The Factories Act is a document of social legislation established to protect workers' health, safety, and welfare at work. The Gujarat Factories Rules, 1963, are the rules that the state of Gujarat has created in accordance with the Act. The document of Gujarat Factories Rules comprises 10 Chapters and 26 Schedules, each of which we shall observe closely in this article.
The Bhopal Gas Tragedy in 1984 made the public aware of factory emissions and threats, compelling the government to take prompt action to expedite modifications to the legislation. The Factories Act applies to all factories that employ 10 or more people when using electricity and 20 people when not.
We shall be touching upon a small segment of history that shall describe the reason for introducing the Factories Act. The act lays down regulations for all employers regarding aspects such as the minimum wages the workers must receive to the number of hours they should work.
Gujarat Factories Rules is an elaborate document comprising 46 Forms, which have been placed in a separate article: Gujarat Factories Rules, 1963 Forms.
Here is what more we shall understand in this article:
- History of Factories Act
- Chapter 1: Title and Extent
- Chapter 2: The Inspecting Staff
- Chapter 3: Health
- Chapter 4: Safety
- Chapter 4A: Site Appraisal Committee
- Chapter 5: Facilities for Workers
- Chapter 6: Working hours for Adult Workers
- Chapter 7: Employment of Young Individuals
- Chapter 8: Annual Leave with Wages
- Chapter 9: Special Provisions
- Chapter 10: Supplemental Information
- How can Deskera Help You?
- Key Takeaways
History of Factories Act
The Factories Act, which was enacted in 1881, regulates the working conditions of workers and establishes various provisions related to health, safety, working conditions, and hazardous processes. It also establishes procedures for imposing penalties in the event of any violation of the Factory Act's provisions. In the following years of 1891, 1911, 1922, 1934, 1948, 1976, and 1987, the Act was revised. In 1948, it was significantly revised.
The Factory Act of 1948 is more extensive than the previous act, focusing on the health, safety, and welfare of factory workers, working hours, the minimum age to work, paid leave, and other issues.
This act is based on the terms of the Factory Act of 1937, which was passed in the United Kingdom. The Factory Act of 1948 regulates the entire day-to-day activity taking place in the factory. The industry is a continuous and methodical activity in which trade is organized, whereas the factory refers to the place where such activities are carried out. This statute covers the entire country of India.
The act's key features are safety, equipment guarding, health and cleanliness, drinking water, washing and toilet facilities, lunchrooms and restrooms, sitting arrangements, first aid, and dispensary facilities in factories employing more than 500 workers. It also includes facilities like creches employing more than 50 women, welfare officers employing more than 500 workers, and holidays with wages at the rate of one day for every 20 days worked.
Let's learn about the regulations and guidelines introduced by Gujarat Factories Rules, 1963.
Chapter 1: Title and Extent
The appraisal of the sites application will be submitted to and accepted by the Chairman of the Site Appraisal Committee. The committee may decide not to provide information on any single item in the application form if it believes it is unrelated to the application being considered.
- The secretary will make arrangements to record the application for site appraisal in a separate register and acknowledge it within seven days.
- The secretary shall schedule meetings in such a way that all applications submitted and enrolled are referred to the committee within one month of their receipt date.
- The committee shall consider the application for site evaluation in light of the prohibitions and limits on the location of industry, as well as the conduct of processes and operations in various regions, as set forth in Rule 5 of the Act.
- The committee may request documents, study exports, investigate the location if necessary, and take other procedures to make an opinion on the location's suitability.
Important Definitions
The significant definitions are given as follows:
Hazardous chemical
- Any chemical that meets the criteria in Part I of Schedule I and is a part of Column (2) of Part II of that Schedule, or
- any chemical enlisted in Column 2 of Schedule 2 or
- any chemical enlisted in Column 2 of Schedule 3
Industry Activity
- any chemical that meets the criteria in part I of Schedule I and is enlisted in column (2), part II, Schedule, or
- any chemical enlisted in Column 2 of Schedule 2; or
- any chemical enlisted in Column 2 of Schedule 3;
Degrees (of temperature) implies degrees on the Fahrenheit scale.
District Magistrate implies the inclusion of such other officials as appointed by the State Government.
Form means a Form indicated for use in these rules.
Fume includes gas or vapor
Health Officer indicates the District Health Officer, Municipal Health Officer, or such other official as appointed by the State Government.
Hygrometer refers to an accurate wet and dry bulb hygrometer confirming the prescribed conditions as regards construction and maintenance
Inspector includes the Chief Inspector of Factories and a District Magistrate, who are both appointed under the Act.
Maintained refers to a state that is efficient, and in good functioning order.
The manager is the person who is responsible for overseeing the factory's operation.
Appointing Competent Person
The Chief Inspector appoints a competent person who would be in charge of the following:
- Performing tests
- conducting examinations
- assessments on such structures and buildings
- defective equipment
- lifting machines and lifting tackles
- hoists and lifts
- pressure plants
- enclosed areas
- air circulation systems
- and other factory processes that involve equipment and plants
Approving Plans
The Chief Inspector of Factories must be contacted in order to receive prior clearance for the factory's location, as well as for the construction or expansion of the factory.
The following documents must be submitted with the application for such permission:
(a) A flow chart describing the manufacturing process and a brief description of the process in its various stages
(b) Plants in duplicate drawn to scale showing:
(i) the factory site and immediate surroundings, including neighboring building structures, roads, drains, and so on
(ii) the plan-buildup, and necessary cross-sections, the plan elevation, and necessary cross-sections of all the buildings. The plants must also clearly show the location of the plant and machinery, as well as alleys and passageways
(c) any additional information required by the Chief Inspector
If the chief inspector is satisfied with the observations and the finding at the site, he may process to give his approval. He approves it by signing the application and returning one copy to the applicant.
Certificate of Stability
The Act implies that there should be no manufacturing process in the premises of the factory until it has been approved by a competent person and allotted a Certificate of Stability.
Application of Registration and License
The manager of a factory must submit an application to the Chief Inspector for registering the factory in Form No. 2. They must also apply for a license in Form No. 3.
Every application in Form No. 2 must comprise a treasury receipt, a crossed Indian Postal Order, a crossed cheque, and an invoice.
Granting License
On receiving the application along with the fees, the Chief Inspector may grant a license on being satisfied with the information provided by the manager.
The license will be granted in Form No. 4.
Amending License
The Chief Inspector has the authority to amend the license granted under Rule 5. You will require to amend the license if there is a change in any of the following:
- Change in the name of the factory
- If the factory oversteps the limits mentioned in the license
Renewing License
You can use Form No. 3 for applying for renewal of your license. It must be sent to the Chief Inspector with a treasury receipt, crossed Indian Postal Code, crossed cheque, and an invoice for paying the fees for the procedure.
Transfer of License
If you wish to transfer the license in the name of another person, you can do so before the license expires. The application must be sent to the Chief Inspector with the name of the person who shall acquire the license. The fee for this application is INR 5.
Process in case of death or disability of license
If the licensee is no more, the individual carrying out the business operations will not be held accountable and will not be subject to any kind of penalty under the Act. They may have to make an application for the amendment of the license to register their name on the new license.
Loss of License
In the case where you lose the license or it gets destroyed under any circumstance, you may apply for a duplicate license.
Mode of Payment of Fees
- When you apply for the license, you must send your application along with a treasury receipt with the correct amount chargeable for the process, to the Chief Inspector.
- Add a crossed cheque or a crossed Indian Postal order
- Also, if your application for the grant of a license, or renewing/amending is rejected, the fees will be refunded to you.
- In case of approval, but you have paid an excess amount, then you shall receive a refund only after the completion of 1 year from the date of the grant.
Suspension of License
- Before 31st October of a year, if you (the licensee) notify the Chief Inspector that the premises will not be used any longer for factory operations, the Chief Inspector will proceed to suspend the license.
- A suspended license can be revived and renewed once you send an application for its renewable in Form No. 3 and paying the relevant fees. You may encounter a surcharge fee of ten percent in this case.
Additional Notes
- You must provide a notice of occupation in Form No. 2.
- Also, if you appoint a new manager, you must notify it through Form No. 3–section 7–subsection 4.
- The manager must maintain records in Form No. 37 detailing the operative environment of the factory.
Health and Safety policy
The managers of a factory are responsible for preparing a document that maintains the details of the health and safety policy of the factory.
This will apply to all factories satisfying the following criteria:
- They are included under section 2(m) but employ only up to 50 workers
- They are included under section 2(m) (II) but employ up to 100 workers. These factories are exempted from sub-rule (1).
The Health and Safety Policy must contain the following information:
- Declaration from the top management of the factory that they are committed to providing good and safe working conditions to all the workers
- It must include the organizational setup to ensure that the points in the policy are enacted.
- The policy must contain and enlist all the arrangements that help the policy be effective.
- The policy must also specify the responsibility of the contractors, sub-contractors, or any other external agency that enter the vicinity of the factory.
- The policy must specify the performance of the health and safety in its Annual Report.
- It must also comprise the safety audits carried out in a periodical manner, once in 2 years.
- They must enclose details about the education imparted to the workers for their safety at different levels.
A copy of this policy must be shared with the Chief Inspector. Also, the managers must revise and amend the policy as and when necessary.
Chapter 2: The Inspecting Staff
Appointment of Inspectors
The Bombay Civil Services Classification and Recruitment Rules fixes and prescribes the qualifications required to become an inspector as directed by the Act.
Powers of the Inspector
The appointed inspector is empowered to take the following actions:
- The inspector may photograph a worker to investigate the case closely.
- They may carry out medical examinations if the inspector is a qualified medical practitioner.
- They may prosecute or defend themselves in court n cases of complaints against them.
