According to a survey by the National Association of Manufacturers, in 2019, 23% of all US manufacturers used Material Requirements Planning (MRP) software to manage their furnace production.
This helpful planning system is designed to help you maximize the efficiency of your furnace operation. With proper planning, you can reduce costs and increase productivity.
MRP for furnaces is designed to save manufacturers time and money. By using this system, manufacturers can reduce the amount of inventory on hand by only ordering what is needed when it is required. It can help to reduce storage costs and stockouts.
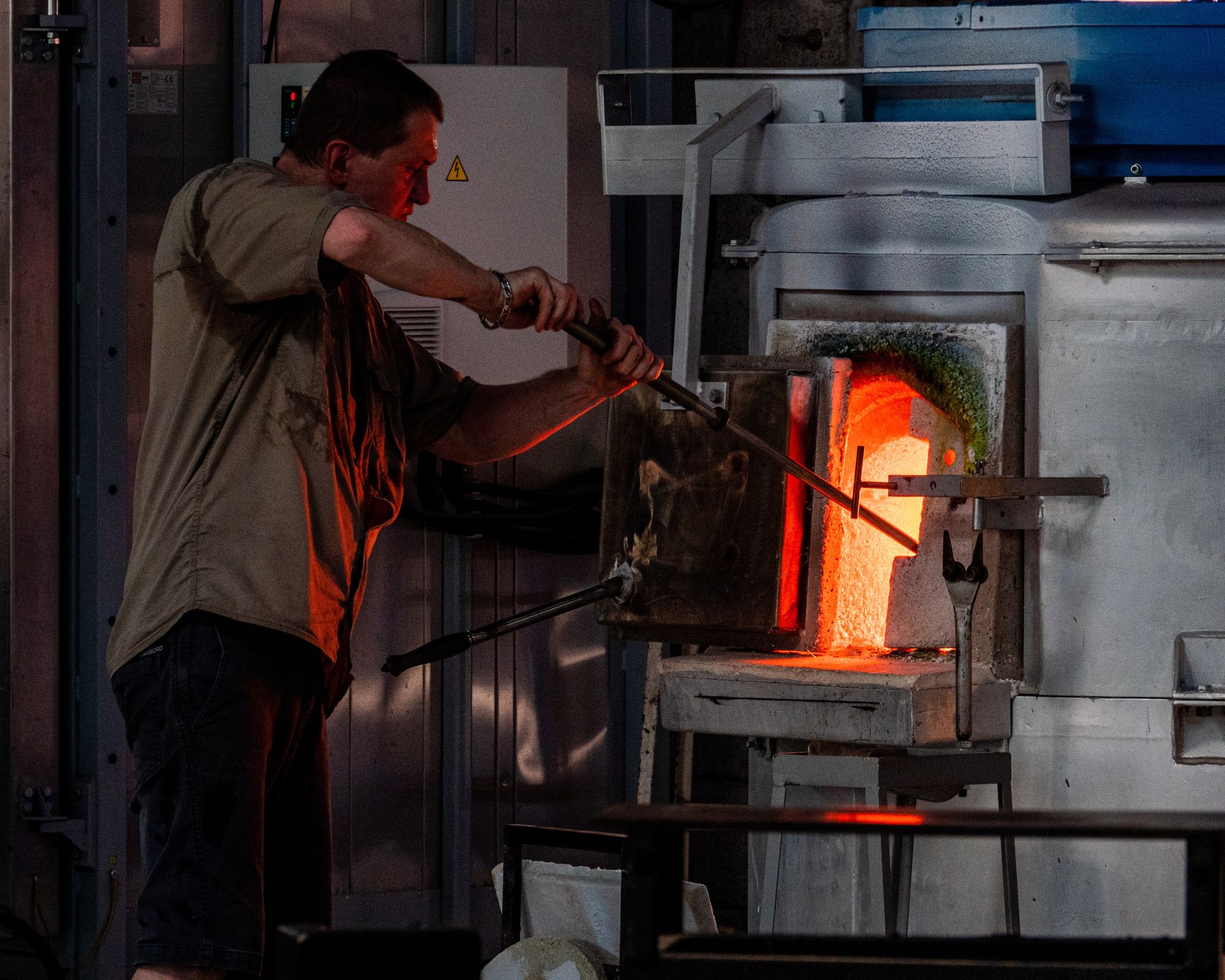
MRP for furnaces also ensures that suitable materials and parts are available when needed, allowing for faster production and shorter lead times.
This article will explore how MRP for furnaces works and how it can help your business streamline production, reduce costs, and increase efficiency.
Here’s what we shall cover in this post:
- What Are Furnaces?
- 5 Benefits of Using Furnaces
- What is MRP for Furnaces?
- Benefits of Using MRP for Furnace Manufacturing
- Implementing MRP for Furnace Manufacturing
- Challenges in Furnace Manufacturing
- Best Practices in Furnace Manufacturing
- Conclusion
- Key Takeaways
What Are Furnaces?
- Furnaces are an essential part of modern homes and businesses. They provide a great source of heat and comfort during the cold winter. furnaces heat homes, offices, other buildings, and industrial and manufacturing facilities.
