Is your company facing increasing demand for its products or services, but the pipeline inventory is dwindling? If you haven't started stockpiling inventory in preparation for future growth, you may be in for a rude awakening.
Pipeline inventory refers to the number of items that a company is ready and willing to produce and sell to customers. When demand outpaces production capacity, it can lead to shortages and price hikes. This situation can be difficult to weather, because customers may become disgruntled and switch to competitors.
If you want your business to thrive in an unpredictable market, it’s essential that you stockpile inventory. In this guide, we’ve discussed pipeline inventory in detail and its related concepts.
Let’s take a look at the table of content:
- What is Pipeline Inventory?
- Understanding Pipeline Inventory
- Significance of Pipeline Inventory for your Business
- Pipeline Inventory Function
- Pipeline Inventory Formula
- Pipeline Inventory Example
- What is the Need for Pipeline Inventory Calculation?
- Pipeline Stock in Inventory Management
- What does Decoupling Inventory Mean?
- Common Challenges Associated with Maintaining a Pipeline Inventory System
- Maintaining Pipeline Inventory Advantages
- Top 5 Tips for Effectively Managing your Pipeline Inventory
- Frequently Asked Questions (FAQs) Associated with Pipeline Inventory
- How Deskera Can Assist You?
- Final Takeaways
Let's get started!
What is Pipeline Inventory?
Pipeline inventory, also known as “pipeline stock” and "expected on-order inventory," refers to those goods that a business has ordered from suppliers or middlemen but has not yet received at its premises.
This includes products that the supplier is now manufacturing, products that are already being produced by the supplier, as well as products that are currently in transit between storage or production facilities.
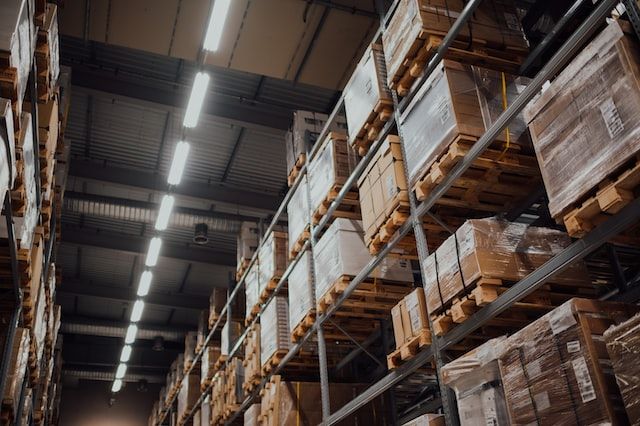
The capacity to organize production or shipments ahead of time without requiring the actual availability of the necessary commodities is one benefit of tracking pipeline inventories.
Note: The concept of ‘Pipeline Inventory’ is quite similar to that of ‘work-in-progress (WIP) inventory.’ In the former inventory, the finished good is still under the process of delivery. Whereas, in the latter inventory — the products are still under production.
Understanding Pipeline Inventory
Pipeline inventory is a particular kind of inventory buffer used during inventory control. By allowing extra room for the availability of stock goods, inventory buffers help to ensure steady business and production flow.
This further can prevent changes in supply and demand, lessen opportunity loss, prevent disruptions in component supply, and have an impact on a variety of other measures.
When there are long wait periods for parts and suppliers, pipeline inventory is employed as a safety net.
Manufacturers who have a strong handle on their pipeline inventory can place such orders frequently rather than only when a manufacturing order is received in order to avoid stock-outs or overstocking. This greatly reduces lead while also ensuring a consistent flow into stock.
Goods that are in the pipeline can be scheduled into new manufacturing orders once they arrive at a warehouse with the help of correctly configured inventory management software.
Considering these movable components is necessary to maintain output when components have far-off shipment dates. Booking en route components into new manufacturing orders frequently requires the use of competent MRP/ERP software. It is because doing so manually would be prohibitively complex for even small enterprises.
Significance of Pipeline Inventory for your Business
Assessing how much pipeline inventory is arriving makes it considerably simpler to plan for client demand. The amount of inventory that is now present at every stage of the supply chain is also fully depicted.
By calculating and keeping track of the worth of your pipeline inventory, you can better manage your stock and steer clear of common issues like amassing too much deadstock.
For instance, if you're only estimating how much inventory you need based on what's on hand, you can overthink the fact that you already have goods in route.
Due to import fees, taxes, and protracted delivery delays, placing an order for items from another country can be very challenging (on top of typically long transit times, the pandemic has led to severe port congestion, significantly extending timelines).
In light of past inventory performance trends and actions, you should have certain pipeline goods in transit.
