A 2021 survey of furniture manufacturers and retailers found that 60% of respondents said they plan to increase their outsourcing of furniture production in the next 12 months, citing cost savings and increased flexibility as the main reasons for outsourcing. (Source: Furniture Today)
In 2021, the global market for furniture outsourcing was valued at $135.5 billion and was projected to reach $219.5 billion by 2028, growing at a CAGR of 6.4% from 2021 to 2028. (Source: Grand View Research)
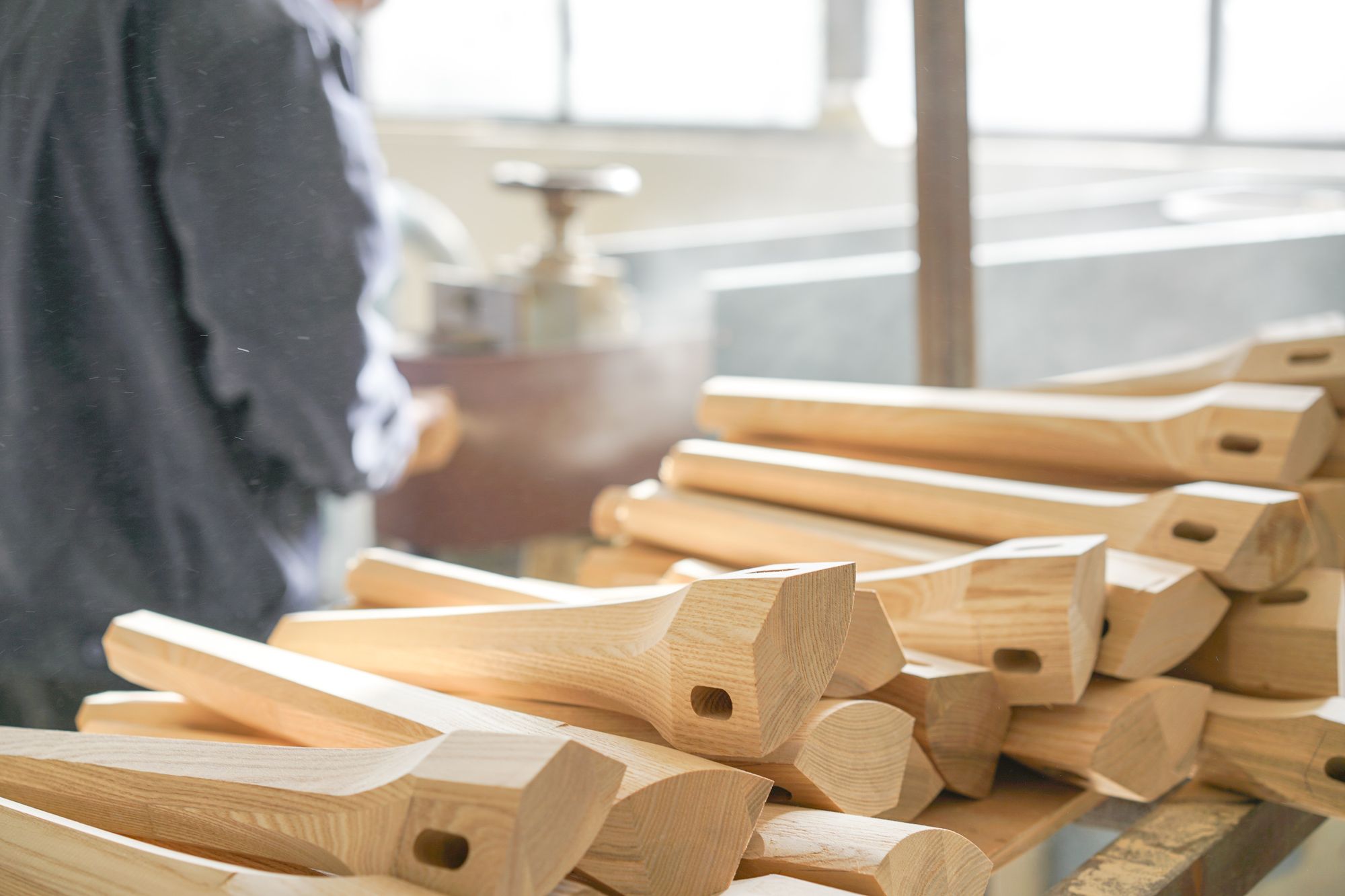
Outsourcing furniture manufacturing has become increasingly popular in recent years as more and more businesses look for ways to reduce costs, improve efficiency, and focus on core competencies.
By outsourcing furniture production, companies can take advantage of a range of benefits, including access to lower labor costs, specialized expertise, and increased flexibility in manufacturing operations.
This can allow companies to improve their bottom line, streamline their supply chains, and ultimately deliver better products to customers. In this context, it's no surprise that outsourcing has become an important strategy for furniture manufacturers and retailers alike.
This article will be your complete guide to outsourcing your furniture manufacturing and the benefits associated with the same by covering the following topics:
- What is Furniture Manufacturing?
- What is Outsource Manufacturing?
- What is Outsourcing in Furniture Manufacturing?
- What are the Benefits of Outsourcing Your Furniture Manufacturing?
- What are the Challenges Associated with Outsourcing Your Furniture Manufacturing?
- How Can You Find a Reliable Furniture Manufacturer to Outsource Your Production to?
- How Can You Ensure Quality Control when Outsourcing Furniture Manufacturing?
- How to Assess if Outsourcing Your Furniture Manufacturing is the Right Choice for You?
- What Intellectual Property Protections Should You Put in Place when Outsourcing Furniture Manufacturing?
- How to Measure the Success of Outsourcing Furniture Manufacturing?
- FAQs related to Outsourcing Furniture Manufacturing
- How can Deskera Help You with Furniture Manufacturing?
- Key Takeaways
- Related Articles
What is Furniture Manufacturing?
Furniture manufacturing is the process of designing, creating, and producing furniture pieces for residential, commercial, and institutional use. The manufacturing process includes various steps such as design, material selection, cutting, shaping, joining, finishing, and packaging.
Furniture can be made from a variety of materials, including wood, metal, plastic, and composite materials. The manufacturing process also includes the use of various tools and machines such as saws, drills, lathes, routers, and sanders, as well as specialized equipment for finishing and upholstery.
Furniture manufacturing involves a range of specialized skills, including design, woodworking, metalworking, and upholstery. Skilled craftsmen and women work to create functional and aesthetically pleasing furniture pieces that meet the needs and preferences of consumers.
The industry includes both large-scale mass production facilities as well as smaller artisanal workshops that specialize in custom furniture pieces.
What is Outsource Manufacturing?
Outsourced manufacturing refers to the practice of hiring an external company or third-party supplier to produce goods or components that are normally produced in-house. Outsourcing manufacturing allows companies to benefit from cost savings, access specialized expertise and equipment, and focus on core business functions.
Outsourced manufacturing can take many forms, including domestic outsourcing, where production is outsourced to a company in the same country, or offshore outsourcing, where production is outsourced to a company in another country with lower labor costs.
