According to the Reverse Logistics Association, the reverse logistics industry in the United States is estimated to have more than $50 billion in annual revenues. Of that, 80% is estimated to come from the retail sector and 20% from the manufacturing industry. Reverse logistics also accounts for about 5% of the total logistics spend in the U.S.
Reverse logistics is an integral part of the supply chain process. It allows businesses to manage the complex process of returns, repairs, and recycling of products.
Reverse logistics has become an increasingly important factor in the success of many companies. It helps to reduce costs, improve customer service, and increase profitability.
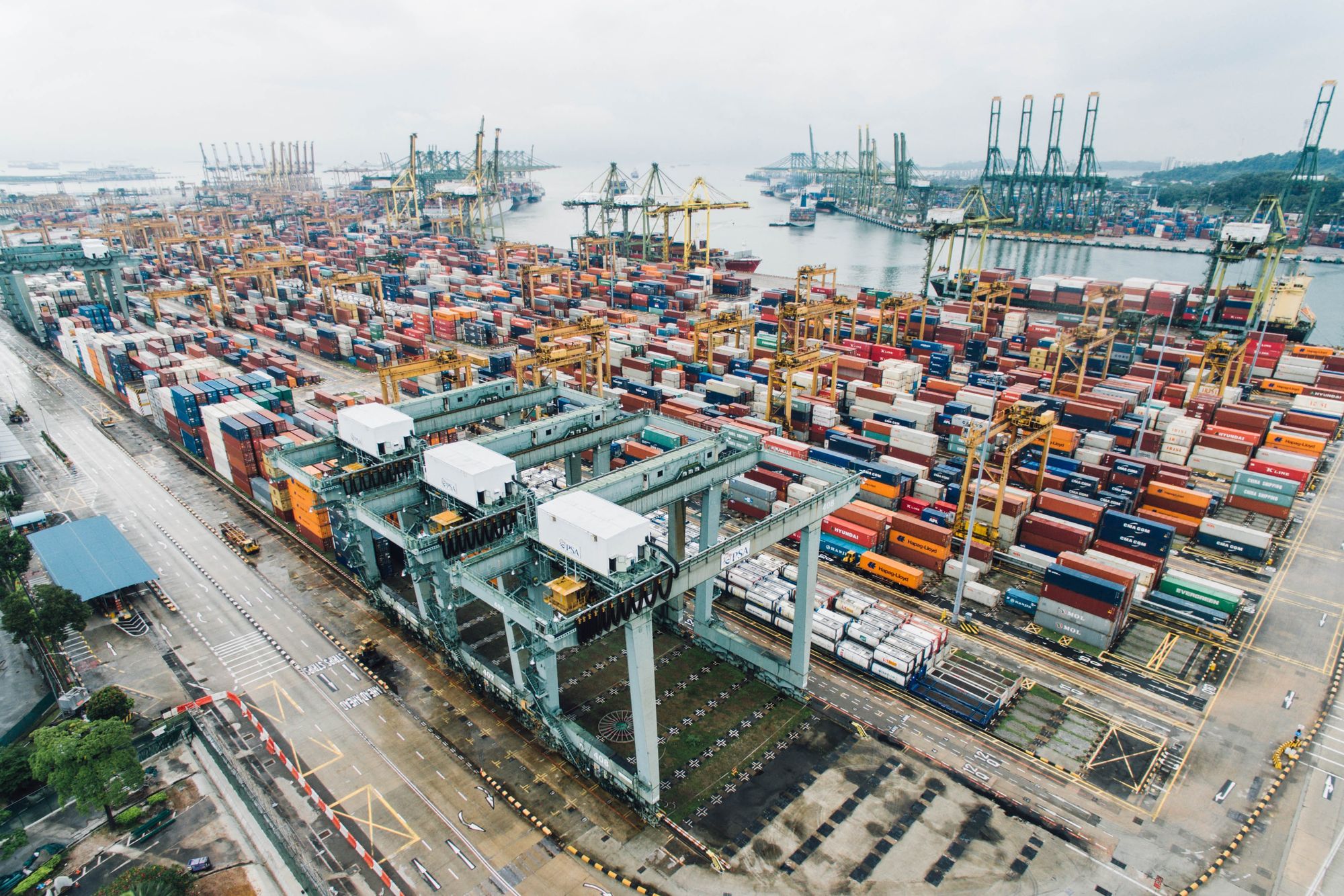
In this article, we will explore the concept of reverse logistics and how it can benefit your business. Here is all that we shall cover in this post:
- What is Reverse Logistics?
- How Reverse Logistics Works
- 11 Benefits of Reverse Logistics
- What Are the Five Rs of Reverse Logistics?
- How to Implement Reverse Logistics Strategies in Your Business?
- How to Monitor Reverse Logistics in Your Supply Chain?
- Challenges of Reverse Logistics
- Conclusion
- Key Takeaways
What is Reverse Logistics?
Reverse logistics is a process that involves the movement of goods, either physical or digital, from the point of sale to the point of origin. It is an essential element of any supply chain. It is vital in reducing environmental waste, ensuring customer satisfaction, and increasing profits.
Reverse logistics is a complex process that requires careful planning and efficient execution. It also requires the ability to identify and react to opportunities quickly. This section will provide an overview of reverse logistics and its importance in modern business.
- Reverse logistics addresses customer returns, product recalls, excess inventory, warranty claims, and other issues that may arise during the business.
- The benefits of a well-implemented reverse logistics system include reduced environmental waste and improved customer satisfaction. Reverse logistics systems also increase profits.
- Reverse logistics can help companies to reduce their environmental impact. It reduces the amount of waste generated through the production and distribution of goods.
- It can improve customer satisfaction by ensuring that products are returned on time. It also ensures that any issues that may arise are resolved quickly and efficiently. Additionally, reverse logistics can help to reduce costs associated with waste disposal, product recalls, and other related expenses.
- Companies should consider the type of goods being returned. They should also consider the reasons for their return and the potential costs associated with the process.
- Companies should also consider the resources available to manage the process. They should also consider the technology needed to track and monitor the movement of goods.
Reverse logistics is an essential part of any supply chain. Companies must carefully plan and execute their reverse logistics process to maximize its benefits.
By understanding the importance of reverse logistics and implementing an effective system, companies can ensure that their supply chain operates efficiently and profitably.
When Is Reverse Logistics Used?
Reverse logistics is returning goods from a customer to a manufacturer or retailer or from one part of the supply chain to another. It is an essential but often overlooked part of the supply chain and is used in many different ways.
