The adoption of Industry 4.0 technologies, such as artificial intelligence (AI) and the Internet of Things (IoT), is increasing rapidly in the US manufacturing industry, with over 50% of companies expected to have implemented these technologies by 2023.
The industry has undergone a rapid transformation in recent years, with new technologies and processes emerging to enhance efficiency, reduce costs, and improve product quality.
This has led to the rise of modern manufacturers embracing automation, digitization, and the interconnectivity of machines, systems, and people, known as Industry 4.0.
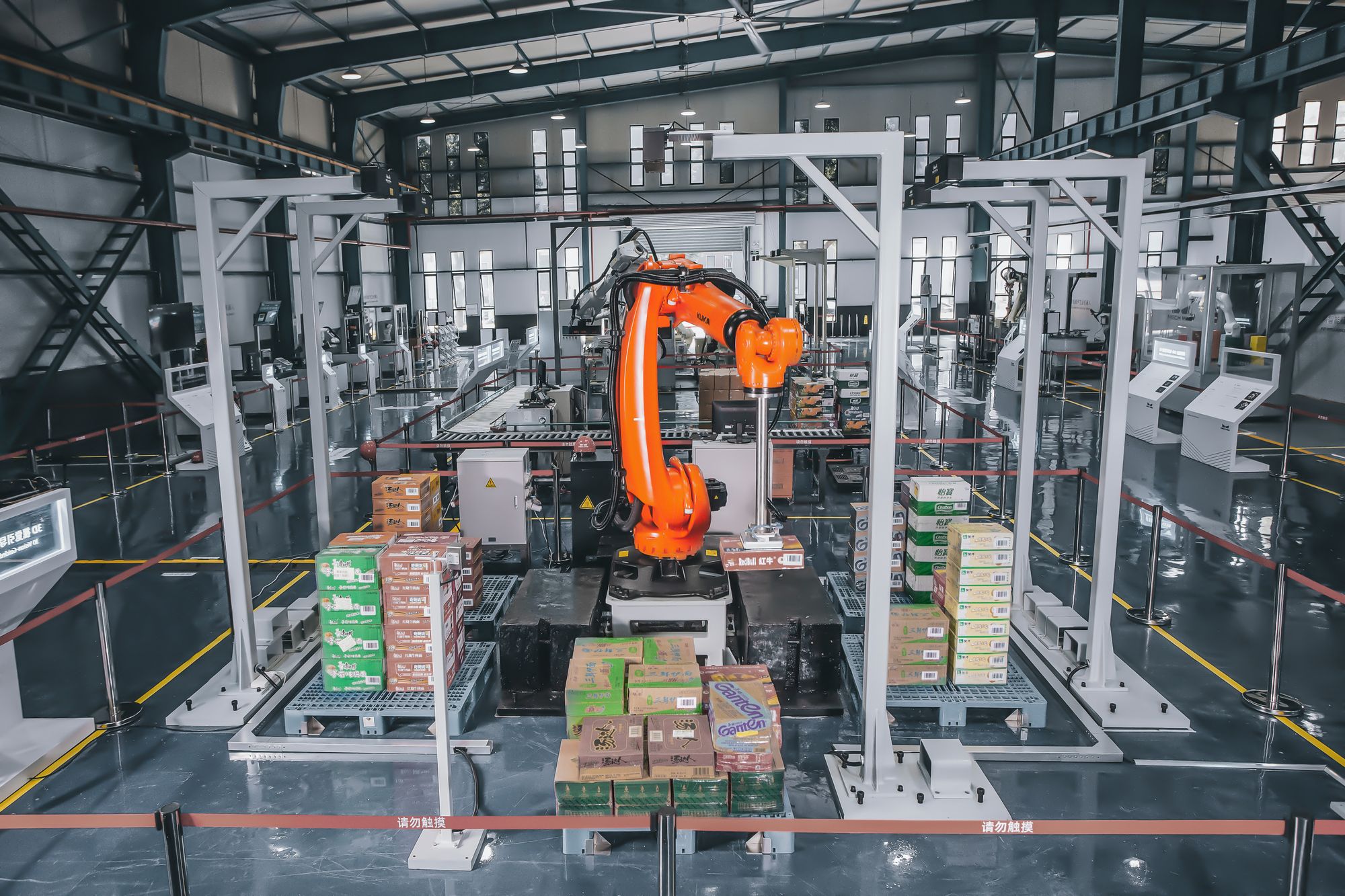
This study aims to examine the current state of modern manufacturers in 2023, exploring the industry's trends and challenges, as well as how technology is transforming the manufacturing landscape.
By providing a comprehensive overview of the current state of modern manufacturing, this study will enable stakeholders to understand the trends and challenges shaping the industry and make informed decisions about the future.
Here's what we shall cover in this post:
- Overview of Modern Manufacturing
- Technological Advancements in Modern Manufacturing
- Impact of Automation and AI on Manufacturing
- Role of Sustainability in Modern Manufacturing
- Role of Data and Analytics in Modern Manufacturing
- The Shift Towards Industry 4.0
- Challenges in Modern Manufacturing
- Future of Modern Manufacturing
- Conclusion
- Key Takeaways
Overview of Modern Manufacturing
Modern manufacturing has undergone significant changes in the past few years and is continuing to evolve rapidly in 2023. The goal of modern manufacturing is to produce high-quality products in an efficient, cost-effective, and sustainable manner.
The demand for modern manufacturing solutions is growing in 2023, driven by the need for high-quality products and the desire for increased efficiency and sustainability.
- The market for modern manufacturing solutions is dominated by a small number of large, established companies, with many smaller companies also entering the market.
- Competition in the market for modern manufacturing solutions is expected to remain intense in 2023 as companies compete to offer the most advanced and cost-effective solutions.
- The market for modern manufacturing solutions is being driven by the adoption of emerging technologies, such as Industry 4.0 technologies and advanced materials and techniques.
- Increased awareness of the benefits of modern manufacturing solutions is also driving demand as companies look to improve their production processes and reduce costs.
- The demand for modern manufacturing solutions is growing in all regions of the world, with the strongest growth in Asia-Pacific and North America.
- Investment in modern manufacturing solutions is expected to remain strong in 2023, with companies investing in new technologies and production processes to stay competitive.
Technological Advancements in Modern Manufacturing
Manufacturing has come a long way since the days of manual labor and traditional production methods. Technological advancements have made modern manufacturing more efficient, cost-effective, and environmentally friendly.
In this section, we'll explore some of the key technological advancements that have transformed the manufacturing industry in recent years.
