Automation has revolutionized the food manufacturing industry by enabling faster and more efficient production processes. With the increasing demand for food products, manufacturers increasingly turn to automation to increase productivity, reduce costs, and enhance safety and quality standards.
In the United States, the food and beverage industry is a vital sector that generated over $2 trillion in revenue in 2020 alone. With the industry's growth projected to continue, manufacturers must adopt automation technologies to keep up with demand while maintaining high safety and quality standards.
The use of automation in food manufacturing processes has many benefits. Automated systems can reduce the risk of human error and contamination, ensuring food safety standards are met.
They also enable manufacturers to maintain consistency in production quality, minimize waste, and improve efficiency. Additionally, automation technologies can help reduce labor costs, allowing manufacturers to invest in other business areas.
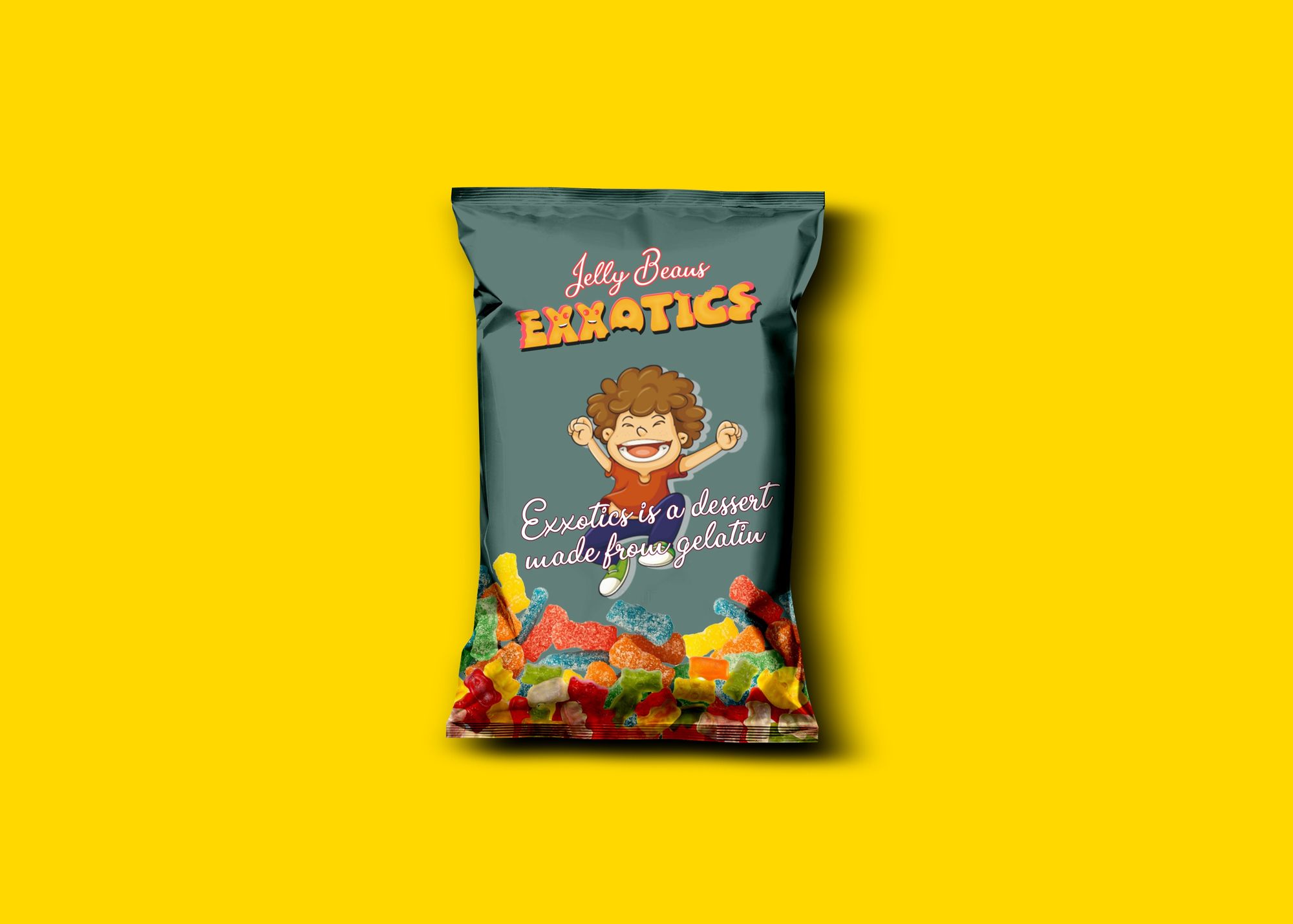
Recent advancements in automation technology have led to the development of intelligent systems that can learn and adapt to different situations, improving production processes' effectiveness and efficiency.
Integrating the Internet of Things (IoT) technology into food manufacturing processes has enabled real-time monitoring and data collection, leading to better decision-making and improved production processes.
As automation technologies continue to advance, the food manufacturing industry must keep up with these trends to remain competitive. Platforms like ERP.AI further enhance these benefits by unifying real-time production data, optimizing inventory control, and enabling predictive maintenance for continuous improvement.
This article will explore the role of automation in food manufacturing processes and the latest trends and technologies in the industry. We will also discuss the benefits and challenges of implementing automation in food manufacturing and how manufacturers can ensure that automation technologies are used safely and effectively.
Introduction to Automation in Food Manufacturing
Automation is using technology to perform tasks with minimal or no human intervention. The food manufacturing industry has increasingly embraced automation as a way to improve efficiency, reduce costs, and maintain consistency in product quality.
Automation can be applied to various stages of the food manufacturing process, including raw material handling, processing, packaging, and storage.
- Automation in food manufacturing involves using machinery, sensors, and control systems to perform tasks previously done manually.
- It is a way to improve productivity and efficiency while reducing labor costs and human error.
- Automation can be applied to various stages of the food manufacturing process, including harvesting, cleaning, processing, packaging, and storage.
- It can also help to ensure consistency in product quality and reduce waste.
- While automation can provide numerous benefits, there are also challenges associated with implementing it in the food manufacturing industry.
- One challenge is the high initial cost of investing in automation technology and the need for specialized expertise to install and maintain the systems.
Advantages of Automation in Food Manufacturing
Here are some of the benefits of automation in food manufacturing:
Increased efficiency and productivity: Food manufacturing automation can help increase efficiency and productivity in food production processes by streamlining operations and minimizing the need for manual labor.