Duties of Certifying Surgeon
- In the case where young people want to obtain fitness certificates, the certifying surgeon will inform the managers about the physical examination.
- Form No. 5 is used for this procedure with the name and left thumb mark of the person undertaking the physical examination. The fee for this will be INR 1.
- In case of loss of the fitness certificate, the Certifying Surgeon shall provide a duplicate certificate charging a fee of annas 8.
- The application for the duplicate certificate will be sent by the manager of the factory who employs the young person.
- The Certifying Surgeon may carry out this examination on the orders of the Chief Inspector and furnish the reports of the same to him.
- The Certifying Surgeon must also indicate any illnesses that have occurred due to the manufacturing process in the factory.
- He may also indicate any likelihood of health hazards in the manufacturing process of the factory.
- He may also inform about the likelihood of any health hazards to the young persons.
- The Certifying Surgeon can also visit the factory vicinity for the examination of the persons employed to check the dangerous operations in the factory.
- In such a visit, the Certifying Surgeon can provide a fitness certificate after the examination of a worker through Form No. 5. This certificate of fitness will lie with the manager of the factory.
- If the Certifying Surgeon finds that a worker is not fit to perform the tasks, he shall suspend the work of this worker for the stipulated time. In this timeframe, the worker shall not be employed without the written permission of the Certifying Surgeon.
- The manager of the factory is expected to cooperate with the Certifying Surgeon in the process of examination of the manufacturing process in the factory.
Chapter 3: Health
Cleanliness of walls and ceilings
Section 11 – sub-section (1) – Clause (d) of the Act will not be applicable to the factories that are kept in a clean state. However, the same clause will be applied to factories with the following conditions:
- The workrooms with less than 14.2 cubic meters of space for every worker based on Part A of the Schedule
- The workrooms with less than 70.75 cubic meters of space for every worker based on Part A of the Schedule
- It shall also apply to engine houses, lunch break rooms, canteens, fitting shops, creches, restrooms, and wash places
- It shall also apply to tops of passages, walls, staircases that have a height lesser than 6.1 meters above the stair or the floor
If the Chief Inspector finds that any part of the factory is kept unclean, he may serve a notice to the manager/occupier of the factory. He may direct the manager to clean, wash, paint, or varnish the same.
If the occupier does not comply within 2 months of the served notice, sub-rule (1) shall no longer apply to the factory or its part, unless the Chief Inspector decides otherwise.
The following parts of factories must be kept clean:
- The rooms where articles will be stored
- The rooms in which the walls or ceilings that have galvanized iron, glazed bricks, glass, slate, and asbestos bamboo match.
- The part of the factory where dense steam evolves continuously in the process.
- The parts in which pitch, tar, or similar material is manufactured or is used to a significant extent, except in brush works.
- The areas or parts of a glass factory are called glasshouses. Rooms in which graphite is produced or is used in a significant quantity in any process.
- The parts in which coal, coke, oxide of iron, ochre, lime, or stone is crushed or ground.
- The parts of walls, partitions, ceilings, or tops of rooms are at least 6.1 meters above the floor.
- The ceilings or tops of rooms in print works, bleach works, or dye works, with the exception of finishing rooms or warehouses.
- The inside walls of oil mills which are lesser than a height of 1.5 meters from the ground floor level. Inside walls in tanneries lesser than the height of 1.5 meters from the ground floor level which carries out a wet process.
It also includes the parts or areas of the factories where unvarnished and unpainted wood manufacturing process is carried out.
All registers to be maintained as prescribed under sub-section (1) of section 11
Record of Whitewashing
All the dates on whitewashing, varnishing, or color-washing were accomplished must be noted as records in a Register under Form No. 7.
The compound must be kept clean
The compound of the factory must be kept clean and all the garbage must be disposed of.
Disposal of Waste
- If the factory that has a proposed drainage system that must be connected to public sewerage requires approvals from local authorities.
- Factories except the ones mentioned in sub-rule (1) must seek approvals from the Health Officer for disposing of the trade wastes.
Ventilation and Temperature
The conditions for maintaining the ventilation and temperature in factories must be as per the table below:
Ventilation
Proper ventilation must be maintained in the areas of the factories where workers carry out the mechanical work. The room must facilitate continuous fresh air.
Artificial Humidification is not permitted
- In rooms that comprise cotton spinning or weaving works shall not have artificial humidification.
- The following schedule mentions that when the wet-bulb reading of the hygrometer is more in relation to the dry-bulb reading or between any two dry bulb readings presented consecutively in the schedule when the dry bulb reading is not more than the wet bulb reading to the limit indicated to the two dry bulbs reading
However, this is applicable only when the difference between the wet bulb temperature as indicated by the hygrometer and the wet bulb temperature taken with a hygrometer outside in the shade is less than 3.5 degrees.
Provision of Hygrometer
The cotton spinning and weaving departments that have been provided with artificial humidification must have approvals from the inspector. The number of hygrometers should be as follows:
Weaving department: 1 hygrometer for departments with up to 500 looms with an additional hygrometer for excess 500 looms
Other departments: 1 hygrometer for rooms with a capacity of less than 8495 cubic meters and one for each for an excess 5663.4 cubic meters.
One more hygrometer will be provided outside each cotton spinning and weaving factory that has artificial humidification. It should have approvals from the Inspector.
Exemption from maintenance of hygrometers
On being satisfied, the Inspector may grant exemption from maintaining the hygrometer. The exemption is for departments except for the weaving department.
Copy of schedule to rule 19
A Copy of the schedule to rule 19 must be placed near every hygrometer.
Temperature at each hygrometer to be recorded
During the working hours, competent persons appointed by the manager or the Inspector shall maintain the hygrometer. The temperature must be taken between 7 a. m. or p. m. and 9 a.m. or p.m. between 11 a. m. or p. m. and 2 a. m. or p.m. and between 4 p.m. or a.m. and 5-30 p.m. or a.m.
The temperatures must be recorded in a factory-maintained Humidity Register, Form No. 6. The person who took the readings must sign the Register and attest the accuracy of the entries at the end of each month. The Inspector shall have access to the Register at all times.
Specifications of hygrometer
- Each hygrometer must contain two mercurial thermometers, one wet bulb, and the other dry bulb, of equivalent construction, size, scale, and divisional scale. They should be put on a frame with an appropriate water reservoir.
- A single layer of muslin is tightly wrapped around the wet bulb, which is kept moist by a wick attached to it and dropped into the reservoir's water. The Muslin covering and the wick must be appropriate for the purpose, and free of grease.
- There shall be no part of the wet bulb within 7.6 centimeters of the dry bulb. Also, it must not be less than 2.5 centimeters from the water's surface in the reservoir.
- The bulb must be circular and of appropriate size, and it must be fully exposed to the room's air on all sides.
- The stems' bores must be large enough to differentiate the location of the top of the mercury column from a distance of 61 cm.
- Each thermometer must be graded to allow for precise readings between 50 and 120 degrees.
- Horizontal lines on the stem must clearly designate every degree from 30 degrees to 120 degrees. Each fifth and tenth degree must be marked by longer markings than the intermediated degrees and the temperature marked opposite each tenth degree.
- The aforementioned markings must be accurate, meaning that at no temperature between 50 and 120 degrees, the stated readings must be within two-tenths of a degree.
- The thermometer must be permanently labeled with a unique number.
- (10) Each thermometer's accuracy must be confirmed by the National Physical Laboratory in London, or by another relevant authority designated by the Chief Inspector, and the certificate must be attached to the Humidity Register.
Thermometers must be maintained in efficient order
Each thermometer must be kept in good working order throughout the period of employment in order to provide accurate readings, with the following inclusions:
- the wick and muslin wrapping of the wet bulb must be restored once every week;
- the reservoir must be filled with water that must be entirely refreshed once a day. During the time of employment, the Chief Inspector may prescribe the use of distilled water or clean rainwater in any mill in certain locations;
- no water shall be put directly to the wick or covering.
Use of Inaccurate Thermometer Not Permitted
If an Inspector issues a written notice that a thermometer is not accurate, the thermometer will not be considered accurate after one month unless it has been re-assessed. The new certificate acquired will be stored with the Humidity Register.
Hygrometer not to be attached to a wall unless protected by wood
- Hygrometers shall not be affixed to a wall, pillar, or another surface unless it is protected by wood or other non-conducting material with a thickness of at least 12.7 millimeters and a distance of at least 2.5 centimeters from the thermometer bulb.
- A hygrometer must not be installed higher than 1.7 meters from the floor to the top of the thermometer stem, or indirect draughts from a fan, window, or ventilation opening.
Reading not to be taken up to 15 minutes from renewal of water
Within 15 minutes of the reservoir being refilled, no reading on any hygrometer shall be recorded for recording.
Introducing steam for humidification
The following provisions apply in any place where steam pipes are used to introduce steam for the purpose of artificially humidifying the air:
- The diameter of such pipes must not exceed 5.1 millimeters, and the diameter must not be more than 2.5 centimeters for pipes constructed after January 1, 1950.
- These pipes must be as short as is safely practical.
- All hangers supporting such pipes must be separated from the naked pipes by an insulator with a thickness of at least 12.7 millimeters.
- Any uncovered jet from such pipes must not extend more than 11.5 centimeters beyond the cover's outer surface.
- The steam pressure must be kept to a minimum, not exceeding 31.8 kilograms/6.3 square centimeters or 5 kg/ square centimeter.
- The pipe used in a department to introduce steam into the air must be adequately covered with a non-conductor as the Inspector may approve.
Lighting – application and commencement
- Rules 30 to 34 will be applicable to factories that employ persons regularly employed in a manufacturing process for more than 48 hours a week, or in shifts. They must be provided with the provision of enough lighting.
- Rules 30 to 34 take effect in respect of the class or description of factories on the dates that the State Government may set in this regard by the announcement in the Official Gazette.