In outsourcing manufacturing, the company that outsources its production retains control over the design, engineering, and quality control processes, while the outsourcing partner handles the production process.
This can help companies reduce overhead costs associated with maintaining a large manufacturing operation and allows them to focus on research and development, marketing, and other core business functions.
Outsourced manufacturing is common in industries such as electronics, aerospace, and automotive, where complex components and assemblies are produced.
However, outsourcing manufacturing can also present challenges, such as quality control issues, intellectual property concerns, and cultural and language barriers.
Therefore, it is important for companies to carefully evaluate potential outsourcing partners and establish clear communication and quality control processes.
What is Outsourcing in Furniture Manufacturing?
Outsourcing in furniture manufacturing refers to the practice of hiring an external company or supplier to produce furniture components or finished products that would otherwise be produced in-house.
Furniture companies may outsource different parts of their manufacturing process, such as cutting and shaping wood, upholstering fabrics, or producing metal frames.
Outsourcing in furniture manufacturing can provide several benefits, such as cost savings, access to specialized expertise and equipment, and increased flexibility in production.
For example, a furniture company may outsource the production of a specific component to a supplier who specializes in that particular process, reducing the need to invest in expensive machinery and training.
Outsourcing in furniture manufacturing can also allow companies to focus on other important aspects of their business, such as design, marketing, and distribution.
This can be particularly useful for small to medium-sized furniture companies that may not have the resources to invest in large-scale manufacturing operations.
However, outsourcing in furniture manufacturing can also present some challenges.
For example, maintaining consistent quality control standards across multiple suppliers can be difficult, as can ensuring that suppliers adhere to production schedules and deadlines.
Additionally, intellectual property concerns can arise when outsourcing production to a third party.
Overall, outsourcing in furniture manufacturing can be a valuable strategy for companies looking to reduce costs and increase flexibility, but it is important to carefully evaluate potential suppliers and establish clear communication and quality control processes to ensure successful partnerships.
What are the Benefits of Outsourcing Your Furniture Manufacturing?
Outsourcing furniture manufacturing can provide several benefits, including:
Cost Savings
Cost savings is one of the primary benefits of outsourcing furniture manufacturing. By outsourcing, furniture companies can reduce the need to invest in expensive equipment, facilities, and skilled labor. Additionally, outsourcing to countries with lower labor costs can result in significant cost savings.
Here are some specific ways that outsourcing furniture manufacturing can result in cost savings:
- Lower Labor Costs: One of the most significant cost savings from outsourcing furniture manufacturing is the lower labor costs. Many countries have lower labor costs than the United States, which can result in significant cost savings for furniture companies.
- Reduced Overhead Costs: Outsourcing can also reduce overhead costs associated with maintaining a large manufacturing operation, such as rent or mortgage payments, utilities, insurance, and maintenance costs.
- Reduced Capital Investment: By outsourcing furniture manufacturing, companies can avoid the need to purchase expensive equipment and machinery, as well as to hire and train skilled labor. This can result in significant savings in capital investment.
- Economies of Scale: Third-party suppliers who specialize in furniture manufacturing often have economies of scale, which can result in lower costs for raw materials and other supplies. This can translate into cost savings for furniture companies that outsource their production.
- Reduced Risk: Outsourcing can also reduce the risk for furniture companies by minimizing exposure to market fluctuations and reducing the need to maintain a large inventory of raw materials and finished goods.
Overall, outsourcing furniture manufacturing can result in significant cost savings for companies, but it is important to carefully evaluate potential suppliers and establish clear communication and quality control processes to ensure successful partnerships.
Access to Specialized Expertise
Access to specialized expertise is another benefit of outsourcing furniture manufacturing. By outsourcing to third-party suppliers who specialize in specific areas of furniture production, furniture companies can tap into advanced skills, technology, or equipment that may be difficult or expensive to acquire in-house.
This can result in several benefits, including:
- Advanced Technology: Third-party suppliers who specialize in furniture manufacturing may have access to more advanced technology and equipment than a furniture company could afford to purchase on their own. This can result in more efficient and effective production processes, higher quality products, and greater overall productivity.
- Specialized Skills: Furniture companies can benefit from the specialized skills of third-party suppliers who have experience in specific areas of furniture production, such as upholstery or metalworking. This can result in higher quality products and more efficient production processes.
- Process Improvement: Third-party suppliers who specialize in furniture manufacturing may have more experience and expertise in process improvement and optimization than a furniture company could afford to dedicate in-house. This can result in more efficient and effective production processes and reduced costs.
- Innovation: By outsourcing furniture manufacturing, companies can tap into the expertise of suppliers who have experience in a wide range of furniture products and processes. This can lead to continuous innovation and differentiation of products, which can help to increase market share and profitability.
Overall, outsourcing furniture manufacturing can provide furniture companies with access to specialized expertise that can result in higher quality products, more efficient production processes, and increased innovation.
It is important to carefully evaluate potential suppliers and establish clear communication and quality control processes to ensure successful partnerships.
Increased Flexibility
Increased flexibility is another benefit of outsourcing furniture manufacturing. By outsourcing, furniture companies can increase their production capacity quickly and efficiently to meet changing market demands. This can be particularly useful for seasonal or short-term orders that require rapid scaling of production.
Here are some ways that outsourcing can increase flexibility:
- Scalability: Third-party suppliers who specialize in furniture manufacturing can quickly scale production up or down as needed, allowing furniture companies to meet fluctuating demand without the need for large capital investments.
- Customization: Outsourcing can allow furniture companies to offer customized products without the need to invest in specialized equipment or training. Third-party suppliers can often accommodate customization requests more quickly and efficiently than a furniture company could in-house.
- Faster Time to Market: Outsourcing furniture manufacturing can help furniture companies get products to market faster by reducing lead times and improving production efficiency. This can result in increased market share and gross profits.
- Risk Mitigation: Outsourcing can also help furniture companies mitigate risk by reducing the need to maintain large inventories of finished products or raw materials. This can reduce the risk of excess inventory and associated costs.
Overall, outsourcing furniture manufacturing can provide furniture companies with increased flexibility to meet changing market demands, reduce risk, and improve time to market.
It is important to carefully evaluate potential suppliers and establish clear communication and quality control processes to ensure successful partnerships.
Focus on Core Business Functions
Focusing on core business functions is another benefit of outsourcing furniture manufacturing. By outsourcing non-core functions, such as manufacturing, furniture companies can free up resources to focus on their core competencies, such as product design, marketing, and sales.
Here are some ways that outsourcing can help furniture companies focus on core business functions:
- Resource Allocation: By outsourcing manufacturing, furniture companies can free up resources, such as labor, capital, and time, to focus on core business functions. This can result in more efficient operations and improved profitability.
- Expertise: By partnering with third-party suppliers who specialize in furniture manufacturing, furniture companies can tap into expertise and experience that they may not have in-house. This can result in higher quality products and more efficient production processes.
- Cost Savings: Outsourcing furniture manufacturing can also result in cost savings, which can be reinvested in core business functions. For example, by reducing labor and overhead costs associated with manufacturing, furniture companies can invest more in product design or marketing.
