In today's fast-paced manufacturing industry, efficiently scheduling production has become increasingly crucial for businesses to remain competitive. Traditional static scheduling techniques, which set and adhere to a predetermined production plan, are often flexible and need more agility to adapt to changing conditions.
Dynamic scheduling, on the other hand, uses real-time data and advanced algorithms to make adjustments to the production schedule as needed, leading to greater efficiency and flexibility.
According to a report by Grand View Research, the global manufacturing execution system market size was valued at USD 8.8 billion in 2020 and is expected to grow at a compound annual growth rate (CAGR) of 11.2% from 2021 to 2028. This growth is driven in part by the increasing adoption of dynamic scheduling techniques by manufacturing companies.
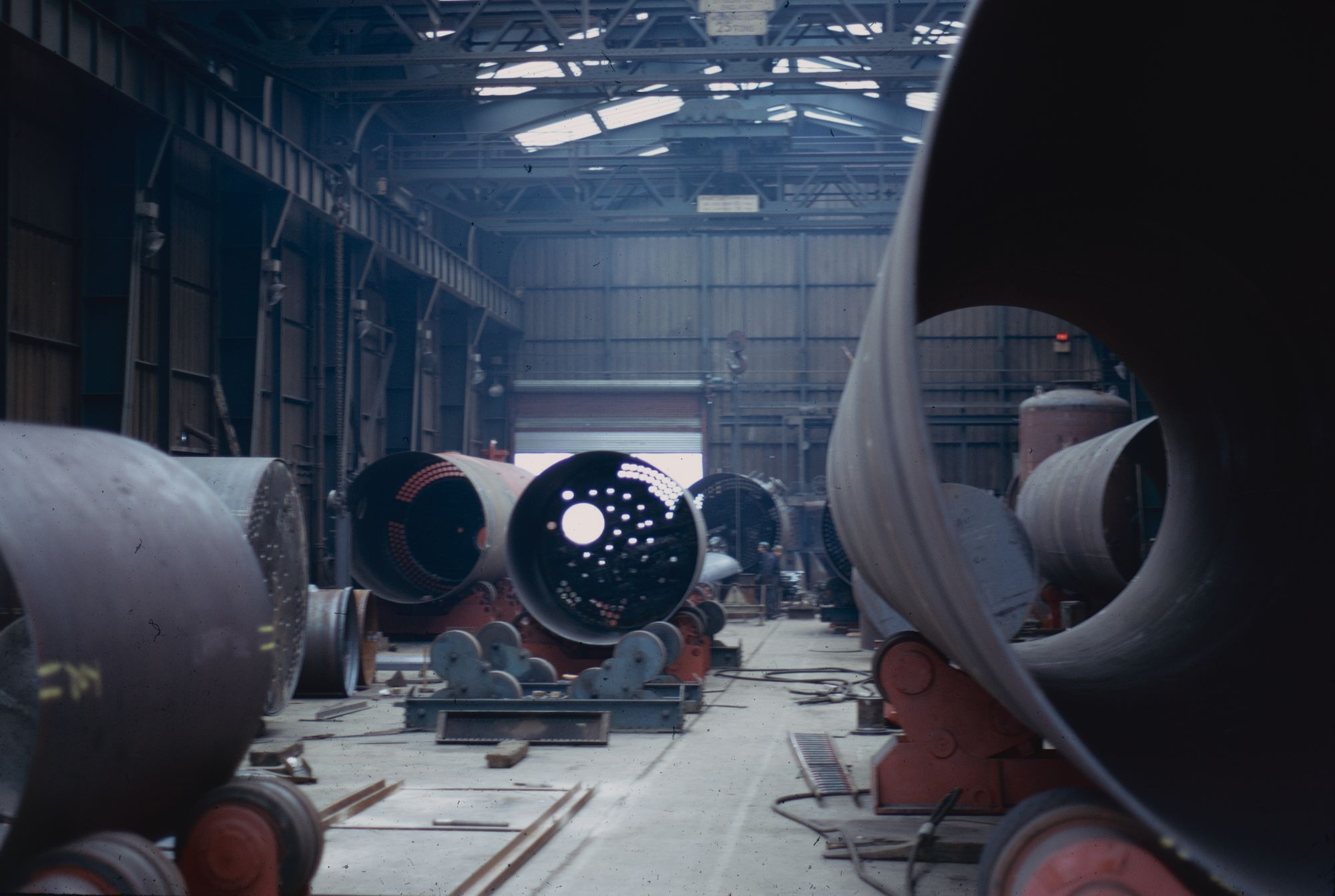
This article will explore the benefits of dynamic scheduling in modern manufacturing and discuss how it can be implemented in your business to improve efficiency and increase profitability. We will also discuss the challenges that come with implementing a dynamic scheduling system and offer strategies for overcoming them.
By the end of this article, you will clearly understand how dynamic scheduling can transform your manufacturing operations and position your business for success in the years to come.
Here's what we shall cover in this post:
- What Is Dynamic Scheduling?
- The History of Scheduling in Manufacturing
- Traditional Scheduling Challenges and Limitations
- Benefits of Dynamic Scheduling for Manufacturers
- How Dynamic Scheduling Differs From Traditional Scheduling
- Key Components of Dynamic Scheduling Systems
- The Role of Data and Analytics in Dynamic Scheduling
- Challenges and Considerations When Implementing Dynamic Scheduling
- Future Trends in Dynamic Scheduling Technology
- Best Practices for Dynamic Scheduling Implementation and Adoption
- Conclusion
- Key Takeaways
What Is Dynamic Scheduling?
Dynamic scheduling is an approach to production planning and scheduling that adjusts in real time based on current conditions and changing demands.
- Dynamic scheduling uses real-time data and predictive algorithms to make scheduling decisions, allowing for quick and flexible adjustments to production schedules.
- Dynamic scheduling takes into account a wide range of factors, including inventory levels, production capacity, machine downtime, and customer demand.
- With dynamic scheduling, production schedules can be adjusted quickly to respond to changes in demand, supply chain disruptions, or other unexpected events.
- Dynamic scheduling aims to improve efficiency, reduce waste, and increase customer satisfaction by ensuring that products are delivered on time and at the right quality level.
Dynamic scheduling also allows for greater flexibility in scheduling and resource allocation. Instead of being locked into a fixed schedule, businesses can adjust production schedules and allocate resources based on real-time information and analysis, maximizing productivity and minimizing downtime.
However, dynamic scheduling also requires a significant investment in technology and software, as well as employee training and support. It may also require a cultural shift within the organization, as employees may need to adjust to a more agile and responsive approach to production scheduling.
The History of Scheduling in Manufacturing
Scheduling has been an essential part of manufacturing since the beginning of the Industrial Revolution, but the methods and techniques used have evolved over time. Here is a brief history of scheduling in manufacturing:
Early Scheduling Techniques
In the early days of manufacturing, scheduling was a simple process of determining what needed to be produced and assigning workers to complete the task. This was done using manual records and often relied on the supervisor's experience to ensure that production was running smoothly.
Here are some of the early scheduling techniques used in manufacturing:
- Gantt Charts: Developed by Henry Gantt in the early 1900s, these charts were used to schedule and track the progress of production tasks. The charts were made up of horizontal bars representing the duration of each task and were used to determine the order in which tasks were performed.
- Critical Path Method: This technique was developed in the late 1950s to help with project management but was later adapted for use in manufacturing. The method involves breaking down a project into smaller tasks and determining the order in which they need to be completed. The critical path is then identified, which is the longest sequence of tasks that must be completed before the project can be finished.
- Line Balancing: This technique involves dividing a production line into workstations and assigning tasks to each station. The goal is to balance the workload across all stations and eliminate bottlenecks, which can improve productivity and reduce lead times.
- Kanban: Developed in Japan in the 1950s, this technique involves using a system of cards to control the flow of materials and information throughout the production process. Each card represents a specific task or product and is used to signal when more materials are needed.
MRP and MRP II
The introduction of Material Requirements Planning (MRP) and Manufacturing Resource Planning (MRP II) in the 1960s and 70s marked a significant step forward in scheduling techniques.
These computer-based systems used data inputs such as customer orders, inventory levels, and machine capacity to create a production schedule. MRP and MRP II were widely adopted in the manufacturing industry and are still used today.
Lean Manufacturing and Just-In-Time
In the 1980s, the introduction of Lean Manufacturing and Just-In-Time (JIT) principles led to a shift in scheduling techniques. These methodologies emphasized the reduction of waste and the optimization of production processes.
Scheduling in Lean Manufacturing and JIT environments focuses on small batch sizes and frequent changes to production schedules to respond to customer demand.
Advanced Scheduling Techniques
In recent years, advanced scheduling techniques such as Finite Capacity Scheduling (FCS), Theory of Constraints (TOC), and Quick Response Manufacturing (QRM) have emerged. These techniques use advanced algorithms and data analysis to create more accurate and efficient production schedules.
- Machine Learning-based Scheduling: Machine learning algorithms can be used to optimize production scheduling based on a wide range of factors, including machine performance, product demand, and resource availability. By analyzing historical data and making predictions about future conditions, machine learning models can generate highly accurate schedules that minimize downtime and maximize throughput.
