Wood manufacturing can be an expensive process, and every manufacturer wants to maximize their output while minimizing their expenses. As the world becomes more conscious about the environment and sustainability, there is an increased demand for sustainable and eco-friendly products. This has led to the development of new technologies and techniques that help manufacturers save money while producing high-quality products.
The global demand for sustainable wood products is expected to increase by 20% annually over the next few years. (Source: WWF)
These statistics highlight the potential for growth and profitability in the wood manufacturing industry, as well as the importance of cost-effective strategies to maximize the use of the available budget.
To stay competitive in the industry, wood manufacturers need to prioritize their budget and make the most of it. From sourcing sustainable materials to optimizing production processes and reducing waste, there are many ways to maximize your budget and boost your profitability.
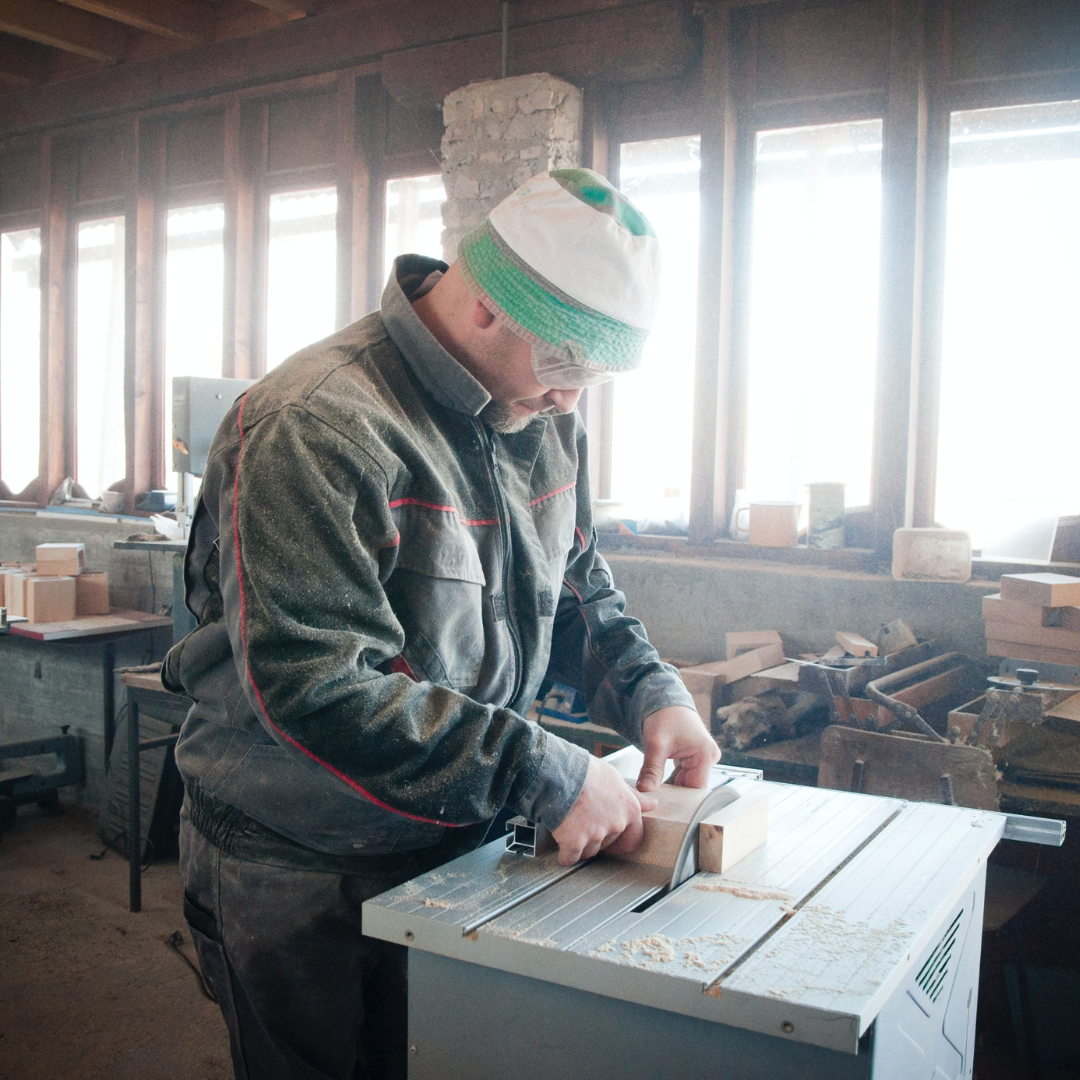
In this article, we will explore some of the key strategies that wood manufacturers can use to make the most of their budget and stay ahead of the competition.
