensuring a smooth and synchronized workflow. It enables teams to identify and address production bottlenecks promptly, driving efficiency and reducing waste.
Moreover, the visual nature of the Kanban system enhances problem identification and resolution. By highlighting deviations from the expected workflow, organizations can quickly identify and address issues, preventing delays and maintaining a steady production flow.
Join us as we explore the principles and implementation of the Kanban system in lean manufacturing. Discover how this powerful tool can revolutionize your production processes, optimize workflow, and drive efficiency, ultimately leading to improved customer satisfaction and business success.
3. Pull Production System
The pull production system is a core component of lean manufacturing that focuses on producing goods based on actual customer demand. In contrast to the traditional push system, where production is based on forecasted demand, the pull system emphasizes responsiveness, waste reduction, and enhanced efficiency. This section explores the principles and advantages of the pull production system in achieving lean manufacturing objectives.
At the heart of the pull production system is the concept of "pulling" work through the production process based on customer orders or actual consumption. Instead of pushing products into the system based on production targets or forecasts, the pull system enables organizations to produce only what is needed when it is needed.
By aligning production with customer demand, the pull system minimizes waste associated with overproduction, excess inventory, and unnecessary processing. This lean approach allows organizations to streamline their operations, reduce costs, and improve overall efficiency.
The pull production system relies on several key elements to ensure its effectiveness. First and foremost, it requires a robust and efficient communication system that allows real-time sharing of customer orders, production needs, and inventory levels. This enables organizations to respond promptly and accurately to customer demands, optimizing production schedules and resource allocation.
Another crucial element of the pull system is maintaining a continuous flow of information and materials throughout the production process. This can be facilitated through the use of visual management tools, such as Kanban boards or electronic signals, to communicate the status of tasks, materials, and workstations. This visibility helps to identify bottlenecks, balance workloads, and ensure a smooth production flow.
The benefits of the pull production system are far-reaching. By producing based on actual demand, organizations can reduce lead times, improve customer responsiveness, and minimize the risk of carrying obsolete inventory. It also enhances flexibility, as the system can quickly adapt to changing customer needs and market conditions.
Moreover, the pull production system fosters a culture of continuous improvement and empowers employees to contribute their expertise and ideas. It encourages problem-solving, collaboration, and innovation, as teams work together to identify opportunities for waste reduction, process improvement, and value enhancement.
B. Optimal Resource Utilization
Optimal resource utilization is a crucial objective of production planning in lean manufacturing. It entails effectively allocating and leveraging resources such as labor, machinery, equipment, and materials to maximize productivity while minimizing waste.
By carefully analyzing production requirements, capacity constraints, and available resources, organizations can ensure that resources are utilized in the most efficient and cost-effective manner. This involves balancing workloads, optimizing production schedules, and implementing strategies to minimize idle time and downtime.
Optimal resource utilization not only improves productivity and reduces costs but also enhances overall operational efficiency, allowing organizations to meet customer demands promptly, reduce lead times, and maintain a competitive edge in the market.
1. Balancing Workload and Capacity
Balancing workload and capacity is a key component of optimal resource utilization in production planning for lean manufacturing. It involves effectively aligning the workload of production activities with the available capacity of resources to maximize efficiency and minimize waste. By carefully analyzing production requirements, resource capabilities, and demand forecasts, organizations can allocate tasks and distribute workloads in a way that optimizes resource utilization.
When workload and capacity are balanced, it ensures that resources are utilized to their fullest potential, avoiding underutilization or overutilization. Underutilization leads to wasted resources and increased costs, while overutilization can result in bottlenecks, delays, and reduced productivity.
By achieving a balance between workload and capacity, organizations can maintain a steady production flow, enhance operational efficiency, and meet customer demands effectively. It enables them to avoid backlogs and excessive lead times, while also preventing idle time and inefficiencies.
Furthermore, balancing workload and capacity allows organizations to identify any capacity constraints or limitations in their production process. This insight enables them to make informed decisions regarding resource allocation, capacity expansion, or process improvements. It helps in identifying areas where additional resources may be required or where adjustments in the production schedule may be necessary to maintain optimal resource utilization.
Overall, balancing workload and capacity as part of optimal resource utilization ensures that resources are utilized efficiently, waste is minimized, and productivity is maximized. It contributes to the lean manufacturing goal of achieving operational excellence by aligning production activities with available resources to meet customer needs effectively and maintain a competitive advantage in the market.
2. Efficient Material Flow
Efficient material flow is a critical aspect of optimal resource utilization in lean manufacturing. It involves the smooth and seamless movement of materials throughout the production process, from raw materials to finished goods, in the most efficient and streamlined manner possible.
Efficient material flow ensures that materials are available when and where they are needed, minimizing waste, delays, and disruptions in the production process. It involves carefully designing and organizing the layout of workstations, storage areas, and transportation routes to facilitate a continuous flow of materials.
By implementing strategies such as just-in-time (JIT) production and Kanban systems, organizations can synchronize material flow with production demand, reducing inventory levels, and eliminating unnecessary stockpiling. This lean approach enables organizations to minimize the risk of carrying excess inventory, reduce storage costs, and optimize space utilization.
Efficient material flow also involves eliminating bottlenecks and optimizing the sequencing of production tasks to maintain a smooth workflow. By identifying and addressing potential constraints or obstacles in the material flow, organizations can prevent disruptions, optimize throughput, and improve overall productivity.
Moreover, efficient material flow enables organizations to respond quickly to changes in customer demand or market conditions. It provides the flexibility to adjust production schedules, prioritize orders, and accommodate variations in product mix or volume. This responsiveness helps in meeting customer expectations, reducing lead times, and enhancing customer satisfaction.
By focusing on efficient material flow, organizations can minimize waste, improve resource utilization, and enhance the overall efficiency of their production processes. It contributes to the goal of lean manufacturing by creating a streamlined and agile operation that maximizes value, reduces costs, and delivers products to customers in a timely and efficient manner.
3. Minimizing Inventory Levels
Minimizing inventory levels is a crucial aspect of optimal resource utilization in lean manufacturing. It involves reducing the amount of inventory held at various stages of the production process, including raw materials, work-in-progress (WIP), and finished goods. The objective is to maintain inventory at the lowest possible level while ensuring uninterrupted production and timely delivery to customers.
By minimizing inventory levels, organizations can achieve several benefits. First, it reduces carrying costs associated with storage, handling, and obsolescence. Excess inventory ties up valuable capital that could be utilized elsewhere in the business. By keeping inventory levels lean, organizations can free up financial resources and improve their cash flow.
Minimizing inventory levels also helps in identifying and addressing issues promptly. When inventory is low, problems such as defects, quality issues, or bottlenecks become more visible, allowing organizations to take immediate corrective actions. This approach fosters a culture of continuous improvement and enables organizations to enhance product quality and process efficiency.
Furthermore, reducing inventory levels improves production flexibility and responsiveness. With less inventory on hand, organizations can more easily adapt to changes in customer demand, market trends, or product variations. This agility enables them to quickly adjust production schedules, prioritize orders, and meet customer expectations in a timely manner.
To achieve minimal inventory levels, organizations employ various lean manufacturing techniques. These include just-in-time (JIT) production, where materials are delivered precisely when needed, and pull systems, where production is based on actual customer demand. By adopting these principles, organizations can eliminate overproduction, reduce lead times, and minimize waste.
Additionally, effective demand forecasting and supply chain management play a vital role in minimizing inventory levels. Accurate forecasting helps organizations plan production schedules and procure materials based on real-time demand data. Collaborative relationships with suppliers also facilitate timely and efficient delivery, reducing the need for excessive safety stock.
In conclusion, minimizing inventory levels is a fundamental aspect of lean manufacturing. By keeping inventory lean, organizations can reduce costs, improve cash flow, enhance flexibility, and maintain a focus on continuous improvement. It enables them to operate efficiently, meet customer demands promptly, and stay competitive in dynamic markets.
