Production planning is a critical process for manufacturers looking to optimize their operations and improve efficiency. It involves setting production goals, determining resource requirements, and developing a plan to meet those goals in the most efficient way possible.
According to a study by the Aberdeen Group, manufacturers who adopt production planning can reduce their inventory carrying costs by up to 22%, increase on-time delivery rates by up to 24%, and reduce lead times by up to 66%.
With such significant benefits, it's no wonder that production planning is becoming increasingly popular in the manufacturing industry.
However, for beginners, understanding the fundamentals of production planning manufacturing can be a daunting task. This guide aims to provide an introduction to the key components and steps involved in the production planning process, as well as the factors that can affect production planning outcomes.
By the end of this guide, beginners should have a good understanding of production planning concepts and be able to develop a basic production plan for their manufacturing operations.
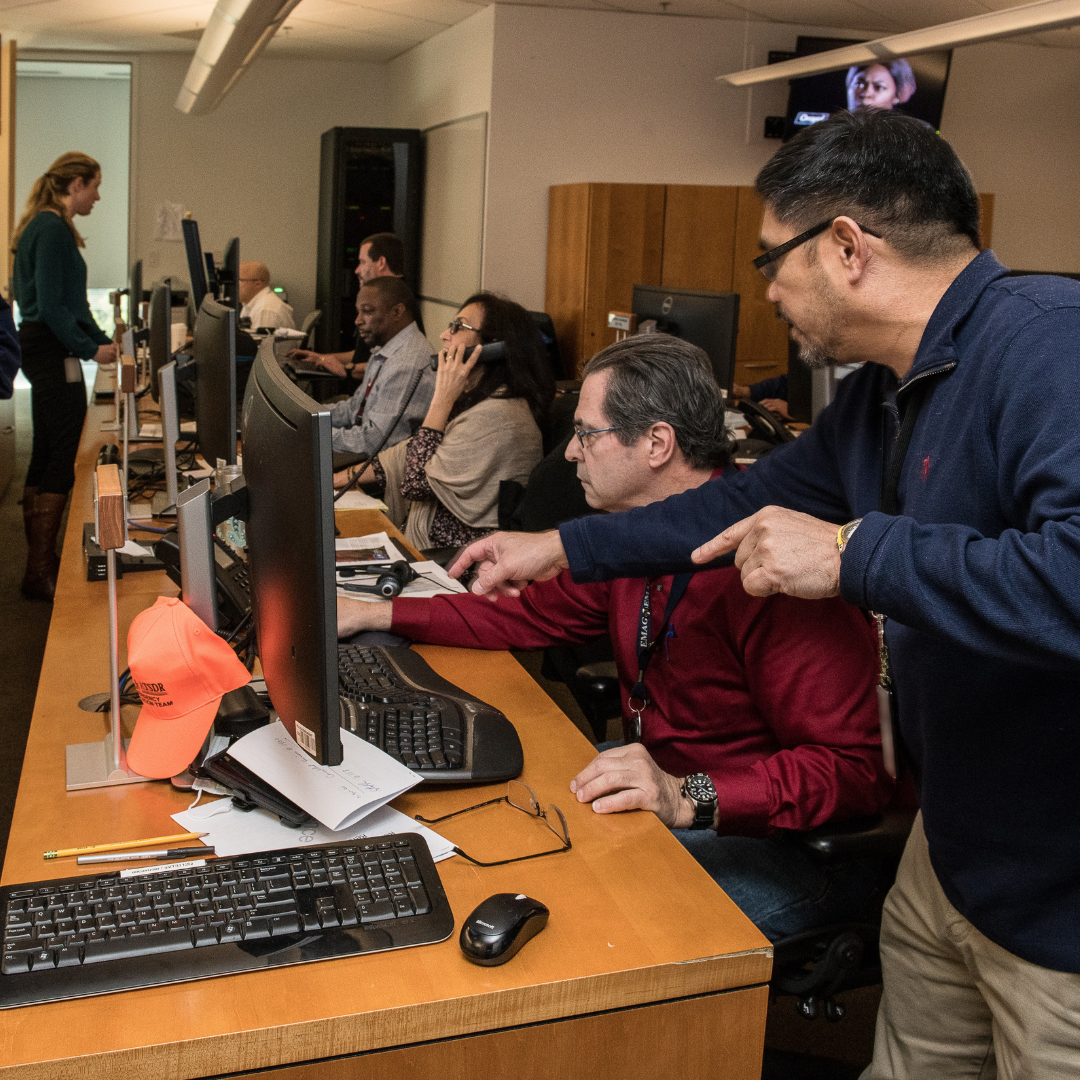
Whether you are a small-scale manufacturer or a large industrial facility, production planning can help you increase efficiency, reduce costs, and improve customer service. By taking the time to understand the fundamentals of production planning manufacturing, you can unlock the full potential of your manufacturing operations and stay ahead of the competition.
- Explanation of Production Planning
- Understanding the Basics of Production Planning
- Components of Production Planning
- The Role of Technology in Production Planning
- Best Practices in Production Planning
- Challenges in Production Planning
- Conclusion
- How can Deskera Help You?
- Key Takeaways
- Related Articles
What is Production Planning?
Production planning is a process of determining the resources needed to produce goods and services, setting production goals, and developing a plan to achieve those goals in the most efficient way possible. It involves forecasting demand, creating a production schedule, determining resource requirements such as raw materials, labor, and equipment, and coordinating all the activities involved in the production process.
Production planning helps manufacturers optimize their operations by minimizing production costs, reducing lead times, and improving product quality. It helps ensure that the right resources are available at the right time, and that production is aligned with demand, so that goods are produced in the right quantities, at the right time, and at the right cost.
Production planning is a critical function in manufacturing and is used in a variety of industries, including automotive, aerospace, pharmaceuticals, and consumer goods. It is an ongoing process that involves continuous monitoring and adjustment to ensure that production goals are met and that resources are used efficiently.
Effective production planning requires collaboration between different departments within a manufacturing organization, such as sales, marketing, and production, to ensure that all aspects of production are aligned with business goals and objectives.
Importance of Production Planning in Manufacturing
Production planning is an essential function in manufacturing, and it plays a crucial role in the success of any manufacturing operation. The following are some of the reasons why production planning is important in manufacturing:
- Optimization of Resources: Production planning helps manufacturers to optimize their resources, including raw materials, labor, and equipment. By forecasting demand and creating a production schedule, manufacturers can ensure that they have the right resources available at the right time, reducing waste and improving efficiency.
- Meeting Customer Demands: Production planning helps manufacturers to produce goods in the right quantities, at the right time, and at the right cost, enabling them to meet customer demands effectively. By aligning production with demand, manufacturers can reduce lead times, improve on-time delivery rates, and enhance customer satisfaction.
- Reduced Costs: Production planning helps manufacturers to reduce costs by minimizing inventory carrying costs, reducing waste, and optimizing the use of resources. By avoiding overproduction, manufacturers can reduce storage costs and minimize the risk of obsolete inventory.
