Capacity utilization for the overall industry moved up in 2021 and early 2022. Both manufacturing and mining contributed to the rise.
If you were to ask a normal person what percentage they think a manufacturing plant would need to produce in relation to its maximum. They might respond with 100%. This wouldn't be the case. The middle ground between excessive and inadequate production is optimal capacity utilization.
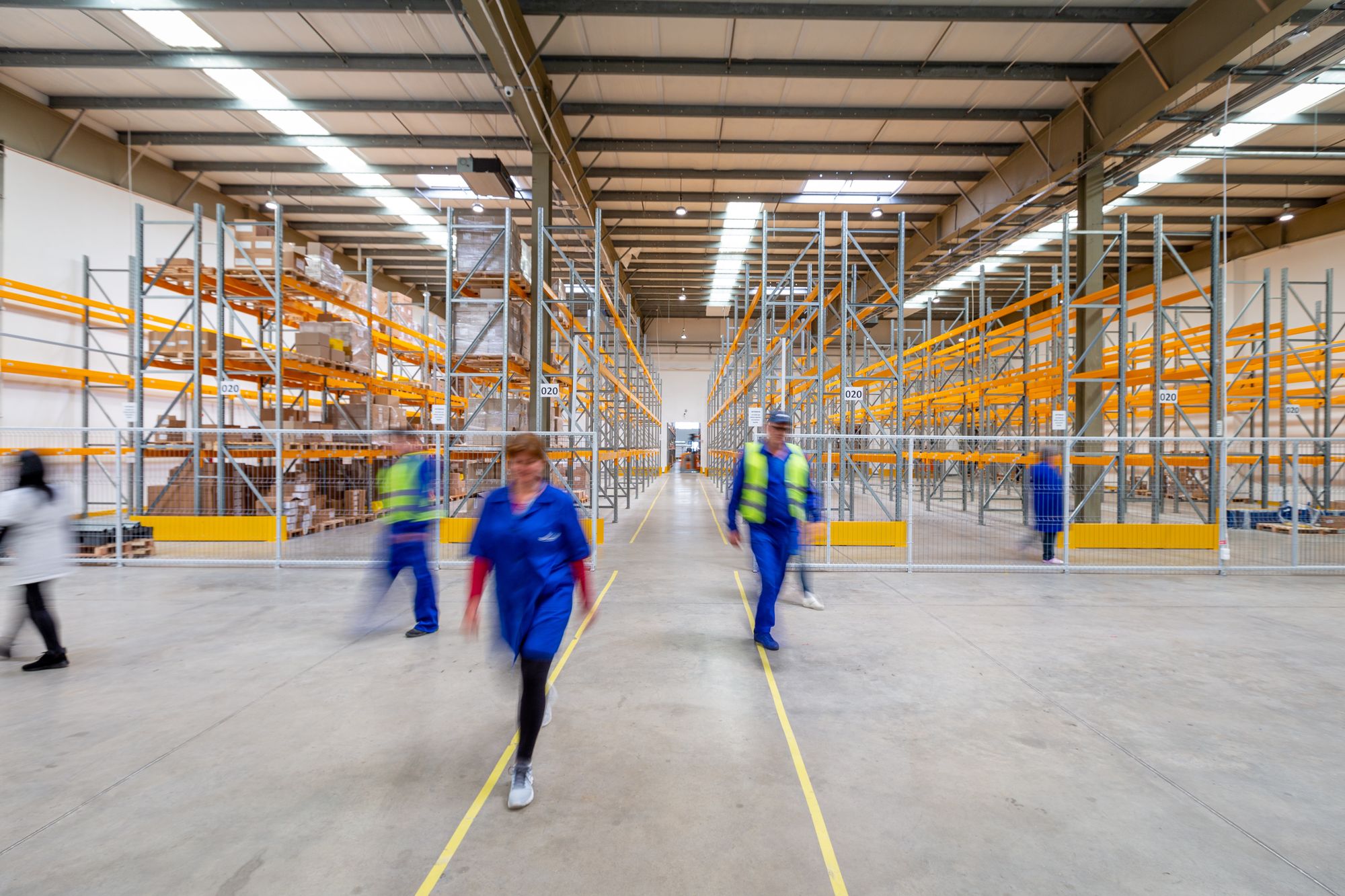
Bottlenecks, waste, and inefficiency are likely to occur in a factory if it operates at 100% output. Yet, if a factory only produces at 50% of its potential, it is wasting money on underutilized resources.
Finding a balance between capacity overuse and under-use should be the aim of any firm which can be done by proper capacity utilization. Capacity utilization is the extent to which a firm or nation employs its installed productive capacity.
In this article, we go through capacity utilization, its calculation, and the reasons it's a crucial indicator for understanding business and economic activities. Following are the topics covered:
- What Is Capacity Utilization?
- How to Calculate the Capacity Utilization Rate?
- Corporate Capacity
- Importance of the Capacity Utilization Rate
- How to Improve Capacity Utilization in Business?
- Effects of Low Utilization
- What Is Manufacturing Capacity Utilization?
- Economic Significance of Capacity Utilization
- Conclusion
- Key Takeaways
What Is Capacity Utilization?
The production and manufacturing resources that a country or business is using at any particular time are referred to as capacity utilization. It describes the link between the output generated with the available resources and the products that might be generated if capacity were completely utilized.
Another way to think of capacity utilization is as a measurement of how quickly projected levels of output are being reached or consumed. The rate, which is shown as a percentage, offers insight into resource use overall. It also shows how a business can boost output without raising production expenses.
The operating rate is another name for the capacity utilization rate. As determining the rate for the latter is significantly more difficult, capacity utilization is a KPI. The rate for the latter is utilized in sectors that create physical things rather than services. Governments also utilize it to map the economic potential of respective sectors.