- Constraint-based Scheduling: Constraint-based scheduling takes into account a wide range of constraints that impact production, such as resource availability, material availability, and production capacity. Manufacturers can reduce waste, minimize downtime, and increase efficiency by using sophisticated algorithms to optimize schedules based on these constraints.
- Finite Capacity Scheduling: Finite capacity scheduling is a method of scheduling production that takes into account the finite capacity of resources such as machines, labor, and materials. Manufacturers can prevent bottlenecks and ensure production processes run smoothly by ensuring that production schedules are aligned with the available resources.
- Just-in-Time Scheduling: Just-in-time scheduling is a production strategy that aims to minimize inventory and reduce waste by producing goods only when they are needed. Manufacturers can minimize inventory costs and increase efficiency by using real-time data to anticipate demand and adjust production schedules accordingly.
- Theory of Constraints Scheduling: The Theory of Constraints (TOC) is a management philosophy that focuses on identifying and resolving bottlenecks in production processes. TOC scheduling uses sophisticated algorithms to identify these bottlenecks and optimize production schedules to reduce their impact on overall throughput.
- Critical Chain Scheduling: Critical chain scheduling is a project management technique that focuses on identifying and managing the most vital tasks in a project. By using advanced algorithms to optimize scheduling around these critical tasks, manufacturers can increase efficiency and reduce the risk of delays.
- Agile Scheduling: Agile scheduling is an iterative production scheduling approach emphasizing flexibility and adaptability. By breaking down production processes into smaller, more manageable tasks, manufacturers can respond quickly to changes in demand or resource availability while minimizing waste and maximizing efficiency.
Industry 4.0 and Smart Manufacturing
The latest trend in manufacturing is Industry 4.0, which incorporates technologies such as the Internet of Things (IoT), Artificial Intelligence (AI), and Big Data analytics. These technologies enable real-time data collection and analysis, which can be used to optimize production schedules and improve overall efficiency.
Here are some points that explain Industry 4.0 and Smart Manufacturing in more detail:
- Industry 4.0 is characterized by the integration of modern technology and data to create a highly automated and interconnected manufacturing ecosystem. This includes the use of sensors, cloud computing, artificial intelligence, and the Internet of Things (IoT) to collect and analyze data from different parts of the manufacturing process.
- Smart Manufacturing, on the other hand, encompasses a broader range of technologies and practices that are designed to make manufacturing more efficient and productive. This includes the use of advanced analytics, predictive maintenance, and digital twins to improve production planning and execution.
- One of the key benefits of Industry 4.0 and Smart Manufacturing is the ability to create highly optimized manufacturing processes that are more flexible and adaptable to changing market conditions. This is achieved through the use of real-time data and analytics, which enable manufacturers to quickly identify and respond to issues and opportunities in the production process.
- The use of advanced technologies in manufacturing is also driving a shift towards more sustainable and eco-friendly production processes. This includes using renewable energy sources, smart energy management systems, and optimizing manufacturing processes to reduce waste and minimize the environmental impact of production.
- Industry 4.0 and Smart Manufacturing are profoundly impacting the manufacturing industry, enabling manufacturers to improve productivity, reduce costs, and create more innovative and sustainable products. This is driving a new manufacturing era focused on integrating technology and data to create more efficient and effective production processes.
As new technologies emerge, the manufacturing industry will continue to adopt more sophisticated scheduling techniques to optimize production processes and increase efficiency.
Traditional Scheduling Challenges and Limitations
Traditional scheduling in manufacturing refers to the manual or semi-manual methods of scheduling production activities. While this approach was suitable in the past, as manufacturing became more complex, traditional scheduling faced many challenges and limitations.
These challenges can impact a manufacturing operation's efficiency, productivity, and profitability. Some of the traditional scheduling challenges and limitations include:
- Limited Flexibility: Traditional scheduling methods rely on predefined schedules, which can be inflexible and unable to adapt to changing conditions or unexpected events. The lack of flexibility can lead to production delays, inefficiencies, and missed delivery dates.
- Poor Communication: Traditional scheduling methods often rely on paper-based or manual systems, which can result in communication breakdowns and errors. These communication issues can lead to incorrect information being shared among team members, leading to further delays and inefficiencies.
- Inaccurate Data: Traditional scheduling methods often rely on outdated data, which can lead to inaccurate production forecasts and schedules. With accurate data, predicting demand, allocating resources effectively, and meeting customer expectations can be easy.
- Inefficient Resource Allocation: Traditional scheduling methods may not optimize resource allocation, leading to over or underutilization of resources. Overutilization of resources can lead to increased costs and reduced efficiency, while underutilization of resources can lead to missed opportunities and revenue loss.
- Limited Visibility: Traditional scheduling methods can lack visibility into the production process, making tracking progress and identifying potential issues difficult. Without visibility, making informed decisions and optimizing the production process can be challenging.
- Time-Consuming: Traditional scheduling methods can be time-consuming, requiring significant manual effort to create and maintain schedules. This can take time away from other essential tasks and limit productivity.
- Lack of Integration: Traditional scheduling methods may not integrate well with other systems, such as inventory management or customer relationship management. The lack of integration can lead to data silos, duplication of effort, and inefficient processes.
Many manufacturing operations are adopting modern scheduling solutions that leverage technology, automation, and data analytics to overcome these challenges and limitations. These solutions can improve flexibility, communication, data accuracy, resource allocation, visibility, and integration, leading to a more efficient and profitable operation.
Benefits of Dynamic Scheduling for Manufacturers
Here are some benefits of dynamic scheduling for manufacturers:
- Increased Flexibility: One of the primary benefits of dynamic scheduling is its increased flexibility to manufacturers. With the ability to adjust production schedules in real time, manufacturers can quickly respond to changes in demand, supply chain disruptions, and unforeseen events. This allows them to optimize resources and reduce lead times, resulting in increased customer satisfaction and profitability.
- Improved Resource Utilization: Dynamic scheduling enables manufacturers to make the most efficient use of their resources, including labor, equipment, and raw materials. Manufacturers can optimize resource utilization, minimize downtime, and reduce waste by adjusting production schedules based on real-time demand and capacity data.
- Enhanced Productivity: Dynamic scheduling helps manufacturers to optimize their production processes, resulting in increased productivity. With the ability to adjust schedules in real time, manufacturers can avoid production bottlenecks and reduce cycle times. This leads to increased throughput and reduced lead times, which can result in improved profitability.
- Better Decision Making: Dynamic scheduling provides manufacturers with real-time data on production performance, enabling them to make informed decisions quickly. This includes production efficiency, lead times, cycle times, and resource utilization data. By having access to this data, manufacturers can make better decisions on production schedules, resource allocation, and process improvements.
- Improved Customer Satisfaction: Dynamic scheduling enables manufacturers to respond quickly to changing customer needs, resulting in increased customer satisfaction. By reducing lead times and improving on-time delivery rates, manufacturers can improve customer loyalty and reduce the risk of lost business.
- Increased Competitiveness: By adopting dynamic scheduling, manufacturers can gain a competitive advantage over their competitors. With the ability to adapt quickly to changing market conditions, manufacturers can meet customer needs more effectively and efficiently, resulting in increased profitability and market share.
By increasing flexibility, improving resource utilization, enhancing productivity, facilitating better decision-making, improving customer satisfaction, and increasing competitiveness, dynamic scheduling is a critical tool for modern manufacturers.
How Dynamic Scheduling Differs From Traditional Scheduling
Traditional scheduling is a static approach where a fixed schedule is created in advance based on projected demand and production capacity.
On the other hand, dynamic scheduling is a real-time approach that continually adjusts production schedules based on changing factors such as customer orders, machine availability, and inventory levels.
Flexibility
Dynamic scheduling offers greater flexibility than traditional scheduling. In traditional scheduling, it is difficult to make changes once a schedule is set. With dynamic scheduling, adjustments can be made in real time as changes occur. This allows for a more agile and responsive production process.
Real-Time Data
Dynamic scheduling relies on real-time data to make production decisions. This means that production managers have access to up-to-date information on inventory levels, machine availability, and customer demand.
In traditional scheduling, decisions are often made based on historical data and assumptions, which can lead to inaccurate production planning.
Integration
Dynamic scheduling is often integrated with other manufacturing systems, such as enterprise resource planning (ERP) and manufacturing execution systems (MES). This integration allows for a seamless flow of information and real-time communication between different departments in the manufacturing process.
Traditional scheduling, on the other hand, is often isolated from other systems, leading to silos of information and slower decision-making.
Optimization
Dynamic scheduling uses optimization algorithms to create the most efficient production schedule possible. These algorithms take into account factors such as machine availability, setup times, and production constraints to create an optimal production plan.
Traditional scheduling, on the other hand, is often based on rules of thumb and experience, which can lead to less efficient production processes.
Collaboration
Dynamic scheduling encourages collaboration between different departments in the manufacturing process. Production managers, sales teams, and customer service representatives can all work together to create a production plan that meets the needs of the customer while optimizing production efficiency.