- Improved Quality Control: Production planning enables manufacturers to identify potential quality issues before they occur, reducing the risk of defects and improving product quality. By ensuring that the right resources are available at the right time, manufacturers can minimize the risk of errors and defects.
- Increased Efficiency: Production planning helps manufacturers to improve efficiency by reducing lead times, minimizing downtime, and optimizing the use of resources. By coordinating all aspects of the production process, manufacturers can improve productivity and reduce costs.
In summary, production planning is essential in manufacturing as it helps manufacturers to optimize resources, meet customer demands, reduce costs, improve quality control, and increase efficiency. By adopting production planning, manufacturers can stay competitive and achieve their business goals more effectively.
Purpose of the Article
The purpose of the article "The Fundamentals of Production Planning in Manufacturing: A Beginner's Guide" is to provide an introduction to the key components and steps involved in production planning for beginners in the manufacturing industry. The article aims to explain the importance of production planning in manufacturing, its benefits, and the factors that can affect production planning outcomes.
The article is intended to help beginners understand the fundamentals of production planning, including demand forecasting, creating a Master Production Schedule (MPS), developing a Bill of Materials (BOM), inventory management, and capacity planning. It also outlines the steps involved in the production planning process and provides practical guidance on how to develop a production plan.
The article is relevant to anyone who is new to production planning, including small-scale manufacturers, entrepreneurs, and students who are interested in the manufacturing industry. By reading this article, beginners can gain a basic understanding of production planning concepts and develop a foundation for more advanced production planning practices.
Ultimately, the article aims to help beginners optimize their manufacturing operations, reduce costs, and improve efficiency by adopting production planning practices.
Understanding the Basics of Production Planning
To effectively implement production planning, it is essential to first understand the basics of this critical process. In this section, we will provide an overview of the fundamental concepts of production planning, including its definition, key objectives, and the various factors that can affect its outcomes.
By gaining an understanding of the basics of production planning, beginners can develop a solid foundation for creating effective production plans that optimize resources, reduce costs, and improve efficiency.
Key concepts of production planning
Production planning is a complex process that involves multiple key concepts that are essential to its success. The following are some of the key concepts of production planning:
- Demand forecasting: Demand forecasting is the process of predicting the quantity of goods and services that customers will require in the future. Accurate demand forecasting is critical to production planning, as it enables manufacturers to produce the right quantities of goods at the right time.
- Master Production Schedule (MPS): The Master Production Schedule (MPS) is a detailed plan that outlines the quantity and timing of production for each item manufactured. The MPS is the backbone of the production planning process and serves as a guide for all production activities.
- Bill of Materials (BOM): The Bill of Materials (BOM) is a comprehensive list of all the components and materials required to manufacture a product. The BOM includes the quantity and specification of each component, as well as any special instructions for assembly.
- Inventory management: Inventory management involves managing the quantity and location of inventory to ensure that production can be carried out efficiently. Effective inventory management is critical to production planning, as it ensures that the right materials are available at the right time, minimizing waste and reducing costs.
- Capacity planning: Capacity planning is the process of determining the resources required to produce goods and services, including labor, machinery, and facilities. Effective capacity planning ensures that production can be carried out efficiently and cost-effectively.
In summary, understanding these key concepts is essential for effective production planning. By leveraging these concepts, manufacturers can optimize their operations, reduce costs, and improve efficiency, resulting in increased profitability and competitiveness.
Types of production planning systems
There are several types of production planning systems that are used in the manufacturing industry. These systems vary in complexity, scope, and functionality, and can be classified into the following categories:
- Material Requirements Planning (MRP): Material Requirements Planning is a software-based production planning and inventory control system that calculates the amount of materials required to manufacture a product. MRP systems use data on production schedules, inventory levels, and demand forecasts to generate a production plan and ensure that the right materials are available at the right time.
- Enterprise Resource Planning (ERP): Enterprise Resource Planning is an integrated software system that allows manufacturers to manage all aspects of their operations, including production planning, inventory management, accounting, and human resources. ERP systems provide a unified view of the entire manufacturing process, enabling manufacturers to make better decisions and optimize their operations.
- Just-in-Time (JIT): Just-in-Time is a production planning system that aims to minimize inventory levels by producing goods only when they are needed. JIT systems rely on accurate demand forecasting, streamlined production processes, and close collaboration between suppliers and manufacturers to minimize waste and improve efficiency.
- Kanban: Kanban is a lean production planning system that uses visual signals to manage inventory levels and production schedules. Kanban systems rely on a pull-based production model, where goods are produced only when there is demand, and inventory levels are controlled by limiting the number of items in the production process.
- Advanced Planning and Scheduling (APS): Advanced Planning and Scheduling is a software-based system that uses complex algorithms to optimize production planning and scheduling. APS systems take into account multiple factors, including demand forecasts, inventory levels, and production capacity, to generate an optimized production plan.
In summary, there are several types of production planning systems that manufacturers can choose from. The type of system chosen will depend on the specific needs of the manufacturer, including the size of the operation, the complexity of the production process, and the level of automation desired.
Components of Production Planning
To effectively plan and manage production processes, it is important to understand the components that make up production planning. In this section, we will delve into the various components of production planning, including capacity planning, scheduling, material requirements planning, and quality control.
By understanding these components and how they interact with each other, manufacturers can create effective production plans that optimize resources, minimize waste, and improve efficiency.
Sales forecasting and demand planning
Sales forecasting and demand planning are critical components of production planning, as they provide insight into the expected demand for products and services. These two concepts are closely related and are used to predict future sales volumes, which in turn drives the production planning process.
Sales forecasting is the process of estimating the future sales volume of a company's products or services. This process takes into account past sales data, market trends, customer behavior, and other relevant factors to generate a forecast for future sales. Sales forecasting is typically carried out on a monthly, quarterly, or annual basis, and is used to inform the overall business strategy, including production planning.
Demand planning, on the other hand, is the process of translating sales forecasts into specific production requirements. This involves identifying the resources required to produce the required volume of goods or services, including materials, labor, and equipment. Demand planning is used to develop a production plan that aligns with sales forecasts and ensures that production can be carried out efficiently.
The key difference between sales forecasting and demand planning is that sales forecasting is focused on predicting future sales volumes, while demand planning is focused on translating these forecasts into specific production requirements. Sales forecasting provides the basis for demand planning, and is typically the starting point for production planning.
Both sales forecasting and demand planning are critical for effective production planning, as they enable manufacturers to align production with customer demand, minimize waste, and optimize resources. Accurate sales forecasting and demand planning can also help manufacturers avoid stockouts, reduce inventory costs, and improve customer satisfaction.
In summary, sales forecasting and demand planning are essential components of production planning. By accurately predicting future sales volumes and translating them into specific production requirements, manufacturers can create effective production plans that optimize resources, reduce costs, and improve efficiency.