- Competitive Advantage: By focusing on core business functions, furniture companies can differentiate themselves from competitors and create a competitive advantage. By partnering with third-party suppliers who specialize in manufacturing, furniture companies can produce higher-quality products more efficiently and gain a competitive edge in the market.
Overall, outsourcing furniture manufacturing can provide furniture companies with the resources, expertise, and cost savings necessary to focus on core business functions and gain a competitive advantage.
It is important to carefully evaluate potential suppliers and establish clear communication and quality control processes to ensure successful partnerships.
Improved Quality Control
Improved quality control is another benefit of outsourcing furniture manufacturing.
By partnering with third-party suppliers who specialize in furniture manufacturing, furniture companies can tap into expertise and experience that they may not have in-house, resulting in higher-quality products and more efficient production processes.
Here are some ways that outsourcing can improve quality control:
- Expertise: Third-party suppliers who specialize in furniture manufacturing have a wealth of expertise and experience in producing high-quality products. By partnering with these suppliers, furniture companies can benefit from their knowledge of best practices, quality control processes, and industry standards.
- Quality Control Processes: Outsourcing furniture manufacturing can also help furniture companies improve their quality control processes. Third-party suppliers often have robust quality control processes in place, including inspections and testing at various stages of production. This can help ensure that products meet the required quality standards before they are shipped.
- Consistency: Outsourcing can also help ensure consistent product quality. By partnering with third-party suppliers who have established quality control processes in place, furniture companies can ensure that products are manufactured consistently to the same high standards, regardless of location or production run.
- Cost Savings: Improved quality control can also result in cost savings. By reducing the need for rework or product recalls, furniture companies can save money and avoid damage to their brand reputation.
Overall, outsourcing furniture manufacturing can provide furniture companies with the expertise, quality control processes, and consistency necessary to improve product quality and avoid costly errors.
It is important to carefully evaluate potential suppliers and establish clear communication and quality control processes to ensure successful partnerships.
Faster Time to Market
Faster time to market is another benefit of outsourcing furniture manufacturing. By partnering with third-party suppliers who specialize in furniture manufacturing, furniture companies can benefit from their expertise and production capacity to accelerate the product development process.
Here are some ways that outsourcing can help furniture companies get products to market faster:
- Reduced Lead Times: Outsourcing furniture manufacturing can help reduce lead times by streamlining the production process and improving supply chain management. This can result in faster turnaround times for product development and delivery.
- Production Efficiency: Third-party suppliers who specialize in furniture manufacturing often have established production processes and a skilled workforce that can manufacture products more efficiently. This can help reduce production time and improve overall speed to market.
- Design and Prototyping: Outsourcing can also help furniture companies accelerate the design and prototyping process. Third-party suppliers can provide design expertise and resources to create prototypes quickly, allowing furniture companies to test and refine their products before full-scale production.
- Market Research: Outsourcing can also help furniture companies conduct market research more efficiently. Third-party suppliers can provide insights into market trends and customer preferences, helping furniture companies develop products that meet customer needs and preferences.
By outsourcing furniture manufacturing, furniture companies can take advantage of the expertise and resources of third-party suppliers to accelerate the product development process and get products to market faster. This can help furniture companies gain a competitive advantage in the market and increase revenue.
Risk Mitigation
Risk mitigation is another benefit of outsourcing furniture manufacturing. Here are some ways that outsourcing can help furniture companies mitigate risks:
- Reduced Inventory Risk: By outsourcing furniture manufacturing, furniture companies can reduce the risk of maintaining large inventories of finished products or raw materials. This can help reduce the risk of excess inventory and associated costs, such as storage and obsolescence.
- Reduced Capital Investment: Outsourcing can also help furniture companies reduce the need for large capital investments in manufacturing equipment and facilities. This can help reduce the risk of over-investing in manufacturing capacity, which can be costly and difficult to recover if demand falls.
- Supply Chain Diversification: Outsourcing furniture manufacturing to multiple suppliers can help furniture companies diversify their supply chain and reduce the risk of disruptions caused by a single supplier. This can help ensure the continuity of supply and reduce the risk of product shortages or delays.
- Quality Control: Outsourcing can also help furniture companies improve their quality control processes by partnering with third-party suppliers who have established quality control processes in place. This can help reduce the risk of quality issues that can damage the company's reputation or result in costly recalls.
By outsourcing furniture manufacturing, furniture companies can reduce their exposure to various risks associated with manufacturing, inventory management, and supply chain disruptions. This can help ensure continuity of supply, reduce costs, and protect the company's reputation.
Scalability
Scalability is another benefit of outsourcing furniture manufacturing. Here are some ways that outsourcing can help furniture companies scale their production capacity:
- Production Flexibility: Third-party suppliers who specialize in furniture manufacturing can quickly scale production up or down as needed, allowing furniture companies to meet fluctuating demand without the need for large capital investments. This can help furniture companies avoid the risk of over-investing in manufacturing capacity during periods of high demand while still being able to meet customer needs.
- Rapid Prototyping: Outsourcing can also help furniture companies scale their product development process by leveraging the expertise and resources of third-party suppliers. These suppliers can provide design expertise and resources to create prototypes quickly, allowing furniture companies to test and refine their products before full-scale production.
- Access to Specialized Equipment: Third-party suppliers who specialize in furniture manufacturing often have access to specialized equipment and resources that can be expensive or difficult for furniture companies to acquire and maintain in-house. By outsourcing furniture manufacturing, furniture companies can tap into these resources to scale production capacity quickly and efficiently.
- Reduced Labor Costs: Outsourcing furniture manufacturing can also help furniture companies reduce labor costs by leveraging the expertise and experience of third-party suppliers who have established production processes in place. This can help reduce the need for expensive in-house staff, allowing furniture companies to focus on their core competencies.
By outsourcing furniture manufacturing, furniture companies can access the resources and expertise of third-party suppliers to scale their production capacity quickly and efficiently. This can help furniture companies meet fluctuating demand, reduce costs, and gain a competitive advantage in the market.
What are the Challenges Associated with Outsourcing Your Furniture Manufacturing?
While outsourcing furniture manufacturing can provide many benefits, there are also some challenges that companies may face. Here are some of the main challenges associated with outsourcing furniture manufacturing:
- Quality Control: Ensuring consistent quality across multiple suppliers can be challenging. Furniture companies must establish clear quality standards and ensure that third-party suppliers adhere to these standards. Failure to maintain quality control can result in costly recalls, damage to the company's reputation, and loss of customers.
- Communication: Effective communication is critical to successful outsourcing. Furniture companies must communicate their needs and expectations clearly to third-party suppliers, while also being receptive to feedback and suggestions. Language barriers and cultural differences can also pose challenges to effective communication.
- Supply Chain Management: Outsourcing furniture manufacturing can add complexity to the supply chain, making it more challenging to manage. Furniture companies must ensure that they have systems and processes in place to manage inventory, track shipments, and manage logistics across multiple suppliers.