Traditional scheduling often results in silos of information and a lack of collaboration between departments.
Cost Savings
Dynamic scheduling can result in significant cost savings for manufacturers. Manufacturers can reduce costs and increase profitability by optimizing production schedules, reducing downtime, and minimizing inventory levels. Traditional scheduling often results in higher inventory levels, longer lead times, and more downtime, all of which increase costs.
Better Customer Service
Dynamic scheduling can improve customer service by providing faster lead times, more accurate order fulfillment, and better communication with customers.
By using real-time data to adjust production schedules, manufacturers can quickly and accurately meet customer demand. Traditional scheduling often leads to longer lead times and less accurate order fulfillment, which can result in dissatisfied customers.
By adopting a dynamic scheduling approach, manufacturers can improve their production processes, increase efficiency, and ultimately increase profitability.
Key Components of Dynamic Scheduling Systems
Here are some key components of dynamic scheduling systems:
Real-time data collection and analysis
Dynamic scheduling systems rely on real-time data collection and analysis to make informed decisions regarding production scheduling. Data can be collected from various sources, such as sensors, ERP systems, and production equipment.
The data is then analyzed to determine production bottlenecks, capacity constraints, and other variables that can impact production.
- The Importance of Real-Time Data: Real-time data is critical for dynamic scheduling since it allows manufacturers to respond to changes in production environments as they occur. This data includes machine performance, operator productivity, material availability, and more information.
- The Role of Sensors and IoT: Sensors and IoT devices are essential for collecting real-time data in modern manufacturing environments. These devices can track the status of equipment and materials, measure performance, and identify bottlenecks or issues that require attention.
- Real-Time Data Analytics: Once data is collected, it must be analyzed in real-time to provide insights that can be used to optimize production. Real-time analytics can help manufacturers identify inefficiencies, predict maintenance issues, and improve overall performance.
Capacity planning and scheduling algorithms
Capacity planning and scheduling algorithms are essential components of dynamic scheduling systems. These algorithms optimize production schedules based on available capacity, demand, and other constraints.
The algorithms take into account factors such as production lead times, inventory levels, and machine availability to create optimized production schedules.
Benefits of Capacity Planning and Scheduling Algorithms
Capacity planning and scheduling algorithms can bring significant benefits to a manufacturing operation. These benefits include:
- Increased efficiency: By optimizing production schedules based on real-time data, manufacturers can reduce downtime, improve machine utilization, and increase overall production efficiency.
- Improved customer service: Dynamic scheduling enables manufacturers to respond quickly to changes in customer demand, ensuring that orders are completed on time and to the required quality standards.
- Better resource management: Capacity planning and scheduling algorithms can help manufacturers identify underutilized resources, reduce waste, and allocate resources more efficiently.
- Cost savings: By optimizing production schedules, manufacturers can reduce labor costs, minimize machine downtime, and reduce inventory costs.
- Improved quality: Dynamic scheduling can help manufacturers identify and eliminate bottlenecks in the production process, resulting in better product quality and consistency.
Advanced planning and scheduling (APS) software
Dynamic scheduling systems typically use advanced planning and scheduling (APS) software to create and manage production schedules. APS software provides a centralized platform for managing production data, scheduling, and other production-related tasks.
The software can be customized to meet the specific needs of a manufacturing facility and can integrate with other systems, such as ERP and MES systems.
- APS software uses advanced algorithms to optimize scheduling decisions, taking into account multiple constraints and factors that impact production, such as capacity, material availability, and demand variability.
- By providing a detailed and accurate view of the production process, APS software enables manufacturers to make better decisions about allocating resources and managing their production workflows.
- APS software can help manufacturers achieve greater visibility into their supply chain, enabling them to anticipate potential bottlenecks and take corrective action before they occur.
- One of the key advantages of APS software is its ability to perform "what-if" analysis, allowing manufacturers to simulate different scenarios and evaluate the impact of changes in production schedules or other variables.
- APS software is typically integrated with other enterprise systems, such as Enterprise Resource Planning (ERP) and Customer Relationship Management (CRM) systems, to provide a seamless flow of data and information across the organization.
- With APS software, manufacturers can achieve greater agility and responsiveness in their production processes, enabling them to adapt to changes in demand or production conditions quickly.
- The adoption of APS software is a significant investment for manufacturers, but the benefits can be substantial, including increased efficiency, reduced costs, and improved customer satisfaction.
- The most effective use of APS software requires a strong commitment to data quality and accuracy and a willingness to monitor and adjust production processes to optimize results continuously.
- To successfully implement APS software, manufacturers should work closely with their software vendors and engage in ongoing training and support to ensure that the software is being used effectively and to its full potential.
Machine learning and artificial intelligence (AI)
Machine learning and artificial intelligence (AI) are becoming increasingly crucial in dynamic scheduling systems. These technologies can help identify production bottlenecks, optimize production schedules, and predict maintenance needs. Machine learning algorithms can also be used to analyze historical data and make predictions about future production needs.
Benefits of Machine Learning and AI in Dynamic Scheduling
Machine learning and AI can improve dynamic scheduling in several ways, including:
- Better prediction: Machine learning algorithms can analyze large amounts of data to predict outcomes, such as how long a specific production process will take. This information can then be used to optimize schedules and improve production efficiency.
- Real-time decision-making: AI systems can analyze data in real time and make decisions based on the current state of production processes. This enables manufacturers to respond quickly to changes and minimize downtime.
- Continuous improvement: Machine learning algorithms can learn from data over time, improving their predictions and decision-making abilities continuously. This can lead to even greater efficiency gains over time.
Communication and collaboration tools
Effective communication and collaboration are critical for successful production scheduling. Dynamic scheduling systems often include communication and collaboration tools that allow production managers, operators, and other stakeholders to communicate in real time.
These tools can help ensure that everyone is on the same page regarding production schedules and can help identify and resolve scheduling conflicts quickly.
- Collaboration platforms: Collaborative platforms are digital tools that help team members communicate and share information. They allow team members to access real-time data, collaborate on tasks, and share insights. Tools like Microsoft Teams, Slack, and Asana are popular examples of collaboration platforms.
- Electronic dashboards: Electronic dashboards provide real-time information to all team members, making tracking production progress and identifying bottlenecks easier. Dashboards can display information about inventory levels, equipment utilization, and production schedules. Tools like Power BI and Tableau are examples of electronic dashboards.
- Mobile devices: Mobile devices allow team members to access information and collaborate on the go. They can be used to access real-time production data, communicate with team members, and receive notifications about schedule changes. Many manufacturing companies use mobile apps that allow workers to view schedules, track time, and report production progress.
- Video conferencing: Video conferencing effectively brings remote team members together for meetings and discussions. It can be used to discuss production issues, collaborate on solutions, and review progress. Video conferencing tools like Zoom and Google Meet have become increasingly popular in recent years.
- Email and messaging: Email and messaging are still essential tools for communication in manufacturing. They can be used to communicate with team members, provide updates on production progress, and share information about schedule changes. Email and messaging tools like Outlook and WhatsApp are commonly used in manufacturing.
Continuous improvement and feedback loops
Continuous improvement and feedback loops are essential components of dynamic scheduling systems. These systems are designed to be agile and flexible, allowing for continuous improvement and adjustment based on production feedback. This approach can help identify areas for improvement and optimize production processes over time.
Real-time data collection and analysis, capacity planning and scheduling algorithms, advanced planning and scheduling software, machine learning and artificial intelligence, communication and collaboration tools, and continuous improvement and feedback loops are key components of dynamic scheduling systems.
By implementing these systems, manufacturers can optimize their production schedules and gain a competitive advantage in today's fast-paced manufacturing environment.
Real-Time Scheduling and Re-Scheduling Capabilities
Here are some key points to consider about real-time scheduling and re-scheduling capabilities:
Real-time scheduling: Real-time scheduling allows manufacturers to manage and monitor production in real time, enabling them to identify and respond to production issues quickly.
With real-time scheduling, manufacturers can view the status of production in real-time, monitor machine utilization and throughput, and adjust schedules as needed.
Re-scheduling capabilities: Re-scheduling capabilities enable manufacturers to adjust production schedules in real-time to respond to changes in demand, capacity, or other factors that impact production.
This allows manufacturers to optimize production schedules to minimize downtime, reduce costs, and improve efficiency.
Benefits of real-time scheduling and re-scheduling: Real-time scheduling and re-scheduling capabilities provide a number of benefits to manufacturers, including:
- Improved responsiveness: Real-time scheduling enables manufacturers to quickly respond to changes and optimize production schedules to meet changing demands or unexpected issues.
- Increased efficiency: Real-time scheduling and re-scheduling capabilities allow manufacturers to optimize production schedules to reduce downtime, improve throughput, and increase efficiency.
- Improved customer service: Real-time scheduling enables manufacturers to quickly adjust production schedules to meet changing customer demands, resulting in better customer service and increased customer satisfaction.
- Reduced costs: Real-time scheduling and re-scheduling capabilities enable manufacturers to optimize production schedules to minimize downtime, reduce waste, and reduce costs.