Understanding Capacity Utilization
Economists use capacity utilization as a key statistic to assess how well enterprises, organizations, and economic entities utilize resources to produce outputs. The estimated rate can reveal a lot about how effectively a business operates. The metric is used to measure the effectiveness of a business to achieve its objectives.
Based on market and consumer demand, capacity utilization yields a percentage that is based on the number of employees. This percentage provides insight into a company's operational effectiveness.
The utilization rates are used to check how industries are faring in the current economic climate. For instance, since the 1960s, the U.S. Federal Reserve has released rates for the American economy. As a result of their conclusions, authorities may modify their fiscal or monetary policies.
- If the percentage is less than 100%, the organization is not operating at its maximum capacity.
- Business executives can use the capacity utilization rate to determine how well an organization is using its total production capacity. The utilization rate can also be used to determine how much production can be increased without incurring additional costs for new equipment.
- Economists use it to check how an economy's industries are doing in relation to the general state of the economy. Depending on the result, fiscal and monetary policies may need to be modified.
- Industries that create tangible goods rather than services are those that are dependent on the capacity utilization of resources. These industries are those where capacity utilization is most essential.
- The Federal Reserve in the United States monitors capacity utilisation rates in 89 industries. These industries are part of the manufacturing, mining, and utility sectors.
In an IT system, any resource and its purpose may be referred to as capacity utilization. When evaluating how well hardware, software, or IT installations are performing for the business, many CIOs and CTOs may use this as a key performance indicator.
What Is the Capacity Utilization Ratio?
The capacity utilization rate evaluates how quickly a nation or business uses its levels of economic output. It is indicated by the share of economic output that a nation actually produces over time.
If the capacity utilization rate is less than 100%, the company or nation has not used up all of its installed production capacity. To increase their economic output, businesses or economies in this category can utilize the underused part of their production capacity.
This is a common practice in the United States and Canada. The capacity utilization rate is a crucial indicator that links economic production to a country's level of productivity.
The ratio discusses two distinct elements.
- The first is the company's actual output.
- The second is the maximum production a business can produce in a specific time frame.
We could find out how much a manufacturing company produced during the course of a month, for instance, by keeping an eye on it. The company's capacity to provide can then be evaluated. These two might be compared to get a sense of how much of the company's capacity was used during the month.
- An organization can improve its production if its capacity utilization is below 100%.
- If we take a different approach, we can also see that this utilization rate describes how much slack a company is operating at a given time.
Historical Capacity Utilization Rates
The Federal Reserve compiles and disseminates information on the capacity utilization of the American economy. The Federal Reserve handles the capacity utilization of the American economy. The Fed actually determines capacity utilization rates for 89 industry sub-sectors. These include 71 in manufacturing, 16 in mining, and 2 in gas and electric utilities.
Deep in the COVID-19 epidemic in the fourth quarter of 2020, the Fed calculated a revised capacity utilization rate for all of the U.S. industry at 73.4%.
Capacity Utilization Rate Formula
You may determine the capacity utilization rate using the capacity utilization formula:
Capacity utilization = (actual output level / potential output) x 100
The formula's "actual output level" refers to the number of units a business or economy produces over a given time frame. The potential output is the level of productivity that businesses and economies can reach when all available resources are utilized. This is achieved without increasing operating costs.
Significance of Capacity Utilization Rate Formula
It is obvious that capacity utilization is a key factor in the company's success. It provides a clear picture of the company's operating performance. The firm's operational efficiency will increase as the utilization rate rises.
Even the capacity utilization rate has a significant impact on the company's economic strategies. When formulating economic policies, decision-makers consider a firm's capacity utilization. This is to determine how to encourage the use of capacity across the entire economy.
How to Calculate the Capacity Utilization Rate?
Finding a manufacturing operation's actual output level is the first step in calculating the capacity utilization rate. To do this, information about the capacity of the current workforce, machinery, and supplies must be collected from purchase reports, inventory movements, cycle times, etc.
Similar verification is required for the manufacturing capacity or maximum possible output. Analyzing indicators like daily productive hours, product throughput times, etc. can help with this. You can use the following steps to determine this rate:
1. Determine the volume of actual production
A corporation tracks the quantity of products it completes during specified accounting and reporting periods. The entire number of completed inventories is included in this figure. This figure represents the formula's level of real production.
2. Estimate the level of your potential output
The potential output is the amount of operation at which a business can operate at full capacity. Utilizing all available resources sustainably can have a favorable impact on production output. It can also have a positive impact on sales and income. Determine the potential output by assessing sales targets. Determine the quantity of products required to meet those targets.
Understanding potential output
It is important to remember that prospective output can be categorised in two ways: technically and economically.
- The greatest output possible under installed conditions within a predetermined time-frame is what is meant by the technical definition.
- This conveys a manufacturer's potential for increased production without raising the average production cost due to the need to hire more workers or buy more machinery.
- The average cost of production may begin to rise even before a manufacturing operation approaches a capacity utilization rate of 100%.
- This is due to the fact that as production is pushed almost to its breaking point, margins for mistake are reduced, equipment depreciation is accelerated, additional shifts are required, more frequent equipment maintenance is required, etc.
- The level of production above which the average cost of production starts to realistically increase is consequently used to express the economic potential output.
- On paper, having a capacity utilization rate of 100% might seem like a fantastic idea, but in practice, it rarely works out economically.
When the company is operating at full capacity, unexpected spikes in demand could result in a production shortfall during a vital period of potential growth, in addition to the tensions brought on by the workers and equipment being pushed to their breaking points on a daily basis. These factors make a capacity utilisation rate of roughly 85% in most situations desirable.
