According to a 2018 Institute for Supply Management survey, Material Requirements Planning (MRP) is the most popular planning method used by industrial gas & chemical companies, with a usage rate of 83%.
The industrial gases and chemicals industry is one of the most important industries in the world. It is responsible for producing a wide range of essential products such as industrial gases, chemicals, and other materials.
As a result, the industry needs to maintain high efficiency and cost-effectiveness to remain competitive. MRP is a powerful tool that can help the industry achieve this goal.
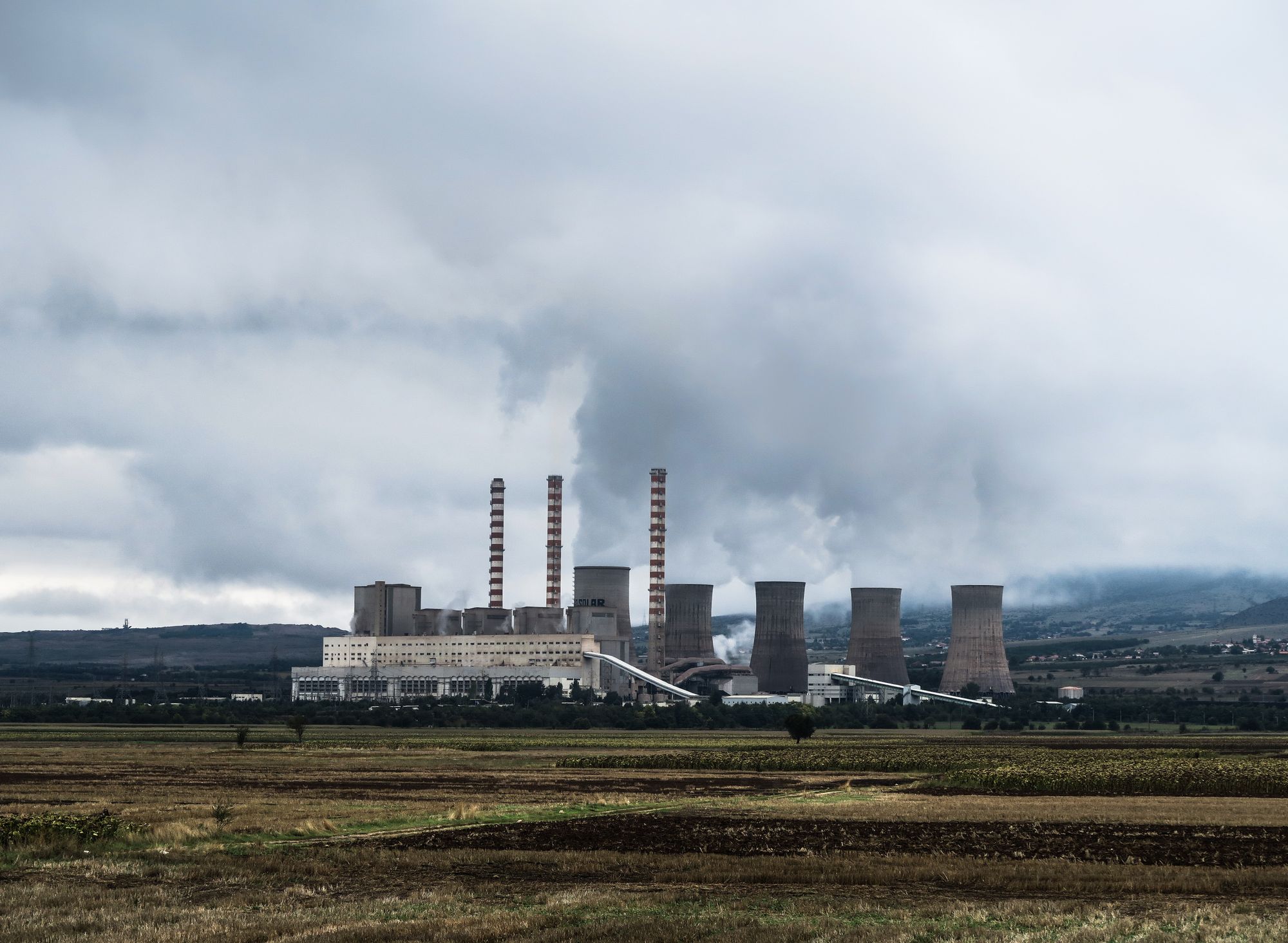
MRP identifies and plans for the materials and resources required to manufacture a product or service. In this industry, it is essential to accurately plan production schedules and manage inventory levels to meet customer demand and maintain a competitive edge.
MRP can help companies achieve this by providing detailed information about production requirements, inventory levels, and resource availability. This information can be used to develop accurate production schedules and ensure inventory is available when needed.
This article will discuss the importance of MRP in the industrial gases and chemicals industry and how it can be implemented to increase efficiency and reduce costs.
Here’s what we shall cover in this post:
- What Are Industrial Gases?
- What Are Industrial Chemicals?
- What is MRP for Industrial Gases and Chemicals?
- 4 Benefits of MRP for Industrial Gases and Chemicals
- Implementing MRP for Industrial Gases and Chemicals
- Challenges Faced by Industrial Gases and Chemicals Industry
- Conclusion
- Key Takeaways
What Are Industrial Gases?
Industrial gases are used in a wide range of commercial and industrial operations. They are used for various purposes, including welding, cutting, cooling, heating, and manufacturing.
Industrial gases are typically produced in large quantities, and their production and supply are highly regulated, as their use can present a variety of safety hazards.
- The most common industrial gases are oxygen, nitrogen, argon, propane, and helium. The use of industrial gases can present a variety of safety hazards, and their production and supply are highly regulated.
- Industrial gases can save time and money when used properly, as they can produce high-quality results and increase productivity.
- Industrial gases are becoming increasingly important in modern industrial processes, as they can improve efficiency, reduce costs, and improve safety.
- These gases are available in different forms, such as compressed, liquid, and solid.
- Understanding the types of industrial gases, their uses, and the potential risks associated with their use is essential for safe and efficient industrial operations.