- Customer Returns: A typical example of reverse logistics is when a customer returns an item for a refund or exchange. Retailers have a procedure in place to handle customer returns. It will involve processing the return, inspecting the item, and determining how to credit the customer's account. Sometimes, the retailer may resell the item or donate it to another party.
- Product Recalls: Product recalls are another everyday use of reverse logistics. If a product has a manufacturing defect or an issue that affects its safety, the manufacturer may need to recall the item from stores. It involves the manufacturer or retailer arranging for the item to be returned and issuing a refund or exchange to the customer. The manufacturer will then inspect the item to determine the cause of the defect.
- End-of-Life Products: Reverse logistics is also used for products that have reached the end of their life cycle. Manufacturers and retailers may need to arrange for the collection and disposal of these products. It is done in an environmentally friendly way. It can involve coordinating the collection of products from customers. It also involves arranging for their disposal or recycling.
Overall, reverse logistics plays an essential role in the supply chain. It helps to ensure that customers receive refunds or exchanges for defective or unwanted products. It also helps to ensure that end-of-life products are disposed of in an environmentally friendly way.
Reverse Logistics and the Supply Chain
Reverse logistics move goods from their final destination to capture value or proper disposal. It is a critical component of any supply chain and involves the management of returns, repairs, and refurbishments.
Reverse logistics is becoming increasingly important as companies focus on becoming more sustainable. It is done by reducing waste and improving their environmental impact.
The supply chain is a complex network of activities, people, organizations, and resources. It is involved in producing and distributing goods. It involves all the processes, from the procurement of raw materials to the delivery of finished products.
Value Capture
Reverse logistics enables companies to capture value from products sold or returned.
- By returning goods to the original supplier, companies can resell them, remanufacture them, or dispose of them in an environmentally responsible way.
- By reusing or recycling materials, companies can reduce waste and environmental impact.
Additionally, by reselling returned goods, companies can generate additional revenue. It creates a more sustainable business model.
Return Management
Return management is an essential part of reverse logistics.
- It involves managing returns and analyzing customer feedback.
- The goal is to improve customer service and satisfaction.
- By understanding the reasons for returns, companies can identify areas for improvement.
- They can take action to reduce the number of returns.
Repair and Refurbishment
Repair and refurbishment are critical components of reverse logistics.
- By repairing and refurbishing goods, companies can extend the life of their products and reduce waste.
- It can also help to reduce costs and improve the sustainability of the supply chain. Additionally, companies can use this process to improve customer satisfaction.
- Companies can ensure high-quality and long-lasting products. Implementation Reverse logistics can be implemented in several ways.
- Companies can set up dedicated reverse logistics centers.
- Companies can outsource the process to third-party logistics providers or use an in-house team.
Additionally, companies can use technology such as RFID tags and shipment tracking software to improve the efficiency and accuracy of the process.
Reverse Logistics Vs Traditional Logistics
Traditional logistics is the management of the flow of goods, services, and data between the point of origin and the point of destination. It involves the physical movement of goods, including their packaging, storage, and transportation.
Traditional logistics also includes the planning, control, and execution of the efficient and cost-effective movement of goods and services from the point of origin to the point of destination. It is a critical part of the supply chain process and is essential for the efficient and cost-effective delivery of goods and services.
Difference between Reverse Logistics and Traditional Logistics
The following points explain the differences between reverse logistics and traditional logistics:
- Definition: Traditional logistics manages the flow of goods and services from the suppliers to the customers. Reverse logistics manages the flow of goods and services from the customers back to the suppliers.
- Objectives: The main aim of traditional logistics is to get products from the supplier to the customer efficiently and cost-effectively. The main aim of reverse logistics is to get products from the customer back to the supplier efficiently and cost-effectively.
- Scope: Traditional logistics covers delivering products from the supplier to the customer. Reverse logistics covers the entire process of returning products from the customer to the supplier.
- Process: Traditional logistics involves the physical movement of products from the supplier to the customer. Reverse logistics involves the physical movement of products from the customer back to the supplier.
- Cost: Traditional logistics is generally more cost-effective than reverse logistics. It is because traditional logistics involves the physical movement of products from the supplier to the customer. In contrast, reverse logistics involves the physical movement of products from the customer back to the supplier.
- Risks: Traditional logistics involves various risks, such as delivery delays, product damage, and theft. Reverse logistics involves additional risks. These risks include product returns, repair or disposal of products, and customer service.
Basically, traditional and reverse logistics are two types of supply chain operations. Traditional logistics focuses on the flow of materials and products from the supplier to the customer. In contrast, reverse logistics focuses on the flow of materials and products from the customer to the supplier.
Traditional logistics is generally more cost-effective than reverse logistics, but reverse logistics involves additional risks.
How Reverse Logistics Works
Reverse logistics is often seen as an afterthought in the supply chain. But it is essential for improving sustainability, reducing waste, and increasing customer satisfaction.
Step 1: Identification
The first step in the reverse logistics process is identifying any items that need to be returned. It includes damaged, defective, expired, or simply no longer needed.
The method of identifying these items can be done either manually or through the use of technology. For example, manufacturers can use RFID tags to track products throughout the supply chain. They can also provide notifications when items need to be returned.
Step 2: Collection
Once items have been identified, they must be collected from the point of consumption. It can be done either through a traditional pick-up and delivery system or a more automated process, such as a self-service kiosk.
In either case, it is essential to ensure that the items are securely packaged and labeled to prevent damage during transit.
Step 3: Processing
Once the items have been collected, they must be processed to determine their condition and whether they can be reused or resold. It includes inspecting the items and running diagnostics to determine if they are still functional.
Depending on the condition of the items, they may be returned to the manufacturer. They may be resold through a third-party retailer or recycled.
Step 4: Transportation
Once the items have been processed, they must be transported back to the point of origin. Depending on the distance and the shipment size, this can be done by ground, air, or sea. It is essential to ensure that the items are securely packed and labeled to ensure their safe arrival.
Step 5: Storage
Once the items have arrived at the point of origin, they must be stored until they can be reused or resold. It involves ensuring that the items are properly organized and stored in an appropriate environment. This is to prevent damage or deterioration.
Depending on the items, they may need to be stored in a temperature-controlled environment or a special facility designed for hazardous materials.
Step 6: Reuse/Resale
Once the items have been stored correctly, they can be reused or resold. For items that can be reused, they may need to be repaired or refurbished before they can be resold. For items that cannot be reused, they will need to be recycled or disposed of in an environmentally responsible manner.