3. Divide actual output by potential output
Divide the actual output by the prospective output once you've determined your actual output and estimated your potential output level.
4. Multiply your result by 100
You need to multiply the result of dividing your output values by 100 in order to transform it from a decimal value to a percent.
5. Summarize your findings
If you assume that 100% represents complete operating capacity when you receive the capacity utilization rate, you can interpret the value as such. Companies are not operating at their full potential if the capacity utilization rate is less than 100%. Operations are over capacity when rates are higher than 100%.
For the majority of business and economic processes, a capacity utilization rate between 85% and 100% is considered appropriate.
Example of Capacity Utilization
Suppose XYZ Company is producing 40,000 and it is determined that the company can produce 80,000 units. The company’s capacity utilization rate is 50% [(40,000/80,000) * 100]. If all the resources are utilized in production, the capacity rate is 100%, indicating full capacity. If the rate is low, it signifies a situation of “excess capacity” or “surplus capacity.”
It is unlikely that an economy or company will function at a 100% capacity rate as there are always hurdles in the production process (such as the malfunction of equipment or unequal distribution of resources).
A rate of 85% is considered the optimal rate for most companies. The capacity utilization rate is used by companies that manufacture physical products and not services because it is easier to quantify goods than services.
Corporate Capacity
It is used to evaluate operating efficiency and offers insight into cost structure. The capacity utilization rate is a crucial metric for businesses.
- It can be used to estimate how much costs per unit will rise or decline. A gain in output will result in a drop in the average cost of production.
- It also sheds light on the cost structure of the company's operations, both in the short and long terms.
- It means that the cost per unit decreases as capacity utilization increases. This gives a corporation an advantage over rivals.
- Many large businesses want to produce at rates as near to 100% as possible.
Even though reaching a full capacity rate is impossible, there are ways for businesses to increase their current utilization rate. Such as:
- Spending less time on equipment maintenance so that more time can be spent on the production of goods.
- Hiring more staff and promoting overtime to ensure that all production goals are met.
Capacity Utilization and the Business Cycle
The entire capacity utilization varies with the business cycle. Businesses modify their output levels in response to shifting consumer demand. When there is a recession, demand drops significantly. This is a result of rising unemployment, declining wages, declining consumer confidence, and falling company investment.
Since the 1960s, the Fed has provided capacity utilization data, covering several economic cycles. In the late 1960s and early 1970s, rates reached an all-time high of about 90%. In 1982 and 2009, when capacity utilization dropped to 70.9% and 66.7%, respectively, there were the biggest drops.
Importance of the Capacity Utilization Rate
For businesses and entire economies, knowing the capacity utilization rate is crucial. It provides a framework for organizing the use of resources to produce the highest-quality products.
- The capacity utilization metric is essential for assessing how effectively a company uses its resources. It is also essential for long-term planning.
- Planning for capacity use also necessitates an understanding of market demand and how it impacts operational capabilities and existing procedures.
- It's also critical that the capacity utilization rate offers insightful data on how effectively an economy's or company's operational operations are doing.
- For instance, a capacity utilization rate of less than 85% may be a sign that production processes, manpower, or other business applications need to be improved.
On the other hand, a corporation runs the risk of exhausting its resources too rapidly if it performs much above full capacity. By not maximizing the possible output, your production line may be wasting resources or being inefficient in certain areas. These may be identified utilizing capacity utilization in your manufacturing analytics.
Low levels of capacity utilization may also point to over- or under-allocation of resources. This allows for wiser ordering and long-term usage strategy decisions. Additionally, you may use capacity usage for a variety of purposes, including calculating overtime, personnel requirements, and even estimating maintenance expenses.
The following are some crucial areas where an ERP or MRP (Material Requirements Planning) system can be helpful in:
- Monitor carrying costs
- Control production
- Evaluate work-in-progress costs
These solutions allow you to quickly view your manufacturing and material expenses. This simplifies your selling price computation in the end.
Use of Capacity Utilization as a KPI
Depending on the industry, inventory/production models, stock building cycles, seasonal demand cycles, and warehousing procedures. The capacity utilization figure may change.
- Setting the target capacity utilization rate is crucial. It should take into account both consumer expectations and the other above-mentioned criteria.
- It's possible that different goal rates will be set for various points during a year or economic cycle.
- It is critical that the majority of gross production really be saleable when capacity utilization is at a high level.
- This calls for a low waste production procedure that also keeps track of its safety stock levels and is effective.
In order to achieve these necessary efficiencies, lean manufacturing principles are helpful. A lean, well-run production process will increase revenue for the company and shorten lead times for customers.
How to Improve Capacity Utilization in Business?
If you are not satisfied with the rate you are looking for, you can adjust one of the other factors in the formula to get a rate that is more realistic. For instance, if you hire a less expensive worker, your job can be of inferior quality.
However, you run the risk of losing customers if you raise the employee's billable rate. Therefore, it would be wise to concentrate on increasing capacity utilization. Before lowering your targets.
Here are some suggestions for raising your company's capacity utilization rate:
Boost scheduled production
It is never easy to secure the funding you believe is necessary to launch your business. It always takes time to raise money from the market, therefore careful planning is essential. Making a plan in advance can always help you make the greatest use of your resources. Many aspiring business owners struggle to adjust to rapid changes in supply, demand, manufacturing, etc.
Whenever something is started from scratch, it always results in efficiency. The two pillars of good operations, including capacity utilisation, are planning and scheduling.
Identify the weak points.
You may spot any bottlenecks in your process and find out who is underperforming by analyzing how each resource is used separately. For instance, you can concentrate on coaching, training, or other choices if one of your employees is only operating at 60% of their potential.
Increase your client base and your revenue.
Perhaps there isn't enough billable work to keep your team occupied, which would explain why utilization is low. If this is the case, increasing your capacity utilization rate would require luring in new clients and taking on new tasks.