For instance, the value of your pipeline inventory will probably rise during the busiest shipping season and the holidays.
If you are aware that new goods typically take to arrive, you may change your delivery timelines and restock value to consider carrier delays.
Pipeline Inventory Function
Pipeline inventory describes goods that are still in the company's shipping chain but have already reached their destination.
The items are still considered to be a part of the shipper's inventory while they are traveling, even if the recipient has not paid for them.
When the recipient pays for the things, the pipeline inventory shows up on the recipient's inventory list even though the receiver hasn't really taken physical possession of the goods.
Products that have been ordered, paid for and shipped into a company's supply chain from the buyer's pipeline inventory.
Even though the buyer hasn't paid for the goods yet and they're still considered to be the manufacturer's or seller's inventory, after a payment is made, regardless of whether the client has custody of the products, they become the recipient's pipeline inventory.
Pipeline Inventory Formula
For the purposes of production management and accounting, it is helpful to know how much of a company's inventory is in the pipeline and how much of it should be retained in the pipeline.
To calculate pipeline inventory, multiply each item's lead time by its expected or actual demand rate.
Note: The lead time is the interval of time between the point at which a corporation manufactures the good and the time required for delivery.
You only learn how much pipeline inventory you presently have from this calculation.
On the other side, in order to avoid any costs related to transportation and holding inventory, it is possible to apply the Economic Order Quantity (EOQ) calculation to estimate how much inventory to actually order. Both must be understood while managing inventories for an online store.
Pipeline Inventory Example
For example, if a component needed additional assembly after it arrived at the production site, which would add another day, the order would have a lead time of 21 days, or three weeks. The demand rate should be expressed in units per interval.
Assume that there is a weekly demand for five units of the product. The quantity of components that must maintain in stock is determined by multiplying the lead time of three (weeks) by the demand rate of five.
In order to ensure dependable production and maintain constant inventory levels, the organization should, on average, have 20 components on order.
For instance, the cost of each component is $100. The value of pipeline inventory can be calculated as 20 x $100 equals $2,000.
When planning, the strategy mentioned above is a solid place to start. It does not, however, say when to place an order or what the pipeline's status is right now.
However, it does allow for the deduction that if the company purchases components for the production of the upcoming three weeks today, a fresh order for 20 extra components should be placed immediately, barring the use of safety stock.
However, there are some situations when ordering five units weekly instead of 20 units every three weeks makes more sense. Additionally, there may be situations in which a corporation decides to fill up stocks for a long period because keeping a stable pipeline inventory is absolutely unneeded.
One method to decide how much to order all at once is to calculate the Economic Order Quantity (EOQ).
This theoretical order quantity seeks to lower inventory expenses by striking the appropriate balance between ordering costs (such as shipping and handling) and holding costs.
When demand is stable and an organization already has a firm understanding of the annual demand rate and carrying cost per unit, as is the case with many factories who apply the make-to-stock technique, EOQ is frequently used.
What is the Need for Pipeline Inventory Calculation?
A pipeline inventory calculation must be done to determine how much money is locked up in inventory, as well as other costs like transportation and carrying costs.
It's also essential for businesses with protracted lead periods. Businesses that have substantial cash invested in inventories must make sure that the asset's value is properly reflected on their balance sheet.
You won't have a thorough understanding of your company's cash flow until that time, neither will your board, your investors, or the leadership.
Pipeline Stock in Inventory Management
Inventory management can be greatly enhanced by gaining a full understanding of the products that are in transit.
Creating data-based forecasts based on a range of order placement-related characteristics is referred to in this context as forecasting.
Since the pipeline stock gives transparency on the product's position in the production process, businesses who are aware of the exact location and quantity of their items in transit are better equipped to forecast demand or order volume.
What does Decoupling Inventory Mean?
Decoupling inventory is the process of dividing a stock into its component parts. Avoiding unplanned production halts and other disruptions is the aim.
In this way, decoupling inventory can be seen as a specific type of safety stock. Inventory decoupling gives businesses a safety net they may fall back on in the case of unplanned slowdowns or volatility.
The inventory is broken down into a number of things and components, many of which come from different sources. Each of these components will also have unique variables and lead times.
Decoupling inventory is not a strategy to get ready for peak demand or the holiday season. In that area of inventory management, sales forecasting would be more helpful in calculating the optimal stock levels.
Furthermore, decoupling inventory serves as a type of protection against any issues that can develop and affect the pipeline inventory.
Decoupling Inventory Example
Stock decoupling is a typical practice among manufacturers. Think about a scenario where a manufacturer of guitars needs to source electronics, guitar necks, and guitar bodies from three different suppliers. Each part can be used to assemble one guitar.