Reverse logistics is an essential part of the supply chain that often goes unnoticed. By understanding the steps involved in the process, businesses can better manage their reverse logistics operations.
It will ensure that their products are returned to the point of origin safely and efficiently. It can help to reduce waste, increase customer satisfaction, and improve sustainability.
Types of Reverse Logistics
Reverse logistics can be divided into three main categories. These are product returns, waste management, and recycling.
Product Returns
Product returns are items returned to the manufacturer or retailer for various reasons, such as customer dissatisfaction or product defects.
Product returns aim to recapture the value of the returned goods and materials. It can be done by repairing or refurbishing the items and reselling them or recycling them into new products.
Waste Management
Waste management is the process of collecting and disposing of waste materials. It is in an environmentally friendly manner. It includes collecting, transporting, and disposing of paper, plastic, and metal materials.
The goal of waste management is to reduce the amount of waste sent to landfills. It also ensures that the waste sent to landfills is disposed of in an environmentally responsible manner.
Recycling
Recycling is collecting and reusing materials that would otherwise be discarded as waste. It includes materials such as paper, plastic, glass, and metal.
Recycling aims to reduce the amount of waste sent to landfills. It also ensures that recycled materials are reused in a way that is beneficial to the environment.
Reverse Logistics Components
Reverse logistics manages resources, goods, and services from the end of the product's life cycle to its beginning. It involves the methods of returns, repairs, and refurbishments. Here are some of the components of reverse logistics:
- Rentals and Leasing: Rentals and leasing are two different methods of acquiring goods and services. Rentals involve a one-time payment for the use of a product for a limited period. On the other hand, leasing consists of a series of payments over a more extended period. Both methods are essential components of reverse logistics. They provide an efficient way for customers to access goods and services without purchasing them outright.
- Return Policy and Procedure (RPP): The RPP outlines the steps companies take to ensure that customer returns are handled efficiently and effectively. It includes the criteria for returns, the process for initiating a return, and the timeline for processing returns. Companies must have a clear and consistent return policy and procedure.
- Unsold Goods: Unsold goods are products that customers do not purchase. These products need to be managed and disposed of appropriately. Companies often use reverse logistics to help manage the disposal of unsold goods. It allows them to maximize the value that can be obtained from the goods.
- Returns Management: Returns management is managing the returns of goods and services. It involves ensuring that returns are handled promptly and efficiently. It also involves ensuring that customers are satisfied with the return process.
- Remanufacturing or Refurbishment: Remanufacturing or refurbishment is restoring a product to its original condition. It is often done when a product has been returned or is no longer in serviceable condition.
- End-of-Life (EOL): EOL is the point at which a product is no longer serviceable and can no longer be sold. Companies must have a clear plan to dispose of products at their EOL. It will help minimize the product's environmental impact and maximize its value.
- Packaging Management: Packaging management is managing the packaging of products. It involves ensuring that products are packaged correctly. The packaging is durable and secure, and the packaging is aesthetically pleasing. Packaging management is an essential component of reverse logistics. It helps to ensure that products reach their destination safely and in good condition.
- Repairs and Maintenance: Repairs and maintenance are used to keep products in good working condition. Companies must ensure a clear and consistent process for repairs and maintenance. It helps to ensure that customers are satisfied with the product and that it functions correctly.
- Delivery Failure: Delivery failure ensures that products are delivered to their destination efficiently. Companies must have a transparent system to ensure that products reach their destination on time and in good condition. It helps to ensure customer satisfaction.
11 Benefits of Reverse Logistics
Reverse logistics is increasingly important in a comprehensive supply chain management strategy. By understanding the benefits of reverse logistics, businesses can maximize their supply chain performance. Reverse logistics reduces costs and improves customer satisfaction. The following are some of the critical benefits of reverse logistics:
- Cost Reduction: Reverse logistics can help businesses reduce costs associated with returns. By streamlining the process, companies can reduce labor, shipping, and other related expenses. Companies can also implement systems to manage returns efficiently. Additionally, businesses can avoid the costs of disposing of returned goods or storing them in warehouses.
- Improved Customer Satisfaction: Reverse logistics can help businesses improve customer satisfaction. It provides customers with an easy and efficient process for returning goods. Companies can quickly address customer concerns, provide refunds, and exchange goods by offering an efficient return process. It can result in improved customer loyalty and higher customer satisfaction.
- Increased Revenue Opportunities: Reverse logistics offers businesses the opportunity to increase revenue. By collecting and analyzing customer data, companies can identify potential upselling opportunities. Additionally, businesses can use the data to improve their marketing and promotional activities, increasing sales.
- Improved Inventory Management: Reverse logistics can help businesses improve their inventory management processes. By analyzing returned goods, companies can identify which products are selling and which are not. This information can be used to adjust inventory levels and supply chain operations accordingly.
- Enhanced Supply Chain Performance: By implementing a reverse logistics system, businesses can enhance their supply chain performance. It can include reducing lead times, increasing inventory accuracy, and improving quality control. Additionally, reverse logistics can help businesses reduce their total supply chain costs by improving their ability to manage returns.
- Reduced Environmental Impact: Reverse logistics can help businesses reduce their environmental impact by reducing the number of returned goods disposed of in landfills. By reusing and recycling returned goods, companies can reduce the amount of waste produced. Additionally, businesses can use reverse logistics to promote sustainable product innovation and development.
- Efficiency: Reverse logistics can increase the efficiency of a company's supply chain. By reducing the time it takes to move products back to the manufacturer, retailers can reduce the time it takes to restock shelves. It can help reduce the time customers have to wait for their orders.
- Increased Product Lifespan: Reverse logistics can increase the lifespan of products. By returning products to manufacturers for repair or refurbishment, companies can extend a product's life without buying a new one. It is done without purchasing a new one. It can reduce costs and increase the company's overall profit margin.
- Increased Productivity: Reverse logistics can help increase employee productivity. It reduces the time it takes to move products back to the manufacturer. It can free employees to focus on other tasks, such as fulfilling customer orders.
- Increased Product Quality: Reverse logistics can help improve product quality. By returning products to the manufacturer for repair or refurbishment, companies can ensure that products are up to their standards and customers' expectations.
- Increased Product Availability: Reverse logistics can help increase product availability. By returning products to the manufacturer for repair or refurbishment, companies can ensure that products are available when customers need them.
Reverse logistics offers businesses numerous benefits. These range from cost reduction and improved customer satisfaction to increased revenue opportunities and reduced environmental impact.
Companies can maximize their supply chain performance by understanding the benefits of reverse logistics. Reverse logistics reduces costs and improves customer satisfaction.
