Efficient inventory management stands at the heart of any successful business operation, ensuring a delicate balance between meeting customer demand and controlling costs. A critical tool in achieving this balance is the Multi-Level Bill of Materials (BOM), a comprehensive framework that outlines the hierarchy of components necessary for product assembly.
This article delves into the symbiotic relationship between inventory management and multi-level BOMs, exploring how this dynamic duo can streamline operations and boost competitiveness.
Trivia: Did you know that the concept of Bill of Materials dates back to the early 20th century? It was initially employed in manufacturing and engineering to list the raw materials, components, and sub-components needed to create a product. Over the years, its significance has grown exponentially as industries embraced complex production processes and global supply chains.
Today, the evolution of technology has transformed the traditional BOM into a multi-level powerhouse, capable of unraveling intricate product structures and optimizing inventory strategies.
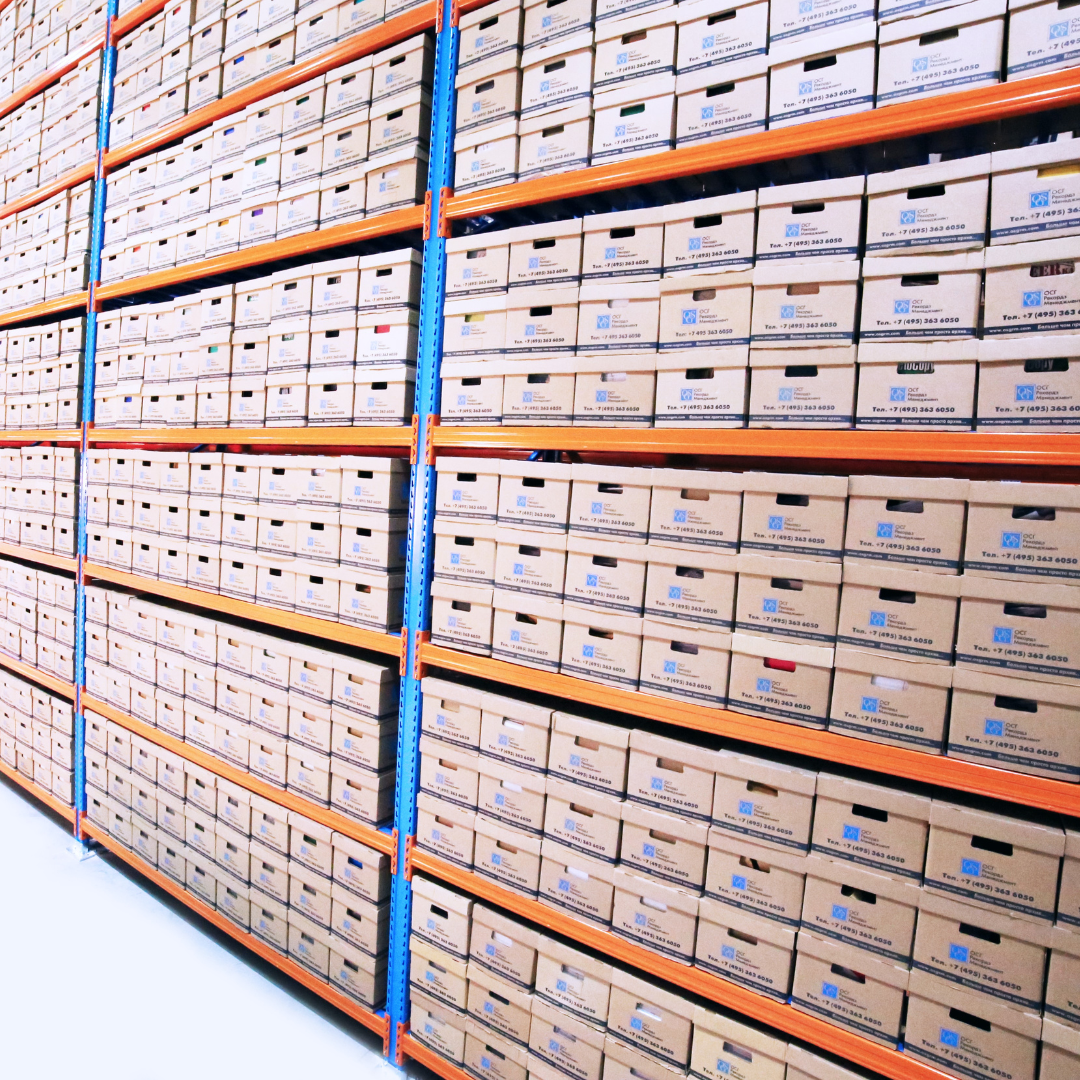
As we embark on this exploration, we will uncover the advantages that multi-level BOMs bring to inventory management. From facilitating accurate demand forecasting to enabling efficient order planning, these hierarchies offer insights that are invaluable in today's fast-paced business landscape.
Join us in discovering how businesses are harnessing the potential of multi-level BOMs to simplify their inventory management complexities and achieve operational excellence.
- Definition of Inventory Management
- Importance of Effective Inventory Management
- Introduction to Bill of Materials (BOM)
- Link between BOM and Inventory Management Efficiency
- Understanding Multi-Level Bill of Materials (BOM)
- Benefits of Multi-Level BOMs in Inventory Management
- Implementing Multi-Level BOMs: Best Practices
- Challenges and Solutions
- Real-World Examples
- Tools and Technologies
- Future Trends in Multi-Level BOM and Inventory Management
- Conclusion
- Key Takeaways
- Related Articles
Definition Of Inventory Management
Inventory management refers to the systematic process of overseeing, controlling, and optimizing a company's inventory of raw materials, work-in-progress goods, and finished products. It involves effectively balancing the supply and demand of goods to ensure that sufficient stock is available to meet customer orders while minimizing excess inventory and associated costs.
Effective inventory management entails various strategies and practices aimed at achieving operational efficiency, reducing carrying costs, and improving overall business performance.
Inventory management encompasses a range of tasks, including inventory tracking, order fulfillment, demand forecasting, procurement, and inventory valuation. The primary goal is to strike a delicate equilibrium between having enough stock to fulfill customer orders promptly and avoiding overstock situations that tie up valuable capital and storage space.
In the context of modern businesses, inventory management extends beyond the physical management of goods. It involves leveraging technology, data analysis, and automation to enhance decision-making processes. Efficient inventory management practices contribute to improved cash flow, better customer satisfaction through on-time deliveries, and the optimization of resources throughout the supply chain.
By implementing sound inventory management practices, businesses can navigate market fluctuations, respond to changing customer demands, and maintain a competitive edge in today's complex and interconnected global economy.
