In the United States, supply chain disruptions have become a significant concern for businesses of all sizes. According to a survey by Resilience360, 80% of companies in the US reported supply chain disruptions in 2020, with 33% stating that inventory issues caused the disruptions.
The cost of these disruptions can be significant, with businesses losing an average of $1.75 million annually due to supply chain disruptions. However, by implementing better inventory management practices, companies can minimize the impact of these disruptions and protect their bottom line.
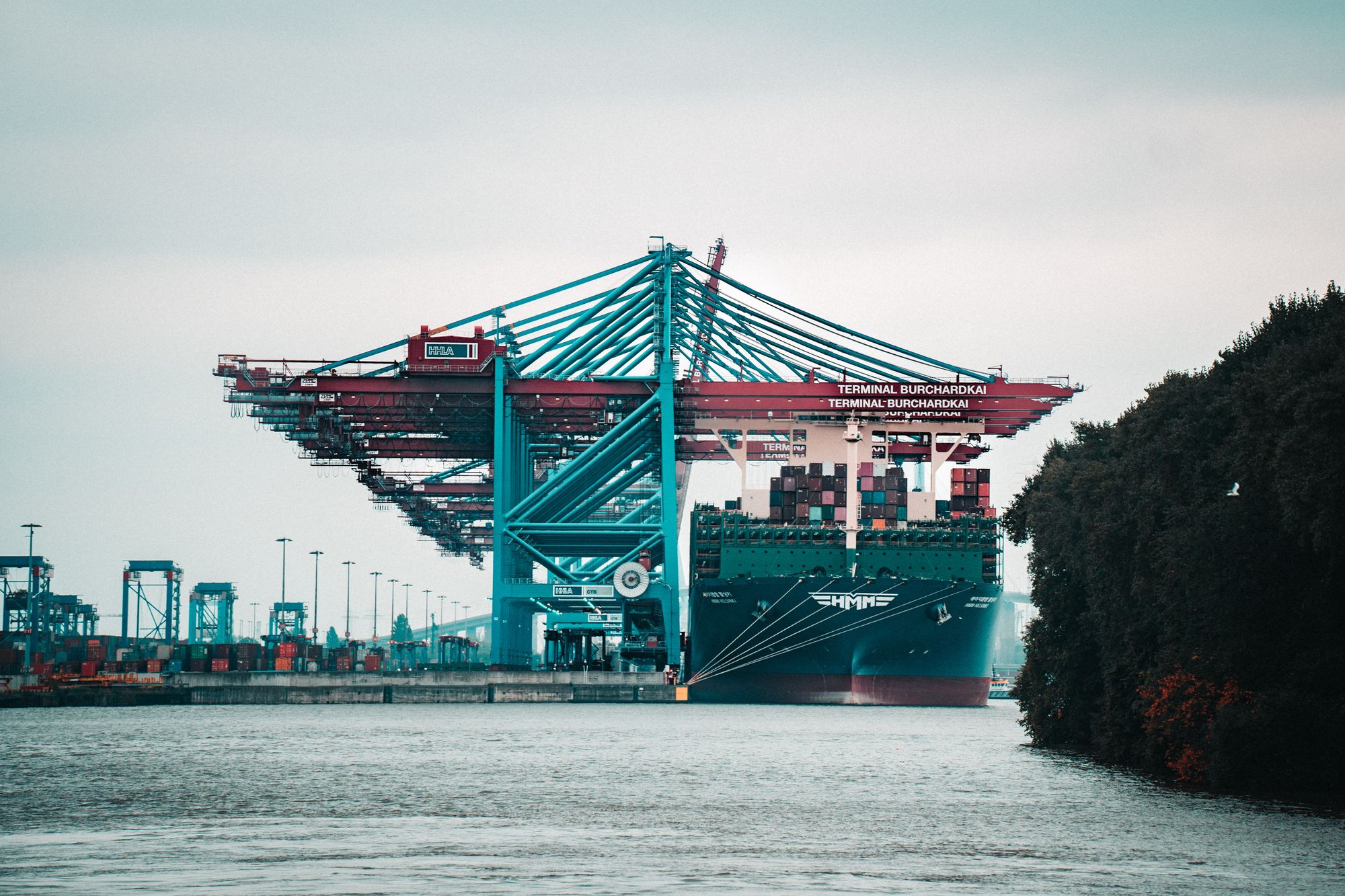
Poor inventory management can disrupt the flow of goods throughout the supply chain, whether it's a shortage of raw materials, manufacturing delays, or an unexpected surge in demand. However, by implementing better inventory management practices, businesses can minimize the impact of these disruptions and protect their bottom line.
In this article, we will explore some effective strategies for improving inventory management and reducing the risk of supply chain disruptions.
Here’s what we shall cover in this post:
- What is a Supply Chain Disruption?
- Causes of Supply Chain Disruption
- 6 Types of Supply Chain Disruptions
- Strategies to Prepare for Supply Chain Disruption
- Steps to Take When A Supply Chain Disruption Has Occurred
- Conclusion
- Key Takeaways
What is a Supply Chain Disruption?
A supply chain disruption is a disruption or interruption in the flow of goods and services that a company relies on to run its business.
- These disruptions can occur at any point in the supply chain, from raw materials to finished goods, and can significantly impact a company's operations and bottom line.
- The effects of a supply chain disruption can be wide-ranging and severe.