Automation
Automation has had a significant impact on modern manufacturing. Robots and automated systems have replaced manual labor in many manufacturing processes, resulting in increased efficiency and reduced production costs. Automated systems can work 24/7, reducing downtime and increasing production output. Automation also helps improve product quality, as machines can perform tasks with greater accuracy and consistency than humans.
Benefits of Automation in Manufacturing: Automation offers a range of benefits to manufacturers, including increased efficiency, improved productivity, and reduced labor costs.
Automation can also help manufacturers minimize errors and enhance the quality of products, increasing flexibility and allowing manufacturers to respond quickly to changing market demands.
Types of Automation in Modern Manufacturing: Many different types of automation are used in modern manufacturing, including robotic process automation, industrial robots, and automated inspection systems.
Each of these technologies offers its own unique benefits, and manufacturers can choose the right type of automation for their operations based on their specific needs and requirements.
Adoption of Automation in Manufacturing: The adoption of automation in modern manufacturing has been increasing in recent years, driven by the need to stay ahead of the competition and meet the demands of an ever-changing global market.
From large multinational corporations to small and medium-sized enterprises, manufacturers of all sizes are embracing automation to improve their operations and remain competitive in the industry.
Challenges of Automation in Manufacturing: While automation offers many benefits to manufacturers, it is not without its challenges. One of the biggest challenges is the cost of implementing and maintaining automation systems, which can be significant for some manufacturers.
Additionally, some workers may resist the adoption of automation due to concerns about job loss, which must be addressed through training and education programs.
Integration of Automation and Industry 4.0: The integration of automation and Industry 4.0 is another important trend in modern manufacturing. By using technologies such as the Internet of Things (IoT) and big data analytics, manufacturers can collect and analyze vast amounts of data about their operations in real time.
This data can then be used to drive efficiency, productivity, and sustainability improvements, helping manufacturers stay ahead of the competition.
3D Printing
3D printing, also known as additive manufacturing, has revolutionized the way that products are manufactured. 3D printing allows manufacturers to create complex parts and prototypes quickly and inexpensively without the need for traditional tooling and molding processes. This technology has opened up new possibilities in product design, allowing manufacturers to create customized products with greater ease.
How 3D Printing Works: 3D printing works by building up layers of material, such as plastic or metal, to create a 3D object. This process is often referred to as additive manufacturing, and it is much faster and more efficient than traditional manufacturing methods, such as injection molding or machining.
Benefits of 3D Printing in Manufacturing: 3D printing offers a range of benefits to manufacturers, including faster prototyping, improved product quality, and greater design freedom.
Additionally, 3D printing allows manufacturers to create custom parts and products that are tailored specifically to their customers' needs, giving them a competitive advantage in the marketplace.
Types of 3D Printing: There are several different types of 3D printing technologies available, including Fused Deposition Modeling (FDM), Stereolithography (SLA), and Selective Laser Sintering (SLS).
Each of these technologies offers its own unique benefits and capabilities, and manufacturers can choose the right type of 3D printing for their operations based on their specific needs and requirements.
Adoption of 3D Printing in Manufacturing: The adoption of 3D printing in modern manufacturing has been increasing in recent years, driven by the need to improve efficiency and competitiveness.
From aerospace and automotive to healthcare and consumer goods, manufacturers of all types are using 3D printing to create custom parts and products that meet the demands of their customers.
Challenges of 3D Printing in Manufacturing: While 3D printing offers many benefits to manufacturers, it is not without its challenges. One of the biggest challenges is the cost of 3D printing technology, which can be expensive for some manufacturers.
There are also concerns about the environmental impact of 3D printing and the need for proper training and education for workers who will be using the technology.
Artificial Intelligence
Artificial intelligence (AI) has the potential to revolutionize the manufacturing industry. AI-powered systems can analyze data and make predictions, helping manufacturers to optimize production processes and improve product quality.
AI can also be used to monitor production processes in real time, providing early warnings of potential problems and reducing downtime.
Applications of AI in Manufacturing: AI has a wide range of applications in modern manufacturing, from predictive maintenance and quality control to supply chain management and process optimization.
For example, AI can analyze production data to identify trends and patterns, helping manufacturers make informed decisions and improve their operations.
Benefits of AI in Manufacturing: One of the key benefits of AI in manufacturing is its ability to automate repetitive tasks and improve efficiency. AI can also help manufacturers enhance the quality of the product by detecting defects early in the production process, reducing the need for rework and saving time and resources.
Additionally, AI can provide manufacturers with valuable insights into their operations, allowing them to identify opportunities for improvement and growth.
Adoption of AI in Manufacturing: The adoption of AI in modern manufacturing is increasing as companies look for new ways to stay competitive and improve their operations.
Companies of all sizes, from large multinational corporations to small startups, are investing in AI technologies to gain a competitive edge and drive growth.
Challenges of AI in Manufacturing: While AI offers many benefits to manufacturers, there are also challenges to overcome. One of the biggest challenges is the need for skilled workers who can develop and implement AI technologies.
Additionally, there are concerns about the security and privacy of data, as well as the potential for job loss due to automation.
Internet of Things
The Internet of Things (IoT) refers to the connected network of devices that are able to collect and exchange data. In modern manufacturing, IoT-powered systems can be used to monitor production processes, track inventory, and collect data on product performance.
This information can be used to optimize production processes, improve product quality, and reduce waste.
Applications of IoT in Manufacturing: IoT has many applications in modern manufacturing, from predictive maintenance and energy management to supply chain tracking and quality control.
For example, IoT sensors can be placed on machines to monitor performance and detect potential issues, allowing manufacturers to prevent downtime and improve productivity.
Benefits of IoT in Manufacturing: IoT in manufacturing is the ability to collect and analyze data in real time, helping manufacturers make informed decisions and optimize operations.
IoT also enables manufacturers to automate many processes, reducing manual labor and improving efficiency. IoT can also help manufacturers enhance the quality of products and reduce waste, leading to cost savings and increased competitiveness.
Adoption of IoT in Manufacturing: The adoption of IoT in modern manufacturing is growing rapidly as companies look for new ways to improve their operations and stay competitive. Companies of all sizes are investing in IoT technologies to gain a competitive edge and drive growth.
Challenges of IoT in Manufacturing: While IoT offers many benefits to manufacturers, there are also challenges to overcome. One of the biggest challenges is the need for a secure and reliable network infrastructure to support the growing number of connected devices.
Additionally, there are concerns about the privacy and security of data collected and transmitted through IoT networks.
Big Data Analytics
Big data analytics is the process of analyzing large data sets to extract insights and make informed decisions. In modern manufacturing, big data analytics can be used to analyze production processes, product performance, and customer behavior.