Importance of Reverse Logistics
Reverse logistics is an essential aspect of the supply chain that helps to keep it running efficiently. It is the process of moving goods from the customer back to the manufacturer for disposal, reuse, or recycling. It helps to reduce waste, keep costs down, and ensure that product quality is maintained.
Route optimization can significantly enhance reverse logistics by minimizing travel time and fuel costs, leading to faster, more efficient returns processing. By leveraging real-time data and intelligent routing algorithms, companies can ensure that returned goods are collected and processed in the most cost-effective manner.
- Reverse logistics help to ensure customer satisfaction. It ensures that customers can return products they are unsatisfied with. The manufacturer can take the appropriate steps to rectify any issues. It helps to maintain good customer relationships and keep customers coming back.
- Reverse logistics also helps to reduce costs associated with disposing of products. Manufacturers can reduce waste disposal costs and keep costs down. By ensuring that products are recycled, reused, or disposed of responsibly. It helps to keep their overall costs down and ensure that their products remain competitively priced.
- Reverse logistics also helps to ensure product quality. By returning defective products to the manufacturer, manufacturers can identify any issues. They can take steps to correct them. It helps to ensure that customers receive the highest quality products. It also helps to ensure that the manufacturer's reputation is maintained.
Finally, reverse logistics is essential for environmental sustainability. Manufacturers can reduce the amount of waste they produce by ensuring that products are recycled, reused, or disposed of responsibly. It helps to protect the environment. It helps to ensure that future generations have a clean and safe environment to live in.
What Are the Five Rs of Reverse Logistics?
The Five Rs of Reverse Logistics refer to the five processes of returns, reselling, repairs, repackaging, and recycling. Reverse Logistics is the process of planning, implementing, and controlling the efficient and effective flow of goods, services, and information from the point of consumption to the point of origin.
Returns
Returns are a crucial part of the reverse logistics process. Companies must have an efficient process in place to handle returns of their products. It includes setting up a system to track refunds, exchanges, and repairs. It also includes ensuring that any returned products are inspected and handled appropriately.
Reselling
Reselling is another essential part of the process. Companies can resell products through their channels or work with a third-party reseller. It helps to recover some of the costs associated with the original product sale.
Repairs
Repairs are when a product is returned for repair. It might be because of a defect in the product or because of damage caused by the customer. Businesses must have a process to assess the damage and determine whether the repair is feasible.
Repackaging
Repackaging is when a product is repackaged. It is often done to ensure that the product meets safety requirements or makes it easier to transport. Businesses must ensure that the product is repackaged and meets all applicable safety standards.
Recycling
Recycling is when a product is recycled. Companies must have a system in place to properly recycle products that are no longer usable. It helps to keep the environment safe and reduces the amount of waste that is sent to landfills.
How to Implement Reverse Logistics Strategies in Your Business?
Reverse logistics is a process that involves the management of products and materials once they have been used and are ready to be returned or disposed of. It is an integral part of any business's supply chain and involves various stages, from product collection to sorting and disposal.
Implementing a reverse logistics strategy can help companies to reduce costs and increase customer satisfaction. It can also help companies to improve their environmental impact.
1. Understand Your Customer's Needs:
The first step in implementing a successful reverse logistics strategy is understanding your customer's needs. It involves conducting customer surveys to determine why and how customers return products.
It also aims to determine what products and services customers would like to see offered in the future. Businesses can develop a comprehensive reverse logistics strategy by understanding customer needs and preferences. This strategy meets their customer's demands.
2. Create a Comprehensive Returns Policy:
A comprehensive returns policy is essential for businesses implementing a reverse logistics strategy. This policy should provide customers with clear instructions on returning a product. It should also provide customers with clear instructions on the return time-frame and what type of refund or exchange is available.
Additionally, businesses should consider providing incentives such as free returns or discounts for future purchases. It is to encourage customers to return products.
3. Establish a Reverse Logistics Process:
A reverse logistics process is key to ensuring that products are returned promptly and cost-effectively. It involves creating a workflow that outlines each step of the return process. This includes where products should be sent and how they should be tracked.
Additionally, businesses should create a cost-effective returns label that can easily track returns. It will ensure that the proper refund or exchange is provided to customers.
4. Track and Analyze Returns Data:
Tracking and analyzing returns data is essential for businesses. Businesses need to understand which products are being returned and why. This information can be used to identify trends in customer returns and any potential issues with products or services.
Additionally, analyzing returns data can help businesses identify opportunities for improvement in their reverse logistics strategy.
5. Leverage Technology:
Technology can be a powerful tool for businesses implementing a reverse logistics strategy. Technology such as automated returns processing systems can streamline the returns process. It can reduce costs associated with managing returns.
Leveraging technology can help businesses track returns in real-time. It provides customers with accurate and up-to-date information about their returns.
How to Monitor Reverse Logistics in Your Supply Chain?
- Understand the Objectives of Reverse Logistics: The first step in developing an effective reverse logistics strategy is to understand the objectives of reverse logistics. These objectives include reducing product returns and reducing costs. They also aim to improve customer service and increase product availability.
- Develop a Process for Returns: A process for returns is essential for maximizing efficiency. It should include clearly defined procedures for receiving, inspecting, and processing returns. It should also include methods for disposing of items that can't be resold.
- Establish Clear Guidelines: Clear guidelines for the process will help ensure that the process is consistent and efficient. Guidelines should include information on handling returns and remanufacturing, as well as how to dispose of products.
- Utilize Automated Systems: Automated systems can help maximize efficiency. Automated systems can streamline and automate the returns process. Examples of automated systems include barcode scanning, tracking and tracing systems, and automatic labeling.
- Utilize Data Analysis: Data analysis can help identify and address inefficiencies in the returns process. Data analysis can provide insights into the returned products' types and return frequency. It can also provide insights into other relevant trends and patterns.
- Employ Quality Control Measures: Quality control measures are essential for ensuring that returned items are in good condition. They can be resold. It could include inspecting and testing returned items and implementing damage control measures.
- Develop a Flexible Plan: A flexible plan is essential for maximizing efficiency. It should include adjusting processes quickly if needed. It should also take advantage of any opportunities to improve the returns process.
- Track Performance: Tracking performance is key to ensuring the process is efficient. Performance should be tracked to identify areas where improvements can be made.
- Utilize Data Analytics: Data analytics can provide valuable insights that can be used to improve the efficiency of the process. Analyzing data can help to identify areas that need improvement and can also help to identify trends that can be used to optimize the process.
