According to a report by McKinsey & Company, MRP systems allow steel producers to increase their production output by 10-15% while reducing inventory costs by up to 25%.
Steel production is a significant industry in the modern world, and material requirement planning (MRP) is essential to its successful operation. Steel production is a complex process that requires careful consideration of materials and resources, and MRP helps to ensure that the process runs smoothly and efficiently.
MRP systems are computerized systems that can be used to manage the planning and ordering of materials. In the steel production process, MRP systems can be used to track the availability of raw materials, the production of finished steel products, and the delivery and storage of those products.
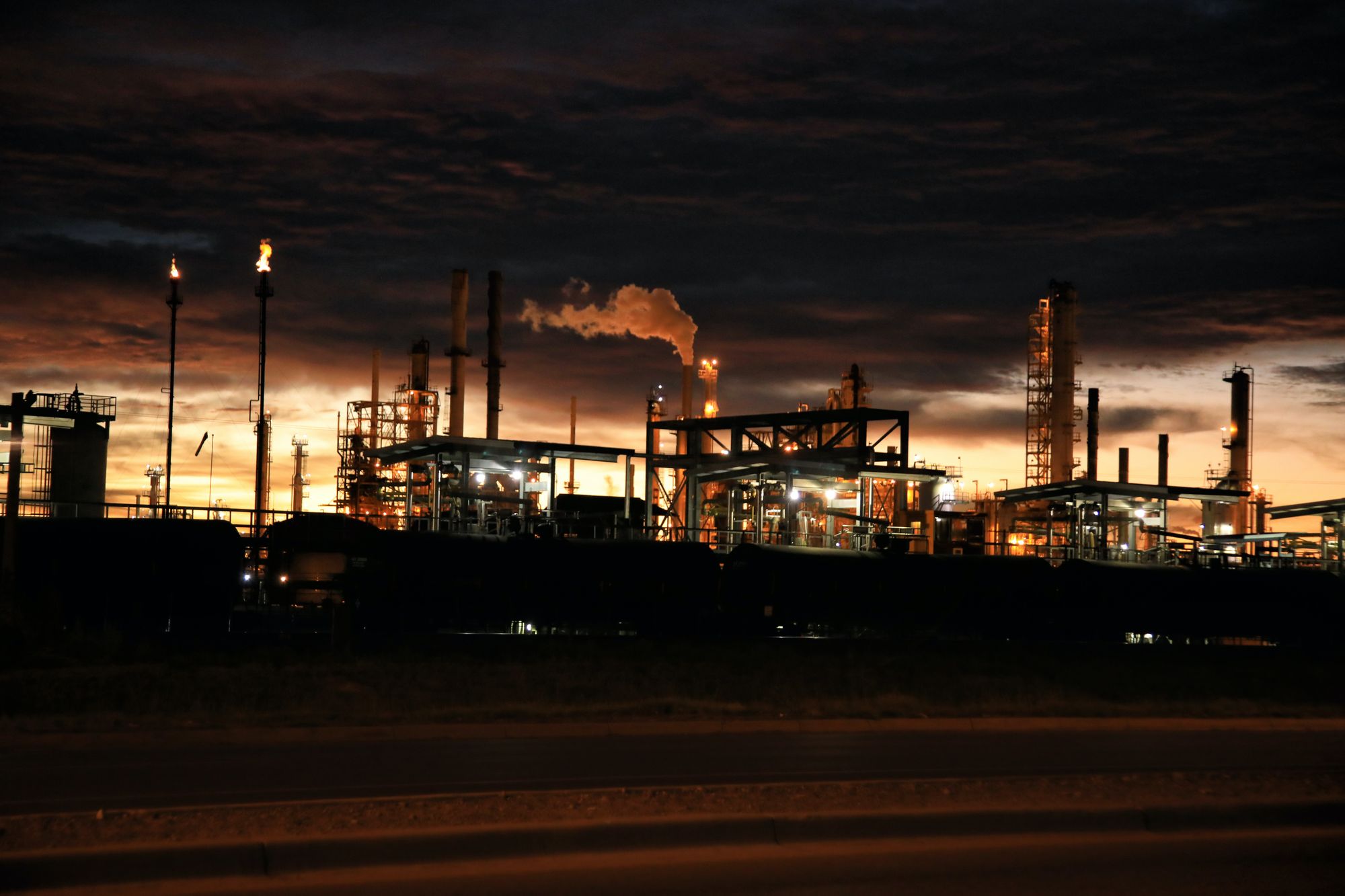
In this article, we'll discuss the basics of Material Requirement Planning for Steel Production, how it can improve steel production, and implement an MRP system. We'll also look at some of the advantages of using MRP for steel production and how it can help increase efficiency, reduce cost, and improve customer satisfaction.
So, whether you're a steel production manager, a materials planner, or someone just looking to learn more about MRP, this article will provide insight into the world of material requirement planning for steel production.
Here’s what we shall cover in this post:
- What is Steel?
- How is Steel Made?
- What is MRP for Steel Production?