Key components of real-time scheduling and re-scheduling: Real-time scheduling and re-scheduling capabilities require a number of key components, including:
- Real-time data collection: Real-time scheduling requires real-time data collection to enable manufacturers to monitor production in real-time and respond quickly to changes.
- Data analytics: Data analytics is critical to real-time scheduling and re-scheduling, enabling manufacturers to identify patterns and trends in production data and optimize production schedules accordingly.
- Automated decision-making: Real-time scheduling and re-scheduling often require automated decision-making capabilities, enabling manufacturers to adjust production schedules based on real-time data and analytics.
- Integration with other systems: Real-time scheduling and re-scheduling systems often need to be integrated with other manufacturing systems, such as ERP and MES systems, to enable real-time data collection and decision-making.
By enabling manufacturers to respond to changes quickly, optimize production schedules in real-time, and improve efficiency and customer service, real-time scheduling and re-scheduling capabilities provide significant benefits to manufacturers.
Impact of Dynamic Scheduling on Production Efficiency and Throughput
Here are some key points to consider about the impact of dynamic scheduling on production efficiency and throughput:
- Improved Production Planning: Dynamic scheduling allows manufacturers to be more responsive to changing customer demands and production variables such as material availability, production capacity, and machine downtime. This makes it easier to plan production schedules that are optimized for efficiency and throughput.
- Reduced Downtime: Dynamic scheduling helps manufacturers reduce downtime by enabling them to quickly adjust production schedules when machines break down or require maintenance. This means that production processes can be optimized to minimize downtime and maximize throughput.
- Increased Resource Utilization: Dynamic scheduling allows manufacturers to optimize the use of resources such as machines, labor, and materials. This means that manufacturers can operate at maximum capacity, thereby increasing throughput and reducing costs.
- Improved Delivery Times: Dynamic scheduling helps manufacturers improve delivery times by ensuring that production processes are optimized for maximum efficiency. This means that manufacturers can deliver products to customers faster, which helps them stay competitive in the marketplace.
- Better Quality Control: Dynamic scheduling allows manufacturers to monitor production processes in real-time so that quality control measures can be implemented more effectively. This results in fewer defects and less waste, which helps manufacturers reduce costs and improve customer satisfaction.
- Enhanced Agility: Dynamic scheduling enables manufacturers to respond more quickly to changing market conditions and customer demands. This means that manufacturers can quickly adjust production schedules to meet changing requirements, which helps them stay competitive in the marketplace.
By leveraging real-time data and advanced algorithms, dynamic scheduling enables manufacturers to optimize production processes for maximum efficiency, reduce downtime, increase resource utilization, improve delivery times, enhance quality control, and stay agile in responding to changing market conditions and customer demands.
As such, dynamic scheduling has become essential to modern manufacturing operations.
The Role of Data and Analytics in Dynamic Scheduling
The manufacturing industry is becoming increasingly data-driven, and dynamic scheduling is no exception. In fact, data and analytics play a crucial role in the success of a dynamic scheduling system. Here are some key points to consider:
- Data collection: To implement dynamic scheduling, it's crucial to gather data on all aspects of the manufacturing process, including equipment availability, inventory levels, order specifications, and more. This data can come from a variety of sources, including IoT sensors, production software, and manual input.
- Real-time data analysis: Once data is collected, it needs to be analyzed in real-time to inform scheduling decisions. Dynamic scheduling systems use algorithms and machine learning to process and analyze data, providing a real-time picture of production status and capacity.
- Predictive analytics: In addition to real-time data analysis, dynamic scheduling systems can use predictive analytics to forecast production needs and potential bottlenecks. This allows manufacturers to proactively adjust scheduling to ensure optimal efficiency.
- Optimization algorithms: Dynamic scheduling systems also use optimization algorithms to determine the most efficient production schedule based on available resources and constraints. These algorithms consider factors such as order priority, equipment availability, and labor requirements.
- Integration with other systems: To fully leverage the benefits of data and analytics in dynamic scheduling, it's essential to integrate scheduling systems with other manufacturing software and systems, such as inventory management and quality control.
Importance of Cross-Functional Collaboration in Dynamic Scheduling
Here are some reasons why cross-functional collaboration is crucial for successful dynamic scheduling:
Understanding the entire production process: Dynamic scheduling requires a comprehensive understanding of the whole production process, including inventory levels, production capacity, lead times, and machine availability.
Collaboration across different departments enables teams to share information and insights, ensuring that everyone has a clear picture of the production process.
Identifying potential bottlenecks: With cross-functional collaboration, teams can identify potential bottlenecks in the production process and work together to resolve them before they become major issues.
For example, the production team may identify a bottleneck in the assembly process, and the logistics team may propose a solution that involves adjusting the shipping schedule to alleviate the bottleneck.
Aligning production with customer demand: Cross-functional collaboration allows teams to align production with customer demand. The sales team can provide insights into customer demand, while the production team can determine the feasibility of meeting that demand.
By working together, teams can optimize production schedules to meet customer demand while minimizing waste and excess inventory.
Reducing lead times: Dynamic scheduling can help reduce lead times by enabling teams to respond quickly to changes in customer demand.
With cross-functional collaboration, teams can identify opportunities to streamline the production process, reduce waste, and improve efficiency, ultimately leading to faster lead times and improved customer satisfaction.
Challenges and Considerations When Implementing Dynamic Scheduling
Data Management
One of the biggest challenges when implementing dynamic scheduling is data management. Dynamic scheduling systems rely heavily on accurate and timely data inputs to function properly.
This includes data related to inventory levels, production capacity, and customer demand. Manufacturers need to have a robust data management system to ensure that the data fed into the dynamic scheduling system is accurate and up-to-date.
Data accuracy: One of the primary challenges of dynamic scheduling is ensuring that the data being used is accurate and up-to-date. This includes data related to orders, inventory, resources, and production processes.
Even small inaccuracies can significantly impact the scheduling system's effectiveness, leading to delays, rework, and increased costs. To address this challenge, manufacturers can invest in tools and processes to ensure data accuracy, such as data validation, verification protocols, and automated data collection systems.
Data integration: In many manufacturing environments, data is stored in multiple systems and formats, including ERP systems, production databases, and spreadsheets. This can make it difficult to integrate data across systems and ensure that all relevant data is available for scheduling purposes.
To address this challenge, manufacturers can invest in data integration tools and processes that enable seamless data exchange between systems.
Data volume: With the increasing volume of data generated by modern manufacturing processes, managing and processing this data can be a significant challenge.
This includes not only the volume of data but also the complexity of the data, which may include unstructured data such as images and sensor data. Manufacturers can invest in data management tools and technologies such as big data analytics and cloud computing to address this challenge.
Data security: In an age of increasing cybersecurity threats, data security is a critical concern for manufacturers. This includes not only protecting sensitive customer data but also ensuring the security of manufacturing data.
To address this challenge, manufacturers can invest in security technologies such as firewalls, intrusion detection systems, and encryption and implement robust data governance and access control policies.
Data governance: Effective data management requires clear policies and processes for data governance, including data ownership, access control, and data quality standards. This can be a significant challenge for manufacturers, particularly those operating in complex supply chain environments.
To address this challenge, manufacturers can invest in data governance frameworks that enable clear roles and responsibilities for data management and provide guidelines and processes for data quality control and standardization.
Data analysis: Finally, one of the key challenges of dynamic scheduling is making sense of the data generated by the system. This includes analyzing historical data to identify patterns and trends and real-time data analysis to enable rapid decision-making.
To address this challenge, manufacturers can invest in data analytics tools and technologies such as machine learning and artificial intelligence and build data analysis capabilities within their teams.
Organizational Alignment
Another challenge that manufacturers may face when implementing dynamic scheduling is organizational alignment. Dynamic scheduling requires cross-functional collaboration between various departments, including production, sales, and finance.
Manufacturers need to ensure that all departments are aligned and working towards the same goals to ensure the success of the dynamic scheduling implementation.
Lack of understanding of the benefits of dynamic scheduling: One of the most significant challenges that organizations face when implementing dynamic scheduling is that different departments may not clearly understand the benefits it can bring.
For example, production and inventory management teams may see it as a tool for increasing throughput and reducing inventory costs, while the finance department may be more interested in its impact on overall profitability.
Siloed departmental approaches: Departments within a manufacturing organization can often have their own priorities and objectives, leading to siloed scheduling approaches. For example, the production team may prioritize the production schedule, while the sales team may prioritize meeting customer orders.
These siloed approaches can create bottlenecks, reduce collaboration and communication, and negatively impact the overall efficiency of the scheduling process.
Communication breakdowns: Communication breakdowns can occur between different departments, particularly when they have different priorities and objectives. For example, the production team may not communicate scheduling changes to the inventory team, leading to stockouts or overstock situations.
Such breakdowns can cause delays, missed deadlines, and increased costs.
Resistance to change: Resistance to change is a common challenge in any organization. When implementing dynamic scheduling, some employees may resist the change because they are accustomed to the traditional scheduling approach or feel threatened by the new technology.
Resistance to change can slow down the implementation process and reduce the overall effectiveness of the dynamic scheduling system.