- Industrial gases are used in a variety of industries and applications. They are essential in many industrial processes and activities and are used to create products we use and consume daily.
Industrial gases are also used to create atmospheres for unique processes, such as protective atmospheres in producing electronic components and packaging food. They can also be used as fuel sources for combustion processes, cooling, and refrigeration.
Types of Industrial Gases
Different types of industrial gases are available in the market depending on the application. Some of the common types of industrial gases are:
1. Oxygen: Oxygen is the most commonly used industrial gas. It is used in various industrial processes, including welding, paper, and steel production. Oxygen also creates an explosive atmosphere for burning fuels like coal and natural gas. Oxygen is also used for medical purposes, such as treating respiratory diseases.
2. Acetylene: Acetylene is a combustible gas made from the reaction of calcium carbide and water. It is used for welding, cutting, and brazing applications. Acetylene is also used to produce organic compounds such as acetic acid and acetone.
3. Nitrogen: Nitrogen is a colorless, odorless, and non-toxic gas used in various industrial processes. It is used as an inert gas to prevent the oxidation of metals and to reduce fire hazards in chemical processes. Nitrogen is also used in the production of fertilizers and explosives.
4. Hydrogen: Hydrogen is a colorless and odorless gas used in various industrial processes. It is used in producing non-flammable fuels and as a reducing agent in chemical processes. Hydrogen is also used in the production of ammonia and other nitrogen compounds.
5. Carbon dioxide: Carbon dioxide is a colorless and odorless gas used in various industrial processes. It is used as a refrigerant, a propellant in aerosols, and a fire suppressant. Carbon dioxide is also used in producing carbonated beverages and synthetic rubber.
These are some of the common types of industrial gases. Each type of gas has its unique properties and applications. Before using them in industrial processes, it is crucial to understand the different types of industrial gases and their uses.
How to Produce and Store Industrial Gases?
The distillation process usually creates industrial gases, but other production methods are also used. This section will discuss how to produce industrial gases and the various methods used for producing them.
Production Process
- Raw Materials: Industrial gases are typically produced from various raw materials, depending on the type of gas and its intended use. Familiar sources of raw materials include air, water, natural gas, petroleum, and coal. Some gases are also created through chemical synthesis.
- Processing: The raw materials are then processed to create the desired gas. This process can involve simple filtration, distillation, cryogenic separation, or more complex chemical reactions. This process purifies the gas and separates it from other gases and impurities.
- Compression: After the gas is processed, it is typically compressed and stored in tanks or cylinders. This is done to make it easier to transport and store the gas.
- Packaging: The compressed gas is then packaged in various containers, depending on the gas and its intended use. These containers can range from small canisters for consumer use to large tanks for industrial applications.
- Distribution: The packaged gas is then transported to its destination, either to a manufacturing facility or to a retail outlet.
Production Methods
Distillation: Distillation is the most common method used to produce industrial gases. This process involves heating a liquid or a solid and collecting the vapor released. The vapor is then cooled and separated into its component gases. This process can produce many gases, including carbon dioxide, nitrogen, and oxygen.
Cryogenic Separation: Cryogenic separation is another method used to produce industrial gases. This process involves cooling the gas to very low temperatures and separating it into component gases. This method is often used to produce oxygen, nitrogen, and helium.
Pressure Swing Adsorption: Pressure swing adsorption (PSA) is a method of producing industrial gases that uses a particular type of adsorbent material. This material adsorbs the gas, which is then released from the material at a different pressure. This method is often used to produce oxygen, carbon dioxide, and hydrogen.
Chemical Reactions: Chemical reactions can also be used to produce industrial gases. This process involves combining two or more chemicals in a reaction vessel and collecting the released gas. This method is often used to produce chlorine and ammonia.
Electrolysis: Electrolysis is another method of producing industrial gases. This process involves using an electric current to break down a liquid and collect the released gas. This method is often used to produce hydrogen and oxygen.
Catalytic Reforming: Catalytic reforming is a process used to produce industrial gases. This process involves combining a hydrocarbon feedstock with a catalyst and collecting the released gases. This method is often used to produce hydrogen and carbon monoxide.
Membrane Technology: Membrane technology is a process used to produce industrial gases. This process involves passing gas through a membrane specially designed to separate it into its component gases. This method is often used to produce nitrogen and oxygen.
Industrial Gas Storage
Storing industrial gases is an essential part of their use, and there are several ways to keep them safely and efficiently. When storing industrial gases, it is essential to consider safety first.
It is crucial to ensure that the storage area is well-ventilated and that all safety equipment, such as protective clothing and respirators, is available. In addition, it is vital to ensure that the storage area is away from any heat sources or sparks, as these can cause an explosion or fire.
Gas Storage Containers: The most common way to store industrial gases is in specially designed gas storage containers. These containers are designed to store gases safely and securely and come in various sizes and capacities.
It is crucial to choose the right size and capacity for the amount and type of gas being stored. The containers must also be well-maintained and regularly checked for any leaks or damage.
Gas Cylinders: Another option for storing industrial gases is gas cylinders. These cylinders are typically made of metal and designed to store gases securely.
Gas cylinders must be adequately maintained and inspected regularly, and it is vital to check for any leaks or damage before using them to store gases.
Pressurized Containers: Pressurized containers are also used to store industrial gases. These containers are designed to maintain a certain pressure level, typically made of metal or plastic.
It is essential to check these containers regularly for any leaks or damage and to ensure that the pressure is maintained at the required level.
Gas Storage Tanks: In some cases, larger amounts of industrial gases may need to be stored in gas storage tanks. These tanks are typically made of metal and designed to safely and securely store large quantities of gas safely and securely.
How are Industrial Gases Used?
Industrial gases can help manufacture goods, provide energy, and more. Industrial gases are an important component of the global economy and essential for manufacturing many products. There are several industrial gases, each with unique properties and uses.
Manufacturing
Industrial gases are used in a variety of manufacturing processes. One of their primary uses is welding, where a gas creates an oxygen-free environment for welding. Other uses include providing a protective atmosphere for heat treating, plasma cutting, and soldering.