Lighting of interior parts
- The general illumination over those portions of a factory where people are routinely employed must be at least 30 meters of candles measured horizontally at a height of 91.4 meters above the floor.
- When a person is passing, the lighting over all other interiors of the factory over which they pass must be at least 5 meters of candles at floor level.
- In the interior of cotton ginning facilities, artificial lighting in compliance with the following standards shall be installed and used:
- i. by candles set in glass lanterns of a pattern approved by the Inspector, each lamp of at least twenty-five candles power
- ii. by placing candles in glass lanterns with patterns permitted by the Inspector.
Prevention of Glare
This point emphasizes the importance of the prevention of glare for all the workers working in the factory. When any local light is used to enlighten or illuminate a specific part of the factory, the workers are not exposed to the glare of the lights.
Exemption Power of Chief Inspector
The Chief Inspector must be satisfied with the description of the workroom or the requisites of the rules 30 to 32. Without this, the Chief Inspector is empowered to exempt the factory or a part of it.
Exemption from Rule 31
- The components of factories listed in Part I of the Schedule appended hereto are not covered by regulation 31.
- The factories or parts of factories indicated in Part II of the said Schedule are not covered by sub-rule (1) of rule 31.
SCHEDULE Part 1
Parts of factories where light-sensitive photographic materials are manufactured or used in an exposed state, or where such exposing procedures are performed.
SCHEDULE Part 2
Parts of factories that have the following process
Quantity of Drinking Water
Every factory must offer at least 4.5 liters of drinking water for its employees, and water must be available throughout working hours.
Source of Supply
The water must come from one of the following sources:
(a) taps connected to a public water supply system or
(b) any other source certified by the Health Officer.
Storage of water
If drinking water is not available from taps connected to a continuous public water supply system, it must be stored in adequate vessels with taps and dustproof covers on plinths in the shade with drains to remove wastewater.
Such vessels must be kept immaculately clean at all times, and the water must be replaced at least once a day. Where water is taken from tube wells, it can be drawn directly into vessels from supply taps.
Cleanliness of wells or reservoirs
- Drinking water will not be supplied from any unprotected water bodies or wells or reservoirs unless it is free from any bacterial or chemical contamination.
- In the case where the water is supplied from such reservoirs or wells, then sterilization must take place weekly or more frequently.
Report from Health Officer
The Inspector may direct the Manager to obtain a report from the Health Officer as to the fitness for human consumption of the water supplied to the workers, at such time or at such intervals as he may direct, and to submit a copy of such report to the Inspector as soon as it is received from the Health Officer.
Cooling of water
In a factory that employs 25 workers must have the following:
- (a) From the 1st of March until the 30th of November each year, the drinking water supplied to the workers must be cooled with ice or another suitable technique:
Provided, however, that the ice used in the drinking water must be clean and come from a source approved in writing by the Health Officer;
- (b) (i) Cooled drinking water shall be provided in every canteen, lunchroom, and restroom, as well as at easily obtainable points all across the factory, which shall be referred to as "Water Centers"
ii) at least one such center shall be provided on each floor;
- c) The "Water Centers" must be protected or covered and properly drained.
- (d) (i) The number of "Water Centers" to be provided shall be one for every 150 workers employed in the factory at any given time:
Provided, however, that if a factory employs more than 450 workers, one "Water Centre" as aforesaid for every 150 workers up to the first 450, and one for every 450 workers or part thereof thereafter, and that when counting the number, the maximum number of workers working at any time during the day is taken into account.
- (ii) Each water center must have at least 3 fountains or taps which shall be at a distance of 61 centimeters. The tap must also have a trough to drain the excess water out.
Where mechanical refrigerating units with drinking water fountains are installed throughout the factory, the number of "Water Centers" may differ from the requirement established under sub clause I above, as long as the total number of fountains supplied meets the specified threshold, if the number of "Water Centers" as defined in sub-clause (i) were provided
- (i) Every "Water Centre" must be kept clean and orderly;
- (ii) every "Water Centre" must be supervised by a suitable person who will distribute the water and be provided with clean clothing while on duty.
Latrine accommodation
There will be 1 latrine at the least where 25 females are employed and one latrine where 25 males are employed. It will be adequate. If one latrine is provided for every 25 males up to the first 100, and one for every 50 subsequently.
Any odd number of workers less than 25 or 50 shall be counted as 25 or 50, respectively, and the number of workers to be considered shall be the total number of workers engaged at any given moment during the day.
Privacy of Latrines
Every latrine must be covered and partitioned to ensure privacy. It must also have a proper door and bolts.
Signboards to be displayed
Where both sexes are employed, a notice "For Men Only" or "For Women Only" shall be posted outside each lavatory block in the language that can be understood by the majority of the workers. The announcement must also include a male or female figure.
Urinal accommodation
There must be one urinal among every 50 male workers at any given time; however, if the number of male workers employed surpasses 500, one urinal for every 50 men up to the first 500 men. Thereafter, there should be one urinal for every 100.
Latrines and Urinals to conform to the requirements of public health
Other than those connected to an efficient water-borne sewerage system, all latrines and urinals must meet the requirements of the Public Health Authorities.
White-washing, color-washing of latrines and urinal
Every toilet and urinal must have its walls, ceilings, and partitions white washed or colored, and the white-washing or coloring must be done at least once every four months. The date for the same will be entered in Form No. 7.
Construction and maintenance of drains
All drains transporting waste or sullage water must be made of masonry or other impervious material and cleansed on a regular basis.
Water taps on latrines
In or near such latrine accommodations, there must be water taps that are easily accessible. For every ten latrines, there must be at least one tap. The water taps must be connected to the municipal water supply or to a sufficiently large overhead storage tank so that water is available at all times when the workers are in the workplace.
Number and location of spittoons
The inspector must be satisfied with the number and position of the spittoons to be delivered. Such spittoons must be mounted on a 91.4-centimeter-high stand or bracket.
Type of spittoons
The spittoons must be one of the following types:
(a) a galvanized iron container that has a conical funnel-shaped cover. The container must have a layer of disinfectant.
(b) a container filled with dry and clean sand and it must have a covered layer of bleaching powder; or
(c) any other type that the Chief Inspector permits
Cleaning of spittoons
Every day, the spittoons indicated in sentence (a) of Rule 52 must be emptied, cleaned, and disinfected once in a day.
Chapter 4: Safety
This chapter comprises seven major Schedules and their sub-sections that explain the various definitions of the tools and components used in the factories.
Schedule I: Textile Machinery Except Jute Mills
Application
This schedule is for the factories involved in the manufacturing process of textile except for jute. However, it does not apply to machinery in the factories that exclusively manufacture synthetic fibers.
Definitions
The schedule needs us to learn specific definitions mentioned as follows:
- Calender: A group of heavy rollers installed on vertical side farms and configured to pass cloth between them is referred to as a calender. Calenders can have anything from two to 10 rollers or bowls, with some of them being heated.
- Embossing Calendar refers to a calendar having two or more rolls, one of which is used to create fabric figures of various types of fabric.
- Card refers to a machine made up of cylinders of various sizes and, in some cases, flats coated in card clothing and arranged in a way to separate stapled fibers into distinct relationships.
- Card clothing refers to the material that covers the surfaces of a card's cylinder and other areas, and comprises a thick base material made of, either textile textiles or other materials.
- Comber refers to a machine for combing cotton wool fibers.
- Combing machinery refers to a broad category of equipment that includes combers, silver lap machines, ribbon lap machines, and gill boxes, but excludes cards.
- A factory staple cutter is a machine with rotary blades that are used to cut textile fibres into staple lengths.
- Garnet machine refers to a variety of machines that open hard twisted waste of wool, cotton, silk, and other materials.
- A GUI box is a machine that is used to manufacture worsted yarns.
- Any pair of rolls or drums with a nip between them is referred to as in-running rolls.
- Interlocking arrangement refers to a device that prevents dangerous parts of a machine or the machine itself from being set in motion while the guard, cover, or door is unlocked. It also keeps the guard, cover, or door closed and locked while the machine or dangerous part is in motion.
- Kier refers to a huge metal vat where fabrics are boiled.
- A ribbon tapper is a mechanism or a component of a machine that prepares laps for feeding a cotton comb.
- Loom refers to a machine that causes two series of yarns to cross at right angles to interlock.
- A starch mangle is a mangle used exclusively for starching cotton items.
- A water mangle is a calendar with two or more rolls that is used to squeeze water out of clothes before drying.
- The term mule refers to a spinning frame with two primary sections: a head stock and a carriage. The head stock does not move but the carriage moves. During the spinning operation, the carriage spans the entire width of the machine and moves steadily towards and away from the head stock.
- The danger zone between two rolls is called nip, which creates a nipping hazard due to their location and movement;
- The term openers and pickers refers to a broad category of machinery that includes breaker nickers.
- Paddlef refers to a solution trough with two or more squeeze rolls through which cloth passes after being mordant or dry bathed:
- Plating machine refers to a machine that folds cloth into standard length folds for ease of future processing
- Roller printing machine refers to a machine with a big central cylinder, or pressure down, around which are arranged a series of engraved colour rollers a furnisher roller, doctor blades, and other components. Fabric printing is done on this machine.
- A machine for bleaching fabric in rope or open width from the following layout is referred to as a continuous bleaching range. After being wetted out, the fabric is squeezed into a saturator containing a caustic soda solution, and then into an enclosed J-Box. Before the cloth is packed down in the J-Box, a V-shaped structure is added to the front part of the J-Box to ensure consistent and speedy steam saturation. The cloth is transferred down the first arm of the "V" and up the second arm as a single strand rope. At this time, steam is pumped into the "V" at the top end of the second arm, rapidly saturating the cloth with the stream. The J-Box capacity ensures that the cloth stays hot for long enough to finish the scouring process. After that, it goes through a set of washers with a squeeze roll in between. The fabric is subsequently treated with the peroxide solution in the second set of saturators, J-boxes, and washers. The procedure can be used to open-width cloth with minor changes to the unit's form.
