Enterprise Resource Planning (ERP) systems have become the backbone of modern manufacturing, offering the tools necessary to streamline operations, improve efficiency, and drive long-term growth.
In today’s competitive industrial landscape, manufacturers face growing pressure to deliver faster, operate leaner, and make data-driven decisions. This is where a robust ERP implementation can make a game-changing difference by connecting core business functions—from inventory and production to finance and compliance—within a single, unified platform.
Manufacturing is a key driver of ERP adoption, with 47% of ERP users belonging to the manufacturing industry. This statistic alone reflects how vital ERP systems have become in transforming manufacturing operations.
By enabling real-time visibility, improving supply chain coordination, and reducing operational silos, ERP software allows manufacturers to meet evolving customer demands while maintaining profitability and compliance. However, the journey from selection to implementation requires a strategic approach, careful planning, and alignment across teams.
One of the biggest challenges manufacturers face is navigating the complexity of ERP implementation itself—choosing the right system, preparing internal processes, migrating data, and ensuring team adoption. Mistakes during this process can result in costly delays, budget overruns, or even system failures. That’s why understanding each phase of ERP implementation, along with best practices tailored to the manufacturing sector, is essential for long-term success.
When it comes to manufacturing ERP solutions, Deskera Manufacturing ERP stands out as a powerful and user-friendly platform designed for modern manufacturers. With built-in modules for inventory management, production planning, procurement, accounting, and reporting, Deskera offers end-to-end automation and real-time analytics.
Its mobile accessibility and AI-powered assistant, David, make it an ideal choice for businesses seeking flexibility and scalability. As we explore ERP implementation in detail, tools like Deskera illustrate how the right solution can elevate your manufacturing operations to the next level.
What is Manufacturing ERP?
Manufacturing ERP (Enterprise Resource Planning) is a specialized software system designed to integrate and manage all core business processes within a manufacturing organization. It connects functions such as production planning, inventory management, order processing, procurement, and financials into a single centralized platform. By eliminating data silos and manual workarounds like spreadsheets, ERP helps manufacturers access real-time information, improve coordination across departments, and respond more quickly to operational changes.
Modern manufacturing ERP systems go beyond basic integration. They often include advanced features like AI-powered demand forecasting, real-time analytics, and automated compliance tracking. Some even connect with IoT (Internet of Things) devices to monitor equipment performance in real time, helping manufacturers prevent downtime and optimize efficiency across the shop floor.
Cloud-based ERP solutions provide additional advantages by offering scalability, remote access, and reduced IT overhead. As companies grow, they can seamlessly add users, expand into new locations, and adopt new capabilities—all while maintaining full visibility and control over their operations.
In short, a manufacturing ERP system transforms how manufacturers operate—enabling them to move from reactive management to proactive, data-driven decision-making.
When Should You Move to a Manufacturing ERP System?
Timing is everything when it comes to implementing a manufacturing ERP system. While every organization is unique, there are clear signs that indicate your business has outgrown spreadsheets, disconnected tools, or legacy systems—and is ready for a more integrated, scalable solution.
1. Your Operations Are Becoming Too Complex to Manage Manually
If you're relying heavily on spreadsheets, paper-based tracking, or standalone software, and it’s becoming difficult to manage production schedules, inventory, or procurement efficiently, it’s time to consider ERP. As your business grows, so does the complexity—and manual methods simply can’t keep up.
2. You Lack Real-Time Visibility into Key Metrics
Not knowing what’s happening on your shop floor, in your warehouse, or in your financials until it’s too late can lead to missed opportunities or costly delays. ERP systems offer real-time dashboards and alerts that keep you informed and in control.
3. Data Is Scattered Across Different Systems
If different departments use separate tools that don’t communicate with each other, it's likely leading to data silos, duplication, and errors. An ERP centralizes information, making collaboration and data accuracy much easier.
4. You’re Experiencing Frequent Stockouts or Overstocking
Inefficient inventory management—like running out of critical parts or overstocking items that tie up capital—is a strong indicator that your current system isn’t working. ERP helps you forecast demand and manage inventory levels more precisely.
5. Order Errors and Delays Are Rising
Increased errors in customer orders, shipping, or invoicing often stem from outdated or disconnected systems. An ERP automates these processes, ensuring accuracy and improving customer satisfaction.
6. You Plan to Scale or Expand
Whether you're opening a new plant, expanding your product line, or entering new markets, ERP software ensures that your operations can scale smoothly. Cloud-based systems especially offer flexibility and scalability without requiring massive IT investments.
If any of these scenarios sound familiar, it’s likely time to invest in a manufacturing ERP system. The sooner you adopt the right technology, the better equipped you'll be to stay competitive, efficient, and resilient in a rapidly evolving manufacturing landscape.
Benefits of Manufacturing ERP
Beyond simply organizing operations, a manufacturing ERP system empowers businesses to become smarter, leaner, and more profitable. By centralizing critical data and automating routine processes, ERP helps manufacturers reduce waste, avoid costly errors, and keep production lines running efficiently.
Below are some of the most impactful benefits manufacturers can expect from a well-implemented ERP system:
1. Improved Stock Optimization
Striking the right balance in inventory is essential. ERP systems use real-time data and demand forecasting to maintain optimal stock levels—avoiding both overstocking, which ties up capital, and understocking, which can halt production. This ensures materials and products are available exactly when needed.
2. Fewer Errors
Manual data entry across orders, invoices, or production schedules increases the risk of mistakes that can lead to delays or customer dissatisfaction. ERP systems minimize these errors by automating data capture, standardizing processes, and syncing information across departments.
3. Reduced Carrying Costs
Holding excess inventory can eat into profits due to warehousing costs, depreciation, and obsolescence. With ERP, manufacturers can automate replenishment, align purchases with real-time demand, and implement just-in-time inventory practices—significantly reducing carrying costs.
4. Increased Visibility
ERP systems provide a centralized dashboard that brings together live data from production, inventory, finance, and procurement. This real-time visibility enables better decision-making, faster issue resolution, and a clear understanding of overall business performance.
