In 2020, the global paper quality control systems market size was valued at USD 268.5 million and was expected to grow at a CAGR of 6.2% from 2021 to 2028. (Source: Grand View Research)
According to a report by MarketsandMarkets, the paper and pulp industry's quality control market size is expected to reach USD 22.5 billion by 2025, growing at a CAGR of 4.5% during the forecast period. (Source: MarketsandMarkets)
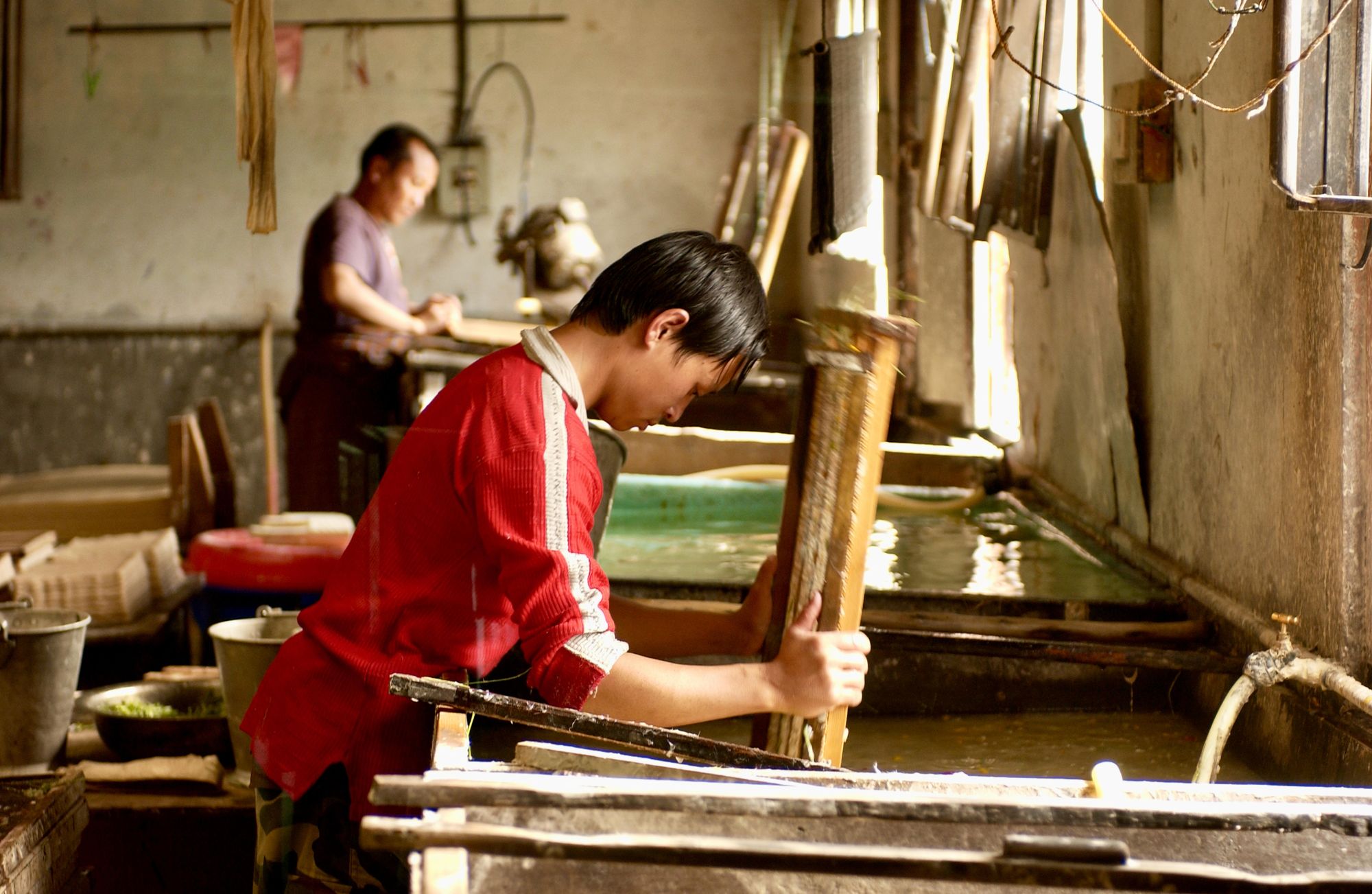
A study by TAPPI (Technical Association of the Pulp and Paper Industry) found that the most common causes of paper defects were related to machine operation and process control, accounting for over 60% of all defects. (Source: TAPPI Journal)
In 2021, a survey of paper mills by Quality Control Systems (QCS) found that 65% of respondents reported using automated inspection systems for paper quality control. (Source: Quality Control Systems)
Quality control in paper manufacturing is the process of monitoring and regulating the quality of paper throughout the manufacturing process. It involves inspecting raw materials, monitoring production processes, testing products as they are produced, and inspecting finished products before they are shipped to customers.
Quality control is important in paper manufacturing as it helps ensure that the paper produced meets the customer’s requirements, is safe to use, and meets all applicable industry standards. This will help in improving customer retention and customer loyalty, which would lead to higher net revenue and net profit ratio.
However, considering the importance of paper manufacturing quality control, it is important to have a complete understanding of the same.
This article will help you thereby covering the following topics:
- What is Quality Control in Paper Manufacturing?
- Importance of Quality Control in Paper Manufacturing
- Steps Involved in Quality Control Planning of Paper Manufacturing
- How to Implement Quality Control in Paper Manufacturing?
- How to Ensure Quality Control in Paper Manufacturing?
- Best Practices for Paper Manufacturing Quality Control
- How to Improve Quality Control in Paper Manufacturing?
- Which Quality Control Tools can be used for Quality Control of Paper Manufacturing?
- How can Technology Help in Implementing Quality Control in Paper Manufacturing?
- How can Deskera Help with Quality Control of Paper Manufacturing?
- Key Takeaways
- Related Articles
What is Quality Control in Paper Manufacturing?
Quality control in paper manufacturing is a process that involves monitoring and testing various stages of the production process to ensure that the paper produced meets specific quality standards.
It involves a range of techniques and procedures to identify and correct any defects that may impact the quality of the final product. Here are some of the key aspects of quality control in paper manufacturing:
- Raw materials testing: Quality control begins with testing the raw materials, including wood pulp, recycled paper, and other additives, to ensure that they meet the required specifications.
- Process control: During the manufacturing process, various parameters such as temperature, pressure, and humidity are monitored and controlled to ensure consistent quality.
- In-process testing: Samples are taken at various stages of the manufacturing process to test for factors such as color, weight, strength, and thickness.
