Are you fascinated by the endless possibilities that plastic can offer? Plastic has become an integral part of our daily lives, from toys to technology. But have you ever wondered what drives the plastic manufacturing industry forward? Well, hold on to your hats because we're about to take a wild ride into the exciting world of plastic manufacturing!
Plastic manufacturing is an essential industry that produces a vast range of products used in daily life. From packaging materials to construction components and medical equipment, plastic products play a significant role in various industries.
One of the main drivers of the plastic manufacturing industry is technological advancements. Innovations in materials science, manufacturing processes, and machinery have greatly improved the efficiency and productivity of the industry.
For example, the introduction of computer-aided design (CAD) and computer-aided manufacturing (CAM) has revolutionized the way plastic products are designed and produced, allowing for faster production times and greater precision.
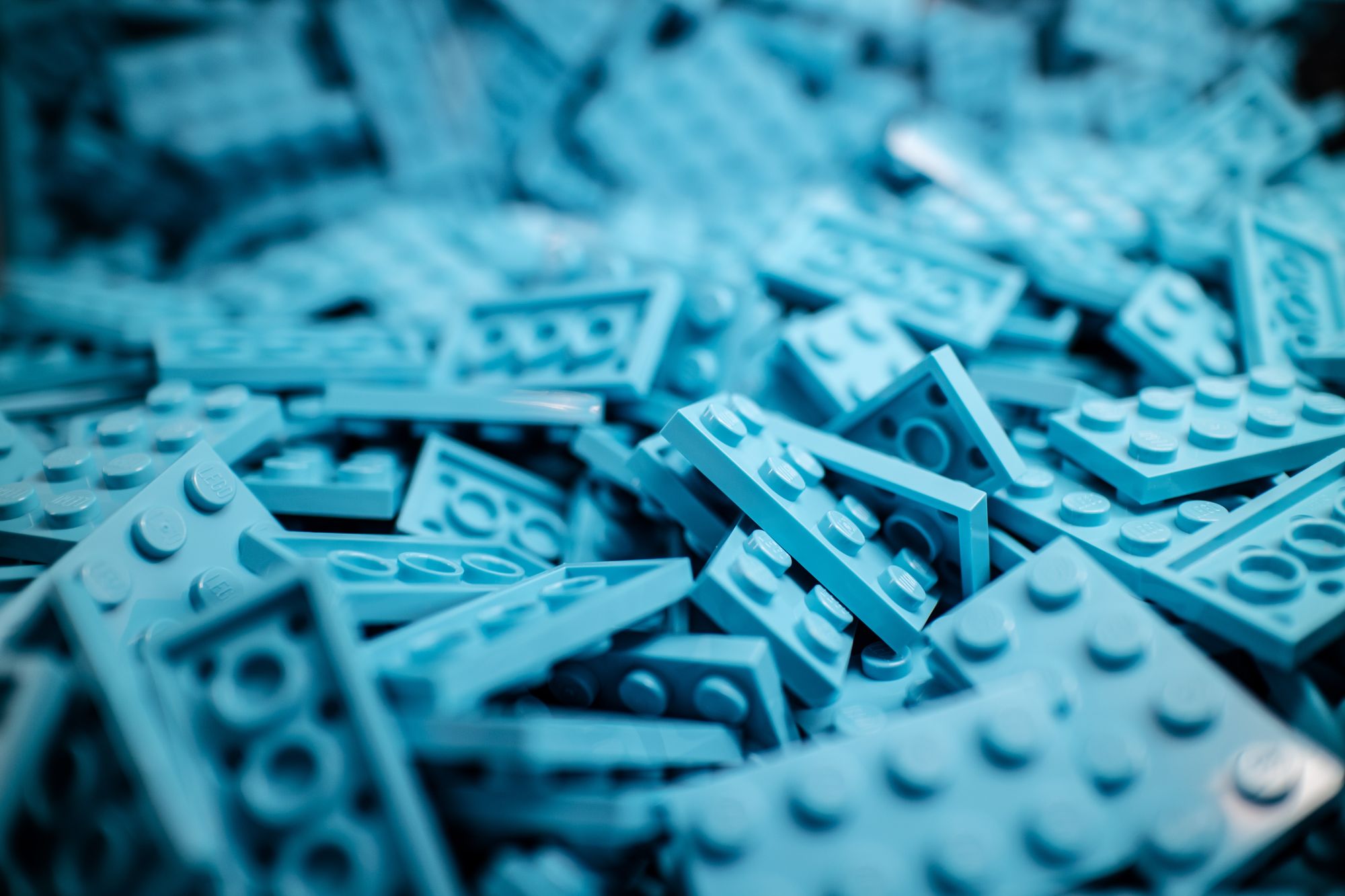
In this article, we will explore the key drivers of plastic manufacturing and discover how they have helped shape the industry into what it is today. So, get ready to dive into the world of polymer chemistry and learn about the latest innovations that are propelling the plastic industry forward!
Here's what we shall cover in this post:
- Raw Materials and Supply Chain Management in Plastic Manufacturing
- Labor and Workforce Management in Plastic Manufacturing
- Quality Control and Assurance in Plastic Manufacturing
- Emerging Technologies in Plastic Manufacturing
- Market Trends and Consumer Demand for Plastic Products
- Collaboration and Partnerships in Plastic Manufacturing
- The Impact of International Trade on Plastic Manufacturing
- Intellectual Property Protection in Plastic Manufacturing
- Strategies for Managing Risk in Plastic Manufacturing
- Conclusion
- Key Takeaways
Raw Materials and Supply Chain Management in Plastic Manufacturing
Plastic is one of the most widely used materials in the world, and its production requires the use of a variety of raw materials. The primary raw materials used in plastic production include petroleum, natural gas, coal, and biomass.
However, the production of plastic can have significant environmental impacts, such as the release of greenhouse gases, and can also have social implications, such as the displacement of communities due to the extraction of raw materials.
Therefore, it is essential to understand the role of raw materials and supply chain management in plastic manufacturing.
Sustainable sourcing of raw materials:
One way to address plastic production's environmental and social impacts is to ensure that raw materials are sourced sustainably. This means sourcing raw materials from suppliers who operate environmentally and socially responsibly. This includes suppliers who minimize their environmental impact, respect local communities' rights, and promote fair labor practices.
Tracking the environmental impact of raw materials:
Another critical consideration in raw materials and supply chain management is the environmental impact of raw materials. Tracking the environmental impact of raw materials throughout the supply chain can help identify areas for improvement and reduce the overall environmental impact of plastic production.
Reducing waste in the supply chain:
Reducing waste in the supply chain is another important consideration in raw materials and supply chain management. This can include measures such as reducing packaging, improving transportation efficiency, and minimizing energy consumption in production processes.
Building resilient supply chains:
Building resilient supply chains is also critical to the success of plastic manufacturing. This includes building relationships with reliable suppliers, diversifying suppliers, and having contingency plans to address supply chain disruptions.
Developing sustainable alternatives:
Finally, developing sustainable alternatives to traditional raw materials is another critical consideration in raw materials and supply chain management. This includes exploring the use of renewable resources, such as bioplastics and plant-based materials, as well as exploring new production processes that reduce the reliance on traditional raw materials.