- Importance of Effective Budgeting in Wood Manufacturing
- Assessing Your Current Budget
- Setting Realistic Goals
- Implementing Cost-Saving Measures
- Maximizing Revenue Streams
- Utilizing Technology to Optimize Production Processes, Reduce Waste, and Improve Efficiency
- Examples of Technology Solutions Available in the Wood Manufacturing Industry
- Collaborating with Suppliers
- Improve Your Manufacturing Budget Strategies with MRP and ERP Systems
- How can Deskera Help You?
- Key Takeaways
- Related Articles
Importance of Effective Budgeting in Wood Manufacturing
Effective budgeting is crucial for wood manufacturing companies because it allows them to plan and allocate their financial resources in a way that maximizes efficiency, profitability, and sustainability. By developing a comprehensive budget, manufacturers can better control costs, reduce waste, and identify areas for potential savings.
Budgeting also helps manufacturers to make informed decisions about capital expenditures, such as equipment upgrades or facility expansions, and to prioritize their spending based on their production goals and strategic objectives. This helps to ensure that the company is investing in areas that will generate the greatest return on investment and enhance their competitiveness in the marketplace.
Additionally, effective budgeting enables wood manufacturers to better manage their cash flow and minimize the risk of financial shortfalls or unexpected expenses. This helps to promote stability and long-term viability for the company, as well as foster a culture of responsible financial management. Ultimately, effective budgeting is essential for wood manufacturing companies that wish to optimize their financial performance and achieve sustainable growth.
Assessing Your Current Budget
Effective budgeting is crucial for any business, and wood manufacturing is no exception. In order to ensure long-term profitability and growth, it is important to regularly assess your current budget and make necessary adjustments.
This involves conducting a thorough review of your current expenses and revenue streams, identifying areas of overspending and underspending, and determining areas where investments could yield a high return.
By carefully analyzing your budget, you can make informed decisions about where to allocate your resources and identify opportunities to improve efficiency and profitability. In this article, we will explore the key steps involved in assessing your current budget and provide practical tips for making the most of your wood manufacturing budget.
Review of Current Expenses and Revenue Streams
Reviewing current expenses and revenue streams is an essential part of assessing your current budget in wood manufacturing. It involves analyzing your company's financial statements, including income statements, balance sheets, and cash flow statements, to understand your current expenses and revenue sources.
This information is critical in identifying areas where your company may be overspending or underspending and opportunities for revenue growth.
For instance, you may discover that your company is spending more on raw materials than necessary, or that you have an opportunity to negotiate better rates with your suppliers. Alternatively, you may identify new revenue streams, such as expanding your product offerings or increasing your marketing efforts to reach new customers.
By regularly reviewing your current expenses and revenue streams, you can make informed decisions about where to allocate your resources and make strategic investments that will help your wood manufacturing business thrive.
Identification of Areas of Overspending and Underspending
To effectively manage a wood manufacturing budget, it is crucial to identify areas of overspending and underspending. This involves a careful review of all expenses and revenue streams to identify which areas are consuming too much money or generating insufficient revenue.
By doing so, wood manufacturers can develop a more accurate budget that aligns with their financial goals and maximizes their resources. Areas of overspending can be addressed by finding ways to reduce costs or negotiating better prices with suppliers, while areas of underspending can be examined for potential investment opportunities or increased marketing efforts to boost revenue.
This analysis of expenses and revenue streams provides a clear picture of the financial health of the wood manufacturing business and allows for informed decision-making when it comes to budgeting.
Setting Realistic Goals
Without clear goals, it is challenging to identify the resources needed to achieve them. Goals can be short-term or long-term and should be specific, measurable, achievable, relevant, and time-bound. For example, a short-term goal could be to reduce material waste by 10% within the next quarter, while a long-term goal could be to increase production capacity by 20% within the next year.
It is crucial to ensure that the goals are achievable and aligned with the company's mission and values. Unrealistic goals can lead to frustration and demotivation among employees, while attainable goals can increase employee engagement and motivation.