- Final testing: Once the paper is produced, it undergoes final testing to ensure that it meets the required quality standards. This includes testing for factors such as tear strength, stiffness, and moisture content.
- Continuous improvement: Quality control is an ongoing process, and manufacturers are constantly looking for ways to improve the quality of their products. This involves analyzing data from testing results and making adjustments to the production process to improve quality.
Overall, quality control in paper manufacturing is critical to ensuring that the paper produced meets customer expectations, regulatory requirements, and industry standards. It helps to improve efficiency, reduce waste, and build a reputation, and therefore a positive brand awareness for quality and reliability.
Importance of Quality Control in Paper Manufacturing
Quality control is essential in paper manufacturing to ensure that the final product meets customer expectations and regulatory requirements. Here are some reasons why quality control is crucial in paper manufacturing:
- Consistency: Quality control ensures that the paper produced is consistent in terms of color, texture, weight, and strength. This consistency is crucial for customer satisfaction and helps to build a reputation for the brand.
- Compliance: Quality control ensures that the paper meets regulatory requirements, such as safety and environmental regulations. Failure to comply with these regulations can lead to fines, additional expenses, and damage to the company's reputation.
- Waste reduction: Quality control helps to identify defects early on in the manufacturing process, reducing the amount of waste produced. This reduces manufacturing costs and operating costs and helps to improve efficiency.
- Cost savings: Quality control helps to identify issues that can lead to customer complaints, returns, and rework. By identifying and addressing these issues early, companies can save money and improve profitability.
- Reputation: Quality control helps to ensure that the paper produced is of high quality, which can help to build a reputation for the brand. This can lead to increased customer loyalty, sales velocity, and market share.
Overall, quality control is essential in paper manufacturing to ensure that the final product meets customer expectations, regulatory requirements, and industry standards.
Steps Involved in Quality Control Planning of Paper Manufacturing
The following are the key steps involved in quality control planning for paper manufacturing:
- Define quality standards: The first step in quality control planning is to define the quality standards that the paper needs to meet. This involves identifying specific parameters such as weight, thickness, brightness, color, and strength.
- Determine quality control methods: Based on the quality standards defined in step one, the next step is to determine the quality control methods that will be used to monitor and control the production process. This may involve using various equipment such as sensors, gauges, and cameras to monitor factors such as temperature, pressure, and humidity.
- Develop quality control procedures: The next step is to develop detailed procedures for each quality control method identified in step two. These procedures should outline the specific steps that will be taken to perform each quality control method and how the results will be recorded.
- Identify quality control checkpoints: Quality control checkpoints should be established at various stages of the production process. These checkpoints should be based on the quality control methods identified in step two and the procedures developed in step three.
- Train personnel: It is important to ensure that all personnel involved in the production process are trained in the quality control procedures and methods identified in steps two and three.
- Establish testing requirements: Testing requirements should be established to ensure that the paper produced meets the defined quality standards. This may include testing raw materials, in-process testing, and final product testing.
- Analyze data: Data collected during the testing process should be analyzed to identify any trends or patterns that may indicate areas for improvement in the production process.
- Continuously improve the quality control plan: The quality control plan should be continuously evaluated and improved based on the data collected and analyzed in step seven. This may involve making adjustments to quality control procedures, equipment, or testing requirements.
Overall, developing a quality control plan for paper manufacturing involves defining quality standards, determining quality control methods, developing detailed procedures, identifying checkpoints, training personnel, establishing testing requirements, analyzing data, and continuously improving the plan.
By following these steps, paper manufacturers can ensure that their paper meets the required quality standards and customer expectations.
How to Implement Quality Control in Paper Manufacturing?
Implementing quality control in paper manufacturing requires a systematic and structured approach. Here are the key steps to implementing quality control in paper manufacturing:
- Define quality standards: The first step in implementing quality control is to define the quality standards for the paper produced. This involves identifying the specific parameters that the paper must meet, such as color, weight, strength, and thickness.
- Develop a quality control plan: Once the quality standards have been defined, the next step is to develop a quality control plan. This plan should outline the specific procedures and techniques that will be used to monitor and control the production process to ensure that the paper produced meets the required quality standards.
- Train personnel: Quality control requires the involvement of all personnel involved in the production process. Therefore, it is essential to provide training to all personnel to ensure that they understand the quality standards and procedures outlined in the quality control plan.
- Install quality control equipment: To monitor the production process, quality control equipment such as sensors, gauges, and cameras may need to be installed. These devices can measure factors such as temperature, pressure, and humidity to ensure that the process is operating within the required parameters.
- Implement testing procedures: To ensure that the paper produced meets the required quality standards, testing procedures should be implemented at various stages of the production process. This includes testing raw materials, in-process testing, and final testing.
- Analyze data: To identify areas for improvement, data from the testing procedures should be collected and analyzed. This will help to identify trends and patterns that can be used to make adjustments to the production process.
- Continuous improvement: Quality control is an ongoing process, and it is essential to continually evaluate and improve the quality control plan to ensure that it remains effective and relevant.
Overall, implementing quality control in paper manufacturing requires a systematic and structured approach that involves defining quality standards, developing a quality control plan, training personnel, installing quality control equipment, implementing testing procedures, analyzing data, and continuously improving the process.
How to Ensure Quality Control in Paper Manufacturing?
Ensuring quality control in paper manufacturing requires a comprehensive approach that involves the implementation of various processes and techniques to ensure that the paper produced meets the required quality standards. Here are some ways to ensure quality control in paper manufacturing:
- Raw material selection: Ensure that the raw materials used in the production of paper are of high quality and meet the required specifications. This can be achieved by performing quality checks on incoming raw materials.
- Process control: Implement a process control system that monitors and controls various parameters such as temperature, pressure, and humidity during the manufacturing process to ensure consistent quality.
- Quality testing: Perform regular quality testing at various stages of the manufacturing process to identify any defects that may impact the quality of the final product.
- Calibration of equipment: Ensure that all equipment used in the manufacturing process is calibrated and maintained to ensure accurate measurement and operation.
- Training and education: Provide regular training and education to employees to ensure that they understand the quality standards and procedures outlined in the quality control plan.
- Document control: Implement a document control system to ensure that all procedures, work instructions, and quality records are up-to-date and easily accessible.
- Continuous improvement: Continuously evaluate and improve the quality control plan to ensure that it remains effective and relevant.
Overall, ensuring quality control in paper manufacturing requires a proactive and systematic approach that involves the implementation of various processes and techniques to monitor and control the production process. This helps to ensure that the paper produced meets the required quality standards and customer expectations.
