Model-Based Design (MBD) is a powerful approach to improve the design and optimization of complex systems in various industries, including chemical production.
The chemical industry is facing increasing pressure to improve efficiency, reduce costs, and maintain compliance with regulatory standards, while also meeting the demand for innovative new products.
MBD can help organizations in the chemical industry to achieve these goals by providing a systematic and data-driven approach to design, simulation, and optimization.
This article will provide an in-depth look at MBD in chemical production, including its definition, benefits, limitations, and strategies for implementation. We will also compare MBD with traditional design methods and discuss its future potential in the chemical industry. By the end of this article, readers will have a thorough understanding of MBD and how it can be applied to improve chemical production processes.
Let’s take a look at the table of content before we get started:
- Importance of Chemical Production in Various Industries
- Model-Based Design (MBD) Explained
- Key Principles of Model-Based Design (MBD)
- Working of Model-Based Design
- Comparison of Model-based Design with Traditional Design Methods in Chemical Production
- Benefits of MBD in Chemical Production
- Implementing MBD in Chemical Production
- Challenges and Limitations of MBD in Chemical Production
- Strategies for Overcoming Challenges and Limitations of MBD in Chemical Production
- Future Potential of MBD in Chemical Production
- Wrapping Up
- How Deskera Can Assist You?
Importance of Chemical Production in Various Industries
Chemical production is a vital aspect of many industries, including pharmaceuticals, food and beverage, cosmetics, agriculture, and construction.
Furthermore, chemicals are used to manufacture a wide range of products, from medicines and personal care items to construction materials and food additives. The quality, efficiency, and cost-effectiveness of chemical production are critical factors that determine the success of these industries.
In the pharmaceutical industry, chemical production plays a critical role in the development of new drugs. The production process must be precise and consistent to ensure the safety and efficacy of the final product.
The food and beverage industry relies on chemical production to create additives and preservatives that keep products fresh and safe for consumption. Furthermore, chemicals are also used in the production of fertilizers and pesticides in the agriculture industry, contributing to the production of crops that feed the world's population.
The construction industry uses chemicals to create materials such as concrete, cement, and asphalt. These materials are essential for building infrastructure such as roads, bridges, and buildings. Chemical production is also crucial in the cosmetics industry, where ingredients are carefully formulated and tested to ensure they are safe for human use.
Overall, chemical production plays a vital role in the success and growth of various industries. By implementing advanced design techniques such as Model-Based Design (MBD), companies can improve the efficiency and effectiveness of their chemical production processes, resulting in higher-quality products, reduced costs, and improved competitiveness.
Model-Based Design (MBD) Explained
Model-Based Design (MBD) is an advanced design methodology that involves the creation and use of models to design, simulate, and optimize complex systems. MBD enables engineers to design and test systems virtually, before physical prototypes are built, resulting in improved design quality and reduced development time and costs.
In MBD, models are created using mathematical equations and algorithms that represent the behavior and interactions of the system's components. These models can be used to simulate the system's response to various inputs and conditions, allowing engineers to evaluate and optimize the design before physical prototypes are built.
MBD can be applied to a wide range of systems, including mechanical, electrical, and software systems. In the context of chemical production, MBD can be used to design and optimize chemical processes, equipment, and control systems.
Key Principles of Model-Based Design (MBD)
Following, we’ve discussed the key principles of MBD. Let’s discuss:
Model-Based Design starts with models: The creation of accurate models is the foundation of MBD. Models should accurately represent the system's behavior and interactions and be validated through testing and analysis.
Model-Based Design is iterative: MBD involves a continuous cycle of design, simulation, and optimization, where models are refined and improved with each iteration.
Model-Based Design is collaborative: MBD requires close collaboration between engineers, designers, and other stakeholders, to ensure the accuracy and effectiveness of the models.
Model-Based Design supports automation: MBD can be automated using advanced software tools, allowing engineers to design, simulate, and optimize systems quickly and efficiently.
MBD offers several benefits over traditional design methods, including improved design quality, reduced development time and costs, and increased productivity and efficiency.
By applying MBD in chemical production, companies can improve their design processes, resulting in higher-quality products, reduced costs, and improved competitiveness.
Working of Model-Based Design
In nature, on a test bench, or within an application, a physical system is often described as a group of interconnected and dependent objects or components that perform a single task or a number of diverse tasks.
Model-based design is predicated on the idea that studying a physical system entail applying basic physical laws and engineering principles to the mechanisms that make up the system.
In a physical system simulation environment, a model depicts a specific object or component, indicating that it is an approximation. This implies that, depending on how accurately the real physical component it represents is modelled, a model might have different levels of abstraction.
The characterization of a model's fidelity is based on the simulated objections of the current design phase and the data available to characterize and verify the model, which may include manufacturer datasheets, measurements, and/or calculated parameters from targeted performance criteria.