- 5 Benefits of MRP for Steel Production
- Implementing MRP for Steel Production
- Challenges in Steel Production
- Best Practices in Steel Production
- Conclusion
- Key Takeaways
What is Steel?
Steel is an alloy of iron and carbon, along with other elements such as manganese, chromium, and nickel. Steel is one of the most widely used materials in the world and is incredibly strong and durable.
- Steel can be used in various forms, such as bars, sheets, rods, and pipes, and is often used in construction, manufacturing, and automotive applications.
- Steel is typically very strong and can resist corrosion, making it a popular choice for many products.
- Steel can also be alloyed with other metals to create different types of steel, each with its unique properties and benefits.
- Steel is also incredibly malleable, allowing it to be formed into a variety of shapes and sizes.
- Steel is produced in various ways, including electric arc, oxygen, and ladle furnaces. The method used depends on the desired properties of the steel.
- Steel is used in a variety of industries, from construction to aerospace. It is also used in the automotive, energy, and medical industries.
Properties of Steel
Steel is composed mainly of iron, with a small amount of carbon and other elements. Here are some of the properties of steel that make it a popular construction material:
- Strength: Steel is one of the strongest construction materials available. Its tensile strength, or the force it can withstand before breaking, is much higher than other materials such as wood or concrete. This makes it ideal for applications that require strength, such as bridges and skyscrapers.
- Durability: Steel is also very durable, meaning it can withstand wear and tear over time. Its resistance to corrosion makes it an excellent choice for outdoor structures and applications.
- Cost-Effective: Steel is also a cost-effective material, as it is cheaper than many other construction materials. This makes it an excellent choice for large-scale projects as well as smaller projects on a budget.
- Versatility: Steel is incredibly versatile, meaning it can be used for many applications. It can be used for structural applications such as bridges, buildings, skyscrapers and more creative projects such as sculptures and art installations.
- Recyclability: Steel is also a recyclable material, meaning it can be reused and repurposed, which is excellent for the environment.
- Fire Resistance: Steel is also highly fire-resistant, which can withstand high temperatures and damage. This makes it an ideal material for fire-resistant structures.
- Low Maintenance: Steel is also a low-maintenance material. It does not require much upkeep and can last for many years with minimal maintenance.
- Easy to Work With: Steel is relatively easy to work with, as it can be cut, shaped, and formed into whatever you need. This makes it an excellent choice for projects that require precise measurements and intricate designs.
Types of Steel
There are many types of steel, each with its unique set of properties. Here are some of the most common types of steel and their uses.
Carbon Steel: Carbon steel is the most common type of steel and is used for a wide range of applications. It is a relatively inexpensive material, making it ideal for construction and other industrial applications. Carbon steel is also highly durable, making it an excellent choice for items that need to withstand a lot of wear and tear.
Stainless Steel: Stainless steel is a type of steel that is resistant to corrosion, making it an excellent choice for applications with a risk of corrosion. It is also very strong, making it ideal for structures and components that can withstand pressure.
Alloy Steel: Alloy steel is a type of steel that combines two or more metals to create a material with unique properties. It is often used in applications where a combination of strength and corrosion resistance is needed, making it a great choice for items like pipelines, car parts, and aircraft components.
Tool Steel: Tool steel is a type of steel designed specifically for use in tools, such as drill bits and saw blades. It is hard and durable, making it ideal for use in tools that can withstand a lot of wear and tear.
High-Speed Steel: High-speed steel is explicitly designed for use in tools that require high precision and accuracy, such as drills and saws. It is harder and more durable than regular tool steel, making it an excellent choice for tools that need to be able to work quickly and accurately.
Spring Steel: Spring steel is a type of steel designed specifically for use in springs. It is highly flexible, making it ideal for use in items that need to be able to bend and flex without breaking.
Maraging Steel: Maraging steel is designed for high-strength applications, such as aerospace components. It is strong and durable, making it an excellent choice for items that can withstand stress.
These are just a few of the most common types of steel. Many other types of steel are available, each with its unique properties. When selecting a type of steel for an application, it is essential to consider the steel's properties and requirements to ensure the correct type of steel is chosen.
How is Steel Made?
Raw Materials
The first step in steel production is to obtain the raw materials. The most important raw material is iron ore, which is found in abundance all over the world. The ore is mined from the earth and then processed to remove impurities such as sulfur, phosphorus, and carbon.
The next step is to combine the iron ore with coke, which is made from coal. This mixture is then heated in a blast furnace, which causes the iron ore to react with the coke and release carbon dioxide.
Blast Furnace
The blast furnace is the most critical part of the steel production process. It is where the raw materials are heated to produce molten iron. The furnace is heated to more than 1700°C, and the molten iron is poured into a converter. The converter is a large vessel that rotates and is lined with a refractory material.
Converter
The molten iron is combined with the converter's scrap steel and other additives. These additives, such as oxygen, manganese, and silicon, are added to control the properties of the steel. The converter is also used to remove impurities such as sulfur and phosphorus. The steel is then poured into a ladle, a large container used to transport the steel.
Ladle Furnaces
The ladle furnace is used to further refine the steel. The furnace is heated to high temperatures, and the steel is stirred to remove any remaining impurities. The steel is then poured into a mold, cooled, and solidified.