Innovations in Plastic Manufacturing Equipment
Innovations in plastic manufacturing equipment have played a significant role in the growth and evolution of the plastics industry. These innovations have led to more efficient and cost-effective processes, increased productivity, and improved product quality.
Here are some of the latest innovations in plastic manufacturing equipment:
3D Printing: 3D printing technology has revolutionized the way plastic products are designed and manufactured. This technology uses a computer-controlled process to build plastic products layer by layer, allowing for highly complex shapes and geometries.
3D printing has the potential to reduce waste and energy consumption in the manufacturing process, as it allows for precise control of material usage.
Injection Molding: Injection molding is a widely used process for manufacturing plastic products. Recent innovations in this process have focused on improving energy efficiency, reducing material waste, and increasing production speed.
One such innovation is the use of electric injection molding machines, which use less energy than traditional hydraulic machines.
Blow Molding: Blow molding is a process used to create hollow plastic parts, such as bottles and containers. Recent innovations in this process have focused on reducing material waste and improving energy efficiency.
One such innovation is the use of lightweight materials, which reduces the amount of plastic needed to create each product.
Extrusion: Extrusion is a process used to create long, continuous plastic products, such as tubing and pipes. Recent innovations in this process have focused on improving the precision and consistency of the extruded product, as well as reducing energy consumption and material waste.
Automation: Automation is increasingly being used in plastic manufacturing to improve efficiency, reduce costs, and improve safety. Automated equipment can perform dangerous or difficult tasks for humans, such as handling hot materials or working in hazardous environments.
Robotics is being used to automate various tasks in plastic manufacturing, including injection molding, blow molding, and extrusion.
Smart Manufacturing: Smart manufacturing is the use of advanced technologies, such as artificial intelligence and the Internet of Things (IoT), to improve the efficiency and productivity of manufacturing processes.In plastic manufacturing, smart manufacturing can be used to monitor and optimize the entire production process, from raw material sourcing to product delivery.
Recycling Equipment: Recycling is an essential aspect of sustainable plastic manufacturing. Recent innovations in recycling equipment have focused on increasing the efficiency and effectiveness of plastic recycling.
This includes the development of new recycling technologies, such as chemical recycling, as well as the improvement of existing technologies, such as mechanical recycling.
Labor and Workforce Management in Plastic Manufacturing
Plastic manufacturing is a complex process that requires skilled and efficient labor. The success of a plastic manufacturing plant depends on the productivity and performance of its workforce. Labor and workforce management are critical factors that influence a plastic manufacturing plant's production output, quality, and profitability.
This section will discuss the importance of labor and workforce management in plastic manufacturing and the strategies to optimize workforce productivity and efficiency.
Importance of Labor and Workforce Management in Plastic Manufacturing:
- Labor is one of the most significant cost factors in plastic manufacturing, and effective workforce management can improve cost efficiency.
- Proper labor management ensures compliance with labor laws and regulations, reduces the risk of accidents, and promotes a safe working environment.
- An efficient workforce management system ensures optimal allocation of resources, reduces production downtime, and minimizes labor turnover rate.
- Proper training and development of employees can enhance their skills and knowledge, increase job satisfaction, and boost morale and motivation.
- Labor and workforce management can affect the company's reputation and branding and the relationship with customers, suppliers, and stakeholders.
Strategies for Optimizing Workforce Productivity and Efficiency in Plastic Manufacturing:
- Conducting a job analysis to identify the required skills and competencies for each job role and define the job description and duties.
- Implementing a performance management system that includes goal-setting, feedback, and reward mechanisms to motivate and engage employees.
- Providing regular training and development opportunities to enhance employees' technical, soft, and leadership skills.
- Ensuring a safe and healthy working environment by complying with safety regulations, providing personal protective equipment, and conducting safety training.
- Encouraging teamwork, collaboration, and communication among employees fosters a positive working environment and enhances productivity and creativity.
- Implementing a fair and competitive compensation and benefits system that reflects the employees' performance and contribution.
- Monitoring and evaluating workforce performance and productivity regularly using key performance indicators (KPIs) and metrics to identify areas for improvement and optimization.
- Encouraging innovation and continuous improvement by involving employees in problem-solving, process improvement, and new product development.
Challenges and Solutions in Labor and Workforce Management in Plastic Manufacturing:
- Attracting and retaining skilled and experienced labor is a significant challenge in plastic manufacturing due to the highly competitive labor market and the perception of the industry as low-skilled and labor-intensive.
- Solutions to this challenge include investing in employee development and training, offering competitive compensation and benefits packages, and creating a positive and supportive working environment.
- Another challenge is managing employee diversity and cultural differences, which can affect communication, collaboration, and teamwork.
- Solutions to this challenge include promoting cultural awareness and sensitivity, providing language training and translation services, and encouraging diversity and inclusion in the workplace.
- Ensuring compliance with labor laws and regulations is another challenge in plastic manufacturing, as the industry is subject to various labor and safety regulations and standards.
- Solutions to this challenge include conducting regular audits and inspections, providing safety training and personal protective equipment, and implementing a robust safety management system.
Design and Engineering Considerations in Plastic Manufacturing
Product Design: The first step in plastic manufacturing is the design of the product. The design should consider the product's function, the intended audience, and any specific requirements of the manufacturing process.
The design must be optimized for the production process to ensure the product can be produced efficiently and cheaply. The design should also consider the product's environmental impact, such as its recyclability or biodegradability.
Material Selection: The selection of materials is critical in plastic manufacturing. The choice of material will impact the product's properties, such as strength, flexibility, and durability.
The material should be selected based on its intended use, and the manufacturing process must be able to work with the chosen material. It is crucial to consider the environmental impact of the material as well, including its carbon footprint and its potential for recycling or biodegradation.
Mold Design: Mold design is a crucial factor in plastic manufacturing. The mold must be designed to produce the desired shape and dimensions of the product. The mold should be made of a durable material that can withstand the rigors of the manufacturing process, and it should be designed to allow for efficient production.
The mold should also be designed to minimize waste and reduce the amount of material needed.
Tooling: Tooling is an essential consideration in plastic manufacturing. The tools used in the manufacturing process must be designed to produce the desired shape and dimensions of the product.
The tools must be made of durable materials that can withstand the manufacturing process and should be designed to minimize waste and reduce the amount of material needed.
Production Process: The production process is critical in plastic manufacturing. The process must be designed to produce high-quality products efficiently and at a low cost.
The process should be designed to minimize waste and reduce the amount of material needed. The process should also be designed with safety in mind, and appropriate safety measures must be put in place to protect workers and equipment.
Quality Control: Quality control is essential in plastic manufacturing. The manufacturing process must be designed to produce consistent, high-quality products. Quality control measures should be put in place at every stage of the manufacturing process, from material selection to production to final inspection.
The quality control process should be designed to identify and correct any defects or issues in the manufacturing process.
Automation: Automation is an increasingly important consideration in plastic manufacturing. Automation can increase production efficiency and reduce costs. Automation can be used to perform repetitive tasks, such as assembly or packaging, and can also be used to monitor and control the manufacturing process.