- Companies may experience a shortage of raw materials, leading to production delays and lost revenue.
- They may also be unable to meet customer demand for their products, leading to lost sales and damage to their reputation. Supply chain disruptions can sometimes even force a company out of business.
Some common causes of supply chain disruptions include natural disasters, geopolitical conflicts, transportation disruptions, supplier issues, quality problems, and unexpected shifts in demand. It is crucial for businesses to have strategies in place to mitigate and manage supply chain disruptions to ensure continuity and resilience in their operations.
Causes of Supply Chain Disruption
Supply chain disruption is a major issue that can have a significant impact on businesses and consumers alike. It can lead to delays in production, increased costs, and difficulty meeting customer demand.
There are several causes of supply chain disruption, including:
Dependence on a Single Supplier
Dependence on a single supplier can cause significant supply chain disruptions, as companies that rely heavily on a single supplier are vulnerable to disruptions in the supplier's operations. It can result in delays, increased costs, and even complete cessation of production.
- One of the main reasons companies become dependent on a single supplier is the cost-effectiveness of working with one supplier.
- It can be especially true when dealing with raw materials or components unique to the supplier. However, this cost-effectiveness can quickly become a liability if the supplier experiences disruptions in their operations.
- Disruptions in a supplier's operations can come in many forms, such as natural disasters, labor strikes, or bankruptcy.
- These disruptions can cause delays in delivery, increased costs, or even the complete cessation of production. It can have a ripple effect throughout the supply chain, as companies that rely heavily on the supplier's products may also experience disruptions in their operations.
Lack of Adequate Inventory Management
Inadequate inventory management can lead to stockouts, where a product is unavailable for purchase. It can lead to lost sales and unhappy customers. Overstocking can also cause problems, as it ties up valuable resources such as money and warehouse space.
- Poor inventory management can also lead to increased costs. For example, if a company overstocks a product, it may have to pay to store the excess inventory.
- Similarly, if a company understocks on a product, they may have to pay rush shipping fees to quickly restock the item.
- There are several steps that companies can take to improve their inventory management. One crucial step is to review and update their inventory levels regularly. It can help to ensure that the right products are in stock at the right time.
Natural Disasters
Natural disasters can majorly impact supply chain management and cause significant disruptions. Various factors, such as damage to transportation infrastructure, power outages, and shortages of raw materials, can cause these disruptions.
- One of the most common ways natural disasters can disrupt the supply chain is by damaging transportation infrastructure.
- Floods, storms, and earthquakes can damage roads, bridges, and ports, making it difficult or impossible for goods to be transported.
- It can lead to delays and increased costs, as companies may have to find alternate routes or use more expensive modes of transportation.
Political Instability
Political instability can significantly impact supply chain management and cause disruptions in the flow of goods and services. This instability can come in the form of trade disputes, sanctions, and tariffs, disrupting the flow of goods across borders and causing delays and increased costs.
Trade disputes between countries can cause disruptions in the supply chain. For example, if two countries have a conflict and one country imposes tariffs on goods from the other country, it can make those goods more expensive and less attractive to buyers. It can cause a decline in demand and lead to disruptions in the supply chain.
Cybersecurity Breaches
Cyberattacks and data breaches can compromise supply chain information systems, disrupt operations, compromise sensitive data, and impact communication and coordination within the supply chain network.
Pandemics
Pandemics, such as COVID-19, can significantly impact supply chain management and cause disruptions in the flow of goods and services. Various factors, including shortages of goods, delays in transportation, and disruptions in manufacturing and production, can cause it.
One of the most common ways that pandemics can disrupt the supply chain is by causing shortages of goods. It can happen when suppliers are unable to produce or transport goods due to lockdowns, quarantines, or other measures to slow the spread of the virus. It can lead to delays and increased costs for companies that rely on those goods.
Demand Volatility
Rapid changes in customer demand, market trends, or consumer preferences can lead to supply chain disruptions. Sudden spikes or drops in demand can result in stockouts or excess inventory, causing disruptions in production and distribution.
6 Types of Supply Chain Disruptions
Supply chain disruptions can take many forms and can have a significant impact on businesses and consumers alike. Understanding the different types of supply chain disruptions can help enterprises to better prepare for and manage these disruptions.
Here are six types of supply chain disruptions:
Production Disruptions
Production disruptions occur when a factory or other production facility is unable to produce goods. Many factors, such as equipment failure, natural disasters, and labor strikes, can cause it.
For example, a fire at a factory can damage equipment and disrupt production, while a strike by workers can shut down a production facility. One of the most common causes of production disruptions is equipment failure. For example, if a machine used in the manufacturing process breaks down, it can cause delays in production and a decrease in output.
Similarly, if a piece of equipment is not maintained correctly, it can also cause disruptions in production. Here are some common types of production disruptions in the supply chain:
Equipment Breakdowns: Breakdowns or malfunctions of machinery and equipment can disrupt production. This includes failures in manufacturing equipment, production lines, or critical components necessary for the production process.
Equipment breakdowns can lead to downtime, delays in production schedules, and potential loss of production capacity.
Material Shortages: Shortages of raw materials or components required for production can cause disruptions. This can result from supplier issues, logistics delays, quality problems, or unexpected increases in demand.
Material shortages can lead to production delays, reduced output, and potential customer dissatisfaction.