Finishing
The final step in the steel production process is the finishing process. The steel is cut and shaped to create the desired products. It is then heat treated to increase its strength and durability. Finally, the steel is tested to meet the required quality standards.
History of Steel Production
Steel production is a long and complex process that has been around for centuries. Steel has been an integral part of human civilization for many years, and its production has evolved. Steel production has been around since the 1700s, and its development has been essential for the growth of modern industry.
Early Steel Production
The earliest form of steel production dates back to the 1700s when it was first produced in the form of wrought iron. This type of steel was created by heating iron with charcoal in a furnace.
This process was laborious and inefficient, and it was soon replaced by puddling, which involved stirring molten iron with a long rod. Puddling allowed for higher-quality steel production and helped set the stage for the modern steel industry.
The Bessemer Process
In 1855, Englishman Henry Bessemer invented the Bessemer Process, revolutionizing steel production. This process allowed for the mass production of steel by blowing air through molten iron, which removed impurities and created stronger steel.
This process was much faster and more cost-effective than the traditional methods and allowed for the mass production of steel. Steel producers quickly adopted this process worldwide and are still used today.
Open-Hearth Process
In the late 1800s, the open-hearth process was developed by German engineer Friedrich Siemens. This process involved heating iron ore and coke in a furnace to create steel.
This process was more efficient than the Bessemer Process and allowed for higher-quality steel production. Steel producers quickly adopted this process worldwide and is still used today.
Electric Arc Furnace Process
In the early 1900s, the electric arc furnace process was developed, which allowed for steel production without using coal or coke. This process involves heating molten iron with electricity, which results in stronger and more consistent steel. This process has become increasingly popular, as it is more efficient and cost-effective than traditional methods.
Modern Steel Production
Today, steel production is a highly industrialized process that involves several different steps. The raw materials, such as iron ore, coke, and limestone, are heated in a blast furnace to produce molten iron.
This molten iron is then treated with oxygen, which removes impurities and creates stronger steel. This steel is then rolled or forged into different shapes and sizes, depending on the application.
Custom Metal Manufacturing
Custom metal manufacturing is creating custom-made metal parts or products according to specifications provided by a customer. It is a complicated process that requires specialized tools, skills, and materials to create the desired item.
Metal manufacturing is used in various industries, from aerospace to automotive, and the process itself can vary depending on the type of metal used and the item's complexity.
Types of Metal Manufacturing
Several types of metal manufacturing processes are used to create custom parts or products. These include machining, casting, forging, stamping, welding, and sheet metal fabrication. Each of these processes has its unique set of advantages and disadvantages, so it is crucial to understand the differences between them to choose the most suitable one for the desired outcome.
Machining
Machining is a metal manufacturing process that involves shaping metal parts or products using tools such as drills, lathes, and milling machines. This process requires high precision and is often used to create complex parts with tight tolerances. It is also used to develop prototype parts for testing and validation before full production.
Casting
Casting is a metal manufacturing process that involves shaping metal parts or products by pouring molten metal into a mold and allowing it to cool and harden. This process is often used to create large parts and products with complex shapes.
Forging
Forging is a metal manufacturing process that involves hammering or pressing metal parts or products into shape. This process often creates complex shapes and parts with tight tolerances.
Stamping
Stamping is a metal manufacturing process that involves pressing metal parts or products into a die to create a specific shape. This process is often used to create parts or products with intricate details and shapes, such as coins and badges.
Welding
Welding is a metal manufacturing process involving combining two or more metals using heat and pressure. This process often creates complex shapes and parts with tight tolerances.
Sheet Metal Fabrication
Sheet metal fabrication is a metal manufacturing process that involves cutting, forming, and assembling sheet metal parts or products. This process often creates parts or products with intricate details and shapes.
Steel Production Applications
In the construction industry, steel is used for a variety of applications. It is an important material for constructing buildings, bridges, and other structures. Steel is also used to construct roads, railways, and other forms of transportation. Steel is also used for the construction of dams and other water structures. Steel is also used in the construction of ships and other vessels.
In the automotive industry, steel is used to produce cars, trucks, and other vehicles. Steel is used for cars' body, chassis, and other components. Steel is also used to build engines, transmissions, and other components. Steel is also used for the production of tires and other automotive parts.
In the manufacturing industry, steel is used to produce various products. Steel is used to create machinery, tools, and other equipment. Steel is also used in making electronics, such as computers and other devices. Steel is also used to produce medical equipment, such as X-ray machines and MRI scanners.
Steel is used in the production of energy. It is used to build power plants and wind turbines and construct pipelines and other energy infrastructure components.
What is MRP for Steel Production?
Material Requirement Planning (MRP) is a tool used by steel production companies to manage their inventory, scheduling, and production processes. It helps to reduce costs, improve efficiency and reduce waste.
MRP is used in steel production to ensure that suitable materials are available at the right time and in the right quantities. It helps manufacturers to plan and manage the resources needed for production, such as raw materials, components, and finished products.