Model-based design enables a design flow shown by a V-diagram. System components are represented, and the design is simulated using models of the appropriate abstraction for each stage of the process.
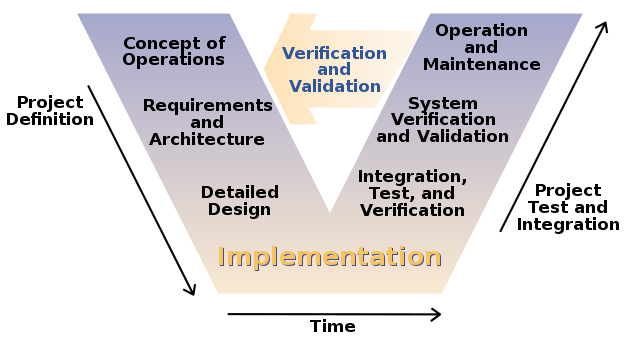
These models, which simulate macro behavior for the study of overarching concepts and conceptual architecture, could initially seem extremely abstract. The models may, however, get more sophisticated when the concept under consideration is finalized during several design phases where more exact questions are being asked, up until the entire system is represented in the models with the necessary accuracy to qualify the design for production.
The implementation and project testing phases of the model-based design flow may be separated to more clearly show how an iterative approach is used to create a reliable model.
Model verification is required before establishing the level of consistency between the observed and simulated behavior. Furthermore, this process of validating that the virtual prototype accurately represents the system model within the predetermined bounds.
Moreover, the degree of agreement between observed and simulated behaviours is a key component of the model validation process after this has been realised and understood. The iterative development process results in an appealing and useful model.
In general, before being incorporated into designs for increasingly complex systems, each model in the system needs to be independently characterized, tested, and validated.
Comparison of Model-based Design with Traditional Design Methods in Chemical Production
In chemical production, Model-Based Design (MBD) offers several advantages over traditional design methods.
Traditional design methods in chemical production often involve trial-and-error experimentation and testing, which can be time-consuming, expensive, and may lead to sub-optimal designs. This is especially true for complex chemical processes, where multiple variables can impact the outcome of the production process.
MBD, on the other hand, allows engineers to create accurate models of the chemical production process, including the behavior and interactions of the system's components. These models can be used to simulate the system's response to various inputs and conditions, enabling engineers to optimize the process without the need for physical prototypes.
Compared to traditional design methods, MBD can significantly reduce the time and cost of the design process. It also allows for a greater degree of design optimization, as engineers can quickly and efficiently test and evaluate a wide range of design scenarios and variations.
Additionally, MBD supports collaboration and automation, enabling teams to work together more efficiently and effectively. Advanced software tools can be used to automate the design process, allowing engineers to focus on the most critical aspects of the design.
Overall, MBD offers significant advantages over traditional design methods in chemical production, resulting in higher-quality products, reduced costs, and improved competitiveness.
Benefits of MBD in Chemical Production
Model-Based Design (MBD) offers several benefits in chemical production, including:
Improved Design Quality:
MBD enables engineers to create accurate and detailed models of the chemical production process, which can be used to simulate the system's behavior and identify potential design flaws or optimization opportunities. By identifying and addressing these issues early in the design process, engineers can improve the overall quality of the final design.
Reduced Development Time and Costs:
MBD allows for a more efficient and streamlined design process, as engineers can quickly and efficiently test and evaluate a wide range of design scenarios and variations without the need for physical prototypes. This can significantly reduce the time and cost of the design process, as well as the risk of errors or design flaws.
Increased Productivity and Efficiency:
MBD supports collaboration and automation, enabling teams to work together more efficiently and effectively. Advanced software tools can be used to automate the design process, allowing engineers to focus on the most critical aspects of the design. This can increase productivity and efficiency, allowing for faster design iterations and faster time-to-market.
Optimization of Chemical Processes:
MBD can be used to optimize chemical processes by simulating the system's response to various inputs and conditions. By evaluating and optimizing the design before physical prototypes are built, engineers can improve the efficiency and effectiveness of the production process, resulting in higher-quality products and reduced costs.
Improved Safety and Environmental Performance:
MBD can be used to simulate the behavior of the chemical production process under different conditions, including potential safety hazards and environmental impacts. This can help engineers identify and address potential safety or environmental issues early in the design process, improving the overall safety and sustainability of the final design.
Reduces Expensive Hardware Iterations:
Designers can test a system's design and optimize the hardware and software implementations before the system is created, or they can do so using already-completed designs to avoid the need for potentially expensive physical prototype iterations.
Enhances Operational Security:
It is suggested by virtual smoke from a virtualized replica of the real system that extended, aggressive testing can be done securely and successfully. This includes the detection of probable embedded software faults that act as sanity checks for intermittent steering stability scenarios in the case of erroneous sensor signals, voltage drops, or other fault events.