C. Meeting Customer Demand
In the world of lean manufacturing, meeting customer demand is a critical objective that drives operational excellence and customer satisfaction. This section explores the strategies and practices employed to ensure that products are delivered to customers in a timely and responsive manner. By aligning production with customer requirements, organizations can create value, maintain a competitive edge, and foster long-term relationships with their customers.
Understanding and anticipating customer demand is at the core of meeting customer expectations. By conducting thorough market research, analyzing trends, and engaging in proactive communication with customers, organizations can gain insights into their needs, preferences, and buying patterns. This knowledge serves as the foundation for effective production planning and resource allocation.
Lean manufacturing principles emphasize agility and responsiveness in production. By implementing strategies such as just-in-time (JIT) production and demand-driven scheduling, organizations can align production with actual customer demand. This approach minimizes overproduction, reduces lead times, and eliminates waste associated with producing goods that exceed customer requirements.
Meeting customer demand also involves efficient order processing, accurate forecasting, and effective supply chain management. Streamlining order fulfillment processes, leveraging advanced forecasting techniques, and collaborating closely with suppliers enable organizations to anticipate customer needs, plan production schedules accordingly, and ensure the availability of materials and components at the right time.
Moreover, a focus on meeting customer demand drives continuous improvement throughout the production process. By regularly monitoring customer feedback, measuring key performance indicators, and engaging in problem-solving initiatives, organizations can identify areas for improvement and implement corrective actions.
This commitment to quality and customer satisfaction fosters a culture of continuous improvement and positions organizations to exceed customer expectations consistently
1. Demand Forecasting and Customer Requirements
One of the key aspects of meeting customer demand in lean manufacturing is demand forecasting and understanding customer requirements. By accurately predicting customer needs and aligning production accordingly, organizations can optimize resource utilization, minimize lead times, and deliver products that meet or exceed customer expectations.
Demand forecasting involves analyzing historical data, market trends, and customer behavior to anticipate future demand. By leveraging advanced statistical models, market research, and customer insights, organizations can develop forecasts that serve as a basis for production planning. Accurate demand forecasting enables organizations to optimize inventory levels, plan production schedules effectively, and avoid stockouts or excessive carrying costs.
Understanding customer requirements goes beyond demand forecasting. It involves actively engaging with customers, conducting surveys, and collecting feedback to gain insights into their preferences, expectations, and desired features. By understanding customer needs and aligning product design and specifications accordingly, organizations can create products that resonate with their target market.
Incorporating customer requirements into the production planning process enables organizations to tailor their operations to meet specific demands. It allows for customization, personalization, or the inclusion of value-added features that differentiate their products in the market. By aligning production with customer requirements, organizations can enhance customer satisfaction and build long-term loyalty.
Demand forecasting and understanding customer requirements also facilitate efficient inventory management. By having a clear understanding of customer demand patterns, organizations can optimize inventory levels, reduce carrying costs, and minimize the risk of obsolete or excess stock. This lean approach ensures that inventory is available when needed, avoids waste, and enhances overall operational efficiency.
Moreover, effective demand forecasting and understanding customer requirements support lean principles such as just-in-time (JIT) production and lean supply chain management. By accurately predicting demand and aligning production accordingly, organizations can minimize overproduction, reduce lead times, and establish efficient supplier relationships.
2. Agile Production Planning and Scheduling
In the dynamic landscape of lean manufacturing, agile production planning and scheduling are instrumental in meeting customer demand. By embracing flexibility and responsiveness in the production process, organizations can adapt to changing customer needs, optimize resource utilization, and ensure timely delivery of products.
Agile production planning revolves around the concept of being able to quickly and effectively respond to variations in customer demand, market trends, or unforeseen circumstances. It involves creating a robust and adaptable framework that allows for rapid adjustments in production schedules, resource allocation, and order fulfillment.
One key aspect of agile production planning is the use of real-time data and advanced analytics. By leveraging technology and data-driven insights, organizations can monitor demand patterns, track inventory levels, and assess production performance in real-time. This information enables them to make informed decisions and proactively adjust production plans to meet customer demand effectively.
Furthermore, agile production planning emphasizes cross-functional collaboration and communication. By fostering a culture of teamwork and information sharing, organizations can ensure that all stakeholders are aligned and working together towards the common goal of meeting customer demand.
Regular communication between sales, production, and other departments enables organizations to anticipate customer needs, resolve bottlenecks, and make timely adjustments to production schedules.
Agile scheduling is another critical component of meeting customer demand. It involves optimizing the sequencing and timing of production tasks to minimize lead times and ensure efficient resource utilization. By employing techniques such as lean flow principles, Kanban systems, and visual management tools, organizations can enhance production flow, reduce setup times, and improve overall productivity.
Additionally, agile production planning and scheduling allow organizations to implement just-in-time (JIT) production practices. By aligning production with actual customer demand, organizations can minimize inventory levels, reduce waste, and optimize resource utilization. This lean approach enables them to avoid overproduction, improve cash flow, and respond swiftly to changes in customer requirements.
In conclusion, agile production planning and scheduling are crucial elements in meeting customer demand in lean manufacturing. By embracing flexibility, real-time data, and cross-functional collaboration, organizations can effectively respond to changes in demand, optimize resource utilization, and ensure timely delivery of products.
The ability to adapt quickly to evolving customer needs enables organizations to remain competitive, enhance customer satisfaction, and drive business success in a dynamic marketplace
3. Flexibility in Response to Changes in Demand
In the fast-paced world of lean manufacturing, the ability to be flexible and responsive to changes in customer demand is a key factor in meeting customer requirements and achieving operational efficiency. Flexibility allows organizations to adjust their production plans, resource allocation, and processes to accommodate variations in demand and swiftly respond to customer needs.
Changes in customer demand can arise due to various factors, such as shifts in market trends, new product launches, seasonal fluctuations, or unexpected events. Organizations that embrace flexibility can quickly adapt their production schedules, adjust inventory levels, and reallocate resources to meet changing customer requirements.
Flexibility in response to changes in demand requires a proactive approach to production planning and resource management. It involves closely monitoring demand patterns, analyzing market trends, and engaging in frequent communication with customers. By staying connected and gathering real-time data, organizations can identify shifts in demand and make informed decisions regarding production schedules and resource allocation.
One aspect of flexibility is the ability to scale production up or down based on customer requirements. When demand increases, organizations can ramp up production capacity, streamline processes, and ensure that resources are allocated efficiently to meet the surge in customer orders. Conversely, during periods of low demand, organizations can adjust production levels, optimize resource utilization, and avoid unnecessary costs.
Moreover, flexibility enables organizations to offer customization and personalization options to customers. By having agile production processes and the ability to accommodate individual customer preferences, organizations can provide tailored solutions that meet specific customer needs. This customization capability not only enhances customer satisfaction but also fosters long-term loyalty and differentiation in the market.
To achieve flexibility in response to changes in demand, organizations can leverage lean manufacturing techniques such as just-in-time (JIT) production, Kanban systems, and cross-training of employees. These approaches enable organizations to streamline processes, reduce lead times, and enhance agility in adjusting production plans.
Additionally, flexibility in response to changes in demand requires a culture of continuous improvement and a willingness to embrace change. Organizations that promote a proactive mindset, encourage innovation, and empower employees to contribute ideas are better equipped to adapt to evolving customer needs.
This culture of flexibility enables organizations to continuously refine their production processes, optimize resource utilization, and stay ahead in a competitive market.
Benefits of Effective Production Planning in Lean Manufacturing
Effective production planning plays a pivotal role in lean manufacturing, driving operational excellence, and facilitating the achievement of organizational goals. This section explores the numerous benefits that organizations can reap by implementing robust production planning strategies in their lean manufacturing practices.
From improving operational efficiency to enhancing customer satisfaction, effective production planning serves as a cornerstone for success in a competitive marketplace.
By carefully analyzing and forecasting demand, organizations can optimize resource allocation, streamline production processes, and minimize waste. This results in improved operational efficiency, reduced lead times, and enhanced productivity.