- A furnace is an appliance that heats the air by burning fuel or using electricity to create hot air. The hot air is circulated through a building or home using air ducts, blowers, and fans. Furnaces are typically used in the winter months to provide heat and comfort.
- Furnaces burn fuel, such as gas, oil, or wood, to generate heat. This heat is circulated throughout the building or home using air ducts, blowers, and fans. furnaces also use electricity to create heat.
- Gas furnaces are the most common type of furnace and use natural gas as their energy source. They are usually more efficient than oil or electric furnaces and can heat a home quickly and evenly.
Types of Furnaces
Furnaces come in various types and models, ranging from simple, basic units to complex, high-efficiency models. Here is a look at the different types of furnaces available:
- Gas Furnaces: Gas furnaces are the most popular type of furnace and use natural gas to heat your home. Gas furnaces are relatively efficient, producing a high heat level while consuming less energy. They are also relatively easy to maintain and can be an excellent choice for homeowners who want to keep their energy costs down.
- Vacuum Furnaces: Vacuum furnaces are used to create high-temperature components. These furnaces combine temperatures, atmospheres, and vacuum to create components. The advantages of vacuum furnaces include the ability to make components with extremely high-temperature tolerances and the ability to create exact components. Disadvantages include the need for specialized equipment and difficulty controlling the temperature precisely.
- Oil Furnaces: Oil furnaces are another popular type of furnace, and they use oil as the fuel source. They are typically used in older homes as they produce a lot of heat and are relatively inexpensive to operate. However, oil furnaces are less efficient than gas furnaces and require more maintenance.
- Heat Treatment Furnaces: Heat treatment furnaces heat and temper materials such as steel, aluminum, and other metals. These furnaces use a combination of heat, atmosphere, and time to change the material's mechanical properties. The advantages of heat treatment furnaces include precise temperature control and uniform heating of the material. Disadvantages include the possibility of overheating, which can cause damage to the material.
- Electric Furnaces: Electric furnaces are becoming more popular in recent years, using electricity to generate heat. Electric furnaces are much more efficient than gas or oil and easy to maintain. However, electric furnaces can be more expensive, so they are usually not the best choice for homeowners on a tight budget.
- Induction Furnaces: Induction furnaces create components through metal casting. These furnaces combine high-frequency alternating current, metal, and heat to develop components. The advantages of induction furnaces include the ability to control the temperature precisely and the ability to create complex shapes and sizes. Disadvantages include the need for a large amount of power and the possibility of overheating.
- Propane Furnaces: Propane furnaces are gas furnaces that use propane as the fuel source. Propane furnaces are relatively efficient and relatively easy to maintain. They are also fairly inexpensive to operate, making them an ideal choice for homeowners who want to keep their energy costs down.
- Heat Pumps: Heat pumps are a type of furnace that uses a compressor to move heat from one area to another. Heat pumps are highly efficient, and they can be used to both heat and cool your home. Heat pumps are an excellent choice for homes in mild climates, as they can help reduce energy costs.
- Wood Furnaces: Wood furnaces are a type of furnace that uses wood as the fuel source. Wood furnaces are relatively efficient and can be an excellent choice for homes in rural areas. However, wood furnaces require more maintenance than other types and can be more expensive.
- Arc Furnaces: Arc furnaces are used to create components through metal melting. These furnaces combine an electric arc and heat to develop components. Advantages of arc furnaces include the ability to make components with extremely high-temperature tolerances and the ability to create components with high levels of accuracy. Disadvantages include the need for specialized equipment and the possibility of producing components with impurities.
No matter which type of furnace you choose, it's essential to research and find the best option for your home. Be sure to consider your budget, the efficiency of the furnace, and your maintenance requirements when deciding which type of furnace is best for you.
Manufacturing Processes Used in Furnace Manufacturing
Manufacturing processes are the steps used to produce goods or services. furnace manufacturing is a complex process that requires the use of a variety of specialized manufacturing processes. This section will discuss the different manufacturing processes used in furnace manufacturing.
- Casting: Casting is a common manufacturing process used to produce parts with complex shapes. This process involves shaping molten metal into a desired shape and then allowing it to cool and solidify. Furnace manufacturers often use this process to create components with intricate designs. In this process, a furnace is used to heat the metal to the melting point and then poured into a mold to form the desired shape.
- Forging: Forging is another popular process used in furnace manufacturing. This process involves hammering or pressing metal into a desired shape. Furnace manufacturers often use this process to create components that require high strength and durability. The metal is heated in a furnace and then hammered or pressed into the desired shape.
- Welding: Welding is a manufacturing process combining two or more metal pieces. This process involves heating the metal until it is malleable, then pressing it with a welding torch.
- Machining: Machining is a manufacturing process that shapes and forms metal into a desired shape. This process involves cutting, drilling, grinding, and turning the metal to create the desired shape. Furnace manufacturers often use machining to develop components that require precise measurements.
- Fabrication: Fabrication is a manufacturing process to create components from raw materials. This process involves cutting, bending, and assembling pieces of metal to create the desired shape. Furnace manufacturers often use fabrication to develop components that require complex designs.