Once the goals are set, it is important to track progress regularly and adjust the budget accordingly. By setting realistic goals and tracking progress, wood manufacturers can make the most of their budget and achieve their desired outcomes.
Defining Clear Objectives for the Budget
Defining clear objectives for the budget is crucial in making the most of your wood manufacturing budget. These objectives can range from increasing profits, reducing expenses, improving product quality, expanding operations, or investing in new technologies. Clear goals will help you focus on what's important and prioritize your spending accordingly.
Once you have defined your objectives, it's essential to establish realistic targets that are achievable within your budget. This will ensure that you're not overcommitting your resources or setting yourself up for failure. By setting realistic targets, you can monitor your progress and adjust your budget as needed to meet your goals.
To help achieve your objectives, it's also important to establish metrics and key performance indicators (KPIs) to track your progress. This can include tracking sales figures, production efficiency, waste reduction, and other relevant metrics. With clear objectives, realistic targets, and effective tracking mechanisms in place, you can make the most of your wood manufacturing budget and achieve sustainable growth for your business.
Prioritizing Goals Based on their Potential Impact on the Business
Prioritizing goals involves identifying and ranking objectives based on their potential impact on the business. This helps to ensure that resources are allocated to the most critical areas of the operation. Prioritization should consider factors such as revenue generation, cost savings, customer satisfaction, and employee engagement.
For example, if the goal is to increase revenue, it is essential to identify the products or services that generate the most profit and focus on expanding those areas. Similarly, if the objective is to reduce expenses, it is essential to evaluate the areas of overspending and find ways to cut costs without compromising quality or customer service.
By prioritizing goals, wood manufacturers can focus their resources on the most critical areas, achieving more significant results with their budget. It also helps to ensure that the budget aligns with the overall business strategy and goals.
Implementing Cost-Saving Measures
Implementing cost-saving measures involves identifying areas where costs can be reduced without sacrificing the quality of your products or services. One approach to reducing costs is to examine your current processes and identify any inefficiencies or areas where waste occurs.
For example, you may be able to optimize your material usage or reduce energy consumption by upgrading to more efficient equipment.
Another strategy is to negotiate with suppliers to get better prices or explore alternative suppliers. This can help you get the materials you need at a lower cost and free up budget for other expenses. Additionally, you can explore new technologies that can help streamline your production processes, reduce waste, and lower costs over time.
It is also essential to review your staffing levels and ensure that you are utilizing your workforce effectively. By aligning your team’s skill sets and experience with your business goals, you can optimize productivity and reduce labor costs.
Overall, implementing cost-saving measures requires a proactive approach to identifying and addressing inefficiencies in your current processes, negotiating with suppliers, adopting new technologies, and optimizing your staffing levels.
Identifying Opportunities for Cost Savings
In wood manufacturing, cost-saving measures are essential to maximizing the budget and improving profitability. One way to implement such measures is to identify areas where expenses can be reduced. For example, optimizing production processes can lead to significant cost savings by reducing material waste, energy consumption, and labor costs. Another way is to negotiate better contracts with suppliers or find new suppliers that offer better pricing or more favorable terms.
Implementing cost-saving measures requires a comprehensive understanding of the business's current financial situation and the potential impact of each measure on the budget. It is crucial to prioritize measures based on their potential impact on the business, such as reducing high-cost inputs, increasing production efficiency, or improving inventory management.
Businesses can also consider implementing green practices that not only reduce costs but also promote sustainability. For example, using energy-efficient lighting, equipment, and machinery can significantly reduce energy costs.
Recycling waste materials can also generate additional revenue while reducing disposal costs. The key is to identify areas where sustainability practices can be integrated into the business without sacrificing quality or productivity.
Ultimately, implementing cost-saving measures requires a proactive approach and a willingness to adapt to changing market conditions. By continuously monitoring and adjusting the budget, businesses can optimize their financial performance and position themselves for long-term success.
Implementing Changes To Reduce Expenses And Increase Efficiency
Once opportunities for cost savings have been identified, it is important to implement changes that will reduce expenses and increase efficiency. This can involve streamlining production processes, eliminating waste, and reducing overhead costs. For example, upgrading equipment or automating certain tasks can increase production efficiency and reduce labor costs.
Another strategy is to analyze and renegotiate supplier contracts to ensure the best possible prices and terms. In addition, implementing energy-saving measures such as using energy-efficient lighting and equipment, can also help reduce operating costs.