Time-to-Market Reduction:
By reducing the time, it takes to market new ideas, the usage of a model-based design approach can be very beneficial. This provides additional, crucial flexibility to meet customer performance requirements.
Warranty Overhead Cost Reduction:
Although while simulation on a nominally specified system is highly beneficial, simulation on a system with components that have assigned tolerances enables priceless statistical investigations and performance evaluations utilising worst-case analysis (WCA).
The number of units that will probably pass the last round of quality assurance testing and ship, as well as the number of units that may ultimately fail in use, may all be predicted by designers in terms of manufacturing yield. WCA simulation data may be used to reduce expensive warranty callbacks.
Overall, MBD offers significant advantages in chemical production, resulting in higher-quality products, reduced costs, increased productivity and efficiency, and improved safety and environmental performance. By adopting MBD in their design processes, companies can improve their competitiveness and remain at the forefront of innovation in the chemical production industry.
Implementing MBD in Chemical Production
Implementing Model-Based Design (MBD) in chemical production involves several steps, including:
Model Development:
The first step in implementing MBD is to develop accurate and detailed models of the chemical production process. These models should include the behavior and interactions of the system's components and be validated through testing and analysis.
Simulation and Optimization:
Once the models are developed, they can be used to simulate the system's response to various inputs and conditions, allowing engineers to evaluate and optimize the design before physical prototypes are built.
This can be done using advanced simulation software, which can quickly and efficiently simulate the chemical production process and provide valuable insights into design performance and optimization opportunities.
Collaboration and Communication:
Implementing MBD requires close collaboration between engineers, designers, and other stakeholders, to ensure the accuracy and effectiveness of the models. Effective communication is also crucial, as it allows for a better understanding of the design requirements and helps to ensure that the final design meets the project goals.
Automation and Integration:
MBD can be automated using advanced software tools, allowing engineers to design, simulate, and optimize systems quickly and efficiently. This can include integrating the MBD process with other design and production software tools, allowing for seamless data transfer and collaboration between different teams and systems.
Testing and Validation:
Once the design is optimized using MBD, it is important to test and validate the final product to ensure that it meets the design requirements and specifications. This can be done using physical prototypes, as well as additional simulations and testing to evaluate the system's performance under real-world conditions.
Overall, implementing MBD in chemical production requires a significant investment in time and resources, but can result in significant benefits, including improved design quality, reduced development time and costs, increased productivity and efficiency, and improved safety and environmental performance. By adopting MBD, companies can improve their competitiveness and remain at the forefront of innovation in the chemical production industry.
Challenges and Limitations of MBD in Chemical Production
While Model-Based Design (MBD) offers many advantages in chemical production, there are also several challenges and limitations that should be considered, including:
Complexity of Models:
The development of accurate and detailed models can be a complex and time-consuming process, requiring significant expertise and resources. As the complexity of the system increases, so too does the complexity of the models, making it challenging to ensure their accuracy and effectiveness.
Integration with Existing Systems:
Integrating MBD with existing production and design systems can be challenging, as it requires significant changes to the design and production processes. This can be time-consuming and may require significant investment in new software and hardware systems.
Data Availability and Quality:
MBD requires accurate and comprehensive data on the behavior and interactions of the system's components. This data may not always be available, and the quality of the data may be variable, making it difficult to develop accurate models and simulations.
Model Validation and Verification:
Models must be validated and verified to ensure their accuracy and effectiveness. This can be challenging, as it requires extensive testing and analysis, and may require physical prototypes or other testing methods.
Cost and Resource Requirements:
Implementing MBD can be costly, requiring significant investment in software, hardware, and personnel resources. This can be challenging for smaller companies or those with limited budgets.
Uncertainty and Variability:
MBD relies on accurate data and assumptions about the behavior and interactions of the system's components. However, there may be uncertainties and variability in the data or the system's behavior, making it challenging to develop accurate models and simulations.
Overall, while MBD offers many advantages in chemical production, there are also several challenges and limitations that must be considered. These challenges highlight the need for careful planning, investment in resources, and ongoing testing and analysis to ensure the accuracy and effectiveness of the models and simulations.
Strategies for Overcoming Challenges and Limitations of MBD in Chemical Production
To overcome the challenges and limitations of Model-Based Design (MBD) in chemical production, several strategies can be employed, including:
Developing Simpler Models:
Developing simpler models that capture the essential features of the chemical production process can help to overcome the challenge of model complexity. Simplifying the models can also make them easier to validate and verify and can help to reduce the amount of data required.
Integrating MBD with existing systems: To overcome the challenge of integrating MBD with existing production and design systems, it is important to involve all stakeholders in the process. This includes personnel from the production, design, and IT departments, as well as external partners and suppliers.