5. Optimized Resource Utilization
Idle machines, bottlenecks, and inefficient labor distribution can drag down productivity. ERP software helps schedule jobs, allocate resources, and plan capacity to ensure that every machine and employee is operating at maximum efficiency.
6. Improved Efficiency
By streamlining workflows and reducing manual interventions, ERP increases operational efficiency across the board. Teams spend less time searching for data and more time acting on insights.
7. Enhanced Collaboration
With shared data and integrated workflows, departments such as production, procurement, sales, and finance can collaborate more effectively. This leads to quicker approvals, fewer misunderstandings, and smoother handoffs.
8. Better Production Planning
ERP systems support advanced production planning, helping manufacturers align resources, manage material requirements, and adjust schedules proactively in response to shifts in demand or supply constraints.
9. Reduced Operational Costs
From minimizing rework and delays to reducing excess inventory and administrative overhead, ERP systems drive down costs through smarter planning and automation.
10. Increased Agility and Better Analytics
ERP platforms offer powerful analytics and reporting features that help manufacturers quickly adapt to market changes. With real-time insights and historical data trends, companies can continuously optimize performance and stay competitive.
How to Implement Manufacturing ERP: A Step-by-Step Guide for Success
Implementing an ERP system in a manufacturing environment is a strategic initiative that requires careful planning, collaboration, and execution. Whether you're upgrading from a legacy system or starting from scratch, this step-by-step guide will help ensure your ERP implementation is successful—minimizing risks, maximizing ROI, and aligning your technology with your operational goals.
1. Assemble the Right Implementation Team
A successful ERP project begins with building the right team. This includes stakeholders from across departments—IT, finance, operations, production, procurement, and supply chain.
Assign a project manager with both technical understanding and leadership skills to oversee planning and execution. Involve power users and end users early to gain insights into operational needs and user expectations.
These internal champions will help drive adoption, provide peer-level support, and advocate for the system post-launch. Clear roles, responsibilities, and communication protocols should be established from the start to avoid misalignment.
2. Define Clear Goals and Requirements
Before selecting any system, define what success looks like. Are you aiming to improve production planning, reduce inventory waste, streamline compliance, or all of the above? Outline business goals and map them to specific ERP functionalities.
Document both functional (e.g., real-time inventory tracking) and non-functional (e.g., scalability, cloud access) requirements. Be sure to engage key users and department heads during this phase to ensure their needs are captured.
Well-defined objectives provide direction for vendor selection and implementation strategy while making it easier to measure ROI later.
3. Evaluate and Select ERP Vendors
With your requirements in hand, begin evaluating ERP vendors. Look for providers with proven experience in manufacturing and similar-sized businesses. Request case studies, conduct demos, and assess core features such as MRP, demand forecasting, warehouse management, and integration options.
Consider customization capabilities, user interface simplicity, vendor support, and implementation track record. Involve both technical and non-technical users in scoring vendors. It’s also crucial to verify post-sales support, upgrade policies, and the vendor’s financial health. Choose a partner, not just a software provider, for long-term success.
4. Calculate Total Cost of Ownership (TCO)
Many ERP implementations fail due to underestimating the full cost. TCO goes beyond licensing or subscription fees—it includes implementation costs, consulting fees, training, data migration, integration, hardware (for on-premise), ongoing support, and system upgrades.
Consider potential downtime during deployment, the cost of change management efforts, and future scaling needs. Create a detailed budget that spans at least 3–5 years. A TCO analysis not only helps in vendor negotiations but also supports internal stakeholder buy-in by showcasing the value of long-term investment over short-term savings.
5. Map Your Business Processes
To configure the ERP effectively, you need a clear understanding of current business workflows. Document processes across procurement, manufacturing, quality control, logistics, and sales. Identify inefficiencies, redundant tasks, and manual workarounds.
This process mapping helps you decide where automation will deliver the highest value. Visual process maps or flowcharts can also assist consultants during implementation.
Additionally, identify compliance requirements and industry-specific regulations that the system must support. A thorough understanding of operations is key to aligning ERP features with real-world use cases and avoiding future misfits.
6. Plan Module Rollouts and Customizations
Instead of attempting to deploy all features at once, phase your implementation to reduce risk. Prioritize core modules like inventory, production, and finance, then expand into advanced areas like CRM or analytics.
Avoid excessive customizations in early stages unless absolutely necessary, as they can complicate maintenance and upgrades. When customization is essential, document the rationale, ensure it aligns with strategic goals, and keep it scalable.
Build a roadmap for phased rollouts with timelines and milestones, ensuring each phase includes sufficient time for testing, training, and user adoption.
7. Ensure Seamless Integration with Third-Party Tools
Modern manufacturers rely on a mix of systems—CRM, PLM, ecommerce platforms, IoT sensors, and legacy databases. ERP should act as a central nervous system, not a silo.
Verify that your ERP supports APIs, webhooks, or pre-built connectors for seamless integration. Integration ensures real-time data flow, eliminates double entry, and supports accurate reporting.
Plan for how and when each integration will be implemented. If needed, bring in third-party integration experts. Poorly integrated systems can result in data fragmentation and reduce the ERP’s overall utility and trustworthiness.
8. Clean and Migrate Your Data
Your ERP system is only as good as the data it runs on. Before migration, perform a data audit to clean up duplicate records, outdated entries, and inconsistent formats. Standardize naming conventions, validate part numbers, and remove redundant SKUs.
Use data migration templates and test import processes in a sandbox environment. Migrate only essential historical data—too much data can slow down performance. Work closely with your ERP partner to map old data structures to the new system and establish validation rules to catch errors during the process.
9. Test the Implementation Thoroughly
Testing is essential to catch issues before they reach production. Build a detailed test plan that covers all modules, workflows, and integrations. Include real-world scenarios—such as order fulfillment, returns, and production changes—to ensure the system performs under normal operating conditions.
Involve end users to validate that processes work as expected from their perspective. Pay attention to data accuracy, system response times, and report outputs. Conduct user acceptance testing (UAT) and document any bugs or gaps. Address these promptly before moving forward with a live deployment.