- Intellectual Property Protection: Outsourcing furniture manufacturing can also pose a risk to intellectual property. Furniture companies must ensure that they have clear agreements in place with third-party suppliers to protect their designs and proprietary information.
- Coordination: Coordinating production across multiple suppliers can be challenging, particularly when suppliers are located in different countries and time zones. Furniture companies must establish clear processes and protocols for managing production and ensuring that suppliers meet production schedules and deadlines.
Overall, while outsourcing furniture manufacturing can provide many benefits, it is not without its challenges. Furniture companies must carefully weigh the benefits and risks of outsourcing and establish clear processes and protocols for managing production and ensuring quality control across multiple suppliers.
How Can You Find a Reliable Furniture Manufacturer to Outsource Your Production to?
To find a reliable furniture manufacturer to outsource your production to, here are some steps you can take:
- Research: Start by researching potential furniture manufacturers online. Look for manufacturers with experience in your specific product category and the necessary capabilities to meet your production requirements.
- Referrals: Ask for referrals from other businesses or industry contacts who have outsourced their furniture manufacturing. This can help you get recommendations from people who have first-hand experience working with furniture manufacturers.
- Qualification process: Develop a qualification process that includes a detailed questionnaire, on-site visits, and reference checks. This process can help you screen potential manufacturers and select the best fit for your needs.
- Request for proposal (RFP): Send out an RFP to your shortlisted manufacturers. This should include detailed specifications, production requirements, delivery schedules, quality standards, and other important details.
- Samples and prototypes: Request samples or prototypes from your shortlisted manufacturers. This can help you evaluate their product quality, production capabilities, and adherence to your specifications.
- Contract negotiation: Once you have selected a manufacturer, negotiate a contract that outlines the scope of work, pricing, delivery schedule, quality standards, and other important terms and conditions.
- Regular communication: Establish regular communication with your outsourced manufacturer to ensure that your production requirements are being met and any issues are addressed in a timely manner.
By following these steps, you can find a reliable furniture manufacturer that can meet your production requirements and help you achieve your outsourcing goals.
How Can You Ensure Quality Control when Outsourcing Furniture Manufacturing?
Ensuring quality control when outsourcing furniture manufacturing is crucial to ensure that the final products meet your standards and specifications. Here are some steps you can take to ensure quality control:
- Define quality standards: Clearly define your quality standards and specifications for the outsourced furniture products. This can include product design, materials, finish, dimensions, and packaging.
- Develop a quality control plan: Develop a detailed quality control plan that outlines the inspection process, testing requirements, acceptance criteria, and sampling procedures.
- Conduct factory audits: Conduct factory audits to ensure that your outsourced manufacturer has the necessary quality control systems in place. This can include reviewing their production processes, quality control procedures, and testing equipment.
- Perform inspections and testing: Conduct inspections and testing at various stages of production to ensure that the products meet your quality standards. This can include material inspections, in-process inspections, and final inspections.
- Corrective actions: Establish procedures for addressing quality issues and taking corrective actions. This can include rework, repair, or rejection of defective products.
- Regular monitoring: Regularly monitor the quality of outsourced furniture products to ensure that your manufacturer is consistently meeting your quality standards.
- Communication: Maintain regular communication with your outsourced manufacturer to ensure that any quality issues are addressed in a timely manner.
By following these steps, you can ensure that your outsourced furniture products meet your quality standards and specifications.
How to Assess if Outsourcing Your Furniture Manufacturing is the Right Choice for You?
Assessing whether outsourcing furniture manufacturing is the right choice for your company involves careful analysis and consideration of several factors. Here are some steps you can take to assess whether outsourcing is the right choice for your company:
- Analyze Your Production Costs: Start by analyzing your current production costs, including labor, materials, and overhead costs. Compare these costs to the costs of outsourcing furniture manufacturing to third-party suppliers. Consider not only the cost savings but also the potential risks and benefits of outsourcing.
- Evaluate Your Capacity and Capabilities: Assess your current manufacturing capacity and capabilities. Consider whether outsourcing can help you scale up production quickly and efficiently or whether it would be more cost-effective to invest in in-house manufacturing capabilities.
- Research Potential Suppliers: Research potential suppliers to assess their capabilities, experience, and reputation. Look for suppliers who have a track record of delivering high-quality products and who are able to meet your specific needs and requirements.
- Consider Intellectual Property Protection: Consider the risks and challenges associated with protecting your intellectual property when outsourcing manufacturing. Ensure that you have clear agreements in place with suppliers to protect your designs and proprietary information.
- Evaluate the Impact on Your Brand: Consider the impact that outsourcing could have on your brand reputation. Ensure that your suppliers share your commitment to quality and that their practices align with your values and mission.
- Create a Detailed Plan: Develop a detailed plan for outsourcing, including supplier selection, production schedules, quality control measures, and logistics. Ensure that you have the resources and systems in place to manage the outsourcing process effectively.
- Monitor and Evaluate Performance: Continuously monitor and evaluate supplier performance to ensure that they meet your quality standards and production schedules. Establish clear metrics for measuring performance and hold suppliers accountable for meeting these metrics.
By carefully assessing your production costs, capacity, and capabilities and evaluating potential suppliers, you can determine whether outsourcing furniture manufacturing is the right choice for your company. Creating a detailed plan and monitoring supplier performance can help ensure that outsourcing is successful and delivers the expected benefits.
What Intellectual Property Protections Should You Put in Place when Outsourcing Furniture Manufacturing?
When outsourcing furniture manufacturing, it's important to protect your intellectual property (IP) to prevent others from using or stealing your ideas, designs, or innovations. Here are some IP protections you can put in place:
- Non-disclosure agreement (NDA): A non-disclosure agreement is a legal agreement that prohibits the manufacturer from disclosing any confidential information about your business, product designs, or manufacturing processes.
- Intellectual property ownership agreement: This agreement outlines the ownership and use of any intellectual property associated with your product, including patents, trademarks, and copyrights.
- Patents: Consider filing for patents to protect any unique designs, innovations, or processes associated with your furniture product.
- Trademarks: Register trademarks to protect any unique branding, logos, or product names associated with your furniture product.
- Copyrights: Register copyrights to protect any original creative work, such as product manuals, instructions, and marketing materials.
- Monitoring and enforcement: Monitor the market for any infringements of your IP rights and take legal action if necessary.
By putting these protections in place, you can safeguard your intellectual property and prevent others from copying or using your designs or ideas without your permission.
How to Measure the Success of Outsourcing Furniture Manufacturing?
Measuring the success of outsourcing furniture manufacturing can be done by monitoring key performance indicators that can include:
- Cost savings: You can measure the success of outsourcing by tracking the cost savings generated by outsourcing compared to producing in-house. This includes savings in labor costs, raw material costs, and other overhead expenses.
- Production efficiency: Measuring the efficiency of outsourced production can help you determine the effectiveness of your outsourcing strategy. This can include tracking production lead times, turnaround times, and cycle times.
- Quality control: Measuring the quality of outsourced furniture products can help you ensure that your supplier is meeting your quality standards. This can include tracking the number of defects, returns, and complaints.