Only the finished guitars we had on hand may be counted. However, producers can learn far more by decoupling inventories. Specifically, how many guitar necks, bodies, and electronics are available. By doing this, excess or insufficient stock of assembly parts will be avoided.
The decoupled inventory can perform similarly to pipeline inventory in terms of lead times. Component orders can be made to fit different lead times and production schedules. However, the manufacturer can also store a stock of the necessary components at their facility using the decoupled inventory system.
There will be variations in the wave durations and manufacturing rates of various products in the decoupling inventory. This may even be more noticeable when dealing with goods from abroad.
In essence, ordering assembly pieces eliminates manufacturing bottlenecks. As a result, consumer-ready product inventory levels and holding costs can be reliable.
In the absence of bottlenecks, retailers should plan for continuous lead times and maintain appropriate stock levels. Thus, a business can improve its cash flow. however, helps keep production going. By better preparing for unforeseen supply chain delays, this is achieved.
Common Challenges Associated with Maintaining a Pipeline Inventory System
Following, we’ve discussed several common challenges associated with maintaining a pipeline inventory system. Let’s learn:
1. Keeping Track of Inventory from Several Vendors
You probably have many suppliers to keep track of when keeping pipeline inventory, and as your firm expands, that number may rise.
It is difficult to store or retain all supplier information using a manual method like spreadsheets or paper documents, including lead times and minimum order amounts for purchase orders.
2. Recognizing the Cost of the Inventory Investment
It's easy to forget about a product that has been lying in your pipeline for months—and subsequently, the money you set aside for it—depending on your supplier lead times.
Many e-commerce businesses struggle to determine the amount of cash stored in pipeline inventories accurately. For accounting purposes and to show it correctly on your balance sheet, you must be aware of it.
3. Risk of Human Error
Monitoring pipeline inventory presents a significant risk of human error, particularly as your business grows.
Manually updating where your product is in transit from each of your suppliers requires work and is prone to inaccuracy.
Spreadsheet-based pipeline inventory management can lead to problems like inaccurate data or data silos that leave critical decision-makers in the dark.
Controlling every part of your business, including orders and warehouse inventories, may quickly make things more difficult and raise the risk of human error.
4. Shipping Issues
Your suppliers could experience shipping problems anytime, as we've seen in recent years. You could have to cope with unusually extended lead times when this happens, resulting in items being out of stock for longer than anticipated.
Maintaining Pipeline Inventory Advantages
Even though most manufacturing companies always have some inventory items in the pipeline, meticulously managing pipeline inventory is a good idea for several reasons.
The following are the main advantages of keeping track of pipeline inventories:
- Process improvements and shorter lead times for goods requiring components with slow shipping periods.
- Improved methods of calculating the lead time for production orders.
- An enhanced understanding of the shipping process, price, and supply chain strategy improved production planning and inventory forecasting.
- Enhanced supply chain efficiency resulted in lower holding costs for standing inventory.
Except for small enough firms that can manually handle their limited pipeline stock, most businesses track and manage their pipeline inventory using specialized or integrated inventory management and optimization software. This could be considered an extra expense.
However, it almost always occurs because it is only possible to remain competitive in the industrial sector with a complete understanding of your inventory and its movements. In the face of quick market shifts and supply chain disruptions, extensive pipeline inventories may provide certain risks.
This can be somewhat mitigated by setting aside time for strategic product management and capacity planning.
Top 5 Tips for Effectively Managing your Pipeline Inventory
Following, we've discussed the five best tips for effectively managing your pipeline inventory. Let's Learn:
#Tip 1: Establish a System for Real-time Inventory Management
The pipeline inventory data you need, such as the location of the inventory, the amount of money in the pipeline inventory, and any shipment delays, is provided to merchants in real time by an inventory management system at every stage of the supply chain.
These technologies also help you automatically generate purchase orders from suppliers when your inventory levels across all sales channels become low.
You can quickly adjust to issues to keep your business running smoothly when you have access to valuable and convenient pipeline inventory data.
#Tip 2: For Pipeline Inventories, Inventory Forecasting is Required
You will know how much inventory you need to buy from merchants once you forecast it. For pipeline inventory, accurate forecasting is essential.
Using real-time data to forecast product demand is more accurate than making an educated guess or manually figuring out how much inventory you need.
In this case, the benefits of an automated inventory management system with stock forecasting are utilized. You are no longer required to manually estimate the quantity of inventory you need and the timing of vendor orders.
#Tip 3: Implement Third-Party Integrations
A solid inventory management system will offer the integrations you require to manage your pipeline and any other business inventory cycles.