Automation can also help to improve safety by reducing the need for manual labor in hazardous areas.
Sustainability: Sustainability is an essential consideration in plastic manufacturing. The manufacturing process should be designed to minimize waste and reduce the product's environmental impact.
This can include using recycled materials, designing products for recyclability or biodegradability, and reducing the carbon footprint of the manufacturing process.
Energy Efficiency and Sustainability in Plastic Manufacturing
Plastic manufacturing is a major contributor to energy consumption and greenhouse gas emissions. As the world becomes more focused on sustainability, the plastic manufacturing industry needs to prioritize energy efficiency and sustainability in its operations.
Here are some ways the industry can do this:
- Adopting renewable energy sources: The use of renewable energy sources such as solar, wind, and hydro can greatly reduce the industry's reliance on non-renewable energy sources like fossil fuels, thereby reducing their carbon footprint.
- Upgrading equipment: Updating and maintaining equipment can increase energy efficiency by reducing energy waste and increasing productivity. Energy-efficient machinery can also reduce operating costs and improve the bottom line.
- Waste reduction and recycling: The implementation of waste reduction and recycling programs can significantly reduce the amount of plastic waste that ends up in landfills or oceans, thereby reducing the industry's carbon footprint.
- Lean manufacturing: Adopting lean manufacturing practices can improve production efficiency and reduce waste, which in turn reduces energy consumption and greenhouse gas emissions.
- Life cycle analysis: Conducting a life cycle analysis of plastic products can help identify areas where energy efficiency and sustainability can be improved, such as in the manufacturing, use, and disposal of the product.
- Collaborating with suppliers and customers: Working with suppliers and customers to identify and implement sustainable practices throughout the supply chain can also help reduce energy consumption and greenhouse gas emissions.
- Monitoring and reporting: Regular monitoring and reporting of energy consumption and greenhouse gas emissions can help identify areas for improvement and track progress toward sustainability goals.
Quality Control and Assurance in Plastic Manufacturing
Quality control and assurance are essential in the plastic manufacturing industry to ensure that products meet the required specifications and are of good quality. Quality control and assurance help to prevent defects, reduce waste, and improve overall efficiency.
Here are some points that explain the importance of quality control and assurance in plastic manufacturing:
Ensuring compliance with regulations and standards: Quality control and assurance in plastic manufacturing help ensure that products comply with regulatory requirements and industry standards.
Regulatory compliance is essential to ensure product safety and prevent legal issues, while adherence to industry standards ensures consistent quality and reliability.
Reducing defects and waste: Defects in plastic manufacturing can result in significant time, money, and resource losses. Quality control and assurance processes can help identify defects early in production, preventing further processing of defective products and reducing waste.
Improving customer satisfaction: Quality products lead to satisfied customers. Quality control and assurance processes ensure that products meet or exceed customer expectations, resulting in increased customer satisfaction and loyalty.
Enhancing brand reputation: Manufacturers that prioritize quality control and assurance in their operations can build a positive reputation for their brand. A good reputation attracts more customers and increases the likelihood of repeat business.
Increasing production efficiency: Quality control and assurance processes can help identify inefficiencies in the production process, leading to improvements in productivity and efficiency. This, in turn, can reduce production costs and lead to higher profits.
Improving supplier relationships: Quality control and assurance in plastic manufacturing can help build better relationships with suppliers. By ensuring that suppliers provide high-quality materials, manufacturers can reduce the risk of defects and improve the overall quality of their products.
Maintaining product consistency: Quality control and assurance processes can help maintain product consistency, ensuring that products are of the same quality every time they are produced. This is essential for building customer trust and brand loyalty.
Implementing continuous improvement: Quality control and assurance processes are not static but rather involve continuous improvement efforts. By analyzing quality data and identifying areas for improvement, manufacturers can make changes to improve quality and efficiency in their operations.
Safety Protocols and Regulations in Plastic Manufacturing
Plastic manufacturing is a large-scale process that involves various risks and hazards. Hence, it is necessary to ensure that appropriate safety protocols and regulations are in place to ensure the well-being of employees, protect the environment, and maintain product quality.
This section will explore the key safety protocols and regulations that must be followed in plastic manufacturing.
Hazard Communication: The Occupational Safety and Health Administration (OSHA) has mandated that plastic manufacturers must develop a hazard communication program. The program must contain information about the hazardous chemicals used in manufacturing, how to handle them safely, and the personal protective equipment (PPE) required to be worn.
Employees must be trained in the hazard communication program to understand the potential hazards and the proper measures to mitigate them.
Machine Guarding: Plastic manufacturing involves the use of various machines that can cause serious injuries if not properly guarded. Hence, it is necessary to have proper machine guarding in place to prevent employees from coming into contact with moving parts of the machine.
Machine guards must be inspected regularly to ensure they are functioning correctly and must be repaired or replaced if damaged.
Fire Safety: The manufacturing process of plastic involves the use of flammable chemicals that can cause fires or explosions. Hence, fire safety protocols must be in place, including the installation of fire suppression systems, smoke detectors, and fire alarms. Employees must be trained on fire safety procedures and evacuation plans in case of an emergency.
Personal Protective Equipment: The use of appropriate PPE is essential in plastic manufacturing to ensure the safety of employees. PPE includes safety glasses, face shields, gloves, and protective clothing. Employees must be trained on the proper use, maintenance, and storage of PPE.
Electrical Safety: Plastic manufacturing involves the use of electrical equipment that can cause electric shocks or fires if not correctly maintained or used. Electrical safety protocols must be in place, including regular inspection and maintenance of electrical equipment and grounding of electrical circuits.
Noise Control: Plastic manufacturing processes generate high levels of noise, which can cause hearing loss or other health issues. Hence, it is necessary to have noise control measures in place, such as noise-reducing barriers or earplugs.
Ergonomics: Plastic manufacturing processes involve repetitive motions that can cause musculoskeletal disorders or injuries. Hence, it is necessary to have ergonomic measures in place, such as adjustable workstations, to reduce the risk of injuries and improve employee comfort.
Environmental Regulations: Plastic manufacturing can significantly impact the environment, so it is necessary to follow environmental regulations. This includes proper waste management, wastewater treatment, and air pollution control measures. Plastic manufacturers must comply with the regulations set by the Environmental Protection Agency (EPA) and local environmental agencies.
Emerging Technologies in Plastic Manufacturing
Additive Manufacturing
Additive manufacturing or 3D printing is a new technology that allows the creation of complex structures with intricate shapes. This technology has revolutionized the way plastic components are manufactured, allowing for faster prototyping, reduced lead times, and decreased costs.
Additionally, 3D printing can help reduce material waste, as only the required amount of material is used to create the product.
Robotics
The use of robotics in plastic manufacturing has increased significantly over the past few years. Robots are used for various tasks such as material handling, assembly, and packaging. Robots in manufacturing have several benefits, including increased efficiency, reduced labor costs, and improved product quality.
Automation
Automation is another technology that is rapidly changing the manufacturing industry. Automation involves the use of machines to perform tasks that humans traditionally did.
