Manufacturing processes generate a lot of waste. From unused raw materials to scrap pieces, the amount of waste created in the manufacturing process can be staggering. But it doesn’t have to be. With the right strategies in place, manufacturers can reduce waste and become more efficient and profitable.
This article will introduce us to the ten remarkable ways to reduce waste in manufacturing.
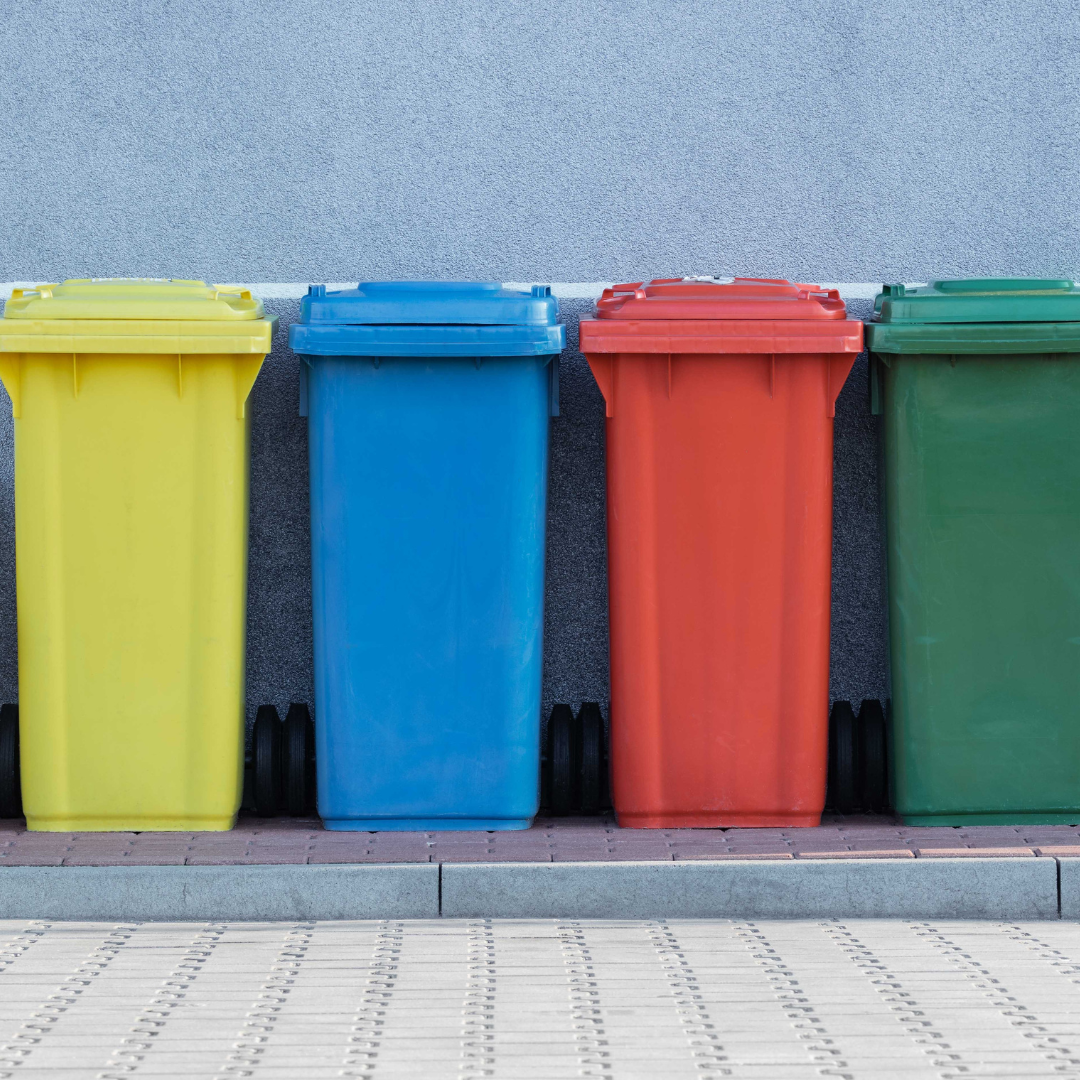
Here is what we shall learn:
- What is Manufacturing Waste?
- Types of Manufacturing Waste
- Why is Reducing Waste in Manufacturing Important?
- Reduce Waste and Boost Manufacturing Productivity
- 10 Remarkable Ways to Reduce Waste in Manufacturing
- Can Manufacturing Software Help in Reducing Manufacturing Waste?
- Conclusion
- How can Deskera Help You?
- Key Takeaways
- Related Articles
What is Manufacturing Waste?
Manufacturing waste is any material or by-product generated during the manufacturing process that is not part of the finished product. This can include materials that are damaged, unusable, or of poor quality.