Lack of cross-functional collaboration: Collaboration between different departments is critical to the success of dynamic scheduling. However, many organizations struggle to foster a culture of cross-functional collaboration.
Departments may be reluctant to share information, or there may be a lack of trust between them. This lack of collaboration can result in inefficiencies, redundancies, and errors in the scheduling process.
Change Management
Dynamic scheduling often requires changes to existing processes and workflows. This can be a challenge for manufacturers who are used to traditional scheduling methods. Manufacturers need to prepare for the changes that come with dynamic scheduling and ensure that all stakeholders are on board with the changes.
This may involve providing training and support to employees to help them adapt to the new processes.
Technology Integration
Dynamic scheduling systems rely on technology to function properly. Manufacturers need to ensure that their existing technology infrastructure is capable of supporting dynamic scheduling. This may require additional investments in hardware, software, and IT resources.
Manufacturers also need to ensure that their dynamic scheduling system is integrated with other technology systems, such as inventory management and customer relationship management (CRM) systems.
- Legacy Systems: One of the main challenges of technology integration in dynamic scheduling is the presence of legacy systems. Older systems may not be compatible with new technologies, and integrating them can be a difficult and expensive process. This can lead to delays and increased costs during the implementation phase.
- Data Integration: Another challenge of technology integration in dynamic scheduling is data integration. Different systems may use different data formats or have different data requirements. This can make it difficult to integrate data from multiple systems into a single, unified view. Data integration challenges can lead to errors in scheduling and a lack of visibility into production processes.
- IT Infrastructure: The infrastructure required to support dynamic scheduling can also be a challenge. This includes hardware, software, and networking infrastructure. Building and maintaining the necessary IT infrastructure can be expensive and time-consuming and may require specialized skills that are not available in-house.
- Interoperability: Dynamic scheduling requires the integration of multiple technologies and systems. Ensuring that these systems can communicate with each other and work together seamlessly can be a significant challenge. This can require the development of custom interfaces or the use of middleware to facilitate communication between systems.
- Security: Integrating new technologies into existing systems can also introduce security risks. Dynamic scheduling systems may require access to sensitive data or production processes, and ensuring the security of this data is critical. This can require the implementation of new security measures or the modification of existing security policies.
Flexibility
One of the key benefits of dynamic scheduling is its ability to adapt to changing circumstances. However, this also means that manufacturers need to be prepared for unexpected changes and disruptions to the production process. This requires a high level of flexibility and adaptability, both in terms of processes and personnel.
Diverse Production Lines: In a typical manufacturing environment, a wide range of products are being produced simultaneously, each with its own unique requirements. This diversity can make implementing a scheduling system that can handle all the different products and their specific needs challenging.
To address this challenge, manufacturers can segment their production lines based on product similarities and then implement a dynamic scheduling system for each segment.
Variability in Demand: The demand for products can vary significantly based on a variety of factors, including seasonality, market trends, and even the weather. This variability can make it difficult to schedule production efficiently.
To address this challenge, manufacturers can use historical data and predictive analytics to forecast demand and adjust their production schedules accordingly.
Unplanned Disruptions: Unplanned disruptions, such as machine breakdowns or material shortages, can significantly impact production schedules. A dynamic scheduling system must be flexible enough to adjust quickly to these disruptions and keep production on track.
One way to address this challenge is by implementing a real-time monitoring system that can detect issues as they arise and automatically adjust the production schedule accordingly.
Dynamic scheduling can be a powerful tool for manufacturers looking to optimize their production processes. However, it is important to recognize that implementing dynamic scheduling is not without its challenges and considerations.
Manufacturers need to be prepared to address these challenges and considerations to ensure the success of their dynamic scheduling implementation.
Future Trends in Dynamic Scheduling Technology
As technology continues to evolve, there are several emerging trends that are expected to shape the future of dynamic scheduling.
Artificial Intelligence and Machine Learning
Artificial intelligence (AI) and machine learning (ML) are expected to play a significant role in the future of dynamic scheduling. By analyzing vast amounts of data, AI and ML algorithms can identify patterns and insights that can help optimize production schedules, improve predictive maintenance, and reduce downtime.
With AI and ML, manufacturers can achieve even greater levels of automation and real-time decision-making, enabling them to adapt to changing market conditions and customer demands quickly.
Internet of Things (IoT) and Industry 4.0
The Internet of Things (IoT) and Industry 4.0 are already transforming manufacturing, and dynamic scheduling technology is no exception. By connecting machines, sensors, and devices, IoT can provide real-time data on production processes, enabling manufacturers to make data-driven decisions and optimize their schedules accordingly.
Industry 4.0 technologies like digital twins and cyber-physical systems can also be integrated with dynamic scheduling systems to improve production planning and performance.
Cloud Computing and Edge Computing
Cloud computing and edge computing are two trends that are already having a significant impact on the manufacturing industry. With cloud computing, manufacturers can access powerful computing resources and storage capacity from anywhere, allowing them to scale their operations quickly and efficiently.
Edge computing, on the other hand, enables real-time data processing and decision-making at the edge of the network, reducing latency and improving performance. By leveraging both cloud and edge computing, manufacturers can optimize their dynamic scheduling systems for maximum efficiency and responsiveness.
Benefits of Cloud Computing for Dynamic Scheduling:
- Scalability: Cloud computing allows for the easy scalability of computing resources, making it ideal for dynamic scheduling systems that require additional resources during peak periods or when managing a large number of tasks.
- Cost savings: Cloud computing eliminates the need for businesses to invest in expensive hardware and infrastructure, as they can rent computing resources as needed from cloud service providers. This can result in significant cost savings over traditional on-premises solutions.
- Accessibility: Cloud computing makes dynamic scheduling systems accessible from anywhere with an internet connection, allowing employees to work remotely and access real-time data and analytics.
- Reliability: Cloud service providers typically offer high levels of uptime and reliability, ensuring that dynamic scheduling systems remain operational even during unexpected downtime or system failures.
- Security: Cloud service providers invest heavily in security measures, including firewalls, encryption, and data backups, which can provide a higher level of security than on-premises solutions.
Benefits of Edge Computing for Dynamic Scheduling:
- Reduced latency: Edge computing allows for the processing of data at or near the source of the data, reducing the amount of time it takes to transfer and process data compared to cloud computing.
- Real-time processing: Edge computing can provide real-time processing of data, allowing for faster decision-making and response times.
- Lower bandwidth requirements: Because edge computing processes data locally, it can reduce the amount of data that needs to be transmitted over the internet, reducing bandwidth requirements and associated costs.
- Increased privacy and security: Edge computing can offer increased privacy and security compared to cloud computing, as data is processed locally rather than being transmitted over the internet.
Predictive Analytics and Prescriptive Analytics
Predictive analytics and prescriptive analytics are two closely related trends that are becoming increasingly important in the manufacturing industry. Predictive analytics uses historical data and machine learning algorithms to forecast future events and trends, while prescriptive analytics uses these forecasts to make recommendations on how to optimize production schedules and processes.
Manufacturers can achieve a more proactive and data-driven approach to production planning and management by combining predictive and prescriptive analytics with dynamic scheduling technology.
Collaborative Robots and Autonomous Systems
Collaborative robots (cobots) and autonomous systems are already being used in many manufacturing operations to improve efficiency, safety, and productivity. As these technologies continue to advance, they are likely to play a more significant role in dynamic scheduling as well.
Cobots can work alongside human operators to perform repetitive or dangerous tasks, freeing up human resources for more complex and creative tasks. Autonomous systems such as drones and AGVs can also be integrated with dynamic scheduling systems to optimize material handling and logistics.
Autonomous Systems in Dynamic Scheduling: Autonomous systems are becoming increasingly popular in manufacturing and production environments. These robots can operate independently, performing tasks without the need for human intervention.
In dynamic scheduling, autonomous systems can be used to monitor the manufacturing process, identify bottlenecks, and adjust production schedules to ensure maximum efficiency. They can also be used to perform too dangerous or difficult tasks for human workers, such as working in hazardous environments or lifting heavy objects.
Impact of Collaborative Robots and Autonomous Systems on Dynamic Scheduling: Collaborative robots and autonomous systems have the potential to transform the manufacturing industry, improving efficiency, reducing costs, and increasing productivity. By working alongside human workers, collaborative robots can help reduce the risk of injury and improve overall safety in the workplace.
Autonomous systems can monitor the manufacturing process in real time, identifying bottlenecks and adjusting production schedules to maximize efficiency. This can help reduce downtime, improve throughput, and ultimately increase profits.
Best Practices for Implementing Collaborative Robots and Autonomous Systems in Dynamic Scheduling: When implementing collaborative robots and autonomous systems in dynamic scheduling, it is essential to ensure that the technology is properly integrated into existing processes. This may require changes to workflows, retraining of staff, and the adoption of new technologies.
It is also essential to select the right type of collaborative robot or autonomous system for the task at hand and to ensure that the technology is properly maintained and serviced to avoid downtime.
Blockchain and Distributed Ledger Technology
Blockchain and distributed ledger technology (DLT) are still in the early stages of adoption in manufacturing, but they are already showing promise for improving supply chain visibility and transparency.