- The term "mercerizing range" refers to a three-bowl mangle, a tenter frame, and a number of washing and scouring boxes. The entire setup is in a straight line, and all components are operational at all times. The process involves soaking the fabric in sodium hydroxide, stretching it while saturated, and then rinsing off the majority of the caustic before relieving tension
- Sanforizing machine refers to a machine that includes a large steam-heated cylinder, an endless, thick, woolen felt that is in close contact with the cylinder for the majority of its circumference, and an electrically heated shoe that processes the cloth against the blanket while it is stretched as it curves around the feed-in-roll;
- Shearing machine refers to a machine that shears the cloth. A number of steel blades spirally placed on a roller produce cutting action. A fixed ladder blade revolves in close proximity to the roller. A machine may have one to six of these rollers.
- A machine may have one to six of these rollers A singering machine is one that includes a heated roller, plate, or an open gas flame. To eliminate fuzz or hairiness, the cloth or yarn is quickly passed over the roller or the spot, or through an open gas flame.
- A tenter frame is a machine that uses tension to dry textiles. It primarily comprises of a pair of infinite traveling chains attached to tracks by fine pin clips. The two chains that diverge as they go forward keep the cloth firmly held at the salvages, allowing the material to be brought to the required width
- Warper refers to a machine that prepares and arranges strands for a fabric's warp, particularly a beam warper.
General safety requirements
- Every textile machine must be equipped with its own mechanical or electrical means of starting and stopping. On machines that use belts and shafting, a belt shifter lock or an equivalent positive locking device should be installed.
- Stopping and starting handles or other controls must be designed and positioned so that the operator's hand or fingers do not come into contact with any moving element or other machine components.
- All belts, pulleys, gears, chains, sprocket wheels, and other dangerous moving parts of machinery must be safely guarded, whether they are part of the machinery or utilized in conjunction with it.
Further, the section explains the functioning of each of the following parts:
- Openers and pickers
- Cotton cards
- Garnett machines
- Gill boxes
- Silver and ribbon tappers (cotton)
- Speed frames
- Spinning mules
- Warpers
- Slashers
- Looms
- Valves of kiers. tanks, and other containers
- Shearing machines
- Continuous bleaching range (cotton and rayon)
- Mercerizing range (piece goods)
- Tenter frames
- Paddlers
- Centrifugal extractors
- Squeezer or wringer extractor, water mangle, starch mangle, back
- Sanforizing and palmar machine
- Rope washers
- Laundry washer tumble or shaker
- Printing-machine(roller-type)
- Calendars
- Rotary staple cutters
- Plating machines
- Hand-baling machine
- Flat work ironer
Schedule II: Cotton Gliming
This schedule highlights the use of Line Shaft. The line or second motion in cotton ginning factories shall be completely enclosed by a continuous wall or unclaimable fencing with only as many openings as are required for access to the shaft for cottonseed removal and cleaning. These kinds of openings will be provided with gates or doors that must be kept closed and locked.
Schedule III: Wood-Working Machinery
This schedule provides definitions of the terms that relate to the Wood-working machinery. Along with the definitions, the original document also provides details of the devices which are as follows:
- Stopping and starting device
- Space around machines
- Floor
- Training and Supervision
- Circular saws
- Push sticks
- Band saws
- Planning machines
- Vertical spindle molding machine
- Chain mortising machines
- Adjustment and maintenance of guard
- Exemption
Schedule IV: Rubber Mills
- A Rubber Mill is defined as a machine that uses rollers to break down, crack, wash, grate, mix, refine, and warm rubber or rubber goods.
- A calendar refers to rubber compound used for friction, sheeting, coating, and spreading machinery with rolls.
The next part of this section comprises details about the installation of devices. Here is what the next paragraphs entail:
- Installation of machines
- Safety devices
- Maintenances of safety devices
Schedule V: Centrifugal Machines
Definition: Centrifugal Machines consists of centrifugal extractors, separators, and driers.
Each of the parts of the centrifugal machines must be of good design, they should be properly maintained. They should be evaluated for their efficiency by a competent person regularly.
Aside from this, the original document of Gujarat Factories Rules 1963, includes the following points with regards to the centrifugal machines:
- Interlocking guard for drum or basket
- Breaking arrangement
- Operating speed
- Exemptions
Schedule VI: Power-Press
Application: This schedule is applicable for all the types of power-presses that includes press brakes apart from working hot metal.
The other parts of the schedule include the following:
- Definitions
- Starting and stopping mechanism
- Protection of tool and die
- Appointment of persons to prepare power presses for use
- Examination and testing power presses and safety device
- Defects disclosed during a thorough examination and test
- Inspection and test of safety device
- Defects disclosed during an inspection and test
- Identification of power presses and safety devices
- Training and instructions to operators
- Exemptions
Schedule VII: Shears, Slitters and Guillotine Machines
The points included under this schedule includes the following factors with regards to the shears, slitters and guillotine machines:
- Definitions
- Guillotine and. Shears:
- Slitting machines
- Index cutters and vertical paper slitters
- Corner cutters
- Band knives
- Register of specially trained adult workers
- Belt etc., to be regularly examined
- Employment of Young persons on dangerous machines
- Exemption of Certain hoists and lifts
- Exemption of Certain hoists and lifts
- Lifting machines, chains, ropes and lifting tackles
- Pressure vessels or plant
- Safety of water sealed gas-holder
- Reaction vessels and kettles
- Excessive weights
- Protection of eyes
- Exemptions under Sub-sec. (5) of Sec. 37
- Means of escape in case of fire
- Fire protection
- Ladders
- Protection of worker attending to prime movers
- Quality of personal protective equipment
- Precautions and examination of machine
- Thermic fluid heaters
- Fragile roots
- Safety Committee
- Ovens and Driers
Chapter 4A: Site Appraisal Committee
The chapter comprises the details of the following terms and terminologies:
- Definitions of Hazardous chemical, industrial activity, isolated storage, major accident, pipeline, schedule, site, words and expressions.
- Collection, development and dissemination of information
- General responsibility of the Occupiers
- Notification of major accidents
- Industrial activities to which sub-rule (6) to (12) apply
- Notification of industrial activity
- Updating of the notification under sub-rule (e)
- Transitional provision
- Safety reports
- Updating of reports under sub-rule (9)
- Requirements for further information
- Preparation of on-site emergency by the Occupier
Schedule 1, Part 1: Improvement notice SCHEDULE –I (Indicative criteria and list of chemicals)
PART 1 includes:
Indicative Criteria
–a) Toxic chemicals
–b) Flammable chemicals
–c) Explosive
PART 2: List of Hazardous Chemicals
This part includes 7 schedules which are as follows:
SCHEDULE – 2 (Isolated Storage of Installation other than those covered by Scheduled 4) SCHEDULE – 3 (List of Hazardous chemicals for application of sub-rules 5 and 7 to 13)
– PART – I – List of Hazardous Chemicals
– PART –II –Classes of chemicals not specifically named in Part I
SCHEDULE – 4 (Industrial Installation within the meaning of sub-rule 1(b) (i))
SCHEDULE – 5 (Safety Data Sheet)
SCHEDULE – 6 (Information regarding notification of a major accident)
SCHEDULE –7 (Information for the notification of activities / sites)
SCHEDULE –8 (Information to be furnished in a Safety Report)
The chapter 4A continues with the following points extensively explaining the terms applicable to the factories:
- Disclosure of information to workers
- Disclosure of information to the Chief Inspector
- Review of the information provided to workers
- Confidentiality of Information
- Health and Safety Policy
- Information on industrial wastes
- Collection, development and dissemination of information
- Making available Health Records to workers
- Qualifications, etc. of Supervisors
- Medical Examination
- Occupational Health Centers
SCHEDULE Rule 68-U (b) (1)Equipment used as Occupational health center in factories
This includes Ambulance van, decontamination facilities, Issues of guidelines, along with a safety committee for every factory.
Chapter 5: Facilities for Workers
This chapter includes details of the facilities that the workers must receive in terms of first aid, ambulance room, canteens and so on. Let’s take a look at what are the points that this chapter covers:
- Washing Facilities
- Facilities for storing and drying clothing SCHEDULE
- First aid appliance 70-A Notice regarding first-aid
- Ambulance room
- Canteens
- Dining Hall
- Equipment
- Prices to be displayed
- Accounts
- Managing Committee
- Food to be served and price for food
- Shelters, rest rooms and lunch-rooms
- Creches
- Wash room
- Supply of Milk and Refreshment
- Creche Staff
- Qualifications of woman in charge
Chapter 6: Working hours for Adult Workers
This chapter includes what the working hours for all the adult workers will be like. It also gives away the details of the compensatory holidays and overtime slips, and so on. Let’s take a look at what this comprises.
- Compensatory Holidays
- Factories exempted under section 58
- Muster-roll for exempted factories
- Overtime Slips
- Double employment of workers
- Notice of periods of work for adults
- Register of adult workers
- Persons designated for supervision or managements or confidential position
The chapter 6 also introduces a schedule for the list of persons defined to hold positions of Supervision or Management in Factories
I – All factories
II – Engineers Workshops
III – Spinning and Weaving Mills
- In continuation with the sub-parts of the chapter, the following factors are listed:
- List to be maintained of persons on confidential position of supervision of management
- Exemption of certain adult workers
SCHEDULE
- Exemption to women workers who work in fish-curing and fish canning factories
Chapter 7: Employment of young Individuals
The chapter 7 provides information about the scenarios in which the young individuals are employed in a factory.