Importance Of Effective Inventory Management
Effective inventory management is a cornerstone of operational success for businesses across various industries. It plays a pivotal role in ensuring smooth operations, customer satisfaction, and financial stability. Several key reasons underscore the significance of implementing robust inventory management practices:
- Optimized Cash Flow: Maintaining the right level of inventory prevents excessive tied-up capital that could be used for other business investments. Effective inventory management minimizes the risk of overstocking or stockouts, thus optimizing cash flow and ensuring financial flexibility.
- Meeting Customer Demand: Timely availability of products is crucial for meeting customer expectations. Well-managed inventory ensures that customer orders are fulfilled promptly, enhancing customer satisfaction and loyalty.
- Cost Control: Balancing inventory levels helps reduce storage and carrying costs. Avoiding excess inventory minimizes warehousing expenses, while accurate demand forecasting prevents rush orders and expedited shipping charges.
- Supply Chain Efficiency: Inventory management is an integral part of supply chain optimization. It enables businesses to align production schedules, procurement activities, and distribution channels to streamline the flow of goods.
- Production Planning: Proper inventory management aids in efficient production planning. With a clear understanding of inventory levels and demand patterns, businesses can avoid production bottlenecks and delays.
- Risk Mitigation: Inventory management safeguards against supply chain disruptions caused by factors like supplier issues, market fluctuations, or natural disasters. Maintaining safety stock provides a buffer against unforeseen events.
- Data-Driven Decision Making: Modern inventory management leverages data analytics to make informed decisions. Accurate data on inventory turnover, lead times, and demand patterns empower businesses to make strategic choices.
- Minimized Waste: Effective inventory management helps reduce waste by preventing product obsolescence. Businesses can accurately track product lifecycles and plan for timely updates or discontinuations.
- Regulatory Compliance: In industries with strict regulations, such as pharmaceuticals or food, inventory management ensures compliance by tracking expiration dates, lot numbers, and other critical data.
- Competitive Advantage: Businesses that can consistently deliver products on time and maintain optimized inventory levels gain a competitive edge. Efficient inventory management supports customer retention and attracts new business.
In essence, effective inventory management is the linchpin that connects production, distribution, and customer satisfaction. It empowers businesses to strike a harmonious balance between supply and demand, fostering resilience, growth, and sustainable success in today's dynamic business landscape.
Introduction to Bill of Materials (BOM)
A Bill of Materials, commonly referred to as BOM, is a foundational document in manufacturing and production industries that provides a comprehensive breakdown of the components, sub-components, raw materials, and resources required to assemble a product.
Essentially, a BOM acts as a roadmap that outlines the hierarchical structure of a product, guiding the entire production process from conception to completion.
The primary purpose of a BOM is to offer a clear and organized representation of how a product is built, highlighting the relationships between various components and their quantities. This enables manufacturers, engineers, designers, and other stakeholders to understand the complexity of the assembly process and aids in planning, procurement, production scheduling, and cost estimation.
A typical BOM includes essential information such as part names, part numbers, descriptions, quantities, unit of measure, and sometimes even additional attributes like supplier information, lead times, and cost data. There are different types of BOMs, each serving a distinct purpose:
Single-Level BOM: This type lists all the components required for a finished product, without detailing the sub-assemblies or their components.
Multi-Level BOM: A more intricate version, the multi-level BOM, extends beyond the surface and delves into sub-assemblies, sub-components, and their interdependencies. It offers a comprehensive view of the entire product structure.
Indented BOM: Also known as a hierarchical BOM, this format visually represents the assembly hierarchy with indentation, making it easier to understand the relationships between components.
The advent of technology has elevated the BOM from a static document to a dynamic tool integrated into various software systems, such as Product Lifecycle Management (PLM) and Enterprise Resource Planning (ERP) systems. This digital transformation enables real-time collaboration, accurate version control, and seamless synchronization of BOM data across departments, improving communication and reducing errors.
In the context of inventory management, the BOM serves as a critical link, facilitating demand forecasting, procurement planning, and efficient allocation of resources. It aids in minimizing excess inventory and ensuring that the right components are available at the right time, ultimately contributing to smoother operations and enhanced customer satisfaction.
Link between BOM and inventory management efficiency
The relationship between a Bill of Materials (BOM) and inventory management efficiency is a symbiotic one, with each complementing the other to create a streamlined and optimized production and supply process. The BOM acts as a bridge that connects the design and engineering aspects of a product with the practicalities of managing inventory.
Here's how the BOM contributes to inventory management efficiency:
Accurate Demand Forecasting: A detailed BOM outlines the exact components needed for each product, allowing for precise demand forecasting. This accuracy helps prevent overstocking or understocking, aligning inventory levels with actual production requirements.
Optimized Procurement: With a multi-level BOM in hand, procurement teams can plan purchases more strategically. They know precisely which materials and components are needed, in what quantities, and when they're needed. This reduces the risk of stockouts and eliminates the need for emergency orders.
Resource Allocation: The BOM provides insights into the allocation of resources, including labor and machinery. This prevents resource bottlenecks, ensures efficient use of assets, and minimizes production delays.
Efficient Production Planning: The BOM's hierarchical structure shows how components fit together. This aids in scheduling production runs, enabling efficient use of manufacturing facilities and reducing downtime.
Minimized Excess Inventory: The clarity provided by the BOM helps prevent over-ordering of materials. This, in turn, reduces excess inventory that ties up working capital and storage space.
Effective Supplier Collaboration: Accurate BOMs facilitate communication with suppliers. Suppliers can better understand the components required, leading to improved lead times and reduced uncertainties.
Change Management: As products evolve, BOMs are updated to reflect design changes. This ensures that only the most current components are ordered, minimizing the risk of obsolete inventory.
Cost Control: By providing a detailed breakdown of components and associated costs, the BOM aids in cost estimation and control. This helps in evaluating the financial impact of different production scenarios.
Enhanced Decision Making: Inventory managers can make informed decisions based on the insights provided by the BOM. They can allocate resources, adjust inventory levels, and plan for production fluctuations more effectively.
Cross-Functional Collaboration: The BOM fosters collaboration between design, engineering, production, and procurement teams. This interdisciplinary cooperation ensures that everyone is aligned, reducing misunderstandings and delays.
In essence, the BOM acts as a guiding map that ensures a smooth journey from raw materials to finished products. Its accurate representation of product structure and interdependencies empowers businesses to optimize their inventory management strategies.
As technology continues to advance, integrating BOMs with digital tools further enhances their impact, making them invaluable assets for businesses striving for operational excellence.