Industrial gases also help to purify and refine materials, such as in the production of aluminum, steel, and other metals.
Power Generation
Industrial gases are also used to generate power. Natural gas, for example, is often used in power plants to generate electricity. Industrial gases are also used in gas turbines and fuel cells, which are used to produce electricity.
Refrigeration and Air Conditioning
Industrial gases are also used in the refrigeration and air conditioning industry. The most common industrial gases used in this industry are fluorocarbons and hydrochlorofluorocarbons.
These gases are used to create a cooling effect on air, which helps to reduce the temperature of a room. They are also used in air conditioning systems to remove moisture from the air.
Medical Applications
Industrial gases are also used in medical applications. Oxygen, for example, is commonly used to help patients who are suffering from respiratory problems. Helium is often used in the medical field to help treat certain conditions, such as asthma.
Industrial gases are also used to assist in the production of pharmaceuticals and in the sterilization of medical equipment.
Food Processing
Industrial gases are also used in food processing. Carbon dioxide, for example, is often used to help preserve food and to increase shelf life.
Nitrogen is used to help prevent oxidation in food, which can cause spoilage. Industrial gases also help create foam on top of the beer and other beverages.
Fire Suppression
Industrial gases are also used in fire suppression. Carbon dioxide and nitrogen are often used to help extinguish fires, as they are both non-flammable. Nitrogen is also used to help reduce the risk of explosions, as it is an inert gas.
Uses in Other Industries
Industrial gases are also used in a variety of other industries. They are used to help with the production of glass, to create a protective atmosphere in semiconductor manufacturing, and to help produce chemicals.
Industrial Gases Requirement In Chemical Industry
Gases used in chemical processes can be divided into two main categories: inert and reactive. Inert gases are mainly used as atmosphere control in thermal processing and storage processes. Reactive gases are used in chemical reactions, such as catalytic reactions, oxidation-reduction reactions, and polymerization.
The chemical industry's most commonly used industrial gases are oxygen, nitrogen, hydrogen, and carbon dioxide. The uses of industrial gases in the chemical industry are diverse and often specialized to a particular process. The most common uses of these gases include:
- Reactivity: Gases are used as reactants or catalysts in many chemical processes. Oxygen, for example, is used to oxidize other compounds to produce desired products. Nitrogen reduces certain compounds and acts as a catalyst in specific reactions. Hydrogen is used to reduce other compounds, while carbon dioxide is used to produce carbonates and other products.
- Cooling: Gases are also used to cool chemical processes and products. They are used to reduce the temperature of the reaction vessel, cool the reactants, and reduce the product's temperature.
- Solvent: Gases are also used as solvents in certain processes. Carbon dioxide, for example, is used as a solvent for many organic compounds.
- Atmosphere control: Gases are used to control the atmosphere of the reaction vessel. Nitrogen is often used to displace air for inerting purposes.
What Are Industrial Chemicals?
Industrial chemicals are substances used to make products, processes, or services used in producing goods. These chemicals are used in various industries, including manufacturing, food processing, and pharmaceuticals.
- They are also used in cosmetics, paints, and other products. Industrial chemicals can be hazardous to human health and the environment.
- They can cause skin, eye, and respiratory irritation and other health problems. It is important to use industrial chemicals safely and responsibly to prevent accidents and injury.
- The government regulates industrial chemicals to ensure their safe use. The Environmental Protection Agency, Department of Labor, and Occupational Safety and Health Administration are responsible for regulating the use of industrial chemicals.
- Regulations are in place to ensure that industrial chemicals are used safely and responsibly.
The use of industrial chemicals can harm the environment. Some industrial chemicals are toxic, and their use can pollute the air, water, and soil. The use of industrial chemicals can also lead to the depletion of natural resources, such as water and land.
Types of Industrial Chemicals
Industrial chemicals are widely used in a variety of industrial processes and have a far-reaching impact on everyday life. In this section, we will take a look at some of the different types of industrial chemicals and their uses.
- Solvents: Solvents are industrial chemicals used to dissolve or disperse other materials. Examples of solvents include ethanol, isopropyl alcohol, acetone, and ethylene glycol. They are used in various industries, including paint manufacturing, pharmaceuticals, and printing.
- Acids: Acids are industrial chemicals used to dissolve or alter other materials. Examples of acids include nitric acid, hydrochloric acid, sulfuric acid, and phosphoric acid. They are commonly used in metal processing, manufacturing, and electronics.
- Bases: Bases are a type of industrial chemical that are used to neutralize or alter other materials. Examples of bases include sodium hydroxide, potassium hydroxide, calcium hydroxide, and magnesium hydroxide. They are commonly used in the production of pharmaceuticals and the manufacturing of textiles.
- Oxidizers: Oxidizers are industrial chemicals used to increase the speed of a reaction. Examples of oxidizers include potassium permanganate, potassium nitrate, and sodium hypochlorite. They are commonly used in the production of explosives and propellants.
- Surfactants: Surfactants are a type of industrial chemical used to reduce the surface tension of liquids. Examples of surfactants include ethoxylates, polyethylene glycols, and sodium laureth sulfate. They are commonly used to produce detergents, paints, and cosmetics.
- Chelating Agents: Chelating agents are industrial chemicals used to bind and remove metal ions from a solution. Examples of chelating agents include EDTA, citric acid, and thioglycolic acid. They are commonly used in producing paints, dyes, and pharmaceuticals.
- Catalysts: Catalysts are industrial chemicals used to increase the rate of a reaction. Examples of catalysts include platinum, palladium, and rhodium. They are commonly used in the production of fuels, polymers, and pharmaceuticals.
- Disinfectants: Disinfectants are a type of industrial chemical used to kill or reduce the growth of microorganisms. Examples of disinfectants include chlorine, hydrogen peroxide, and iodine. They are commonly used to produce food, water, and medical products.
- Additives: Additives are a type of industrial chemical used to improve a material's properties. Examples of additives include antioxidants, emulsifiers, and stabilizers. They are commonly used to produce foods, cosmetics, and paints.