It is important to ensure that cost-saving measures do not compromise the quality of the products or services provided. Careful consideration should be given to maintaining product quality while reducing costs. This may involve finding ways to reduce material waste without sacrificing quality, or implementing quality control measures to catch defects before they result in wasted resources.
Overall, implementing cost-saving measures requires a careful analysis of the budget and a willingness to make changes to reduce expenses and increase efficiency. By prioritizing cost savings and implementing changes, businesses can improve their financial position and better compete in the marketplace.
Maximizing Revenue Streams
Maximizing revenue streams is crucial to the success of any wood manufacturing business. One effective way to do this is by identifying new market opportunities and diversifying product lines. By understanding the needs and preferences of potential customers, businesses can develop new products that appeal to a wider audience.
Another way to maximize revenue is by optimizing pricing strategies. Conducting market research to determine the prices of similar products in the market can help businesses set competitive prices while still maintaining profitability.
In addition, offering excellent customer service can also lead to increased revenue. Customers are more likely to make repeat purchases and recommend a business to others if they have a positive experience with the company.
Furthermore, implementing upselling and cross-selling strategies can also help to maximize revenue. By offering complementary products or encouraging customers to upgrade to higher-end products, businesses can increase the value of each sale.
Overall, by focusing on both cost-saving measures and revenue-maximizing strategies, wood manufacturing businesses can make the most of their budget and achieve long-term success.
Identifying New Revenue Streams, such as Diversifying Product Offerings or Expanding Into New Markets
In order to make the most of a wood manufacturing budget, it is important to not only focus on reducing expenses, but also on maximizing revenue streams. One way to do this is by identifying new opportunities for revenue. This may involve diversifying product offerings, expanding into new markets, or finding new ways to monetize existing products.
For example, a wood manufacturer may consider offering customized products to appeal to a wider range of customers, or expanding into international markets to increase sales.
In addition to identifying new revenue streams, it is important to optimize existing ones. This may involve improving marketing and sales strategies, increasing prices where appropriate, or reducing waste and inefficiencies in the production process to maximize profits. By taking a comprehensive approach to revenue maximization, wood manufacturers can ensure that they are making the most of their budget and generating as much revenue as possible.
Implementing Changes to Increase Revenue and Profitability
One effective strategy for maximizing revenue is to focus on increasing customer retention rates. This can be achieved by improving the quality of your products and services, providing excellent customer support, and offering loyalty programs and discounts.
Another strategy is to identify new opportunities for growth, such as entering new markets or expanding your product offerings. This can be achieved by conducting market research to identify unmet customer needs or by partnering with other companies to develop new products and services.
Finally, it's important to optimize your pricing strategies to ensure that you are charging a fair price for your products while still maintaining profitability. This may involve conducting regular pricing audits to identify areas where prices can be adjusted, or implementing dynamic pricing strategies that adjust prices based on supply and demand.
By implementing these and other strategies, you can maximize revenue and profitability, allowing you to make the most of your wood manufacturing budget.
Utilizing Technology to Optimize Production Processes, Reduce Waste, and Improve Efficiency
Technology can play a significant role in optimizing production processes, reducing waste, and improving efficiency in wood manufacturing. For instance, computer-aided design (CAD) software can help design products with minimal waste, and computer-aided manufacturing (CAM) systems can automate the manufacturing process to reduce human error and improve accuracy.
Furthermore, sensors and automation technologies can be used to monitor the production process, allowing for real-time data analysis, identifying bottlenecks, and optimizing production flows. Additionally, advanced data analytics and machine learning algorithms can be applied to production data, enabling predictive maintenance and identifying opportunities for improvement.
In terms of waste reduction, technology can help in the tracking of waste materials and by-products, which can be repurposed, recycled, or sold to other businesses for reuse. Furthermore, the use of renewable energy sources, such as solar panels, can reduce energy costs and environmental impacts.
Overall, technology can help wood manufacturers increase efficiency, reduce waste, and improve profitability. However, it is important to note that the implementation of technology requires a significant investment, and companies must carefully consider the benefits and costs before adopting new technologies.
Examples of Technology Solutions Available in the Wood Manufacturing Industry
There are several technology solutions available in the wood manufacturing industry that can help optimize production processes, reduce waste, and improve efficiency. Some examples include:
- Computer-Aided Design (CAD) software: This software helps create and modify 2D or 3D designs of products, components, and assemblies. It can also generate engineering documentation and bill of materials (BOM), improving accuracy and reducing errors in the manufacturing process.