The MRP process starts by determining the estimated demand for finished products. It is then used to determine the number and type of materials required for production. The MRP system then creates a bill of materials (BOM) which lists all the materials needed for production.
The main components of MRP systems include
- Forecasting: The first step in the MRP process is forecasting. The MRP system uses past sales data and customer orders to forecast the demand for steel products. It helps to ensure that the right amount of raw materials and other components are available at the right time to meet the demand.
- Scheduling: The next step in the MRP process is scheduling. The MRP system creates a production schedule that outlines the production process from start to finish. It includes setting deadlines for each step.
- Inventory Management: The MRP system is also used to manage the inventory of raw materials and other components. The system helps to ensure that the right amount of materials are available at the right time to meet the production schedule. It also helps to identify and rectify any shortages or excesses in the inventory.
- Quality Control: The MRP system is also used to monitor the quality of steel products. It helps to ensure that the quality of the steel meets the required standards. It also helps to identify any problems with the quality of the steel and take corrective action.
5 Benefits of MRP for Steel Production
1. Improved Inventory Management
One of the main benefits of using an MRP system for steel production is improved inventory management. MRP systems can track and manage inventory levels, helping to ensure that suitable materials are always in stock when needed. It helps to reduce the risk of running out of essential materials, which can lead to costly delays in production.
2. Streamlined Production Processes
Another key benefit of using an MRP system for steel production is improved efficiency in the production process. MRP systems help to streamline the process by automating tasks like scheduling, ordering, and budgeting. It helps to reduce errors and improves the overall efficiency of the production process.
3. Reduced Costs
Using an MRP system for steel production can also help to reduce costs. The system can help identify areas where cost savings can be made and ensure that materials are purchased at the most cost-effective prices. It can help to reduce overall production costs significantly.
4. Improved Quality
MRP systems can also help improve steel products quality. The system can monitor and analyze the production process, helping identify areas where quality can be improved. It helps to ensure that only the highest quality steel products are manufactured.
5. Increased Visibility
Finally, an MRP system for steel production can help to increase visibility into the production process. The system can provide real-time data about the production process, helping to ensure that production is running smoothly and that any potential problems are addressed quickly. It helps ensure that the production process runs as efficiently as possible.
Implementing MRP for Steel Production
The implementation of MRP for steel production can be broken down into four main steps.
- Define the Manufacturing Process: The first step is to define the manufacturing process. It includes determining the types of steel components that need to be produced, the machines that will be used to create them, and the materials and tools required.
- Develop an MRP System: Once the manufacturing process is defined, the next step is to develop an MRP system that meets the needs of the production process. It includes developing the software needed to manage the production process and the hardware and peripherals required to make it work.
- Set Up the System: Once the system is developed, it must be set up to ensure that it is operational. It includes configuring the system to meet the production process requirements and testing it to ensure that it meets quality standards.
- Train Staff: The final step is to train staff on how to use the MRP system. It includes teaching them how to use the system to manage inventory, track production processes, and ensure that the production process is efficient and cost-effective.
Implementing MRP for steel production is critical to ensuring that the production process is efficient, cost-effective, and compliant with industry standards. It is important to understand the steps required to do so and ensure that the system is properly set up and staff is adequately trained. By doing so, steel production companies can maximize their efficiency and profitability.
Challenges in Steel Production
Steel production is an essential part of the global economy, as it is used in various industries. However, steel production also faces several challenges that can affect the product's quality and the process's overall efficiency. Here are five of the most common challenges in steel production.
1. Raw materials: One of the significant challenges in steel production is the availability of the raw materials needed for the process. Steel production requires large amounts of iron ore, coal, and limestone. Depending on the region, these materials may not be readily available or may be of poor quality. It can lead to delays in production and a decrease in the final product quality.
2. Cost: Another challenge in steel production is the cost associated with the process. Steel production is expensive due to the large amounts of raw materials and energy required. The cost of these materials can be affected by economic and political climates, which can make steel production more expensive than it needs to be.
3. Energy consumption: Steel production is an energy-intensive process requiring a lot of energy to heat the raw materials and keep the steel production process running smoothly. This energy consumption can be a significant challenge for steel producers, leading to higher costs and decreased efficiency.
4. Pollution: Steel production is a major source of air, water, and land pollution. The process releases large amounts of hazardous gases that can harm the environment. These pollutants can also impact the health of the people living near the steel production plant.
5. Waste: Steel production produces a large amount of waste materials, such as slag and dust. These materials must be safely disposed of, which can be a challenge for steel producers. If the waste is not disposed of properly, it can harm the environment.
These are just a few of the challenges faced by steel producers. As the steel demand continues to grow, steel producers must be able to overcome these challenges to ensure the quality and efficiency of the process. By taking the necessary steps to address these issues, steel producers can help ensure the industry's sustainability.
Best Practices in Steel Production
Steel production is an essential industry with a long history. The process of steel production has been refined over the years, leading to the development of modern steel production methods. Several best practices should be followed to ensure the highest quality steel products.
1. Use of Quality Raw Materials: High-quality raw materials are essential for producing quality steel products. Using the best quality steel scrap, iron ore, and other raw materials is necessary. Failure to use high-quality raw materials can lead to substandard products.