Subcontracting
You accept orders and produce goods for other companies when you subcontract. By doing this, the capacity is utilized to its fullest and you are creating value for both your firm and other enterprises. Subcontracting in some ways enables you to maximize capacity utilization and profit at the same time.
In short, capacity utilization affects firm profitability significantly, and vice versa. Every manufacturer and business establishment must provide the enhancement of capacity utilization their full attention. Planning well, taking a disciplined approach, and making smart decisions helps increase capacity utilization.
Cut back on non-billable work.
What is being done with the extra three hours if your staff can only work five billable hours each day? You might be able to eliminate these hindrances and raise their overall potential.
Structured approach
When trying to balance your finances, start small. As product demand rises, boost your capacity. Paying too much for too little output will reduce your profit rate because you may always expand your area as demand rises. For varying demand, you should be adaptable.
Capacity for sharing
A crucial strategy for maximizing capacity usage is capacity sharing. For both parties, it is a win-win situation because they both stand to gain from it. It improves their chances of remaining in the market even with minimal resources. One can obtain desired industrial capacity from an owner, which benefits both the owner and the seekers.
This enhances usage, prevents investment duplication, and improves profitability and cash flow conditions. Sharing capacity helps to build an ecosystem where capacity owners and seekers may easily engage for improved capacity utilisation. It also helps to answer the challenges of aspiring entrepreneurs.
Maximizing utilization = Increasing profits
To make the most of the capacities available, entrepreneurs should develop creative concepts. One should constantly carefully examine their capacity to ascertain how it can be used from a certain perspective.
Before starting a business, it is advised that you have a thorough understanding of your product. This includes knowing every last nuance of the capabilities of your hand. To maximize usage and, consequently, revenues. Take into account varied conditions and develop creative concepts.
More importantly, the capacity owner should make every effort to increase the reach of their capacity. His or her industrial capacity's context and competence can be important depending on the business need. In a specific region of the nation or the world. In order to meet the demand, the capacity owner should use all available strategies.
Decision-making in strategic areas
Strategic development is essential for the growth of your firm if you decide to start something new. Strategic decisions have a significant impact on a company's future. Successful investors seek out organizations with these characteristics.
The main goal of your plan should be to grow low-production businesses in order to maximize capital gains. This will improve the consistency of your company's operations and increase the number of its customer base.
Promotions work best
Product demand and capacity utilization go hand in hand. Any business, whether it is starting out or already established, should always work to raise customer demand for their product. It should also work to improve its quality.
By engaging in promotional activities and adopting novel methods for enhancing the value of the product. One can raise production rates and achieve maximum capacity utilization.
What Is a Good Manufacturing Capacity Utilization?
Although simple logic might lead one to believe that this number ought to be as high as possible, this is not the case. Anything above 85% capacity utilisation for the majority of manufacturing plants starts to pose issues like:
- Materials wasted: If a production facility produces more than is required, materials may be lost. This damages the environment and drives up costs.
- Excess inventory: If a plant is operating at or close to its maximum capacity, it is likely to accumulate excess inventory. As money is invested on items that might not sell for some time, this can be expensive and lead to an increase in external debt.
- Machine malfunctions: When a machine is operating at or close to its maximum capacity, it is more prone to malfunction. Production delays and higher maintenance expenses may result from this.
- Lessened adaptability: If a business is already running at capacity, it will find it challenging to meet an increase in demand. Reduced client satisfaction and lost sales could result from this.
- Inefficient use of resources: Running at full capacity rates might also result in inefficiencies. Bottlenecks and other problems with resource management may appear. Costs may go up as a result, and quality control may suffer.
- Shipping delays: If a business can't keep up with demand, shipping delays may occur. This can result in dissatisfied customers and decreased sales.
Towards these reasons, 80 to 85% capacity utilization is what most companies strive for. This maintains a high level of efficiency while still allowing for some space for error.
It's critical to remember that capacity utilization is a moving target. It will alter as the demand for your goods or services shifts over time. Because of this, it's critical to monitor capacity usage over time. Ideally with the aid of production management software, in order to spot trends and alter your production as required.
What Is a Good Capacity Utilization Rate?
One option to respond to this query is to look up industry benchmarks and trends, then establish the average as your objective. Examining the past performance of your company is an additional choice. An organization's capacity utilization rate should ideally be 100%.
A business wouldn't want to maintain 100% production for very long, though. To boost its revenue, it would seek to raise its production capacity. That would lower the company's perfect utilization rate score, but in the long run, it would boost its prospects.
Does a High Capacity Utilization Rate Increase Investment?
When the capacity utilization rate is high, investment should increase. According to the resources at its disposal, it shows that a company is creating as much as it can. If its leaders don't foresee rising demand in the future and make the necessary investments, its rivals will step in to fill the void.
How Do you Measure the KPI?
By dividing the overall capacity used during a certain period by the total production capacity or optimal levels. Multiplying by 100, capacity utilization is calculated.
Which Resources Would You Employ to Compute the KPI?
You need to collect information from a few different sources in order to track your capacity usage rate. The first step is to start collecting information on your resource capacity. This includes purchase records, inventory inflows and outflows, cycle periods, and output capacity.
You should also track information about your actual output. Gross production figures, resource consumption, and total materials intake against output.
Disadvantages of the Capacity Utilization Rate
From many angles, the idea may be deceptive. First, a company should only manufacture the amount of goods that are immediately required.
Any further usage of capacity will merely result in the storage of unused goods as inventory, which will add to the cost of retaining that inventory and increase the risk of obsolete goods.
Second, since downtime is required for repairs and maintenance, the metric is based on a notional capacity level. This is a level that cannot be maintained over the long run.