- Finishing: Finishing is a process used to add a protective coating to components. This process involves applying a protective coating to the component to protect it from corrosion and damage. Furnace manufacturers often use finishing to create components that require a long lifespan.
Overall, furnace manufacturing is a complex process that requires the use of a variety of specialized manufacturing processes. Casting, forging, welding, machining, fabrication, and finishing are some of the most commonly used manufacturing processes in furnace manufacturing. Each process plays an essential role in the production of high-quality components.
5 Benefits of Using Furnaces
- Energy Efficiency: Furnaces are one of the most energy-efficient heating options available. They are designed to provide maximum heating with minimal energy consumption, resulting in lower energy bills. Additionally, newer furnaces include variable-speed motors, electronic ignition, and programmable thermostats, which all help reduce energy consumption even further.
- Reliability: Furnaces are incredibly reliable and designed to last many years with proper maintenance. They are also relatively easy to maintain, with simple tasks such as changing filters and cleaning burners that can be done regularly. It helps to ensure your furnace is running at its optimal level, so you can be sure you'll have heat when needed.
- Cost-Effectiveness: Furnaces are inexpensive to purchase and install and often much cheaper than other heating systems. Additionally, they are very energy-efficient, so you can expect to save money on your energy bills over the long term.
- Safety: Furnaces are also a very safe heating option, as they are enclosed and don't produce any open flames or sparks. It helps prevent fires and carbon monoxide poisoning, two of the most common dangers of heating systems.
- Convenience: Furnaces are incredibly convenient, as they can be easily turned on and off with the flip of a switch. It means you can easily adjust the temperature in your home to suit your needs, whether it's a cold winter night or a warm summer day.
These are just a few of the many benefits of using furnaces for home heating. They are energy-efficient, reliable, and cost-effective, and they are also incredibly safe and convenient. A furnace may be the perfect choice if you're looking for a reliable and efficient heating system.
Application of Furnaces
The furnace is a device or system used for heating a building or a room. This device has been used since the Roman and Greek times and is still in use today. Furnaces are used in many different applications ranging from residential to industrial, automotive, and other benefits. The following section will discuss seven of the most common furnaces applications today.
Residential Applications
Residential applications of furnaces are by far the most common. Furnaces are used to keep homes warm and comfortable. They are available in various sizes and designs and can be used with multiple fuels, including natural gas, propane, and electricity. Furnaces are also used to heat water for hot water tanks.
Industrial Applications
Furnaces are also used in industrial settings. They commonly produce steel, aluminum, copper, and other metals. furnaces are also used in the production of glass and ceramics. They can also be used to heat and treat materials for specific applications.
Automotive Applications
Furnaces are also used in automotive applications. They heat engine parts and components and treat engine oils and other fluids. Furnaces also create parts such as catalytic converters, spark plugs, and other components.
Food Processing
Furnaces are also used in the food processing industry. They are used to heat and process food products such as meats, poultry, and dairy products. Furnaces are also used to heat and process other food products, such as fruits and vegetables.
Plastics Manufacturing
Furnaces are also used in the plastics manufacturing industry. They are used to heat and process plastics and other materials used in the production of plastic products. Furnaces also heat and treat plastic resins and other materials used to produce plastic products.
Glass Manufacturing
Furnaces are also used in the glass manufacturing industry. They are used to heat and process glass and other materials used to produce glass products. Furnaces heat and treat glass and other materials used to produce glass products.
Chemical Processing
Furnaces are also used in the chemical processing industry. They are used to heat and process chemicals and other materials used in the production of chemical products. Furnaces also heat and treat chemicals and other materials used to produce chemical products.
What is MRP for Furnaces?
Material Requirement Planning (MRP) is a type of software used in the manufacturing industry to manage production. It helps in planning, scheduling, and controlling the production process from the beginning of the process to the end.
- In furnace manufacturing, MRP manages the entire process of producing a furnace. It begins with the planning phase, in which the production requirements are determined. It includes the quantity and type of materials needed, the time frame for production, and any other specific requirements.
- The MRP system then creates a plan for the production process and schedules the materials that need to be purchased and delivered on time. The next step is the scheduling phase, in which the MRP system creates a detailed timeline for the production process. It includes the sequence in which each step in the process should be completed.
- The MRP system also ensures that the materials are available in the right quantities and at the right time to meet the production requirements. Once the production process is completed, the MRP system monitors the progress of the furnace production.
- It can detect any problems in the production process and alert the appropriate personnel so that they can take corrective action. It ensures that the production process runs smoothly and efficiently.
Benefits of Using MRP for Furnace Manufacturing
Material Requirement Planning (MRP) is a tool used by furnace manufacturers to ensure efficient production and inventory management. It is an automated process that considers the availability of materials, labor, and equipment to ensure that all resources are used efficiently and cost-effectively. This section will discuss the benefits of using MRP for furnace manufacturing.
- Improved Forecasting Accuracy: MRP systems use historical data to help manufacturers accurately forecast the materials, labor, and equipment needed for production. It helps to reduce the risk of over or under-stocking materials and allows for better control of production costs. With accurate forecasting, manufacturers can also plan for unexpected changes in customer demand.