Understanding Multi-Level Bill of Materials (BOM)
A Multi-Level Bill of Materials (BOM) is an advanced variant of the traditional BOM used in manufacturing and production industries. It goes beyond the surface-level representation of a product's components and delves deeper into the hierarchical structure of assemblies and sub-assemblies.
This comprehensive breakdown provides a more detailed and intricate view of how products are built, highlighting not only the primary components but also the relationships and dependencies between each element in the production process.
A. Definition of multi-level BOM
A Multi-Level Bill of Materials (BOM) is a structured document that systematically outlines the components, sub-components, and raw materials required to construct a complex product. It presents a hierarchical representation of the assembly process, illustrating how various parts come together to form the final product. This type of BOM extends beyond the primary components to include sub-assemblies, their constituents, and the connections that bind them.
B. Components of a multi-level BOM
A Multi-Level BOM consists of several key components:
Parent Components: These are the top-level components that constitute the final product. They can be assemblies, sub-assemblies, or even individual parts.
Sub-Assemblies: These are intermediate components that consist of further sub-components. Sub-assemblies are often pre-assembled units that simplify the manufacturing process.
Sub-Components: These are the individual parts that make up sub-assemblies or assemblies. They are the smallest units listed in the BOM.
Quantities: The BOM includes the quantity of each component required to build the product. This ensures accurate material procurement and production planning.
Descriptions: Descriptive information about each component helps in identifying and sourcing the correct parts.
Part Numbers: Unique identifiers assigned to each component facilitate easy tracking and ordering.
Relationships and Dependencies: Multi-level BOMs showcase how components are connected, revealing the order in which they are assembled.
C. How multi-level BOMs differ from single-level BOMs
Multi-level BOMs differ from single-level BOMs primarily in their depth and complexity:
Single-Level BOM:
- Lists only the primary components required to build a product.
- Does not include sub-assemblies or their components.
- Suitable for simpler products with minimal assembly complexity.
- Primarily used for basic inventory tracking and production planning.
Multi-Level BOM:
- Offers a hierarchical view that includes sub-assemblies and their sub-components.
- Illustrates the complete product structure, including nested assemblies.
- More suitable for complex products with multiple layers of assembly.
- Enables detailed production planning, accurate procurement, and deeper insights into the manufacturing process.
In essence, a Multi-Level BOM provides a comprehensive understanding of a product's architecture, making it an essential tool for managing intricate manufacturing processes, optimizing inventory, and ensuring accurate production planning across all levels of a product's assembly.
Benefits of Multi-Level BOMs in Inventory Management
Multi-Level Bill of Materials (BOMs) offer a range of advantages in inventory management due to their detailed and hierarchical representation of product structures. These benefits significantly impact operational efficiency and enable businesses to make informed decisions:
A. Enhanced visibility into component hierarchy
Multi-Level BOMs provide a clear visual representation of how components, sub-assemblies, and finished products are interconnected. This visibility helps inventory managers understand the entire production process, aiding in identifying critical components, potential bottlenecks, and dependencies.
B. Accurate demand forecasting
With a detailed understanding of component relationships, inventory managers can accurately forecast demand. This minimizes the risk of understocking or overstocking, optimizing inventory levels and ensuring products are available when needed.
C. Efficient order planning and procurement
Multi-Level BOMs enable precise planning of raw material and component procurement. Inventory managers can identify which parts are required for upcoming production runs, streamlining order placement and minimizing lead times.
D. Streamlined production processes
By showcasing the hierarchical structure of assemblies, Multi-Level BOMs assist in organizing production processes. Manufacturers can plan the sequence of assembly, optimize labor allocation, and reduce production time by knowing exactly which components are needed at each stage.
E. Reduction in excess and obsolete inventory
Accurate demand forecasting and production planning based on Multi-Level BOMs lead to reduced excess inventory. This prevents over-purchasing and ensures that only the necessary components are ordered, minimizing the risk of obsolete inventory.
F. Improved cost control and resource allocation
Multi-Level BOMs provide detailed insights into the cost breakdown of products. This enables better cost estimation, allowing businesses to allocate resources more effectively and make informed decisions regarding pricing and profitability.
Incorporating Multi-Level BOMs into inventory management practices offers a holistic approach to supply chain optimization. By harnessing these benefits, businesses can achieve operational excellence, respond more effectively to market fluctuations, and deliver products to customers with precision and efficiency.
Implementing Multi-Level BOMs: Best Practices
Successfully implementing Multi-Level Bill of Materials (BOMs) requires a strategic approach that encompasses various aspects of data management, software integration, communication, and personnel development. Following these best practices can ensure the effective utilization of Multi-Level BOMs in inventory management:
A. Data Accuracy and Consistency: Ensure that the data included in the BOMs is accurate, consistent, and up-to-date. Mistakes in part numbers, quantities, or descriptions can lead to production delays and inventory management challenges. Regularly audit and validate data to maintain integrity.
B. Integration with Inventory Management Software: Integrate Multi-Level BOMs with your inventory management software or Enterprise Resource Planning (ERP) system. This integration ensures real-time synchronization of data, enabling efficient procurement, demand forecasting, and production planning.
C. Regular Updates and Revisions: Products evolve over time due to design changes, component updates, and market demands. Regularly update and revise Multi-Level BOMs to reflect these changes accurately. Ensure that all stakeholders are informed of the updates to avoid discrepancies.
D. Collaboration between Departments: Facilitate collaboration among different departments involved in the product lifecycle, such as design, production, and procurement. Clear communication and well-defined processes ensure that everyone is aligned with the BOM, minimizing misunderstandings and delays.
E. Training and Skill Development for Personnel Involved: Provide training to personnel who work with Multi-Level BOMs. This includes not only those directly involved in design and manufacturing but also inventory managers and procurement teams. Enhancing their understanding of BOMs improves their decision-making and efficiency.
Implementing these best practices helps businesses fully leverage the advantages of Multi-Level BOMs in their inventory management processes. From maintaining accurate data to fostering cross-functional collaboration, these steps contribute to more effective production, optimized inventory levels, and improved overall operational efficiency.
Challenges and Solutions
Implementing Multi-Level Bill of Materials (BOMs) in inventory management comes with its set of challenges. However, these challenges can be effectively addressed with the right strategies and tools in place.
A. Data Complexity and Management:
ERP Systems and Data Centralization: Challenge: Multi-Level BOMs involve a large amount of data that needs to be managed cohesively across departments. Maintaining consistency and ensuring everyone has access to the same accurate data can be challenging.
Solution: Implement an Enterprise Resource Planning (ERP) system that centralizes data. This allows different departments to access, update, and collaborate on the same set of information. A centralized database reduces duplication, improves data accuracy, and enhances collaboration.