This information can be used to optimize production processes, improve product quality, and increase customer satisfaction.
Impact of Automation and AI on Manufacturing
The manufacturing industry has undergone significant changes in recent years, largely due to the integration of automation and artificial intelligence (AI). These technologies have profoundly impacted the industry, bringing new levels of efficiency, accuracy, and cost-effectiveness to manufacturing processes.
This section will explore the impact of automation and AI in manufacturing.
Increased Efficiency: One of the most significant impacts of automation and AI in manufacturing is increased efficiency. Automated systems can work 24/7, reducing downtime and increasing production output.
AI-powered systems can analyze data and make predictions, helping manufacturers to optimize production processes and improve efficiency. Automation and AI can also help to reduce human error, improve product quality, and reduce waste.
Improved Product Quality: Automated systems can perform tasks with greater accuracy and consistency than humans, which can lead to improved product quality. AI-powered systems can monitor production processes in real time, providing early warnings of potential problems and reducing the risk of defects.
Automation and AI can also help ensure that products are manufactured according to industry standards, improving product reliability and customer satisfaction.
Cost Savings: Automation and AI can help to reduce manufacturing costs in several ways. By reducing downtime and increasing production output, automation can lower production costs.
AI-powered systems can also help optimize production processes, reducing the need for manual labor and the cost of materials. Additionally, automation and AI can help to improve product quality, reducing the cost of defects and returns.
Better Data Management: Automation and AI can help manufacturers to collect and analyze data on production processes, product performance, and customer behavior. This information can be used to optimize production processes, improve product quality, and increase customer satisfaction.
AI-powered systems can also help to monitor production processes in real-time, providing early warnings of potential problems and reducing downtime.
Enhanced Customer Experience: Automation and AI can help manufacturers create customized products more easily, improving the customer experience. AI-powered systems can also analyze customer behavior and preferences, helping manufacturers to create products that better meet customer needs.
Automation and AI can also help to reduce delivery times and improve product reliability, enhancing customer satisfaction.
Increased Job Opportunities: While automation has replaced some manual labor in the manufacturing industry, it has also created new job opportunities. For example, workers are needed to design, build, and maintain automated systems.
AI also requires workers with specialized skills, such as data analysts and software engineers. Additionally, workers are needed to manage and interpret the data generated by automated systems, helping to inform production processes and improve product quality.
Environmental Benefits: Automation and AI can also positively impact the environment. By reducing human error and improving product quality, automation can reduce waste and emissions. AI-powered systems can also help to optimize production processes, reducing energy consumption and carbon emissions.
Additionally, automation and AI can help manufacturers create more environmentally friendly products, reducing the impact of manufacturing on the planet.
Role of Sustainability in Modern Manufacturing
Sustainability has become an increasingly important aspect of modern manufacturing in recent years. The drive to reduce waste, minimize negative impacts on the environment, and promote sustainable practices is changing manufacturers' operations. In this section, we'll explore the role of sustainability in modern manufacturing in more detail.
Reduced Waste
Sustainability in modern manufacturing is focused mainly on reducing waste. Manufacturers are looking for ways to minimize waste in production processes and use resources more efficiently.
This includes reducing material waste, minimizing energy consumption, and optimizing production processes to reduce downtime.
Improved Resource Efficiency
Sustainability in modern manufacturing also involves improving resource efficiency. This includes finding ways to reduce the use of raw materials and minimize energy consumption.
For example, manufacturers may use renewable energy sources or adopt lean manufacturing practices to reduce waste and improve resource efficiency.
Environmental Protection
Sustainability in modern manufacturing also involves protecting the environment. This includes reducing greenhouse gas emissions, minimizing the use of hazardous chemicals, and improving waste management practices.
Manufacturers are also looking for ways to reduce the impact of production processes on the environment, such as using sustainable materials and adopting environmentally-friendly production methods.
Enhanced Reputation
Implementing sustainable practices in modern manufacturing can also enhance a company's reputation. Consumers are increasingly concerned about the environmental impact of the products they buy and are more likely to choose products from companies that are committed to sustainability.
This can lead to increased brand loyalty and improved customer satisfaction.
Improved Product Quality
Sustainability in modern manufacturing can also lead to improved product quality. For example, using sustainable materials can result in more durable and long-lasting products. Adopting environmentally-friendly production methods can also improve product quality by reducing the risk of defects and improving production processes.
Competitive Advantage
Implementing sustainable practices in modern manufacturing can also provide a competitive advantage. Companies committed to sustainability are more likely to attract customers concerned about the environmental impact of the products they buy.
Additionally, companies that adopt sustainable practices are better positioned to meet consumers' changing needs and government regulations.
Role of Data and Analytics in Modern Manufacturing
Introduction to Data and Analytics in Manufacturing Data and Analytics has become increasingly important in modern manufacturing as technology has evolved and data has become more accessible.
With the rise of the Internet of Things (IoT) and Industry 4.0, manufacturers have access to vast amounts of data about their operations and can use analytics to turn this data into actionable insights.
Improved Decision-Making
One of the key benefits of using data and analytics in manufacturing is the ability to make more informed decisions. With access to real-time data, manufacturers can make decisions that are based on accurate and up-to-date information.
This helps them identify trends and patterns in their operations and make improvements to increase efficiency and reduce costs.
Predictive Maintenance
Data and analytics can also be used to predict when maintenance is required on machines and equipment. By analyzing data from sensors, manufacturers can identify when a machine is starting to show signs of wear and tear, allowing them to schedule maintenance before a breakdown occurs.
This can save time and money by reducing downtime and avoiding the cost of repairing a broken machine.
Quality Control
Data and analytics can also be used to improve quality control in manufacturing. By analyzing data from quality control systems, manufacturers can identify trends and patterns in quality issues and make changes to improve the process.
This can help to reduce defects, enhance the quality of products and increase customer satisfaction.
Inventory Management
Data and analytics can also be used to improve inventory management in manufacturing. By analyzing data about inventory levels and usage patterns, manufacturers can identify areas where they can optimize their inventory to reduce costs and improve efficiency.
This can help to reduce waste, minimize inventory carrying costs, and improve overall supply chain management.
Resource Optimization
Data and analytics can also be used to optimize the use of resources in manufacturing. By analyzing resource usage and availability data, manufacturers can identify areas where they can reduce waste and improve efficiency.
This can help to reduce costs, improve the use of energy and other resources, and minimize the environmental impact of manufacturing operations.