It can also include materials that are used during the manufacturing process but are not part of the finished product, such as dust, fumes, and scraps. Manufacturing waste can also be generated from energy sources, such as electricity and fuel, as well as from water and other liquids used during the production process.
Why is Reducing Waste in Manufacturing Important?
Manufacturing waste is a major environmental concern, as it can pollute the air, water, and land if not properly managed. It can also be harmful to human health if it contains toxic or hazardous materials, such as heavy metals or solvents.
To minimize the environmental and health impacts of manufacturing waste, manufacturers should strive to reduce, reuse, and recycle the materials they generate.
Types of Manufacturing Waste
The manufacturing sector often comes across the following types of waste. It also seeks to reduce these wastes. There are lean wastes also but we shall learn more about them shortly.
The common types of manufacturing waste are enlisted here:
- Raw material waste: This occurs when raw materials are not used efficiently and end up being discarded. Examples include off-specification materials, over-purchased materials, and scrap metal.
- Production waste: This is waste created during the production process, such as defective parts, unusable products, and scrap metal.
- Packaging waste: This includes the packaging materials used to contain and protect products, such as cardboard boxes, plastic bags, and shrink wrap.
- Contamination waste: This occurs when pollutants or chemicals are released as a result of production processes. Examples include oil and chemical spills, and dust and smoke from burning materials.
- Hazardous waste: This occurs when hazardous materials are produced as a result of production processes. Examples include toxic chemicals, radioactive materials, and medical waste.
Waste Classification According to Lean Principles
The following are the different types of manufacturing waste classified by lean principles:
- Overproduction: This happens when companies produce more than is required in order to store it.
- Waiting: Idle machines and technicians may create bottlenecks.
- Processing: Adding unnecessary processing steps to your product's manufacturing
- Inventory: Keeping too many supplies on hand causes manufacturing overheads in storage and inventory management
- Inefficient workflows or Motion: These result in unnecessary movement of people, machinery, or equipment are referred to as motion.
- Correction: Making defective products or using a process that generates a large amount of scrap.
- Waste due to multiple trips: When parts and products are moved repeatedly, it may result in waste (of time.)
- Untapped potential: This is frequently regarded as another waste category in lean manufacturing. The most significant and hardest to eliminate waste is likely underutilizing the skills of your workforce.
Reduce Waste and Boost Manufacturing Productivity
The previous section discussed about the diverse types of waste generated in manufacturing sector. The type of waste may differ based on the type of industry and size of the business.
For example, waste from the two industries, food manufacturing and pharmaceutical manufacturing will differ considerably. These carry perishable wastes.
Similarly, plastic manufacturing and garment manufacturing will generate waste in form of scraps. So, the kind of waste you generate will depend on your business.
Identifying its type is your first step. Once you have classified your waste, you can move ahead with taking steps to reduce it.
How can Reducing Waste Boost Productivity?
Reducing manufacturing waste can boost productivity by cutting down on the amount of time and resources spent on disposing of or recycling waste. This can free up resources and personnel to be used more productively elsewhere in the manufacturing process.
When you have lesser waste, it helps to improve product quality, as less defects and waste materials can be produced. Moreover, you can save costs associated with waste disposal and help to improve the overall efficiency of the manufacturing process.
10 Remarkable Ways To Reduce Waste in Manufacturing
This section presents the ten remarkable ways of reducing waste irrespective of the sector. So let’s check them here:
1.Implement Lean Manufacturing Techniques
Lean manufacturing techniques are a set of principles and practices that aim to reduce waste in the manufacturing process. This includes reducing the number of resources used and minimizing any steps that don’t add value. It also includes eliminating activities that don’t generate a return on investment.
These techniques also include streamlining processes, standardizing workflows, automating where possible, and reducing inventory levels. Lean manufacturing techniques can help reduce waste, save time and money, and create a more efficient and effective manufacturing process.
Some of the key principles include the following:
- continuous improvement
- eliminating waste
- creating value for the customer
- creating a culture of respect and trust.
2. Optimize Production Processes
Optimizing production processes can be done by analyzing and streamlining production processes to reduce energy and material consumption, improve productivity and minimize waste. By reducing inefficiencies in production processes, manufacturers can save money and resources, and reduce the amount of waste they produce.
Optimizing production processes may involve incorporating lean manufacturing principles such as Just-in-Time manufacturing, Total Quality Management, and Six Sigma. Additionally, manufacturers may use automation, robotics, and other advanced technologies to improve production efficiency and reduce waste. Also, competent production planning can aid the process.
Ultimately, optimizing production processes can help manufacturers reduce their environmental impact by reducing their waste and energy consumption. Additionally, it can help them save money, increase productivity, and improve their overall product quality.