- Lubricants: Lubricants are industrial chemicals used to reduce friction between two surfaces. Examples of lubricants include mineral oil, vegetable oil, and synthetic oils. They are commonly used in producing machinery, vehicles, and other mechanical components.
Chemical Manufacturing Process
The chemical manufacturing process is a complex and multi-faceted procedure. It involves transforming raw materials into a purified or usable form through a series of chemical reactions. Here, we look at the steps involved in the chemical manufacturing process and how they all come together.
Raw Material Acquisition
The first step in the chemical manufacturing process is the acquisition of raw materials. It will depend on the type of chemical produced and the desired end product. Common raw materials used in the chemical manufacturing process include petroleum, natural gas, minerals, organic compounds, and organic compounds.
These raw materials must be acquired from reliable sources and in the necessary quantities to ensure the quality of the final product.
Preparation and Mixing of Materials
Once the raw materials have been acquired, they must be prepared for the chemical manufacturing process. It typically involves mixing and blending the raw materials in specific proportions, often using specialized equipment.
Reaction
Once the raw materials have been properly mixed, the reaction can take place. Depending on the chemicals being used, this reaction can take place in various ways, such as under pressure, at specific temperatures, in a vacuum, or a sealed container.
This process step is highly regulated and must be carefully monitored to ensure the desired results.
Separation
After the reaction, the next step is to separate the desired product from any byproducts that may have been created in the process. It is done through a variety of methods such as distillation, filtration, or centrifugation.
Purification
The next step in the chemical manufacturing process is purification. It involves removing any impurities that may remain in the chemical after the reaction. It can be done through a variety of methods such as precipitation, crystallization, or adsorption.
This step is important as it ensures that the final product is of high quality and meets all the necessary safety and quality standards.
Packaging and Storage
The final step in the chemical manufacturing process is packaging and storage. It involves putting the final product into containers for storage and transport. It is an essential step as it ensures the safety and quality of the product. It also helps to reduce the risk of contamination from outside sources.
Benefits of Using Industrial Chemicals
Industrial chemicals are used in many industries to make products and processes more efficient and to reduce costs. This section outlines the benefits of using industrial chemicals in a variety of industries.
Improved Efficiency: Industrial chemicals are used to improve the efficiency of a variety of processes. For example, they can be used to reduce the time and effort required to manufacture a product or to speed up the process of refining a material.
It can lead to increased productivity and improved profitability for businesses. Additionally, industrial chemicals are often used to reduce the cost of production.
Cost Savings: Industrial chemicals can be used to reduce the cost of production. They can be used to reduce the amount of energy and raw materials needed to produce a product and the cost of labor. It can lead to significant cost savings for businesses.
In addition, industrial chemicals can be used to reduce the cost of waste disposal, as they often break down materials quickly and safely.
Improved Quality: Industrial chemicals can be used to improve the quality of products. For example, they can be used to improve a product's appearance, performance, and durability. This can lead to increased customer satisfaction and improved profitability.
Additionally, industrial chemicals can be used to reduce the environmental impact of manufacturing processes.
Safety: Industrial chemicals are often used to improve a product's or process's safety. For instance, they can be used to reduce the risk of injury or illness caused by exposure to toxins or hazardous materials.
It can help to protect workers and the public from harm. Additionally, industrial chemicals can be used to reduce the risk of fire or explosion.
Versatility: Industrial chemicals can be used in various industries, from agriculture to manufacturing. It means that businesses can benefit from using industrial chemicals regardless of their industry.
Additionally, industrial chemicals can be used for various purposes, from cleaning to lubrication. It makes them a versatile and cost-effective option for businesses.
How Industrial Chemicals Are Used To Innovate In Manufacturing?
Industrial chemicals are used in manufacturing to produce a wide range of products. By using industrial chemicals, manufacturers can create products that are more durable, resistant to damage, and more cost-effective.
- Industrial chemicals are used in a variety of manufacturing processes. They are used to create new products, improve existing products, and develop processes that can be used more efficiently and economically.
- These chemicals can also modify existing products or processes, making them more efficient and cost-effective. For example, industrial chemicals can improve the strength of plastics, making them more durable and resistant to damage.
- Industrial chemicals are also used to create new products. For example, they can be used to develop new drugs, medical devices, and other products. These chemicals can form compounds that are more effective than existing products or make existing products more efficient.
- Industrial chemicals are also used to develop processes that can be used faster and more efficiently. For example, they can be used to create new catalysts or catalytic processes, allowing manufacturers to produce products more quickly and with less waste. These processes can also be used to increase the efficiency of existing processes, making them more cost-effective.
What is MRP for Industrial Gases and Chemicals?
Material Requirement Planning (MRP) is a vital tool in supply chain management (SCM) that helps organizations ensure that they have the right amount of materials at the right time to meet production and customer demands. Industrial gases and chemicals are essential components in the production of many products.
- MRP helps to ensure that the supply of these materials is always sufficient to meet the organization's demands.
- MRP for industrial gases and chemicals works by looking at the demand for these materials and creating a plan to ensure that the organization has enough of these materials to meet the demand.
- The MRP system will track the materials inventory and ensure the organization is not overstocked or running out of materials.
- It will also track the costs of the materials so that the organization can be sure that they are getting the best value for their money.
How Does MRP Work for Industrial Gases and Chemicals?
MRP for industrial gases and chemicals is based on the principles of inventory management. It uses a computer system to keep track of the materials used in the production process.
- The system considers the company's current and future needs, and it helps identify any potential shortages or overages.
- It is also used to create detailed plans for the purchase and storage of materials, as well as to track their usage.
- It includes analyzing current and future demand and the existing inventory. The system then creates a plan for purchasing and storing the required materials and tracking their usage.
The main components of MRP systems include:
- Bill of Materials: Bill of Materials is a list of all the components and materials needed in the production process. The bill of materials contains information such as item numbers, descriptions, and quantities of each item required.