- Computer Numerical Control (CNC) machines: These machines use computer programs to control the movement and operation of tools that cut and shape wood. CNC machines are highly accurate and can produce consistent and complex shapes, reducing waste and increasing efficiency.
- Radio Frequency Identification (RFID) technology: RFID tags can be attached to products or components, enabling real-time tracking of inventory, production progress, and quality control. This technology helps improve inventory management, reduce errors, and increase transparency.
- Internet of Things (IoT) sensors: IoT sensors can be installed in machines, equipment, or products to collect and transmit data on their performance, location, and status. This data can be analyzed to optimize maintenance schedules, reduce downtime, and improve product quality.
- Cloud-based software: Cloud-based software solutions can help streamline business processes, such as supply chain management, accounting, and customer relationship management (CRM). These solutions can improve communication, collaboration, and data management, leading to increased efficiency and cost savings.
Collaborating with Suppliers
Collaborating with suppliers can be a valuable strategy for optimizing your wood manufacturing budget. By working closely with suppliers, you can negotiate better pricing and payment terms, reduce lead times, and improve the quality and consistency of materials.
Additionally, suppliers can offer valuable insights and expertise that can help you streamline your production processes and identify new cost-saving opportunities.
To effectively collaborate with suppliers, it's important to establish clear communication channels and build strong relationships based on trust and transparency. This includes sharing information about your production processes, inventory levels, and sales projections, as well as being open to feedback and suggestions for improvement.
One effective way to collaborate with suppliers is to establish vendor-managed inventory (VMI) programs, where suppliers take on responsibility for managing inventory levels and replenishing supplies as needed. This can help reduce inventory costs and improve supply chain efficiency.
Overall, collaborating with suppliers can help you optimize your production processes, reduce costs, and improve the quality of your products, all of which can have a positive impact on your bottom line.
Strong Relationships with Suppliers for Cost Savings and Improved Production Processes
their budget and improve their overall performance. Building strong relationships with suppliers can enable manufacturers to negotiate better prices, access better quality materials, and streamline their supply chain processes. By working together, manufacturers and suppliers can identify areas where costs can be reduced and efficiencies can be improved.
For example, suppliers may be able to offer bulk discounts or reduced lead times for orders placed in advance. Manufacturers can also work with suppliers to identify and address any quality control issues that may be causing waste or delays in production.
In addition, collaborating with suppliers can enable manufacturers to stay up-to-date on the latest trends and technologies in the industry, which can help them stay competitive and improve their products. This can include innovations in materials, machinery, and production techniques.
Overall, building strong relationships with suppliers can help wood manufacturers optimize their budget, improve their production processes, and ultimately deliver higher quality products to their customers.
Improve Your Manufacturing Budget Strategies with MRP and ERP Systems
MRP (Material Requirements Planning) and ERP (Enterprise Resource Planning) systems are software solutions that can help wood manufacturers optimize their production processes and improve their budget strategies. MRP systems focus on the materials and components needed to produce goods, while ERP systems provide a more comprehensive view of a company's resources and operations.
By implementing these systems, wood manufacturers can gain better visibility into their supply chain, manage inventory more effectively, and reduce waste. They can also improve forecasting accuracy and respond more quickly to changes in demand, resulting in more efficient production processes and higher customer satisfaction.
MRP and ERP systems can also help manufacturers identify areas of overspending and underspending in their budget, and make data-driven decisions about where to allocate resources. This can lead to cost savings, increased revenue, and improved profitability.
In addition, MRP and ERP systems can help wood manufacturers comply with regulations and sustainability standards, such as FSC certification, by providing greater transparency and traceability in their supply chain.
Overall, MRP and ERP systems are powerful tools that can help wood manufacturers make the most of their budget and improve their overall performance.
How can Deskera Help You?
Deskera ERP and MRP systems help you to keep your business units organized. The system's primary functions are as follows:
- Keep track of your raw materials and final items inventories
- Control production schedules and routings
- Keep a bill of materials
- Produce thorough reports
- Make your own dashboards
Deskera's integrated financial planning tools enable investors to better plan and track their investments. It can assist investors in making faster and more accurate decisions.
Deskera Books allows you to better manage your accounts and finances. Maintain good accounting practices by automating tasks like billing, invoicing, and payment processing.