- Delivery times: Measuring the delivery times of outsourced furniture products can help you ensure that your supplier is meeting your delivery schedule. This can include tracking the number of on-time deliveries and late deliveries.
- Customer satisfaction: Measuring customer satisfaction can help you determine the effectiveness of your outsourcing strategy. This can include tracking customer feedback, reviews, and ratings.
- Return on investment (ROI): Measuring the ROI of outsourcing can help you determine the financial benefits of outsourcing compared to producing in-house.
Overall, monitoring these key performance indicators can help you evaluate the effectiveness of your outsourcing strategy and make data-driven decisions to improve your outsourcing process.
FAQs related to Outsourcing Furniture Manufacturing
- What should I look for in a furniture manufacturing outsourcing partner?
When looking for a furniture manufacturing outsourcing partner, you should look for a partner with a proven track record of delivering high-quality products, a deep understanding of your needs and requirements, and a commitment to customer service.
- How can I manage logistics when outsourcing furniture manufacturing?
You can manage logistics when outsourcing furniture manufacturing by having a clear plan for managing inventory, tracking shipments, and coordinating production schedules across multiple suppliers.
- What are the risks of outsourcing furniture manufacturing?
Risks of outsourcing furniture manufacturing include quality control issues, supply chain disruptions, intellectual property theft, and potential damage to brand reputation.
- How do I manage relationships with third-party furniture manufacturers?
To manage relationships with third-party furniture manufacturers, you should establish clear expectations and communication protocols, develop strong relationships based on trust and mutual benefit, and regularly monitor and evaluate supplier performance.
- How do I ensure that my outsourced furniture products meet my quality standards?
To ensure that your outsourced furniture products meet your quality standards, you should establish clear quality control processes, communicate your expectations clearly to suppliers, and monitor supplier performance regularly.
- How can I ensure that my outsourced furniture products are delivered on time?
To ensure that your outsourced furniture products are delivered on time, you should establish clear production schedules and deadlines, communicate these expectations to suppliers, and monitor supplier performance regularly.
- How do I ensure that my intellectual property is protected when outsourcing furniture manufacturing?
To ensure that your intellectual property is protected when outsourcing furniture manufacturing, you should establish clear agreements with suppliers on the use and protection of confidential information, sign non-disclosure agreements, and establish clear ownership of designs and trademarks.
How can Deskera Help You with Furniture Manufacturing?
Deskera is a cloud-based software solution that offers a range of features to help streamline and optimize the furniture manufacturing process. Here are some ways Deskera MRP can help you with furniture manufacturing:
- Inventory management: Deskera can help you manage your inventory levels and track the movement of raw materials and finished goods in real time.
- Production planning: With Deskera, you can plan and schedule your production process, track progress, and monitor resource utilization to ensure efficient production.
- Quality control: Deskera offers tools to help you manage quality control throughout the manufacturing process, from design to finishing, to ensure that your products meet the required standards.
- Sales and distribution: Deskera can help you manage your sales orders, track customer orders, and manage your distribution channels, allowing you to manage your sales process more efficiently.
- Financial management: With Deskera, you can manage your financial transactions, track expenses, and generate financial reports, giving you greater visibility into your financial performance.
- Business intelligence: Deskera provides advanced analytics and reporting capabilities, allowing you to gain insights into your business performance and make data-driven decisions.
Key Takeaways
Outsourcing furniture manufacturing refers to the practice of hiring third-party manufacturers to produce furniture products instead of producing them in-house. The benefits of outsourcing your furniture manufacturing are:
- Cost savings: Outsourcing furniture manufacturing can result in significant cost savings for furniture companies by reducing labor and overhead costs associated with manufacturing.
- Access to specialized expertise: By partnering with third-party suppliers who specialize in furniture manufacturing, furniture companies can tap into expertise and experience that they may not have in-house, resulting in higher-quality products and more efficient production processes.
- Increased flexibility: Outsourcing can allow furniture companies to increase their production capacity quickly and efficiently to meet changing market demands, such as seasonal or short-term orders.
- Focus on core business functions: By outsourcing non-core functions, such as manufacturing, furniture companies can free up resources to focus on their core competencies, such as product design, marketing, and sales.
- Improved quality control: Outsourcing can help furniture companies improve their quality control processes by partnering with third-party suppliers who have established quality control processes in place.
- Faster time to market: Outsourcing can help furniture companies get products to market faster by reducing lead times and improving production efficiency.
- Risk mitigation: Outsourcing can help furniture companies reduce risk by reducing the need to maintain large inventories of finished products or raw materials, which can reduce the risk of excess inventory and associated costs.
- Scalability: Third-party suppliers who specialize in furniture manufacturing can quickly scale production up or down as needed, allowing furniture companies to meet fluctuating demand without the need for large capital investments.
Overall, outsourcing furniture manufacturing can provide furniture companies with the resources, expertise, and cost savings necessary to focus on core business functions, improve product quality, and gain a competitive advantage in the market.
Lastly, by using Deskera's comprehensive suite of software tools, furniture manufacturers can streamline their operations, improve efficiency, and reduce costs, resulting in better business performance and increased customer satisfaction.