Quality Issues: Quality problems during production can result in disruptions. This includes defects, errors, or inconsistencies in the manufacturing process that require rework, scrap, or additional quality control measures.
Quality issues can lead to production slowdowns, increased costs, and potential product recalls.
Labor Shortages or Strikes: Insufficient labor availability or labor strikes can disrupt production. Labor shortages can occur due to factors such as attrition, skill gaps, or changes in labor market conditions.
Strikes or labor disputes can result in work stoppages, production delays, and disruptions in meeting customer demand.
Production Line Bottlenecks: Bottlenecks or inefficiencies in the production line can lead to disruptions. This can occur when certain stages or processes in the production line cannot keep up with the demand, causing a slowdown in overall production.
Bottlenecks can result from imbalances in workloads, inadequate capacity, or suboptimal workflow design.
Power or Utility Outages: Power outages or interruptions in utilities such as electricity, water, or gas can halt production activities.
Without access to essential resources, manufacturing operations may come to a standstill, leading to significant disruptions and financial losses.
Logistics Disruptions
Logistics disruptions in the supply chain can occur for various reasons, such as natural disasters, transportation strikes, and pandemics. These disruptions can significantly impact businesses and consumers, as they can cause delays and shortages in the delivery of goods.
One of the most common logistics disruptions is a delay in transportation. It can happen due to various factors, such as poor weather conditions, road closures, or a shortage of truck drivers. Transportation delays can cause a ripple effect throughout the supply chain, leading to delays in delivering goods to customers.
Here are some common types of logistics disruptions in the supply chain:
Transportation Delays: Delays in transportation can occur due to various factors such as traffic congestion, adverse weather conditions, accidents, or mechanical breakdowns.
These delays can result in late deliveries, disruptions in production schedules, and increased lead times.
Carrier Issues: Problems with carriers, such as capacity constraints, labor shortages, or strikes, can cause disruptions in the supply chain.
Inadequate carrier availability can lead to difficulties in securing transportation services, delays in delivery, and increased shipping costs.
Customs and Compliance Delays: Delays in customs clearance and compliance processes can disrupt the movement of goods across borders.
Changes in regulations, inspections, or documentation requirements can lead to extended lead times, increased administrative burdens, and potential penalties.
Warehousing and Storage Challenges: Capacity constraints, inefficient storage layouts, or improper inventory management can create disruptions in the supply chain.
Limited warehouse space, disorganized inventory, or stockouts can affect order fulfillment, lead to delays in product availability, and impact customer satisfaction.
Packaging and Handling Issues: Inadequate packaging, mishandling of goods, or improper labeling can lead to logistics disruptions. Damaged products, loss of goods, or errors in shipment handling can result in additional costs, delays, and customer complaints.
Information and Communication Gaps: Lack of real-time visibility and communication within the logistics network can cause disruptions.
Inaccurate or incomplete information about shipment status, inventory levels, or order updates can lead to miscoordination, delays in decision-making, and inefficiencies in logistics operations.
Inventory Disruptions
Inventory disruptions in the supply chain can occur for various reasons, such as natural disasters, manufacturing delays, and increased demand for a product. These disruptions can significantly impact businesses and consumers, as they can cause delays and shortages in the delivery of goods.
One of the most common types of inventory disruptions is a shortage of raw materials. It can happen due to various factors, such as supply chain disruptions, natural disasters, or increased demand for a product.
When there is a shortage of raw materials, it can lead to delays in the manufacturing process and can also cause businesses to lose sales. Here are some common types of inventory disruptions in the supply chain:
Stockouts: Stockouts occur when there is insufficient inventory to fulfill customer orders or meet production requirements. This can result from inaccurate demand forecasting, delays in replenishment, production disruptions, or unexpected increases in customer demand.
Stockouts can lead to lost sales, dissatisfied customers, and potential damage to the company's reputation.
Excess Inventory: Excess inventory occurs when there is an accumulation of inventory beyond the required levels. This can result from overproduction, inaccurate demand forecasting, or changes in customer preferences.
Excess inventory ties up working capital, increases holding costs and poses a risk of obsolescence or spoilage.
Inaccurate Inventory Records: Inaccurate inventory records occur when there are discrepancies between the actual inventory levels and the recorded inventory data. This can be caused by errors in data entry, improper tracking, theft, or poor inventory management practices.
Inaccurate inventory records can lead to misjudgments in demand planning, incorrect order fulfillment, and inefficient inventory replenishment.
Supply Chain Disruptions: Disruptions in the supply chain, such as delays in raw material delivery, supplier issues, or transportation disruptions, can impact inventory availability.
These disruptions can lead to inventory shortages, production delays, and challenges in meeting customer demands.
Shelf-Life Expirations: Certain products, especially perishable goods or those with limited shelf life, can face inventory disruptions due to expiration or obsolescence.
Inadequate inventory rotation, poor visibility of expiration dates, or inaccurate demand forecasting can result in inventory write-offs and financial losses.
Counterfeit or Damaged Inventory: Counterfeit or damaged inventory can disrupt the supply chain and pose risks to product quality and customer satisfaction. Counterfeit products can lead to legal and reputational issues, while damaged inventory may require rework or disposal.
Customs and Border Disruptions
Customs and border disruptions occur when goods are unable to be imported or exported due to issues with customs or border regulations. A wide range of factors, such as political instability, increased security measures, and changes in trade agreements, can cause it.