3. Establish a Culture of Continuous Improvement
Establishing a culture of continuous improvement can help reduce waste in manufacturing by setting a goal to continuously improve processes, products, and services. This involves having a focus on identifying areas for improvement and implementing changes to increase efficiency and reduce waste.
It can involve tracking production data, implementing lean manufacturing principles, and using problem-solving techniques to identify and make changes. Additionally, it involves instilling a culture of continuous improvement in the workforce.
This could be done by encouraging employees to identify areas of improvement and suggest changes. It can help to ensure that waste is reduced and processes are continuously optimized over time.
4. Utilize Automation and Robotics
Utilizing automation and robotics in manufacturing can help reduce waste by increasing production efficiency, improving product quality, and reducing labor costs. Automated systems can streamline processes and reduce the need for manual labor, allowing companies to produce more with fewer resources.
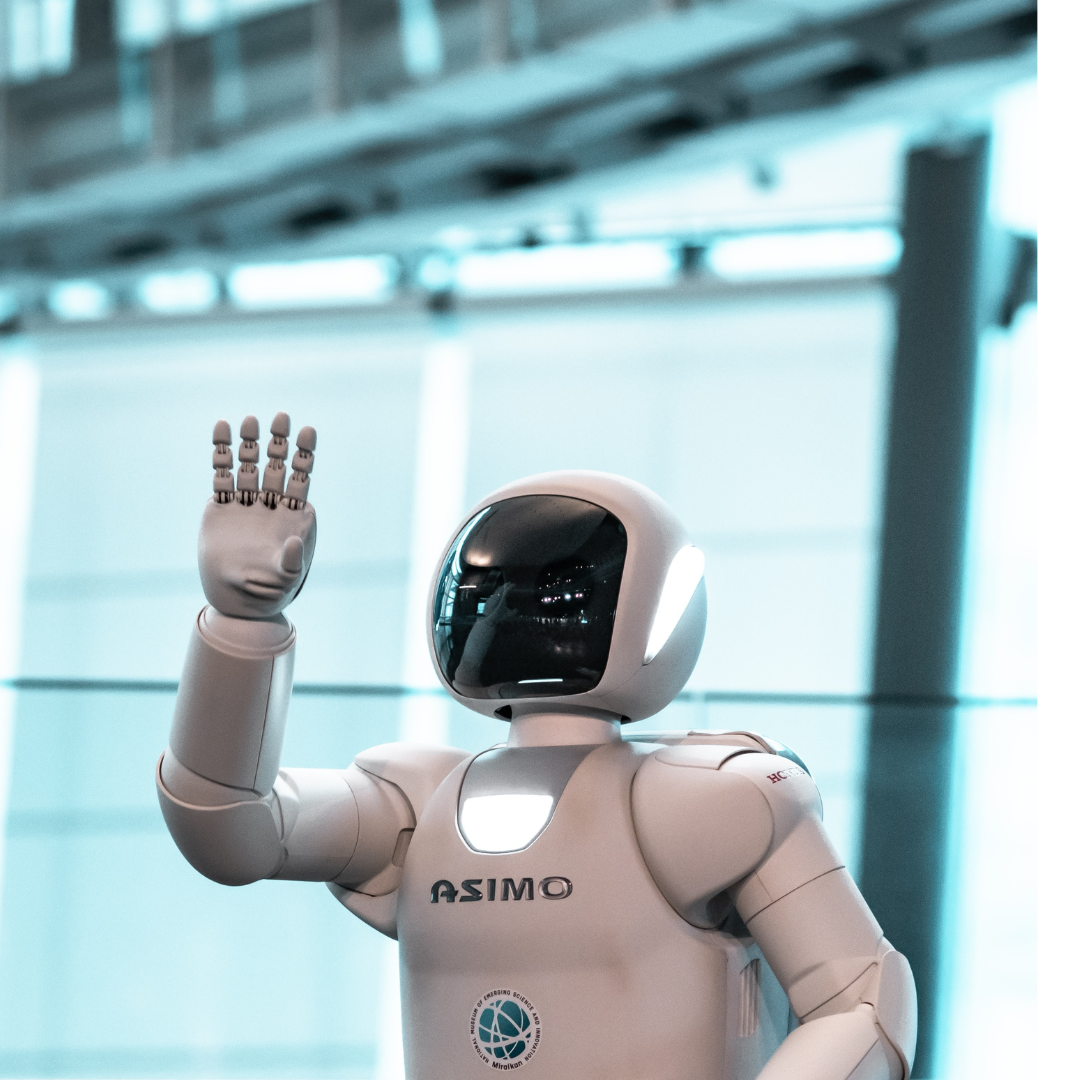
Automation and robots can also help detect and prevent defects in materials, reduce the need for rework, and reduce the amount of scrap material produced. Automation and robotics can also reduce energy consumption by eliminating manual tasks and reducing the amount of energy required to power the machines.