Deskera CRM is a powerful solution that manages your sales and helps you close deals quickly. It not only enables you to perform critical tasks like lead generation via email, but it also gives you a comprehensive view of your sales funnel.
Deskera People is a straightforward tool for centralizing your human resource management functions.
Key Takeaways
- Effective budgeting is crucial for wood manufacturing businesses to optimize their resources and achieve their financial goals.
- Assessing current expenses and revenue streams is essential to understand where the business stands financially.
- Setting clear objectives and prioritizing goals based on their potential impact can help businesses focus their resources.
- Implementing cost-saving measures, such as optimizing production processes, negotiating better supplier contracts, and reducing waste, can lead to significant savings.
- Maximizing revenue streams by identifying new opportunities, diversifying product offerings, and expanding into new markets can help businesses increase profitability.
- Technology solutions such as MRP and ERP systems can be used to optimize production processes, reduce waste, and improve efficiency.
- Collaborating with suppliers can lead to cost savings and improved production processes.
- Regularly reviewing and adjusting the budget is necessary to stay on track and make informed decisions.
- Monitoring financial performance through key performance indicators (KPIs) can help businesses stay on top of their finances.
- Developing a contingency plan can help businesses prepare for unexpected financial challenges.
- Investing in employee training and development can lead to increased productivity and efficiency.
- Implementing sustainable practices can not only benefit the environment but also reduce costs and improve the brand's reputation.
Related Articles
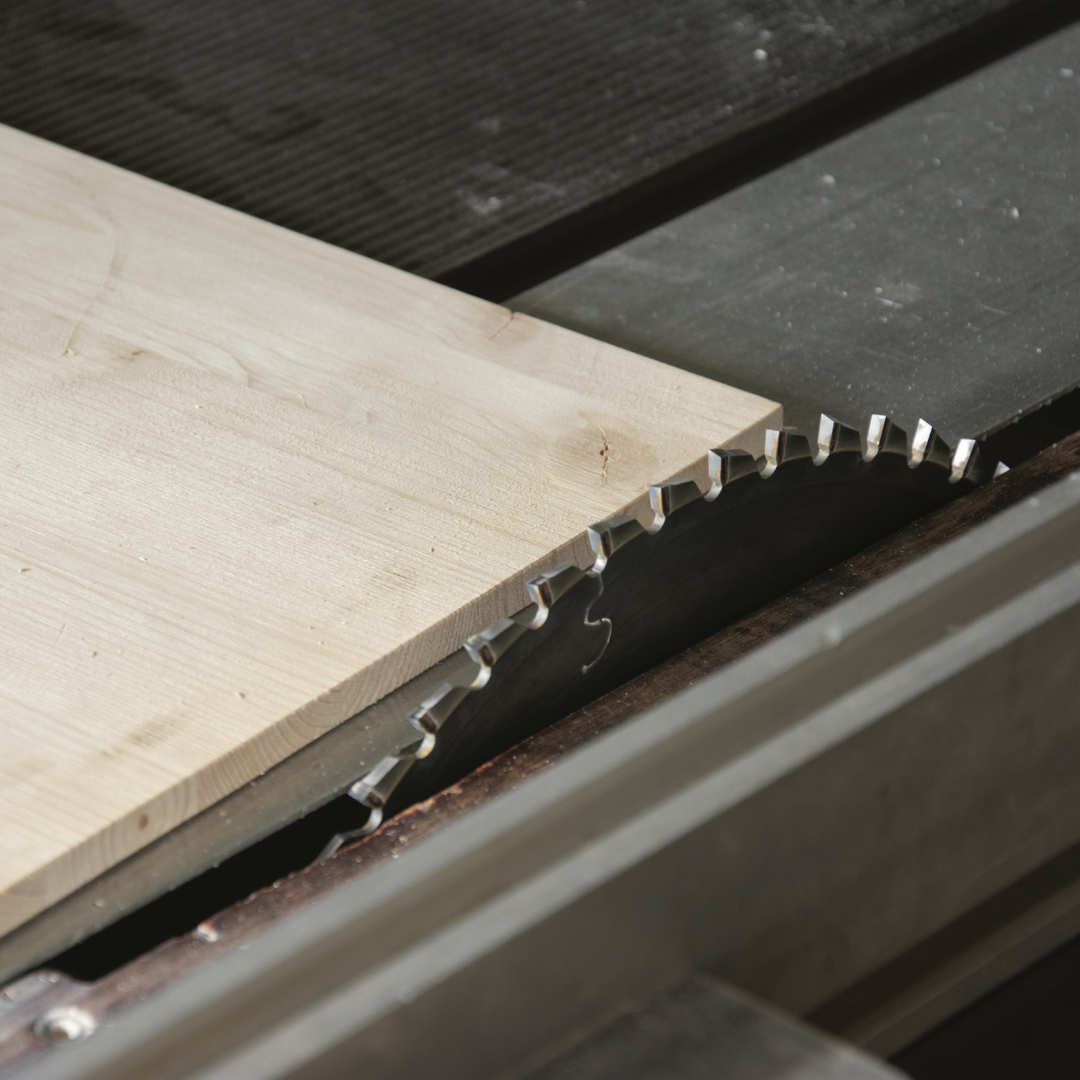
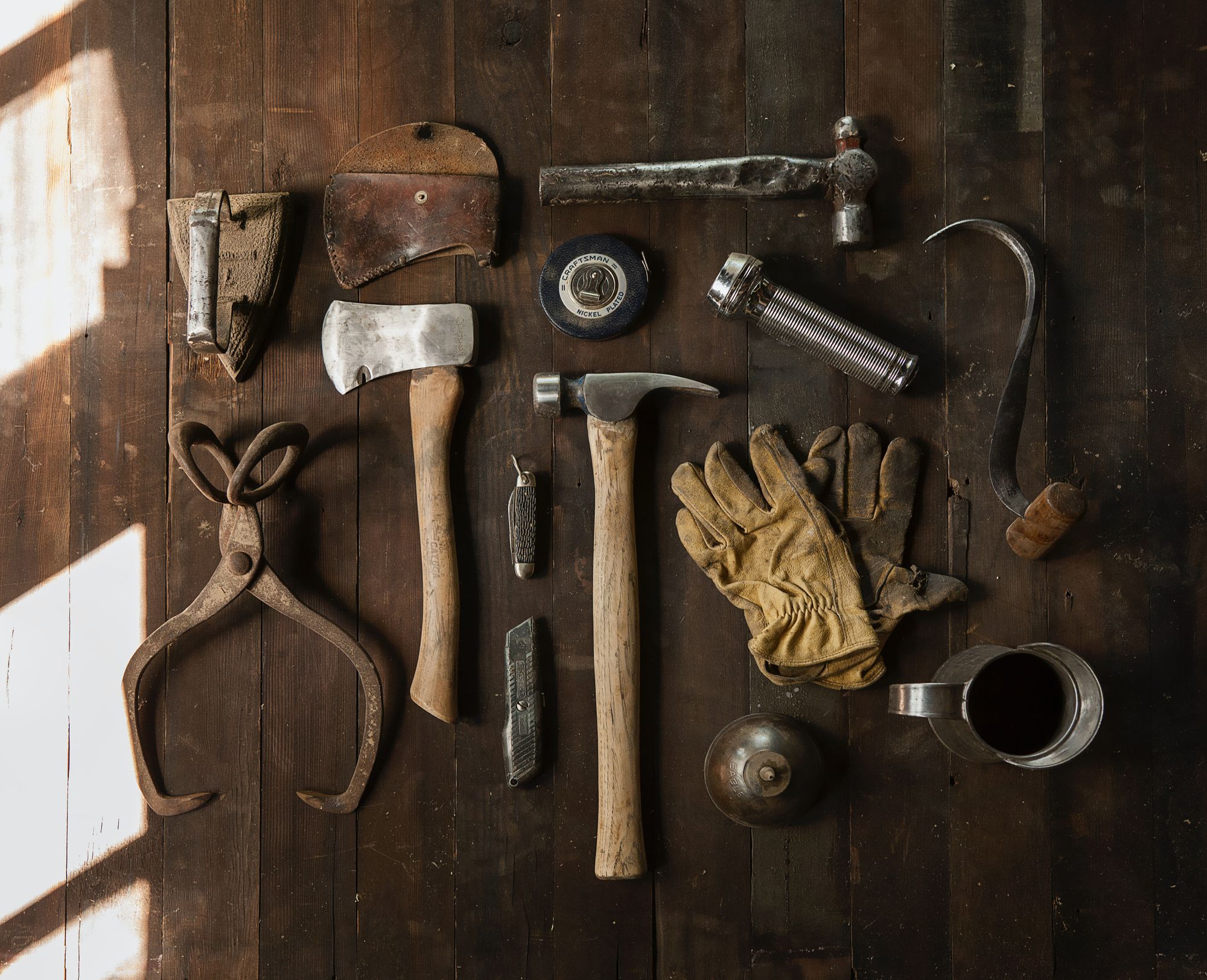
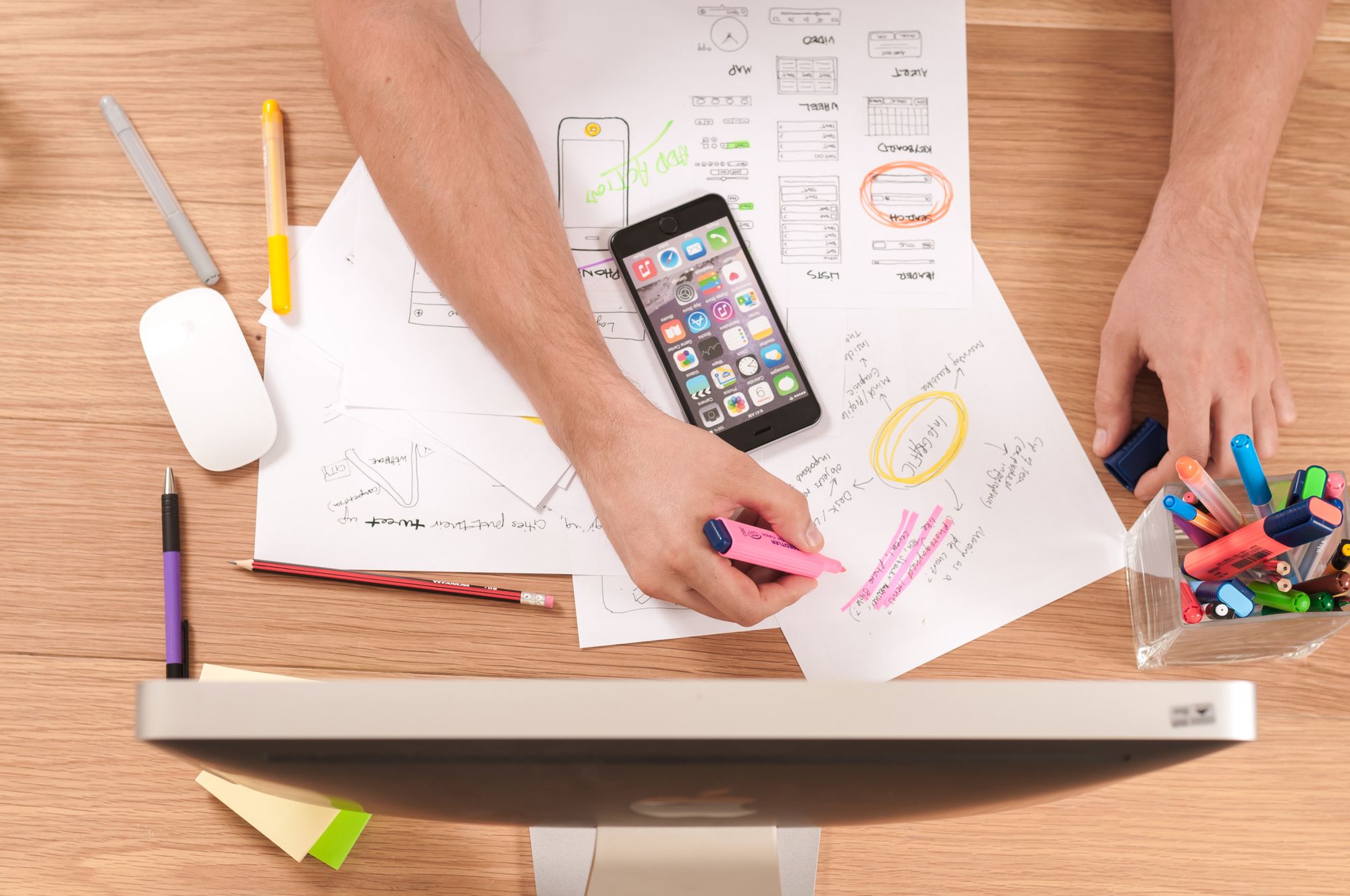