The Shift Towards Industry 4.0
Introduction to Industry 4.0 Industry 4.0 refers to the fourth industrial revolution, which is characterized by integrating advanced technologies such as the Internet of Things (IoT), artificial intelligence (AI), and cloud computing into manufacturing processes. This shift is transforming how manufacturers operate, allowing them to be more flexible, efficient, and responsive to changing customer demands.
Increased Automation
One of the key drivers of Industry 4.0 is the increased automation of manufacturing processes. With robots, smart machines, and other automated systems, manufacturers can streamline their operations and reduce the need for manual labor. This leads to improved efficiency, reduced costs, and increased productivity.
Data-Driven Decision
Making Another important aspect of Industry 4.0 is the use of data and analytics to drive decision-making. By collecting and analyzing vast amounts of data, manufacturers can gain insights into their operations and identify areas where they can improve.
This leads to better-informed decision-making, increased efficiency, and improved customer satisfaction.
Real-Time Data Analysis: Data-driven decision-making enables real-time data analysis, which helps make informed decisions on time. The data collected from various sources, such as machines, sensors, and customer feedback, can be analyzed in real-time, providing valuable insights into the manufacturing process.
This allows for quick and effective corrective actions to be taken, improving the overall efficiency of the manufacturing process.
Customer Feedback: Data-driven decision-making helps in collecting and analyzing customer feedback. This helps understand customer preferences and needs, allowing for personalized and targeted marketing efforts.
Customer feedback also helps improve the quality of manufactured products, providing valuable insights into the customer's needs and expectations.
Smart Factories
Smart factories are a key component of Industry 4.0. These factories use advanced technologies such as IoT and AI to create a connected and automated manufacturing environment. This allows for real-time monitoring of production processes, reduced downtime, and improved quality control.
Customization and Personalization
Industry 4.0 is also leading to increased customization and personalization in manufacturing. With advanced technologies, manufacturers can quickly and easily change production processes to meet the specific needs of individual customers. This leads to improved customer satisfaction and increased competitiveness in the market.
Understanding Customer Needs: Smart factories use data collected from various sources, such as customer feedback, market research, and social media, to understand the needs and preferences of customers.
This information is then used to create customized products that meet individual customers' specific needs and preferences. This helps improve customer satisfaction, as customers receive products specifically designed for them.
Mass Customization: The integration of advanced technologies such as IoT and AI allows for the creation of flexible manufacturing systems, enabling mass customization. This means that large quantities of customized products can be produced while still meeting individual customers' specific needs and preferences.
This helps reduce costs and increase efficiency, as the manufacturing process can be optimized to meet individual customers' specific needs and preferences.
Personalized Marketing: Smart factories use the data collected from various sources to create targeted marketing campaigns tailored to individual customer needs and preferences. Personalized marketing helps improve customer satisfaction, as customers receive products and marketing efforts specifically designed for them.
Increased Customer Satisfaction: Smart factories allow for the production of customized products that meet individual customers' specific needs and preferences. In addition, personalized marketing efforts also help in improving customer satisfaction.
Increased customer satisfaction leads to increased customer loyalty and higher customer retention rates, which are essential for long-term success in the manufacturing industry.
Supply Chain Optimization
The shift towards Industry 4.0 is also leading to improved supply chain management. By connecting the supply chain's various elements through IoT and other technologies, manufacturers can optimize their operations and reduce waste. This leads to improved efficiency, reduced costs, and increased sustainability.
Reskilling and Upskilling
The shift towards Industry 4.0 also leads to the need for reskilling and upskilling of the workforce. As automation and other advanced technologies become more prevalent, workers will need to acquire new skills to remain competitive in the job market. This presents both challenges and opportunities for workers and employers alike.
Need for New Skills: Integrating advanced technologies in manufacturing processes requires new skills and knowledge. Workers need to be trained in new technologies such as IoT, AI, big data analytics, and data analysis and decision-making.
This requires investment in upskilling and reskilling programs to ensure that the workforce has the necessary skills to operate and maintain the new technologies.
Job Displacement: The integration of advanced technologies in manufacturing processes may lead to job displacement, as some tasks become automated. This requires the reskilling of workers to help them transition to new roles in demand in the industry.
Investment in reskilling programs is essential to ensure that workers are equipped with the necessary skills to transition to new roles and remain competitive in the job market.
Improved Productivity and Efficiency: Investment in upskilling and reskilling programs helps improve workers' productivity and efficiency. Workers trained in new technologies and processes are better equipped to perform their jobs, improving productivity and efficiency.
This helps improve companies' competitiveness, as they can produce high-quality products at lower costs.
Attraction and Retention of Talent: Investment in upskilling and reskilling programs helps attract and retain industry talent. Workers equipped with the latest skills and knowledge are more likely to remain with their current employer, as they can perform their jobs effectively and have better job security.
This helps reduce turnover and improve workforce stability, which is essential for long-term success in the industry.
Future-Proofing the Workforce: Investment in upskilling and reskilling programs helps in future-proofing the workforce, ensuring that workers are equipped with the necessary skills to remain competitive in the job market.
This helps reduce the risk of job displacement and helps ensure that the workforce can keep up with the changing technological landscape in the industry.
Challenges in Modern Manufacturing
Modern manufacturing faces several challenges as the industry evolves and becomes increasingly complex. These challenges range from improved efficiency and productivity to the increasing importance of sustainability and the need for a skilled workforce.
The Skills Gap
One of the biggest challenges facing modern manufacturers is the skills gap. As technology advances and automation becomes more prevalent, workers will need to acquire new skills to remain competitive in the job market.
This challenges manufacturers who need to invest in reskilling and upskilling their workforce.
Sustainability
Another major challenge facing modern manufacturers is the need to become more sustainable. With increasing pressure from consumers, governments, and environmental organizations, manufacturers must find ways to reduce their environmental impact and improve their sustainability practices.
This requires investment in new technologies and changes to business processes.
Energy Efficiency: One of the major challenges facing manufacturers is energy efficiency. The need for energy has increased with the integration of advanced technologies such as the Internet of Things (IoT), artificial intelligence (AI), and big data analytics.
However, manufacturers must also reduce energy consumption to meet sustainability goals and reduce costs. This requires investment in energy-efficient technologies and processes, as well as in renewable energy sources.
Waste Reduction: Another major challenge facing manufacturers is waste reduction. With the integration of advanced technologies, manufacturers can produce more products with less waste. However, they also need to reduce the waste generated by their operations to meet sustainability goals.
This requires investment in recycling and waste management technologies and process improvement initiatives that reduce waste.
Carbon Emissions Reduction: Reducing carbon emissions is a major challenge for manufacturers, as they strive to meet sustainability goals and reduce their environmental impact. This requires investment in renewable energy sources, energy-efficient technologies, and process improvements that reduce emissions.