Best Practices for Paper Manufacturing Quality Control
Here are some best practices for quality control of paper manufacturing:
Define and Communicate Quality Standards
Defining and communicating quality standards is an important aspect of quality control in paper manufacturing. Quality standards are a set of criteria or requirements that the final product must meet in order to be considered acceptable. These standards should be established based on customer requirements, industry standards, and regulatory requirements.
To define quality standards, the first step is to identify the specific requirements that the paper must meet. This may include physical properties such as weight, thickness, strength, and moisture content, as well as chemical properties such as pH, brightness, and color.
Other requirements may include environmental or sustainability criteria, such as the use of recycled materials or compliance with specific regulations.
Once the quality standards have been defined, it is important to communicate these standards to all personnel involved in the production process. This may include operators, supervisors, quality control personnel, and management. Communication can be done through training sessions, written procedures, or visual aids such as posters or job aids.
The communication of quality standards should be clear and concise and should include specific instructions on how to measure and monitor the quality of the paper. This may include the use of specific instruments or equipment or the performance of certain tests or measurements.
Regular communication and reinforcement of quality standards is important to ensure that all personnel understand the importance of quality control in paper manufacturing and are committed to maintaining the quality of the final product.
By defining and communicating quality standards, paper manufacturers can ensure that their products meet customer requirements, regulatory requirements, and industry standards and maintain a competitive advantage in the market.
Implement a Quality Management System
Implementing a quality management system (QMS) is an important step in ensuring consistent quality control in paper manufacturing.
A QMS is a set of policies, procedures, and processes for managing and controlling quality throughout the production process. Here are some steps to implement a QMS in paper manufacturing:
- Define the scope and objectives of the QMS: The first step is to define the scope and objectives of the QMS. This includes identifying the processes and activities that will be covered by the QMS, as well as the goals and objectives that the QMS is intended to achieve.
- Establish a quality policy and quality manual: The quality policy is a statement of the company's commitment to quality and should be communicated to all personnel involved in the production process. The quality manual is a document that outlines the policies and procedures that will be followed to ensure quality throughout the production process.
- Identify and document procedures: Identify the key procedures that are necessary to control quality in paper manufacturing and document these procedures in the quality manual. This may include procedures for product design and development, raw material selection and testing, production and process control, and product testing and inspection.
- Establish a document control system: Establish a document control system to ensure that all quality-related documents are controlled, current, and readily available to personnel who need them. This may include procedures for document creation, review, approval, distribution, and revision.
- Implement an internal audit program: Implement an internal audit program to ensure that the QMS is being followed and is effective in identifying and correcting quality issues. This may include conducting regular audits of the production process and the QMS and documenting any non-conformities or corrective actions.
- Establish a corrective and preventive action (CAPA) program: Establish a CAPA program to address any quality issues that are identified through internal audits or other quality control processes. This may include documenting and investigating quality issues, implementing corrective actions, and monitoring the effectiveness of these actions.
- Establish a management review process: Establish a process for management review of the QMS to ensure that it remains effective and relevant. This may include reviewing quality metrics, analyzing trends and patterns, and making changes to the QMS as necessary to improve quality control.
By implementing a QMS, paper manufacturers can ensure that quality control is consistent and effective throughout the production process. This can help improve customer satisfaction, reduce waste and defects, and maintain a competitive advantage in the market.
Conduct Regular Audits
Regular audits are an essential part of quality control in paper manufacturing. Audits help to ensure that the production process is operating effectively and efficiently and that quality standards are being met.
Here are some steps for conducting regular audits for quality control of paper manufacturing:
- Define audit scope: The first step in conducting an audit is to define the scope of the audit. This includes identifying the processes and activities that will be audited, as well as the criteria or standards that will be used to evaluate these processes.
- Develop an audit checklist: Develop an audit checklist that outlines the specific criteria or standards that will be evaluated during the audit. The checklist should be based on the quality standards that have been defined for the production process, as well as any relevant industry standards or regulations.
- Select an audit team: Select an audit team that includes personnel with relevant knowledge and expertise. This may include quality control personnel, production supervisors, and other personnel who are familiar with the production process.
- Schedule the audit: Schedule the audit at a time that is convenient for all personnel involved. The audit should be conducted during a normal production cycle and should not disrupt the production process.
- Conduct the audit: Conduct the audit according to the defined scope and checklist. This may involve observing the production process, reviewing documents and records, and interviewing personnel.
- Document findings: Document any findings or observations that are made during the audit. This may include non-conformities or areas where the production process is not meeting quality standards.
- Develop corrective actions: Develop corrective actions to address any non-conformities or areas where the production process is not meeting quality standards. These corrective actions should be documented and tracked to ensure that they are implemented effectively.
- Follow-up: Follow up on corrective actions to ensure that they have been implemented effectively and are addressing the identified non-conformities or issues.
By conducting regular audits, paper manufacturers can identify areas where the production process can be improved, ensure that quality standards are being met, and continuously improve the quality control process.
Use Statistical Process Control (SPC)
Statistical process control (SPC) is a tool that can be used for quality control in paper manufacturing. SPC is a method of monitoring and controlling a production process through the use of statistical analysis.
By using SPC, manufacturers can identify patterns and trends in the production process and take corrective action before quality issues arise. Here are some steps for using SPC for quality control of paper manufacturing:
- Define process variables: The first step is to identify the key process variables that affect the quality of the paper product. These variables may include raw materials, production equipment, and environmental factors such as temperature and humidity.
- Collect data: Collect data on the process variables using a sampling plan. The sampling plan should be designed to capture enough data to be statistically significant while still being practical for the production process.
- Create control charts: Create control charts that show the variation in the process variables over time. Control charts typically include upper and lower control limits, which represent the acceptable range of variation for the process variable.
- Analyze control charts: Analyze the control charts to identify patterns and trends in the process variables. This may include looking for data points that fall outside of the control limits or identifying patterns of variation that may indicate a problem with the production process.
- Take corrective action: If a problem is identified through the analysis of the control charts, take corrective action to address the issue. This may involve adjusting the production process, changing the raw materials used, or taking other steps to bring the process back into control.
- Monitor results: Monitor the results of the corrective action to ensure that it is effective in addressing the identified problem. This may involve continuing to collect data and monitor control charts or conducting additional testing to verify that the quality of the paper product has improved.
By using SPC, paper manufacturers can proactively monitor and control the production process, identify potential quality issues before they arise, and take corrective action to ensure consistent quality in the paper product.
Train Personnel
Training personnel is an important aspect of quality control in paper manufacturing. Well-trained personnel are better equipped to identify quality issues, implement quality control procedures, and continuously improve the production process.
Here are some steps for training personnel for quality control of paper manufacturing:
- Define training needs: The first step is to define the training needs of personnel involved in quality control. This may include training on specific quality control procedures, equipment operation, safety procedures, or other topics related to the production process.