Improving Data Quality and Availability:
To overcome the challenge of data availability and quality, it is important to invest in data collection and analysis tools. This includes developing data acquisition systems that can collect and analyze data in real-time, as well as investing in data analytics tools that can help to identify patterns and trends in the data.
Validating and Verifying Models:
To overcome the challenge of model validation and verification, it is important to invest in testing and analysis tools that can validate the accuracy and effectiveness of the models. This includes using physical prototypes or other testing methods to validate the models and simulate real-world conditions.
Optimizing Resources:
To overcome the challenge of cost and resource requirements, it is important to optimize the use of resources. This includes investing in software and hardware systems that can support MBD, as well as leveraging the expertise of personnel from different departments.
Managing Uncertainty and Variability:
To overcome the challenge of uncertainty and variability, it is important to use statistical analysis tools that can help to identify and quantify the sources of uncertainty and variability. This can help to improve the accuracy of the models and simulations, and can help to identify areas for optimization.
Future Potential of MBD in Chemical Production
The future potential of Model-Based Design (MBD) in chemical production is significant. As the chemical industry continues to evolve and become more complex, MBD can help organizations to improve their design and production processes, and to stay ahead of their competitors. Some of the future potential of MBD in chemical production includes:
Improved Accuracy and Efficiency:
MBD can help organizations to develop more accurate and efficient chemical production processes, by using real-time data and simulations to optimize the behavior and interactions of the system's components.
Reduced Costs and Waste:
By improving the accuracy and efficiency of chemical production processes, MBD can help organizations to reduce their costs and waste, and to improve their bottom line.
Enhanced Safety and Compliance:
MBD can help organizations to improve the safety and compliance of their chemical production processes, by using simulations to identify potential hazards and risks, and to develop effective risk management strategies.
Accelerated Innovation:
MBD can help organizations to accelerate the pace of innovation in chemical production, by allowing them to rapidly develop and test new products and processes, and to bring them to market more quickly.
Enhanced Collaboration:
MBD can help to enhance collaboration between different departments and stakeholders, by providing a common platform for data analysis and communication. This can help to break down silos and improve the flow of information across the organization.
Wrapping Up
In conclusion, Model-Based Design (MBD) has emerged as a powerful approach for improving chemical production processes. By using real-time data and simulations, MBD can help organizations to develop more accurate and efficient chemical production processes, while also reducing costs, waste, and risks. MBD also offers several advantages over traditional design methods, including improved accuracy, efficiency, and collaboration.
However, MBD also has some limitations and challenges that organizations must overcome to realize its full potential. These include challenges related to model complexity, data availability and quality, and model validation and verification.
Nonetheless, by employing strategies such as developing simpler models, integrating MBD with existing systems, and improving data quality and availability, organizations can overcome these challenges and limitations and maximize the benefits of MBD.
Overall, the future potential of MBD in chemical production is significant, and organizations that adopt this approach are likely to benefit from improved accuracy, efficiency, safety, and innovation, as well as enhanced collaboration and communication. Therefore, it is essential for chemical production organizations to adopt MBD in order to stay competitive in today's fast-paced and rapidly evolving industry.
How Deskera Can Assist You?
Deskera's integrated financial planning tools allow investors to better plan their investments and track their progress. It can help investors make decisions faster and more accurately.
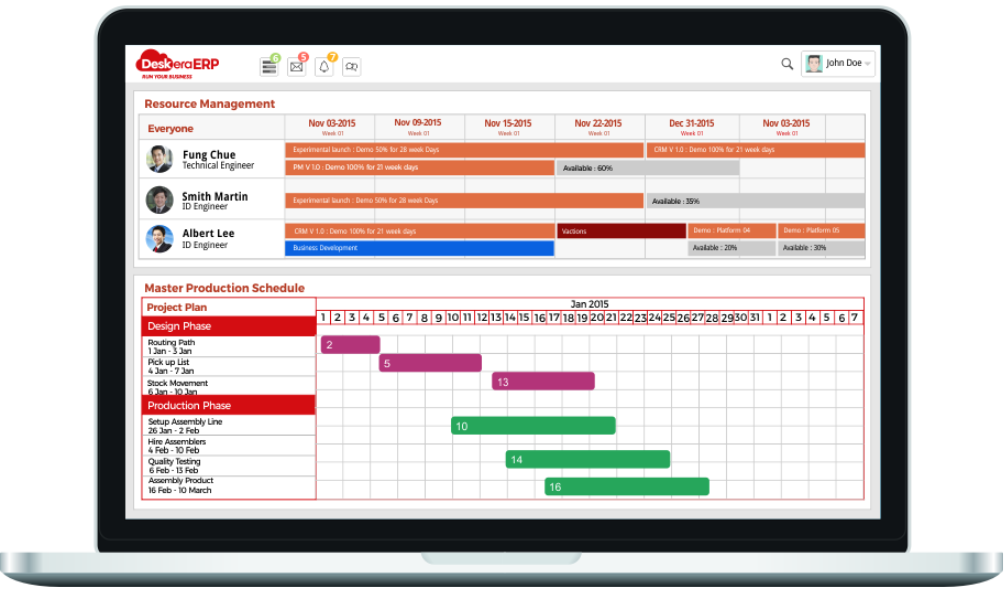
Deskera Books enables you to manage your accounts and finances more effectively. Maintain sound accounting practices by automating accounting operations such as billing, invoicing, and payment processing.