Material requirements planning (MRP)
Material Requirements Planning (MRP) is a software-based production planning and inventory control system that calculates the amount of materials required to manufacture a product. MRP systems use data on production schedules, inventory levels, and demand forecasts to generate a production plan and ensure that the right materials are available at the right time.
The MRP process typically begins with a master production schedule (MPS), which outlines the planned production quantities for each product over a specific time period. The MRP system then uses this information to generate a detailed material requirements list, which specifies the quantities of each raw material, component, and subassembly required to meet the production schedule.
MRP systems also take into account lead times, or the time required for materials to be delivered, and safety stock levels, or the amount of inventory kept on hand to protect against unexpected demand or supply disruptions. By factoring in lead times and safety stock levels, MRP systems can ensure that the required materials are available when needed, and avoid stockouts or production delays.
In addition to calculating material requirements, MRP systems also generate purchase orders and production schedules to ensure that the required materials are delivered and production is carried out efficiently. MRP systems can also be integrated with other systems, such as inventory management and accounting, to provide a unified view of the entire production process.
The benefits of MRP systems include increased production efficiency, reduced inventory costs, and improved customer service. By accurately calculating material requirements and streamlining the production planning process, manufacturers can optimize resources, reduce waste, and improve the accuracy and timeliness of order fulfillment.
However, it is important to note that MRP systems have some limitations. For example, they are highly dependent on accurate data inputs, including production schedules, inventory levels, and demand forecasts. Inaccurate or outdated data can lead to incorrect material requirements calculations, which can result in production delays or excess inventory. Additionally, MRP systems may not be suitable for highly customized or rapidly changing product lines.
In summary, Material Requirements Planning (MRP) is a software-based production planning and inventory control system that calculates the amount of materials required to manufacture a product. MRP systems play a critical role in optimizing resources, reducing waste, and improving the accuracy and timeliness of order fulfillment. However, they have some limitations and may not be suitable for all types of production processes.
Capacity planning
Capacity planning is the process of determining the production capacity required to meet the demand for a product or service. The goal of capacity planning is to ensure that a company has the resources and capabilities to meet the expected demand for its products, while avoiding excess capacity that can lead to unnecessary costs.
Capacity planning involves analyzing historical production data, demand forecasts, and other relevant factors to determine the required production capacity for a given time period. This analysis takes into account factors such as production lead times, production rates, and available resources such as labor and equipment.
Once the required production capacity has been determined, capacity planning involves developing a production plan that maximizes the use of available resources and minimizes the risk of overproduction or underproduction. This may involve adjusting production schedules, investing in new equipment or technology, or hiring additional staff.
Capacity planning is critical for effective production planning, as it enables companies to balance production capacity with expected demand, reduce the risk of stockouts or excess inventory, and optimize the use of available resources. Effective capacity planning can also help companies respond quickly to changes in demand, such as seasonal fluctuations or unexpected shifts in customer behavior.
There are several techniques used for capacity planning, including resource forecasting, production rate analysis, and simulation modeling. Resource forecasting involves projecting the availability of resources such as labor and equipment, and determining the production capacity that can be achieved with these resources.
Production rate analysis involves analyzing historical production data to determine the rate at which products can be produced, and using this information to develop a production plan. Simulation modeling involves using computer simulations to model production scenarios and identify optimal production strategies.
In summary, capacity planning is a critical component of production planning that involves determining the production capacity required to meet expected demand, and developing a production plan that maximizes the use of available resources. Effective capacity planning can help companies optimize resources, reduce costs, and improve the accuracy and timeliness of order fulfillment.
Production scheduling
Production scheduling is the process of determining when and how much of a product should be produced to meet customer demand while optimizing the use of resources such as labor, equipment, and materials. The goal of production scheduling is to ensure that production runs smoothly and efficiently, with minimal downtime or waste.
Production scheduling typically involves the use of software tools to generate a detailed production plan, taking into account factors such as production capacity, lead times, inventory levels, and customer demand. The production schedule specifies when each product should be produced, how much should be produced, and which resources should be used.
The production schedule is typically based on a master production schedule (MPS), which outlines the planned production quantities for each product over a specific time period. The MPS provides a high-level view of the production schedule, while the detailed production schedule breaks down the production requirements into specific time periods and production runs.
Production scheduling is a complex process that requires careful coordination between different departments within a company, such as production, procurement, and logistics. Effective production scheduling can help companies optimize production processes, reduce inventory costs, and improve customer service by ensuring that products are delivered on time and in the correct quantities.
There are several techniques used for production scheduling, including material requirements planning (MRP), finite capacity scheduling, and just-in-time (JIT) scheduling. MRP involves calculating the amount of materials required to manufacture a product, based on the production schedule and demand forecasts.
Finite capacity scheduling takes into account the availability of resources such as labor and equipment when generating the production schedule. JIT scheduling involves producing products only when they are needed, in order to minimize inventory costs and reduce waste.
In summary, production scheduling is the process of determining when and how much of a product should be produced to meet customer demand while optimizing the use of resources.
Effective production scheduling can help companies optimize production processes, reduce inventory costs, and improve customer service. There are several techniques used for production scheduling, including MRP, finite capacity scheduling, and JIT scheduling.
Inventory management
Inventory management is the process of overseeing the flow of goods and materials into and out of a company's inventory. The goal of inventory management is to ensure that the company has the right amount of inventory on hand to meet customer demand, while minimizing the costs associated with holding and managing inventory.
Effective inventory management involves several key activities, including forecasting demand, setting inventory levels, tracking inventory movements, and managing stockouts and overstock situations. These activities are typically supported by software systems that provide real-time visibility into inventory levels and enable companies to track inventory movements and forecast demand.
One of the key challenges of inventory management is balancing inventory levels with customer demand. Holding too much inventory can tie up working capital and increase storage and handling costs, while holding too little inventory can result in stockouts and lost sales. To address this challenge, companies typically use inventory planning techniques such as just-in-time (JIT) inventory, economic order quantity (EOQ), and safety stock.
JIT inventory involves producing or acquiring goods only when they are needed, in order to minimize inventory costs and reduce waste. EOQ involves calculating the optimal order quantity based on factors such as demand, lead time, and ordering costs. Safety stock involves maintaining a buffer of inventory to protect against unexpected fluctuations in demand or supply.
Another key aspect of inventory management is tracking inventory movements and managing inventory accuracy. This involves implementing inventory control systems and procedures to ensure that inventory levels are accurately reflected in the company's records, and that inventory is properly accounted for and managed.
In summary, inventory management is the process of overseeing the flow of goods and materials into and out of a company's inventory. Effective inventory management involves balancing inventory levels with customer demand, and using inventory planning techniques such as JIT inventory, EOQ, and safety stock to minimize inventory costs and reduce waste.
Inventory management also involves tracking inventory movements and managing inventory accuracy, to ensure that inventory levels are accurately reflected in the company's records and that inventory is properly accounted for and managed.