- Streamlined Production Scheduling: MRP systems can track the availability of materials, labor, and equipment in real-time to ensure that production runs smoothly. It helps to reduce production delays, allowing manufacturers to meet customer deadlines and save time and money.
- Improved Inventory Management: MRP systems can track inventory levels in real-time, helping manufacturers ensure that suitable materials are available when needed. It prevents over or under-stocking, leading to cost savings and increased efficiency.
- Cost Savings: By using an MRP system, furnace manufacturers can reduce their production costs by reducing the number of wasted materials, labor, and equipment. Additionally, they can reduce the cost of purchasing materials by ensuring that they only order the needed quantity.
- Increased Efficiency: MRP systems can automate ordering, scheduling, and inventory tracking processes. It helps to reduce the amount of time and effort required to manage production, leading to increased efficiency and cost savings.
Implementing MRP for Furnace Manufacturing
Develop a Bill of Materials (BOM)
The first step in implementing MRP for furnace manufacturing is to create a Bill of Materials (BOM). This document lists all the parts, components, and materials required for furnace manufacturing. It should include the quantity and description of each item, the estimated cost, the lead time, and the supplier.
Establish Inventory Levels
The second step in implementing MRP for furnace manufacturing is establishing inventory levels. It involves determining the minimum and maximum levels of each item in stock. It helps ensure enough materials and components are available to meet customer demand. It also helps to prevent overstocking, which can lead to unnecessary costs.
Monitor Demand
The third step in implementing MRP for furnace manufacturing is to monitor demand. It involves keeping track of customer orders and production schedules. It helps ensure enough materials and components are available to meet customer demand. It also helps to identify potential demand changes that may require additional planning.
Calculate Lead Time
The fourth step in implementing MRP for furnace manufacturing is calculating lead time. It involves determining the time it will take for each item to be delivered. Lead time should be taken into consideration when planning the production process.
Review Data
The fifth step in implementing MRP for furnace manufacturing is reviewing the collected data. It includes reviewing the BOM, inventory levels, demand, and lead time. It helps ensure that the MRP system runs efficiently and meets customer requirements.
Make Adjustments
The sixth step in implementing MRP for furnace manufacturing is to make adjustments. It involves making necessary changes to the system to ensure it works as efficiently as possible. It may include changing inventory levels, lead time, and customer orders.
Monitor Progress
The final step in implementing MRP for furnace manufacturing is to monitor progress. It involves tracking the system's progress to ensure it meets customer requirements. It also helps to identify any problems or areas for improvement.
Implementing MRP for furnace manufacturing can be a complicated process. However, following these steps ensures that the system runs efficiently and meets customer requirements. With proper planning and monitoring, MRP can help to streamline the manufacturing process and increase profitability.
Challenges in Furnace Manufacturing
Furnace Manufacturing is a highly complex and challenging process. Companies must clearly understand the challenges associated with the furnace manufacturing process to ensure that the furnace they produce meets their and customers' needs.
- Cost of Materials: One of the significant challenges in furnace manufacturing is the cost of materials. The cost of raw materials used in the manufacturing process can vary depending on the type of furniture produced and the required quality. Companies must ensure they can source the required materials at an affordable cost to remain competitive and profitable.
- Quality Control: Quality control is essential in furnace manufacturing. Companies must ensure that all the components are of the highest quality and meet industry standards. It can be difficult and time-consuming as it requires careful inspection of each component and adherence to tight production schedules.
- Safety: Safety is also a significant challenge in furnace manufacturing. As the furnace is a heat-emitting device, it is vital to ensure proper safety measures are in place to protect workers and the environment. It includes proper safety equipment, adequate ventilation, and fire suppression systems.
- Design and Development: Designing and developing a furnace is another challenge that companies face. It is essential to consider the type of furnace produced, the materials used, and the desired output. Companies must also ensure that the design is efficient and safe to be used effectively.
- Scheduling: Scheduling is one of the most difficult challenges companies face when manufacturing a furnace. Companies must ensure they meet production deadlines and complete the project on time. It requires careful planning and coordination between the different departments involved in the process.
Best Practices in Furnace Manufacturing
Furnace Manufacturing is a complex and specialized process that requires a high level of expertise and experience. Companies must ensure that their furnace manufacturing processes are up-to-date and adhere to the highest standards of quality to ensure that the products manufactured are consistent and meet customer expectations.
The best practices in furnace manufacturing involve using advanced technologies, efficient processes, and a rigorous quality control system. This section will look at some of the best practices that should be followed in furnace manufacturing to ensure the production of high-quality products.
Use of Advanced Technologies
Advanced technologies is an essential factor in furnace manufacturing. Using modern technologies such as computer-aided design (CAD) and computer-aided manufacturing (CAM) can help improve the accuracy and efficiency of the manufacturing process.
These technologies allow for precise measurements, which can help reduce the time and cost associated with producing high-quality products. Additionally, 3D printing technology can further reduce the time and cost associated with the production process and improve the parts' accuracy.