Deskera CRM is a strong solution that manages your sales and assists you in closing agreements quickly. It not only allows you to do critical duties such as lead generation via email, but it also provides you with a comprehensive view of your sales funnel.
Deskera People is a simple tool for taking control of your human resource management functions. The technology not only speeds up payroll processing but also allows you to manage all other activities such as overtime, benefits, bonuses, training programs, and much more. This is your chance to grow your business, increase earnings, and improve the efficiency of the entire production process.
Final Takeaways
We've arrived at the last section of this guide. Let's have a look at some of the most important points to remember:
- Chemicals are used to manufacture a wide range of products, from medicines and personal care items to construction materials and food additives. The quality, efficiency, and cost-effectiveness of chemical production are critical factors that determine the success of these industries.
- Model-Based Design (MBD) is an advanced design methodology that involves the creation and use of models to design, simulate, and optimize complex systems. MBD enables engineers to design and test systems virtually, before physical prototypes are built, resulting in improved design quality and reduced development time and costs.
- MBD offers several benefits over traditional design methods, including improved design quality, reduced development time and costs, and increased productivity and efficiency. By applying MBD in chemical production, companies can improve their design processes, resulting in higher-quality products, reduced costs, and improved competitiveness.
- Model verification is the process of validating that the virtual prototype accurately represents the system model within the predetermined bounds. The degree of agreement between observed and simulated behaviours is a key component of the model validation process after this has been realised and understood. The iterative development process results in an appealing and useful model.
- MBD enables engineers to create accurate and detailed models of the chemical production process, which can be used to simulate the system's behavior and identify potential design flaws or optimization opportunities. By identifying and addressing these issues early in the design process, engineers can improve the overall quality of the final design.