2. Efficient Production Process: It is crucial to ensure the production process is as efficient as possible to reduce wastage and improve productivity. It includes using the latest technologies and techniques and ensuring that the production process is streamlined.
3. Quality Control: Quality control is essential for ensuring that the steel products meet the required standards. Regular testing and inspections should be carried out to ensure that the products are up to standard.
4. Use of Protective Gear: Steel production can be dangerous, so it is vital to ensure all workers wear the correct protective gear. It includes safety goggles, gloves, and other items.
5. Adherence to Regulations: It is important to adhere to all relevant regulations and laws when producing steel products. It includes environmental regulations, health and safety regulations, and other regulations.
6. Regular Maintenance: Regular maintenance should be carried out on the equipment used in steel production. It includes cleaning, lubricating, and inspecting the equipment. It will help ensure that it is in good working condition and reduce the risk of problems.
7. Waste Management: Steel production can produce a lot of waste, so it is crucial to have a sound waste management system. It should include recycling and reusing materials whenever possible, as well as disposing of any waste safely and responsibly.
How can Deskera Help You?
Deskera software is a cloud-based business software. It is designed to help you manage and streamline your business operations. It offers a complete suite of integrated applications for business management.
These include inventory control, order management, accounting, and more. It is an ideal solution for businesses that need to manage just-in-time manufacturing.
Deskera MRP is the one tool that lets you do all of the above. With Deskera, you can:
- Control production schedules
- Compile a bill of materials
- Produce thorough reports
- Make your own dashboard.
Deskera ERP is a complete solution that allows you to manage suppliers, track supply chain activity in real time, and streamline a range of other company functions.
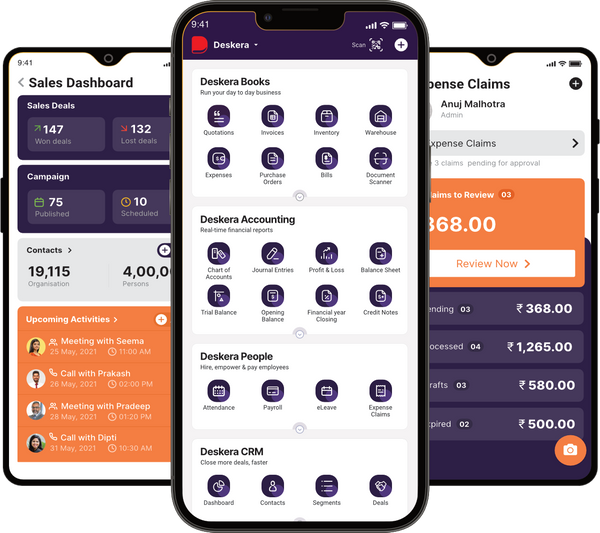
Deskera Books allows you to manage your accounts and finances better. It helps maintain good accounting standards by automating billing, invoicing, and payment processing tasks.
Deskera CRM is a powerful tool that organizes your sales and helps you close deals rapidly. It enables you to perform crucial tasks like lead generation via email and gives you a comprehensive view of your sales funnel.
Deskera People is a straightforward application for centralizing your human resource management activities. Not only does the technology expedite payroll processing, but it also helps you to handle all other operations such as overtime, benefits, bonuses, training programs, and much more.
Conclusion
The steel production industry is a significant component of the global economy. It provides essential raw materials for construction, manufacturing, and other industries. Steel production is a complex process that requires a great deal of energy, resources, and capital. It is a highly competitive industry in which companies must continually innovate and optimize their operations to remain competitive.
Despite the challenges, the steel production industry plays a vital role in the global economy and has been a significant source of employment and economic growth. As the world progresses technologically, the demand for steel production will only grow, making it an important industry to watch in the years ahead.
Material Requirement Planning (MRP) is an essential tool for ensuring the efficient production of steel products. It helps to plan the supply and production of materials most effectively and efficiently as possible.
With MRP, steel producers can quickly identify their needs, reducing the time and resources required to restock or reallocate resources. MRP also helps reduce the risk of stockouts, as it can forecast and order materials ahead of time.
Key Takeaways
- Material Requirement Planning (MRP) is a process used in the steel production industry to improve production efficiency and reduce production costs. It is used to forecast and manage the availability of materials and components in order to meet customer demands.
- MRP systems generate production plans and purchase orders for raw materials, semi-finished and finished goods. It helps to ensure that suitable materials are available at the right time.
- MRP systems optimize production schedules by considering customer demands, stock levels, lead times, and other constraints.
- Steel production is an essential industry in the modern world as it is used in various applications. It is crucial to understand the process of steel production to ensure that it is efficient and cost-effective.
- The production process used in steel production is also vital for the quality of the final product. Different approaches shape the steel into the desired shape and size. The method used depends on the type of product being produced.
- The steel quality is also determined by the equipment used in the production process. Different types of equipment are used in the production process, and it is essential to ensure that the equipment is of the highest quality.