- Notice of periods of work for children: The information about the notice of periods for child workers will be covered in Form No. 16.
- Register of child workers: Form No. 17 shall be used to keep track of child workers. This registration must be typed up from scratch every year and kept for a period of twelve months.
Chapter 8: Annual Leave with Wages
This chapter of Gujarat Factories Rules 1963 is dedicated to the annual leaves with wages of the workers. The following points are included in this chapter:
- Leave with wages register
- Leave Book
- Medical Certificate
- Notice Of Inspector of Lay off
- Notice by worker
- Notice by Manager
- Mode of leave
- Payment of leave wages due if worker pass
- Maintenance of register in case of exemption under section 84
Chapter 9: Special Provisions
We shall get to know about the special provisions drafted for the various dangerous manufacturing process in this chapter. Here is what the chapter covers:
Dangerous manufacturing Process or Operations
SCHEDULE–I
(Manufacture of aerated wasters and related processes)
1. Fencing of machines
2. Face-guards and gauntlets
3. Wearing of face guards and gauntlets
SCHEDULE–II
Electrolytic plating or oxidation of metal articles by use of an electrolyte containing acids, bases or salts of metals such as chromium, nickel, cadmium, zinc, copper, silver, gold, etc.
Schedule II of this chapter includes definitions of the following terms:
a) “electrolytic process”
b) “bath”
c) “employed”
It also covers the points relevant to the factory industry:
- Exhaust draught
- Prohibition relating to women and young persons
- Floor of workrooms
- Protective devices
- Water facilities
- Cautionary placard
- Medical facilities provided and record of examinations and tests
- Medical Examination by the Certifying Surgeon
SCHEDULE–III : Manufacture and repair of electric accumulators
This schedule comprises definitions of the following terms:
- a) “Lead Process”
- b) “Manipulation of raw oxide of lead”
- c) “Suspension”
- Prohibition relating to women and young persons
- Separation of certain processes
- Air space
- Ventilation
- Distance between workers in pasting room Floor of work-rooms
- Work-benches
- Exhaust draught
- Fumes and gases from melting post
- Container for dross
- Container for lead waste
- Racks and shelves in drying room
- Medical examination
- Protective clothing
- Mess room
- Cloak-room
- Washing facilities
- Time to be allowed for washing
- Facilities for bathing
- Foods, drinks, etc. prohibited in work-rooms
- Storage of lead oxides
- Re-use of paper or cloth restricted
SCHEDULE –IV: Glass Manufacturers
The schedule 4 gives details about the exemption and definitions of the terms relevant to the field of glass manufacturers.
- Exemption
- Definitions
- a) “Efficient exhaust draught”
- b) “Lead Compound”
- Exhaust draught
- Prohibition relating to women and young persons
- Floor and work-benches
- Use of Hydrofluoric acid
- Storage and transport of hydrofluoric acid
- Food, drinks, etc., prohibited in work-rooms
- Protective clothing
- Washing facilities
- Medical checkup
SCHEDULE –V: Grinding of glazing of metals and processes incidental thereto
The schedule gives complete explanation of the terms which are Grindstone, Abrasive wheel, Grinding, Glazing, Racing, Hacking, Rodding.
The following points are touched upon in the schedule:
- Exception
- Equipment for removal of dust
- Restriction on employment on grinding operation
- Glazing
- Hacking and rodding
- Evaluation of dust equipment
SCHEDULE –VI : Manufacture and treatment of lead and certain compounds of lead
- Exemptions
- Definitions
- a) Lead Compound
- b) Efficient Exhaust Draught
- Application
- Prohibition relating to women and young persons
- Requirement to be observed
- Exhaust draught
- Certificate of fitness
- Medical Examination
- Food drinks, etc. prohibited in work-rooms
- Protective clothing
- Cleanliness of work rooms, tools, etc.
- Washing facilities
- Mess-room or Canteen
- Cloak room
SCHEDULE –VII
This schedule is about the Generation of gas from dangerous petroleum as defined in clause (b) of Section 2 of the Petroleum Act, 1934.
It comprises explanation of the following terms:
- Prohibition relating to women and young persons
- Flame traps
- Generation buildings or room
- Fire extinguishers
- Plant to be approved by Chief Inspector
- Escape of Petrol
- Prohibition relating to smoking etc.
- Access to petrol or container
- Electric fittings
- Construction of doors
- Repair of containers
SCHEDULE –VIII
This schedule consists of the details of Cleaning, smoothing, roughening or removing or any part of the surface of articles, by a jet of sand, metal shot, or grit or other abrasive propelled by a blast of compressed air or steam (Blasting Regulations).
Along with this, there are definitions of the following terms:
- Definitions
a) Blasting
b) Blasting enclosure
c) Blasting chamber
d) Cleaning of castings
- Prohibition of Sand Blasting
- Precautions in process of Blasting Operations
1) Blasting to be done in blasting enclosure
2) Maintenance of blasting enclosure
3) Provision of separating apparatus
4) Provision of ventilating plant
5) Operation of ventilating plant
- Inspection and examination
- Provision of protective helmets gauntlets and overalls
- Precautions while cleaning and other work
- Storage accommodation for protective wear
- Maintenance and cleaning of protective wear
- Maintenance of vacuum cleaning plant
- Restrictions in employment of young persons
- Power to exempt or relax
SCHEDULE –IX
The schedule 9 is about Liming and tanning of raw hides and skins and processes incidental thereto.
Fundamentally, the schedule has cautionary notices, protective clothing, washing facilities, foods, and first aid treatments.
SCHEDULE –X
“Manufacture of chromic acid or manufacture or recovery of the bichromate of sodium, potassium or ammonium” is described in this schedule.
There are definitions of Chrome process, efficient exhaust draught, and suspension. Furthermore, it has the following points:
- Prohibition relating to women and young persons
- Efficient exhaust draught 3-A Separation of certain processes
- Washing facilities
- Time to be allowed for washing
- Flooring
- Medical facilities
- Protective equipment
- Use of protective equipment
- Cloak room
- Mess room
- Food, drinks prohibited in work-rooms
- Medical examination
- Fencing of vessels
- Cautionary notice
- Exemption
SCHEDULE –XI
This schedule is about Manufacture or Manipulation of carcinogenic dye Intermediates. The Schedule will be applicable to all factories or parts of factories where the substances mentioned in paragraphs 3 and 4 are found, manufactured, handled, or used.
The schedule comprises of the following parts:
- Application
- Definition
a) “Controlled substances”
b) “efficient exhaust draught”
c) “prohibited substances”
d) “first Employment”
- Prohibited substances
- Controlled substances
- Prohibition of employment
- Requirements for processing or handling controlled substances
- Personal Protective Equipment
- Prohibition relating to employment of women and young persons
- Floor of work-room
- Disposed of empty containers
- Manual handling
- Instructions regarding risk
- Cautionary placards
- Obligations of the workers
- Washing and bathing facilities
- Food, drinks etc. prohibited in work-room
- Cloak room
- Mess room
- Time allowed for washing
- Restriction on age of persons employed
- Medical facilities and records of examination and tests
- Medical examination by the Certifying Surgeon
- Exemptions – Prohibited substances
It also mentions an appendix that pans out the details about cautionary Placard / Notice – Carcinogenic dye intermediates.
SCHEDULE –XII
Schedule XII is about Manipulation of acids or alkalis. It has the following parts under it:
- Definitions
- Application
- Flooring
- Protective equipment
- Water facilities
- Cautionary Notice
- Transport
- Device for handling acids or alkalis
- Opening of valves
- Cleaning tanks, stills, etc.
- Storage
- Fire extinguishers
- Exemption
SCHEDULE –XIII
Manufacture of bangles and other articles from cinematograph film and toxic and inflammable solvents is what this schedule is about. The schedule includes definitions of the terms as follows:
- Toxic inflammable solvents
- Bangle polish and bangle mixture
- Suspension
- Approval
- First employment
After listing the definitions, here is what the other parts of the schedule include:
- Application
- Prohibition relating to the employment of women and young persons
- Medical Examination
- Protective clothing
- Ventilation
- Drying of cinematograph film
- Storage of raw materials
- Disposal of waste films
- Prohibition for smoking
- Caution with regard to electrical installation
- Floor of work-rooms
- Time to be allowed for washing
- Washing facilities
- Facilities for bathing
- Cloakroom
- Food, drinks, etc. prohibited in work-rooms
- Mess-room
- Fire-fighting appliances
- Means of escape in case of fire
- Cautionary notices
SCHEDULE –XIV
This schedule applies to the Processes involving manufacture, use or evolution of carbon Disulphide and hydrogen sulphide.
It includes the following parts that apply to the industry:
- Definitions
a) (i) breathing apparatus
(ii) any other suitable apparatus
b) churn
c) dumping
d) efficient exhaust draught”
e) fume process
f) life belt
g) suspension
- Efficient exhaust draught and supply of fresh air
- Air analysis
- Electric fittings in carbon disulphide fume process room except the spinning room
- Washing facilities
- Protective equipment
- Use of protective equipment
- Storage of protective equipment
- Mess room
- Prohibition relating to smoking etc. in carbon disulphide fume process room
- Prohibition to remain in fume process room
- Mechanical Examination
- Breathing apparatus and measures
- Cautionary placard and instructions
- Exemption
SCHEDULE –XV
Manufacture and Manipulation of Dangerous Pesticides
- Definitions
a) Pesticides
b) dangerous pesticides
c) Suspension
d) first employment
e) efficient exhaust draught
f) manipulation
- Application
- Cautionary placard
- Prohibition relating to the employment of women and young persons
- Air space
- Prohibition of the said manufacturing process without efficient exhaust draught
- Floor of work-room
- Work Benches
- Waste
- Empty containers used for dangerous pesticides
- Manual handling
- Protective clothing
- Medical facilities
- Medical examination
- Time allowed for washing
- Washing and bathing facilities
- Food, Drinks prohibited in work rooms
- Cloak-Room
- Mess Room
- Exemption
- Manipulation not be undertaken
APPENDIX I : List of Dangerous Pesticides
APPENDIX II: Cautionary Placard
This is the placard that cautions about pesticides and their use. It lays down the following norms:
Pesticides are harmful substances in general.