Effective production planning allows organizations to align their production capacities with customer requirements, ensuring that the right products are available at the right time and in the right quantities.
A. Increased Efficiency and Productivity
One of the primary benefits of effective production planning in lean manufacturing is increased efficiency and productivity. By implementing a well-designed production planning system, organizations can optimize their operations, streamline processes, and achieve higher levels of efficiency throughout the production cycle.
Effective production planning helps organizations identify and eliminate bottlenecks, reduce unnecessary downtime, and minimize waiting times. By carefully analyzing production processes, organizations can identify areas where improvements can be made, such as eliminating non-value-added activities, reducing setup times, and improving workflow. This optimization of operations leads to increased efficiency, allowing organizations to produce more with the same resources and achieve higher productivity levels.
Moreover, effective production planning ensures optimal utilization of resources, including labor, machinery, and materials. By aligning production schedules with resource availability, organizations can avoid overloading or underutilizing their resources. This balance leads to smoother production flows, reduced idle time, and improved overall productivity.
Efficient production planning also allows for better coordination and synchronization of activities across different departments or production stages. By creating a well-structured production plan, organizations can ensure that all necessary tasks and processes are sequenced correctly and that materials are available when needed. This coordination minimizes delays, reduces rework, and enables a seamless flow of operations, enhancing overall efficiency.
In addition, effective production planning facilitates the identification and elimination of waste. By employing lean principles such as value stream mapping and continuous improvement, organizations can identify areas of waste, such as excess inventory, overproduction, or unnecessary movement, and take appropriate measures to eliminate them. This lean approach improves efficiency by focusing resources and efforts on value-adding activities while reducing waste and non-value-added tasks.
By increasing efficiency and productivity through effective production planning, organizations can achieve significant cost savings. By minimizing waste, optimizing resource utilization, and improving operational processes, organizations can reduce production costs, lower lead times, and enhance overall profitability. These cost savings can be reinvested in further process improvements, product development, or other strategic initiatives.
In conclusion, effective production planning plays a vital role in increasing efficiency and productivity in lean manufacturing. By optimizing operations, aligning resources, improving coordination, and eliminating waste, organizations can achieve higher levels of efficiency, reduce costs, and enhance overall productivity.
B. Reduced Lead Times and Cycle Times
By implementing efficient production planning strategies, organizations can streamline their operations, minimize delays, and deliver products to customers in a timely manner.
Lead time refers to the total time it takes from receiving a customer order to delivering the finished product. Effective production planning helps organizations identify and optimize each step of the production process, eliminating bottlenecks and unnecessary delays.
By carefully analyzing the sequence of tasks, optimizing resource allocation, and minimizing setup times, organizations can significantly reduce lead times. This enables them to fulfill customer orders more quickly, improving customer satisfaction and gaining a competitive edge in the market.
Cycle time, on the other hand, refers to the time it takes to complete one cycle of a specific operation or process. Effective production planning enables organizations to identify opportunities for reducing cycle times by streamlining workflows, improving work methods, and eliminating non-value-added activities.
By analyzing and optimizing each step of the production process, organizations can achieve smoother operations, faster completion of tasks, and ultimately reduce cycle times.
Reducing lead times and cycle times has several benefits for organizations. Firstly, it improves customer satisfaction by ensuring timely delivery of products. Customers appreciate prompt delivery, and organizations that can consistently meet or exceed delivery expectations gain a competitive advantage. Reduced lead times also allow organizations to respond quickly to changes in customer demand or market conditions, adapting their production plans accordingly.
Additionally, reduced lead times and cycle times enable organizations to operate with leaner inventory levels. By minimizing the time between order placement and product delivery, organizations can reduce the need for excessive inventory storage. This lean approach helps organizations optimize cash flow, reduce holding costs, and avoid the risks associated with excess inventory, such as obsolescence or spoilage.
Efficient production planning also contributes to improved production scheduling accuracy. By carefully analyzing production capacity, resource availability, and demand patterns, organizations can create realistic and achievable production schedules. This accuracy helps in avoiding overcommitment or underutilization of resources, leading to better resource planning and optimized production flow.
Furthermore, reduced lead times and cycle times contribute to improved overall operational efficiency. By streamlining operations and minimizing delays, organizations can achieve higher productivity levels, optimize resource utilization, and reduce waste. This lean approach leads to cost savings, increased throughput, and improved profitability.
In conclusion, effective production planning plays a crucial role in reducing lead times and cycle times in lean manufacturing. By optimizing workflows, streamlining operations, and eliminating bottlenecks, organizations can achieve faster order fulfillment, improved customer satisfaction, and enhanced operational efficiency. The benefits of reduced lead times and cycle times extend beyond timely delivery and positively impact the organization's competitiveness, customer loyalty, and overall business success.
C. Lower Inventory and WIP (Work in Progress) Levels
Effective production planning in lean manufacturing leads to lower inventory and work in progress (WIP) levels, which is a significant advantage for organizations. By implementing lean principles and optimizing production processes, organizations can achieve efficient resource management, reduce waste, and enhance overall operational performance.
One of the key objectives of effective production planning is to align production levels with customer demand. By accurately forecasting demand and synchronizing production schedules, organizations can minimize excess inventory and avoid overproduction. This lean approach helps in reducing inventory holding costs, optimizing warehouse space, and improving cash flow.
Furthermore, effective production planning enables organizations to implement just-in-time (JIT) production practices. JIT focuses on producing goods only when they are needed, minimizing the need for excessive inventory storage. By closely monitoring customer demand, organizations can adjust their production plans accordingly, ensuring that products are produced and delivered precisely when required. This JIT approach results in leaner inventory levels, reduced carrying costs, and improved efficiency.
Lower WIP levels are also achieved through effective production planning. WIP refers to the inventory of unfinished goods or partially completed work at various stages of the production process. By optimizing production schedules, ensuring smooth workflow, and eliminating bottlenecks, organizations can minimize WIP levels. This reduces the risk of product obsolescence, improves resource utilization, and enhances overall operational efficiency.
Reduced inventory and WIP levels have several benefits for organizations. Firstly, it frees up capital that would otherwise be tied up in inventory, allowing organizations to invest in other strategic initiatives. Secondly, it minimizes the risk of inventory obsolescence or spoilage, ensuring that products are delivered to customers in their freshest and most relevant state.
Additionally, lower inventory levels enable organizations to respond quickly to changes in customer demand or market conditions, as they are not burdened by excessive stock.
D. Enhanced Customer Satisfaction and On-Time Delivery
Effective production planning in lean manufacturing plays a vital role in enhancing customer satisfaction and ensuring on-time delivery. By aligning production processes with customer requirements and implementing efficient planning strategies, organizations can meet customer expectations, build strong relationships, and gain a competitive edge.
One of the key benefits of effective production planning is the ability to accurately fulfill customer orders. By analyzing demand patterns, forecasting customer requirements, and synchronizing production schedules, organizations can ensure that the right products are available at the right time. This enables them to deliver on customer expectations, reducing the risk of stockouts, backorders, or delayed deliveries. The result is increased customer satisfaction and loyalty.
On-time delivery is a critical factor in customer satisfaction, and effective production planning helps organizations achieve this objective. By optimizing production schedules, coordinating activities, and minimizing lead times, organizations can consistently meet or exceed delivery deadlines. This reliability in delivering products on time builds trust with customers and enhances the organization's reputation in the market.
Efficient production planning also enables organizations to respond swiftly to changes in customer demand. By closely monitoring market trends, analyzing customer feedback, and adopting agile production planning strategies, organizations can adapt their production plans to meet evolving customer needs. This flexibility allows them to introduce new products, adjust production volumes, or modify delivery schedules in a timely manner, catering to customer demands and preferences.
Moreover, effective production planning contributes to improved product quality. By streamlining operations, eliminating waste, and ensuring smooth workflow, organizations can enhance the consistency and reliability of their production processes. This results in higher-quality products that meet or exceed customer expectations, leading to increased satisfaction and loyalty.