Data Validation and Cleansing Tools: Challenge: Inaccurate or incomplete data can lead to errors in production, procurement, and inventory management.
Solution: Utilize data validation and cleansing tools to identify and rectify inconsistencies, duplicates, and errors in the BOM. Regular data audits and validation checks help maintain data accuracy.
B. Coordination among Departments:
Cross-Functional Teams and Communication Protocols: Challenge: Different departments (design, production, procurement) may have varying priorities, leading to miscommunication and misunderstandings regarding BOM requirements.
Solution: Establish cross-functional teams with representatives from each department involved. Implement clear communication protocols and regular meetings to ensure everyone is aligned. Document processes and responsibilities to avoid ambiguity.
C. Changes in Design or Components
Change Management Processes: Challenge: Design changes or component substitutions can lead to confusion and errors if not managed properly. Ensuring that everyone is aware of changes and their implications is crucial.
Solution: Implement a change management process where design changes are documented, reviewed, and communicated across relevant departments. This ensures that all stakeholders are informed and can adapt their processes accordingly.
Version Control for BOMs: Challenge: Multi-Level BOMs are subject to frequent updates, and maintaining version control becomes complex as product designs evolve.
Solution: Implement version control mechanisms for BOMs, ensuring that each iteration is documented, dated, and tracked. This prevents confusion and ensures that the correct BOM version is used in production and procurement.
By addressing these challenges with the suggested solutions, businesses can overcome hurdles related to data management, coordination, and changes in design. Effectively managing these aspects enhances the successful integration of Multi-Level BOMs into inventory management practices, resulting in streamlined operations and optimized supply chain processes.
Real-World Examples
Real-world examples illustrate the practical application and benefits of incorporating Multi-Level Bill of Materials (BOMs) in various industries. Here are three specific scenarios:
A. Automotive Industry: Managing Complex Assemblies In the automotive sector, vehicles are comprised of intricate assemblies and sub-assemblies. Multi-Level BOMs play a crucial role in managing the complexity of components, ranging from the engine to the interior electronics. For instance, when manufacturing a car, a Multi-Level BOM breaks down the engine into its individual components, such as cylinders, pistons, and valves.
Further, it outlines the various sub-assemblies that go into creating the transmission system, suspension, and electronics. This detailed view helps streamline production processes, optimize inventory levels for various parts, and facilitate efficient procurement, ultimately leading to cost savings and high-quality vehicles.
B. Electronics Sector: Navigating Frequent Component Updates In the fast-paced electronics industry, components and technologies evolve rapidly. Multi-Level BOMs are essential in managing these changes. For example, when designing a smartphone, a Multi-Level BOM specifies not only the main components like the screen and battery but also the sub-components that constitute these main parts.
When a new screen technology becomes available, the BOM can be updated to reflect the change, ensuring that the design and procurement teams are aware of the modification. This proactive approach prevents the use of obsolete components and minimizes production bottlenecks caused by last-minute design alterations.
C. Consumer Goods: Ensuring Supply Chain Efficiency Consumer goods, such as clothing, appliances, and packaged food items, rely on efficient supply chains. Multi-Level BOMs aid in ensuring this efficiency. For example, when manufacturing a packaged food product, the BOM details not only the ingredients but also the packaging materials, labels, and other components.
By understanding the relationships between various components, manufacturers can optimize production runs to reduce waste and streamline packaging processes. Furthermore, integrating Multi-Level BOMs with inventory management systems enables accurate demand forecasting and minimizes stockouts, contributing to smooth supply chain operations.
In these real-world scenarios, Multi-Level BOMs prove their value by enhancing product design, production efficiency, inventory management, and supply chain optimization. The use of BOMs in these industries showcases their versatility and impact on operational excellence.
Tools and Technologies
Modern business environments benefit significantly from advanced tools and technologies that streamline operations and enhance decision-making. In the context of Multi-Level Bill of Materials (BOMs) and inventory management, certain tools play a crucial role in optimizing processes and improving overall efficiency.
A. BOM Management Software:
BOM management software is designed to create, manage, and collaborate on Multi-Level BOMs efficiently. These tools offer features such as version control, real-time updates, and integration with other systems like Enterprise Resource Planning (ERP) and Product Lifecycle Management (PLM) software.
BOM management software centralizes BOM data, making it easily accessible to different departments involved in design, production, procurement, and inventory management. Examples of BOM management software include Autodesk Fusion Lifecycle, Arena Solutions, and Siemens Teamcenter.
B. Inventory Tracking and Optimization Tools:
Inventory tracking and optimization tools help businesses monitor their inventory levels, movement, and usage patterns. These tools leverage data analytics to forecast demand, plan procurement, and prevent overstocking or stockouts. They integrate with Multi-Level BOMs to provide a holistic view of the entire supply chain.
Such tools help streamline inventory management, reduce carrying costs, and improve customer satisfaction. Examples include tools like SAP Integrated Business Planning, Oracle Inventory Optimization, and Logility Inventory Optimization.
C. Demand Forecasting and Analytics Platforms:
Demand forecasting and analytics platforms use historical data, market trends, and predictive algorithms to forecast future demand for products. By integrating Multi-Level BOM data, these platforms offer accurate predictions of component requirements, enabling better production planning and inventory management.
Such platforms enhance decision-making, minimize excess inventory, and optimize supply chain operations. Examples include platforms like IBM Planning Analytics, Microsoft Power BI, and SAS Demand Forecasting.
These tools and technologies empower businesses to leverage the potential of Multi-Level BOMs in inventory management. They enhance collaboration, accuracy, and visibility, resulting in improved operational efficiency, cost savings, and the ability to adapt to changing market demands.
Future Trends in Multi-Level BOM and Inventory Management
The landscape of Multi-Level Bill of Materials (BOM) and inventory management is constantly evolving as technology advances and business practices adapt to changing demands. Several future trends are poised to shape how Multi-Level BOMs are utilized in inventory management:
A. Integration with IoT and Real-Time Tracking: As the Internet of Things (IoT) continues to expand, it offers the opportunity to integrate real-time data from connected devices into Multi-Level BOMs. IoT-enabled sensors can provide instant insights into factors such as production progress, inventory levels, and equipment performance.
By integrating IoT data with Multi-Level BOMs, businesses can achieve unparalleled visibility into their supply chain, enabling proactive decision-making, reducing lead times, and optimizing production processes.