- Develop training materials: Develop training materials that are tailored to the specific needs of the personnel being trained. Training materials may include written manuals, videos, presentations, or other materials that can effectively communicate the required information.
- Deliver training: Deliver training to personnel using a variety of methods, such as classroom instruction, hands-on training, and online courses. The training should be conducted by knowledgeable trainers who have experience in the production process and quality control procedures.
- Assess knowledge and skills: Assess the knowledge and skills of personnel following the training to ensure that they have understood and retained the information presented. This may involve testing, evaluations, or other methods of assessment.
- Provide ongoing training: Provide ongoing training to personnel to ensure that they are up-to-date with the latest quality control procedures and best practices. This may involve regular refresher courses, new-hire training, or additional training as needed.
- Encourage continuous learning: Encourage personnel to engage in continuous learning and professional development. This may involve providing access to industry conferences, workshops, and other training opportunities.
By training personnel effectively, paper manufacturers can ensure that they have a knowledgeable and skilled workforce that is able to implement quality control procedures, identify quality issues, and continuously improve the production process.
Use Quality Control Tools
There are several quality control tools that can be used for the quality control of paper manufacturing. These tools are designed to help identify quality issues, monitor production processes, and improve the overall quality of the paper product.
Here are some of the most commonly used quality control tools for paper manufacturing:
- Pareto analysis: Pareto analysis is a tool that can help identify the most significant quality issues in the production process. This tool involves analyzing data to determine the frequency and impact of different types of quality issues and then prioritizing them based on their significance.
- Control charts: Control charts are a tool that can help monitor the variation in a production process over time. Control charts plot data points on a graph and then identify upper and lower control limits that indicate the acceptable range of variation for the process variable.
- Root cause analysis: Root cause analysis is a tool that can help identify the underlying causes of quality issues. This tool involves analyzing data and conducting investigations to determine the root cause of a quality issue, and then implementing corrective actions to address the underlying cause.
- Six Sigma: Six Sigma is a methodology that can help improve the quality of the production process by reducing variation and minimizing defects. This methodology involves a structured approach to problem-solving, data analysis, and process improvement.
- Statistical process control: Statistical process control is a tool that can help monitor the variation in a production process over time and identify patterns and trends that may indicate a problem with the process. This tool involves using statistical analysis to monitor and control the production process.
By using quality control tools such as these, paper manufacturers can identify quality issues, monitor production processes, and continuously improve the quality of their paper products. These tools can help to ensure that the paper product meets the required quality standards and that production processes are optimized for maximum efficiency and quality.
Monitor and Measure Performance
Monitoring and measuring performance is an important aspect of quality control in paper manufacturing. By monitoring and measuring key performance indicators (KPIs), paper manufacturers can identify quality issues, track progress toward quality goals, and continuously improve the production process. Here are some steps for monitoring and measuring performance for quality control in paper manufacturing:
- Define KPIs: The first step is to define the KPIs that will be used to monitor and measure performance. These may include quality metrics such as defect rate, customer complaints, or product specifications, as well as operational metrics such as production efficiency or equipment uptime.
- Collect data: Collect data on the identified KPIs using a variety of methods such as manual data collection, automated sensors, or machine learning algorithms. The data should be accurate, timely, and reliable to ensure that it can be used to make informed decisions.
- Analyze data: Analyze the data collected to identify patterns, trends, and areas for improvement. This may involve using statistical analysis, data visualization, or other analytical tools to gain insights into the production process.
- Set targets: Set targets for each of the identified KPIs based on industry standards, customer requirements, or other relevant benchmarks. These targets should be realistic, achievable, and aligned with the overall quality objectives of the company.
- Monitor performance: Monitor performance against the identified KPIs on a regular basis to track progress and identify areas for improvement. This may involve using dashboards, reports, or other visualization tools to provide real-time insights into the production process.
- Take corrective actions: Take corrective actions to address any quality issues or performance gaps identified through the monitoring and measuring process. This may involve implementing process improvements, retraining personnel, or adjusting equipment settings to optimize the production process.
By monitoring and measuring performance in this way, paper manufacturers can ensure that their production processes are optimized for quality and efficiency and that their products meet the required quality standards.
Continuous Improvement
Continuous improvement is a key aspect of quality control in paper manufacturing. By continuously improving the production process, paper manufacturers can identify and address quality issues, reduce waste and costs, and improve overall efficiency and productivity.
Here are some steps for implementing a continuous improvement program for quality control in paper manufacturing:
- Define the scope: Define the scope of the continuous improvement program, including the specific processes, systems, and functions that will be targeted for improvement.
- Establish a cross-functional team: Establish a cross-functional team of employees from different departments and levels of the organization to participate in the continuous improvement program. This team should be empowered to identify and implement improvements to the production process.
- Identify opportunities for improvement: Identify opportunities for improvement by analyzing data, conducting audits, and gathering feedback from customers and employees. These opportunities may include reducing defects, increasing efficiency, improving safety, or reducing waste.
- Develop improvement plans: Develop improvement plans for each opportunity identified. These plans should include specific objectives, timelines, and metrics for measuring success.
- Implement improvements: Implement the improvement plans using a structured approach such as Plan-Do-Check-Act (PDCA) or Six Sigma. This may involve testing and validating improvements on a small scale before rolling them out across the production process.
- Monitor and measure results: Monitor and measure the results of the improvements using the KPIs established earlier. Analyze the data to determine whether the improvements are meeting the objectives and whether further adjustments are necessary.
- Sustain the improvements: Sustain the improvements by establishing standard operating procedures, providing training and education to employees, and continuously monitoring and measuring performance to identify opportunities for further improvement.
By implementing a continuous improvement program for quality control in paper manufacturing, paper manufacturers can improve the overall quality of their products, reduce costs, and increase efficiency and productivity.
Continuous improvement can also help to create a culture of quality within the organization, with employees at all levels committed to identifying and addressing quality issues.
How to Improve Quality Control in Paper Manufacturing?
Improving quality control in paper manufacturing is an ongoing process that requires continuous evaluation and improvement of the quality control plan. Here are some ways to improve quality control in paper manufacturing:
- Implement statistical process control (SPC): SPC is a technique that uses statistical methods to monitor and control the production process. By analyzing data collected during production, SPC can identify areas of the process that are not performing as expected, allowing for timely corrective actions.
- Use automation: Automation can help to improve quality control by reducing the potential for human error and ensuring that production parameters are consistent.
- Implement a lean manufacturing system: Lean manufacturing focuses on reducing waste and improving efficiency in the manufacturing process. By implementing a lean system, quality control can be improved by identifying and eliminating non-value-added activities.