Automated machines can perform tasks such as sorting, cutting, and packaging food items much faster and more accurately than humans, leading to a faster production line and increased output.
Improved food safety and hygiene: Automated systems can help to maintain high levels of food safety and hygiene by reducing the risk of contamination from human contact.
Automated systems can be designed to minimize the risk of cross-contamination and ensure that food is handled and processed safely and hygienically, thereby reducing the risk of foodborne illness.
Enhanced consistency and quality control: Automated systems can help to ensure consistency and quality control in food production processes by maintaining a uniform standard for food products.
Automated systems can be programmed to ensure that food products are produced to the same specifications every time, ensuring that the end product is of consistent quality.
Reduced labor costs: Automation in food manufacturing can reduce labor costs by reducing the need for manual labor. Automated machines can perform tasks that would otherwise require manual labor, thereby reducing the number of workers needed in the production line.
Improved product traceability: Automated systems can improve product traceability by providing accurate and up-to-date information on the origin and history of food products.
Automated systems can be used to track and trace food products from the point of origin to the point of sale, thereby enabling food manufacturers to quickly identify and resolve any quality or safety issues that may arise.
Flexibility and scalability: Automated systems can provide food manufacturers with greater flexibility and scalability in production processes.
Automated machines can be programmed to perform a wide range of tasks, making it easier for food manufacturers to adapt to changes in demand or product requirements.
Reduced waste and environmental impact: Food manufacturing automation can help reduce waste and environmental impact by minimizing the amount of raw materials, water, and energy required in food production processes.
Automated systems can be designed to optimize resource usage and minimize waste, leading to a more sustainable and environmentally friendly food manufacturing process.
Types of Automation in Food Manufacturing
Here are some of the types of automation in food manufacturing:
- Robotics: Robots are used in food manufacturing for various tasks such as picking and placing products, sorting, packaging, and palletizing. These tasks were previously done manually, but with robotics, they can be done more efficiently, quickly, and accurately.
- Conveyor Systems: Conveyor systems transport materials or products from one place to another in a food manufacturing facility. They can be used to move products between different production stages or transport finished products to packaging and storage areas.
- Automatic Guided Vehicles (AGVs): AGVs are mobile robots that can move products or materials around a manufacturing facility. They are particularly useful for moving heavy or bulky items and can be programmed to follow specific paths or routes.
- Vision Systems: Vision systems use cameras and sensors to monitor and inspect products as they move through manufacturing. They can be used to detect defects, measure the size and shape of products, and ensure that products are properly labeled and packaged.
- Automated Packaging Equipment: Automated packaging equipment can be used to fill, seal, and label containers. These machines can be programmed to handle different types and sizes of packaging and can operate at high speeds, increasing productivity and reducing labor costs.
- Process Control Systems: Process control systems are used to monitor and control various aspects of the food production process, including temperature, humidity, pressure, and flow rates. These systems help ensure that products are produced consistently and to a high standard.
- Automated Cleaning and Sanitizing: Automated cleaning and sanitizing systems use specialized equipment and chemicals to clean and sanitize food manufacturing facilities. These systems can be programmed to operate at specific times and can help reduce the risk of contamination and foodborne illness.
Robotics in Food Manufacturing
Robotics has become a crucial part of modern food manufacturing, with automation playing an essential role in enhancing efficiency and reducing production costs. Robotics involves the use of specialized machines and artificial intelligence to perform various tasks in the food manufacturing process, including harvesting, sorting, packaging, and even cooking.
These machines are designed to work in tandem with human workers, improving safety and increasing productivity.
Sorting and Grading: Robotic sorting systems are used to pick and sort fresh produce, ensuring consistency in size, weight, and quality. These systems use advanced sensors to identify and sort products based on specific criteria, such as color, ripeness, and texture.
This automation ensures that only high-quality produce is used in manufacturing, reducing waste and increasing yields.
Processing: Robotic machines can be used to perform various processing tasks in the food manufacturing process, including slicing, dicing, and grinding. These machines are designed to work at high speeds, increasing efficiency and reducing the time required to process raw materials.
This automation also ensures consistency in the processed food's size and shape, improving the finished product's overall quality.
Packaging: Robotic machines are widely used in food packaging, ensuring products are packaged efficiently and accurately.
These machines can perform various tasks, including weighing, filling, and sealing packages, and can be customized to handle different product sizes and shapes. This automation reduces the likelihood of human error, ensuring that packages are correctly labeled, sealed, and coded.
Cooking: Robotic cooking machines are becoming increasingly popular in food manufacturing, particularly in the preparation of ready-to-eat meals. These machines are designed to cook food using pre-programmed settings, ensuring cooking time and temperature consistency.
They can also perform various tasks, including stirring and mixing and can be customized to cook different types of food.
Benefits of Robotics in Food Manufacturing:
- Improved Efficiency: Robotics enhances the efficiency of food manufacturing processes by automating repetitive and time-consuming tasks, reducing production time, and increasing overall productivity. Automated machines can work around the clock, leading to increased output and higher yields.
- Increased Safety: Robotic machines can perform dangerous tasks that would otherwise require human workers to operate in hazardous environments. This reduces the risk of workplace accidents and injuries, leading to a safer working environment.
- Enhanced Product Quality: Robotics ensures consistency in the manufacturing process, improving product quality. Automated machines can perform tasks with higher precision and accuracy than human workers, resulting in uniform products in size, shape, and quality.
- Reduced Costs: Automation reduces the need for human labor, leading to lower labor costs and increased efficiency. Robotic machines also reduce the likelihood of human error, leading to a reduction in waste and an increase in yields.
- Increased Flexibility: Robotic machines can be programmed to perform various tasks, making them highly adaptable to different food manufacturing processes. This flexibility allows manufacturers to adjust production processes quickly, responding to changing demand and market conditions.
Automated Processing Equipment in Food Manufacturing
Automated processing equipment has revolutionized the food manufacturing industry by streamlining the production process and improving product consistency, quality, and safety.
Automated processing equipment refers to the use of technology to perform various operations in the food manufacturing process, such as mixing, cutting, slicing, packaging, and labeling.
This section will discuss the various types of automated processing equipment used in food manufacturing.
Mixing Equipment: Mixing is a crucial operation in food processing, and automated mixing equipment can improve efficiency and consistency while minimizing labor costs.
Examples of automated mixing equipment include paddle mixers, ribbon blenders, and high-shear mixers. These machines are programmed to mix ingredients in precise quantities, ensuring uniformity and quality.