This technology can help reduce labor costs, increase production efficiency, and improve product quality. Automation also reduces the risk of accidents caused by human error.
Internet of Things (IoT)
The IoT is a network of physical devices that are connected to the internet and can communicate with each other. This technology has many applications in the plastic manufacturing industry.
For example, sensors can be used to monitor the temperature and humidity of the manufacturing environment, ensuring that the conditions are optimal for production. Additionally, IoT devices can be used to track the movement of materials and products throughout the manufacturing process, providing real-time data on production progress.
Artificial Intelligence (AI)
AI is an emerging technology that can potentially transform the plastic manufacturing industry. AI can be used to analyze large amounts of data to identify patterns and trends that can help improve production efficiency and reduce costs.
Additionally, AI can be used to optimize manufacturing processes by predicting maintenance needs, identifying potential bottlenecks, and improving quality control.
Nanotechnology
Nanotechnology is a field of science that involves the manipulation of matter at the nanoscale level. This technology has many potential applications in the plastic manufacturing industry, including the development of new materials with enhanced properties.
For example, nanocomposites can be created by adding nanoparticles to plastic resins, resulting in stronger, lighter, and more durable materials.
Bioplastics
Bioplastics are a new type of plastic that is made from renewable sources such as corn starch, sugarcane, or potato starch. This technology has several advantages over traditional plastics, including reduced carbon footprint, biodegradability, and reduced dependence on fossil fuels.
Bioplastics can be used in a variety of applications, including packaging, textiles, and automotive parts.
Market Trends and Consumer Demand for Plastic Products
Plastic products are ubiquitous in our daily lives. Plastic is an essential component of many products, from packaging materials to electronics, toys, and medical devices. The plastic industry has seen significant growth over the years, with increasing demand from various sectors of the economy.
This section will explore the market trends and consumer demand for plastic products.
Sustainable Packaging
There is a growing demand for sustainable and environmentally friendly packaging solutions. Consumers are becoming more conscious of the impact of plastic waste on the environment and are seeking products that have a minimal environmental impact.
Companies are responding to this demand by adopting sustainable packaging practices, such as using biodegradable and compostable materials.
Lightweight Materials
Lightweight plastics are becoming increasingly popular due to their versatility and cost-effectiveness. They are used in various applications, including automotive, aerospace, and construction industries.
Lightweight plastics offer several advantages, such as improved fuel efficiency, increased durability, and reduced production costs.
Health and Safety Concerns
There is an increasing concern about the health and safety implications of plastic products. Consumers are demanding safer products that do not contain harmful chemicals, such as BPA and phthalates.
Manufacturers are responding to this demand by developing new materials and production processes that eliminate these harmful chemicals.
Recycling and Circular Economy
The circular economy is a concept that aims to reduce waste by reusing materials and resources. The plastic industry is embracing this concept by adopting recycling practices and developing recyclable products. The demand for recycled plastics is also increasing, with many companies committing to using recycled materials in their products.
Innovation and New Applications
The plastic industry is constantly evolving, with new innovations and applications emerging. For example, plastic is being used in the development of 3D printing, which is revolutionizing manufacturing processes. Other applications include plastic electronics, medical implants, and nanotechnology.
Consumer Behavior
Consumer behavior is a significant driver of market trends and demand for plastic products. Consumers are seeking products that are functional, aesthetically pleasing, and affordable. They are also becoming more conscious of the environmental impact of their purchases and are seeking products that align with their values.
Regulatory Environment
The regulatory environment is a crucial factor in shaping the plastic industry. Regulations are put in place to protect consumers and the environment from harmful products and production practices. Manufacturers must comply with these regulations, which can significantly impact the industry's growth and development.
Collaboration and Partnerships in Plastic Manufacturing
Access to New Technology and Expertise
Collaboration and partnerships in plastic manufacturing can give companies access to new technology and expertise that they may not have otherwise.
By partnering with other companies or research institutions, companies can leverage their expertise and resources to improve their manufacturing processes, develop new products, and improve their efficiency.
Risk Sharing
Collaboration and partnerships can help mitigate risks associated with plastic manufacturing. By sharing resources and knowledge, companies can reduce their financial risks and share research and development costs.
Collaboration can also help companies manage their supply chain and reduce the risk of supply chain disruptions.
Innovation
Collaboration and partnerships in plastic manufacturing can foster innovation. By working together, companies can combine their expertise and resources to develop new products and solutions that meet the needs of consumers.
Collaboration can also help companies stay ahead of the competition by developing new manufacturing processes that increase efficiency and reduce costs.
Cost Savings
Collaboration and partnerships in plastic manufacturing can lead to cost savings. By sharing resources and knowledge, companies can reduce manufacturing costs and improve efficiency. Collaboration can also help companies save money by reducing the costs associated with research and development.
Increased Market Share
Collaboration and partnerships can help companies increase their market share. By working together, companies can develop new products and solutions that appeal to consumers, allowing them to expand their customer base and increase their sales. Collaboration can also help companies enter new markets, both domestic and international.
Environmental Sustainability
Collaboration and partnerships in plastic manufacturing can also promote environmental sustainability.
Companies can develop new materials and manufacturing processes that reduce waste and pollution by working together. Collaboration can also help companies find new ways to recycle and reuse plastic, reducing their environmental impact.
The Impact of International Trade on Plastic Manufacturing
Plastic manufacturing is a global industry that is heavily impacted by international trade. The trade of plastic products and raw materials across borders significantly influences the growth, profitability, and sustainability of plastic manufacturing.
In this section, we will discuss the impact of international trade on plastic manufacturing.
Global supply chain: International trade plays a crucial role in the supply chain of plastic manufacturing. Raw materials such as crude oil, natural gas, and petrochemicals used in the production of plastic are sourced from different parts of the world.
Plastic manufacturers rely heavily on importing and exporting these raw materials to keep their production running. Any disruption in the global supply chain can significantly impact the plastic manufacturing industry.
Access to new markets: International trade offers plastic manufacturers access to new markets. The demand for plastic products is growing worldwide, and plastic manufacturers can tap into new markets through export.
Exporting plastic products can also provide a competitive advantage for manufacturers, as they can sell their products at a lower cost than the local manufacturers.
Competition: International trade can also increase competition in the plastic manufacturing industry. To remain competitive, plastic manufacturers must innovate and adopt new technologies to reduce costs and increase efficiency.
Environmental concerns: International trade can also have an impact on the environment. Plastic manufacturing produces significant greenhouse gases that contribute to climate change.
The transportation of raw materials and plastic products across borders further adds to the industry's carbon footprint. As a result, governments worldwide are implementing regulations to reduce the environmental impact of plastic manufacturing and trade.
Tariffs and trade agreements: Tariffs and trade agreements are also essential factors that impact the plastic manufacturing industry. The imposition of tariffs on plastic products or raw materials can increase the cost of production, which can impact the profitability of manufacturers.
On the other hand, trade agreements can provide a level playing field for manufacturers by reducing tariffs and promoting free trade.
Technological advancements: International trade also enables plastic manufacturers to adopt new technologies and innovations from other countries.