Meeting customer expectations and delivering products on time not only enhances customer satisfaction but also strengthens the organization's competitive position. Satisfied customers are more likely to become repeat customers, recommend the organization to others, and contribute to positive word-of-mouth marketing. This can lead to increased market share, improved brand reputation, and sustainable business growth.
In conclusion, effective production planning in lean manufacturing is instrumental in enhancing customer satisfaction and ensuring on-time delivery. By aligning production processes with customer requirements, responding to changes in demand, and consistently meeting delivery deadlines, organizations can meet customer expectations, build strong relationships, and gain a competitive advantage.
The benefits of enhanced customer satisfaction extend beyond individual transactions and contribute to the long-term success and profitability of the organization.
Challenges and Strategies for Effective Production Planning in Lean Manufacturing
In the journey towards achieving operational excellence in lean manufacturing, organizations often encounter various challenges in implementing and maintaining effective production planning practices. These challenges can range from complex supply chains to unpredictable demand patterns.
However, with the right strategies and approaches, these obstacles can be overcome, and organizations can ensure smooth and efficient production planning processes.
This section delves into the common challenges faced by organizations in this realm and explores proven strategies to address them. By understanding these challenges and adopting appropriate strategies, organizations can enhance their production planning capabilities, optimize resource utilization, and achieve sustainable success in lean manufacturing.
A. Overcoming Uncertainty in Demand
One of the significant challenges in effective production planning in lean manufacturing is dealing with uncertainty in demand. Demand variability can arise from factors such as changing customer preferences, market fluctuations, or unforeseen events. However, organizations can employ strategies to overcome this challenge and make more accurate demand forecasts.
The first step in addressing uncertainty in demand is to gather and analyze relevant data. Organizations should collect historical sales data, customer feedback, market research, and other relevant information to gain insights into demand patterns and trends. By leveraging this data, organizations can identify demand drivers, seasonality, and other factors that affect demand.
Next, organizations can employ statistical techniques and forecasting models to predict future demand. These models can include time series analysis, regression analysis, and advanced forecasting algorithms. By analyzing historical data, organizations can identify patterns and correlations to develop more accurate demand forecasts. It is important to regularly review and update these forecasts based on changing market conditions and emerging trends.
Collaboration with stakeholders is also crucial in overcoming uncertainty in demand. Organizations should engage with sales teams, marketing departments, and customer representatives to gather insights and perspectives on customer demand.
By involving these stakeholders in the forecasting process, organizations can benefit from their expertise and real-time market intelligence. This collaborative approach helps in aligning production plans with customer requirements, reducing the risk of overproduction or stockouts.
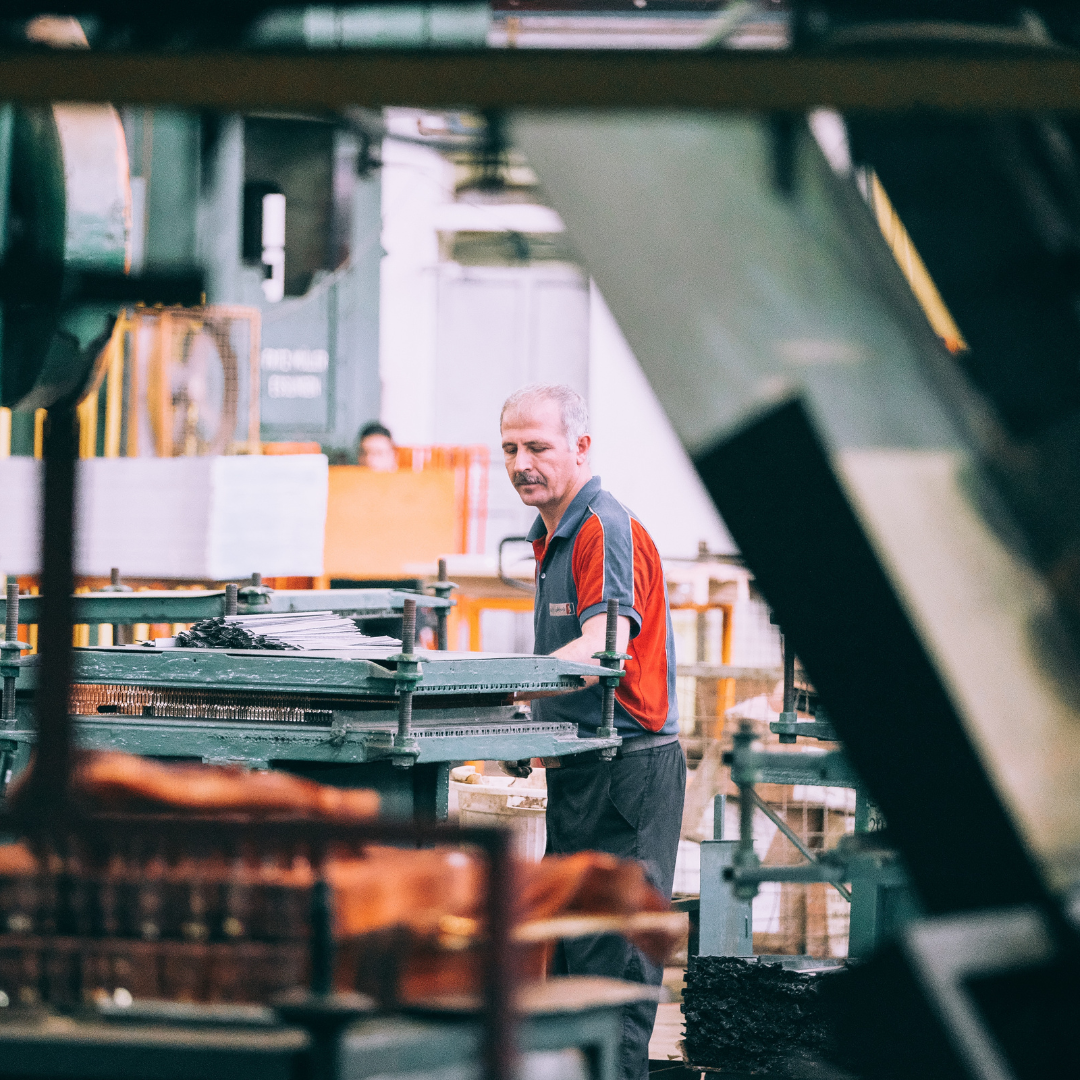
To further mitigate the impact of uncertain demand, organizations can implement agile production planning strategies. This involves maintaining flexibility in production schedules, utilizing modular production systems, and adopting a just-in-time (JIT) approach. Agile production planning allows organizations to respond quickly to changes in demand, adjusting production volumes and schedules as needed.
Another effective strategy is to establish strong relationships with suppliers and implement a robust supply chain management system. By fostering collaboration and transparency with suppliers, organizations can enhance their ability to respond to fluctuations in demand. Collaborative forecasting and sharing of information with suppliers enable better coordination and alignment of production plans with the availability of raw materials and components.
Furthermore, organizations can leverage technology solutions such as advanced planning and scheduling (APS) software to optimize production planning processes. APS systems help in automating demand forecasting, resource allocation, and production scheduling, enabling organizations to make data-driven decisions and respond efficiently to demand fluctuations.
B. Dealing with Variability in Production Processes
Another significant challenge in effective production planning in lean manufacturing is dealing with variability in production processes. Variability can arise from factors such as machine breakdowns, operator skill variations, or unexpected disruptions in the supply chain. However, organizations can employ strategies to mitigate and manage this variability, ensuring stability and consistency in their production operations.
One approach to dealing with variability is to implement standardized work procedures. Standardization involves defining and documenting the best practices for each production task, including specific instructions, tools, and quality standards. By establishing standardized work procedures, organizations can reduce variation and ensure that production processes are executed consistently across different shifts, operators, and workstations.