Related Articles
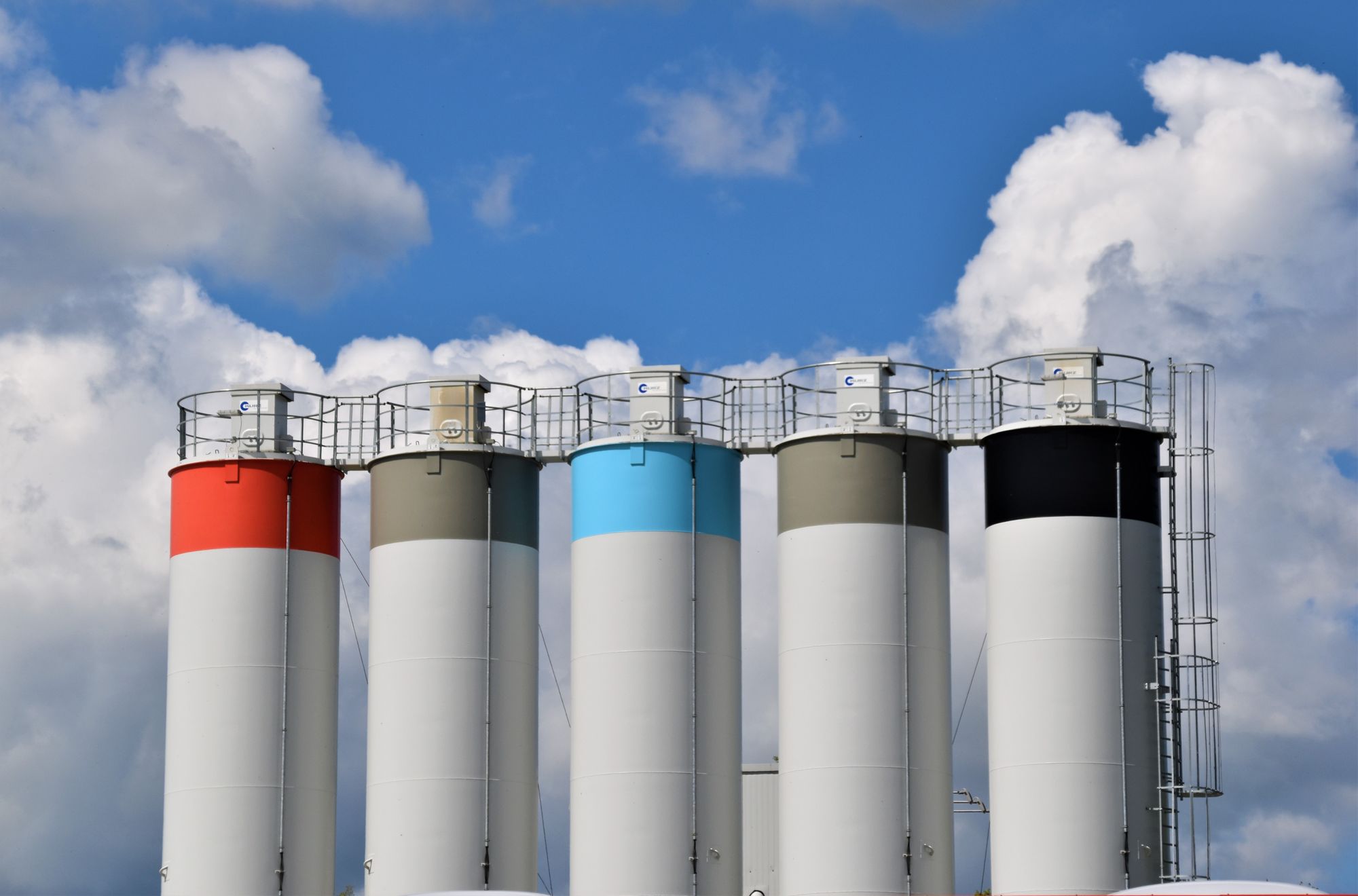