New technologies and manufacturing processes can help manufacturers reduce their costs, improve product quality, and increase efficiency. Collaboration with other countries can help plastic manufacturers stay ahead of the curve and compete more globally.
Intellectual Property Protection in Plastic Manufacturing
Intellectual property (IP) protection is crucial for any industry, and plastic manufacturing is no exception. Companies invest significant resources in developing new products, processes, and technologies, and they must safeguard their innovations from being copied or stolen by competitors.
This section will discuss the importance of intellectual property protection in plastic manufacturing and how companies can protect their innovations.
Understanding Intellectual Property (IP)
Intellectual property refers to the legal ownership of creative works, inventions, or ideas. In plastic manufacturing, IP can include patents, trademarks, copyrights, and trade secrets.
Patents protect inventions, while trademarks protect brand names and logos. Copyrights protect artistic and literary works, while trade secrets protect confidential information like recipes, formulas, or manufacturing processes.
Importance of IP Protection in Plastic Manufacturing
IP protection is critical for plastic manufacturing companies as it can help them gain a competitive advantage in the market. By protecting their innovations, companies can prevent competitors from replicating their products or processes and gaining an unfair advantage.
IP protection can also help companies generate revenue by licensing or selling their patents or technologies.
Types of IP Protection
Companies can use several types of IP protection to safeguard their innovations. Patents are the most common form of IP protection in plastic manufacturing, and they can be granted for new products, processes, or designs.
Trademarks protect brand names, logos, and slogans, while copyrights protect original artistic or literary works. Trade secrets protect confidential information, such as manufacturing processes or product formulas, that provides a competitive advantage.
Steps to Protect IP
Plastic manufacturing companies should take several steps to protect their IP, including conducting thorough research to ensure their inventions are unique and not already patented. Companies should also file patent applications as soon as possible to secure their ownership of the invention.
Additionally, companies can protect their IP by keeping their confidential information secret, creating agreements with employees and contractors to protect their IP, and using trademarks to protect their brand identity.
IP Enforcement
If a plastic manufacturing company suspects that its IP has been infringed upon, it can take legal action to enforce its rights. This can include filing a lawsuit to stop the infringement, seeking monetary damages for the harm caused by the infringement, or negotiating a settlement with the infringing party.
However, IP enforcement can be a complex and costly process, and companies should consult with legal experts to ensure they are taking the appropriate steps.
Strategies for Managing Risk in Plastic Manufacturing
Conduct a thorough risk assessment: A risk assessment is the foundation of any effective risk management program. It involves identifying and analyzing potential risks and their likelihood of occurrence.
The assessment should be conducted by a qualified safety professional who can identify and evaluate all potential risks in the facility.
Implement a safety management system: A safety management system (SMS) is a comprehensive system designed to manage safety in the workplace. It includes policies, procedures, and processes for identifying, assessing, and controlling risks.
The SMS should be regularly reviewed and updated to reflect any changes in the facility's operations.
Provide employee training: Proper training is critical for ensuring employee safety. All employees should receive training on the hazards associated with their job, the proper use of equipment and machinery, and emergency response procedures. Regular refresher training should also be provided.
Maintain equipment: Regular equipment maintenance is essential to prevent accidents caused by malfunctioning machinery. A preventive maintenance program should be established to ensure all equipment is inspected, serviced, and repaired on a regular basis.
Use appropriate personal protective equipment (PPE): PPE such as safety glasses, gloves, and respirators can help protect employees from exposure to hazardous chemicals and other risks in the facility. Employees should be trained on the proper use and maintenance of PPE.
Implement a hazard communication program: A hazard communication program ensures that employees are informed about the hazards associated with the materials they are working with.
The program should include labeling hazardous materials, safety data sheets, and employee training on the hazards of the chemicals used in the facility.
Implement an emergency response plan: An emergency response plan is critical for responding to accidents and other emergencies in the facility. The plan should include procedures for evacuating employees, contacting emergency services, and controlling the release of hazardous materials.
Conduct regular safety audits: Regular safety audits can help identify potential hazards and ensure that safety policies and procedures are being followed. Audits should be conducted by a qualified safety professional and should include a review of all safety policies and procedures, equipment maintenance records, and employee training records.
Establish a safety committee: A safety committee can help promote a culture of safety in the facility. The committee should include representatives from all areas of the facility and should be responsible for reviewing safety policies and procedures, identifying potential hazards, and making recommendations for improvements.
Continuously improve safety practices: Risk management is an ongoing process, and it is essential to evaluate and improve safety practices in the facility continuously. Regular reviews of safety policies and procedures, equipment maintenance records, and employee training records can help identify areas for improvement.
The Role of Industry Associations and Trade Organizations in Plastic Manufacturing
Representation and Advocacy: Industry associations and trade organizations represent the interests of plastic manufacturers and advocate for policies and regulations that support the industry.
They also work with government agencies to ensure that regulations are reasonable and do not impose undue burdens on manufacturers.
Information Sharing: These organizations provide a platform for members to share information and knowledge on best practices, emerging technologies, and market trends.
This information sharing helps members stay up-to-date with industry developments, improve their production processes and stay competitive.
Networking Opportunities: Industry associations and trade organizations provide numerous networking opportunities for members to connect and build relationships with other manufacturers, suppliers, and customers.
These connections can lead to new business opportunities, collaborations, and partnerships.
Training and Professional Development: Many industry associations and trade organizations offer training and professional development programs for members to enhance their skills and knowledge in areas such as manufacturing processes, product design, and regulatory compliance.
These programs help members stay up-to-date with the latest industry trends and improve their competitiveness.
Research and Development: Industry associations and trade organizations often undertake research and development projects that aim to improve plastic manufacturing processes, product design, and environmental sustainability.
Members can benefit from these projects by gaining access to new technologies, best practices, and innovative solutions.
Standards Development: Industry associations and trade organizations play a significant role in developing and maintaining industry standards that help ensure product quality, safety, and environmental sustainability. These standards help members improve their product offerings and meet the expectations of customers and regulators.
Branding and Marketing: Industry associations and trade organizations provide branding and marketing opportunities for members to promote their products and services to a wider audience. These efforts can include trade shows, exhibitions, and industry publications.
How Deskera Can Assist You?
Deskera MRP allows you to closely monitor the manufacturing process. From the bill of materials to the production planning features, the solution helps you stay on top of your game and keep your company's competitive edge.