For example, if a country experiences a revolution, it can lead to the shutdown of ports and make it difficult to import or export goods. Here are some common types of customs and border disruptions in the supply chain:
Customs Inspections and Documentation: Customs inspections involve the examination of shipments to ensure compliance with import/export regulations, tax requirements, and safety standards.
Delays can occur if shipments are selected for inspection, resulting in additional time spent at customs checkpoints. Incomplete or inaccurate documentation can also lead to delays and potential penalties.
Trade Policy Changes: Changes in trade policies, tariffs, or customs regulations can disrupt the flow of goods across borders. This includes the introduction of new trade agreements, trade barriers, or the imposition of additional duties.
Such changes may require businesses to adjust their import/export procedures, leading to delays, increased costs, and potential disruptions in supply chain operations.
Non-Compliance Issues: Non-compliance with customs regulations, such as incorrect declarations, undeclared goods, or improper classification of products, can lead to customs disruptions.
Non-compliance can result in penalties, fines, or even shipment confiscation. Ensuring compliance with customs regulations is essential to maintaining smooth cross-border operations.
Trade Disputes and Embargoes: Trade disputes or embargoes between countries can lead to customs and border disruptions. These disputes may result in restrictions, bans, or additional scrutiny on certain goods, impacting the flow of imports and exports.
Businesses operating in affected industries may experience delays, increased costs, and changes in supply chain dynamics.
Security Measures: Heightened security measures at borders, such as increased inspections, cargo scanning, or security checks, can cause delays in the supply chain. These measures are often implemented to ensure the safety and security of goods and prevent illegal activities.
While necessary, they can impact the timely movement of goods across borders.
Customs Brokerage and Clearing Agent Issues: Customs brokers and clearing agents play a crucial role in facilitating smooth customs clearance. However, disruptions or delays caused by the inefficiency or non-compliance of these intermediaries can affect the supply chain.
It is essential to work with reliable and experienced customs brokers to minimize the risk of customs disruptions.
Cybersecurity Disruptions
Cybersecurity disruptions occur when a company's IT systems are compromised, leading to disruptions in the flow of information and delays in production and logistics. A wide range of factors, such as cyberattacks, data breaches, and system failures, can cause it.
For example, a ransomware attack can lock a company out of its systems until a ransom is paid, which can cause significant delays in the supply chain. Here are some common types of cybersecurity disruptions in the supply chain:
Data Breaches: Data breaches occur when unauthorized individuals gain access to sensitive data, such as customer information, intellectual property, or financial records.
These breaches can result from hacking, phishing attacks, malware infections, or insider threats. Data breaches can lead to financial losses, legal liabilities, and damage to customer trust.
Ransomware Attacks: Ransomware attacks involve malicious software that encrypts data and demands a ransom payment in exchange for its release.
If a ransomware attack affects critical systems or data within the supply chain, it can disrupt operations, cause financial harm, and compromise sensitive information.
Vendor and Third-Party Risks: Supply chains often involve numerous vendors and third-party service providers. Cybersecurity disruptions can occur through vulnerabilities in their systems, inadequate security measures, or insider threats.
An attack on a vendor or third-party can impact the supply chain by compromising shared systems, data exchanges, or introducing malware into the network.
Phishing and Social Engineering: Phishing attacks involve deceptive emails or messages that trick individuals into revealing sensitive information or granting unauthorized access.
Social engineering tactics manipulate individuals to divulge confidential data or perform actions that compromise security. These attacks can lead to unauthorized access to supply chain systems, compromising data integrity and operational stability.
Malware and Viruses: Malware and viruses are malicious software programs that can infect supply chain systems and compromise data security. They can disrupt operations, steal information, or gain unauthorized access.
Malware can enter the supply chain through infected files, compromised websites, or external devices.
Insider Threats: Insider threats refer to individuals within the organization who misuse their access privileges to compromise security.
This can include employees, contractors, or partners with authorized access to supply chain systems. Insider threats can involve data theft, sabotage, or unintentional actions that lead to cybersecurity breaches.
To mitigate cybersecurity disruptions in the supply chain, businesses can implement strategies such as:
- Implementing robust cybersecurity measures, including firewalls, encryption, and multi-factor authentication.
- Conducting regular vulnerability assessments and penetration testing to identify and address weaknesses.
- Educating employees about cybersecurity best practices, such as recognizing phishing emails and practicing strong password hygiene.
- Establishing clear security protocols and access controls for vendors and third-party partners.
- Monitoring network traffic and implementing intrusion detection systems to detect and respond to potential threats.
- Maintaining up-to-date software and patching systems regularly to address known vulnerabilities.
- Developing and regularly updating an incident response plan to effectively manage and mitigate the impact of cyber incidents.
Human-induced Disruptions
Human-induced disruptions are caused by various reasons, such as strikes, protests, and riots. These disruptions can cause significant delays in the movement of goods and services and disrupt the normal functioning of businesses.
For example, strikes by workers at a port can disrupt the movement of goods, while riots can cause damage to infrastructure and disrupt transportation. To mitigate human-induced disruptions in the supply chain, businesses can implement strategies such as:
- Implementing robust training and education programs to enhance employee skills and knowledge.
- Establishing clear standard operating procedures and quality control processes to minimize errors and improve efficiency.
- Promoting a culture of accountability, responsibility, and continuous improvement within the organization.
- Conducting regular audits and inspections to ensure compliance with regulations and standards.