Effects of Low Utilization
For fiscal and monetary policymakers who deploy such policies to stimulate the economy. Low capacity utilization is a challenge. Many European economies, including France and Spain, struggled in 2015 and 2016 as a result of low capacity utilization.
Inflation remained notably low with a deflationary threat. This was despite government intervention through historically low interest rates.
Due to the significant unemployment caused by the low capacity utilization. Prices found it difficult to respond to monetary stimulus. With excess capacity, increasing production of commodities did not necessitate a substantial capital outlay. The resulting production did not necessitate a substantial capital outlay.
Low utilization has various widespread implications, including:
High unemployment: Employment may also be impacted by low utilization. Companies may not require as many employees to complete duties when they don't generate as many things as they can.
Minimum investment: A corporation can be able to satisfy greater needs with little investment, which is a good outcome. They frequently have the capacity to accomplish this without incurring additional expenditures. Since they are able to generate more.
When a business experiences a rise in demand for its products, it frequently manages to satisfy the demand without increasing the cost per unit. Without incurring additional costs, the business can increase output levels. This is done by investing in better infrastructure.
Low stimulation: It can be challenging to stimulate economies when there is low utilization. Because of this, countries run the danger of experiencing deflation.
What Can Be Done to Increase Capacity Utilization?
In the event that your calculations result in a poor capacity utilisation rate, you can:
Effective resource allocation: Strategic planning can help resource allocation processes be improved by removing stale resources and ensuring that current resources are used effectively.
Decide strategically: Select the items to produce more of, the extra resources to use in production, and the output strategy to match market demand.
Increase production output just a little: Increase output as demand rises and monitor operating costs to guarantee proper financial coverage.
Consider subcontracting: Take on contracts and production orders from other companies as a subcontractor. Profits and productivity may rise as a result of this.
Create production timetables: Create production schedules and note due dates for crucial production quotas.
Rates of share capacity: To increase capacity and resource usage, share the capacity rate with other owners who have comparable production, revenue, and profit objectives.
What Is Manufacturing Capacity Utilization?
A more specific phrase than capacity utilization is manufacturing capacity utilization. The quantity of output produced by a manufacturing facility in relation to its maximum potential output is measured by a metric called capacity utilization. It is frequently stated as a percentage.
Manufacturing companies are mainly affected by the capacity utilization rate. The assembly line may account for the majority of their expenses. However, there are additional expenses like shipping and storage.
- The capacity utilization rate of a manufacturer is calculated taking into account all of these expenditures.
- This crucial key performance indicator (KPI) aids companies in monitoring productivity and streamlining production while ensuring they have room to accommodate an unexpected rise in market demand.
- It can be applied to certain factories, production lines, or even machinery in isolation.
- The most important aspect is the exploitation of production capacity.
If a company's current equipment can only process 1,000 units per day, it cannot boost that number to 1,200 without purchasing new equipment. However, this frequently results in resource overuse, which can subsequently result in bottlenecks, waste, and inefficiency. Finding a balance between too much and too little production is the objective.
Capacity Utilization Business Considerations
It is crucial to keep in mind a production operation's capacity utilization rate because this measure offers crucial information about the cost structure of the business.
- It enables the determination of the point at which the operation rate and average cost per unit are balanced.
- Many businesses strategically change their capacity utilization rates as a result of changes in consumer demand, raw material pricing, business cycle stages, etc.
- To further boost production capacity when the rate is consistently very high, it would probably be a good idea to invest in additional manufacturing facilities.
- This helps to ensure that market caps for new or current companies are filled, among other things.
On the other hand, if the rate is consistently low, the business should concentrate on improving the effectiveness of its manufacturing operation. There are numerous approaches to accomplish this. For instance, by installing new production systems, hiring more workers, outsourcing certain aspects of the manufacturing process, or by becoming a subcontractor yourself.
Economic Significance of Capacity Utilization
The capacity utilization rate will rise as market demand rises, but it will reduce as market demand declines. The rate serves as a gauge for inflationary pressures among economists. Due to surplus capacity and inadequate demand for the output produced, a low capacity utilization rate will lead to a fall in price.
Economies with capacity ratios considerably below 100% can increase production substantially without changing associated costs.
High surplus capacity rates are common in capitalist countries, and economists use the rate to criticize capitalism by claiming that resources are not being used as efficiently as they could be. However, because of inefficiencies in resource allocation, an economy will never operate at 100% capacity, regardless of the state of the economy.
How Capacity Utilization Affects Economies?
This value is frequently analyzed by economists to see how efficiently businesses utilize the resources required for manufacturing. Low resource utilization rates are common among businesses, which means that few of the resources they own are actually used to produce things.
Prices often decline when utilization is low since it may indicate that there is less demand for particular products. Inflation can result from excessive demand since prices can rise along with utilization.
Capacity Utilization Best Practices
Concentrating only on a company's bottleneck operations will give you a better understanding of capacity utilization rate. Without effectively managing this one function to obtain the maximum potential utilization rate, the company cannot produce any extra throughput.
It is really unproductive to concentrate on the capacity utilization of any other work center inside a company because doing so generates an inherent incentive to expand that center's usage even when it is not required to do so.
How can Deskera Help You?
As a manufacturer, you must keep track of your inventory stock. The condition of your inventory has a direct impact on production planning, people and machinery use, and capacity utilization.
Deskera ERP and MRP systems can assist you in the following ways:
- Control production schedules
- Compile a Bill of Materials
- Produce thorough reports
- Make your own dashboard.
Deskera ERP is a complete solution that allows you to manage suppliers, track supply chain activity in real time, and streamline a range of other company functions.
Deskera Books allows you to manage your accounts and finances better. It helps maintain good accounting standards by automating billing, invoicing, and payment processing tasks.