10. Resolve Issues Promptly
During and after testing, issues will arise—missing fields, incorrect data flows, or workflow mismatches. Create a structured issue resolution process with severity levels, assigned owners, and clear SLAs. Use a centralized tracking system to log, prioritize, and resolve bugs efficiently.
Maintain open lines of communication between users, IT, and the vendor. Encourage feedback from all users—not just managers—since frontline staff often catch issues others miss. Timely resolution of issues builds user trust and ensures system stability, reducing the likelihood of delays or costly rework post-launch.
11. Deliver Role-Based Training and Documentation
ERP training shouldn’t be one-size-fits-all. Develop training programs tailored to each user group—planners, shop floor operators, warehouse staff, accountants, and managers.
Use hands-on sessions, simulations, and guided workflows rather than long theoretical sessions. Supplement training with quick reference guides and video tutorials.
Provide refresher sessions post-launch and include training as part of your onboarding program for new hires. Documentation should be comprehensive, easy to update, and accessible. Well-trained users make fewer errors, adapt faster, and are more likely to embrace the system’s full capabilities.
12. Execute a Controlled Go-Live
Avoid the "big bang" approach unless you’ve thoroughly tested and prepared. Instead, consider a soft launch with a subset of users or locations. Monitor key metrics like order accuracy, system speed, and stock discrepancies in real time. Keep IT support and vendor teams on standby to respond to issues instantly.
Have a rollback plan in case of critical errors. Ensure everyone knows whom to contact for support. A controlled go-live minimizes risk, ensures smoother operations, and builds confidence in the system’s capabilities from day one.
13. Establish a Continuous Improvement Plan
ERP implementation doesn’t end at go-live. Set up KPIs to track system performance, user satisfaction, and operational efficiency over time. Schedule periodic reviews to assess whether the system is meeting business goals.
Encourage ongoing feedback, especially from end users, and create a backlog of enhancement requests. Stay updated with vendor upgrades and new features, and assess whether these can add value.
As your business evolves, your ERP should evolve too. A continuous improvement mindset helps you derive long-term value and stay competitive in a changing landscape.
Overcoming Common ERP Implementation Challenges in Manufacturing
Even the most strategically planned ERP rollouts in manufacturing can encounter roadblocks—ranging from cost overruns to user resistance and integration failures. These challenges can derail timelines, inflate budgets, and reduce overall ROI if not handled proactively.
Understanding what can go wrong—and how to respond effectively—helps manufacturers minimize risk and build resilience throughout the implementation process. Below are some of the most frequent challenges and actionable strategies to overcome them.
1. Escalating Costs
Challenge: ERP implementation often becomes more expensive than expected. Licensing fees are just one part of the equation—expenses can quickly multiply due to data migration, extended user training, customizations, and hiring consultants.
How to Overcome It: Break down the Total Cost of Ownership (TCO) into four parts: upfront costs (software, hardware), ongoing costs (maintenance, subscriptions), scalability costs (upgrades, user additions), and indirect costs (productivity loss during transition).
A realistic budget should account for all of these. Choosing out-of-the-box features over heavy customization, negotiating vendor terms, and phasing your implementation can significantly reduce financial strain.
Cloud ERP solutions may offer more predictable costs over time, though they require monthly or yearly subscriptions.
2. Deployment Delays
Challenge: Timelines often slip due to poor planning, lack of resource alignment, or unforeseen technical hurdles. These delays disrupt operations and demotivate stakeholders.
How to Overcome It: Develop a detailed implementation roadmap with defined milestones, responsibilities, and contingency plans. Assign a dedicated project manager to keep stakeholders aligned, track progress, and mitigate bottlenecks.
Regular check-ins, early-stage testing, and vendor collaboration can uncover and address issues before they escalate. If delays do occur, re-evaluate timelines and task priorities to regain momentum.
3. Resistance to Change
Challenge: Employees may be hesitant—or outright resistant—to adopting a new ERP system, particularly if they feel the change is imposed without their input or increases their workload.
How to Overcome It: Engage employees from the start. Involve them in needs assessments, system demos, and pilot testing. Communicate how the ERP system benefits them directly—such as reducing redundant tasks or improving data visibility.
Train users by role and learning style, provide continuous support channels (help desks, super users), and appoint internal champions to promote positive adoption. A formal change management strategy is key to driving acceptance.
4. Integration Issues with Legacy Systems
Challenge: Manufacturers often operate with legacy software that doesn’t integrate smoothly with modern ERP platforms, resulting in fragmented data and inefficient workarounds.
How to Overcome It: Audit existing systems early to identify potential integration challenges. Select ERP software that offers robust APIs or native connectors to the tools you use most. If necessary, use middleware to bridge the gap between old and new systems.
Consider running legacy tools alongside the ERP during transition to ensure continuity, and plan for phased replacement or consolidation over time.
5. Security Vulnerabilities
Challenge: Centralizing sensitive data in a single ERP system increases the risk of cybersecurity breaches, whether through external threats or internal misuse.
How to Overcome It: Implement layered security practices. For cloud-based ERPs, ensure the vendor offers enterprise-grade protection, such as encryption, intrusion detection, and frequent security updates.
Internally, enforce multi-factor authentication (MFA), set up role-based access controls, and conduct regular audits to detect vulnerabilities.
Training employees on phishing prevention and basic cybersecurity hygiene is also essential. For on-premises systems, IT teams must handle all security infrastructure and updates diligently.
Best Practices for a Successful Manufacturing ERP Implementation
Implementing an ERP system in a manufacturing environment is a high-stakes initiative that affects every part of the business—from production and inventory to finance and customer service.
Success depends not just on the technology itself, but also on how well the implementation is planned, executed, and embraced by the people using it.
Below are best practices that can help manufacturers navigate ERP implementation with greater confidence and efficiency.
1. Define Clear Objectives and KPIs
Why it matters: Without a clear understanding of what you want the ERP system to achieve, it’s difficult to measure success or keep the project aligned with business goals.
Best Practice: Start by identifying the core challenges you want the ERP to solve—such as improving production scheduling, reducing inventory waste, or enhancing visibility across departments. Set measurable KPIs aligned with these goals.