- Implementing security measures, such as access controls, surveillance systems, and cybersecurity protocols, to safeguard the supply chain against breaches and theft.
- Developing strong relationships and communication channels with labor unions and workers to address potential labor issues and disputes.
- Regularly reviewing and updating supply chain processes to identify and address vulnerabilities and inefficiencies.
Strategies to Prepare for Supply Chain Disruption
Supply chain disruption can be a significant business issue, leading to delays, increased costs, and lost revenue. However, there are ways to prepare for and mitigate the effects of supply chain disruption through better inventory management.
Here are some strategies to consider:
Diversify Your Suppliers
Having multiple suppliers for the same product or service ensures that if one supplier experiences a disruption, you have a backup option to turn to. It can also help you negotiate better prices and terms with your suppliers.
Keep Safety Stock on Hand
Safety stock is a buffer of extra inventory you keep on hand to prepare for unexpected demand or supply chain disruptions. It can help you avoid stockouts and keep your operations running smoothly during a disruption.
Use Inventory Forecasting Techniques
Inventory forecasting techniques, such as statistical forecasting or demand-driven forecasting, can help you predict future demand for your products and services. It can help you ensure that you have the proper inventory to meet customer demand and avoid stockouts.
Implement a Just-In-Time Inventory Management System
Just-in-time inventory management is a system where you only order as needed rather than keeping large amounts of inventory on hand.
It can help you save money on inventory storage costs, but it requires careful planning and coordination with your suppliers to ensure that you always have the necessary inventory.
Consider Using Third-Party Logistics Providers
Third-party logistics providers can handle the logistics and transportation of your inventory, which can help you avoid disruptions in your supply chain. They can also help you manage your inventory more effectively and efficiently, saving you money and improving your bottom line.
Create a Crisis Management Plan
Having a crisis management plan in place can help you respond quickly and effectively to a supply chain disruption.
The plan should outline the steps you will take to minimize the effects of the disruption, such as identifying alternative suppliers or implementing a contingency plan to keep your operations running.
Steps to Take When A Supply Chain Disruption Has Occurred
Here are some steps to take when a supply chain disruption has occurred:
- Assess the situation: The first step is to assess the situation and understand the extent of the disruption. It includes identifying which parts of the supply chain are affected, how long the disruption is likely to last, and the potential impact on the business.
- Communicate with suppliers: It is essential to communicate with suppliers to understand their situation and any potential delays. It will allow you to plan for alternative suppliers or sources of materials, if necessary.
- Review inventory levels: Reviewing inventory levels can help you determine which products or materials are running low and which are in high demand. It will help you prioritize which products or materials need to be sourced first.
- Look for alternative suppliers: If a supplier is unable to meet demand, it is crucial to look for alternative suppliers who can provide the necessary materials or products. It may involve finding new suppliers or reaching out to existing suppliers with excess capacity.
- Evaluate logistics options: Evaluating logistics options can help you find ways to get products to customers on time, even if the supply chain is disrupted. It may involve using different transportation methods or finding alternative routes to get products to customers.
- Review contracts and insurance: Reviewing contracts and insurance can help you understand your rights and obligations in the event of a supply chain disruption. It includes understanding the compensation available if a supplier cannot meet their obligations.
- Monitor the situation: It is essential to continue monitoring the situation and make adjustments as necessary. It may include adjusting production schedules, sourcing new suppliers, or finding new logistics options.
- Communicate with customers: It is vital to keep them informed of any potential delays or disruptions and manage their expectations.
- Be prepared: Businesses should always have a plan in place in case of a supply chain disruption, including identifying critical suppliers and alternative sources of materials and having emergency protocols.
By following these steps, businesses can mitigate the effects of a supply chain disruption and minimize the impact on their operations. It is crucial to be prepared and plan before a disruption occurs to respond quickly and effectively.
Optimizing Supply Chain Management for the Future
Supply chain management is the process of planning, implementing, and controlling the flow of goods, services, and information from suppliers to customers. As the business environment continues to evolve, companies need to optimize their supply chain management for the future.
Here are some ways to do that:
- Embrace technology: Technology can play a critical role in optimizing supply chain management. It includes using software tools for inventory management, logistics, and forecasting. It also includes utilizing technologies like IoT, blockchain, and AI for improved visibility, traceability, and automation across the supply chain.
- Foster collaboration: Collaboration is critical to optimizing supply chain management. It includes working closely with suppliers, partners, and customers to create a more efficient and effective supply chain. Collaboration can also be achieved through shared platforms, data sharing, and partnerships.
- Prioritize sustainability: Sustainability is becoming increasingly crucial for businesses of all sizes. It includes reducing the environmental impact of the supply chain, using sustainable materials, and supporting ethical business practices. By prioritizing sustainability, companies can improve their reputation and customer loyalty, as well as lower costs.
- Adopt a flexible approach: The ability to adapt and respond quickly to changes in the business environment is crucial for future-proofing supply chain management. It includes having a flexible supply chain that can quickly adapt to changing customer demand and a risk management plan to respond to unexpected disruptions.
- Develop a talent strategy: As the supply chain industry continues to evolve, it's crucial to develop a talent strategy that focuses on recruiting, developing, and retaining a skilled workforce that can meet future demands. It includes investing in training and professional development and creating a culture of continuous learning.