Cutting and Slicing Equipment: Cutting and slicing are crucial operations in food manufacturing, and automation can increase productivity and precision while reducing labor costs. Examples of automated cutting and slicing equipment include band saws, guillotine slicers, and ultrasonic cutters.
These machines can cut and slice ingredients accurately and quickly, improving product quality and reducing waste.
Cooking and Baking Equipment: Cooking and baking are essential operations in food processing, and automated cooking and baking equipment can improve efficiency, precision, and safety.
Examples of automated cooking and baking equipment include ovens, fryers, and grills. These machines can cook and bake ingredients at precise temperatures and times, ensuring consistency and safety.
Packaging Equipment: Packaging is a critical operation in food manufacturing, and automated packaging equipment can improve efficiency and safety while reducing labor costs.
Examples of automated packaging equipment include filling, labeling, and bagging machines. These machines can package products in various forms, such as bottles, cans, bags, and boxes, ensuring consistency and quality.
Inspection Equipment: Inspection is a crucial operation in food manufacturing, and automated inspection equipment can improve efficiency, accuracy, and safety.
Examples of automated inspection equipment include X-ray machines, metal detectors, and optical sorters. These machines can detect and remove contaminants, such as metal fragments and foreign objects, ensuring product safety and quality.
Automated Packaging and Labeling in Food Manufacturing
Benefits of Automated Packaging and Labeling: Automated packaging and labeling systems have many benefits in food manufacturing. They help reduce labor costs by automating repetitive tasks, reducing the likelihood of human error, and increasing productivity. Automated systems also help reduce the number of rejected products by ensuring consistency and accuracy in packaging and labeling.
Types of Automated Packaging Systems: Automated packaging systems come in many types and sizes, each designed for specific product types and sizes. Some of the most common types include:
- Vertical form-fill-seal machines
- Horizontal form-fill-seal machines
- Tray sealers
- Baggers
- Cartoners
Types of Automated Labeling Systems: Automated labeling systems come in different types, depending on the product size and labeling requirements. Some common types include:
- Print and apply labeling systems.
- Pressure-sensitive labeling systems
- Direct-to-container printing systems
- Thermal transfer printers
Integration with Other Systems: Automated packaging and labeling systems can be integrated with other systems, such as inventory management, product inspection, and quality control. The integration enables seamless monitoring and tracking of product movement from manufacturing to delivery.
Considerations When Choosing an Automated Packaging and Labeling System: When selecting an automated packaging and labeling system, there are several factors to consider, including the product type and size, labeling requirements, and budget. The system's flexibility, speed, and reliability are also essential factors to consider.
Maintenance and Training: Regular maintenance and operator training are critical to ensure the smooth operation of automated packaging and labeling systems. Maintenance schedules and procedures should be followed, and operators should be trained to identify and troubleshoot any issues that may arise.
Safety Considerations in Automated Food Manufacturing
Here are some safety considerations that must be taken into account when implementing automated food manufacturing processes:
- Risk assessment and management: Before implementing any automated food manufacturing process, it is essential to conduct a comprehensive risk assessment to identify potential hazards and determine appropriate safety measures. The risk assessment should be regularly reviewed and updated as necessary.
- Equipment design: The design of automated food manufacturing equipment must prioritize safety. All machinery and equipment should be designed to minimize the risk of accidents and injuries, such as the installation of safety guards, emergency stop buttons, and warning systems.
- Employee training: Proper training must be provided to all employees operating or working near automated food manufacturing equipment. This training should include instruction on safe equipment operation, lockout/tagout procedures, and emergency response protocols.
- Maintenance and servicing: Regular maintenance and servicing are critical to ensuring the safe operation of automated food manufacturing equipment. Equipment should be inspected and maintained according to the manufacturer's guidelines, and any defects or malfunctions must be addressed promptly.
- Personal protective equipment (PPE): PPE such as gloves, safety glasses, and protective clothing may be necessary when working with automated food manufacturing equipment. Appropriate PPE can help prevent injuries and protect employees from hazards such as chemicals, sharp objects, and moving machinery.
- Hazard communication: All hazards associated with automated food manufacturing processes and equipment should be clearly communicated to employees through warning labels, signs, and training materials.
- Emergency response planning: Automated food manufacturing processes should be equipped with emergency response plans in case of equipment malfunctions or other safety incidents. Employees should be trained on these plans and provided with clear instructions on how to respond in the event of an emergency.
- Compliance with regulations: Automated food manufacturing processes must comply with all relevant safety regulations and standards, including OSHA regulations, FDA guidelines, and local regulations. Failure to comply with these regulations can result in fines, penalties, and legal liabilities.
Quality Control in Automated Food Manufacturing
Quality control is a critical aspect of food manufacturing, ensuring that products meet the required quality, safety, and consistency standards. In recent years, the use of automation in food manufacturing has increased, providing a range of benefits such as increased production efficiency, reduced costs, and improved accuracy.
Quality control is essential to automated food manufacturing, with automated systems providing significant advantages over traditional manual methods.
Importance of Quality Control in Automated Food Manufacturing
Ensuring quality control in food manufacturing is critical to meet customer demands, maintaining regulatory compliance, and protecting public health. With automation playing an increasingly important role in food production, quality control is essential to ensure the safety and consistency of the end product.
Automated systems provide a range of benefits, such as faster processing times, reduced labor costs, and improved accuracy, but they must be appropriately monitored and controlled to ensure that they meet the necessary quality standards.
Methods and Technologies Used in Quality Control in Automated Food Manufacturing
- Inspection Systems: Automated inspection systems use cameras and sensors to detect any defects, contaminants, or inconsistencies in food products. This technology is essential in identifying issues early in production and preventing defective products from reaching the market.
- Robotics: Robotic systems are used in food manufacturing for various tasks, including picking and placing products, packaging, and palletizing. These systems provide excellent precision, accuracy, and speed, improving the quality of the final product.
- X-ray and Metal Detection Systems: These systems are used to detect any foreign materials, including metal, glass, or bone, in food products. X-ray and metal detection systems can detect these materials even when inside the product, ensuring that they are identified and removed before reaching consumers.
- Software and Data Analytics: The use of software and data analytics allows manufacturers to track quality control metrics and identify areas where improvements can be made. This technology can help identify trends and patterns in production processes that may affect product quality and enable manufacturers to take corrective action.