- Production Scheduling: This component of MRP helps in the scheduling of production activities. It uses the bill of materials to determine the order and timing of production activities.
- Inventory Management: MRP systems help track and manage industrial gases and chemicals inventories. It includes tracking the current inventory levels, issuing purchase orders for replenishment, and reserving inventory for specific orders.
- Capacity Planning: Capacity Planning helps plan and schedule the capacity requirements for industrial gases and chemicals production. It helps determine the resources and capacity needed to meet the production requirements.
4 Benefits of MRP for Industrial Gases and Chemicals
1. Improved Inventory Management
MRP helps companies in the industrial gases and chemicals industry to manage their inventory more effectively. With MRP, companies can generate accurate forecasts for their material needs, plan their production and purchase requirements, and monitor their inventory levels.
It ensures that companies always have the necessary materials to meet customer demand. It also eliminates the need to overstock and the risk of running out of needed materials.
2. Improved Accuracy
MRP helps companies to accurately predict customer demands and plan their inventory needs accordingly. It eliminates the need to guess when it comes to inventory planning, which can lead to costly mistakes and unnecessary expenses.
MRP also helps companies accurately plan for their production and purchase requirements, ensuring they always have the necessary materials to meet customer demand.
3. Increased Efficiency
MRP helps companies to streamline their inventory management processes and increase their overall efficiency.
By streamlining their operations, companies can reduce costs and increase profitability. MRP also helps companies reduce their lead times and increase customer satisfaction by ensuring that orders are filled on time.
4. Improved Visibility
MRP helps companies better understand their inventory needs and ensure that their materials are always stocked appropriately. MRP also allows companies to track their inventory levels and monitor their performance.
It helps companies to identify areas where there may be inefficiencies or problems and make necessary adjustments.
Implementing MRP for Industrial Gases and Chemicals
Implementing MRP for industrial gases and chemicals is an important step in ensuring that these materials are used efficiently and effectively. It helps to ensure that the right quantity of materials is ordered at the right time, reduces inventory costs, and helps to maximize inventory turnover.
Create an Effective Inventory Management System: The first step in implementing MRP for industrial gases and chemicals is to create an effective inventory management system. It should include a system for tracking the quantity of materials in inventory and the current stock levels.
It should also include a system for ordering new materials and tracking their delivery. This system should be regularly monitored and updated to ensure that it is kept up to date.
Develop a Clear Production Schedule: An effective MRP system requires a clear production schedule. It should include details of when each material needs to be ordered when it needs to be delivered, and when it should be used in the production process.
The schedule should also include details of when each material should be reordered and when it should be disposed of.
Implement Effective Quality Control Measures: Quality control is essential to any MRP system. It includes ensuring that the materials used in the production process meet the required quality standards.
Quality control measures should also be implemented to ensure that the materials are stored and used safely.
Regularly Monitor and Update the MRP System: Finally, it is important to regularly monitor and update the MRP system to ensure that it is kept up to date. It includes tracking changes in the materials used in the production process and any changes in the production schedule.
Regular monitoring and updating of the MRP system will help to ensure that the system remains effective and efficient.
Challenges Faced by Industrial Gases and Chemicals Industry
The industrial gases and chemicals industry is the backbone of many industrial processes worldwide. It plays an important role in the overall economy by providing essential raw materials for manufacturing a wide range of products.
Despite its importance, the industry has faced several challenges recently, ranging from volatile raw material prices to increasing environmental regulations.
Volatile Raw Material Prices
One of the primary challenges faced by the industrial gases and chemicals industry is the volatility of raw material prices. It can have a significant impact on the profitability of the industry, as the cost of raw materials is a major component of the overall production cost.
The prices of raw materials are affected by a variety of factors, such as global supply and demand, government policies, and currency exchange rates. It makes it difficult for the industry to predict and manage costs, which can lead to unexpected losses.
Increasing Environmental Regulations
Another challenge the industrial gases and chemicals industry faces is the increasing environmental regulations. These regulations are designed to reduce the environmental impact of industrial emissions, such as greenhouse gases and hazardous substances.
While these regulations are necessary to protect the environment, they can add additional costs to production, reducing profitability. Additionally, the industry needs to invest in new technologies and processes to meet the regulations, which can be expensive.
Technology Adoption
The industrial gases and chemicals industry must also be aware of the need to adopt new technologies. The industry is constantly evolving, and new technologies are emerging that can improve the efficiency and effectiveness of the industry's operations.
The industry must be willing to invest in and implement new technologies to remain competitive.
Rising Competition
The industrial gases and chemicals industry also faces increased competition from other industries. It is due to the emergence of new technologies that can produce similar products at lower costs.
Additionally, the industry faces competition from foreign companies, which can produce goods at lower prices due to lower labor and production costs. This is making it difficult for companies in the industry to remain competitive in the global market.
Maintaining Quality
Finally, the industrial gases and chemicals industry must ensure that their products are of the highest quality possible. Quality control is essential for the industry, as it must ensure its products are safe for use and meet the necessary standards.
Quality control also helps to ensure that the industry's products are competitively priced.
How can Deskera Help You?
Deskera software is a cloud-based business software. It is designed to help you manage and streamline your business operations. It offers a complete suite of integrated applications for business management.
These include inventory control, order management, accounting, and more. It is an ideal solution for businesses that need to manage just-in-time manufacturing.
Deskera MRP is the one tool that lets you do all of the above. With Deskera, you can:
- Control production schedules
- Compile a bill of materials
- Produce thorough reports
- Make your own dashboard.
Deskera ERP is a complete solution that allows you to manage suppliers, track supply chain activity in real time, and streamline a range of other company functions.