- Leverage Partnerships: Establishing partnerships with suppliers and other key stakeholders can help improve the process's efficiency. Partnerships can ensure that the process is efficient and cost-effective.
- Monitor Results: Monitoring the results of the process is key to ensuring that it is efficient and effective. Results should be monitored to identify areas where improvements can be made.
Analyzing the Cost of Reverse Logistics
The cost of reverse logistics is an essential consideration for any business. Measuring and analyzing the cost of reverse logistics can be challenging. But this is necessary to understand the overall cost of doing business. This section will explore the various components of reverse logistics. It will provide a framework for analyzing the cost of reverse logistics.
Components of Reverse Logistics Costs
The cost of reverse logistics can be broken down into several components. These components include the cost of transportation, the cost of processing returns, the cost of storage, the cost of refurbishing or repairing items, and the cost of inventory management.
- Analyzing the Cost of Transportation: Transportation costs are a significant component of the cost of reverse logistics. This cost will vary depending on the product type, the distance it needs to be transported, and the type of transportation used. It is essential to analyze the cost of transportation to understand the total cost of reverse logistics.
- Analyzing the Cost of Processing Returns: Another essential component of reverse logistics cost is processing returns. It includes the cost of processing refunds, returns, repairs, and other services related to the product or service. It is essential to analyze the cost of processing returns to understand the total cost of reverse logistics.
- Analyzing the Cost of Storage: The cost of storage is another critical component of the cost of reverse logistics. It includes the cost of storing returned items, refurbished items, and inventory. It is essential to analyze the cost of storage to understand the total cost of reverse logistics.
- Analyzing the Cost of Refurbishing or Repairing Items: The cost of refurbishing or repairing items is an essential component of the cost of reverse logistics. It includes the cost of repairing or refurbishing items that have been returned or damaged. It is crucial to analyze the cost of refurbishing or repairing items to understand the total cost of reverse logistics.
- Analyzing the Cost of Inventory Management: The cost of inventory management is an essential component of the cost of reverse logistics. It includes the cost of managing the inventory of returned items, refurbished items, and other items. It is essential to analyze the inventory management cost to understand the total cost of reverse logistics.
Monitoring Reverse Logistics in Your Supply Chain
Reverse logistics manages the return and reuse of products, components, and materials. It's an integral part of any supply chain and is often overlooked. Without proper monitoring and management, reverse logistics can lead to significant losses in terms of cost, waste, and customer satisfaction. Here are a few tips for monitoring reverse logistics in your supply chain.
Develop a Return Policy
A good return policy will help you manage and track returns. It will also give customers a clear understanding of what to expect when returning a product. Make sure to include details such as return time-frames, refund policies, and any restocking fees that may apply.
Track Returned Products
Tracking returned products allows you to identify and address any potential problems with the product or process. By tracking returns, you can quickly identify any issues that need to be addressed and take corrective action.
Additionally, tracking returns can help you identify any patterns in the types of products being returned. It can help you make better decisions about what products to produce.
Analyze Return Data
Once you've tracked returned products, you need to analyze the data to identify any problems or opportunities for improvement. Analyzing return data can help you identify trends in product returns.
For example, which products are being returned more often or which customers are returning more. With this information, you can make more informed decisions about improving the product and process. It will help reduce the number of returns.
Reuse and Recycle Products
Reusing and recycling returned products is a great way to reduce waste and save money. Reusing products can help you reduce the number of raw materials and energy used in production. It also reduces the amount of waste that needs to be disposed of.
Additionally, recycling returned products can help you generate additional revenue. You can sell them as refurbished or used items.
Engage Customers
Engaging customers is essential to managing reverse logistics. Customers can provide meaningful feedback about their experience with the product. It can help you make better decisions about product design and quality.
Additionally, engaging customers can help you identify any problems or potential opportunities for improvement in the return process.
Monitoring reverse logistics in your supply chain can help you reduce costs and waste. It can also help you reduce customer dissatisfaction. By developing a return policy, tracking returns, analyzing return data, reusing and recycling returned products, and engaging customers, you can ensure that your reverse logistics process is efficient and effective.
Key Reverse Logistics Supply Chain Metrics
To ensure the success of the reverse logistics process, it is crucial to track and evaluate the performance of the supply chain. It can be done by monitoring various key metrics that measure different aspects of the reverse logistics process.
1. Reverse Supply Chain Cost
The reverse supply chain's cost includes returning, repackaging, and reselling returned goods. This metric can measure the overall efficiency of the reverse logistics process. It can indicate how much money is being spent on returns and how much money is being saved through efficient reverse logistics operations.
2. Return Volume
Return volume is a metric that measures the number of goods returned to the supply chain. This metric can be used to identify trends in returns, as well as to identify potential problems with the supply chain.
3. Return Rate
The return rate is a metric that measures the rate at which goods are returned to the supply chain. This metric can be used to identify areas of the supply chain that are not performing as expected and to identify areas of improvement.
4. Recovery Rate
The recovery rate is a metric that measures the rate at which goods are being recovered from the supply chain. This metric can be used to identify opportunities for improvement in the reverse logistics process. It can also identify areas of the supply chain that could perform better.
5. Resale Rate
The resale rate is a metric that measures the rate at which goods are being resold. This metric can be used to identify opportunities for improvement in the reverse logistics process. It can also identify areas of the supply chain that could perform better.
These five key metrics can be used to measure the performance of the reverse logistics process. By monitoring these metrics, companies can identify areas of improvement in the reverse logistics process. It can also help identify potential problems with the supply chain.
By taking the time to track and evaluate these metrics, companies can ensure the reverse logistics process's success. It is a crucial component of the supply chain's overall success.
Challenges of Reverse Logistics
Despite its growing importance, reverse logistics challenges still need to be addressed to implement sustainable product return strategies successfully. Here, we will discuss some of the key challenges of reverse logistics.
Lack of Standardized Processes
One of the significant challenges of reverse logistics is the lack of standardized processes for product returns. Every company has its unique process for handling product returns. This makes it difficult for customers to know how to return products and for companies to track the progress of returns.
Also, with standard processes, companies can easily determine the best way to manage product returns. It is to ensure that products are returned safely and responsibly.
High Costs
Reverse logistics is a complex process that can be expensive to manage. Companies must invest in resources to collect, store, and transport products. They must also process the products for reuse or disposal. Additionally, companies must invest in personnel to manage the process.
They also need to invest in technology to track the progress of product returns. These costs can add up quickly, making it difficult for companies to profit from product returns.