Deskera CRM is a powerful tool that organizes your sales and helps you close deals rapidly. It enables you to perform crucial tasks like lead generation via email and gives you a comprehensive view of your sales funnel.
Deskera People is a straightforward application for centralizing your human resource management activities. Not only does the technology expedite payroll processing, but it also helps you to handle all other operations such as overtime, benefits, bonuses, training programs, and much more.
Conclusion
A percentage indicator or KPI called capacity utilization shows how much of the available capacity is being used to meet the demand at hand. When times are good, most factories are able to function at close to 70–80% capacity utilization, and in some circumstances, up to 100%, making it a useful predictor of business and market conditions.
A common KPI and operational metric in various industries used in the strategic capacity and business planning functions of many firms is capacity utilization.
It can be used as a metric to help determine the best time to increase capacity, enter new markets, leave existing markets, establish cost curves for various manufacturers, and determine profitability.
Key Takeaways
- The efficient use of resources is referred to as capacity utilization, a business phrase that is occasionally used to describe IT. The term "capacity utilization rate," as used by industry experts, indicates how effectively or to what extent existing resources are being utilized.
- Capacity utilization, which is frequently stated as a percentage, is a crucial KPI for firms to monitor effectiveness and boost output.
- Although 100% capacity utilization would be ideal, this is not realistic, hence an existing rate of 85% is thought to be excellent. In the majority of businesses, this rate is regarded as ideal.
- The average cost of goods or cost per unit and capacity utilization are inversely related; the higher the utilization rate, the lower the average cost of goods, and vice versa.
- Companies react to the current economic cycle. They will reduce output if there is little demand for their goods. As a result, their capacity utilization rates will drop.
Related Articles
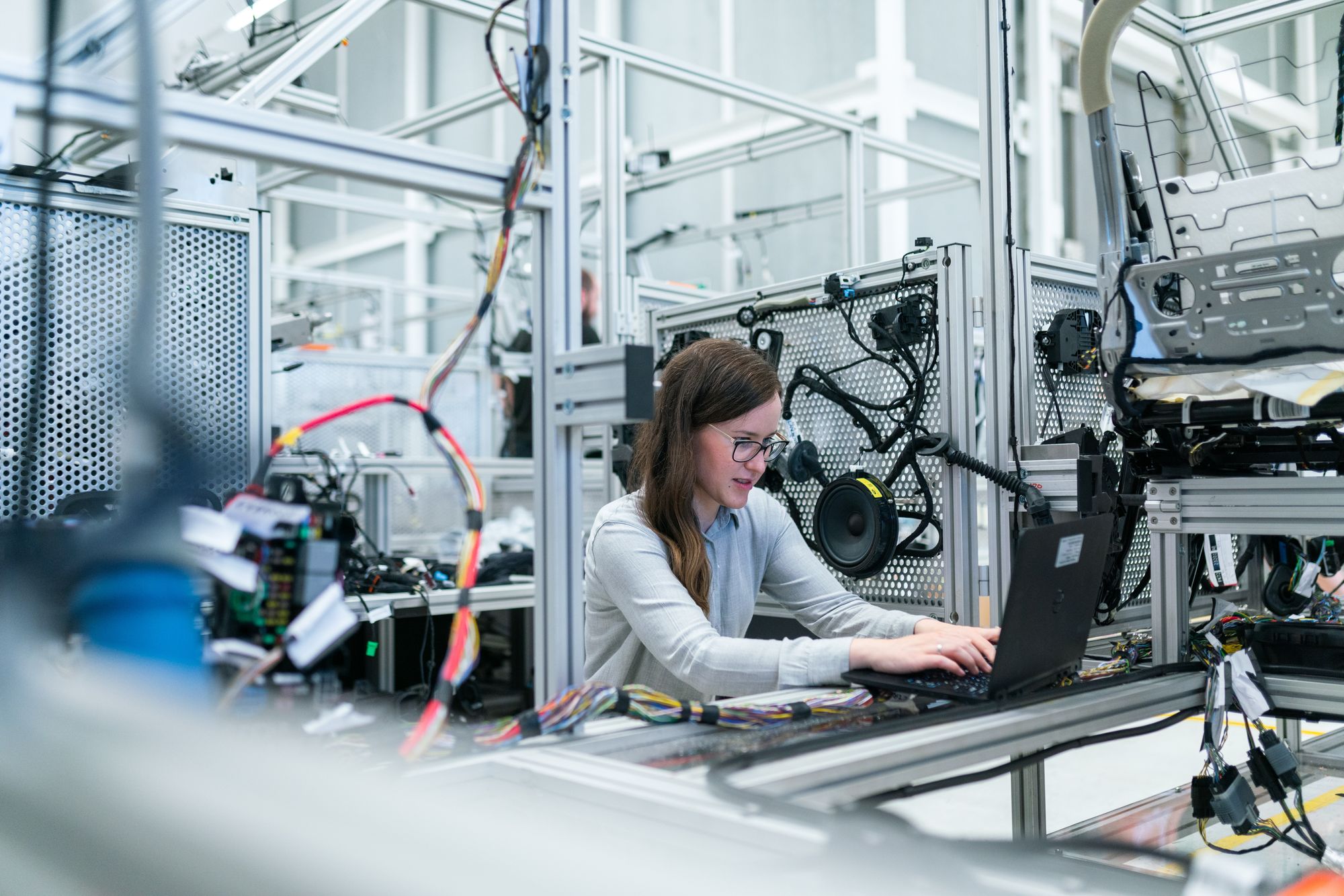
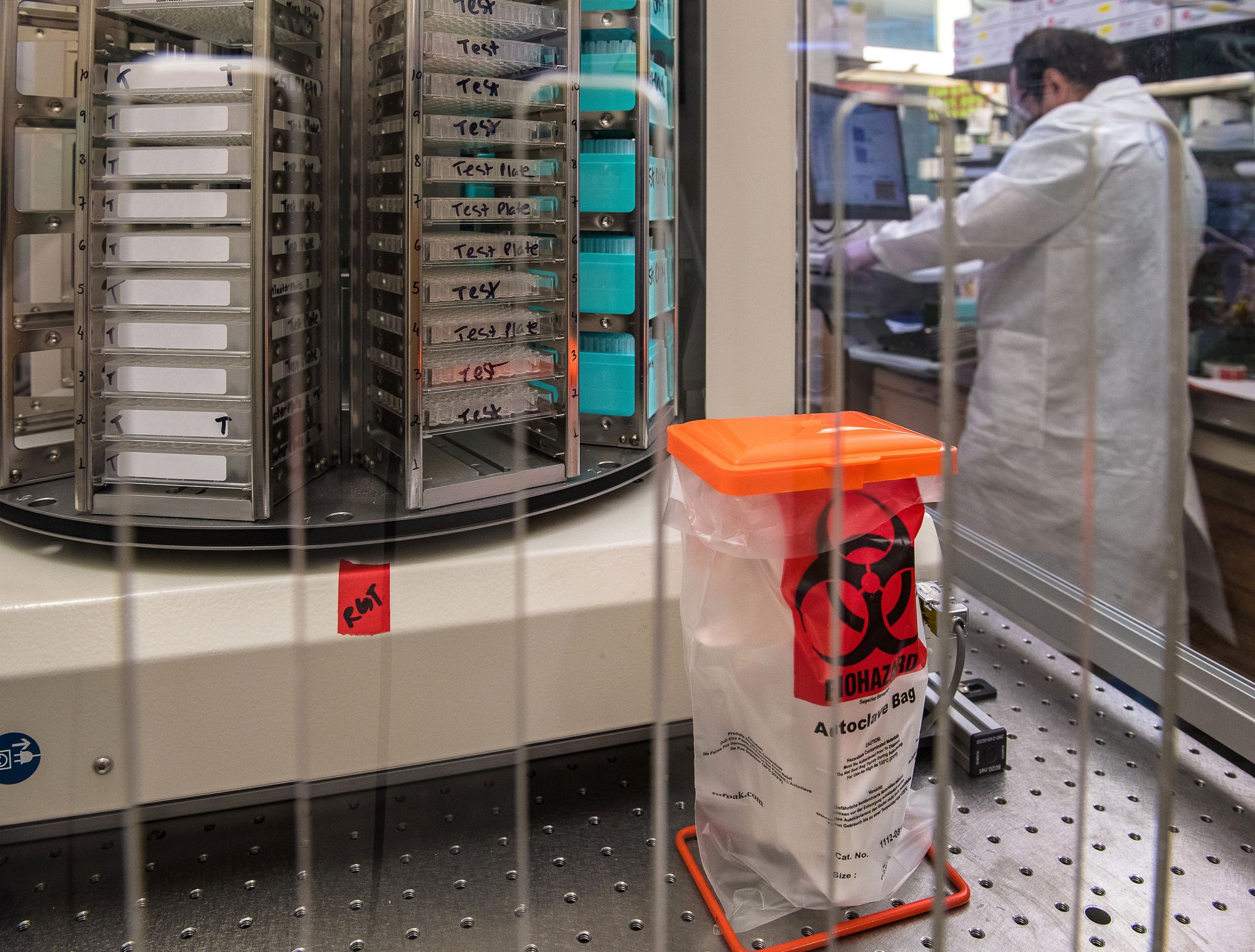
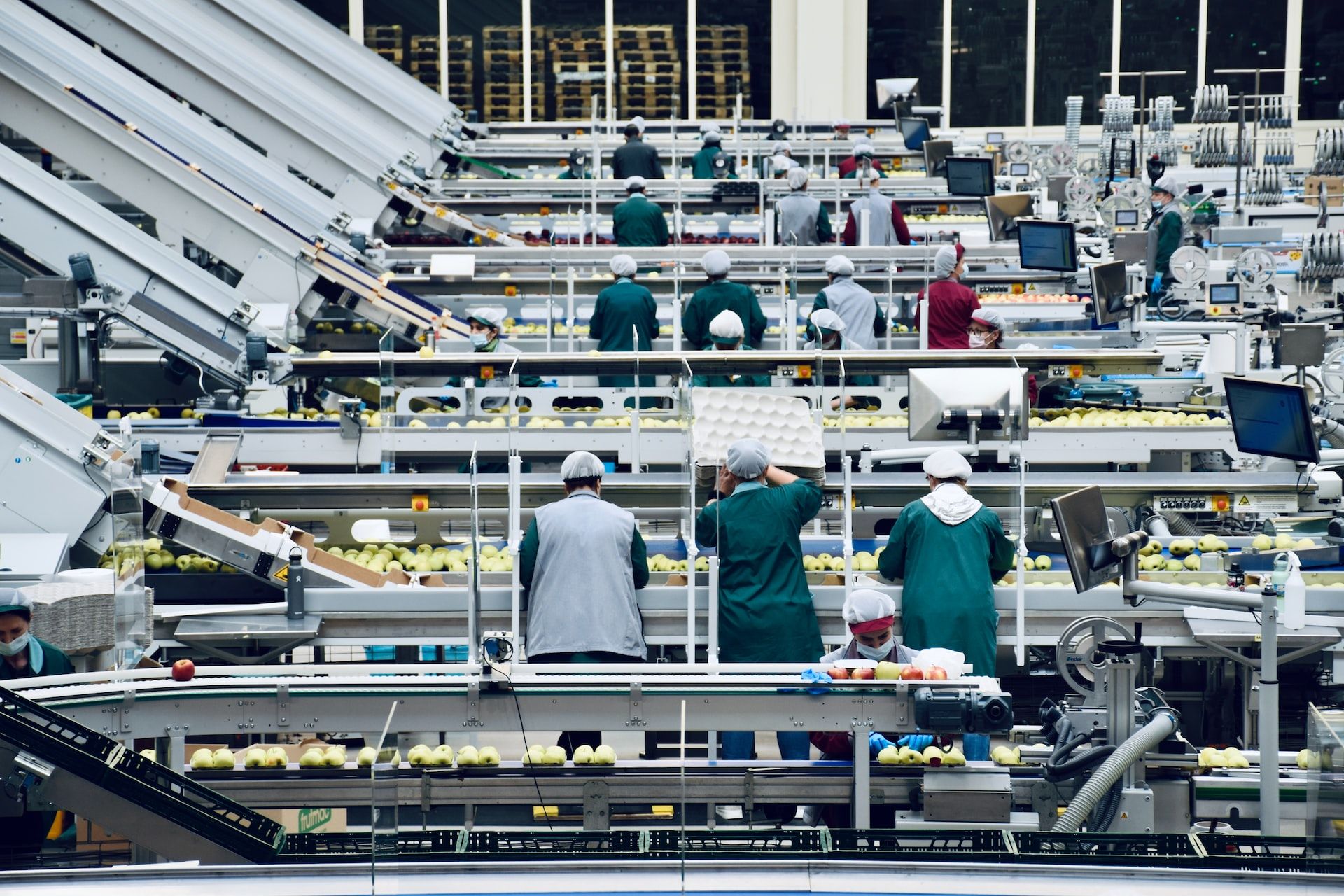
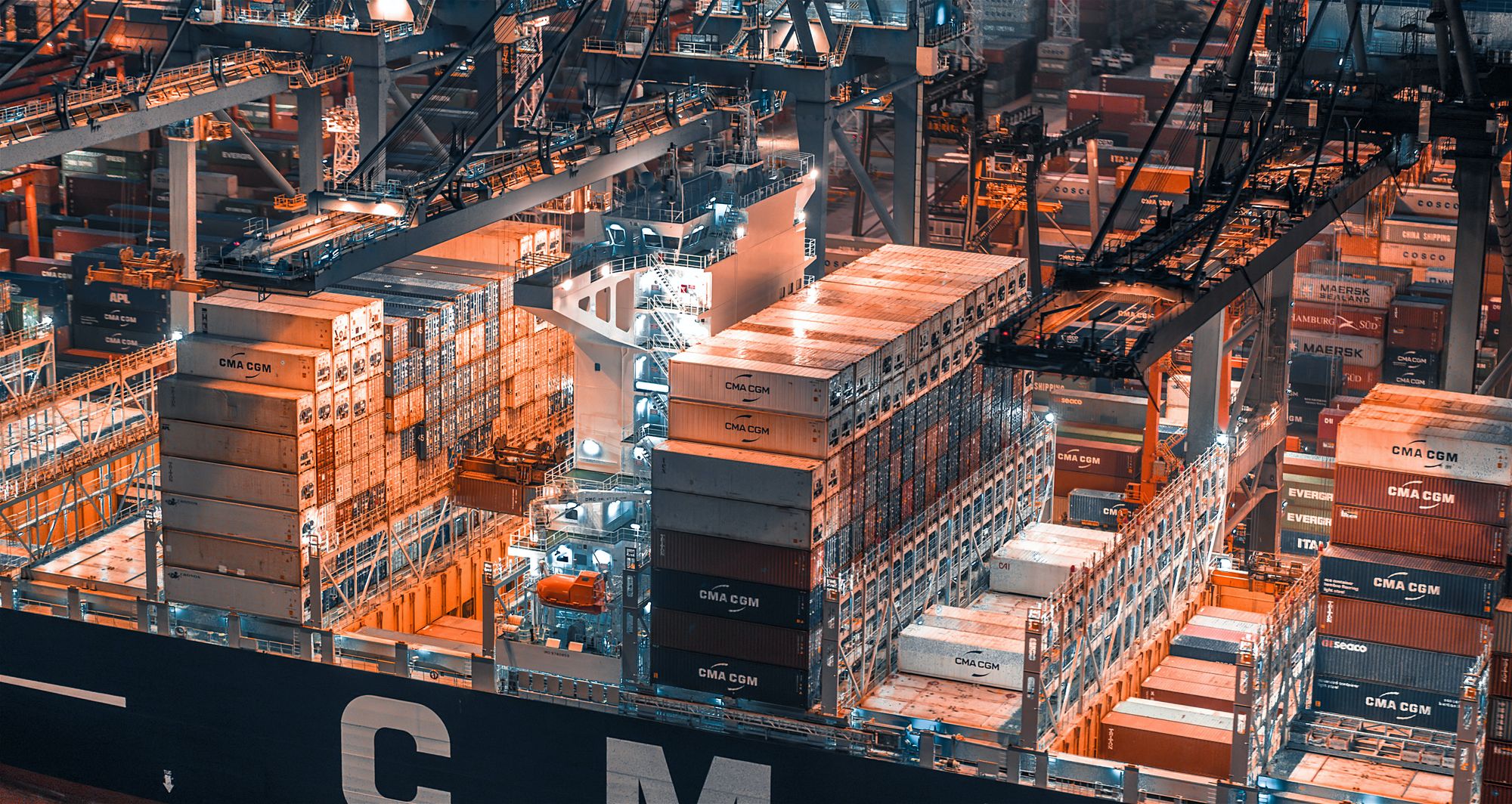