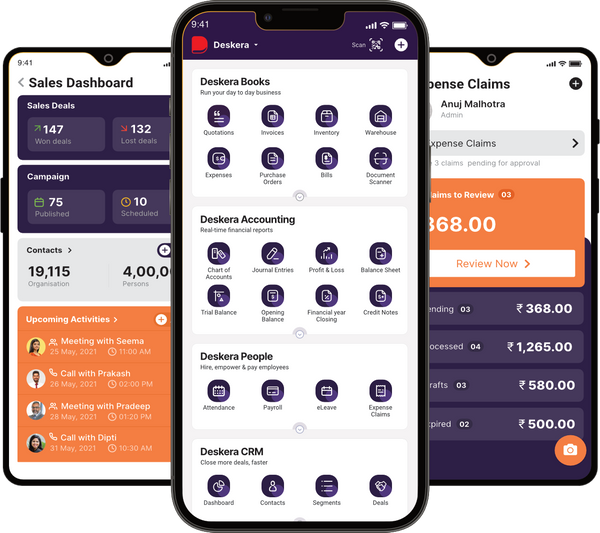
Deskera Books allows you to manage your accounts and finances better. It helps maintain good accounting standards by automating billing, invoicing, and payment processing tasks.
Deskera CRM is a powerful tool that organizes your sales and helps you close deals rapidly. It enables you to perform crucial tasks like lead generation via email and gives you a comprehensive view of your sales funnel.
Deskera People is a straightforward application for centralizing your human resource management activities. Not only does the technology expedite payroll processing, but it also helps you to handle all other operations such as overtime, benefits, bonuses, training programs, and much more.
Conclusion
The industrial gases and chemicals industry has grown tremendously over the past few years. This industry plays a vital role in powering the global economy by providing essential components for industrial and commercial activities.