B. AI-Driven Demand Forecasting and Decision-Making: Artificial Intelligence (AI) and machine learning are transforming demand forecasting and decision-making in inventory management. By analyzing historical data, market trends, and external factors, AI-driven algorithms can predict demand patterns with greater accuracy. Integrating AI with Multi-Level BOMs enhances production planning, minimizes stockouts, and reduces excess inventory.
AI-powered algorithms can also optimize reorder points and suggest dynamic adjustments to production schedules based on changing market conditions.
C. Sustainable and Eco-Friendly Inventory Practices: With increasing emphasis on sustainability, businesses are shifting towards eco-friendly inventory practices. Multi-Level BOMs can play a vital role in this transition. By providing detailed information about the components used in products, companies can assess the environmental impact of their supply chain.
This information can aid in selecting eco-friendly materials, optimizing transportation routes, and reducing waste. Multi-Level BOMs can also help track the lifecycle of components and products, enabling efficient recycling and disposal practices.
Embracing these trends ensures that Multi-Level BOMs remain at the forefront of inventory management strategies, enabling businesses to stay agile, reduce costs, minimize environmental impact, and deliver products that meet the evolving needs of customers and markets.
Conclusion
In conclusion, Multi-Level Bill of Materials (BOMs) stands as a critical tool in the realm of modern inventory management, offering a structured and comprehensive approach to managing complex production processes and supply chains. The integration of Multi-Level BOMs into inventory management practices presents a wealth of benefits that enhance operational efficiency, reduce costs, and improve overall business performance.
From the automotive industry's intricate assemblies to the electronics sector's rapid component updates and consumer goods' supply chain efficiency, Multi-Level BOMs provide a versatile solution that adapts to various industries and product complexities. The enhanced visibility into component hierarchies, accurate demand forecasting, efficient order planning, streamlined production processes, and reduction in excess inventory collectively contribute to optimized operations and customer satisfaction.
As technology advances, the future of Multi-Level BOMs and inventory management is marked by trends such as integration with IoT and real-time tracking, AI-driven demand forecasting and decision-making, and a focus on sustainable and eco-friendly practices. These trends promise even greater levels of efficiency, adaptability, and responsible resource utilization.
Embracing the challenges and solutions associated with Multi-Level BOMs, leveraging cutting-edge tools and technologies, and aligning with future trends positions businesses to excel in the dynamic landscape of inventory management. By harnessing the power of Multi-Level BOMs, businesses can not only meet the demands of today but also prepare for the challenges and opportunities that lie ahead, ultimately leading to enhanced competitiveness, resilience, and sustainable growth.
How can Deskera Help You?
Deskera ERP and MRP systems help you to keep your business units organized. The system's key features of demand forecasting with Deskera include as follows:
- Establish Demand Forecasting Process
- Automate Data Collection
- Monitor Market Trends
- Analyze Historical Data
- Estimate Future Demand
- Adjust Production Levels
- Manage Supply Chain and much more!
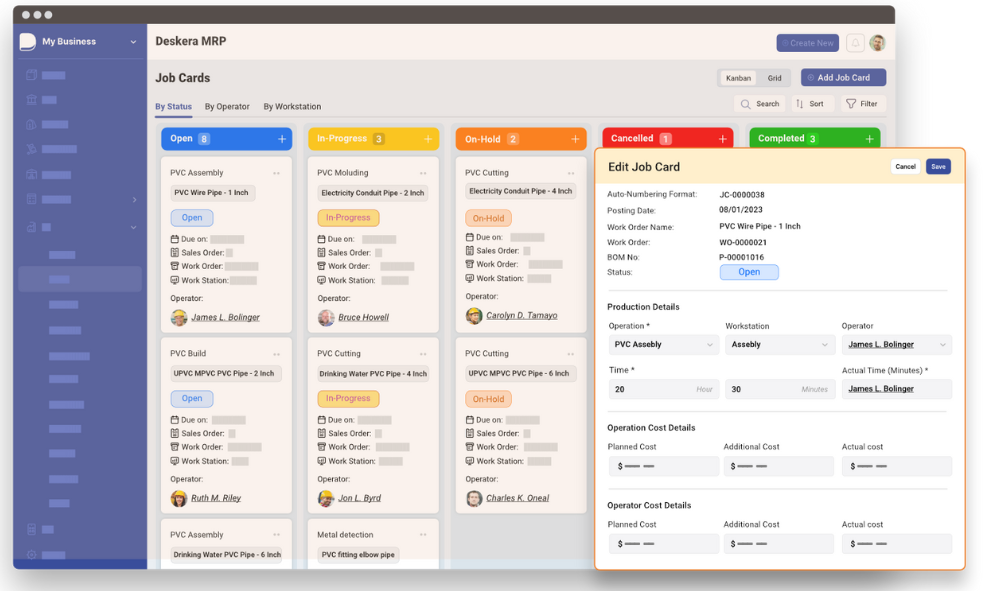
Deskera's integrated financial planning tools enable investors to better plan and track their investments. It can assist investors in making faster and more accurate decisions.
Deskera CRM is a powerful solution that manages your sales and helps you close deals quickly. It not only enables you to perform critical tasks like lead generation via email, but it also gives you a comprehensive view of your sales funnel.
Deskera Books allows you to better manage your accounts and finances. Maintain good accounting practices by automating tasks like billing, invoicing, and payment processing.
Deskera People is a straightforward tool for centralizing your human resource management functions.
Key Takeaways
- Core Inventory Management: Effective inventory management is crucial for balancing customer demand and cost control, and Multi-Level BOMs play a pivotal role in achieving this balance.
- Multi-Level BOM Definition: A Multi-Level BOM outlines the hierarchical structure of components, sub-assemblies, and raw materials needed for product assembly.
- BOM Complexity: Multi-Level BOMs go beyond surface-level components, delving into sub-assemblies and their interdependencies, providing a holistic view of product architecture.
- Advantages of Multi-Level BOMs: Multi-Level BOMs enhance visibility, aid accurate demand forecasting, streamline production planning, optimize resource allocation, and reduce excess inventory.
- Integration Challenges: Challenges include data accuracy, cross-departmental coordination, and managing changes in design or components.
- Data Management Solutions: ERP systems, data validation tools, and centralized databases enhance data accuracy and consistency in Multi-Level BOMs.
- Cross-Functional Coordination: Effective collaboration among departments, facilitated by cross-functional teams and communication protocols, is vital for successful Multi-Level BOM integration.
- Managing Design Changes: Change management processes and version control mechanisms are crucial to adapting Multi-Level BOMs to evolving product designs.
- Future Trends: Integration with IoT for real-time tracking, AI-driven demand forecasting, and eco-friendly inventory practices are shaping the future of Multi-Level BOMs and inventory management.