The Role of Technology in Production Planning
Technology has revolutionized the field of production planning, providing companies with powerful tools to optimize their production processes, improve efficiency, and reduce costs. In this section, we will explore the role of technology in production planning, and examine some of the key software tools and technologies used in modern production planning systems.
Overview of production planning software
Production planning software is a category of software tools designed to support the planning and execution of production processes in manufacturing environments. These tools are designed to automate and optimize key aspects of production planning, including demand forecasting, materials planning, capacity planning, scheduling, and inventory management.
Production planning software can be divided into several categories based on their specific focus and functionality. Some software tools are designed to address specific aspects of production planning, such as demand forecasting or inventory management, while others provide end-to-end support for the entire production planning process.
One of the key advantages of production planning software is that it enables companies to optimize their production processes and reduce costs by identifying inefficiencies and bottlenecks. For example, production planning software can help companies identify areas where production capacity is underutilized or where materials are being wasted, and provide recommendations for how to improve efficiency and reduce waste.
Another advantage of production planning software is that it enables companies to better manage their inventory levels, ensuring that they have the right amount of inventory on hand to meet customer demand while minimizing inventory costs. This is particularly important in industries with high demand volatility, where companies must be able to quickly adjust production and inventory levels in response to changing market conditions.
In summary, production planning software is a category of software tools designed to support the planning and execution of production processes in manufacturing environments. These tools are designed to automate and optimize key aspects of production planning, and can help companies reduce costs, improve efficiency, and better manage their inventory levels.
Benefits of using technology in production planning
Technology has had a significant impact on the manufacturing industry, providing numerous benefits for companies that adopt advanced production planning tools and software. In this section, we will explore some of the key benefits of using technology in production planning in greater detail.
- Improved efficiency: Technology can help automate and optimize key aspects of production planning, such as demand forecasting, materials planning, and scheduling, reducing the time and effort required to perform these tasks manually. This can help companies save time and reduce the cost of production planning activities, while also enabling them to respond more quickly to changing market conditions.
- Increased accuracy: One of the main advantages of production planning software is that it can provide more accurate and reliable forecasts, reducing the risk of overproduction or stockouts, and ensuring that the right amount of inventory is on hand to meet customer demand. By providing real-time visibility into inventory levels and demand, production planning software can help companies make more informed decisions about production and inventory levels, reducing the risk of costly errors.
- Cost savings: By optimizing production processes and reducing waste, technology can help companies reduce costs and increase profitability. For example, by providing tools for capacity planning and scheduling, production planning software can help companies reduce the amount of time that production lines are idle or underutilized, reducing the cost of production and improving overall efficiency.
- Better decision-making: Technology provides real-time visibility into production processes and inventory levels, enabling companies to make more informed decisions about production, inventory, and resource allocation. By providing access to real-time data and analytics, production planning software can help companies identify trends and opportunities, optimize production processes, and respond more quickly to changing market conditions.
- Improved customer satisfaction: By ensuring that the right products are available at the right time, technology can help companies improve customer satisfaction and loyalty. By reducing the risk of stockouts and delays, production planning software can help companies ensure that customers receive their orders on time and in full, improving their overall experience and satisfaction with the company.
- Scalability: Technology can help companies scale their production processes and expand their operations more easily by providing tools for planning, scheduling, and resource allocation. By providing a platform for centralizing and streamlining production planning activities, production planning software can help companies manage multiple production sites and production lines more efficiently, improving overall scalability and flexibility.
In summary, the benefits of using technology in production planning are many and varied, including improved efficiency, increased accuracy, cost savings, better decision-making, improved customer satisfaction, and greater scalability. By adopting advanced production planning tools and software, companies can gain a competitive advantage in the marketplace, reduce costs, and improve profitability.
Best Practices in Production Planning
Now that we have covered the basics of production planning and the role of technology in the process, it's important to discuss best practices in production planning. Implementing these best practices can help manufacturing companies optimize their production processes, reduce costs, and increase efficiency.
In this section, we will explore some of the key best practices that manufacturing companies should consider when implementing a production planning strategy. From demand forecasting to inventory management and scheduling, we will provide actionable insights on how to improve production planning processes to achieve better outcomes.
By following these best practices, manufacturing companies can gain a competitive advantage and drive sustainable growth.
Establishing clear goals and objectives
Establishing clear goals and objectives is a critical component of effective production planning. Goals and objectives provide direction and purpose, helping manufacturing companies to align their resources and efforts towards achieving specific outcomes. Without clear goals and objectives, production planning can become disjointed and inefficient, leading to wasted resources, delays, and other negative outcomes.
In this section, we will discuss the importance of establishing clear goals and objectives in production planning and provide guidance on how to set them effectively.
Firstly, clear goals and objectives help manufacturing companies to prioritize their efforts and allocate resources more effectively. By establishing specific, measurable, achievable, relevant, and time-bound (SMART) goals and objectives, companies can focus their attention on the most important areas of their production processes, ensuring that resources are used efficiently and effectively. This can help to reduce waste and improve productivity, leading to lower costs and higher profits.
Secondly, clear goals and objectives help to motivate employees and create a sense of purpose and direction. When employees understand the goals and objectives of the company, they are more likely to be engaged and committed to their work, leading to better performance and higher job satisfaction.
To establish clear goals and objectives in production planning, manufacturing companies should start by conducting a comprehensive analysis of their production processes, identifying key areas for improvement and setting specific goals and objectives for each area.
These goals and objectives should be SMART, ensuring that they are specific, measurable, achievable, relevant, and time-bound. They should also be communicated clearly to all employees, ensuring that everyone is aligned and working towards the same objectives.
Overall, establishing clear goals and objectives is a critical component of effective production planning. By setting specific, measurable, achievable, relevant, and time-bound goals and objectives, manufacturing companies can focus their attention on the most important areas of their production processes, allocate resources more effectively, and improve overall efficiency and productivity.
Collaboration among departments
Collaboration among departments is another key best practice in production planning. Production planning involves many different departments, including production, procurement, inventory management, and sales, among others. For the production planning process to be effective, it's essential that these departments work together and collaborate closely.
In this section, we will discuss the importance of collaboration among departments in production planning and provide guidance on how to achieve it effectively.
Firstly, collaboration among departments helps to ensure that all relevant information is shared and considered. For example, if the sales department is forecasting a surge in demand for a particular product, this information needs to be communicated to the production department so that they can adjust their production schedules accordingly. Collaboration ensures that all departments have access to the information they need to make informed decisions.
Secondly, collaboration among departments helps to improve communication and coordination. By working together, departments can share their expertise and insights, identify potential problems early on, and work together to find solutions. This can help to reduce delays, improve efficiency, and increase overall productivity.