Examples include order fulfillment rate, inventory turnover ratio, or time to close financial periods. These KPIs should guide your decision-making throughout implementation and serve as benchmarks for success post-launch.
2. Involve Key Stakeholders Early
Why it matters: ERP implementation is not just an IT project—it affects every department. Lack of cross-functional input can lead to unmet needs and resistance.
Best Practice: Form a cross-functional project team that includes leaders from operations, finance, procurement, HR, and IT. These representatives should contribute to system selection, requirements gathering, and user acceptance testing. Involving stakeholders early ensures that the system supports actual business processes and increases the likelihood of organization-wide buy-in.
3. Choose the Right ERP Vendor and Deployment Model
Why it matters: An ERP system is only as good as how well it fits your specific industry needs, integrates with existing tools, and scales with your business.
Best Practice: Select a vendor with proven experience in the manufacturing sector. Evaluate both cloud and on-premises options based on your budget, internal IT capabilities, and desired scalability. Review case studies, request demos, and assess customer support options. Look for built-in features specific to manufacturing, such as bill of materials (BOM) management, shop floor control, and demand forecasting.
4. Prioritize Data Quality and Migration
Why it matters: Poor data leads to poor decisions—especially in ERP systems that rely heavily on accurate, real-time information.
Best Practice: Conduct a data audit before implementation to identify and clean up duplicates, outdated records, and inconsistencies. Define data ownership and validation protocols. Plan the migration in stages and test small batches before going live. In some cases, it may be better to migrate only essential data initially and bring in historical records later.
5. Develop a Phased Rollout Plan
Why it matters: Going live with an entire ERP system all at once can overwhelm users and increase the risk of system-wide disruptions.
Best Practice: Implement the ERP system in stages—starting with core modules like finance and inventory before expanding to production planning or CRM. Each phase should include detailed testing, user training, and feedback loops. A phased approach reduces risk, improves change management, and allows teams to gradually build confidence with the system.
6. Invest in Training and Change Management
Why it matters: Even the most feature-rich ERP system will fail without proper user adoption. Change can be disruptive, especially if users don’t understand the system’s value.
Best Practice: Create a structured training plan tailored to different roles, functions, and learning styles. Use hands-on sessions, video tutorials, and documentation to reinforce learning. Pair this with a formal change management strategy that includes frequent communication, leadership support, and internal champions who can drive enthusiasm and adoption across teams.
7. Monitor, Measure, and Optimize
Why it matters: Implementation isn’t the end—it’s the beginning of continuous improvement. Without ongoing monitoring, it’s hard to ensure you’re getting value from your ERP investment.
Best Practice: Establish regular review cycles to track KPIs, gather user feedback, and assess system performance. Use this data to identify areas for improvement—whether it’s process bottlenecks, underutilized features, or integration gaps. Most ERP vendors release regular updates and enhancements—staying current can unlock new capabilities and ensure long-term success.
How Deskera Manufacturing ERP Supports Seamless Implementation and Operational Excellence
Deskera Manufacturing ERP is designed to help small and mid-sized manufacturers gain full visibility and control over their production, inventory, and supply chain operations—all in one integrated platform. With built-in automation, mobile accessibility, and powerful MRP features, Deskera addresses many of the pain points that typically arise during ERP implementation and day-to-day manufacturing management.
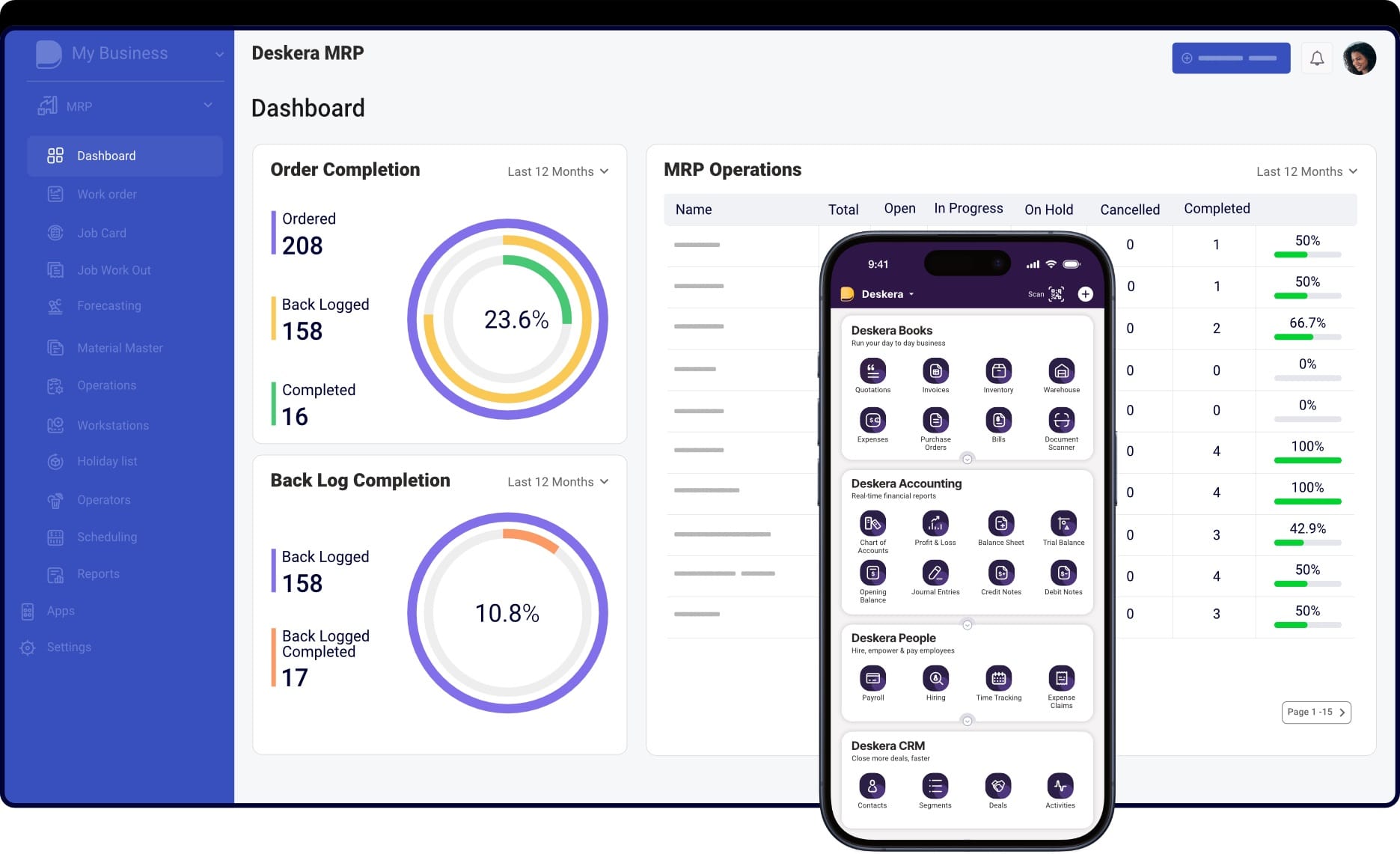
1. Accelerated Implementation with Out-of-the-Box Features
Deskera offers a user-friendly interface and ready-to-use modules tailored for manufacturers, including bill of materials (BOM), work orders, and production planning. This reduces the need for extensive customization, helping businesses go live faster while minimizing setup costs. For organizations with limited IT resources, Deskera’s cloud deployment ensures lower upfront investment and minimal infrastructure requirements.