By creating a secure, decentralized database of transactions and events, blockchain and DLT can provide real-time visibility into orders, inventory, and shipment status. This can help manufacturers optimize their production schedules and supply chain operations, improving efficiency and reducing costs.
Benefits of using Blockchain in Dynamic Scheduling:
- Transparency and traceability: Blockchain technology provides a transparent and traceable platform for sharing data between different parties involved in the scheduling process. It allows for real-time tracking of the progress of the task and the exchange of information related to it.
- Security: Blockchain technology is highly secure due to its decentralized nature, making it difficult for hackers to attack the system. The use of cryptography in blockchain ensures that the data recorded on the blockchain cannot be tampered with.
- Efficiency: Using blockchain technology in dynamic scheduling can increase efficiency by eliminating intermediaries and automating tasks currently done manually.
ROI Analysis for Dynamic Scheduling Investments
Return on Investment (ROI) is an essential financial metric that companies use to evaluate the benefits of investing in a particular project or technology. When it comes to dynamic scheduling systems, ROI analysis can help manufacturers determine whether the investment is worth it and if the implementation of such a system can help improve their bottom line.
Here are some key points to consider in ROI analysis for dynamic scheduling investments:
- Identify the potential benefits: To determine ROI, it is necessary to identify the potential benefits of implementing a dynamic scheduling system. Some benefits include reduced lead times, improved on-time delivery, increased production efficiency, reduced inventory levels, and increased capacity utilization.
- Identify the costs: In addition to identifying potential benefits, it is essential to identify the costs associated with implementing a dynamic scheduling system. These costs may include software licensing fees, hardware costs, implementation costs, and ongoing maintenance costs.
- Determine the timeframe: To calculate ROI, it is necessary to determine the timeframe for the benefits and costs. This timeframe should consider the dynamic scheduling system's expected lifespan and the investment payback period.
- Calculate ROI: Once the potential benefits, costs, and timeframe have been identified, it is possible to calculate the ROI for the dynamic scheduling investment. The ROI is calculated by dividing the net benefits (benefits minus costs) by the initial investment. A positive ROI indicates that the investment is expected to generate a profit, while a negative ROI indicates that the investment is expected to result in a loss.
- Consider intangible benefits: In addition to the quantifiable benefits of implementing a dynamic scheduling system, it is also important to consider intangible benefits. These benefits include improved customer satisfaction, improved employee morale, and increased competitiveness in the market. While these benefits may not be easily quantifiable, they can still significantly impact a company's overall success.
- Consider the risks: Any investment carries risks, and it is essential to consider the potential risks associated with implementing a dynamic scheduling system. These risks may include software bugs, data security breaches, and the possibility of the system not delivering the expected benefits. It is vital to have a risk management plan in place to mitigate these risks.
- Evaluate the sensitivity of the ROI analysis: ROI analysis is sensitive to the assumptions and estimates used in the calculation. It is crucial to evaluate the sensitivity of the ROI analysis by conducting a sensitivity analysis. This analysis involves changing the assumptions and estimates used in the calculation to determine how sensitive the ROI is to these changes.
Best Practices for Dynamic Scheduling Implementation and Adoption
Start with a clear understanding of business needs: Before implementing a dynamic scheduling system, it is essential to identify and document specific business needs and goals.
This information can guide the selection of the appropriate technology and ensure that the implementation process aligns with the company's overall strategic direction.
Establish cross-functional collaboration: A successful dynamic scheduling implementation requires collaboration across all departments and functions, including production, supply chain, and IT.
This collaboration helps to ensure that all stakeholders understand the goals and benefits of the system and that they are engaged and committed to making the technology work effectively.
Select the right technology: Many dynamic scheduling solutions are available on the market, each with unique features and capabilities. It is essential to select a solution tailored to the business's specific needs and requirements. Factors to consider include ease of use, scalability, integration with other systems, and flexibility.
Prioritize data quality: Dynamic scheduling systems rely heavily on accurate and timely data. Companies need to ensure that their data is up-to-date, complete, and consistent. This requires establishing data governance practices and investing in tools and resources to support data quality management.
Build a strong change management program: Dynamic scheduling implementation involves significant changes to business processes and workflows. It is critical to have a robust change management program in place to help employees understand why the changes are necessary, what the benefits are, and how to use the new technology effectively.
Provide adequate training and support: Employees must be adequately trained to use the new system effectively. Training should be tailored to the needs of each department and role, and it should include hands-on practice to build confidence and proficiency.
Additionally, providing ongoing support and troubleshooting resources is critical to ensuring that employees can continue to use the system effectively over time.
Continuously monitor and refine the system: Dynamic scheduling is not a set-it-and-forget-it solution.
Companies must continuously monitor and refine the system to ensure that it is meeting business needs and goals. This involves collecting and analyzing system performance data, identifying improvement areas, and implementing changes as necessary.
How can Deskera Help You?
Deskera MRP allows you to closely monitor the manufacturing process. From the bill of materials to the production planning features, the solution helps you stay on top of your game and keep your company's competitive edge.
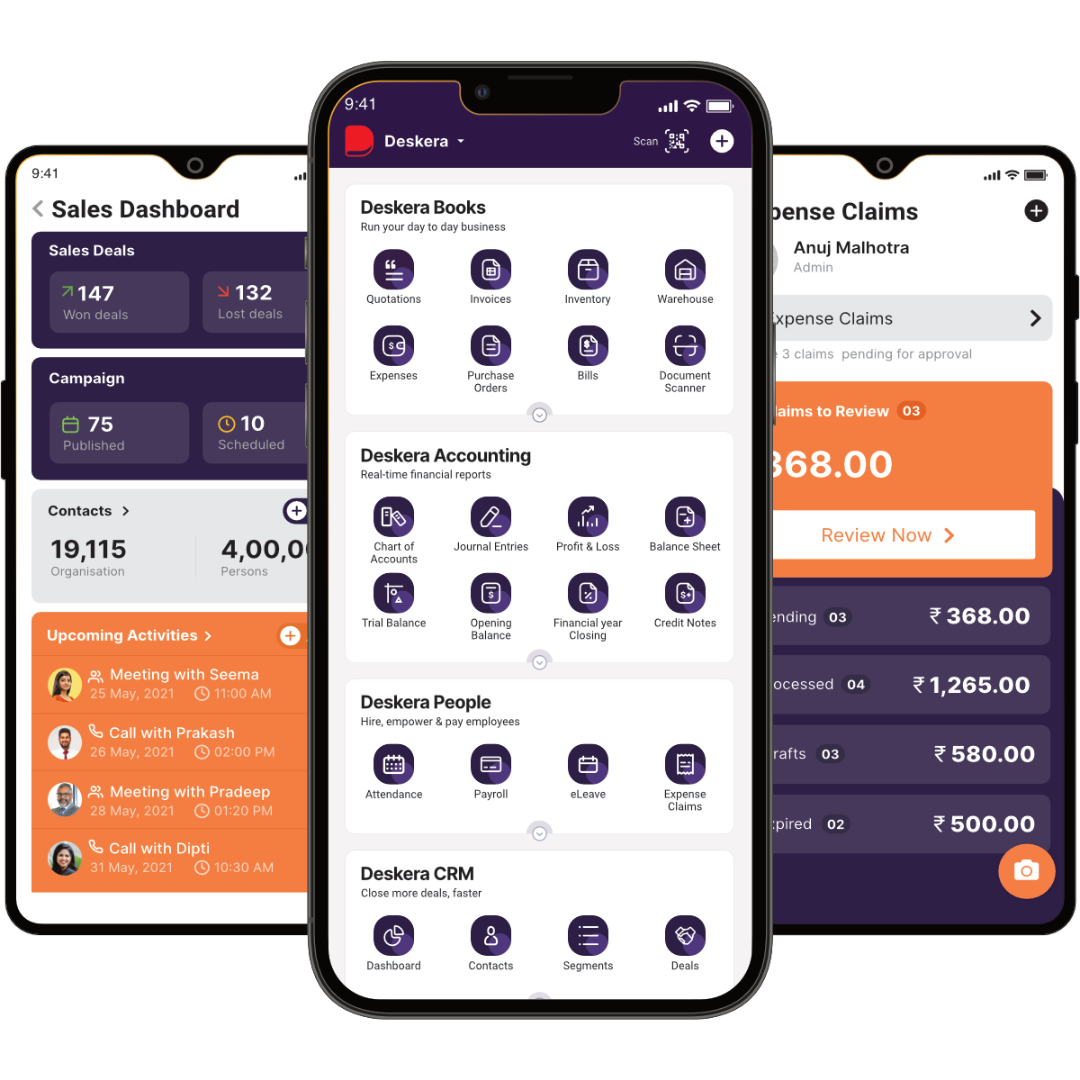
Deskera ERP and MRP system can help you:
- Manage production plans
- Maintain Bill of Materials
- Generate detailed reports
- Create a custom dashboard
Deskera ERP is a comprehensive system that allows you to maintain inventory, manage suppliers, and track supply chain activity in real-time, as well as streamline a variety of other corporate operations.