To achieve effective collaboration among departments in production planning, manufacturing companies should establish clear lines of communication and encourage open dialogue. This can be achieved through regular meetings, cross-functional teams, and other collaborative initiatives. It's also important to establish a culture of collaboration and teamwork, where departments are encouraged to work together and share their knowledge and expertise.
Overall, collaboration among departments is a critical component of effective production planning. By working together and sharing information and expertise, departments can ensure that production processes are optimized, resources are used efficiently, and the company is able to achieve its goals and objectives.
Continual monitoring and adjustment of plans
Continual monitoring and adjustment of plans is another essential best practice in production planning. The production planning process is not a one-time event; it's an ongoing process that requires constant monitoring and adjustment to ensure that plans are on track and aligned with changing market conditions and business objectives.
In this section, we will discuss the importance of continual monitoring and adjustment of plans in production planning and provide guidance on how to achieve it effectively.
Firstly, continual monitoring of production plans allows companies to identify potential problems early on and take corrective action before they become major issues. For example, if the production department is falling behind schedule, this can be identified through ongoing monitoring, and adjustments can be made to production schedules to ensure that deadlines are met. This can help to reduce the risk of delays, improve efficiency, and maintain customer satisfaction.
Secondly, continual adjustment of production plans allows companies to respond quickly to changing market conditions and customer demands. For example, if there is a sudden surge in demand for a particular product, the production plan can be adjusted to increase production and ensure that customer needs are met. This can help to increase sales, improve customer satisfaction, and strengthen the company's position in the market.
To achieve effective continual monitoring and adjustment of plans in production planning, manufacturing companies should establish regular review processes and performance metrics. This can include regular meetings to review progress, analyze performance data, and identify areas for improvement. It's also important to establish a culture of continuous improvement, where teams are encouraged to identify problems and suggest solutions proactively.
Overall, continual monitoring and adjustment of plans is a critical component of effective production planning. By monitoring plans regularly and making adjustments as needed, companies can ensure that they remain on track to achieve their goals and objectives, respond quickly to changing market conditions, and optimize their production processes for maximum efficiency and productivity.
Implementation of lean manufacturing principles
Implementation of lean manufacturing principles is a key best practice in production planning that can help companies optimize their production processes, reduce waste, and improve efficiency. Lean manufacturing is a philosophy that emphasizes continuous improvement and the elimination of waste throughout the production process.
In this section, we will discuss the importance of implementing lean manufacturing principles in production planning and provide guidance on how to achieve it effectively.
Firstly, implementing lean manufacturing principles in production planning can help companies to identify and eliminate waste in their production processes. This can include reducing inventory levels, minimizing transportation and movement, and eliminating unnecessary steps in production. By streamlining production processes, companies can reduce costs, improve efficiency, and increase throughput.
Secondly, lean manufacturing principles emphasize the importance of continuous improvement and empowering employees to identify and solve problems proactively. This can help to create a culture of innovation and continuous improvement, where employees are encouraged to identify opportunities for improvement and implement changes to optimize production processes.
To achieve effective implementation of lean manufacturing principles in production planning, manufacturing companies should focus on identifying areas of waste and inefficiency in their production processes, and developing strategies to address them.
This can involve adopting lean manufacturing tools and techniques, such as value stream mapping, 5S, and Kaizen, as well as providing training and support to employees to ensure that they have the skills and knowledge needed to implement these principles effectively.
Overall, implementation of lean manufacturing principles is a critical component of effective production planning. By adopting a lean manufacturing philosophy and focusing on continuous improvement, companies can optimize their production processes, reduce waste, and improve efficiency, leading to increased profitability and a stronger competitive position in the market.
Importance of communication
Effective communication is essential in production planning to ensure that all departments are aligned on production goals and schedules, and to identify and address any issues or bottlenecks in the production process. In this section, we will discuss the importance of communication in production planning and provide guidance on how to establish effective communication channels.
Clear communication between departments is necessary to ensure that everyone is working towards the same production goals and schedules. This involves sharing production plans, schedules, and forecasts with all relevant departments, including sales, purchasing, production, and logistics. This ensures that all departments have a clear understanding of the production plan and can work together to achieve it.
Effective communication also enables departments to identify and address any issues or bottlenecks in the production process proactively. This can include identifying material shortages, machine breakdowns, or scheduling conflicts, and addressing them quickly to avoid delays or disruptions in production.
To establish effective communication channels in production planning, companies should prioritize transparency and collaboration among departments. This can involve holding regular meetings to discuss production plans and schedules, setting up communication platforms such as email, messaging apps, or project management tools, and providing training and support to employees to ensure that they understand the importance of communication in production planning.
Overall, effective communication is critical in production planning to ensure that all departments are aligned on production goals and schedules, and to identify and address any issues or bottlenecks in the production process proactively. By establishing clear communication channels and prioritizing collaboration among departments, companies can improve efficiency, reduce waste, and increase profitability.
Challenges in Production Planning
Despite the many benefits of production planning, there are also several challenges that manufacturers face when implementing production planning strategies. In this section, we will explore some of the most common challenges in production planning and discuss strategies for overcoming them.
Common production planning challenges
Production planning can be a complex process that involves coordination between different departments, managing resources, and adapting to changes in demand. Here are some of the most common challenges that manufacturers face in production planning:
- Uncertainty in demand: One of the biggest challenges in production planning is uncertainty in demand. Manufacturers must be able to accurately forecast demand to ensure that they have enough inventory and production capacity to meet customer needs. However, changes in customer demand, supply chain disruptions, or unexpected events can make it difficult to predict demand accurately.
To overcome this challenge, manufacturers can use advanced forecasting methods, such as predictive analytics, machine learning, or simulation models, to improve the accuracy of demand forecasts. They can also use flexible production strategies, such as just-in-time (JIT) or lean manufacturing, to adjust production quickly to changes in demand.
2. Resource allocation: Another common challenge in production planning is allocating resources effectively. Manufacturers must ensure that they have enough raw materials, labor, and equipment to meet production targets while minimizing waste and optimizing efficiency. However, resource constraints, such as limited inventory or production capacity, can make it difficult to balance supply and demand.
To overcome this challenge, manufacturers can use production planning software to optimize resource allocation and improve efficiency. They can also use lean manufacturing techniques, such as value stream mapping, to identify and eliminate waste in the production process.
3. Coordination between departments: Production planning requires coordination between different departments, such as sales, production, purchasing, and logistics. However, communication breakdowns or conflicting priorities can make it difficult to align production plans and schedules across departments.
To overcome this challenge, manufacturers can establish clear communication channels and prioritize collaboration among departments. This can involve holding regular meetings to discuss production plans and schedules, setting up communication platforms, such as email or project management tools, and providing training and support to employees to ensure that they understand the importance of communication in production planning.
4. Managing lead times: Another challenge in production planning is managing lead times, which is the time between placing an order and receiving the finished product. Long lead times can make it difficult to respond quickly to changes in demand or supply chain disruptions, while short lead times can increase the risk of stockouts or production delays.