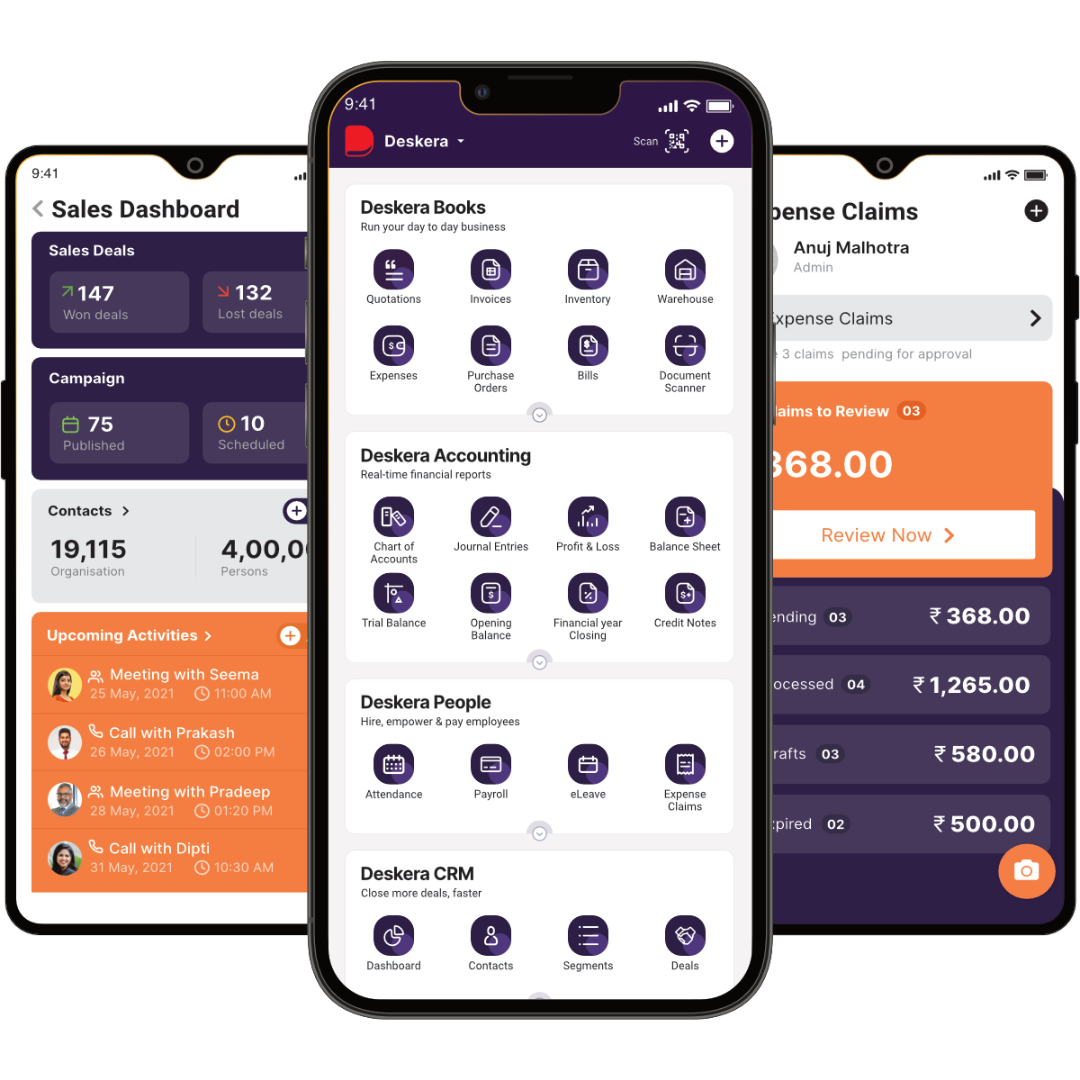
Deskera ERP and MRP system can help you:
- Manage production plans
- Maintain Bill of Materials
- Generate detailed reports
- Create a custom dashboard
Deskera ERP is a comprehensive system that allows you to maintain inventory, manage suppliers, and track supply chain activity in real-time, as well as streamline a variety of other corporate operations.
Deskera Books enables you to manage your accounts and finances more effectively. Maintain sound accounting practices by automating accounting operations such as billing, invoicing, and payment processing.
Deskera CRM is a strong solution that manages your sales and assists you in closing agreements quickly. It not only allows you to do critical duties such as lead generation via email, but it also provides you with a comprehensive view of your sales funnel.
Deskera People is a simple tool for taking control of your human resource management functions. The technology not only speeds up payroll processing but also allows you to manage all other activities such as overtime, benefits, bonuses, training programs, and much more. This is your chance to grow your business, increase earnings, and improve the efficiency of the entire production process.
Conclusion
Plastic manufacturing is a complex and highly dynamic process that has been integral to modern society for decades. The industry has witnessed significant growth and advancements over the years, with the development of new technologies and materials and improvements in production efficiency and quality control.
Identifying the key drivers of plastic manufacturing is crucial for businesses to stay competitive, meet customer demands, and comply with regulatory requirements. These drivers include factors such as raw material availability, manufacturing costs, environmental sustainability, market demand, and innovation.
To ensure the sustainable growth of the plastic manufacturing industry, companies need to adopt a comprehensive approach to safety that includes employee training, safety protocols, and regular equipment maintenance.
Companies can also benefit from partnerships with academic institutions and research organizations to develop new materials and manufacturing techniques that are more efficient and environmentally friendly.
Overall, the future of plastic manufacturing looks promising, with a growing focus on sustainability and innovation. The industry will continue to evolve as new technologies and materials emerge, but businesses that prioritize safety, efficiency, and environmental responsibility will be well-positioned to thrive in this dynamic landscape.
Key Takeaways
- Raw material sourcing, energy efficiency, and labor costs are the key drivers of plastic manufacturing.
- The demand for sustainable plastic manufacturing processes is increasing, driven by consumer and regulatory pressures.
- Innovation in polymer science and engineering is driving the development of new, high-performance plastics.
- Advancements in additive manufacturing and 3D printing enable more efficient and cost-effective production of plastic parts.
- The adoption of Industry 4.0 technologies, such as artificial intelligence and the Internet of Things, is revolutionizing plastic manufacturing processes.
- The rise of e-commerce and online shopping drives demand more efficient and sustainable packaging solutions.
- The development of bioplastics is becoming a key driver of plastic manufacturing, as they offer a more sustainable alternative to traditional plastics.
- The increasing use of recycled plastics in manufacturing drives demand for more efficient and cost-effective recycling processes.