- Leverage data and analytics: Data and analytics can play a crucial role in optimizing supply chain management. This includes using data to track performance, identify trends, and make data-driven decisions. It also includes using analytics to forecast demand, optimize logistics, and improve inventory management.
- Optimize logistics: Optimizing logistics can improve the efficiency and effectiveness of the supply chain. This includes using technology to track and manage transportation and data analytics to optimize routes and reduce transportation costs. It also includes using logistics service providers to manage transportation, warehousing, and distribution.
- Continuously improve: Continuously monitoring and improving the supply chain is crucial for future-proofing it. This includes regularly reviewing performance, identifying areas for improvement, and implementing changes to optimize the supply chain.
By embracing technology, fostering collaboration, prioritizing sustainability, adopting a flexible approach, developing a talent strategy, leveraging data and analytics, optimizing logistics, and continuously improving, companies can optimize their supply chain management for the future and remain competitive in the marketplace.
How Deskera Can Assist You?
Deskera ERP and MRP system can help you:
- Manage production plans
- Maintain Bill of Materials
- Generate detailed reports
- Create a custom dashboard
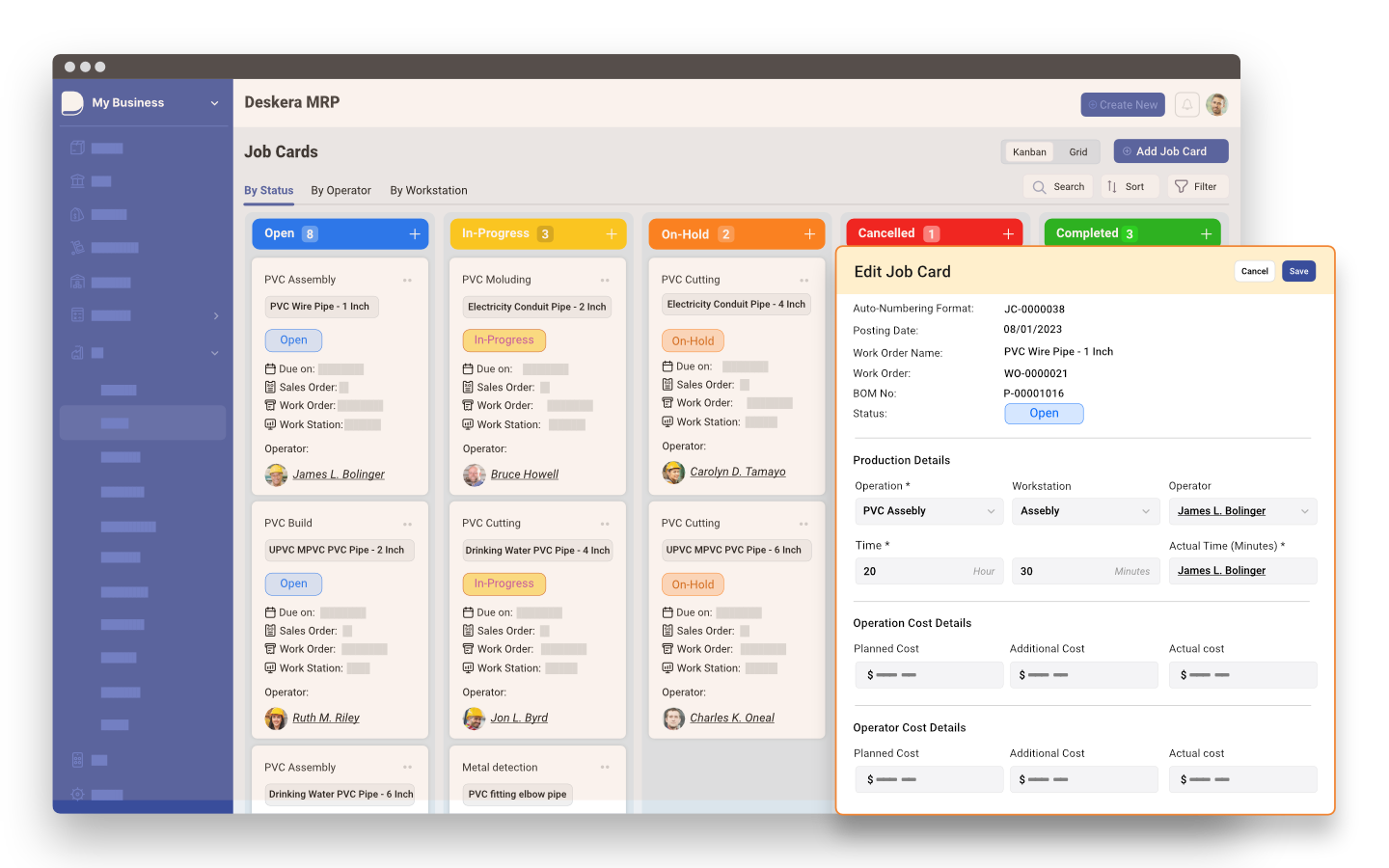
Deskera ERP offers comprehensive inventory management capabilities that empower businesses to efficiently control, track, and optimize their inventory operations. Whether in manufacturing, distribution, retail, or any other industry, Deskera ERP's inventory management features help businesses achieve accurate inventory levels, reduce carrying costs, and enhance supply chain efficiency.
Here's how Deskera ERP can help in inventory management:
- Real-Time Inventory Tracking: Deskera ERP provides real-time visibility into inventory levels across different locations, warehouses, and sales channels. This helps businesses make informed decisions about stock replenishment and allocation.