To overcome this challenge, manufacturers can use production planning software to optimize lead times and improve delivery times. They can also work with suppliers to improve lead times for raw materials or components, and use agile manufacturing techniques, such as modular production or cross-training, to improve flexibility and responsiveness in the production process.
Overall, production planning requires careful coordination and management of resources, demand, and production schedules. By addressing these common challenges, manufacturers can improve efficiency, reduce waste, and increase profitability.
Strategies for overcoming challenges
Production planning is a complex process and can face various challenges that can impact the productivity and efficiency of manufacturing operations. Here are some strategies to overcome these challenges:
- Flexibility: One way to overcome production planning challenges is by being flexible. Manufacturing companies need to be able to quickly adapt to changes in demand, supply chain disruptions, or unexpected events. This can be achieved by having contingency plans, having multiple suppliers, and being open to changing production schedules.
- Collaboration: Collaboration and communication among different departments is essential for successful production planning. Different departments such as sales, production, and inventory management need to work together to develop an effective production plan. This will help in identifying potential issues and finding solutions quickly.
- Advanced technology: The use of advanced technology such as production planning software, automation, and data analytics can help to overcome production planning challenges. These tools can provide real-time data on inventory, production schedules, and demand, enabling manufacturers to make informed decisions and adjust production plans accordingly.
- Continuous improvement: Continuously monitoring and analyzing production planning processes can help to identify areas for improvement. Manufacturers can use techniques such as lean manufacturing and Six Sigma to identify and eliminate inefficiencies and improve overall productivity.
- Skilled workforce: Having a skilled and well-trained workforce is crucial for successful production planning. This can be achieved by providing training and development programs for employees to enhance their skills and knowledge in production planning processes.
By implementing these strategies, manufacturers can overcome production planning challenges and achieve greater productivity, efficiency, and profitability in their operations.
Conclusion
In conclusion, production planning is a critical process in manufacturing that ensures products are produced efficiently, cost-effectively, and delivered on time to customers. This beginner's guide has provided an in-depth understanding of the key concepts, components, and best practices in production planning.
We have explored the different types of production planning systems, the importance of technology, and the challenges faced in the process.
By understanding the fundamentals of production planning manufacturing and implementing best practices, manufacturers can improve their operations, optimize resources, reduce waste, and improve customer satisfaction. The use of advanced technology, collaboration among departments, continual monitoring and adjustment of plans, and a skilled workforce can help manufacturers overcome production planning challenges and achieve their goals.
In conclusion, production planning is an ongoing process that requires continuous improvement, flexibility, and adaptation to meet the changing demands of customers and the marketplace. By following the best practices outlined in this guide, manufacturers can develop effective production plans, optimize their operations, and achieve long-term success in the manufacturing industry.
How can Manufacturers further their Learning and Implementation?
If you are a manufacturer or aspiring to be one, it is crucial to understand the fundamentals of production planning to achieve success. This guide has provided an overview of the key concepts, components, and best practices in production planning, and the challenges that may be encountered.
To further your learning and implementation, we encourage you to take the time to research and explore different production planning software and technologies that can enhance your manufacturing operations. You can also seek out industry experts or consultants to provide guidance and expertise in production planning.
Remember that production planning is an ongoing process, and continual improvement is essential for success. Keep yourself updated with the latest trends and best practices in production planning and strive to implement them in your manufacturing operations.
By investing time and effort in learning and implementing best practices in production planning, you can optimize your operations, improve customer satisfaction, and achieve long-term success in the manufacturing industry.
How can Deskera Help You?
Deskera ERP and MRP systems help you to keep your business units organized. The system's primary functions are as follows:
- Keep track of your raw materials and final items inventories
- Control production schedules and routings
- Keep a bill of materials
- Produce thorough reports
- Make your own dashboards
Deskera's integrated financial planning tools enable investors to better plan and track their investments. It can assist investors in making faster and more accurate decisions.
Deskera Books allows you to better manage your accounts and finances. Maintain good accounting practices by automating tasks like billing, invoicing, and payment processing.
Deskera CRM is a powerful solution that manages your sales and helps you close deals quickly. It not only enables you to perform critical tasks like lead generation via email, but it also gives you a comprehensive view of your sales funnel.
Deskera People is a straightforward tool for centralizing your human resource management functions.
Key Takeaways
- Production planning is a critical process that helps manufacturers optimize their operations and achieve long-term success in the industry.
- Sales forecasting and demand planning are essential components of production planning as they enable manufacturers to anticipate demand and plan accordingly.
- Material requirements planning (MRP) helps manufacturers ensure they have the right materials and components to meet production requirements.
- Capacity planning enables manufacturers to determine the amount of production that can be completed in a given time frame.
- Production scheduling is a vital component of production planning as it ensures that production occurs in the most efficient and effective manner.
- Inventory management is essential in production planning to ensure that the right amount of inventory is available to meet production needs without overstocking.
- The use of technology, such as production planning software, can significantly enhance the efficiency and effectiveness of production planning.
- Collaboration among departments is crucial to ensure all teams are working towards a common goal and that the production plan is optimized.
- Continual monitoring and adjustment of plans are necessary to ensure that production is meeting expectations and that any issues are addressed promptly.
- Implementing best practices such as establishing clear goals and objectives, lean manufacturing principles, and effective communication can help manufacturers overcome challenges and optimize their operations.