You can integrate with retail channels like Amazon, Walmart, and Shopify as well as social media platforms like TikTok.
You can also include the channels used by customers in your target market.
This level of connectedness teaches you when to ask suppliers to restock your inventory, helping you avoid stockouts and underselling inventory.
#Tip 4: Identify the Location of the Inventory in the Supply Chain
Using an automated inventory management system, you can keep track of inventory levels across all warehouse locations and know exactly where inventory is in the supply chain.
Think about the situation where you recently ordered inventory from one of your vendors. If you employ an automated system, you will know exactly how much and what kind of goods you have requested from that vendor.
You can track the location of your goods once orders are fulfilled without spending a lot of time exploring spreadsheets by removing the chance of human error.
When transporting the pipeline inventory, be sure to have a backup plan in case of any shipping issues.
Having a wide variety of providers is one strategy to reduce shipping risks if one supplier needs to fulfill your order demand promptly.
#Tip 5: Consider Placing a Safety Stock
If lead time fluctuations and supplier delays occur, a safety stock should be kept on hand. Keeping more inventory on hand than is required to satisfy consumer demand is known as safety stock.
Why store safety equipment? The risk of stockouts, which result in lost sales opportunities and future recurring revenue, is decreased by maintaining a safety stock level. Operations in the supply chain frequently run into issues.
Depending on your business, you might require a specific amount of safety stock. The basis for safety stock levels can be a proportion of cycle stock levels. How much buffer or wiggle room a firm is willing to hold is another factor influencing how much safety stock to keep on hand.
Frequently Asked Questions (FAQs) Associated with Pipeline Inventory
Following, we’ve discussed some common and crucial frequently asked questions (FAQs) associated with pipeline inventory. Let’s learn:
Que 1: What is a Pipeline Supply Chain?
Ans: The pipeline supply chain refers to the procedure that the raw materials for your products go through before being used in manufacturing. When there are fewer materials, the pipeline supply chain is less complicated.
The supply chain, however, grows more intricate as a product's material requirements grow. Due to the manufacturing component, it is anticipated that the majority of organizations will have at least some pipeline inventory.
Que 2: Cycle Inventory and Pipeline Inventory: What's the Difference?
Ans: Cycle inventory refers to the amount of stock that a company keeps on hand to meet regular product demand.
Inventory that is in transit from the source to a warehouse or other physical place is referred to as inventory that is in the pipeline.
Que 3: What is the Meaning of In Transit Inventory?
Transit inventory, also known as transportation inventory or goods in transit, is any item that has been transported by a seller but has not yet been acquired by a buyer. It resembles pipeline inventory almost exactly.
But the company that is marketing and distributing the item is the one that employs the phrase most frequently. It offers an alternative viewpoint on a shipment order for unfinished work.
The primary consideration for shippers is the point at which inventory ownership is legally passed to the buyer. Or the buyer really completes the transaction. That might happen either way:
- When the inventory or goods are loaded aboard the freight ship, also known as the freight-on-board shipping point, or
- When the inventory is delivered to the buyer, also known as the freight-on-board location
The exchange of money and, subsequently, inventory occurs at any of the two, depending on the terms of the buyer and seller's contract.
Que 4: In-Transit Inventory Cost: What is it?
The cost of pipeline inventory and its value to your business are both referred to as "in-transit inventory cost." The costs of transporting and storing the components are in addition to the price of purchasing them.
Calculating your company's in-transit inventory cost is much easier with the right formula. How to do it is as follows:
Step 1: Average shipment value x annual inventory carrying cost / 365 = daily carrying cost
Step 2: Daily carrying cost x number of days in transit = average shipping container cost
Step 3: Average shipping container cost x number of containers shipped = average in-transit inventory cost
Que 5: What is the Difference between Pipeline Inventory and Work-in-Progress?
Ans: Work-in-progress inventory is sometimes confused with inventory of pipeline.
Unlined pipeline inventory, also referred to as ready stock that has been bought but is still in transit, describes a ready product that is still going through several manufacturing processes. These objects are solely referred to as "work-in-progress (WIP)."
Factory-unfinished goods are referred to as WIP, yet both are included in the inventory. Pipeline inventory, on the other hand, refers to products that have moved past the production stage and are currently in the distribution stage.
Que 6: What is the Average Pipeline Inventory?
Your average pipeline inventory will be determined by the number of units you request with each order and the product lead time required. Due to the variety of each industry and supplier, it is challenging to standardize pipeline inventory across businesses.
However, you can use the following formula to get your own average pipeline inventory:
The average pipeline inventory is calculated by multiplying the quantity of units ordered each week by the lead time in weeks for the product.