Deskera Books enables you to manage your accounts and finances more effectively. Maintain sound accounting practices by automating accounting operations such as billing, invoicing, and payment processing.
Deskera CRM is a strong solution that manages your sales and assists you in closing agreements quickly. It not only allows you to do critical duties such as lead generation via email, but it also provides you with a comprehensive view of your sales funnel.
Deskera People is a simple tool for taking control of your human resource management functions. The technology not only speeds up payroll processing but also allows you to manage all other activities such as overtime, benefits, bonuses, training programs, and much more. This is your chance to grow your business, increase earnings, and improve the efficiency of the entire production process.
Conclusion
Dynamic scheduling is a powerful tool that modern manufacturing businesses can use to improve their operations in various ways. By utilizing data analytics and machine learning algorithms, businesses can create schedules that are responsive to the ever-changing production environment.
These schedules optimize production capacity, minimize lead times, reduce inventory costs, and improve customer satisfaction. With the ability to adjust to changing conditions in real-time, dynamic scheduling helps manufacturers keep up with the unpredictable nature of modern business.
The benefits of dynamic scheduling are not limited to production efficiency. This approach also supports lean manufacturing practices by reducing waste and increasing productivity. Furthermore, it allows businesses better to manage their resources, including labor and equipment, resulting in significant cost savings. By optimizing production schedules, manufacturers can improve their performance and market competitiveness.