- Continuous training and education: Ensure that employees are regularly trained and educated on quality control procedures and techniques to improve their understanding and ability to identify quality issues.
- Implement root cause analysis (RCA): RCA is a problem-solving technique used to identify the underlying causes of quality issues. By using RCA, the root cause of a problem can be identified and eliminated, improving quality control.
- Regularly review and update quality control procedures: Quality control procedures should be reviewed regularly to ensure that they remain effective and relevant. Updates can be made based on changes in technology, customer requirements, or industry standards.
- Implement a quality management system (QMS): A QMS is a formalized system that focuses on continuous improvement of the manufacturing process. Implementing a QMS can help to improve quality control by ensuring that all quality-related activities are standardized and consistent.
Overall, improving quality control in paper manufacturing requires a proactive and continuous effort to evaluate and improve the quality control plan. By implementing these techniques, quality control can be improved, leading to better quality paper and increased customer satisfaction.
Which Quality Control Tools can be used for Quality Control of Paper Manufacturing?
There are several quality control tools that can be used in paper manufacturing to ensure that the final product meets the required quality standards. Here are some of the most common quality control tools used in paper manufacturing:
- Statistical process control (SPC): SPC is a statistical tool used to monitor and control the production process. By analyzing data collected during production, SPC can identify areas of the process that are not performing as expected, allowing for timely corrective actions.
- Control charts: Control charts are a graphical representation of the data collected during production. By plotting data on a chart, trends, and patterns can be easily identified, allowing for timely corrective actions.
- Pareto charts: Pareto charts are used to identify the most common causes of quality issues. By analyzing data on the frequency of quality issues, Pareto charts can identify the root cause of the problem, allowing for corrective actions to be taken.
- Fishbone diagrams: Fishbone diagrams are used to identify the root cause of a problem by breaking down the problem into its various causes and sub-causes. By identifying the root cause of the problem, corrective actions can be taken to prevent the problem from occurring in the future.
- 5S methodology: The 5S methodology is a lean manufacturing tool that focuses on improving workplace organization and efficiency. By implementing the 5S methodology, the production process can be streamlined, reducing the potential for quality issues.
- Failure mode and effects analysis (FMEA): FMEA is a tool used to identify potential failure modes in the production process and their potential effects. By identifying potential failures and their effects, steps can be taken to prevent these failures from occurring.
Overall, these quality control tools can be used to monitor and control the production process in paper manufacturing, identify potential quality issues, and take corrective actions to ensure that the final product meets the required quality standards.
How can Technology Help in Implementing Quality Control in Paper Manufacturing?
Technology can play a crucial role in implementing quality control in paper manufacturing. Here are some ways that technology can be used to improve quality control:
- Automated Quality Inspection: With advancements in technology, paper manufacturers can use automated quality inspection systems to identify defects and inconsistencies in the paper. These systems use cameras, sensors, and software to analyze the paper and detect any quality issues. This can help to reduce the reliance on manual inspections, which can be time-consuming and prone to errors.
- Data Analytics: Data analytics can be used to analyze large volumes of data generated during the production process to identify trends and patterns that may be indicative of quality issues. By analyzing this data, paper manufacturers can make data-driven decisions to improve the production process and address any quality issues.
- Real-Time Monitoring: Real-time monitoring systems can be used to monitor the production process in real time and identify any quality issues as they occur. This can help to reduce the amount of time it takes to identify and address quality issues, resulting in higher-quality products.
- Digital Quality Management System: A digital quality management system can be used to streamline quality control processes by automating tasks such as quality inspections, data collection, and analysis. This can help to reduce the amount of time and effort required to implement quality control measures.
- Virtual Reality Training: Virtual reality training can be used to train employees on quality control procedures and simulate different scenarios. This can help to improve employee skills and reduce the likelihood of quality issues occurring.
- Internet of Things (IoT): The Internet of Things (IoT) can be used to connect different pieces of equipment and sensors used in the production process. This can provide real-time data on the production process, which can be analyzed to identify any quality issues and improve overall efficiency.
Overall, technology can help to improve quality control in paper manufacturing by providing real-time data, automating tasks, and reducing the likelihood of errors. By embracing technology, paper manufacturers can improve the quality of their products, reduce costs, and increase efficiency.
How can Deskera Help with Quality Control of Paper Manufacturing?
Deskera is a cloud-based business management software that can help paper manufacturers to implement quality control measures. Here are some ways that Deskera can help in quality control of paper manufacturing:
- Quality Management System (QMS): Deskera MRP can be used to manage quality control processes and ensure compliance with industry standards. This module allows paper manufacturers to create quality control plans, perform inspections, track non-conformances, and generate reports. This can help to streamline quality control processes and improve the overall quality of the paper products.
- Supplier Management: Deskera MRP can be used to manage supplier relationships and ensure that suppliers meet quality standards. This module allows paper manufacturers to track supplier performance, conduct audits, and manage supplier documents. This can help to reduce the risk of quality issues caused by suppliers.
- Production Planning: Deskera MRP can be used to plan and schedule production processes. This module allows paper manufacturers to create production plans, track materials, and inventory, and monitor production progress. This can help to ensure that production processes are efficient and produce high-quality paper products.
- Inventory Management: Deskera MRP can be used to manage inventory levels and track materials used in the production process. This module allows paper manufacturers to track inventory levels, manage stock levels, and monitor inventory usage. This can help to reduce the risk of quality issues caused by inventory shortages or stockouts.
- Reporting and Analytics: Deskera MRP can be used to generate reports on quality control processes and production performance. This allows paper manufacturers to analyze data on quality control processes, identify trends, and make data-driven decisions to improve quality and efficiency.
Key Takeaways
Quality control of paper manufacturing is a process of ensuring that the paper products produced by a paper mill meet the quality standards specified by the customer. It involves monitoring and verifying the quality of raw materials, process parameters, and finished products throughout the paper production process.
Quality control also includes testing for physical, chemical, and mechanical properties of paper, such as brightness, tensile strength, and water absorption. This is done using specialized testing equipment.
Quality control also includes inspecting the paper for defects such as blemishes, tears, and spots. Quality control ensures that products meet the customer's requirements and are free of defects.
The importance of quality control in paper manufacturing is:
- Consistency
- Compliance
- Waste reduction
- Cost savings
- Reputation
The best practices for paper manufacturing quality control are:
- Define and communicate quality standards
- Implement a quality management system
- Conduct regular audits
- Use statistical process control (SPC)
- Train personnel
- Use quality control tools
- Monitor and measure performance
- Continuous improvement
Some of the quality control tools that can be used for quality control of paper manufacturing are:
- Statistical process control (SPC)
- Control charts
- Pareto charts
- Fishbone diagrams
- 5S methodology
- Failure mode and effects analysis (FMEA)
Some of the ways in which technology can help in implementing quality control in paper manufacturing are:
- Automated quality inspection
- Data analytics
- Real-time monitoring
- Digital quality management system
- Virtual reality training
- Internet of Things
Overall, Deskera MRP can help paper manufacturers to implement quality control measures, streamline production processes, and improve the overall quality of paper products.