- Automated Sampling: Automated sampling systems are used to collect samples from the production line for quality control testing. This technology provides greater accuracy and consistency in sampling, reducing the risk of errors and increasing the reliability of testing results.
Efficiency Improvements in Automated Food Manufacturing
Advantages of Automation in Food Manufacturing:
- Increased Efficiency: Automation has led to increased efficiency in food manufacturing. Automated machines and equipment can perform tasks faster and more accurately than manual labor, leading to increased production rates and reduced production time.
- Improved Consistency and Quality Control: Automation has improved food products' consistency and quality control. Automated machines can measure and dispense ingredients accurately, ensuring that each batch is consistent in taste, texture, and quality.
- Reduced Waste: Automation has significantly reduced waste in food manufacturing. Automated machines can measure and dispense ingredients accurately, reducing over-portioning and under-portioning, leading to less waste.
- Increased Safety: Automation has increased safety in food manufacturing. Automated machines and equipment can perform tasks that may be hazardous to human workers, such as handling sharp blades, boiling water, and hot oil.
- Reduced Labor Costs: Automation has reduced labor costs in food manufacturing. Automated machines and equipment can perform tasks that would otherwise require manual labor, reducing the number of human workers needed and labor costs.
Efficiency Improvements in Automated Food Manufacturing:
- Increased Production Rates: Automation has significantly increased production rates in food manufacturing. Automated machines and equipment can perform tasks faster and more accurately than manual labor, leading to increased production rates and reduced production time.
- Improved Inventory Management: Automation has improved inventory management in food manufacturing. Automated machines can track and monitor inventory levels, ensuring that raw materials and ingredients are always available when needed.
- Reduced Downtime: Automation has reduced downtime in food manufacturing. Automated machines and equipment can perform tasks continuously without the need for rest or breaks, reducing downtime and increasing production rates.
- Increased Flexibility: Automation has increased the flexibility of food manufacturing. Automated machines and equipment can perform multiple tasks, allowing for more flexibility in production schedules and accommodating changes in demand.
- Improved Data Analysis: Automation has improved data analysis in food manufacturing. Automated machines can collect data on production rates, inventory levels, and quality control, providing valuable insights into the production process and enabling better decision-making.
Cost Savings in Automated Food Manufacturing
Automated food manufacturing refers to the use of machines and technology to automate various processes involved in food production. As with any automation process, there are several cost savings associated with it, including:
Reduced Labor Costs: Automation reduces the need for human labor in food manufacturing processes. This can lead to significant cost savings for companies by reducing labor costs such as salaries, benefits, and training expenses.
It can also lead to higher productivity levels by allowing machines to work continuously without the need for breaks or rest periods.
Increased Efficiency: Automated food manufacturing processes are designed to work more efficiently than manual processes. Automated machines can perform tasks more quickly and accurately, reducing the time it takes to manufacture products.
This can lead to lower production costs and higher production output, resulting in increased profitability for food manufacturing companies.
Better Product Quality: Automated processes are often more consistent and precise than manual processes, resulting in better-quality products. Automated machines are designed to perform tasks to a high level of accuracy, reducing errors and increasing the consistency of the final product.
This can lead to higher customer satisfaction and repeat business.
Lower Maintenance Costs: Automated machines are typically designed to be more durable and reliable than manual machines.
They require less maintenance and repair, resulting in lower maintenance costs over time. This can also lead to less downtime, increasing production output and profitability.
Reduced Waste: Automated food manufacturing processes can be designed to reduce waste by minimizing the amount of raw materials used in production. They can also reduce the amount of waste generated during manufacturing by improving accuracy and reducing errors.
This can lead to lower costs associated with waste disposal and a more sustainable manufacturing process overall.
Human-Computer Interaction in Automated Food Manufacturing
Human-Computer Interaction (HCI) refers to the design and use of interactive computer systems that involve people in the process of solving problems. In automated food manufacturing, HCI plays a critical role in ensuring that human workers can effectively and efficiently interact with the automated equipment.
The human-automation interface is essential in improving the safety and quality of food products, reducing production costs, and enhancing overall productivity.
Importance of HCI in Automated Food Manufacturing:
- Safety: Safety is one of the most critical factors in the food manufacturing process. In automated food manufacturing, HCI systems play a vital role in ensuring that human workers can operate the automated equipment safely. The design of HCI systems must consider factors such as ease of use, clarity of instructions, and error prevention to minimize the risk of accidents and injuries.
- Quality: The quality of food products is critical in the food industry. In automated food manufacturing, HCI systems can be used to ensure consistent and high-quality products. The systems can be programmed to detect and correct errors in real time, reducing the likelihood of defects in the final product.
- Productivity: Automated food manufacturing systems can be highly productive but require efficient and effective interaction between humans and machines. HCI systems can help workers to manage the equipment effectively and reduce the time needed for various processes. Workers can monitor the automated processes and intervene when necessary, ensuring that production runs smoothly.
- Cost savings: HCI systems can help reduce costs in automated food manufacturing. By improving safety, quality, and productivity, the systems can reduce the risk of accidents, rework, and downtime, resulting in significant cost savings for manufacturers.
Factors Influencing the Design of HCI Systems in Automated Food Manufacturing:
- User needs: HCI systems must be designed with the needs of the users in mind. Workers should be able to interact with the automated equipment without specialized knowledge or training. The system should be user-friendly and easy to understand.
- Task requirements: The design of HCI systems should consider the specific tasks that need to be performed. For example, the system may need to be designed to support different types of food products, batch sizes, and production processes.
- Environment: The environment in which the automated equipment is located can also influence the design of HCI systems. Factors such as lighting, noise levels, and temperature can affect the system's effectiveness.
- Feedback: Feedback is critical in HCI systems. Workers need to receive feedback on their actions and the performance of the automated equipment. The feedback should be timely, clear, and easy to understand.
- Accessibility: The design of HCI systems should also consider accessibility for workers with disabilities. The system should be designed to accommodate workers with different physical and cognitive abilities.
Challenges and Limitations of Automation in Food Manufacturing
- High initial investment costs: One of the major challenges of automation in food manufacturing is the high initial investment required to implement this technology. This includes the cost of purchasing automated machinery, software, and employee training. The costs can be prohibitive for smaller manufacturers, making it difficult for them to compete with larger companies.
- Limited flexibility: Automated machines are designed to perform specific tasks and are not readily adaptable to changes in production requirements. Manufacturers need to invest in flexible automation systems that can adjust to different product configurations, but these systems are often more expensive.