Efficient Processes
The production process should be designed to be as efficient as possible to maximize the output of high-quality products. Companies should strive to use the most efficient production methods and processes. It includes using automated machines and robots to reduce the need for manual labor.
Additionally, the use of lean manufacturing principles can reduce the amount of waste and increase efficiency. Companies should also strive to implement just-in-time manufacturing, which allows them to reduce inventory costs and improve production throughput.
Quality Control System
Another critical factor in furnace manufacturing is implementing a rigorous quality control system. Companies should establish detailed quality control protocols and procedures throughout production.
It includes visual inspections, dimensional measurements, and sophisticated testing equipment to ensure that the parts produced meet all of the required specifications. Companies should also have a process to address any problems arising during production.
How can Deskera Help You?
Deskera software is a cloud-based business software. It is designed to help you manage and streamline your business operations. It offers a complete suite of integrated applications for business management.
These include inventory control, order management, accounting, and more. It is an ideal solution for businesses that need to manage just-in-time manufacturing.
Deskera MRP is the one tool that lets you do all of the above. With Deskera, you can:
- Control production schedules
- Compile a bill of materials
- Produce thorough reports
- Make your own dashboard.
Deskera ERP is a complete solution that allows you to manage suppliers, track supply chain activity in real time, and streamline a range of other company functions.
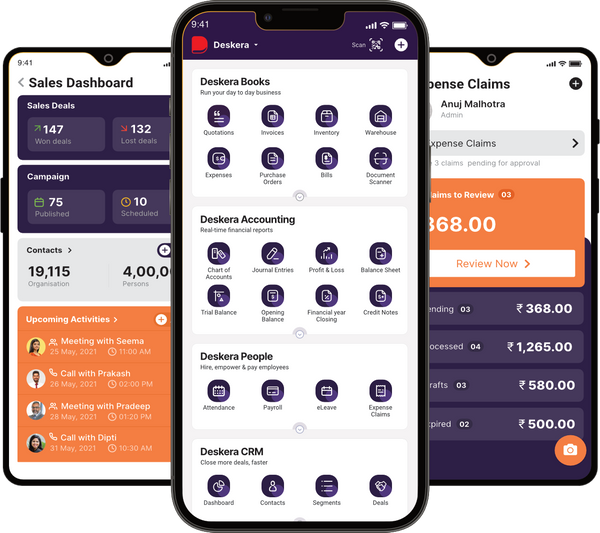
Deskera Books allows you to manage your accounts and finances better. It helps maintain good accounting standards by automating billing, invoicing, and payment processing tasks.
Deskera CRM is a powerful tool that organizes your sales and helps you close deals rapidly. It enables you to perform crucial tasks like lead generation via email and gives you a comprehensive view of your sales funnel.
Deskera People is a straightforward application for centralizing your human resource management activities. Not only does the technology expedite payroll processing, but it also helps you to handle all other operations such as overtime, benefits, bonuses, training programs, and much more.
Conclusion
Furnace manufacturing is an essential part of the industrial world. It has been an integral part of the manufacturing process for many years and is continuing to evolve. The variety and complexity of modern furnaces are constantly increasing, as are their applications.
While the cost of purchasing a furnace can be high, the potential savings in energy costs can be an excellent investment. Furnaces are also increasingly being used to help reduce pollution and improve air quality. MRP for furnaces is based on three fundamental principles: forecasting, inventory management, and scheduling.
Forecasting predicts future demand and identifies potential shortages or excesses in materials and parts. This helps manufacturers to better plan and prepare for future production needs. Inventory management ensures that the right parts and materials are available in the right quantities and quality when needed. Scheduling ensures that production runs smoothly and is completed on time.
As technology continues to improve, so too will the industry of furnaces manufacturing, leading to even more efficient and reliable products. Clearly, the furnaces manufacturing industry has a bright future and will continue to be a vital part of our everyday lives.
Key Takeaways
- The furnace manufacturing industry is an important sector of the global economy, providing jobs, products, and services to many businesses and consumers. The industry is highly competitive, and manufacturers must continuously innovate.
- To properly plan for furnace material requirements, it is crucial to understand the furnace's production process and its associated materials.
- The furnace's Bill of Materials should be reviewed and updated regularly, as it provides the basis for the MRP process. It is also essential to have accurate inventory data for all furnace-related materials to ensure that the MRP system can adequately plan for future demand.
- MRP systems for furnaces can also be used to track costs associated with materials, labor, and other costs related to production, allowing for improved cost management.
- MRP systems for furnaces can also be used to track the quality of materials and production, allowing for better quality control.
- MRP systems for furnaces are also beneficial in that they can help reduce lead times for production and delivery, allowing for faster production and delivery of items.
- MRP systems for furnaces can also be used to manage supply chains, allowing for better control and visibility into sourcing materials and components.