The industry has seen significant investments in research and development and has been able to develop new products and processes to meet the demands of the global markets. It has been a key factor in driving the growth of the industry.
The outlook for the industry is positive, with the demand for industrial gases and chemicals expected to grow in the coming years. It is due to the growth in the global population and the increasing demand for industrial and commercial products.
MRP for industrial gases and chemicals can be a powerful tool in the manufacturing industry, allowing companies to increase the efficiency and productivity of their production processes. MRP can help companies reduce waste, streamline production processes and maximize resources. It also helps to ensure that companies can effectively manage their inventories and resources.
Key Takeaways
- Utilizing MRP can help industrial gases, and chemicals companies reduce costs, improve customer service, and increase efficiency.
- Material Requirements Planning (MRP) is a key tool for industrial gases and chemicals companies to ensure they have the right materials in the right quantities when needed to meet production demands.
- Industrial gases and chemicals are used in various industries, including food and beverage, automotive, and healthcare.
- The industrial gases and chemicals industry is expected to grow significantly in the coming years due to increasing demand in emerging markets.
- MRP should be integrated with other systems, such as enterprise resource planning (ERP), to provide a comprehensive view of the supply chain.
- MRP is beneficial for industrial gas and chemical companies as it helps them to optimize their production and delivery operations. Additionally, it helps to reduce inventory costs, improve customer service, and identify opportunities for cost savings.
- MRP is essential for effective inventory management. It helps to identify the right inventory levels and ensure that the right products are available at the right time.
Related Articles
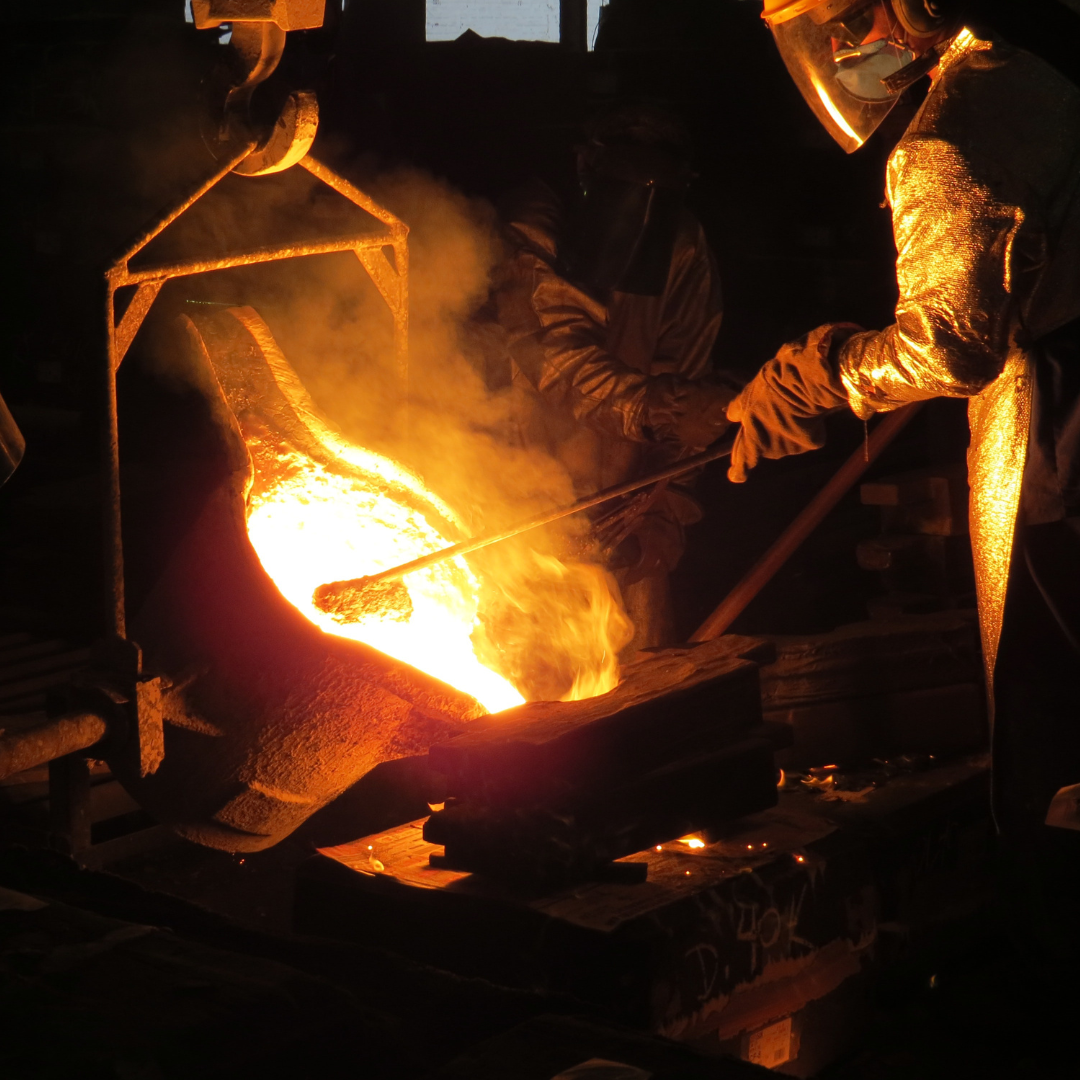
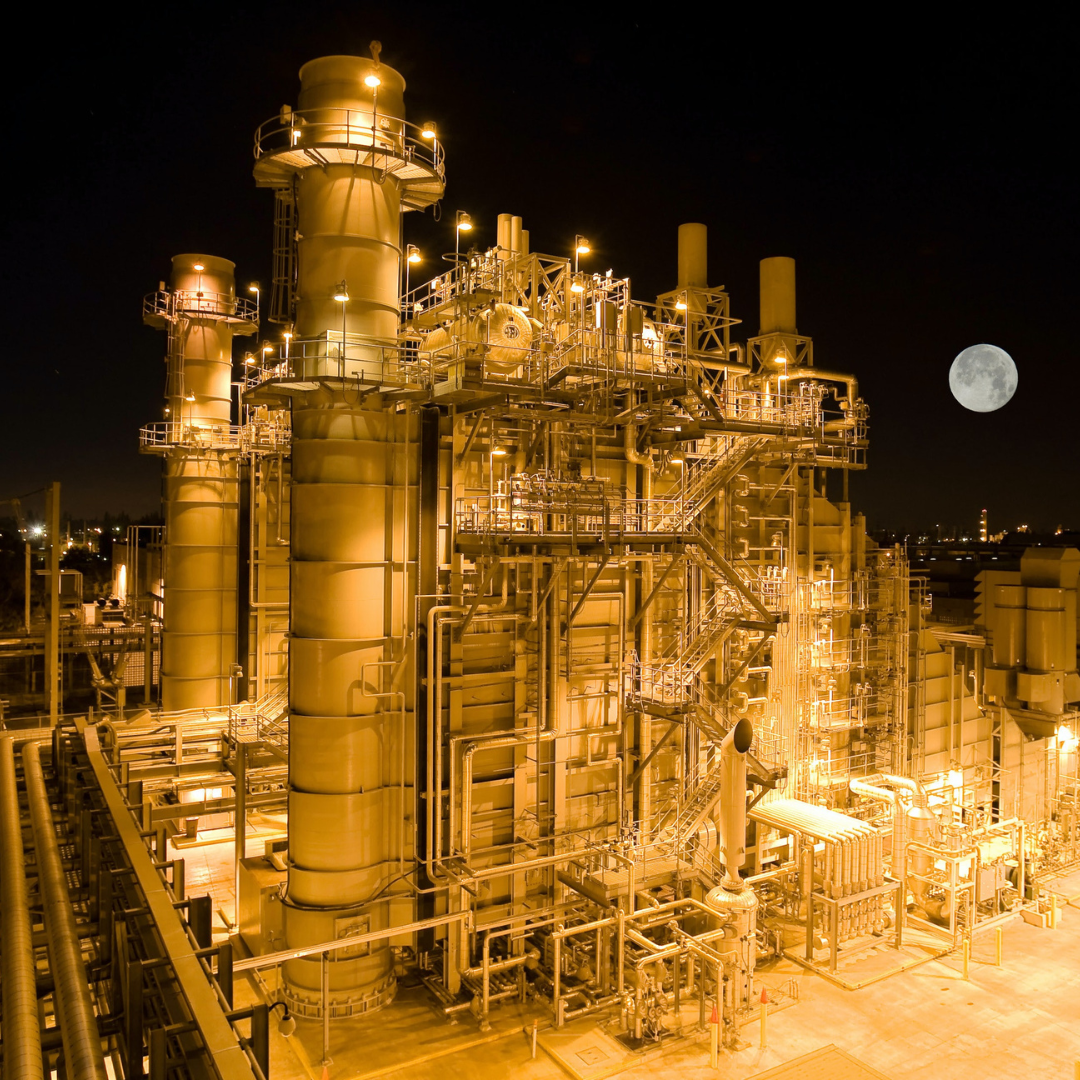
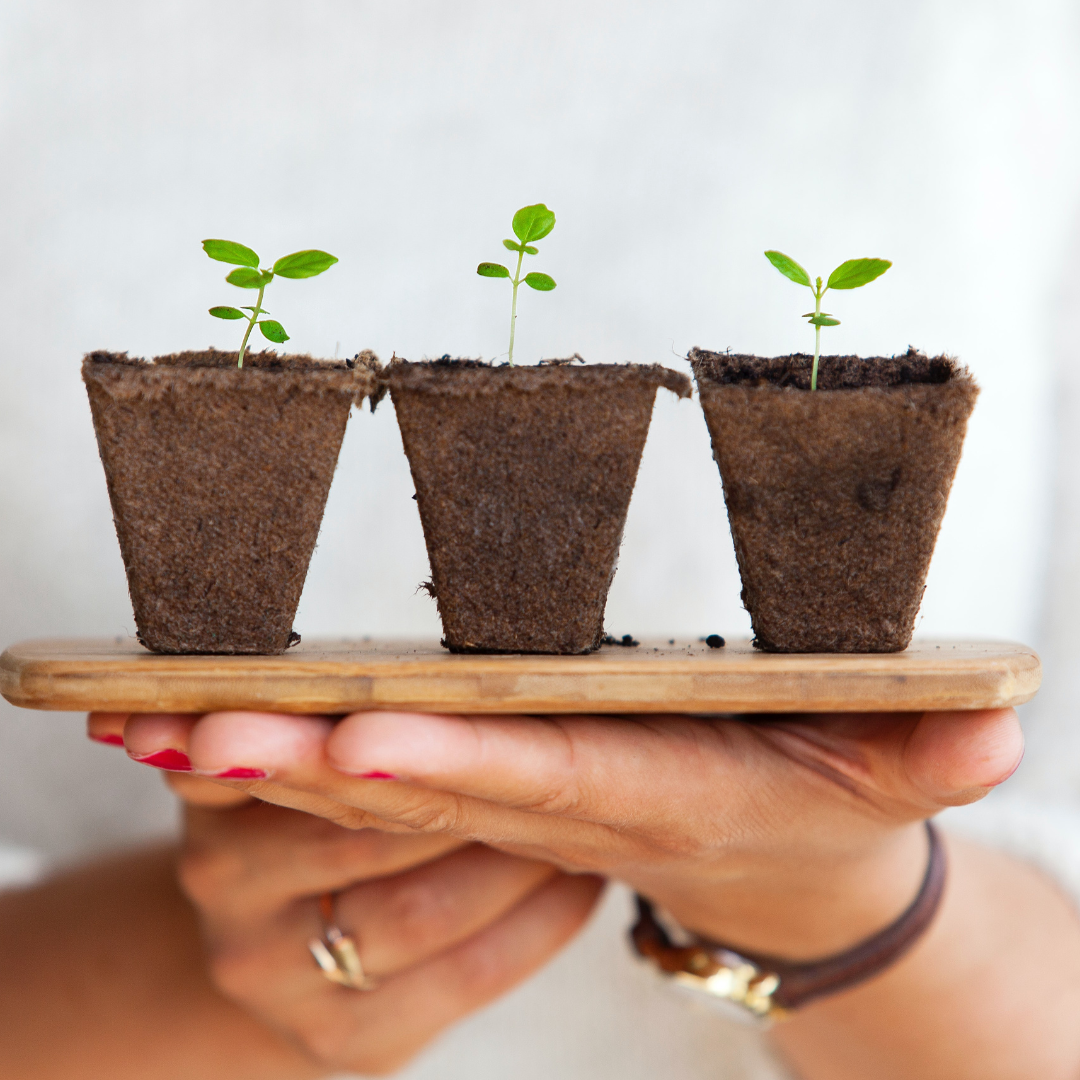
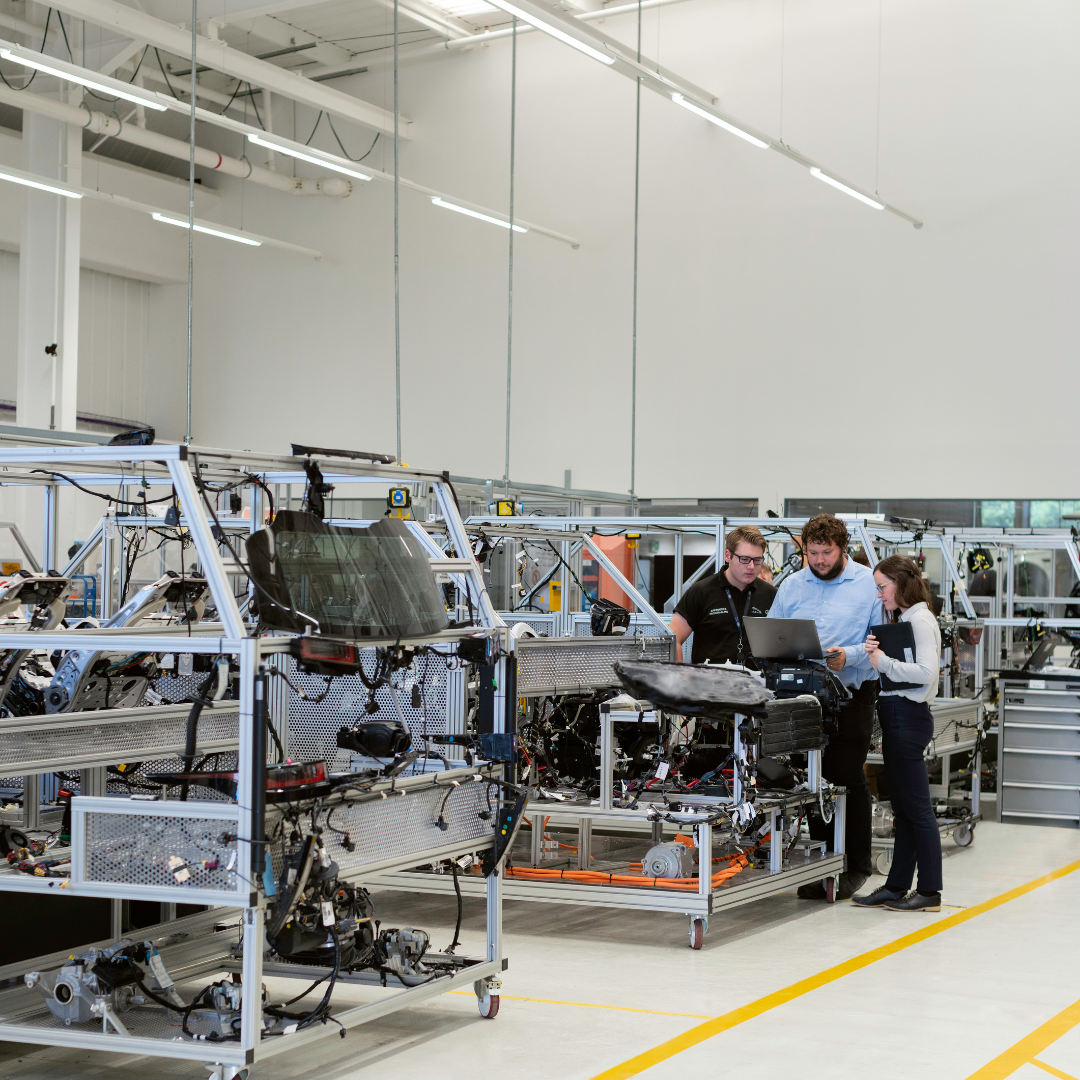