- Strategic Outlook: Leveraging Multi-Level BOMs, advanced tools, and future trends enhances operational efficiency, competitiveness, and sustainability in inventory management.
These takeaways encapsulate the key insights into how Multi-Level BOMs are transforming inventory management, enabling businesses to navigate complexities and position themselves for success in a rapidly changing business landscape.
Related Articles
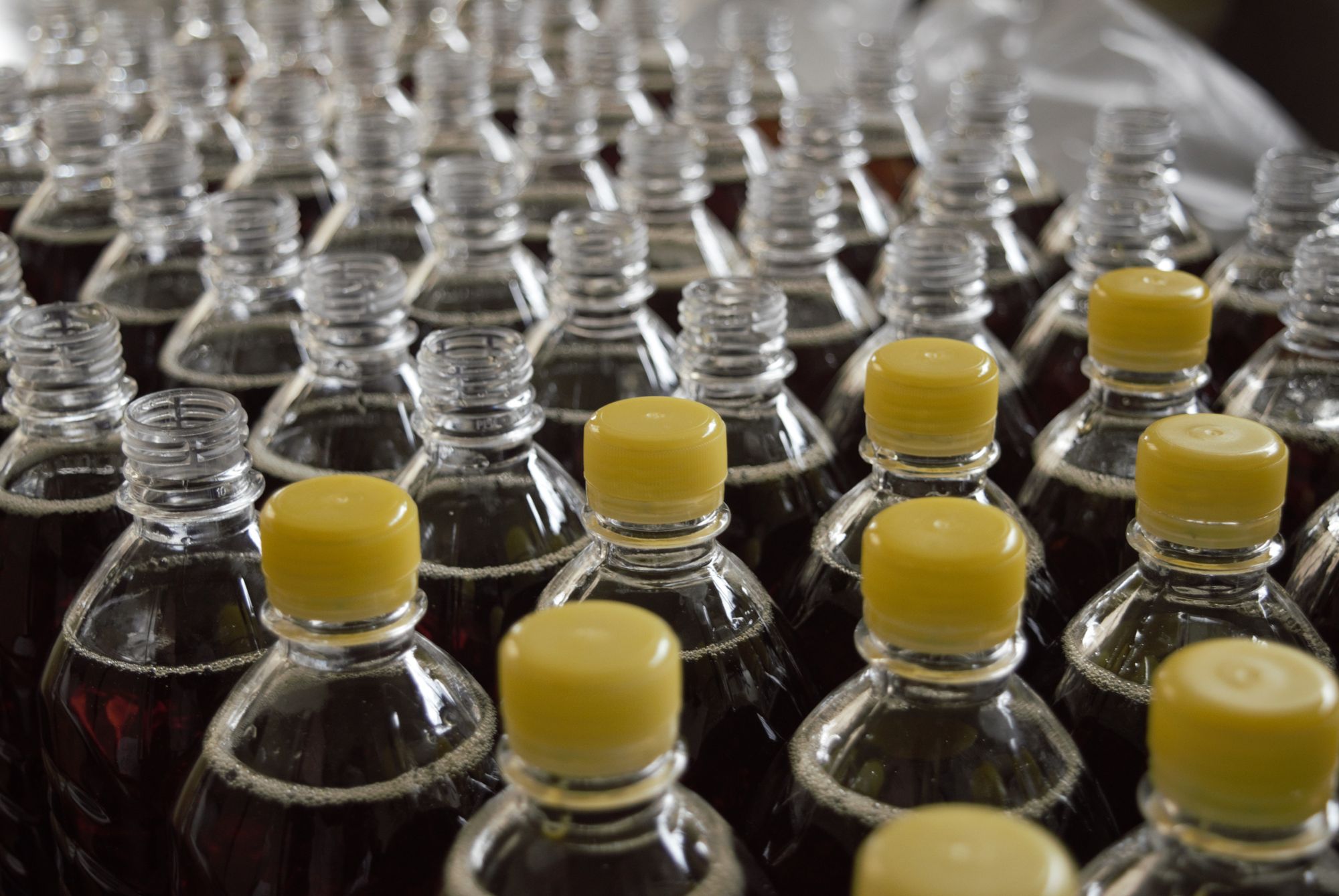
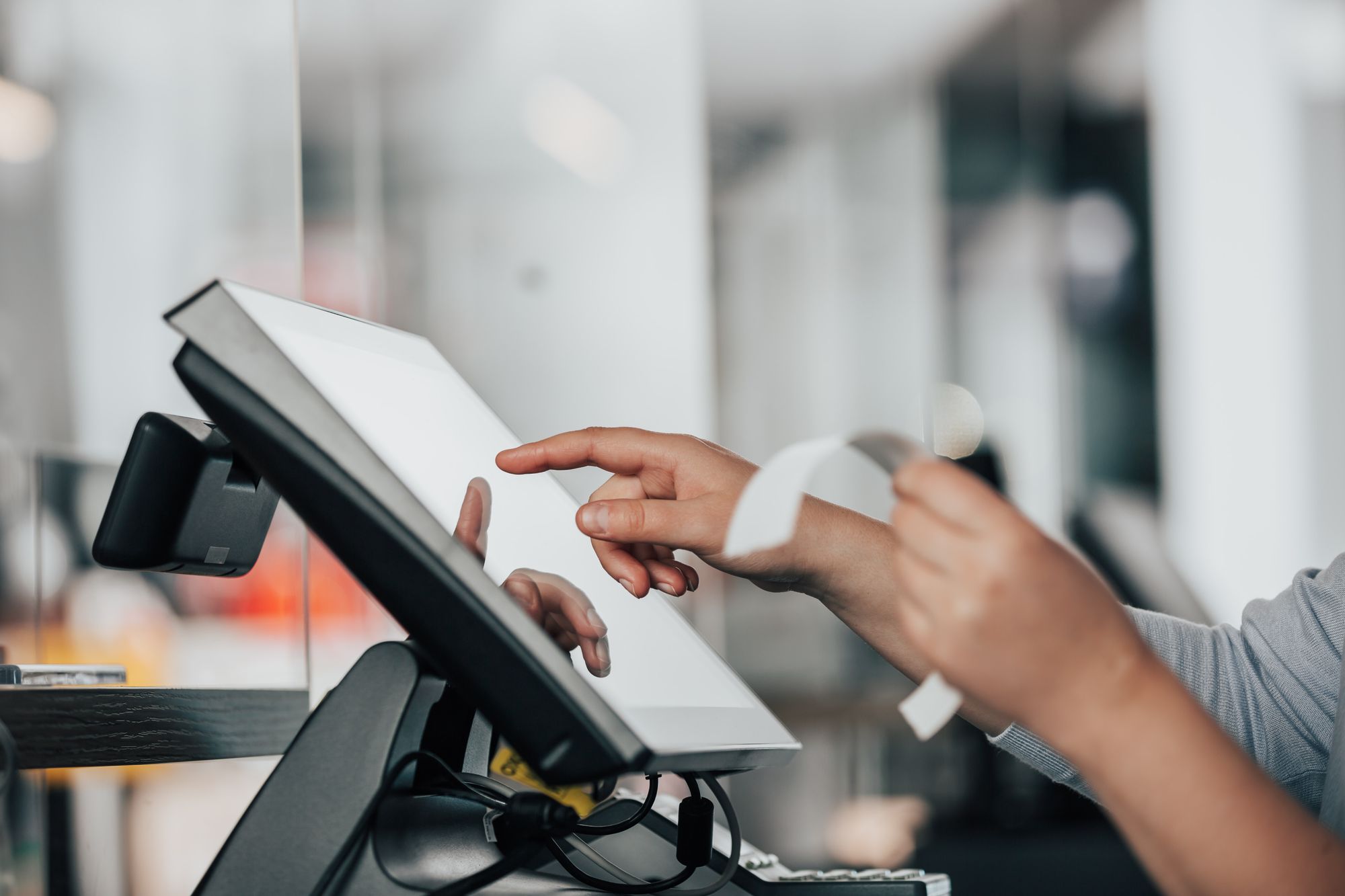
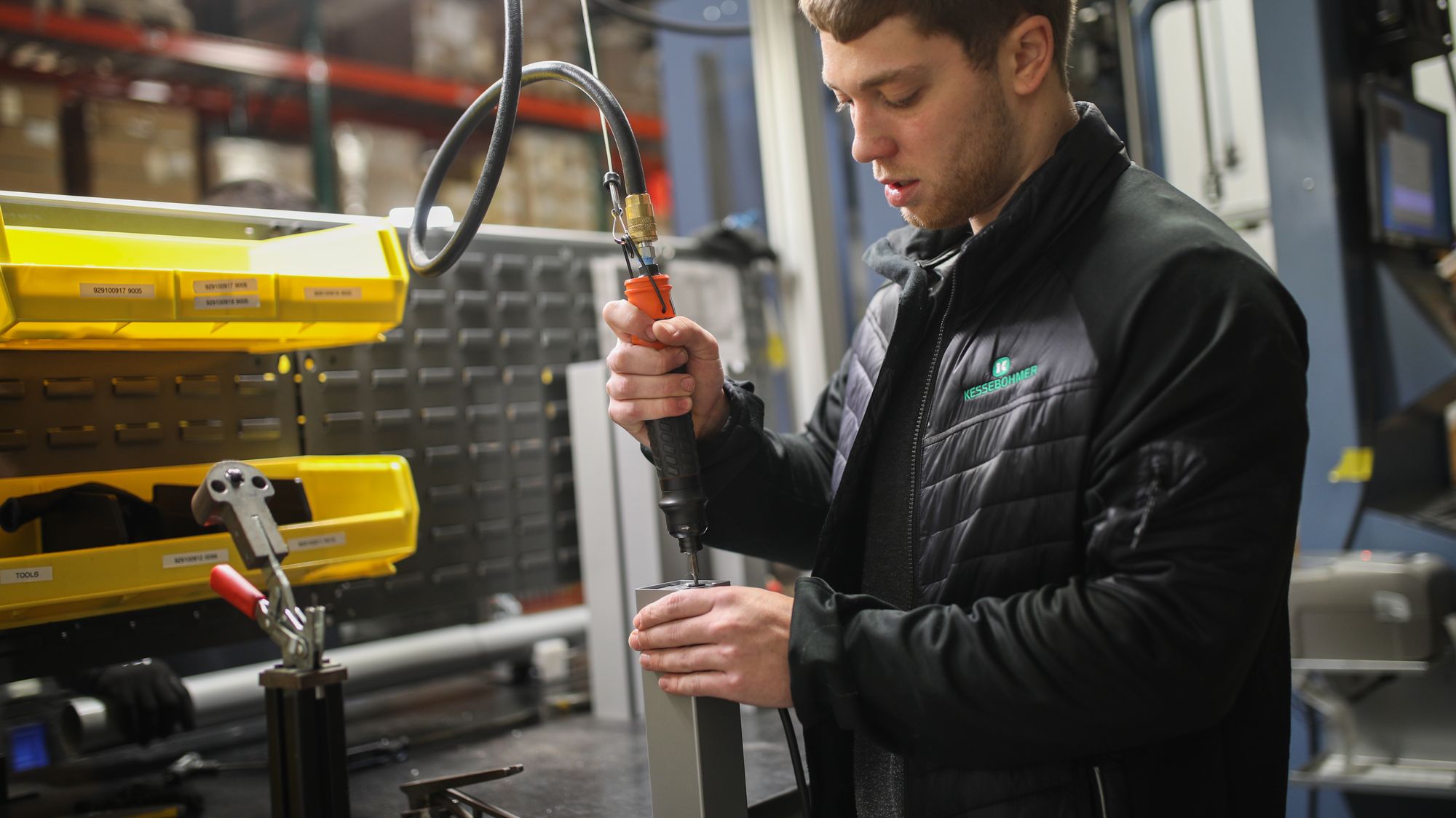
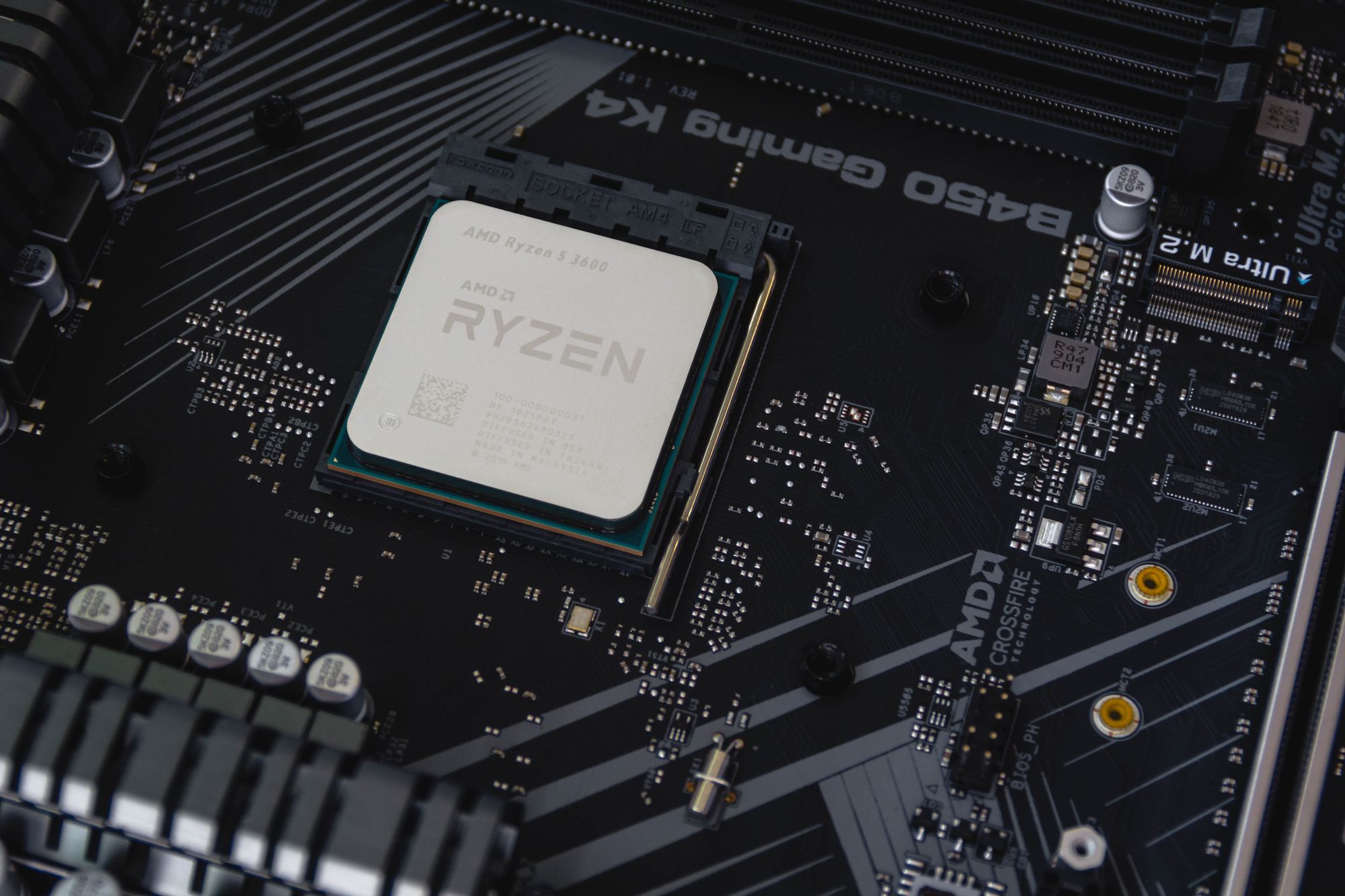
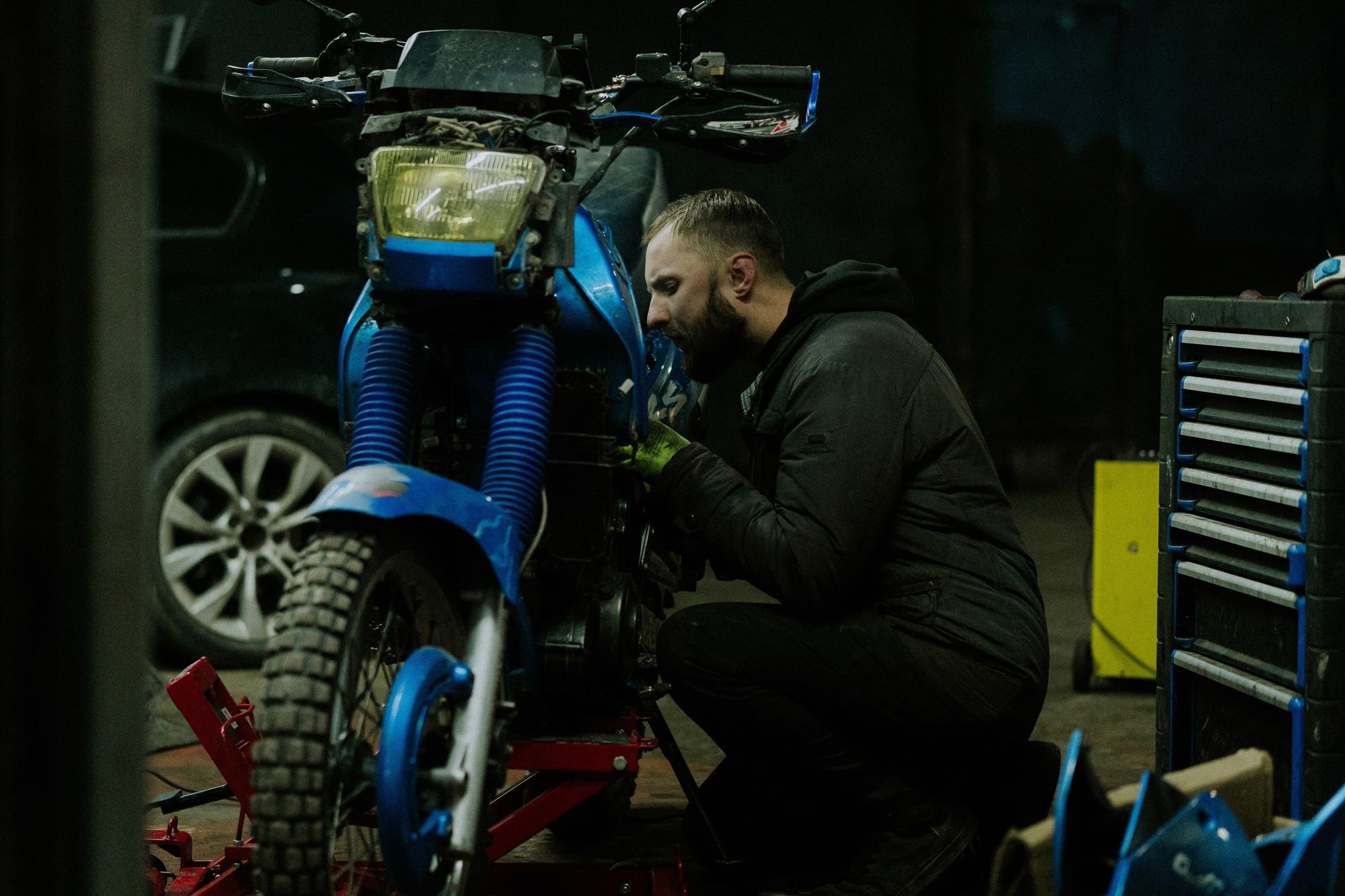