- As a result, do not chew, eat, drink, or smoke in rooms where pesticides are handled, and keep food and drink away from pesticides. Put on the provided protective gear, such as gloves, aprons, clothing, boots, and so on.
- Wash your hands before meals or after coming into contact with pesticides on any area of your body with water and soap.
- Take a shower and change into another set of clothes before leaving the factory.
- Never use a pesticide-contaminated container as a pot for food or drink.
- Use a handled scoop instead of your hands while handling pesticides.
- Avoid splashing pesticides on your body, the floor, or the table.
- Maintain physical hygiene
- Report any illness, such as nausea, vomiting, or giddiness, to the manager, who will make the required medical arrangements.
SCHEDULE XVI
This schedule takes us through the Compression of oxygen and hydrogen produced by the electrolysis of water.
This schedule touches upon the the room in which the electrolyser plant is situated. It must be distinct from the oxygen and hydrogen storage and compression plant, as well as the electric generator room. Apart from this, the schedule explains how oxygen and hydrogen should be treated and handled.
Both the gases must not be compressed and all the electric devices handling them must be placed in the electrolyser rooms. Moreover, no light ot flame must come in contact with the hydrogen compressor. Each gas holder must also have an alarm and a trip switch to stop the compression.
Schedule XVII
This schedule deals with the Handling and Processing Of Asbestos. Manufacture Of Any Article of Asbestos and Any Other Process of Manufacture or Otherwise In Which Asbestos Is Used In Any Form.
Application:
This Schedule applies to all factories or sections of factories that carry out any of the following procedures:
- asbestos disintegrating, mixing, or sieving, and any other processes requiring asbestos handling and manipulation.
- all steps in the production of asbestos textiles, including preparation and finishing
The schedule also applies to the manufacturing units of asbestos cement goods and any other process in which the asbestos is let out in the environment.
The schedule provides an insight in to the definitions of the following terms:
- Asbestos
a) asbestos dust
b) airborne asbestos dust
c) respirable asbestos fibers
d) exposure to asbestos
e) asbestos textile
f) Approved
g) breathing apparatus
h) efficient exhaust draught
i) preparing
k) Protective clothing
- Tools and Equipment
- Exhaust drought
- Testing and examination of ventilating system
- Segregation in case of certain process
- Storage and distribution of loose asbestos
- Asbestos sacks
- Maintenance of floors and workplaces
- Breathing Apparatus and Protective clothing
- Separate accommodation for personal clothing
- Washing and bathing facilities
- Mess-room
- Prohibition of employment of young persons
- Prohibition relating to smoking
- Cautionary Notice
- Air Monitoring
- Medical facilities and records of medical examinations and tests
- Medical examination by Certifying Surgeon
SCHEDULE XVIII
This schedule is for the Manufacture of Articles from Refractory Materials Including Manufacture of Refractory Bricks.
- Application
- Definitions
a) Refractory material
b) Refractory bricks
c) Efficient exhaust draught
The following processes are covered by this Schedule:
handling, moving, breaking, crushing, grinding, or sieving any refractory materials comprising not less than 25% total silica for the purpose of manufacture. It also includes the items used in the construction of furnaces and flues, as well as crucibles, and compositions or other materials used in the preparation of metal-casting molds.
SCHEDULE XIX
PART – I: Chemicals Works
- Application: This Schedule shall apply to all incidental operations carried out in chemical works.
- Definitions
a) Chemical Works
b) efficient exhaust draught
c) bleaching power
d) chlorate
e) caustic
f) chrome process
g) nitro or amino process
h) permit to work
i) toxic substances
j) emergency
k) dangerous chemical reactions
l) manipulation
m) approved personal protective equipment
n) appropriate personal protective equipment
o) confined space
PART – II: First Schedule of the Act
The part will include the following points:
- Housing keeping
- Improper use of chemicals
- Prohibition on the use of food, etc
- Cautionary Notices and instructions
- Evaluation and provision of safeguards before the commencement of process
- Authorized entry
- Examination of instruments and safety devices
- Electrical installations
- Handling and storage of chemicals
- Facilities for isolation
- Personal protective equipment
- Alarm systems
- Control of escape of substances into the work atmosphere
- Conduct of dangerous chemical reactions
- Testing examination and repair of plant and equipment
- Staging
- Seating arrangements
- Entry into or work in confined spaces
- Maintenance work etc
- Permit to work system
- Safety sampling personnel
- Ventilation
- Procedure for meeting emergencies
- Danger due to effluents
PART – III: Fire and Explosions Risks
Here is what this part consist of:
- Internal combustion engine, electric motor or other electrical equipment
- Static Electricity
- Lightning protection
- Process heating
- Leakage of flammable liquids
- Safety valves
- Installation of pipe line etc
- Fire-fighting systems
PART – IV: Risks of Toxic Substances
Here is what the part comprises:
- Leakage
- Drainage
- Covering of vessels
- Continuous exhaust arrangement
- Work Bench
- Waste disposal
PART – V: Special Provisions
The various special provisions are as follows:
- Special precautions for Nitro or Amino processes
- Special precautions for chrome processes
- Special precautions for processes carried out in all glass vessels
- Special precautions for processes involving chlorate manufacture
- Special precautions in use of plant and equipment made from reinforced plastics
PART – VI: Additional Welfare Amenities
- Washing facilities
- Mess-room facilities
- Cloakroom facilities
- Special bathing facilities
The next parts, PART – VII involves Duties of workers and PART – VIII is all about Restrictions on the employment of young persons under 18 years of age and women. There is also an appendix concerning special bathing accommodation in pursuance of para 4 of Part VI.
Appendix (Concerning special bathing accommodation in pursuance of para 4 of Part VI.)
SCHEDULE XX
The schedule entails the description related to the manufacture and use of Benzene and its allied products. It also comprises the following elements:
- Definition
a) substances containing benzene
b) substitute
c) enclosed system
e) efficient exhaust draught
- Manner of using Benzene or its substitutes
- Protection against inhalation
- Measures against skin contact
- Prohibition relating to employment of women and young persons
- Labelling
- Improper use of benzene
- Prohibition of consuming of food etc. in work rooms
- Instructions regards risks
- Cautionary notices
- Washing facilities, cloak rooms and mess room
- Medical Examination
An Appendix A (referring to clause 3 b) which is about production of benzene, steps where benzene is used for the process of chemical analysis. Also, Appendix B (referring to clause 11) highlights the hazards of inhaling benzene and the corresponding preventive measures that need to be taken for the same.
Schedule XXI
This schedule explains Process of Extracting Oils and Fats from Vegetables and Animal Sources in Solvent Extraction Plants.
This includes specific definitions and the following terms:
- Location and Layout
- Electrical installations
- Restriction on smoking
- Precautions against friction
- Fire-fighting
- Precaution against power failure
- Magnetic separators
- Venting
- Waste water
- Ventilation
- Housekeeping
- Examination and repairs
- Operating personnel
- Employment of women and young persons
- Vapor detection
- Examination
SCHEDULE XXII
The schedule includes details about the manufacturing process or operations in Carbon Disulphide plants.
The various components of this schedule are as follows:
- Application
- Construction, installation and operation
- Electrodes
- Maintenance of charcoal level
- Charcoal separator
- Rupture discs and safety seal
- Pyrometer and manometers
- Check valves
- Inspection and maintenance of electric furnaces
- Maintenance of records
- Electric apparatus, wiring and fittings
- Prohibition relating to smoking
- Means of escape
- Warning in case of fire
- Fire-fighting equipment
- Bulk
- Liquid Sulphur
- Training and supervision
- Washing facilities
- Personal protective equipment
- Cloak rooms
- Unauthorized persons
SCHEDULE XXIII
Operations involving High Noise levels is the subject this schedule discusses. It also clarifies on the following points:
- Application
- Definitions
a) "Noise"
b) "High noise level"
c) "Decibel"
d) "Frequency"
e) "dBA"
f)" A-weighting"
- Protection against noise
SCHEDULE XXIV
The schedule is about Welding/Cutting operation with the use of LPG/Acetylene/Argon. It discusses the two points as mentioned:
- Applicability
- Equipment
SCHEDULE XXV
Manufacture of pottery
- Application
- Definitions
a) "pottery"
b)" efficient exhaust draught"
c) "jetting"
d) "leadless glaze"
e) "low solubility glaze"
f) "ground or powdered flint or quartz"
g) "potter’s shop"
- Efficient exhaust draught
- Separation of processes
- Prohibition on use of glaze
- Prohibition relating to women and young persons
- Prohibition of screen to potter’s wheel
- Control of dust during cleaning
- Floor of certain workroom
- Protective equipment
- Washing facilities
- Time allowed for washing
- Messroom
- Food, Drinks, etc. prohibited in work-rooms
- Cloakroom
- Medical examination
- Certificate of fitness
SCHEDULE XXVI
The schedule focuses on the Operations in Foundries. The other parts of the section include the following:
- Application
- Definitions
a) approved respirator
b) cupola or furnace
c) dressing or fetting operator
d) foundry
e) Knock-out operation
f) pouring aisle
- Prohibition of use of certain materials as parting materials
- Arrangement and storage
- Construction of floors
- Cleanliness of indoor workplaces
- Manual operations involving molten metal
- Gangways and pouring aisles
- Work near cupolas and furnaces
- Dust and fumes
- Maintenance and examination of exhaust plant
- Protective Equipment
- Washing and bathing facilities
- Disposal of waste
- Disposal of dress and skimmings
- Material and equipment left out of doors
- Medical facilities and records of examinations and tests
- Medical examination by Certifying Surgeon
The subsequent sections include “notification of accidents and dangerous occurrences” and “notice of poisoning or disease”
Chapter 10: Supplemental Information
This chapter is based on the rule prescribed under section 107.It includes the following:
- Procedure in appeals
- Appointment of assessors
- Remuneration of assessors
- Display of notice
- Returns
1) Annual Return
2) Half yearly return
3) Annual return of holidays
- Service of notice
- Information required by the Inspector
- Muster-roll
- 110-A Identity Cards
- (1) Register of accidents and dangerous occurrences
- Maintenance of Inspection Book
- Information regarding closure of factories
- Repeal and saving
The details pertaining to the chapters and appendices of the rules conclude here. However, if you are looking for the various forms applicable in the scope of Gujarat Factories Rules, we have put together a separate page that helps you find details of all the forms.