Related Articles
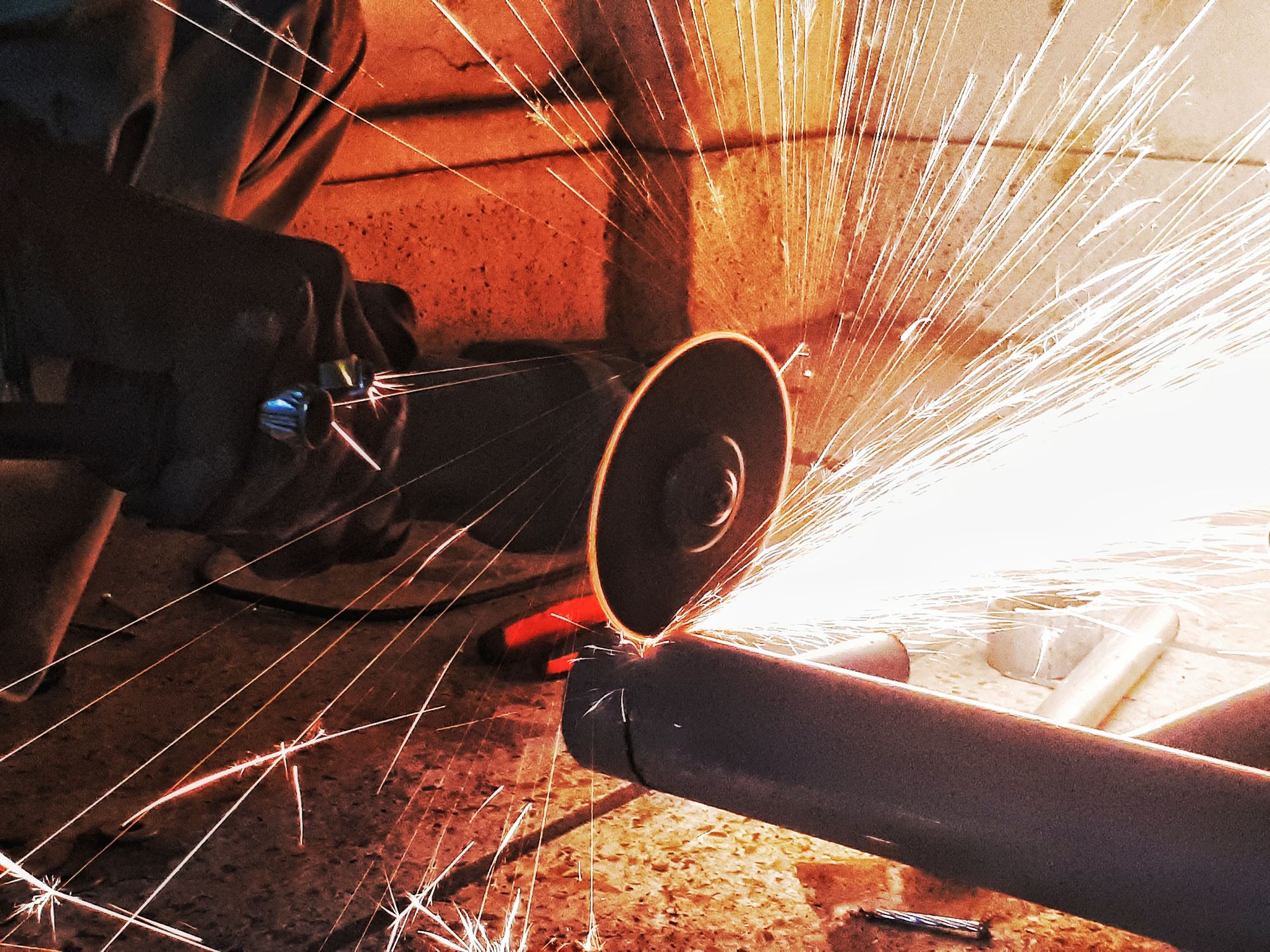