Overall, automation and robotics can help reduce waste in manufacturing by increasing efficiency, reducing labor costs, and improving product quality. By utilizing these technologies, companies can save money, reduce their environmental impact, and become more competitive in the market.
5. Invest in Sustainable Technologies
Investing in sustainable technologies can be accomplished by using materials, processes, and products that are designed to reduce the environmental impact of production. This includes using renewable, recyclable, and biodegradable materials in production, as well as utilizing energy-conserving and efficient technologies such as solar power and hybrid engines.
Investing in sustainable technologies also helps to reduce carbon emissions, water pollution, and other environmental damage caused by the production. Additionally, sustainable technology can help to streamline production and create more efficient processes that require less energy, materials, and water.
By using sustainable technologies, manufacturers can reduce their waste output and create a more sustainable and efficient production process that is better for the environment.
6. Effective Inventory Management
Efficient inventory management is all about ensuring enough materials and components are available to complete production while minimizing the amount of excess inventory that is stored. This method involves forecasting and tracking inventory levels, utilizing just-in-time inventory systems to minimize storage costs, and monitoring production levels to ensure that materials are used efficiently.
By keeping a close eye on inventory levels, manufacturers can reduce the number of resources that go unused, leading to a decrease in the amount of waste produced. Effective inventory management can also help to reduce production delays by ensuring that the right components are available when needed.
This can help to reduce the amount of energy and resources that are wasted by having to rework or scrap items due to a shortage or delay in receiving materials. Furthermore, this method can help to improve customer satisfaction by reducing the amount of time it takes to complete orders.
7. Waste Reduction Audits
A waste reduction audit is an assessment of the production processes and waste management procedures used in a manufacturing facility. It is designed to identify sources of waste and identify potential ways to reduce or eliminate it.
This type of audit typically involves a detailed analysis of the production process, with a focus on identifying and evaluating opportunities to reduce or eliminate waste. The audit may also consider other factors such as energy efficiency, labor productivity, cost savings, and environmental impact.
The goal of a waste reduction audit is to improve the efficiency and sustainability of production while reducing waste. These audits are usually conducted by an external consultant or a team of experts who evaluate the production process and waste management practices.
The consultant or team will review the production process, identify sources of waste and make recommendations on how to reduce or eliminate it.
After the audit, the team will provide a report of their findings, along with a list of recommendations on how to reduce waste. The audit may also include a cost-benefit analysis to help the company decide whether the recommended changes are cost-effective.
8. Reduce Lead Times
Reducing lead times is a lean manufacturing principle that involves reducing the amount of time it takes for a product to move through the manufacturing process. By reducing the amount of time it takes to produce a product, manufacturers are able to reduce the amount of waste that is generated in the process.
This is because there is less inventory sitting around waiting to be turned into a finished product and less time spent having to make adjustments to the manufacturing process due to changes in materials or customer orders.
Additionally, reducing lead times helps to reduce the costs associated with managing inventory, as well as the costs associated with delays in production. Overall, reducing lead times is a great way to reduce waste in manufacturing, as it makes the production process more efficient and ensures that products are produced in a timely manner.
9. Identify Major Waste Sources
Identifying major waste sources is a key step in reducing waste in manufacturing. This involves analyzing the manufacturing process to identify areas where materials are wasted, such as through inefficient processes, overproduction, or excess packaging.
Once these sources of waste are identified, manufacturers can take steps to reduce them, for example by streamlining processes. After recognizing this, they can also reduce the number of materials used, or implement better packaging solutions.
By reducing waste in these areas, manufacturers can reduce costs and create a more environmentally friendly production process.
10. Reduce Packaging
Reducing packaging can be a good tool to reduce waste in manufacturing by using fewer materials to package products. This could include using more lightweight materials, such as cardboard or paper, instead of heavier plastic or metal materials.
Additionally, manufacturers can reduce the size of the packages or use fewer pieces in the packaging to achieve a more efficient design. The goal of reducing packaging is to not only reduce waste but also to save on costs and improve the overall sustainability of the manufacturing process.
Reducing packaging also helps to increase efficiency in the packing process, as fewer materials need to be handled and less time is required to pack items. This also helps to reduce the amount of energy needed to move the materials, which can help to lower the carbon footprint associated with manufacturing.
Finally, reducing packaging can help to reduce the amount of landfill waste generated in the manufacturing process, as fewer materials will need to be disposed of in the end.
Can Manufacturing Software Help in Reducing Manufacturing Waste?
ERP (Enterprise Resource Planning) and MRP (Material Requirements Planning) software can guide you through the various processes of manufacturing and organizational planning. Both systems include a slew of modules and features critical to a company's overall performance.