2. Real-Time Visibility Across Operations
Deskera connects production, sales, inventory, procurement, and finance in a single dashboard. This centralized view eliminates silos and empowers teams to make data-driven decisions. Real-time inventory tracking ensures that raw materials and finished goods are accounted for accurately, which helps prevent stockouts, overproduction, and material wastage.
3. Integrated MRP for Smarter Production Planning
Manufacturers can benefit from Deskera’s Material Requirements Planning (MRP) engine, which automates the calculation of raw material needs based on demand forecasts and production schedules. This improves lead times, reduces manual errors, and enables more accurate procurement planning. As demand fluctuates, Deskera helps manufacturers adapt quickly without disrupting workflows.
4. Mobile Accessibility and AI Assistant (David)
With Deskera’s mobile app and AI assistant, David, users can monitor operations, approve workflows, and access reports on the go. David provides intelligent suggestions and insights, enabling faster decision-making and proactive management of production bottlenecks or inventory shortfalls—even when managers are away from the office.
5. Built-in Templates and Advanced Reporting
Deskera includes built-in templates for invoicing, purchase orders, and inventory reports, saving time and standardizing documentation. Its advanced reporting capabilities allow users to track KPIs like production efficiency, inventory turnover, and order fulfillment rates. These insights are critical for identifying improvement areas and ensuring the ERP implementation continues delivering ROI.
6. Scalable and Secure Cloud-Based Infrastructure
Whether you’re a growing manufacturer or an established player, Deskera scales with your business. Its cloud-based infrastructure ensures robust data security, regular backups, and automatic software updates—reducing the IT burden while keeping systems up to date and protected from cyber threats.