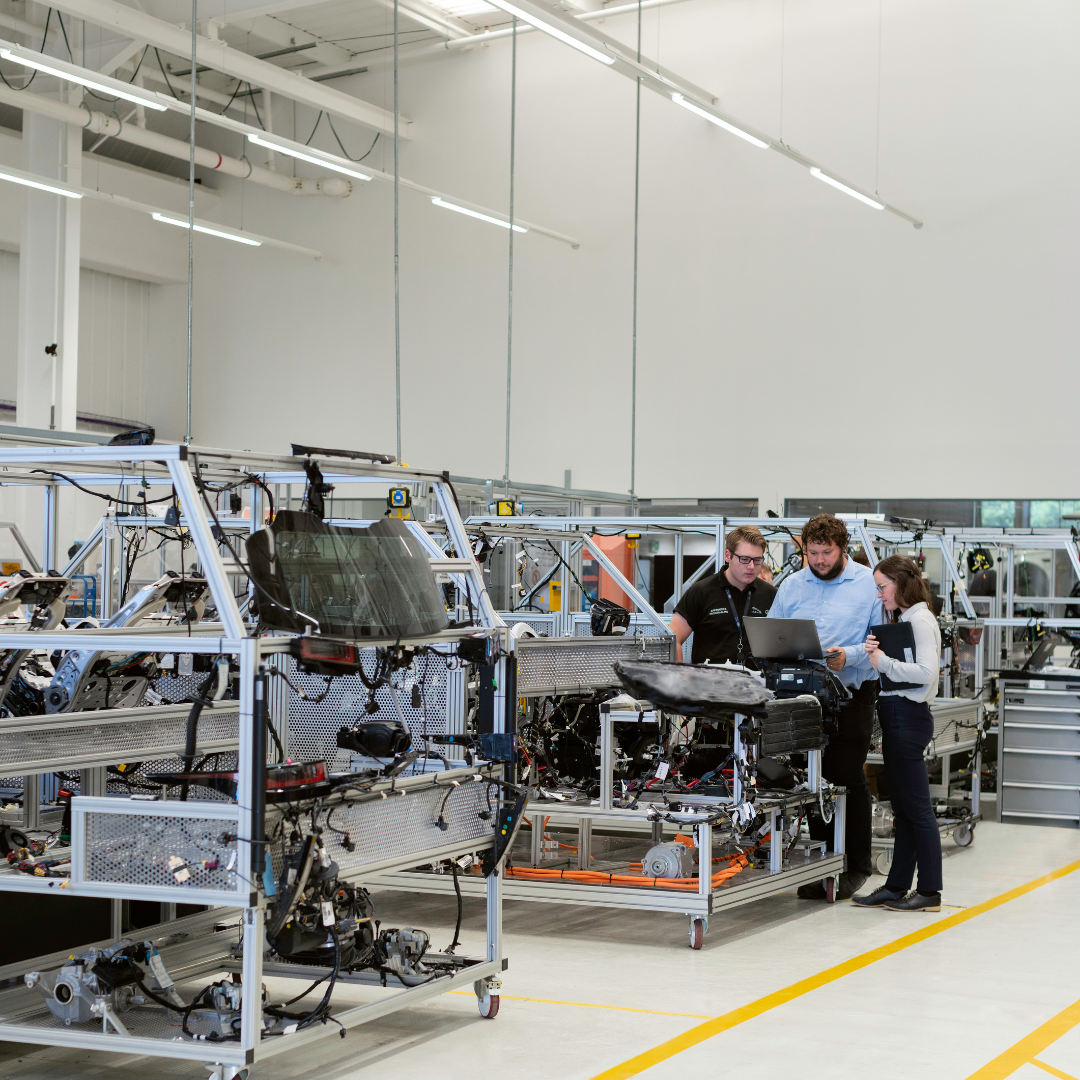
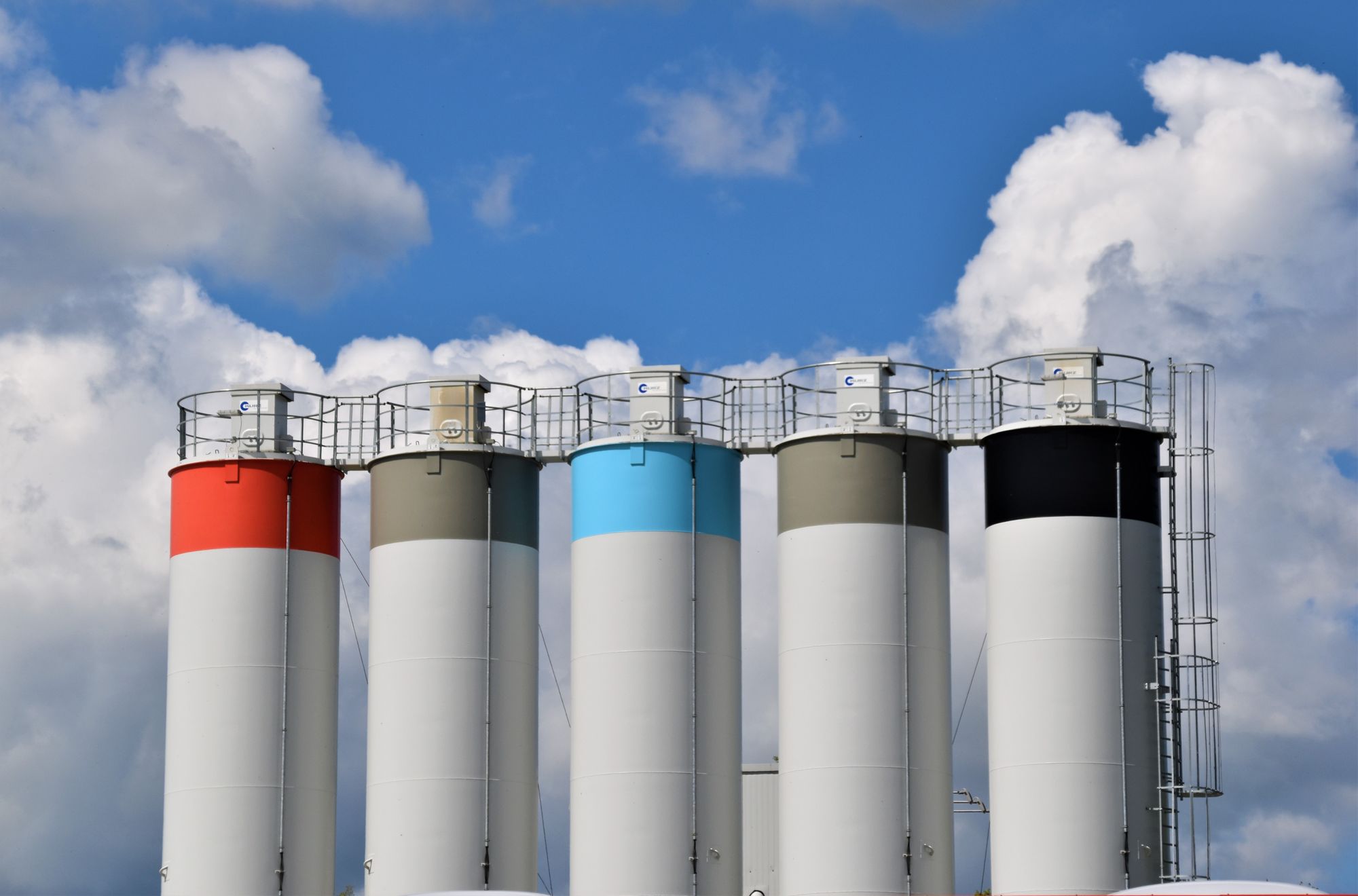