The inventory management module of ERP helps in inventory management by automating and streamlining the inventory process. It tracks and monitors stock levels, provides real-time visibility into inventory levels, and generates purchase orders and invoices.
It also assists with forecasting and demand planning, allowing users to view and analyze data to make accurate decisions. Additionally, it can optimize warehouse management and distribution operations, allowing users to keep track of inventory and shipments in one place.
Here is how we can summarize the benefits of an ERP manufacturing system:
- ERP manufacturing software provides visibility into inventory levels across multiple warehouses and locations, helping managers to monitor and adjust inventory levels accordingly.
- ERP/MRP software can generate automated alerts to notify managers when inventory levels are low, ensuring that there is always an adequate supply of products on hand.
- ERP/MRP software provides accurate and up-to-date reporting on inventory levels, allowing managers to make informed decisions when it comes to ordering and stocking products.
- ERP/MRP software can also help track and monitor the movement of inventory from one location to another, providing an accurate view of where inventory is located at any given time.
- ERP/MRP software can also be used to track purchasing and production trends, helping managers to plan for future needs and adjust inventory levels accordingly.
Conclusion
The manufacturing industry is a significant contributor to global waste. By implementing the 10 remarkable ways to reduce waste in manufacturing, companies can make their operations more efficient and cost-effective while preserving the environment.
By reducing the number of materials and energy used, investing in technology and automation, and utilizing green manufacturing practices, manufacturers can reduce their environmental footprint and save money in the long run. These strategies will benefit both the environment and the bottom line, making them a win-win for businesses and the planet.
How can Deskera Help You?
Briefly stated, Deskera ERP provides you with everything required to optimize your procedures and achieve improved inventory control.
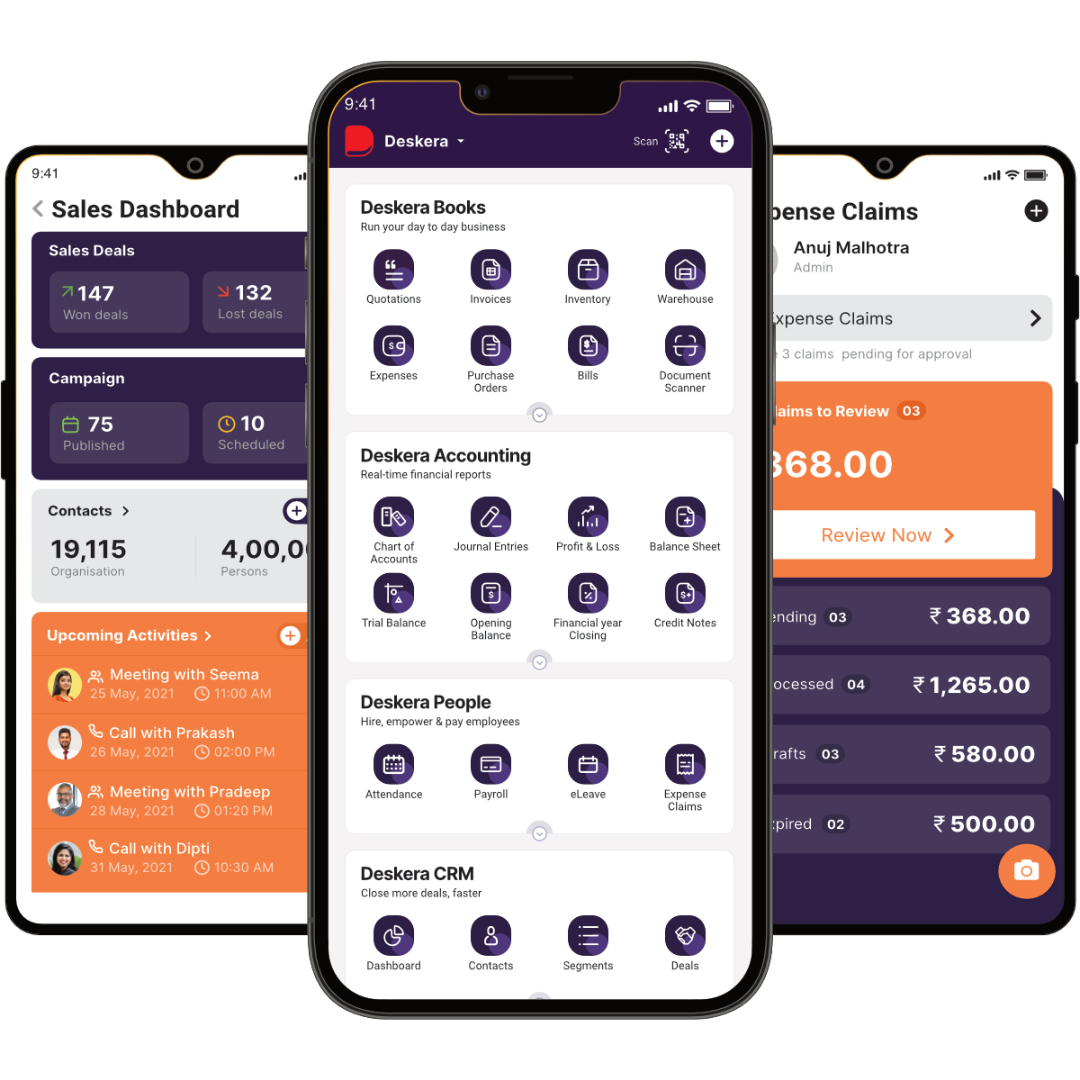
Deskera Books is a tool that allows you to maintain good accounting practices. Accounting software automates your accounting tasks such as billing, invoicing, expenses, and payments.