Related Articles
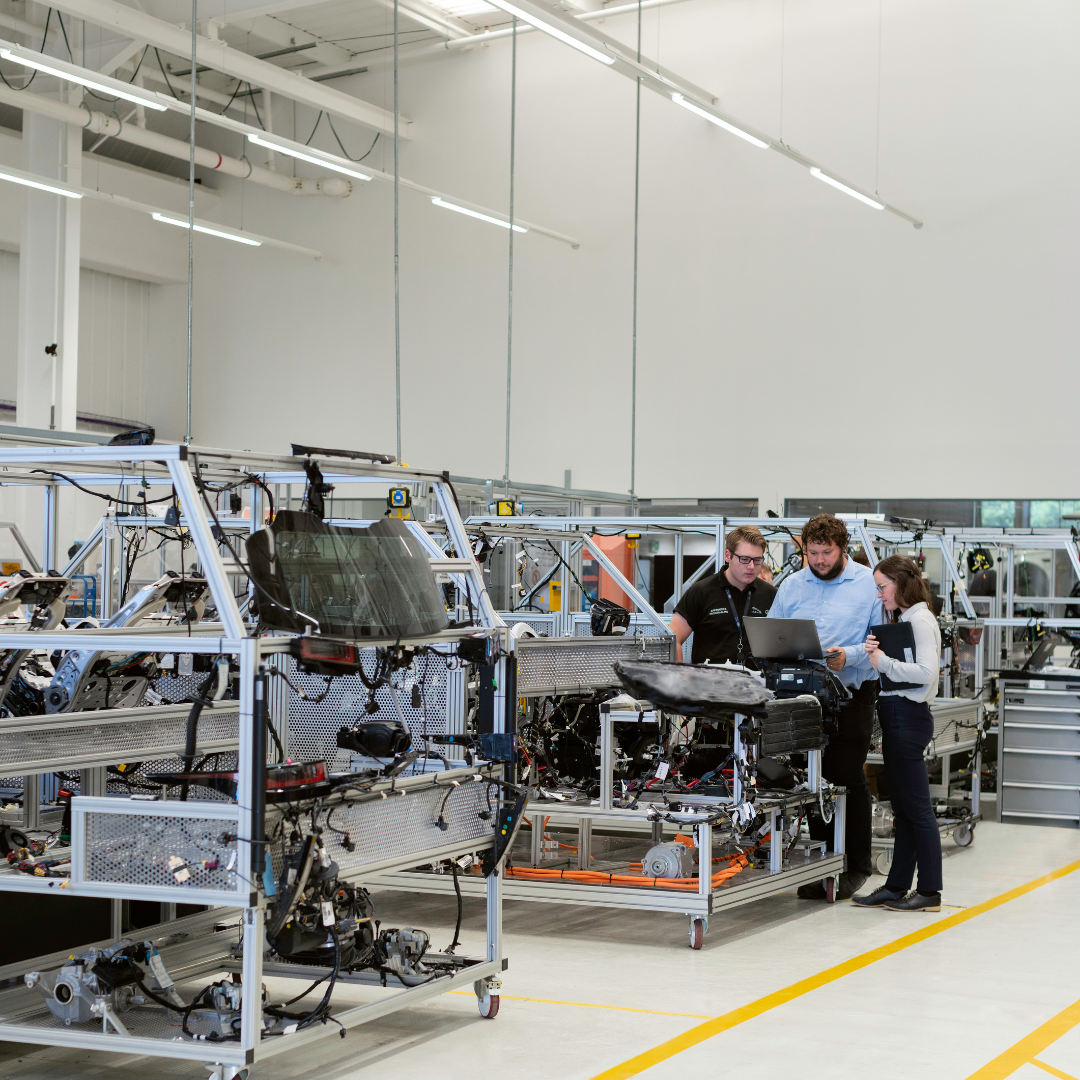
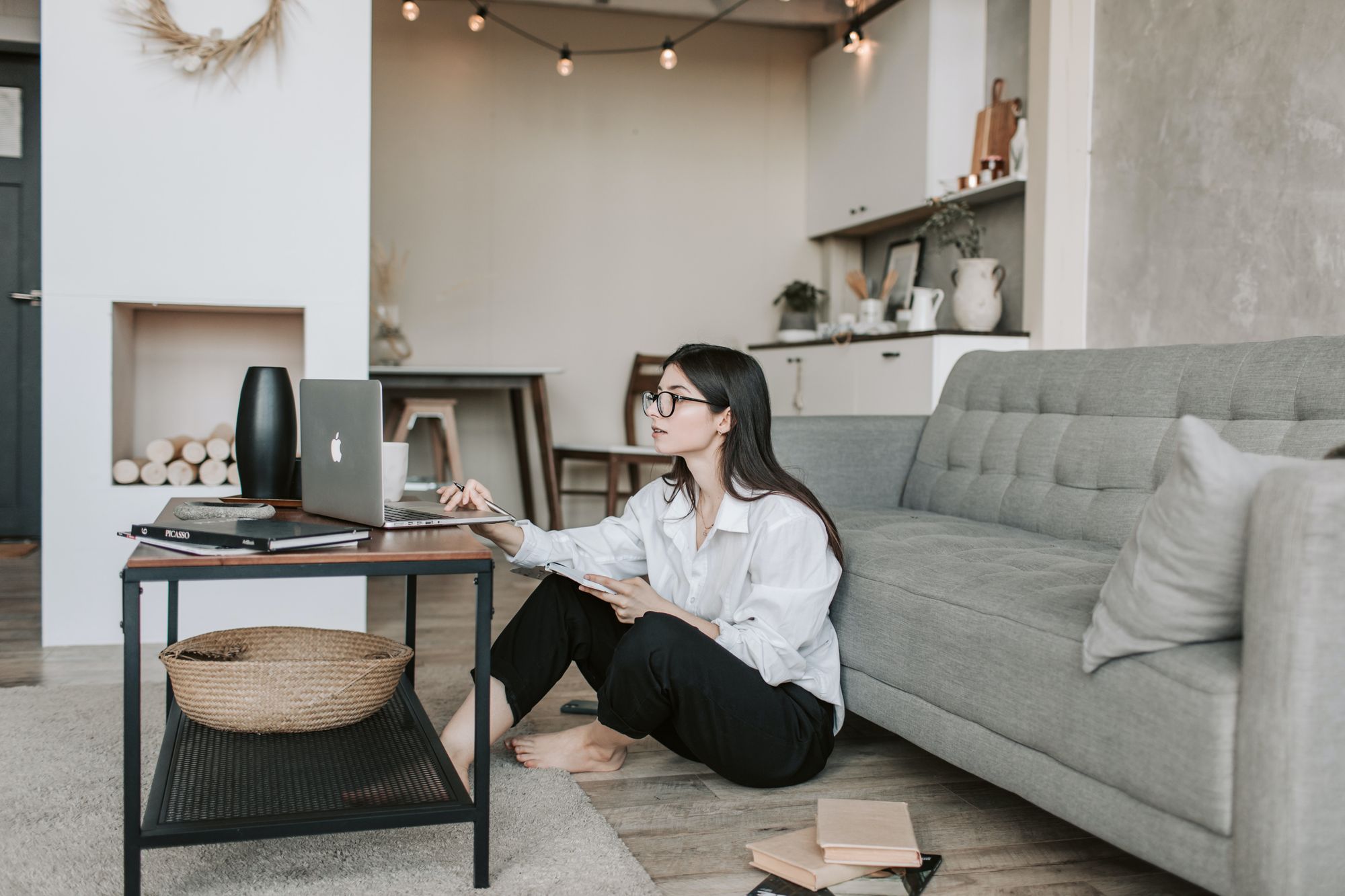