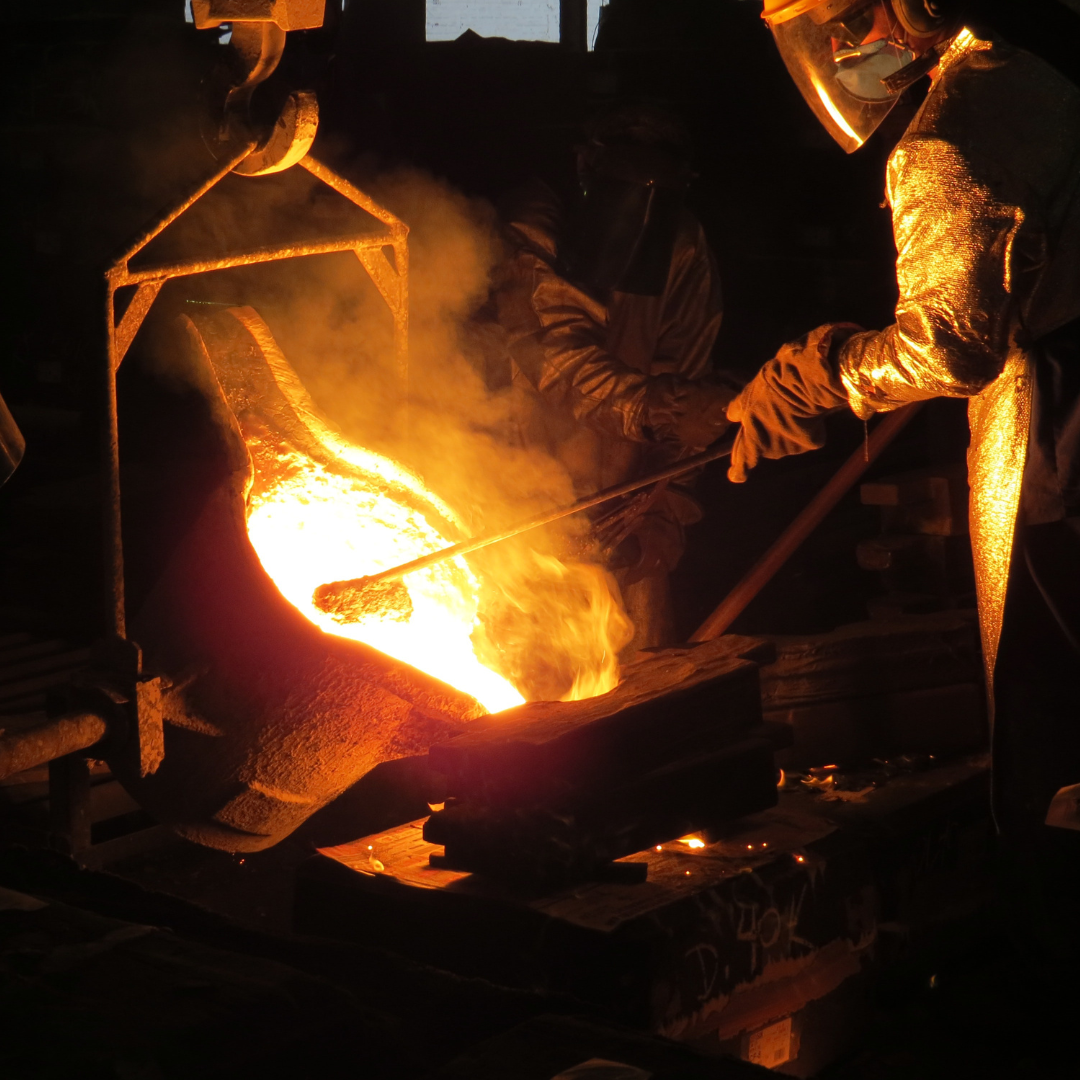
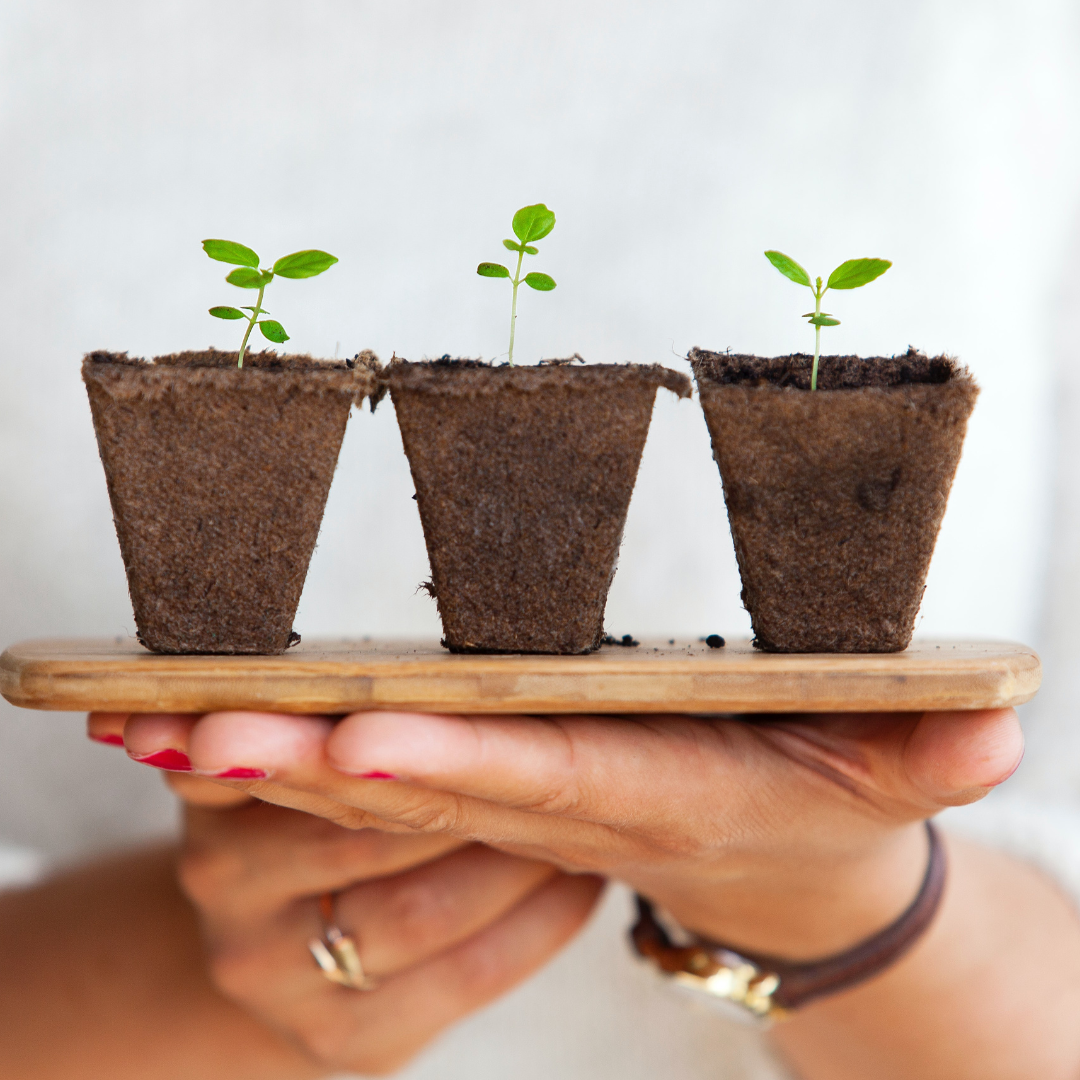