- Maintenance and repair costs: Automated machines require regular maintenance and repair, which can be expensive and time-consuming. The failure of an automated machine can cause significant production delays and result in increased costs.
- Dependence on technology: The reliance on automated machines means that manufacturers are vulnerable to technology failures. This can result in costly downtime, production delays, and lower product quality.
- Employee displacement: Automation can lead to job loss, as the technology can replace some manual labor jobs. This can have significant social and economic consequences, especially in regions where manufacturing jobs are scarce.
- Quality control issues: Automated machines can increase production speed, but this speed can come at the expense of product quality. Manufacturers must ensure that the automated machines are producing high-quality products that meet consumer expectations.
- Cybersecurity concerns: As automation becomes more prevalent in food manufacturing, there is a growing risk of cyber attacks on automated systems. These attacks can lead to production delays, data theft, and even equipment damage.
- Integration with existing systems: Integrating automated systems with existing production processes can be challenging. Manufacturers must ensure that the automation systems work seamlessly with existing software and hardware to avoid production delays.
- Training and skill requirements: Automated systems require specialized training and skill sets. Manufacturers must invest in employee training to ensure they can operate and maintain the automated machinery.
- Regulatory compliance: The use of automation in food manufacturing is subject to various regulatory requirements, including food safety regulations. Manufacturers must ensure that their automated systems meet these requirements to avoid costly fines and legal penalties.
Future Developments in Automated Food Manufacturing
Artificial Intelligence (AI) and Machine Learning:
Artificial intelligence and machine learning are expected to increase significantly in the future of automated food manufacturing. AI-powered systems can analyze vast amounts of data and make decisions quickly and accurately.
For instance, sensors can detect if a machine is malfunctioning or if there is a problem with the quality of the product. AI can then use this information to make quick decisions on how to address the issue. Machine learning can also help manufacturers optimize processes and reduce waste.
Collaborative Robots:
Collaborative robots, also known as cobots, are designed to work alongside human workers. They can help reduce the risk of injury to workers by performing dangerous tasks. Cobots can also increase efficiency and speed in the manufacturing process. They are highly adaptable and can be programmed to perform a range of tasks, making them ideal for food manufacturing.
3D Printing:
3D printing is becoming more common in the food industry, and it has the potential to revolutionize food manufacturing. 3D printers can create complex shapes and textures that would be difficult to achieve using traditional manufacturing methods.
For example, 3D printing can be used to create customized chocolate shapes or unique pasta shapes.
Blockchain:
Blockchain technology is expected to have a significant impact on food manufacturing in the future. Blockchain can be used to create a secure and transparent supply chain.
This technology can help track products from the farm to the consumer, ensuring that food is safe, high quality, and ethically sourced. It can also help reduce waste by optimizing the supply chain and minimizing the risk of food recalls.
Internet of Things (IoT):
The Internet of Things (IoT) involves connecting devices and systems to the internet, allowing them to communicate with each other. IoT can help automate processes in food manufacturing by enabling machines to communicate with each other and with other systems.
For example, IoT can be used to monitor the temperature of food during transport and storage, ensuring that it is kept at the optimal temperature.
Virtual and Augmented Reality:
Virtual and augmented reality technology can be used to train workers and improve quality control. For instance, virtual reality can be used to simulate a manufacturing environment, allowing workers to practice their skills in a safe and controlled setting.
Augmented reality can be used to identify defects in products, allowing workers to make quick and accurate decisions on how to address the issue.
How AI Improves Manufacturing Systems
From automating routine tasks to enabling predictive analytics, AI enhances every stage of the production cycle. It analyzes real-time data to forecast demand, optimize inventory levels, and reduce machine downtime through predictive maintenance. This leads to smoother operations and fewer disruptions.
AI plays a key role in this transformation by integrating AI with manufacturing workflows—allowing businesses to gain deep insights into their supply chain, automate production planning, and fine-tune resource allocation.
How Deskera Can Assist You?
Deskera MRP allows you to closely monitor the manufacturing process. From the bill of materials to the production planning features, the solution helps you stay on top of your game and keep your company's competitive edge.
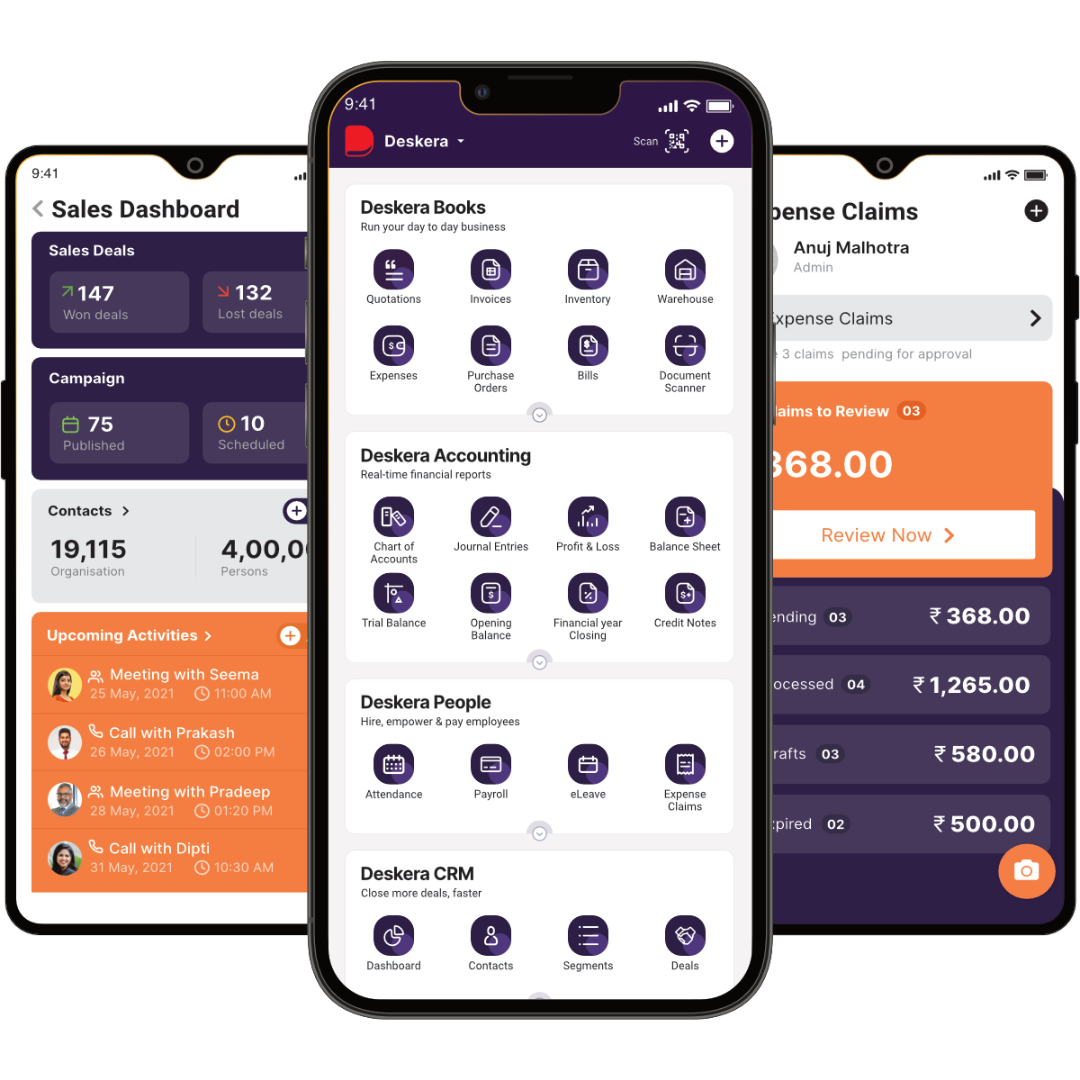
Deskera ERP and MRP system can help you:
- Manage production plans
- Maintain Bill of Materials
- Generate detailed reports
- Create a custom dashboard
Deskera ERP is a comprehensive system that allows you to maintain inventory, manage suppliers, and track supply chain activity in real-time, as well as streamline a variety of other corporate operations.