How can Deskera Help You?
Deskera People has the tools to help you manage your payroll, leaves, employee onboarding process, and managing employee expenses, all in a single system. Easily generate pay slips for your employees and simplify your payroll management with Deskera People. It also digitizes and automates HR processes including hiring, expenses, payroll, leave, attendance, and more.
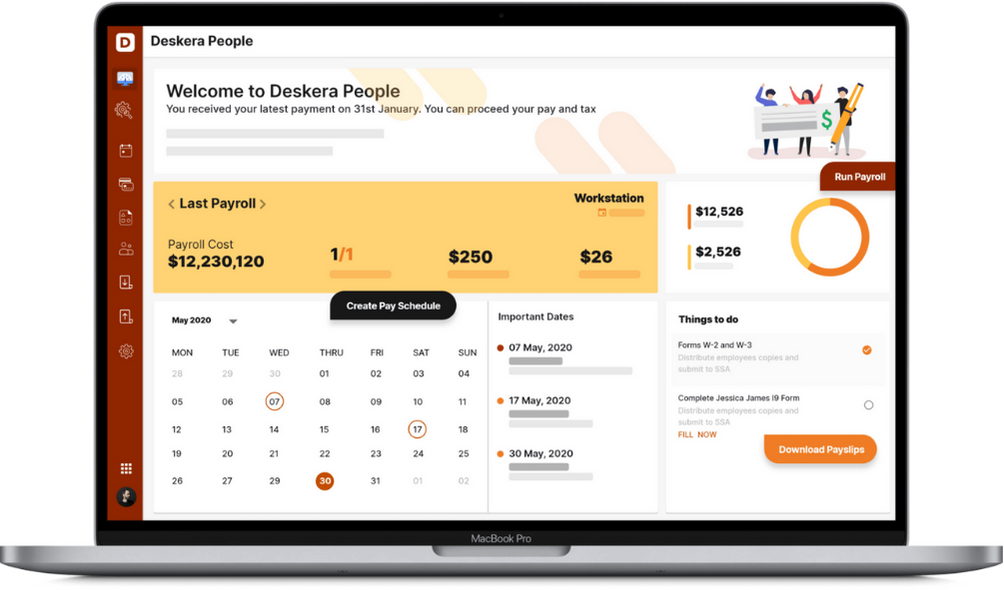
Key Takeaways
The Factories Act is a document of legislation intended to protect workers' health, safety, and welfare at work. The Gujarat Factories Rules, 1963, are the rules that the state of Gujarat has created in accordance with the Act.
With the diverse rules, chapters, and schedules the plan the rules lay out the laws for the ways workers must be treated and the facilities they must receive while