It also requires collaboration between manufacturers, suppliers, and customers to reduce emissions throughout the supply chain.
Market Differentiation: Investing in sustainability can provide a competitive advantage for manufacturers as consumers become more environmentally conscious and demand more sustainable products.
Manufacturers who demonstrate their commitment to sustainability and their efforts to reduce their environmental impact can differentiate themselves in the market and increase their appeal to consumers.
Competition and Market Demands
Manufacturers are also facing increased competition and changing market demands. With the rise of new technologies, consumers are becoming increasingly demanding and manufacturers must be able to quickly adapt to meet these changing needs.
This requires investment in research and development, innovation, and the ability to quickly bring new products to market.
Meeting Market Demands: One of the major challenges facing manufacturers is the need to quickly and efficiently meet changing market demands. Consumers are becoming increasingly demanding and expect high-quality products at affordable prices.
Manufacturers must be able to respond quickly to changes in consumer preferences and market trends while also maintaining quality and efficiency.
Global Competition: Another major challenge facing manufacturers is global competition. With the rise of globalization, manufacturers are facing increased competition from companies around the world.
They must be able to compete on price, quality, and delivery time to remain profitable and relevant in the global marketplace.
Keeping Up with Technological Advances: Manufacturers must keep up with technological advances to remain competitive.
The integration of advanced technologies such as the Internet of Things (IoT), artificial intelligence (AI), and big data analytics is changing the manufacturing landscape, and manufacturers must be able to adapt quickly to stay ahead of the curve.
Data Management and Analytics
Data management and analytics are becoming increasingly important in modern manufacturing. With the rise of the Internet of Things (IoT) and Industry 4.0, manufacturers have access to vast amounts of data about their operations.
However, this data must be properly managed and analyzed to provide valuable insights and drive improvements.
Data Analytics: One of the manufacturers' biggest challenges is the need for effective data analytics. Manufacturers must be able to turn their data into actionable insights to improve operations and make better decisions.
This requires investment in data analytics tools and training for employees, as well as the development of data-driven processes and workflows.
Data Security: Data security is a growing concern for manufacturers as cyber threats and data breaches become more common. Manufacturers must ensure that their data is protected from unauthorized access and that sensitive information is confidential. This requires investment in robust data security measures and processes.
Supply Chain Management
Modern manufacturers must also find ways to optimize their supply chains. This requires coordination and collaboration across the entire supply chain, including suppliers, logistics providers, and customers.
The increasing complexity of supply chains presents a major challenge, as manufacturers must find ways to balance the need for efficiency and cost savings with the need for flexibility and resilience.
Cybersecurity
Cybersecurity is a growing concern in modern manufacturing, as advanced technologies such as IoT and AI make the industry increasingly vulnerable to cyber-attacks.
Manufacturers must find ways to protect their operations and ensure the security of their data and systems while maintaining their competitiveness in a fast-changing market.
Future of Modern Manufacturing
The future of modern manufacturing is bright, with new technologies, innovative business models, and a focus on sustainability driving the industry forward. Manufacturers willing to embrace change and innovation will find many opportunities to improve their competitiveness and succeed in the global market.
Additive Manufacturing
Additive manufacturing, also known as 3D printing, is another technology poised to have a major impact on the future of modern manufacturing.
This technology allows manufacturers to produce complex parts and components quickly and cost-effectively, reducing the need for traditional manufacturing methods and opening up new possibilities for product design and development.
- Flexibility and Speed: One of the biggest advantages of additive manufacturing is its flexibility and speed. With 3D printing, manufacturers can quickly and easily produce complex parts and prototypes without needing tooling or molds.
This allows manufacturers to quickly respond to changes in customer demand and produce unique and custom products.
- Improved Product Design: Additive manufacturing also offers the opportunity to improve product design. With 3D printing, manufacturers can create complex and innovative designs that would be impossible to produce with traditional manufacturing methods.
This leads to the creation of new and improved products and increased competitiveness in the marketplace.
- New Business Models: Additive manufacturing enables new business models and opportunities. With the ability to produce parts on demand, manufacturers can reduce inventory costs and increase their responsiveness to customer demand.
Additionally, manufacturers can use 3D printing to create new products and services, expanding their business offerings and increasing revenue.
Advanced Robotics
The rise of advanced robotics is another key trend in the future of modern manufacturing. Robotics will play an important role in increasing efficiency, improving productivity, and reducing the need for manual labor.
The use of robots will also help manufacturers meet the demands of consumers who are increasingly focused on sustainability and environmental responsibility.
Advanced robotics can also improve safety in the manufacturing process. With the ability to perform tasks that are too dangerous for human workers, manufacturers can reduce the risk of accidents and injuries. Additionally, robots can work 24/7, increasing overall productivity and reducing downtime.
Digital Transformation
The digital transformation of modern manufacturing is another key trend that will shape the industry's future. From digital twin technology to virtual and augmented reality, digital solutions transform how manufacturers operate and interact with their customers.
As technology advances, digital solutions will become even more critical to success in the modern manufacturing landscape.
Circular Economy
The circular economy is another important trend that will shape the future of modern manufacturing. This new business model focuses on reducing waste and increasing sustainability, allowing manufacturers to reduce their environmental impact while improving their competitiveness.
From closed-loop supply chains to product-as-a-service offerings, the circular economy offers many opportunities for manufacturers looking to stay ahead in the industry.
- Benefits: Adopting a circular economy approach in manufacturing can have numerous benefits, such as reducing waste, conserving natural resources, lowering carbon emissions, and creating more sustainable economic growth. This can also lead to increased competitiveness, reduced costs, and improved brand reputation.
- Key Principles: The principles of the circular economy include designing out waste and pollution, keeping products and materials in use, and regenerating natural systems. These principles can be applied to the entire lifecycle of a product, from design to production, use, and end-of-life disposal.
- Industry Examples: The circular economy is already being implemented in various industries, such as fashion, electronics, and packaging. For example, in the fashion industry, companies use sustainable materials, design products that can be reused, recycled, or repurposed, and implement closed-loop systems to minimize waste.
On-demand Manufacturing
On-demand manufacturing is another trend that is transforming modern manufacturing. With the rise of e-commerce and the increasing importance of customization, on-demand manufacturing allows manufacturers to quickly and efficiently produce products to meet the changing demands of their customers.
As this trend continues to grow, it will become an increasingly important part of the future of modern manufacturing.
The Sharing Economy
The sharing economy is another trend that is shaping the future of modern manufacturing. This business model allows manufacturers to share resources and equipment, reducing costs and increasing efficiency.