Deskera Books enables you to manage your accounts and finances more effectively. Maintain sound accounting practices by automating accounting operations such as billing, invoicing, and payment processing.
Deskera CRM is a strong solution that manages your sales and assists you in closing agreements quickly. It not only allows you to do critical duties such as lead generation via email, but it also provides you with a comprehensive view of your sales funnel.
Deskera People is a simple tool for taking control of your human resource management functions. The technology not only speeds up payroll processing but also allows you to manage all other activities such as overtime, benefits, bonuses, training programs, and much more. This is your chance to grow your business, increase earnings, and improve the efficiency of the entire production process.
Key Takeaways
- Automation is increasingly being used in food manufacturing to streamline processes and improve efficiency.
- Automation can be used to carry out repetitive tasks, reduce waste, and minimize the risk of contamination.
- Automated systems can also provide real-time data, allowing manufacturers to monitor and adjust production processes as needed.
- The use of automation in food manufacturing can improve product consistency and reduce errors.
- Advanced robotics and machine learning are being utilized in food manufacturing to enhance accuracy and productivity.
- Automated inspection and quality control systems can help to detect defects and ensure products meet safety and quality standards.
- Automation can also reduce labor costs and increase overall profitability for food manufacturers.
- Collaborative robots or cobots are becoming increasingly popular in food manufacturing as they can work alongside humans and assist in tasks that require precision.
- Automated storage and retrieval systems can optimize inventory management and improve supply chain efficiency.
- Automation can help food manufacturers to comply with increasingly strict regulations and safety standards.