Deskera CRM is a platform that enables you to increase sales and close deals faster. It enables critical functions such as lead generation via email, lead-generation landing pages, and excellent customer service.
Deskera People is an easy-to-use payroll automation tool. The tool processes payroll faster, from hiring, onboarding, and managing employee benefits and bonuses to leave and attendance management.
Key Takeaways
- Manufacturing waste is any material or by-product generated during the manufacturing process that is not part of the finished product.
- Manufacturing waste can also be generated from energy sources, such as electricity and fuel, as well as from water and other liquids used during the production process.
- Raw material waste, production waste, packaging waste, and hazardous waste are some of the types of manufacturing waste.
- Overproduction, too many processing steps, and inefficient workflows are some of the waste categorized by lean principles.
- Implementing lean manufacturing techniques reduces the number of resources used and minimizes any steps that don’t add value. It also includes eliminating activities that don’t generate a return on investment.
- Optimizing production processes can be done by analyzing and streamlining production processes to reduce energy and material consumption, improve productivity and minimize waste.
- Establishing a culture of continuous improvement can help reduce waste in manufacturing by setting a goal to continuously improve processes, products, and services.
- Automated systems can streamline processes and reduce the need for manual labor, allowing companies to produce more with fewer resources.
- Investing in sustainable technologies can be accomplished by using materials, processes, and products that are designed to reduce the environmental impact of production.
- Efficient inventory management is all about ensuring enough materials and components are available to complete production while minimizing the amount of excess inventory that is stored.
- A waste reduction audit and reducing lead times are some other methods to reduce waste in the manufacturing process.
Related Articles
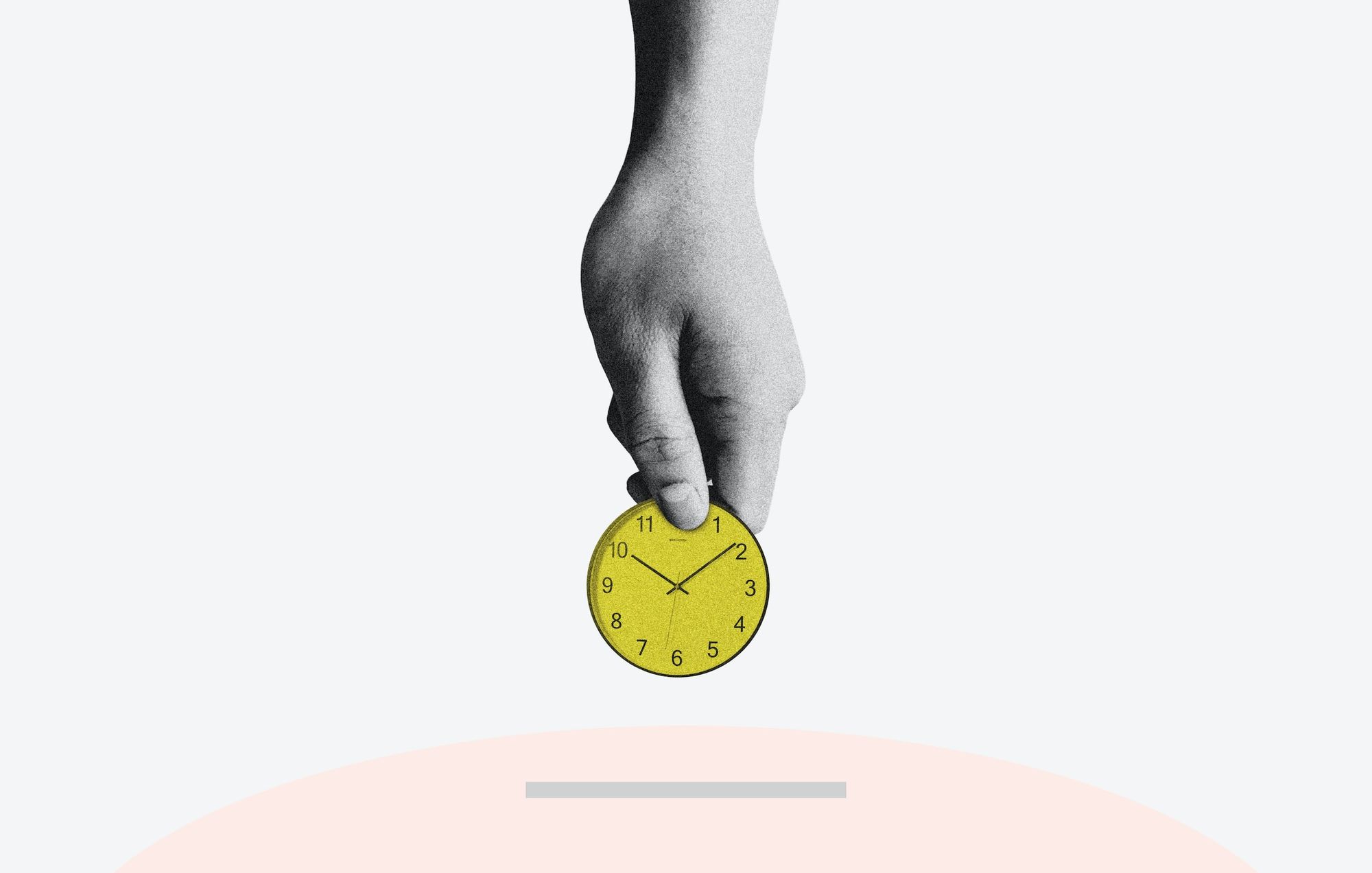

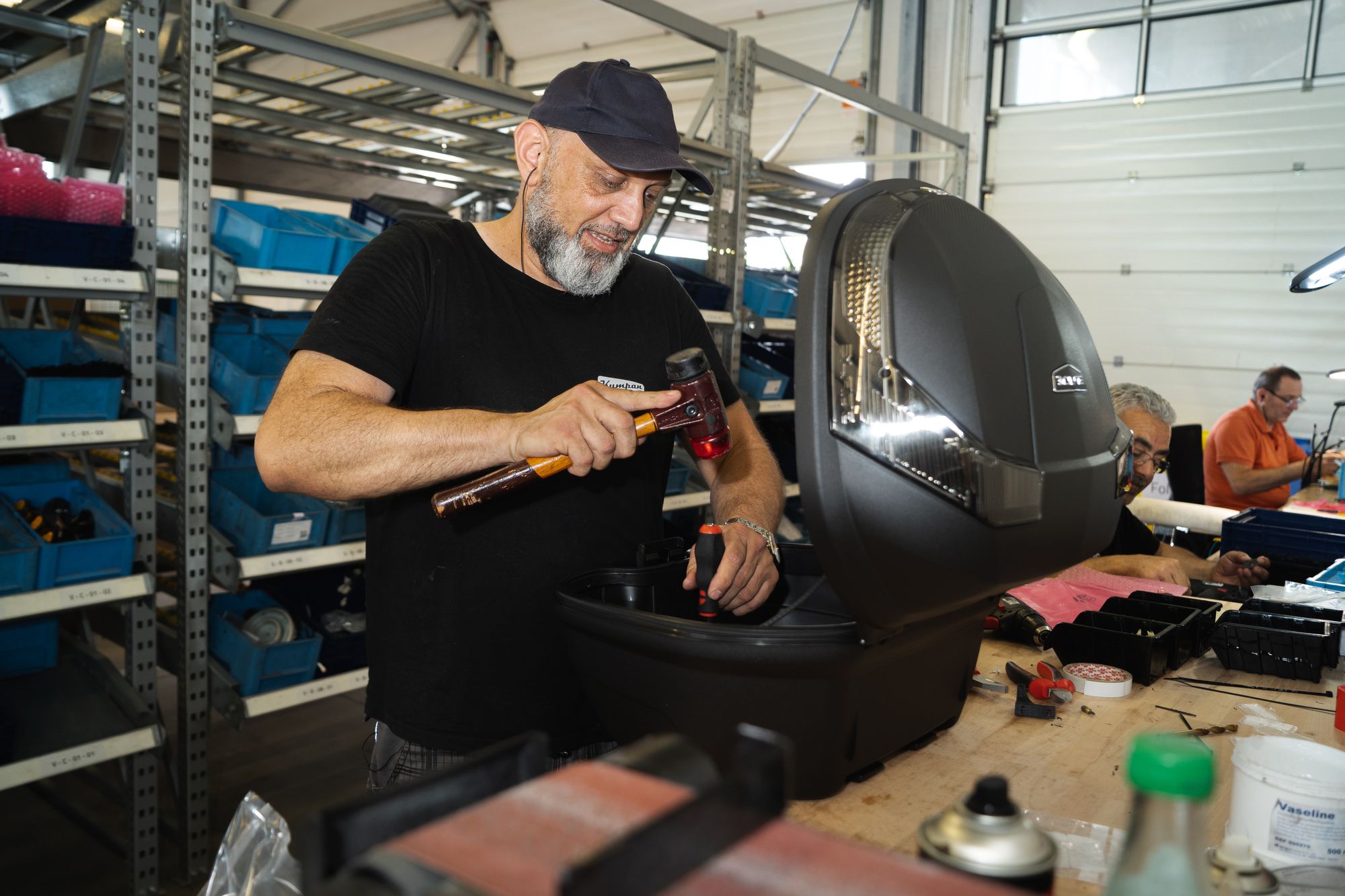
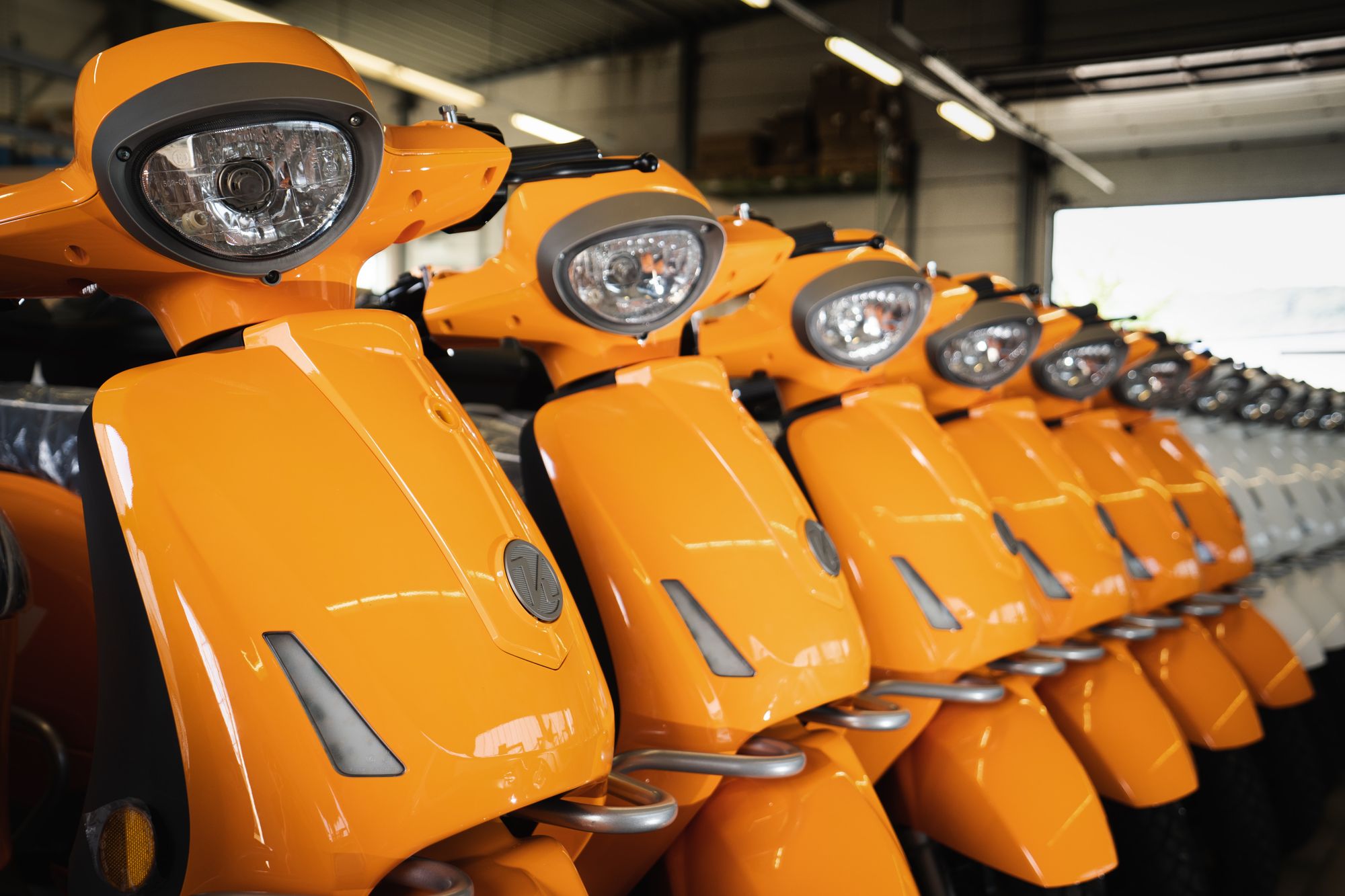