If you order 1,000 units per week with a two-week lead time, your pipeline inventory will be 2,000 units.
Que 7: What is Safety Stock?
Your usual pipeline inventory is now known to you. When pipeline stock is considered, inventory management is more precise and efficient.
However, it does not reduce the risks brought on by production stops and transit delays. In this case, retailers would gradually see their inventory decline to zero.
Businesses that wait will miss out on potential sales. Retailers might have a reserve supply on hand to safeguard themselves from a drop in sales.
As a result, a corporation's holding costs will increase. Costs and benefits must therefore be balanced. The reserve stock amounts will differ for each business depending on a variety of factors. However, the basic formula for calculating safety stock is as follows:
This will provide you with the necessary amount to have on hand as a reserve.
Que 8: Difference between Safety Stock and Decoupling Inventory?
Ans: Despite having similar meanings and being widely used interchangeably, the words "safety stock" and "decoupled inventory" relate to two tasks with different goals.
As we've seen, decoupling inventory aims to avoid production pauses or delays by maintaining an additional stock of raw materials or components; it's intended to satisfy unforeseen internal needs.
Safety stock, on the other hand, is extra inventory kept on hand to satisfy unforeseen client demand surges or outside needs. Both provide a safety net to deal with unforeseen needs, one for internal and external demand.
How Deskera Can Assist You?
Deskera MRP allows you to closely monitor the manufacturing process. From the bill of materials to the production planning features, the solution helps you stay on top of your game and keep your company's competitive edge.
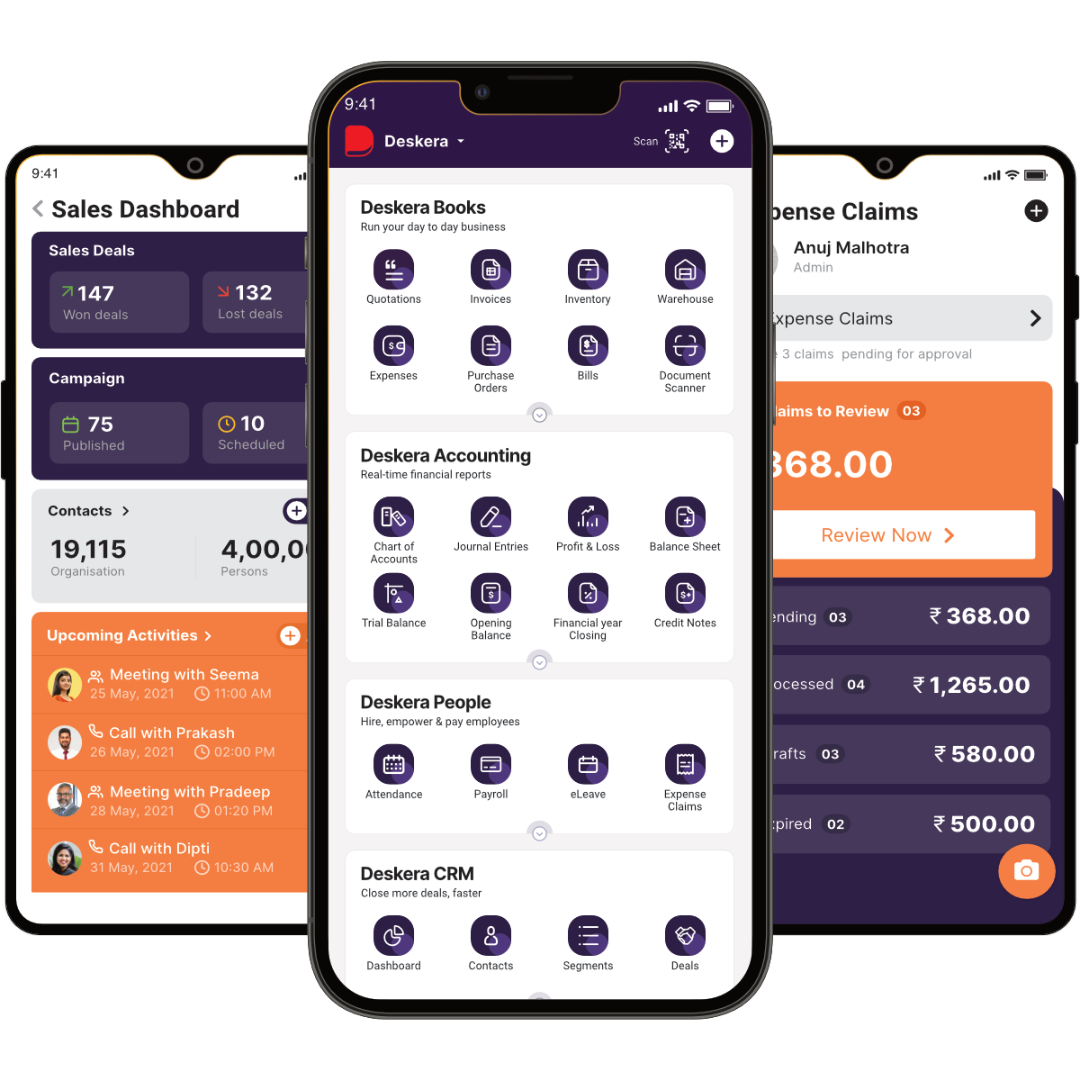
Deskera ERP and MRP system can help you:
- Manage production plans
- Maintain Bill of Materials
- Generate detailed reports
- Create a custom dashboard
Deskera ERP is a comprehensive system that allows you to maintain inventory, manage suppliers, and track supply chain activity in real-time, as well as streamline a variety of other corporate operations.