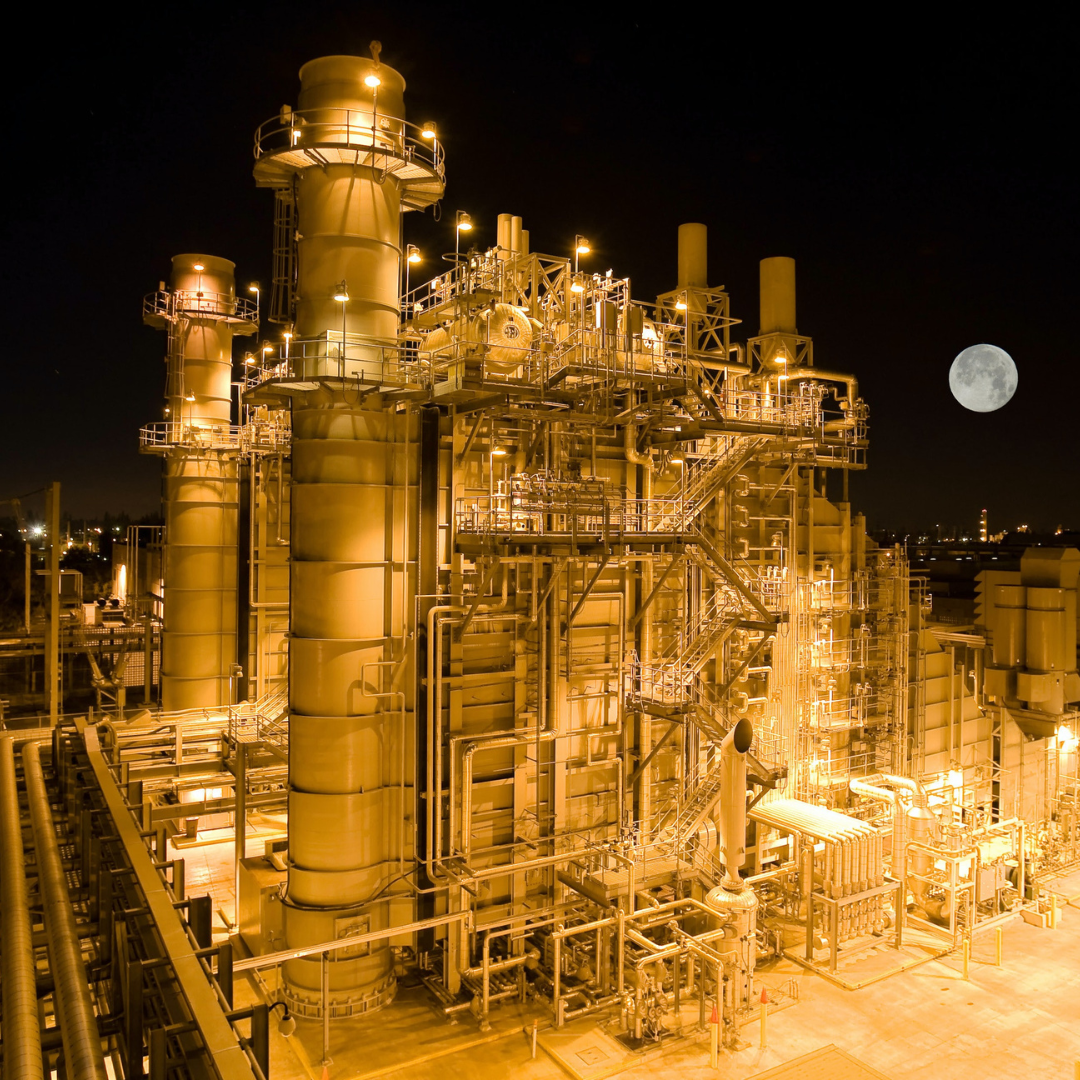