Risk of Product Damage
Another challenge of reverse logistics is the risk of product damage. Products can become damaged during collection, transportation, and storage. It can result in reduced value or un-usability.
Companies must invest in resources to ensure that products are appropriately handled during reverse logistics. Additionally, companies must invest in technology to track the progress of product returns. This is so they can quickly identify and address any issues that may arise.
Limited Visibility
Another challenge of reverse logistics is limited visibility. Companies often lack full visibility into the process of product returns. It is challenging to track product returns' progress and determine how to manage them.
Companies must invest in technology to gain visibility into the product returns process. It allows them to monitor and adjust their strategies accordingly.
Complex Regulations
The process of product returns is often subject to complex regulations. This can make it difficult for companies to ensure compliance. Companies must invest in resources to understand the rules and ensure that their processes comply.
Additionally, companies must invest in technology to track the progress of product returns. This is so they can quickly identify and address any issues that may arise.
Trends in Reverse Logistics
Automation
Automation is becoming increasingly popular in reverse logistics. Companies strive to streamline the process and reduce costs. Automation can be used to automate the tracking and tracing of returns, as well as the processing of inventories.
Automation can also be used to optimize the fulfillment process. It allows companies to deliver products more quickly and efficiently.
Tracking
Tracking is also becoming an important trend in reverse logistics. Automated tracking systems can monitor and track returns. It enables companies to identify any problem areas and take corrective action quickly.
Analytics
Companies are investing in improved analytics to gain better insights into customer behavior and their supply chains. It allows them to anticipate customer needs and optimize their operations.
It also allows them to make informed decisions about product returns. Companies are also using analytics to improve customer service. They also identify and resolve problems in their supply chain.
Green Initiatives
Green initiatives are becoming more popular in the reverse logistics industry. Companies are increasingly looking to reduce the environmental impact of their operations. Companies are implementing sustainable reverse logistics practices. It includes initiatives such as reusing packaging materials, reducing waste, and increasing recycling.
Companies are looking to reduce their reliance on single-use plastic packaging and paper products. They are also looking to invest in more sustainable shipping and delivery methods.
Collaboration
Companies are increasingly looking to collaborate with their suppliers and customers. It is to improve efficiency and reduce costs. It includes initiatives such as shared shipping arrangements and co-branded packaging.
It also includes cooperative returns processes. Companies are also looking to use cloud-based solutions to facilitate collaboration across the supply chain.
Omni-Channel
Omni-channel is becoming increasingly crucial in reverse logistics. Companies are looking for ways to provide a seamless experience across multiple channels, such as web, mobile, and in-store.
Customer Service
Companies also focus on customer service in reverse logistics. They are looking for ways to provide customers with a better experience when returning or exchanging items.
Data Security
Data security is becoming increasingly important in the reverse logistics process. Companies are looking for ways to protect customer data and ensure that it is not used for malicious purposes.
These are just a few trends in reverse logistics that are emerging in the industry. As companies, continue investing in improved technology and analytics, the reverse logistics landscape will become more complex and efficient. Companies should continue to look for new ways to reduce costs, improve customer satisfaction, and optimize their operations.
How can Deskera Help You?
Deskera software is a comprehensive cloud-based platform. It enables businesses to manage their entire supply chain efficiently. It provides end-to-end visibility and allows companies to track and monitor all aspects of their supply chain. With Deskera, businesses can easily manage their inventory, orders, and returns.
The system also integrates with other modules, such as the inventory, order, and customer management modules. This allows businesses to quickly and accurately address product returns. Here are some of the ways Deskera ERP and MRP systems can help you:
- Make a manufacturing schedule
- Maintain a Bill of Materials
- Produce detailed reports
- Create your own dashboard, among other things!
Deskera ERP is a complete solution that allows you to manage suppliers and track supply chain activity in real-time. It also allows you to streamline a range of other company functions.
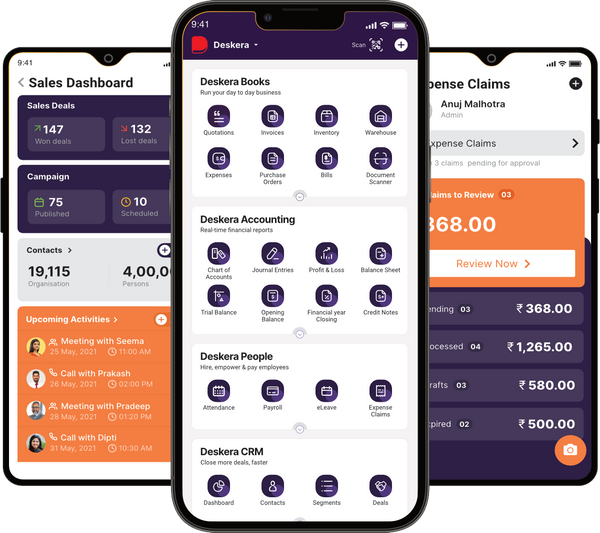
Deskera Books allows you to manage your accounts and finances better. It helps maintain good accounting standards by automating billing, invoicing, and payment processing tasks.
Deskera CRM is a powerful tool that organizes your sales and helps you close deals rapidly. It enables you to perform crucial tasks like lead generation via email and gives you a comprehensive view of your sales funnel.
Deskera People is a straightforward application for centralizing your human resource management activities. Not only does the technology expedite payroll processing, but it also helps you to handle all other operations such as overtime, benefits, bonuses, training programs, and much more.
Conclusion
Reverse logistics is an emerging field in the logistics industry that has been gaining prominence in the past decade. This is due to the increasing focus on sustainability and resource efficiency. It involves the collection, transport, and disposal of returned goods, as well as the management of the associated costs.
Reverse logistics offers various advantages, such as cost savings, improved customer service, and better environmental protection. Effective reverse logistics implementation requires a well-defined strategy. This strategy includes the proper identification, collection, sorting, and disposal of returned goods.
It also involves associated managing costs such as transportation, storage, and handling. Companies should also consider the potential environmental impacts of their reverse logistics activities. They should ensure that their operations are compliant with relevant laws and regulations.
Key Takeaways
- Reverse logistics is an essential aspect of the supply chain. It deals with the movement of goods from the customer back to the manufacturer.
- Reverse logistics is primarily used to collect, store and dispose of returned, damaged, or excess products efficiently and economically.
- Reverse logistics enables organizations to reduce waste and improve customer satisfaction. It also reduces inventory costs. Reverse logistics helps to improve customer service levels by providing complete product returns, refunds, and exchanges.