As the sharing economy continues to grow, manufacturers can collaborate with other companies and increase their competitiveness in the global market.
- Key Components: The sharing economy uses technology to facilitate sharing and collaboration between individuals and companies. This includes platforms and apps that allow users to easily find and access goods and services and data analysis and algorithms that help match supply and demand.
- Industry Examples: The sharing economy is already being adopted in various industries, such as transportation, tourism, and consumer goods. For example, car-sharing services like Zipcar and car-pooling services like UberPOOL allow individuals to share vehicles and reduce the number of cars on the road.
- Consumer Behavior: Consumers play a crucial role in the growth and success of the sharing economy. By choosing to access goods and services rather than owning them, consumers can help drive change in the manufacturing industry and encourage companies to adopt sharing economy principles.
How Deskera Can Assist You?
Deskera MRP allows you to closely monitor the manufacturing process. From the bill of materials to the production planning features, the solution helps you stay on top of your game and keep your company's competitive edge.
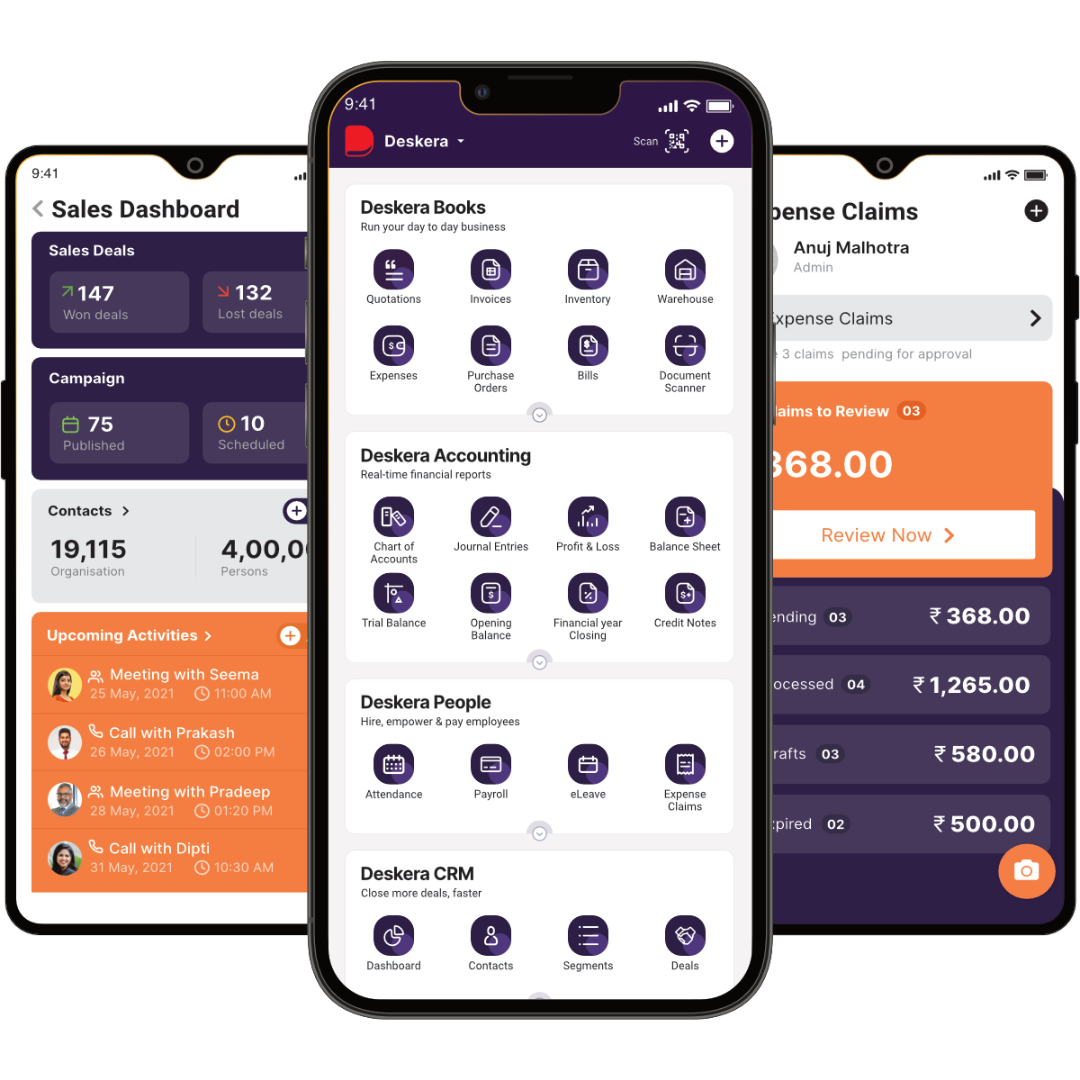
Deskera ERP and MRP system can help you:
- Manage production plans
- Maintain Bill of Materials
- Generate detailed reports
- Create a custom dashboard
Deskera ERP is a comprehensive system that allows you to maintain inventory, manage suppliers, and track supply chain activity in real-time, as well as streamline a variety of other corporate operations.
Deskera Books enables you to manage your accounts and finances more effectively. Maintain sound accounting practices by automating accounting operations such as billing, invoicing, and payment processing.
Deskera CRM is a strong solution that manages your sales and assists you in closing agreements quickly. It not only allows you to do critical duties such as lead generation via email, but it also provides you with a comprehensive view of your sales funnel.
Deskera People is a simple tool for taking control of your human resource management functions. The technology not only speeds up payroll processing but also allows you to manage all other activities such as overtime, benefits, bonuses, training programs, and much more. This is your chance to grow your business, increase earnings, and improve the efficiency of the entire production process.
Conclusion
The study of modern manufacturers in 2023 highlights the growing trend toward automation and digitization in the manufacturing industry. The industry is undergoing a rapid transformation, with new technologies and processes emerging to enhance efficiency, reduce costs, and improve product quality.
This has resulted in an increased focus on data-driven decision-making, innovative production methods, and the development of smart factories. Additionally, the rise of Industry 4.0, with its emphasis on the interconnectivity of machines, systems, and people, has significantly impacted the industry.
Moreover, the study reveals that modern manufacturers face several challenges, including shortages of skilled labor, increasing competition, and the need for greater sustainability.
However, despite these challenges, the industry remains optimistic about its future, with many companies investing in research and development to stay ahead of the curve.
As the manufacturing industry continues to evolve, it is evident that the role of technology will become increasingly important. Companies must stay up-to-date with the latest technological advancements to remain competitive and meet the changing needs of consumers.