However, implementing dynamic scheduling is not without challenges. The process requires significant software and hardware investment and a skilled workforce to manage and operate the system.
Additionally, businesses must ensure that they have access to accurate and timely data to support the scheduling process. Finally, it is important to note that dynamic scheduling is not a one-size-fits-all solution, and businesses must tailor their approach to meet their unique production needs and goals.
Key Takeaways
- Dynamic scheduling in modern manufacturing can lead to significant cost savings and increased efficiency.
- Dynamic scheduling can help manufacturers respond quickly to changing demand and supply chain disruptions.
- Dynamic scheduling can optimize machine utilization and reduce production lead times.
- Real-time data can improve scheduling accuracy, reduce waste, and increase productivity.
- Manufacturers can use dynamic scheduling to optimize their production resources and reduce downtime.
- Dynamic scheduling can help manufacturers prioritize their orders and meet their customer's demands on time.
- The use of dynamic scheduling can help manufacturers stay competitive in the global marketplace.
- Machine learning and artificial intelligence can enhance the effectiveness of dynamic scheduling in modern manufacturing.
- Dynamic scheduling can help manufacturers manage their inventories more efficiently and avoid overstocking or stockouts.
- With dynamic scheduling, manufacturers can improve their planning and decision-making capabilities.
Related Articles
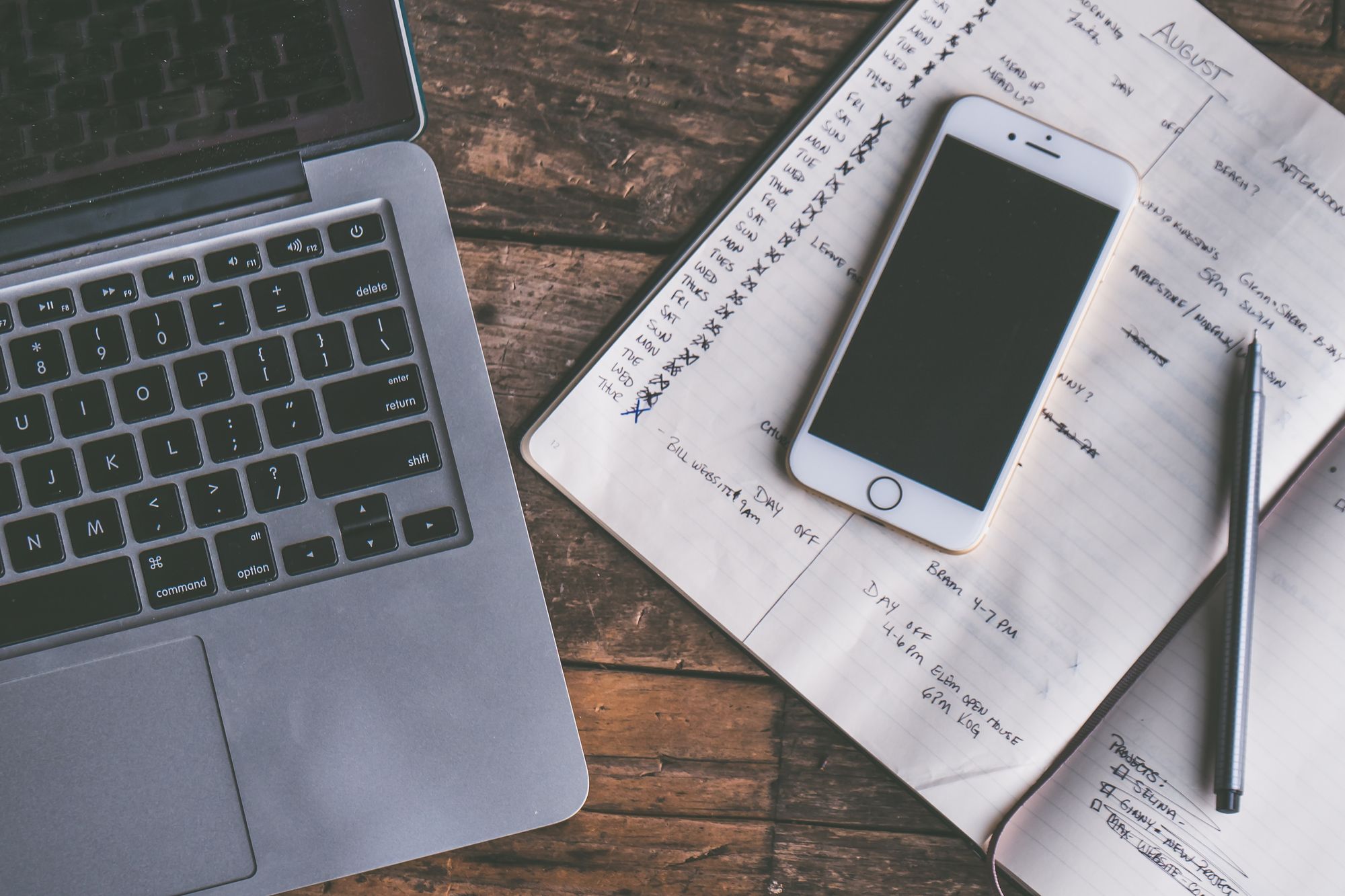
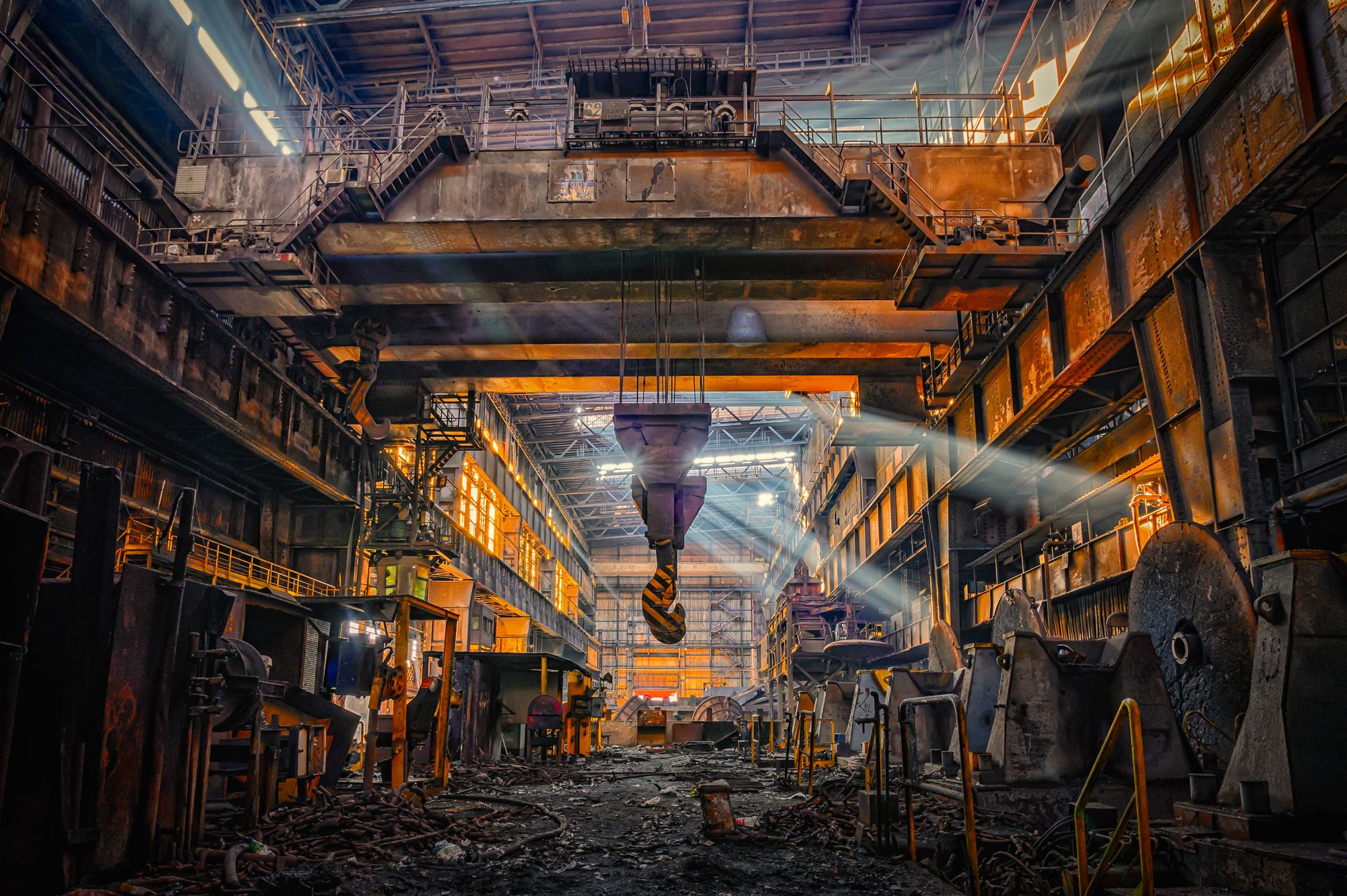
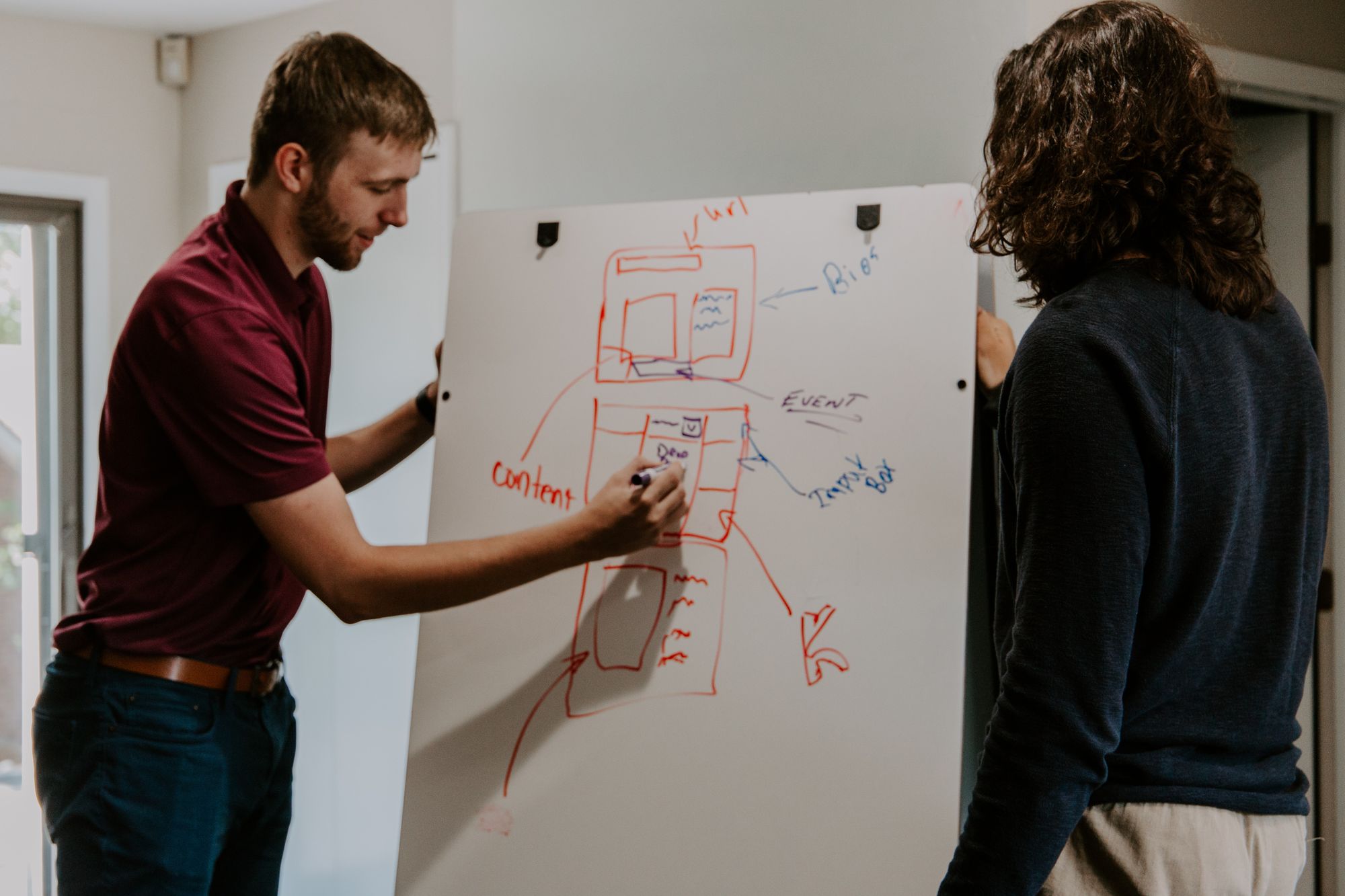
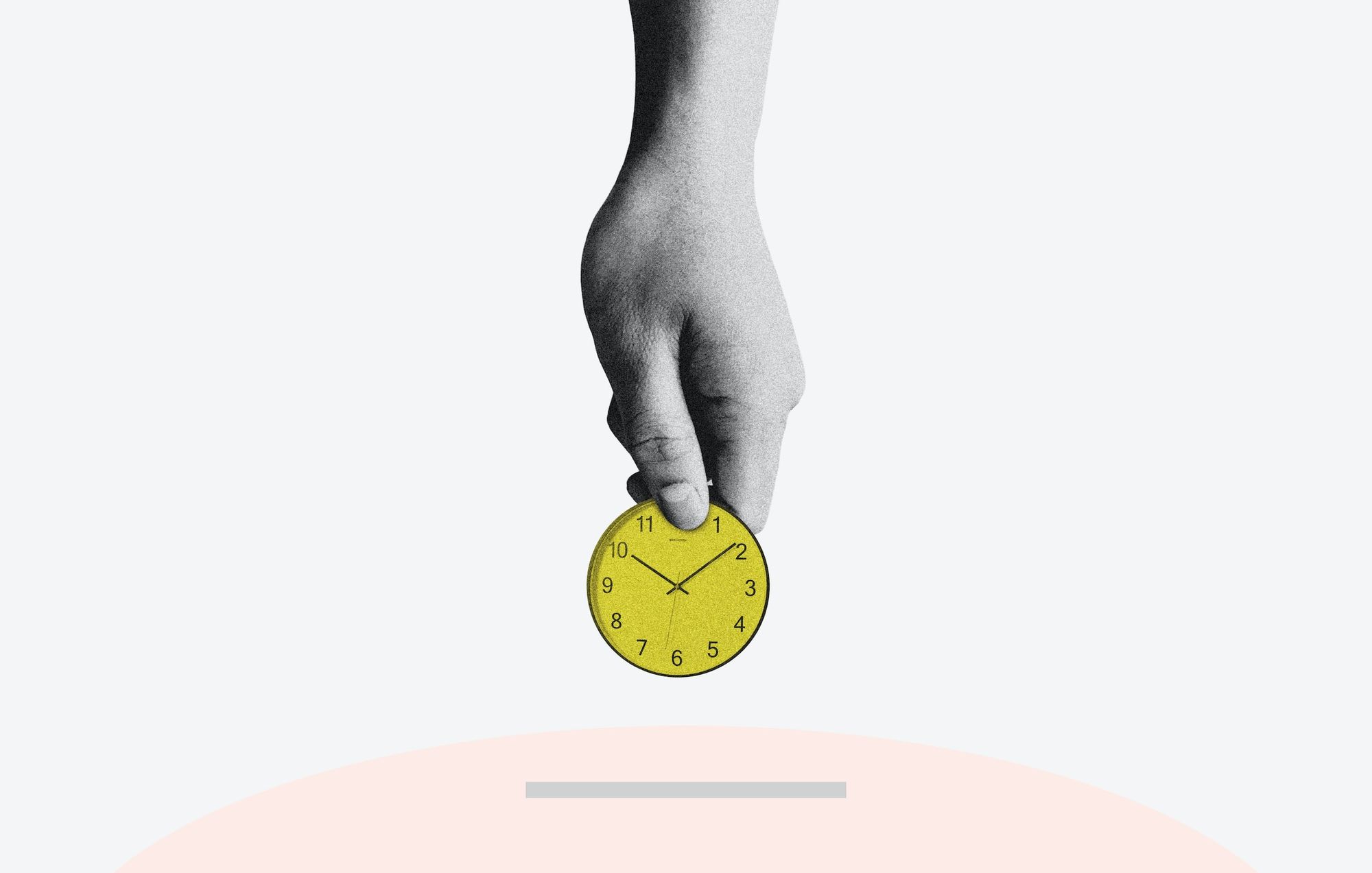