Related Articles
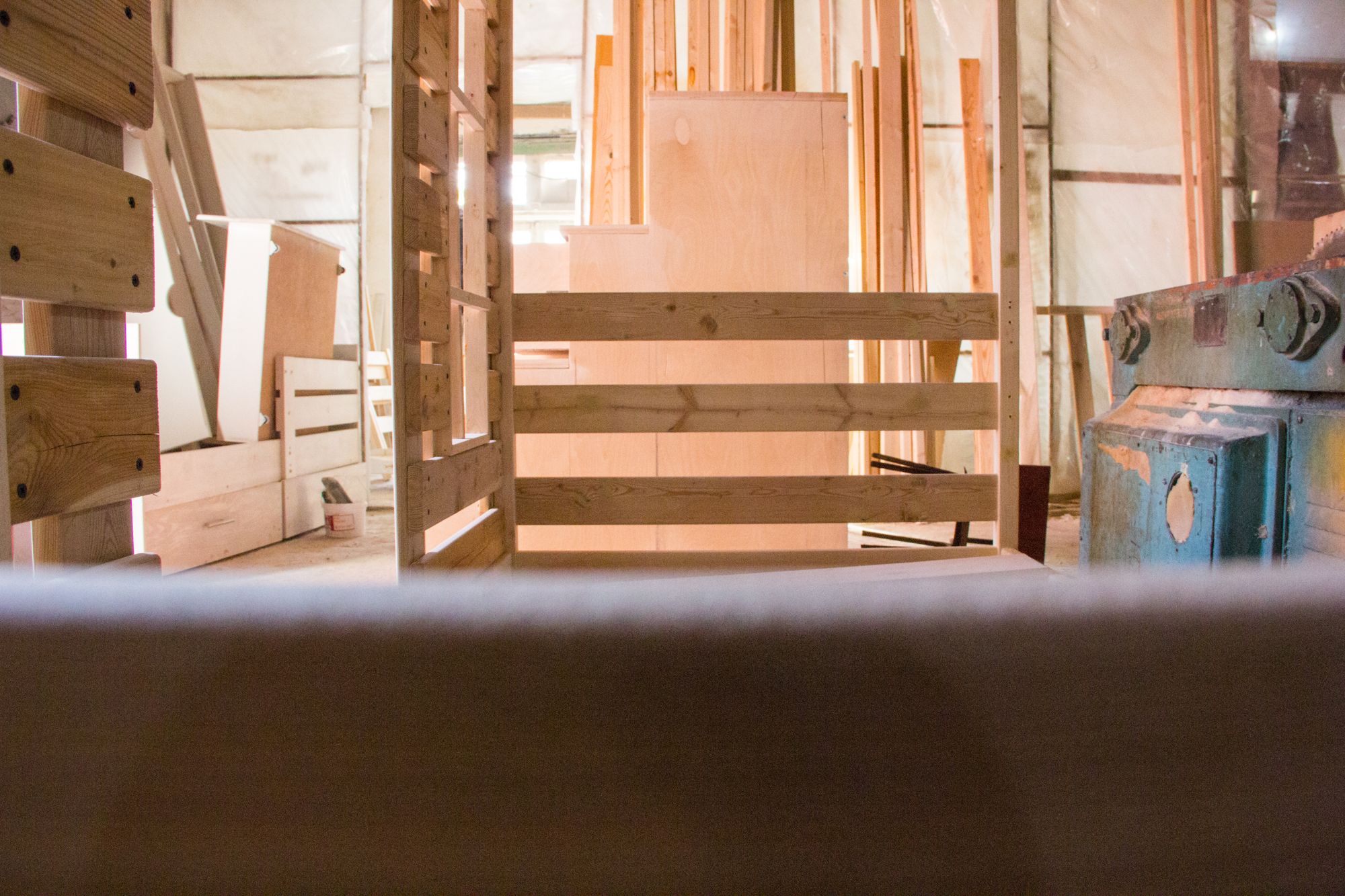
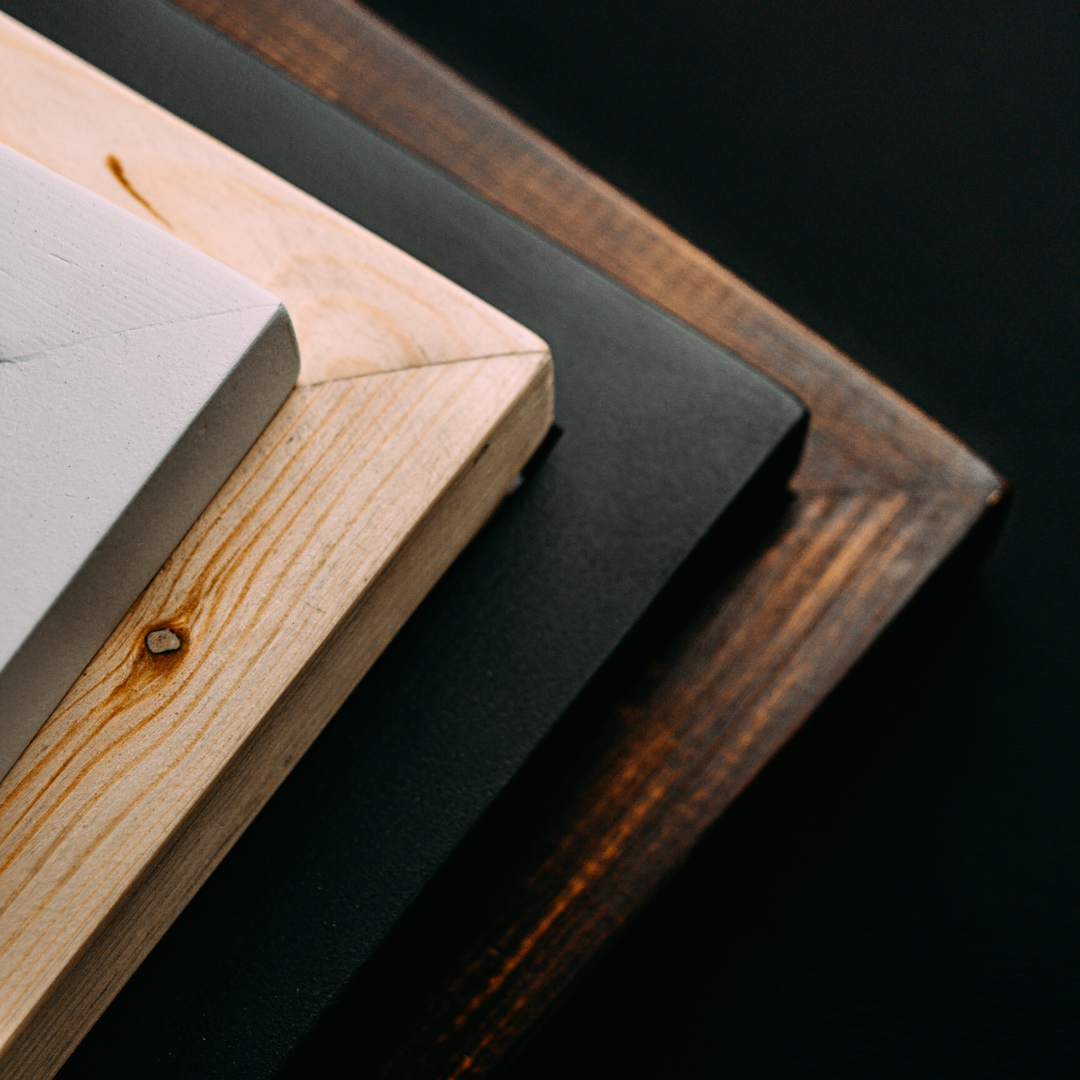