Key Takeaways
- Successful ERP implementation in manufacturing involves more than just software installation—it requires strategic planning, process alignment, and organizational buy-in to fully realize operational efficiency and scalability.
- Thorough preparation—including defining clear objectives, evaluating existing workflows, and securing executive sponsorship—is crucial to setting the stage for a smooth ERP rollout and reducing risks from the outset.
- Selecting an ERP that fits your industry, budget, and future growth needs—while offering scalability, strong integration, and relevant manufacturing features—is key to long-term success.
- A phased approach with structured steps—ranging from data migration and customization to training and post-launch support—ensures an organized and efficient ERP deployment.
- Challenges like cost overruns, resistance to change, integration issues, and deployment delays can derail ERP projects. Addressing these with proper planning, communication, and contingency strategies is essential for success.
- Involving stakeholders early, prioritizing training, maintaining transparent communication, and leveraging vendor expertise are best practices that drive adoption and minimize disruption.
- Deskera simplifies manufacturing ERP implementation through intuitive interfaces, built-in MRP features, real-time insights, mobile access, and scalable cloud-based infrastructure—making it ideal for small and mid-sized manufacturers.
Related Articles
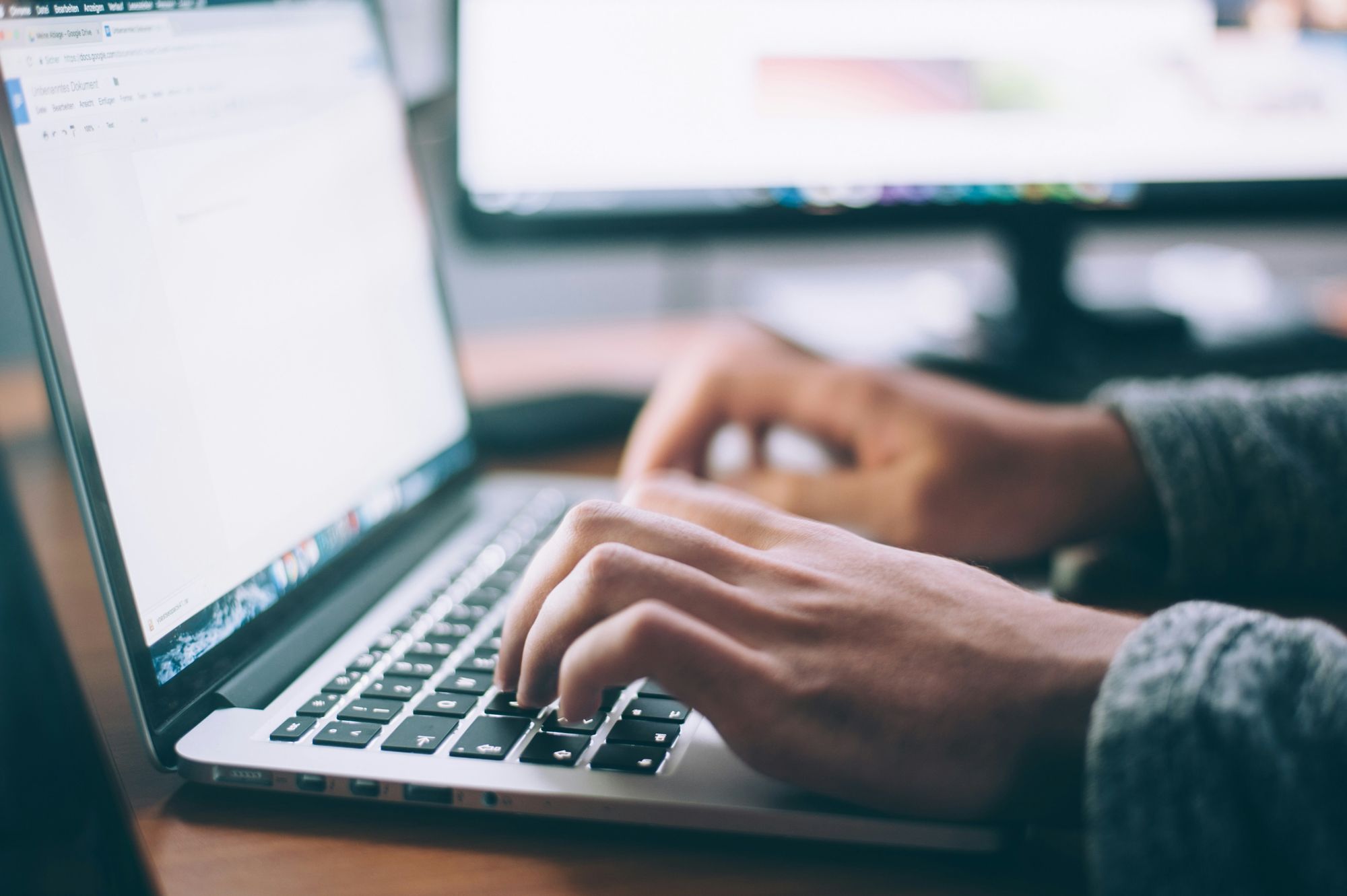
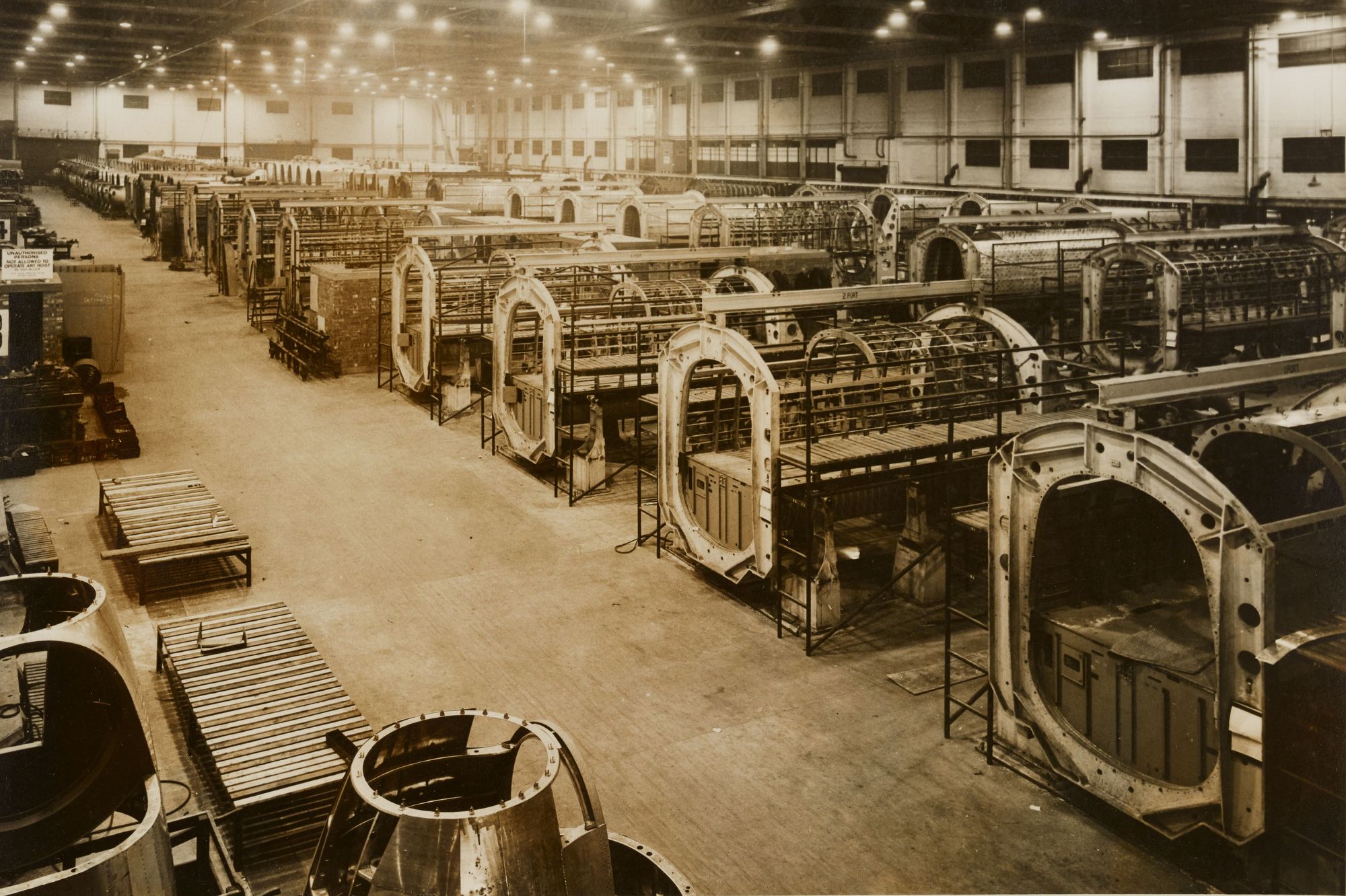
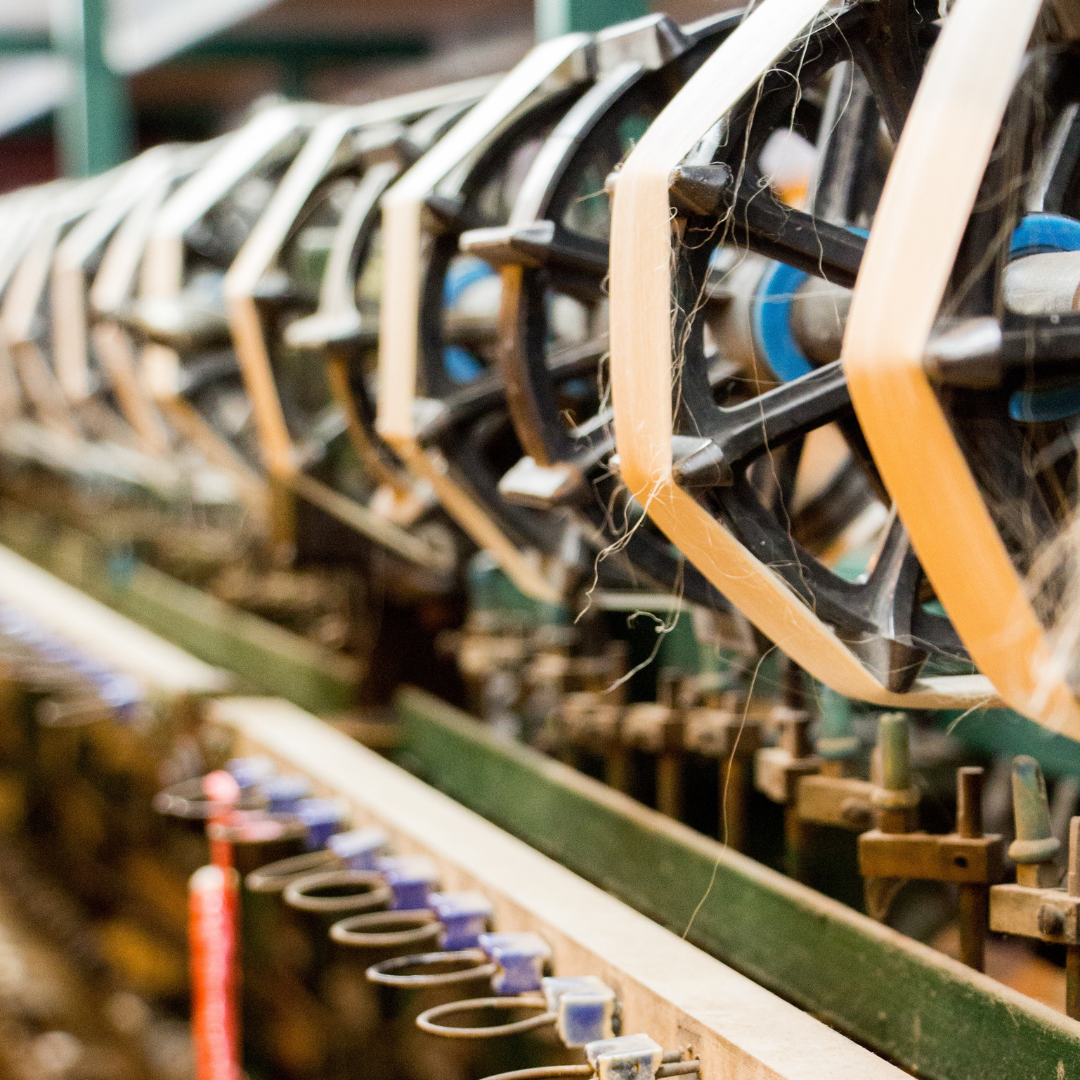
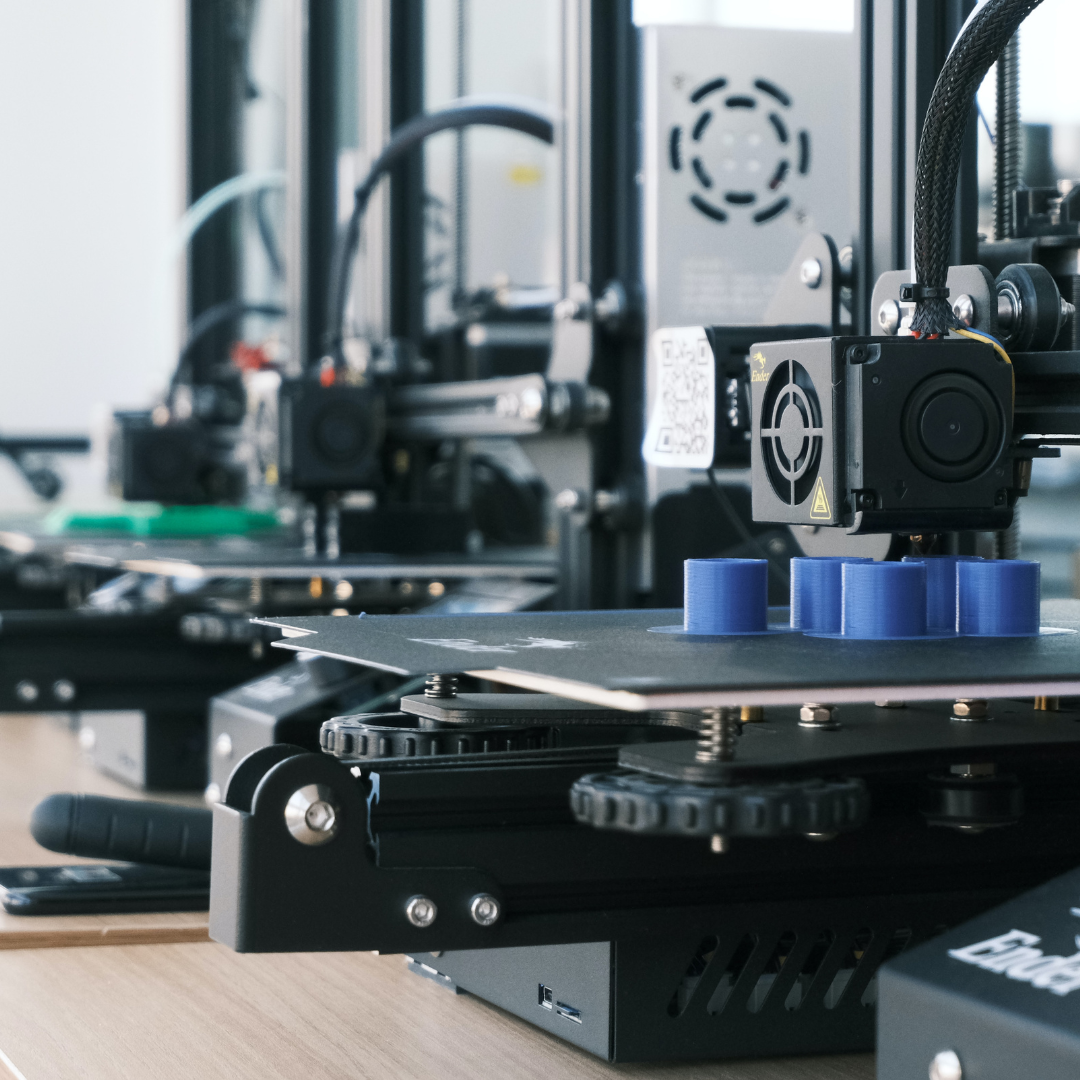
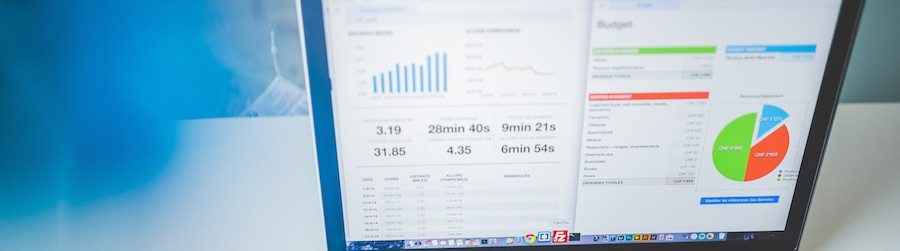
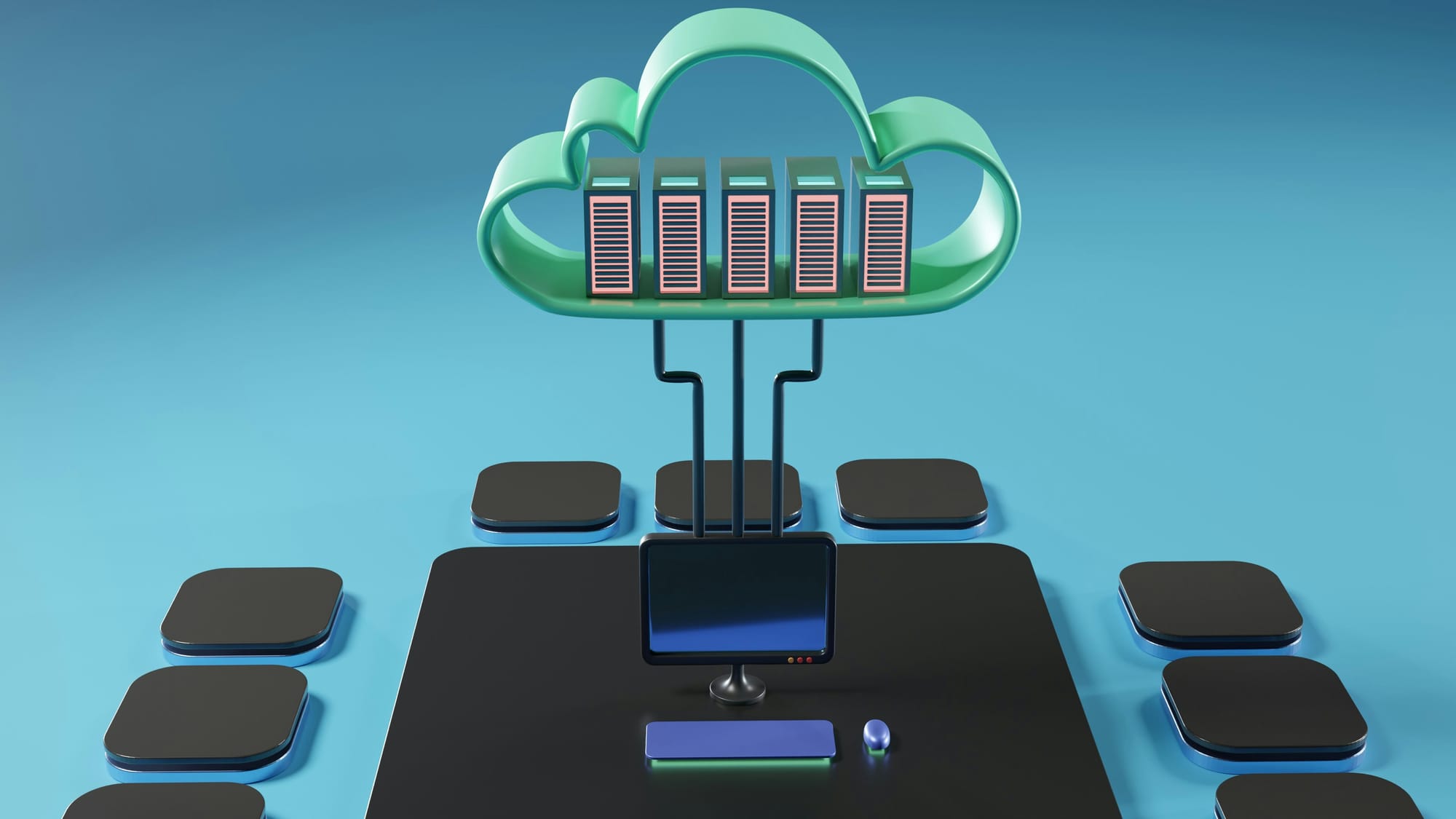