- Multi-Location Management: For businesses with multiple warehouses or locations, Deskera ERP allows you to track inventory movements, transfers, and stock levels at each location. This ensures accurate inventory management and reduces stockouts or overstocking.
- Stock Reordering: Deskera ERP supports automated stock reordering based on predefined reorder points or minimum stock levels. When inventory reaches a specified threshold, the system can generate purchase orders or replenishment requests.
- Purchase Order Management: The system streamlines purchase order creation, approval, and tracking. It helps in maintaining optimal stock levels by ensuring timely procurement of goods based on demand forecasts.
- Sales Order Integration: Deskera ERP integrates with sales orders, allowing businesses to allocate inventory based on customer orders and prioritize fulfillment based on demand.
Conclusion
Supply chain disruptions can have a significant impact on businesses, leading to delays, increased costs, and lost sales. However, by implementing better inventory management practices, companies can minimize the impact of these disruptions and protect their bottom line.
Some effective strategies for improving inventory management include diversifying the supply chain, building up inventory, and developing a contingency plan.
Additionally, businesses can use technology, such as inventory management software, to track and manage their inventory in real-time, allowing them to identify and respond to disruptions quickly.
By sourcing materials and products from multiple suppliers, businesses can reduce the risk of supply chain disruptions caused by a single supplier. This can also help businesses to negotiate better prices and improve lead times.
Businesses can use technology, such as inventory management software, to track and manage their inventory in real-time. These systems can provide real-time visibility into inventory levels, allowing businesses to identify and respond to disruptions quickly.