Furthermore, organizations can invest in training and skill development programs for their workforce. By providing comprehensive training and cross-training opportunities, organizations can enhance the skills and knowledge of their employees, reducing variability in production performance. Well-trained employees can adapt to changes, troubleshoot issues, and maintain a high level of consistency in their work.
Implementing preventive maintenance programs is another effective strategy for managing variability. Regular maintenance and inspection of machines and equipment help in identifying and addressing potential issues before they escalate into major breakdowns. This proactive approach minimizes unplanned downtime, reduces variability in production output, and ensures the smooth functioning of production processes.
Additionally, organizations can employ techniques such as error-proofing (poka-yoke) and visual management to reduce variability and improve process stability. Error-proofing involves incorporating design features or process controls that prevent or detect errors before they occur or reach the customer. Visual management tools, such as Kanban boards or Andon systems, provide real-time visibility into production status, enabling timely interventions and reducing variability.
Lean tools and methodologies, such as Six Sigma and Kaizen, can also be utilized to identify and eliminate process variability. These continuous improvement approaches focus on analyzing data, identifying root causes of variability, and implementing corrective actions to enhance process stability and consistency.
In conclusion, managing variability in production processes is a significant challenge in effective production planning in lean manufacturing. By implementing strategies such as standardization, training, preventive maintenance, error-proofing, visual management, and lean methodologies, organizations can mitigate the impact of variability and ensure stability and consistency in their production operations.
This leads to improved quality, reduced waste, and enhanced overall operational performance. By addressing this challenge, organizations can achieve greater efficiency, customer satisfaction, and competitiveness in the lean manufacturing landscape.
C. Communication and Collaboration across Departments
Effective production planning in lean manufacturing requires strong communication and collaboration across different departments within an organization. The coordination and alignment of activities between departments are essential to ensure seamless production planning and achieve operational excellence.
However, challenges related to communication gaps and siloed approaches can hinder the effectiveness of production planning. Organizations must employ strategies to foster communication and collaboration for optimal production planning outcomes.
One strategy is to establish cross-functional teams that include representatives from various departments involved in the production process, such as production, procurement, logistics, and quality control. These teams facilitate regular communication, knowledge sharing, and collaboration among departments. By working together, teams can address challenges, share insights, and make collective decisions that optimize production planning.
Organizations should also invest in robust communication channels and technologies that enable real-time information sharing and collaboration. This can include implementing project management software, collaboration tools, and digital platforms that allow seamless communication and access to relevant data across departments. Such technologies enhance transparency, facilitate quick decision-making, and foster a culture of collaboration.
Regular meetings, both formal and informal, are vital for effective communication and collaboration. Department heads and key stakeholders should gather for periodic production planning meetings to discuss progress, challenges, and opportunities. These meetings provide a platform for sharing updates, aligning goals, and resolving any issues or bottlenecks that may impact production planning.
In addition to formal meetings, organizations can encourage informal interactions and open communication channels between departments. This can include promoting a culture of collaboration, encouraging cross-departmental discussions, and establishing feedback mechanisms that allow employees to share ideas, suggestions, and concerns related to production planning.
Furthermore, organizations can implement performance metrics and key performance indicators (KPIs) that promote cross-departmental collaboration and align goals. By establishing shared performance metrics, departments are encouraged to work together towards common objectives, fostering a sense of ownership and accountability for overall production planning outcomes.
In conclusion, effective communication and collaboration across departments are crucial for successful production planning in lean manufacturing. By establishing cross-functional teams, leveraging technology, conducting regular meetings, promoting a culture of collaboration, and aligning goals through performance metrics, organizations can bridge communication gaps and foster seamless coordination.
This leads to optimized production planning, improved efficiency, and enhanced overall operational performance. By addressing this challenge, organizations can drive success in lean manufacturing and achieve their strategic objectives.
D. Continuous Improvement and Kaizen Culture
One of the key elements for effective production planning in lean manufacturing is the adoption of a continuous improvement mindset and fostering a Kaizen culture within the organization. Continuous improvement involves constantly seeking opportunities for enhancing processes, eliminating waste, and optimizing production planning practices.
By embracing a Kaizen culture, organizations can drive excellence in production planning and ensure ongoing progress towards operational efficiency and customer satisfaction.
A Kaizen culture encourages all employees, regardless of their role or level, to actively participate in identifying improvement opportunities and implementing changes. It fosters a mindset of continuous learning, innovation, and problem-solving. This culture creates an environment where employees feel empowered to share their ideas, contribute to process improvements, and collaborate towards common goals.
To cultivate a Kaizen culture in production planning, organizations can establish structured improvement initiatives such as Kaizen events or lean project teams. These initiatives bring together cross-functional teams to focus on specific production planning challenges or improvement areas. By engaging employees in these initiatives, organizations tap into their collective knowledge and experience, fostering a sense of ownership and collaboration in driving continuous improvement.
Furthermore, organizations can implement tools and methodologies such as Value Stream Mapping (VSM), 5S, and standardized work procedures to support the Kaizen culture. Value Stream Mapping helps identify areas of waste and bottlenecks in production planning processes, enabling targeted improvements.
The 5S methodology promotes workplace organization, cleanliness, and standardization, creating a foundation for efficient production planning. Standardized work procedures ensure consistency and provide a baseline for continuous improvement efforts.
Regular performance reviews and feedback loops are also integral to the Kaizen culture. Organizations should establish mechanisms for monitoring and evaluating production planning performance against key performance indicators (KPIs). These reviews help identify areas for improvement, celebrate successes, and provide feedback to individuals and teams. By incorporating feedback loops, organizations foster a culture of learning and continuous growth.
Continuous improvement and Kaizen culture require leadership commitment and support. Leaders should encourage and recognize employee contributions to continuous improvement initiatives. They should also provide resources, training, and mentorship to empower employees to drive change and participate in the improvement journey.
Continuous improvement and a Kaizen culture are essential components of effective production planning in lean manufacturing. By fostering a culture of continuous improvement, organizations encourage employee involvement, innovation, and problem-solving.
Through structured improvement initiatives, tools and methodologies, performance reviews, and leadership support, organizations can drive excellence in production planning, optimize processes, and achieve sustainable success in lean manufacturing. Embracing a Kaizen culture positions organizations for continuous growth and ensures they stay competitive in a rapidly evolving business landscape.
Case Studies and Examples of Successful Production Planning in Lean Manufacturing
Examining real-life examples of organizations that have achieved success in production planning within the framework of lean manufacturing can provide valuable insights and inspiration for implementing effective strategies.
A. Toyota Production System (TPS)
When it comes to successful production planning in lean manufacturing, the Toyota Production System (TPS) stands as an exemplary model that has revolutionized the industry. Developed by Toyota, the TPS is renowned for its efficiency, quality, and customer-centric approach. It has become the gold standard for lean manufacturing and serves as a source of inspiration for organizations worldwide.
At the heart of the TPS is a deep focus on eliminating waste, improving efficiency, and maximizing value for customers. Production planning plays a pivotal role in this system, as it aims to synchronize production with customer demand while maintaining high levels of quality and flexibility.
One key aspect of TPS production planning is the concept of Just-in-Time (JIT) production. Instead of maintaining large inventories, materials and components are delivered to the production line precisely when they are needed. This approach minimizes inventory holding costs, reduces waste, and enables a more responsive production process.
Another critical element of TPS production planning is the use of Kanban, a visual signal system that facilitates efficient material flow and production control. Kanban cards or electronic signals are used to signal the need for replenishment or the movement of materials within the production system. This ensures that production is aligned with customer demand, eliminates overproduction, and enables a smooth and efficient workflow.
TPS production planning also emphasizes the importance of cross-functional collaboration and employee empowerment. Teams are encouraged to continuously improve processes, identify bottlenecks, and implement innovative solutions. By fostering a culture of continuous improvement and providing the necessary training and support, Toyota empowers its employees to actively contribute to production planning and drive efficiency gains.