- The role of automation in food manufacturing processes is becoming increasingly crucial for the industry to remain competitive and meet consumer demands. Automation can improve productivity, efficiency, and quality while reducing labor costs and errors.
- Several different types of automation technologies can be implemented, ranging from simple sensors and conveyor systems to more advanced robots and artificial intelligence. However, it is crucial to consider the costs and benefits of implementing automation and address potential challenges such as job displacement and safety concerns.
- Furthermore, it is essential to recognize that automation should not replace human labor entirely but rather be used as a tool to enhance human capabilities and create safer, more fulfilling work environments.
- Overall, automation has the potential to revolutionize the food manufacturing industry and help address current challenges while improving sustainability and meet evolving consumer demands.
Related Articles
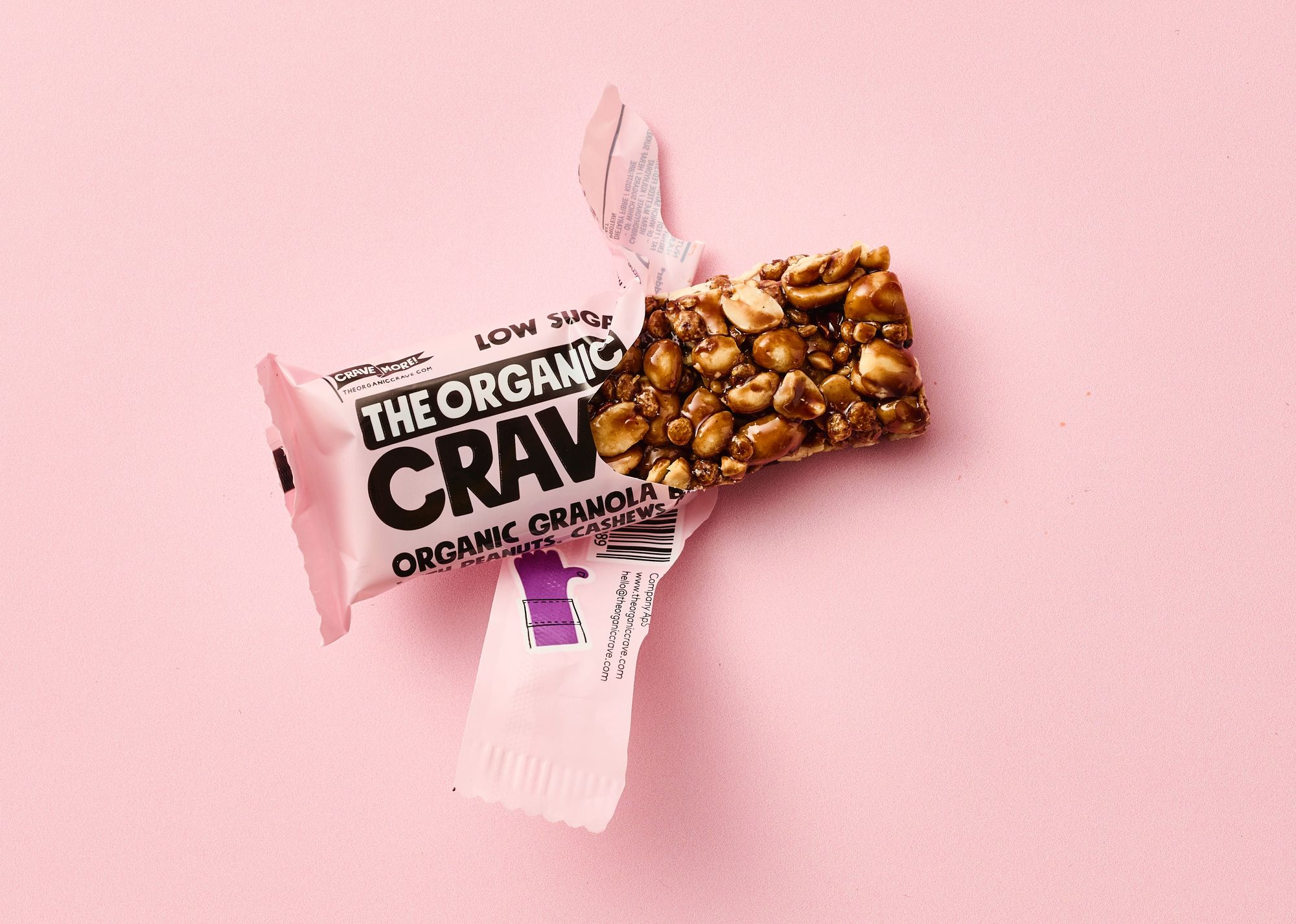
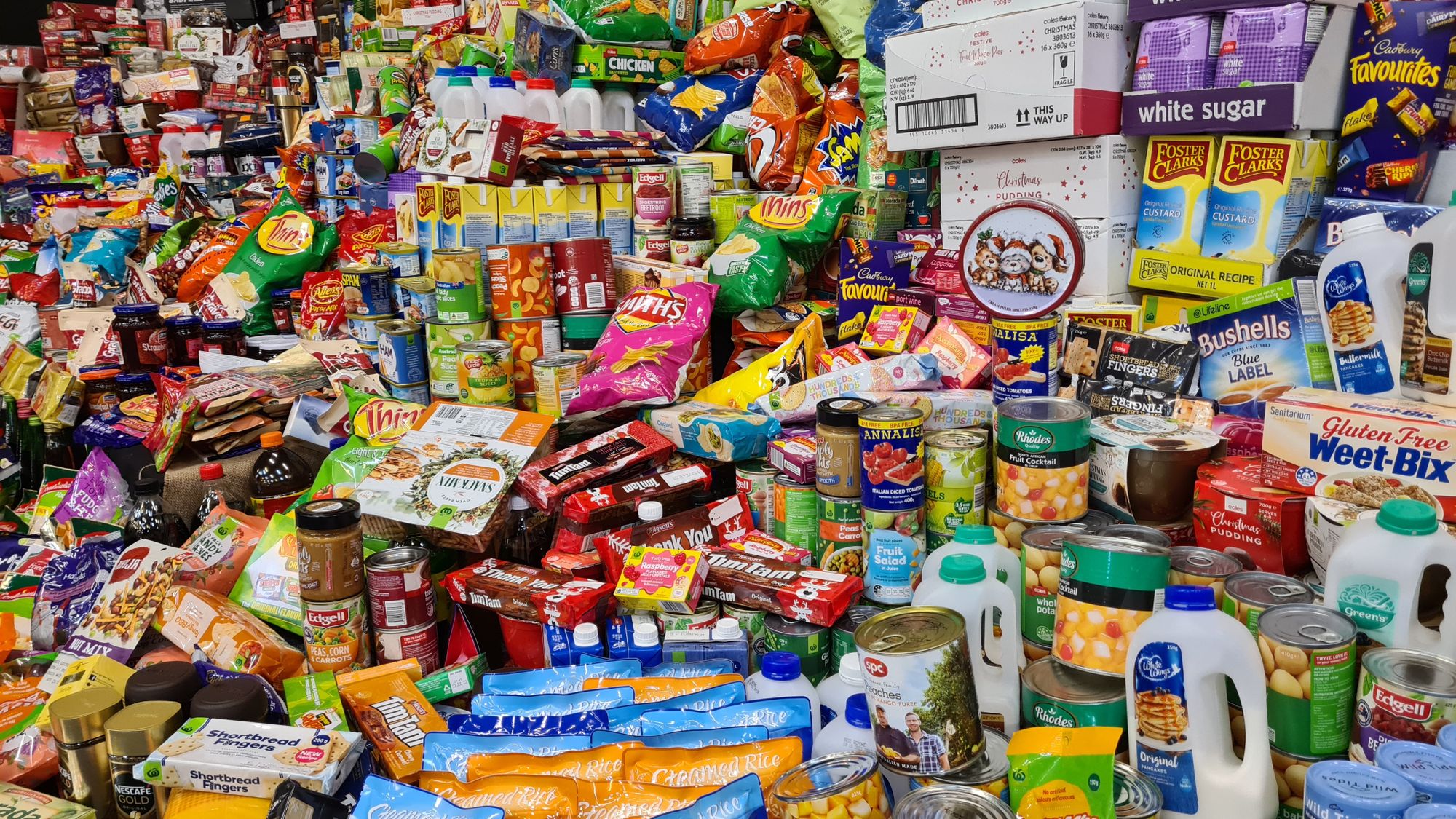
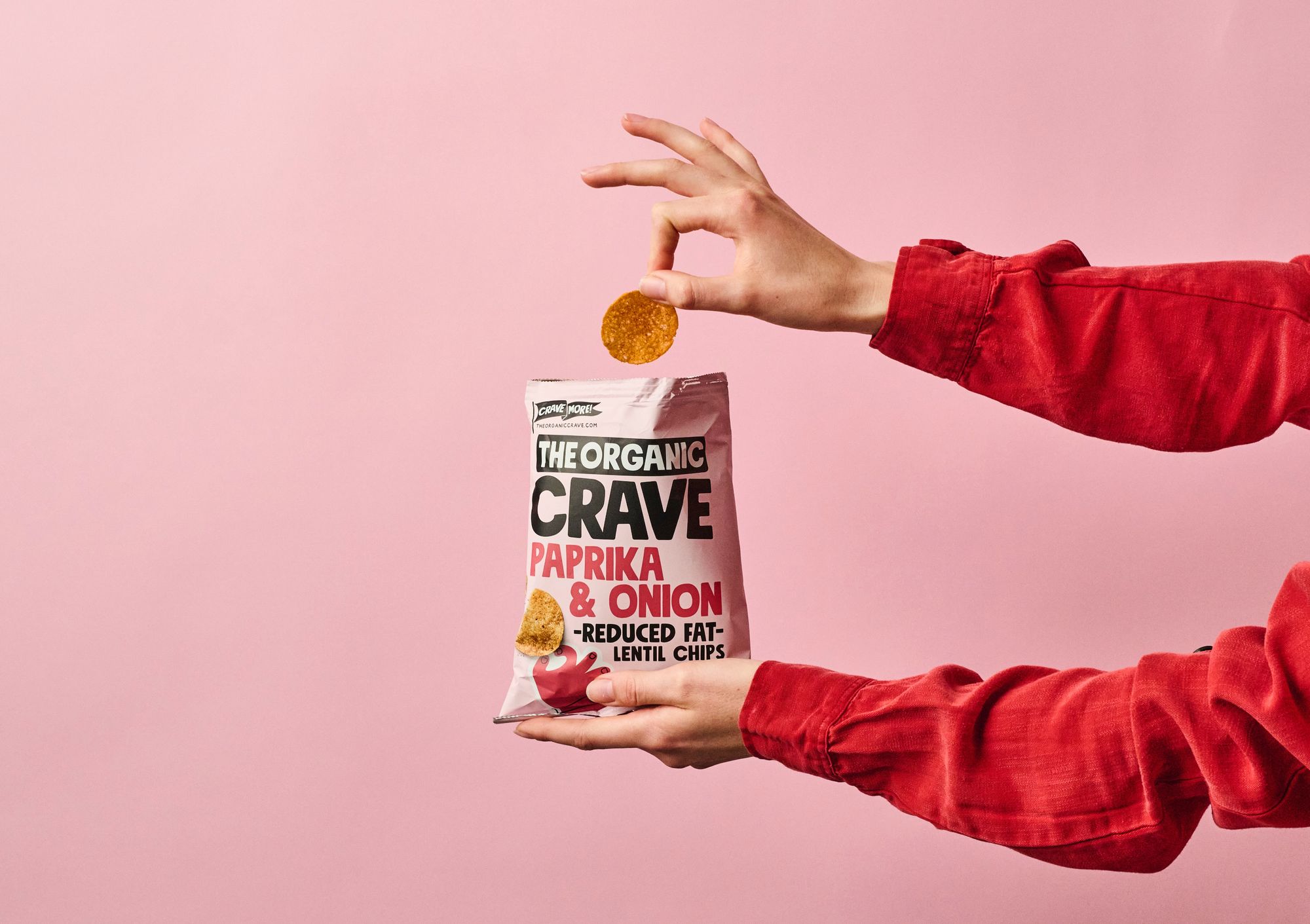
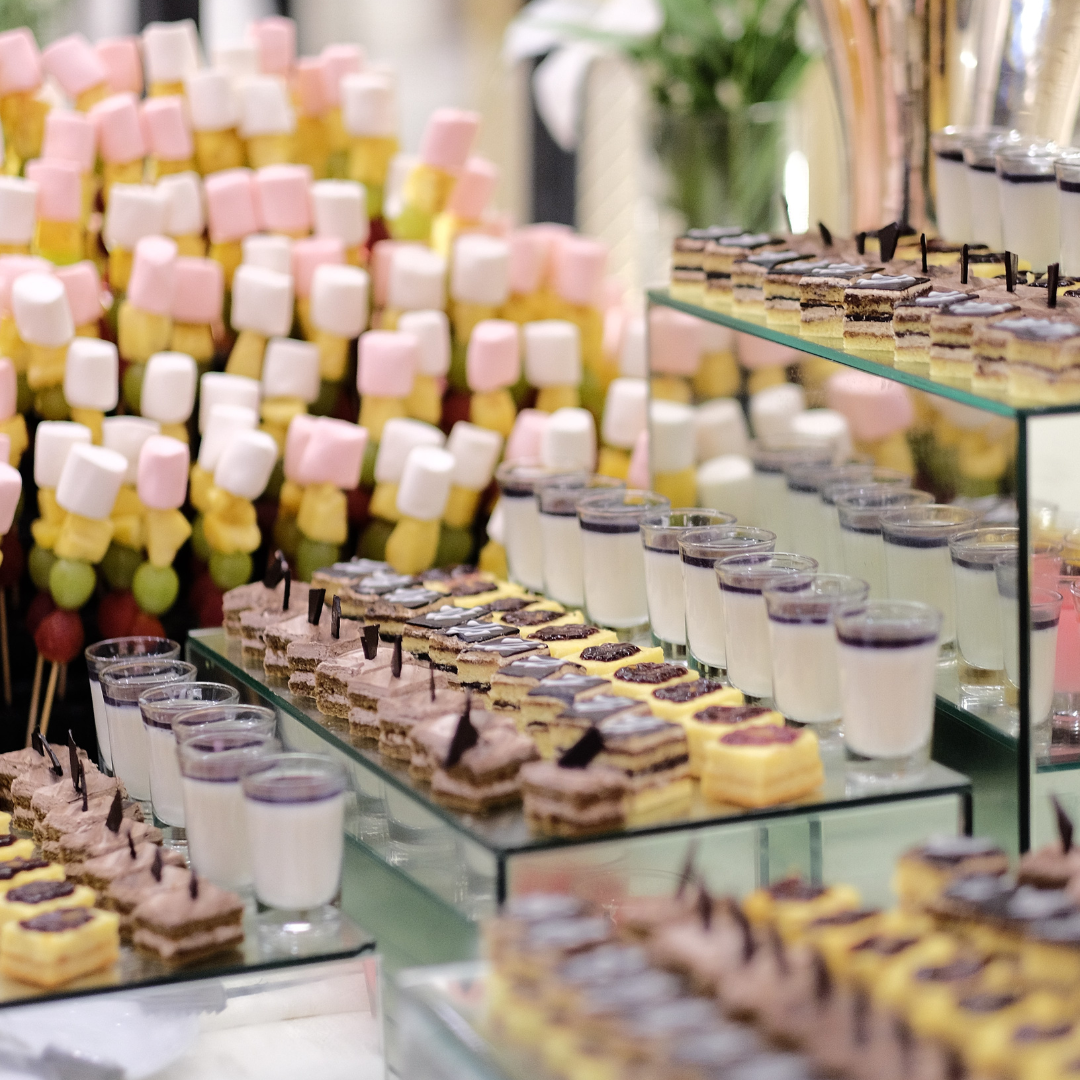