at work. The document also introduces the rules for so many different industries and factories where a wide range of manufacturing process is being carried out.
Whether it is welding/cutting operation or operations in foundries, or whether it is the manufacturing and storage of diverse gases like hydrogen and oxygen. The rules also include guidelines for the working hours of adults and children employed at the factories.
To sum up, the Gujarat Factories Rules, 1963 is a comprehensive social legislative document that ensures a better life for the workers in the factories along with reinforcing a general wellbeing.
Related Articles
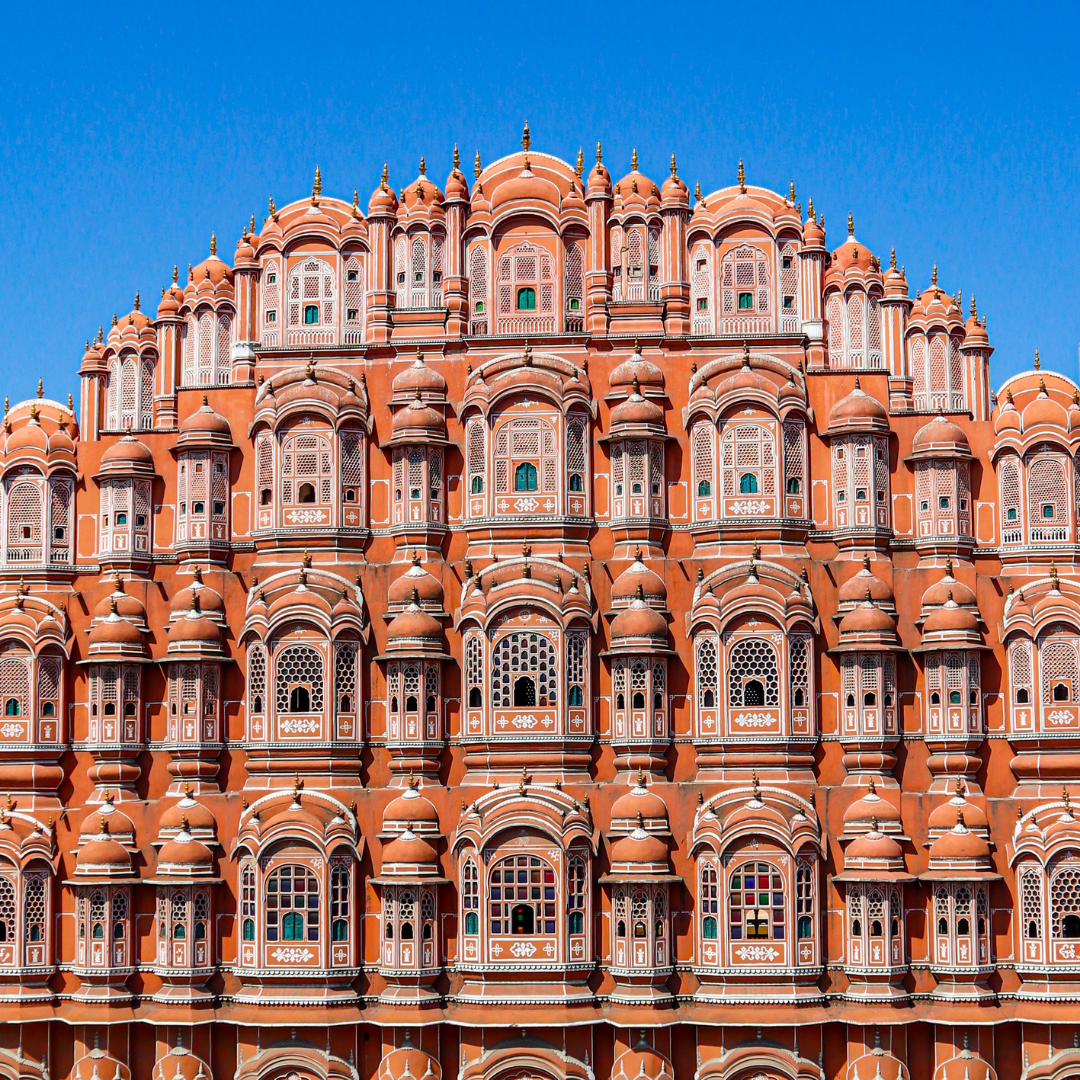
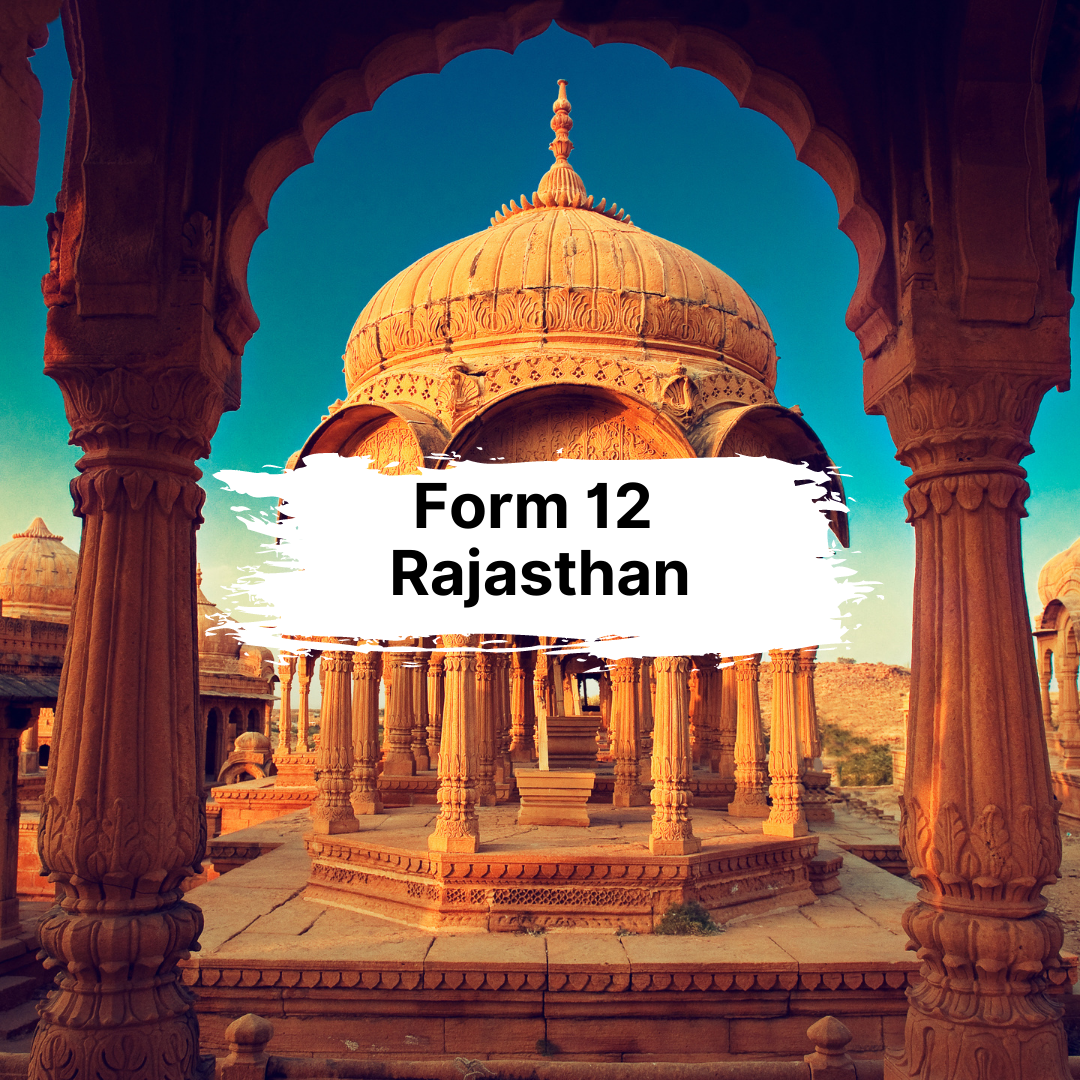
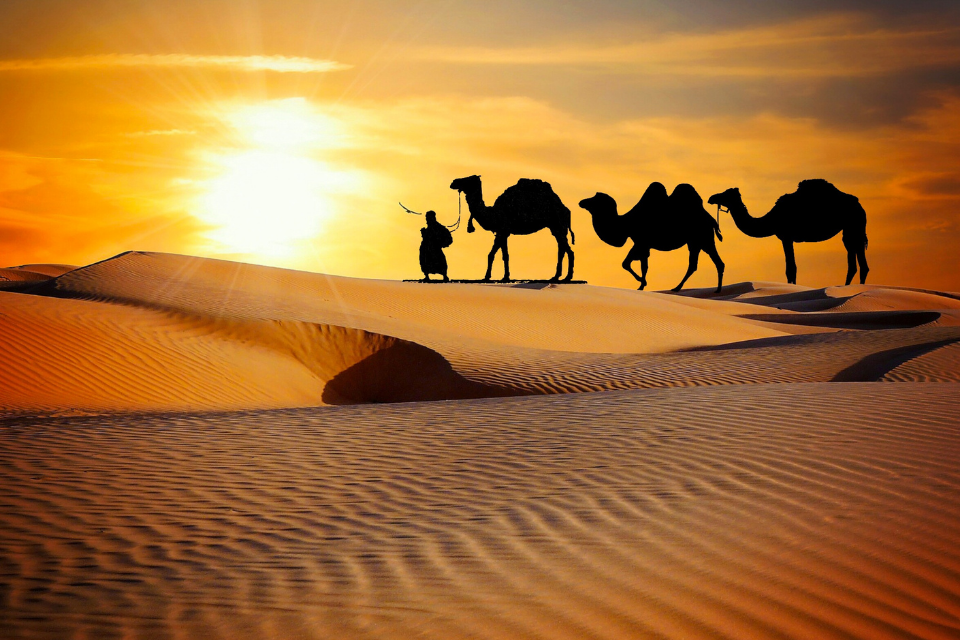
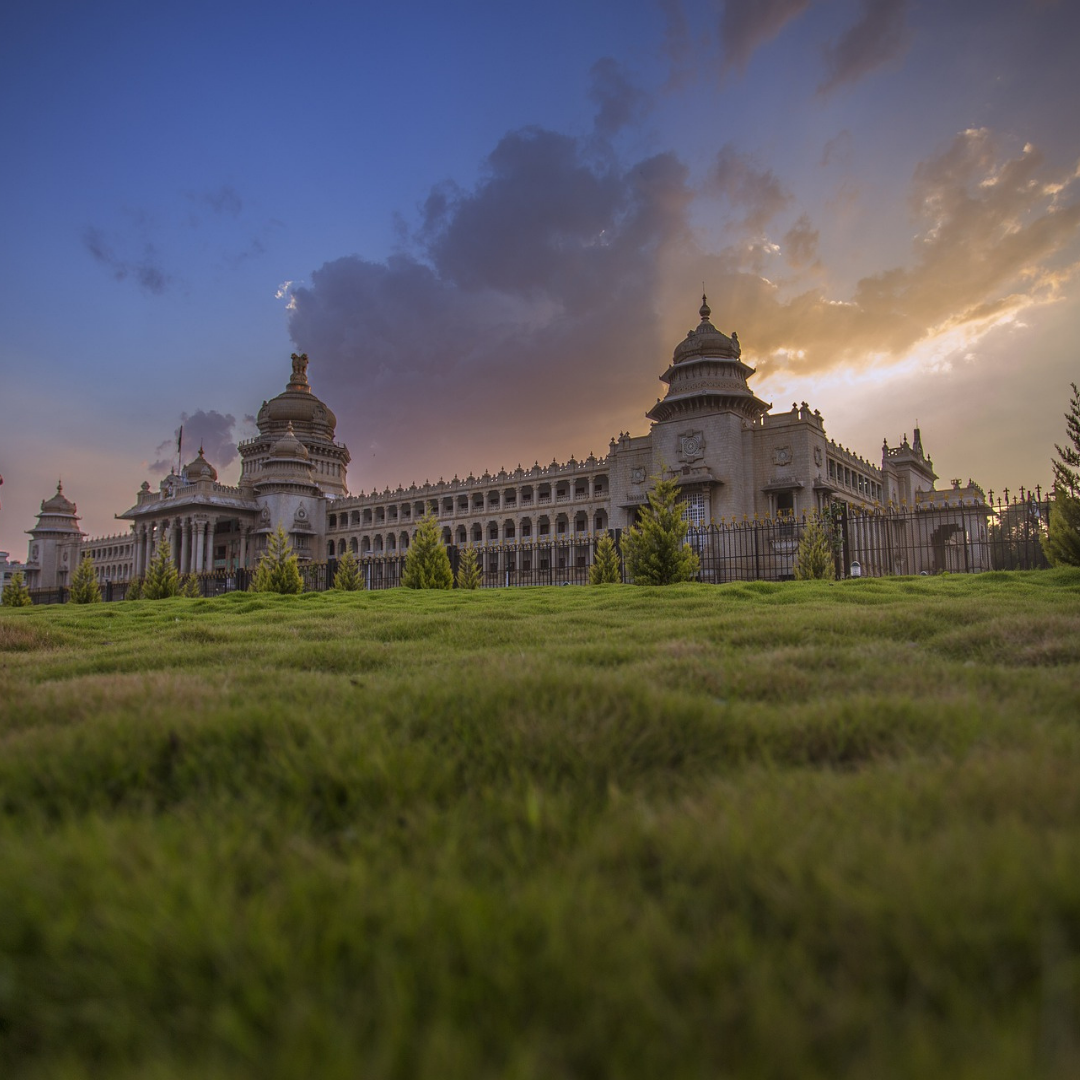
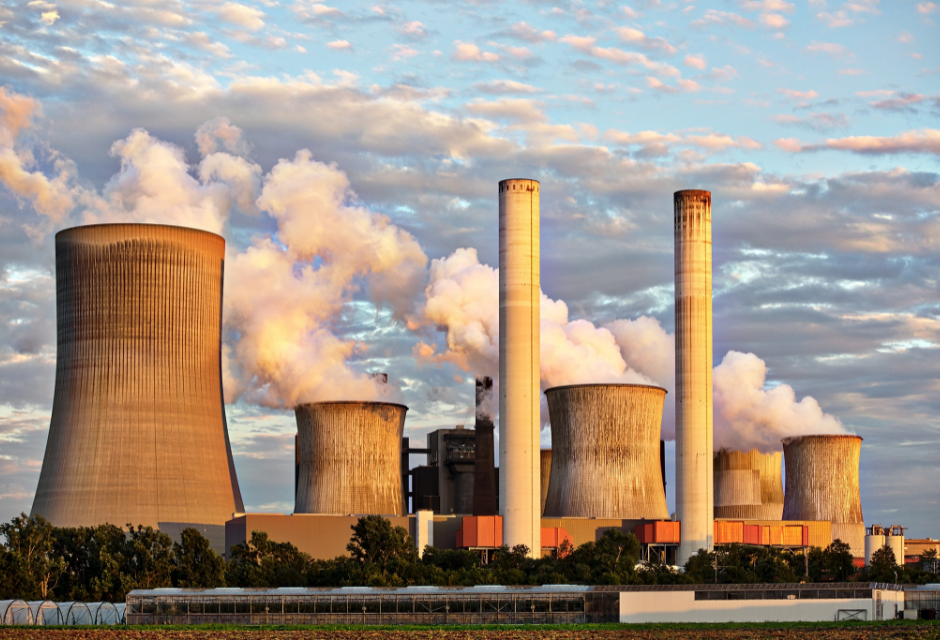