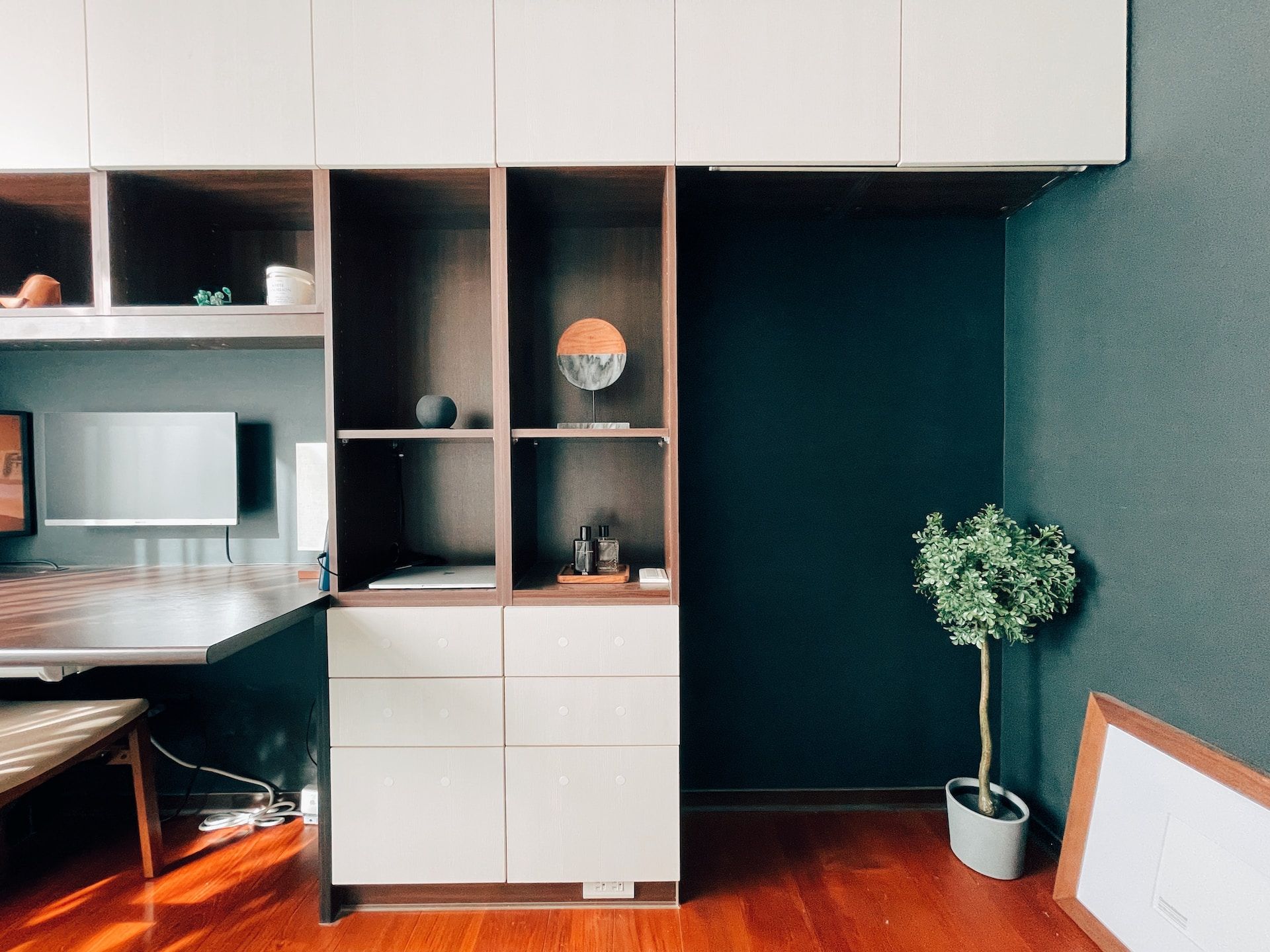
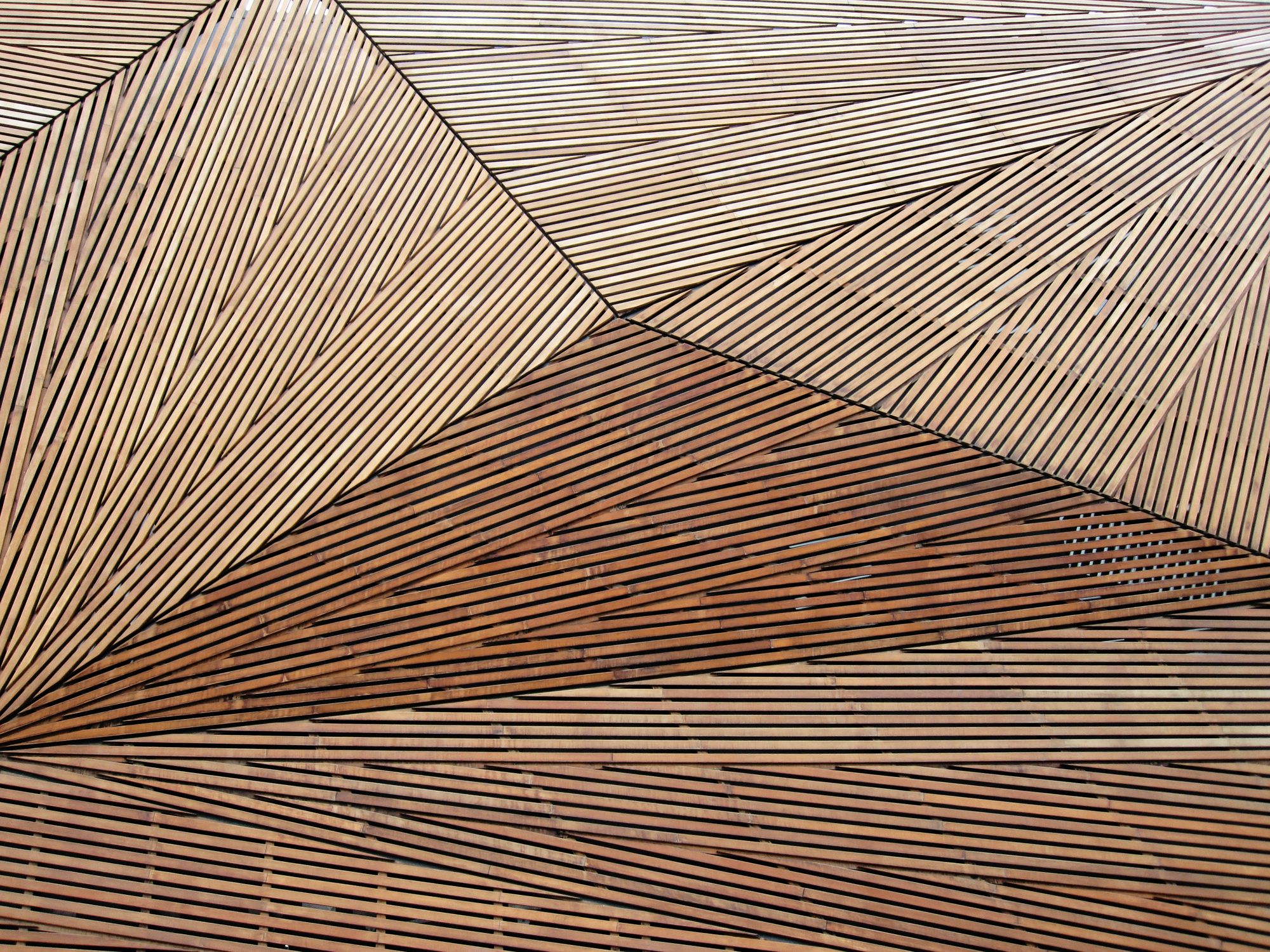