The success of TPS is evident in Toyota's reputation for high-quality vehicles, on-time delivery, and cost-effective production. The principles and practices of TPS have been widely adopted by organizations in various industries, demonstrating the enduring impact of effective production planning in lean manufacturing.
B. Dell's build-to-order model
Dell, a global leader in the computer industry, has made significant strides in production planning through its innovative build-to-order model. This approach, which focuses on customization and responsiveness, has reshaped traditional manufacturing practices and set new benchmarks for efficiency and customer satisfaction.
At the core of Dell's build-to-order model is the concept of producing computers based on customer specifications, rather than building and stocking a large inventory of pre-configured systems. This approach minimizes the risk of obsolete inventory and allows Dell to tailor each computer to the specific requirements of the customer.
Production planning plays a crucial role in Dell's build-to-order model by orchestrating a seamless flow of components and assembly processes. The key to success lies in accurate demand forecasting and the coordination of suppliers, manufacturing facilities, and logistics operations. By aligning production with real-time customer demand, Dell can minimize lead times and respond swiftly to changing market needs.
Dell's production planning also relies on efficient information systems and supply chain management. Through advanced technologies, such as real-time order tracking and inventory management systems, Dell gains visibility into its global supply chain, allowing for precise coordination and optimization of production activities. This streamlined approach enables Dell to reduce inventory holding costs and minimize the risk of excess stock.
Moreover, Dell's build-to-order model leverages a network of strategic suppliers. Close collaboration with these suppliers ensures a reliable and timely supply of components, enabling Dell to meet customer demands without excessive buffer stock. This supplier integration further enhances production planning efficiency and agility.
The success of Dell's build-to-order model is evident in its ability to deliver customized computers to customers in remarkably short timeframes. By aligning production planning with customer preferences and market demand, Dell has gained a competitive edge and set industry benchmarks for efficient manufacturing and on-time delivery.
The build-to-order model has not only transformed Dell's operations but has also influenced the broader manufacturing landscape. Other industries have adopted similar approaches, leveraging Dell's success as a testament to the power of responsive production planning in meeting customer needs and maximizing operational efficiency.
Dell's build-to-order model stands as a testament to the transformative impact of effective production planning. By embracing customization, accurate demand forecasting, streamlined supply chain management, and supplier collaboration, Dell has revolutionized production planning in the computer industry and set new standards for responsiveness and customer satisfaction.
C. Lean implementation in a food processing industry
The principles of lean manufacturing are not limited to automotive or electronics industries but have also found significant application in the food processing sector. Lean implementation in a food processing industry focuses on optimizing production planning processes, improving efficiency, and ensuring the delivery of safe, high-quality products to consumers.
One key aspect of lean implementation in the food processing industry is the reduction of waste throughout the production process. This includes minimizing food waste, reducing energy consumption, and optimizing the utilization of resources such as ingredients, packaging materials, and labor. Production planning plays a vital role in identifying opportunities to streamline operations, eliminate non-value-added activities, and improve overall efficiency.
Effective production planning in a food processing industry involves careful synchronization of processes to meet customer demand while minimizing lead times and ensuring product freshness. Lean principles such as Just-in-Time (JIT) production and Kanban systems are utilized to optimize inventory levels, reduce waste, and enable a smooth flow of materials and products throughout the production line.
By aligning production with customer demand, food processors can minimize stockouts, prevent overproduction, and maintain optimal inventory levels.
Furthermore, lean implementation in the food processing industry emphasizes the importance of quality management and food safety. Production planning involves incorporating robust quality control measures at every stage of the process, from ingredient sourcing to packaging and distribution.
By implementing lean quality control practices, such as standardized work procedures, visual management, and error-proofing techniques, food processors can reduce defects, ensure consistency, and enhance customer satisfaction.
Additionally, lean implementation in the food processing industry focuses on fostering a culture of continuous improvement. This involves empowering employees to actively participate in problem-solving, suggesting process enhancements, and implementing innovative ideas.
By engaging the workforce in production planning and providing the necessary training and tools, food processors can tap into the collective knowledge and experience of their employees to drive efficiency gains and process optimization.
Conclusion
In conclusion, production planning plays a pivotal role in achieving lean manufacturing principles and driving operational excellence. By adopting effective production planning strategies, organizations can streamline workflows, eliminate waste, and optimize resource utilization.
The key objectives of production planning, including balancing workload and capacity, efficient material flow, and minimizing inventory levels, contribute to achieving lean manufacturing goals.
Moreover, production planning enables organizations to meet customer demand by implementing agile planning and scheduling processes and being flexible in response to changes.
The benefits of effective production planning in lean manufacturing are numerous, including increased efficiency, reduced lead times, lower inventory levels, and enhanced customer satisfaction.
By overcoming challenges and leveraging successful case studies, organizations can harness the power of production planning to achieve lean manufacturing and gain a competitive advantage in today's dynamic business environment.
How can Deskera Help You?
Deskera ERP and MRP systems help you to keep your business units organized. The system's primary functions are as follows:
- Keep track of your raw materials and final items inventories
- Control production schedules and routings
- Keep a bill of materials
- Produce thorough reports
- Make your own dashboards
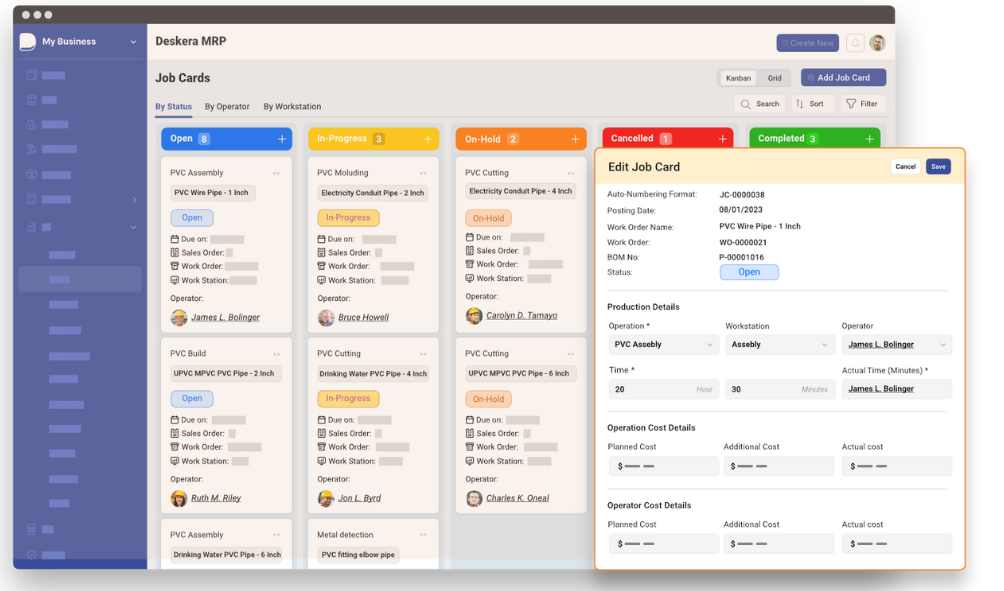
Deskera's integrated financial planning tools enable investors to better plan and track their investments. It can assist investors in making faster and more accurate decisions.
Deskera Books allows you to better manage your accounts and finances. Maintain good accounting practices by automating tasks like billing, invoicing, and payment processing.
Deskera CRM is a powerful solution that manages your sales and helps you close deals quickly. It not only enables you to perform critical tasks like lead generation via email, but it also gives you a comprehensive view of your sales funnel.
Deskera People is a straightforward tool for centralizing your human resource management functions.
Key Takeaways
- Production planning is essential for achieving lean manufacturing goals by optimizing processes, reducing waste, and maximizing value for customers.
- Balancing workload and capacity is crucial to ensure efficient resource utilization and maintain a smooth production flow.
- Efficient material flow, facilitated by tools like Kanban systems, minimizes inventory, reduces waste, and improves overall productivity.
- Minimizing inventory levels through just-in-time production helps prevent excess stock, lowers holding costs, and improves cash flow.