Related Articles
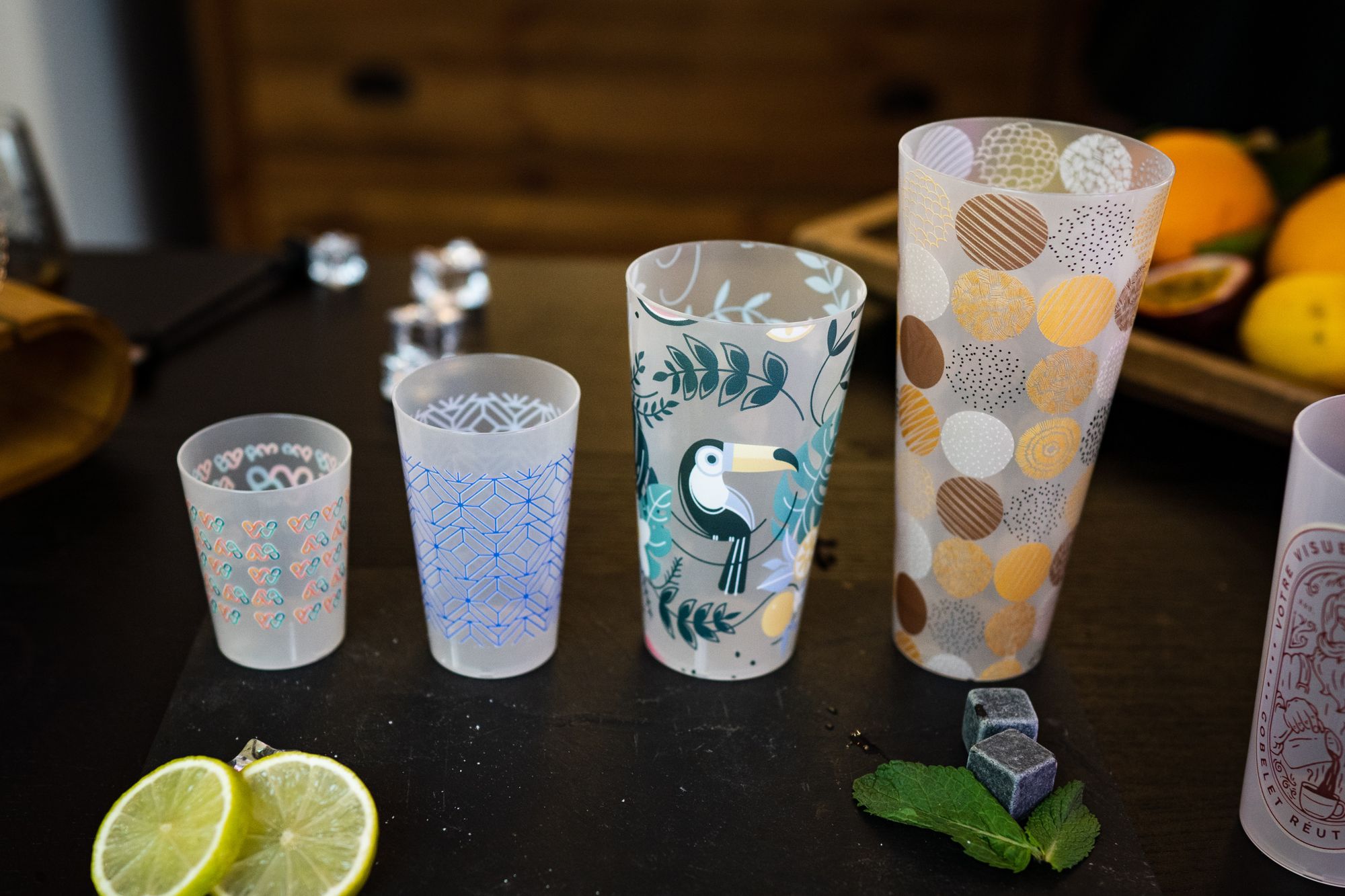
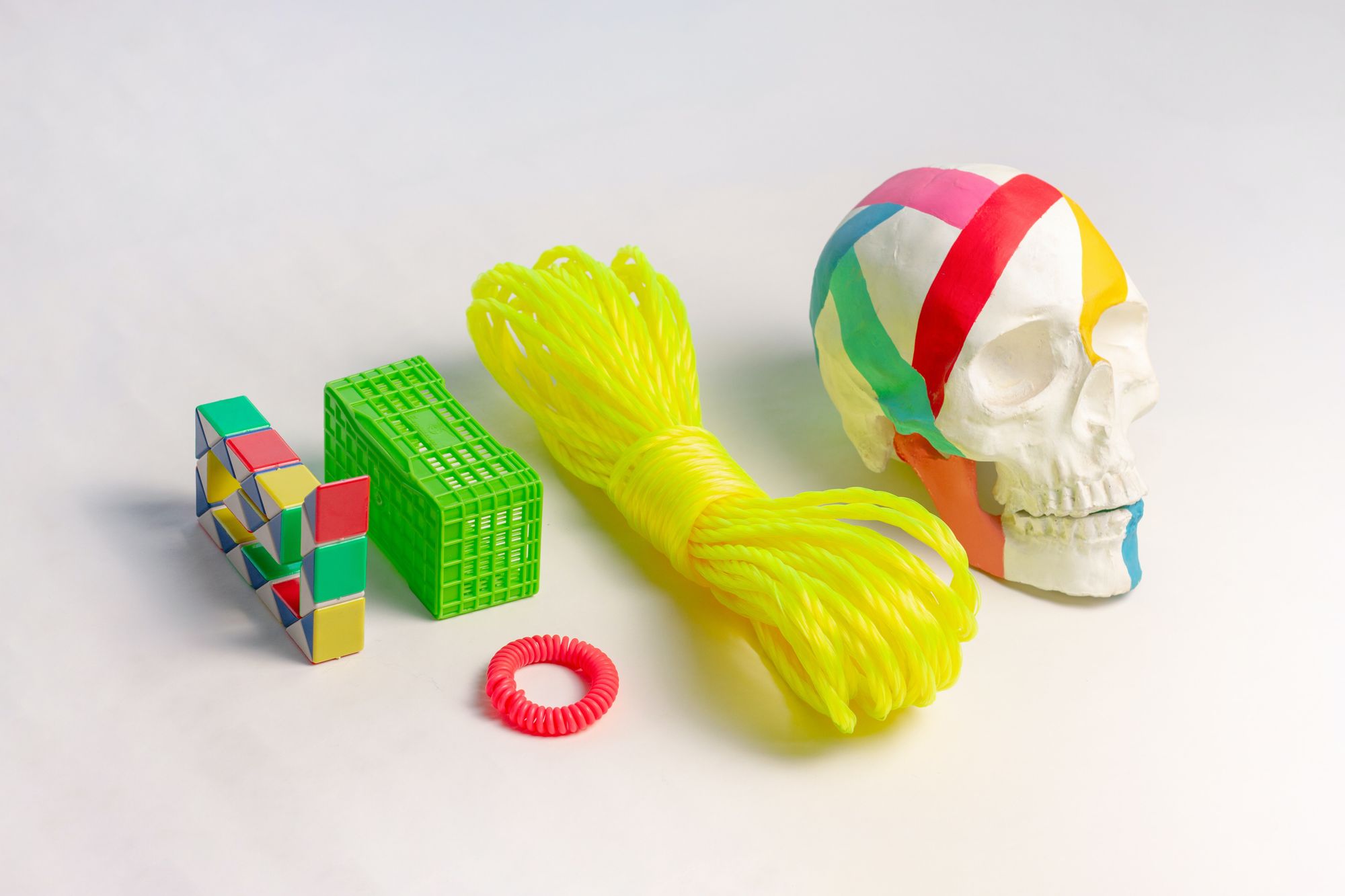