- Organizations must understand the importance of reverse logistics and develop effective strategies to manage the process. It includes creating a clear plan for handling returns and setting up systems to track and monitor product returns. It also includes leveraging technology to improve visibility and efficiency.
- To maximize the benefits of reverse logistics, organizations must focus on making it an integral part of their supply chain strategy.
- Reverse logistics includes developing a comprehensive process for product returns. It also includes establishing an efficient transportation network and clear customer communication channels.
- Reverse logistics is a complex and costly process, but it is essential for the long-term success of an organization.
- Organizations can significantly reduce costs and boost customer satisfaction by understanding its importance and developing effective strategies.
Related Articles
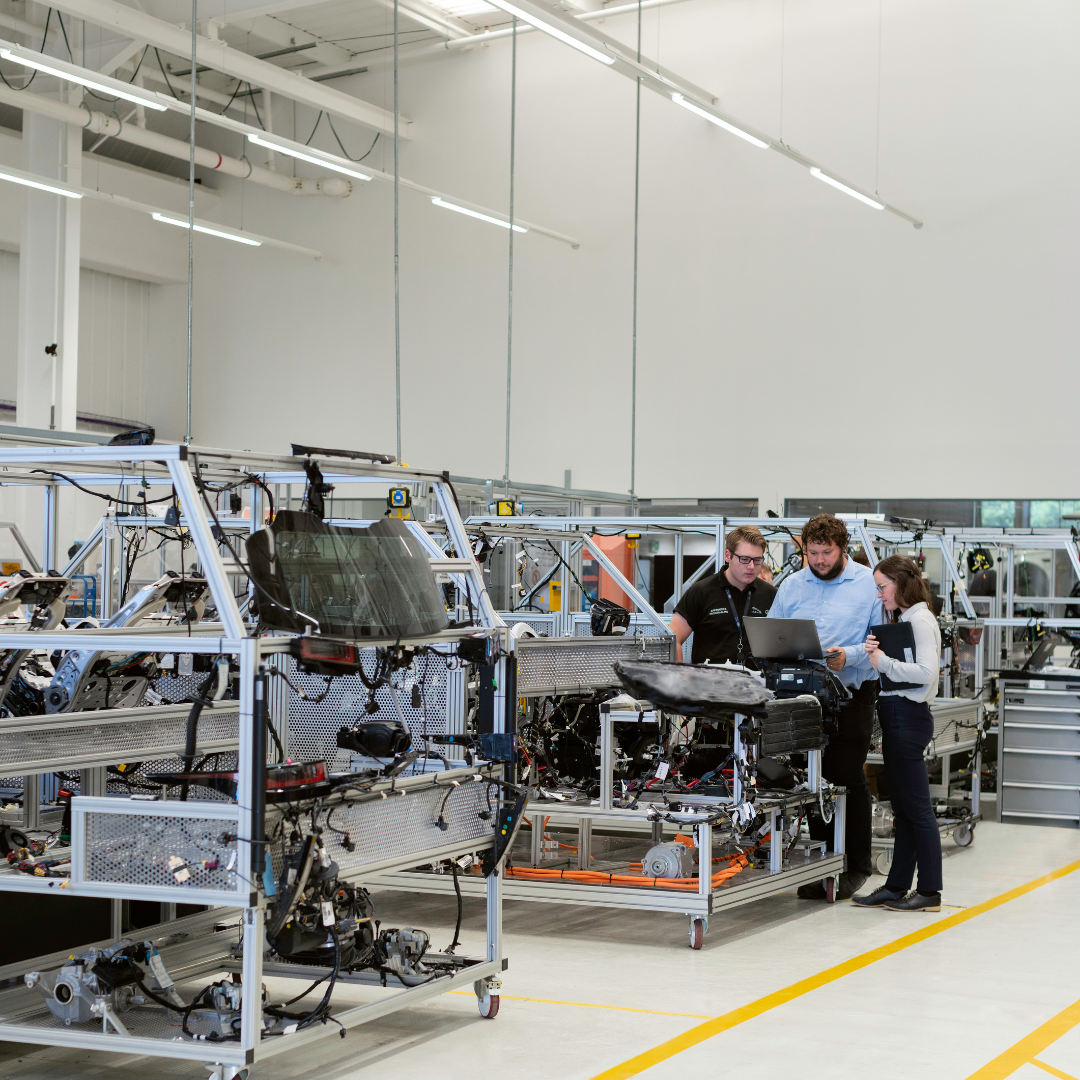
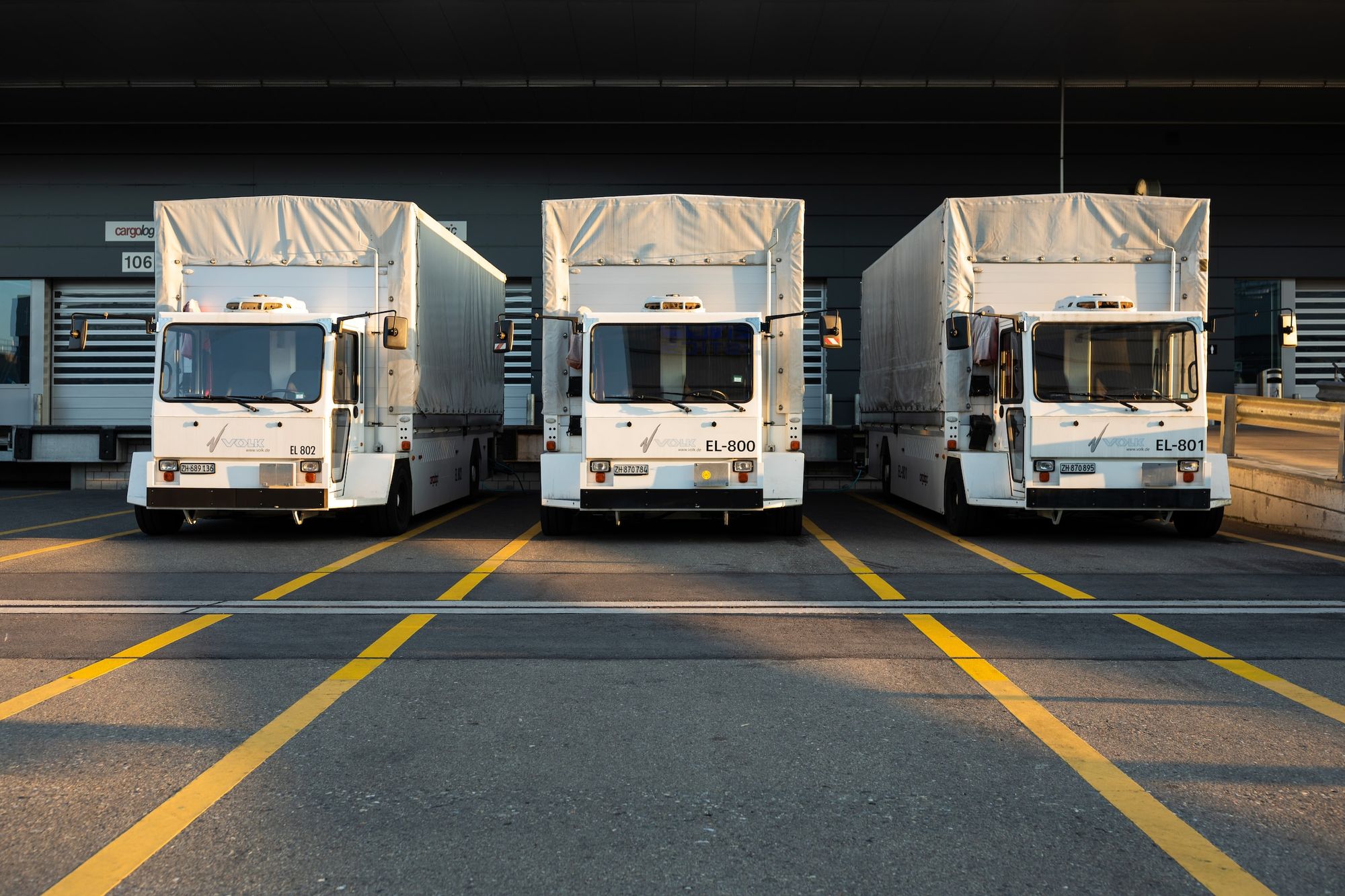
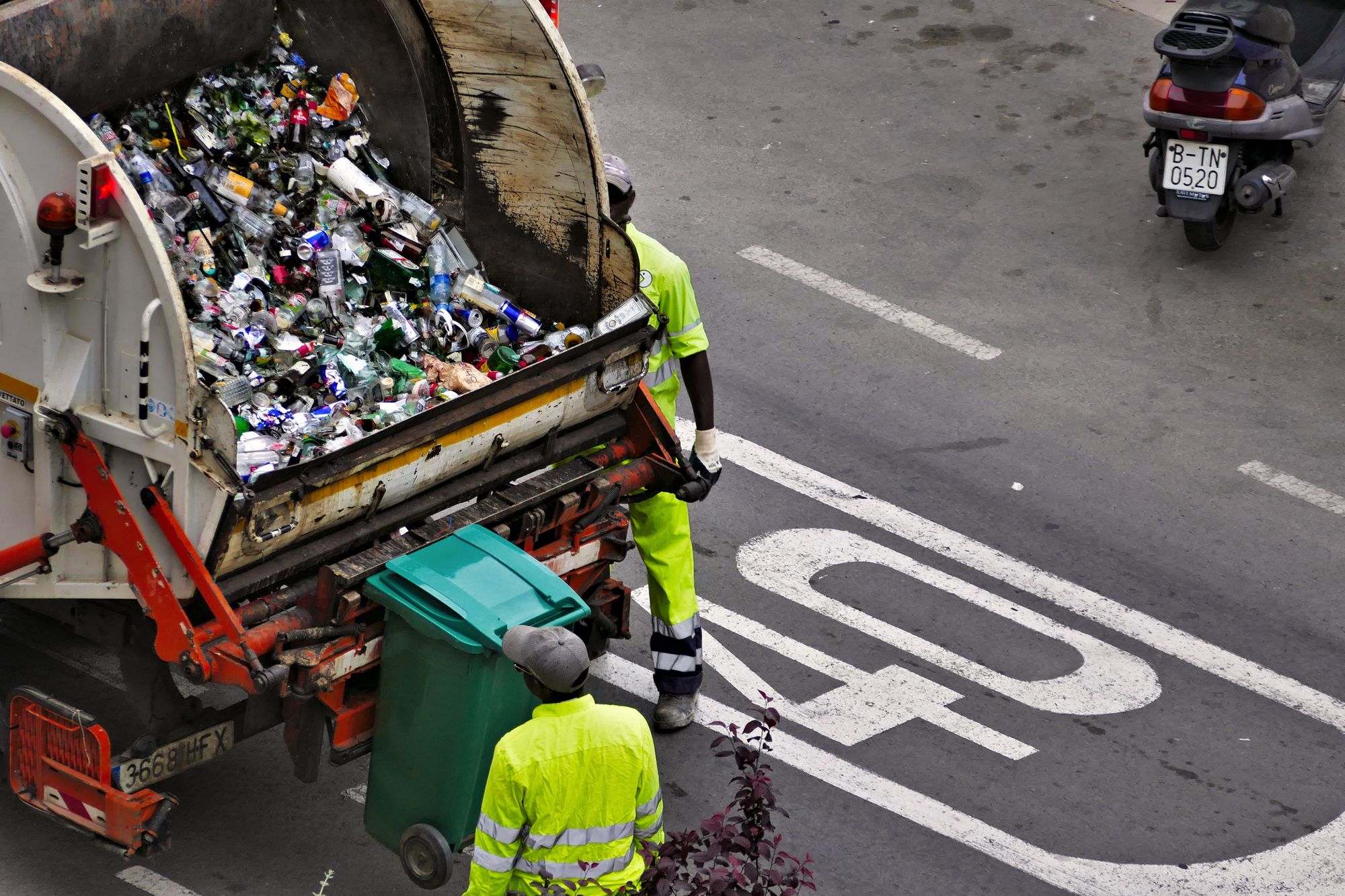
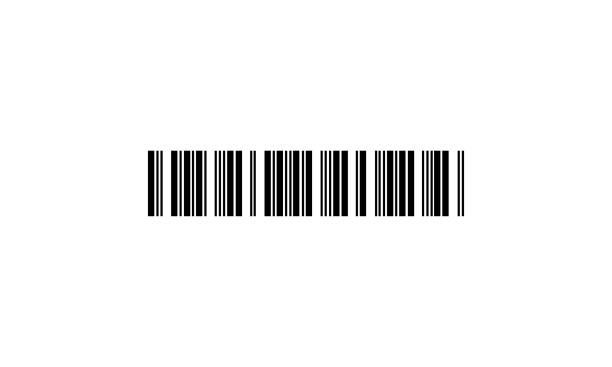