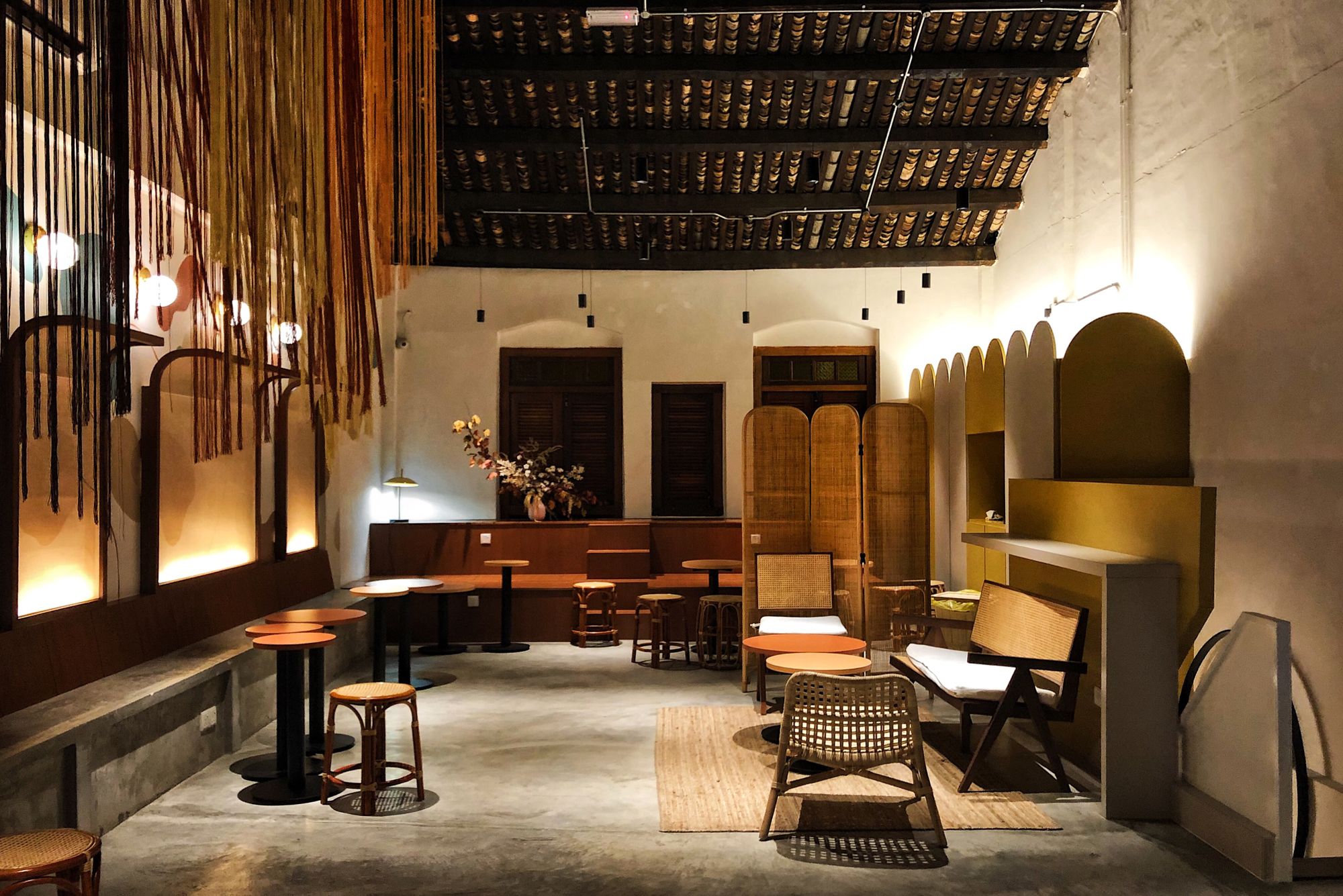
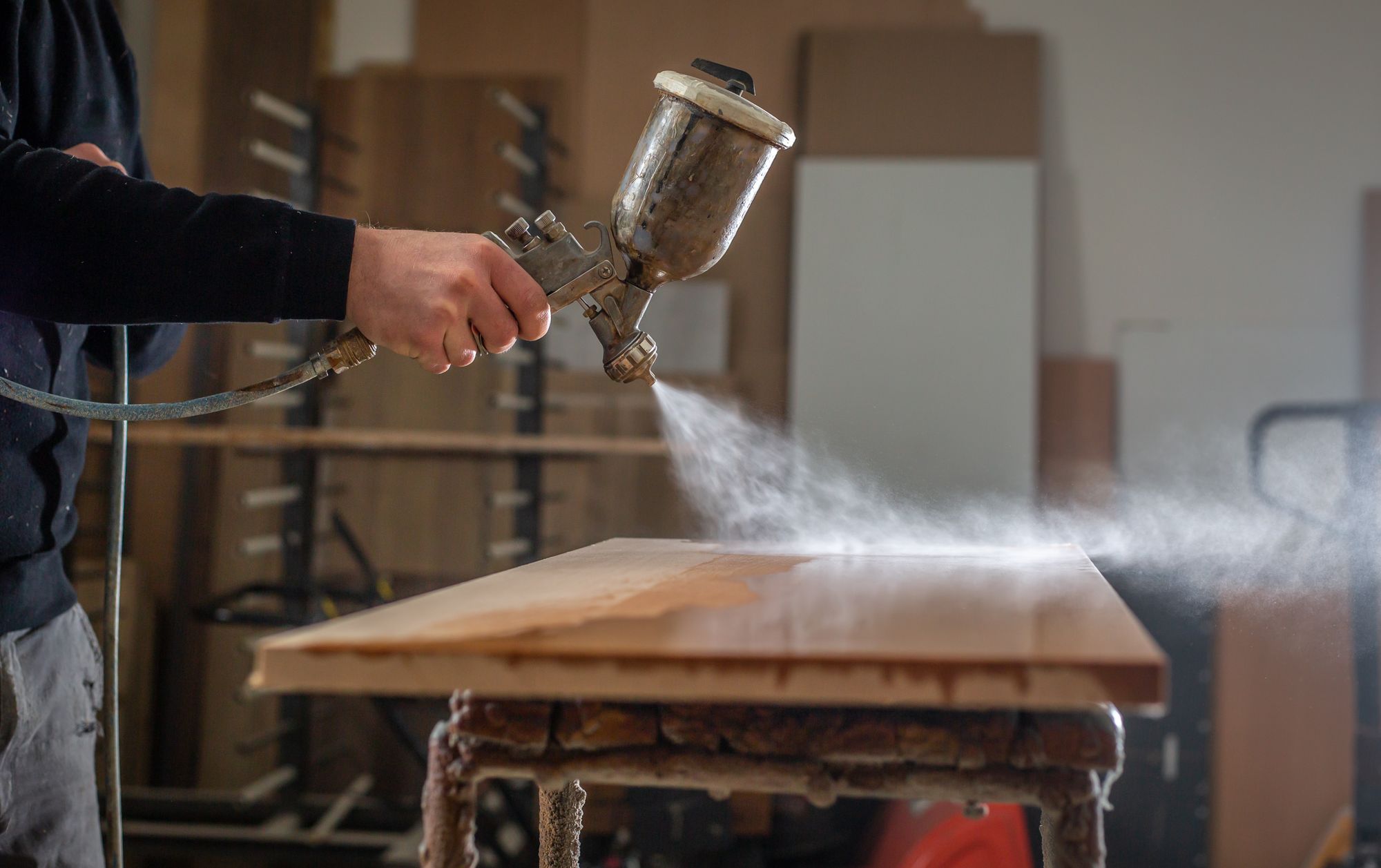