- Improved safety and environmental performance: MBD can be used to simulate the behavior of the chemical production process under different conditions, including potential safety hazards and environmental impacts. This can help engineers identify and address potential safety or environmental issues early in the design process, improving the overall safety and sustainability of the final design.
- Collaboration and communication: Implementing MBD requires close collaboration between engineers, designers, and other stakeholders, to ensure the accuracy and effectiveness of the models. Effective communication is also crucial, as it allows for a better understanding of the design requirements and helps to ensure that the final design meets the project goals.
Related Articles
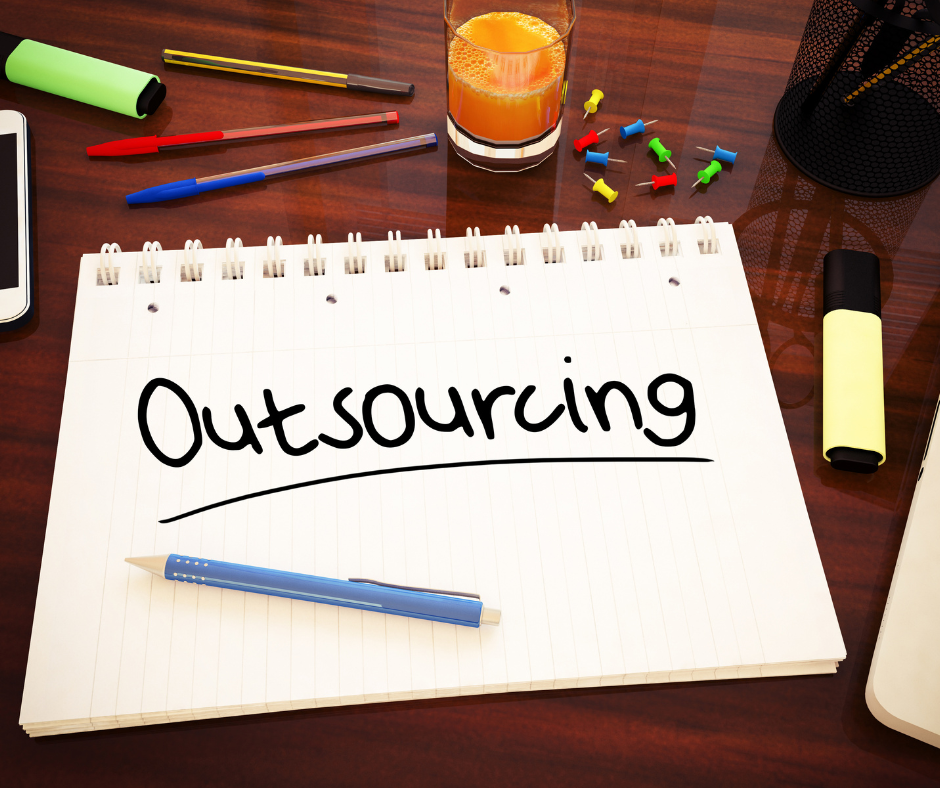
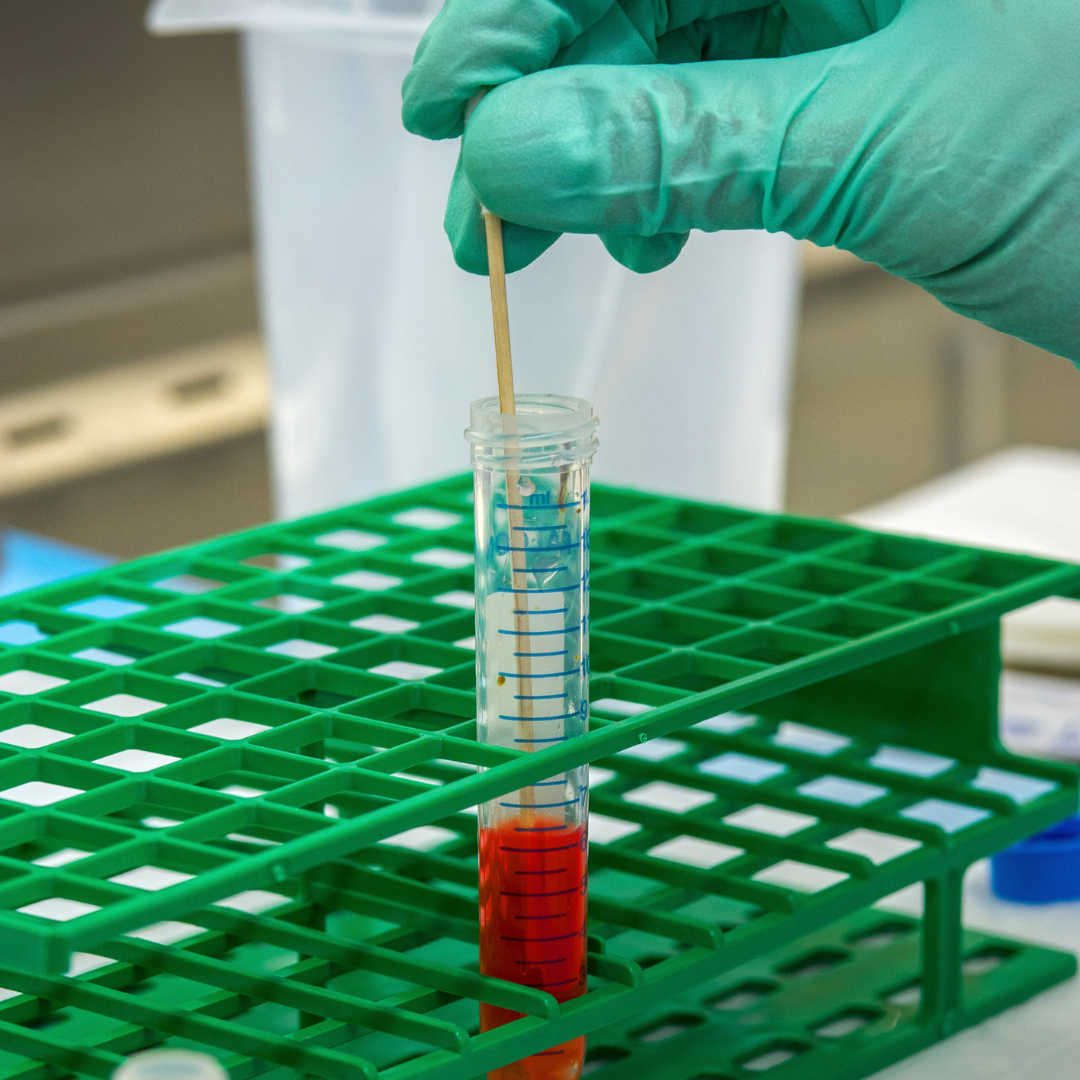
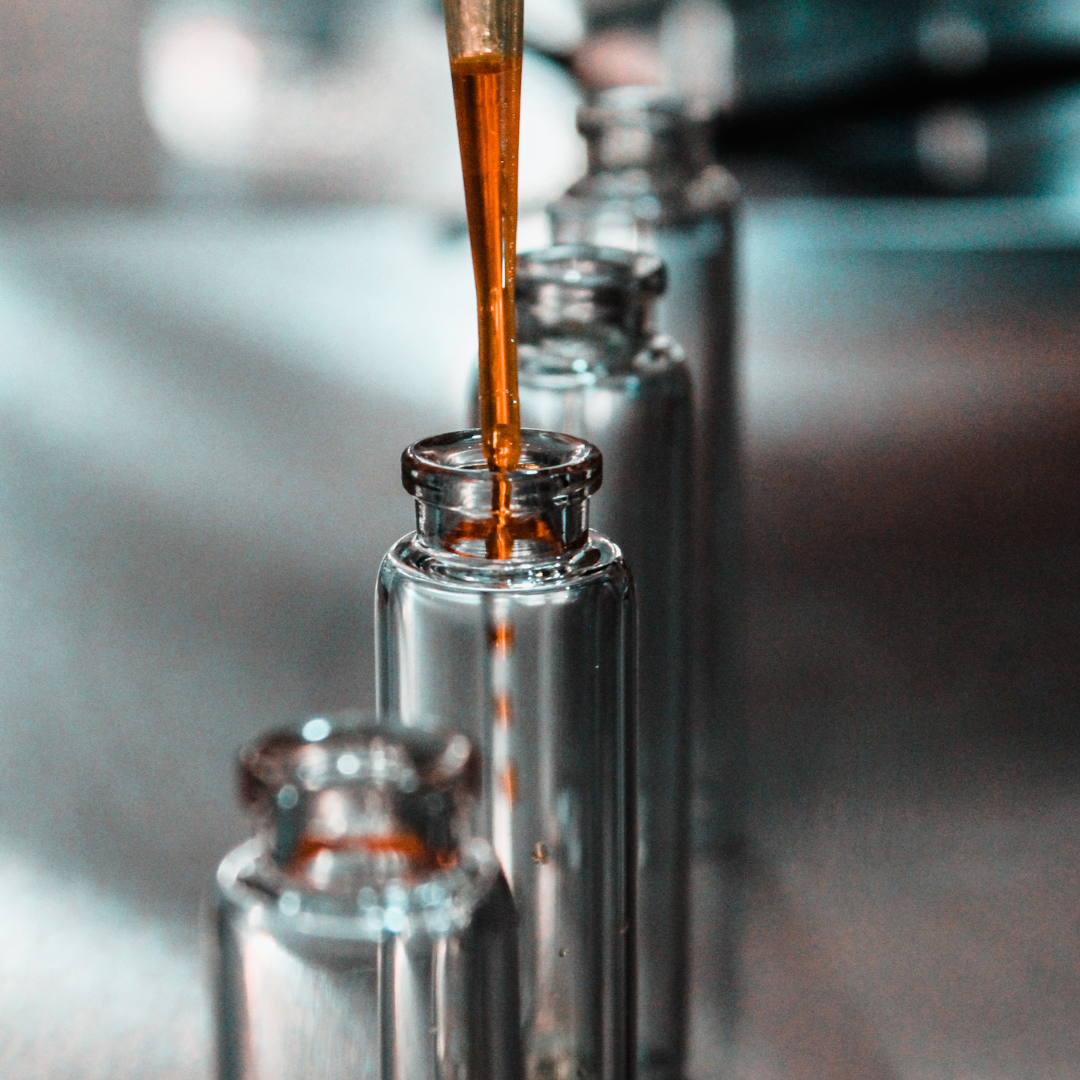
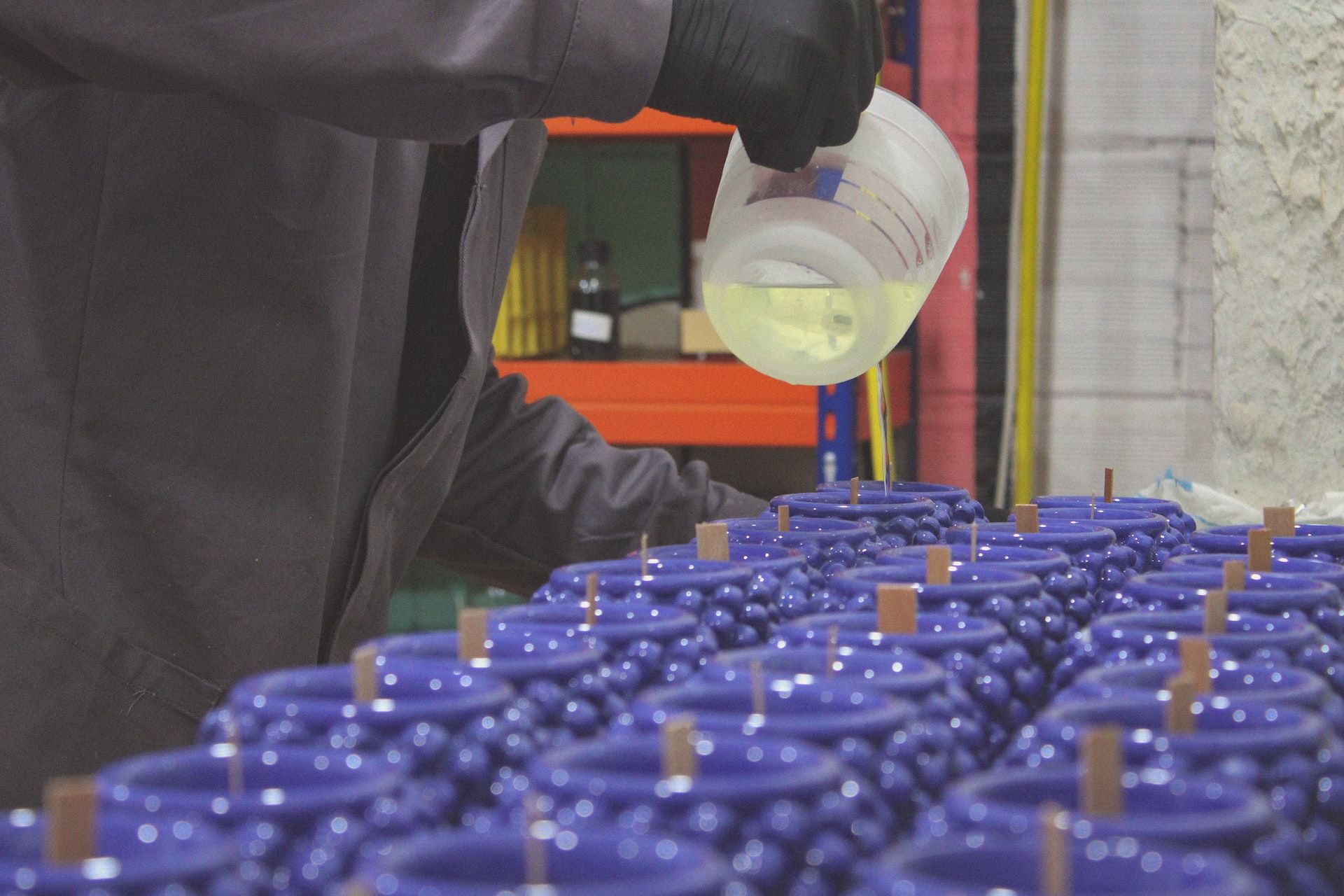
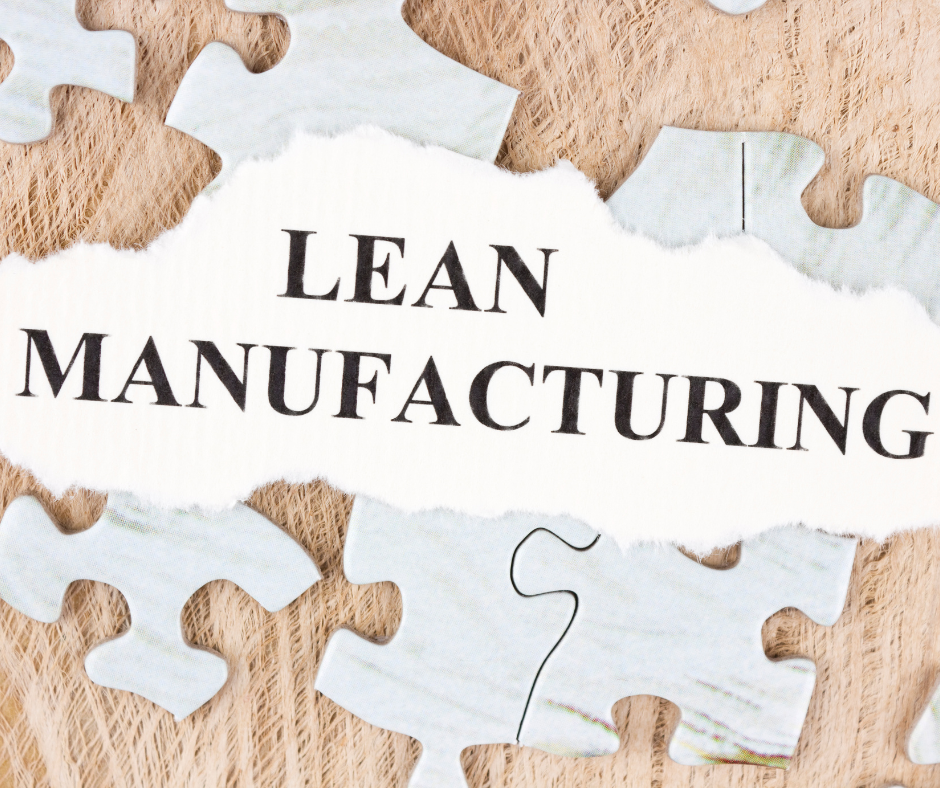