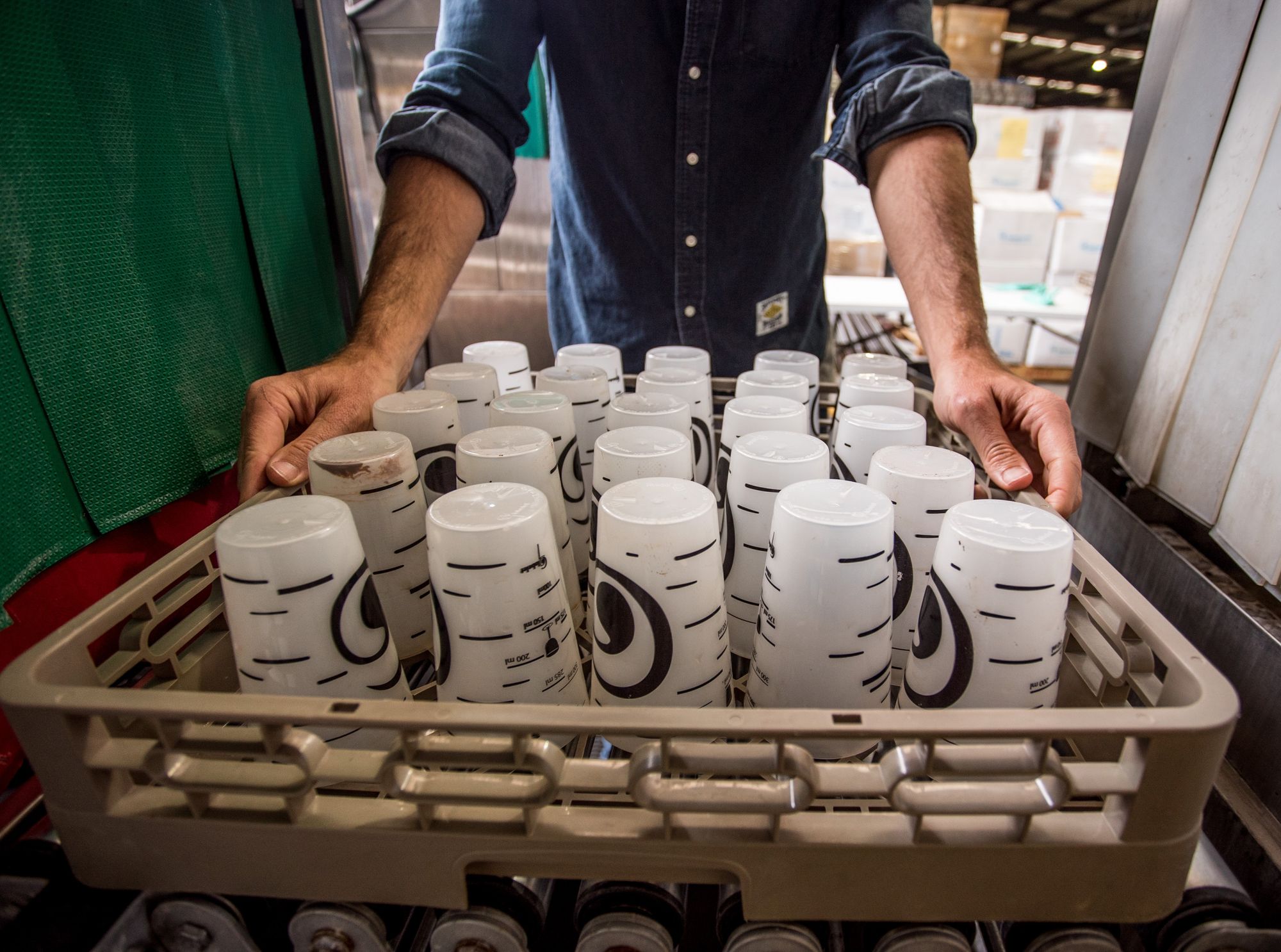
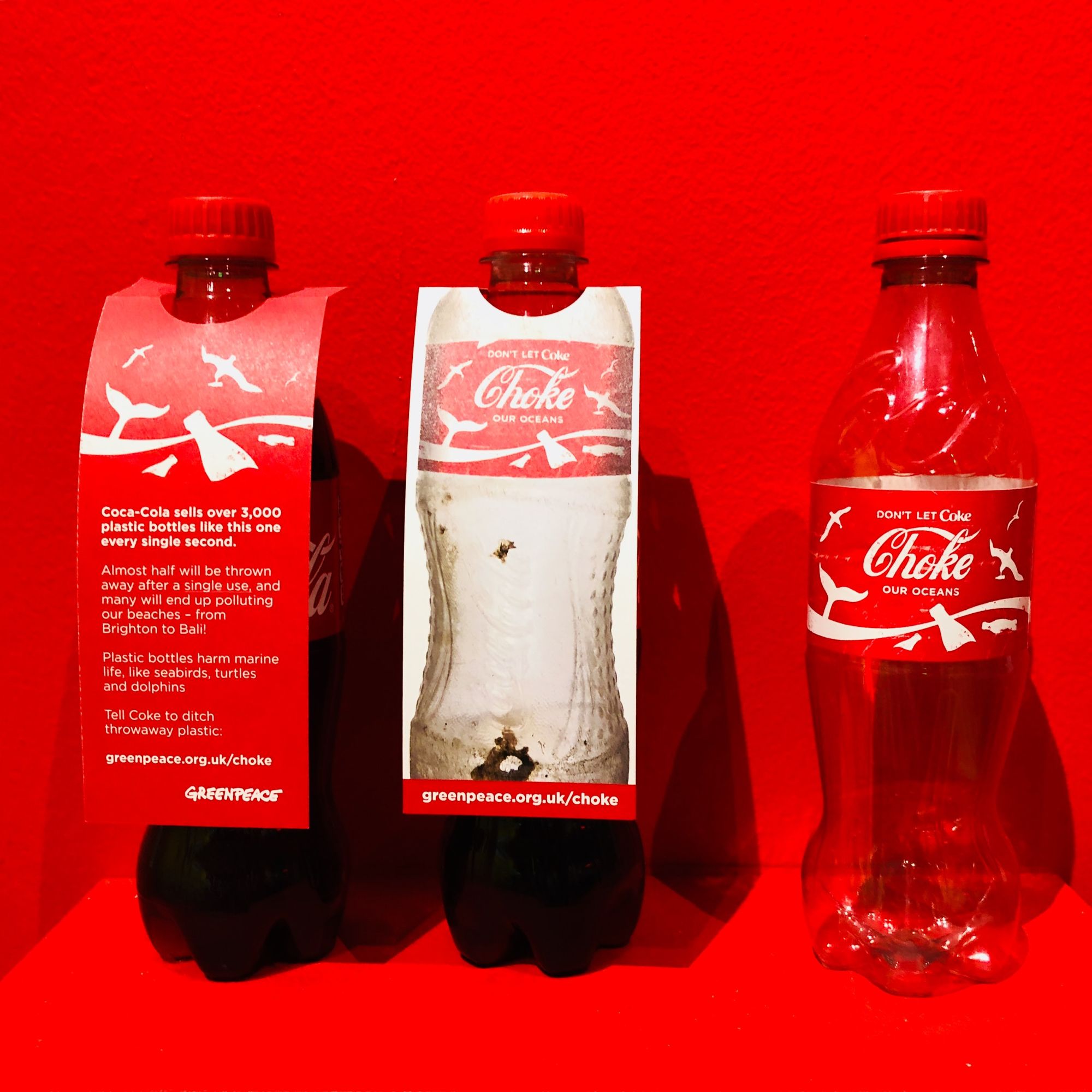