Related Articles
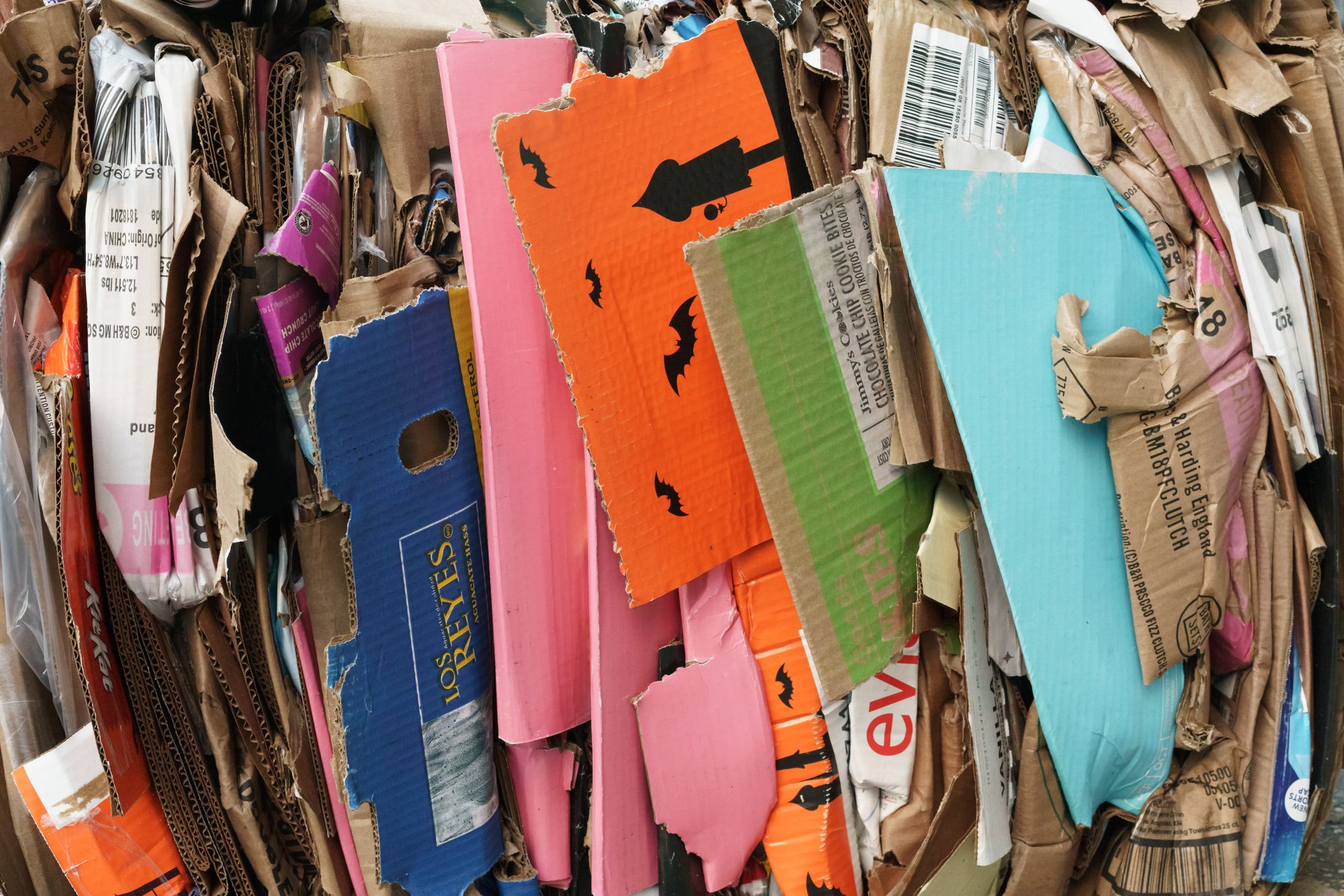