Key Takeaways
- Automation and digitization are the dominant trends in the manufacturing industry in 2023, leading to an increased focus on data-driven decision-making and innovative production methods.
- The rise of Industry 4.0, emphasizing interconnectivity between machines, systems, and people, has had a major impact on the manufacturing industry and its processes.
- The shortage of skilled labor, increasing competition, and the need for greater sustainability are some challenges modern manufacturers face.
- Despite these challenges, the industry remains optimistic about its future, and many companies are investing in research and development to stay ahead of the curve.
- The role of technology is becoming increasingly important in the manufacturing industry, and companies must stay up-to-date with the latest advancements to remain competitive.
- Data analysis and the use of artificial intelligence (AI) and the Internet of Things (IoT) are increasingly critical in optimizing production processes and enhancing product quality.
Related Articles
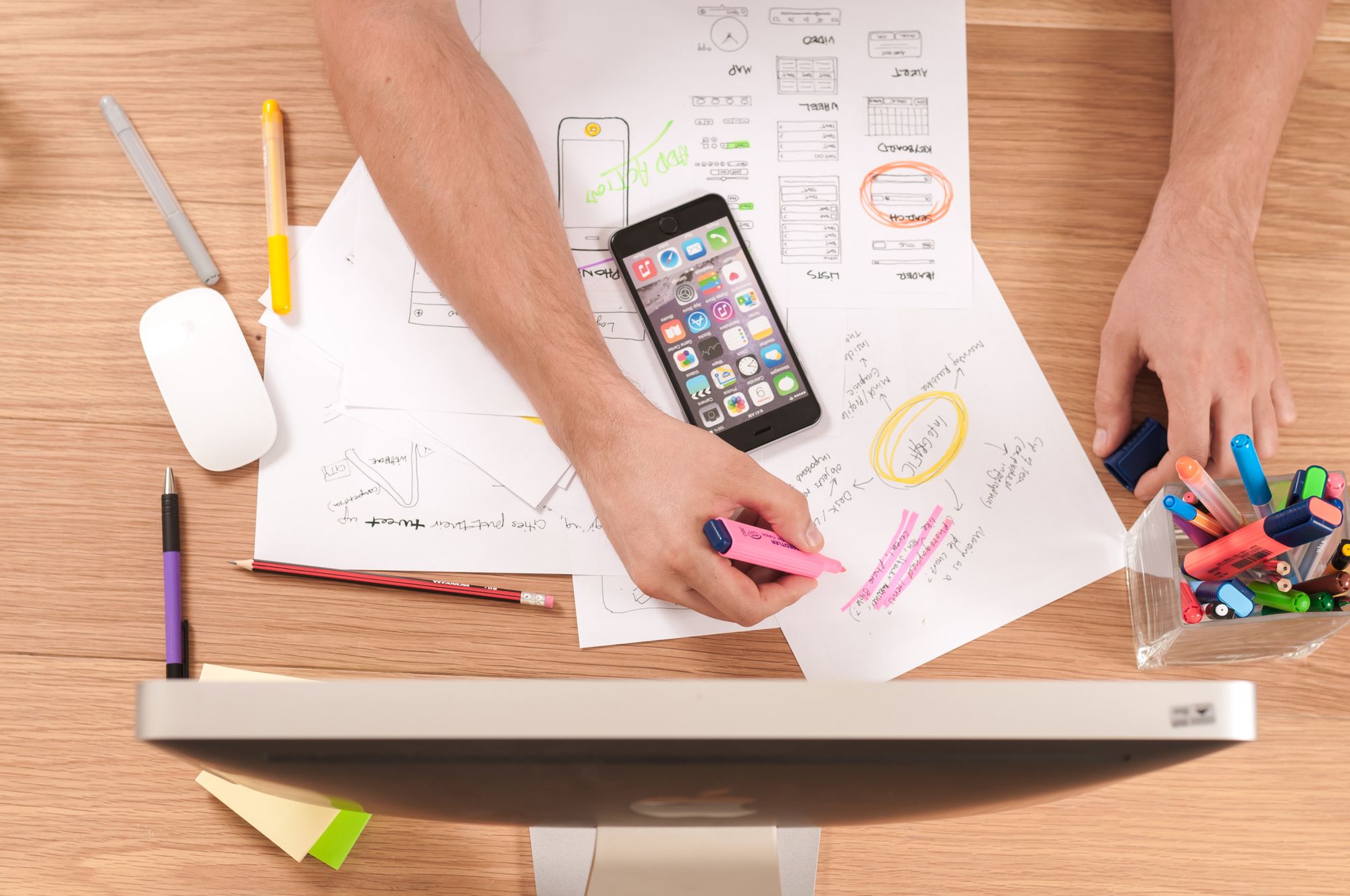
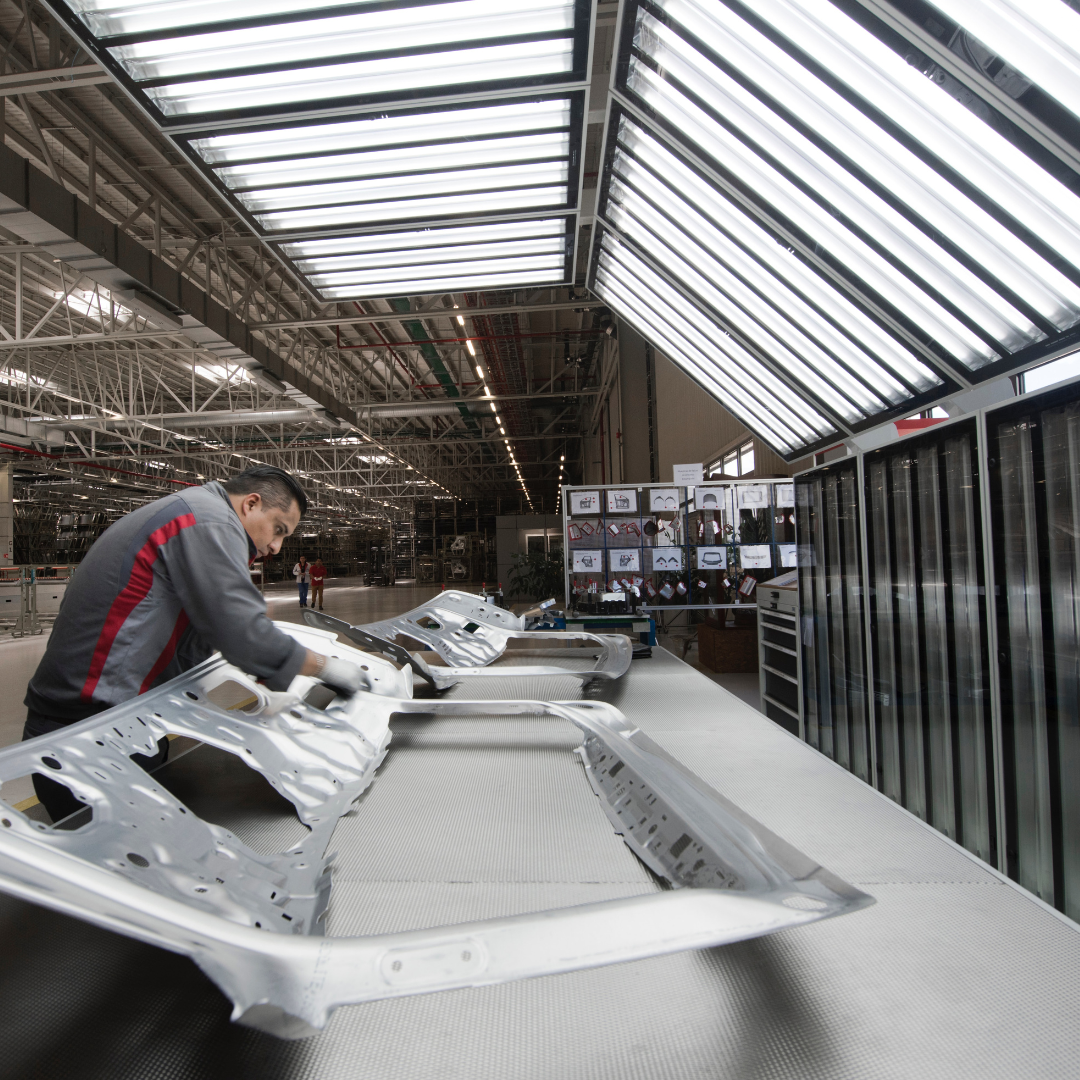
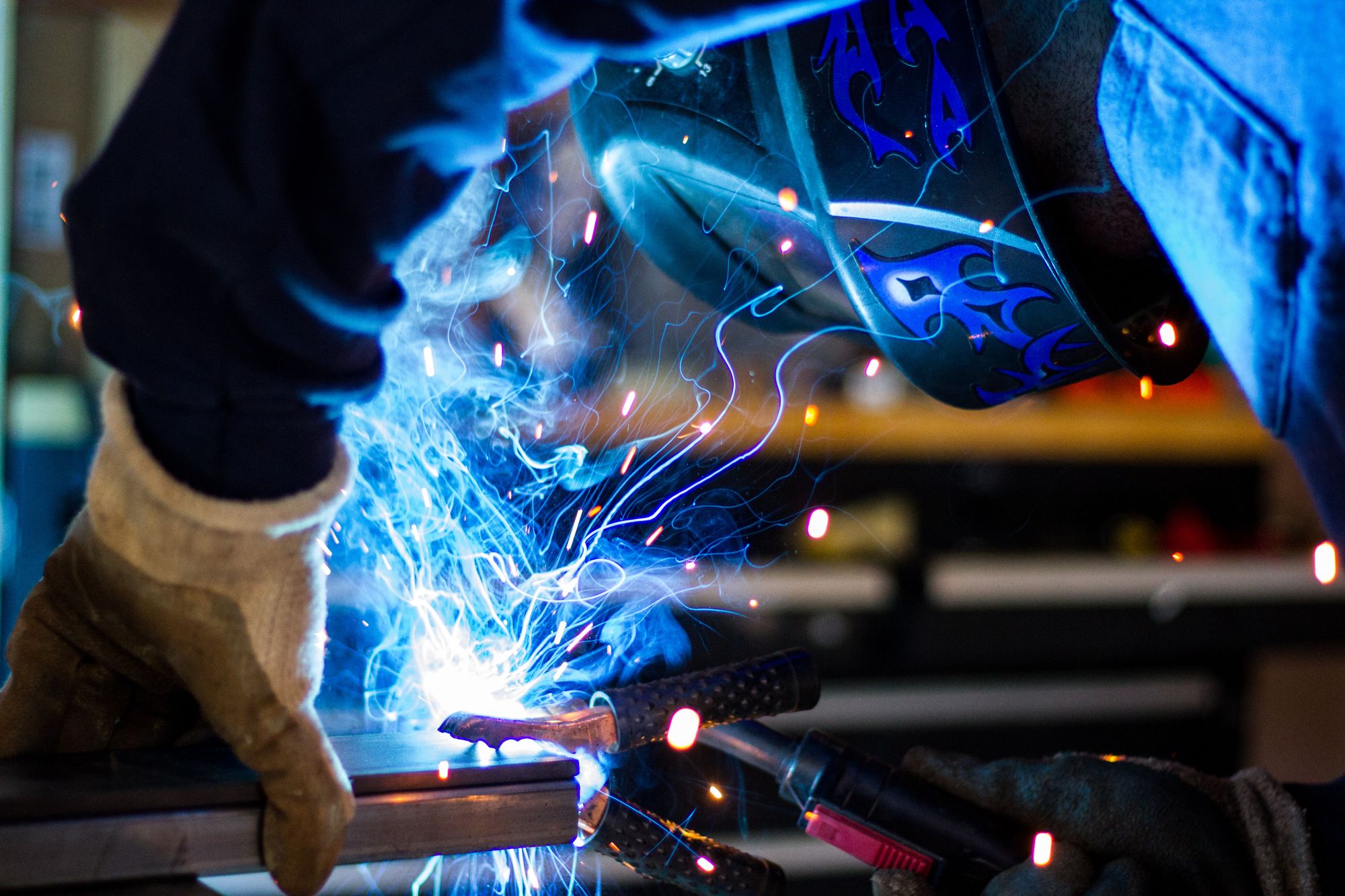
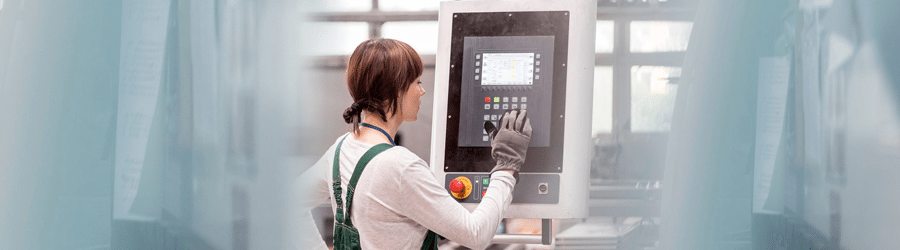