- Meeting customer demand requires accurate demand forecasting, agile production planning, and scheduling processes to ensure timely delivery.
- Optimal resource utilization involves efficient use of labor, machinery, and materials, eliminating bottlenecks and optimizing productivity.
- Effective production planning helps reduce lead times and cycle times, enabling faster response to customer demands and reducing time-to-market.
- Lower inventory and work-in-progress (WIP) levels achieved through lean production planning result in cost savings and improved operational efficiency.
- Enhanced customer satisfaction and on-time delivery are direct outcomes of efficient production planning, meeting customer expectations and improving brand reputation.
- Overcoming challenges such as demand uncertainty, process variability, communication gaps, and fostering a culture of continuous improvement are vital for successful production planning and lean manufacturing implementation.
Related Articles
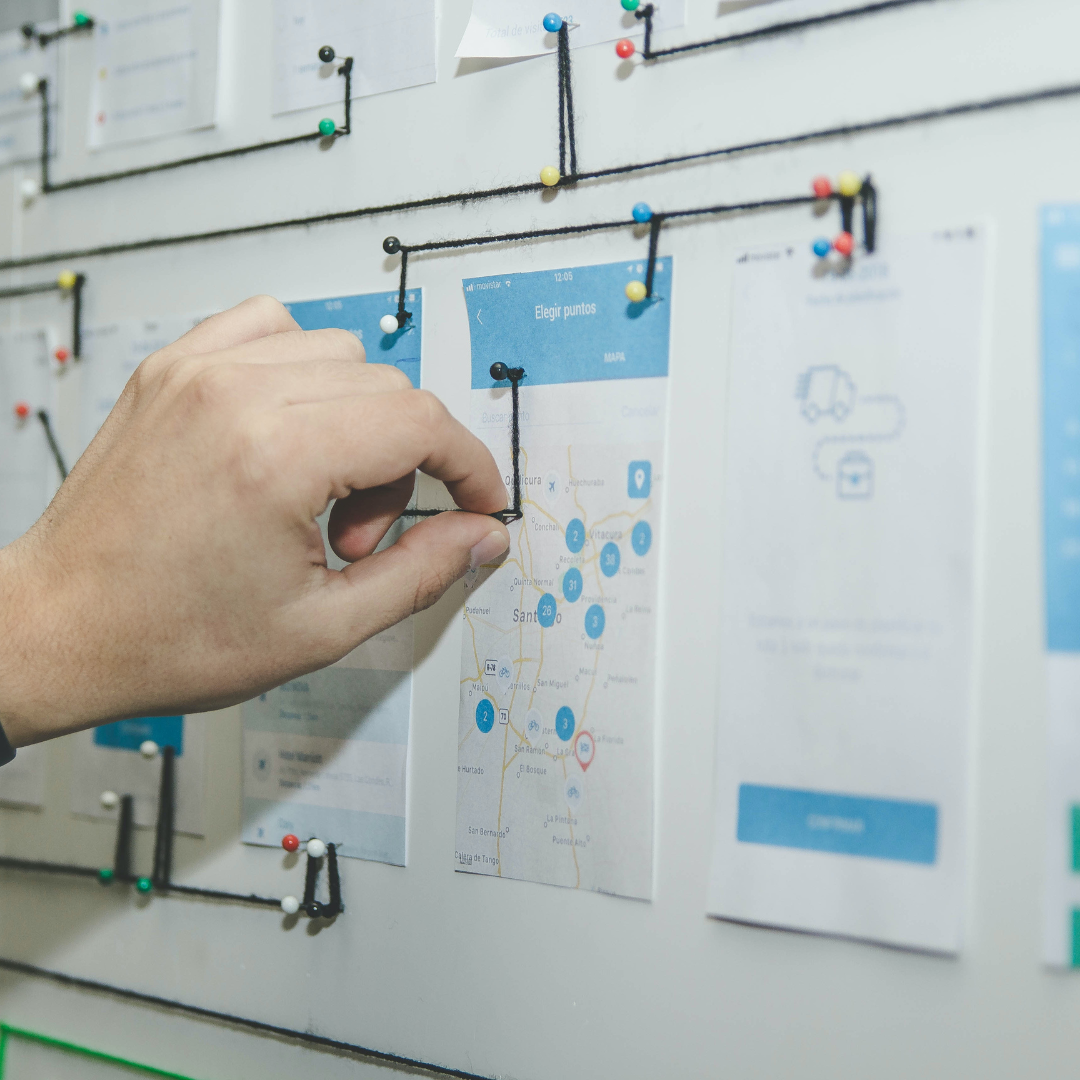
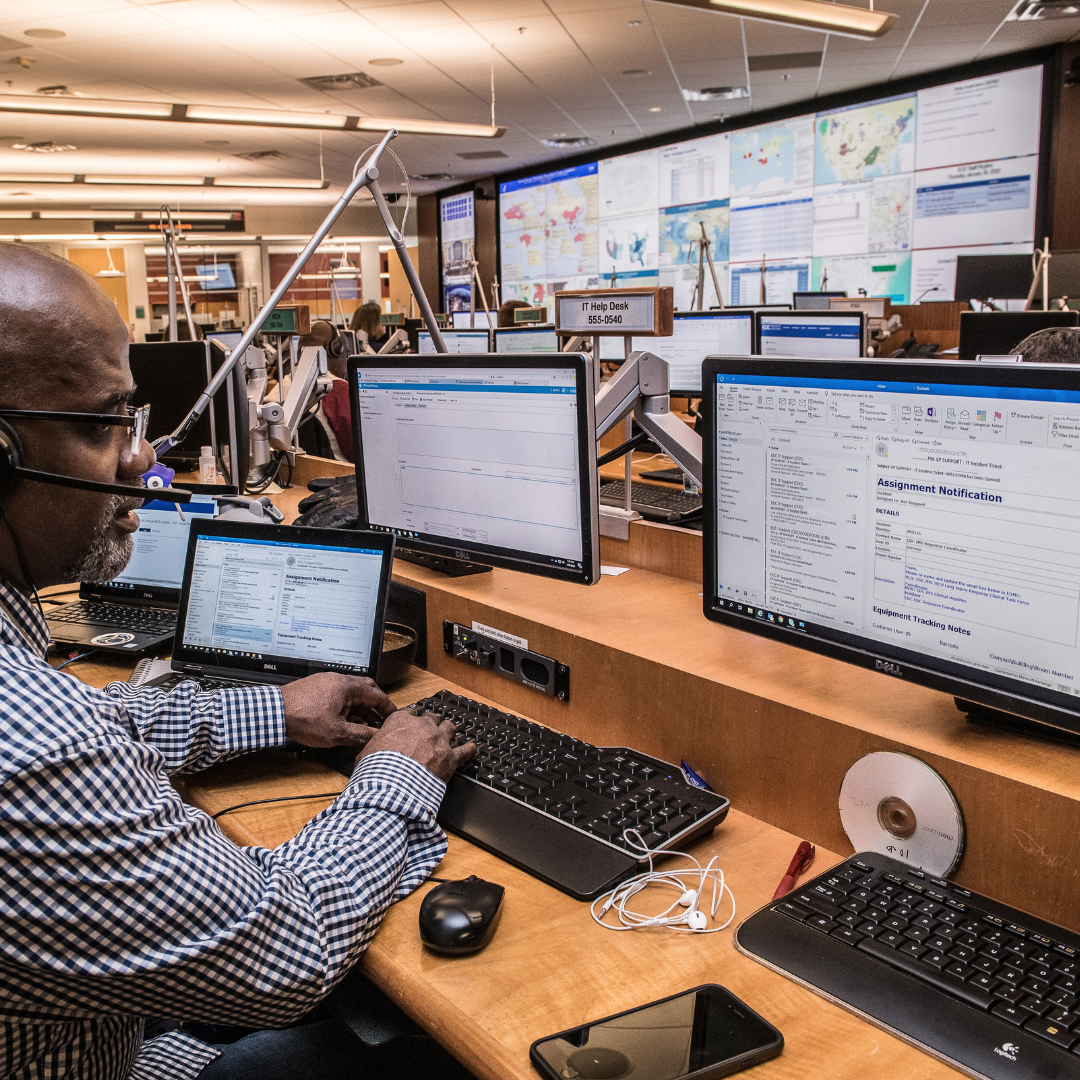
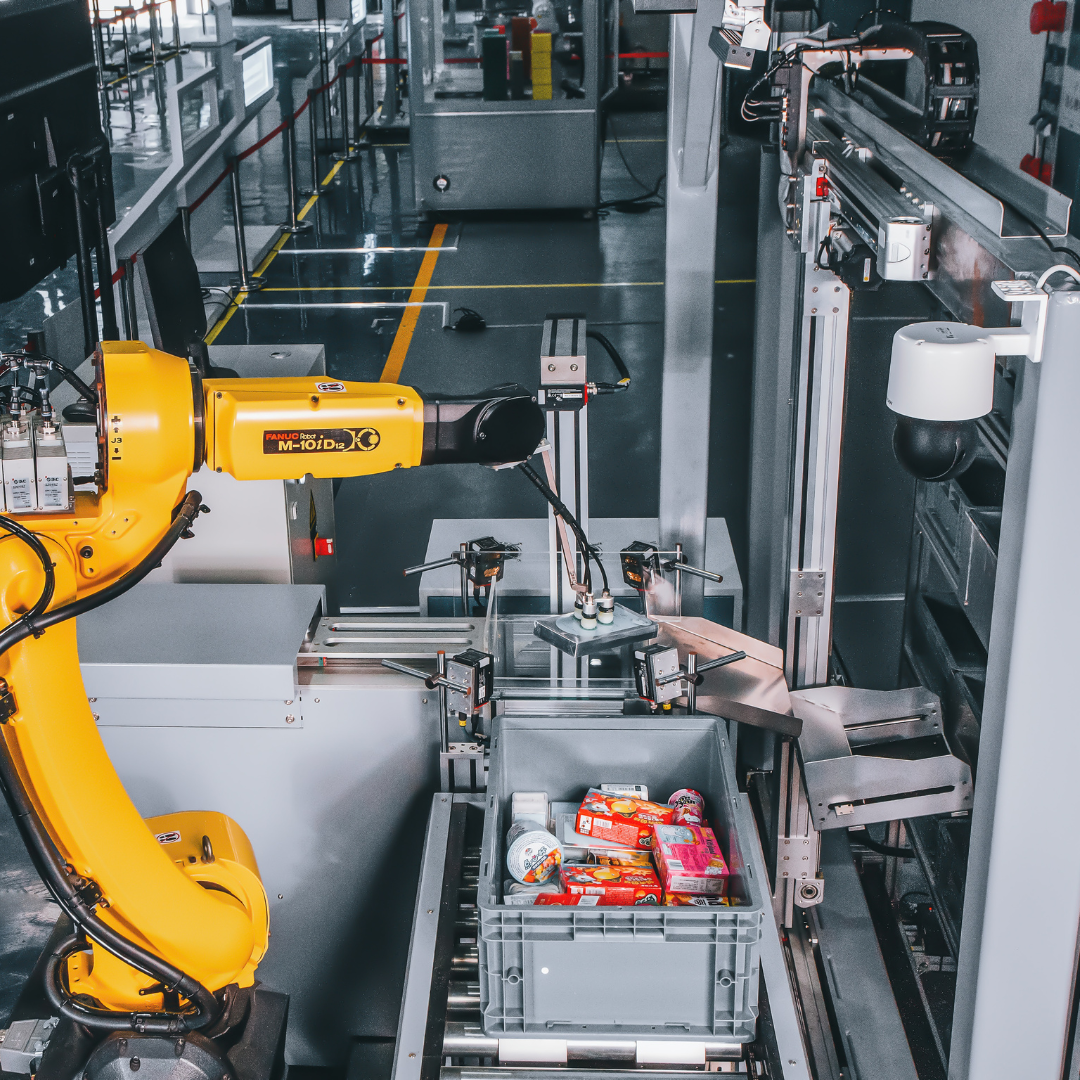
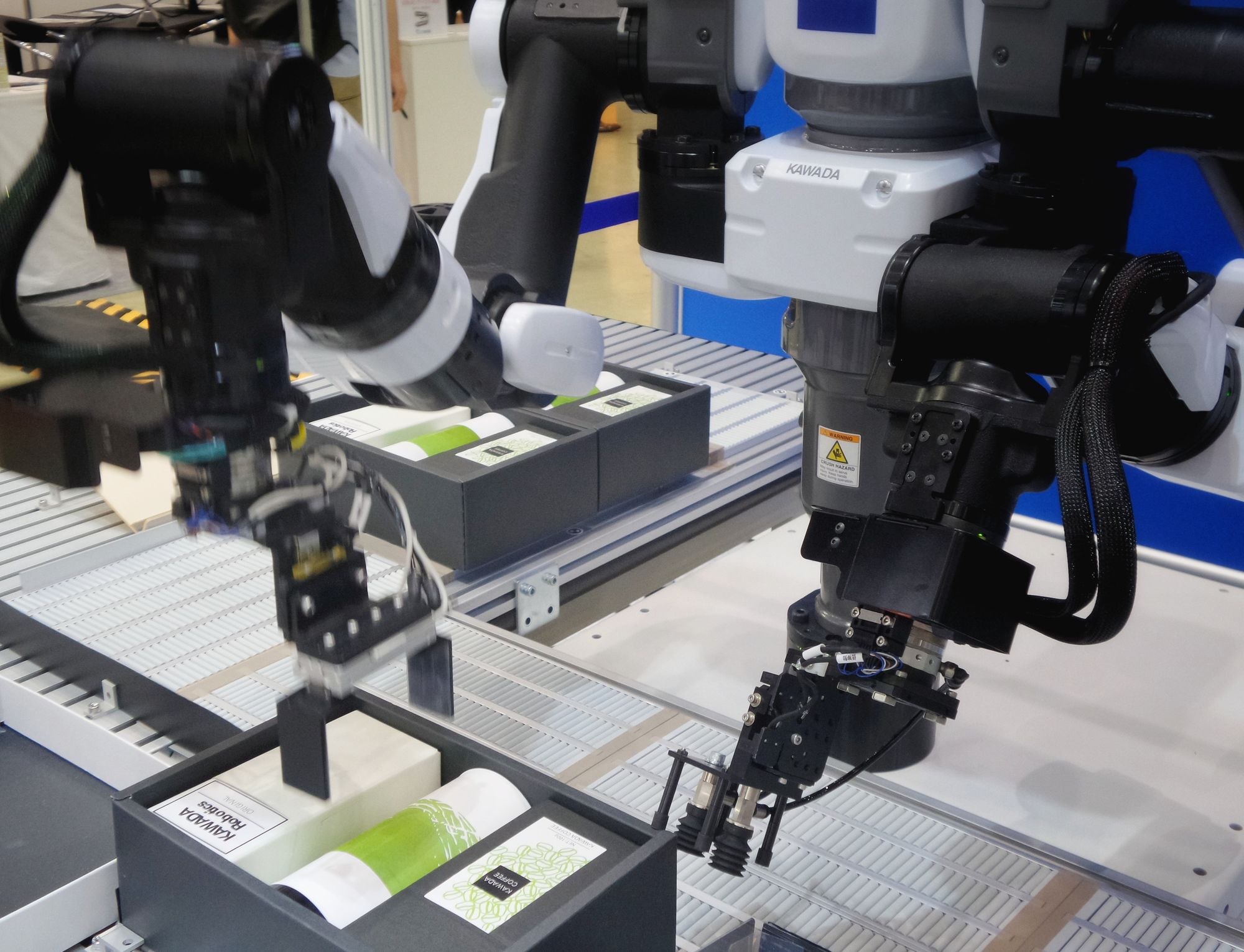