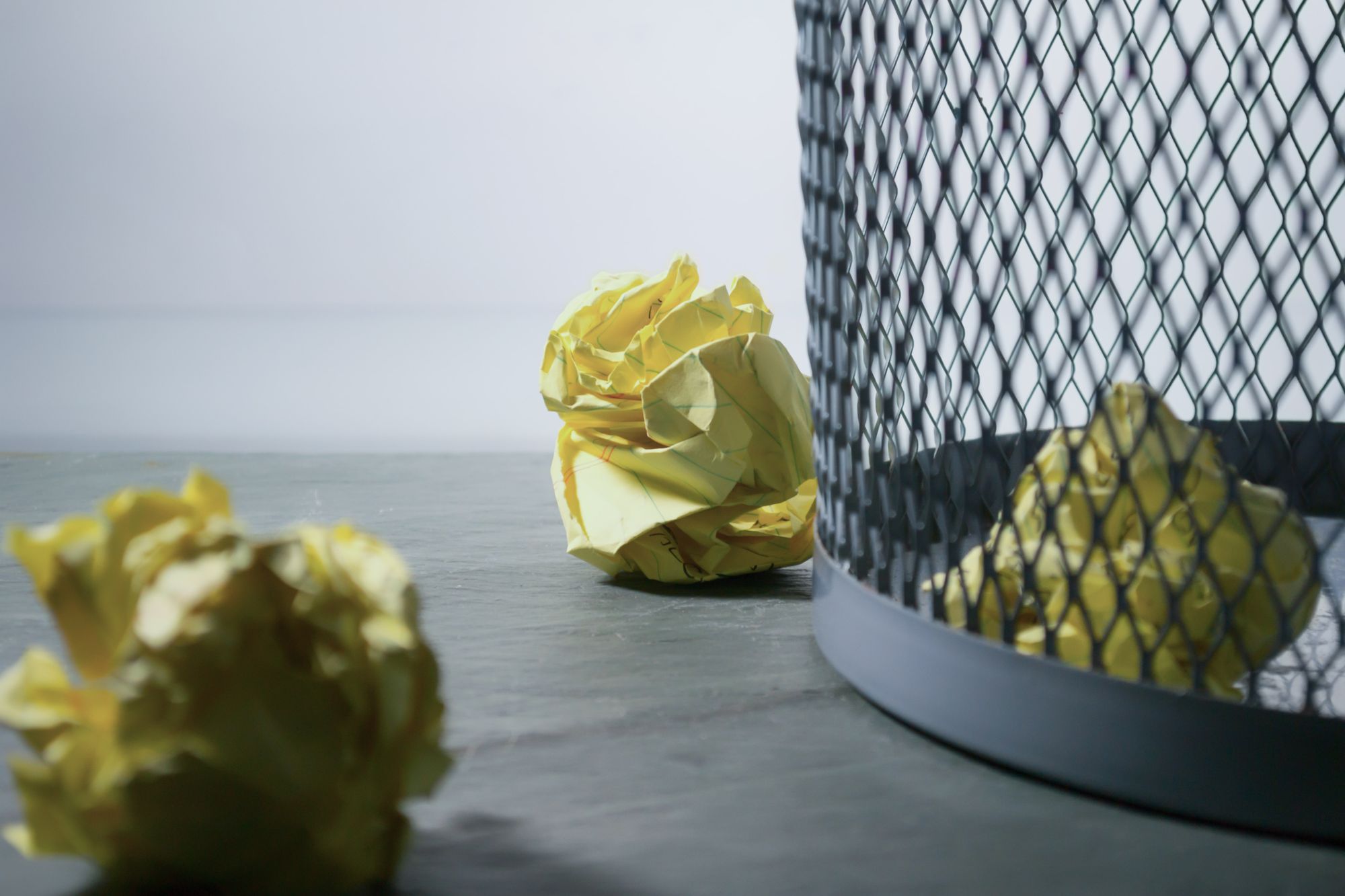
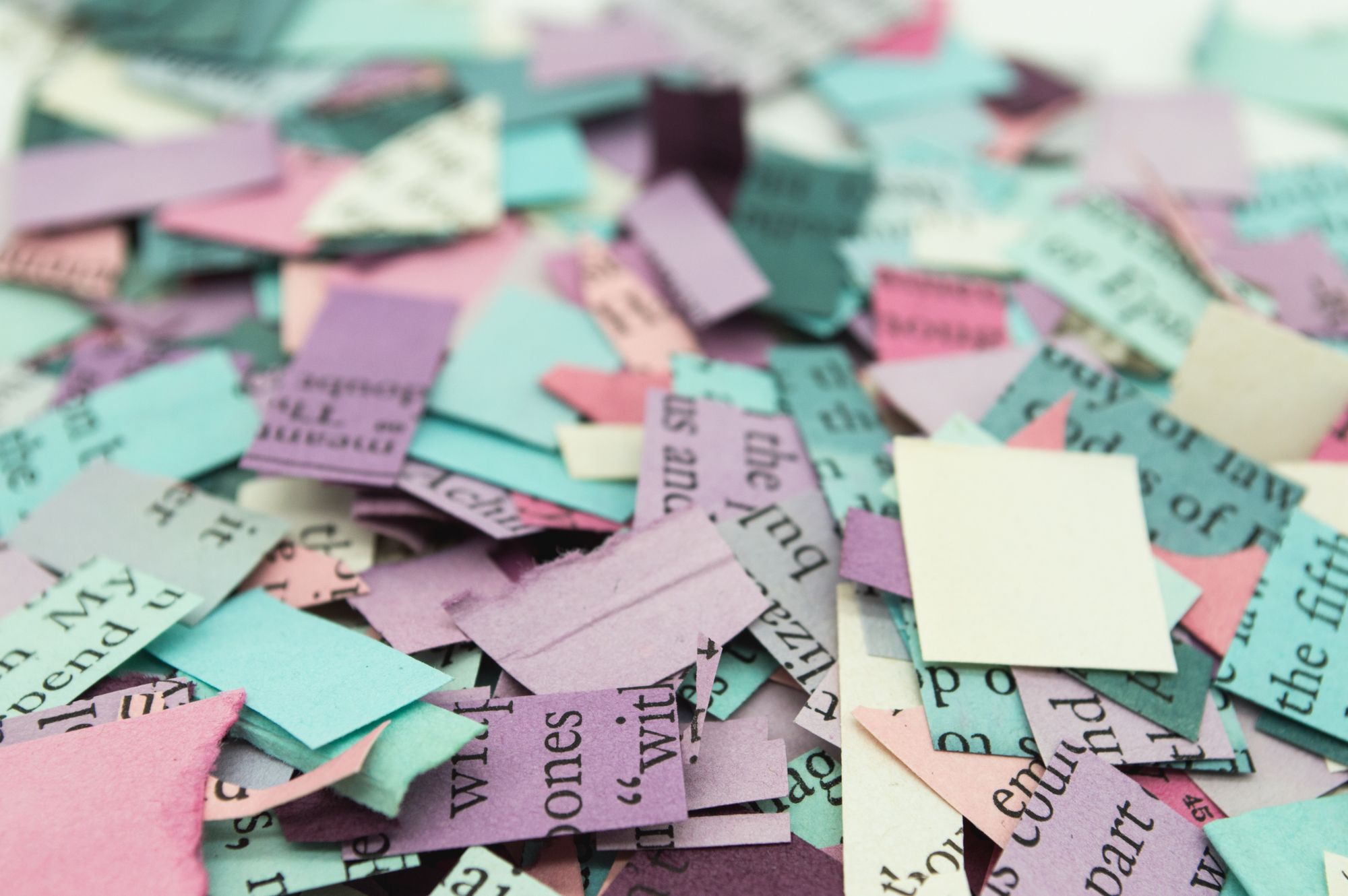