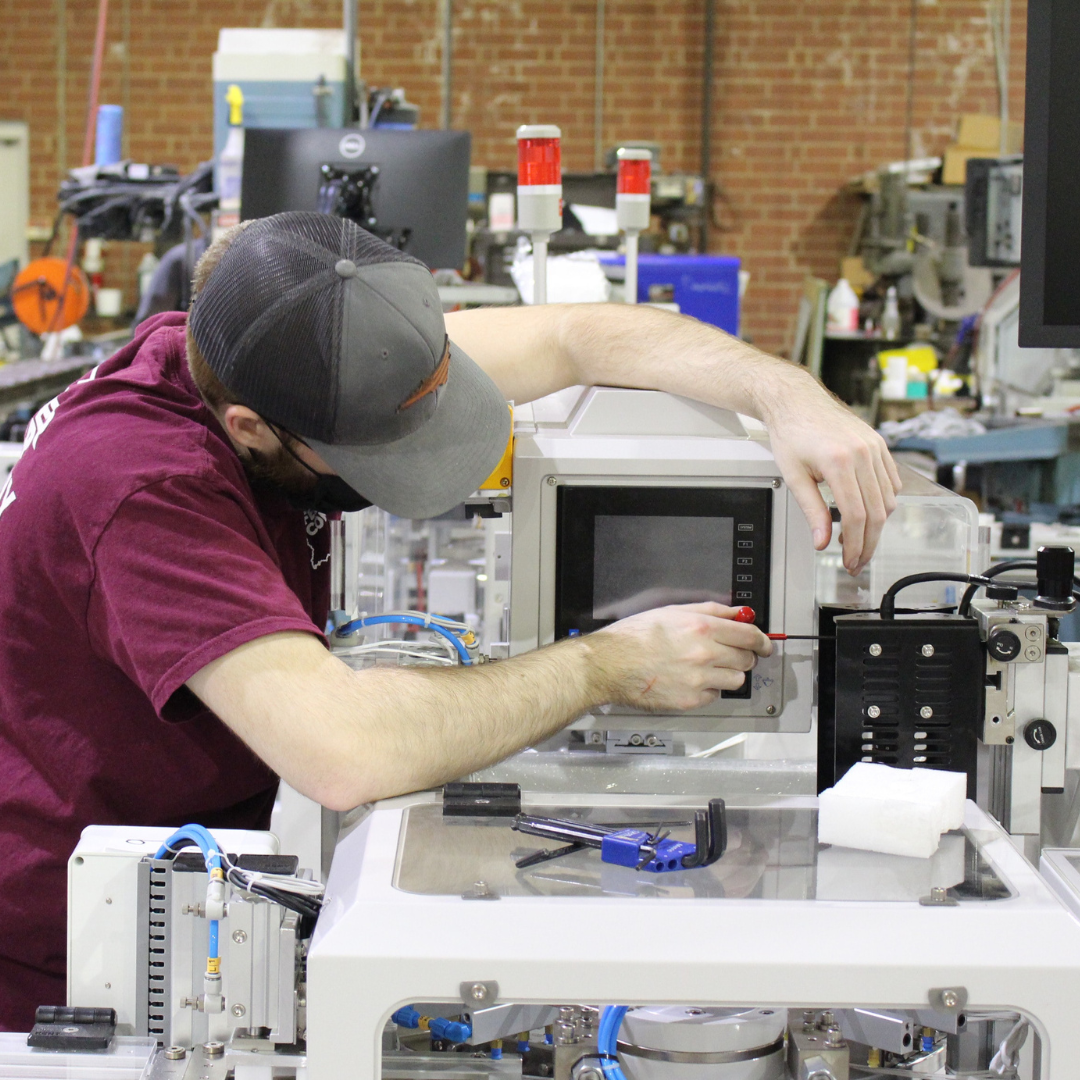
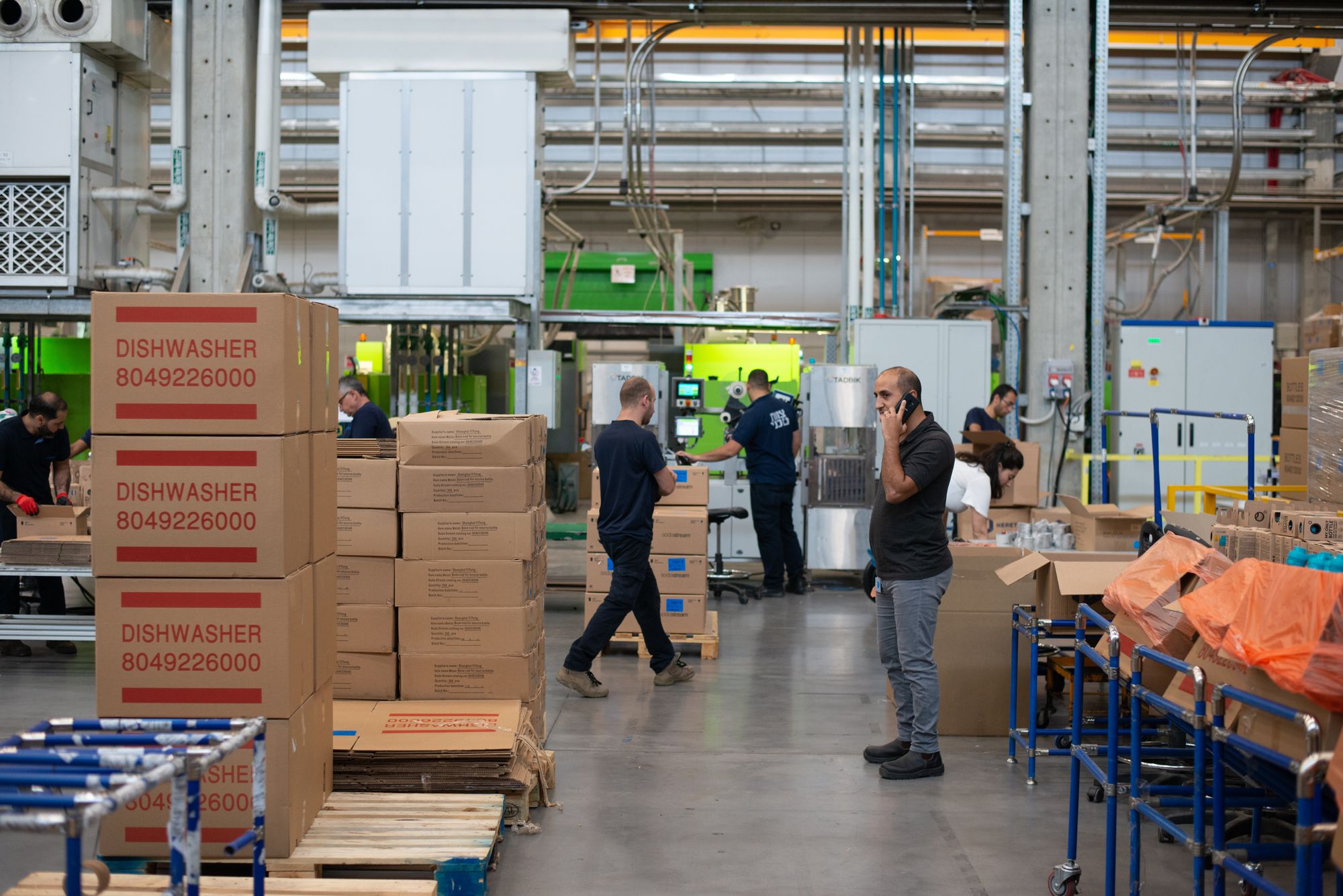