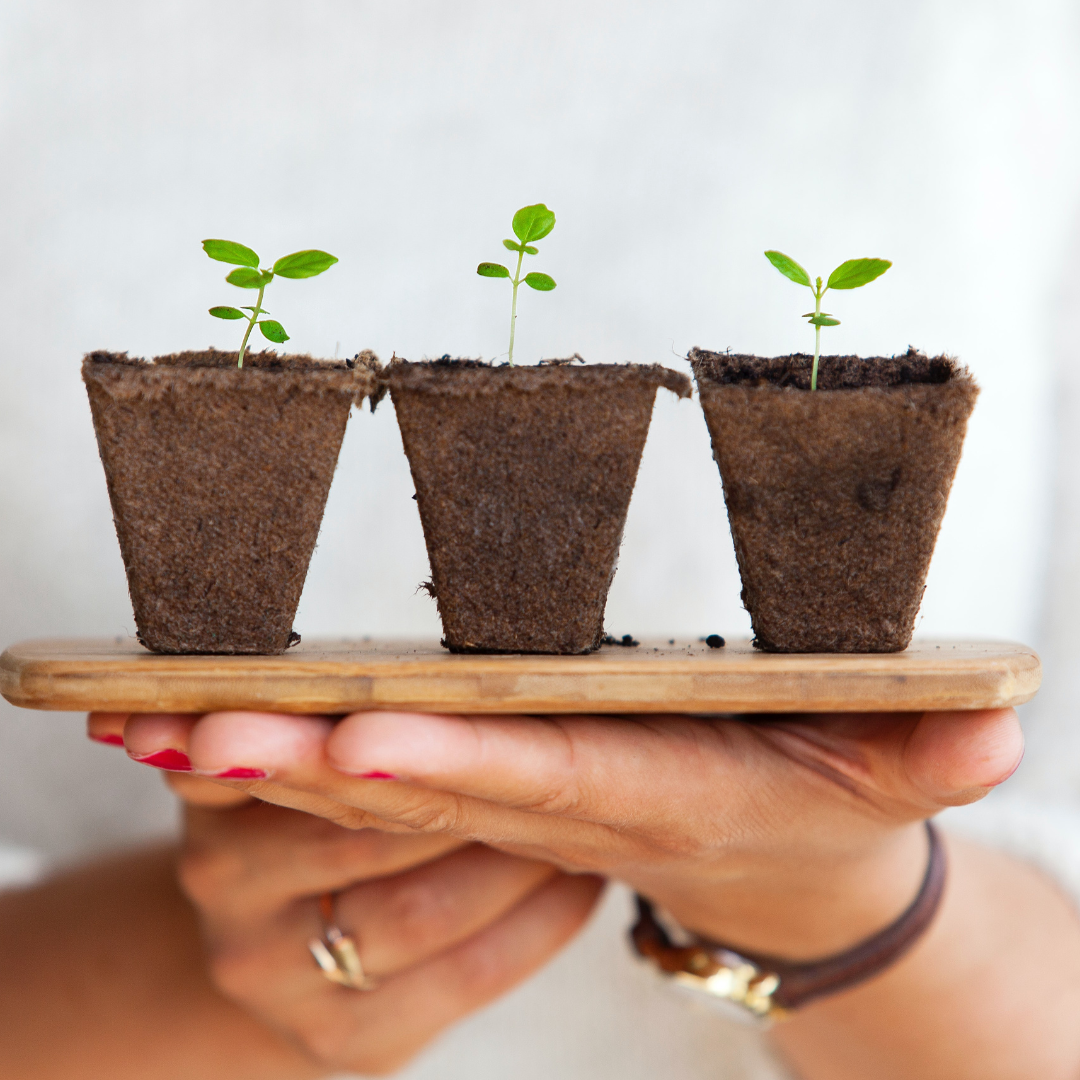