Deskera Books enables you to manage your accounts and finances more effectively. Maintain sound accounting practices by automating accounting operations such as billing, invoicing, and payment processing.
Deskera CRM is a strong solution that manages your sales and assists you in closing agreements quickly. It not only allows you to do critical duties such as lead generation via email, but it also provides you with a comprehensive view of your sales funnel.
Deskera People is a simple tool for taking control of your human resource management functions. The technology not only speeds up payroll processing but also allows you to manage all other activities such as overtime, benefits, bonuses, training programs, and much more. This is your chance to grow your business, increase earnings, and improve the efficiency of the entire production process.
Final Takeaways
We've arrived at the last section of this guide. Let's have a look at some of the most important points to remember:
- Pipeline inventory, also known as “pipeline stock” and "expected on-order inventory," refers to those goods that a business has ordered from suppliers or middlemen but has not yet received at its premises.
- Pipeline inventory is a particular kind of inventory buffer used during inventory control. By allowing extra room for the availability of stock goods, inventory buffers help to ensure steady business and production flow.
- By calculating and keeping track of the worth of your pipeline inventory, you can better manage your stock and steer clear of common issues like amassing too much deadstock.
- For the purposes of production management and accounting, it is helpful to know how much of a company's inventory is in the pipeline and how much of it should be retained in the pipeline.
- To calculate pipeline inventory, multiply each item's lead time by its expected or actual demand rate.
- Decoupling inventory is the process of dividing a stock into its component parts. Avoiding unplanned production halts and other disruptions is the aim.
- The pipeline inventory data you need, such as the location of the inventory, the amount of money in the pipeline inventory, and any shipment delays, is provided to merchants in real time by an inventory management system at every stage of the supply chain.
Related Articles
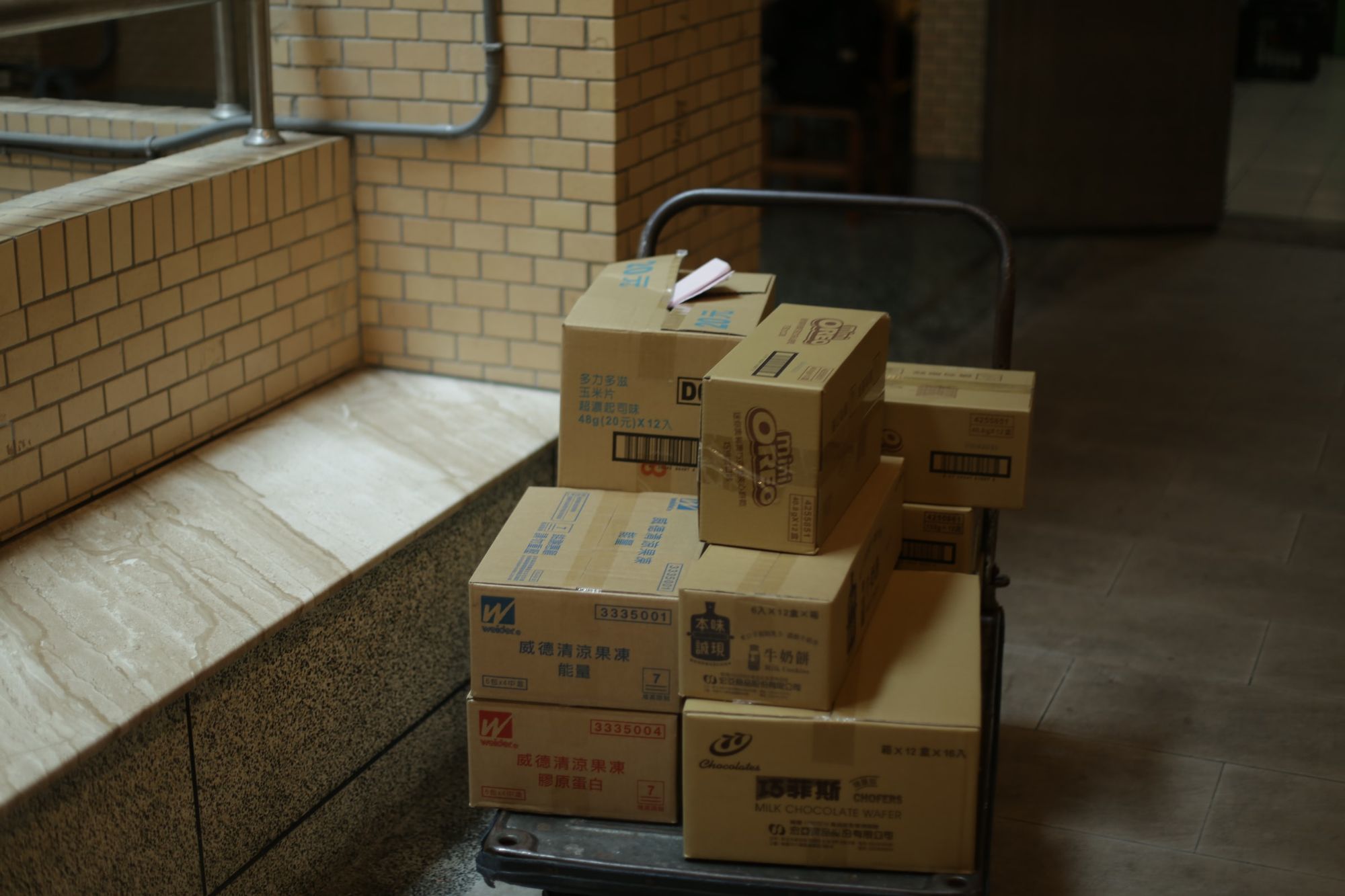
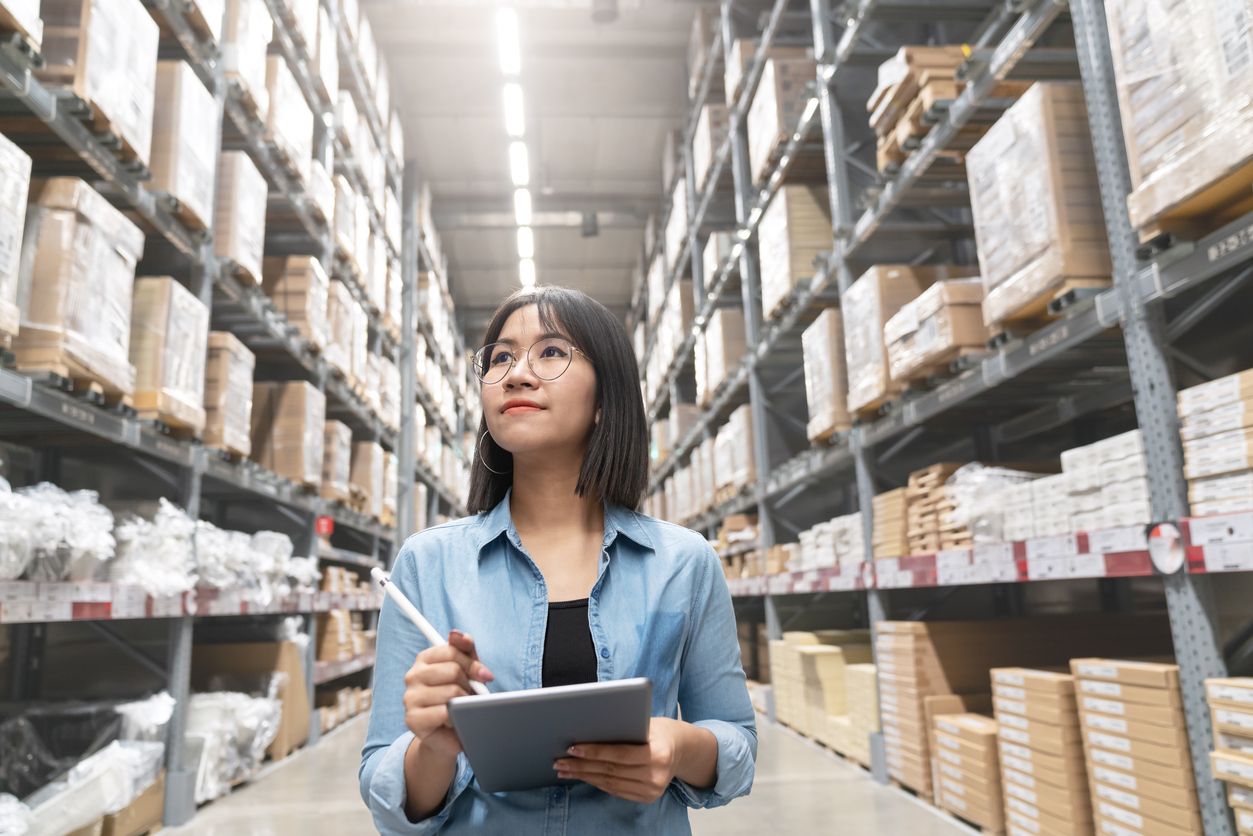
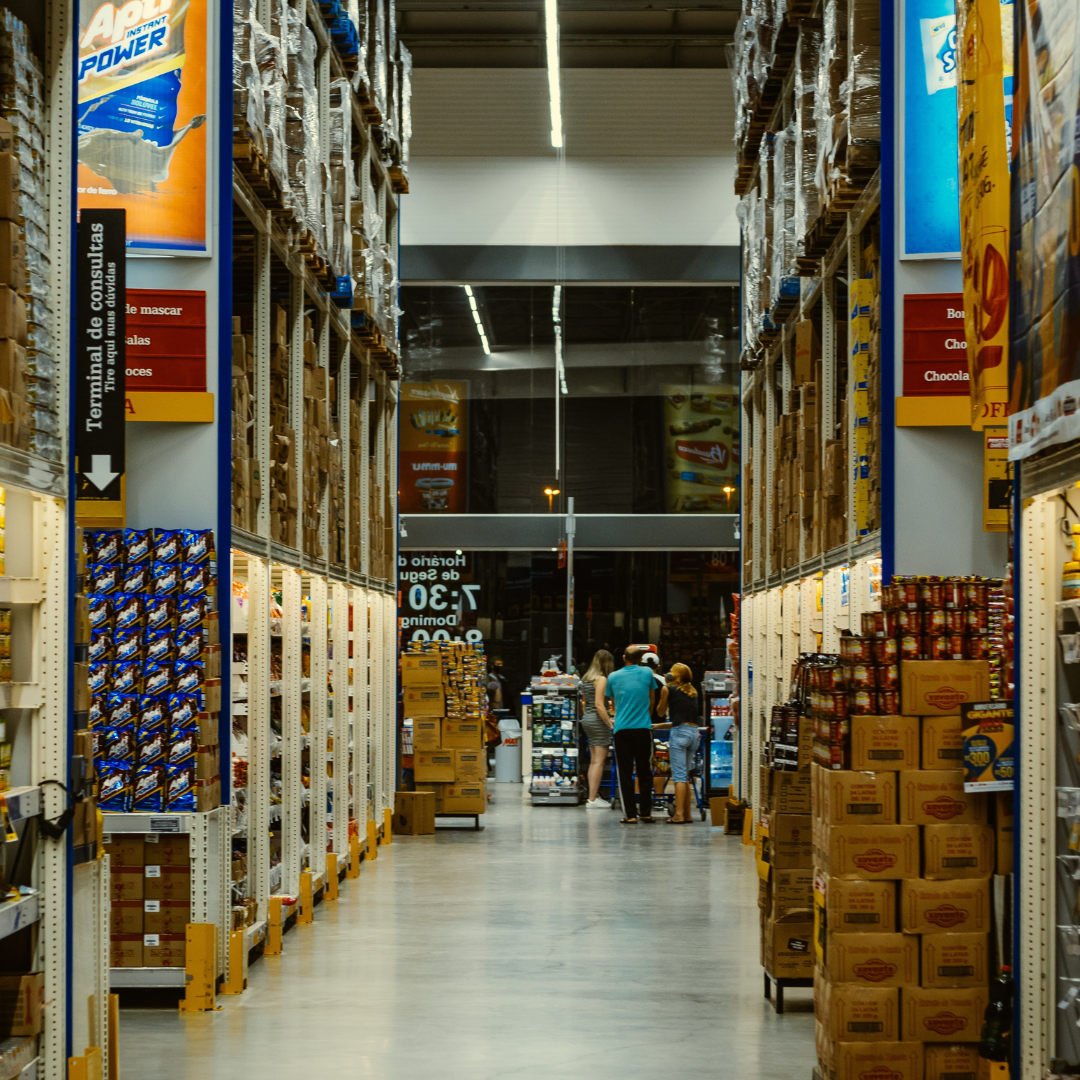