By taking these steps, businesses can reduce the risk of supply chain disruptions and ensure the smooth flow of goods throughout the supply chain.
Key Takeaways
- Diversifying the supply chain can reduce the risk of supply chain disruptions caused by a single supplier. By sourcing materials and products from multiple suppliers, businesses can reduce the risk of disruptions and also negotiate better prices and improve lead times.
- It's important to find the balance between having too much or too little inventory, as carrying too much inventory can lead to increased costs and storage challenges, while carrying too little inventory can lead to stockouts and lost sales.
- A contingency plan outlining steps to take in the event of a supply chain disruption can help a business respond quickly and effectively. This plan should include identifying alternative suppliers, increasing production, and other strategies to minimize the impact of disruptions.
- Using inventory management software can help businesses to track and manage their inventory in real-time, providing real-time visibility into inventory levels and allowing companies to identify and respond to disruptions quickly.
- Predictive analytics can help businesses to predict future demand, set reorder points, and forecast inventory needs, which can help them to avoid stockouts and overstocking.
- Implementing a Just in Time (JIT) inventory system can help businesses to minimize the amount of inventory they need to hold and reduce the risk of stockouts and overstocking.
- Utilizing warehouse management systems (WMS) can help businesses to optimize their warehouse operations, by tracking inventory levels, managing stock, and optimizing space utilization.
Related Articles
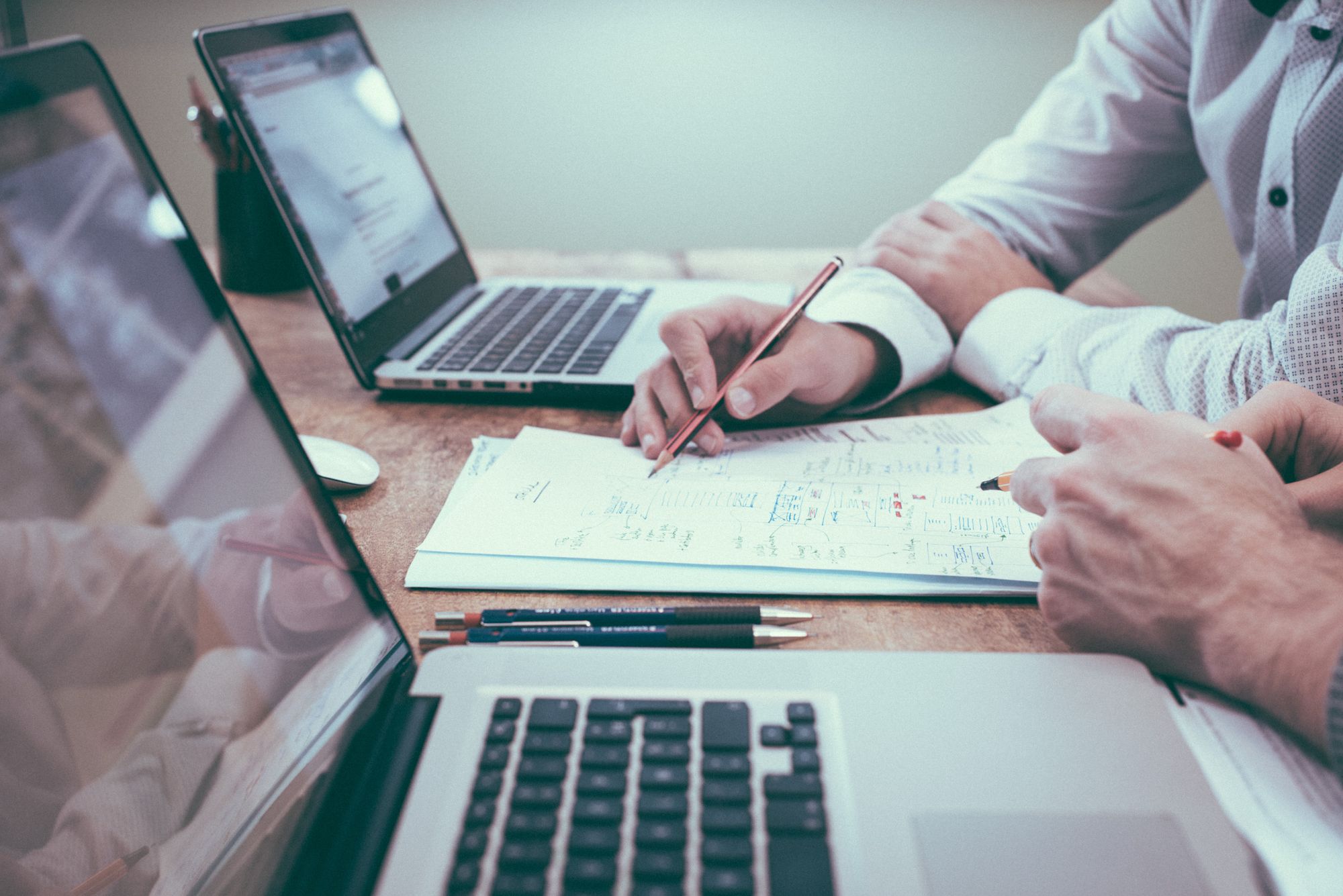
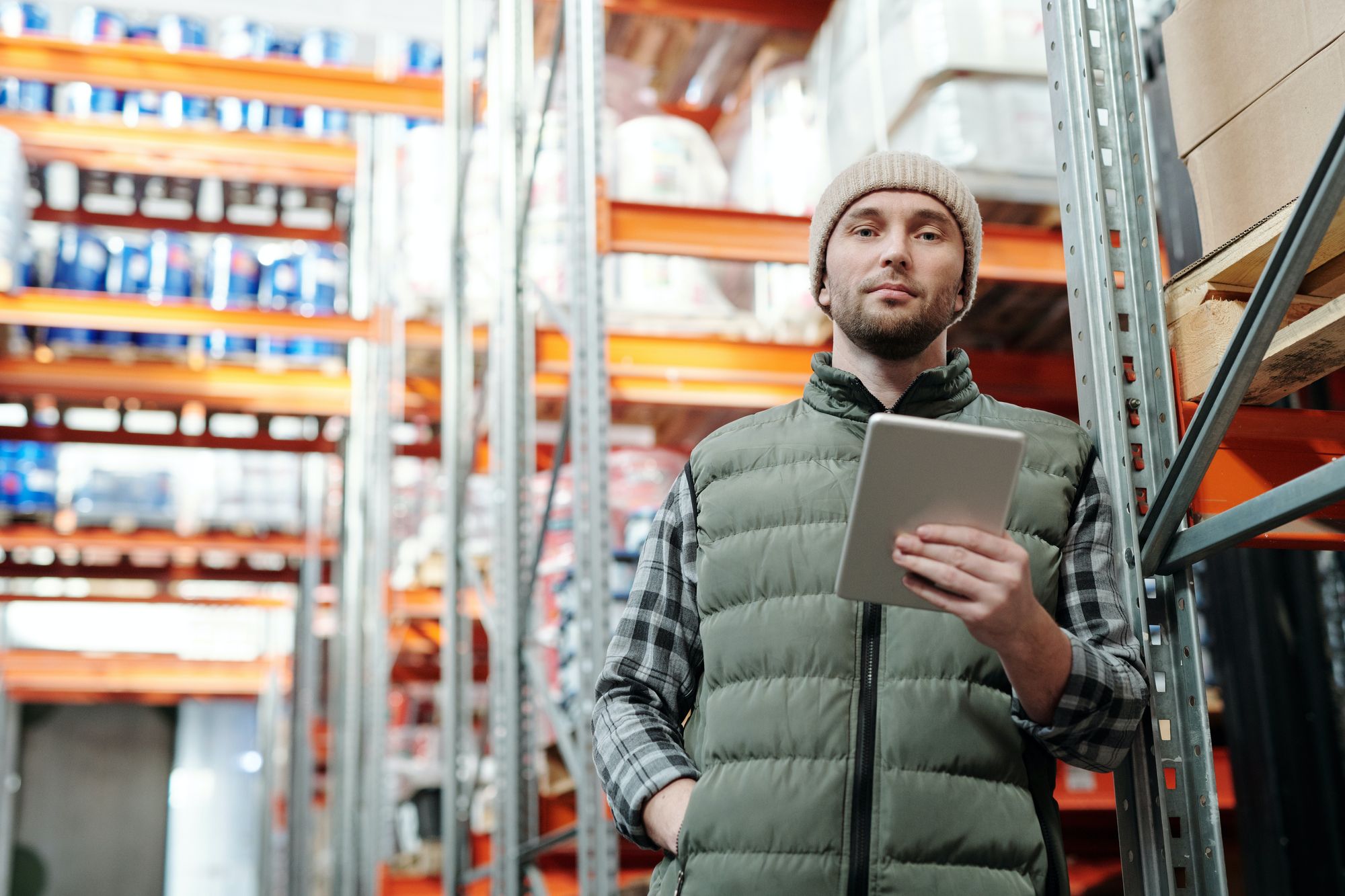