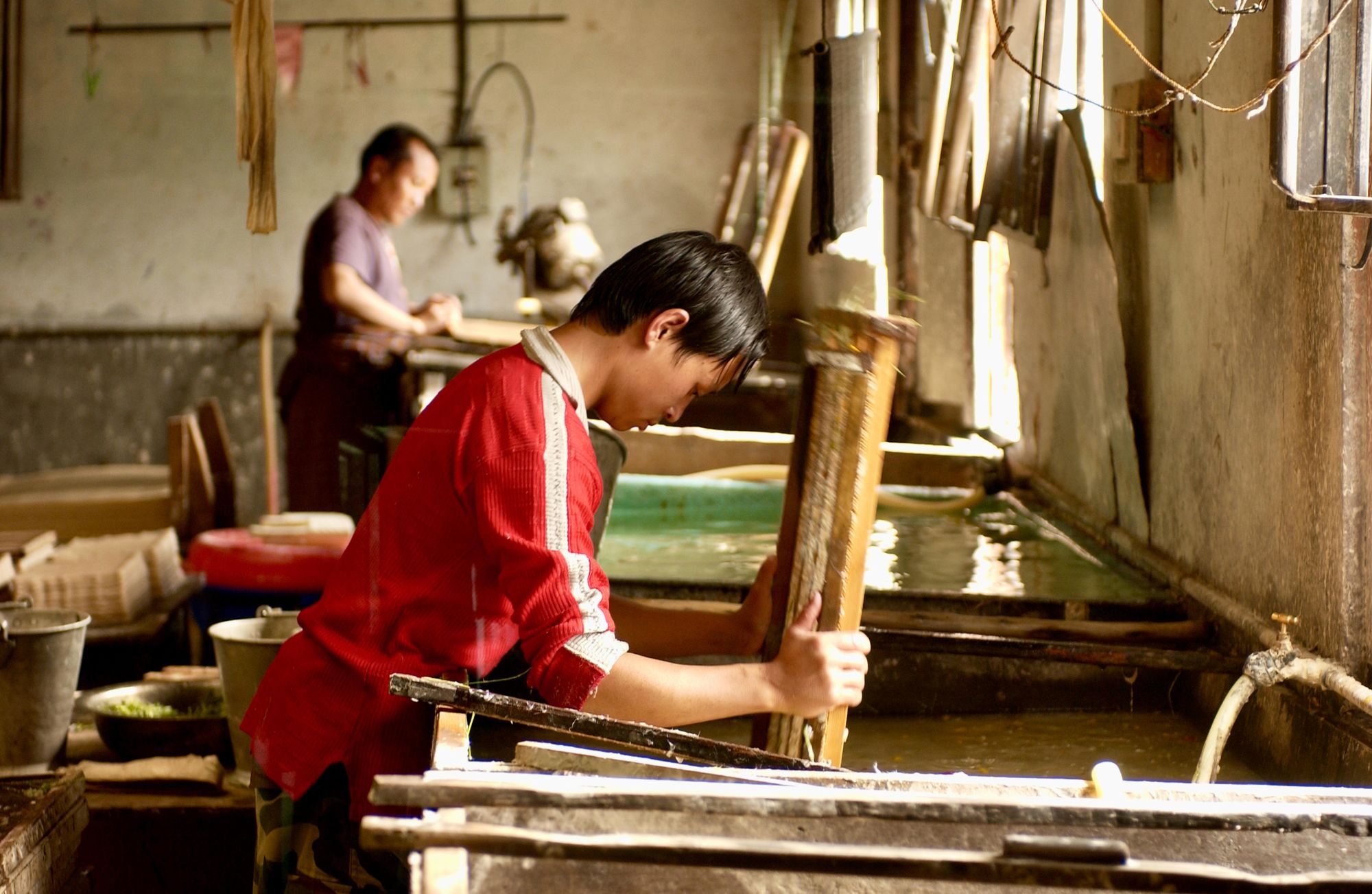
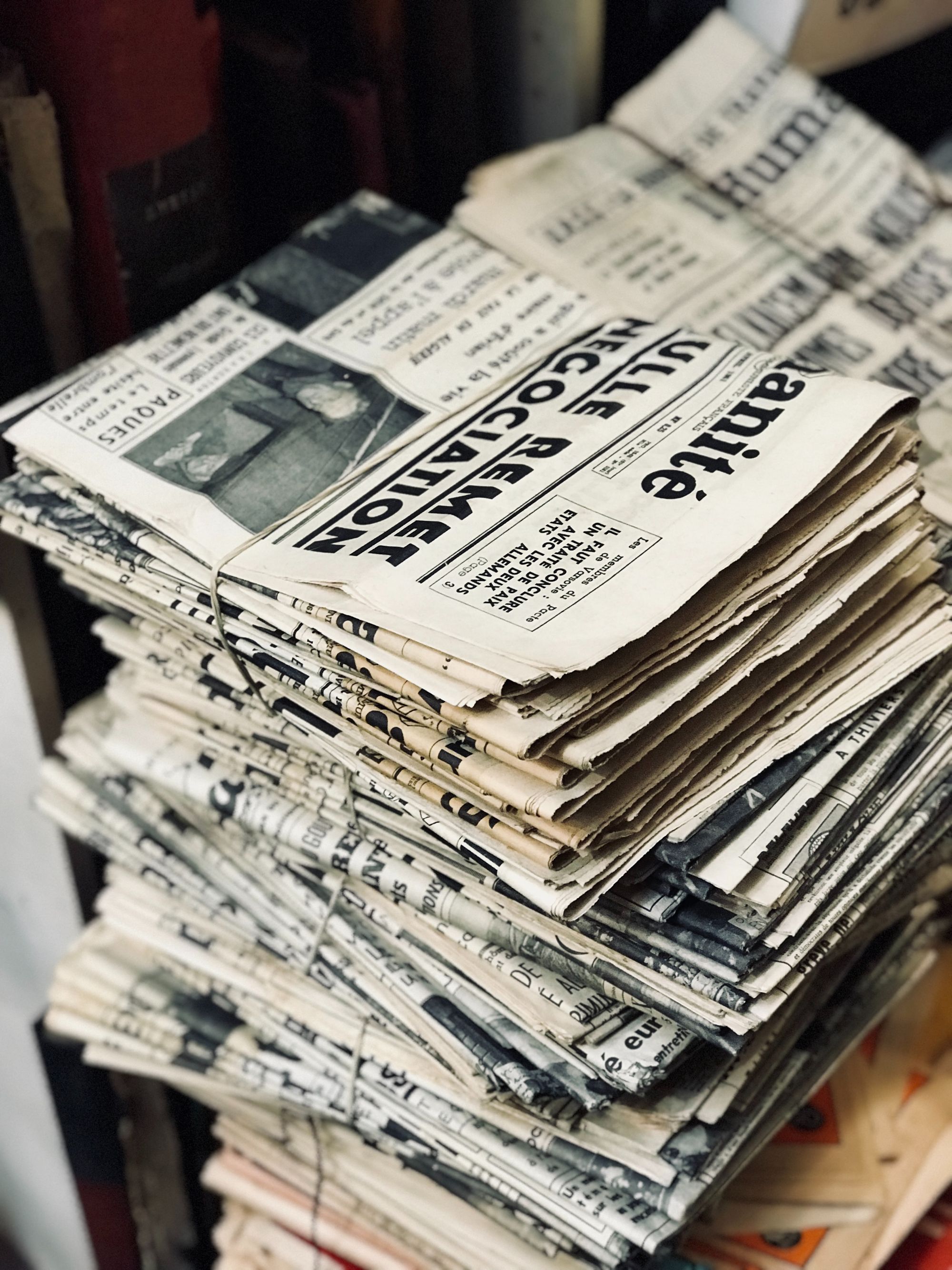